Этапы производства керамзита | ООО «АКЗ» (Алексинский керамзитовый завод)
Для того чтобы материал получился высокого качества, важно грамотно подобрать сырье и подходящую технологию производства. Технология производства керамзита включает следующие основные этапы:
- добыча сырья (глины) в карьере и его транспортирование в глинозапасник;
- лабораторные испытания;
- дробление глины. На выходе получаются сырцовые гранулы установленного размера;
- термическая обработка сырцовых гранул, включающая сушку, обжиг и последующее охлаждение продукта;
- при необходимости дробление готового продукта;
- контроль качества производимого товара;
- сортировка керамзита по фракциям;
- складирование товара;
- фасовка товара;
- отгрузка заказчику.
Разработку месторождений глинистых пород производят открытым способом. Для добычи глинистого сырья используют одноковшовые и многоковшовые экскаваторы, ведущие разработку в карьере по всей высоте уступа, при необходимости с выделением отдельных пластов материала.
Мягкие глинистые породы добывают в карьерах, работающих сезонно, камнеподобные — в течение всего года. Для обеспечения непрерывной работы заводов устраивают глинохранилища вместимостью до полугодового запаса сырья с предохранением его от промерзания. Запасы глины также хранят в промежуточных конусах, где она вылеживается в течение нескольких месяцев на открытом воздухе.
В результате температурных воздействий, особенно мороза, переменного увлажнения и высушивания происходит предварительное разрушение естественной структуры сырья, значительно облегчающее его последующую переработку в однородную формовочную массу.
Технологические особенности производства керамзита
В качестве сырья для изготовления данной категории нерудных материалов используются преимущественно осадочные глинистые породы. Они имеют сложный состав и состоят как из минералов (гидрослюды, каолинита), так и из полевого шпата, кварца, карбонатов, органических и железистых примесей. Возможность использования сырья для производства керамзита определяется по критериям вспучивания во время обжига, легкоплавкости и нужного интервала вспучивания. Иногда для модификации данных параметров в материал могут быть добавлены специальные компоненты — органические или синтетические вещества.
Результатом обработки исходного сырья являются сырцовые гранулы нужного состава и размеров. Они подвергаются термической обработке — просушиванию, обжигу и охлаждению. На следующем этапе полученный материал сортируется и при необходимости дробится на мелкие фракции.
Оборудование для производства керамзита
Изготовление материала осуществляется с применением широкого спектра дорогостоящего оборудования — смесителей, специальных станков для разрыхления глины, камневыделительных и дырчатых вальцов, сушильных барабанов, печей для обжига, бункеров, пневматических транспортеров и аппаратов для сортировки гравия. Также для производства керамзита используются лотки, конвейеры, силосные банки и другие приспособления, объединенные в технологические линии.
Более подробную информацию читайте в нашей статье “производство керамзита”.
Добыча сырья (глины)
1 этап производства керамзита.
Добыча сырья (глины)
2 этап производства керамзита.
Добыча сырья (глины) однокошковым экскаватором. 3 этап производства керамзита.
Добыча сырья (глины) однокошковым экскаватором. 4 этап производства.
Транспортироване глины в глинозапасник
5 этап производства керамзита
Транспортироване глины в глинозапасник
6 этап производства керамзита
Дробление глины
7 этап производства керамзита
Дробление глины
8 этап производства керамзита
Транспортирование глины в сушильный барабан 9 этап производства керамзита
Термическая обработка сырцовых гранул
10 этап производства керамзита
Термическая обработка сырцовых гранул
11 этап производства керамзита
Термическая обработка сырцовых гранул
12 этап производства керамзита
Термическая обработка сырцовых гранул
13 этап производства керамзита
Транспортирование готового продукта в силоса 14 этап производства керамзита
Готовый продукт
15 этап производства керамзита
Отгрузка готового продукта заказчику
16 этап производства керамзита
Отгрузка готового продукта заказчику
17 этап производства керамзита
Отгрузка готового продукта заказчику
18 этап производства керамзита
Обслуживание оборудования
19 этап производства керамзита
Контроль качества
20 этап производства керамзита
Обслуживание техники
21 этап производства керамзита
Лабороторные испытания
22 этап производства керамзита
Взаимодействие с партнерами
23 этап производства керамзита
Ведение складской логистики.
24 этап производства керамзита.
Созерцание на природу.
25 этап производства керамзита.
Технология производства керамзита – Как производят керамзит
Технология производства керамзита и сущность технологического процесса производства состоит в обжиге глиняных гранул по оптимальному режиму.
Для вспучивания глиняной гранулы нужно, чтобы активное газовыделение совпало по времени с переходом глины в пиропластическое состояние.
Между тем, в обычных условиях газообразование при обжиге глин происходит в основном при более низких температурах, чем их пиропластическое размягчение.
Например, температура диссоциации карбоната магния — до 600°С, карбоната кальция — до 950 °С, дегидратация глинистых минералов происходит в основном при температуре до 800 °С. А выгорание органических примесей еще ранее, реакции восстановления окислов железа развиваются при температуре порядка 900 °С, тогда как в пиропластическое состояние глины переходят при температурах, как правило, выше 1100 °С.
Схема вращающейся печи для производства керамзита:
1—загрузка сырцовых гранул; 2— вращающаяся печь; 3— форсунка; 4— вспученный керамзитовый гравий; 5—поток горячих газов
В связи с этим при обжиге сырцовых гранул в производстве керамзита необходим быстрый подъем температуры. Так как при медленном обжиге значительная часть газов выходит из глины до ее размягчения и в результате получаются сравнительно плотные маловспученные гранулы. Но чтобы быстро нагреть гранулу до температуры вспучивания, ее сначала нужно подготовить, т. е. высушить и подогреть. В данном случае интенсифицировать процесс нельзя. Так как при слишком быстром нагреве в результате усадочных и температурных деформаций, а также быстрого парообразования гранулы могут потрескаться или разрушиться (взорваться).
Оптимальным считается ступенчатый режим термообработки по С. П. Онацкому: с постепенным нагревом сырцовых гранул до 200—600 °С (в зависимости от особенностей сырья) и последующим быстрым нагревом до температуры вспучивания (примерно 1200 °С).
Обжиг осуществляется во вращающихся печах (рис.), представляющих собой цилиндрические металлические барабаны диаметром до 2,5—5 м и длиной до 40— 75 м, футерованные изнутри огнеупорным кирпичом. Печи устанавливаются с уклоном примерно 3% и медленно вращаются вокруг своей оси. Благодаря этому сырцовые гранулы, подаваемые в верхний конец печи, при ее вращении, постепенно передвигаются к другому концу барабана, где установлена форсунка для сжигания газообразного или жидкого топлива. Таким образом, вращающаяся печь работает по принципу противотока: сырцовые гранулы перемещаются навстречу потоку горячих газов,подогреваются. И, наконец, попав в зону непосредственного воздействия огненного факела форсунки,вспучиваются. Среднее время пребывания гранул в печи — примерно 45 мин.
Технология производства керамзита – оптимальный режим термообработки.
Чтобы обеспечить оптимальный режим термообработки, зону вспучивания печи, непосредственно примыкающую к форсунке, иногда отделяют от остальной части (зоны подготовки) кольцевым порогом. Применяют также двухбарабанные печи, в которых зоны подготовки и вспучивания представлены двумя сопряженными барабанами, вращающимися с разными скоростями.
В двухбарабанной печи удается создать оптимальный для каждого вида сырья режим термообработки.
Промышленный опыт показал, что при этом улучшается качество керамзита, значительно увеличивается его выход, а также сокращается удельный расход топлива.
В связи с тем, что хорошо вспучивающегося глинистого сырья для производства керамзита сравнительно мало, при использовании средне- и слабовспучивающегося сырья необходимо стремиться к оптимизации режима термообработки.
Из зарубежного опыта известно, что для получения заполнителей типа керамзита из сырья (промышленных отходов), отличающегося особой чувствительностью к режиму обжига. Используют трехбарабанные вращающиеся печи или три-четыре последовательно располагаемые печи. В которых обеспечиваются не только оптимальные скорость и длительность нагрева на каждом этапе термообработки, но и различная газовая среда.
Значение характера газовой среды в производстве керамзита обусловлено происходящими при обжиге химическими реакциями. В восстановительной среде окись железа Fe2O3 переходит в закись FeO. Это является не только одним из источников газообразования, но и важнейшим фактором перехода глины в пиропластическое состояние.
Внутри гранул восстановительная среда обеспечивается за счет присутствия органических примесей или добавок, но при окислительной среде в печи (при большом избытке воздуха) органические примеси и добавки могут преждевременно выгореть.
Поэтому окислительная газовая среда на стадии термоподготовки, как правило, нежелательна, хотя имеется и другая точка зрения, согласно которой целесообразно получать высокопрочный керамзитовый гравий с невспученной плотной корочкой. Такая корочка толщиной до 3 мм образуется (по предложению Северного филиала ВНИИСТ) при выгорании органических примесей в поверхностном слое гранул, обжигаемых в окислительной среде.
По мнению автора, при производстве керамзита следует стремиться к повышению коэффициента вспучивания сырья, так как невспучивающегося или маловспучивающегося глинистого сырья для получения высокопрочного заполнителя имеется много, а хорошо вспучивающегося не хватает.
С этой точки зрения наличие плотной корочки значительной толщины на керамзитовом гравии свидетельствует о недоиспользовании способности сырья к вспучиванию и уменьшении выхода продукции.
В восстановительной среде зоны вспучивания печи может произойти оплавление поверхности гранул, поэтому газовая среда здесь должна быть слабоокислительной. При этом во вспучивающихся гранулах поддерживается восстановительная среда, обеспечивающая пиропластическое состояние массы и газовыделение, а поверхность гранул не оплавляется.
Характер газовой среды косвенно, через окисное или закисное состояние железистых примесей, отражается на цвете керамзита. Красновато-бурая поверхность гранул говорит об окислительной среде (Fe2O3), темно-серая, почти черная окраска в изломе — о восстановительной (FeO).
Технология производства керамзита: 4 основных схемы
Различают четыре основные технологические схемы подготовки сырцовых гранул, или четыре способа производства керамзита: сухой, пластический, порошково-пластический и мокрый.
Сухой способ используют при наличии камнеподобного глинистого сырья (плотные сухие глинистые породы, глинистые сланцы). Он наиболее прост: сырье дробится и направляется во вращающуюся печь. Предварительно необходимо отсеять мелочь и слишком крупные куски, направив последние на дополнительное дробление.
Этот способ оправдывает себя, если исходная порода однородна, не содержит вредных включений и характеризуется достаточно высоким коэффициентом вспучивания.
Наибольшее распространение получил пластический способ. Рыхлое глинистое сырье по этому способу перерабатывается в увлажненном состоянии в вальцах, глиномешалках и других агрегатах (как в производстве кирпича). Затем из пластичной глиномассы на дырчатых вальцах или ленточных шнековых прессах формуются сырцовые гранулы в виде цилиндриков, которые при дальнейшей транспортировке или при специальной обработке окатываются, округляются.
Качество сырцовых гранул во многом определяет качество готового керамзита.
Поэтому целесообразна тщательная переработка глинистого сырья и формование плотных гранул одинакового размера.
Размер гранул задается исходя из требуемой крупности керамзитового гравия и установленного для данного сырья коэффициента вспучивания.
Гранулы с влажностью примерно 20% могут сразу направляться во вращающуюся печь или, что выгоднее, предварительно подсушиваться в сушильных барабанах. В других теплообменных устройствах с использованием тепла отходящих дымовых газов вращающейся печи. При подаче в печь подсушенных гранул ее производительность может быть повышена.
Таким образом, технология производства керамзита по пластическому способу сложнее, чем по сухому.
Более энергоемко, требует значительных капиталовложений. Но, с другой стороны, переработка глинистого сырья с разрушением его естественной структуры, усреднение, гомогенизация, а также возможность улучшения его добавками позволяют увеличить коэффициент вспучивания.
Порошково-пластический способ отличается от пластического тем, что вначале помолом сухого глинистого сырья получают порошок, а потом из этого порошка при добавлении воды получают пластичную глиномассу, из которой формуют гранулы, как описано выше. Необходимость помола связана с дополнительными затратами. Кроме того, если сырье недостаточно сухое, требуется его сушка перед помолом. Но в ряде случаев этот способ подготовки сырья целесообразен: если сырье неоднородно по составу, то в порошкообразном состоянии его легче перемешать и гомогенизировать; если требуется вводить добавки, то при помоле их легче равномерно распределить.
Если в сырье есть вредные включения зерен известняка, гипса, то в размолотом и распределенном по всему объему состоянии они уже не опасны.
Если такая тщательная переработка сырья приводит к улучшению вспучивания, то повышенный выход керамзита и его более высокое качество оправдывают произведенные затраты.
Мокрый (шликерный) способ заключается в разведении глины в воде в специальных больших емкостях — глиноболтушках. Влажность получаемой пульпы (шликера, шлама) примерно 50%. Пульпа насосами подается в шламбассейны и оттуда — во вращающиеся печи. В этом случае в части вращающейся печи устраивается завеса из подвешенных цепей. Цепи служат теплообменником: они нагреваются уходящими из печи газами и подсушивают пульпу, затем разбивают подсыхающую «кашу» на гранулы, которые окатываются, окончательно высыхают, нагреваются и вспучиваются. Недостаток этого способа — повышенный расход топлива, связанный с большой начальной влажностью шликера. Преимуществами являются достижение однородности сырьевой пульпы, возможность и простота введения и тщательного распределения добавок, простота удаления из сырья каменистых включений и зерен известняка. Этот способ рекомендуется при высокой карьерной влажности глины, когда она выше формовочной (при пластическом формовании гранул). Он может быть применен также в сочетании с гидромеханизированной добычей глины и подачей ее на завод в виде пульпы по трубам вместо применяемой сейчас разработки экскаваторами с перевозкой автотранспортом.
Керамзит, получаемый по любому из описанных выше способов, после обжига необходимо охладить. Технология производства керамзита.
Установлено, что от скорости охлаждения зависят прочностные свойства керамзита. При слишком быстром охлаждении керамзита его зерна могут растрескаться или же в них сохранятся остаточные напряжения, которые могут проявиться в бетоне. С другой стороны, и при слишком медленном охлаждении керамзита сразу после вспучивания возможно снижение его качества из-за смятия размягченных гранул. А также в связи с окислительными процессами, в результате которых FeO переходит в Fe2O3, что сопровождается деструкцией и снижением прочности.
Сразу после вспучивания желательно быстрое охлаждение керамзита до температуры 800—900 °С для закрепления структуры и предотвращения окисления закисного железа. Затем рекомендуется медленное охлаждение до температуры 600—700 °С в течение 20 мин для обеспечений затвердевания стеклофазы без больших термических напряжений, а также формирования в ней кристаллических минералов, повышающих прочность керамзита. Далее возможно сравнительно быстрое охлаждение керамзита в течение нескольких минут.
Технология производства керамзита
Первый этап охлаждения керамзита осуществляется еще в пределах вращающейся печи поступающим в нее воздухом. Затем керамзит охлаждается воздухом в барабанных, слоевых холодильниках, аэрожелобах.
Для фракционирования керамзитового гравия используют грохоты, преимущественно барабанные — цилиндрические или многогранные (бураты).
Внутризаводской транспорт керамзита — конвейерный (ленточные транспортеры), иногда пневматический (потоком воздуха по трубам). При пневмотранспорте возможно повреждение поверхности гранул и их дробление. Поэтому этот удобный и во многих отношениях эффективный вид транспорта керамзита не получил широкого распространения.
Фракционированный керамзит поступает на склад готовой продукции бункерного или силосного типа.
Технология производства керамзита, раскрыта не в полной мере в данной статье. Но, если у Вас появились вопросы, то можете задать их нашим менеджерам в любое удобное время.
Из чего делают керамзит и технология изготовления своими руками
Состав и характеристики
В составе керамзита содержатся глина и ее сланцы, процесс изготовления проходит методом обжига исходной сырьевой массы в специальных печах
При температуре в 1 000 – 1 300 градусов глина вспучивается и переходит в пиропластическое состояние. С учетом качества исходного материала, создаваемого температурного режима, длительности процесса обжига и иных технологических особенностей изготовления получаются разные технические показатели материала, самыми значимыми из которых считаются размеры зерен, плотность и объемный вес.
Параметры керамзита определены ГОСТом, регламентирующим качественные показатели строительных материалов с пористой структурой. Часть показателей не регулируется, но они все же остаются важными характеристиками. Основные свойства рассмотрим более подробно:
- фракции керамзита. Их всего три, и размеры варьируются в диапазонах 5 – 10, 10 – 20, 20 – 40 мм. В отдельную категорию вынесены фракции, используемые в строительстве. Это гранулы и щебенка, размеры которых составляют от 2.5 до 10 мм, и широкие смесевые фракции от 5 до 20 мм;
- марки по насыпной плотности. Всего их семь. Этот параметр определяет плотность материала без учета промежуточных участков, образуемых гранулами или осколками;
- показатель прочности.
Гравийный материал насчитывает тринадцать марок, для щебня их несколько меньше – всего одиннадцать. Показатель прочности щебня и гравия одной марки отличается. Между керамзитовыми марками по значениям плотности и прочности прослеживается взаимосвязь – рост плотности влечет за собой увеличение прочности;
- коэффициент уплотнения. Данная величина согласовывается с потребителем и не превышает показатель 1.15. Ее применяют для учета уплотнения керамзита в процессе транспортировки и хранения. Пользуются таким показателем часто при погрузке материала и его реализации;
- тепловая проводимость. Один из важных показателей, определяющий теплоизоляционные возможности керамзита. Диапазон узкий, что подтверждает высокие теплоизоляционные показатели керамзита, и от роста плотности этот коэффициент увеличивается;
- влагопоглощение. Этот важный параметр показывает изменения качеств керамзита под воздействием воды. Керамзит считается относительно устойчивым материалом, значение влагопоглощения составляет 8 – 20 процентов;
- шумоизоляция.
Лучших показателей с помощью керамзита можно достичь, засыпав керамзит под деревянный пол;
- устойчивость к морозам. Из-за низкого влагопоглощения и особенностей основного сырья (глины) керамзит обладает высокими морозоустойчивыми свойствами.
Особенности технологии изготовления
С помощью специальных исследований исходного сырья определяют его пригодность к производству керамзита. Основными требованиями к начальному материалу считаются:
- возможность вспучивания от обжига;
- легкая плавкость;
- определенное время для вспучивания.
В сырье иногда добавляют специальные компоненты, улучшающие вспучивание. Это могут быть мазут или соляровое масло, перлит, анулит и т. п.
Результатом переработки сырья становятся сырцовые гранулы с определенными размерами и составом. Их сначала высушивают, потом обжигают и охлаждают. На очередном этапе производства материал рассортировывается по показателю плотности, при необходимости – дробится, чтобы получились более мелкие фракции. В завершении всего керамзит сортируется, складируется либо отгружается для отправки.
Весь процесс по своей сущности выглядит следующим образом: после подготовки глина подвергается тепловому удару, придающему ей пористость и способствующему процессу вспучивания. Из-за оплавлений оболочки керамзит получает герметизацию и становится прочным.
Добыча исходного сырья
Производственный процесс начинается с добычи исходного материала карьерным способом и его перевозки в глинозапасники. Разработки ведутся открытым способом, для этого используются одно- и многоковшовые экскаваторы. Отдельные пласты не выделяются, добыча идет по всей высоте.
При добыче камнеподобных пород в виде аргиллита и глинистых сланцев, используют буровзрывные работы. Такие породы могут разрабатываться в любое время года, а мягкие – только в подходящий для этого период.
Чтобы производственный процесс шел непрерывно, возводятся специальные морозостойкие хранилища для складирования глины, вмещающие полугодовой запас сырья. Можно под хранение использовать промежуточные конусы, в которых глина под открытым воздухом находится несколько месяцев.
Производство керамзита
Под воздействием температуры, периодических увлажнений и высыханий, структурное строение сырья частично нарушается, что существенно облегчает процесс его последующей переработки в однородную массу.
Как осуществляется производство керамзита
Производство керамзита начинается с добычи. Чаще всего используется открытый способ изъятия материала по всей плоскости и высоте залежей без разделения на слои. Для реализации поставленных задач привлекают специальные экскаваторы.
Аргиллиты, глинистые сланцы и другие камнеподобные породы добывают взрывным методом. Разработка ведется круглогодично. Для хранения используют вместительные глинохранилища, где можно разместить полугодовой запас добытого сырья.
Производство керамзита переходит в пассивный этап сушки. В ходе процедуры из материала уходит лишняя влага. Перепады температур и высыхание разрушают внутреннюю структуру материала. Это существенно облегчает последующие этапы обработки.
Способы получения керамзитовых гранул
Для изготовления керамзита применяют один из четырех способов
Сухой способ
Применяется, если керамзит получают из плотных каменистых глинистых пород и сланцев, используется иная технология изготовления. Исходный материал размельчается на дробильном оборудовании до получения зерен размером 1 – 20 мм. Керамзитовое сырье обжигается в барабанной печи, охлаждается, распределяется по фракциям. В таком варианте производства не предусмотрен этап формовки зерен, и конечный продукт отличается кубическими угловатыми очертаниями.
Мокрый способ
Глина помещается в большие емкости, называющиеся глиноболтушками. После этого заливается вода, чтобы получился шликер с уровнем влажности до пятидесяти процентов. Насосными установками его перекачивают в шламбассейны, откуда он попадает во вращающиеся печи. В печных барабанах происходит разбивка на отдельные гранулы, которые просушиваются газами, выделяемыми печью.
Способ подразумевает большой расход топлива, так как уровень влажности шликера достаточно высок. Но с его помощью сырье очищается от каменистых вкраплений, в него вводятся добавки, чтобы получилась однородная масса. Применяется такой вариант для сырья, отличающегося большим показателем влажности.
Пластический способ
Подготовленную природную глину, влажность которой не превышает тридцати процентов, подвергают двум этапам помола на специальных зубчатых вальцах – грубом и тонком. От такого процесса образуются гранулы, диаметр которых составляет 5 – 10 мм, поступающие в сушильные барабаны. В них полуфабрикат просушивается, подвергается окончательной обкатке, пока не приобретет овальные формы. После этого начинается обжиг, для которого в печах создается температурный режим от 800 до 1 350 градусов. Процесс проходит под постоянным вращением печных барабанов. Спекшиеся керамические гранулы, которые увеличили свой диаметр из-за вспучивания, попадают во вращающиеся холодильные установки. После остывания наступает последний этап – керамзит рассеивается по фракциям.
Порошково-пластический способ
Как производится керамзит таким способом? Исходный материал в сухом состоянии доводится до порошкообразной массы, потом в него добавляется вода. В итоге образуется пластичная масса, пригодная для формирования гранул. Способ считается довольно дорогостоящим, потому что приходится дополнительно измельчать сырье. Второй недостаток – гранулы подвергаются дополнительной сушке.
Так как качество керамзита зависит от качественного состояния сырца, глину следует хорошо переработать и сформировать из нее гранулы одинаковых размеров, параметры которых увеличатся при вспучивании.
Производство керамзита его состав
Состав керамзита
Основным материалом, из которого изготавливается строительный керамзит – это осадочные глинистые породы. Состав глинистых пород достаточно разнообразен и включает в себя не только обычную глину, а разнообразные примеси: кварца до 30%, органических соединений, полевого шпата, карбонатов и незначительное количество соединений разного рода металлов. Состав керамзита зависит от особенностей той или иной местности, где осуществлялась добыча сырья для производства.
Кроме изначально содержащихся в сырье компонентов, для достижения эффекта вспучивания в состав, на стадии производства могут добавляться искусственные примеси и органические соединения (соляра и масло).
Производство керамзита
Зависит от состава природного сырья и осуществляется тремя основными способами:
- Сухой способ производства
Используется для изготовления керамзита из максимально однородной глинистой каменистой породы, с минимальным количеством имеющихся примесей. Добытую однородную породу дробят и отправляют на обжиг. Считается самым простым и дешевым способом производства керамзита.
- Мокрый способ производства
При данном способе глинистую породу смешивают с водой и дополнительными примесями, которые необходимы для получения определенных свойств керамзита. Данную смесь подают во вращающуюся печь, где она комкуется естественным способом и высушивается под воздействием печных газов.
Такой способ эффективен при использовании влажной глинистой породы и необходимости дополнительных включений в материал.
печь для производства керамзита
- Пластичный способ производства
Наиболее затратный способ, с помощью которого создается материал с улучшенными техническими характеристиками. В данном случае, также применяется увлажнение сырья и добавка дополнительный примесей, для достижения однородной массы. Но в отличие от сухого производства, из полученной смеси, на ленточном прессе формируется гранулы примерно одинаковой формы, которые подаются в печь для обжига и просушки. Таким образом, получается твердый керамзит однообразной формы, со всеми свойствами кирпича. Однако, в отличие от кирпича, имеющий большую теплоэффективность, за счет пористости и значительно меньший вес. Подробнее про свойства кирпича.
Оборудование для производства керамзита
Из чего делают керамзит, мы выяснили. Остается разобраться, как устроена производственная линия по изготовлению этого строительного материала. В нее входят следующие агрегаты и приспособления:
- устройства для рыхления;
- дырчатые вальцы;
- глиносмесители;
- барабаны для сушки;
- печи, в которых выполняется обжиг;
- бункеры;
- пневматические транспортеры, ленточные и другие конвейеры;
- лотки;
- сортировщики для гравия.
Для производств керамзита требуется глиномеситель
На первичной обработке исходного материала применяется специальная дробильная установка. Состоит она из узла измельчения, в который входят:
- валы лопастного типа, способные совершать вращательные движения по направлению друг к другу;
- жесткая рама;
- зубчатый привод;
- приемочный бункер.
Как только валы начинают свое вращение, сырье измельчается до необходимых размеров. Специальные добавки вводятся через смесительную установку.
Сырье обжигается в печных устройствах с вращающимися барабанами, имеющими цилиндрические корпуса из стального материала. Конструктивно печь состоит из следующих элементов:
- головки для загрузки сырья и выгрузки материала;
- опорной станции;
- приводов;
- уплотнения концов;
- кожуха венцовой пары и т. д.
Печь устанавливается на фундаментной площадке. Опорой служит сварная рама и ролики, регулирующие ее положение.
Обустройства слоя гидроизоляции
Гидроизоляция поверхности – один из важнейших этапов утепления пола керамзитом. Наравне с другими теплоизоляционными материалами он способен терять свои свойства и характеристики, находясь под постоянным воздействием влаги.
Гидроизоляцию можно сделать одним из следующих способов:
- Настлать плотную полиэтиленовую пленку, делая на хлест между полосами и проклеивая стыки скотчем
- Обмазать всю поверхность перекрытия мастикой на основе битума
Для железобетонных перекрытий наибольшее распространение получил второй метод. Наносятся битумные мастики обычным валиком в несколько слоев. Каждый из них высыхает не более 3-4 часов
. Таким образом, вся работа будет завершена в течение одного дня.
По периметру стен наклеивают специальную гидроизолирующую демпферную ленту. Ее предназначение – значительно уменьшить воздействие на поверхность со стороны расширяющейся стяжки. Последняя, при росте температуры, будет незначительно увеличиваться в размерах, при снижении – наоборот сужаться.
Силикагель – один из самых эффективным материалов для гидроизоляции поверхностей. Он представляет собой гелиевые высушенные гранулы, произведенные из кремниевой кислоты. Материал способен устранить самый главный недостаток керамзита – низкий показатель влагостойкости.
Использование силикагеля рекомендуется одним из следующих методов:
- Укладка равномерного 8-10 мм слоя по подготовленной поверхности до керамзита
- Смесь силикагеля и керамзита в соотношении 1 к 10
Однако материал применяется крайне редко в частном строительстве по следующим причинам:
- В пыли содержатся вредные организму частицы
- В составе может содержаться хлорид кобальта – канцероген, который способен нанести здоровью человека вред
- Материал пожароопасен и взрывоопасен
Монтаж маяков
Следующий этап – монтаж маяков, между которыми будет засыпаться керамзит. Предпочтение рекомендуется отдавать металлическим Т-образным рейкам.
В первую очередь нужно прикрутить рейку вдоль стены, которая противоположна дверному проему. Для фиксации используют цементно-песчаную смесь или шурупы.
Устанавливая каждый из маяков, необходимо следить за их параллельностью и высотой. Они все должны находиться на общем уровне. Если пол имеет значительный уклон, под низ для выравнивания кладут раствор или деревянные клинья.
Расстояние между планками делается равным от 0.5 до 1 м. Большим оно быть не должно. Высота будет зависеть от толщины теплоизоляционного слоя – чаще 8-10 см.
Приступаем к утеплению
Подготовив основание, утепление пола керамзитом можно осуществить одним из следующих способов:
- Сухим
- Мокрым
- Комбинированным
Сухой метод утепления подразумевает насыпку гранул материала между установленными маяками без добавления каких-либо жидких примесей, например, цементного раствора. Затем поверхность накрывается сухим полом (древесина, ДСП и т. д.).
Мокрый метод более сложный. Он представляет собой цементную стяжку, непосредственно в которую добавляется керамзит. Рабочая инструкция, позволяющая добиться наибольшей эффективности, следующая:
- Первый слой утеплителя необходимо приготовить из смеси, которая состоит из керамзита и бетона в соотношении 1:5
- Пол заливается полученной смесью таким образом, чтобы верхний уровень не достигал верхушек маяков примерно от 2 до 3 см
- У керамзита имеется свойство плывучести, поэтому в жидких составах он имеет особенность приподниматься вверх. При заливке раствора придется мастерком аккуратно погружать камушки в массу
- Когда 1-й слой немного застынет, необходимо заливать чистую бетонную стяжку без каких-либо примесей и выровнять ее правилом по маякам – это будет финишное покрытие пола
Недостаток мокрого способы заключается в том, что к дальнейшей работе разрешается приступать лишь через три недели. В этот период стяжку рекомендуется смачивать и укрывать от лучей солнца, чтобы не допустить появления трещин.
Комбинированный метод очень схож с сухим, за исключением одного «НО»: поверхность керамзита необходимо полить жидким бетоном, чтобы камушки скрепились между собой. Это исключит возможное появление поскрипываний.
Некоторые другие особенности утепления керамзитом
Не для кого не секрет, что утепление пола керамзитом одно из самых выгодных в экономическом плане. К тому же данный материал не отличается особой требовательностью к климату и эксплуатационным условиям. Однако, чтобы теплоизоляция получилась качественной, последовать некоторым советам:
- Мокрая стяжка может показаться достаточно высохшей спустя пару суток, однако максимальной прочности она достигнет не ранее, чем через 3 недели
- Чтобы гранулы получше сцеплялись друг с другом, рекомендуется смешивать керамзит различных фракций
- Чтоб готовая поверхность меньше поддавалась деформационным нагрузкам, керамзит рекомендуется армировать сеткой
- Алебастровый раствор сохнет гораздо быстрее чем классический цементный, поэтому многие используют его в процессе установки маяков
- Рассчитывая толщину слоя, необходимо принимать во внимание внешнюю нагрузку на поверхность – эти показатели прямо пропорциональны
- Сухой керамзит, не смешанный с цементным раствором, характеризуется лучшими теплоизоляционными свойствами, однако имеет особенность поскрипывать
Изготовление керамзита в домашних условиях
Возможно ли изготовление керамзита своими руками? Для этого потребуется качественное оснащение, с помощью которого можно готовить до 250 тысяч кубометров керамзита за один год. Для приготовления керамзита своими руками пользуются мини-заводами, топливом для которых служат мазут, уголь, газ природный.
При помощи таких заводиков получают керамзитовый песок, размеры гранул которого варьируются от 0.16 до 5 мм. Для этого гранулированное либо подвергнутое измельчению сырье обжигается в печи.
Зачастую для домашнего пользования покупают специальные дробильные установки, существенно упрощающие весь производственный процесс. Отметим, что с помощью чертежей, необходимых материалов и наличия желания, можно изготовить дробилку своими руками.
Для изготовления керамзита в домашних условиях часто пользуются дробильными установками
На домашнем мини-заводе производится керамзитовый песок из гравийного некондиционного материала. Для получения глинозольного керамзита используют в виде сырья плавкие породы и золу, полученную при сжигании торфа либо каменного и бурого угля. В результате образуется заполнитель, своими свойствами схожий с простым керамзитом. Зольный керамзитовый материал получается с помощью обжига или безобжиговым методом.
Изготовление керамзита – процесс достаточно энергоемкий. Но высокий уровень производительности и постоянный спрос на этот строительный материал помогают быстро окупить все предварительные затраты.
Как сделать глиняную гальку для гидропоники в домашних условиях [LECA, Hydroton]
Перейти к содержимому Как сделать гальку из глины для гидропоникиjoshp2018-09-27T18:45:22+00:00 Вы когда-нибудь задумывались, как сделать глиняные камешки для гидропоники? Если это так, то вы не одиноки. Но возможно ли это без сложного оборудования? Проекты «сделай сам» — это весело и часто экономят ваши деньги, но не все такие эксперименты успешны и практичны. Сначала мы рассмотрим преимущества глиняной гальки в качестве среды для выращивания, а затем покажем вам, как сделать глиняную гальку для гидропоники в домашних условиях, если вы хотите попробовать это самостоятельно.
Одно из первых решений, которое вам придется принять перед посадкой нового урожая, — это выбор среды для выращивания (или субстрата). Как вы, возможно, читали на нашей странице
Легкий керамзитобетонный заполнитель (LECA) — часто называемый гидротоном или глиняной галькой — состоит из шариков глины, которые были перегреты (во вращающейся печи) от температуры от 1100 до более 2000°F. процесс вызывает хлопки, которые создают характерные поры гальки. Эти поры, в дополнение к промежуткам между галькой, делают Hydroton легкой и воздушной средой для выращивания, которая обеспечивает воду, воздух и дренаж. Они pH-нейтральны, не разлагаются и не добавляют никаких дополнительных питательных веществ или веществ в питательный раствор в резервуаре гидропонной системы. Глиняные камешки также можно использовать повторно, что облегчает первоначальную стоимость. Из-за своих полезных свойств глиняная галька очень популярна в обеих гидропониках. На самом деле, глиняная галька также является самой популярной средой для выращивания аквапоники.
Преимущества гидропонной глиняной гальки- В отличие от перлита и песка гидропонная глиняная галька имеет достаточно места между собой для надлежащей просачивания (потока питательных веществ через среду выращивания).
Даже если мусор, водоросли или микробы цепляются за гальку, вероятность засорения минимальна.
- Хотя глиняные камешки не могут конкурировать с перлитом по воздухоудерживающей способности (AHC), они обладают способностью удерживать пузырьки воздуха и, таким образом, предотвращать появление зон, свободных от кислорода.
- Несмотря на то, что глина является широко распространенной экологически чистой средой, предприятия добывают ее для коммерческой продажи. Открытая добыча не является экологически чистой; тем не менее, вам не нужно чувствовать себя виноватым, если вы будете использовать свою глину как можно больше раз. Если вам когда-нибудь понадобится выбросить глиняные камешки, сначала раздавите их, чтобы они быстрее рассыпались.
- Глиняные камешки многоразового использования. Просто смойте любой налет, особенно органический, и вы сможете использовать его много раз.
- Поскольку Гидротон является рыхлым субстратом, с ним легко работать при пересадке или сборе растений.
- Глиняные гальки относительно гладкие, но они обеспечивают достаточную биологическую площадь поверхности (BSA) для выращивания колоний микробов, которые обеспечивают чувствительность и стабильность питательных веществ в системе.
- Поскольку глина инертна, она более устойчива к вредителям, чем органические среды. Опять же, смывайте органические отложения после каждого использования.
Керамзит Hydro Crunch
Купить сейчас
LECA Grow Media
Купить сейчас
Глиняная галька GROW!T
Купить сейчас
Емкость катионного обмена ( CEC ) — это измерение, используемое для оценки способности питательной среды привлекать, удерживать и обменивать определенные ионы из питательных веществ.
Поскольку галька Hydroton имеет высокое содержание CEC, на ней может образовываться белый налет из остатков соли, оставленных питательными растворами. Это может в конечном итоге убить ваши растения. Чтобы предотвратить это, регулярно удаляйте растения из горшков и промывайте перед повторной посадкой или промывайте систему. Всегда используйте воду со сбалансированным pH для полоскания и замачивания камней. При необходимости используйте продукты «Up pH» и «Down pH».
- Водоудерживающая способность (WHC) не так хороша с глиняной галькой, как с некоторыми другими средами. Так как Гидротон имеет тенденцию быстро стекать и высыхать, вам может потребоваться более частый полив. Однако, если вы живете в прохладном климате, выращиваете засухоустойчивые культуры или имеете систему орошения, это не будет проблемой.
- Поскольку галька Hydroton будет плавать до тех пор, пока не станет насыщенной, она может попасть в дренажные линии или фильтры и вызвать засор . Мелкие производители могут избежать этого, предварительно замочив их.
- Некоторым людям не нравится беспорядок , который создает красная пыль от коммерческого Hydroton.
Другие говорят, что тот, кто не хочет пачкаться, не должен быть фермером!
- Hydroton может быть дорогим вариантом . Если вы живете в районе с местными источниками глины, я призываю вас заняться изготовлением гальки в домашних условиях. Многие люди делают шарики из глины. Это то же самое, что и Hydroton, за исключением того, что глина не нагревается. См. Получение и обработка местной глины. Кроме того, поддерживайте связь с группами производителей (такими как форум Backyard Aquaponics), чтобы обмениваться идеями и информацией обо всем, что связано с гидропоникой.
Глиняная галька, используемая в гидропонике, производится агрегатными компаниями. Они добывают глину из земли, измельчают ее огромными шлифовальными машинами, а затем, по сути, обжигают глину (для расширения) в массивных вращающихся печах при чрезвычайно высокой температуре от 1100 до 2000 градусов. Так что, если вы думали, что будет легко воспроизвести то, как крупные компании-производители щебня производят свою глиняную гальку, угадайте еще раз! Поройтесь в Интернете, и вы практически не найдете обучающих видеороликов о том, как сделать глиняную гальку для гидропоники. Почему? Просто проще купить расходные материалы в Интернете, чем инвестировать тысячи долларов и бесчисленные часы, пытаясь сделать свои собственные с помощью этого типа (потенциально опасного) оборудования. Однако, если вы хотите поэкспериментировать и попробовать, следующий способ может помочь вам в этом.
Примечание. Мы не знаем, пробовал ли кто-нибудь этот метод, поэтому действуйте на свой страх и риск. Если вы это сделаете, дайте нам знать, как это работает!
1. Изучите источники природной или коммерческой глины в вашем регионе. Гончары — ваши лучшие друзья в этом начинании. Коммерческий Hydroton состоит из специального заполнителя, но я предполагаю, что глина, используемая для изготовления гончарных изделий, тоже подойдет. Поставщики предоставят или продадут вам небольшой образец для тестирования, прежде чем вы возьмете на себя обязательство купить большее количество.
2. Если вы можете арендовать или одолжить вращающуюся печь, вы можете загружать глину в больших количествах.
3. Если вы не можете воспользоваться вращающейся печью:
- Вручную сформируйте из глины гальку (диаметром около 1 дюйма). Вы можете раскатать глину в длинные полоски (или использовать экструдер), а затем разрезать ее на более мелкие кусочки, чтобы ускорить этот процесс. Ваши камешки не обязательно должны быть идеально сферическими.
- Поместите камешки в гончарную печь или другой источник тепла, способный нагреваться до 2000°F.
4. Нагревайте камешки до тех пор, пока они не превратятся в пузыри и не лопнут. Время, необходимое для этого, зависит от многих факторов. Моя знакомая гончар всегда обжигает свою работу на ночь, затем дает ей остыть в течение 8-10 часов.
5. Замочите камешки. Затем погладьте себя по спине. Вы на шаг ближе к тому, чтобы выйти из сети.
Советы по использованию глиняной гальки для гидропоники 1. Промойте перед использованием, чтобы удалить пыль и мусор, которые могут засорить фильтры или капельницы.
2. Замочите на 6–24 часа перед использованием. Убедитесь, что 3-дюймовый радиус вокруг всех растений остается насыщенным.
3. Во время замачивания добавьте питательный раствор. Смешайте раствор с концентрацией от одной четверти до половины вашей обычной концентрации или используйте раствор с электропроводностью (EC) 0,4 или меньше.
4. После сбора урожая переработайте гальку, удалив старые корни и промыв водой со сбалансированным pH. Некоторые садоводы рекомендуют стерилизовать гальку отбеливателем, горячим паром, изопропиловым спиртом или перекисью водорода. Важно попытаться убедиться, что ваш Hydroton не переносит никаких примесей с одной культуры на другую.
Как прорастить семена в гидропонике Глиняная галька Новички могут захотеть прорастить семена в другой среде, такой как минеральная вата или дробленый гидротон, чтобы уменьшить потребность в частом поливе. Чтобы использовать глиняные камешки:
1. Наполните сетчатые горшки диаметром от 1,5 до 2,5 дюймов предварительно замоченной галькой.
2. Поместите семена поверх гальки. Если указано типом растения, также покройте семена галькой.
3. Поместите эти горшки под купол влажности и используйте господа, чтобы держать растения увлажненными. Всплески тумана продолжительностью 4-10 секунд каждые 2-3 часа должны вызвать прорастание семян. Обязательно держите среду для выращивания, а также растения во влажном состоянии.
Как вырастить клоны (черенки) с помощью гидропонных глиняных камешков1. Техника низкой трансплантации. Наполните сетчатый горшок предварительно замоченной галькой примерно на одну треть или наполовину. Посадите стебель с узлом примерно на 1 дюйм ниже вершины гальки. Узел должен быть близко ко дну горшка. Узел — это то место, где будет прорастать новое растение. Перенесите рассаду в вашу гидропонную систему.
2. Метод верхнего капельного полива. Поместите черенки непосредственно в глубоководную культуру (DWC) или систему приливов и отливов (залив и слив). Расположите капельницы достаточно близко к свежепосаженным черенкам, чтобы обеспечить достаточный приток воды и питательных веществ.
10 фунтов. Галька Hydro Clay
Купить сейчас
10 фунтов. Гидротон 10L
Купить его сейчас
Органический гидротон
Купить его сейчас
Альтернативы гидропонике глиняной гальки Работатели, как правило, имеют свои любимые растущие средства и смешивать их в зависимости от индивидуальных условий. Альтернативы глиняной гальке включают кубики оазиса, кокосовое волокно (кокосовое волокно), торф, компостированную кору, гравий, песок, вулканическую породу, изоляцию из стекловолокна, опилки, пемзу, пенопласт, полиуретановые плиты для выращивания и рисовую шелуху (шелуху). В зависимости от вашего местоположения вы можете найти или сделать некоторые из этих носителей дома.
- Мы также рекомендуем изучить альтернативы:
- Growstone является более экологически чистым материалом, чем глина, состоящая из переработанного стекла. Минеральная вата
- (также называемая каменной ватой) состоит из волокон, полученных из расплавленной породы. Grodan — популярный бренд. Он уже давно используется в качестве среды для выращивания и до сих пор считается отраслевым стандартом среди крупных производителей. Из-за дороговизны и сложности утилизации (не разлагается, не может быть использован повторно) мелкие производители склонны выбирать другие среды. Замочите его на ночь перед использованием.
- Перлит — это форма обсидиана (вулканического стекла), обладающая превосходной воздухоудерживающей способностью из-за трещин, образующихся при остывании. Тем не менее, он имеет тенденцию смещаться или смываться при контакте с проточной водой. Его можно использовать с другими носителями, чтобы сохранить его на месте.
Всегда надевайте пылезащитную маску при работе с перлитом и другими пыльными средами.
- Вермикулит представляет собой терморасширенную форму слюды. Как и перлит, он легкий и имеет тенденцию смещаться в проточной воде. И перлит, и вермикулит обладают хорошими впитывающими свойствами, но перлит быстро высыхает, а вермикулит удерживает слишком много воды. Таким образом, эти два продукта хорошо сочетаются друг с другом.
- Еще одна рекомендованная среда для выращивания: торфяной мох сфагнум. Сфагнум — одна из разновидностей мха, известная как торфяной мох. Его преимущества в качестве гидропонной среды для выращивания включают в себя: – Полностью натуральный и биоразлагаемый
– Растет в виде хорошо впитывающих прядей, которые выходят за пределы сетчатых горшков для впитывания воды - Его основной недостаток заключается в том, что он со временем разлагается и может выделять мелкие частицы, которые могут засорить насосы и капельницы. Обычно его приобретают в прессованных блоках, которые необходимо замочить примерно за час до использования.
Дополнительные предложения см. на наших страницах для гидропоники и для аквапоники.
Спасибо, что прочитали нашу статью «Как сделать глиняную гальку для гидропоники». Не стесняйтесь просматривать другие статьи uPONICS для более полезных страниц о гидропонике и садоводстве с аквапоникой.
Избранная страница:
Лучшие светодиодные светильники для выращивания растений
В этой статье мы обсудим, что такое светодиодные лампы для выращивания растений, каковы их преимущества и как выбрать для вас лучшие светодиодные лампы для выращивания растений. Сегодня мы также рассмотрим лучшие лампы для выращивания растений на рынке..
Загрузите наше БЕСПЛАТНОЕ руководство!
Введите свое имя и адрес электронной почты ниже, и мы вышлем вам ссылку для загрузки нашего БЕСПЛАТНОГО 49-страничного руководства по системам гидропоники своими руками!
Имя
Адрес электронной почты:
Область ползунка переключения
Имя
Адрес электронной почты:
Руководство по подготовкеLECA — Что нужно знать перед переводом предприятия на LECA — LECA Addict
Подготовка к LECA
Вам бы не хотелось жить в комнате, заполненной мусором, верно? Ну, твоему растению это тоже не нужно.
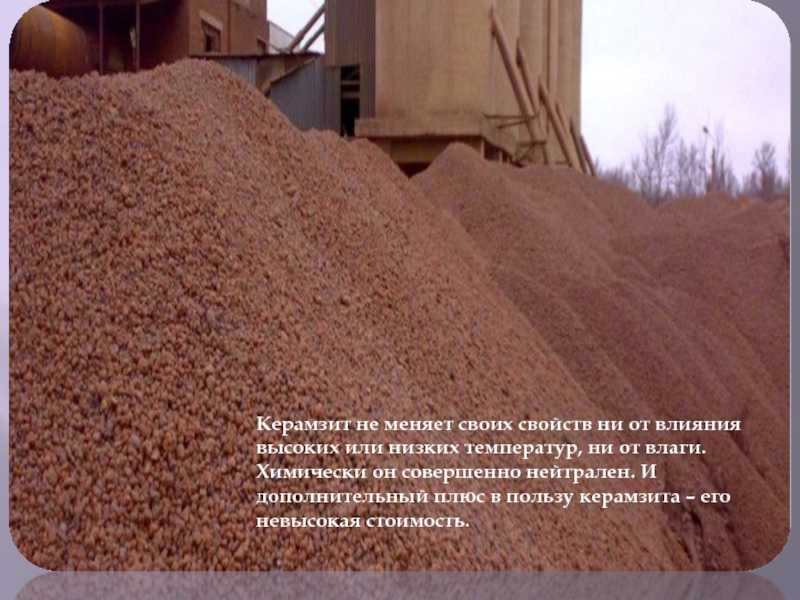
Почему?
LECA производится путем обжига предварительно обработанной глины во вращающейся печи при высоких температурах с последующим охлаждением. Конечным результатом является легкий керамзитовый заполнитель (LECA), размер которого во время этого процесса увеличивается в 5 раз. «Предварительная обработка» натуральной глины является своего рода загадкой, но она, вероятно, включает химические вещества и связующие вещества, которые при контакте с теплом заставляют глину расширяться и формироваться в маленькие шарики. В процессе обжига, вероятно, некоторые химические вещества становятся инертными или испаряются, но внутри этих шаров LECA определенно есть «вещь», «мусор» или «мусор». Кроме того, после того, как эти шарики выходят из печи, их обдают прохладной водой, чтобы снизить температуру, но что в этой воде?
«Но я просто промываю его и использую, и мои растения в порядке!» — говорит много людей в интернете. Конечно, я тоже могу жить в доме с кучей мусора, но я не собираюсь радоваться этому!
Обработка LECA перед использованием, как правило, является хорошей идеей, чтобы ваше растение могло начать жизнь полугидропоники со здорового начала. Если LECA не замочить должным образом, это может привести к тому, что растение будет расти намного медленнее, чем должно. За последний год выращивания LECA я также заметил, что хорошо пропитанная LECA требует гораздо меньше промывки, чем незамачиваемая LECA. Если вы ленивый пользователь LECA, сделайте сознательный выбор, как вы хотите быть ленивым здесь. Для меня несколько дней предусмотрительности полностью оправдывают отказ от еженедельной промывки.
Шаг 1: Промойте LECA
Выньте LECA из пакета и хорошенько промойте его, чтобы удалить мусор и глиняную пыль.
Совет : Я использую сетчатый мешок для белья и садовый шланг и делаю это на улице. Старайтесь не сбрасывать глиняную пыль в канализацию, это вредно для труб.
Шаг 2: Первое замачивание
Замочите LECA на 24 часа в водопроводной воде или воде из шланга. Это первое замачивание удалит первую волну грязи из LECA.
Для дополнительного ленивого режима просто дайте первому замачиванию продолжаться в течение 2+ дней, и теперь вы можете использовать LECA! (Если вы хотите быть очень ленивым, вы должны быть терпеливы.)
Совет : Я беру мешок для белья, полный LECA, и замачиваю его в большом пластиковом контейнере. Для 50 литров LECA я могу поместить все это в два сетчатых мешка для белья.
Научные материалы : Вы можете наблюдать PPM воды для замачивания после первого замачивания. (Чтобы узнать о PPM-праймере, см. мое руководство по питательным растворам). Моя водопроводная вода имеет концентрацию около 150 частей на миллион, а после 24 часов замачивания Hydroton LECA показал 800 частей на миллион. По сравнению с раствором удобрения с концентрацией 300 частей на миллион, в воде содержится много дополнительной грязи. Представьте, что вы не замачивали, ваш питательный раствор составляет 1/3, а неизвестные химические вещества — остальные 2/3. Валовой.
Этап 3: Второе замачивание
Слейте воду для замачивания и замените ее свежей водопроводной водой или водой из шланга. Замочить еще на 24 часа. После этого замачивания вы можете использовать LECA! Однако для ценных растений, для которых вы хотите обеспечить отличный старт, читайте дальше.
Science Stuff : Второе замачивание обычно дает около 300-400 частей на миллион через 24 часа. Помните, на уроке естествознания в старшей школе вы узнали о законе химического равновесия? Да нет, я тоже. Но в основном, когда вы смешиваете свой LECA (продукт) с водой (реагентом), вода и химические вещества внутри LECA хотят быть в равновесии с водой снаружи, пока они не станут равными внутри и снаружи. Если ваша вода имеет концентрацию 100 частей на миллион, а LECA — 800 частей на миллион, со временем в вашей воде будет больше значений частей на миллион, а в вашей LECA — меньше частей на миллион. Причина второго замачивания – ускорить процесс. Замачивание 800 PPM LECA в воде, которая составляет 100 PPM против 400 PPM, 100 PPM будет работать намного быстрее, и точка равновесия будет ниже.
Шаг 4. Высушите и храните
Сушка и хранение рекомендуется, если вы не собираетесь использовать LECA сразу. Вы можете сушить LECA в сетчатых мешках для белья, они обеспечивают отличную циркуляцию воздуха! Если вы планируете использовать LECA сразу же, вы можете пропустить этот шаг.
Совет : я буду выполнять шаги 1-4 летом на улице для всех LECA, которые я планирую использовать зимой. Кроме того, если вы оставите свою LECA на улице и пойдет дождь, это будет двойной победой, потому что мать-природа ополаскивает вашу LECA за вас! Но не забудьте занести эти сетчатые мешки для белья в дом после того, как закончите, мои теперь сломаны, потому что твари хотели увидеть, что внутри.
Шаг 5: Третье замачивание
Дополнительное замачивание – неплохая идея, особенно для ценных растений. Если я делаю этот шаг, я использую фильтрованную / обратноосмотическую / дистиллированную воду с концентрацией 0 частей на миллион.
Некоторые предпочитают замачивать LECA более чем на 2 недели перед использованием. Это также хорошая идея, если вы используете очищенный, высушенный LECA из предыдущих шагов. Вы всегда хотите использовать LECA, который был промокшим и влажным, а не сухим.
Вы также можете добавить CalMag (кальций-магниевая добавка) в воду для замачивания, а также любые гормоны для укоренения, такие как KLN. Добавление этих добавок может происходить уже при первом замачивании, так как ионы Ca и Mg заменяют менее желательные растворимые минералы в LECA.
Совет : У меня есть два ведра, которые всегда заполнены LECA, которые находятся в CalMag и KLN. Иногда они замачиваются на несколько недель, прежде чем я их использую.
Научные материалы : Почему не следует использовать сухой LECA? Это потому, что LECA очень эффективно впитывает воду. Если ваши корни соприкасаются с очень сухой LECA, она отводит воду от корней и может привести к высыханию корней. Всегда убедитесь, что они хорошо пропитаны перед использованием.
Но подождите, разве мне не нужно варить?
Вы можете вскипятить LECA, если хотите. Я бы рекомендовал после 2-го замачивания. Однако я нахожу это утомительным и ненужным, потому что я нахожу идею варить что-то, что прошло через вращающуюся печь, совершенно избыточной. Возможно, для этих ценных растений можно было бы хорошо прокипятить для стерилизации, но я обычно пропускаю этот шаг для LECA прямо из пакета, так как у меня есть другие способы борьбы с органическими незваными гостями, такими как плесень, грибки или бактерии.
Если вы повторно используете ЛЕКА, пожалуйста, Вскипятите. Я опубликую руководство по повторному использованию LECA позже.
Продукты и инструменты, упомянутые в этой статье
Все упомянутые продукты собраны в этом списке Amazon для легкого доступа. Я получаю комиссию за вашу покупку. Спасибо за Вашу поддержку!
Купить сейчас
Линия по производству легкого керамзитобетона (LECA)
Что такое легкий керамзитовый заполнитель (LECA)?
Определение : свет заполнитель керамзита или заполнитель керамзита (LECA или ECA), также называемый керамическим гранулы, являются одним из самых популярных легких заполнителей, изготовленных путем спекания глины. во вращающейся печи до 1200°С.
Вращающаяся печь для спекания глины
Сырье и применение : существуют различные типы легкого заполнителя из керамзита, а основными материалами являются глина, сланец, сланец, угольный порошок, хвосты и т. д.
LECA в основном применяется в строительстве, внутренняя отделка, сельское хозяйство, садоводство, садоводство, детская площадка, гидропоника, и т.п.
Сортировка (мм) | Плотность (кг/м 3 ) | Приложения |
0-4 | ≤710 | Легкий бетон, легкий кирпич, сборная плита, облегченная плитка, система очистки воды, сельское хозяйство |
4-10 | ≤480 | Легкий бетон, легкая плитка, сборные плита, аквакультура, шумозащита |
10-20 | ≤380 | Легкий бетон, канализация, озеленение, дренажная система |
0-25 | ≤430 | Отделка пола, легкая обивка, дорога строительство, аквакультура |
Перспектива развития легкого керамзитобетона
Текущий легкий керамзитовый заполнитель
рыночные данные показывают, что рынок LECA изменил свое направление с
традиционная строительная техника для ремесленных изделий и садоводческих
техническое обслуживание.
Перспектива развития LECA
Производственные материалы из традиционных материалов такие как глина и сланец, были заменены остатками промышленных отходов и илом и тенденция развития машин превратилась в крупномасштабную и автоматизация.
С тенденцией глобализации защиты окружающей среды, ресурсосберегающая экономика и устойчивая промышленность будут энергично продвигается в различных странах и регионах.
В дальнейшем, сосредоточившись на экономического развития, поставщики LECA должны обратить внимание на сокращение загрязнения и растраты ресурсов для обеспечения быстрого и стабильного развития производственные линии.
Технологии производства LECA
Обычно существует два типа LECA. технологии изготовления: спекание и спекание-расширение. Различия между ними находится в процессе спекания-вспененный, заполнитель расширяется на больший объем.
Производительность LECA за счет спекания
Агломерационная машина, используемая для процесса агломерации LECA
- Прочность на сжатие : прочность на сжатие
прочность спекаемого заполнителя относительно высока, достигая 3,0-7,0 МПа,
а прочность на сжатие высокоспекшихся заполнителей может достигать 25-40 МПа.
- Плотность : плотность спеченного агрегат больше, который обычно больше, чем 600 кг/м3, даже некоторые из них более 900 кг/м3.
- Водопоглощение : водопоглощение у обычного спеченного заполнителя несколько выше, чем у спеченно-расширенного продукт, а высокопрочные продукты аналогичны спеченно-расширенному продукту.
- Сопротивление карбонизации : спеченный заполнитель обладает высокой устойчивостью к карбонизации, поэтому его прочность на сжатие не уменьшится даже под действием углекислого газа.
Производительность LECA за счет расширенного спекания
Вращающаяся печь, используемая для расширенного процесса спекания LECA
- Прочность на сжатие : прочность на сжатие прочность спеченно-расширенного заполнителя обычно ниже 2,0 МПа, поэтому в основном используется для внутренней отделки, такой как шумозащита и садоводство.
- Теплоизоляционные характеристики : спеченно-расширенный
продукт имеет закрытую микропористую структуру с очень высокой пористостью, что обычно
составляет 48–70 % от общего объема заполнителя, в результате чего всего 0,08–0,15 Вт.
/(м.к) теплопроводности.
- Низкая плотность : много пор в спеченно-расширенный материал, поэтому плотность в основном 300-500 кг/м 3 , что составляет лишь половину от спеченного заполнителя. Тем не менее, он имеет значительное преимущество в легком исполнении, поэтому его также можно использовать для различных отделочные работы и строительство с более низкими требованиями к плотности в строительстве материалы.
- Отличное звукопоглощение и изоляция : среди всех видов заполнителей звукопоглощающие и изоляционные характеристики из спеченно-расширенного заполнителя является наиболее выдающимся.
Когда звук проходит через материал, большое количество звуковых волн поглощается его порами, что уменьшает распространение звука.
Для разных процессов требуется разное оборудование.
Агломашина обычно используется в процессе агломерации, в то время как роторная
печь используется в расширенном процессе спекания.
По сравнению с агломерационной машиной, роторная печь более эффективна и более экологична, поэтому предпочтительное оборудование для поставщиков LECA.
Производственная линия LECA и основные машины
Производство LECA в целом требуется семь этапов: дробление, смешивание, измельчение, гранулирование, спекание, охлаждение и просеивание.
Производственная линия ЛЕКА
Основное оборудование производства LECA линия включает в себя щековую дробильную машину, смесительную машину, шаровую мельницу, гранулятор, вращающаяся сушилка, барабанный грохот, вращающаяся печь, охлаждающая машина.
Щековая дробилка — первичное дробление
Щековая дробилка является основной машиной, которая применяется для грубого, среднего и мелкого дробления различных руд и горных пород с всеобъемлющей прочностью от 147 до 245 МПа, и перерабатывает их в мелкие куски 10-350 мм.
Зубодробилка, мордоворот
Преимущества : В последние годы FTM
Специально разработанная мощная щековая дробилка для удовлетворения потребностей дробления
высокопрочный и высокотвердый микроуглеродистый феррохром в металлургической,
горнодобывающая, строительная и другие отрасли промышленности.
Шаровая мельница — дальнейшее измельчение
Шаровая мельница является ключевым оборудованием для измельчения материал после дробления. Шаровая мельница широко используется в производстве цемента, силикатные изделия, новые строительные материалы, огнеупоры, удобрения, обработка черных и цветных металлов и стеклокерамики, сухая или мокрая шлифовка различных руд и других измельчаемых материалов.
Шаровая мельница
Преимущества : Энергосбережение, гибкая конструкция разгрузочной части, большое загрузочное отверстие, высокая эффективность измельчения, хорошая качество футеровки и закрытая система для уменьшения пыли.
Дисковая грануляционная машина — контроль размера частиц
Диск – это ключевой механизм, определяющий частицы керамзитового заполнителя.
Диск гранулирования имеет общую круглую форму.
дуговая структура, а скорость грануляции может достигать 93% и более. Грануляция
лоток имеет три разгрузочных порта, которые облегчают прерывистое производство
операций, что значительно снижает трудоемкость и повышает эффективность труда.
Дисковая грануляционная машина
Преимущества : Высокая скорость образования шариков, большой размер округлая прочность частиц, интуитивно понятное управление и простота обслуживания.
Осушитель — удаление воды из LECA
Сушилка в основном используется для сушки определенных влажные или гранулированные материалы переработки полезных ископаемых, строительные материалы, металлургия и химическая промышленность, а работа оборудования проста и надежный.
Сушилка
Adv anta ges : Долговечность деталей, износостойкость, высокая прочность при сушке, высокая эффективность, простота в эксплуатации, экологичность защита и энергосбережение, усовершенствованная структура и сильная способность сушки.
Барабанное сито — отделение неквалифицированных LECA
Барабанный сетчатый фильтр часто используется для измельчения
порошкообразных материалов, обладающих хорошим просеивающим эффектом и стабильной работой
и он производит низкий уровень шума во время рабочего процесса.
Экран барабана
Преимущества : Оборудование имеет Диапазон применения, а также его можно настроить. Он имеет низкий уровень шума, высокий эффективность и защита окружающей среды, усовершенствованная система смазки, долгий срок службы срок службы, небольшой угол наклона установки и хороший экранирующий эффект.
Вращающаяся печь — спекание LECA
Вращающаяся печь является наиболее необходимой машиной и играет важную роль в процессе спекания, что определяет производительность из ЛЕКА.
Вращающаяся печь
Преимущества : Осевое перемещение цилиндр управляемый, скорость гибкая, установка и техническое обслуживание удобно, а герметичность хорошая.
Кулер — быстро охлаждает LECA
Одноцилиндровый охладитель является одним из
важное оборудование в системе вращающейся печи. Клинкер из вращающейся печи
(1000-1200°С) полностью обменивается с воздухом через вращающийся цилиндр
лента для охлаждения материала до температуры ниже 200 °C, в то же время улучшает качество клинкера
качество и шлифуемость.
Кулер
Преимущества : Высокая тепловая эффективность, высокая качество клинкера, быстрое охлаждение и улучшенная скорость работы.
Спецификация производственной линии LECA (для только ссылка)
- 01 тип : 0,45–0,9 мм (20–40 меш) Высокая прочность при средней плотности
- 02 тип : 0,9-1,25 мм (16-20 меш) Высокая прочность при средней плотности
- 03 тип : 1,0-1,70 мм (12-18 меш) Высокая прочность при средней плотности
- 04 тип : 0,224-0,65 мм (40-60 меш) Высокая прочность при средней плотности
Рекомендован производителем машин LECA – FTM
Fote Mining Machinery (FTM), расположенная в г.
Хэнань является одним из самых известных поставщиков горнодобывающей техники, который занимается
на производство горнодобывающих машин из экологически чистых строительных материалов, а также обеспечивает
интеллектуальные продукты для майнинга и передовые решения.