Кондитерская мастика | Декорирование выпечки
Кондитерская мастика — это сладкая, удивительно пластичная масса, которая предназначена для обтяжки тортов и лепки съедобных украшений. Основное предназначение этого декоративного материала состоит в том, чтобы придавать готовым изделиями более красивый, праздничный вид, делать их оригинальными и неповторимыми.
В профессиональных руках кондитерская мастика способна превратиться в абсолютно любые украшения, начиная от элементарных листочков, простых цветков, звездочек и заканчивая фантастическими букетами, фигурками персонажей и целыми сюжетами из жизни и любимых мультфильмов. Данный материал позволяет не только преобразить праздничную выпечку, но и скрыть ее некоторые дефекты. Например, небольшие неровности на поверхности торта. С кондитерской мастикой приятно и удобно работать, особенно если использовать готовый продукт.
Преимущества готовой кондитерской мастики
Несмотря на огромное количество рецептов кондитерской мастики, на 100% безотказного не существует.
Все это не имеет никакого отношения к готовой кондитерской мастике, которая благодаря тщательно выверенному и сбалансированному составу имеет стабильно высокое качество и неизменные свойства мягкости и пластичности. Подобный декоративный материал полностью готов к использованию. Вам не нужно тратить время, силы и нервы на готовку. А что может быть лучше, чем просто открыть упаковку и начать творить?
Готовая кондитерская мастика бывает самых различных цветов. И это еще один неоспоримый плюс. Ведь вам не придется искать качественные красители и думать, как получить, какой-нибудь необычный или сложный цвет и оттенок.
Купить кондитерскую мастику сейчас несложно. Достаточно изучить ассортимент интернет-магазина «С. Пудовъ», где вы наверняка найдете именно то, что вам нужно, а также сможете подобрать множество других интересных материалов для декорирования домашней выпечки.
Пищевые красители: часть 1 – мастер-класс для кондитеров
Каждый охотник желает знать, где сидит фазан. С детства знакомая фраза, которая всегда выручает в случае, если забыл последовательность цветового спектра. И если с этим вопросом можно разобраться лишь с помощью шутливого высказывания, то вопрос про пищевые красители также запросто не решить. В чём разница между сухим и жидким красителями? Почему шоколад сворачивается при окрашивании? Чем лучше окрашивать мастику или крем для торта? И это лишь малая часть основных вопросов про пищевые красители. А ведь именно с этим ингредиентом каждый кондитер сталкивается чаще всего! Разберёмся в деталях.
Начнем с классификации. Все пищевые красители можно разделить на несколько групп: сухие, жидкие, гелевые, пищевые блески, спреи, пищевые фломастеры. Помимо разнообразия форм выпуска, красители делятся на две большие (и очень важные!) категории по своей химической основе: водорастворимые и жирорастворимые. О том, к какой из двух категорий относиться тот или иной краситель можно прочесть на упаковке. Если краситель жирорастворимый обычно присутствуют маркировки: choco colour (у производителя FoodColours), слово «Лак» (у российских производителей) и другие подобные. Водорастворимые зачастую не маркируются, поэтому если на упаковке вы не видите специального знака или надписи, то этот краситель точно на водной основе.
Из школьного курса нам всем известно, что разная плотность воды и масла (и продуктов, его содержащих) не позволяет им смешиваться между собой. Одна из самых распространённых кондитерских ошибок,— добавить в шоколад первый подвернувшийся под руку краситель. Конечно, может магически случится и так, что под руку вам попадётся именно нужный краситель, но скорее всего нет. Шоколад свернётся, превратиться в пластилиновую массу и отправится в мусорку.
Сухие красители.
Порошкообразные красители. Чаще всего перед использованием разводятся в воде или водке. Используются для окрашивания бисквитов, кремов и шоколада. В последнем случае краситель не разводится водой, также не забываем про маркировку (oil) на упаковке. Кроме этого, все сухие красители можно использовать в сухом виде в качестве пигмента. С их помощью окрашивают мастику или вафельную бумагу, например, при создании сахарных или вафельных цветов. С помощью сухих красителей нанесённых кистью или губкой можно добиться плавных и естественных переходов. Помимо прочего, сухие красители – важный помощник при приготовлении французского пирожного Макарон. Никакой лишней влаги, равномерное окрашивание и экономичный расход.
Гелевые красители.
Универсальные водорастворимые красители, которые подходят для окрашивания бисквитов, мастики, айсинга, кремов, безе и многого другого. Обладают густой текстурой, насыщенным цветом, хорошей укрывистостью. Гелевые красители — самый необходимый инструмент для создания уникальных тортов. Ведь именно среди них можно найти необходимый оттенок для крема или мастики. Палитра гелевых красителей очень разнообразна.
Жидкие красители.
Менее плотные, текучие красители на водной основе. В меньшей степени подходят для окрашивания кремов и мастики, но с их помощью все же можно окрашивать практически любые смеси. С ними стоит быть немного более аккуратным в работе, так как лишняя влага может разрушить текстуру окрашиваемого продукта. Перестаравшись с жидким красителем при приготовлении капкейков, можно получить нестабильный крем, а мастика может стать чрезмерно мягкой и липнущей. Зато жидкие красители идеально подходят для прямого окрашивания. С их помощью можно рисовать на поверхности торта, пряника и на мастике. Также использование жидких красителей при окрашивании бисквитов (например, для красного бархата) более рациональное и экономичное решение.
Пищевые блески.
Особый вид сухих пищевых красителей с характерными блестящими частичками. Частички эти бывают разной фракции, то есть помола, от этого некоторые пищевые блески выглядят, как сплошная блестящая пыль, а другие состоят из порошка с блестками внутри. Их можно использовать, как в сухом, так и в разведенном с водой или водкой виде. С их помощью любому изделию можно придать блестящий оттенок. Пищевые блески обычно наносятся на поверхность крема, мастики, айсинга, шоколада. Самые популярные оттенки: золото, серебро, медь. Именно эти оттенки незаменимы при создании метализированных тортов. И если в случае с шоколадом пищевой блеск рекомендуют наносить именно в сухом виде, то на крем или мастику в разведанном. В этих случаях блеск будет максимальным, а покрытие равномерным. Также пищевые блески незаменимы при финишном декоре тортов и капкейков,— несколько взмахов сухой кистью уместны к практически любому оформлению.
Спреи.
Помимо традиционных видов красителей особо актуальными становятся красители в виде спреев. Чаще всего используются золотые, серебряные и перламутровые варианты. С помощью спрея можно добиться равномерного металлического цвета. Спреем можно покрыть любую, абсолютно любую поверхность: шоколад, мастику, макарон и, самое главное, крем. Ведь нет больше другого варианта покрыть блеском шапочку капкейка, например.
Пищевые фломастеры.
Красители в форме фломастеров на спиртовой основе незаменимы при работе с пряниками и мастикой , в частности при декоре сахарными фигурками и цветами. С их помощью на слегка подсушенную поверхность сахарной пасты можно нанести небольшие детали, акценты, надписи. Также пищевые фломастеры используются при работе с вафельной бумагой. Например, при разметке листа на лепестки во время создания вафельного цветка.
С любовью, команда Tortomaster и Мария Сухомлина.
Рекомендуемые товары
← Все статьи
Как приготовить мастику для тортов
Мастику используют для декорирования торта и других изделий. Ей можно покрыть готовый торт, поверхность торта благодаря мастике будет иметь мягкие и разнообразные формы.
Украшения из мастики могут превратить простой торт в произведение искусства. Можно сделать всевозможные украшения из мастики: листья, цветы, композиции из цветов, различные фигурки, которыми украшают торт. Порой украшения бывают такими красивыми, что их даже жалко есть!
Мастика на первый взгляд проста в приготовлении, однако с первого раза она может не получиться. Поэтому необходимо набраться терпения и как можно чаще практиковаться, тогда вы научитесь её «чувствовать». Масса должна быть пластичной, как пластилин, но не прилипать к рукам. Для начала лучше экспериментировать с небольшим количеством мастики.
Для того чтобы сделать различные изделия из мастики, можно использовать трафареты или специальные вырубки.
Как приготовить мастику
Мастика готовится из сахарной пудры с добавлением воды, желатина и лимонного сока. Также добавляют глицерин и масло, это делается для того, чтобы мастика сохла не так быстро. Вымешивается сахарная масса минут 15.
Готовую мастику лучше вымешивать на столе, который предварительно посыпали сахарной пудрой, также можно использовать крахмал. Это необходимо делать для предотвращения прилипания мастики к столу и рукам во время работы с ней.
Мастику можно подкрашивать свекольным соком, соком шпината, морковным соком, соком различных ягод или красителями, продающимися в магазине.
Готовую мастику необходимо упаковать в пищевую плёнку, чтобы она не высохла.
Украшать торты мастикой нужно после того, как крем застынет. Лучше, если торт покрыт марципановой массой или поверхность торта состоит из сухого бисквита.
Как покрыть торт мастикой
Для того чтобы покрыть торт мастикой, необходимо поставить его на поворотный круг, так удобнее будет с ним работать. Поверхность стола посыпать сахарной пудрой, затем раскатать мастику до5 ммтолщиной на столе. Раскатанная мастика должна быть шире торта.
Используя скалку, поместить мастику на торт. Руки посыпать крахмалом и разровнять мастику сначала по поверхности торта, так, чтобы она плотно прилегала к нему, затем по бокам. Лишнюю мастику обрезать по основанию торта ножом. Из остатков можно сделать фигурку или иные украшения – листья или цветок.
Интересное о мастичных тортах с экспертом Анной Красовской
Сегодня мастика – один из наиболее популярных продуктов, которыми украшают торт. Однако, отношение к мастике как у кондитеров, так и у заказчиков может быть абсолютно разным.
Нам удалось задать несколько интересных вопросов о мастике мастеру, чьи работы знают во всем мире! Встречайте, Анна Красовская, мастер по работе с мастикой и украшению кондитерских изделий в английской технике.
Очень интересное интервью с Анной об английской технике Вы можете прочитать здесь.
Анна, самый популярный вопрос от клиентов: можно ли есть мастику?
Когда я слышу фразу “Я не люблю мастику, она невкусная“, у меня сразу возникает вопрос, а зачем человек её вообще ел. Несмотря на то, что мастика продукт съедобный, есть её непринято. Она является упаковкой, как коробка, сохраняющая и украшающая торт. Мастика на 90% состоит из сахара, поэтому перебьёт вкус абсолютно любого торта. Вы не почувствуете ни тонкого аромата ванили, ни горьких оттенков шоколада, ни соленой карамели – вам будет просто сладко. Если сам по себе торт не вкусный, это не страшно, но когда речь идёт об авторских начинках, то обидно, что человек лишает себя удовольствия их распробовать.
Восхитительный торт от Анны
Ещё одна причина, по которой не рекомендую есть мастику – это все же упаковка, в ней содержатся красители и она взаимодействует с окружающей средой. Поэтому мастику отделяют от торта и оставляют на тарелке. Многие об этом не знают и задача кондитера рассказать об этих тонкостях своему клиенту.
Торт, украшенный мастичными цветами и фигурками от Анны
Анна, сегодня многие кондитеры часто украшают торты живыми цветами, т. к. украшение сахарными требует больше временных и денежных вложений. Как по Вашему мнению, чем предпочтительнее украшать торт: живыми цветами или сахарными?
Дело в том, что все цветы, которые сейчас можно купить, выращены с помощью химикатов. Это помогает им пережить транспортировку и долгое время оставаться свежими. Но употреблять их в пищу и украшать ими пищевые продукты категорически запрещено. Поэтому их заменяют сахарными цветами. Кроме того, цветы из сахара не вянут и выдержат любую жару.
Торт, украшенный сахарными цветами от Анны Красовской
Анна, среди Ваших работ есть торты, которые украшены оригинальными мастичными фигурками. Вы можете сказать, что чему-то больше отдаете предпочтение: созданию сахарных цветов или созданию мастичных фигурок? Где необходимо больше фантазии? На создание каких декораций уходит больше времени?
И цветы, и фигурки требуют большого количества времени и мастерства, но не фантазии. Если честно, ни цветы, ни фигурки не могут увлечь меня так, как создание единой концепции торта, разработка нового дизайна. Мастичные декорации – это всего лишь инструмент в создании чего-то более ценного. Самое интересное для меня – ставить перед собой и своей командой невыполнимые цели и добиваться их.
Украшение в виде балерины от Анны
Не просто сделать торт большим, а изящным! Не просто многоярусным, а гармоничным! И именно это самое сложное.
Например, привезти пятидесятикилограмовый торт в Сочи на гала-ужин, организованный Димой Биланом, Яной Рудковской и Натальей Водяновой или создать сладкий парк аттракционов для Лондонской благотворительной ярмарки Fund Fair, организованной фондом Обнаженные сердца – очень сложные и невероятно интересные задачи.
Торт для гала ужина «Не молчи» в Сочи
Анна на благотворительной ярмарке Fund Fair
Следующий вопрос будет интересен для начинающих кондитеров и для клиентов: насколько сильно отличается стоимость тортов, украшенных сахарными цветами и тортов, украшенных мастичными фигурками и композициями?
Цена мастичных тортов в среднем на 40% выше, чем тортов без обтяжки. Это напрямую связано не только с трудозатратами кондитера, но и со стоимостью материалов. Очень многие инструменты, некоторые виды мастики, айсинг и проволоку я заказываю из Великобритании, так как у нас нет качественных аналогов.
Абсолютно разные, но одинаково очаровательные торты от Анны
Что касается трудозатрат, то на хороший мастичный торт кондитеру потребуется в разы больше времени, чем на торт в любой другой технике. На создание цветка уходит от одного до трёх часов. А в торте их могут быть сотни! Соответственно, торт во французской технике может быть создан за 3 часа, а в английской – минимум за 6.
Я не разделяю стоимость фигурок и цветов. Знаю, что некоторые кондитеры отдельно считают каждый элемент. Но я уважаю своего клиента и не хочу его путать, поэтому стоимость у меня фиксированная за килограмм. Благодаря такому подходу клиент сам легко может рассчитать вес и предварительную стоимость торта с учётом своего количества гостей.
Восхитительные сладкие украшения от Анны
Создание сахарных цветов очень трудоемкий процесс. За какое количество времени, в идеале, заказчик должен сделать такой заказ? Как происходит обсуждение таких заказов? Делаете ли Вы эскизы?
Для создания уникального торта требуется как минимум две недели. Мы разрабатываем дизайн, создаём молды и подставки, лепим цветы. Если кондитер делает типовые торты (например, только три вида дизайна), то времени будет уходить меньше, так как цветы и подставки можно подготовить заранее, в межсезонье.
Неповторимый детский торт от Анны
Эскизы иногда помогают, а иногда наоборот мешают при работе. Например, при сборке торта вы видите, что элемент, который должен был смотреться идеально, совсем не подходит. Или вдруг пришла новая идея, а она не согласована с заказчиком. Идеальный вариант – оговаривать заранее стиль, ярусность, цвета и ключевые элементы торта.
Эскиз и результат
Мы еще раз хотим поблагодарить Анну за выделенное время. Советуем Вам прочитать очень интересное интервью об особенностях английской техники декорирования тортов от Анны.
Сахарная мастика
Свойства сахарной мастики
Сколько стоит сахарная мастика ( средняя цена за 1 кг.)?
Москва и Московская обл.
465 р.
Не только опытные кондитеры, но новички-любители наверняка знакомы с сахарной мастикой. Причем первые уже набили руку в работе с этим довольно капризным продуктом, в то время как неопытные кулинары пока еще только приглядываются к этой эластичной массе, интересуясь тонкостями и секретами в обращении с сахарной мастикой.
Тестообразная сахарная масса, после приведения в необходимую консистенцию раскатыванием скалкой или длительным вымешиванием, используется для покрытия тортов и лепки декоративных кондитерских изделий, таких как фигурки и цветы. При желания сахарная мастика окрашивается различными пищевыми красителями или ароматизируется с помощью некоторых вкусовых добавок.
Приступая к работе, сахарную мастику тщательно вымешивают, раскатывают на столе, присыпав пудрой сахарной или крахмалом во избежание прилипания пасты к поверхности и рукам. Ее нельзя выкладывать непосредственно на кондитерский крем – предварительно обязательно покрыть его тонким слоем бисквита или жиросодержащим кремом. После работы мастику хорошенько закрывают пленкой, чтобы она не заветривалась и не высыхала.
Сахарную мастику можно сделать в домашних условиях – благо, рецептов ее приготовления масса. Кто-то предпочитает готовить ее из зефира маршмеллоу, кому-то нравится желатиновая или молочная. Однако существует еще и другой вариант – сегодня без проблем можно приобрести уже готовую мастику. Правда в России этот продукт не изготавливается, в связи с чем купить можно только сахарную мастику иностранного производства. Как правило, паста носит название gum paste или sugar paste, паста сахарная, фондант, паста для моделирования, пластичная или желатиновая масса.
Когда делаются украшения из сахарной мастики, их лучше подсушить на открытом воздухе перед тем как поместить на кондитерское изделие. Вообще порядок изготовления тортов с использование сахарной мастики состоит из нескольких этапов. Вначале заранее лепятся необходимые для украшения фигурки и детали (можно даже за неделю, но главное – хранить их в закрытой емкости). Непосредственное выпекание коржей, их прослойка и обволакивание ганашем или масляным кремом – следующий шаг.
Теперь начиняется самый что ни на есть творческий процесс – раскатывание сахарной мастики для покрытия всей поверхности торта, а также установка на него готовых изделий. Соединяются цветы с мастичной поверхностью и между собой при помощи капельки воды или специального кондитерского клея. Достаточно смахнуть кистью остатки пудры и кулинарный шедевр готов.
Калорийность сахарной мастики 393 кКал
Энергетическая ценность сахарной мастики (Соотношение белков, жиров, углеводов – бжу):
Белки: 0 г. (~0 кКал)
Жиры: 1 г. (~9 кКал)
Углеводы: 96 г. (~384 кКал)
Энергетическое соотношение (б|ж|у): 0%|2%|98%
Рецепты с сахарной мастикой
Пропорции продукта.
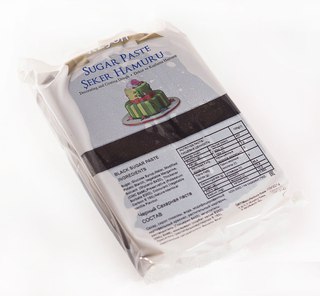
в 1 упаковке 1000 граммов
Аналоги и похожие продукты
Просмотров: 8471
Мастика битумная морозостойкая масляная МБМи
Мастика битумно масляная морозостойкая изоляционная относится к масляно-битумным мастикам, мастичный слой не высыхает, предназначена для антикоррозионной защиты бетонных, металлических, деревянных и других конструкций, в том числе трубопроводов. Цена на масляно битумную мастику в нашей компании минимальна, т.к. мы являемся ее производителями и можем предоставить серьезные скидки оптовикам. Важно! Применяется как составной компонент гидроизоляции и антикоррозионной защиты, это значит, что мастичный слой должен быть закрыт изолирующим материалом от грунтовых вод и других внешних воздействий природных осадков и нагрева. Не является клеящим составом, полностью не высыхает, не применяется в жилых помещениях.
Представляет собой однородную массу чёрно-коричневого цвета полужидкой консистенции. Состоит из битумов и масленых растворителей. За счет масленых растворителей мастика легко наносится и лучше впитывается в бетонные и др. конструкции. Сохраняет эластичную структуру после высыхания. Мастика битумно-масляная – морозостойкая, нетвердеющая. Для лучшей адгезии, при температуре окружающей среды ниже +5°С может применяться в разогретом состоянии. Не имеет огнеопасный растворитель, и при необходимости может нагреваться с помощью открытого огня. Перед применением необходимо перемешать.
Обратите внимание! Мастика МБМи не является клеящим составом, не применяется на отмостках, открытых кровлях, в жилых помещениях. Мастичный слой должен быть закрыт от солнечных излучений и природных осадков.
Мастику наносят на сухую и очищенную поверхность шпателем, наливом с разравниванием специальными гребками, валиком, шпателем, кистью или способом распыления. Толщина наносимого слоя 1,5 – 2,5 мм. Расход 0,8 кг. – 0,9 кг. на кв.м.
Производитель: ИП Дроздовский В.К., М.О., Пушкинский р-н, д.Талицы.
Основные физико-механические свойства морозостойкой мастики
Наименование показателей | |
---|---|
Теплостойкость в течение 5 ч., °С, не менее | не нормируется |
Прочность сцепления с бетоном, МПа (кгс/см2), не менее | 0,10 (1,0) |
Вязкость по вискозиметру ВЗ-4 при 20 °C, град | 60..100 |
Гибкость на стержне диаметром 10 мм. без образование трещин при температуре, °C | -40 |
Содержание пылевидного наполнителя, % по массе | – |
Отзывы
5/ 5stars
СтройУфа Олег
Обычная масляная мастика, менеджер Василий хорошо консультирует, за что отдельное спасибо.
Изоляционная мастика – Гидроизоляционные материалы BITUMAST Гидроизоляционные материалы BITUMAST
Мастика изоляционная
Для начала разберемся, что же такое битумная мастика. По сути это смесь дёгтя (составленного и отогнанного) или нефтяного битума с минеральным наполнителем. Обычно, чтобы получить мастику, применяют такие вещества, как:
• волокнистые наполнители (минеральная вата, асбест и другие),
• пылевидные наполнители (доломит, измельченный известняк, цемент, мел, золы твердых видов топлива).
Мастика приобретает свои качества твёрдости и теплостойкости благодаря адсорбции масел на своей поверхности. Более того, расход дегтя или битума уменьшается, а волокнистые наполнители повышают прочность конструкции путем армирования материала. Это также увеличивает сопротивление изгибам.
В целом, мастики можно группировать по разным признакам. По видам связующих материалов — есть мастики битумные, битумно-полимерные и битумно-резиновые. Группируют мастики и по способу применения – горячие, подогреваемые предварительно до определенной температуры (160°С), и холодные, которые не нужно подогревать перед применением, но с обязательным условием – температура окружающей среды не должна быть ниже 5°С; некоторые холодные мастики нужно лишь немного нагреть – до 50°С-60°С. И, наверное, самое часто встречающееся деление – по назначению. Назначений у мастик может быть много – от мастик изоляционных, до антикоррозийных, асфальтовых и приклеивающих.
Если целью своей ставить склеивание рулонных материалов, которые будут использоваться для оклеечной гидроизоляции или будут монтированы на многослойные кровельные покрытия, то нужно использовать приклеивающие мастики. Но есть некоторые особенности, в частности, касающиеся битумных кровельных материалов. Например, если склеивать рулоны рубероида или пергамина, то нужно использовать мастику из битума. Еже ли вы кроете крышу менее долговечным материалом, таким как толь или толь-кожа, то применение дегтевых мастик необходимо.
Если нужна штукатурная или литая гидроизоляция или нужен вяжущий материал для изготовления плит, можно использовать мастику изоляционную.
А уже на более серьезных объектах, таких как гидротехнические сооружения, или на заливку гидроизоляционных швов, используют горячие битумно-минеральные мастики. Их делают из того же битума, но уже с примесями минерального наполнителя. Концентрация таких примесей может варьировать от 30% до 64%. Точная концентрация должна соответствовать требованиям тех или иных условий.
Хамаст, или холодная асфальтовая мастика «Bitumast» – масса черного цвета густой консистенции. Состоит она из вяжущего битума и наполнителя из минеральных веществ. Применяется в основном на работах по гидроизоляции асфальта.
Наносить мастику нужно механизированным методом в два слоя, общая толщина должна получиться 10 миллиметров. Процесс схватывания длится больше 1 часа. Если не получается наносить механизированным методом, то прибегнуть к ручному нанесению с использованием гребка или щетки. Если температура в течение 48 часов не сдвинется с отметки в 20°С, то произойдет полное высыхание как раз за этот период. Работать с этим материалом нельзя при температуре окружающей среды ниже 15°С. А если работы происходят в замкнутом пространстве, то необходимо обеспечить приточную вентиляцию помещения. Горячие мастики требуют нагрева до 180°С. Горячая мастика вырабатывается без растворителя, а холодная – с растворителем.
Мастика изоляционная Bitumast – отличный материал, подходящий для разного рода деятельности
Что означает мастика – Определение мастики
Примеры использования слова “mastic”.
Стены покрыты экскрементами, химически подобными выделениям свай, которые образуют мастику для усиления туннеля.
Он держал пест вертикально на столе, жевал свою мастику и растирал свои лекарства в ступке до поздних часов в глубокой осторожности.
Но она полулежала на мягких подушках за решеткой балкона на улице, пила щербет, жевала мастику и разглядывала прохожих.
Он держал венчик для мух и медленно двигал им из стороны в сторону, чтобы удержать мух от мешочков с гвоздикой, мускатным орехом, мастики, и корицы и стаканчиков с лавровым и миртовым маслом.
Я проходил мимо совершенно пустых холстов на мольбертах, холстов, торчащих сзади в нескольких местах колышками, так что листовые поверхности были разбиты на геометрические формы, и я проходил мимо серо-коричнево-зеленых мешковинных форм в рамах, форм, материал которых мог бы различить глаз. узнаю только очень близко – клочки сетки , воткнутые под мастику или клей, железные шпатлевки, резиновые гильзы – но на следующей работе я остановился.
Он держал пест вертикально на столе, жевал свою мастику и растирал свои лекарства в ступке до поздних часов в глубокой осторожности.
Он играет в шашки с митрополитом, они пьют мастику , едят пахлаву и всю ночь сидят вместе, шепча секреты!
Себастьяно смешал мастику и смолу с известью, сварил их вместе, наложил штукатурку мастером, нагретым над огнем.
Асфальтовая промышленность с 1800-х годов до Второй мировой войны
Джон Дэвис
Еще во времена Моисея асфальт использовался бесчисленным количеством способов. Он не только веками использовался в качестве лекарства и защиты от штормов для кораблей, но и раньше использовался в качестве дорожного покрытия. Историки установили, что еще в 1500 году нашей эры инки Перу построили сложную систему автомобильных дорог, некоторые из которых были вымощены по составу, похожему на современный битумный щебень.
В 1800-х годах большие залежи асфальта были обнаружены во Франции и Швейцарии, и торговцы из этих стран начали продавать асфальтовые изделия для различных целей.
Одной из значительных находок стало месторождение асфальта Зейссель, обнаруженное в 1735 году в долине Роны во Франции. Асфальт Seyssel продавался во Франции под названием «каменно-асфальтовая мастика» и использовался для покрытия полов, мостов и тротуаров.
В 1829 году асфальтово-мастиковое покрытие, состоящее из смеси 93 процентов асфальта Seyssel и 7 процентов заполнителя, было уложено в качестве пешеходного покрытия в Pont Morand, Lyons, France, а также использовалось для покрытия ступеней.В июне 1835 года на мосту Пон-Рояль в Париже было положено первое мастико-асфальтовое покрытие. Он был сложен из асфальта Зейсселя. Позже, в 1836 году, в Лондоне был введен асфальт Зейссель для строительства пешеходных дорожек.
Самый ранний зарегистрированный случай использования каменного асфальта в США для тротуаров произошел в портике старого здания торговой биржи в Филадельфии в 1838 году. Был использован сейссельский асфальт.
Первая асфальтированная дорога
Первое упоминание об асфальтовой дороге, построенной в 1800-х годах, было из Парижа в Перпиньян, Франция, в 1852 году с использованием современной щебеночной конструкции с каменным асфальтом Валь-де-Траверс.
Месторождение асфальта Валь-де-Траверс было открыто в 1712 году в горах Юра в Швейцарии. Ограниченный сбыт асфальта с месторождения начался в конце 1700-х – начале 1800-х годов.
В 1849 году швейцарский инженер М. Мериан заметил, что фрагменты каменного асфальта, упавшие с тележек, перевозящих асфальт из шахты в Валь-де-Траверс, в летние месяцы сжимались под колесами тележки, образуя грубое асфальтовое покрытие. Наблюдения Мериана привели к строительству участка дороги, уплотненного катком на улице Бержер в Париже.Он находился в хорошем состоянии шестьдесят лет. Первый участок асфальтовой дороги в Лондоне был проложен на Треднидл-стрит возле Финч-лейн в мае 1869 года. Он состоял из каменного асфальта Валь-де-Траверс.
Первые асфальтированные дороги в США
Историки считают, что бельгийский химик Э.Дж. Де Смедту за укладку первой дороги из каменного асфальта в США. В 1870 году он построил небольшую экспериментальную полосу из европейского асфальта напротив мэрии в Ньюарке, штат Нью-Джерси.
Год спустя, в 1871 году, в Вашингтоне, округ Колумбия, были уложены несколько асфальтоподобных тротуаров. Эти тротуары состояли из смеси щебня и песка с каменноугольным пеком и креозотовым маслом. Эти тротуары прослужили более 15 лет. В том же 1871 году небольшой участок асфальтового покрытия был проложен в Бэттери-парке в Нью-Йорке. Затем, в 1872 году, на Юнион-сквер был проложен более крупный участок, состоящий из каменного асфальта Валь-де-Траверс.
Первый асфальт на озере Тринидад тротуар в U.С.
Первое листовое асфальтовое покрытие, состоящее из асфальта озера Тринидад, уложенного в США, было на Пенсильвания-авеню в Вашингтоне, округ Колумбия, в 1876 году. Асфальт Валь-де-Траверс использовался от здания Капитолия до Шестой улицы. Остальная часть тротуара была покрыта асфальтом озера Тринидад. Пешеходы и автомобилисты сочли каменный асфальт слишком скользким, но асфальтовый участок на озере Тринидад имел сопротивление скольжению и был признан успешным.
Разработка асфальта Bermudez в Венесуэле началась в 1891 году компанией New York-Bermudez и впоследствии была передана компании Barber Asphalt Paving Company.Асфальт Bermudez впервые был использован в Детройте, штат Мичиган, в 1892 году, а в следующем году был использован для тротуаров в Вашингтоне, округ Колумбия.
Консервация грунтовых, песчаных и гравийных дорог
До 1890-х годов дорожные строители полагались на камень, гравий и песок при строительстве дорог. Дороги были стабилизированы за счет добавления воды, которая могла бы поддерживать движение на конной тяге.Когда автомобили выезжают на дорогу, грязь и пыль становятся серьезными проблемами.
К 1904 году по существующим дорогам страны использовалось более 55 000 автомобилей, а к 1910 году количество грузовиков и автомобилей возросло почти до 470 000. США внезапно столкнулись с серьезной проблемой – сохранением хороших необработанных грунтовых и гравийных дорог. Главный вопрос для дорожных инженеров был: «Как построить дорогу, которая выдержит экстремальный износ грузовиков и автомобилей?»
Дорожные масла и пропитывающий щебень оказались ответом.Они были самым эффективным средством защиты от пыли и разрушений. Дорожные инженеры начали экспериментировать со смешиванием асфальта и тяжелых дорожных масел с заполнителями различных размеров.
«Топика Микс» использовал камень максимального размера 1/2 дюйма и открыл поле для асфальтовых смесей, чтобы обеспечить покрытие для первых междугородних магистралей. С успехом Topeka Mix и криком путешественников по стране, асфальтовая промышленность осознала, что ей нужен единый голос, чтобы представлять все компании, производящие асфальт, – голос, объясняющий и защищающий их продукт, и голос, с которым можно было бы тесно сотрудничать. пользовательские агентства.
В результате этой потребности одиннадцать асфальтовых компаний собрались в клубе Union League в Нью-Йорке в мае 1919 года, чтобы сформировать Асфальтовую ассоциацию, позже названную Институтом асфальта.
Стабилизация поставок из фермы на рынок Дороги
По мере увеличения автомобильного движения возрастал спрос на обработку асфальтовых поверхностей, щебень для проникновения, листовой асфальт и различные асфальтовые смеси. В начале 1920-х годов на уровне штата, округа и города была большая потребность в информации о правильном использовании асфальта для различных типов строительства дорог и улиц.
К концу 1920-х годов Институт асфальта и Федерация американских фермерских бюро объединились в общенациональную кампанию по информированию американского народа о преимуществах модернизации национальных дорог между фермами и рынками с использованием местных заполнителей и обрезного асфальта для стабилизации дороги. дороги.
Асфальт во время депрессии лет
Годы депрессии породили множество проблем, но также породили масштабную программу общественных работ, включая строительство дорог и аэродромов. Нефтяная промышленность разрабатывала дорожные масла, асфальтобетонные и эмульгированные асфальты, которые удовлетворяли потребности страны в мощении основных и второстепенных дорог.
За десятилетие 1930-х годов количество недорогих дорог с асфальтовым покрытием увеличилось с 50 000 до 210 000. В то же время использование жидких битумов увеличилось с 500 000 до 1 800 000 тонн в год.
Ассоциация гражданской авиации (CAA) также была основана в 1930-х годах. Он инициировал обширную программу строительства аэропорта и попросил Институт асфальта провести школы по асфальтированию для сотрудников CAA.Строительство улучшенных дорог и аэродромов больше, чем какое-либо другое достижение, положило начало развитию индустрии грузовых и авиаперевозок в США.
С 1931 по 1937 год использование обрезного асфальта значительно расширилось. Он был экономичным и обеспечивал быстрый ремонт, необходимый в 1930-е годы. В годы депрессии производство почти каждого товара резко сократилось, за исключением сокращения объемов производства асфальта. Между 1929 и 1936 годами общее потребление дорожных масел и асфальтобетонных изделий увеличилось на 160 процентов, в то время как общее использование асфальтовых вяжущих для дорожного строительства существенно снизилось.
Растворители и эмульсии – дорожные спасатели
Экономика была девизом во время депрессии, и почти во всех штатах были приняты менее дорогостоящие виды дорожного строительства. Дорожные инженеры определили жидкий асфальт в качестве поверхностного покрытия и асфальтосодержащие вяжущие для пенетрации щебня.
В 1931 году Пенсильвания начала строительство недорогих дорог Пинчот по цене 6000 долларов за милю. В течение многих лет Пенсильвания использовала гудрон для нанесения на свои дороги.Инженеры государственных дорог не думали всерьез об использовании асфальта, потому что они очень мало знали об этом продукте. Институт асфальта обратился с просьбой о встрече с секретарем автодорог Пенсильвании Сэмюэлем Льюисом, чтобы объяснить достоинства укороченного асфальта. Президент Института асфальта Бернард Грей объяснил способность обрезанного асфальта обрабатывать дороги Пенсильвании и заверил Льюиса, что асфальт может быть поставлен по значительно более низкой цене.
Заявки были запрошены как на гудрон, так и на асфальт.Разница в цене была настолько разительной, что Льюис быстро решил отдать весь контракт на асфальт. В том же 1932 году производители асфальта отправили приблизительно 30 000 000 галлонов обрезного асфальта в штат Пенсильвания. Штат построил 4900 миль асфальтовых дорог, на которых было занято более 48000 дорожных рабочих.
Матовое покрытие дорог Флориды, асфальтовое покрытие гравийных дорог в Мичигане и Висконсине, грунтовка в Северной Каролине и масляный мат, использованный на более чем 400 милях дорог в Канзасе, были примерами того, насколько широко использовался асфальт. .Нанесение покрытий в Техасе и Оклахоме, а также использование песчано-гравийного асфальта в Массачусетсе, Нью-Гэмпшире и Лонг-Айленде были примерами диапазона и разнообразия асфальта для недорогих дорог по всей стране.
Асфальт для дамб, причалов, каналов и водохранилищ
В 1936 году инженерный корпус армии США обратился в Институт асфальта с просьбой разработать асфальтобетонную смесь с местным песком и лессовым наполнителем, чтобы стабилизировать большие пустоты на пристани Галвестона, штат Техас, и сделать их непроницаемыми.Смесь выливалась в массу и вибрировала в пустотах причала, что стабилизировало пристань и останавливало дальнейшее движение крупных камней. В результате стабилизации было восстановлено много акров пригодной земли.
Необходимость экономии воды на западе заставила Бюро мелиорации искать способы уменьшить просачивание воды из оросительных каналов. Уровень просачивания от 16 до 18 процентов и до 48 процентов убедил бюро обратиться в Институт асфальта с просьбой изучить возможность использования асфальтовых покрытий для предотвращения потери воды.
Разработаны четыре типа лайнеров и фильтрационных емкостей. Они включали заглубленные мембраны, покрытия из горячего асфальта, сборный асфальт и нижние уплотнения. Каждый из четырех был успешно использован – с укладкой более 7 миллионов ярдов засыпанной асфальтовой мембраной.
Вторая мировая война
Хотя начало Второй мировой войны в 1939 году изменило экономику США с депрессивного состояния на быстро развивающуюся, планы строительства и обслуживания новых дорог были отложены.Тысячи миль дорог содержались в минимальном состоянии или совсем не содержались с 1941 по 1945 годы. Производство частных автомобилей было остановлено в 1942 году, а бензин был строго нормирован.
Начиная с 1942 года инженерный корпус армии США стал отвечать за все военные работы по укладке дорожных покрытий. Корпус обратился в Институт асфальта с просьбой обучить своих инженеров строительству асфальта, а также правильному строительству и обслуживанию аэродромов большой грузоподъемности. Когда война закончилась, эти военные инженеры вернулись на работу в частные транспортные агентства и государственные дорожные департаменты.
Перед войной Корпус предполагал, что большинство военных самолетов будут действовать с дерновых полей. Но в 1940 году, когда с конвейера сходили колеса весом 37000 фунтов, Корпус понял, что дерновых аэродромов недостаточно. В то время ни Корпус, ни какое-либо другое государственное учреждение не имели методов расчета толщины покрытия для шоссе, взлетно-посадочных полос или любого другого покрытия, которое требовало колесных нагрузок более 12 500 фунтов.
Бомбардировщик B-29 полной массой 140 000 фунтов также находился в стадии разработки.Корпус обратился в Институт асфальта с просьбой предоставить экспертные знания о каменных и других асфальтовых материалах для мощных дорожных покрытий.
К концу войны в 1944 году в США и по всему миру было построено 1800 командных пунктов и 2200 промышленных объектов с использованием асфальта. Машины для укладки асфальта, которые были разработаны для укладки дорожных покрытий в сельской местности в США, хорошо зарекомендовали себя в военных целях. По мощности, универсальности и мобильности эти машины превосходили возможности как вражеской, так и союзной техники.А скорость, с которой были построены взлетно-посадочные полосы с асфальтовым покрытием, дала США и их союзникам стратегическое и материально-техническое преимущество для победы в войне.
Лабораторная оценка характеристик каменно-мастичного асфальта в качестве поверхности взлетно-посадочной полосы без канавок
Реферат
Многие аэропорты покрыты канавками из плотного отсортированного асфальта, спроектированного Маршаллом. Нарезание канавок требуется для удовлетворения нормативных требований к сопротивлению скольжению воздушного судна, но при этом возникает риск повреждения, связанного с канавками, например, закрытие канавки.Следовательно, аэропорты ищут вариант поверхности взлетно-посадочной полосы без бороздок, который по своим характеристикам аналогичен плотному отсортированному асфальту, но позволяет избежать образования бороздок. Каменно-мастичный асфальт является наиболее жизнеспособным решением для покрытия взлетно-посадочных полос без бороздок и используется на взлетно-посадочных полосах в Европе и Китае. Однако, прежде чем он будет принят в качестве поверхности взлетно-посадочной полосы без канавок в Австралии, каменно-мастичный асфальт должен соответствовать нормативным требованиям к сопротивлению скольжению воздушных судов на взлетно-посадочной полосе, а в остальном работать аналогично типичным плотным асфальтовым смесям для покрытия взлетно-посадочной полосы, включая сопротивление деформации, сопротивление усталостному растрескиванию. и долговечность.На основании лабораторных испытаний, связанных с эксплуатационными характеристиками, было установлено, что смеси каменно-мастичного асфальта размером 10 и 14 мм, полученные из четырех различных источников заполнителя, в целом соответствуют требованиям к характеристикам асфальта в аэропорту. Было обнаружено, что 14-миллиметровая смесь работает лучше, чем 10-миллиметровая смесь, особенно в отношении макротекстуры поверхности и сопротивления деформации. Был сделан вывод о том, что в будущем аэропортам следует рассматривать каменно-мастичный асфальт размером 14 мм в качестве нерезаной поверхности взлетно-посадочной полосы.
Ключевые слова: взлетно-посадочная полоса, асфальт, нерезной, каменно-мастичный, каменно-мастичный асфальт (SMA)
1.Введение
В Австралии и некоторых других странах взлетно-посадочные полосы обычно покрываются рифленым плотным отсортированным асфальтом (DGA), разработанным Маршаллом. Прорезание канавок требуется для обеспечения отвода воды с взлетно-посадочной полосы во время влажных погодных явлений, а также для выполнения нормативных требований, установленных Международным управлением гражданской авиации (ИКАО) в отношении сопротивления скольжению воздушных судов, которые в Австралии установлены Управлением безопасности гражданской авиации (CASA). [1]. Закрытие бороздок – это повреждение поверхности ВПП, которое препятствует дренажной способности поверхности ВПП [2] и снижает характеристики трения поверхности покрытия во время влажной погоды, увеличивая вероятность аквапланирования [3].Кроме того, когда происходит закрытие канавки, затраты на исправление значительны, как и влияние на эксплуатационную способность взлетно-посадочной полосы.
Существуют альтернативы DGA с канавками, которые используются в некоторых округах для покрытия взлетно-посадочных полос. Из этих материалов обычно используется каменно-мастичный асфальт (SMA) из-за его высокой устойчивости к колееобразованию и крупной макротекстуры, исключающей необходимость в нарезании канавок [4]. SMA используется на австралийских дорогах в качестве покрытия премиум-класса для интенсивного движения. Однако использование SMA на тротуарах австралийских аэропортов ограничено.Операторам австралийских аэропортов не хватает уверенности, необходимой для использования SMA, потому что этот асфальтовый поверхностный материал не был переведен в спецификации австралийского аэропорта, и его характеристики не были утверждены как материал для покрытия австралийского аэропорта. Чтобы подтвердить SMA в качестве подходящего альтернативного покрытия взлетно-посадочной полосы, оно должно соответствовать опубликованным и установленным требованиям к характеристикам асфальта в аэропорту. То есть производительность SMA без канавок должна быть не хуже, чем у сопоставимого DGA с канавками. К эксплуатационным требованиям относятся сопротивление деформации и сопротивление разрушению, а также долговечность смеси [5].Кроме того, чтобы избежать образования канавок, SMA также должен соответствовать нормативным требованиям к сопротивлению скольжению самолета, включая трение и текстуру поверхности.
Это исследование оценило лабораторные характеристики SMA как поверхности взлетно-посадочной полосы без бороздок. Во-первых, обсуждаются требования к характеристикам, ожидаемые от курсов износа ВПП, с упором на сопротивление скольжению и текстуру поверхности. Затем описывается процесс оценки SMA на соответствие этим требованиям. Наконец, представлены и обсуждаются результаты лабораторной оценки семи смесей SMA, чтобы определить пригодность SMA в качестве поверхности взлетно-посадочной полосы без канавок.Хотя данное исследование сосредоточено на австралийском контексте и использует австралийские методы испытаний, оно также актуально для Великобритании, Соединенных Штатов Америки (США), Ближнего Востока и других стран, которые обычно используют DGA с бороздками для покрытия взлетно-посадочной полосы.
2. Справочная информация
2.1. Асфальт для аэропортов
В Австралии, США и Великобритании DGA, разработанный Маршаллом, является преобладающим материалом для покрытия гибких герметичных покрытий самолетов [2]. Метод расчета смеси Маршалла был разработан Министерством обороны США в период между Второй мировой войной и до конца 1950-х годов для разработки и контроля асфальтобетонных смесей [6].Метод Маршалла включает уплотнение лабораторного образца с помощью заданного количества ударов стандартного молотка (Маршалла), предназначенного для моделирования ожидаемых условий движения в полевых условиях. Затем выбирается оптимальное содержание битумного вяжущего на основе измеренных в лаборатории свойств, известных как стабильность Маршалла и потока Маршалла, а также удельного веса всей смеси, процента пустот в общей смеси и процента пустот (в агрегат), заполненный связующим.
В Австралии для DGA аэропорта, разработанного Маршаллом размером 14 мм, обычно требуется 13–17% (по объему) пустот в минеральном заполнителе (VMA) и содержание пустот в воздухе 3.5–4,5% [7]. Обычно для этого требуется содержание битумного вяжущего 5,4–5,8% (по массе) [8].
2.2. Требования к характеристикам
Традиционно асфальт для аэродромов определялся на основе предписаний или рецептов [8]. Эти требования направлены на достижение целевой градации агрегатов, свойств Маршалла и объемных свойств образцов, приготовленных с использованием метода Маршалла. Однако с появлением метода Маршалла самолеты стали тяжелее и имели значительно более высокое давление в шинах.Наряду с свидетельствами снижения качества вяжущего в Австралии [9], некоторые асфальтовые покрытия в аэропортах, которые соответствовали предписывающим требованиям, не смогли работать так, как ожидалось в полевых условиях [2].
Снижение доверия к традиционной спецификации, основанной на предписаниях, привело к разработке спецификации асфальта для австралийских аэропортов, связанной с характеристиками [8]. Эта спецификация, относящаяся к характеристикам, была впервые выпущена в феврале 2018 года и фокусируется на четырех основных физических требованиях, направленных на защиту поверхности дорожного покрытия от обычных повреждений.В технических условиях, связанных с эксплуатационными характеристиками, используются стандартизированные тесты, позволяющие оценить каждое из требований к физическим характеристикам при разработке смеси [7]. Испытания, ориентированные на эксплуатационные характеристики, обеспечивают уверенность и объективные доказательства того, что смесь может работать в полевых условиях, как ожидается, до начала любого укладки асфальта. подробно описывает требования к рабочим характеристикам, а также стандартные тесты, используемые в спецификации, относящейся к рабочим характеристикам DGA австралийского аэропорта [7]. Показательные испытания в рамках спецификации обеспечивают основу для оценки любой альтернативной (для DGA) асфальтовой смеси или типа.То есть, если альтернативный тип асфальта удовлетворяет требованиям к характеристикам, указанным в спецификации, он теоретически считается пригодным для использования в качестве покрытия взлетно-посадочной полосы.
Таблица 1
Требования к характеристикам и стандартные испытания асфальта для аэропортов [2].
Требование | Защищает от | Стандартное лабораторное испытание |
---|---|---|
Сопротивление деформации | Закрытие канавки Колебание Срезание / толкание | Угол поворота колеса 2891 новозеландский доллар.2.2) |
Устойчивость к излому | Растрескивание сверху вниз Усталостное растрескивание | Усталостная долговечность (AG: PT / T274) |
Прочность | Рыхлый материал, образующийся в дорожном покрытии Устойчивость к повреждению от влаги | 902 : PT / T236) |
Поверхностное трение и текстура | Сопротивление скольжению Требование соответствия | – |
2.3. Сопротивление скольжению и обработка канавок
Важно отметить, что это не включает никаких испытаний на трение поверхности или текстуру. Это связано с тем, что DGA размером 14 мм имеет недостаточную текстуру поверхности для соответствия нормативным требованиям, а также потому, что испытания на трение поверхности могут быть надежно выполнены только в полевых условиях после завершения строительства. Следовательно, во время разработки смеси испытания, связанные с эксплуатационными характеристиками, не назначаются. Тем не менее, сопротивление скольжению по-прежнему важно, поскольку австралийские правила, известные как Руководство по стандартам 139 (MOS 139), требуют, чтобы каждая взлетно-посадочная полоса, независимо от размера, удовлетворяла по крайней мере одному из следующих требований [1]:
1- мм текстуры поверхности, или;
минимальных уровней трения, измеренных оборудованием для измерения трения непрерывного действия (CFME).
Поверхности DGA в аэропорту не соответствуют требованиям 1 мм и обычно имеют текстуру поверхности 0,4–0,6 мм [10]. Кроме того, начальное трение смачиваемой поверхности DGA, измеренное с помощью CFME, может быть незначительным по сравнению с нормативными значениями [11]. Следовательно, чтобы соответствовать нормативным требованиям к сопротивлению скольжению и снизить риск аквапланирования во время влажной погоды, поверхности взлетно-посадочной полосы DGA обычно имеют канавки, что увеличивает измеренные CFME уровни трения до значений, превышающих требуемые значения.
Обработка бороздок на поверхности взлетно-посадочной полосы является дорогостоящей, разрушительной, усложняет уход за дорожным покрытием и создает риск повреждения, связанного с бороздками. Закрытие канавок является одним из наиболее часто регистрируемых повреждений асфальтового покрытия в аэропортах в жарком климате и влияет на способность покрытия отводить воду с поверхности из-за уменьшения объема канавок [2]. Ремонт канавок повторной распиловкой невозможен, и единственное решение – удалить замкнутые канавки, заменить их новым асфальтом и проточить новую поверхность [12].Этот процесс не только дорогостоящий, но и влияет на работу аэропорта во время ремонтных работ. Следовательно, аэропортам нужна альтернативная асфальтовая смесь, которая обеспечивает требования к сопротивлению скольжению без необходимости нарезания канавок. Из доступных альтернатив SMA, вероятно, будет наиболее подходящей [5]. Однако для того, чтобы SMA без канавок было признано подходящей поверхностью взлетно-посадочной полосы, оно должно иметь лабораторные характеристики, сравнимые с DGA в аэропорту, а также иметь текстуру поверхности более 1 мм и / или уровни поверхностного трения выше нормативных минимумов.
2.4. Каменно-мастичный асфальт в качестве альтернативного покрытия
SMA был первоначально разработан в Германии в 1960-х годах. Цель заключалась в том, чтобы уменьшить нагрузку на дорожки износа асфальта, вызванные шипованными зимними шинами [13]. Как и все асфальтовые смеси, SMA состоит из трех частей:
Каркас крупного заполнителя состоит из заполнителя крупнее, чем так называемое сито с пределом прочности (4,75 мм для смесей размером 10–14 мм), и обеспечивает высокую устойчивость к деформации благодаря до контакта камня с камнем ().В то же время высокое содержание связующего и мастики (наполнителя, мелочи и связующего) приводит к получению прочной и устойчивой к усталости смеси. Однако более высокое содержание связующего также создает риск утечки связующего во время производства, транспортировки и укладки. Для уменьшения стекания связующего вещества смеси SMA обычно включают стабилизаторы или ингибиторы дренажа, обычно в форме целлюлозных волокон.
Образцы керна ( a ) плотного гранулированного асфальта (DGA) и ( b ) каменно-мастичного асфальта (SMA).
Критически важным для использования SMA в качестве поверхности взлетно-посадочной полосы без бороздок является макротекстура поверхности. Из-за своей градуированной природы смеси SMA с максимальным размером заполнителя более 10 мм обычно имеют глубину текстуры более 1 мм [14,15,16], что удовлетворяет требованиям ИКАО и CASA к сопротивлению скольжению на взлетно-посадочных полосах.
Несмотря на ограниченное использование в Австралии, SMA использовалась в качестве покрытия взлетно-посадочной полосы в Европе и Китае, а наземные испытания также проводились в Южной Африке и США [17,18].Норвегия использовала SMA в качестве поверхности взлетно-посадочной полосы на более чем 15 взлетно-посадочных полосах с 1992 года [18], включая западную взлетно-посадочную полосу международного аэропорта Осло, поверхность которой была заменена на SMA размером 11 мм в 2015 году [19]. Германия также использовала SMA размером 11 мм для покрытия взлетно-посадочных полос в аэропорту Гамбурга и на базе ВВС Шпангдалем [17], а также три взлетно-посадочные полосы, покрытые SMA в аэропорту Франкфурта. Другие европейские страны, которые использовали SMA в качестве покрытия взлетно-посадочной полосы, включают Испанию, Великобританию, Италию, Австрию, Данию и Швецию. Китай, однако, является мировым лидером в использовании SMA на аэродромах с более чем 40 аэропортами, включая Пекин и Шанхай, покрытых смесями размером 13 или 16 мм [20].
Успешное использование SMA в качестве покрытия взлетно-посадочной полосы в Европе и Китае, а также его повседневное использование на австралийских дорогах показало, что SMA, вероятно, подходит в качестве покрытия взлетно-посадочной полосы без грунтовки в Австралии. Однако для того, чтобы SMA была принята в аэропортах Австралии, особенно для покрытия взлетно-посадочной полосы, она должна быть оценена на соответствие лабораторным требованиям к характеристикам асфальта взлетно-посадочной полосы аэропорта, а также нормативным требованиям к трению и текстуре поверхности. Также должны быть продемонстрированы требования к сливу связующего.
2,5. Требования к асфальтовому покрытию взлетно-посадочной полосы
В 2017 году в Австралии были разработаны требования к характеристикам DGA, используемого в качестве покрытия для покрытия аэропорта [8]. Впоследствии была разработана спецификация, связанная с производительностью [7]. Спецификация в значительной степени сохраняет традиционные объемные требования DGA, но позволяет разработчику смеси выбрать или разработать любое битумное вяжущее для достижения заданных эксплуатационных свойств (). В 2019 году спецификация DGA, относящаяся к характеристикам австралийского аэропорта, была расширена и теперь включает требования SMA [14].Включение SMA в спецификацию потребовало:
незначительных изменений требований к совокупным свойствам для надежного производства SMA;
добавление требований к объемному составу SMA для расчета смеси;
удаление и корректировка несоответствующих методов испытаний DGA;
добавление объемной текстуры поверхности и испытаний стекания связующего в конструкцию смеси SMA, и;
добавление тестирования и составления отчетов о текстуре поверхности во время строительства.
Таблица 2
Требования к асфальту в аэропорту, связанные с эксплуатационными характеристиками [7].
Свойство испытаний | Метод испытаний | Требование |
---|---|---|
Коэффициент непрямого растяжения (TSR) | AG: PT / T232 | Не менее 80% | AG: PT / T231 | Не более 2,0 мм |
Усталостная долговечность (при 20 ° C и 200 мкм) | AG: PT / T274 | Не менее 500000 циклов до 50% от начальной жесткости при изгибе |
Потери частиц | AG: PT / T236 | Не более 15% |
Единственным изменением в агрегатных свойствах было уменьшение максимально допустимого процента некубических формованные частицы грубого заполнителя, измеренные как индекс лещадности.Два объемных состава SMA были определены как жизнеспособные: один основан на требованиях аэропорта Германии с номинальным максимальным размером заполнителя 10 мм, а другой – в соответствии с требованиями аэропорта Китая с номинальным максимальным размером заполнителя 14 мм [14]. Агрегированные градации сравниваются, а другие объемные свойства находятся в.
Сравнение пределов градации SMA-10 и SMA-14.
Таблица 3
SMA дополнительные объемные и связанные требования [14].
Свойство | Метод испытаний | SMA-10 | SMA-14 |
---|---|---|---|
Содержание связующего (% по массе) | AS / NZS 289.1.3 | ≥6,1 902 | |
Воздушные пустоты по Маршаллу (% по объему) | AS / NZS 2891,8 AS / NZS 2891.9.2 AS / NZS 289.1.7.1 | 2,0–4,0 | 3,0–5,0 |
Образцы, подготовленные Marshall обычно используются как для DGA, так и для SMA в Австралии.Однако 75 ударов, обычно используемых для DGA в аэропорту, представляют риск раздавливания агрегатов при применении к SMA, поэтому подготовка проб по Маршаллу была сокращена до 50 ударов, что соответствует австралийскому SMA, предназначенному для дорожных применений. Более того, плотность воздушных пустот в отказе, обычно выполняемая в соответствии с AS 2891.2.2, не проверяется на SMA для дорожных приложений в Австралии, поэтому это требование было снято для SMA аэропорта. Текстуру поверхности измеряли с помощью объемного песчаного пятна на плитах, подготовленных для движения колеса, и измеряли стекание связующего при предполагаемой максимальной температуре производства асфальта, как указано в.
Таблица 4
Дополнительные требования к производительности SMA [14].
Свойство | Метод испытаний | SMA-10 | SMA-14 |
---|---|---|---|
Утечка вяжущего вниз (% по массе) | AG: PT / T235 | 902,15||
Текстура поверхности (мм) | AG: PT / T250 | ≥1 мм | ≥1 мм |
Несмотря на эти изменения, требования к характеристикам (), допуски при производстве асфальта и процессы строительства поверхности, полевой воздух Пределы содержания пустот и общие требования к качеству были сохранены для SMA такими же, как и для DGA.Для целей разработки лабораторных смесей смеси были произведены в соответствии с требованиями, а характеристики оценивались на основе требований и.
3. Материалы и методы
Для оценки SMA как варианта покрытия взлетно-посадочной полосы без канавок, были выбраны различные источники грубого заполнителя, которые будут репрезентативными для различных источников, доступных в Австралии. Каждая смесь SMA была протестирована в лаборатории на соответствие требованиям к характеристикам, установленным для асфальта в аэропортах в Австралии, а также к текстуре поверхности и стеканию связующего.
3.1. Методы
Сначала смеси были разработаны теоретически, а затем произведены, чтобы подтвердить выполнение требований к объему для градации, содержания связующего и воздушных пустот (и). Во-вторых, были проверены требования к сливу связующего (). Наконец, были подготовлены образцы для испытаний производительности (и текстуры поверхности от). Поскольку в некоторые смеси были внесены некоторые корректировки, процесс был частично повторяющимся. Например, некоторые смеси изначально не удовлетворяли требованиям по сливу связующего.Были добавлены дополнительные волокна, и испытание было повторено, чтобы подтвердить, что требование было выполнено, до того, как начались другие испытания производительности. Кроме того, были измерены некоторые вторичные параметры испытаний, такие как скорость колейности колесных колей и начальный модуль усталостных балок. Основные и специфические для Австралии лабораторные тесты производительности описаны ниже.
3.1.1. Испытание на отслеживание колес
Австралия использует устройство отслеживания колес Copper для определения сопротивления деформации асфальта (AG: PT / T231), которое включает уплотнение двух образцов размером 300 мм × 300 мм × 50 мм до 5 ± 1% воздушных пустот с помощью лабораторного уплотнителя, описанного в AG. : PT / T220 [21].Затем образцы перемещаются колесом с вертикальной нагрузкой 700 ± 20 Н за 10 000 проходов [22]. Выполняется несколько измерений глубины, и записывается средняя глубина отслеживания. Помимо глубины колеи, показатель глубины колеи регистрируется как наклон глубины колеи на проходах от 4000 до 10 000 проходов (мм / кмпасс). Глубина колеи является хорошим индикатором вторичной ползучести, ожидаемой после начальной деформации, вызванной ранним перемещением.
Для контекста Austroads [23] рекомендует, чтобы окончательная глубина колеи была меньше 3.5 мм при стандартной температуре 60 ° C указывает на лучшие характеристики асфальта при использовании AG: PT / T231 для австралийских дорог. Что касается асфальта в австралийском аэропорту, надлежащим образом работающий DGA должен иметь глубину колеи не более 2 мм при температуре 65 ° C. Более высокая температура испытаний характерна для поверхностей взлетно-посадочных полос с бороздками, поскольку рифленая (только верхняя 6 мм) часть поверхности подвергается воздействию более высоких температур, чем середина поверхностного слоя, что более применимо к колейности и толчкам на поверхности [7].
3.1.2. Усталостная долговечность
В соответствии с AG: PT / T274 [24] для оценки усталости асфальта при промежуточных температурах используется четырехточечный изгиб при повторной нагрузке при 20 ° C. С помощью этого метода измеряется начальная жесткость прямоугольных балок с размерами 390 мм × 50 мм × 63,5 мм, подготовленных с содержанием воздушных пустот 5 ± 0,5%. Образцы подвергаются синусоидальной нагрузке при контролируемом уровне максимальной величины деформации 200 µε. Усталостная долговечность определяется как количество циклов до тех пор, пока измеренная жесткость не снизится до 50% от начальной жесткости, хотя обычно испытание прекращают после 500000 циклов нагружения и записывают жесткость в это время в процентах от начальное значение жесткости.Снижение жесткости на 50% (или менее) считается хорошим сопротивлением усталости, и большинство асфальтовых смесей для аэропортов Австралии, которые обычно содержат 5,4–5,8% сильно модифицированного эластомерного связующего, обычно легко удовлетворяют этому требованию [25].
3.1.3. Потери частиц
Австралия использует испытание на потери Кантабро, которое измеряет потерю массы образца во время абразивного кондиционирования либо вращающегося, либо уплотненного по Маршаллу образцов асфальта, согласно AG: PT / T236 [26]. Потери Кантабро обычно используются для смесей с открытым градиентом трения из-за того, что прочность смеси зависит от когезии связующего и адгезии к частицам заполнителя.Образцы взвешивают до и после воздействия 300 оборотов в абразивном барабане Лос-Анджелеса. Считается, что потеря массы не более 15% от исходной массы образца свидетельствует о хорошей устойчивости к потере абразивных частиц. Однако тест на потери Cantabro оценивает только потерю частиц из-за истирания и приложения механической энергии, когда образец асфальта ударяется о стенки барабана. В асфальте для аэропортов истирание и расслоение чаще всего вызвано ухудшением качества связующего из-за окисления, разложением заполнителя из-за воздействия влаги и общего атмосферного воздействия [27].Испытание на потерю частиц не учитывает это, и требуется ускоренное лабораторное испытание асфальтовой мастики на выветривание и старение [28]. Однако в настоящее время более подходящего теста нет, и для этого исследования использовался тест на потерю частиц. Было установлено, что DGA в аэропорту, полученный с использованием модифицированного полимером связующего, обычно имеет потерю частиц менее 5%.
3.1.4. Коэффициент прочности на разрыв
Австралия использует модифицированный тест Лоттмана на устойчивость к повреждению от влаги, также известный как удаление асфальта, как подробно описано в методе испытаний AG: PT / T232 [29].Шесть номинально идентичных образцов уплотняют до образования воздушных пустот 8 ± 1% в спиральном компакторе и испытывают на непрямую прочность на разрыв при 25 ° C. Три образца испытываются без кондиционирования, а три других – в условиях водонасыщения и цикла замораживания-оттаивания. Коэффициент прочности на разрыв (TSR) рассчитывается как среднее значение условных результатов, деленное на среднее значение безусловных результатов. Австралия считает, что асфальтовые смеси обладают хорошей устойчивостью к повреждению от влаги, если TSR превышает 80%, а многие асфальтовые смеси для аэропортов достигают 90% или выше.
3.1.5. Поверхностная текстура
Макротекстура поверхности для австралийских дорожных покрытий измеряется с использованием метода объемных песчаных пятен, как подробно описано в AG: PT / 250 [30] (Austroads 2008). Этот метод требует, чтобы на асфальтовую поверхность поместили известный объем мелкого песка и распределили по кругу до тех пор, пока макротекстура не заполнится и не останется песка выше уровня текстуры поверхности. Диаметр песчаного пятна зависит от средней глубины текстуры поверхности. Хорошо известно, что асфальтовые покрытия в аэропортах размером 14 мм имеют текстуру поверхности 0.4–0,6 мм [5], в то время как SMA и открытые градиентные поверхности могут привести к глубине текстуры поверхности 1,5 мм и более [31].
3.1.6. Binder Drain Down
Австралия использует версию теста Шелленберга [32] для оценки риска стекания связующего из смесей SMA, как подробно описано в AG: PT / T235 [33]. Этот метод позволяет связующему в образце асфальта весом 1 кг стекать при фиксированной температуре в течение одного часа. Затем асфальт удаляется из контейнера, и остаточная масса вяжущего рассчитывается как процент от исходной массы вяжущего в образце асфальта.Некоторые юрисдикции предпочитают указывать минимальное содержание волокна, обычно 0,3% обеспечивает приемлемый результат. Однако для технических характеристик, связанных с производительностью, предпочтение отдается тесту, ориентированному на результат, а не предписывающему содержанию волокна.
3.2. Сырье
Для производства семи смесей SMA использовались четыре разных источника агрегатов, три – по объемным требованиям SMA-10 и четыре – по требованиям SMA-14. Чтобы смеси SMA были разнообразными и репрезентативными, были выбраны агрегаты латита, базальта, амфиболита и грейвакке.Все совокупные источники использовались ранее для производства асфальта на дорогах большой грузоподъемности или в аэропортах. Следовательно, все они были твердыми и долговечными, со свойствами, подходящими для использования в аэропортах. Например, все агрегаты курса были раздроблены на 100% с индексом лещадности ниже 20%.
То же связующее, модифицированное эластомерным полимером (PMB), известное в Австралии как A15E [34], было использовано для производства всех семи смесей, основные свойства связующего подробно описаны в.PMB был выбран, поскольку большинство аэродромных и тяжелых дорожных приложений используют PMB для повышения производительности. A15E был выбран, поскольку он рекомендован в качестве подходящего связующего для SMA [35] и определен для ряда тяжелых дорожных приложений в Австралии, а также для некоторых применений в покрытиях DGA в аэропортах.
Таблица 5
Свойства связующего, модифицированного полимером A15E [34].
Свойство связующего | Метод испытаний | Требование |
---|---|---|
Вязкость при 165 ° C (Па · с) макс. | AS / NZS 2341.4 | 0,9 |
Восстановление при кручении при 25 ° C, 30 с (%) | AG: PT / T122 | 55–80 |
Температура размягчения (° C) | AG: PT / T131 | 82–105 |
Консистенция 6% при 60 ° C (Па · с) мин. | AG: PT / T121 | 900 |
Жесткость при 25 ° C (кПа) макс. | AG: PT / T121 | 30 |
3.3. Асфальтовые смеси
Эффективность SMA оценивалась путем сравнения результатов различных испытаний с требованиями к характеристикам аэропорта () и рассмотрения общих тенденций по четырем типам заполнителей, а также путем сравнения результатов для китайских (14 мм) и Объемные композиции на немецкой основе (10 мм).Семь наименований смесей, включая тип добавляемого наполнителя и содержание целлюлозного волокна, суммированы в. Из-за доступности материала из заполнителя Greywacke была произведена только 14-миллиметровая смесь.
Таблица 6
Обозначения и детали смесиSMA.
Обозначение | Заполнитель | Добавлен наполнитель | Содержание волокна (% по массе) | |
---|---|---|---|---|
SMA-10L | Латит | 902 известняк 19 0220.4 | ||
SMA-14L | Латит | Молотый известняк | 0,4 | |
SMA-10B | Базальт | Смесь измельченного известняка и гашеной извести | 0,4 | 0,4 | 215 | Смесь измельченного известняка и гашеной извести | 0,5 |
SMA-10A | Амфиболит | Пыль на рукавных фильтрах долерита | 0,3 | |
SMA-14A | Мешок для амфиболита | Амфиболит | 3 | |
SMA-14G | Greywacke | Молотый известняк | 0,3 |
5. Обсуждение
5.1. Требования к составу
Перед тем, как рассматривать характеристики смесей, необходимо было убедиться, что семь смесей достигли заданного состава. Градации, как правило, находились на более грубой стороне целевых пределов, при этом смесь на основе амфиболита падала ниже целевой границы как для вариантов размера 10 мм (), так и 14 мм ().Форма двух целевых градаций была аналогичной: смесь размером 10 мм имела в среднем на 4% больше заполнителя, прошедшего через каждое сито, чем для эквивалентных смесей 14 мм.
SMA-10 градаций по сравнению с целью.
градаций СМА-14 относительно цели.
Смеси меньшего размера имели VMA на 1-2% ниже, отражая более замкнутый скелет заполнителя, и, как правило, на 0,0–0,2% более высокое содержание связующего, как подразумевается целевыми требованиями (). Содержание пустот в смеси с воздухом размером 10 мм также обычно было примерно на 1% выше, чем для смесей диаметром 14 мм.Следует отметить, что VMA, содержание воздушных пустот и содержание связующего связаны математически на основании относительной плотности заполнителя и связующего.
Семь смесей в целом соответствовали требованиям к составу в пределах допусков, обычно ожидаемых при попытке уравновесить различные объемные свойства с различными источниками заполнителя. Следовательно, был сделан вывод, что измеренные различия в характеристиках SMA 10 мм и 14 мм в целом являются репрезентативными для типичных смесей SMA, которые предполагается использовать на покрытиях ВПП Австралии.
5.2. Сопротивление деформации
Все смеси не соответствовали требованиям к асфальту в аэропорту по сопротивлению деформации, измеренному с использованием глубины колейности колесных колей (). В среднем, окончательная глубина колеи, связанная со смесями размером 14 мм, была на 18% ниже, чем для смесей 10 мм, хотя разница не была статистически значимой (значение p 0,27). Глубина колеи колесных колей SMA превышала те, которые обычно достигаются для смесей DGA для аэропортов [25], и это не согласуется с установленными преимуществами SMA, включая высокое сопротивление деформации [5].Кроме того, скорость роста глубины следа колеса варьировалась, при этом некоторые образцы значительно деформировались в течение первых 500 циклов, но дальнейшая деформация затем значительно снижалась (например, SMA-14G), в то время как другие образцы деформировались с более постоянной скоростью на протяжении всех 10000 циклов. проходит (например, SMA-14L), как показано на.
Сводная информация о средней глубине колеи колеса SMA и скорости.
Рост глубины колеи.
Джеймисон и Уайт [36] продемонстрировали чувствительность результатов отслеживания асфальтового колеса к содержанию воздушных пустот и температуре испытания образца.В текущих спецификациях на асфальт в австралийском аэропорту тестируется отслеживание колес при температуре 65 ° C на образцах, подготовленных с заданным содержанием воздушных пустот 5%. Температура испытания выше, чем обычно используется в Австралии, которая составляет 50–60 ° C, и предназначена для лучшего представления температуры поверхностных канавок в полевых условиях, а не температуры среднего слоя. Однако это не применимо к SMA без канавок. Кроме того, чтобы гарантировать, что канавки DGA не закрываются при движении транспорта при высоких температурах, обычно используют больше связующих, модифицированных полимером.Эти связующие имеют высокие точки размягчения [37] и приводят к низкой глубине колеи при копировании колес. Напротив, ожидается, что SMA для аэропортов будет производиться с умеренно модифицированными полимерами связующими, такими как A15E, используемыми в этом исследовании, которые имеют более низкие точки размягчения и, следовательно, более подвержены деформации при повышенных температурах. Независимо от типа смеси, целевое содержание воздушных пустот в образце предназначено для отражения полевых воздушных пустот. Поскольку SMA обычно имеет примерно на 1% меньше воздушных пустот в эксплуатации, чем DGA, целевой показатель 5% подходит для DGA, но не для SMA.
Для подтверждения этих эффектов одна смесь SMA (SMA-14G) была повторно испытана при 60 ° C при содержании воздушных пустот 4% и 5% (). Конечная глубина колеи уменьшилась с 3,2 мм (65 ° C и 5% воздушных пустот) до 1,0 мм (60 ° C и 4% воздушных пустот). Содержание воздушных пустот в образце оказало значительное влияние на начальную деформацию, в то время как температура испытания в большей степени повлияла на текущую скорость деформации. Это указывает на то, что SMA соответствует требованиям к сопротивлению деформации асфальта в аэропорту при испытаниях в условиях, более репрезентативных для ожидаемых полевых условий.Однако практическая реализация этой разницы в испытаниях требует назначения различных условий испытаний для конструкций смесей SMA и DGA в будущем.
Влияние температуры и воздушных пустот на глубину колеи.
5.3. Сопротивление усталости
Все смеси превзошли требования по сопротивлению усталости со снижением модуля упругости на 17–33% (). Это сопоставимо с характеристиками DGA в аэропорту и отражает относительно высокое содержание связующего, используемого как в DGA, так и в SMA для аэропортов, а также используемое связующее, модифицированное эластомерами.В среднем 14-миллиметровые смеси имели снижение модуля упругости на 12% меньше, чем 10-миллиметровые смеси; однако это различие не было статистически значимым ( p -значение 0,37). Также следует отметить, что все средние значения начального модуля были согласованными в диапазоне от 1540 до 1650 МПа. Это ниже, чем у типичных DGA аэропортов в Австралии, и это снова отражает более высокое содержание только умеренно модифицированного связующего, по сравнению с типичными смесями DGA в аэропортах. Смеси SMA явно соответствовали требованиям к характеристикам асфальта для аэропортов по сопротивлению усталости.
Среднее снижение модуля упругости SMA при усталости и сводка начального модуля.
5.4. Прочность смеси
Все семь смесей SMA превысили минимальное значение TSR, составляющее 80%, со значениями TSR в диапазоне от 84% до 113%. Эти значения сопоставимы с типичными результатами для DGA в аэропорту, полученного с использованием связующих, модифицированных полимером. Аналогичным образом, значения потерь частиц варьировались от 1,4% до 3,8%, которые все значительно ниже максимума 15% и меньше типичного максимального значения 5%, измеренного для смесей DGA в аэропортах, произведенных с использованием связующих, модифицированных полимером.Следовательно, SMA соответствовала требованиям к долговечности смесей для асфальтовых покрытий в аэропортах, с такими же характеристиками, как смеси DGA, которые в прошлом обычно использовались на взлетно-посадочных полосах Австралии. Однако доступные методы испытаний не включали оценку относительной прочности связующего DGA и SMA и стойкости мастики к эрозии.
5.5. Поверхностная текстура
Все четыре смеси размером 14 мм превышали текстуру поверхности 1 мм, необходимую для предотвращения образования бороздок в соответствии с правилами сопротивления скольжению самолетов.Напротив, только одна (из трех) смесь размером 10 мм превысила минимум 1 мм (). В среднем текстура поверхности, связанная со смесями размером 14 мм, была на 35% выше, чем для смесей 10 мм, и это различие было статистически значимым ( p – значение 0,03). Это указывает на то, что вариант 14 мм SMA китайского производства, вероятно, более надежно обеспечит текстуру поверхности, необходимую для использования SMA в качестве поверхности взлетно-посадочной полосы без канавок, для широкого диапазона типов заполнителей. Вариант 10 мм может достигать 1 мм с некоторыми заполнителями, но ожидается, что это потребует нацеливания на более грубую сторону градации градации во время разработки смеси.
Сводка средней текстуры поверхности SMA.
5.6. Отвод связующего вниз
Для всех смесей достигается требование стекания связующего при 185 ° C, за исключением двух смесей, полученных с использованием латитного заполнителя. Содержание волокон в смеси латита было увеличено с 0,3% до 0,4%, но стекание связующего все еще превышало максимум 0,15% при 185 ° C (). Однако при повторных испытаниях при 175 ° C смесь латита соответствовала требованиям. Это подчеркивает высокую чувствительность риска стекания вяжущего к температуре производства асфальта, на которую также, вероятно, влияет тип вяжущего.Это также демонстрирует, что предел стекания связующего, связанный с эксплуатационными характеристиками, более подходит, чем минимальное содержание волокна, которое обычно принято во многих юрисдикциях [5].
Осушение связующего SMA при 185 ° C (если не указано иное) краткое описание.
Вклад авторов
Концептуализация, G.W. и S.J .; методология, G.W. и S.J .; формальный анализ, S.J .; расследование, S.J .; ресурсы, ГВт .; курирование данных, S.J .; письмо – подготовка оригинального проекта, S.J .; написание – просмотр и редактирование, G.W .; визуализация, G.W .; надзор, Г. Все авторы прочитали и согласились с опубликованной версией рукописи.
UDOT использует Crafco Mastic One для решения сложной проблемы с шоссе
Тротуар с нанесенными отметками или дорожные полосы предупреждают невнимательных водителей о потенциальной опасности. Эти полосы, обычно накладываемые на плече или по средней линии, доказали свою эффективность в снижении количества несчастных случаев и спасении жизней. Многочисленные исследования также показывают очень высокое соотношение цены и качества плечевых полос, что делает их одними из наиболее экономически эффективных доступных средств обеспечения безопасности дорожного движения.
Следовательно, крайне важно поддерживать дорожное покрытие и задир, чтобы полосы работали должным образом. Но, как и все тротуары, грохочущие полосы подвержены растрескиванию, обмыванию, затоплению и повреждению снегоочистителями.
Министерство транспорта штата Юта (UDOT) и местные агентства заметили, что тротуар забит на участках шоссе U.S. Rte. 89 в округе Санпете обнажились и покрылись выбоинами. Rte. 89 – длинная автомагистраль штата с севера на юг, протянувшаяся более чем на 502 мили через центральную часть штата.
UDOT должен был сохранить и продлить срок службы дорожного покрытия, не устраняя и не уменьшая эффект оценки безопасности. В 2011 году UDOT и местные агентства впервые использовали Mastic One от Crafco. Мастика была нанесена на зазубрины тротуара, и это имело успех.
Mastic One – это горячая текучая, полимерно-модифицированная мастика для ремонта асфальтовых покрытий черного цвета. Он используется для заполнения и ремонта повреждений как в асфальтобетонном покрытии (ACP), так и в портландцементном бетонном покрытии, которые больше, чем те, которые обычно ремонтируются с помощью герметизации трещин или стыков, но меньше, чем ремонт, требующий процедуры удаления и замены ямочного покрытия.
Типичные области применения Mastic One включают заполнение и выравнивание широких поперечных или продольных трещин и стыков, заполнение выбоин и выемок в коммуникациях, выравнивание высоких стояков колодцев, локальный ремонт кожных покровов, герметизацию и выравнивание подходов к мосту и устранение несоответствий по высоте. Он разработан для обеспечения аккуратной укладки со скошенными краями и обеспечивает прочный, гибкий, прочный и устойчивый к дорожному движению ремонт.
Это высокосамоклеящееся вяжущее для гребневого асфальта содержит тщательно подобранный заполнитель, обеспечивающий хорошие характеристики несущей способности и устойчивости к скольжению.Он устойчив к растрескиванию и расслоению, имеет доказанный срок службы более пяти лет и обеспечивает водонепроницаемость ACP.
Mastic One легко устанавливается бригадой из двух человек. Расфасован в твердом виде в плавкий полиэтиленовый пакет в картонной коробке; каждая коробка весит 40 фунтов. Для использования ее вынимают из коробки, затем смешивают и нагревают в подходящей плавильной печи до достижения температуры нанесения. Затем его заливают в подготовленное место для ремонта и разравнивают. Он достигает 100% плотности без уплотнения и готов к перевозке, когда остынет.
В дополнение к использованию Mastic One для нанесения задиров на асфальте, UDOT размещал его в трещинах шириной более 2 дюймов и поверх них, где покрытие стало вдавленным и шероховатым. За последние четыре года компания UDOT нанесла более 180 000 фунтов Mastic One на такие повреждения поверхности дорожного покрытия.
В результате устранения неисправностей и ухода за дорожным покрытием с зазубринами компания UDOT повысила качество езды и безопасность для водителей на дорогах США. 89.
Колейность и усталостные свойства каменно-мастичных асфальтобетонных смесей с добавлением целлюлозного волокна
В данной статье исследуются динамический отклик, сопротивление колейности и усталостное поведение трех бетонных смесей из каменно-мастичного асфальта (SMA), выбранных на основе номинального максимального размера заполнителя (NMAS) : 25 мм, 19 мм и 12.5 мм с использованием целлюлозного волокна, добавленного в количестве 0,3% от общего веса заполнителя. Были изготовлены спиральные образцы суперпроцесса и подвергнуты испытаниям на динамический модуль () и текучесть (число и время потока) с использованием тестера характеристик асфальтобетонной смеси. Результаты испытаний были использованы для построения зависимых от напряжения основных кривых для каждой смеси, показывающих, что смесь с NMAS 25 мм является относительно более жесткой, чем другие испытанные смеси; эта смесь также демонстрирует отличную стойкость против колейности.Кроме того, определяется параметр усталости, который выводится из динамического отклика и фазового угла, и результаты показывают, что смесь NMAS толщиной 12,5 мм имеет относительно лучшее сопротивление усталости, чем другие выбранные смеси. Кроме того, спецификации модели нелинейной регрессии использовались для прогнозирования накопленных деформаций в зависимости от циклов нагружения. Кроме того, разработана модель числа потоков, которая прогнозирует колейность смесей, и результаты показывают, что прогнозируемые и наблюдаемые модели выходы смеси 25 мм SMA оказываются очень близкими.Результаты этого исследования помогают понять характеристики и поведение асфальтобетонных смесей из каменно-мастичной мастики с добавлением целлюлозного волокна при различных смоделированных температурах и уровнях напряжения, которые могут быть использованы в областях, где часто наблюдается преждевременное разрушение гибких покрытий. Протокол испытаний, использованный в этом исследовании, также поможет в оценке характеристик покрытия с использованием Механико-эмпирического Руководства по проектированию дорожного покрытия.
1. Введение
Колейность и усталость на гибких покрытиях – два распространенных нарушения, которые проявляются на национальных автомагистралях по всему миру.С этими повреждениями связаны различные факторы, включая перегрузку, высокие температуры и эмпирический подход к проектированию, используемый для проектирования конструкций. С этой целью SMA считается эффективным решением в районах с интенсивным движением транспорта из-за большего размера заполнителя одного размера, который можно использовать с увеличенным битумом, таким образом контролируя склонность к образованию колейности. Устойчивость к усталости и растрескиванию при отражении повышается за счет более высокого содержания связующего в смесях SMA. В различных частях мира использование SMA очень распространено для районов с интенсивным движением.Причиной такого использования может быть конструкция смесей SMA, в которых нагрузку на колесо выдерживает каркас из крупного заполнителя, который способствует сопротивлению колейности, и богатое связующее, которое герметизирует пустоты и, следовательно, делает его более жестким. Таким образом, преобладает контакт между камнями в крупном заполнителе, в то время как мелкий и средний размеры заполнителей помогают захватить более крупные частицы, когда смесь разнесена.
Текстура SMA обычно обеспечивает хорошее качество езды, лучшее сопротивление скольжению при относительно низком уровне шума.Крупный заполнитель обеспечивает долговечность, что способствует огромному сопротивлению остаточной деформации, а более высокое содержание битума герметизирует пустоты и делает его чрезвычайно эластичным. Ингибитор дренажа необходим для предотвращения вытекания битума на протяжении всего срока службы конструкции дорожного покрытия. Для улучшения механических свойств SMA можно использовать модифицированный битум вместе с подходящими добавками; а в некоторых ситуациях это может снизить или даже исключить потребность в других ингибиторах дренажа.
В недавнем прошлом наблюдалось значительное улучшение конструкции конструкции дорожного покрытия, в которой фундаментальным механистическим свойствам придавалось существенное значение. Были разработаны различные новые смеси для дорожных покрытий, а также система классификации и анализа смеси, основанная на характеристиках, более известная как Superior Performing Asphalt Pavements (Superpave) в рамках программы стратегических исследований автомобильных дорог (SHRP). Такие разработки значительно снизили зависимость промышленности от традиционных методов эмпирического расчета смеси, предлагаемых Маршаллом и Хвимом во всем мире.Более подробное обсуждение будет продолжено в следующих разделах.
2. Обзор литературы
Bonaquist et al. [1] рекомендовали три типа испытаний производительности в отчете 513 Национальной совместной программы исследований автомобильных дорог (NCHRP): испытания динамического модуля (), числа потока (FN) и времени потока (FT) для процедуры расчета смеси суперпрощадок для прогнозирования характеристик разработаны асфальтовые смеси. Испытание уже использовалось для прогнозирования характеристик асфальтобетонных смесей на месте, а также для использования испытаний на текучесть (т.е., FN и FT) был очень ограничен. Позже выяснилось, что сам по себе тест не может точно предсказать поведение смеси при более высоких температурах; больше внимания теперь уделяется двум другим тестам производительности, то есть тестам FN и FT [2]. Чтобы пролить больше света, ниже представлен подробный обзор литературы.
Judycki [3] определил влияние низкотемпературного физического упрочнения на жесткость и предел прочности при растяжении обычного асфальтобетона и SMA. и непрямые испытания на прочность на разрыв были проведены на смесях после изотермического хранения при температуре -20 ° C в различные интервалы времени до 16 дней.Это исследование пришло к выводу, что после хранения прочность заметно увеличилась. Muniandy et al. [4] оценили усталостное поведение смесей модифицированного и немодифицированного асфальтового вяжущего SMA с использованием недавно разработанной методики меандра трещин. Результаты, полученные при испытании на анализ трещин, сравнивались с использованием графиков деформации, полученных при косвенном испытании на усталость при растяжении, и пришли к выводу, что усталостные характеристики можно определить с использованием метода появления трещин. Искендер [5] определил стойкость к колейности базальта и комбинации базальт-известнякового заполнителя для SMA с помощью теста отслеживания колес Laboratoire Central des Ponts et Chaussées (LCPC).Это исследование пришло к выводу, что сопротивление колейности уменьшилось при добавлении известняка в SMA в качестве мелкозернистого материала / наполнителя. Исследование иллюстрирует влияние добавления отработанного полиэтилентерефталата (ПЭТ) на жесткость и усталостные свойства смесей SMA. Это исследование показывает, что жесткость смесей увеличивается при добавлении меньшего количества ПЭТ, а смеси, армированные ПЭТ, демонстрируют более высокую усталостную долговечность по сравнению с контролируемыми смесями (без ПЭТ) [6]. Ахмадиния и др. [7] использовали отходы пластиковых бутылок в качестве добавки к смесям SMA, и 6% по весу битума были сочтены оптимальным количеством ПЭТ.В этом исследовании сделан вывод о том, что введение ПЭТ в смеси SMA значительно улучшает инженерные и механические свойства. Бенуд и Амери [8] использовали заполнитель стального шлака в SMA, и результаты показывают, что использование стального шлака в качестве заменителя крупного заполнителя улучшило стабильность по Маршаллу, модуль упругости, предел прочности при растяжении, устойчивость к повреждениям от влаги и устойчивость к остаточной деформации.
Sengul et al. [9] провели подход с использованием коэффициента Маршалла (MQ), повторное испытание на ползучесть (RCT), непрямое испытание на прочность на разрыв (ITST) и испытания на отслеживание колес SMA, модифицированного полимером SBS.Результаты показывают, что добавление SBS увеличивает сопротивление пластической деформации и снижает колейность по сравнению с обычными смесями. В другом исследовании к SMA добавляли известь, чтобы снизить способность к отгонке и чувствительность к влаге. Методология поверхности отклика использовалась для определения влияния содержания и сортировки извести на способность отделяться от SMA с использованием индекса коэффициента прочности на разрыв (TSR), и было обнаружено, что содержание извести 1% и самый мелкий заполнитель дало оптимальное значение TSR 91.8% ± 0,8% [10]. Cao et al. [11] оценивали SMA (базальт, B-SMA, известняк, L-SMA и BL-SMA), и результаты показывают, что B-SMA продемонстрировала лучшую устойчивость к колейности, чем другие испытанные смеси. Пазетто и Бальдо [12] провели сравнительный анализ SMA со стальным шлаком электродуговых печей. Исследование было сформулировано в предварительном исследовании химических, выщелачивающих, физических и механических свойств стального шлака и привело к выводу, что стальной шлак удовлетворяет всем требованиям технических стандартов дорожного сектора и показывает более высокие механические характеристики, чем другие смеси.Многочисленные исследования показали использование различных добавок в SMA помимо целлюлозного волокна [4–6, 9, 11, 13–15]. Различные исследования продемонстрировали оценку и развитие мастер кривых [14, 16–28].
Дизайн смеси SMA состоит из выбора материала, определения оптимальной градации заполнителя, выбора добавки и ее количества, а также оптимального содержания связующего. Кроме того, смеси SMA должны обеспечивать стабильность и устойчивость к колейности, достигаемую за счет контакта агрегатов и блокировки; Долговечность смесей SMA достигается за счет соответствующей конструкции смеси, включая воздушные пустоты, пустоты в минеральном заполнителе, толщину асфальтовой пленки и количество наполнителя.
Асфальтобетонный материал ведет себя как вязкоупругий материал, и его жесткость зависит от температуры. Более высокая жесткость / модуль при низких температурах (зимой) приводит к усталостному растрескиванию, а более низкая жесткость / модуль при высоких температурах (летом) приводит к колейности. Прочность асфальтового материала значительно снижается с повышением температуры, как в Пакистане. Следовательно, необходимо охарактеризовать смеси с добавкой, используя полный протокол испытаний с простыми характеристиками (, FN и FT) для различных нагрузок и условий окружающей среды в Пакистане.В этом исследовании оцениваются характеристики смесей SMA, содержащих целлюлозное волокно, с помощью трех тестов производительности, то есть FN и FT. Результаты, полученные в результате этих испытаний, в дальнейшем были использованы для построения основных кривых и оценки усталостного растрескивания путем определения параметра усталости.
3. Цель и объем
Целью данного исследования является изучение характеристик различных смесей SMA с добавлением целлюлозных волокон путем варьирования NMAS. В данном исследовании используются следующие показатели эффективности: FN и FT.Полученные результаты используются для определения модулей жесткости и оценки сопротивления усталостному растрескиванию на основе значений фазового угла. Это исследование также описывает колейность смесей с использованием статистических моделей, которые используют две разные нелинейные формулы для выражения количества циклов до разрушения как функции осевой деформации. Три различных градации номинального максимального размера заполнителя (NMAS) 25 мм, 19 мм и 12,5 мм выбраны из диапазонов градаций, разработанных Национальным центром асфальтовых технологий (NCAT).Добавляли 0,3% целлюлозного волокна от общего веса заполнителя смесей SMA и использовали асфальтовое вяжущее со степенью проницаемости 60/70. Обратите внимание, что различные процентные содержания целлюлозного волокна были протестированы на начальном этапе тестирования, и было обнаружено, что 0,3% является оптимальным количеством, которое удовлетворяет критериям дизайна смеси Маршалла.
4. Методология
В следующих разделах объясняется методология, принятая в этом исследовании и проиллюстрированная на Рисунке 1.
4.1. Выбор материалов
Это исследование включает испытание трех смесей SMA, дифференцированных NMAS, которые практикуются во всем мире. Три различных градации на основе NMAS: 25 мм, 19 мм и 12,5 мм выбраны из диапазонов градаций, разработанных Национальным центром асфальтовых покрытий (NCAT) в отчете Национальной совместной программы исследований автомобильных дорог (NCHRP) [29], и диаграмм градаций. для смесей SMA представлены на рисунке 2. Целлюлозные волокна прессованных гранул длиной 2-3 мм использовались в качестве добавки к смесям SMA для улучшения пленочного покрытия на агрегате, стабильности смеси и лучшего сцепления скелета агрегата.Оптимальное содержание битума и объемный анализ смеси представлены в Таблице 1.
|
Расчет смесей SMA в первую очередь зависит от объемных свойств, таких как воздушные пустоты, пустоты в минеральном заполнителе, пустоты в крупном заполнителе и содержание связующего.Браун и Хэддок [30] представили выбор оптимального соотношения крупных и мелких заполнителей. Объем крупного заполнителя принимается как доля и объемная плотность крупного заполнителя. Пустоты в крупном заполнителе для заполнителя номинальным размером 14 мм обычно составляют от 41 до 46% для заполнителей, уплотненных связующим без мелкого заполнителя.
Еще одним важным фактором при разработке SMA является наполнитель / добавка. В этом исследовании используются гранулы целлюлозного волокна VIATOP® производства J. Rettenmaier and Söhne, Германия (рис. 3).VIATOP® представляет собой гранулированную смесь ARBOCEL® ZZ 8/1 (90% по весу) и битума 50/70 (10% по весу). Волокна целлюлозы в качестве стабилизатора имеют более высокое содержание асфальта, толстопленочное покрытие, высокую стабильность смеси, повышенную прочность и меньший дренаж. Оптимальное количество целлюлозного волокна основано на соответствующем количестве связующего и содержании волокна.
4.1.1. Подготовка образца
Для всех испытаний производительности для изготовления образцов использовался сверхмощный гираторный уплотнитель.Образцы помещали в печь для кратковременного старения за 2 часа до уплотнения. Цилиндрические образцы диаметром 100 мм были взяты из прессованных спиральных образцов диаметром 150 мм в соответствии со стандартом AASHTO [31]. Отношение высоты к диаметру образца сохранялось 1,5 для всех испытаний.
4.2. Тестирование производительности
Тестер производительности асфальтовой смеси (AMPT), широко известный как простой тестер производительности (SPT), используется для тестов FN и FT. Оборудование имеет климатическую камеру, которая поддерживает температуру от 4 до 60 ° C и ограничивающее давление до 210 кПа.Испытание проводится при четырех различных температурах (4,4, 21,1, 37,8 и 54,4 ° C) и шести частотах (0,1–25 Гц). После завершения испытания данные собираются из программного обеспечения и используются для разработки зависимых от напряжения основных кривых и параметра усталости.
AMPT также использовался для проведения тестов FN и FT. Эти испытания проводились при единственной эффективной температуре 54,4 ° C и девиаторном напряжении 210 кПа. В случае испытания FN подготовленные образцы подвергались повторяющемуся импульсу осевого гаверсинусного сжимающего нагружения 0.1 секунда, за которой следует период отдыха 0,9 секунды. Однако для испытания FT предварительно кондиционированные образцы подвергались постоянной осевой нагрузке до тех пор, пока она не разрушилась, и остаточная деформация измерялась в зависимости от времени нагружения. Это испытание должно было завершаться через 10 000 циклов или до тех пор, пока максимальная накопленная постоянная деформация в образце не достигнет 5%, или в зависимости от того, что наступит раньше [32].
5. Результаты и обсуждение
5.1. Динамический модуль,
Испытания проводились в соответствии со стандартом AASHTO TP 62-07 [16], который рекомендует проводить оценку при четырех различных температурах и шести разных частотах для построения эталонных кривых.Результаты, полученные в результате испытания, показывают, что для данной частоты нагружения повышение температуры (с 21,1 до 37,8 ° C) выражается в падении значений на 41, 55 и 26% в среднем для 25, 19 и 12,5 мм. смеси соответственно. Однако для данной температуры и увеличения частоты нагружения (от 0,1 до 25 Гц) 76, 85 и 74% изменения значений в среднем приходились на смеси 25, 19 и 12,5 мм соответственно.
Поскольку AASHTO TP 62 рекомендует разработку эталонных кривых, он имеет несколько преимуществ: он позволяет сравнивать линейные вязкоупругие материалы, которые испытываются при различных скоростях напряжения (частоте нагружения) и температурах испытаний, а также позволяет прогнозировать даже при более низких температурах. которые нельзя получить из лабораторного оборудования из-за его невозможности.Усредненные результаты испытаний берутся для каждой температуры и используются при разработке эталонной кривой для усреднения при эталонной температуре 21 ° C с использованием принципа наложения времени и температуры, в котором каждое значение температуры сдвигается к эталонной температуре для получения гладкой однородной массы. изгиб. Лист Microsoft Excel © был использован для разработки мастер-кривых, которые работают на основе минимизации суммы квадратов ошибок для соответствия кривой. Общая форма сигмоидной функции, используемой для построения эталонных кривых, задается следующим уравнением: где – логарифм динамического модуля, – это минимальное значение модуля, – это приведенная частота, – это диапазон значения модуля и – параметры формы. .
Максимальная жесткость смеси является функцией связующего при более низкой температуре, в то время как при более высоких температурах сцепление заполнителя преобладает над эффектом связующего и становится индикатором жесткости смеси. На рисунке 4 представлены эталонные кривые для смесей SMA, которые показывают, что смесь SMA 25 мм имеет самые высокие значения на всех частотах, а смесь 12,5 мм имеет самые низкие значения.
Значения испытаний в дальнейшем используются для получения параметра усталости, который оценивает сопротивление усталости асфальтобетонных смесей [18, 33].Параметр усталости является продуктом вязкоупругого поведения смеси, то есть фазового угла, и может быть оценен с помощью уравнения (2). Значение параметра усталости обратно пропорционально сопротивлению усталостному растрескиванию. Более высокое значение параметра усталости приводит к более низкому сопротивлению усталостному растрескиванию и наоборот: где – динамический модуль (МПа), а – фазовый угол (градусы). Параметр усталости оценивает сопротивление усталости асфальта, как и у асфальтовых вяжущих. На рис. 5 показаны усталостные характеристики и сопротивление растрескиванию при различных градациях SMA с использованием принципов и фазового угла при температуре 21 ° C.Смесь SMA толщиной 25 мм показывает наивысшее значение параметра усталости, что означает минимальное сопротивление усталости, тогда как смесь SMA толщиной 12,5 мм работает относительно лучше среди испытанных градаций и демонстрирует более высокое сопротивление усталостному растрескиванию.
5.2. Тесты потока
Тест числа потока (FN) был выполнен в соответствии с AASHTO TP 79 [31, 34] и определен как номер цикла нагружения, при котором начинается третичная деформация. FN аналогичен полевым условиям, поскольку нагрузка на дорожное покрытие не является непрерывной.FN пытается определить сопротивление смеси остаточной деформации путем измерения деформации сдвига, которая возникает из-за нагрузки гаверсинуса. Наиболее важным результатом теста FN является кривая накопленной деформации от количества циклов нагружения, которая описывает устойчивость смесей к колейности (рис. 6). Взаимосвязь между накопленной деформацией и циклами нагружения основана на механизмах колейности, уплотнении и сдвиговом потоке. На рисунке 6 показано, что только 12.Смесь 5 мм достигла третичной текучести среди испытанных смесей. Смеси не подвергаются третичной стадии потока; поэтому количество циклов для завершения испытания считается числом потока (FN) этих образцов.
Третичный поток показывает, что скорость деформации снова увеличивается с циклами нагружения. Когда образец достигает третичной стадии, данные, полученные с помощью программного обеспечения оборудования AMPT, содержат резонанс, который приводит к ложному FN. Чтобы удалить шум / резонанс из данных, метод сглаживания данных, т.е.е., пятиточечная скользящая средняя используется для получения скорректированной FN (рисунок 7). Скорость деформации относительно заданного цикла получается как половина разницы соседних циклов. FN – это начальная точка зоны третичной деформации, и ее можно указать как самую низкую точку в соотношении скорости изменения податливости и времени нагружения. Чтобы подтвердить, что значение FN является наименьшим на кривой, уравнение решается путем приравнивания y к нулю, как указано Витчаком [31], что теоретически FN – это номер цикла, соответствующий скорости изменения постоянной деформации, равной нуль.Таблица 2 иллюстрирует FN и накопленную деформацию SMA, и совершенно ясно, что 25 мм выдерживают больше повторений нагрузки, чем любые другие испытанные градации, и менее подвержены образованию колейности. Однако две другие смеси подвергаются большему деформированию за короткий промежуток времени, что снижает их устойчивость к колейности.
|
Окончание FN настроено на достижение любого из двух условий, т. Следовательно, для выполнения теста требуется больше времени, чем обычно. Данные, полученные в результате обширных лабораторных испытаний, были использованы для разработки статистической модели для прогнозирования характеристик покрытия. В этом исследовании для прогнозирования осевых деформаций от циклов нагружения использовались две разные нелинейные формулировки.Общая форма модели представлена в следующем уравнении:
Данные, полученные в результате испытаний FN, были подвергнуты первоначальной проверке, которая предполагает, что степенная и полиномиальная (2-го порядка) формулировки лучше всего подходят для такого типа данных. Общая форма этих моделей представлена в следующем уравнении:
Эту функциональную форму для данного исследования можно переписать следующим образом: где – постоянная деформация, – это циклы нагружения (10 000) и – коэффициенты регрессии.
Сводка и статистика модели представлены в таблице 3. t -Статистика всех переменных выше, чем t -critical () при уровне достоверности 95%, что означает, что переменные модели значимы для прогнозирования постоянной деформации. Коэффициент детерминации ( R 2 ) составляет 0,99 и 0,91 для степенной и полиномиальной моделей соответственно, что указывает на то, что 99% и 91% вариации постоянной деформации объясняются изменением циклов нагружения.
|
Прогностическая способность разработанной модели оценивалась с использованием средней абсолютной процентной ошибки. Его можно определить как среднее значение абсолютной разницы между фактическим и прогнозируемым значением: где – процентная погрешность для наблюдения фактического и прогнозируемого. . .
Значение MAPE для степенной и полиномиальной моделей составляет 0,19 и 0,20 соответственно. Значение MAPE 0.19 (модель мощности) представляет в среднем, что прогнозы занижают или завышают истинные значения на 19%. Значения MAPE, близкие к нулю, означают лучшую точность.
Испытание FT проводилось в соответствии с отчетами NCHRP [35, 36], в которых предварительно подготовленный образец подвергался постоянной осевой нагрузке до тех пор, пока он не вышел из строя, а остаточная деформация измерялась в зависимости от времени нагрузки. Результаты показывают, что ни одна из смесей SMA не достигла стадии третичного потока. Таким образом, никакой техники сглаживания данных не требовалось, и данные, полученные из программного обеспечения AMPT, используются для сравнения накопленной деформации на момент завершения теста.Результаты FT предполагают, что все смеси прошли максимальное количество циклов в 10 000 циклов, и смеси сравнивают на основе накопленных штаммов. Таблица 4 показывает, что на момент прекращения, смесь SMA 25 мм имеет относительно небольшую накопленную деформацию, что позволяет предположить, что эта смесь имеет относительно более высокое сопротивление остаточной деформации.
|