из чего делают строительную паклю? Что это такое? Льняная ленточная пакля и джутовая в рулонах. Лучше ли она пены и мха?
Со стороны пакля очень похожа на сильно запутанные волосы. На самом же деле этот материал не имеет с ними ничего общего. Пакля используется при сантехнических и строительных работах. В статье пойдет речь о том, из чего ее делают, и для чего именно она нужна.
Что это такое и из чего делают?
Прежде чем разбираться во всех особенностях пакли, целесообразно ответить на вопрос, что она собой представляет. Итак, пакля – это грубое волокно, имеющее однородную структуру. Характеризуются природным, растительным происхождением. Качественная пакля производится в соответствии с определенными требованиями ГОСТа. Пакля – недорогой, но очень полезный материал. Ее применяют в самых разных сферах.
В основе рассматриваемого продукта заложен обыкновенный лен. В настоящее время, наряду с этим сырьем, нередко задействуется и джут. Лен очень хорошо себя чувствует в условиях наших почв, поэтому его выращивают в больших количествах и в России, и на территории Беларуси.
Джут же является растением азиатским, поэтому его к нам обычно завозят из Бангладеш. И лен, и джут представляют собой сырье, хорошо насыщенное таким компонентом, как целлюлоза, поэтому они могут похвастаться неплохими прочностными характеристиками. Материалы устойчивы к большим нагрузкам, которых невозможно избежать по ходу строительства дома или другой постройки.
В клеточных мембранах джута присутствует больший процент лигнина (вплоть до 12%), что делает материал более влагостойким, нежели лен.
Лен богат пектинами, поэтому является более гибким.
Это качество особенно важно, если пакля изо льна используется с целью изоляции пазов сруба.
Особенности
Пакля неслучайно является очень популярным и незаменимым материалом в проведении разных работ. Дело в том, что она имеет ряд характеристик и особенностей, делающих ее весьма практичной и функциональной. Узнаем, в чем же скрыты самые важные особенности данного материала.
- Пакля – очень крепкий материал. Она не портится и не теряет своих эксплуатационных характеристик даже под действием серьезных нагрузок.
- Очень легко и просто подобрать паклю для конкретного вида работ. Каждый из видов материала маркируется и имеет внешние отличительные признаки, поэтому найти продукт для определенных процедур не составляет труда.
- В материале присутствуют поры.
- Пакля представляет собой продукт, отличающийся высокими показателями гигроскопичности.
- Рассматриваемый материал долговечен и устойчив к износу.
- Пакля – бактерицидный материал.
- Это экологически чистый продукт, который не способен провоцировать аллергические реакции у людей.
Сегодня паклю продают в виде рулонов, лент и тюков. Для работы с этим простым, но эффективным материалом не нужно покупать специальный дорогостоящий инструмент.
Обычно льняные косички демонстрируют экономный расход и стоят дешево, поэтому и являются очень привлекательным товаром для современных потребителей.
Сравнение с другими материалами
Пакля является востребованным материалом, но у него есть и не менее актуальные аналоги. К таковым относят мох, современные виды утеплителей для межвенцовых швов и многие другие продукты данной категории. В определенных ситуациях вместо пакли можно использовать обычную монтажную пену.
Имеет смысл разобраться более детально, в чем кроются основные отличия пакли от других аналогичных материалов. Для начала сравним паклю и мох.
- При использовании и пакли, и мха строителям и мастерам приходится прибегать к дополнительной конопатке межвенцовых швов. Мох не даст красивый и ровной шов, а вот льняная пакля будет выглядеть гораздо привлекательнее.
- Если материал подбирается для укладки в межвенцовых швах, то мастера чаще выбирают именно паклю, поскольку работать с ней легче, нежели со мхом – его не так просто тщательно уложить в щели.
- Птицы больше интересуются паклей, нежели мхом. Часто они растаскивают джутовый и льняной материал, выдергивая его волокна из межвенцовых швов.
Мох привлекает их намного меньше.
- В пакле нередко заводятся древесные паразиты, которые никогда не появляются во мху.
- В строительстве мох используют реже, поскольку он выглядит менее привлекательно, нежели пакля. Он сразу бросается в глаза.
И мох, и пакля имеют свои слабые и сильные стороны. Каждый пользователь решает сам, какой продукт лучше выбрать.
Рассматриваемый материал можно сравнить и с другим сырьем, используемым в строительстве. Речь идет об утеплителе под названием политерм. Разберемся в различиях между этими материалами.
- Если сырье применяется для укладки в межвенцовых швах, то политерм не будет нуждаться в дополнительной конопатке в отличие от пакли.
- Конопатка изо льна или джута может впитывать в себя влагу, а политерм таким проблемам не подвержен.
- Джутовая или льняная конопатка не может похвастаться паропроницаемостью. Политерм же – паропроницаемый материал.
- Эксплуатировать паклю повторно не удастся, а вот утеплитель политерм допускает многократное применение.
Стоит сказать и о сроке службы льняных или джутовых материалов – он гораздо более скромный, нежели срок службы политерма. Последний может прослужить почти 100 лет, а вот пакля между венцами нередко отрабатывает всего пару лет. Паклю часто сравнивают с другими материалами подобного типа. В чем-то она уступает им, а в чем-то оказывается более качественной. Многое зависит от того, для каких именно целей подбирается подобное сырье, и какого эффекта от него ожидают пользователи.
Описание видов
Пакля подразделяется на несколько разновидностей. Каждый из продуктов имеет свои отличительные характеристики и даже внешние отличия. Познакомимся поближе с разными видами рассматриваемого сырья.
Бежевая
Лен, имеющий характерный бежевый оттенок, является натуральным. Сам его оттенок свидетельствует об этом. Пакля бежевой расцветки не имеет в своем составе дополнительных химических или вредных компонентов. Подобный материал является экологически чистым и безопасным, продается во многих магазинах. Бежевую расцветку имеет пакля, которую задействуют для дальнейшего процесса конопатки.
При работе с данным материалом сначала формируют небольшие жгутики, которые потом заталкивают в межвенцовые швы посредством специального инструмента. Самой удобной в монтаже оказывается ленточная бежевая пакля, продающаяся в разных форматах. Полотно различается и по показателям ширины, и по длине (от 10 до 50 метров) с толщиной.
Опытные специалисты рекомендуют конопатить свежие постройки не менее двух раз.
В первый раз – по ходу укладки стеновых конструкций, а в следующий раз – спустя год.
Коричневая
Существует не только бежевая, но и более темная пакля коричневого оттенка. Такие изделия в большинстве случаев используют в качестве герметика при обустройстве трубопроводных систем. Коричневая пакля позволяет максимально быстро устранить протечку труб без необходимости демонтажа большого количества важных деталей и соединений.
В отличие от тюковой или рулонной пакли бежевого оттенка, сантехнические изделия имеют специальную пропитку. Коричневая пакля обрабатывается особым образом, поэтому идеально подходит для монтажа водопроводных или отопительных систем. Рассматриваемый материал давно зарекомендовал себя и продемонстрировал свою эффективность.
Благодаря коричневой пакле мастера могут беспроблемно состыковать места соединений труб, чтобы предупредить образование протечек. Темный материал имеет особую структуру волокон, благодаря которой очень легко наматывается на нужные основания, отлично впитывает лишнюю влагу и расширяется в случае намокания.
Пакля различается не только по своему окрасу и назначению, но и по виду, в котором реализуется. Так, более темные продукты, которые предназначены для проведения качественных сантехнических работ, чаще всего продаются в виде мотков разных размеров. А вот пакля, которая предназначена для дальнейшей конопатки, продается в тюках разного веса или в рулонах.
Нюансы выбора
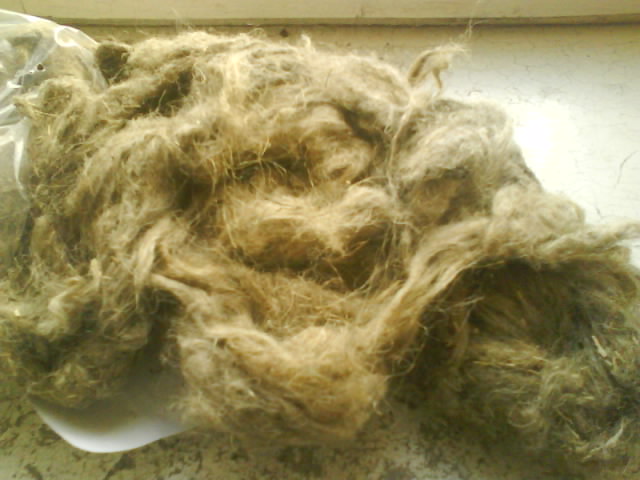
- Покупатель должен знать, что после изготовления пакле дается определенный номер. Именно он отражает качество натурального продукта. Обычно значения варьируются в пределах от 8 до 24. Чем выше отметка, тем качественней продукт. В таких изделиях присутствует меньший процент лишних примесей.
- Важно обращать внимание не только на цифровое обозначение, но и на сам цвет пакли. Выше уже говорилось о том, что бежевый материал применяется с целью конопатки, а коричневый задействуют в мероприятиях, связанных с сантехническими работами. Важно не ошибиться, чтобы не разочароваться в эффективности выбранной продукции.
- Надо учитывать, что лен, из которого сделана пакля, обязательно должен быть абсолютно сухим. От продукта не должен исходить никакой запах.
- Следует присмотреться к маркировке товара, делая выбор в пользу качественного варианта.
Целесообразно уточнить и показатель, указывающий на процент влажности (должен быть не выше 12%).
- Если выбор пал на паклю, от которой исходит очень неприятный гнилостный запах, то от покупки лучше вовремя отказаться. Для дальнейших работ подобный материал точно не подойдет, поскольку является низкокачественным.
- Найти качественную паклю для бруса, бани или деревянного дома, а также для проведения сантехнических работ можно только в специализированных магазинах. Именно в таких торговых точках удастся отыскать материал, имеющий необходимый сертификат соответствия ГОСТам. На рынке или в уличных лавках паклю лучше не покупать – высок риск приобретения некачественного продукта.
Обычно качественная пакля продается в простых, но аккуратных упаковках. На них не должно быть каких-либо повреждений или дефектов. Да и сама льняная или джутовая косичка не должна пышно махриться и выглядеть излишне потрепанной. Новый и качественно изготовленный продукт и выглядеть будет соответствующе.
Правила использования
Паклей нужно пользоваться правильно, чтобы она продемонстрировала все свои положительные качества и высокие показатели эффективности. Разберем правила использования пакли на примере герметизации соединений.
- В большинстве сантехнических работ не обойтись без пакли. Работать с ней очень просто и легко. Если на резьбе нет насечек, а их наличие необходимо для более крепкого и надежного крепежа, то для нанесения целесообразно воспользоваться надфилем или напильником.
- Многие мастера наносят насечки простыми плоскогубцами, если постепенно сдавливать резьбу, делая круговые движения. Присутствие маленьких зазубринок не даст материалу для крепления труб сползать в дальнейшем.
- Далее нужно отделить первую прядку волокна от общей «косы» пакли.
Толщина выбранного куска должна соответствовать соединению, к которому его запланировано применить. Если заметны хотя бы маленькие комочки, их необходимо сразу же убрать.
- На соединение можно наматывать как распушенный, так и предварительно скатанный в аккуратные косички лен.
- Разрешается воспользоваться материалом, предварительно обработанным и пропитанным специальной пастой. Можно наносить паклю на уже намотанный предварительно первый слой пакли. И первый, и второй способы являются равноценными, заметно снижают риск порчи материала по ходу его эксплуатации.
- Наматывать материал следует крест-накрест. Первый виток нужно зафиксировать замком. К примеру, мастер может начать с самого конца резьбового соединения. Стартовый виток потребуется оформить внахлест. Витки необходимо делать максимально тугими и крепкими.
- После стартового можно делать и все остальные витки, но с перемещением на начальную точку резьбового основания.
- Когда будет достигнуто начало резьбы, надо будет вновь вернуться к ее концу. При этом не следует пренебрегать максимальной плотностью в середине. Конец льняной косички следует вернуть к ее начальной отметке. Кончик понадобится вывести за границы.
- Обязательно нужно будет убедиться в достаточной плотности сделанной намотки. Учтите – пакля ни в коем случае не должна прокручиваться на поверхности фитинга. Если материал будет гулять по поверхности основания, то намотку придется произвести еще раз, чтобы исправить ситуацию. Поверх слоя надо будет уложить специальную защитную пасту-уплотнитель.
- Все излишки, которые остались от пакли, можно оставить на своих местах, а можно аккуратно отрезать ножницами. Все зависит от пожеланий хозяев. На герметичность эти остатки никак повлиять не смогут.
Работая с рассмотренными соединениями, мастер должен быть аккуратным и последовательным.
Лишняя спешка в таких делах будет неуместна.
Рассмотрим и другие особенности использования пакли для конопатки.
- Ленточная пакля, которая состоит из натуральных компонентов, применяется чаще всего. Ее допустимо задействовать при первичной конопатке.
- Мастеру нужно лишь аккуратно развернуть таблетку на брусе или бревне основания. Следует закрепить материал или в один, или в пару слоев.
- Если это тюковая пакля, то ее целесообразно задействовать в таких ситуациях, когда между бревнами имеются неоднородные щели с разной шириной.
- Волокно, которое сделано более коротким, станет идеальным решением, если необходимо заполнить неоднородные пустые пространства, поскольку количество используемого материала мастер определяет самостоятельно.
Работать с паклей предельно просто. Пользуясь совершенно нехитрыми технологиями, строители могут возвести настоящий дом-долгожитель, в котором будет тепло и уютно.
То же касается и пакли, задействованной в сантехнических соединениях. Натуральный материал продлит срок службы трубопроводных конструкций, позволит предупредить их протечки и прочие повреждения подобного рода.
из чего делают строительную паклю? Что это такое? Льняная ленточная пакля и джутовая в рулонах. Лучше ли она пены и мха?
Со стороны пакля очень похожа на сильно запутанные волосы. На самом же деле этот материал не имеет с ними ничего общего. Пакля используется при сантехнических и строительных работах. В статье пойдет речь о том, из чего ее делают, и для чего именно она нужна.
Что это такое и из чего делают?
Прежде чем разбираться во всех особенностях пакли, целесообразно ответить на вопрос, что она собой представляет. Итак, пакля – это грубое волокно, имеющее однородную структуру. Характеризуются природным, растительным происхождением. Качественная пакля производится в соответствии с определенными требованиями ГОСТа. Пакля – недорогой, но очень полезный материал. Ее применяют в самых разных сферах.
В основе рассматриваемого продукта заложен обыкновенный лен. В настоящее время, наряду с этим сырьем, нередко задействуется и джут. Лен очень хорошо себя чувствует в условиях наших почв, поэтому его выращивают в больших количествах и в России, и на территории Беларуси.
Джут же является растением азиатским, поэтому его к нам обычно завозят из Бангладеш. И лен, и джут представляют собой сырье, хорошо насыщенное таким компонентом, как целлюлоза, поэтому они могут похвастаться неплохими прочностными характеристиками. Материалы устойчивы к большим нагрузкам, которых невозможно избежать по ходу строительства дома или другой постройки.
В клеточных мембранах джута присутствует больший процент лигнина (вплоть до 12%), что делает материал более влагостойким, нежели лен.
Лен богат пектинами, поэтому является более гибким. Это качество особенно важно, если пакля изо льна используется с целью изоляции пазов сруба.
Особенности
Пакля неслучайно является очень популярным и незаменимым материалом в проведении разных работ. Дело в том, что она имеет ряд характеристик и особенностей, делающих ее весьма практичной и функциональной. Узнаем, в чем же скрыты самые важные особенности данного материала.
- Пакля – очень крепкий материал. Она не портится и не теряет своих эксплуатационных характеристик даже под действием серьезных нагрузок.
- Очень легко и просто подобрать паклю для конкретного вида работ. Каждый из видов материала маркируется и имеет внешние отличительные признаки, поэтому найти продукт для определенных процедур не составляет труда.
- В материале присутствуют поры.
- Пакля представляет собой продукт, отличающийся высокими показателями гигроскопичности.
- Рассматриваемый материал долговечен и устойчив к износу.
- Пакля – бактерицидный материал.
- Это экологически чистый продукт, который не способен провоцировать аллергические реакции у людей.
Сегодня паклю продают в виде рулонов, лент и тюков. Для работы с этим простым, но эффективным материалом не нужно покупать специальный дорогостоящий инструмент.
Обычно льняные косички демонстрируют экономный расход и стоят дешево, поэтому и являются очень привлекательным товаром для современных потребителей.
Сравнение с другими материалами
Пакля является востребованным материалом, но у него есть и не менее актуальные аналоги. К таковым относят мох, современные виды утеплителей для межвенцовых швов и многие другие продукты данной категории. В определенных ситуациях вместо пакли можно использовать обычную монтажную пену.
Имеет смысл разобраться более детально, в чем кроются основные отличия пакли от других аналогичных материалов. Для начала сравним паклю и мох.
- При использовании и пакли, и мха строителям и мастерам приходится прибегать к дополнительной конопатке межвенцовых швов. Мох не даст красивый и ровной шов, а вот льняная пакля будет выглядеть гораздо привлекательнее.
- Если материал подбирается для укладки в межвенцовых швах, то мастера чаще выбирают именно паклю, поскольку работать с ней легче, нежели со мхом – его не так просто тщательно уложить в щели.
- Птицы больше интересуются паклей, нежели мхом. Часто они растаскивают джутовый и льняной материал, выдергивая его волокна из межвенцовых швов. Мох привлекает их намного меньше.
- В пакле нередко заводятся древесные паразиты, которые никогда не появляются во мху.
- В строительстве мох используют реже, поскольку он выглядит менее привлекательно, нежели пакля. Он сразу бросается в глаза.
И мох, и пакля имеют свои слабые и сильные стороны.
Каждый пользователь решает сам, какой продукт лучше выбрать.
Рассматриваемый материал можно сравнить и с другим сырьем, используемым в строительстве. Речь идет об утеплителе под названием политерм. Разберемся в различиях между этими материалами.
- Если сырье применяется для укладки в межвенцовых швах, то политерм не будет нуждаться в дополнительной конопатке в отличие от пакли.
- Конопатка изо льна или джута может впитывать в себя влагу, а политерм таким проблемам не подвержен.
- Джутовая или льняная конопатка не может похвастаться паропроницаемостью. Политерм же – паропроницаемый материал.
- Эксплуатировать паклю повторно не удастся, а вот утеплитель политерм допускает многократное применение.
Стоит сказать и о сроке службы льняных или джутовых материалов – он гораздо более скромный, нежели срок службы политерма. Последний может прослужить почти 100 лет, а вот пакля между венцами нередко отрабатывает всего пару лет. Паклю часто сравнивают с другими материалами подобного типа. В чем-то она уступает им, а в чем-то оказывается более качественной. Многое зависит от того, для каких именно целей подбирается подобное сырье, и какого эффекта от него ожидают пользователи.
Описание видов
Пакля подразделяется на несколько разновидностей. Каждый из продуктов имеет свои отличительные характеристики и даже внешние отличия. Познакомимся поближе с разными видами рассматриваемого сырья.
Бежевая
Лен, имеющий характерный бежевый оттенок, является натуральным. Сам его оттенок свидетельствует об этом. Пакля бежевой расцветки не имеет в своем составе дополнительных химических или вредных компонентов. Подобный материал является экологически чистым и безопасным, продается во многих магазинах. Бежевую расцветку имеет пакля, которую задействуют для дальнейшего процесса конопатки.
При работе с данным материалом сначала формируют небольшие жгутики, которые потом заталкивают в межвенцовые швы посредством специального инструмента. Самой удобной в монтаже оказывается ленточная бежевая пакля, продающаяся в разных форматах. Полотно различается и по показателям ширины, и по длине (от 10 до 50 метров) с толщиной.
Опытные специалисты рекомендуют конопатить свежие постройки не менее двух раз. В первый раз – по ходу укладки стеновых конструкций, а в следующий раз – спустя год.
Коричневая
Существует не только бежевая, но и более темная пакля коричневого оттенка. Такие изделия в большинстве случаев используют в качестве герметика при обустройстве трубопроводных систем. Коричневая пакля позволяет максимально быстро устранить протечку труб без необходимости демонтажа большого количества важных деталей и соединений.
В отличие от тюковой или рулонной пакли бежевого оттенка, сантехнические изделия имеют специальную пропитку. Коричневая пакля обрабатывается особым образом, поэтому идеально подходит для монтажа водопроводных или отопительных систем. Рассматриваемый материал давно зарекомендовал себя и продемонстрировал свою эффективность.
Благодаря коричневой пакле мастера могут беспроблемно состыковать места соединений труб, чтобы предупредить образование протечек. Темный материал имеет особую структуру волокон, благодаря которой очень легко наматывается на нужные основания, отлично впитывает лишнюю влагу и расширяется в случае намокания.
Пакля различается не только по своему окрасу и назначению, но и по виду, в котором реализуется. Так, более темные продукты, которые предназначены для проведения качественных сантехнических работ, чаще всего продаются в виде мотков разных размеров. А вот пакля, которая предназначена для дальнейшей конопатки, продается в тюках разного веса или в рулонах.
Нюансы выбора
Несмотря на то что рассматриваемый материал является предельно простым и состоит из элементарных компонентов, его необходимо выбирать правильно. Нужно учитывать ряд нюансов, связанных с подбором данного продукта.
- Покупатель должен знать, что после изготовления пакле дается определенный номер. Именно он отражает качество натурального продукта. Обычно значения варьируются в пределах от 8 до 24. Чем выше отметка, тем качественней продукт.
В таких изделиях присутствует меньший процент лишних примесей.
- Важно обращать внимание не только на цифровое обозначение, но и на сам цвет пакли. Выше уже говорилось о том, что бежевый материал применяется с целью конопатки, а коричневый задействуют в мероприятиях, связанных с сантехническими работами. Важно не ошибиться, чтобы не разочароваться в эффективности выбранной продукции.
- Надо учитывать, что лен, из которого сделана пакля, обязательно должен быть абсолютно сухим. От продукта не должен исходить никакой запах.
- Следует присмотреться к маркировке товара, делая выбор в пользу качественного варианта. Целесообразно уточнить и показатель, указывающий на процент влажности (должен быть не выше 12%).
- Если выбор пал на паклю, от которой исходит очень неприятный гнилостный запах, то от покупки лучше вовремя отказаться. Для дальнейших работ подобный материал точно не подойдет, поскольку является низкокачественным.
- Найти качественную паклю для бруса, бани или деревянного дома, а также для проведения сантехнических работ можно только в специализированных магазинах. Именно в таких торговых точках удастся отыскать материал, имеющий необходимый сертификат соответствия ГОСТам. На рынке или в уличных лавках паклю лучше не покупать – высок риск приобретения некачественного продукта.
Обычно качественная пакля продается в простых, но аккуратных упаковках. На них не должно быть каких-либо повреждений или дефектов. Да и сама льняная или джутовая косичка не должна пышно махриться и выглядеть излишне потрепанной. Новый и качественно изготовленный продукт и выглядеть будет соответствующе.
Правила использования
Паклей нужно пользоваться правильно, чтобы она продемонстрировала все свои положительные качества и высокие показатели эффективности. Разберем правила использования пакли на примере герметизации соединений.
- В большинстве сантехнических работ не обойтись без пакли. Работать с ней очень просто и легко. Если на резьбе нет насечек, а их наличие необходимо для более крепкого и надежного крепежа, то для нанесения целесообразно воспользоваться надфилем или напильником.
- Многие мастера наносят насечки простыми плоскогубцами, если постепенно сдавливать резьбу, делая круговые движения. Присутствие маленьких зазубринок не даст материалу для крепления труб сползать в дальнейшем.
- Далее нужно отделить первую прядку волокна от общей «косы» пакли. Толщина выбранного куска должна соответствовать соединению, к которому его запланировано применить. Если заметны хотя бы маленькие комочки, их необходимо сразу же убрать.
- На соединение можно наматывать как распушенный, так и предварительно скатанный в аккуратные косички лен.
- Разрешается воспользоваться материалом, предварительно обработанным и пропитанным специальной пастой. Можно наносить паклю на уже намотанный предварительно первый слой пакли. И первый, и второй способы являются равноценными, заметно снижают риск порчи материала по ходу его эксплуатации.
- Наматывать материал следует крест-накрест. Первый виток нужно зафиксировать замком. К примеру, мастер может начать с самого конца резьбового соединения. Стартовый виток потребуется оформить внахлест. Витки необходимо делать максимально тугими и крепкими.
- После стартового можно делать и все остальные витки, но с перемещением на начальную точку резьбового основания.
- Когда будет достигнуто начало резьбы, надо будет вновь вернуться к ее концу. При этом не следует пренебрегать максимальной плотностью в середине. Конец льняной косички следует вернуть к ее начальной отметке. Кончик понадобится вывести за границы.
- Обязательно нужно будет убедиться в достаточной плотности сделанной намотки. Учтите – пакля ни в коем случае не должна прокручиваться на поверхности фитинга. Если материал будет гулять по поверхности основания, то намотку придется произвести еще раз, чтобы исправить ситуацию. Поверх слоя надо будет уложить специальную защитную пасту-уплотнитель.
- Все излишки, которые остались от пакли, можно оставить на своих местах, а можно аккуратно отрезать ножницами. Все зависит от пожеланий хозяев. На герметичность эти остатки никак повлиять не смогут.
Работая с рассмотренными соединениями, мастер должен быть аккуратным и последовательным. Лишняя спешка в таких делах будет неуместна.
Рассмотрим и другие особенности использования пакли для конопатки.
- Ленточная пакля, которая состоит из натуральных компонентов, применяется чаще всего. Ее допустимо задействовать при первичной конопатке.
- Мастеру нужно лишь аккуратно развернуть таблетку на брусе или бревне основания. Следует закрепить материал или в один, или в пару слоев.
- Если это тюковая пакля, то ее целесообразно задействовать в таких ситуациях, когда между бревнами имеются неоднородные щели с разной шириной.
- Волокно, которое сделано более коротким, станет идеальным решением, если необходимо заполнить неоднородные пустые пространства, поскольку количество используемого материала мастер определяет самостоятельно.
Работать с паклей предельно просто. Пользуясь совершенно нехитрыми технологиями, строители могут возвести настоящий дом-долгожитель, в котором будет тепло и уютно.
То же касается и пакли, задействованной в сантехнических соединениях.
Натуральный материал продлит срок службы трубопроводных конструкций, позволит предупредить их протечки и прочие повреждения подобного рода.
Джутовая лента сравнение с паклей
Строительство деревянных домов, за исключением строительства из клееного бруса, подразумевает под собой использование межвенцового утеплителя, в роли которого может применяться пакля из джута или специальная джутовая лента.
Это делается для того, чтобы снизить последствия усадки деревянного дома, а также придать плотности отдельным бревнам. На первый взгляд, прочитав название этих утеплителей, кажется, что мы говорим об одном и том же. На самом деле все не так, и, чтобы убедиться в этом, давайте узнаем, в чем заключаются отличия, и сходства джутовой пакли и ленты.
Сходства джутовой ленты и пакли
Среди сходств данных утеплителей, выделяют:
- Оба этих материала изготовлены из джута, который представляет собой универсальный, подходящий к любым породам дерева – утеплитель.
Кроме того, джут не боится влаги, в случае намокания он быстро сохнет, является прекрасным утеплителем. В целом, джут экологически чистый и природный материал, а, значит, он полностью безопасен для здоровья людей, которые будут проживать в доме. Кроме того, джутовый утеплитель – это результат вторичной переработки, что делает его очень дешевым и доступным для покупки самым рядовым пользователям.
- Такое странное сходство, можно сказать, что общий недостаток этих материалов заключается в том, что они очень интересны пролетающим мимо дома птицам, которые стремятся выдернуть из нее больше волокон для строительства гнезд, тем самым нарушая теплоизоляцию деревянного дома в целом. Собственно поэтому строители рекомендуют плотно упаковывать торчащие участки пакли в дерево. Рекомендовано применять внешнюю облицовку или герметик.
Основные отличия пакли джутовой от ленты:
- Самое главное отличие заключается в строении данного материала. К примеру, лента, на рынке строительных материалах поставляется в катышках, ширина и длина которых строго регламентирована.
Джутовая пакля поставляется в мешках или тюках. Требует дополнительного проветривания от сырости.
- В зависимости от строения, различают способ применения данных утеплителей. Например, джутовая лента применяется непосредственно в момент строительства деревянного дома. Ее ширина подбирается с небольшим запасом. С ней просто и легко работать. Для укладки, ее раскатывают на поверхности венца, отрезают нужную длину, а, затем, прижимают верхним венцом из бревен.
Что касается запаса длины, то это делается для того, чтобы впоследствии закрыть вновь образованные отверстия между венцами дома, которые были образованы в процессе усадки стен.
В свою очередь, паклю тоже можно укладывать на поверхности венца. Вот только делать – это гораздо сложнее, чем работать с лентой. Поэтому в современном строительстве пакля представляет собой вторичный утеплитель, который используется после окончания усадки деревянного дома. С его помощью закрывают трещины в бревнах, межвенцовые отверстия и другие участки, нарушающие теплоизоляцию. - Джутовая пакля наиболее мягкий материал, поэтому считается, что с ним проще работать. В свою очередь, лента, наиболее упруга и совсем не подойдет для того, чтобы с ее помощью закрыть отверстия в стенах дома. По этой же причине, лента в большей степени сопротивляется атакам птиц.
Данный материал подготовлен администраторами сайта «Лесной Дом»
Адрес сайта: http://www.foresthouse.ru/
Купить утеплительные материалы указанные в статье, можно позвонив по телефону в Москве +7 (495) 971-57-20.
Как конопатить паклей? | Конопатим
Прежде чем отвечать на вопрос как конопатить паклей, давайте разберемся с понятием пакля.
Что такое пакля?
Что это за материал? Из чего он сделан, как? Подходит ли он для современной конопатки?
Пакля — это отход от первичной обработки (мягчение, трепетание) льна, джута, конопли, а также других лубяных культур, таких как популярный ныне джут. Пакля непригодна для прядения и очень сильно загрязнена кострой.
Пакля в контексте конопатки — это материал для забивания в зазоры между венцами, продающийся в мешках различного веса.
Также в разговорах часто паклей называется любой утеплитель любого сорта и происхождения. Что в корне не верно.
Мы кратко ознакомились с определением пакли. Знаем из чего она делается.
Пакля в конопатке.
Теперь мы расскажем о роли пакли в процессе конопатки и методы работы с ней.
Прежде всего напишем главное — пакля самый доступный и дешевый утеплитель в розничной продаже.
Именно благодаря применению отходов основного производства достигается низкая цена. Материал можно встретить во многих строительных магазинах и именно благодаря цене он знаком всем и часто используется в строительстве.
Как правильно конопатить паклей?
Благодаря тому, что материал поставляется в мешках, конопатить паклей достаточно просто и удобно. Набирается необходимое количество пакли и забивается в зазор между бревнами. Можно бить, просто добавляя материал по мере необходимости, или же плести из пакли косичку по типу каната и вбивать ее! Материал мягкий, податливый, очень хорошо уплотняется. Конопатить сруб, баню, брус паклей очень удобно и легко. Ведь чем мягче материал, тем легче конопатить! Отличный материал!? Так ли это?
Вспомним определение, которое было выше и некоторые слова из него. Слово отход и костра.
Отход даже звучит не очень, и это так и есть. Пакля — это низший сорт среди прочих.
Костра — это крайне жесткая кожица и деревянистые волокна льна, конопли, джута, которые остались после трепания и чесания как- отброс. То есть это то, что должно идти на выброс, но зачем же производственникам это выбрасывать?? Ведь есть разные сорта качества материалов и в низшем сорте утеплителей большое количество костры не зазорно.
А теперь поразмышляем про применимость пакли для конопатки. Если экономия на первом месте-то вроде отличный выбор, пакля —самая дешевая, отлично!
Однако выбор пакли для конопатки — это не всегда оправданная экономия. Из-за наличия огромного количества костры и мусора-пакля подвержена гниению, в зонах применения может образовываться грибок. После попадания влаги пакля может неприятно пахнуть! И именно паклю из-за костры и мягкости любят таскать птицы для строительства гнезд!!
Однако так ли все плохо? Мы считаем, что если уж вы хотите использовать максимально недорогие материалы, то правильно конопатить сруб паклей с внутренней стороны и в местах сухих, не влажных. Именно поэтому, когда спрашивают, как конопатить паклей баню, мы отвечаем, что в бане можно применять паклю, только в местах, где будет сухо!
Так что, выбирая, что вы будете использовать при конопатке и как правильно конопатить дом из бревна или бруса паклей нужно помнить, что вы выбираете материал не только самый простой и дешевый, но и имеющий нюансы, ограничивающие его применение, по сравнению с иными материалами!
Поэтому, когда вы задаете вопрос как правильно конопатить паклей-мы отвечаем- с умом и отдавая себе отчет что вы используете и для чего.
В статье написана наша авторская позиция, мы никого не принуждаем думать по-другому!
К списку статей
Сантехническая пакля (лен) – как намотать паклю на резьбу? (видео)
При сборке любого резьбового соединения, будь то для газа, водоснабжения или отопления, нельзя забывать о герметичности всей системы. Опытный сантехник вооружен целым арсеналом средств и инструментов, а новичкам в этом деле нужно тщательно осваивать самые основные приемы и подходы. Одним из примеров базовых знаний служит вопрос: как наматывать паклю на резьбу? Что ж, разберемся!
Подготовительный этап
Перед тем, как наматывать лен или паклю на резьбу, нужно подготовить поверхность соединения и определить нужное количество пакли. Накрутите фитинг на резьбу как есть, ничего не наматывая. Это поможет определить, сколько надо будет взять пакли.
Если резьба гладкая и ровная (в случае заводской нарезки, скорее всего, так и будет), для лучшего сцепления рекомендуется нанести насечки на витках. Для этого подойдет водопроводный ключ, нафтиль-трехгранник или обычные плоскогубцы; всё, что требуется сделать – нанести насечки поперек резьбы, при этом не слишком усердствуя. Это делается для того, чтобы предотвратить скольжение пакли по виткам резьбы.
Насечки не должны быть слишком глубокими, не нужно буквально продирать металл (смотрите видео). От того, как правильно намотана пакля, будет зависеть надежность соединения в будущем. Если положить слишком мало и редко – будет протекать, избыточное же количество может быть куда опаснее – слишком плотно обмотанный участок может лопнуть при повышении температуры (как известно, металл расширяется при нагревании).
Загрузка …Приступаем к намотке
От общего пучка следует взять небольшое количество пакли, при этом волокна должны быть ровными, гладкими, без узелков и разрывов.
Паклю нужно скрутить в веревочку такой толщины, чтобы она (толщина) равнялась шагу резьбы, т. е. заполняла собой впадину между витками.
Намотку осуществляем с внутреннего края резьбы;
существует несколько способов, как наматывать паклю – к примеру, некоторые советуют начинать намотку с отступом и затем перехлестнуть волокна, чтобы они лучше держались (см. видео).
Но для начинающих будет проще наматывать непосредственно с края.
Итак, приложив конец льняной веревочки к первому витку, совершаем намотку в направлении, обратном ходу закручивания – то есть по часовой стрелке, если резьба правая (в подавляющем большинстве случаев так и есть).
Мотать надо плотно, но не слишком обильно – двух слоев будет более чем достаточно. Как только намотали паклю на резьбу, следует, не отпуская пальцев, наложить пасту для фиксации. Для этого часто применяют силикон, краску или клей, но по личному опыту рекомендуем обратить внимание на «Unipak» — эта паста более нейтральна по отношению к металлу и не обладает вкусом и запахом, что поможет избежать проблем при монтаже водопровода.
Видео процесса
Лен (пакля), фум или сантехническая нить?
Обычная пакля является старым, но проверенным средством в сантехнике, фактически это «дедовский способ». Годится пакля как для наматывания, так и для других работ. Современная индустрия предлагает такие альтернативы, как фторопластовая (фум) лента и готовые уплотнительные нити.
В то время как их использование может быть удобнее по ряду причин, лен имеет свои преимущества: он более экологичен в сравнении с фторопластом и значительно более доступен, чем специальная сантехническая нить. Вполне возможно, что в будущем нас ждут новые решения, которые вытеснят лен, но пока знание того, как наматывать паклю на резьбу, никогда не будет излишним для хозяйственного человека.
Загрузка …Статьи по теме:
Техника правильной и надежной намотки пакли на резьбу
Намотать паклю на резьбу. Казалось бы, что может быть проще? Но это сложнее, чем кажется на первый взгляд. Даже начинающие сантехники иногда испытывают определенные трудности в этом. Следовательно, требуется учитывать некоторые моменты, чтобы не испортить работу и не потерять время.
Процесс наматывания
Насечки
Следует изначально запомнить, что резьба может быть 2-х видов:
1. С насечками;
2. Без насечек.
Эти самые насечки обеспечивают более плотное прилегание намотанной пакли, а также не дают ей проворачиваться и скользить.
Следовательно, при отсутствии насечек на используемой резьбе, желательно сделать их своими силами. В идеале для этого потребуется специальный инструмент, но если его под рукой не оказалось, можно применить и другие средства: плоскогубцы, ножовочное полотно и т.д.
Наматывание пакли
Когда с созданием насечек покончено, необходимо оторвать от мотка пакли прядь. Ее должно быть не слишком много, но и не мало. Все витки резьбы должны быть заполнены материалом, только это гарантирует полную герметичность будущего соединения. Если пакли будет слишком мало, вполне вероятен разрыв деталей, ведь для их изготовления используются мягкие виды металлов (латунь, бронза и т.д.).
После намотки паклю следует расправить и стянуть комочки (при их наличии). Моток необходимо приложить к резьбе (5 витков от начала), зажать пальцем и сделать полтора оборота от себя дальним краем, после этого он перекрещивается с другим отрезком. Это обязательное условие при правосторонней резьбе, если же она левосторонняя, то все делается с точностью до наоборот. После этого рекомендуется сделать еще 1 оборот и объединить 2 отрезка в 1.
Далее требуется только равномерно наматывать паклю по виткам резьбы, следя за тем, чтобы ее было одинаково везде. После намотки нужно провести по ней пальцами, чтобы равномерно уложить. Следует помнить, что необходимо прижимать уплотнитель, пока не произойдет его замазка сантехнической смазкой. Иначе, если отпустить ее не намазав, пакля распустится.
Придерживаясь данных рекомендаций, надежно намотать паклю на резьбу не составит никакого труда.
Термостатический смеситель – избавитель от лишних проблем в душе
Типы водяной схемы и нюансы, возникающие при их эксплуатации
Конопатка сруба, способы. Материалы для конопатки сруба, видео
Конопатка сруба первый раз делается сразу после возведения сруба. Волокнистые материалы, используемые для этого, при сборке сруба кладутся на бревна или брусья ровным слоем, волокнами поперек паза. При этом они должны выступать на обе стороны не менее чем на 50 мм.
Материалы для конопатки сруба
Для конопатки издавна используются такие материалы как пакля, пенька, лен, мох, войлок. В последнее время также стал использоваться джут.
Пакля – грубое спутанное волокно, загрязненное кострой, отходы первичной обработки лубяных культур – конопли, льна и других, обладающая хорошими теплоизоляционными и звукоизоляционными свойствами и некоторым асептическим действием.
Пенька – это волокна стеблей конопли, отличающиеся высокой стойкостью и прочностью. Канаты и веревки из нее до сих пор используются в морском деле, так как практически не изнашиваются даже при постоянном контакте с морской соленой водой.
Войлок – плотный текстильный нетканый материал из валяной шерсти. Для конопатки нарезается полосами. При его использовании для конопатки обязательна предварительная пропитка составами, защищающими войлок от моли и других вредителей, и последующая его просушка. Можно использовать импрегнированный войлок – прошедший пропитку смолой или битумом.
Джут – это однолетнее лубяное растение из тропических районов Юго-Восточной Азии. В качестве межвенцового утеплителя и для конопатки используются продукты его первичной обработки – очесы джута, как правило в виде льноджутового полотна. Его широкое распространение связано с такими его свойствами, как небольшая теплопроводность и большое содержание лигнина – смолы, защищающей его от гниения.
При использовании мха нужно следить, чтобы мох был сухим, но достаточно гибким, не пересушенным. Дело в том, что пересушенный мох при конопатке будет крошиться, слишком же влажный может привести к загниванию дерева. Так как сухой мох быстро выветривается, его лучше смешивать с паклей. Дополнительное преимущество мха – птицы к нему не проявляют интереса, не растаскивают на гнезда.
Повторная конопатка делается через год – полтора, после полной осадки и просушки сруба.
Способы конопатки сруба
Конопатка может делаться двумя способами: «в растяжку» и «в набор».
Конопатка «в растяжку» делается в пазах и щелях. При этом делают из пакли прядь, и приставив ее к щели или пазу, вдавливают ее рукой или конопаткой, повторяя эту операцию до тех пор, пока паз не заполнится полностью. Затем паклю в пазу тщательно уплотняют наборной конопаткой. После этого делают из пакли валик, вставляют его в паз и, захватывая валик выступающими из этого паза волокнами, с силой его туда забивают. Необходимо обратить внимание на обязательность захвата валика волокнами – иначе он потом может выпасть обратно.
Конопатка «в набор» делается в широких пазах. При этом из пакли свивают длинные пряди диаметром 15 – 20 мм, сматывают их в клубки. «Набирая» из клубка петли пряди пакли забивают в паз. Количество вставляемых прядей зависит от глубины и ширины паза. Уплотнение паза делается сначала по верхней, а затем по нижней кромке. Окончательно выравнивают и уплотняют паклю дорожником.
Как конопатить сруб
Оконопачивание сруба во избежание его перекоса делается по венцам поочередно. Сначала самый нижний паз по кругу по всем стенам, затем следующий и т.д. Сначала конопатятся внешние стены, затем внутренние. Очень тщательно конопатятся углы, там наиболее продуваемые места . В процессе конопатки должны быть заполнены все пустоты, циркуляции воздуха сквозь них быть не должно.
Посмотрите видео конопатки сруба паклей
Стены в результате произведенных работ поднимаются на высоту до 10 – 15 сантиметров, поэтому перед конопаткой освобождают печную трубу в районе чердачного перекрытия и крыши, убирая около нее обмазку и засыпку. После оконопачивания заново восстанавливают герметичность и утепление пространства вокруг трубы.
После последней конопатки щели закрывают, чтобы птицы не растаскивали паклю, да и дополнительная защита от ветра. Для этого можно использовать деревянные рейки – нащельники, можно обить сруб евровагонкой, сайдингом, в зависимости от предпочтений, вкусов и финансовых возможностей. Более простой вариант – пропитка пакли с внешней стороны сруба после завершения окончательной конопатки масляной краской.
Также недавно стали применять такой способ защиты пазов, как набивка поверх них канатов – джутовых, льняных и т.д., обычно с помощью степлера. Такая отделка одновременно является и декоративным украшением постройки. Применяют ее как снаружи, так и внутри строений, особенно когда внутренняя отделка бревен заключается в их шлифовке и тонировке, если хотят, чтобы они сохраняли внешний вид и запах дерева.
Смотрим видео конопатки сруба джутовым волокном
Нужно отметить также недавнее появление такого метода защиты пазов и щелей, как герметики для деревянного строительства, создающих эластичный теплый шов поверх межвенцовых пазов, на который не влияет усадка сруба. Создаются такие герметики на основе акриловых полимеров.
Похожие статьи
Carbon Fiber Tow – обзор
1.7.1 Снижение стоимости волокна и разработка новых волокон
Армированное волокно является основным сырьем для композитных материалов. Текущая тенденция заключается в снижении цены на высококачественные волокна и разработке армирующих волокон со специальными функциями. В Таблице 1.2 и Таблице 1.3 показаны, соответственно, оценочный спрос на современные волокна и средняя цена на различные волокна в период с 1970 по 1995 год и с 1995 по 2015 год. Можно видеть, что спрос на современные волокна увеличивается с каждым годом, а цена падает.Например, на углеродное волокно спрос увеличивается с 8000 тонн в 1995 году до 40 000 тонн в 2015 году, увеличившись в 4 раза, а средняя цена составляет от 50 долларов США за кг до 20 долларов США за кг, снизившись на 60%. Очевидно, что снижение цен на передовые волокна расширяет сферу применения композитных материалов, например, применение в автомобилях. Напротив, увеличение количества может способствовать снижению цен на материалы.
Таблица 1.2. Расчетный спрос на современные волокна в мире в период с 1970 по 1995 год 1)
Тип волокна | Спрос (тонны) | Стоимость продаж в 1995 году (млн долларов) | |||
---|---|---|---|---|---|
1970 | 1980 | 1990 | 1995 | ||
Углеродное волокно 2) | 100 | 1000 | 6000 | 8000 | 400 |
Органическое волокно 3) | 50 | 5000 | 15000 | 18000 | 500 |
Высококачественное стекловолокно 4) | 10 | 500 | 2000 | 3000 | 50 |
Итого | 160 | 6 500 | 23000 | 39000 | 950 |
Примечание:
Таблица 1.3. Расчетный спрос на современные волокна в мире в период с 1995 по 2015 год 1)
Типы волокон | Спрос (тонны) | Стоимость продаж в 2015 году (млн долларов) | |||
---|---|---|---|---|---|
1995 | 2000 | 2005 | 2015 | ||
Углеродное волокно 2) | 8000 | 15000 | 25000 | 40 000 | 800 |
Органическое волокно 3) | 18000 | 26000 | 35000 | 45000 | 900 |
Высокоэффективное стекловолокно 4) | 3000 | 8000 | 15000 | 25000 | 200 |
Итого | 39000 | 49000 | 75000 | 110 000 | 1 900 0 |
Примечание:
Ключевое мероприятие по сокращению Цена на углеродное волокно заключается в разработке углеродного волокна на основе смолы и углеродного волокна большого размера.Цена на асфальт намного ниже, чем на полиакрилонитрильное (PAN) волокно, характеристики современного углеродного волокна на основе пека были близки или эквивалентны характеристикам стандартного углеродного волокна на основе PAN, а углеродное волокно на основе пека, как ожидается, будет становятся основными продуктами питания. В прошлом углеродное волокно аэрокосмического класса, используемое в военной оборонной технике, в основном включало 1K, 3K и 6K, но теперь постепенно развивается до 12K и 24K, как углеродное волокно для небольших буксиров. Углеродное волокно товарного сорта плотностью более 48К, которое отвечает потребностям общепромышленного применения, называется углеродным волокном большого размера, оно было разработано до 480К, 540К, что дает абсолютное преимущество в цене.В качестве стандартного углеродного волокна типа T300 уровень цен на текущем международном рынке коммерческой крупногабаритной буксировки был снижен до 8 ~ 10 $ / 1 млрд, ① , в то время как цена аэрокосмического качества составляет 15 ~ 20 $ / 1 млрд.
В прошлом высокомодульное органическое волокно было в основном арамидом. С 1980-х годов был разработан ряд новых органических волокон. Представителями являются полиэтилен сверхвысокой молекулярной массы (UHMWPE), PBO (полибензоксазол) и ароматическое полиэфирное волокно. Волокно СВМПЭ обладает высокой прочностью и модулем упругости, большим ценовым потенциалом и малым весом, является перспективным армированным материалом.
Чтобы адаптироваться к требованиям жаропрочных и многофункциональных композиционных материалов, в последние годы был разработан ряд специальных волокон, из которых более важны волокна из карбида кремния и нитрида кремния, которые характеризуются высокой термостойкость и полупроводник. Их композитные материалы на основе смол обладают абсорбирующими (незаметными) характеристиками.
Что такое пакля в текстиле? – Mvorganizing.org
Что такое пакля в текстиле?
Пряжа или ткань из жгута, а именно из коротких или рваных волокон (например, из льна, пеньки или синтетического материала), которые используются, в частности, для пряжи, шпагата или набивки.Непрерывные нити синтетического волокна (без скручивания), собранные в виде рыхлой веревки и скрепленные обжимом. Жгут – это форма перед нарезкой волокна на штапель.
Сколько волокон содержится в жгуте 1K?
С жгутом из углеродного волокна у нас обычно есть число «K», или тысячи нитей на жгут. 1K означает 1000 нитей / жгут, 3K 3000, 6K 6000, 12K 12000 и т. Д.
Что такое конопля и пакля?
Мокрое или сухое прядение из льна или хлопка и жгута из конопли или конопли для ткачества и изготовления ниток; прядение прочих чистых и смешанных волокон на льняных и конопляных машинах, кроме прядения льна для шнуров.Eurlex2019. КОНСОЛЬ «CANNABIS SATIVA», ОБРАБОТАННАЯ, НО НЕ ОТРАЖЕННАЯ; БУКСИРОВКА И ОТХОДЫ КОНСОЛИ, ВКЛ. ЕврЛекс-2. 5302.90.
Что означает буксировка?
На попечении или под непосредственным руководством; вместе с одним. Например, старшая девочка везла нового ученика на буксире, или Питер всегда вез семью на буксире. Это выражение отсылает к буквальному значению «тянуть за собой». [
Что такое буксирный сленг?
Значение TOW Итак, теперь вы знаете – TOW означает «Другая вики (Википедия)» – не благодарите нас.TOW – это аббревиатура, аббревиатура или сленговое слово, которое объяснено выше, где дано определение TOW.
Что означает буксировка в тексте?
прилагательное. неприятный. Альтернативное написание / произношение слова «разорвал». Эй, этот дом буксируют. Найдите больше слов с таким же значением: плохо, плохо, отстой, часто, в целом неприятно.
Что такое буксир в строительстве?
TOW: Верх стены.
Что означают пальцы ног?
(Запись 1 из 2) 1a (1): один из конечных элементов стопы позвоночного.(2): передний конец ступни или копыта. б: конечный сегмент конечности беспозвоночного.
Как называются ваши пальцы ног?
Фаланги (единственное число: фаланга) – 14 костей, из которых состоят пальцы ног. Большой палец стопы состоит из двух фаланг – дистальной и проксимальной. На других пальцах их по три. Сесамовидная кость – две маленькие гороховидные кости, которые лежат под головкой первой плюсневой кости на подушечке стопы.
Можете ли вы все еще ходить без пальцев ног?
Доктор объясняет, что без пальцев стопы человек вряд ли будет ходить естественно и уравновешенно.Хотя можно ходить, бегать и стоять без пальцев ног, кому-то это может быть очень трудно. Пальцы ног позволяют человеку естественно стоять на ногах.
Что было бы, если бы у нас не было пальцев на ногах?
Без пальцев ног вам было бы сложно стоять на одном месте. Чтобы оставаться в вертикальном положении, вам нужно будет переступать с ноги на ногу. Пальцы также помогают отталкиваться при каждом шаге. Без пальцев ног вы бы более или менее падали с ноги на ногу.
У пальцев ног есть цель?
Основная функция пальцев ног – обеспечивать осанку и равновесие, поддерживать вес нашего тела и двигаться во время цикла походки.Пальцы ног не только помогают выталкивать тело вперед при ходьбе, но и увеличивают длину шага, позволяя бегать быстрее.
Сколько пальцев на ногах вы можете потерять, продолжая ходить?
Пальцы ног влияют на равновесие: пальцы ног обеспечивают равновесие и поддержку при ходьбе. Скорее всего, потеря одного или нескольких пальцев может повлиять на ваше равновесие. Отсутствие любого из трех средних пальцев ног может существенно повлиять на вашу ходьбу. Восстановление и реабилитация: после операции боль значительно уменьшится через неделю.
Почему наши пальцы ног разделены?
Если два ваших пальца ноги больше напоминают V-образную форму между ними, а не находятся рядом друг с другом, это для вас. Разрыв подошвенной пластинки является наиболее частой причиной такого отрыва пальца ноги, и некоторые люди могут не осознавать, что это произошло, пока не увидят этот знак.
Почему хорошо разводить пальцы ног?
↳ ПОСАДКА: Растопыренные пальцы ног в земле – это фантастика для осанки. Наши ступни – это основа для ходьбы, бега, йоги, пеших прогулок и т. Д.Если наша основа тугая и сморщенная, то и осанка будет такой же. ↳ БОЛЬШЕ ПРОСТРАНСТВА: разведение пальцев ног дает нам больше места (даже в пояснице).
Распространение пакли
«Распространенный жгут» относится к практике распределения волокна в более тонкую и плоскую арматуру, например, жгут высокопрочного (HS) углеродного волокна шириной 5 мм обычно наносят на ленту шириной 25 мм. Затем эту однонаправленную ленту можно использовать в процессах автоматической укладки ленты (ATL) и автоматического размещения волокна (AFP).Его также можно использовать для производства тонких тканых материалов или многослойных не изгибающихся тканей. Хотя стекловолокно, арамид и полимерные волокна можно распространять, углеродное волокно является усилением, стимулирующим рост технологии распространения жгутов, поскольку отрасли, от спортивных товаров до авиакосмической промышленности, ищут более легкие и тонкие композиты. Усиление растяжек может весить всего 15 г / м 2 при толщине всего 0,02 мм (см. «Технологический тормоз для американских горок с подачей углерода?»).
Согласно источникам глобального производителя углеродного волокна, 80% углеродного волокна, которое сейчас используется во всем мире, распределяется до дальнейшей обработки.Это включает в себя большую часть углеродных волокон 50K, 24K и некоторую часть 12K, которые дешевле, чем более мелкие жгуты 1K, 3K и 6K, но могут использоваться для производства высококачественного армирования весом менее 300 г / м 2 . Например, эпоксидный препрег Toray (Токио, Япония), изготовленный из ткани полотняного переплетения T700S 12K, имеет такой же поверхностный вес, что и ткань из жгута 3K, и теперь повсеместно используется в ракетах и космических конструкциях.
Распространение также позволяет адаптировать поверхностный вес, а также другие свойства, такие как сопротивление распространению трещин для повышения устойчивости к повреждениям.Плоскостность расправленного жгута означает, что нити более прямые, чем те, которые связаны в обычные волокна. Это приводит к более эффективной несущей способности по весу и улучшенному качеству поверхности, а также к эстетической привлекательности.
Несомненно, буксирный буксир является отправной точкой для создания культового «тканого вида», который все чаще используется в спортивных товарах, небольших самолетах и в автоспорте.
Жгуттакже оказался полезным в конструкции ламинатов, которые выдерживают значительно более высокие нагрузки до разрушения первого и последнего слоев (см.рис.1), по словам доктора Стивена Цая, почетного профессора Стэнфордского университета (Пало-Альто, Калифорния, США) и соавтора критерия разрушения Цай-Ву для анизотропных материалов. Его идея двухугловой мультиаксиальной ткани CF, представленная как C-PLY компанией Chomarat (Ле Шейлар, Франция и Уильямстон, Южная Каролина, США), сочетает в себе один тонкий слой волокна под углом 0 ° и второй под малым углом, например 20 °. °, для достижения характеристик препрега, отверждаемого в автоклаве, в пропитанных смолой ламинатах, изготовленных без затрат времени и средств на автоклав (см. «Двухугловые ткани находят первое коммерческое применение»).
Распространение и ткачество: параллельные разработкиСегодня существует ряд компаний, которые могут поставить оборудование, необходимое для раскладывания жгутов для изготовления ленты, а также ткацкое оборудование с лентой. Но упомянутые здесь поставщики – это те, кому приписывают значительные разработки, которые часто представляют собой поворотные моменты в инновационной технологии буксировки.
Ленточное плетение – плетение ткани из лент вместо жгутов – было изобретено в 1995 г.Нандан Хокар из Технологического университета Чалмерса (Гётеборг, Швеция). Он представил свою работу в 2002 году, где студенты Андреас Марцман и Хенрик Бликер увидели потенциальную ценность для производителей композитных деталей и основали Oxeon (Борос, Швеция) в 2003 году, став вице-президентом по маркетингу и продажам и генеральным директором, соответственно.
«Когда мы основали Oxeon, мы не знали, что такое буксирное волокно», – говорит Марцман. Oxeon представила свои ткани для тесьмы TeXtreme в 2005 году. Ткани для тесьмы TeXtreme получили широкое распространение в автоспорте и спортивных товарах – Bauer, Bell, Cobra и Giro, и это лишь некоторые из них, – а также в промышленности и аэрокосмической отрасли.К последним относятся спортивные самолеты BlackWing и новое сиденье для коммерческих самолетов, разработанное совместно с HAECO Cabin Solutions (Гринсборо, Северная Каролина, США), которое снижает вес его предыдущего композитного сиденья на 20%.
Хотя Oxeon был первым на рынке, в других местах продолжались разработки. В патентной заявке 2001 года производитель тяжелых жгутов из углеродного волокна Zoltek (Сент-Луис, Миссури, США) подробно описал устройство для разделения углеродного волокна, в котором использовалась распорка и два или более эксцентриковых разделителя. В том же году основатели того, что впоследствии станет North Thin Ply Technology (NTPT, Рененс, Швейцария), начали разработку тонкослойных материалов, направленных на улучшение парусов CF.Эта тонкослойная технология использовалась в 2005 году на яхтах Alinghi America’s Cup и была названа 3Di дочерней компанией NTPT North Sails (Милфорд, Китай, США). В настоящее время NTPT продает тонкослойный препрег , а также композитные трубы и блоки, изготовленные из тонкослойных материалов для авиакосмической, морской, автомобильной, спортивной и потребительской отраслей.
Также в 2005 году компания Boeing Aerostructures Australia (Мельбурн, Виктория) произвела облицовку задней кромки длиной более 9 м для модели 787 Dreamliner компании Boeing Co. (Чикаго, Иллинойс, США), используя настойку смолы и ткани PrimeTex для распространения жгутов. разработан производителем углеродного волокна Hexcel (Стэмфорд, Коннектикут, США).Примечательно, что ткани PrimeTex уникальны по своей конструкции: «Мы не перематываем пакли в ленты и не ткаем», – говорит Гийом Кусто, менеджер по маркетингу композитных материалов Hexcel в Европе. «Мы плетем ткань, а затем расстилаем ее, используя запатентованную технологию, в результате чего ткань получается более плоской, без необходимости распределять входящие волокна» [см. Рис. 2]. Ткани Hexcel PrimeTex расширились: они используются, например, в велосипедных колесах CORIMA и лыжах Fischer, а также в космической, оборонной, автомобильной и морской сферах.
Параллельно с этим LIBA (Naila, Германия) запустила в 2002 году машину для укладки утка MAX 5 для производства многоосных тканей CF, разработала технологию распространения-буксировки в 2004 году, запустила офлайн-машину UD 500 в 2007 году, а затем использовала эту технологию для усовершенствования. его машины MAX 5, позволяющие вводить уток ленты UD из углеродного волокна. Машина также предлагала возможность укладывать отдельные слои под углом от -45 ° до 45 °, регулируемым с шагом 1 °. Ленты UD можно было выкладывать онлайн до ширины 227 мм или офлайн до 254 мм.Автономная система может распространять оптоволокно 50K или 60K с возможностью добавления второго уровня для распространения жгута 12K или 24K. Онлайн-система предлагала только последнее. LIBA была приобретена в 2014 году Карлом Майером (Обертсхаузен, Германия).
Компания Sigmatex установила машины MAX 5 как в Бенисии, Калифорния, США, так и в Нортоне, Великобритания. Машины MAX 5 также были приобретены SGL Kümpers (Латен, Германия), FORMAX (Лестер, Великобритания, приобретена Hexcel в 2016 году) и Vectorply (Феникс-Сити, Алабама, США). Chomarat использовала станки MAX 5 для производства мультиаксиальных дисков C-PLY во Франции в 2010 году и на своем новом заводе в США в 2014 году.Они также производят линию C-WEAVE компании Chomarat, занимающуюся ткацкими тканями и жгутом.
ПрезидентChomarat в Северной Америке Брайан Лауфенберг также отмечает, что «мы добились большого успеха в распространении очень большого и недорогого жгута углеродного волокна 457K, разработанного в Национальной лаборатории Ок-Ридж (ORNL, Ок-Ридж, Теннесси, США)». Он ссылается на жгут ORNL 400K-600K, сделанный из недорогого текстильного прекурсора, преобразованного в углеродное волокно, которое обеспечивает прочность на разрыв 400 ksi и модуль упругости 40 Msi (см. «ORNL ищет лицензиатов для своей недорогой технологии углеродного волокна»).«Его распределяют на 2 слоев плотностью 120 г / м и превращают в двухосную углеродную нежёбную ткань с углом наклона ± 45 °», – добавляет Лауфенберг. «Мы не просто покупаем машину у производителя и используем ее, а вместо этого немного адаптируем ее, и мы продолжаем развивать технологию». Например, жгут 457K также использовался для изготовления высокопроницаемой арматуры колпака лонжерона лонжерона 2 плотностью 600 г / м, которая впоследствии была подвергнута пултрузии и использована в 9-метровой лопасти из термопласта, изготовленной Институтом инноваций в области производства композитов (IACMI). и номинирован на премию JEC Innovation Award 2018.
Еще один крупный игрок – DORNIER Composite Systems (Линдау, Германия). «Мы производим машины и производственные линии, а не материалы или детали», – объясняет менеджер по продукции DORNIER Composite Systems Марио Крупка. «Однако мы предлагаем нашим клиентам возможность провести испытания в нашем технологическом центре, где у нас есть все наши машины, включая ткацкие линии, линии по производству лент и машины для ткачества лент / ткацких лент, а также стандартное и трехмерное ткацкое оборудование». Как и Oxeon, компания DORNIER сначала вышла на рынок, ткнув ленты.«7 лет назад покупательский спрос был, поэтому мы разработали специальный ленточный ткацкий станок», – поясняет Крупка. «Покупатели вернулись и захотели сами сделать кассеты». Таким образом, DORNIER также производит линии для производства полностью пропитанной термореактивной ленты и из термопластичного препрега. Последние, как он отмечает, могут использовать стекловолокно так же часто, как и ленты CF.
Индустриализация и стоимостьОдним из ключей к расширению охвата буксировкой на рынке является степень ее адаптации для массового производства . NTPT производит продукцию для спреда. «Но мы также занимаемся автоматизацией», – говорит президент компании Джеймс Остин, отмечая, что компания продает специализированное оборудование для автоматической укладки ленты (ATL), разработанное собственными силами. «Поскольку слои очень тонкие, например 0,03 мм для препрега 2 с плотностью 30 г / м, мы могли укладывать от 10 до 100 слоев, что вначале препятствовало продажам материала. Но поскольку мы автоматизировали ламинирование и комплектование, это изменилось. Теперь мы видим больше возможностей помочь другим компаниям разрабатывать такие уникальные решения для различных рыночных ниш.”
Когда Остин говорит об автоматическом ламинировании, он имеет в виду нанесение 10 или 16 слоев с цифровым управлением на рабочую зону размером 10 на 4 м. «Если вы делаете деталь размером 1 м на 1 м, то мы можем разрезать эту большую площадь на 40 плиток. По 10 слоев в каждом, вы можете создать стек из 400 слоев на одной машине, работающей в фоновом режиме, ламинируя и комплектуя материалы для этой детали экономичным способом ».
Марцман Oxeon, оглядываясь назад, отмечает: «Наши продукты гораздо более индустриализированы, чем когда мы впервые представили их, и технология значительно улучшилась.Мы работали с этими материалами в течение 15 лет, над разными типами деталей и узнали, что и где работает ». Он видит в Oxeon больше партнера по разработке, чем поставщика материалов. «Благодаря гибкости, которую обеспечивает наша технология, мы можем позволить производителям опробовать множество других вариантов». Как? «При традиционных технологиях ткачества вам потребуется 500 катушек, даже если необходимое пробное количество составляет всего 5 м 2 », – поясняет он. «Но мы можем легко установить несколько катушек и произвести 10 м 2 продукта с 10 вариантами.Так что у клиента будет более эффективное развитие ».
Обязан ли этот продукт с более высокими характеристиками надбавкой к цене? «Не обязательно», – говорит Кусто из Hexcel. «Если бы PrimeTex был намного дороже, его бы не использовали так часто, как раньше. Он добился успеха благодаря производительности при разумной цене за приложение ».
Крупка в DORNIER возвращается к масштабу: «Вы можете намазывать жгут 50K до 100 г / м², обрезать ленты до ширины 25 мм и ткать их в ткань плотностью 200 г / м². Скорость ткачества 50 резцов в минуту позволяет сделать 1.25 погонных метров ткани или 2,25 м² ткани шириной 180 см. Это очень экономично по сравнению с использованием более дорогого и легкого буксира CF для обеспечения того же поверхностного веса ».
Контроль поверхностного веса и распространения трещинХотя автоматизация и контроль затрат, безусловно, помогли устранить препятствия на пути распространения и буксировки, именно адаптируемость технологии в настоящее время способствует ее расширению на рынке . «Я думаю, людям сложно понять гибкость нашей технологии», – говорит Марцман.«Мы раскладываем паклю любой ширины, которую предпочитаем. Таким образом, жгут шириной 10 мм представляет собой один поверхностный вес, а жгут шириной 11 мм – другой поверхностный вес. Мы также можем использовать широкий спектр входных буксиров – от 1К до 60К и даже 320К от SGL. Мы также можем взять несколько входных буксиров. Таким образом, вы действительно можете точно подобрать нужный вам удельный вес волокна ».
По словам Крупки из DORNIER, распределение одной буксировки по сравнению с несколькими буксировками выполняется на одной и той же машине, но использует другую настройку. Распределение одиночной буксировкой имеет смысл для меньшей буксировки 12K или 24K, но требует большего количества катушек.В качестве альтернативы часто используются несколько жгутов, чтобы сделать более широкую ленту, которую затем разрезают на желаемую ширину. «Многократное разбрасывание жгута делает вас независимым от размера жгута по отношению к весу на участке», – добавляет он, однако точный коэффициент распределения зависит от требований заказчика и области применения.
Размер зависит от веса и толщины, что дает явное преимущество в ударопрочности. «Ударные характеристики улучшаются при использовании более тонких слоев», – говорит Марцман из Oxeon. Боб Скиллен, основатель и главный инженер VX Aerospace (Моргантон, Северная Каролина, США), который использовал C-PLY Chomarat в нескольких проектах самолетов, соглашается: «Чем больше тонких слоев, тем более прочная и жесткая деталь, чем меньше толстых слоев. .Он отмечает, что тонкослойные двухугловые ламинаты превосходят обычные квазиизотропные ламинаты (например, 0 °, 90 °, + 45 °, -45 °).
«Мы делаем super квазиизотропным, – говорит Остин из NTPT, – используя восемь ориентаций волокон вместо четырех, и мы можем даже перейти к 16 в крайних случаях. Поскольку слои очень тонкие, достигается своего рода однородность с очень хорошим распределением смолы по волокну, что улучшает передачу нагрузки от нити к нити для повышения производительности ».
Использование буксирной развязки vs.обычные пучки волокон в тканых тканях также улучшают ударопрочность. «Тканые ткани передают энергию удара большему количеству волокон, потому что они переплетаются, а не просто накладываются друг на друга, как в многоосных тканях», – объясняет Мартсман. «Однако плетение сгибает волокна, что ограничивает количество энергии, которое они могут поглотить, поскольку снижает их максимальную нагрузку. Spread-жгут Ткани имеют гораздо меньшую изгибаемость, обеспечивая лучшее из обоих миров ».
Марцман также отмечает, что крупные производители самолетов комбинируют тонкие слои с традиционными толстыми слоями.«Например, пять тонких слоев с 10 стандартными толстыми слоями дают интересную характеристику распространения трещин, которая позволяет им адаптировать характеристики устойчивости к повреждениям в конструкциях самолета».
У всех преимуществ производительности есть одно предостережение. «Вы должны адаптировать свои компьютерные модели и моделирование для тонких материалов, потому что механика различна», – говорит Марцман, отмечая, что Oxeon вложила значительные средства для этой цели в анализ методом конечных элементов (FEA) три года назад.«Мы можем комбинировать наши материалы с другими материалами и вариациями моделей ламината и структурных характеристик. Мы моделируем новые конструкции для клиентов и сравниваем с тем, что у них есть сегодня, включая оценку различных вариантов, таких как изменение типа волокна, поверхностного веса или укладка большего количества волокна в одном направлении по сравнению с другим. Важно иметь возможность быстро и легко сравнивать все эти варианты ».
Будущие продукты, процессы и приложенияЧто ждет в будущем буксировочную технику? «Мы видим рост не только в эстетике, но и в части жесткости деталей на 20%», – заявляет Крупка из DORNIER.«Это связано с меньшим обжатием. Например, использование 20 слоев жгутной ткани вместо 10 слоев ткани 3K обеспечивает более высокую жесткость при той же толщине стенок. Из-за этого мы наблюдаем больший интерес к использованию лент и тканых лент для структурного усиления ».
Еще одна причина – использование полностью пропитанных термопластичных лент. «Высокая ударопрочность этих материалов очень привлекательна для автомобильных деталей, таких как двери и бамперы», – отмечает Крупка. «Композиты из стекловолокна / полипропиленовых лент конкурентоспособны по цене по сравнению с легкими металлами, такими как алюминий или магний, а процесс формования проходит быстро с высокой степенью свободы дизайна.Он ссылается на применение в моделях автомобилей высокого класса в Азии и Европе, которые в настоящее время переходят на модели массового производства.
Austin в NTPT обсуждает новые возможности на устаревших рынках, таких как морские шахты и шахты для гольфа. Для морских судов автоматизация препрега NTPT позволила использовать сэндвич-панели для переборок и других интерьеров, которые предлагают более низкую стоимость, время доставки и вес по сравнению с панелями, пропитанными смолой. В валах для гольфа технология прерывистого препрега обеспечивает улучшенные характеристики, что, по мнению Остина, может обеспечить преимущества для других труб, таких как карданные валы (см. «Жгут с разбрасыванием дает новую жизнь традиционным рынкам»).
Он также видит возможности на новых рынках, таких как городская мобильность, где растет число программ, направленных на разработку нетрадиционных аэрокосмических транспортных средств, таких как электрические самолеты вертикального взлета и посадки (EVTOL) (например, Airbus Vahana ). «Все это очень зависимые от веса и естественные области применения тонкослойных материалов», – утверждает он. «Мы активно работаем над несколькими программами, разрабатывая сверхлегкие аэроструктуры. У углепластика также есть множество применений для электродвигателей, которые открывают для нас огромные возможности.Я думаю, здесь происходит гораздо больше, чем люди оценивают. Мы думаем, что электромобили окажут значительное влияние на будущее нашей компании ».
Марцман в Oxeon также оптимистично смотрит на аэрокосмическую отрасль, для которой его компания изготовила новую буксирную решетку с разбросом на ± 45 °. Он говорит, что сокращение брака стимулирует рост спроса. «Для детали длиной 1 м, изготовленной из ткани шириной 1 м 0 ° / 90 °, вы производите косые слои, обрезая ее под углом, но в результате получается 50% брака. Другой случай – большие детали, такие как 1.Крылья шириной 5 м, из которых можно получить только ткань шириной 1,6 м 0 ° / 90 °. Опять же, вы обрезаете косые слои под углом, в результате чего получаются отброшенные треугольники. При изготовлении крупных деталей, таких как резервуары и панели пола, процент брака невероятно высок ».
DORNIER также разрабатывает продукты для повышения производительности, в том числе машины для изготовления более толстых лент и более широких тканей, увеличивая ширину со 150 см до 266 см. «Мы также планируем ткать более широкие ленты, переходя от 40 мм основы и 45 мм утка к 50 мм.Более высокая скорость также является приоритетом, но чем быстрее вы едете, тем ниже качество. Заказчикам нужна скорость 50 м / мин и идеальное качество ленты. Хотя это невозможно, мы продолжаем разработку улучшений ».
Hexcel видит постоянный рынок распространения жгутов как тканых, так и многоосных тканей, производя последний в Лестере, Великобритания. «Мы все еще работаем над разработками на всех рынках», – говорит Кусто. «Это ключевая технология, и мы будем ее продвигать».
Материалы и процессы: форматы волокна для композитов
Волокна, используемые для армирования композитов, поставляются непосредственно производителями волокна и косвенно – переработчиками в различных формах, которые различаются в зависимости от области применения.
Ровинг и буксир. Ровинг – это самый простой и наиболее распространенный вид стекловолокна. Его можно нарезать, соткать или иным образом обработать для создания вторичных форм волокон для производства композитов, таких как циновки, тканые материалы, тесьма, трикотажные ткани и гибридные ткани. Ровинги поставляются весовыми с указанным диаметром нити накала. Термин выход обычно используется для обозначения количества ярдов в каждом фунте ровинга из стекловолокна. Точно так же жгут является основной формой углеродного волокна.Типичный размер жгута аэрокосмического класса составляет от 1K до 24K (K = 1000, поэтому 12K означает, что жгут содержит 12000 углеродных волокон). Углеродные волокна 12K на основе PAN и пека доступны с умеренным (33-35 Msi), промежуточным (40-50 Msi), высоким (50-70 Msi) и сверхвысоким (70-140 Msi) модулем упругости. (Модуль – это математическое значение, которое описывает жесткость материала путем измерения его прогиба или изменения длины под нагрузкой.) Новые тяжелые жгутовые углеродные волокна, иногда называемые волокнами товарного сорта , с числом нитей 48–320 тыс. доступны по более низкой цене, чем волокна аэрокосмического качества.Обычно они имеют модуль упругости 33–35 Msi и предел прочности на разрыв 550 ksi и используются, когда требуется быстрое наращивание деталей, чаще всего на рынках отдыха, промышленности, строительства и автомобилестроения. Тяжелые жгутовые волокна обладают свойствами, приближающимися к свойствам волокон аэрокосмического класса, но их можно производить с меньшими затратами из-за различий в исходных материалах и технологиях. (Высокая стоимость углеродного волокна и исторически значимые колебания его предложения и спроса вызывают неизменно высокий интерес в индустрии композитов к состоянию мирового рынка углеродного волокна, о чем говорилось в статье «Спрос и предложение: современные волокна.”)
Потенциально значительным недавним изменением является жгут из углеродного волокна, который содержит выровненных прерывистых волокон . Эти жгуты создаются с помощью специальных процессов, которые либо натягивают углеродный жгут с разной скоростью, что вызывает случайное разрушение отдельных нитей, либо иным образом разрезают или разделяют отдельные углеродные нити, так что начало и конец нити расположены в шахматном порядке, а их относительная длина примерно одинакова. так, чтобы они оставались выровненными, а жгут сохранял свою целостность.Разрывы позволяют волокнам с большей независимостью смещать положение относительно соседних волокон, что делает жгут более пластичным и дает ему возможность растягиваться под нагрузкой с более высокими прочностными характеристиками, чем рубленые, беспорядочные волокна. Формы волокна, изготовленные из выровненных прерывистых жгутов (см. «Маты» ниже), более драпируемые ; то есть они более податливы и, следовательно, легче приспосабливаются к изогнутым поверхностям инструмента, чем формы волокон, сделанные из стандартного жгута (см. «Выровненные прерывистые волокна достигают зрелости.»).
Маты – это нетканые материалы, изготовленные из волокон, скрепленных химическим связующим. Они бывают двух видов: рубленая и непрерывная. Рубленые маты содержат случайно распределенные волокна, нарезанные на длину, обычно от 38 мм до 63,5 мм. Мат из непрерывных волокон состоит из завитков из непрерывных волокон. Поскольку их волокна ориентированы беспорядочно, маты изотропны – они обладают одинаковой прочностью во всех направлениях. Маты из рубленых прядей обеспечивают недорогое армирование, прежде всего, при ручной укладке, непрерывном ламинировании и некоторых применениях закрытого формования. По своей сути более прочный мат из непрерывных прядей используется в основном при компрессионном формовании, формовании с переносом смолы и пултрузии, а также при производстве преформ и штампованных термопластов. Некоторые маты с непрерывной прядью, используемые для пултрузии, и маты с иглой, используемые для формования листов, исключают необходимость хранения шпулярников и измельчения.
Ткани изготавливаются на ткацких станках разного веса, переплетения и ширины.Тканые материалы являются двунаправленными, обеспечивая хорошую прочность в направлении осевой ориентации пряжи или ровницы (0º / 90º), и они способствуют быстрому изготовлению композитов. Однако прочность на разрыв тканых материалов в некоторой степени снижается, потому что волокна изгибаются, когда они проходят над и под друг друга в процессе ткачества. Под действием растягивающей нагрузки эти волокна имеют тенденцию выпрямляться, вызывая напряжение в матричной системе.
Для двунаправленных тканей используется несколько различных типов плетения.В полотняном переплетении каждая пряжа наполнителя (то есть пряжа, ориентированная под прямым углом к длине ткани) попеременно пересекает и под каждой основной пряжей (продольной пряжей). Другие переплетения, такие как жгут , сатин и корзина переплетения, позволяют пряже или ровнице пересекать и под множеством волокон основы (например, больше двух, меньше двух). Такое переплетение, как правило, более драпируемое, чем полотняное переплетение.
Тканый ровинг относительно толстый и используется для тяжелого армирования, особенно при ручной укладке и применении инструментов.Тканый ровинг из-за относительно грубого переплетения быстро смачивается и стоит относительно недорого. Однако можно производить исключительно тонкие ткани из стекловолокна для таких применений, как усиленные печатные платы.
Гибридные ткани могут быть изготовлены из различных типов волокон, составов прядей и типов тканей. Например, высокопрочные пряди из S-стекла или волокна малого диаметра могут использоваться в направлении основы, в то время как менее дорогие пряди составляют наполнитель.Гибрид также можно создать, сшив вместе тканый материал и нетканый мат.
Мультиаксиальные ткани – это нетканые материалы, изготовленные из однонаправленных волоконных слоев, уложенных друг на друга в разной ориентации и скрепленных сшиванием по всей толщине, вязанием или химическим связующим. Долю пряжи в любом направлении можно подбирать по желанию. В многоосных тканях исключается изгиб волокон, связанный с ткаными тканями, потому что волокна лежат друг на друге, а не пересекаются и снижаются.Это позволяет лучше использовать внутреннюю прочность волокон и создавать более гибкую ткань, чем тканая ткань аналогичного веса. Доступны сверхтяжелые нетканые материалы (до 200 унций / ярд²), которые могут значительно уменьшить количество слоев, необходимых для укладки, делая производство более рентабельным, особенно для крупных промышленных сооружений. Высокий интерес к многослойной арматуре без обжима стимулировал значительный рост этой категории арматуры.
Новый стиль многоосного армирования, разработанный Dr.Стивен Цай из Стэнфордского университета вместе с Chomarat (Ле Шейлард, Франция и Андерсон, Южная Каролина, США) был представлен в 2011 году, который ориентирует волокна под очень малыми углами, такими как 0 ° / 20 °, что может заменить квазиизотропные ориентации волокон для лучшая производительность и меньший вес. Одним из результатов является продукт под названием C-PLY, который недавно использовался компанией VX Aerospace (Моргантон, Северная Каролина, США) на своем четвертомасштабном БПЛА VX-1 KittyHawk . Он имеет крылья, плавно переходящие в аэродинамический фюзеляж, и является первым самолетом, использующим анизотропные ламинаты Цая, а его полномасштабная версия предназначена для использования в качестве беспилотных гражданских или военных (см. Изображение и изображение слева).Подробнее о БПЛА KittyHawk и о том, как его создатели использовали эту новую форму волокна, читайте в статье «VX Aerospace: Маленькая компания, большая производительность».
Плетеные ткани ткутся непрерывно под косым углом и имеют по крайней мере одну осевую пряжу, которая не гофрируется в процессе ткачества. Сила тесьмы зависит от переплетения трех или более пряжи без скручивания любых двух пряжей друг вокруг друга. Эта уникальная архитектура обычно обеспечивает большую прочность по сравнению с тканью.Он также имеет естественную формуемость, что делает оплетку особенно подходящей для производства рукавов и преформ (см. «Преформы» ниже), поскольку она легко принимает форму армируемой детали, тем самым устраняя необходимость в разрезании, сшивании или манипуляциях с ней. размещение волокна. Косы также доступны в виде плоской ткани. Они могут изготавливаться с трехосной архитектурой, с волокнами, ориентированными под углом 0 °, + 60 °, -60 ° в одном слое. Эта квазиизотропная архитектура в одном слое плетеной ткани может устранить проблемы, связанные с наложением нескольких слоев ткани 0˚, + 45˚, -45˚ и 90˚.Кроме того, склонность к расслоению (разделению волоконных слоев) резко снижается при использовании квазиизотропной плетеной ткани. Его архитектура 0 °, + 60 °, -60 ° придает ткани одинаковые механические свойства во всех направлениях, поэтому возможность несоответствия жесткости между слоями исключается.
Как в рукаве, так и в плоской ткани волокна сплошные и механически переплетены. Поскольку все волокна в конструкции участвуют в событии нагрузки, нагрузка равномерно распределяется по всей конструкции.Таким образом, тесьма может поглотить много энергии, если она разорвется. Ударопрочность, устойчивость к повреждениям и усталостные характеристики оплетки привлекают производителей композитов в самых разных областях, от хоккейных клюшек до корпусов вентиляторов реактивных двигателей.
Заготовки представляют собой армирующие формы почти чистой формы, предназначенные для использования в производстве конкретных деталей путем наложения и формирования слоев из рубленого, однонаправленного, тканого, сшитого и / или плетеного волокна в заданную трехмерную форму.Сложные формы деталей могут быть максимально приближены путем тщательного выбора и интеграции любого количества армирующих слоев различной формы и ориентации. В связи с их потенциалом высокой эффективности и скорости обработки был разработан ряд технологий предварительного формования с помощью специальных связующих, методов нагрева и уплотнения, а также использования автоматизированных методов распыления, ориентации и уплотнения рубленых волокон.
Недавний и необычно творческий пример , автоматизирующего производство преформ , – это технология Fiber Patch Placement (FPP) компании Cevotec (Гархинг, Германия), автоматизированный способ размещения преформ из углеродного волокна в менее дорогостоящее армированное стекловолокном кайтборды, созданные North Kiteboarding (Оберхахинг, Германия), как средство удовлетворения сугубо индивидуальных предпочтений с точки зрения «производительности доски» со стороны энтузиастов кайтбординга без радикального повышения цен на кайтборды (см. иллюстрацию / фото и подпись слева).Чтобы узнать больше об этом, нажмите «Преформы Fiber patch помогают оптимизировать характеристики кайтборда».
Препреги представляют собой пропитанные смолой волокна, изготовленные путем пропитки волокон контролируемым количеством смолы (термореактивной или термопластичной) с использованием технологий растворителя, горячего плавления или порошковой пропитки. Препреги можно хранить на «В-стадии», то есть в частично отвержденном состоянии, до тех пор, пока они не потребуются для изготовления. Лента или ткань препрега используются при ручной укладке, автоматической укладке ленты, укладке волокон и в некоторых операциях намотки нитей (см. Соответствующие заголовки в сегменте «Методы изготовления» справочника материалов CW ). Однонаправленная лента (все волокна параллельны) является наиболее распространенной формой препрега. Препреги, изготовленные из тканых волокон и других плоских изделий, предлагают армирование в двух или более измерениях и обычно продаются полными рулонами, хотя некоторые поставщики доступны в небольших количествах. Изготовленные путем пропитки волокнистых преформ и оплеток обеспечивают трехмерное армирование.
Препрегиобеспечивают однородное сочетание волокна и смолы и обеспечивают полное смачивание. Они также устраняют необходимость взвешивания и смешивания смолы и катализатора для мокрой укладки.Для большинства термореактивных препрегов драпировка и липкость «обработаны» для облегчения обращения, но они должны храниться при температуре ниже комнатной и иметь ограничения по времени хранения; то есть их необходимо использовать в течение определенного периода времени после извлечения из хранилища, чтобы избежать реакции преждевременного отверждения. Термопластичные препреги не нуждаются в охлаждении и не подлежат ограничениям по сроку службы, но без специального состава они не имеют липкости или драпировки, как у термореактивных препрегов, и, следовательно, их труднее формировать.
Бесспорно, что препреги позволяют производить готовые детали с наименьшей массой, высочайшими механическими свойствами и низким содержанием пустот.Однако они также были исторически самыми дорогими, отчасти потому, что они исторически производились специалистами – производство препрега было промежуточным, дискретным этапом в цепочке поставок композитов. Недавно были предприняты усилия по устранению неэффективности и связанных с этим затрат, связанных с этим дополнительным этапом. Два интересных подхода к этой цели, оба встроенных процессов , были представлены на конференции и выставке SPE Automotive Composites Conference & Exhibition 2015 в Детройте, штат Мичиган, США.Они превращают производителей композитов в препреггеры во многом так же, как процесс прямого изготовления длинноволоконных термопластов (D-LFT) в конце 1990-х – начале 2000-х годов, когда работа композиторов была переложена на производителей. Обе новые технологии исключают ранее необходимые и дорогостоящих, этапов замораживания и хранения препрега перед его отправкой покупателю, который затем должен также хранить и размораживать его перед использованием в процессе формования, расходы на которые несет процессор и, предположительно, заказчик процессора.
Наиболее близким к коммерциализации является встроенный процесс предварительной обработки, разработанный совместно Mitsubishi Rayon Co. Ltd. (Токио, Япония) и Mitsubishi Rayon Carbon Fiber and Composites Inc. (Ирвин, Калифорния, США). Ученые Mitsubishi сокращают расходы за счет непосредственного покрытия отдельных пучков углеродного жгута, калибровки ширины и последующей перемотки продукта на катушки. Система автоматической укладки волокон (AFP) – Mitsubishi называет ее автоматизированной укладкой towpreg – затем используется для укладки стопки слоев, чтобы избежать ручной укладки.Затем стопки предварительно формируются и формуются с помощью собственного процесса компрессионного формования препрега (PCM). Другой подход – это новый процесс InPreg (встроенный препрег), разработанный Институтом химической технологии им. Фраунгофера (ICT) (F-ICT, Пфинцталь, Германия). Подобно подходу Mitsubishi PCM, препреги InPreg предназначены для формования в прессах для сжатия, а не на более экзотическом оборудовании, что открывает возможности для изготовления ламинатных композитов более широкому кругу производителей. этапы предварительного формования и формования InPreg выполняются в пресс-инструменте.Это исключает не только время, необходимое для нагрева, предварительного формования и охлаждения препрега, но также стоимость и место для станции предварительного формования. Ключом к процессу Inpreg является четырехкомпонентная система эпоксидной смолы с B-стадией от Huntsman Advanced Materials (Базель, Швейцария) и более дешевое жгутовое углеродное волокно 24-50K, которое формируется в UD-ткань без обжима (NCF). . (Подробнее об обоих поточных методах читайте в разделе «Более низкая стоимость, меньше отходов: поточное производство препрега».)
Распределенный жгут – это отдельный жгут (или нескрученная пряжа) волокна, который разложен до тех пор, пока отдельные нити не будут лежать бок о бок, образуя ультратонкую ленту.Например, жгут углеродного волокна 12K может иметь ширину от 5 до 25 мм, уменьшая его толщину на 80%. Эти расправленные жгуты могут быть вплетены в ткань, размещены для образования многоосной не изгибающейся ткани (NCF) или для приема жидкой или порошковой смолы с образованием ленты для расправленных жгутов или жгутов. Использование тканого жгутного полотна вместо более обычных армирующих материалов может привести к снижению веса композитного ламината на 20-30%. Это достигается за счет закрытия промежутков между основой и утком в основе и утке, чтобы меньше смолы задерживалось там, а также за счет уменьшения извитости волокон, в результате чего получаются более прямые волокна, что повышает прочность.Таким образом, конечный композитный ламинат может использовать меньшее количество более тонких слоев для достижения таких же или лучших характеристик.
Поставщик волокна Hexcel (Стэмфорд, Китай, США) заявляет о 5-8% сокращении зазоров в ткани и возможности достижения с углеродным волокном свойств жгута 6K при поверхностном весе 3K, свойств жгута 12K при поверхностном весе 6K и т. Д. . North Thin Ply Technology (NTPT, Penthalaz-Cossonay, Швейцария) утверждает, что может быть распределено по любому волокну , и заявляет, что достижимы очень низкие поверхностные веса: 30 г / м 2 для углеродного волокна на основе PAN и 14 микрон диаметр кварцевого волокна, 35 г / м 2 для стекловолокна диаметром 9 микрон, 20 г / м 2 для арамидного волокна и 30 г / м 2 для полибензоксазола (ПБО) и других синтетических волокон.Поставщиками усиленного жгута являются Hexcel, NTPT, Oxeon (Борас, Швеция), Sigmatex (UK) Ltd. (Ранкорн, Великобритания), Chomarat и FORMAX (Лестер, Великобритания). Приложения включают в себя велосипеды, лыжи, хоккейные клюшки, ракетки, парусные лодки, гоночные автомобили и самолет Solar Impulse .
Вторичное углеродное волокно (RCF) армирующие элементы доступны в различных формах, включая рубленые волокна, нарезанные на определенную длину, рубленые волокна, составленные в виде гранул из термопласта с длинными волокнами (LFT), трехмерные преформы в форме сетки и произвольно ориентированные маты из рубленого волокна – сухие или комбинированные с термопластами – включая полипропилен (PP), полиэтилентерефталат (PET), полиамид (PA или нейлон), полифениленсульфид (PPS), полиэфиримид (PEI), полиэфирэфиркетон (PEEK).Маты из рубленого волокна также можно обрабатывать, например, чесанием, чтобы добиться большего выравнивания волокон, что приводит к лучшим механическим свойствам. Это разнообразие продуктов доступно у ряда поставщиков RCF по всему миру, и они перерабатываются с помощью пиролиза, при котором смола сжигается из отходов препрега и отвержденных структур. Компания Technical Fiber Products Inc. (TFP, Скенектади, Нью-Йорк, США и Бернсайд, Великобритания) производит вуали из RCF плотностью 2 г / м 2 .
ПродукцияRCF также производится собственными силами из отходов производства сухого волокна. В продуктах SigmaRF повторно используются собственные сухие производственные отходы Sigmatex путем объединения углеродных волокон диаметром от 45 до 60 мм с термопластическим носителем для образования лент, которые используются для изготовления не изгибающихся тканей, например, 220 г / м 2 Углеродное волокно ± 45 ° / двухосный ПЭТ NCF. Другие варианты включают RCF / Kevlar / PEI, RCF / PA и RCF / PES.
Институт обработки пластмасс (IKV) при RWTH Aachen University (Ахен, Германия) взял зарождающиеся волокна, не собранные роликами во время формования прекурсора углеродного волокна PAN (отходы производства углеродного волокна или побочный продукт), а затем нарезал, карбонизировал и сформировал из них однородные маты с использованием непрерывного процесса воздушной прослойки.(Подробнее о технологиях регенерации углеродного волокна и рынке вторичного продукта см. «Обновление вторичного углеродного волокна: завершение цикла жизненного цикла углепластика».)
Также разрабатываются новые методы производства непрерывных переработанных волокон, включая сольволиз с использованием спиртов или других растворителей для удаления смол без горения или высоких температур, пиролиз и разматывание сосудов высокого давления с намотанной нитью и использование эпоксидных смол, которые позволяют матрице быть переработанный как термопласт, такой как отвердители Recyclamine от Connora Technologies (Хейворд, Калифорния, США).
Формовочные смеси – еще один способ включения волокон в композит. Традиционно они были разработаны в пластмассовой промышленности и содержат короткие волокна (2-25 мм) при низком весовом процентном содержании (5-50%). Компаунд для формования массы (BMC), похожий на замазку, используется при литье под давлением, в то время как компаунд для формования листов (SMC) используется для более крупных деталей и более высоких требований к прочности, как правило, в процессе компрессионного формования.
Стекломат термопласта (GMT), который также поддается прессованию, имеет сплошное армирование случайными волокнами.GMT был разработан в 1960-х годах как шаг вперед от короткого нейлона, армированного волокном. Он столкнулся с растущей конкуренцией со стороны армированного длинным волокном термопласта (LFRT или LFT), который производится путем разрезания пултрузионных непрерывных стекловолоконных стержней малого диаметра на гранулы. LFT имеет непрерывное однонаправленное волокно, проходящее по всей длине гранулы, и предлагает свойства между GMT и термопластами с коротким стеклом. В 1990-х производители оборудования разработали системы поточного компаундирования (ILC), которые объединяют ранее раздельные процессы компаундирования и формования.Эти системы прямого длинноволоконного термопласта (D-LFT) сочетают в себе смолу, арматуру и добавки на прессе, доставляя отмеренную дробь или заряд непосредственно к оборудованию для литья под давлением или компрессионного формования. Это исключает запасы предварительно приготовленного продукта и позволяет выбирать длину волокна.
SMC, BMC, GMT и LFT используются в широком диапазоне приложений, где требуются сложные формы и формованные детали, включая автомобильные детали, бытовую технику (бак стиральной машины), медицинские приборы, потребительские товары, электронику, спортивные товары, кронштейны, корпуса. , запчасти для транспортных средств и электрооборудования.
SMC, в частности, предлагает уплотнение деталей, контур глубокой вытяжки и множество других преимуществ по сравнению со сталью и алюминием: он обычно на 40% легче металлов при сопоставимой по характеристикам геометрии. Хотя он не ржавеет и не подвергается коррозии и не требует такой обработки, он обладает термической и химической стойкостью, чтобы выдержать электрофоретическое (электронное покрытие) осаждение процессов предотвращения ржавчины на металлических компонентах шасси, поэтому детали SMC могут быть прикреплены к корпусу в белом (предпочтительный метод сборки) и не требует специальной сборки электронного покрытия.Однако до недавнего времени SMC имела преимущество в стоимости при объемах производства не более 150 000 единиц. Однако новый SMC низкой плотности от Continental Structural Plastics (CSP, Auburn Hills, MI, US) получил название TCA (жесткий класс A) Ultra Lite. При удельном весе (SG) 1,2 он обеспечивает снижение массы на 28% по сравнению с марками TCA Lite средней плотности (1,6 SG) компании CSP и на 43% по сравнению с обычными марками SMC 1,9 SG. Кроме того, он не только предлагает механические характеристики, сравнимые с TCA Lite (оба имеют матрицу из ненасыщенного полиэфира от AOC Resins, Collierville, TN, US), но также, как сообщается, более эффективно связывается с краской и клеем.Что наиболее важно, анализы жизненного цикла, проведенные CSP, как сообщается, показывают, что даже при объемах до 350 000-400 000 автомобилей в год TCA Ultra Lite стоит дешевле в расчете на одну деталь, чем алюминий (см. Фото и подпись слева). Подробнее о новом SMC см. «SMC низкой плотности: лучше жить благодаря химии».
Стекловолокно является наиболее распространенным и наименее дорогим армированием, используемым в формовочных смесях, арамидное волокно обеспечивает износостойкость, волокно из нержавеющей стали обеспечивает защиту как от электростатического рассеяния (ESD), так и от электромагнитных помех (EMI), а углеродное волокно обеспечивает более высокий модуль упругости и меньший вес. а также свойства ESD.Также были разработаны формовочные смеси, армированные натуральными волокнами (конопля, лен, сизаль и древесные волокна), в том числе. Они набирают популярность в автомобильной промышленности, спортивных товарах и потребительских товарах.
Формовочные смесиAdvanced предназначены для применения в областях с более высокими эксплуатационными характеристиками, в том числе в аэрокосмической и военной промышленности. В этих материалах используются смолы с более высокими характеристиками, такие как эпоксидная, фенольная, винилэфирная, бисмалеимидная (BMI) и полиимидная, и с содержанием волокон от 45% до 63% по весу.Волокна включают углеродное стекло и стекло E, а также стекло S2 с более высокими характеристиками. TenCate Advanced Composites BV (Нейвердал, Нидерланды) производит BMC с эпоксидной смолой, цианатным эфиром, нейлоном, смолами PPS или PEEK и углеродным или стекловолокном S2 длиной от 12 мм до 50 мм. HexMC производится Hexcel с использованием углеродных волокон длиной 50 мм и эпоксидной смолы. Множество других продуктов SMC из углеродного волокна доступны от поставщиков, включая Continental Structural Plastics, Quantum Composites Inc. (Бэй-Сити, Мичиган, США) и совместное предприятие Zoltek Corporation (Санкт-Петербург).Луи, Миссури, США) и Magna Exteriors (Париж, Франция).
В последнее время формовочные смеси позволяют армировать изделия, созданные с помощью того, что стало известно как процессы аддитивного производства, также известные как 3D-печать. Рубленое и коротковолокнистое армирование может быть адаптировано для использования в обычном типе 3D-печати, называемом моделированием наплавления. Большая часть 3D-печати из армированного пластика имеет ограниченный размер (для обзора см. «3D-печать: ниша или следующий шаг к производству по запросу?»).Но, по крайней мере, один недавний демонстрационный проект показывает, что широкоформатная печать технически практична. и экономически оправданы: Национальная лаборатория Ок-Ридж (Ок-Ридж, Теннесси, США) и производитель оборудования Cincinnati Inc. (Харрисон, Огайо, США) продемонстрировали большие размеры. возможность форматной печати с помощью системы Big Area Additive Manufacturing (BAAM) в сотрудничестве с Local Motors (Чандлер, Аризона, США) для производства первого в мире автомобильного кузова, напечатанного на 3D-принтере. Специально разработанный кузов спортивного автомобиля Strati был напечатан на полу выставки на выставке IMTS в 2014 году за 44 часа с использованием смеси акрилонитрилбутадиенстирола (ABS), армированной 15% углеродным волокном, поставляемой SABIC (Питтсфилд, Массачусетс, США).Подробнее о демонстрации читайте в разделе «Аддитивное производство: можно ли напечатать автомобиль ?» ”
Примечание редактора: Чтобы продолжить чтение статей в «Industry Overivew, Часть I: Материалы и процессы», вы можете вернуться в главное меню SourceBook, нажав здесь .
Усиление> Ткани для развязки – NetComposites
Производство STF включает распространение жгута углеродного волокна с большим количеством волокон (например, 12–12 000 нитей) на тонкие и широкие ленты Spread Tow Tap (STT), а затем их плетение в легкую ткань с использованием новой техники ткачества.STF обеспечивает относительно низкую степень обжатия и большее покрытие и, таким образом, может улучшить механические характеристики, обеспечить снижение веса на 20-30% и улучшенную драпируемость.
Благодаря этому новому маршруту STF становится возможным заменить обычные тканые углеродные ткани с малым весом, произведенные с использованием жгутов 1–6k, на жгуты из углеродного волокна 12k или более при одновременном получении армирования с еще меньшим поверхностным весом. Таким образом, производители углеродного волокна теперь имеют возможность поставить, по сути, пару штук жгутов, т.е.грамм. 12k и 24k вместо производства различных углеродных волокон в диапазоне 1k – 6k.
Концепция STF проста и прямолинейна. Путем расположения волокон в тканой структуре с максимально возможной прямой ориентацией, как в плоскости, так и вне плоскости, свойства волокна могут быть наиболее эффективно использованы при растягивающей нагрузке. Лист STF механически аналогичен конструкции с перекрестным слоем (0 ° -90 °), сделанной с использованием лент UD, с преимуществом в том, что STF обеспечивает улучшенную способность к драпированию и сопротивление расслаиванию по сравнению с перекрестно сложенными UD.
За счет контролируемой операции жгуты из углеродного волокна, обычно плотностью 12k и более, аккуратно распределяются до STT желаемой ширины и стабилизируются, чтобы предотвратить скручивание ленты обратно в исходную форму жгута / пряжи. Благодаря растеканию полученные ленты становятся очень тонкими. Эти STT затем используются в качестве основы и утка в процессе ткачества ленты для производства STF. По сравнению с обычными тканями, использование лент с растянутыми волокнами при производстве STF напрямую приводит к получению тканого материала с высокой объемной долей волокна и меньшим количеством точек переплетения, что соответственно снижает частоту обжима и угол обжима.
На рис. 1 сравниваются коэффициенты покрытия традиционной ткани 1k, плоской жгутной ткани, полученной с использованием жгута 12k, и STF, также произведенной с использованием жгутов 12k. Как можно заметить, традиционные и плоские жгуты могут иметь отверстия в каждой точке переплетения, тогда как STF является сплошным.
Рис. 1 Традиционная ткань 1k (слева) и плоская жгутовая ткань (в центре) имеют меньший коэффициент покрытия по сравнению с STF (справа).
Более низкие механические характеристики традиционных тканых армирующих тканей можно отнести к углу обжима и частоте обжима из-за использования жгутов, которые сравнительно уже и толще, чем STT.Эти факторы, которые отрицательно сказываются на характеристиках тканого материала для применения в композитах, значительно уменьшаются за счет вплетения STT в виде основы и утка в STF.
Наряду с другими армирующими материалами, такими как ровницы, однонаправленные ленты (UD), не гофрированные ткани (NCF) и традиционные тканые структуры из пряжи / пакли, STF в настоящее время является признанным членом семейства текстильных армирующих материалов и все чаще используется в ряде передовые композитные приложения.
Опубликован с разрешения Dr.Нандан Хокар и Фредрик Олссон
http://www.oxeon.se
Поделиться статьей
Твиттер Facebook LinkedIn Электронная почта
Вернуться к другим тканям
Жгут из ацетата целлюлозы Estron | Eastman
Eastman производит жгут ацетатного волокна Estron ™ в виде пучка или ленты непрерывных волокон, упакованных в тюк. Тюки ацетатного жгута продаются покупателям для использования в качестве одного из компонентов при производстве сигаретных фильтров.
Жгут ацетата целлюлозы – это целлюлозное волокно на биологической основе, которое биоразлагаемо в почве и в промышленных и домашних условиях компостирования.
Ацетатный жгут Eastman Estron ™ получают из древесной массы, возобновляемого ресурса, получаемого из деревьев, выращиваемых в ответственно управляемых лесах, и производятся в процессе почти замкнутого цикла, когда отходы либо перерабатываются, либо повторно используются, либо предлагаются для продажи.Смотрите наши
политика в отношении источников экологически чистой древесной массы для получения дополнительной информации. | |
Во время производства Estron ™ производственные растворители возвращаются в систему для очистки и использования снова и снова. Это создает почти замкнутую систему, которая гарантирует, что все отходы либо повторно используются, либо предлагаются для перепродажи. | |
Мы заботимся о безопасности и благополучии наших сотрудников, окружающей среды и наших глобальных сообществ, поэтому мы работаем в рамках общекорпоративных инициатив в области устойчивого развития и безопасности.Узнайте больше на
www.eastman.com/sustainability. | |
Ацетатный жгут Eastman Estron ™ также является биоразлагаемым в определенных средах, что делает возможными решения по окончании срока службы. Устойчивое развитие на протяжении всего жизненного цикла нашего продукта является ключевым моментом, и мы стремимся к дальнейшему развитию в этой области. Свяжитесь с вашим представителем Eastman для получения дополнительной информации. |
Как работает эвакуатор?
25 сен Как работает эвакуатор?
Отправлено в 00:00 в блогах по ШубхамЭвакуаторы – захватывающие автомобили.Издалека кажется, что водитель делает несколько подключений и эвакуатор готов к работе. Но, конечно, происходит нечто большее, чем кажется на первый взгляд. Эвакуаторы сложные. В конце концов, у них должна быть сила, чтобы буксировать целую машину.
Эвакуаторы работают за счет установки кронштейнов между колесами автомобиля и надежного крепления автомобиля к грузовику с помощью штифтов. Это простая концепция, но материал и прочность деталей эвакуатора являются чрезвычайно мощными и надежными инструментами.
Если вас интересует именно эвакуатор, эта статья для вас. Скоро появится дополнительная информация о том, как работает эвакуатор, а также несколько других ответов на вопросы, которые могут у вас возникнуть. Просто продолжай читать.
5 основных принципов работы эвакуатора
Подключение к системе кронштейнов
В современных эвакуаторах используется система кронштейнов для облегчения буксировки. В задней части эвакуатора находится большая стальная рама, которая используется для поддержки автомобиля, который буксирует грузовик.Этот метод считается наиболее безопасным, поскольку он требует от водителя небольшой ручной работы, а также касания только колес буксируемого автомобиля.
Эвакуаторы с кронштейномможно использовать как для передних, так и для задних колес легкового автомобиля. Этот способ буксировки считается наиболее быстрым и эффективным, и владелец буксируемого автомобиля может быть уверен, что его автомобиль не будет поврежден из-за использования крюков или цепей.
Закрепите автомобиль
При использовании системы кронштейнов колеса автомобиля устанавливаются между стальными балками и затем фиксируются на месте прочными стальными штифтами.Это работает с использованием механизма, который опускает и поднимает стальные балки, известные как желток.
Машина установлена на место для опускания желтка. Автомобиль равномерно вводят в желток, а затем вставляют в колеса штифты, чтобы автомобиль оставался на месте.
Как мы уже говорили, это самый безопасный способ буксировки автомобиля, так как он гарантирует, что любые другие части автомобиля не будут повреждены в процессе буксировки. Как только автомобиль будет прикреплен к желтку стальными штифтами, он готов к буксировке.
Эффективность и скорость
Эффективность и скорость работы необходимы для обеспечения безопасности водителей эвакуаторов. В случае водителя эвакуатора единственный ручной труд, который требуется, – это правильная установка штифтов через желток и колеса. Помимо этого, все опускание и подъем желтка осуществляется механически.
Это также безопаснее для водителя эвакуатора. В то же время опытный водитель эвакуатора может покрыть весь этот процесс менее чем за минуту.При использовании других методов буксировки поиск подходящего места для ручного прикрепления цепей или крюков к днищу автомобиля может оказаться изнурительным процессом.
Буксировка с цепью и крюком
Конечно, не все эвакуаторы используют брекет-систему, и какой тип эвакуатора используется, зависит от владельца компании-эвакуатора. Эвакуаторы с брекет-системой, в которых для буксировки используется желток и штифты, – это просто самые современные типы эвакуаторов. Другие эвакуаторы все еще используются сегодня и работают так же хорошо.
Эвакуатор с крюком и цепью работает так же, как эвакуатор с кронштейном.Однако вместо механического стального приспособления, поднимающего автомобиль, грузовик использует прочный крюк, который крепится к днищу автомобиля. Также может потребоваться несколько дополнительных цепей для надежного соединения с эвакуатором. Это эффективный метод, но, как мы уже говорили, некоторым людям не нравится идея, что их автомобиль буксируют детали, находящиеся под ним.
Буксирная платформа
Еще один вид эвакуатора – бортовой. Опять же, его основная функция такая же, как и у любого другого эвакуатора; это просто работает по-другому.В бортовом эвакуаторе используется механическая система, которая наклоняет платформу, как пандус, и автомобиль, которому требуется буксировка, затем маневрирует на платформе.
Колеса автомобиля скреплены проходящими через них цепями, которые крепятся к бортовой платформе. Затем платформа механически опускается обратно в плоское состояние, и автомобиль готов к буксировке.
Плюс бортовых эвакуаторов в том, что они могут буксировать не только автомобиль. Они могут буксировать строительную технику, мотоциклы и многие другие транспортные средства.Однако они могут быть не первым выбором для башни из-за требуемых дополнительных трудозатрат.
Насколько тяжелый эвакуатор?
Вес эвакуатора зависит от того, какие автомобили он предназначен для буксировки. Некоторые грузовики лучше подходят для буксировки обычных автомобилей, таких как седаны и внедорожники, в то время как другие могут быть созданы для буксировки крупных машин или автобусов.
Существует три основных классификации эвакуаторов, и основной характеристикой, определяющей, в какую категорию попадает эвакуатор, является его вес.
- Легкие эвакуаторы весят от 8600 фунтов. И 10 000 фунтов. Эти грузовики могут без проблем перевозить большинство типов автомобилей и могут быть наиболее распространенным типом эвакуатора, который вы можете встретить на дороге в любой день.
- Эвакуаторы средней грузоподъемности весят от 10 001 фунт. И 26000 фунтов. Также довольно стандартные, эти эвакуаторы могут буксировать как обычные автомобили, так и более крупные автомобили или грузовики. Иногда они могут буксировать более мелкие машины.
- Тяжелые эвакуаторы состоят из любого эвакуатора, который весит более 26 000 фунтов.Эти грузовики могут буксировать автомобили, но они часто используются для крупногабаритных транспортных средств, как упоминалось выше, таких как строительная техника, автобусы и любые другие крупногабаритные транспортные средства.
Источник: TOW TRUCKS
Сколько времени нужно, чтобы подключить эвакуатор?
Время, необходимое для подключения эвакуатора, также зависит от типа эвакуатора, аналогично весу эвакуатора. Еще один фактор, влияющий на то, сколько времени потребуется, чтобы подключить эвакуатор, – это количество задействованного персонала по сравнению ссколько грузовик делает сам по себе.
Водитель эвакуатора, который знает, что делает, и может правильно совместить желток с автомобилем, может выполнить свою работу менее чем за минуту. Это причина того, что грузовики с брекет-системой являются такими стандартными. Это безопасная и удобная ставка для обеих сторон.
Эвакуатор с крюком и цепью, вероятно, займет немного больше времени, чтобы подсоединиться к транспортному средству, которое они буксируют. Здесь больше ручного труда. Водитель эвакуатора не может просто поставить крюк на случайную часть буксируемого автомобиля.
Он или она должны найти место под автомобилем, которое сможет выдержать вес автомобиля, когда его тянет эвакуатор. Поиск подходящего места для крепления автомобиля и последующее закрепление автомобиля другими цепями может занять пять минут.
Буксировка с платформой, хотя и является эффективным методом, вероятно, занимает больше всего времени, чтобы подсоединиться к транспортному средству. Однако использование механических средств для подъема и опускания станины требует почти такого же ручного труда, как и установка кронштейнов.
Больше всего времени уходит на медленный наклон кузова, чтобы буксируемое транспортное средство можно было безопасно переместить на грузовик. После этого водитель эвакуатора должен пристегнуть автомобиль к станине цепями или ремнями через каждое колесо транспортного средства.
Разным эвакуаторам требуется разное количество времени для правильного подключения к транспортному средству, которое буксирует водитель грузовика, но, в конце концов, ваше мнение или мнение вашего работодателя о том, какой грузовик лучше всего использовать, будет зависеть от вас. .Некоторые люди согласны с преобладающей зависимостью эвакуаторов с системой кронштейнов, в то время как другие предпочитают методы с крюком и цепью или с платформой.
Должен ли я ехать с эвакуатором?
Многие люди могут оказаться в ситуации, когда может потребоваться эвакуатор, будь то автомобильная авария, нехватка бензина на шоссе, поломка или любая другая неисправность. Если это когда-либо ваша ситуация, вы можете получить услуги эвакуатора через помощь на дороге Mach 1. Крайне важно понимать, что то, что ваша машина или другое транспортное средство, кажется, работает правильно после происшествия, не означает, что водить можно.
Подумайте об этом. Даже автомобили, серьезно поврежденные в автокатастрофе, могут по-прежнему иметь способность двигаться и, теоретически, управлять автомобилем, но это не означает, что полная машина безопасна в эксплуатации.
Если вы не очень разбираетесь в функциональности транспортного средства и оказались в ситуации, когда с вашим транспортным средством происходит что-то необычное, управление им может быть небезопасным, и эвакуатор может быть вашим лучшим выбором. . Если это механическая проблема или замена спущенного колеса, вы можете узнать стоимость эвакуатора и решить, какая услуга вам наиболее удобна.
Связь с буксирной компанией может быть хлопотной, так как она требует оплаты, поиска подходящей компании и времени ожидания. Однако иметь дело со всем этим гораздо безопаснее, чем рисковать жизнью своего автомобиля и собственной жизнью, игнорируя возможную проблему.
Каковы требования, чтобы быть водителем эвакуатора?
Основные требования к водителю эвакуатора относительно просты, как и для любой другой типичной работы. Во-первых, вам должно быть не менее 18 лет, чтобы управлять эвакуатором.В случае найма сотрудника буксирной компании может потребоваться первоначальное подтверждение физических возможностей.
Ничего особенного, но как водителю эвакуатора вам придется довольно часто выполнять легкие подъемные работы, а также уметь работать в разных условиях, будь то жаркий летний день или морозная дождливая ночь. Кроме того, вам, вероятно, придется пройти тест на наркотики.
Во время других частей медицинского осмотра проверяется ваш слух и зрение, чтобы убедиться, что вы сможете безопасно и правильно управлять эвакуатором.Для того, чтобы стать водителем эвакуатора, вам не нужно иметь специальную лицензию на эвакуатор, но вы должны иметь обычные водительские права.
Опять же, как и в любой другой компании, вам придется пройти проверку биографических данных, которая также будет проверять ваши записи о вождении. Буксирные компании не хотят нанимать безрассудного водителя. Если вы соответствуете этим простым критериям, ваш путь к тому, чтобы стать водителем эвакуатора, начался.
В чем разница между эвакуатором и эвакуатором?
Большинство людей может не знать, что эвакуатор технически представляет собой разновидность эвакуатора.Он используется, как вы уже догадались, для затонувших судов, но может также и для обычных буксиров.
Грузовики, буксируемые с двумя оторванными от земли и двумя колесами на грузовике, считаются аварийными. Кронштейны, а также тележки с крюком и цепью – вредители.
Основная спецификация заключается в том, что эвакуаторы лучше подходят для буксировки транспортных средств, которые необходимо более осторожно транспортировать из-за повреждений или отсутствия места для правильной буксировки транспортного средства с помощью другого типа эвакуатора.
Последние мысли
Как работают эвакуаторы, можно разделить на пять основных принципов, которые мы обсуждали выше, хотя большинство эвакуаторов полагаются на систему кронштейнов для выполнения своей работы.
.