Как делают шины для автомобилей?
Говоря об автомобильной резине, мы редко задумывается из чего и как делают этот товар. А между тем всё не так просто, как может показаться на первый взгляд. Технология производства покрышек включает множество этапов и нюансов. Начальной стадией создания автомобильных шин является разработка их профиля и рисунка протектора посредством специализированных компьютерных программ объёмного моделирования. Далее компьютер просчитывает и анализирует эффективность шины в различных ситуациях и условиях эксплуатации, после чего устраняются недостатки, пробные образцы нарезаются на специальных станках вручную и тестируются в реальных условиях.
В результате испытаний происходит сбор информации для сравнения с показателями лидеров рынка того же класса, после чего осуществляется финальная доводка, предшествующая запуску на конвейер и массовому производству.
Изготовление резиновой смеси
Материал, из которого изготовлена покрышка, имеет первостепенное значение. Следует понимать, что шины различных производителей существенно отличаются в первую очередь свойствами резины, состав которой зачастую является коммерческой тайной. Столь серьёзный подход объясняется тем, что резиновая смесь определяет технические характеристики шин, включая:
- Уровень сцепления с дорогой.
- Долговечность и надежность.
- Сезонность и износостойкость.
Состав резины современных автопокрышек включает множество материалов и компонентов: всевозможных присадок и химических соединений, которые и определяют свойства и поведение шин. Подбором и комбинацией этих элементов занимаются целые лаборатории в каждой компании, ведь именно химические добавки и их дозировка позволяют изделию превзойти конкурентов. Базой же для всех служит обычная резина, состав которой ни для кого не является секретом. Она состоит из:
- Каучука, который бывает изопреновым (натуральным) и синтетическим, и является основой резиновой смеси (от 40 до 50 процентов состава).
- Технического углерода (промышленная сажа), благодаря молекулярным соединениям которого шина имеет не только чёрный цвет, но и становится прочной и устойчивой к износу и температурам (от 25 до 30 процентов состава).
- Кремниевой кислоты, повышающей показатели сцепления покрышки с влажным покрытием, и применяемой в основном иностранными шинниками (примерно 10 процентов состава).
- Смол и масел, выступающих вспомогательными составляющими для обеспечения мягкости и эластичности изделия (около 10-15 процентов состава).
- Вулканизирующих агентов, роль которых чаще всего отводится соединениям серы и специальным активаторам.
Отметим, что российский каучук признан лучшим во всём мире, а потому востребован и применяется большинством ведущих мировых компаний-производителей. А поскольку синтетический каучук уступает натуральному по всем показателям, то в этой области РФ останется лидером ещё очень долго.
Производство компонентов
Технологический процесс создания шины, кроме прочего, включает в себя несколько параллельных этапов изготовления её компонентов, среди которых:
- Прорезиненная лента – это первичная заготовка для изготовления протектора, разрезаемая в зависимости от требуемого размера.
- Брекер и каркас – элементы, несущие ответственность за устойчивость к порезам, прорывам и прочим повреждениям. Также брекер и каркас отвечают за жёсткость всей конструкции покрышки.
- Борт шины — является наиболее жёсткой её частью, и обеспечивает герметичность при монтаже на обод колеса.
В качестве материала для каркаса и брекера современных шин служит либо металлокорд, либо стекловолокно. Последнее применяется при изготовлении покрышек класса «премиум», в то время как металлокорд незаменим в моделях, предназначенных для оснащения грузового автотранспорта.
Сборка и вулканизация
Заключительным этапом производства автопокрышки является сборка. Данная технологическая процедура выполняется методом наложения слоев каркаса, боковин, борта и протекторной части, и осуществляется на специальном сборочном барабане. После компоновки и придания нужной формы все составляющие элементы соединяются в монолитную конструкцию посредством процедуры вулканизации. Далее изделие проходит необходимые проверки, маркируется и отправляется на рынки по всему миру.
Видео по теме:
wheel-info.ru
Как сделать самодельную автошину – (старые методы) » Полезные самоделки
Старые способы самостоятельного изготовления автомобильных и мото шин.
Автомобильные и мотоциклетные изготавливают с наличием так называемого «каркаса», силовой части, воспринимающей толчки и удары, которые испытывает при движении колесо. Даже на ровной дороге количество таких толчков весьма велико. Если изготовить шину из одной только резиновой массы (а модельные шины именно так и изготовляются), она очень быстро потеряет форму и разрушится, не выдержав прилагаемых к ней нагрузок, Чтобы этого не случилось, в конструкцию шины вводится каркас.
Он состоит из большого количества прочных нитей, которые расположены по всему ее периметру и образуют как бы сетку, которая способна выдерживать высокое давление заключенного в шине воздуха и большое количество толчков и ударов, воспринимаемых шиной извне. А для того, чтобы шина надежно держалась на ободе колеса, в ее борта заформовываются кольца из гибкой стальной проволоки.
А для асфальта изготовляются шины с более мелким рисунком. Поперечный разрез шины показан на рис. 1. и рис. 2
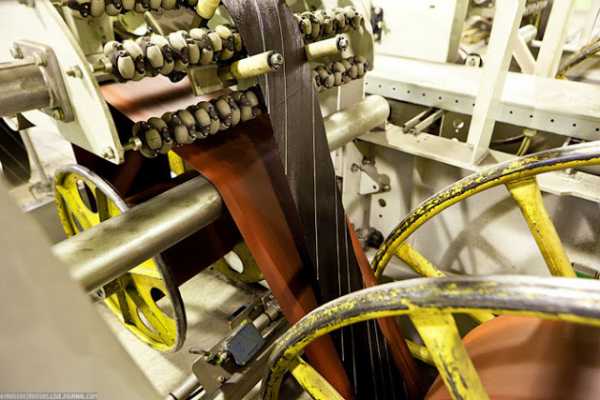
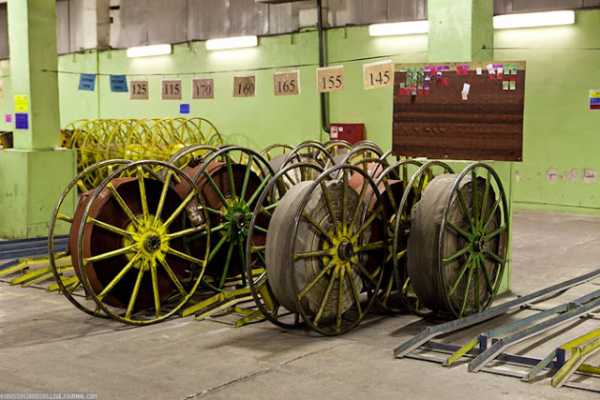
Рис.1. Поперечный разрез самодельной шины.
На микромотоциклах шины работают в исключительно тяжелых условиях. К примеру, если нормальное мотоциклетное колесо при прохождении десяти метров дороги должно повернуться вокруг своей оси восемь раз, то колесо микромотороллера совершает в три или четыре раза больше оборотов, поскольку диаметр его меньше.
Так, при скорости 70 км/час колесо микромотоцикла диаметром 320 мм должно делать 1200 об/мин. При таких больших оборотах частота деформаций шины и нагрев очень велики. Перегрев шины приводит к ее быстрому разрушению. В самых неблагоприятных условиях находится шина заднего колеса.
У микромотоциклов примерно г/з веса приходятся на заднее колесо, которое к тому же охлаждается хуже, чем переднее. Вследствие небольших размеров микромотоциклов и микромотороллеров расстояния между горячим двигателем и колесами очень невелики. От этого шины могут быстро перегреваться.
Поэтому самой трудной проблемой при проектировании шин для микро мототранспорта является увеличение их теплоотдачи. Стенки шины, имеющие большую теплоемкость, не позволяют рассеивать в окружающее пространство необходимое количество тепла.
Уменьшать толщину покрышки можно только в определенных допустимых пределах, поскольку нагрузка на нее очень велика. Учитывая все это, при конструировании микрошин мы руководствуемся следующими соображениями: каркас покрышки изготовляется из двух слоев высокопрочного капронового корда, больше других материалов отвечающего условиям работы в шине, поскольку он обладает малым весом и высоким сопротивлением многократным изгибам. Мы изготовили несколько покрышек из вискозного и хлопчатобумажного корда, каркасы которых ввиду малой прочности пришлось делать 4-х слойными. эти покрышки быстро выходили из строя из-за перегрева.
При накачивании шины воздухом в нитях слоев корда действуют большие растягивающие усилия. Величина этих усилий зависит не только от давления воздуха, но и от количества слоев корда, и от геометрического профиля шины, ее размеров, нагрузки и ширины обода. Каждый профиль шины рассчитан на определенную ширину обода. Применение ободьев от детских роллеров (самокатов) не обеспечивает необходимых условий для нормальной работы шин, даже при скорости движения 40 км/час и нагрузке порядка 50 кг. Для обеспечения необходимых условий работы ободья должны быть значительно шире (не менее 35-З8 мм между буртиками). В этом случае можно изготовить покрышки, рассчитанные на нагрузку 60-80 кг и скорость порядка 60-70 км/час.
Геометрический профиль спроектированной нами шины приведен на рис. 2 в натуральную величину, а конструкция покрышки изображена на рис. 3.
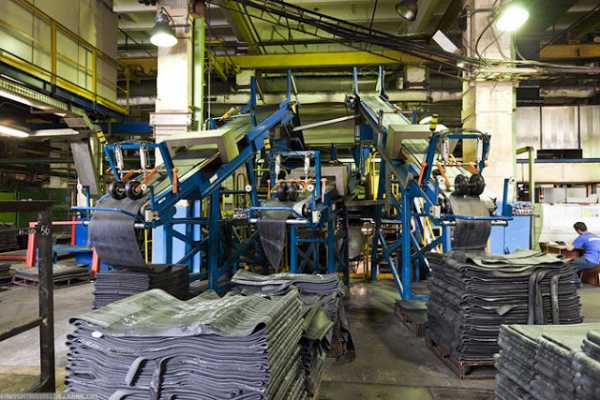
Рис.3. Конструкция авто шины.
Технология изготовление шин (мини завод по производству шин
При работе покрышки важно, чтобы нити корда были хорошо изолированы,, друг от друга резиной и не перетира лись. Для этого между слоями корда (хотя он уже обрезинен) прокладывается тонкий слой резины (0,5 мм), так называемый «сквидж». Для этой цели можно использовать сырую резину, применяемую для ремонта автомобильных камер в автохозяйствах. Наличие слоя эластичной резины между слоями корда и такой же резины поверх всего каркаса не только предотвращает перетирание нитей корда, но сообщает каркасу эластичность и увеличивает прочность связи между слоями каркаса и следующим слоем, называемым брекером.
Брекер – это дополнительный слой эластичной резины толщиной 2- 2,5 мм, служащий для повышения прочности связи каркаса покрышки с протектором. Он предохраняет каркас от возможных пробоев и повреждений. При резких торможении и ускорении получается внутренний сдвиг между малоэластичным, но износостойким слоем протекторной резины и каркасом. Задача брекерного слоя – погасить энергию этого сдвига, не дать шине расслоиться. Резина брекера должна быть эластичной, теплостойкой и прочной на разрыв.
При сборке шины брекерная лента делается шире протекторной на 5-6 мм. Для нее наиболее подходящей является готовая сырая резина на основе изопренового или натурального каучука. Но поскольку такую резину не всегда возможно достать, нами с успехом применяется следующий способ: берем обычную сырую резину, предназначенную для ремонта камер (толщина примерно 0,8-1 мм) и кусок натурального каучука для изготовления резинового клея. Из него остро отточенным ножом вырезаются пластинки толщиной 1-1,5 мм. Затем, тщательно промазав клеем для горячей вулканизации заготовленную полоску из сырой резины и нарезанные пластинки каучука и дав клею подсохнуть 5-6 мин., наклеиваем пластинки на полоску сплошным слоем, без щелей и наползания друг на друга.
Полученная двухслойная лента приклеивается к каркасу стороной из каучуковых пластинок, а затем на нее наклеивается протекторный слой. Протектор изготовляется из высокопрочной, износостойкой резины. Он располагается только на беговой дорожке покрышки. Его толщина зависит от величины самой шины. Для наших шин, имеющих диаметр 320 мм, толщина протектора должна быть в пределах 4-6 мм. Качество протектора определяет долговечность шины, поэтому требования к резине, из которой он изготовляется, несколько иные, чем к резине брекерного слоя. Наилучшей оказывается резина, предназначенная для ремонта протекторов покрышек автомобилей.
Рисунок протектора может быть различным, в зависимости от назначения шины и условий эксплуатации.
Показанный на рис. 4 рисунок протектора является универсальным. Шины с таким протектором одинаково хорошо работают на дорогах с самыми различными покрытиями.

Рис.4. Универсальный рисунок протектора шины.
Изготовление матрицы для получения такого рисунка протектора не представляет трудностей и может быть выполнено даже в домашних условиях.
Для этого берется полоса мягкого алюминия толщиной 4-6 мм (толщина материала определяет желаемую глубину рисунка) и в ней согласно рис. 5 высверливаются отверстия. Затем полоса разрезается ножовкой вдоль по осевой линии на две равные части. В каждой части выпиливаются фасонные пазы, острым ножом снимаются фаски и заусенцы, напильником выравниваются все неровности, а концы, оставшиеся после выпиливания шипов, стачиваются под углом 45°.
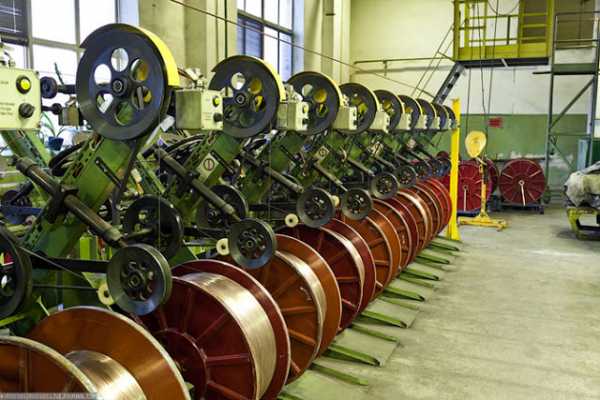
Рис.5. изготовления матрицы для рисунка протектора.
После окончательной зачистки шкуркой части матрицы приклепываются заклепками из мягкой алюминиевой проволоки к половинкам пресс формы с ее внутренней стороны. Такая конструкция пресс формы позволяет избежать сложных фрезерных работ. Сама пресс форма изготовляется путем отливки в землю, из алюминия или другого легкого сплава (нами были использованы для этого старые поршни от автомобильных двигателей, собранные на свалке).
Оснастка для отливки (форма и ящик) показаны на рис. 6. Расплав алюминия можно вести прямо в форме, нагревая его пламенем газовой горелки или, как обычно, в муфельной печи. Мы, например, выполнили отливку на месте ремонта металлической ограды парка, где велись газосварочные работы.
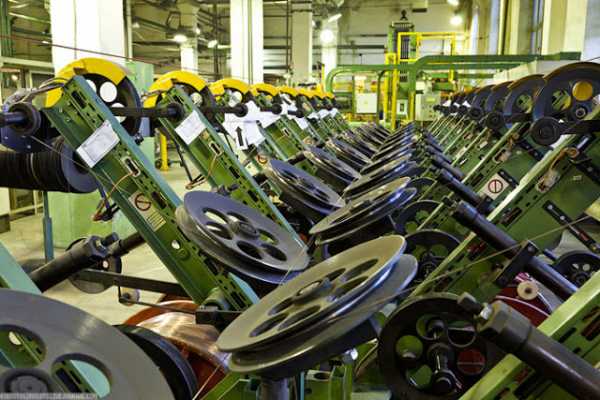
Рис.6. Оснастка для отливки шин.
Отливки надо вынимать из формы, не разрушая ее, и только после полного их остывания. Ускорять остывание, смачивая отливку водой, нельзя.
Подготовка матрицы заканчивается сверлением отверстий под болты, стягивающие ее во время варки покрышки.
Отлитые заготовки для пресс-формы обрабатываются на токарном станке в соответствии с рисунком. Особое внимание должно быть уделено подгонке половинок формы и дисков друг к другу, а также тщательной наклепке решетки протектора (рис. 2).
Сборка покрышки
В качестве оправки для сборки мы используем негодную («лысую», но не деформированную) покрышку от детского самоката. Сначала на наждаке, а потом – шкуркой разной зернистости с нее удаляются остатки протектора, чтобы поверхность стала совершенно гладкой.
Заправив внутрь обработанной таким путем покрышки камеру и слегка подкачав ее воздухом, сшиваем внутренние края покрышки прочными нитками, тщательно прихватывая при этом и бортовые кольца. Расстояние между бортами должно быть одинаковым по всей окружности (рис. 9).
Порядок сборки покрышки на оправке
1) Приготовление кусков обрезиненной кордовой ткани.
Их длина должна быть такой, чтобы после оборачивания вокруг оправки под углом 52° на загиб вокруг бортового, (проволочного) кольца оставалось 20-25 мм.
2) Накачивание воздухом оправки.
3) Укладка первого слоя корда.
При этом необходимо слегка растягивать середину заготовок, увеличивая тем самым расстояние между нитями с таким расчетом, чтобы они были одинаковыми по всему периметру колеса. Нити корда должны ложиться ровно, в один слой, и не наползать друг на друга даже в месте расположения бортового кольца (там, где густота нитей максимальна). Для облегчения укладки не рекомендуется делать слишком широких заготовок корда, удобнее всего ширина 40-50 мм.
4) Укладка бортовых колец из стальной проволоки диаметром 0,25-0,3 мм – очень ответственная операция.
Для этого необходимо сначала вырезать полоску из 3-мм резины (например, из старой автомобильной камеры) шириной 10-12 мм и из нее склеить кольцо диаметром несколько меньше посадочного места обода. Это кольцо натягивается на обод, затем из сырой резины толщиной 0,5 мм вырезается ленточка шириной 10 мм и из нее делается один виток вокруг надетого на обод кольца. Наматывая после этого проволоку (8- 10 витков) непосредственно на сырую резину, большой натяг делать не следует, так как можно прорезать тонкой проволокой резину насквозь. Скрепив концы готового кольца скруткой, обильно смажем его клеем, дадим подсохнуть и завернем, не снимая с обода, в ленточку из сырой резины, на которую оно наматывалось. Готовое кольцо снимается с обода вместе с резиновым кольцом, которое можно использовать многократно.
Промазывание клеем и обрезинивание проволочного кольца необходимо для того, чтобы проволока не отслаивалась от борта покрышки при ее дальнейшей обработке.
Для каждой покрышки надо изготовить два кольца. Они тщательно промазываются клеем и укладываются на свои места после укладки первого слоя корда.
5) Оклейка сырой резиной толщиной 0,5-0,7 мм поверхности первого слоя корда.
Приклеенная резина не должна наползать на бортовые кольца. Но не должно оставаться больших промежутков между ними; обклеивать удобнее, предварительно нарезав, сырую резину в виде ленты, немного более широкой, чем расстояние между бортовыми кольцами, а затем – после приклейки – удалить ее излишки при помощи кривых маникюрных ножниц.
6) Заворачивание концов корда вокруг бортовых колец с приклейкой их к слою сырой резины (сквиджу).
Приклеенные концы не должны наползать друг на друга и быть длиннее 15-20 мм. Если они получились длиннее, их необходимо обрезать.
7) Укладка второго слоя корда. Она производится так же, как и первого, с той лишь разницей, что угол наклона нитей корда должен быть противоположен углу наклона первого слоя. Концы нитей корда второго слоя заворачиваются вокруг бортовых колец не наружу, как первого, а внутрь покрышки. Эту операцию удобнее сделать, когда готовая покрышка будет снята с оправки.
8) Приклеивание ленты брекерного слоя.
Лента должна закрывать беговую дорожку и несколько заходить на борта (примерно на 2-3 мм на каждую сторону).
9) Оклеивание бортов сырой резиной.
Применима сырая резина для ремонта камер толщиной 0,5-0,7 мм. Сначала ее нарезают в виде ленты, которая должна наклеиваться плотно к борту покрышки встык с краем уже наклеенной брекерной ленты. При этом надо тщательно приглаживать ленту к борту покрышки, чтобы не образовывались воздушные пузыри. Излишки бортовой ленты обрезаются кривыми ножницами по внутреннему (посадочному) диаметру покрышки.
10) Приклеивание слоя протекторной резины толщиной 4-5 мм.
Протекторная лента не должна заходить на борта покрышки и обязательно плотно прилегать к наклеенной ленте брекерного слоя.
11) Удаление оправки из покрышки.
Для этого из нее выпускают воздух, вынимают из покрышки, после чего второй слой корда заворачивается и приклеивается к внутренней поверхности покрышки с перехлестом порядка 15-20 мм. На этом сборка покрышки заканчивается. Желательно еще обклеить посадочные места собранной покрышки «чефером», то есть слоем обрезиненной ткани полотняного переплетения. Это укрепляет борта, что особенно важно, если покрышка будет эксплуатироваться на колесе, имеющем обод с мелким ручьем. Но если у обода глубокий ручей, как, например, у микромотоцикла «Агидель», – оклейке чефером не обязательна. Лента из чефера наклеивается на посадочные места так, чтобы по наружной стороне покрышки ширина ее равнялась 30-35 мм, а 20-25 мм было завернуто внутрь.
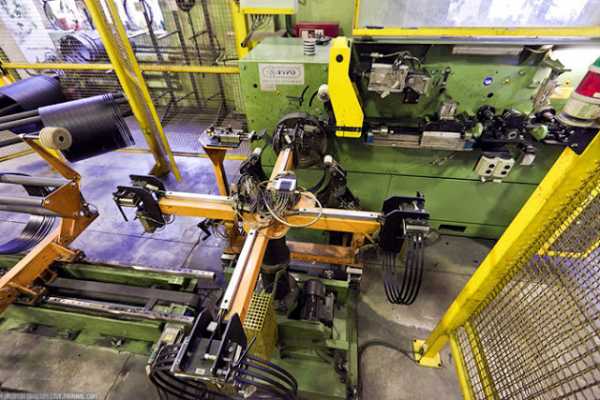
Рис. 7. Пресс-форма для отливки шин.
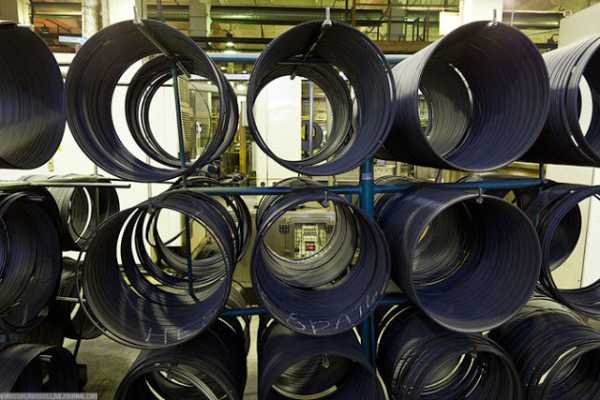
Рис. 8. Пресс-форма с решеткой протектора.
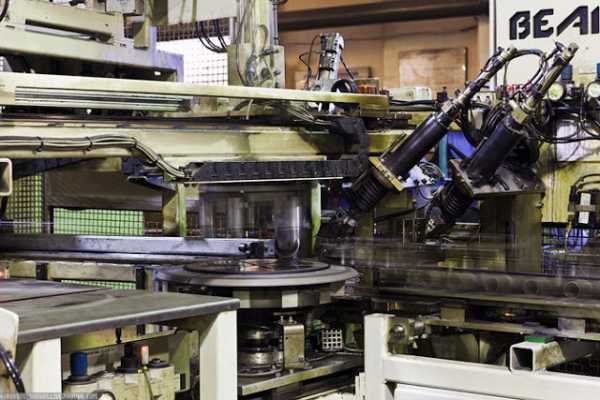
Рис. 9. Порядок сборки покрышки.
1 – участок с уложенным первым слоем, 2 – сшитые края понрышни1 3 вентиль, 4 – прослойка из сырой резины (толщина = 0,5 мм), 5 – второй слой корда, 6 – бортовое кольцо, 7 – завернутые наружу концы корда, 8 – вворачиваемые внутрь края корда.
Собранную описанным способом покрышку необходимо вулканизировать, чтобы придать ей износоустойчивость и прочность. Ведь сырая резина, из которой мы собирали покрышку, потому и называется сырой, что она не обладает достаточной стойкостью против различных механических и химических воздействий. Но после непродолжительного нагревания до определенной температуры сырая резина необратимо меняет свои физико-химические свойства – она становится практически нерастворимой, твердой, упругой, способной выдерживать большие ударные и растягивающие нагрузки и хорошо сопротивляться истиранию. Этот процесс называется вулканизацией.
Вулканизация в настоящее время широко применяется не только в промышленности, но и для бытовых нужд, например, при ремонте резиновой обуви и других предметов обихода. Портативные вулканизаторы, работающие от аккумулятора или снабженные бензиновой горелкой, позволяют ремонтировать автомобильные камеры в пути.
Клей для горячей вулканизации
Такой клей не всегда удается достать, но его можно изготовить и в домашних условиях. Для этого натуральный каучук растворяют в чистом бензине (авиационном, или так называемом «калоша») и на один литр клея добавляют 50 г порошкообразной серы. Если такой серы в готовом виде нет, следует размельчить кусковую серу и просеять ее через металлическое сито с ячейками 0,2X0,2 мм. Перед нанесением клея на поверхность вулканизированной резины она должна быть подготовлена: тщательно зачищена на наждачном круге или вручную – крупнозернистой шкуркой. Касаться пальцами зачищенных поверхностей нельзя. Сырую резину зачищать не нужно. Если ее поверхность окажется загрязненной, достаточно протереть тряпочкой, смоченной в бензине.
Нанеся клей на обе склеиваемые поверхности, их подсушивают на воздухе и плотно прижимают друг к другу, следя За тем, чтобы между ними не оставалось воздушных пузырьков. При склейке колец, варочных или ходовых камер концы ленты надо не только зачистить, но и свести на конус, чтобы толщина склейки не была толще самой ленты. Если клей долго стоял без употребления, его необходимо тщательно размешать, доставая до дна Посуды, в которой он хранился, так как сера со временем осаждается на дно.
В. Петровский, г. Уфа
Категория: Самоделки для бизнеса / Самодельные мини заводы
www.freeseller.ru
Как сделать резину в домашних условиях — Elfterra.ru
Содержание статьи:
В разделе Техника на вопрос Вопрос про резину. Как расплавить резину в домашних условиях. заданный автором Qqq www лучший ответ это Расплавить можно каучук, а не резину. В резине слишком много наполнителе, типа сажи, и сера для вулканизации.
пахнуть будет плохо, можно отравиться
А кто тебе сказал, что резину можно расплавить?
Резина не пластмасса, и чтоб ее девулканизировать надо сина много движений сделать При паровом методе дозированные порции обестканен-ной резиновой крошки смешивают с мягчителями и загружают в девулка-иизационный котел, где обрабатывают острым пар
никак если нужна форма или изделие используем вулканизатор и “сырую” резину
Одинокая женщина прочла в газете рекламу новой услуги — вызов мужчины на дом. Предлагались мужчины самых различных видов и характеров — от интеллигента до супермена. Поразмыслив она позвонила и заказала супермена. Явился здоровенный мужчина. В
Смесь для получения прочного упругого материала получила название сырая резина. После термической обработки изменяются молекулярные связи каучука, образуя сплав с пластификаторами. Можно своими руками в домашних условиях провести вулканизацию и сделать небольшую деталь из резины или просто заклеить пробоину в велосипедной камере, заделать порезы на скатах. В продаже есть несложное оборудование для частных мастерских, в которых делается сырая резина своими руками.
Сок каучуконосных деревьев широко применялся аборигенами для выделки непромокаемой обуви, покрытия лодок, защиты хижин от дождя и решения других бытовых проблем. Они добывают его из каучуконосных растений аналогично сбору весной березового сока. Полиизопрен — углевод, составляющий большую часть природного латекса, — в тепле соединяется с кислородом и со временем становится хрупким. После нагрева молекулярные связи становятся устойчивыми, и вещество не реагирует даже на кислотные растворы.
Ценность каучука исходя из технических характеристик:
- высокая стойкость к истиранию;
- хорошие теплоизоляционные свойства;
- не растворяется в воде и большинстве агрессивных жидкостей;
- пластичность;
- эластичность.
Добавление пластификаторов и речного песка позволяет создавать материал с запланированными качествами и цветом. Сырая резина превращается в изделие, долго сохраняющее свою форму, через вулканизацию — нагрев под прессом до температуры 150 градусов.
Натуральный и синтетический каучук при нагреве до 50 градусов превращается в мягкую массу, которая хорошо смешивается с другими компонентами:
Состав компонентов меняется и зависит от качеств, которыми должна обладать полученная сырая резина. Сера входит в молекулярные соединения, и от нее зависит твердость резины. Ускорители сокращают время вулканизации. Сажа и масло придают пластичность готовому изделию. Песок и другие органические вещества делают ее тверже, уменьшают стирание, увеличивают усилие разрыва.
По твердости выделяют три основные ее группы:
Природный компонент обладает лучшими эксплуатационными качествами, поэтому шины для автомобилей делают из натурального каучука. На небольших предприят
elfterra.ru
Как сделать чернитель резины своими руками. 5 способов чернения шин в домашних условиях
С начала 2000-ых автомобильная косметология переживает настоящий «ренессанс», если к этому течению можно отнести процессы в нем происходящие. Особая популярность к этому движению пришла во время прихода производителей и расширения ассортимента товаров по доступным ценам. Почти на каждую систему пришлось несколько десятков видов улучшений, о которых ранее можно было мечтать. Повальная заинтересованность коснулась как иномарок, так и отечественный автопром. Очень популярным в обоих случаях стала методика чернения шин. Но платить желающих немного, особенно если схожего эффекта можно добиться, используя сделанный чернитель резины своими руками.
Самостоятельно сделанный чернитель резины своими руками показывает хороший результатЗачем делать чернение шин автомобиля
Казалось бы, наиболее естественная причина подобной операции заключается в косметологическом оформлении своего автомобиля. И вправду, с помощью чернения собственных шин можно замаскировать их настоящий «возраст», или скрыть погрешности от длительной эксплуатации. Удачное применения различных чернителей значительно повышает внешний вид транспортного средства, делая его более респектабельным и приятным для взгляда.
Читайте также: Накачка шин азотом — плюсы и минусы. Что дает закачка шин азотом?Но кроме такой естественной причины, которая лежит на поверхности, существует еще одна, очень важная функция у такой манипуляции, а именно защитная функция. Некоторые виды чернителей (куда входит чернитель резины своими руками) после их нанесения создают на покрышке тонкий слой или «плёнку», которая становится барьером от внешних раздражителей. Кроме того, доказаны и «смягчающие» свойства чернителей, тем самым такая эластичная резина способна будет дольше сохранять свою целостность.
Чернение покрышек недолговечно и требует частой профилактикиКакие средства для чернения доступны в магазинах
Прежде чем приступать к покраске покрышек используя чернитель резины сделанный своими руками, следует найти необходимый вариант, который наиболее подойдет к вашему автомобилю. Как правило, этот выбор не влияет на какие-то функции, кроме как внешних, и зависит лишь от предпочтений самого покупающего. На рынке и в автомобильных магазинах можно смело выделить 2 основных лидеров продаж:
- блестящие чернители.Как правило, это смазки с добавлением изрядного количества силикона. Как замечено в названии группы, подобные средства после их нанесения позволяют покрышке приобрести более свежий вид и зеркальный блеск. При достаточно долгом периоде действия, такие чернители плохи тем, что при попадании небольшого количества грязи – они теряют первоначальный вид;
- матовые чернители.Такой тип краски уже давно используется при покраске авто, но теперь доступен и для шин. Благодаря таким средствам, колеса приобретают более глубокий и насыщенный темный цвет и выглядит привлекательно. Серьезным недостатком такого метода принято считать его короткую службу. Чернитель быстро вступает в действие с водой, и впитывается в резину. На деле вид шины становится еще хуже, чем до первой покраски.
Способы чернения резины своими руками в домашних условиях
Как и в любой другой методике, желание «народных умельцев» сделать самим никуда не делось. Удобность в этом плане, состоит как раз в простате таких рецептов «омоложения» собственных покрышек. На вопрос «Как сделать чернитель резины своими руками?» сегодня доступно более десятка активно используемых и действенных методов. Мы попробуем разобрать наиболее распространенные из них.
Рецепт на основе глицерина
Чернение резины глицерином принято считать самым популярным методом у автовладельцев. При сравнительно низкой себестоимости процесса может получится вполне неплохой результат на выходе, превосходя некоторые магазинные аналоги. В основе раствора для покраски используется смешивание равных частей глицерина и воды (желательно дистиллируемой).
На одну покрышку необходимо приблизительно 150-200 мл такого раствора. Приобрести глицерин можно в самой обычной аптеке. Ожидаемый эффект от использования напоминает блестящие чернители. Сам процесс покраски прост: смоченной губкой с раствором медленно и плавными движениями натираем предварительно очищенную покрышку (от грязи, пыли и влаги). К сожалению, глицерин сам по себе жирный компонент, а потому долговечность подобной косметологии скоротечна.
Популярное средство для окрашивания – глицеринЧернение резины хозяйственным мылом
С этим методом знакомы более опытные автолюбители. Возможно, что вы слышали от отцов/дедушек о старом методе натирания покрышек куском хозяйственного мыла, щедро смоченного большим количеством воды. Желающие приобщиться к подобному способу могут не рассчитывать на особый прогресс в изучении этого метода. Как и прежде, это жидкость с растворенным внутри бруском. Однако, следует быть осторожными и не перегибать палку используя такой метод – мыло сушит резину, из-за чего резко снижается эксплуатационный срок последней.
Чернение с помощью мыльного раствора может пересушивать покрышкуИспользование гуталина или другого средства для натирания обуви
Простой и действенный (хоть и ненадолго) метод. Использовать лучше всего жидкие краски для обуви. Выбор темноцветного гуталина или бесцветного силикона зависит только от собственных предпочтений автовладельца. Нанеся небольшое количество средства на губку, принимайтесь за натирание покрышки. Чтобы краска продержалась как можно дольше – желательно оставить машину высыхать после покраски.
Жидкий силикон для чернения шин
Об эффективности этого метода часто возникают горячие дискуссии. Некоторые расхваливают, другие жалуются на недостаточный эффект и долговечность. Ходовым средством для чернения является силиконовое масло ПМС-200. Использование схожее с методами выше. На самом деле, во время тестов аналог показал хорошие результаты, однако ценник на жидкий силикон гораздо выше тех же гуталинов или глицерина.
Чернение резины кока-колой
Довольно шуточный, но при этом самый доступный метод чернения (согласитесь, газированный напиток продается в радиусе 50 метров от вас). Учитывайте, что после процедуры, резина будет липкой несколько часов, а значит езда в это время крайне нежелательна. В зависимости от количество преодолеваемого километража и состояния дорог, в среднем держится 2-3 дня.
automotolife.com
Как делают шины
Многие автовладельцы имеют общее представление о строении автомобильных шин, но о том, как делают шины, мало кто сможет рассказать. Наиболее распространено представление, что резина заливается в некую форму, из которой затем выпрессовывается готовое изделие.
На самом деле это не так, а изготовление автомобильных шин – это сложный высокотехнологичный процесс, для которого необходимо наличие сложного специализированного оборудования, тщательного автоматизированного контроля и участие специалистов высокой квалификации.
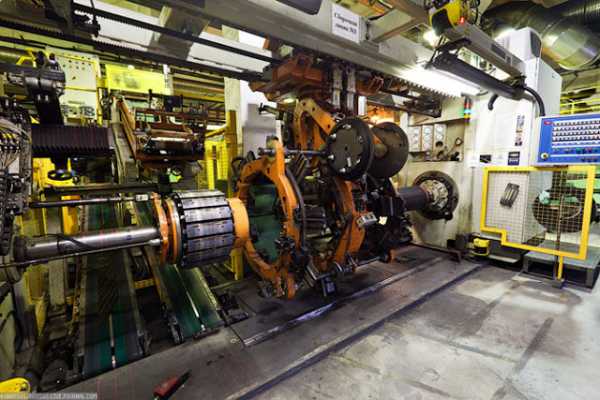
Немного истории
Первая резиновая шина была создана в далеком 1846 году Робертом Вильямом Томсоном. На тот момент его изобретением никто не заинтересовался, и повторно к идее пневматической шины вернулись лишь через 40 лет, когда в 1887 году шотландец Джон Данлоп придумал сделать из поливального шланга обручи, надеть их на колеса велосипеда своего сына и накачать их воздухом.
Спустя три года Чарльз Кингстон Уэлтч предложил разделить камеру и покрышку, вставить в края покрышки кольца из проволоки и посадить их на обод, который затем получил углубление к центру. В то же время были предложены рациональные способы монтажа и демонтажа шин, что позволило применять резиновые покрышки на автомобилях.
Процесс производства шин
Из чего делают
Основной материал, который применяется при производстве шин, резина, изготовленная на основе натурального или искусственного каучука. В зависимости от того, в каких пропорциях и какой каучук добавляется, в конечном итоге получаются летние или зимние автомобильные покрышки.
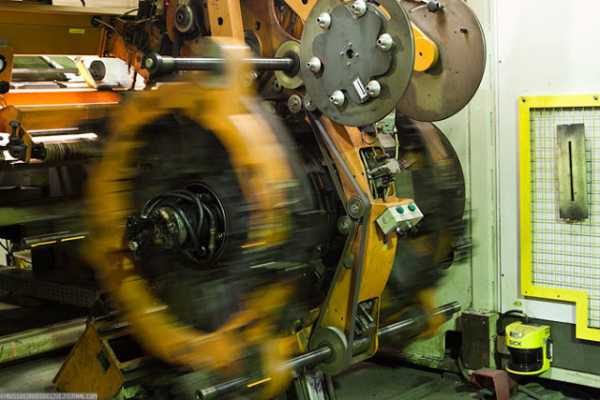
Так, в резиновую смесь для летних шин добавляется преимущественно искусственный каучук, поэтому резина получается более жесткой, устойчивой к износу, она не «плывет» при высокой температуре и обеспечивает надежное сцепление с дорожным полотном. Чтобы изготовить зимние покрышки, добавляют натуральный каучук, который делает резину более мягкой и эластичной. Благодаря этому зимние шины не «дубеют» даже при очень сильных морозах.
- Помимо каучука в резиновую смесь добавляют множество других компонентов, таких как пластификаторы, наполнители, сажа, вулканизирующие добавки.
- Шина состоит из нескольких элементов, объединенных в одно целое: каркаса или корда, слоев брекера, протектора, борта и боковой части.
Как делают каркас
Корд будущей покрышки делают из металлических, текстильных или полимерных нитей на специальном станке – «шпулярнике». От множества катушек проволока нити сходятся в одном месте. В общих чертах конструкция напоминает ткацкий станок. Далее сплетенный корд попадает в экструдер, где происходит его обрезинивание.
Готовый каркас впоследствии раскраивается на полосы разной ширины, для производства шин разной размерности. И сматывается в катушки для хранения и транспортировки. Поскольку невулканизированная резина очень липкая, во избежание порчи каркаса между слоями вставляются прокладки.
Как делают протектор
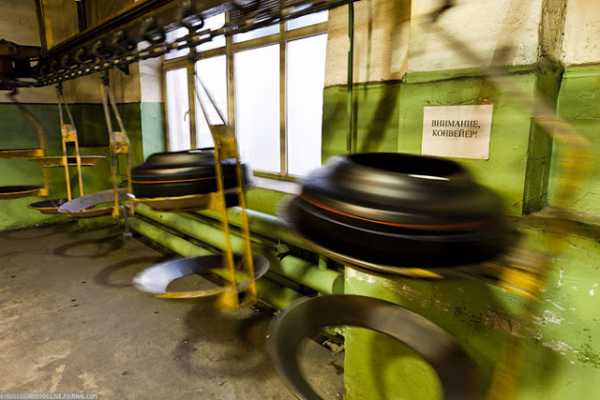
Боковая часть
Борт покрышки состоит из бортового кольца и слоя вязкой воздухонепроницаемой резины. Производство бортов шин начинается с того, что металлическая проволока обрезинивается, после чего закручивается под требуемый радиус колесного диска и нарезается кругами. После этого на станке осуществляется сборка. Подробнее этот процесс можно посмотреть на видео.
Сборка
Предпоследний этап – сборка готовой покрышки. Осуществляется она на станке, на который поступают все готовые элементы. Обслуживают станок два работника: сборщик и перезарядчик.
Первый навешивает бортовые кольца, а второй вставляет катушки с компонентами. После этого станок все делает автоматически: соединяет части воедино и раздувает заготовку воздухом под протектор с брекером. Почти готовую шину взвешивают и осматривают на предмет наличия дефектов. Этот процесс также можно посмотреть на видео.
Вулканизация
Последний этап производства – вулканизация. Шина обрабатывается горячим паром под давлением 15 бар и при температуре порядка 200 градусов по Цельсию. В результате каучук, сажа и всевозможные присадки спекаются, а на поверхности покрышки при помощи пресс-форм наносится рисунок протектора и надписи. Готовые шины проверяются на соответствие всем требуемым характеристикам.
znanieavto.ru
Из чего делают автомобильную резину
Условия суровой конкуренции заставляют многих производителей автомобильных покрышек утаивать состав резиновой смеси, используемый для производства автошин. Этапы технологического процесса держатся в строгой секретности. При этом основные составляющие, из которых изготавливается авторезина, известны. Без них невозможно создание покрышек. Давайте разберемся, из чего делают резину.
Натуральные и синтетические составляющие
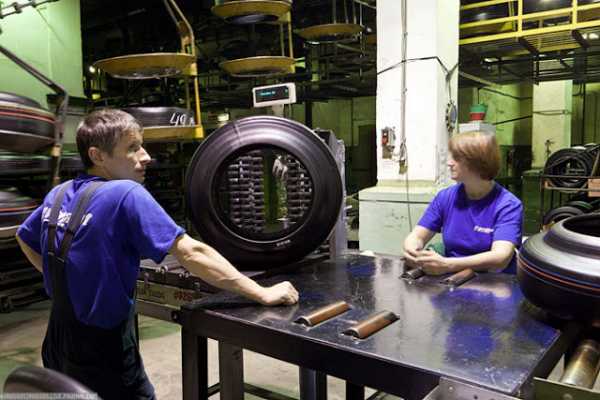
Резину для автомобилей делают из каучука, который может быть природного либо синтетического происхождения. Натуральный каучук добывают из каучуковых деревьев. Дословно название «каучук» переводится как плачущее дерево. Сок указанного дерева имеет очень большую ценность, из него производится авторезина. Синтетический каучук имеет меньшую себестоимость, его чаще применяют для производства.
Примерно 30% от общего состава резины составляет технический углерод (сажа). Он выступает скрепляющим компонентом, действующим на молекулярном уровне. Сажа увеличивает такие характеристики резины:
- эксплуатационный период;
- прочность изделия;
- износостойкость.
Иногда технический углерод заменяется кремниевой кислотой. Этот компонент используют с целью уменьшения себестоимости продукции. Указанная кислота дешевле сажи. При ее использовании увеличивается сцепление колес с мокрым дорожным покрытием, при этом уменьшается стойкость шин к износу.
При производстве резины, для обеспечения ей определенных свойств домешивают разнообразные масла и смолы. Они уменьшают жесткость покрышек, предназначенных для зимы.
Каждый производитель покрышек применяет особый состав авторезины, делает упор на определенные характеристики покрышек:
- сцепление с дорожной поверхностью;
- устойчивость к абразивным частицам дороги;
- улучшение скоростных характеристик и так далее.
Рекомендуем посмотреть видео о том, из чего делают резину:
Технология производства авторезины
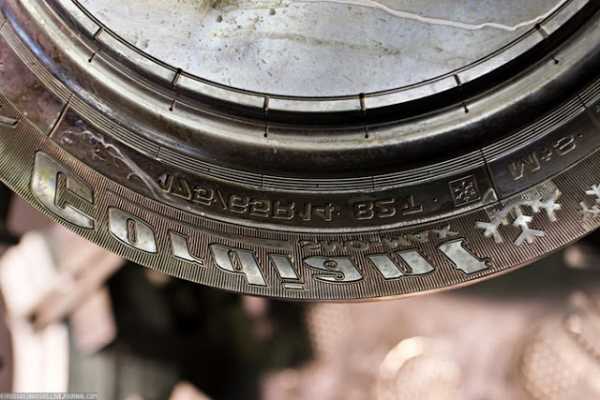
Летняя резина отличается от зимней авторезины количеством и качеством, входящего в ее состав каучука. Чтоб сделать летние автошины, необходим каучук ненатурального происхождения. Он обеспечивает жесткость автопокрышкам. Натуральное сырье наоборот смягчает резину, поэтому его используют в зимних шинах. Присутствие натурального каучука позволяет зимним покрышкам не «дубеть» при очень низких температурах.
Сок каучуковых деревьев собирают, затем помещают его в большие чаны, наполненные кислотой на 10 и более часов. Такая технология позволяет сырью затвердеть и в результате получается латекс. Из полученного латекса убирают излишнюю влагу и пропускают его через специальные валы, для образования широкой ленты. Указанная лента с помощью специальных ножей измельчается, в итоге получается легкая воздушная масса, которую с помощью обжига в специальных печах преобразуют в эластичные блоки.
Указанные блоки помещают в специальный котел, в который производителем добавляются дополнительные элементы с учетом четких пропорций для придания резине определенных качественных характеристик. Этот «коктейль», состоящий из каучука и химических элементов нагревается и превращается в резину. Разогретую смесь раскатывают специальными валами в полосы определенной толщины, затем охлаждают.
Процесс изготовления автопокрышек
Из чего делаются покрышки? Готовые автопокрышки состоят не только из резины. Каркас автопокрышек изготавливают из специальных нитей. Они могут быть:
- текстильными;
- металлическими;
- полимерными.
Технология производства корда напоминает работу ткацкого станка. Образованный корд помещается в экструдер, в котором осуществляется его обрезинивание. Готовый каркас раскатывается на полосы, имеющие различную ширину для изготовления покрышек разной размерности.
Для создания протекторного слоя обрезиненный корд помещается на специальный станок, превращающий методом экструзии заготовку в протектор.
Борт авторезины изготавливается следующим образом:
- Металлическая проволока обрезинивается.
- Производится нарезка обрезиненной проволоки кругами (с учетом радиуса будущей покрышки).
- На специальном станке проводится сборка боковин.
Для сбора составляющих элементов шин в единую конструкцию применяют специальный станок. На него устанавливают бортовые кольца и катушки с компонентами. Станок автоматически соединяет все части автопокрышки, затем наполняет заготовку воздухом под протектор с брекетом.
Завершающим этапом создания шин есть вулканизация. После обработки покрышки горячим паром под давлением, каучук с всевозможными присадками спекается. Затем с применением специальных форм для пресса наносится протекторный рисунок с разнообразными надписями. Готовая продукция проверяется на соответствие всем необходимым характеристикам.
Заключение
Автомобильная резина состоит, в большинстве случаев, из таких компонентов:
- каучук;
- смолы;
- кремниевая кислота;
- сажа;
- секретные химические элементы, добавляемые в резину для придания ей определенных качеств (мел, глицерин, ацетилированный ланолин и так далее).
От качественных и количественных характеристик указанных компонентов зависит качество готовой продукции. Не стоит поддаваться рекламному воздействию и отдавать предпочтение автошинам, изготовленным с применением новых химических компонентов. Перед покупкой таких покрышек, стоит поинтересоваться, насколько заявленные производителем авторезины параметры соответствуют реальности.
pro-zamenu.ru
Как делают автомобильные шины? | Журнал Популярная Механика
Все знают, что такое автомобильная шина, как она выглядит и зачем она нужна, многие даже их покупали для своего автомобиля и ремонтировали на них проколы, однако мало кто видел, как их изготавливают. А зря, потому что это довольно интересный процесс! Наверстать упущенное поможет этот познавательный видеоролик.
Александр Пономарёв
Автомобильная шина представляет собой упругую оболочку из резины, металла и ткани, установленную на обод колёсного диска. Шина обеспечивает контакт транспортного средства с дорожным покрытием и предназначена для поглощения незначительных колебаний от неровностей и компенсации погрешности траекторий колёс. Основными материалами для производства шин являются резина, которая изготавливается из натуральных и синтетических каучуков, и корд. Кордовая ткань может быть изготовлена из металлических, полимерных и текстильных нитей. В целом шина состоит из каркаса, слоёв брекера, протектора, борта и боковой части.
В зависимости от ориентации нитей корда в каркасе различают диагональные и радиальные шины. У диагональных каркас состоит из нитей корда, направленных по диагонали, под некоторым углом к плоскости колеса, причём в двух соседних слоях каркаса нити корда перекрещиваются и работают в паре друг с другом. Толщина каркаса боковины и протектора у таких шин отличается мало, брекер тонкий и усиливает основной каркас лишь в незначительной степени. У радиальных нити каркаса расположены в направлении радиуса по профилю шины от одного борта до другого, так что нити каркаса во всех его слоях параллельны друг другу.
Ещё больше по темам
www.popmech.ru