Карбон – характеристики углеполотна
Полотно определяет не только внешний вид получившегося карбона, но и его прочностные и технологические характеристики. От плетения и плотности углеполотна зависит и то, как легко и качественно можно выложить его в форме при заливке смолой.
Для получения оптимальной прочности, плотности и жесткости зачастую требуется послойное сочетание разных типов углеполотна. Чтобы лучше понимать эксплуатационные характеристики каждого вида плетения, попробуем пояснить, какими бывают самые популярные виды плетения полотна.
Виды плетений полотна
|
Полотно (Plane Weave, P) — cамый плотный вид плетения карбонового волокна, самый распространенный. Нити утка и основы переплетаются поочередно 1Х1. Высокая плотность позволяет избежать искажений фактуры, но в то же время такое плетение делает полотно менее пластичным.
|
|
Елочка (Twill, T) — саржевое плетение 2Х2, наиболее универсальное полотно. Нити утка и основы переплетаются через две нити. Такое плетение прочнее, чем 1Х1, вопреки расхожему мнению. Тоже очень распространенный, универсальный тип плетения. Подходит для приобретения навыков работы с углеполотном. Ткань рыхлая и пластичная, что позволяет легко подтянуть ее в нужном направлении. Главное при этом не получить просветы и искажение фактуры. |
|
Разновидность елочки, которая используется весьма редко. Очень пластичная структура для нестандартных решений. |
|
Сатин (Satin WEAVE, R) — наименее плотное и самое пластичное полотно. Рыхлость полотну придают особенности плетения: каждая нить утка и основы проходит над несколькими нитями утка или основы. При работе с этим типом полотна необходим определенный уровень навыков.
|
|
Реже используется корзинное плетение — Leno, Basket Weave. Красивая фактура, но такое полотно сложно выложить без искажений рисунка. |
Схематически виды плетения карбонового полотна представлены на рисунке.
Правила выбора углеполотна
Выбор текстиля определяется назначением, способом использования углеволокна и способом получения углепластика. Его основными характеристиками являются:
- Плотность, масса на единицу площади г/м.кв,
- Линейная плотность, количество нитей на 1 см2 в каждом направлении,
- Число К, количество тысяч элементарных нитей углерода (цепочек) в одной нити. Наиболее распространено волокно с К3. Обычно К=6-12-24-48.
Для автотюнинга чаще всего используются полотна плотностью 150-600 г/м.куб с толщиной волокон 1-12К. А для велосипедных рам К3. Обратите внимание при выборе необходимых вам параметров на единицы измерения, на китайских сайтах — это не метрическая система!
Технические характеристики карбоновых волокон
Для углеродных волокон основными механическими характеристиками являются предел прочности на растяжение σв и предел прочности на единицу объема, а также модуль упругости, определяющий эластичность и способность работать на изгиб. Механические свойства сильно зависят от ориентации волокон, то есть они анизотропны, хотя в плетении Pane и Twill эффект анизотропии свойств проявляется меньше. Технические характеристики, как правило, приводятся для продольного направления.
Углеродные волокна обладают следующими механическими характеристиками по сравнению с армирующими металлическими, стекловолокном и полимерными волокнами.
Волокно (проволока) |
ρ, кг/ м³ |
Тпл, °C |
σB, МПа |
σB/ρ, МПа/кг*м-3 |
Алюминий |
2 687 |
660 |
620 |
2 300 |
Асбест |
2 493 |
|
1 380 |
5 500 |
Бериллий |
1 856 |
1 284 |
1 310 |
7 100 |
Карбид бериллия |
2 438 |
2 093 |
1 030 |
4 200 |
Углерод |
1 413 |
3 700 |
2 760 |
157 |
Стекло E |
2 548 |
1 316 |
3 450 |
136 |
Стекло S |
2 493 |
1 650 |
4 820 |
194 |
Графит |
1 496 |
3 650 |
2 760 |
184 |
Молибден |
0 166 |
2 610 |
1 380 |
14 |
Полиамид |
1 136 |
249 |
827 |
73 |
Полиэфир |
1 385 |
248 |
689 |
49 |
Сталь |
7 811 |
1 621 |
4 130 |
53 |
Титан |
4 709 |
1 668 |
1 930 |
41 |
Вольфрам |
19 252 |
3 410 |
4 270 |
22 |
Например, параметры углеродных волокон Toray из полиакрилата (PAN) c высокой прочностью на растяжение High Modulus Carbon Fiber.
Волокно (fiber) |
Модуль упругости (msi) |
Предел прочности (ksi) |
M35J |
50 |
683 |
M40J |
57 |
398 |
M40J |
55 |
640 |
M46J |
63 |
611 |
M50J |
69 |
597 |
M55J |
78 |
583 |
M60J |
85 |
569 |
Существует взаимосвязь — чем выше предел прочности, тем ниже модуль упругости.
Что влияет на технические характеристики карбоновых композитов
При подборе материала очень важно найти оптимальный баланс между этими характеристиками, подбирая слои, направление волокна, метод плетения и плотность.
Механические свойства композитов определяются следующими параметрами:
- Тип карбонового волокна и смолы,
- Тип плетения, ориентация волокон,
- Соотношение волокон (т.е. плотность полотна) и смолы в композиции,
- Плотность, однородность, пористость и пр.
Ирина Файдюк
При копировании материалов не забывайте, что у каждого текста есть автор. Поэтому при добавлении материала на свой сайт не забывайте ставить индексируемую ссылку на первоисточник!!!
engitime.ru
Что такое углепластик (карбон)
Общие положения
Углепластик — это композиционный многослойный материал, представляющий собой полотно из углеродных волокон в оболочке из термореактивных полимерных (чаще эпоксидных) смол, Carbon-fiber-reinforced polymer .
Международное наименование Carbon — это углерод, из которого и получаются карбоновые волокна carbon fiber.
Но в настоящее время к карбонам относят все композитные материалы, в которых несущей основой являются углеродные волокна, а вот связующее сможет быть разным. То есть карбон и углепластик объединились в один термин, привнеся путаницу в головы потребителей.
Это инновационный материал, высокая стоимость которого обусловлена трудоемким технологическим процессом и большой долей ручного труда при этом. По мере совершенствования и автоматизации процессов изготовления карбона его стоимость будет снижаться. Для примера: стоимость 1 кг стали — менее 1 доллара, 1 кг карбона европейского производства стоит около 20 долларов. Удешевление возможно только за счет полной автоматизации процесса.
Применение карбона
Изначально карбон был разработан для спортивного автомобилестроения и космической техники, но благодаря своим отличным эксплуатационным свойствам, таким как малый вес и высокая прочность, получил широкое распространение и в других отраслях промышленности:
- в самолетостроении,
- для спортивного инвентаря: клюшек, шлемов, велосипедов.
- удочек,
- медицинской техники и др.
Гибкость углеродного полотна, возможность его удобного раскроя и резки, последующей пропитки эпоксидной смолой позволяют формовать карбоновые изделия любой формы и размеров, в том числе и самостоятельно. Полученные заготовки можно шлифовать, полировать, красить и наносить флексопечать.
Технические характеристики и особенности карбона
Популярность углепластика объясняется его уникальными эксплуатационными характеристиками, которые получаются в результате сочетания в одном композите совершенно разных по своим свойствам материалов — углеродного полотна в качестве несущей основы и эпоксидных компаундов в качестве связующего.
Армирующий элемент, общий для всех видов углепластика — углеродные волокна толщиной 0,005-0,010 мм, которые прекрасно работают на растяжение, но имеют низкую прочность на изгиб, то есть они анизотропны, прочны только в одном направлении, поэтому их использование оправдано только в виде полотна.
Дополнительно армирование может проводиться каучуком, придающим серый оттенок карбону.
Карбон характеризуются высокой прочностью, износостойкостью, жёсткостью и малой, по сравнению со сталью, массой. Его плотность — от 1450 кг/м³ до 2000 кг/м³. Технические характеристики углеволокна можно посмотреть всравнительной таблице плотности, температуры плавления и прочностных характеристик.
Еще один элемент, используемый для армирования вместе с углеродными нитями — кевлар . Это те самые желтые нити, которые можно видеть в некоторых разновидностях углепластика. Некоторые недобросовестные производители выдают за кевлар цветное стекловолокно, окрашенные волокна вискозы, полиэтилена, адгезия которых со смолами гораздо хуже, чем у углепластика, да и прочность на разрыв в разы меньше.
Кевлар—это американская торговая марка класса полимеров арамидов, родственных полиамидам, лавсанам. Это название уже стало нарицательным для всех волокон этого класса. Армирование повышает сопротивление изгибающим нагрузкам, поэтому его широко используют в комбинации с углепластиком.
Особенности технологии изготовления углеродного волокна
Волокна, состоящие из тончайших нитей углерода, получают термической обработкой на воздухе, то есть окислением, полимерных или органических нитей (полиакрилонитрильных, фенольных, лигниновых, вискозных) при температуре 250 °C в течение 24 часов, то есть практически их обугливанием. Вот так выглядит под микроскопом нить после обугливания.
forma-odezhda.ru
Что такое карбон
Что такое карбон?Карбон – это техническая ткань, состоящая из тысяч переплетенных между собой углеродных волокон, образующих ту самую ткань. Карбон выпускается в виде тканей с самыми разнообразными переплетениями в зависимости от целевого применения и является всего лишь одной частью конструкционных материалов, включающих в себя много частей, которые известны всем, как композитные материалы. Композиты производятся из составляющих, которые объединяют в себе качества разных материалов, а целью является отсутствие жесткости или получение прочности. В случае с карбоном, стекловолокном, Кевларом или другими аналогичными тканями, композитный материал, о котором идет речь, носит название «FRP» (Fiber Reinforced Polymer – полимер, армированный волокнами). В производстве такого полимера ткань используется для того, чтобы «усилить» конструкционную жесткость смолистого подслоя. Смола обеспечивает прочность композита, а карбон добавляет структурную целостность пластику, который в ином случае будет хрупким.
Как производится карбон?
Карбон (углеволокно), как видно из его названия, это ткань, состоящая только из угля и не имеющая иных элементов в своем составе. Но начинать производство просто с карбона и с создания ткани с переплетениями волокон было бы настоящим, но труднодостижимым, подвигом. Вместо использования карбона в качестве сырья, заводы по производству текстиля начинают с пластмасс с более сложным молекулярным составом, где толщина нити меньше толщины человеческого волоса. Затем требуется выполнить ряд определенных действий, начиная от термообработки и заканчивая химической обработкой. Окончательным результатом этих сложных процессов является доводка состава полимерных материалов до его самой эмпирической формы – формы чистого карбона.
Карбон часто замеряется и продается с ориентиром на несколько критериев, на тип плетения волокон, на абсолютные значения (измерение прочности отдельно взятого волокна) и вес ткани. Все замеры идут в унциях на квадратный ярд, плюс указывается количество волокон (обычно в диапазоне от 3 000 до 12 000 волокон).
Какие существуют типы переплетения?
Однонаправленное плетение:
Однонаправленное плетение подразумевает направление всех карбоновых жгутов (волокон) в одном и том же направлении. Плетение в этом стиле не является видимым невооруженному глазу. Поскольку плетение, как таковое, отсутствует, нити волокна необходимо как-то удерживать вместе. И в этом случае необходимо протягивать другую нить по диагонали или перпендикулярно так, чтобы ткань оставалась гладкой и равномерной (и этот элемент плетения не является конструкционным). В результате того, что жесткость ткани обеспечивается только в одном направлении, такой тип плетения редко применяется в автоспорте, где нагрузка может идти в любом направлении.
Двунаправленное плетение волокон:
Карбон двунаправленного плетения – это базовый и наиболее часто встречающийся тип переплетения волокна. Жгуты переплетаются друг с другом под требуемым углом, за счет чего ткань получает структуру типа «шахматная доска», где нити полотна прокладываются боком и по вертикали. В этом случае все волокна направлены таким образом, чтобы нагрузка могла налагаться в любом направлении, при этом композитный материал должен сохранять свою прочность.
Плетение по диагонали в две через две нити
Плетение по диагонали в две через две нити – это самый распространенный тип плетения карбона, который повсеместно применяется в автоспорте. Это плетение немного сложнее по сравнению с двунаправленным волокном, поскольку две нити проходят над другими двумя нитями, либо одна над двумя или две над одной. В результате такого переплетения нитей на ткани создается рисунок «елочка». Из-за того, что плетение две через две нити по диагонали идет как с вертикальными, так и с горизонтальными нитями (нить основы и уток), ткань становится очень гибкой и может принимать различные сложные формы. При работе с карбоном этого типа плетения не требуется выполнять такие работы, как «пакетирование», «растягивание» или резка.
Плетение по диагонали в четыре через четыре нити
Аналогично плетению по диагонали в две через две нити, а именно в четыре через четыре нити, этот тип относится к двустороннему переплетению по диагонали, где один жгут включает в себя четыре нити. В результате ткань не настолько плотная по сравнению с плетением в две через две нити, но в случае с изогнутыми поверхностями достигается лучший коэффициент покрытия, поскольку между фактическими точками переплетения «над и под» расстояние больше, что эффективнее, поскольку в этом случае достигается меньшее количество жестких швов. Благодаря этому покрытие карбоном изогнутых литых форм становится простым.
Прорезиненное переплетение
Прорезиненная карбоновая ткань – это очень специфический способ изготовления ткани, который встречается намного реже по сравнению со всеми типами плетения, которые мы обсуждаем. Прорезиненное плетение волокон означает, что каждая прядь состоит от 3000 до 12000 нитей, при этом каждая нить выкладывается плотно в ряд, одна за другой, образуя тончайшую карбоновую ленту. Стандартные пряди соединяются вместе посредством нескольких слоев карбоновых нитей. Прорезиненную ткань можно определить за счет наличия широких открытых участков. За счет шахматного порядка двунаправленного карбонового волокна со структурой прорезиненной ткани образуются квадратные участки размером один дюйм.
Поскольку за счет крупного размера этих участков переплетения ткань теряет в своей плотности, точки плетения «над и под» находятся на большом расстоянии друг от друга. Итак, точки пересечения нитей находятся на расстоянии друг от друга, частота изменения направления сильно снижена, и ткань может намного плотнее прилегать к поверхности.
Как было описано на сайте, английском поставщике материалов и полимеров, «прорезиненные ткани набирают свою популярность в сфере применения высокотехнологичных композитов благодаря своему невероятно плоскому профилю, который практически исключает так называемый «копир-эффект» и эффект проявления определенной текстуры на поверхностях, требующих идеальной гладкости (например, крылья самолета).
Поскольку слой ткани намного тоньше, можно накладывать слой поверх другого слоя и тем самым достичь необходимых прочностных характеристик. Этот тип карбона часто используется в тех сферах, где аэродинамические характеристики преобладают над прочностными. Прорезиненная ткань имеет внешний вид, отличный от стандартного, который сразу вызывает или любовь, или ненависть.
Различные смолы
Карбоновая ткань является только одной составляющей композитного материала, на который ссылаются, когда говорят об автоспорте и гонках на треках. Другим важным компонентом является смола, которая обогащает саму ткань и придает ей фактическую жесткость. Смолы применяются в различных полимерных «блюдах». Два наиболее часто используемых материала – это эпоксидная смола и полиэфирная смола. Любой, кто когда-либо работал со стекловолокном, чтобы просто починить хоть свою доску для серфинга, хоть деталь от автомобиля, знает, что эта смола может оказаться самой настоящей проблемой. Летучие органические соединения (ЛОС) – это пары, которые являются отличительной чертой многих вид смол, хотя в свободном доступе есть и такие, в которых эти химические составляющие, способные повредить ваш мозг, не применяются. Практически всем известен обратный эффект работы со смолой, когда надлежащие средства индивидуальной защиты не используются, но при этом развивается гиперчувствительность и аллергия. И эти случаи стали уже настолько привычными, что мы часто слышим анекдоты про людей, не способных находиться в помещении, в котором идет работа со смолой.
Эпоксидная смола
Эпоксидная смола – это самая распространенная многоцелевая структурная смола. Как и в случае с практически всеми типами смол, это двухкомпонентный раствор из смолы и катализатора. Время реакции варьируется, но при этом напрямую зависит от условий окружающей среды. Срок годности (рабочее время), в основном, составляет от пяти до тридцати минут. В общем, тепловое воздействие всегда ускоряет процесс «созревания», но весь процесс схватывания обычно занимает, ни много, ни мало, а целые сутки (24 часа) – если на смесь никак не воздействовать. По сравнению с полиэфирной смолой эпоксидная смола отличается более высокой прочностью, но требует терпения при работе с ней.
Полиэфирная смола
Полиэфирная смола – это более дешевая альтернатива эпоксидной смоле, с быстрым временем схватывания. В основном, она используется в тех ситуациях, когда структурная целостность уступает эстетической стороне вопроса, как утверждают специалисты с сайта easycomposites.co.uk: «Тем не менее, существуют ситуации, в которых многослойная структура имеет наименьшее значение, а такие свойства, как внешний вид, стойкость к УФ излучению и цена, стоят на первом месте по своей значимости».
Препреги (ткани с предварительной пропиткой)
Некоторые ткани из карбона могут выпускаться, как предварительно пропитанные раствором смолы, где катализатором выступает термообработка. Препреги используются во многих промышленных сферах, занятых производством композитов, поскольку их применение не требует выполнения каких-то сложных процессов, а при непосредственной работе беспорядок сведен к минимуму: нужно всего лишь смешать смолы и уложить влажную ткань слоями.
Препреги также являются предпочтительным материалом в тех сферах промышленности, где вес играет важную роль. К таким сферам относится авиация, где большая часть от массы деталей приходится на смолу, а не на ткань. С учетом того минимума, который нужен для тщательной и равномерной пропитки ткани смолой, препрег может применяться для создания самой прочной и легковесной конструкции.
Производственные процессы
Влажные выкладки
Традиционно небольшие детали выкладываются во влажном состоянии, вместе с вогнутой формой, затем создается пробка (но это уже другая история). Сухая ткань размещается внутри формы. Смола наносится малярной кистью до тех пор, пока ткань не будет ей насквозь пропитана или насыщена. Следующие слои ткани кладутся поверх первого слоя, при этом нужно соблюдать направление плетения: 45 градусов для двунаправленного плетения и 90 градусов для ткани с саржевым переплетением. Если слои ткани не совпадают по направлениям, на выходе деталь потеряет свою жесткость по одной оси, а по другой будет слишком усилена.
Уложив, таким образом, столько слоев ткани, сколько необходимо для получения нужной толщины, излишек смолы соскребается с помощью скребка так, будто вы убираете воду со своего ветрового стекла. Затем деталь подвергается обработке в вакуумном мешке под низким давлением. В результате смола заполняет все оставшиеся воздушные пустоты, вытесняя тем самым мельчайшие воздушные пузырьки, а излишки смолы уходят.
В некоторых случаях все эти манипуляции выполняются в обратном порядке. Сухая ткань подвергается обработке в вакуумном мешке в форме, и только затем наносится смола. Благодаря этому методу отходы и грязь отсутствуют. На финальном этапе проходит термообработка. Все детали «запекаются» внутри духовки под давлением, так называемом автоклаве, и смола полностью схватывается.
Хотя большинство не имеет доступа к специализированному оборудованию, такие процедуры, как обработка в вакуумном мешке и запекание в автоклаве являются факультативными для рабочих деталей, структура которых не должна отвечать специфическим требованиям.
Сферы применения
Карбон набрал свою силу в автомобильной сфере промышленности. На вторичном рынке карбон – это материал, который чаще всего используется для покрытия деталей. Кузовные детали, детали для внутренней отделки салона – и все это выполнено из карбона, который обеспечивает автомобилю внешний вид высочайшего класса. Функционально детали из карбона применяются практически во всех сферах – начиная от автомобильной промышленности, продолжая судостроением и заканчивая авиацией.
Карбон используется в постройке гоночных кресел, карданных валов, таких защитных приспособлений, как шлемы и средства пассивной безопасности (подголовники), и даже технология производства составных пружин начинает применять карбон для систем подвесок.
Карбон – это не панацея
Привлекательность карбона настолько высока для многих, что сегодня существует тенденция неверного использования этого материала в тех сферах, где наилучшим решением до сих пор является металлический сплав. Карбон, а особенно смола, плохо переносят работу в высокотемпературной среде, с теплозащитой, с компонентами выхлопной системы или любыми другими деталями двигателя. Когда в этих случаях карбон выбирается в качестве исходного материала, следует очень тщательно проводить оценку рабочих условий. Существуют жаропрочные смолы, но сфера их применения до сих пор имеет свои ограничения.
Сопротивление удару
Карбон может похвастаться тем, что эта (уже ставшая крылатой) фраза полностью отвечает его сущности: чем легче алюминий, тем прочнее сталь. Хотя это действительно правда, важно понимать, что речь идет о прочности на разрыв, а не об ударной вязкости или жесткости. С инженерной точки зрения «ударная вязкость» – это технический термин, который говорит об износостойкости, поскольку этот композит является армированным слоистым полиэстером, сопротивление удару которого – низкое. И даже слабый точечный удар может привести к отслаиванию и, в кончено итоге, выходу материла из строя. По этой причине карбон не может применяться для создания износостойких или многоразовых опорных плит седельно-сцепного устройства удовлетворительного качества, для производства различных компонентов подвески или любых других деталей, которые эксплуатируются в условиях максимальной нагрузки.
Проводимость
Карбон является проводимым материалом! Чистый карбон чрезвычайно эффективно передает тепло сам по себе. Например, капот автомобиля, выполненный из карбона, может очень быстро нагреваться на солнце до нескольких сот градусов. Ультрафиолетовые лучи могут повредить композит: придать ему желтый оттенок или стать причиной растрескивания смолы, поэтому деформация является распространенным дефектом. В авиации многие запчасти из карбона покрываются глянцевой белой краской, поскольку тепло, образующееся от воздействия УФ лучей, может деформировать раму, оказать негативное воздействие на аэродинамические характеристики. Кроме того, УФ лучи могут как-то иначе изменить структуру самолета.
Карбон – это еще и электропроводящий материал. Возможно, вас смутит то, каким же образом композит на основе пластмассы может вдруг стать электропроводящим, но ткань из чистого карбона «прокладывает» своеобразный путь электричеству, даже если карбон обогащен изоляционным полимером. Когда карбон выбирается в качестве поверхности для электроники или в качестве кожуха охлаждающего вентилятора, убедитесь в наличии заземления, которое не должно «проходить» через карбон. Анекдот из жизни: мы как-то были свидетелями чуть не начавшегося возгорания в двигателе владельца грузовика Geiser Trophy, поскольку он просто-напросто не верил, что карбон является проводимым материалом, а возгорание смолы – это вам не шутки.
Работа с карбоном
Если стекловолокно когда-нибудь попадало вам на кожу, то вы знаете, как сильно раздражают эти невидимые глазу частички. А карбон гораздо хуже! Избегайте прикасаться голыми руками к рваным краям карбона и к рубленому волокну.
При заказе ткани из карбона важно убедиться, что он поставляется в рулонах, как оберточная бумага. Карбон, упакованный «сложениями», будет иметь загибы и, в результате, конструкционная целостность его загнутых волокон будет нарушена. Соблюдайте эти инструкции при работе с материалом, и храните ткань в чистоте во избежание появления пыли и жирных отпечатков пальцев, обеспечивая при этом максимально правильную укладку. Смешивать смолу необходимо в небольших емкостях, что является нормой. Будьте внимательны, смолу нельзя смешивать в емкостях, покрытых воском. Воск вступает в реакцию со смолами, в результате чего смола затвердевает. Затвердевание смолы – это экзотермическая реакция, что значит нагнетание тепла в качестве побочного продукта в результате химической реакции. Смешивая большое количество смолы, убедитесь, что ее излишки находятся вне зоны хранения горючих материалов, иначе существует высокий риск возникновения пожара.
Заключение
Объем базовых знаний, которые мы даже не затронули в этой статье, просто огромен. Но мы надеемся, что этот общий обзор помог вам лучше представить себе, что такое карбон. Это крайне универсальный и прочный материал, если с ним обращаться с умом. Но если его использовать неверно, он становится самым настоящим бельмом на глазу. Создание простых деталей в домашних условиях не представляет собою никаких сложностей, но приготовьтесь выделить немного больше времени на работу с ним по сравнению со стекловолокном. Учитывайте в своем проекте все – цели, бюджет. И только потом принимайте решение, является ли карбон правильным выбором или вам просто хочется добавить эстетики своему автомобилю?
Данные взяты с сайта: tourerv.ru
artex-fabric.com
Углеводородное волокно, карбоновая нить, производство полимерных материалов и карбона, углеволокно цена
Углеродное волокно – материал, состоящий из тонких нитей диаметром от 3 до 15 микрон, образованных преимущественно атомами углерода. Атомы углерода объединены в микроскопические кристаллы, выровненные параллельно друг другу. Выравнивание кристаллов придает волокну большую прочность на растяжение. Углеродные волокна характеризуются высокой силой натяжения, низким удельным весом, низким коэффициентом температурного расширения и химической инертностью.
Производством углеродного волокна в России занимается компания ООО «Композит-Волокно», входящее в холдинг “Композит”
Углеродное волокно является основой для производства углепластиков (или карбона, карбонопластиков, от “carbon”, “carbone” – углерод). Углепластики – полимерные композиционные материалы из переплетенных нитей углеродного волокна, расположенных в матрице из полимерных (чаще эпоксидных) смол.
Углеродные композиционные материалы отличаются высокой прочностью, жесткостью и малой массой, часто прочнее стали, но гораздо легче.
Производство полимерных материалов
Наше предложение
Производство полимерных материалов требует значительного опыта. Для достижения принятых стандартов качества необходимы не только квалифицированные сотрудники, но и налаженная технология изготовления изделий. По этим причинам все представленные позиции в каталоге имеют высокое качество, гарантируют достижение поставленных перед ними задач и обладают регулярными положительными отзывами.
В каталоге вы сможете подобрать изделия для таких сфер:
- машиностроение;
- космическая и авиационная промышленность;
- ветроэнергетика;
- строительство;
- спортивный инвентарь;
- товары народного потребления
Наше производство изделий из полимерных материалов может обеспечить вас тем количеством изделий, которое вам будет необходимо. Отсутствуют ограничения по объему заказа. При этом вы можете рассчитывать на полную консультацию от профессионалов и оперативное выполнение поставленных задач. Производство полимерных материалов в России, которое мы осуществляем, дает возможность приобретения необходимых единиц каталога по оптовой системе. Изучите наш каталог, а также, если у вас остались какие-либо вопросы – не откладывайте их на потом и обращайтесь прямо сейчас в нашу службу поддержки.
Почему цена на углеволокно так высока?
Большие затраты энергии — основная причина высокой себестоимости углеродного волокна. Впрочем, это с лихвой компенсируется впечатляющим результатом. Даже не верится, что все начиналось с «мягкого и пушистого» материала, содержащегося в довольно прозаических вещах и известных не только сотрудникам химических лабораторий. Белые волокна — так называемые сополимеры полиакрилонитрила — широко используются в текстильной промышленности. Они входят в состав плательных, костюмных и трикотажных тканей, ковров, брезента, обивочных и фильтрующих материалов. Иными словами, сополимеры полиакрилонитрила присутствуют везде, где на прилагающейся этикетке упомянуто акриловое волокно. Некоторые из них «несут службу» в качестве пластмасс. Наиболее распространенный среди таковых — АБС-пластик. Вот и получается, что «двоюродных родственников» у карбона полным-полно. Карбоновая нить имеет впечатляющие показатели по усилию на разрыв, но ее способность «держать удар» на изгиб «подкачала». Поэтому, для равной прочности изделий, предпочтительнее использовать ткань. Организованные в определенном порядке волокна «помогают» друг другу справиться с нагрузкой. Однонаправленные ленты лишены такого преимущества. Однако, задавая различную ориентацию слоев, можно добиться искомой прочности в нужном направлении, значительно сэкономить на массе детали и излишне не усиливать непринципиальные места.
Что такое карбоновая ткань?
Для изготовления карбоновых деталей применяется как просто углеродное волокно с хаотично расположенными и заполняющими весь объем материала нитями, так и ткань (Carbon Fabric). Существуют десятки видов плетений. Наиболее распространены Plain, Twill, Satin. Иногда плетение условно — лента из продольно расположенных волокон «прихвачена» редкими поперечными стежками только для того, чтобы не рассыпаться. Плотность ткани, или удельная масса, выраженная в г/м2, помимо типа плетения зависит от толщины волокна, которая определяется количеством угленитей. Данная характеристика кратна тысячи. Так, аббревиатура 1К означает тысячу нитей в волокне. Чаще всего в автоспорте и тюнинге применяются ткани плетения Plain и Twill плотностью 150–600 г/м2, с толщиной волокон 1K, 2.5K, 3К, 6K, 12K и 24К. Ткань 12К широко используется и в изделиях военного назначения (корпуса и головки баллистических ракет, лопасти винтов вертолетов и подводных лодок, и пр.), то есть там, где детали испытывают колоссальные нагрузки.
Бывает ли цветной карбон? Желтый карбон бывает?
Часто от производителей тюнинговых деталей и, как следствие, от заказчиков можно услышать про «серебристый» или «цветной» карбон. «Серебряный» или «алюминиевый» цвет — всего лишь краска или металлизированное покрытие на стеклоткани. И называть карбоном такой материал неуместно — это стеклопластик. Отрадно, что и в данной области продолжают появляться новые идеи, но по характеристикам стеклу с углем углеродным никак не сравниться. Цветные же ткани чаще всего выполнены из кевлара. Хотя некоторые производители и здесь применяют стекловолокно; встречается даже окрашенные вискоза и полиэтилен. При попытке сэкономить, заменив кевлар на упомянутые полимерные нити, ухудшается адгезия такого продукта со смолами. Ни о какой прочности изделий с такими тканями не может быть и речи. Отметим, что «Кевлар», «Номекс» и «Тварон» — патентованные американские марки полимеров. Их научное название «арамиды». Это родственники нейлонов и капронов. В России есть собственные аналоги — СВМ, «Русар», «Терлон» СБ и «Армос». Но, как часто бывает, наиболее «раскрученное» название — «Кевлар» — стало именем нарицательным для всех материалов.
Что такое кевлар и какие у него свойства?
По весовым, прочностным и температурным свойствам кевлар уступает углеволокну. Способность же кевлара воспринимать изгибающие нагрузки существенно выше. Именно с этим связано появление гибридных тканей, в которых карбон и кевлар содержатся примерно поровну. Детали с угольно-арамидными волокнами воспринимают упругую деформацию лучше, чем карбоновые изделия. Однако есть у них и минусы. Карбон-кевларовый композит менее прочен. Кроме того, он тяжелее и «боится» воды. Арамидные волокна склонны впитывать влагу, от которой страдают и они сами, и большинство смол. Дело не только в том, что «эпоксидка» постепенно разрушается водно-солевым раствором на химическом уровне. Нагреваясь и охлаждаясь, а зимой вообще замерзая, вода механически расшатывает материал детали изнутри. И еще два замечания. Кевлар разлагается под воздействием ультрафиолета, а формованный материал в смоле утрачивает часть своих замечательных качеств. Высокое сопротивление разрыву и порезам отличают кевларовую ткань только в «сухом» виде. Потому свои лучшие свойства арамиды проявляют в других областях. Маты, сшитые из нескольких слоев таких материалов, — основной компонент для производства легких бронежилетов и прочих средств безопасности. Из нитей кевлара плетут тонкие и прочные корабельные канаты, делают корд в шинах, используют в приводных ремнях механизмов и ремнях безопасности на автомобилях.
А можно обклеить деталь карбоном?
Непреодолимое желание иметь в своей машине детали в черно-черную или черно-цветную клетку привели к появлению диковинных суррогатов карбона. Тюнинговые салоны обклеивают деревянные и пластмассовые панели салонов углеродной тканью и заливают бесчисленными слоями лака, с промежуточной ошкуриванием. На каждую деталь уходят килограммы материалов и масса рабочего времени. Перед трудолюбием мастеров можно преклоняться, но такой путь никуда не ведет. Выполненные в подобной технике «украшения» порой не выдерживают температурных перепадов. Со временем появляется паутина трещин, детали расслаиваются. Новые же детали неохотно встают на штатные места из-за большой толщины лакового слоя.
Как производятся карбоновые и/или композитные изделия?
Технология производства настоящих карбоновых изделий основывается на особенностях применяемых смол. Компаундов, так правильно называют смолы, великое множество. Наиболее распространены среди изготовителей стеклопластиковых обвесов полиэфирная и эпоксидная смолы холодного отверждения, однако они не способны полностью выявить все преимущества углеволокна. Прежде всего, по причине слабой прочности этих связующих компаундов. Если же добавить к этому плохую стойкость к воздействию повышенных температур и ультрафиолетовых лучей, то перспектива применения большинства распространенных марок весьма сомнительна. Сделанный из таких материалов карбоновый капот в течение одного жаркого летнего месяца успеет пожелтеть и потерять форму. Кстати, ультрафиолет не любят и «горячие» смолы, поэтому, для сохранности, детали стоит покрывать хотя бы прозрачным автомобильным лаком.
Компаунды холодного твердения.
«Холодные» технологии мелкосерийного выпуска малоответственных деталей не позволяют развернуться, поскольку имеют и другие серьезные недостатки. Вакуумные способы изготовления композитов (смола подается в закрытую матрицу, из которой откачан воздух) требуют продолжительной подготовки оснастки. Добавим к этому и перемешивание компонентов смолы, «убивающее» массу времени, что тоже не способствует производительности. Говорить о ручной выклейке вообще не стоит. Метод же напыления рубленого волокна в матрицу не позволяет использовать ткани. Собственно, все идентично стеклопластиковому производству. Просто вместо стекла применяется уголь. Даже самый автоматизированный из процессов, который к тому же позволяет работать с высокотемпературными смолами (метод намотки), годится для узкого перечня деталей замкнутого сечения и требует очень дорогого оборудования.
Эпоксидные смолы горячего отверждения прочнее, что позволяет выявить качества карбонов в полной мере. У некоторых «горячих» смол механизм полимеризации при «комнатной» температуре запускается очень медленно. На чем, собственно, и основана так называемая технология препрегов, предполагающая нанесение готовой смолы на углеткань или углеволокно задолго до процесса формования. Приготовленные материалы просто ждут своего часа на складах.
В зависимости от марки смолы время жидкого состояния обычно длится от нескольких часов до нескольких недель. Для продления сроков жизнеспособности, приготовленные препреги, иногда хранят в холодильных камерах. Некоторые марки смол «живут» годами в готовом виде. Прежде чем добавить отвердитель, смолы разогревают до 50–60 C, после чего, перемешав, наносят посредством специального оборудования на ткань. Затем ткань прокладывают полиэтиленовой пленкой, сворачивают в рулоны и охлаждают до 20–25 C. В таком виде материал будет храниться очень долго. Причем остывшая смола высыхает и становится практически не заметной на поверхности ткани. Непосредственно при изготовлении детали нагретое связующее вещество становится жидким как вода, благодаря чему растекается, заполняя весь объем рабочей формы и процесс полимеризации ускоряется.
Компаунды горячего твердения.
«Горячих» компаундов великое множество, при этом у каждой собственные температурные и временные режимы отверждения. Обычно, чем выше требуемые показания термометра в процессе формовки, тем прочнее и устойчивее к нагреву готовое изделие. Исходя из возможностей имеющегося оборудования и требуемых характеристик конечного продукта, можно не только выбирать подходящие смолы, но делать их на заказ. Некоторые отечественные заводы-изготовители предлагают такую услугу. Естественно, не бесплатно.
Препреги как нельзя лучше подходят для производства карбона в автоклавах. Перед загрузкой в рабочую камеру нужное количество материала тщательно укладывается в матрице и накрывается вакуумным мешком на специальных распорках. Правильное расположение всех компонентов очень важно, иначе не избежать нежелательных складок, образующихся под давлением. Исправить ошибку впоследствии будет невозможно. Если бы подготовка велась с жидким связующим, то стала бы настоящим испытанием для нервной системы рабочих с неясными перспективами успеха операции.
Процессы, происходящие внутри установки, незатейливы. Высокая температура расплавляет связующее и «включает» полимеризацию, вакуумный мешок удаляет воздух и излишки смолы, а повышенное давление в камере прижимает все слои ткани к матрице. Причем происходит все одновременно.
С одной стороны, одни преимущества. Прочность такого углепластика практически максимальна, объекты самой затейливой формы делаются за один «присест». Сами матрицы не монументальны, поскольку давление распределено равномерно во всех направлениях и не нарушает геометрию оснастки. Что означает быструю подготовку новых проектов. С другой стороны, нагрев до нескольких сотен градусов и давление, порой доходящее до 20 атм., делают автоклав очень дорогостоящим сооружением. В зависимости от его габаритов цены на оборудование колеблются от нескольких сотен тысяч до нескольких миллионов долларов. Прибавим к этому нещадное потребление электроэнергии и трудоемкость производственного цикла. Результат — высокая себестоимость продукции. Есть, впрочем, технологии подороже и посложнее, чьи результаты впечатляют еще больше. Углерод-углеродные композиционные материалы (УУКМ) в тормозных дисках на болидах Формулы-1 и в соплах ракетных двигателей выдерживают чудовищные нагрузки при температурах эксплуатации, достигающих 3000 C. Эту разновидность карбона получают путем графитизации термореактивной смолы, которой пропитывают спрессованное углеродное волокно заготовки. Операция чем-то похожа на производство самого углеволокна, только происходит она при давлении 100 атмосфер. Да, большой спорт и военно-космическая сфера деятельности способны потреблять штучные вещи по «заоблачным» ценам. Для тюнинга и, тем более, для серийной продукции такое соотношение «цены-качества» неприемлемо.
Если решение найдено, оно выглядит настолько простым, что удивляешься: «Что же мешало додуматься раньше?». Тем не менее, идея разделить процессы, происходящие в автоклаве, возникла спустя годы поиска. Так появилась и стала набирать обороты технология, сделавшая горячее формование карбона похожим на штамповку. Препрег готовится в виде сэндвича. После нанесения смолы ткань с обеих сторон покрывается либо полиэтиленовой, либо более термостойкой пленкой. «Бутерброд» пропускается между двух валов, прижатых друг к другу. При этом лишняя смола и нежелательный воздух удаляются, примерно так же, как и при отжиме белья в стиральных машинах образца 1960-х годов. В матрицу препрег вдавливается пуансоном, который фиксируется резьбовыми соединениями. Далее вся конструкция помещается в термошкаф.
Тюнинговые фирмы изготавливают матрицы из того же карбона и даже прочных марок алебастра. Гипсовые рабочие формы, правда, недолговечны, но пара-тройка изделий им вполне по силам. Более «продвинутые» матрицы делаются из металла и иногда оснащаются встроенными нагревательными элементами. В серийном производстве они оптимальны. Кстати, метод подходит и для некоторых деталей замкнутого сечения. В этом случае легкий пуансон из вспененного материала остается внутри готового изделия. Антикрыло Mitsubishi Evo — пример такого рода.
Механические усилия заставляют думать о прочности оснастки, да и система матрица — пуансон требует либо 3D-моделирования, либо модельщика экстра-класса. Но это, все же, в сотни раз дешевле технологии с автоклавом.
Алексей Романов редактор журнала «ТЮНИНГ Автомобилей»
www.hccomposite.com
Карбоновые удилища. Вся правда о карбоне – Carptoday – карпфишинг
В последнее время, как только заходит речь об удилищах, сразу же вспоминают про различные аббревиатуры, которые характеризуют карбон, из которого сделаны удилища. 1К, 2К, 3К. «Это удилище из высокотехнологичного карбона», «Высококачественный карбон, делает удилище..», «Карбон, из которого сделан бланк, отвечает самым высоким требованиям» и так далее, и так далее. А что же скрывается за всей этой маркетинговой терминологией?
Что такое карбон?
Карбон — углерод, представляющий собой полимерный композиционные материал из переплетенных нитей углеродного волокна, расположенных в матрице из полимерных смол. Отличается высоко прочностью и малой массой. Зачастую гораздо прочнее стали, но в разы легче. По удельным характеристикам превосходит многие высокопрочные стали.
Но отойдем в сторону от точных определений. Самое главное, что вы должны понимать в карбоне, что его на самом деле существует два вида: чистое углеродное волокно (оно же carbon fiber) и углепластик (полимер, усиленный углеродным волокном — carbon fiber reinforced polymer). Оба этих материала в быту называют карбоном, что, в конечном итоге, привело к тому, что понятия стали путать между собой.
Практически весь карбон, из которого делаются удилища получается из полиакрилонитрила (сокращенно ПАН) при помощи окислительного пиролиза и последующей обработки в инертном газе. Нити углерода получаются очень тонкие (ориентировочно 0,005-0,10мм в диаметре), сломать их очень просто, а вот порвать очень сложно. Из этих нитей и сплетаются ткани, из которых затем делаются бланки для удилищ.
Почему карбон так удобен для производстве удилищ?
Использование карбона позволяет достигнуть высокой прочности удилища, жесткости, при очень малом весе. Дело в том, что карбон является материалом, механические свойства которого зависят от направления волокон. Комбинируя их в различных направлениях, можно добиваться оптимальных характеристик различных изделий, будь то удилища или любое другой изделие. То есть, характеристики бланка зависят напрямую от того плетения, на которое пал выбор разработчиков удилища. Карбон позволяет добиться практически любой формы изделия, именно поэтому у инженеров куда больше возможностей и свободы в создании «идеального» удилища.
Из какого карбона лучше всего покупать удилища?
Это очень сложный вопрос. Определить на глазок что за карбон перед вами очень тяжело. Производители могут написать всякое. Единственный совет, который точно можно дать — это избегать различных дешевых «трехкопеечных» бланков непонятного производства. Остается только гадать откуда производитель берет этот материал. А самое главное, большинство рецептов карбонового волокна являются частной собственностью (запатентованными) и просто так ни одна фирма не расскажет вам состав.
Точно так же не стоит доверять различным рекламным лозунгам, что такая-то компания использует «особенный», «исключительный», «высокотехнологичный» и так далее карбон. Правда состоит в том, что две трети мирового рынка по производству карбона принадлежат трем японским фирмам — Toray (30%), Mitsubishi (18%), Toho (18%). За ними расположились такие фирмы, как венгерская Zoltek (17%), немецкая Hexcel (7%), американская Cytek (3%), на всех остальных приходится в общей сложности еще 6%.
Всего в год производится порядка 43,5 тысяч тонн карбона. Из них 41% — потребляет авиация, космическая и военные промышленности. 17% — спорт, 12% — строительство 12% — различные нужды, по 5%-6% автомобилестроение, гражданская инженерия и так далее. Не будем тонуть в цифрах.
Важно, что из всего оборота на спорт, рыбалка забирает не более 2-3%. Теперь вдумайтесь — если вы владеете инфраструктурой, позволяющей исследовать новые виды карбоновых волокон, чем вы займетесь — производством деталей для космической промышленности или для удилищ? Будете работать с 41% рынка или сосредоточитесь на двух процентах даже не от общего рынка, а от 1/5 этого рынка? Ответ очевиден, поэтому искренность заявлений производителей рыболовных аксессуаров касательно «уникального карбона» вызывает большие подозрения. Мы не беремся утверждать, правда это или нет. Мы просто даем пищу для размышлений.
Характеристики карбона
При получении карбона из поликарилонитрила, под микроскопом полученная нить будет напоминать ствол дерева. Плотный в центре, с шероховатой корой снаружи. Если продолжать очищать нить от «коры», то получится нить меньшего диаметра, но большей плотности. Соответственно на одну и ту же единицу площади поместится большее количество таких нитей, что позволит добиться не меньшей жесткости, но гораздо уменьшить вес. Производство таких тонких волокон сопряжено с большими издержками, потому что волокно получается хрупким и использовать его необходимо с большой осторожностью. Отсюда и высокая стоимость такого карбона. Однако очень эластичный карбон является очень хрупким материалом. Поэтому инженером постоянно приходится ломать голову, чтобы найти оптимальный баланс между прочностью и эластичностью. Это достигается уже при помощи рецепта карбонового волокна, в котором комбинируют несколько слоев карбона с различными характеристиками. Каждая такая комбинация и есть главная тайна и секрет любого удилища, да и просто изделия.
Теперь стоит поговорить о самых наших любимых характеристиках — 1К, 2К, 3К, которыми часто маркируют карбон. Подобная маркировка относится к плетению углеродного волокна. Нити собирают в полоски и эти полоски переплетают друг с другом. 1К означает, что в полосе 1000 нитей, 2К — 2000 нитей, а 3К — 3000 нитей. На самом деле эта характеристика никаким образом не является признаком тех или иных свойств самого волокна. Важно не количество нитей в полосе, а то, каким образом плетутся эти полосы, и из какого состава-рецепта сделаны волокна. А это уже зависит от производителя.
Вернемся к мировому рыболовному рынку!
Здесь все сурово. Подавляющее большинство удилищ, которые сегодня продаются в магазинах изготовлены в Азии, на фабриках, каждая из которых обслуживает сразу несколько брендов. Современные бренды, причем не только в рыболовной индустрии, в большинстве своем являются самыми настоящими маркетинговыми и инженерными центрами, но не производителями. Они заключает контракты с так называемыми Original Equipment Manufactures, если говорить по-русски, посредниками, отсылают им дизайн и желаемые характеристики, которые они хотят получить на выходе, а уже OEM несет ответственность за производство. Такие фабрики отправляют готовые удилища, на которых стоит Made in China, или же могут отправить удилище, которое будет еще доведено до ума. Во втором случае вы можете зачастую видеть заветные Made in UK, Made in Germany и так далее.
Вполне распространенная практика, когда сразу несколько компаний работает с одной и той же фабрикой. Но также и бывает масса случаев, когда один бренд работает с несколькими OEM, когда хочет производить несколько видов удилищ.
Но это вовсе не означает, что вас обманывают. Как раз нет. Ведущие бренды отдают процесс производства карбоновых удилищ в руки профессионалов, которые занимаются только плетением карбоновых волокон и изделиями из карбона. Конечно, это все стоит денег, и увеличивает цену исходного продукта. Теперь представим ситуацию, когда вы покупаете вроде бы карбоновое удилище, которое стоит ну совсем дешево.
Сразу можете убрать отсюда работы по инженерным расчетам и дизайнеров. Вам просто продают готовую, стандартную заготовку, уберите затраты на маркетинговые исследования и сертификацию производства (самый главный признак отсутствия контроля качества) и так далее.
Репутационные риски заставляют известные бренды подходит крайне ответственно к вопросу качества, тогда как никому неизвестные производители подобных рисков вообще не имеют. Ну закрыл ты эту фирму, открыл завтра новую. Вот и все дела. Вы никогда не узнаете какие конкретно материалы были использованы, какая смола, что ожидать от удилища. Если вы считаете данный риск оправданным низкой ценой, конечно, покупайте. Но разве много у нас людей осознают эти риски? Надеемся, что после прочтения данной статьи, их число хотя бы немножко увеличится.
Полное или частичное копирование без согласования с редакцией портала запрещено
carptoday.ru
Понятие о карбоне, его основные свойства и назначение — Мегаобучалка
Введение
Полимерные вещества внедрились во все сферы человеческой деятельности – технику, здравоохранение, быт. Ежедневно мы сталкиваемся с различными пластмассами, резинами, синтетическими волокнами. Полимерные материалы обладают многими полезными свойствами: они высокоустойчивы в агрессивных средах, хорошие диэлектрики и теплоизоляторы. Некоторые полимеры обладают высокой стойкостью к низким температурам, другие – водоотталкивающими свойствами и так далее. Например карбон прочный, как сталь, но при этом легче ее во много раз. Его фактура и прочностные качества привлекают много внимания со стороны промышленных дизайнеров, и появление карбоновых деталей в корпусах автомобилей и мотоциклов становится не редким. А стеклопластики могут выдерживать невероятную нагрузку и воздействие воды, имея низкий удельный вес. Благодаря таким качествам как: экологичность, износостойкость, экономичность и удивительная легкость, стеклопластик стал очень популярен у промышленных дизайнеров, так как эти качества позволяют создавать невероятные формы корпусов катеров, яхт.
В реферате будут подробно рассмотрены технологии производства изделий из резины, карбона, стеклопластика и оборудования, которое при этом используется.
К реферату будут прилагаться видеоматериалы с подробным описание технологического процесса производства изделий с использованием всех выше перечисленных материалов. Например: изготовление шин, судна из стеклопластика, каноэ из кевлара, резиновых ковриков и т.д.
Ниже будут приведены свойства и особенности рассматриваемых материалов. Будет описан их химический состав и краткая история появления.
Большой интерес представляет использование этих материалов современными промышленными дизайнерами, что так же будет проанализировано в реферате.
Производство изделий из карбона
Понятие о карбоне, его основные свойства и назначение.
Углеродное волокно – материал, состоящий из тонких нитей диаметром от 3 до 15 микрон, образованных преимущественно атомами углерода. Атомы углерода объединены в микроскопические кристаллы, выровненные параллельно друг другу. Выравнивание кристаллов придает волокну большую прочность на растяжение. Углеродные волокна характеризуются высокой силой натяжения, низким удельным весом, низким коэффициентом температурного расширения и химической инертностью.
Рисунок 1. Карбоновая ткань
Углеродное волокно является основой для производства углепластиков (или карбона, карбонопластиков, от “carbon”, “carbone” – углерод). Углепластики – полимерные композиционные материалы из переплетенных нитей углеродного волокна, расположенных в матрице из полимерных (чаще эпоксидных) смол.
Углеродные композиционные материалы отличаются высокой прочностью, жесткостью и малой массой, часто прочнее стали, но гораздо легче.
Слово «карбон» — своего рода профессиональный жаргонизм, точнее сокращение от английского Carbon Fiber (углеродное волокно), под эгидой которого, в общем понимании, объединилось огромное количество самых разных материалов. Примерно, как тысячи различных веществ с отличающимися физическими, химическими и техническими свойствами носят название «пластмасса». В случае с карбоном, общим для материалов стал углеволоконный наполнитель, но не связующее вещество, которое может быть разным. Даже полиэтиленовая пленка с впаянными в нее угольными нитями с полным правом может носить это гордое имя. Просто сложившейся классификации углепластиков еще нет.
Применение карбона.
В последние годы проникновение карбона в конструкцию затюнингованных энтузиастами «аппаратов» приняло лавинообразный характер. Кроме того, углепластик все чаще и чаще упоминается в описаниях серийных машин. Этот материал, имеющий военно-космическую и спортивную предысторию, становится все популярнее. Прочность и легкость материалов ценятся конструкторами автомобилей уже давно, примерно с 50-х годов прошлого века. Сегодняшний прогресс технологий производства увеличивает соблазн применять больше композитов в новых разработках. Для владельца машины подобные детали ценны не только декоративностью рисунка углеродной ткани и завораживающей «переливчатостью» отраженного волокнами света, но и сохраняющейся аурой эксклюзивности. Со стороны производителя предложение карбоновых элементов в отделке — показатель технологической «продвинутости» фирмы.
Рисунок 2. Карбоновые детали автомобиля
Краткий курс истории.
Не нарушая сложившихся традиций, после «службы в армии» углепластик «занялся» спортом. Лыжники, велосипедисты, гребцы, хоккеисты и многие другие спортсмены по достоинству оценили легкий и прочный инвентарь. В автоспорте карбоновая эра началась в 1976 году. Сначала на машинах McLaren появились отдельные детали из диковинного черно-переливчатого материала, а в 1981 на трассу вышел McLaren MP4 с монококом, полностью изготовленным из углеволоконного композита. Так идея главного конструктора команды Lotus Колина Чепмена, создавшего в 1960-х несущую основу гоночного кузова, получила качественное развитие. Однако в то время новый материал был еще неведом технологам от автоспорта, потому неразрушаемую капсулу для McLaren изготовила американская компания Hercules Aerospace, обладающая опытом военно-космических разработок. Сейчас же в активе практически всех ведущих команд Формулы-1 есть собственное оборудование для выпуска карбоновых монококов, рычагов подвески, антикрыльев, спойлеров, сидений пилотов, рулей и даже тормозных дисков.
Углеродное волокно состоит из множества тончайших нитей углерода. Прочность нитей на разрыв, сравнимая с прочностью легированной стали, при массе, меньшей, чем у алюминия, обуславливает высокие механические характеристики карбонов. Интересно, что наиболее распространенная технология получения столь прочного материала основана на методе «обугливания» волокон, по изначальным свойствам близким к шерсти. Исходный полимер белого цвета с мудреным названием полиакрилонитрил подвергается нескольким циклам нагрева в среде инертных газов. Сначала под воздействием высокой температуры (около 260 C) на молекулярном уровне изменяется внутренняя структура вещества. Затем при температурах повыше (около 700 C) атомы углерода «сбрасывают» водород. После нескольких «поджариваний» водород удаляется полностью. Теперь удерживавшие его силы направлены на упрочнение связей между оставшимися элементами. На шерсть материал уже не похож, однако его прочность еще далека от идеала. И процесс под названием графитизация продолжается. Повторяющиеся операции нагрева до 1300 C «очищают» почерневшее волокно уже от азота. Полностью избавиться от последнего не удается, однако его количество уменьшается. Каждый «шаг» делает содержание в веществе атомов углерода все больше, а их связь все крепче. Механизм упрочнения такой же, как и при «изгнании» водорода. Самая прочная продукция проходит несколько ступеней графитизации при температуре до 3000 C и обозначается аббревиатурой UHM.
Причины высокой стоимости карбона. Большие затраты энергии — основная причина высокой себестоимости углеродного волокна. Впрочем, это с лихвой компенсируется впечатляющим результатом. Даже не верится, что все начиналось с «мягкого и пушистого» материала, содержащегося в довольно прозаических вещах и известных не только сотрудникам химических лабораторий. Белые волокна — так называемые сополимеры полиакрилонитрила — широко используются в текстильной промышленности. Они входят в состав плательных, костюмных и трикотажных тканей, ковров, брезента, обивочных и фильтрующих материалов. Иными словами, сополимеры полиакрилонитрила присутствуют везде, где на прилагающейся этикетке упомянуто акриловое волокно. Некоторые из них «несут службу» в качестве пластмасс. Наиболее распространенный среди таковых — АБС-пластик. Вот и получается, что «двоюродных родственников» у карбона полным-полно.
Угольная нить имеет впечатляющие показатели по усилию на разрыв, но ее способность «держать удар» на изгиб «подкачала». Поэтому, для равной прочности изделий, предпочтительнее использовать ткань. Организованные в определенном порядке волокна «помогают» друг другу справиться с нагрузкой. Однонаправленные ленты лишены такого преимущества. Однако, задавая различную ориентацию слоев, можно добиться искомой прочности в нужном направлении, значительно сэкономить на массе детали и излишне не усиливать непринципиальные места.
Понятие карбоновой ткани.
Для изготовления карбоновых деталей применяется как просто углеродное волокно с хаотично расположенными и заполняющими весь объем материала нитями, так и ткань (Carbon Fabric). Существуют десятки видов плетений. Наиболее распространены Plain, Twill, Satin. Иногда плетение условно — лента из продольно расположенных волокон «прихвачена» редкими поперечными стежками только для того, чтобы не рассыпаться.
Плотность ткани, или удельная масса, выраженная в г/м2, помимо типа плетения зависит от толщины волокна, которая определяется количеством угленитей. Данная характеристика кратна тысячи. Так, аббревиатура 1К означает тысячу нитей в волокне. Чаще всего в автоспорте и тюнинге применяются ткани плетения Plain и Twill плотностью 150–600 г/м2, с толщиной волокон 1K, 2.5K, 3К, 6K, 12K и 24К. Ткань 12К широко используется и в изделиях военного назначения (корпуса и головки баллистических ракет, лопасти винтов вертолетов и подводных лодок, и пр.), то есть там, где детали испытывают колоссальные нагрузки.
Часто от производителей тюнинговых деталей и, как следствие, от заказчиков можно услышать про «серебристый» или «цветной» карбон. «Серебряный» или «алюминиевый» цвет — всего лишь краска или металлизированное покрытие на стеклоткани. И называть карбоном такой материал неуместно — это стеклопластик. Отрадно, что и в данной области продолжают появляться новые идеи, но по характеристикам стеклу с углем углеродным никак не сравниться. Цветные же ткани чаще всего выполнены из кевлара. Хотя некоторые производители и здесь применяют стекловолокно; встречается даже окрашенные вискоза и полиэтилен. При попытке сэкономить, заменив кевлар на упомянутые полимерные нити, ухудшается адгезия такого продукта со смолами. Ни о какой прочности изделий с такими тканями не может быть и речи.
Отметим, что «Кевлар», «Номекс» и «Тварон» — патентованные американские марки полимеров. Их научное название «арамиды». Это родственники нейлонов и капронов. В России есть собственные аналоги — СВМ, «Русар», «Терлон» СБ и «Армос». Но, как часто бывает, наиболее «раскрученное» название — «Кевлар» — стало именем нарицательным для всех материалов.
Определение кевлара.
По весовым, прочностным и температурным свойствам кевлар уступает углеволокну. Способность же кевлара воспринимать изгибающие нагрузки существенно выше. Именно с этим связано появление гибридных тканей, в которых карбон и кевлар содержатся примерно поровну. Детали с угольно-арамидными волокнами воспринимают упругую деформацию лучше, чем карбоновые изделия. Однако есть у них и минусы. Карбон-кевларовый композит менее прочен. Кроме того, он тяжелее и «боится» воды. Арамидные волокна склонны впитывать влагу, от которой страдают и они сами, и большинство смол. Дело не только в том, что «эпоксидка» постепенно разрушается водно-солевым раствором на химическом уровне. Нагреваясь и охлаждаясь, а зимой вообще замерзая, вода механически расшатывает материал детали изнутри. И еще два замечания. Кевлар разлагается под воздействием ультрафиолета, а формованный материал в смоле утрачивает часть своих замечательных качеств. Высокое сопротивление разрыву и порезам отличают кевларовую ткань только в «сухом» виде. Потому свои лучшие свойства арамиды проявляют в других областях. Маты, сшитые из нескольких слоев таких материалов, — основной компонент для производства легких бронежилетов и прочих средств безопасности. Из нитей кевлара плетут тонкие и прочные корабельные канаты, делают корд в шинах, используют в приводных ремнях механизмов и ремнях безопасности на автомобилях.
Применительно к автопромышленности, кевлар и карбон – легкие композитные материалы, представляющие собой застывшую полимерную смолу (эпоксидную, полиэфирную или др.), армированную сверхпрочными нитями. В этих нитях и состоит различие. Более распространенный карбон (он же углепластик, карбонопластик) укреплен углеродным волокном. Из него делают как крупные части обвеса гоночных машин – капоты, крылья, спойлеры, так и мелкие элементы – от трубопроводов до деталей оформления интерьера. Кевлар реже встречается в производстве автомобилей. Собственно, кевлар – это торговая марка одного из синтетических волокон, известного химикам как арамид. Из него изготавливают ткань, которая и применяется в автомобилестроении (а также в авиации, космической технике). Из нее делают композиты, армированные арамидной тканью. Из них, как правило, формуют крупные кузовные детали, в том числе несущие. Изделия из карбона и кевлара имеют значительные преимущества перед металлическими и пластиковыми. Они легче (плотность 1440–1450 кг/м3 против 7700–7900 кг/м3 у стали), прочнее, жестче. Однако они примерно в 20 раз дороже, чем стальные. Поэтому карбон и кевлар применяются только на гоночных болидах и мелкосерийных спортивных автомобилях.
megaobuchalka.ru
Где применяется углепластик 🚩 детали из углепластика 🚩 Естественные науки
Карбон одновременно очень легкий и чрезвычайно прочный материал, из него можно изготавливать детали любого размера и конфигурации. Углепластик обладает прекрасными аэродинамическими показателями, он способен выдерживать любые критические температуры. Нити углерода очень устойчивы к растяжению, наравне со сталью. Однако при сжатии или точечных ударах они могут поломаться, поэтому их переплетают под определенным углом и добавляют резиновые нити.В строительстве углеродопластики используют в системах внешнего армирования, например, при возведении или ремонте мостов, промышленных или складских зданий. Это позволяет проводить реконструкцию со значительно меньшими трудозатратами в сравнении с традиционными способами и в более сжатые сроки. При этом срок службы несущей конструкции увеличивается в несколько раз.
В авиации из углепластиков создают цельные композитные детали. Алюминиевые сплавы проигрывают в сравнении углепластиковым. Композитные детали имеют в 5 раз меньший вес и гораздо большую прочность и гибкость, а также устойчивость к давлению и некоррозийность. Даже их высокая стоимость не является критичной, так как масштабы применения карбонов в этой области не столь велики. Количество углеродных волокон здесь составляет около 10 процентов общего объема их производства.
В ракетостроении композиционные материалы используются очень широко. Высокие нагрузки космических полетов предъявляют соответствующие требования к материалам, используемым при производстве деталей. Углеродные материалы могут работать в условиях высоких и низких температур, при огромных вибрационных нагрузках, в вакууме и в условиях радиационного воздействия.
Атомная промышленность использует углепластики при создании энергетических реакторов, стойким к высоким температурам, радиации и большому давлению. Кроме этого, в этой отрасли особое внимание придается общей прочности внешних конструкций, и система внешнего армирования тоже имеет обширное применение.
В автомобилестроении из композитных материалов производят отдельные детали и узлы, а также автомобильные корпуса целиком. Сочетание прочности и легкости позволяет создавать безопасные и экологичные автомобили. Из углепластика делают обвесы, капоты, спойлеры. Карбоновые тормозные диски – непременный атрибут гоночных автомобилей.
В судостроении высокая прочность, коррозионная стойкость, высокая ударостойкость и низкая теплопроводность делают углепластики лучшим материалом для изготовления конструкций корпусов подводных лодок.
Одна из самых значимых областей применения углеродопластиков – ветроэнергетика. Легкость и непревзойденная прочность на изгиб этих материалов позволяют создавать удлиненные лопасти, обладающие большей энергопроизводительностью.
Эти же показатели углепластиков востребованы и в железнодорожной отрасли. Применение этих материалов позволяет облегчить конструкцию вагонов, снизив этим общий вес составов, что позволяет увеличивать их длину и улучшать скоростные характеристики. Кроме того, углепластики могут использоваться при строительстве железнодорожного полотна.
Композиционные материалы интенсивно входят и в быт каждого человека. Из углепластиков создаются многие товары народного потребления – детали бытовых приборов, спортивная экипировка и инвентарь, мебель, детали интерьера, музыкальные инструменты и многое другое.
Впервые карбон в автопромышленности начал использоваться при создании спортивных автомобилей еще в 60-е годы. Постепенно он стал привлекать внимание производителей обычных машин, что было связано с необычными свойствами этого материала.
Содержание статьи
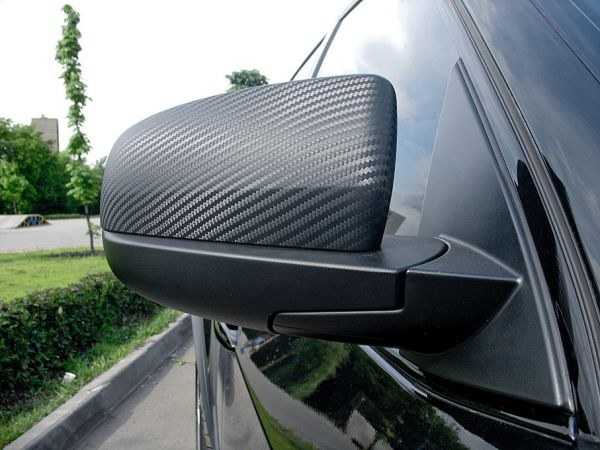
Карбон (или углеродное волокно) представляет собой множество тончайших нитей (диаметр 0,09 мм) углерода, прочность которых сравнима с легированной сталью при гораздо меньшей массе (примерно, как у алюминия). Из этих нитей сплетают волокно; в результате получается очень прочная ткань. Волокна могут располагаться хаотично, а могут быть и в виде плетения.
Исходным материалом для получения углеродного волокна служит полиакрилонитрил – вещество белого цвета, по свойствам напоминающее шерсть. Его несколько раз нагревают в среде инертных газов. На первом этапе при температуре в +260оС изменяют структуру вещества (на молекулярном уровне), затем уже при +700оС углеродные атомы «заставляют сбросить» водород. Постепенно, за несколько раз нагревов доводят до +3000оС, – данный процесс называют графитизацией. В результате углерода становится больше, а связь между его атомами прочнее. Упрощенно говоря, карбоном можно считать углеродное волокно, нагретое до обугливания.
Одно из главных положительных качеств карбона – высокая прочность, достигающая 1500 кг/куб. м. При этом прочность на растяжение достигает 1800 мПа. Температурный предел этого материала составляет +2000оС. Нити углеродного волокна хорошо работают только на растяжение, поэтому изготовление жесткой конструкции весьма проблематично. Карбон достаточно хрупок, при ударе крошится, поэтому отремонтировать деталь практически невозможно. При постоянном воздействии ультрафиолета углеволокно теряет первоначальный цвет. Однако положительные свойства перекрывают минусы; подтверждением этого служит изготовление из него тормозных дисков, колодок для спортивных машин, не говоря уже о космической технике.
Одной из характеристик карбона является удельная масса (или плотность ткани), выражаемая в г/кв. м. Этот параметр зависит от толщины волокна, в котором может быть несколько тысяч нитей. Например, если в маркировке присутствует обозначение 2К, то в волокне находится 2000 нитей. Самый прочный карбон обозначают аббревиатурой UHM. Помимо плотности, важной характеристикой является способ плетения нитей (в наиболее дешевом материале оно отсутствует).
При тюнинговании автотранспорта чаще всего используют такие типы плетения, как Twill, Satin, Plain. Наиболее распространенное число нитей в волокне – от 1 до 24К. Последний тип ткани широко используется при изготовлении военной техники, испытывающей огромные нагрузки.
Видео по теме
www.kakprosto.ru