Легкие бетонные стяжки, керамзит, перлит, вермикулит
class=”eliadunit”>
Вступление
Общеизвестно, что для стяжки пола толщиной больше 5 см прекрасно подходит “классическая” цементно-песчаная стяжка. К сожалению, у нее есть один недостаток, который может стать проблемным. Она очень тяжелая. Ее вес составляет 20-22 кг одного метра стяжки при укладки толщиной в один сантиметр. Одним из способов снижения веса стяжки является простой и технологичный способ добавление в раствор, на этапе его замешивания, пористых наполнителей, например керамзит, перлит, вермикулит. Такие стяжки называют легкие бетонные стяжки.
Стоит отметить, что легкий бетон используется не только для стяжки пола. Это отличный материал для формирования строительных блоков. Вам хорошо известны пустотелые (перегородочные) и полнотелые (стенные) керамзитобетонные блоки, которые благодаря низкой цене и отличному качеству используются в строительстве частных домов и планировки новостроек. Всё это еще раз говорит в пользу качества легкого бетона.
Устройство легкой бетонной стяжки
Смесь для легкой бетонной стяжки делается непосредственно на обьекте. К классическому сочетанию цемента, песка и воды добавляются пористые заполнители. Вода в таких растворах добавляется в минимальных количествах, только для получения пластиной и удобной для укладки смеси. Пористыми заполнителями служат: керамзит, вермикулит и перлит. Поговорим о них поподробнее.
Пористые наполнители для легкой бетонной стяжки
Керамзит
Керамзит это строительный материал, имеющий пористую структуру. Производится керамзит в виде овальный гранул разного размера. Размер керамзита называют фракцией. Производится керамзит из глины, методом обжига.
Объемный вес керамзита 250-600 килограмм 1 кубического метра.
Легкий бетон с добавлением керамзита называется керамзитобетонной стяжкой. Вес 1 см такой стяжки составляет около 18 кг.
Вермикулит
Вермикулит это слоистый природный минерал. При нагревании образуются нити или палочки серебристого или золотистого цвета, напоминающие червяков. Отсюда название вермикулит, от латинского vermiculus-червяк.
В строительстве используется только вспученный вермикулит. Вермикулит имеет очень высокий коэффициент водопоглащения.100 грамм перлита впитывают 450 грамм воды. Также вермикулит имеет высокие коэффициенты теплоизоляции и звукоизоляции.
Перлит
Перлит это горная вулканическая порода. В строительстве применяется вспученный перлит, который получается из перлита после теплового удара в 900-1100° C. После теплового удара из перлита удаляется лишняя влага.
class=”eliadunit”>По внешнему виду перлит напоминает щебень или песок.
Фракции пористых заполнителей для легкого бетона
При изготовлении легких бетонных стяжек нужно добавлять пористые наполнители определенного размера (фракции)
Фракция керамзита должна быть 5-10 мм. Фракция вермикулита 0,6-2,0 мм. Фракция перлита не более 15 мм. Влажность пористых заполнителей должна не превышать 10 %.Пористые материалы таких фракций добавляются непосредственно в приготавливаемый раствор.
Добавляются пористые заполнители в самом конце замешивания раствора, после смешивания цемента песка и воды.
Важно! Так как пористые наполнители имеют большой коэффициент водопоглащения. Количество воды в растворе должно быть минимальным. Только до получения удобной для укладки консистенции.
- Керамзит фракции 10-20 мм применяется для устройства легкой двухслойной стяжки. Относится такая стяжка к полусухим стяжкам на разделяющем слое. В качестве разделяющего слоя выступает полиэтиленовая пленка (для бетонного основания) или бумага пропитанная битумом или парафином (для деревянного основания).
- Первый слой такой стяжки делается толщиной от 50 мм из смеси керамзита и цементного молочка. Второй слой стяжки это полусухая цементно-песчаная стяжка толщиной также от 50 мм.
- Первый слой укладывается без маяков, но обязательно разравнивается и уплотняется. Второй слой укладывается через 40 минут после первого и ориентируется на предварительно выставленные маяки.
Положительные свойства легкой бетонной стяжки
У легких бетонных стяжек много преимуществ по сравнению с «мокрыми» цементно-песчанными стяжками.
- Теплопроводность легких бетонных стяжек в 4-6 раз меньше, чем у простых цементно-песчанных стяжек.
- Вес легких бетонных стяжек в 1,5 раза меньше цементно-песчанной стяжки. Время высыхания таких стяжек также значительно меньше, 7-10 суток.
Но также нужно помнить, что легкие бетонные стяжки, требуют финишного выравнивания наливными полами.
©Opolax.ru
Другие статьи раздела: Выровнять пол
class=”eliadunit”>
Технология особо легкого керамзита –
За последние годы в СССР и за рубежом гюе больше развивается промышленность пористых заполнителей для лег- кого бетона различного назначения.
РИЛЕМ (Международное общество по испытанию строительных материалов) созывает в марте нынешнего года в Будапеште специальный международный симпозиум, посвященный методам испытания пористых заполнителей, легкобетонных смесей и затвердевшего легкого бетона.
В этой области в Советском Союзе накоплен большой опыт, систематически освещаемый в нашем журнале. В последних четырех номерах (№№ 9—12 1966 г.) опубликованы статьи: Б. Н. Виноградова. М. П. Элннзона, Р. У. Хасяновой. «Минералогический состав и агломерация песчано-глинистых пород»; Д. И. Резникова «Влияние степени переработки глины на объемный вес керамзита»; Г. И. Книгпной, И. Д. Метелкина. «Корректирование свойств глины при сушке керамзита- сырца»; Р. Л. Певзнера, И. ЛЯ. Гиндиной. «Важный фактор улучшения экономны! производства и применения керамзита»; Б. М. Гриссика, М. П. Элннзона, «Пути развития промышленности пористых заполнителей»: А. В. Волженского, Б. В. Сендерова «Ползучесть и усадка керамзитобетона на гипсоцементнопуццолановом вяжущем»; Р. Л. Мачлпна. «Методика испытания и оценка прочности пористых заполнителей бетона»; Э. Я. Сюнякова. «К вопросу о пневмотранспорте керамзита»; М. П. Элннзона, И. А. Якуб, В. П. Старостиной, В. Г. Довжнка, Л. А. Хренникова, Ю. А. Ульянова. Новый Гостгравий керамзитовый (9759—65)».
Ниже публикуем ряд новых статей также посвяшенных методике испытаний пористых заполнителей, технологии производства особо легких материалов, эффективных утепляющих смесей из легких заполнителей и другие.
Исследованиями. приведенными в ИИНКс/амзите (1964—1966 гг) установлено, что опудриванием сырцовых гранул порошком огнеупорной глины можно значительно увеличить их вспучиваемость в производственных условиях. Опудривание повышает огнеупорность поверхностного слоя гранул и температуру об к ига, позволяет прогреть внутреннюю зону гранулы до оптимального состояния, не опасаясь образования «козлов».
В лабораторных условиях кроме ранее опробованных опудривателей (каолин, часовярская глина и чапаевский песок) испытаны местные огнеупорные глины: моитморилонитогидрослюдистая жирная смышляевская глина, известкочистая кряжская (с добавкой молотого мела) и слабо вспучивающийся суглинок Куйбышевского кирпичного комбината, огнеупорные глины Евсинского месторождения Южного участка Новосибирской области, а также цемеы и известь.
Кроме того, в производственных условиях были опробованы глины Смышляевского и Кряжекого месторождений (г. Куйбышев), Куйбышевского участка (г. Новосибирск) и Чекаловского месторождения (г. Ленинград).
Опудривание сырцовых гранул производится обкаткой их вместе с порошкообразным огнеупорным или тугоплавким материалом. При обкатке зерна порошка частично втапливаются в поверхностный слой глиняной гранулы, частично прилипают к ее поверхности. Б результате этого на поверхности гранулы образуется корочка, состав которой изменяется от состава чистого опудривателя снаружи до чистой исходной глины — внутри. В соответствии с этим температура плавления отдельных участков по толщине корочки определяется соотношением входящих в его состав компонентов и характером протекающих между ними процессов взаимодействия.
Для изучения влияния опудривателей на тугоплавкость поверхностного слоя гранул была определена огне упорность (по ГОСТ 4069—48) глины с различными добавками (рис. 1). Чапаевская огнеупорная глина (кривая 1) даже в небольших дозах увеличивает тугоплавкость глин, в то время как известь и цемент в таких же дозах снижают ее. Только при добавлении их более 60% огнеупорность глин начинает увеличиваться. На известковистую глину (кряжская с добавкой тонкомолотого мела) и безымяиский сравнительно тощий суглинок действие добавок полностью аналогично и при добавках (более 60%) огнеупорность смесей превосходит огнеупорность исходных глин.
Опыты дополнительно подтверждают справедтивость вывода, что алюмосиликатные материалы являются эффективными опудривателями.
Опудривание гранул тугоплавкими материалами позволило повысить температуру слипания гранул при обжиге до оптимальной (рис. 2), при которой можно получить керамзит с минимальным объемным весом. При увеличении температуры до 1!60°С (точка 1) объемный вес опудренных и неопудренных гранул изменяется одинаково. При 160°С неопудренные гранулы начинают слипаться настолько прочно, что разделение их после охлаждения становится невозможным. Поэтому обжиг неопудренных гранул выше 1160°С проводить нельзя. Опудренные гранулы обнаруживают признаки слипания только при 120СГС, что позволяет снизить их объемный вес примерно в 2 раза по сравнению с неопудреннымм гранулами.
Вместе с тем опыты показали, ч,о слой опудривателя из извести-пушонки не с поверхностью сырой гранулы и сразу же оттает при перенесении ее в печь. Цемент держится лучше, но тоже недостаточно надежно. Видимо, это объясняется тем, что связание порошков очень мала, кроме того, их усадка не равна усадке основной массы гранулы при сушке, что приводит к их отслаиванию.
Опыты, проведенные в 1964 г., показали, что огнеупорная оболочка гранул сохраняется при обработке в 18— 22- и печах. Стойкость оболочки гранул в 40-.il печах представлялась сомнительной.
Так как в районе г. Куйбышева нег заводов, оснащенных 40-л печами, изучение стойкости пришлось проводи оборудования, позволяющего имитировать процессы истирания поверхности гранул, происходящие в обжиговой печи.
Испытания проводились в барабане Девали, в который загружалось 1 кг гранул. Изнашиваемость оболочки гранулы оценивалось по изменению химического состава порошка, получающегося при истирании гранул — в первую очередь но изменению содержания г, порошке А1г03.
Испытанию подвергались гранулы, взятые непосредственно с транспортера после обкатки и опудривания их каолином Просяновского месторождения во время производственных испытаний на опытном заводе. Часть гранул была высушена до влажности 8%, а остальные обожжены при 400, 700 н 1000°С. Удаление порошка из барабана и его испытания проводились через каждые 5 мин.
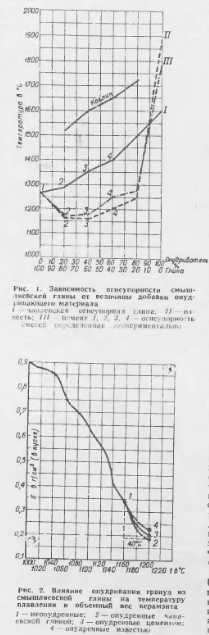
Для определения длины указанных выше температурных зон была использована температурная кривая материала при испытании 40-.ч печи Лианозовского завода. Полученные длины зон и степень истирания оболочки в каждой из них позволяют определять состояние оболочки гранул в момент поступления в зону вспучивания (рис. 3). Гранула из предыдущей зоны поступает в последующую с некоторой степенью износа, выражающейся в изменении содержания А12Оз (рис. 4) Содержание М2О3 в порошке, получающемся при истирании поверхностного слоя гранул, при прохождении пути, соответствующему пребыванию в зоне подготовки, снижается с 39 до 30%, что соответствует смеси равных долей каолина из смышляевской глины и вполне гарантирует достаточную огнеупорность поверхностного слоя. Взятые для испытания гранулы представляют собой цилиндрики, поэтому обогащение порошка смышляевской глиной, очевидно, происходило в результате истирания острых углов и ребер. Во всяком случае обнаружить визуально большие участки поверхности, лишенные опудривающего слоя, не удалось. Это обстоятельство создает уверенность в том, что даже в 40-.и печи при питании ее сырыми гранулами поступающий в зону вспучивания материал будет иметь достаточно огнеупорную оболочку. Создание такой оболочки зерна, обладающей большим интервалом плавкости, позволяет избежать слипания гранул и является особенно эффективным при использовании в качестве сырья короткоплавких глин. В дальнейшем это полностью подтвердилось при изготовлении опытной партии опудренного керамзита на Ленинградском заводе керамических изделий, оборудованном 40-.и печами. Ни этом заводе за счет опудривання объемный вес керамзита удалось снизить на одну марку.
Изготовтение опудреиного керамзита в производственных масштабах организовано на экспериментальном керамзитовом заводе института НИИКерамзит. Особо легкий керамзит с объемным весом от 100 до 150 кг/и3 изготовлен на этом заводе в объеме более 3000 м3.
alyos.ru
Керамзит — легкий и доступный способ утепления фундамента
В этой статье мы поговорим о преимуществах, недостатках и способах утепления фундамента дома керамзитом по следующему плану:
- Почему именно керамзит?
- Плюсы и минусы керамзита
- Как правильно выбрать керамзит
- Непосредственно сам процесс утепления фундамента керамзитом
Фундамент это надежность и опора вашего дома. Но кроме основных работ, для дополнительного свойства — тепла, используют различные материалы. Одним из таких материалов для утепления, который становится очень популярен в последние время есть керамзит.
Почему керамзит?
Утеплить основу дома фундамент недорого и качественно поможет легкий теплоизоляционный материал керамзит.
Выпускают его в сыпучей форме мелкими фрагментами. Методом производства есть обжигание пород из глины. И в зависимости от размера делится на: порошок, гравий и щебенку. Все эти размеры предназначены для разных видов работ. В качестве теплоизолятора подойдет любой размер.
Чтоб изолировать часть фундамента над и под землей используют зерна керамзита. Для сбережения тепла сооружают перегородки и копают траншеи, а все пространство засыпают фрагментами керамзита. Весь процесс сопутствуют работы по дренажу и гидроизоляции.
Казалось бы застарелый метод, если посмотреть на современные технологии, но он держит крепкие позиции среди схожих материалов, ведь простой технологии и не очень затратный.
Но есть свои нюансы при использовании керамзита, которые обязательно следует учитывать. Этот материал впитывает в себя много воды, поэтому на низких участках или в местах стока где води его не применяют.
В основном керамзит используют на даче, для деревянного дома или для другого вида построек, фундамент которых нужно утеплить.
“За“ и “против” утепления фундамента керамзитом
Как и все материалы керамзит имеет свои плюсы и минусы. Основными аргументами “за” керамзит есть:
- независимость теплоизоляционных свойств от погоды;
- агрессивное воздействие внешней среды не разрушает этот материал;
- не притягивает к себе насекомых и грызунов;
- простота и легкость в использование;
- при утеплении снаружи эксплуатация конструкции более долговечна;
- можно использовать на любой стадии строительства или после ее окончания.
Нюансы которые могут оттолкнуть вас от выбора керамзита как утеплителя фундамента:
- слой утеплителя с ограждением не очень эстетичен, груб и в этом негативно отличается от большинства современных утеплителей;
- водопоглощения, о котором написали выше;
- возможен больший расход материала чем означено.
openfile.ru
Керамзит
Керамзит – это легкий пористый материал, который имеет ячеистое строение. Это материал в виде гравия, иногда в виде щебня. Керамзит получают при обжиге глинистых пород. Качество керамзита характеризуют размером его зерен, объемным весом и прочностью. В зависимости от размера зерен керамзитовый гравий или керамзит делит на следующие фракции: 5 – 10, 10 – 20 и 20 – 40 мм, зерна менее 5 мм относят к керамзитовому песку. В зависимости от объемного насыпного веса (в кг/м3) гравий делят на марки от 150 до 800. Водопоглощение керамзитового гравия 8–20 %, морозостойкость должна быть не менее 25 циклов. Керамзит применяют в качестве пористого заполнителя для легких бетонов, а также в качестве теплоизоляционного материала в виде засыпок. Керамзитовый гравий или керамзит — частицы округлой формы с оплавленной поверхностью и порами внутри. Керамзит получают главным образом в виде керамзитового гравия. Зерна керамзита его имеют округлую форму. Структура пористая, ячеистая. На поверхности его часто имеется более плотная корочка. Цвет керамзитового гравия или керамзита обычно темно-бурый, в изломе — почти черный. Его получают вспучиванием при обжиге легкоплавких глин во вращающих печах. Такой гравий с размерами зерен 5 – 40 мм морозоустойчив, огнестоек, не впитывает воду и не содержит вредных для цемента примесей. Керамзитовый гравий используют в качестве заполнителя при изготовлении легкобетонных конструкций. Керамзитовый щебень — заполнитель для легких бетонов произвольной формы, преимущественно угловатой с размерами зерен от 5 до 40 мм, получаемый путем дробления крупных кусков вспученной массы керамзита. Некоторые глины при обжиге вспучиваются. Например, при производстве глиняного кирпича один из видов брака— пережог — иногда сопровождается вспучиванием. Это явление использовано для получения из глин пористого материала — керамзита. Вспучивание глины при обжиге связано с двумя процессами: газовыделением и переходом глины в пиропластическое состояние. Источниками газовыделения являются реакции восстановления окислов железа при их взаимодействии с органическими примесями, окисления этих примесей, дегидратации гидрослюд и других водосодержащих глинистых минералов, диссоциации карбонатов и т. д. В пиропластическое состояние глины переходят, когда при высокой температуре в них образуется жидкая фаза (расплав), в результате чего глина размягчается, приобретает способность к пластической деформации, в то же время становится газонепроницаемой и вспучивается выделяющимися газами. Для изготовления керамзитобетонных изделий нужен не только керамзитовый гравий, но и мелкий пористый заполнитель. Керамзитовый песок — заполнитель для легких бетонов и растворов с размером частиц от 0,14 до 5 мм получают при обжиге глинистой мелочи во вращающих и шахтных печах или же дроблением более крупных кусков керамзита. Производство керамзитового песка по обычной технологии во вращающейся печи неэффективно. Некоторая примесь песчаной фракции получается при производстве керамзитового гравия за счет разрушения части гранул в процессе термообработки, однако он сравнительно тяжелый, так как мелкие частицы глинистого сырья практически не вспучиваются (резервы газообразования исчерпываются раньше, чем глина переходит в пиропластическое состояние). Кроме того, в зоне высоких температур мелкие гранулы разогреваются сильнее крупных, при этом, возможно, их оплавление и налипание на зерна гравия. На многих предприятиях керамзитовый песок получают дроблением керамзитового гравия, преимущественно в валковых дробилках. Себестоимость дробленого керамзитового песка высока не только в связи с дополнительными затратами на дробление, но главным образом потому, что выход песка всегда меньше объема дробимого гравия. Коэффициент выхода песка составляет 0,4—0,7, т. е. в среднем из 1 м3 гравия получают только около 0,5 м3 дробленого керамзитого песка. При этом почти вдвое возрастает его насыпная плотность. В настоящее время при получении керамзитового песка лучшей считают технологию его обжига в кипящем слое. Часто при получении керамзитобетона в качестве мелкого заполнителя применяют вспученный перлит, а также природный песок. Сырье для производства керамзита. Сырьем для производства керамзита служат глинистые породы, относящиеся в основном к осадочным горным. Некоторые камнеподобные глинистые породы — глинистые сланцы, аргиллиты — относятся к метаморфическим. Для производства керамзита наиболее пригодны монт-мориллонитовые и гидрослюдистые глины, содержащие не более 30% кварца. Общее содержание SiO2 должно быть не более 70%, А12О3 — не менее 12% (желательно около 120%), Fe2O3 + FeO — до 10%, органических примесей -1-2%. Пригодность того или иного глинистого сырья для производства керамзита устанавливают специальным исследованием его свойств. Важнейшее из требований к сырью – вспучивание при обжиге. Марки керамзита В ГОСТ 9759-76 предусматриваются следующие фракции керамзитового гравия по крупности зерен: 5-10, 10-20 и 20-40 мм. В каждой фракции допускается до 5% более мелких и до 5% более крупных зерен по сравнению с номинальными размерами. Из-за невысокой эффективности грохочения материала в барабанных грохотах трудно добиться разделения керамзита на фракции в пределах установленных допусков. По насыпной плотности керамзитовый гравий подразделяется на 10 марок: от 250 до 800, причем к марке 250 относится керамзитовый гравий с насыпной плотностью до 250 кг/м3, к марке 300 — до 300 кг/м3 и т. д. Насыпную плотность определяют по фракциям в мерных сосудах. Чем крупнее фракция керамзитового гравия, тем, как правило, меньше насыпная плотность, поскольку крупные фракции содержат наиболее вспученные гранулы. Для каждой марки по насыпной плотности стандарт устанавливает требования к прочностикерамзитового гравия при сдавливании в цилиндре и соответствующие им марки по прочности. Маркировка по прочности позволяет сразу наметить область рационального применения того или иного керамзита в бетонах соответствующих марок. Более точные данные получают при испытании заполнителя в бетоне.
ru-stroyka.com