Плотность стеклопластика – Содержание стекла в полиэфирной смоле
Емкости из стеклопластика напрямую от производителя
Прайс-листНовости
Осенняя распродажаАкция на септик из стеклопластика от производителя при оплате за наличный расчет.
Плотность стеклопластика. Содержание стекла в полиэфирной смоле
Прочность септика из стеклопластика и других изделий (накопительные емкости, пожарные резервуары, кнс, септик с биофильтром и прочих) зависит от многих факторов. И толщина стенки является последним по важности. Важно содержание стекла в процентном соотношении, а также вид стекловолокна.
Необходимо разделять виды стеклопластика в зависимости от метода получения. Стеклопластик, полученный методом машинной намоткой тела на станке, где при удачных условиях получается содержание стекла порядка 40%. И стеклопластик, полученный при помощи ручной формовки, в котором содержание тоже может достигать 40%, но в реальности не более 25-30%.
Только при качественной намотке можно получить содержание стекла 40%.Произведем расчет плотности стеклопластика.
Плотность стекла известна и составляет ρст.=2500 кг/м3. Плотность смолы составляет ρсм.=1150 кг/м3.
Соответственно при содержании ровинга в материале 40% по весу (не по объему), получаем:
ρстеклопластика=1 кг/(0,4 кг/ρст.+0,6 кг/ρсм.)=1,467кг/м3
Цена одного кг смолы 150 р., ровинга 80 р.
Соответственно себестоимость одного килограмма составляет:
P=0,6*150 руб/кг+0,4*80 руб/кг=122 р.
Основные виды стекловолокна:
- Рогожа.
- Стекломат.
- порошковый;
- эмульсионный;
- длинноволокнистый.
- Стеклоровинг.
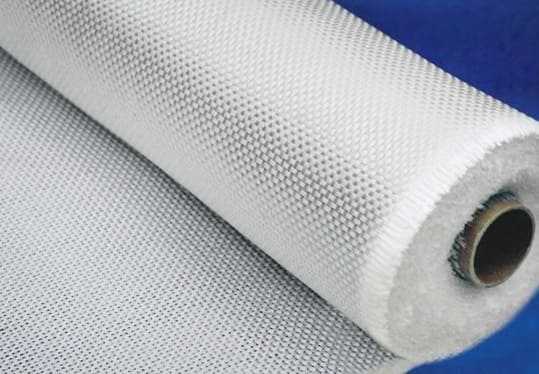
Рогожей – это стеклоткань, она и внешне напоминает ткань, переплетенную крест на крест. В старину плели ткань из листьев травы, которая называлась Рогоза. Сегодня эта ткань применяется как основа для производства из стеклопластика. Она очень имеет очень высокую прочность на разрыв. И при этом великолепно пропитывается смолой. Рогожа изготавливается при помощи плетения пучков ровинга. Нити проходят параллельно друг другу, а иначе их не сможет на сто процентов пропитать смола. Производится в различных вариациях плотности. У нас рогожа применяется при изготовлении плоских частей (перегородки, стенки и полусферы), а также иногда используется в намотке для получения так называемого “сэндвича”.
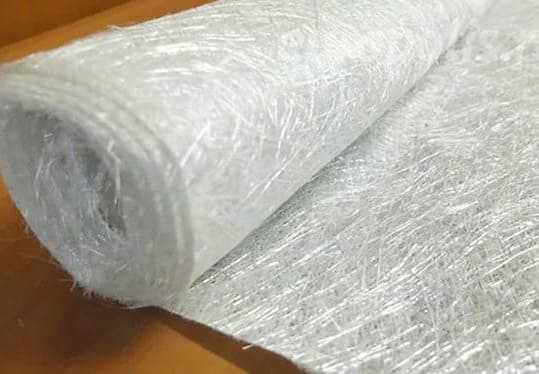
Стекломат рубленный. Изготавливается при помощи прессовки и склеивания кусочков ровинга (кусочки нитей длиной по 40 мм). Также стекломаты бывают трех типов:
Так же как и у рогожи, стекломат бывает разной плотности. На нашем производстве стекломат применяется при производстве плоских поверхностей, полусфер и формовки швов емкостей из стеклопластика.
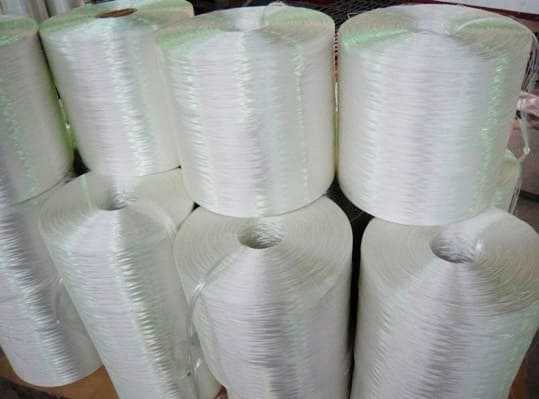
Стеклоровинг представляет собой пучок нитей. Их вытягивают из расплавленного стекла. Они имеют толщину около 15 мкм в зависимости от вида нитей и производителя (может доходить до 50 мкм. На нашем производстве применяется для машинной намотки цилиндра крест на крест. В процессе намотки септика из стеклопластика на барабан подается нитка, смоченная смолой. Имеет очень высокую устойчивость на разрыв. В погони за экономией, зачастую используется некачественный материал, который на станке рвется на подаче, в результате чего образуются пузыри и неравномерная плотность, что приводит к протечкам и трещинам в стеклопластике. Мы заинтересованы в постоянных клиентах, которые занимаются монтажом инженерных сетей в промышленных масштабах, поэтому мы так не делаем. Стеклопластик должен быть качественным, благодаря чему можно съэкономить на толщине изделия и не заклеивать дырки.
septik-master.ru
Cлоистые стеклопластики
Категория: Плотничкие работы
Cлоистые стеклопластики
Свойства стеклопластиков
Для получения стеклопластиков стеклянные волокна пропитывают смолой. Стеклянные волокна применяют в виде жгута (штапельные волокна, идущие в одном направлении, иногда предварительно напряженные), ткани (волокна в двух перпендикулярных направлениях, причем в каждом направлении их число различно) и, наконец, в виде холста (с произвольной ориентацией волокон).
Для пропитки используют полиэфирные, мочевиномеламиноформальдегидные и эпоксидные смолы, последние, правда, значительно дороже, но воспринимают намного большее количество наполнителя, обладают иными электрическими свойствами и т. д.
Прочность обычного стеклопластика при растяжении приближается к прочности стали — нагрузку воспринимают стеклянные волокна. Напряжения сжатия воспринимает смола, обладающая относительно высокой прочностью — около 30 % прочности стали. Показатели продольного сжатия, динамической нагрузки и стойкости такой конструкции ниже, поэтому, применяя стеклопластик как конструкционный материал, следует учитывать его свойства.
Для повышения прочности при растяжении стремятся применить максимум стеклянных волокон и минимум смолы; однако каждое волокно должно быть покрыто смолой, непропитанных мест быть не должно. Воздушные пузырьки снижают прочность материала. В связи с этим прочность стеклопластика, полученного под высоким давлением, гораздо выше, чем прочность материала, изготовленного без давления. В обычных условиях можно добиться объемного содержания стеклянных волокон до 50 %. Плотность стекловолокна равна 2,54 т/м3, смолы — 1,27 т/м3, т. е. при отношении 50 : 50 плотность стеклопластика равна 1,91 т/м3. Поскольку плотность стали равна 7,85 т/м3, стеклопластик той же массы выдержит нагрузку в 4 раза выше, чем сталь.
Стеклопластик обеспечивает герметичность, не корродирует, обладает маслостоикостью, стойкостью против воздействия большинства кислот, щелочей и растворителей. Этот материал удобен для формирования криволинейных поверхностей, а поэтому из него делают изделия, предназначенные для эксплуатации в воде, даже, в морской (от байдарок до небольших яхт, буи, садки). Из него делают кровельные детали (прозрачные). Поскольку его можно обрабатывать на простых станках (в сравнении с прессами для штамповки листовой стали), из стеклопластика изготовляют кузова транспортных средств, выпускаемых небольшими сериями (спортивных автомобилей, трамваев, локомотивов, опытных образцов). Пригоден стеклопластик и для корпусов электрошкафов, антенн, для печатных плат (благодаря изоляционным свойствам). Высокая прочность при малой плотности делает его пригодным для изготовления лыж, удочек, шлемов (для мотоциклистов).
Для любителей представляет интерес использование стеклопластика для ремонта и доработок изделий.
Стеклопластик обладает высокой стойкостью к атмосферным воздействиям, однако речь все же идет об органическом материале, изменяющемся под действием этих факторов. Кроме того, смола нередко начинает выделяться» как, например, на асфальте. Зола, смог, механические’ воздействия также вызывают повреждения стеклопластика, в связи с чем необходимо периодически (каждые 4—10 лет) восстанавливать наружную поверхность изделий из него.
Еще несколько слов о смоле. Она относится к материалам, в ходе полимеризации (образования цепи молекул) которых образуется новая структура. Полиэфир состоит из трех компонентов: смолы (густоватой бесцветной маслянистой жидкости), катализатора (менее густой жидкости, с запахом) и ускорителя (промотора) — обычно нафтената кобальта (темно-фиолетовая жидкость). Катализатор и ускоритель смешивать нельзя — даже небольшое количество смеси приведет к взрыву. Чтобы процесс полимеризации начался, смесь необходимо нагреть до температуры, при которой оба компонента начнут действовать. Для полного отверждения смолы в изделии ее температура должна быть выше точки инициирования и поддерживаться в течение определенного времени — при охлаждении процесс полимеризации прекращается. Об этом следует хорошо помнить в холодную погоду, особенно при изготовлении тонкостенных изделий. На те места, которые быстрее охлаждаются, следует внести больше ускорителя или же подвести теплоту, не забывая об опасности возгорания.
Для наслаивания можно также использовать эпоксидные смолы, которые наносят так же, как полиэфиры. Охлаждение смолы не связано с опасностью быстрого самопроизвольного отверждения.
Технология наслаивания
После того как продумана конфигурация изделия и готова форма, следует выбрать сепаратор — прослойку между формой и изделием, обеспечивающую извлечение готового изделия из формы.
В промышленности применяют специальные сепараторы, непрерывно появляются новые, более эффективные их виды. Сепаратор не должен приклеиваться к изделию, нарушать его поверхность, он должен обеспечивать гладкую поверхность и т. п.
В домашних условиях для плоских деталей в качестве сепаратора применяют стекло, небольшие детали делают вообще без сепаратора — изделие отделяется после усадки. Для поверхностей небольшой кривизны, главным образом выпуклых, достаточного целлофана (желательно, красного цвета, чтобы видеть места контакта). Целлофан смачивают в воде, натягивают, выравнивают и закрепляют по краям кнопками. С вогнутыми формами сложнее: целлофан наклеивают по частям, в местах соединения его следует тщательно обрезать. Формование с целлофаном всегда отражается на изделии — нужна дополнительная зачистка. Натяжение целлофана на форме не должно быть чрезмерным, чтобы он после высыхания (усадки) не отделился. Для поверхностей большой кривизны в качестве сепаратора используют, например, расплавленный парафин, порошкообразный воск и т. п., создавая сплошную жирную прослойку.
Небольшие поверхности можно разделять алюминиевой фольгой с обязательным тщательным разглаживанием во избежание попадания смолы в морщины. Для слоистых поверхностей используют промышленные сепараторы, например, поливиниловый спирт.
Способ приготовления жидкого сепаратора. В 1 л денатурированного спирта при 20 °С тщательно размешивают 320 г порошкообразного поливинилового спирта. В большом сосуде нагревают до 90 °С 3,5 л воды. Снимают сосуд с огня и очень осторожно, постоянно перемешивая, в горячую воду доливают приготовленный ранее раствор. Затем добавляют еще 1 л денатурированного спирта, вносят 40 г любого стирального порошка и тщательно размешивают. Раствор наносят на форму щеткой. С готового изделия этот сепаратор смывают теплой водой.
Прежде чем приступать к наслоению, в чашку насыпают опилки и стиральный порошок, увлажняют и размешивают. Если в процессе работы на руках начинает отверждаться смола, ее стирают этой смесью. Нельзя смывать смолу ацетоном, так как на руках образуется тонкая -пленка, причем даже там, где смолы не было. В рукавицах обычно работать не удается.
После этого готовят стеклянную ткань или холст: ткань целесообразнее использовать для ровных участков, холст — для изгибов. Тонкую ткань (масса до 150 г/м2) используют для тонких изделий, которые должны обладать высокой прочностью. Для вогнутых поверхностей такая ткань неудобна, так как возникают воздушные пузырьки. Легче всего работать с тканью массой 250 г/м2. Более толстые ткани (500—600 г/м2) используют для крупных деталей, однако они часто вздуваются. Вначале на сухую форму накладывают ткань и мягким карандашом или углем очерчивают контуры. В сосуд вместимостью 4 л наливают слоем около 1 см бензол, а затем весь сосуд заполняют пенополистиролом, который мгновенно растворяется. Кистью, смоченной в этом растворе, обводят контур, нанося линию шириной около 2 см. После высыхания бензола стеклоткань обрезают ножницами по этой линии. При такой обработке она не будет «сыпаться». Отдельные куски ткани нумеруют и закатывают в рулон бумаги.
Приготавливают весы, полиэфир, катализатор и ускоритель, несколько чистых жестянок или стаканов, кисть и шпатели, ацетон (для промывки кисти). Необходимо приспособление для перемешивания смеси: в патроне-электродрели закрепляют стальной стержень соответствующего диаметра длиной 40 см, на конце которого
Рис. 1. Лопасть мешалки с хвостовиком для крепления в патроне дрели
приварена лопасть из листовой стали толщиной 2 мм. Этим приспособлением (рис. 1) надежно перемешивают катализатор и смолу. Их необходимое количество целесообразно приготовить заранее (за несколько дней)с целью совершенного осмотического перемешивания. Следует помнить, что некоторые специальные смолы, особенно импортные, уже содержат ускоритель, а инициируются катализатором.
Рассмотрим обычный для домашнего применения способ — наслоение без давления на вогнутую или выпуклую форму.
Итак, берут приготовленную точно в соответствии с инструкцией по применению смесь смолы с катализатором, используя ее с большой осторожностью. В небольшой сосуд (вместимостью 1 л) наливают смесь и, согласно инструкции, пипеткой вводят немножко фиолетового ускорителя. При этом нужно учитывать температуру формы и окружающей среды: если холодно, ускорителя добавляют больше, если тепло — меньше; в противном случае можно не успеть наложить смесь, и она отвердеет. Если же ускорителя мало, смола останется холодной, не отвердеет и не удастся достичь заданной прочности. Тогда следует сохранить хотя бы то, что можно: нанести на поверхность слой ускорителя, нагреть и т. д. Иногда материал отвердеет через год, иногда не отвердеет вообще.
Следовательно, начинать надо с небольшого количества смеси.
Чистота — важнейшее требование. Каждый раз необходимо пользоваться новой чистой посудой, поскольку даже небольшое количество смолы с катализатором из предыдущей порции намного, ускорит инициацию новой порции и ее не удастся использовать. Ни в коем случае нельзя занести даже каплю смолы с ускорителем в сосуд с чистой смолой или смесью с катализатором. В обоих случаях рано или поздно смола в сосуде отвердеет. Нельзя, разумеется, переносить мешалку куда-либо, тщательно ее не очистив.
Начало операции формования зависит от требований, предъявляемых к поверхности изделия. Если поверхность будет подвергаться обработке или будут присоединяться другие детали, достаточно тонкого слоя смолы на лицевой стороне изделия: на очищенную поверхность сепаратора, начиная с края, накладывают первый слой стеклоткани, инициируют ускорителем смолу, наливают смесь на ткань, растирая ее шпателем или кистью равномерно по всей поверхности. Пропитанная смолой стеклоткань становится прозрачной. Шпателем, кистью или кончиками пальцев равномерно обрабатывают всю поверхность, не оставляя нигде непропитанных мест или воздушных пузырьков под тканью. Пузырьки, особенно в других слоях, можно вскрыть, например лезвием, а их кромки покрыть смолой. Куски стеклоткани накладывают, начиная с одного края, последовательно покрывая всю поверхность, при этом ткань натягивают от центра к краям, избегая морщин. Если это не удается, морщины прорезают ножницами, а кромки разрывают. Для следующего слоя можно нарезать сухую ткань. При накладке стеклоткани ее края должны выступать на 3—6 см.
Следующий слой укладывают сразу же, пока смола не начала нагреваться. В противном случае необходимо подождать, пока она немного остынет, иначе химическая реакция начнется прежде, чем удастся устранить пузырьки и хорошо разгладить ткань. Работать следует быстро, чтобы смола начала отвердевать сразу же после нанесения всех слоев и окончательного выравнивания и обтяжки поверхности целлофаном. При укладке стеклоткани в последующих слоях места стыковки необходимо чередовать. Для последующих слоев потребуется меньше смолы, так как верхний слой частично насыщается снизу. Если новый слой нанести с перерывом, поверхность окажется неровной, с наплывами. Перед отверждением новый слой стеклоткани вдавливается в неровности; после отверждения необходимо наложить более толстый слой смолы только для выравнивания наплывов и создания следующей целостной пленки из новой стеклоткани. Если края ткани приподнимаются, их следует обрезать ножом или ножовкой и разровнять или же укрыть поврежденное место холстом или штапелем, чтобы следующий слой мог лечь на ровную поверхность. Такой расход смолы приводит к увеличению массы изделия и снижению его прочности.
Желательно работать с двумя формами — нижней и верхней (матрицей и пуансоном), чтобы избыточная смола своевременно выдавливалась, а воздух не подсасывался (это происходит при ручном наслаивании, когда ткань отпружинивает от нижнего слоя). Однако две формы можно себе позволить только в редких случаях. С ровными и искривленными в одном направлении поверхностями (гофрами) работать проще.
Для лучшего понимания технологии целесообразно изложить процесс промышленного производства волнистого стеклопластика, в котором применяют стальную матрицу, т. е. плиту с образцом волнистой детали снизу, и пуансон в виде стальных труб, наружный радиус которых равен внутреннему радиусу гофров.
Рис. 2. Фазы 1—3 получения волнистых кровельных материалов из стеклопластика
На плоский рабочий стол вначале кладут целлофановую ленту — сепаратор, разматывают нарезанную ткань, наливают и растирают смолу шпателем шириной 30 см равномерно по всей поверхности, сразу же после этого накладывают второй слой стеклоткани, наливают смолу, вновь растирают шпателем, укладывают верхний слой целлофана, сухим шпателем разглаживают его и удаляют воздушные пузырьки. Затем все набранные слои сдвигают со стола на подготовленную стальную матрицу. Ткань шириной 1 м, уложенную на волнистую матрицу, последовательно нагружают трубами от центра к краям (рис. 2). Необходимо следить за тем, чтобы не возникали наклонные морщины — их выравнивают, подтягивая свободный край целлофана. Стальные матрицы нагревают паром, что значительно ускоряет отверждение. После завершения основной части полимеризации стальные трубы снимают, а кромки изделия отрезают по стальной матрице. Целлофан оставляют как защитную упаковку для погрузочно-разгрузочных и транспортных операций.
При надлежащем технологическом процессе не приходится касаться смолы ни рукой, ни кистью. Нужно подумать, как с помощью простейшего приспособления добиться обжатия всей верхней поверхности стеклопластика. Если в рассмотренном примере вместо свободных труб была бы применена иная форма, возникли бы сложности с исправлением местных дефектов по толщине смолы. Приспособление оказалось бы очень дорогим, возникали бы трудности укладки проклеенных слоев между матрицей и пуансоном. Целлофан обеспечивает получение стеклообразной поверхности без дополнительной оснастки, его можно применять для любых поверхностей большой площади.
Усадка слоистых пластиков — фактор, который необходимо всегда учитывать. Ее значение лежит в пределах 1—15 % в зависимости от температуры наслоения, вида смолы, наполнителей, формы изделия. Устранить усадку нельзя, можно лишь регулировать в определенном интервале температуру — чем выше температура отверждения, тем больше усадка. У плоских и вогнутых форм большой площади и объема усадка способствует извлечению изделий. В больших выпуклых формах, наоборот, изделие напрессовывается, а поэтому форма должна быть разъемной, надувной и т. п. (рис. 3).
Стеклянные волокна применяют обычно в виде ткани или холста. Штапель — полуфабрикат для производства стеклянных тканей и холста, однако в последнее время его используют непосредственно, например, для изготовления витых сосудов, удочек. Для получения стержня стеклянную предварительно напряженную арматуру выдерживают до полного отв.рждения смолы. Прочность таких стержней при изгибе значительно выше, чем с арматурой без предварительного напряжения. Слоистые пластики можно использовать в качестве упругих элементов, например для кресел-качалок (речь идет о дугах длиной около 120 см, устанавливаемых на ножках кресла; сжимаясь, дуги сообщают креслу обратное движение).
Рис. 3. Формы (А) и детали (Б) из стеклопластика: 1 — вогнутая негативная; 2 — выпуклая негативная; 3 — Еыпуклая позитивная; 4 — вогнутая; 5 — выпуклая разъемная; 6 — выпуклая надувная; 7 — лицевая сторона
Существует ряд промышленных технологий наслоения» например, в специальный пистолет-распылитель поступают раздельно смола с катализатором и ускоритель. Капли компонентов уносятся воздухом, падают на форму и смешиваются. Более сложным является пистолет с тремя каналами, в котором третий канал служит для подачи стеклянных волокон, выбрасываемых одновременно с двумя компонентами на полость формы. Пучок стеклянных волокон поступает в пистолет и в потоке воздуха разрезается вращающимся ножом до заданной длины. Речь, собственно, идет о стеклянном холсте, получаемом на месте. Устройство работает с большой скоростью, руки не касаются жидких компонентов, поток воздуха способствует уплотнению изделия. Очистка пистолета не представляет трудности, так как реагенты смешиваются вне сопла. Штапель, конечно, наиболее дешедый материал, холст — дороже, стеклоткань — самый дорогой.
Обычная стеклоткань имеет полотняное переплетение, т. е. число волокон в основе и утке одинаково. Ее применяют для изделий, равномерно нагруженных во все стороны. Ткани выпускаются массой 135, 250, 365, 500, 600, 800 и 1000 г/м2, в небольших количествах — 50 г/м2 для поплавков гидросамолетов, кузовов автомобилей.
Саржевое переплетение характеризуется большим числом волокон в основе, следовательно, выдерживает гораздо большие в сравнении с утком нагрузки в этом направлении.
Стеклянный холст имеет вид войлока. Хаотично расположенные стеклянные волокна соединены различными средствами. Холст очень удобен в работе, особенно при закругленных поверхностях, он не вспучивается, не пружинит, как ткань. Правда, прочность изделий из холста несколько ниже. Его используют, например, для перекрытия соединяемых деталей из слоистого пластика. Из холста можно нарезать ленточки, которые пропитывают смолой и кистью заталкивают в угловые швы, что облегчает отделочное шлифование.
Еще одно замечание. Для асфальтовой изоляции используют стеклоткань, похожую на джутовую ворсовую ткань или на тонкую белую кирзу. Однако она изготовлена не из бесконечных волокон, а из стеклянного штапеля. В связи с этим ее нельзя применять для изделий, подвергающихся воздействию воды и атмосферных факторов: под воздействием влаги стеклопластик разрушается. Для домашнего интерьера можно использовать почти любой материал — ткани, бумажные волокна, пластмассы, древесину и т. д.
Стеклянные волокна для слоистых пластиков необходимо подвергнуть специальной обработке — замасливанию, сообщающей им смачиваемость смолой. Однако за-масливатели не должны снижать прочность слоистого пластика. Такие свойства стеклянных волокон, как хрупкость, острота, требуют особого внимания к технике безопасности работы с ними.
Рассмотрим способ получения качественной глянцевой или цветной поверхности криволинейных изделий непосредственно при изготовлении слоистого пластика, без дополнительного шлифования. Обязательными условиями являются негативная тщательно отполированная форма и сепаратор с твердой и плотной поверхностью. Необходимо также иметь тиксотропную смолу, обычно содержащую так называемую белую сажу, т. е. коллоидную окись кремния. Речь идет об обычной смоле с добавкой 15% по массе коллоидной окиси кремния. Под ее действием полиэфирная смола желатинизируется, не стекает с вертикальных поверхностей и способна образовывать сплошную пленку. В смолу можно добавить и светостойкую минеральную краску, окрасив тем самым геле-образную пленку. Используя краситель впервые, необходимо предварительно проверить, не будет ли он препятствовать отверждению. Однако длительные испытания выполнить трудно. Для смол выпускают специальные красители, большей частью довольно дорогие.
Итак, имеем качественную форму, сепаратор (например поливиниловый спирт) и окрашенную смолу. Удалив сжатым воздухом с сепаратора пыль, доливают в смесь смолы с катализатором ускоритель, перемешивают, равномерно наносят смесь на сепаратор и растирают, как при применении тиксотропных материалов (однако толщина слоя в этом случае должна быть больше, чем у лака). Затем на лицевую сторону осторожно накладывают первый слой тонкого холста без особого нажима, чтобы не вдавить его в лицевую поверхность изделия. Немедленно после этого смешивают смолу для второго слоя (можно без лака и красителя), наносят как обычно, и пропитывают ею ткань сверху. С гелеобразной пленкой дело обстоит проще — она не стекает, ее не нужно растирать. Быстро наносят следующие слои ткани и смолы, устраняя воздушные пузырьки и непропитанные места. В заключение накладывают целлофан или другие пленки, натягивают и нагружают так, чтобы ткань везде прилегала плотно.
Если все операции выполнены правильно и нет пузырьков, на второй день изделие готово. В противном случае основная работа впереди. Вначале необходимо замазать пузырьки: на поверхности их видно хорошо, а внутренние обычно проявляются прогибом тонкой стенки при шлифовании. Пузырьки вскрывают, обрезают кромки или делают надрезы, заполняют полости смолой и полиэфирной мастикой с холстом или штапелем. Учитывая усадку и обработку, материал накладывают с некоторым припуском. Поверхность покрывают целлофаном, закрепляя края лейкопластырем или иным способом. Очень удобна для этого гелеобразная эмаль. Полиэфирная мастика должна быть свежей, тогда она быстро отверждается; при работе с ней следует точно соблюдать требования инструкции по применению. Если изделие не будет подвергаться воздействию воды, достаточно автомобильной мастики.
После того как завершены отделка поверхности стеклопластика окрашенной смолой и шлифование, все изделие полируют тонкой полировальной пастой и фетром. В промышленных условиях дополнительно напыляют слой бесцветного эпоксидного лака.
Иногда после зачистки дефектов и затирки мастикой на поверхность изделия наносят лакокрасочное покрытие. Технология аналогична окраске металлов. Полиэфирные лаки и лаки на базе примененной смолы нельзя рекомендовать для домашних условий (шлифуются и полируются под водой, наносится толстый слой). Эпоксидные лаки наносятся лучше и почти не требуют полировки, однако обладают небольшим сроком службы.
Изготавливаемые на предприятиях лодки окрашивают нитролаком, в домашних условиях этого не делают.
Представляет интерес ремонт поврежденных лодок. Разлохмаченные кромки обрезают, изнутри снимают защитное лакокрасочное покрытие, шероховатят поверхность вокруг отверстия на ширину 5 см, обезжиривают ее и накладывают заплату из материала, аналогичного материалу лодки. Предварительно снаружи накладывают целлофан и планкой или стальной лентой прикрепляют его к дну лодки, копируя ее конфигурацию. Вначале пропитывают смолой трещины в корпусе лодки, затем промазывают шероховатую поверхность, после чего последовательно укладывают слои ткани или холста, пропитывая их смолой до заданной толщины. В заключение валиком накатывают целлофан и поджимают стальным листом, картоном или мешками с песком. После отверждения снимают бандаж и шлифуют восстановленное место до заданной формы, а изнутри — только для удаления наплывов.
Крупные деревянные или железные суда, которые тяжело кантовать, устанавливают на козлы на высоте 1 м от земли. Очищают дно до основного материала и последовательно наклеивают кусок стеклоткани размером 30 X X 30 см с перекрытием 3—4 см. Затем приготавливают небольшое количество смолы с малым временем реакции. Второй слой накладывают с таким расчетом, чтобы чередовать перекрытия первого слоя. Если судно изношено настолько, что стеклопластик уже стал несущим элементом, число слоев должно быть достаточно большим.
Очистка инструмента при работе с полиэфиром довольно проблематична. После отверждения смолы ее нельзя снять никаким растворителем. Ацетоном можно промыть кисть, если смола еще жидкая, однако часть смолы в ней остается, поэтому кисть можно использовать не более 5 раз. Целесообразнее пользоваться шпателем. Жестянки хотя и можно обжечь, но нет смысла тратить время. Руки вначале очищают смесью опилок с моющим средством, а затем моют теплой водой с мылом. Ножницы и другой металлический инструмент приходится очищать острым предметом после высыхания смолы, когда она после усадки несколько отстанет от металла. С одежды смолу можно удалить ацетоном только сразу же после ее попадания. Твердые шарики смолы иногда можно раздробить молотком, не повреждая ткань. Рабочие одежду и обувь очистить практически нельзя.
Отвержденный стеклопластик выдерживает кратковременный нагрев до 100 °С, размягчаясь, что позволяет при необходимости выправить форму изделия. Специальные смолы выдерживают более высокую температуру. В состав пластика можно ввести самогасящее средство, и тогда после удаления непосредственно от пламени изделие перестает гореть. Волнистый пластик с такой добавкой имеет специальное обозначение. Однако испытания показали, что при высоких температурах влияние добавки становится противоположным.
До сих пор речь шла о листах из слоистого пластика — плоских, волнистых, криволинейных. В то же время слоистые пластики обладают исключительными свойствами благодаря возможности выполнять трехслойные пластики — «сандвичи» и объемные несущие системы.
На рис. 4 изображены различные виды арматуры для плит, профилей из слоистых пластиков, в том числе многослойных, из продольной и пространственной арматуры. Продольные ребра могут быть изготовлены из листового алюминия, сотовых конструкций, папье-маше. Плиту из слоистого пластика можно усилить проволочной сеткой для повышения несущей способности, например, для небольших судов. «Сандвичи» можно изготовить с арматурой из пенополистирола, который приклеивают эпоксидным клеем к плитам. В процессе наслаивания следует эпоксидной смолой защитить поверхность полистирола от полиэфирной смолы, так как она мгновенно растворяется в стироле, как в бензоле или ацетоне, и сублимируется при температуре свыше 40 *С.
Рис. 4. Виды армирования многослойных стеклопластиков
В промышленных условиях применяют следующие многослойные конструкции: полиэфирный стеклопластик+ f бальза -f стеклопластик. Например, фирма «Белько бальза» (Франция) поставляет запатентованные материалы «Контуркор», выполненные в середине из бальзовых стоек с волокнами, перпендикулярными к поверхности; толщина материалов 5 мм и более в зависимости от конструкции. Материал обычно имеет вид плит, используемых с учетом их высоких тепло и звукоизоляционных, прочностных свойств, химической стойкости и низкой стоимости. Основные области применения — судостроение (переборки, обшивка танкеров, корпуса судов и т. д.), строительство (изоляционные облицовки, перегородки, стены, временные сооружения), химическое машиностроение (резервуары, сосуды, смесители).
Хорошо выполненный трехслойный материал из стеклопластика толщиной 1,5 мм с обеих сторон и проклеенной смолой бальзовой древесины толщиной 7 мм, т. е. общей толщиной 10 мм, имеет поверхностную массу около 8 кг/м2, причем масса бальзы составляет 1,3 кг. Плита 100 X 100 см с ребрами по контуру выдерживает 10 человек. Однако бальза —- дорогой материал. Если же бальзовую древесину (плотностью 0,2 т/и3) заменить липовой, тополевой, еловой древесиной (0,47 ТЛУГ*), поверхностная масса упомянутого трехслойного пластика возрастает на 1,5 кг/ма или до 9,5 кг/м2, т. е. бальзовая древесина дает лишь 16 % экономии. Для использования в домашних условиях этот материал очень удобен. Такие материалы с основой, например из древесно-стружечных плит, хотя и тяжелее, выдерживают большие нагрузки. Для менее нагруженных конструкций применяют плиты с комбинированной основой, например, с решеткой из древесно-стружечных плит, древесины с пенополистиро-лом или иным поропластом с соответствующими свойствами.
В судостроении материал «Контуркор» применяют В виде плит с использованием их способности изгибаться в небольших пределах. Технология строительства судов из этих плит такая же, как и стальных судов.
Трехслойные пластики обеспечивают получение изделий без применения форм, что очень экономично. Из них можно изготовить несущий каркас в окончательном исполнении согласно проекту, вырезать точные фасонные детали, их можно клеить, монтировать, соединять болтами, комбинировать с металлическими и другими несущими элементами корпуса и палубы. После проверки и тщательной сушки на элементы конструкции можно монтировать трехслойные плиты, изгибая, приклеивая и закрепляя их на каркасе. В местах соединения других плит необходимо выполнить специальной формы рабочие швы (обычно с уклоном 1 : 20, в замок и т. д.). Иногда перед установкой плиты необходимо доработать. Они должны быть тщательно склеены не только между собой, но и с ребрами, балками. Крепление необходимо при клеевом соединении, причем изнутри (рабочими распорками между несущим каркасом) и снаружи (вспомогательной наружной рабочей конструкцией). Специальными шаблонами проверяют отклонения от заданной формы, плавность кривых и симметрию поверхностей. Постепенно подходят к килю, борту или поверхностям большой кривизны, т. е. к местам, где необходимо применять другую технологию.
Полуфабрикаты небольшой площади фирма «Контуркор» изготавливает в негативных формах со следующими слоями: сепаратор, гелеобразная эмаль, поверхностный холст, ткань или несущий холст в заданном количестве с пропиткой смолой, плашки из древесины, внутренний слой стеклопластика, обычно пропитываемый с помощью трехканального пистолета-распылителя (штапель, смола с ускорителем и катализатор).
Лодки обычно склеивают из двух оболочек; одна из них образует дно, другая — палубу.
Рис. 5. Склеивание катамарана из двух оболочек: а — общий вид; 5 — элемент соединения борта; 1 — холст, пропитанный смолой
Их соединение должно быть прочным и водонепроницаемым. Соединяемые поверхности предварительно зачищают, шероховатят и обезжиривают. Ленту холста отрезают по размеру этих поверхностей. Затем готовят медленно отверждающуюся смолу, тщательно наносят ее на поверхность одной оболочки, накладывают ленту холста, пропитывают ее смолой. То же делают со второй оболочкой, а затем их соединяют. На швы накладывают рейки и стягивают несколькими струбцинами по всему контуру, затем нагревают или наносят слой ускорителя, чтобы смола начала полимеризоваться только после стыковки обеих оболочек. После отверждения обрезают выступающие стекло ткань и смолу, снаружи шов заделывают мастикой, а изнутри .заполняют холстом, штапелем и массой из пропитанных смолой древесных опилок, а затем заклеивают лентой холста (рис. 5).
Детали из слоистых пластиков, помимо склеивания, соединяют заклепками или винтами, как деревянные детали. Окончательно на изделие наносят еще один слой ткани, защищающий его от коррозии.
Формы
Существуют различные виды форм. Наиболее типичными являются негативные формы, в которых лицевая поверхность изделия образуется в первом слое формирования, снизу.
В совершенно гладкой форме из тиксотропной смолы получают изделия с высококачественной поверхностью. Сами формы изготавливают из любого материала: гипса, древесины, металла, слоистого пластика, резины, стекла, глины.
При наличии предмета, копию которого необходимо получить из слоистого пластика, форму изготавливают так же, как для отливки. Для детали сложной конфигурации форму делают разъемной в нескольких плоскостях, а в качестве машриала применяют гипс. Вначале изготавливают нижнюю половину формы, после отверждения поверхности разъема шлифуют и лакируют. Для повышения герметичности устанавливают два направляющих штифта (рис. 78). После отверждения второй половины извлекают модель, собирают форму, устраняют неточности и полируют форму. Затем наносят сепаратор, и форма готова к наслоению изделия.
Гипс засыпают в клеевой грунт (с целью замедления схватывания), непрерывно перемешивая до получения не очень густой кашицы. (Клеевой грунт приготавливают следующим образом: в сосуд вместимостью 3 л наливают холодную воду, засыпают 500 г клея и выдерживают 24 ч. Затем воду нагревают, добавляют 150 г гашеной извести и нагревают до кипения. После охлаждения грунт выливают в чистую воду в соотношении 50—100 мл раствора на 1 л воды. С целью ускорения схватывания добавляют поваренную соль или раствор квасцов.)
Рис. 6. Разъемная форма для изделия из стеклопластика: 1 — форма в сборе; 2 — нижняя полуформа со штифтами; 3 — верхняя полуформа с отверстиями для штифтов
Рис. 7. Деревянные формы вращения: 1 — плоскость разъема формы
Гипсовую массу заливают в ящик, в котором закреплена модель, и дают ей высохнуть. После контроля на лицевую сторону наносят сепаратор — шеллак или воск.
Если изделие из слоистого пластика имеет конфигурацию детали вращения, изготавливается «на глазок» или по собственному эскизу, целесообразно применять позитивные деревянные (орех, клен, ольха, липа и др.) формы, вытачиваемые на токарном станке (рис. 7). Поверхность формы не должна быть очень гладкой, так как ее облицовывают целлофановой пленкой, чтобы обеспечить съем изделия после усадки. Эти формы можно сделать разъемными — из двух или четырех деталей, что упрощает снятие изделия. Стенки делают не цилиндрическими, а с конусностью 2°. Иногда вытачивают модель в натуральную величину, наносят на нее слой шеллака и выполняют по ней форму из пластилина. Такая форма является негативной и позволяет наносить на изделие глазурь (гелеобразную эмаль).
Форму для изделий из слоистых пластиков обрабатывают так же, как и сами изделия. Следовательно, ее можно выполнить по модели, например по лодке, для чего на копируемую часть лодки напыляют сепаратор, остальное защищают от загрязнения фольгой, а затем напыляют слой смолы. После этого наносят гелеобразную эмаль, а на нее — несколько слоев стеклоткани или холста. Из древесно-стружечной плиты вырезают поперечины (рис. 80), накладывают их на корпус лодки через 50 см и прикрепляют к оболочке полосками холста. Оболочку между поперечинами скрепляют планками из твердой древесины и укрепляют полосками ткани. В заключение поперечины соединяют между собой продольными брусьями сверху и по бокам, а в плоскости разъема кромку усиливают жесткой планкой. (Возможность выполнения всех этих операций за один процесс определяется конструкцией лодки.) После этого форму снимают. Если борта лодки имеют большую крутизну или если лодка внизу вообще шире, чем палуба, форму вначале снимают — даже если ее придется разрезать, а потом устанавливают арматуру по обмерам. Модель очищают и делают форму палубы или той ее части, которую намечено использовать. После этого обе половины формы собирают, обмеряют, устраняют все дефекты и тщательно полируют.
Рис. 8. Форма из слоистого пластика, полученная снятием оттиска готовой лодки: а — последовательность работы; б — готовая форма в упрочняющем каркасе
Резиновые формы удобны для круглых изделий: достаточно надуть камеру мяча и, если ее размеры устраивают, форма готова. Таким способом делают, например, светильники. На камеру (у клапана) накладывают металлическое кольцо (размер которого обеспечивает проход лампы накаливания). На кольце закрепляют конец лубяной полоски или иного материала, обтягивают ею камеру и закрепляют другой конец на кольце. Так продолжают до полного укрытия поверхности камеры. На поверхность наносят слой инициированной смолы (или прозрачного лака) и выдерживают в течение суток. Если нужно получить не светильник, а просто шар, нарезают из холста полоски, как кожуру апельсина, и накладывают на слой смолы с небольшим перекрытием. Готовый шар подвешивают за кольцо для сушки. Нельзя забывать, что воздух внутри камеры за счет тепла полимеризации нагревается и расширяется. Во избежание разрыва изделия часть воздуха необходимо периодически выпускать. На следующий день выпускают воздух из камеры и извлекают ее из изделия. Шар можно прошлифовать шлифовальным кругом или лентой (лучше — шкуркой или стеклянной крошкой). Окончательную внешнюю отделку выполняют известными способами.
Каучук — еще более эффективный материал для изготовления форм. Обладая хорошей текучестью, он заполняет малейшие полости модели. Благодаря упругости каучука формы легко снимаются даже с очень сложной модели, а значит, число разъемов можно свести к минимуму. В качестве сепаратора достаточно нанести тонкий слой растительного масла, зачастую же сепаратор вообше не требуется.
Сразу же по окончании вулканизации (в зависимости от марки каучука и температуры окружающей среды) форму снимают, каучук разрезают острым ножом и модель извлекают. В каучуковых формах можно получать изделия из эпоксидной и полиэфирной смол.
Поскольку каучуковые формы очень мягкие (а сам каучук дорогой), их делают очень тонкими — 3—6 мм. Поскольку при наслоении пластика в результате вынужденного обжатия при обработке смолы и удалении из него пузырьков форма может изменяться, ее вкладывают в отлитую из гипса толстостенную разъемную оболочку, обеспечивая стабильность каучуковой формы в процессе обработки и отверждения (полимеризации) смолы. После отверждения изделия раскрывают гипсовую оболочку, снимают каучуковую форму, а изделие подвергают необходимой обработке.
Техника безопасности
Смолы, катализатор и ускоритель — горючие вещества, которые необходимо беречь от огня и теплоты. При их хранении следует соблюдать осторожность, чтобы в случае, если разобьются банки, катализатор и ускоритель не смешались. Катализатор раздражает кожу, опасен для роговицы глаз: Смолу счищают с рук древесными опилками в смеси с раствором моющего средства или смывают теплой водой с мылом. По окончании работы на кожу рук наносят очищающую пасту (например-ИЭР-1, ХИОТ-6). При наслоении пластика стеклоткань или химикалии могут вызвать ухудшение самочувствия. Рабочее помещение необходимо тщательно проветривать.
Плотничкие работы – Cлоистые стеклопластики
gardenweb.ru
SammaS – Стеклонить
Для армирования пластиков могут использоваться самые разнообразные волокна, но для высокопрочных пластиков чаще всего используются стеклянные волокна. Это объясняется удачным сочетанием их свойств и не в последнюю очередь низкой стоимостью большого разнообразия промышленных стекловолокон.
Секловолокна по прочности превосходят все другие распространенные конструкционные материалы. Так, прочность неповрежденных волокон из E-стекла равна в среднем 365 кг/мм2, они имеют довольно высокий модуль Юнга (5-11)·103 кг/мм2 и на много превосходят в этом отношении армируемые ими полимеры. Поэтому в стеклопластиках большую часть нагрузки воспринимают волокна. А поскольку плотность стекла сравнительно низкая (~2.5 г/см3), стекловолокна имеют высокую удельную прочность и удельный модуль, что особенно важно при применении этих материалов в авиации и на водном или сухопутном транспорте и т.д.
Стекловолокна довольно инертны химически, а поскольку полимеры также хорошо устойчивы во многих агрессивных средах, то стеклопластики часто используются там, где металлы сильно корродируют, например, при изготовлении трубопроводов для химически агрессивных жидкостей, подземных емкостей для хранения бензина и т.д.
Промышленностью выпускаются стекловолокна двух основных типов, в виде непрерывной нити и штапельного (резанного) волокна. Исходным технологическим процессом для получения всех видов стекловолокон является процесс вытяжки нитей из расплава.
Стеклонить – это тонкая белая прядь собранная из некоторого количества элементарных нитей, изготовленных из стекла типа «E», произведенных с правым или левым направлением крутки и заданным числом оборотов на каждый метр длины. Нити могут быть одинарного и двойного плетения.
Однонаправленные стеклонити представляют собой срезы (отрезки нити определенной длины) с паковок стеклянных комплексных нитей или непрерывных элементарных нитей. Предназначены для фильтрации, изготовления теплозвукоизоляционных материалов, наполнения пластмасс и других целей.
Стеклонити двойного плетения применяются для производства различных тканых и нетканых материалов, для электроизоляции обмоточных и монтажных проводов, для производства композиционных материалов на основе эпоксидных, фенольных и других связующих.
В зависимости от применения стеклонити имеют различные типы замасливателя для обеспечения наилучших потребительских и технологических свойств при их дальнейшей переработке. Намотка стеклонити производится на катушки разного типа, исходя из требований оборудования для дальнейшего использования. Нанесение замасливателя в 2 – 3 раза увеличивает прочность стеклонити, придает эластичность и гибкость, что позволяет подвергать ее дальнейшей переработке. Намотка стеклонитей, пропитанных термореактивной смолой, является методом изготовления многих крупногабаритных изделий для авиационной, ракетостроительной, судостроительной и гражданской промышленности. Для стеклонити применяется парафиновый, крахмальный или водно-эмульсионный замасливатели.
Свойства стекловолокон
Свойства стекловолокон в первую очередь определяет состав стекла. Не менее значимой оказывается и термическая предыстория стекла.
Высокая прочность при растяжении – стекловолокна имеют очень высокий предел прочности при растяжении, превышающий прочность других текстильных волокон. Удельная прочность стекловолокон (отношение прочности при растяжении к плотности) превышает аналогичную характеристику стальной проволоки.
Тепло- и огнестойкость – так как природа стекловолокон неорганическая, они не горят и не поддерживают горение. Высокая температура плавления стекловолокон позволяет использовать их в области высоких температур.
Хемостойкость – стекловолокна не воздействуют на большинство химикатов и не разрушаются под их влиянием. Устойчивы стекловолокна и к воздействию грибков, бактерий и насекомых.
Влагостойкость – стекловолокна не сорбируют влагу, следовательно, не набухают, не растягиваются и не разрушаются под ее воздействием. Стекловолокна не гниют и сохраняют свои высокие прочностные свойства в среде с повышенной влажностью.
Термические свойства – Стекловолокна имеют низкий коэффициент линейного расширения и большой коэффициент теплопроводности. Эти свойства позволяют эксплуатировать их при повышенных температурах, особенно, если необходима быстрая диссипация температуры.
Электрические свойства – Поскольку стекловолокна не проводят ток, они могут быть использованы как очень хорошие изоляторы. Это особенно выгодно там, где необходимы высокая электрическая прочность и низкая диэлектрическая постоянная.
Свойства | Марка стекла | |||
A | C | E | S | |
Физические | ||||
Плотность, кг/м2 | 2500 | 2490 | 2540 | 2480 |
Твердость по Моосу | – | 6,5 | 6,5 | 6,5 |
Механические | ||||
Предел прочности при растяжении, МПа: | 3033 | 3033 | 3448 | 4585 |
при 22 °C | – | – | 2620 | 3768 |
при 371 °C | – | – | 1724 | 2413 |
при 533 °C | ||||
Модуль упругости при растяжении при 22 °C, МПа | – | 69,0 | 72,4 | 85,5 |
Предел текучести, % | – | 4,8 | 4,8 | 5,7 |
Упругое восстановление, % | – | 100 | 100 | 100 |
Термические | ||||
Коэффициент линейного термического расширения, 10-6К-1 | 8,6 | 7,2 | 5,0 | 5,6 |
Коэффициент теплопроводности, Вт/(м·K) | – | – | 10,4 | – |
Удельная теплоемкость при 22 °C | – | 0,212 | 0,197 | 0,176 |
Температура размягчения, °C | 727 | 749 | 841 | – |
Электрические | ||||
Электрическая прочность, В/мм | – | – | 19920 | – |
Диэлектрическая постоянная при 22 °C: | ||||
при 60 Гц | – | – | 5,9-6,4 | 5,0-5,4 |
при 1 МГц | 6,9 | 7,0 | 6,3 | 5,1 |
Потери при 22 °C: | ||||
при 60 Гц | – | – | 0,005 | 0,003 |
при 1 МГц | – | – | 0,002 | 0,003 |
Объемное сопротивление при 22 °C и 500 В постоянного тока, Ом·м | – | – | 1017 | 1018 |
Поверхностное сопротивление при 22 °C и 500 В постоянного тока, Ом·м | – | – | 1015 | 1016 |
Оптические | ||||
Коэффициент преломления | – | – | 1,547 | 1,423 |
Акустические | ||||
Скорость звука, м/с | – | – | 5330 | 5850 |
Табл. Свойства стекловолокон произведенных из различных марок стекла.
sammas.ru
Стекловолокно — Традиция
Пучок стеклянных волокон (стекловолокно) Сткловолокно для замеса бетонаСтекловолокно́ (стеклонить) — волокно или комплексная нить, формеруемая из стекла. В такой форме стекло демонстрирует необычные для себя свойства: не бьётся и не ломается, но вместо этого легко гнётся без разрушения. Это позволяет ткать из него — стеклоткань и прменять в разных областях производсва, например, бетона и т.д.
Стекловолокна естественного происхождения встречаются в местах, где в прошлом происходили извержения вулканов, название данного вида волокон — волосы Пеле[1]. Волосы Пеле имеют химический состав базальтовых пород, имеют включения кристаллов и по физико-механическим свойствам не являются аналогами стекловолокна[2].
Виды стекловолокна (стеклонити)[править]
Стекловолокно экструдируют из расплава стекла специального химического состава. Экструзия, как и в других случаях, производится путем продавливания расплава через прядильные фильеры. Исходный продукт, как и в других областях производства химических волокон получается в виде бесконечных элементарных волокон (филаментов), из которых далее в процессе переработки формируются или комплексные нити (диаметр филаментов 3—100 мкм (линейная плотность до 0,1 Текс)) и длиной в паковке 20 км и более (непрерывное стекловолокно), линейная плотность до 100 Текс, или в стеклянные ровинги (продукты линейной плотностью более 100 Текс). В этом случае, как правило, продукт перерабатывается в крученые нити (ровинги) на крутильно-размоточных машинах. Данные полуфабрикаты далее могут быть подвергнуты любым формам текстильной переработки в крученые изделия (нити сложного кручения, шнуры, шпагаты, канаты), текстильные полотна (ткани, нетканые материалы), сетки (тканые, специальной структуры).
СтекловолокноСтекловолокна также могут выпускаться в дискретном (штапельном) виде. Также исходный стеклянный ровинг может быть переработан путем резки, рубки или разрывного штапелирования в дискретные (штапельные) волокна со штапельной длиной 0,1 (микроволокно) — 50 см, титр волокна в данном случае как правило ниже, чем филаментных нитей и соответствует диаметру 0,1—20 мкм. Основная масса штапельных стекловолокон перерабатывается в нетканые материалы (кардные, иглопробивные, нитепрошивные, стеклохолст) по различным технологиям (кардочесание, преобразование прочеса, иглопробивание, нитепрошивание, «вэт-лэйд»), стекловату, штапельную пряжу. По внешнему виду непрерывное стекловолокно напоминает нити натурального или искусственного шёлка, а штапельное — короткие волокна хлопка или шерсти.
Основная область применения стекловолокна и стеклотекстильных материалов, — использование в качестве армирующих элементов стеклопластиков и композитов (т. н. «препреги»). Также стеклоткани могут самостоятельно использоваться в качестве конструкционных и отделочных материалов. В этом случае они зачастую подвергаются той или иной форме отделки, главным образом — пропитке связующим (латекс, полиуретан, крахмалы, смолы. прочие полимеры).
Непрерывное стекловолокно формуют вытягиванием из расплавленной стекломассы через фильеры (число отверстий 200—4000) при помощи механических устройств, наматывая волокно на бобину. Диаметр волокна зависит от скорости вытягивания и диаметра фильеры. Технологический процесс может быть осуществлен в одну или в две стадии. В первом случае стекловолокно вытягивают из расплавленной стекломассы (непосредственно из стекловарочных печей), во втором используют предварительно полученные стеклянные шарики, штабики или эрклез (кусочки оплавленного стекла), которые плавят в стеклоплавильных печах или в стеклоплавильных аппаратах (сосудах).
Производство штапельного стекловолокна.[3] Сткловолокно для тканейШтапельное стекловолокно формуют путём раздува струи расплавленного стекла паром, воздухом или горячими газами и др. методами.
Физико-механические свойства[править]
Механические свойства волокон:[4]
Волокно | Плотность, 103·кг/м3 | Модуль растяжения, ГПа | Предел прочности при растяжении, ГПа |
---|---|---|---|
E-стекло | 2,5 | 73 | 2,5 |
S-стекло | 2,5 | 86 | 4,6 |
Кремнезём | 2,5 | 74 | 5,9 |
Свойства высокомодульных волокон и однонаправленных эпоксидных композиционных материалов:[5]
Тип волокон | Марка волокна | Свойства волокон длиной 10 мм | Свойства композиционных материалов | |||
---|---|---|---|---|---|---|
σв | E | σв | E | σв / (pg), км | ||
ГПа | ГПа | ГПа | ГПа | |||
Стеклянные | ВМ-1 | 3,82 | 102,9 | 2,01 | 69,1 | 98 |
>> | ВМП | 4,61 | 93,3 | 2,35 | 64,7 | 114 |
>> | М-11 | 4,61 | 107,9 | 2,15 | 72,6 | 98 |
Борные | БН (сорт 2) | 2,75 | 392,2 | 1,37 | 225,5 | 75 |
>> | БН (сорт 1) | 3,14 | 382,4 | 1,72 | 274,6 | 87 |
>> | Борофил (США) | 2,75 | 382,4 | 1,57 | 225,5 | 80 |
Органические | СВМ | 2,75 | 117,7 | 1,47 | 58,5 | 111 |
>> | Кевлар-49 (США) | 2,75 | 130,4 | 1,37 | 80,4 | 100 |
Объёмная доля наполнителя 60 %.
Механические свойства волокон:[6]
Марка стекла | Плотность ρ, 10−3 кг/м3 | Модуль упругости Е, ГПа | Средняя прочность на базе 10 мм, ГПа | Предельная деформация ε, % |
---|---|---|---|---|
Высокомодульное | 2,58 | 95 | 4,20 | 4,8 |
ВМ-1 | 2,58 | 93 | 4,20 | 4,8 |
ВМП | 2,46 | 85 | 4,20 | 4,8 |
УП-68 | 2,40 | 83 | 4,20 | 4,8 |
УП-73 | 2,56 | 74 | 2,00 | 3.6 |
Кислотостойкое 7-А |
- Физико-механические свойства стекла
На предел прочности на растяжение стекол влияют микроскопические дефекты и царапины на поверхности, для конструктивных целей в основном применяют стекло с прочностью на растяжение 50 МПа. Стекла имеют Модуль Юнга около 70 ГПа.[4]
Применение стекловолкна[править]
Новый вид кровли[править]
По виду материал как металлочерепица, но качество в десятки раз лучше. Главными компонентами стеклопластиков являются стекловолокнистые армирующие материалы и синтетические связующие. Тонкие высокопрочные стеклянные волокна обеспечивают прочность и жесткость стеклопластика. Связующее придает материалу монолитность, способствует эффективному использованию механических свойств стеклянного волокна и равномерному распределению усилий между волокнами, защищает волокно от химических, атмосферных и других внешних воздействий, а также само воспринимает часть усилий, развивающихся в материале при работе под нагрузкой. Связующее придает материалу способность формоваться в изделия самых различных форм и размеров, что обеспечивает широкое применение материалов из стекловолокна — стеклопластиков во многих отраслях промышленности. Стеклопластик является материалом, куда входят стеклянный наполнитель и синтетическое связующее вещество (полимер).
Палочки из стекловолкна[править]
Палочки из стекловолокнаПалочка из стекловолокна хорошо справляется с застарелыми загрязнениями на посуде, плите, и даже литых дисков автомобилей. Борется с известковым налетом.
Материалы для строительства и отделки[править]
- Это:
- Стеклопластиковая арматура
- Теплоизоляция базальтовая
- Фибра базальтовая
- Блоки стеновые
- Штукатурные фасады.
Удивительно, но хрупкое стекло, расплавленное и вытянутое в виде тончайших нитей, полностью изменяет свои свойства, становится эластичным и гибким, мрожет применяться как ткань.
Стеклоткань – и ГОСТ устанавливает ее технические параметры, обладает целым рядом удивительных свойств, которые не имеют другие ткани:
- эта ткань не горит и представляет собой великолепный теплоизолятор. Отсюда – ее применение для изготовления одежды рабочих, связанных с открытым огнем – металлургов, сварщиков, пожарных;
- стеклоткань – экологически чистый продукт, никаких вредных воздействий на человека не оказывающий. Она пришла на смену ранее применявшемуся асбесту, тоже надежному против огня, но при этом вредному для здоровья;
- материал этот отлично выдерживает воздействие агрессивных сред – кислот и щелочей, к тому же может работать при высоких температурах. Поэтому одно из применений стеклоткани – это изготовление фильтров для газов и жидкостей в различных химических производствах;
- диэлектрические свойства позволили использовать стеклоткань для обматывания кабелей и обмоток трансформаторови т.д.
- ↑ Волосы Пеле — статья из Большой советской энциклопедии
- ↑ Аблесимов Н. Е., Земцов А. Н. Релаксационные эффекты в неравновесных конденсированных системах. Базальты: от извержения до волокна. — Раздел 6.1.1. Терминология. — М.: ИТиГ ДВО РАН, 2010.
- ↑ http://www.findpatent.ru/patent/231/2314370.html
- ↑ а б Болтон У. Конструкционные материалы, металлы, сплавы, полимеры, керамика, композиты. Карманный справочник /Пер с анг. — М.: Додека-XXI, 2004. — 320 с. — Карманный справочник. — ISBN 5-94120-046-3>
- ↑ Б. Н. Арзомасов. Конструкционные материалы. — Машиностроение, 1990. — 688 с. — ISBN 5-217-01112-2>
- ↑ Медведев В. В., Червяков А. Н. «Обоснование выбора композиционного материала для корабельных виброизоляторов».
traditio.wiki
Стекловолокно — Википедия
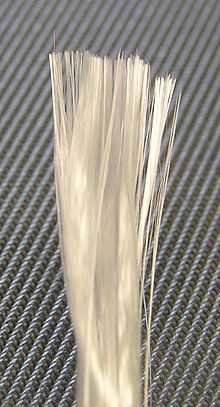
Стекловолокно́ (стеклонить) — волокно или комплексная нить, формируемые из стекла. В такой форме стекло демонстрирует необычные для себя свойства: не бьётся и не ломается, а вместо этого легко гнётся без разрушения. Это позволяет ткать из него стеклоткань.
Стекловолокна естественного происхождения встречаются в местах, где в прошлом происходили извержения вулканов, название данного вида волокон — волосы Пеле[1]. Волосы Пеле имеют химический состав базальтовых пород, имеют включения кристаллов и по физико-механическим свойствам не являются аналогами стекловолокна[2].
Виды стекловолокна (стеклонити)
Стекловолокно экструдируют из расплава стекла специального химического состава. Экструзия, как и в других случаях, производится путём продавливания расплава через прядильные фильеры. Исходный продукт, как и в других областях производства химических волокон, получается в виде бесконечных элементарных волокон (филаментов), из которых далее в процессе переработки формируются или комплексные нити (диаметр филаментов 3—100 мкм (линейная плотность до 0,1 Текс)) и длиной в упаковке 20 км и более (непрерывное стекловолокно), линейная плотность до 100 Текс, или в стеклянные ровинги (продукты линейной плотностью более 100 Текс). В этом случае, как правило, продукт перерабатывается в крученые нити (ровинги) на крутильно-размоточных машинах. Данные полуфабрикаты далее могут быть подвергнуты любым формам текстильной переработки в крученые изделия (нити сложного кручения, шнуры, шпагаты, канаты), текстильные полотна (ткани, нетканые материалы), сетки (тканые, специальной структуры).
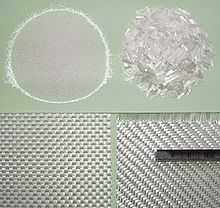
Стекловолокна также могут выпускаться в дискретном (штапельном) виде. Также исходный стеклянный ровинг может быть переработан путём резки, рубки или разрывного штапелирования в дискретные (штапельные) волокна со штапельной длиной 0,1 (микроволокно) — 50 см, титр волокна в данном случае, как правило, ниже, чем филаментных нитей и соответствует диаметру 0,1—20 мкм. Основная масса штапельных стекловолокон перерабатывается в нетканые материалы (кардные, иглопробивные, нитепрошивные, стеклохолст) по различным технологиям (кардочесание, преобразование прочеса, иглопробивание, нитепрошивание, «вэт-лэйд»), стекловату, штапельную пряжу. По внешнему виду непрерывное стекловолокно напоминает нити натурального или искусственного шёлка, а штапельное — короткие волокна хлопка или шерсти.
Основная область применения стекловолокна и стеклотекстильных материалов, — использование в качестве армирующих элементов стеклопластиков и других композитов. Также стеклоткани могут самостоятельно использоваться в качестве конструкционных и отделочных материалов. В этом случае они зачастую подвергаются той или иной форме отделки, главным образом — пропитке связующим (латекс, полиуретан, крахмалы, смолы. прочие полимеры).
Производство
Непрерывное стекловолокно формуют вытягиванием из расплавленной стекломассы через фильеры (число отверстий 200—4000) при помощи механических устройств, наматывая волокно на бобину. Диаметр волокна зависит от скорости вытягивания и диаметра фильеры. Технологический процесс может быть осуществлён в одну или в две стадии. В первом случае стекловолокно вытягивают из расплавленной стекломассы (непосредственно из стекловарочных печей), во втором используют предварительно полученные стеклянные шарики, штабики или эрклез (кусочки оплавленного стекла), которые плавят в стеклоплавильных печах или в стеклоплавильных аппаратах (сосудах).
Производство штапельного стекловолокнаШтапельное стекловолокно формуют путём раздува струи расплавленного стекла паром, воздухом или горячими газами и др. методами.
Физико-механические свойства
Механические свойства волокон:[3]
Волокно | Плотность, 103·кг/м3 | Модуль растяжения, ГПа | Предел прочности при растяжении, ГПа |
---|---|---|---|
E-стекло | 2,5 | 73 | 2,5 |
S-стекло | 2,5 | 86 | 4,6 |
Кремнезём | 2,5 | 74 | 5,9 |
Свойства высокомодульных волокон и однонаправленных эпоксидных композиционных материалов:[4]
Тип волокон | Марка волокна | Свойства волокон длиной 10 мм | Свойства композиционных материалов | |||
---|---|---|---|---|---|---|
σв | E | σв | E | σв / (pg), км | ||
ГПа | ГПа | ГПа | ГПа | |||
Стеклянные | ВМ-1 | 3,82 | 102,9 | 2,01 | 69,1 | 98 |
>> | ВМП | 4,61 | 93,3 | 2,35 | 64,7 | 114 |
>> | М-11 | 4,61 | 107,9 | 2,15 | 72,6 | 98 |
Борные | БН (сорт 2) | 2,75 | 392,2 | 1,37 | 225,5 | 75 |
>> | БН (сорт 1) | 3,14 | 382,4 | 1,72 | 274,6 | 87 |
>> | Борофил (США) | 2,75 | 382,4 | 1,57 | 225,5 | 80 |
Органические | СВМ | 2,75 | 117,7 | 1,47 | 58,5 | 111 |
>> | Кевлар-49 (США) | 2,75 | 130,4 | 1,37 | 80,4 | 100 |
Объёмная доля наполнителя 60 %.
Механические свойства волокон:[5]
Марка стекла | Плотность ρ, 10−3 кг/м3 | Модуль упругости Е, ГПа | Средняя прочность на базе 10 мм, ГПа | Предельная деформация ε, % |
---|---|---|---|---|
Высокомодульное | 2,58 | 95 | 4,20 | 4,8 |
ВМ-1 | 2,58 | 93 | 4,20 | 4,8 |
ВМП | 2,46 | 85 | 4,20 | 4,8 |
УП-68 | 2,40 | 83 | 4,20 | 4,8 |
УП-73 | 2,56 | 74 | 2,00 | 3.6 |
Кислотостойкое 7-А |
К сведению
- Физико-механические свойства стекла
На предел прочности на растяжение стекол влияют микроскопические дефекты и царапины на поверхности, для конструктивных целей в основном применяют стекло с прочностью на растяжение 50 МПа. Стекла имеют Модуль Юнга около 70 ГПа.[3]
См. также
Примечания
- ↑ Волосы Пеле // Большая советская энциклопедия : [в 30 т.] / гл. ред. А. М. Прохоров. — 3-е изд. — М. : Советская энциклопедия, 1969—1978.
- ↑ Аблесимов Н. Е., Земцов А. Н. Релаксационные эффекты в неравновесных конденсированных системах. Базальты: от извержения до волокна. — Раздел 6.1.1. Терминология. — М.: ИТиГ ДВО РАН, 2010.
- ↑ 1 2 Болтон У. Конструкционные материалы, металлы, сплавы, полимеры, керамика, композиты. Карманный справочник /Пер с анг. — М.: Додека-XXI, 2004. — 320 с. — (Карманный справочник). — ISBN 5-94120-046-3.
- ↑ Б. Н. Арзомасов. Конструкционные материалы. — Машиностроение, 1990. — 688 с. — ISBN 5-217-01112-2.
- ↑ Медведев В. В., Червяков А. Н. Обоснование выбора композиционного материала для корабельных виброизоляторов.
wikipedia.green
Стекловолокно Википедия
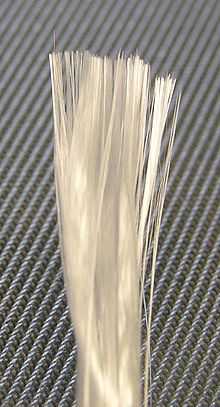
Стекловолокно́ (стеклонить) — волокно или комплексная нить, формируемые из стекла. В такой форме стекло демонстрирует необычные для себя свойства: не бьётся и не ломается, а вместо этого легко гнётся без разрушения. Это позволяет ткать из него стеклоткань.
Стекловолокна естественного происхождения встречаются в местах, где в прошлом происходили извержения вулканов, название данного вида волокон — волосы Пеле[1]. Волосы Пеле имеют химический состав базальтовых пород, имеют включения кристаллов и по физико-механическим свойствам не являются аналогами стекловолокна[2].
Виды стекловолокна (стеклонити)[ | ]
Стекловолокно экструдируют из расплава стекла специального химического состава. Экструзия, как и в других случаях, производится путём продавливания расплава через прядильные фильеры. Исходный продукт, как и в других областях производства химических волокон, получается в виде бесконечных элементарных волокон (филаментов), из которых далее в процессе переработки формируются или комплексные нити (диаметр филаментов 3—100 мкм (линейная плотность до 0,1 Текс)) и длиной в упаковке 20 км и более (непрерывное стекловолокно), линейная плотность до 100 Текс, или в стеклянные ровинги (продукты линейной плотностью более 100 Текс). В этом случае, как правило, продукт перерабатывается в кручёные нити (ровинги) на крутильно-размоточных машинах. Данные полуфабрикаты далее могут быть подвергнуты любым формам текстильной переработки в кручёные изделия (нити сложного кручения, шнуры, шпагаты, канаты), текстильные полотна (ткани, нетканые материалы), сетки (тканые, специальной структуры).
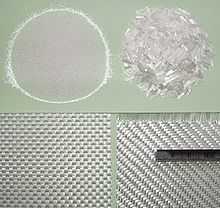
Стекловолокна также могут выпускаться в дискретном (штапельном) виде. Также исходный стеклянный ровинг может быть переработан путём резки, рубки или разрывного штапелирования в дискретные (штапельные) волокна со штапельной длиной 0,1 (микроволокно) — 50 см, титр волокна в данном случае, как правило, ниже, чем филаментных нитей и соответствует диаметру 0,1—20 мкм. Основная масса штапельных стекловолокон перерабатывается в нетканые материалы (кардные, иглопробивные, нитепрошивные, стеклохолст) по различным технологиям (кардочесание, преобразование прочёса, иглопробивание, нитепрошивание, «вэт-лэйд»), стекловату, штапельную пряжу. По внешнему виду непрерывное стекловолокно напоминает нити натурального или искусственного шёлка, а штапельное — короткие волокна хлопка или шерсти.
Основная область применения стекловолокна и стеклотекстильных материалов, — использование в качестве армирующих элементов стеклопластиков и других композитов. Также стеклоткани могут самостоятельно использоваться в качестве конструкционных и отделочных материалов. В этом случае они зачастую подвергаются той или иной форме отделки, главным образом — пропитке связующим (латекс, полиуретан, крахмалы, смолы. прочие полимеры).
Производство[ | ]
Непрерывное стекловолокно формуют вытягиванием из расплавленной стекломассы через фильеры (число отверстий 200—4000) при помощи механических устройств, наматывая волокно на бобину. Диаметр волокна зависит от скорости вытягивания и диаметра фильеры. Технологический процесс может быть осуществлён в одну или в две стадии. В первом случае стекловолокно вытягивают из расплавленной стекломассы (непосредственно из стекловарочных печей), во втором используют предварительно полученные стеклянные шарики, штабики или эрклез (кусочки оплавленного стекла), которые плавят в стеклоплавильных печах или в стеклоплавильных аппаратах (сосудах).
ru-wiki.ru
Свойства стеклопластиков – Слоистые стеклопластики – Основные сведения
Для получения стеклопластиков стеклянные волокна пропитывают смолой. Стеклянные волокна применяют в виде жгута (штапельные волокна, идущие в одном направлении, иногда предварительно напряженные), ткани (волокна в двух перпендикулярных направлениях, причем в каждом направлении их число различно) и, наконец, в виде холста (с произвольной ориентацией волокон).
Для пропитки используют полиэфирные, мочевиномеламиноформальдегидные и эпоксидные смолы, последние, правда, значительно дороже, но воспринимают намного большее количество наполнителя, обладают иными электрическими свойствами и т. д.
Прочность обычного стеклопластика при растяжении приближается к прочности стали — нагрузку воспринимают стеклянные волокна.
Напряжения сжатия воспринимает смола, обладающая относительно высокой прочностью — около 30 % прочности стали. Показатели продольного сжатия, динамической нагрузки и стойкости такой конструкции ниже, поэтому, применяя стеклопластик как конструкционный материал, следует учитывать его свойства.
Для повышения прочности при растяжении стремятся применить максимум стеклянных волокон и минимум смолы; однако каждое волокно должно быть покрыто смолой, непропитанных мест быть не должно. Воздушные пузырьки снижают прочность материала. В связи с этим прочность стеклопластика, полученного под высоким давлением, гораздо выше, чем прочность материала, изготовленного без давления. В обычных условиях можно добиться объемного содержания стеклянных волокон до 50 %.
Плотность стекловолокна равна 2,54 т/м3, смолы — 1,27 т/м3, т. е. при отношении 50 : 50 плотность стеклопластика равна 1,91 т/м3. Поскольку плотность стали равна 7,85 т/м3, стеклопластик той же массы выдержит нагрузку в 4 раза выше, чем сталь.
Стеклопластик обеспечивает герметичность, не корродирует, обладает маслостойкостью, стойкостью против воздействия большинства кислот, щелочей и растворителей.
Этот материал удобен для формирования криволинейных поверхностей, а поэтому из него делают изделия, предназначенные для эксплуатации в воде, даже в морской (от байдарок до небольших яхт, буи, садки).
Из него делают кровельные детали (прозрачные). Поскольку его можно обрабатывать на простых станках (в сравнении с прессами для штамповки листовой стали), из стеклопластика изготовляют кузова транспортных средств, выпускаемых небольшими сериями (спортивных автомобилей, трамваев, локомотивов, опытных образцов).
Пригоден стеклопластик и для корпусов электрошкафов, антенн, для печатных плат (благодаря изоляционным свойствам). Высокая прочность при малой плотности делает его пригодным для изготовления лыж, удочек, шлемов (для мотоциклистов).
Для любителей представляет интерес использование стеклопластика для ремонта и доработок изделий.
Стеклопластик обладает высокой стойкостью к атмосферным воздействиям, однако речь все же идет об органическом материале, изменяющемся под действием этих факторов. Кроме того, смола нередко начинает выделяться как, например, на асфальте. Зола, смог, механические воздействия также вызывают повреждения стеклопластика, в связи с чем необходимо периодически (каждые 4 — 10 лет) восстанавливать наружную поверхность изделий из него.
Еще несколько слов о смоле. Она относится к материалам, в ходе полимеризации (образования цепи молекул) которых образуется новая структура.
Полиэфир состоит из трех компонентов: смолы (густоватой бесцветной маслянистой жидкости), катализатора (менее густой жидкости, с запахом) и ускорителя (промотора) — обычно нафтената кобальта (темно-фиолетовая жидкость). Катализатор и ускоритель смешивать нельзя — даже небольшое количество смеси приведет к взрыву.
Чтобы процесс полимеризации начался, смесь необходимо нагреть до температуры, при которой оба компонента начнут действовать. Для полного отверждения смолы в изделии ее температура должна быть выше точки инициирования и поддерживаться в течение определенного времени — при охлаждении процесс полимеризации прекращается.
Об этом следует хорошо помнить в холодную погоду, особенно при изготовлении тонкостенных изделий. На те места, которые быстрее охлаждаются, следует внести больше ускорителя или же подвести теплоту, не забывая об опасности возгорания.
Для наслаивания можно также использовать эпоксидные смолы, которые наносят так же, как полиэфиры. Охлаждение смолы не связано с опасностью быстрого самопроизвольного отверждения.
«Домашняя мастерская»,
Ф.Кусл, Ф.Крамериус
Трехслойные пластики обеспечивают получение изделий без применения форм, что очень экономично. Из них можно изготовить несущий каркас в окончательном исполнении согласно проекту, вырезать точные фасонные детали, их можно клеить, монтировать, соединять болтами, комбинировать с металлическими и другими несущими элементами корпуса и палубы. После проверки и тщательной сушки на элементы конструкции можно монтировать трехслойные плиты, изгибая,…
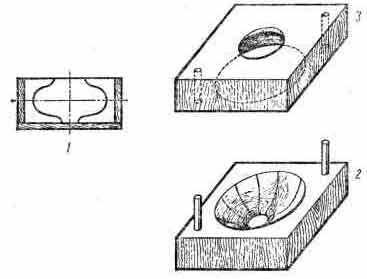
Существуют различные виды форм. Наиболее типичными являются негативные формы, в которых лицевая поверхность изделия образуется в первом слое формирования, снизу. В совершенно гладкой форме из тиксотропной смолы получают изделия с высококачественной поверхностью. Сами формы изготавливают из любого материала: гипса, древесины, металла, слоистого пластика, резины, стекла, глины. При наличии предмета, копию которого необходимо получить из слоистого…
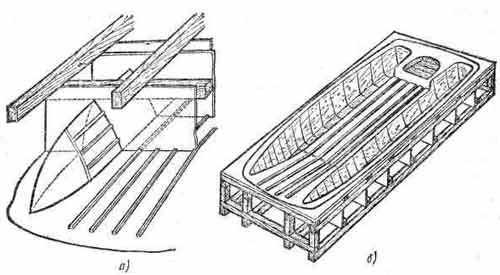
Форму для изделий из слоистых пластиков обрабатывают так же, как и сами изделия. Следовательно, ее можно выполнить по модели, например по лодке, для чего на копируемую часть лодки напыляют сепаратор, остальное защищают от загрязнения фольгой, а затем напыляют слой смолы. После этого наносят гелеобразную эмаль, а на нее — несколько слоев стеклоткани или холста. Из…
После того как завершены отделка поверхности стеклопластика окрашенной смолой и шлифование, все изделие полируют тонкой полировальной пастой и фетром. В промышленных условиях дополнительно напыляют слой бесцветного эпоксидного лака. Иногда после зачистки дефектов и затирки мастикой на поверхность изделия наносят лакокрасочное покрытие. Технология аналогична окраске металлов. Полиэфирные лаки и лаки на базе примененной смолы нельзя рекомендовать…

Отвержденный стеклопластик выдерживает кратковременный нагрев до 100 °С, размягчаясь, что позволяет при необходимости выправить форму изделия. Специальные смолы выдерживают более высокую температуру. В состав пластика можно ввести самогасящее средство, и тогда после удаления непосредственно от пламени изделие перестает гореть. Волнистый пластик с такой добавкой имеет специальное обозначение. Однако испытания показали, что при высоких температурах влияние…
www.ktovdome.ru