Клееный брус – технология изготовления хорошего материала для деревянных домов
Как изготавливают клееный брус хорошего качества? Этот вопрос волнует многих, кто решил построить дом из современного древесного материала. Последний привлекает внимание тем, что из него получается возводить красивое и комфортное жилье, другие здания, в частности, бани, где можно приятно и полезно провести время.
Сырье
Из чего делают клееный брус? На завод по изготовлению клееного бруса поступает пиломатериал, который тщательным образом отбирается. Он проверяется на наличие различных природных дефектов, сучковин. При превышении допустимых норм пиломатериал не допускается до использования в качестве сырья для изготовления клееного бруса. Так получается обеспечить качество продукции уже на первом производственном этапе.
Для изготовления клеевого древесного материала используется древесина хвойных пород. В нашем случае это кедр, сосна, а также лиственница.
- Сосна – прочная, с красивой структурой. Отличается устойчивостью к поражениям грибком. Мало подвергается воздействию насекомых.
- Лиственница обладает высокими параметрами по огнестойкости. В сыром виде мало подвержена расколу. Отличается прочностью, практически уступая по этому параметру только дубу. Имеет уникальный рисунок древесины.
- Кедр обладает оригинальным ароматом за счет природных эфирных масел. Способен создать особенный микроклимат. Обладает обеззараживающими свойствами.
Процесс сушки и обработки
Как делают клееный брус для деревянных домов, бань? С обязательным применением сушильного оборудования – специальных объемных камер, куда помещают доски для просушки. Это делать необходимо, чтобы удалить природную влагу из древесного сырья. В процессе сушки требуется обеспечивать определенную постоянную температуру. При изготовлении качественного клееного бруса заготовки сушатся строго указанное технологией время.
После сушки сырье попадает в цех по обработке. Используются станки, которые позволяют максимально ровно обстругать пиломатериал. И на этом этапе выполняется строгий контроль. При выявлении недопустимых изъянов, дефектов сырье снимается с производства. Отбираются доски, которые идут на внутреннюю и внешнюю стороны клееного бруса.
Технология производства клееного бруса – применение клея
В ходе производства используются специальные клеи. От их особенностей напрямую зависит экологичность конечной продукции. Важно знать, что некоторые клеи способны выделять в воздух довольно опасные вещества. Это происходит и тогда, когда дом построен. В таком доме жить нельзя.
Производители, которые заботятся о качестве своей продукции, выбирают безопасные клеевые составы. В частности, компания Гринсайд использует клей Akzo Nobel, не содержащий формальдегидов. Этот клей многократно протестирован его изготовителем, информация об этом находится в широкой доступности.
Для склеивания досок применяется специальное оборудование. Клей распределяется по всей площади доски. При образовании излишек они убираются. Потом доски укладываются друг на друга и помещаются под пресс на определенное время. После данного этапа заготовка вновь попадает на обрабатывающий станок, где она стругается с 4-х сторон. Потом следует стадия фигурной обработки. В частности, вырезается углубление, которое требуется для сборки.
Что дальше?
После изготовления каждой партии выполняются контрольные срезы. Они исследуются в лаборатории завода, чтобы выявить степень их качества.
Клееный брус обрабатывается антисептическими веществами, обеспечивающими их огнеупорность, а также биозащиту. Обработанный материал менее подвержен воздействию грибка, насекомых, плесени. Он лучше сопротивляется воздействию огня.
Важно! На каждом производственном этапе обеспечивается участие квалифицированных мастеров, обладающих соответствующими знаниями и опытом работы. Осуществляется тщательный контроль процесса, что позволяет гарантировать выпуск максимально качественного материала для строительства.
Можно ли изготовить клееный брус своими руками?
Технология изготовления достойного по качеству клееного бруса, как мы рассказали, требует применения специального оборудования. Это промышленные станки, стоимость которых достаточно высока. Конечно, можно попытаться изготовить брус в домашних условиях. Однако вряд ли получится соблюсти все требования технологии именно потому, что непросто обеспечить выполнение всех этапов без оборудования, которое имеется на заводах. В результате клееный брус будет только номинально так называться. Ни о каком качестве в данном случае не может идти речь.
Заключение
Итак, мы рассказали, как делается клееный брус, технология его изготовления, как мы поняли, требует привлечения опытных специалистов, использования промышленного оборудования, а также тщательного контроля качества на каждом производственном этапе. Дом, построенный из материала, который был изготовлен с соблюдением всех требований технологического процесса, гарантировано будет радовать своих владельцев долгое время.
Как производят клеенный брус для деревянных домов
Вопрос о собственной жилплощади возникает рано или поздно у каждого человека. Волнует эта проблема и меня в том числе. Недавно, побывав на одной выставке посвященной строительству дома я заинтересовался вопросом, из чего и как делаются стройматериалы для простого деревянного домика, который по цене доступнее, чем самая дешевая однушка в столице. Я договорился с заводом Good Wood об экскурсии на производство, и на днях выяснил как это делается.
Сегодня в специальном репортаже для kak_eto_sdelano мы посмотрим как производят брус из которого строят современные деревянные дома.
Все начинается с того, что на завод поступают вот такие пакеты с деревянными досками. Специалист производства перед началом производственного цикла проверяет каждый такой пакет на соответствие качеству. Выборочно проверяются доски и после подтверждения качества они отправляются на первый этап. Если процент дефектов и сучковин на заготовках превышают допустимые нормы, то такой пакет отправляется обратно поставщику.
Сырье, из которого будет сделан брус – из сосны и ели.
Территория завода не маленькая, вдалеке можно видеть строящийся корпус, в котором будет производится больше заготовок чем в остальных цехах.
После того, как доски выбраны, они собираются в сушильный пакет – набор из заготовок, который будет помещен в сушильную камеру. Доски предварительно перетягивают такой лентой, чтобы в процессе сушки они не деформировались.
На производстве 6 сушильных камер объемом до 75 куб.м.
Заглянем внутрь.
Пакеты с досками находятся в камере 6-8 дней, при температуре 65-68 градусов. Сушильная камера снабжена датчиками влажности воздуха, температуры, чтобы следить за правильной технологией сушки досок.
Это фото свежесклеенного не обработанного бруса, здесь можно видеть, как из досок разного размера делают единый прочный брус. О нем я расскажу далее.
Но вернемся к производству. После сушки пакет с досками попадает в цех.
Здесь он проходит через станок, который строгает доску со всех четырех сторон. На этом этапе рабочие проводят визуальный контроль, каждая доска заново проверяется на наличие дефектов и сучковин. Тут же определяется какие доски пойдут на внутреннюю и внешнюю сторону будущего бруса. Более красивые доски, с меньшим количеством сучковин идут на внешнюю сторону.
Как я говорил, доски из которых делается брус из сосны и ели. Так как они схожи по структуре волокон, их можно без особых проблем склеивать друг с другом. И еще информация для наблюдательных – доски ели и сосны можно отличить по сучковинам – у сосны они крупнее, чем у ели.
Далее, доски склеивают. Здесь аппарат был отключен потому можно на фото из соседнего цеха увидеть склеивающий аппарат в работе.
Вот таким дождем клей покрывает доску с одно стороны.
Лишнее убирается валком. В зависимости от каждого индивидуального заказа брус делают/склеивают из нескольких досок различной длины и ширины. Чуть не забыл сказать – на производстве не делают впрок брус. Его изготовление начинается только после того, как клиент заказал дом (уже подготовил фундамент) или отдельные детали.
Клей используемый в производстве прошел сертификацию на безопасность и не содержит формальдегидов и опасных для человека веществ.
В этой бочке отвердитель, который смешивается с клеем непосредственно перед склейкой.
После того, как доски смазаны клеем и правильно уложены, они помещаются под пресс, в котором находятся 40 минут. Затем их вынимают и они “отдыхают” еще два часа до того, как попадут на следующий этап.
Далее заготовки передвигаются на следующий этап, но перед этим заготовка бруса опять проходит через станок, который обрабатывает его с четырех сторон.
Так выглядит брус после профилирования, но и это еще не все. Как видите торцы неровные, и брусья не нарезаны на нужные детали.
Кстати, точность нарезки профиля определяется такими лазерными датчиками.
Попробовал прожечь свой блокнот, но почему-то не получилось.
Еще одна приятная деталь – кулер с прохладной водой. Очень нужная вещь на производстве.
Но мы отвлеклись. Далее брус попадает на станок, который обрезает торец и…
нарезает чашу – углубление в брусе, необходимое для поперечной сборки. Чаша, кстати, единственное место, которое будет обложено утеплителем. При сборке стен дома утеплитель не используется, только в местах стыка.
Ну, вот и готовы детали для дома. Торцы обрабатываются торцевым герметиком.
А это уже готовый пакет для дома. Таких для одного дома будет несколько.
Каждая деталь маркируется бумажкой со штрих-кодом, в котором содержится вся информация о брусе, вплоть до того, где он должен быть уложен в доме.
И еще одна деталь: после подготовки каждой такой партии для отдельного проекта, делаются контрольные срезы, которые потом исследуются в заводской лаборатории на соответствие качеству. Срез нагревается и охлаждается до определенной температуры в течении 50 циклов, которые имитируют зиму и лето, то есть теоретически дом из такого бруса может простоять 50 лет.
За процессом следит и камера, которая, как мне сказали показывает процесс производства онлайн посетителям сайта завода.
На мониторах отображаются детали производственного процесса. На фотографиях – проекты, которые осуществляются в данный момент.
На примере этого образца, который стоит в цеху можно видеть как выглядит угол стен дома. Такими железными штырями скрепляются только углы, а по остальной длине стен брусы насаживаются на деревянные штыри.
Идем на следующий этап. Здесь готовый брус обрабатывается антисептиком для огне-биозащиты. Он предохраняет его от жучков-короедов, плесени, гниения и предотвращает дом от возгорания. Должен уточнить, что действие антисептика конечно не вечно, но он сохраняет свойства бруса на некоторое время, и в случае пожара дом не воспламенится как спичка, потому что при обработке антисептиком из дерева выводится кислород.
При необходимости брус может принять антисептические ванны.
После этого этапа, можно сказать, что процесс производства и подготовки бруса для заказчика завершен. Однако это еще не все.
После обработки антисептиком брус собирают опять в такие пакеты готовые к отправке клиенту.
На каждом пакете информация о заказчике и содержимом. Обратите внимание на слова “мин. венец 20” и “макс. венец 43” – это означает, что в этом пакете есть детали, которые подходят для сборки от 20 “слоя” стен до 43. Это нужно для того, чтобы не вскрывать все пакеты в поисках нужных деталей – все они могут оказаться в одном пакете, до определенного этапа сборки.
Мы увидели практически всю цепочку производства, однако, наша экскурсия не завершена, мы идем в следующий цех, чтобы узнать еще кое-какие детали. Кстати, обратите внимание на этот домик, здесь находится один из офисов компании, в котором работают менеджеры по продажам, специалисты колл-центра, архитекторы и конструкторы. Как понимаете, он полностью сделан на этом производстве и собран работниками компании.
Кстати, о велосипедах на фото – они безвозмездно покупаются компанией любому работнику производства, который готов ездить на нем из дома до работы и обратно). Еще одна интересная информация о компании: работникам производства, которые бросили курить выдается премия в 10 тыс. руб! Правда, если работник не справляется с недостатком никотина и опять начинает курить, его штрафуют на 15 тыс).
Следующий цех производства больше размером, здесь более новые, немецкие станки, здесь делают брус длиной до 12 метров и супербрус, сечение которых больше, чем у тех, которые мы видели ранее.
В этом цеху брус также делают из отдельных досок, которые сращивают с помощью клея в длинную доску.
Участки досок с дефектами и сучковинами, которые могут повредить будущему изделию вырезают. На этом фото – отход производства.
А это готовые доски, из которых будут клеить брус. Здесь происходит вся та же технологическая цепочка, что мы видели ранее, потому не буду повторяться.
Тринадцатиметровый пресс.
После обработки досок, их торцы нарезаются “елочкой” и далее станок при склейке с давлением прижимает доски друг к другу. Этого достаточно, чтобы склеить доску.
Ну а дальше доски склеиваются в брус, обрабатываются, и на этом станке нарезается профиль. И еще добавлю, что брус, склеенный из отдельных досок различного размера прочнее, чем из цельных досок, потому что дерево со временем дает усадку и в нем повышается напряжение между другими склеенными досками, а короткие нарезанные заготовки полностью минимизируют этот эффект. Поперечные балки при строительстве дома тоже делают из такого бруса, в обязательном порядке.
А вот и супербрус. Кстати, клиент, который заказывает брус для своего дома, выбирает размер сечения под свой вкус. Здесь же, компания может помочь ему определиться с проектом, или создать собственный проект с помощью архитектора и инженеров компании Good Wood.
А это суперстанок Хундеггера, который в этот момент нарезает чашу в брусе.
Заметил, что в цехах хорошо работает вентиляция и пыль, которая неизбежна на таком производстве не висит долго в воздухе.
С пылью и мельчайшими опилками также борются и увлажнители воздуха. Хорошая вещь, надо завести себе дома.
Хотя у производства бывают отходы в виде обрезков, можно сказать, что это практически безотходное производство (в экономическом плане), потому что древесина не пригодная для изготовления бруса продается как топливо для камина, и используется для собственных нужд, также как топливо.
Из опилок делают вот такие брикеты для растопки каминов.
В конце экскурсии мне опять встречаются готовые пакеты для сушильной печи.
В эту емкость собираются опилки производства.
Напоследок зайдем в небольшой двухэтажный домик на территории компании, который может осмотреть любой желающий. Выглядит симпатично.
Чуть не забыл сказать, дома для своих клиентов собирают только специалисты компании, начиная от закладки фундамента, до кровельных работ и установки бойлера, и т.п., что очень удобно.
Здесь есть своя котельная, что немаловажно.
Домик сделан из самого простого бруса. Конечно же, после сборки дома нужно его покрасить, чтобы сохранить его свойства. Кстати, приемущество бруса перед обычным бревном в том, что со временем брус дает усадку всего в 1-2% а бревно – 15%! К тому же цельное бревно невозможно подвергнуть сушке без деформации.
Очень просторная, светлая кухня.
Плавно перетекающая в гостиную. В туалет и ванную заглядывать не стал, так как в этот момент ими были заинтересованы потенциальные покупатели, бродившие по дому).
На первом этаже нет жилых комнат, потому что площадь домика совсем небольшая. А на втором этаже их три. Первые две – детские комнаты.
Третья комната – спальня для родителей.
Тут же есть балкончик. Домик хорош, но маловат, буду присматривать себе другой проект.
Теперь и вы знаете, как делается брус для строительства дома. Спасибо всем, кто дочитал до конца.
А всем, кто заинтересовался строительством собственного домика советую посетить сайт компании Good Wood, где очень подробно рассказывается о различных проектах таких домов, и можно подобрать под свой вкус и цену.
Жми на кнопку, чтобы подписаться на “Как это сделано”!
Если у вас есть производство или сервис, о котором вы хотите рассказать нашим читателям, пишите Аслану ([email protected]) и мы сделаем самый лучший репортаж, который увидят не только читатели сообщества, но и сайта Как это сделано
Подписывайтесь также на наши группы в фейсбуке, вконтакте, одноклассниках, в ютюбе и инстаграме, где будут выкладываться самое интересное из сообщества, плюс видео о том, как это сделано, устроено и работает.
Жми на иконку и подписывайся!
– http://kak_eto_sdelano.livejournal.com/
– https://www.facebook.com/kaketosdelano/
– https://www.youtube.com/kaketosdelano
– https://vk.com/kaketosdelano
– https://ok.ru/kaketosdelano
– https://twitter.com/kaketosdelano
– https://www.instagram.com/kaketosdelano/
Официальный сайт – http://ikaketosdelano.ru/
Мой блог – http://aslan.livejournal.com
Инстаграм – https://www.instagram.com/aslanfoto/
Facebook – https://www.facebook.com/aslanfoto/
Вконтакте – https://vk.com/aslanfoto
Tags: Московская область, брус, специальный репортаж, строительство
видео-инструкция по монтажу, особенности горизонтально-клееного материала, используемого клея, перил, дуплексов, особняков, установки проводки, цена, фото
Статьи
Клееный брус имеет очень широкую сферу использования в строительстве и мебельном производстве благодаря своим высоким эксплуатационным качествам. Примечательно, что его можно изготовить даже в домашних условиях своими руками. Об этом и пойдёт речь далее.
Горизонтально клееный брус – превосходный строительный материал
Общие положения
В первую очередь следует понимать, что собой представляет клееный брус. Это набор тщательно отобранных, подготовленных и склеенных между собой ламелей. Наличие застывших клеевых прослоек значительно меняет технические характеристики изделия в сравнении с цельными образцами. Давайте ознакомимся с основными отличиями.
Преимущества
- Увеличение показателя прочности до DIN 1052, гарантирующее высокую надёжность собранной мебели;
Перила из клееного бруса выдержат колоссальные механические нагрузки
- Снижение теплопроводности, которое наглядно отображает следующая таблица:
Строительный материал | Коэффициент теплопроводности, Вт/(м×К) |
Железобетонные блоки | 2,04 |
Пеноблоки | 0,37 |
Цельный брус | 0,18 |
Клееный брус | 0,1 |
Особняк из клееного бруса не нуждается в дополнительном утеплении
- Уменьшение напряжённости древесины и, как следствие, усадки возведённого здания до практически не ощутимых одного или двух процентов;
- Повышение влагостойкости, исключающее начало процессов гниения и распространения плесени.
То есть, мы видим устранение практически всех возможных недостатков простых цельных деревянных изделий. Но о паре «подводных камней» также стоит знать:
Недостатки
- Относительно высокая цена. Но ведь за качество стоит платить, к тому же вы сэкономите на отсутствии утепляющих материалов, а если ещё сделать клееный брус собственноручно, то повышение стоимости выйдет и вовсе незначительным;
- Возможное понижение экологичности вследствие применения некачественного клея.
Совет: при осуществлении клейки ламелей в домашних условиях очень внимательно отнеситесь к выбору клея соответствующего качества.
Это позволит сохранить необходимый уровень экологической чистоты готового изделия.
Клей для клееного бруса на акриловой основе
Ход работ
Инструкция, конечно же, начинается с подготовительных этапов.
Этап №1: подготовка необходимого инструмента
Вам понадобятся:
- Ножовка для резки заготовок;
Совет: при наличии возможности рекомендуется использовать электрический лобзик для дерева.
Он значительно упростит и ускорит работу.
- Струбцины. Это чуть ли не самые важные инструменты, которые заменят вам в домашних условиях заводской пресс;
Фото набора струбцин
- Рубанок и шлифовальная машинка для обработки древесной поверхности;
- Кисти для нанесения клея;
Плоские кисти различных размеров
- Рулетка и другие, необходимые для нанесения разметки, приспособления.
Пример подходящей строительной рулетки
Этап №2: подготовка необходимых материалов
- Древесина в виде досок, цельного бруса или реек, в зависимости от того, в какой области вы планируете использовать готовые изделия;
- Клей, который может быть следующих видов:
Тип клея | Внешний вид | Расход, г/м2 |
Полиуретановый | Жидкость свето-коричневого цвета | 200-450 |
Меламин-карбамид-формальдегидный | Жидкость молочно-белого цвета | 300-450 |
Эмульсионный полимер-изоцианатный | Жидкость молочно-белого цвета | 250-400 |
- Ацетон с целью осуществления обезжиривания склеиваемых поверхностей.
Образец бутылки с ацетоном
Этап №3: создание ламелей
Ламель в данном случае – это одна из склеиваемых частей изделия, соединение которых можно осуществлять одним из следующих методов:
Способы осуществления стыковки ламелей
Обозначение на рисунке | Название метода |
а | На гладкую фугу |
б | В четверть |
в | На шпонку |
Совет: при этом старайтесь, чтобы рисунок годовалых колец был направлен в различные стороны.
Это позволит уменьшить эффект коробления.
Для примера возьмём три бруска сечением 100 на 100 мм и будем осуществлять соединение на шпонку.
Для этого:
- Обрезаем каждый пиломатериал до нужной нам длины;
Распилка заготовок
- Строгаем и шлифуем те стороны, которые будут склеиваться;
- Далее у боковых ламелей выбираем паз с одной стороны, а у средней с обеих;
Ламели с выбранными пазами и вставленными ламелями
- Соединяем все элементы на сухую и при необходимости дорабатываем их для более качественной стыковки.
Соединённые элементы
Если вы в дальнейшем планируете применить готовое изделие для монтажа внутренних перегородок в доме, то есть смысл создать дополнительный паз для прокладки проводки.
Проводка в клееном брусе отлично маскируется
Этап №4: предварительная обработка
Чтобы склейка прошла идеально обрабатываем сопрягаемые плоскости:
- Выполняем шлифовку шлифовальной машиной;
Процесс шлифовки
- Устраняем весь собравшийся мусор и древесную пыль с помощью щётки или пылесоса;
- Тщательно обезжириваем ацетоном и оставляем заготовки просохнуть;
- Наносим слой антисептика и снова ждём высыхания деревянных поверхностей;
Пример подходящего антисептика
- Последним шагом осуществляем пропитку дерева антипиреном.
Пример подходящего антипирена
Таким образом, мы получаем гладкие, чистые, защищённые от сырости и возгорания древесные поверхности, готовые к дальнейшим операциям.
Этап №5: склеивание
Теперь переходим к выполнению наиболее важной задачи:
- Разводим клей в соответствии с инструкцией на упаковке в удобной чистой ёмкости;
- Макаем в получившуюся смесь кисть, после чего тщательно обрабатываем ею подготовленные плоскости;
- Вставляем в пазы шпонки и также наносим на них клей;
- Далее соединяем все элементы и крепко стягиваем их струбцинами, после чего оставляем изделия до момента полного застывания клеящего раствора в сухом месте, не подверженном прямому воздействию солнечных лучей.
Промазанные клеем и зажатые струбцинами ламели
Этап №6: окончательная обработка
После того, как изделие полностью высохнет, выполняем финишные операции:
- Строгаем и шлифуем получившийся брус со всех сторон;
- Пропитываем антисептиком и антипиреном;
- После просыхания можем использовать по назначению.
Готовый клееный собственноручно брус
В некоторых случаях для повышения прочности соединения можно использовать специальные шканты, которые вставляются в заранее просверленные отверстия и скрепляют ламели.
Дополнительная фиксация шкантами
Заключение
Клееный брус очень надёжный, тёплый и простой в эксплуатации строительный материал. Единственный его существенный недостаток – это достаточно высокая стоимость. Но, во-первых, за качество следует платить, во-вторых, можно существенно сэкономить, выполнив склеивание собственными силами. Примечательно, что некоторые технические параметры самодельного изделия при этом могут оказаться даже лучше, чем у заводского.
Готовые дуплексы из клееного бруса
Видео в этой статье сможет ознакомить вас с некоторой дополнительной информацией, имеющей прямое отношение к изложенной выше теме. Пробуйте, и у вас всё выйдет.
Доски для склеивания кромок (DIY) | Семейный мастер на все руки
Обновлено: 10 мая 2022 г.
Вот как добиться отличных результатов с минимальными трудностями!
Следующий проект›
Семейный мастер на все руки
Добейтесь лучших результатов при склеивании досок, следуя этим 10 советам профессионалов от профессионалов. К ним относятся советы по нанесению клея, выравниванию зажима и другие.
Эксперты DIY журнала The Family Handyman Magazine
Как соединить два куска дерева встык Видео: Склеивание кромок досок
Кен Коллиер, редактор The Family Handyman, покажет вам , как склеивать кромки досок . Этот базовый навык деревообработки поможет вам во многих различных проектах по деревообработке. Все, что вам нужно, это доски, которые вы хотите соединить, зажимы, клей и вощеная бумага.
Склеивание досок вместе для получения более широких панелей — это удобный навык деревообработки, которому легко научиться. Плотники с хорошо оборудованными мастерскими часто покупают грубые пиломатериалы, а затем распиливают, строгают и соединяют пиломатериалы, чтобы получить прямые края для плотных соединений. Но вы можете получить такие же результаты, тщательно выбирая доски в домашнем магазине или на лесопилке. Ищите доски с похожим цветом и текстурой. Затем осмотрите край каждой доски, чтобы убедиться, что он прямой. Наконец, убедитесь, что доски ровные и не скручены.
Как соединить два куска дерева Совет 2: Расставьте доски, чтобы они выглядели лучшеПометьте доски
Расставьте доски, чтобы они выглядели лучше. Затем нарисуйте на них мелом букву «V», чтобы вы могли легко выровнять их позже.
Для таких проектов, как столешницы, где одна сторона склеенных досок будет более заметной, выберите самую красивую сторону каждой доски, чтобы она была обращена вверх. Если доски различаются по оттенку, расположите их так, чтобы различия как можно лучше сливались. Например, не ставьте темную доску между двумя светлыми. Наконец, переверните доски конец за концом и перетасуйте их, пока узоры волокон не станут естественными и приятными. Когда вы будете довольны результатом, нарисуйте на доске букву «V» (фото) мелом или карандашом. Если вы собираете несколько панелей, также пронумеруйте их. Когда пришло время склеивать доски, просто совместите метки, чтобы убедиться, что доски расположены правильно.
Как соединить два куска дерева Совет 3: Нанесите ровный слой клеяНанесите столярный клей
Нанесите столярный клей гладко и равномерно вдоль края доски, ориентируясь пальцем.
Используйте белый или желтый столярный клей для внутренних работ. Для проектов, подверженных воздействию влаги, используйте водостойкий клей. Нанесите каплю клея диаметром от 1/8 до 3/16 дюйма вдоль края одной доски. Чтобы валик получился ровным по центру края, держите бутылку с клеем одной рукой, а носик — другой. Быстро перемещайте бутылку с клеем вдоль доски, позволяя указательному пальцу двигаться вдоль доски в качестве меры, чтобы капля клея оставалась по центру. Используйте пружинный зажим, чтобы удерживать доску в вертикальном положении, пока вы наносите клей. Вам нужно только нанести клей на одну из двух соединяемых досок.
Как соединить два куска дерева Совет 4: Не наносите слишком много клея. пора убираться. Цель состоит в том, чтобы нанести ровно столько клея, чтобы при сжатии досок по всей длине стыка оставался ровный слой выдавленного клея шириной 1/16 дюйма. Также старайтесь не допускать попадания клея на лицевую сторону досок, где позже могут возникнуть проблемы с отделкой.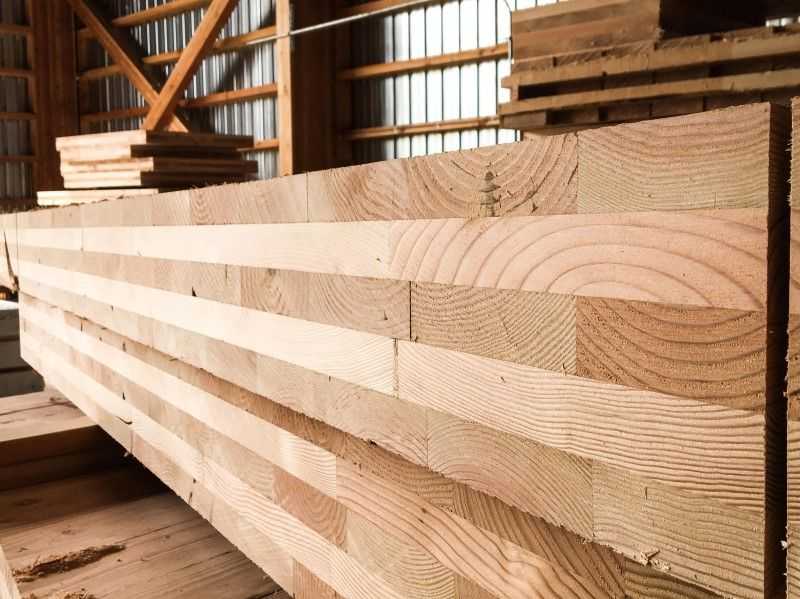
Сдвиньте доски вместе
Совместите доски и сдвиньте их края вместе, чтобы равномерно распределить клей.
Сожмите две доски вместе и двигайте их вперед и назад друг относительно друга. Это лучший способ равномерно распределить клей по краям обеих досок.
Совет: Накройте верхнюю часть зажимов малярной лентой, чтобы не испачкать доски и упростить очистку.
Как соединить два куска дерева Совет 6: Осмотрите клеевое соединение перед зажимомПроверьте покрытие клеем
Ищите места, где клей тонкий или отсутствует. Распределите больше, если необходимо.
Разделите доски и осмотрите края. Цель состоит в том, чтобы на каждом краю был тонкий ровный слой клея. Если есть области, где клей тонкий или отсутствует, нанесите немного больше клея на эти участки, прежде чем скреплять доски вместе.
Ищите выступы клея
Клей должен выдавливаться вдоль соединения. Если нет, добавьте больше зажимов.
Хороший клеевой шов должен иметь ровный валик выдавленного клея по всей длине. Добавьте зажимы в места, где нет выдавленного клея.
Как соединить два куска дерева Совет 8: Тщательно выровняйте верхние поверхностиВыровняйте доски
Отрегулируйте доски, чтобы точно выровнять их и упростить окончательную работу позже.
Вы сэкономите массу времени на шлифовании, убедившись, что верхние поверхности находятся как можно ближе к идеальному уровню. Есть пара хитростей, чтобы сделать это проще. Во-первых, склеивайте и зажимайте только один стык за раз. Это займет немного больше времени, потому что вам придется подождать, пока клей схватится, прежде чем снимать зажимы и добавлять следующую доску. Но гораздо легче добиться хороших результатов, если вы сосредоточитесь на одном суставе за раз. Во-вторых, начните зажимать с одного конца и двигайтесь вдоль досок, убедившись, что верхние поверхности находятся на одном уровне, когда вы затягиваете зажимы. Ощупайте поверхность пальцем и регулируйте доски вверх или вниз, пока верхние части не будут вровень друг с другом. Затем приложите достаточное усилие зажима, чтобы закрыть любые зазоры, и выдавите примерно от 1/16 до 1/8 дюйма. клеевой шарик.
Соскребите мягкий клей.
При комнатной температуре и средней влажности выдавленный клей будет готов к соскабливанию примерно через 20 минут. Подождите, пока клей не изменит свою жидкую консистенцию на желеобразную. Затем соскребите его стамеской или шпателем. Если хомуты мешают, их можно смело снять примерно через 20 минут в нормальных условиях. Однако с наклеенными панелями обращайтесь осторожно, так как клей еще несколько часов не достигнет максимальной прочности.
Подкладывайте изогнутые доски
Подкладывайте или добавляйте дополнительные зажимы, чтобы исключить изгибы при склеивании.
Склейки с бантиками невозможно разгладить после того, как клей схватится. Проведите линейкой по склеенным доскам, чтобы убедиться, что они ровные. Выровняйте их, вбивая прокладки между досками и зажимами. Если сборка искривлена, добавьте еще один зажим поверх досок.
Совет: Поместите деревянные планки между зажимами и досками, чтобы защитить края досок.
Необходимые инструменты для этого проекта по соединению двух кусков дерева
Подготовьте необходимые инструменты для этого проекта «Сделай сам» перед началом работы — вы сэкономите время и нервы.
- Зажимы
- Молоток
- Поверочная линейка
- Стамеска по дереву
Пружинный зажим
Материалы, необходимые для соединения двух деревянных деталей, проект
Избегайте походов за покупками в последнюю минуту, подготовив все материалы заранее. Вот список.
- Мел
- Прокладки
- Клей для дерева
Первоначально опубликовано: 24 июня 2019 г.
Похожие проекты
7 способов склеивания дерева без струбцин
Как говорится, всегда нужно на одну струбцину больше, чем есть на самом деле. Или, может быть, вы работаете с небольшими кусками дерева, и вы просто не можете их зажать. Не волнуйся! Склеить дерево без струбцин очень просто!
Чтобы склеить древесину без зажимов, наносите столярный клей мазками с небольшим промежутком между мазками. Добавьте суперклей в эти места, затем сожмите деревянные части вместе. Держите дерево вместе в течение нескольких секунд. Суперклей застынет, удерживая древесину на месте, пока клей для дерева сохнет.
Если это не сработает (скажем, у вас дома нет суперклея), не волнуйтесь! У меня есть целый список техник, так что продолжайте читать!
Примечание. Этот блог содержит партнерские ссылки. Если вы нажмете и совершите покупку, я могу получить компенсацию (без каких-либо дополнительных затрат для вас).
Способ 1: Суперклей
Это мой любимый метод, так как он очень универсальный, а суперклей есть у большинства людей дома.
Начните с нанесения столярного клея на стык, оставляя зазоры в клее.
В эти зазоры капните пару капель суперклея.
Затем держите деревяшки вместе несколько секунд. Суперклей схватывается очень быстро, поэтому этих нескольких секунд будет достаточно, чтобы суперклей приклеился. Суперклей будет удерживать древесину на месте, пока клей для дерева сохнет.
Теперь, просто чтобы уточнить, вы не хотите использовать только суперклей. Клей для дерева крепче, когда скрепляет два куска дерева вместе (даже прочнее, чем шурупы!)
Но клей для дерева достаточно прочен, чтобы временно удерживать соединение на месте, пока клей для дерева сохнет, что делает его идеальным средством для использования, если вы не нет зажима!
Способ 2. Малярная лента
Малярная лента — отличный вариант, если вы склеиваете вместе небольшие куски дерева. Оторвите кусок ленты достаточной ширины, чтобы покрыть стык, и, желательно, достаточной длины, чтобы приклеить ленту на близлежащую сторону.
Нанесите клей и прижмите доски друг к другу, затем заклейте малярным скотчем. Постарайтесь сделать ленту максимально тугой; вы хотите соединить куски дерева как можно сильнее.
Это не идеальное решение; малярная лента не будет оказывать такого сильного давления на детали. Но впринципе здорово!
Метод 3: использование тяжелых предметов
Это мой любимый метод, возможно, потому, что я часто склеиваю вещи таким образом, чтобы гравитация могла мне помочь.
Например, я однажды добавил молдинг на панель толщиной 1/4″ на двери. Я бы с удовольствием прибил его на место, но 1/4-дюймовая панель была слишком тонкой, чтобы использовать гвозди.
Я положил пару книг на молдинг и оставил их на час или около того. Прошло больше года, а лепка до сих пор держится!
Забавный факт: как бы я ни любил Гарри Поттера, я определенно чаще использую книги для склеивания кусочков, чем читаю их.
В другом примере я сделал венок из кусочков дерева. Чтобы удержать все на месте, хватило нескольких банок с краской.
Используйте любой тяжелый предмет, который сможете найти — держу пари, у вас получится!
Метод 4: Гвозди со штифтами
Этот метод является золотым, если у вас есть пистолет для гвоздей со штифтами. Если у вас нет пистолета для гвоздей, проблем больше, чем пользы.
Гвоздильные пистолеты забивают гвозди быстро и эффективно, а если вам нужно забить гвоздь, вы, вероятно, будете слишком сильно покачивать древесину, чтобы получить хороший стык.
В любом случае, если у вас есть гвоздезабивной пистолет, это быстрый и простой способ временно закрепить дерево на месте, пока клей сохнет. Вы оставите гвозди на месте навсегда, но как только клей высохнет, это то, что делает структурную поддержку.
Кроме того, использование пистолета для гвоздей означает, что вы можете перемещать деталь и продолжать строительство, пока клей сохнет. Большой плюс.
Я приколотил гвоздями к органайзеру для ящика, и весь проект был выполнен менее чем за час. Я просто добавил клей, соединил детали, затем добавил пару гвоздей и перешел к следующему стыку.
Метод 5: банджи-шнур или веревка
Это действительно отличный метод, если вы строите что-то большое и у вас закончились большие зажимы. Добавьте клей и соберите все в ряд. Затем оберните банджи-шнур или веревку вокруг конструкции и затяните как можно сильнее.
Банджи-шнуры, вероятно, будут работать лучше, чем веревка, из-за эластичности, но любой из них справится со своей задачей.
Способ 6. Ремни с храповым механизмом
Подобно методу с веревкой/банджи-шнуром, ремни с храповым механизмом можно использовать для закрепления дерева на месте. Преимущество ремней с храповым механизмом заключается в том, что функция храпового механизма помогает оказывать давление на сустав.
Суть в том, чтобы крутить медленно — не следует прилагать слишком много усилий, иначе конструкция может деформироваться, в зависимости от того, как вы склеиваете детали. Вы просто хотите применить достаточное давление, чтобы затянуть соединение.
Также стоит отметить, что если вы слишком сильно затянете храповые ремни на мягкой древесине, это может привести к образованию вмятин на древесине. Это вряд ли произойдет с твердой древесиной, но если вы работаете с мягкой древесиной, будьте осторожны, не затягивайте слишком сильно.
Способ 7. Струбцины своими руками
На самом деле очень легко сделать быстродействующую струбцину, если вам это нужно. Вам понадобится несколько кусков дерева, чтобы сделать основную «зажимную» часть, и клиновидный кусок дерева.
Привинтите или прибейте гвозди друг к другу куски дерева так, чтобы они были немного больше, чем дерево и соединение, которое вы собираетесь сделать.
Затем заклейте сустав и поместите его в «зажим». Используя молоток, вбивайте клин на место, пока он не войдет плотно между куском дерева и соединением, которое вы пытаетесь склеить.
Когда подождите, пока клей высохнет, и наслаждайтесь!
Бонусный метод: шурупы с потайными отверстиями
Я оставил этот метод напоследок, потому что считаю его глупым. Многие люди рекомендуют использовать винты / соединения с карманным отверстием (Kreg Jig), чтобы закрепить соединение на месте, пока клей сохнет.
Проблема в том, что винты с отверстием в кармане должны быть зажаты сами по себе, чтобы получить хорошее соединение. Экспонат A: Эти барные стулья. Это был один из моих первых крупных проектов по деревообработке, и я расколол пару кусков дерева, прежде чем понял, что соединения карманных отверстий действительно нужно зажимать.
В противном случае небольшие движения делают древесину более восприимчивой к растрескиванию. Конечно же, как только я начал зажимать свою древесину, у меня больше не было проблем с раскалыванием древесины.
Все это говорит о том, что соединения с карманными отверстиями — это метод, который многие рекомендуют, если вы не можете зажать древесину. Я говорю: стыки с отверстием в кармане великолепны, но они не отменяют необходимости в зажиме.
8 способов соединения встык, которые удерживают
Шиповые соединения
Шиповые соединения обеспечивают склеивание торцевых или краевых поверхностей с соединениями встык для более прочного клеевого соединения.
Любое соединение, которое стыкуется встык, будет слабым, потому что вы склеиваете древесные волокна по их пористым концам, а не по бокам. (Представьте, что вы пытаетесь склеить две соломинки для питья вместе на концах, а не вдоль их сторон.) К счастью, вы можете усилить соединения встык в тех редких случаях, когда они необходимы, например, при соединении двух частей молдинга на длинная стена или максимальное использование частей, которые слишком короткие для вашего проекта, но слишком длинные, чтобы их можно было выбросить.
Суть в том, что вы должны либо добавить усиления, такие как пластины, дюбели или винты, либо вырезать соединение таким образом, чтобы создать механическую прочность и обнажить больше поверхности или кромки для более прочного соединения, как показано на рисунке. над , фрезерованным с шиповым соединением. Ознакомьтесь с этими восемью решениями, от простого до красивого.
Таблица
Простые, практичные лямки
Используйте простые металлические или фанерные лямки для усиления стыковых соединений, где их можно спрятать или где внешний вид не важен, например, на обратной стороне широкого карниза, где вы не можете позволить себе любые траты. Изготовление ремешков нестандартного размера из 1 ⁄ 4 ” фанера экономит ваши деньги и обеспечивает прочную поверхность для склеивания.
Чтобы установить деревянную планку, отрежьте ее настолько широко, насколько позволяет заготовка. Если вы соединяете детали с профилем на противоположной стороне, например, на молдинге, расположите отверстия для винтов в самых толстых точках профиля, например, на вершине гребня или изгиба. приклейте вторую половину ремешка и прижмите сборку к плоской поверхности.Для плотного соединения поднимите другую заготовку примерно на 1 ⁄ 4 “на расстоянии 3 фута от соединяемого конца. Затем прижмите детали друг к другу, добавляя монтажные винты, как показано под . Положите обе детали на ровную поверхность и дайте клею высохнуть, прежде чем обрабатывать соединение.
Привинчиваемая доска с 5-м винтом
Восемь шурупов #8×1/2″ с плоской головкой и клей плотно скрепляют это сквозное соединение молдинга.
Шурупы с потайными отверстиями
Еще один простой способ быстро скрепить стыковые соединения. Чтобы установить винты с потайными отверстиями, используйте приспособление для потайных отверстий, чтобы просверлить наклонное отверстие через одну заготовку и в другую. Винт, вставленный в отверстие, стягивает детали вместе, как показано на рисунке 9.0184 ниже . Заготовки должны иметь толщину не менее 1 ⁄ 2 дюймов (с помощью винтов 1 дюйм), и вы можете прикрепить детали толщиной 1 1 ⁄ 2 дюймов или толще с помощью винтов 2 5 ⁄ 8 дюймов. Узнайте больше об изготовлении столярных изделий с карманными отверстиями.
Плата с отверстиями под винты
Карманные отверстия, просверленные в задней части (вверху), невидимы спереди. Затем винт стягивает детали вместе (внизу).
Шлицы обеспечивают внутреннюю прочность
Сплайны создают контактную поверхность клея, устойчивую к изгибу. Используйте сквозные шлицы для легкого соединения с видимыми шлицами. Отметьте каждое соединение на его верхней поверхности и установите пильный диск 3 ⁄ 4 ” на высоту? — половину длины шлицов. Сориентируйте верхние поверхности каждой детали относительно направляющей планки, чтобы пазы между частями были одинаковыми. Для закрепления очень длинных деталей добавьте вспомогательную направляющую.Используя опорный блок, чтобы предотвратить отрыв, сделайте надрезы на концах, чтобы сформировать канавку шириной в одну треть толщины вашего материала.
Затем выстрогайте и отпилите шлицевую заготовку, чтобы она соответствовала ширине и общей глубине канавок. Вы можете сделать шлицы из фанеры или твердого материала. Если вы выбираете сплошную заготовку, как показано под , сориентируйте шлицевое зерно параллельно с зерном заготовки. Вставьте сплайн; затем склейте и зажмите детали.
Шлиц между досками
Этот шлиц измеряет треть толщины соединяемых деталей, волокна идут перпендикулярно длине шпонки.
Чтобы немного потрудиться, создайте скрытый сплайн, подобный показанному ниже , который исчезнет после того, как вы соберете соединение. Мы сделали это соединение, используя прямую фрезу 1 ⁄ 4 ” на фрезерном станке, установленном на столе. Установите высоту фрезы чуть больше половины ширины шлицов. толщина концов заготовки
Соединение
Скруглите углы шлицев для плотного прилегания к пазу, но обрежьте шлицы на 1/32 дюйма уже общей глубины пазов.
Затем соберите простой шаблон для направления заготовок. Из лома чуть толще ваших заготовок вырежьте две упорные колодки. Разместите их на расстоянии, равном двойной ширине вашей заготовки за вычетом врезных вставок с обоих краев. Затем прикрепите крестовину, которая 1 ⁄ ⁄ 2 ” шире, чем высота фрезы, для дополнительной безопасности и контроля. Закрепите соединенные стопорные блоки готового зажимного приспособления с упором фрезерного стола так, чтобы они находились на одинаковом расстоянии от фрезы, как показано . ниже .Чтобы незначительные ошибки регулировки направляющей не создавали неровного соединения, отметьте верхние грани ваших заготовок и расположите их лицом к себе при фрезеровании пазов. Используя нажимную панель, прижмите заготовку к упору фрезера и вниз по краю правого стопорного блока к столу фрезера. Сдвиньте заготовку к левому стопорному блоку, как показано ниже , и поднимите ее, не касаясь сверла.
Оранжевая прижимная пластина к доске
Прижимная пластина надежно удерживает этот тестовый лом на упоре фрезера. Добавьте высокий вспомогательный упор, чтобы длинные заготовки не наклонялись.
Сверло и дюбель
Соединение на дюбелях, показанное под , обеспечивает еще одно невидимое соединение. Соедините соединяемые детали встык и отметьте положение дюбелей на обеих сторонах. Расположите приспособление для установки дюбелей над отметками и просверлите отверстия 1 ⁄ 16 ” глубже, чем половина длины дюбеля. Нанесите клей на одну деталь в отверстия, вставьте дюбели и прижмите ее к плоской поверхности. другую часть, склейте торцевые волокна и отверстия, соедините части вместе и зажмите, пока они не высохнут.0003
Соединение
Скошенные косые соединения
Обрезая концы под углом перед их соединением, вы обнажаете более длинное волокно для лучшего соединения. Чем острее угол, тем больше и качественнее будет поверхность склеивания. Например, скос под углом 45° увеличивает площадь склеивания примерно на 40 процентов и помогает скрыть линию стыка на профилированной поверхности. Чтобы совместить углы, отрежьте один конец на одной стороне пильного диска и ответный конец на противоположной стороне, как показано ниже . Даже если угол скоса вашего лезвия немного отличается от 45 °, детали будут сопрягаться.
Пильное полотно под углом
Обрежьте концы молдинга на противоположных сторонах полотна для плотного соединения встык.
Чтобы соединить половинки, прижмите нижнюю к плоской поверхности. Затем прижмите верхнюю часть вниз к фаске на нижней части. При необходимости выровняйте детали линейкой.
Соединение под углом
Попробуйте это соединение, чтобы увеличить поверхность склеивания. Начните с изготовления угловой направляющей 4:1, которая более чем в два раза превышает ширину заготовок. (Направляющая, показанная на фотографиях, имеет размеры 5×20 дюймов для заготовки шириной 2 дюйма.) Одинаковые планки с обеих сторон треугольника помогают расположить его на лицевой стороне обеих заготовок, как показано на рисунке 9. 0184 ниже . Отметьте углы на обеих заготовках и распилите их в пределах 1 ⁄ 32 ” от линий на сторонах отходов.
Разметка треугольного куска доски
Чтобы разметить более широкие молдинги, просто увеличьте размер этого 4 :1 угловая направляющая. ленточной пилы под угловой направляющей и рядом с узким наконечником, как показано на рисунке 9.0184 ниже , чтобы помочь стабилизировать основание фрезера и зафиксировать рез на конце. Затем обрежьте оставшиеся отходы до отмеченной линии. Переверните направляющую вверх дном и обработайте другую заготовку.
Шлифованная сторона доски
Проведите краем основания фрезера по угловой направляющей 4:1, чтобы края клея были гладкими.
Чтобы собрать соединение, склейте скошенные края и соедините их неплотно, чтобы оба края образовывали прямые линии. Затем прижмите обе детали к плоской поверхности, чтобы предотвратить их скольжение при сжатии соединения, как показано на рисунке 9. 0184 ниже.
Зажимная пластина
Угол 4:1 увеличивает площадь склеивания этого косого соединения более чем на 450 процентов.
Основные соединения внахлестку
Привлекательные, прочные и простые в изготовлении на настольной пиле или фрезерном столе соединения внахлест создают поверхности склеивания лицом к лицу. Чем больше перехлест, тем лучше связь.
Чтобы сделать простое соединение внахлестку, начните с разметки разрезов. Для получения одинаковых нахлестов поместите обе заготовки рядом друг с другом так, чтобы концы были заподлицо и лицевой стороной вверх на одной детали и вниз на другой. Отметьте «X», где вы будете резать колени на каждой части; затем отметьте линию на обеих частях и продолжайте линии от граней до краев на обеих частях, как показано на рисунке 9.0184 ниже .
Карандашная разметка угольником
Используйте ширину ваших заготовок, чтобы отметить длину нахлеста.
Затем установите набор пазов шириной не менее 5 ⁄ 8 дюймов на настольную пилу и установите высоту лезвия, чтобы резать половину толщины ваших заготовок. Проверьте посадку соединения, используя обрезки, как показано ниже . Лицевые стороны тестовых обрезков должны быть заподлицо, с плотным контактом древесины с древесиной в местах нахлеста
Стопка досок, нарезанных друг на друга
Точно отрегулируйте высоту лезвия плинтуса, используя пробные пропилы на ломе такой же толщины, как заготовки.
Теперь разрежьте паз от отмеченных линий стыков до концов, как показано ниже . Удлинитель упора помогает позиционировать каждый проход и уменьшает отрыв. (Одна деталь будет обтачиваться лицевой стороной вниз.)
Маркировка полунахлеста на доске
Наметьте начало и конец полунахлеста на обеих заготовках вместе. Затем удалите материал между ними.
Затем проверьте соединение, как показано на рисунке ниже и проверьте наличие зазоров между нахлестами или между рабочим столом или верхней частью пилы и одной из сторон. Приклейте и зажмите внахлест для постоянного соединения.
Доски с маркировкой A и B
Это соединение внахлест создает прочное соединение лицевой стороны и волокон между частями. Вы можете увеличить или уменьшить перекрытие по мере необходимости.
Соединение внахлестку на столе
Это соединение сочетает в себе прочность соединяемых деталей с большой поверхностью клея соединения внахлест. Чтобы сделать это, добавьте 1 ⁄ 4 ” по ширине заготовки. (Вы удалите его позже, когда будете настраивать соединение.) Затем измерьте это расстояние от конца заготовки. Отметьте обе детали одновременно, как описано для базовое соединение внахлест Скопируйте эти маркировки на пару пробных деталей толщиной ваших окончательных заготовок
Используйте ту же настройку паза, что и для основного соединения внахлест, но вместо этого установите высоту лезвия ровно на одну треть толщины ваших заготовок. Затем сделайте шпунт на обеих деталях и на двух пробных заготовках от маркировки кромок до концов, как показано на рисунке ниже.
Фальцевая часть вместе
Для идеального совпадения половин внахлест, сделайте фальц одновременно на обеих заготовках.
Теперь установите высоту лезвия плинтуса ровно на две трети толщины заготовок. Используя обрезки, проверьте и отрегулируйте глубину пазовой части до тех пор, пока более толстая часть ближе к концу не окажется внутри более тонкой части, так что лицевые стороны обеих частей будут на одном уровне, как показано ниже.
Отходы теста
Угловой шпунт на одном образце должен едва касаться дна цапфы на другом.
Измерьте расстояние от выступа цапфы до половины ширины заготовки и поставьте там отметку. Закрепив обе детали на угловом упоре, сделайте два прохода, чтобы определить ширину этой второй пары пазов, как показано ниже .