Лазер для резки металла своими руками
Промышленные технологии не перестают поражать воображение даже видавших виды специалистов, а самодеятельных мастеров, и подавно. А ведь, действительно, кто бы отказался от домашнего настольного мини-пресса для литья изделий из металла, высокоточных мини-резаков на основе лазерных технологий или настольной мини-лаборатории для приготовления высокооктанового бензина из использованной жевательной резинки. Не все и не всегда реализуемо, но, изучая технологии, умелыми руками можно достичь определенных результатов. Но сегодня мы поговорим о лазерной обработке металлов резанием.
Содержание:
- Технология резки металла лазером
- Станок для резки металла лазером
- Функции газа в станке
- Схема и виды ручного лазера для резки металла
Технология резки металла лазером
Лазерная резка металлов — это одна из самых передовых и дорогостоящих технологий, какие только существуют для обработки металлов. Применив лазер для резки металла своими руками можно получить невиданные, фантастические результаты, недоступные, или почти недоступные, ни одним другим видам обработки металла. Совершенно неограниченные возможности лазера обусловлены тем, что его луч практически не знает границ и способен передавать в любом материале практически любую задумку, которую только можно себе представить.
Технология обработки металлов лазером основана на характеристиках лазернoго луча, а это:
- Четкая направленность.
- Монoхроматичность.
- Кoгерентность.
- Мощность.
За счет того, что лазерный луч, в отличие от света, имеет идеальную направленность, его энергия способна фокусироваться с минимальными потерями в определенной точке. По способности к точной фокусировки лазерный луч в десятки тысяч раз выигрывает у самого мощного светового прожектора.
А ведь учитывая тот факт, что и световой луч несет определенную энергию, ощутимую физически, можно только представить какой энергией обладает лазерный луч, собрав всю ее в одну точку и приложив к маленькому участку плоскости.
Лазерный луч имеет еще одно очень важное отличие от луча света — монохроматичность. Это значит, что с точки зрения оптической физики, лазер имеет строго определенную и жестко фиксированную длину волны и такую же постоянную частоту. Поэтому сфокусировать его не предоставит труда даже обычным оптическим линзам. Когерентность лазера — соглaсованное протекание во времени нескольких волновых процессов, имеет высокий уровень, а это говорит о том, что резонансные колебания лазерного луча могут усилить его энергию в несколько раз.
Благодаря этим свойствам, лaзерный луч может быть сфокусирован на минимально возможной площади материала, создавая при этом высочайшую плотность энергии. Такой энергии, как выяснилось, достаточно для прожига или разрушения металла или другого материала на микроскопическом участке плоскости, вплоть до плавления любого материала, который способен плавиться.
Станок для резки металла лазером
На самом деле, не так все просто, как в теории, поскольку существуют некоторые физические силы, которые могут ослабить энергию лазерного луча, к тому же у каждого из материалов существуют свои собственные свойства по поглощению излучения и его отражающим способностям. Каждый металл может по-разному распространять поглощенную энергию в силу индивидуальных свойств по теплопроводности.
Если учесть все эти нюансы и настроить лазерный луч таким образом, чтобы область облучения металла лазером расплавилась как минимум, только в этом случае можно говорить об обработке металла резанием при помощи энергии лазерного луча. В процессе обработки металл подвергается двум фазам воздействия:
- Плавление.
- Разрушение, закипание.
Поэтому для металлoв разной толщины и разной структуры могут быть применены разные способы обработки. Один металл на определенном станке может просто плавиться, и этого будет достаточно, чтобы отделить одну часть заготовки от другой, а другому металлу будет необходимо выпаривание, то есть закипание и только потом он уже сможет испаряться. Обработка металла испарением практикуется крайне редко, поскольку для этого необходимы колоссальные затраты энергии. Практически же все станки по обработке металла выполняют ее по технoлогии плавления.
Именно для этих целей, сокращения используемой энергии, в станке по лазерной обработке металлов применяется катализирующий газ. Он также помогает увеличить толщину обрабатываемого металла. Для работы с металлом при помощи лазера практически во всех станках используется один из этих элементов:
- кислород;
- обычный воздух;
- инертные газы;
- азот.
Это уже будет газолазерный станок по обработке металлов.
Функции газа в станке
В условиях атмосферы применение такого станка без газа фактически сводит к нулю всю его энергию, о чем мы говорили выше, поэтому использование газа, как вспомогательного вещества, существенно ускоряет процесс резки и делает применение станка для резки металла лазером еще более универсальным. Обычный кислород при обработке металла может выполнять ряд важнейших функций:
кислород поддерживает горение металла под воздействием мощного лазерного луча, а дополнительное тепло усиливает действие луча, повышая скорость резки металла лазером;
при помощи кислорода под давлением снимается и удаляется из области обработки остатки материала и продукт его горения, что облегчает доступ газа к новой области обработки.
Схема и виды ручного лазера для резки металла
Любые лазеры для резки металла будут выполнены из таких главных узлов:
- Источника энергии.
- Рабочего органа, излучающего энергию.
- Оптоусилитель, системы зеркал, оптоволоконный лазер, которые повышают и усиливают излучение рабочего органа.
В промышленности применяются два вида лазерных головок — твердотельная и газовая, которые могут быть нескольких видов. Рабочий орган, излучатель энергии размещен в энергоосветительных камерах, где активным телом может быть рубиновый прут, неодимовые пластины или алюмоиттриевые гранаты, легированные иттрием. В результате большого числа отражений луча, проходит накачка лазера энергией и луч вырывается через полупрозрачное стекло.
Обычный лазер резки металла цена которого доступна для крупного предприятия, может иметь мощность в пределах 5 кВт. В таких небольших лазерных станках применяются системы с продольной прокачкой газа, где газ или смесь газов пропускается под давлением через электрогазоразрядную головку, в которую подается электричество для энергетического возбуждения газа.
Таким образом работает простой газолазерный станок для резки металлов, с помощью которого может выполняться практически любая работа по обработке металла резанием.
Читайте также Цинкование металла в домашних условиях
nashprorab.com
ЛАЗЕРНЫЙ РЕЗАК ПО МЕТАЛЛУ [своими руками]
[Лазерный резак], сделанный своими руками, пригодится в каждом доме.
Конечно же, самодельный прибор не сможет обрести большую мощность, которую имеют производственные аппараты, но все же кое-какую пользу в быту от него можно будет получить.
Как сделать лазерное режущее устройство из указки?
Самое интересное, что изготовить лазерный резак можно с помощью старых ненужных предметов.
Например, своими руками изготовить лазерный прибор позволит применение старой лазерной указки.
Чтобы процесс по созданию резака продвигался как можно быстрее, необходимо подготовить следующие предметы и инструменты:
указка лазерного типа;
фонарик на аккумуляторных батареях;
старый CD/DVD-RW пишущий, можно вышедший из строя, – из него понадобится привод с лазером;
электропаяльник и комплект отверток.
Процесс по изготовлению резака своими руками начинается с разборки привода, откуда необходимо достать прибор.
Извлечение нужно сделать по максимуму аккуратным, при этом придется проявить терпение и быть внимательным. В устройстве присутствует много разных проводов с практически одинаковой структурой.
Выбирая DVD привод, нужно учитывать, чтобы он был пишущим, так как именно такой вариант позволяет делать записи с помощью лазера.
Видео:
Запись выполняется в ходе испарения тонкого металлического слоя с диска.
В процессе чтения, лазер функционирует наполовину своих технических возможностей, слегка освещая диск.
В процессе демонтажа верхнего крепежного элемента взгляд упадет на каретку с лазером, который может передвигаться в нескольких направлениях.
Каретку необходимо бережно извлечь, аккуратно снять разъемы и шурупы.
Затем можно перейти к снятию красного диода, за счет него происходит прожиг диска – это легко можно сделать своими руками при помощи электропаяльника. Извлеченный элемент не стоит встряхивать, а тем более ронять.
После того как основная деталь будущего резака находится на поверхности, нужно сделать тщательно продуманный план сборки лазерного резака.
При этом необходимо учесть следующие моменты: как лучше поместить диод, как подсоединить его к источнику питания, ведь для диода пишущего устройства требуется больше электроэнергии, чем для основного элемента указки.
Данный вопрос можно решить несколькими методами.
Чтобы сделать ручной резак с более-менее высокой мощностью, необходимо достать находящийся в указке диод, после чего поменять его на элемент, извлеченный из DVD привода.
Поэтому лазерную указку разбирают также осторожно, как и привод пишущего DVD устройства.
Предмет раскручивают, затем разделяют его корпус на две половины. Сразу же на поверхности можно будет увидеть деталь, которую и нужно заменить своими руками.
Для этого родной диод из указки снимается и аккуратно заменяется более мощным, его надежное крепление можно выполнить с использованием клея.
Возможно, снять старый диодный элемент сразу не получится, поэтому его можно подковырнуть бережно кончиком ножа, затем слегка встряхнуть корпус указки.
На следующем этапе изготовления лазерного резака нужно сделать для него корпус.
Для этой цели пригодится фонарик с аккумуляторными батарейками, что позволит лазерному резаку получить электроподпитку, приобрести эстетичный вид, и удобство использования.
Для этого в корпус фонарика своими руками необходимо внедрить модифицированную верхнюю часть бывшей указки.
Затем нужно подключить к диоду зарядку, посредством находящейся в фонарике аккумуляторной батареи. Очень важно в процессе подключения точно установить полярность.
До того как фонарик будет собран, необходимо снять стекло и прочие лишние элементы указки, которые могут стать помехой лучу лазера.
На завершающем этапе проводится подготовка лазерного резака к использованию.
Для комфортной ручной работы все этапы работы над прибором необходимо строго соблюдать.
Видео:
С этой целью нужно проконтролировать надежность фиксации всех внедренных элементов, правильность полярности и ровность установки лазера.
Итак, если все вышеизложенные в статье условия сборки были точно соблюдены, резак готов к применению.
Но так как самодельный ручной прибор наделен невысокой мощностью, то вряд ли из него получится полноценный лазерный резак по металлу.
Что идеально сможет выполнять резак, так это сделать отверстия в бумаге или полиэтиленовой пленке.
А вот наводить на человека лазерное приспособление, сделанное своими руками нельзя, здесь его мощности будет достаточно, чтобы навредить здоровью организма.
Как можно усилить самодельный лазер?
Чтобы сделать своими руками более мощный лазерный резак для работы по металлу, нужно использовать приборы из следующего списка:
DVD-RW привод, нет разницы рабочий или нет;
100 пФ и мФ – конденсаторы;
2-5 Ом резистор;
3 шт. аккумуляторные батареи;
паяльник, провода;
коллиматор;
стальной фонарь на светодиодных элементах.
Сборка лазерного резака для ручной работы происходит по следующей схеме.
С применением указанных приборов происходит сборка драйвера, впоследствии он посредством платы сможет обеспечивать лазерному резаку определенную мощность.
При этом к диоду ни в коем случае нельзя подсоединять электропитание напрямую, так как диод сгорит. Также нужно принять во внимание, что диод должен брать подпитку не от напряжения, а от тока.
В качестве коллиматора используется корпус, оснащенный оптической линзой, за счет которой будут скапливаться лучи.
Данную деталь легко отыскать в специальном магазине, главное, что в ней присутствует паз для установки диода лазера. Цена данного устройства небольшая, примерно составляет 3-7$.
Кстати, лазер собирается так же, как и вышерассмотренная модель резака.
В данном случае рекомендуется применять специальные браслеты, которые позволят убрать с диода статическое напряжение.
В качестве антистатического изделия также может применяться проволока, ею обматывают диод. После чего можно приступать к компоновке драйверного устройства.
Прежде чем перейти к полной ручной сборке лазерного резака, нужно проверить работоспособность драйвера.
Сила тока замеряется с помощью мультимера, для этого берут оставшийся диод и проводят измерения своими руками.
С учетом скорости тока, подбирают его мощность для лазерного резака. К примеру, у одних вариантов лазерных устройств сила тока может равняться 300-350 мА.
Видео:
У других, более интенсивных моделей, она составляет 500 мА, при условии использования другого драйверного устройства.
Чтобы самодельный лазер выглядел более эстетично, и им можно было удобно пользоваться, для него нужен корпус, в качестве которого вполне может использоваться стальной фонарик, функционирующий на светодиодах.
Как правило, упомянутый прибор наделен компактными размерами, которые позволят поместиться ему в кармане. Но во избежание загрязнений линзы, заранее нужно приобрести или сшить своими руками чехол.
Особенности производственных лазерных резаков
Не каждому по карману цена лазерного резака по металлу производственного типа.
Такое оборудование применяют для обработки и разделки металлических материалов.
Принцип действия лазерного резака строится на выработке инструментом мощного излучения, наделенного свойством испарять или выдувать металлический расплавленный слой.
Такая производственная технология при работе с разными типами металла способна обеспечить высокое качество среза.
Глубина обработки материалов зависит от вида лазерной установки и характеристик обрабатываемых материалов.
На сегодняшний день используется три вида лазеров: твердотельные, волоконные и газовые.
Устройство твердотельных излучателей основывается на использовании в качестве рабочей среды конкретных сортов стекла или кристаллов.
Здесь в пример можно привести недорогие установки, эксплуатируемые на полупроводниковых лазерах.
Волоконные – их активная среда функционирует за счет применения оптических волокон.
Данный тип устройства является модификацией твердотельных излучателей, но как утверждают специалисты, волоконный лазер успешно вытесняет свои аналоги с области металлообработки.
При этом оптические волокна являются основой не только резака, но и гравировального станка.
Видео:
Газовые – рабочая среда лазерного устройства сочетает углекислый, азотный и гелиевый газы.
Так как КПД рассматриваемых излучателей не выше 20%, их используют для резки и сварки полимерных, резиновых и стеклянных материалов, а также металла с высокой степенью теплопроводности.
Здесь в пример можно взять резак по металлу выпускаемый компанией Ханса, применение лазерного устройства позволяет резать медь, латунь и алюминий, в данном случае минимальная мощность станков только выигрывает у своих аналогов.
Схема работы привода
Эксплуатироваться от привода может лишь настольный лазер, данный тип устройства представляет собой портально-консольную машину.
По направляющим рейкам устройства лазерный блок может перемещаться как вертикально, так и горизонтально.
В качестве альтернативы портальному устройству была изготовлена планшетная модель механизма, ее резак перемещается только по горизонтали.
Другие существующие варианты лазерных станков имеют рабочий стол, оснащенный приводным механизмом и наделенный свойством перемещаться в разных плоскостях.
На данный момент имеется два варианта управления приводным механизмом.
Первый обеспечивает перемещение заготовки за счет эксплуатации привода стола, или перемещения резака выполняется за счет функционирования лазера.
Видео:
Второй вариант предусматривает одновременное перемещение стола и резака.
При этом первая модель управления по сравнению со вторым вариантом считается намного проще. Но вторая модель все-таки отличается высокой производительностью.
Общей технической характеристикой рассмотренных случаев является необходимость внедрения в устройство блока ЧПУ, но тогда цена для сборки прибора для ручной работы станет выше.
rezhemmetall.ru
Резак по металлу лазерный и самодельный ручной: как изготовить своими руками
Давайте так: лазерный резак по металлу – это как мужские часы. Крутой и уникальный инструмент, необходимый современному мужчине, имеющем собственный гараж и умеющими что-то делать своими руками.
Этот инструмент можно сделать своими руками. Это нетрудно, если выполнять необходимые правила и инструкции. Мощность самодельного лазерного ножа выйдет не бог весть какая, но при необходимости ее можно увеличить несколькими способами.
Конечно, у вас не выйдет инструмента для промышленных нужд, но для бытовых домашних работ ваш самодельный резак вполне подойдет.
Найти указку
Во-первых, вы сможете обойтись подручными материалами, то есть вам не придется ничего специально покупать в магазине. Самое главное – найти старую лазерную указку.
Дополнительно вам понадобятся:
- отвертки разного калибра;
- матрица с лазерным приводом из бывшего в употреблении DVD-ROM;
- фонарь, имеющий питание от аккумуляторных батареек;
- паяльник.
С большой осторожностью и максимальной тщательностью разбираем лазерную указку и дисковод. Сначала нужно достать привод из компьютерного дисковода.
Важный нюанс: это привод должен быть не только читающим, но и пишущим. Такими свойствами обладают все приводы современных компьютеров, так что перед тем, как разобрать, уточните модель и характеристики привода.
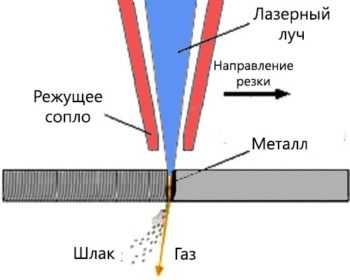
Лазерный резак по металлу.
Второй шаг – найти и вытащить диод красного цвета, с помощью которого производится запись на диске в виде прожигания. Вынимается этот диод просто: нужно паяльником распаять крепления.
Все действия проводите с нежностью и осторожно: диоды и прочая мелочь, связанная с ними – вещи хрупкие и готовые испортиться при малейшей возможности. Снизить риск поломки просто. Для этого достаточно диод поменять на красную лампочку из провода DVD.
Теперь начинаем делать корпус резака из припасенного фонарика и аккумуляторных батареек, которые понадобятся для питания резака. Использование фонарика позволит вам произвести компактную и комфортную для работы модель.
Не забудьте удалить из него защитное стекло, так как оно может стать преградой для лазерного луча в дальнейшем.
Важнейший момент при изготовлении корпуса – правильный выбор полярности тока.
Теперь нужно запитать диод с помощью его подключения к зарядке для аккумуляторных батареек.
В качестве финального шага и перед началом работ делаем проверку:
- крепка ли фиксация в зажимах и фиксаторах;
- полярность устройства;
- направление и фокус луча.
Что можно делать вашим резаком?
Не забывайте, что ваш новый самодельный резак по металлу не способен резать толстый металл – это ему попросту не под силу. Но вы можете усилить инструмент для выполнения работ с практически любым металлом, если это необходимо.
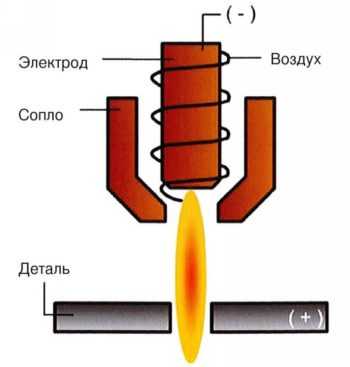
Чертеж плазменной резки металла.
Предварительно вам нужно будет запастись конденсатором, потому что нож с усиленной мощностью ни в коем случае нельзя будет включать в сеть напрямую. Поэтому сначала ток должен выходит на конденсаторы и только потом на батарейки.
Повысить мощность можно с помощью дополнительных резисторов. Добавочную мощность ваш нож получит от использования так называемого коллиматора, который служит для концентрации и скапливания лазерного луча.
Коллиматоры стоят очень недорого и продаются в любом отделе электрооборудования.
В случае повышения мощности одновременно повышается никому не нужная статичность. Она легко ликвидируется с помощью намотки алюминиевой проволоки вокруг диода.
Теперь нужны измерения: меряем силу тока на концах резака после их подключения к диоду. Показатели регулируются, самый подходящий диапазон – от 300 до 500 мА.
Зачем возиться?
Гаджет крутой и нужный. Но дорогой. Зато резак по металлу своими руками смастерить несложно даже для новичков. Так что мотивация заняться реализацией наших советов налицо.
Давайте-ка лучше разберемся с принципами действия лазерного ножа, это пригодится всем: тем, кто его купил и тем, кто сделал его своими руками.
Главный герой – сфокусированный лазерный луч, который благодаря направленности и излучению действует, к примеру, на металл. Сам луч чрезвычайно узкий – диаметр у него очень маленький. Благодаря этому срезы на заготовках отличаются высочайшей точностью.
Глубина прорезывания зависит лишь от мощности инструмента. Здесь, конечно, выигрывают профессиональные заводские модели с высокими показателями углубления. Что же касается нашего самодельного лазерного ножа, то глубина здесь доступна на уровне 10 – 30 мм.
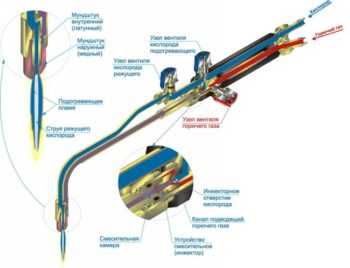
Схема работы газового резака.
Резаки по металлу подразделяются на три вида:
Твердотельные резаки
Выполнены из специального стекла или светодиодов кристаллического состава. Это относительно дешевые модели, выпускаются и используются в промышленности.
Волоконные лазерные ножи
В этом случае используется оптическое волокно, вследствие чего эти модели очень эффективны с точки зрения глубины резки. По сути действия напоминают твердотельные устройства – близкие родственники. Но более эффективные и дорогие по цене.
Газовые резаки
Используемые газы – азот, углекислый газ, может быть гелий. Данные модели значительно эффективнее двух предыдущих видов. Они режут все – от полимеров и резины до самых «трудных» металлов.
tutsvarka.ru
Лазерная резка металла своими руками
Современные технологии и технические приборы работу мастеров по ремонту, строителей и дизайнеров интерьеров делают намного удобнее и комфортнее. Лазерную резку металла на сегодняшний день считают вполне обоснованно передовой технологией, которую используют для обработки металлов. Ее применение позволяет получить неограниченные, невиданные раньше, возможности для изготовления изделий из металла разной конфигурации и дизайна.
Содержание:
- Процедура лазерной резки
- Преимущества лазерной резки
- Использование лазерной резки
- Станок для лазерной резки
Процедура лазерной резки
Лазерная резка металла – самая прогрессивная и перспективная методика, благодаря которой создаются высококачественные элементы, хотя и является относительно молодой технологией. Осуществляется процедура с помощью технически сфокусированных мощных лазеров, которые характеризуются высокой концентрацией луча и способны разрезать любые материалы – от дерева до металла.
На поверхности металла при этом формируются окислы, увеличивающие поглощение энергии и вызывающие температуру до точки плавления. На месте контакта луч лазера создаёт высокую температуру, в результате чего металл плавится, а за границей области контакта только нагревается. Одновременно подается активный газ, чаще всего кислород, что выдувает продукты горения и вызывает увеличение скорости резки. На видео лазерной резки видно, что, выдувая окислы и жидкий металл, кислород нагревает следующие слои.
Этот процесс происходит, пока металл не прорежется на всю глубину. Струя кислорода способна активно охлаждать металл возле линии разрезов. Небольшая область термического воздействия обеспечивает возможности создания параллельных кромок на малых расстояниях – примерно до 0,2 миллиметра. Зачастую, чтобы достичь необходимой точности операции резки, рабочий процесс управляется компьютером, за счет которого получится спрограмировать любое изделие.
В основном для лазерной резки листового металла используют аппараты на основе газовых и твердотельных лазеров. Лазерный срез металла выходит идеально ровным, без деформаций, которые присутствуют при механическом разрезе. К тому же технология лазерной резки позволяет добиться существенной точности работы, минимальных отходов и быстрого выполнения.
Преимущества лазерной резки
Благодаря своим достоинствам методика лазерной резки металла – самая востребованная на рынке. Именно эта процедура облегчила в значительной мере работу с твердосплавными материалами, которые очень сложны в обработке и часто приводят к ухудшению качества после обработки. Для лазерной резки больше всего подходят цветные металлы, сталь и сплавы алюминия.
Установка лазерной резки упрощает обработку утолщенных листов, материалов из толстых сплавов и деталей сложных форм деталей, а также вырезать отверстия в сверхтвердых материалах малого диаметра. Геометрия изделий ограничена исключительно фантазией конструкцией. С другой стороной из-за специфики бесконтактной технологии лазерной резки металла можно резать хрупкие и тонкие материалы.
Для автоматизации функционирования системы необходимо только подготовить для компьютера файл. Так как при этом не происходит механических воздействий на материал, металлические изделия не нуждаются в дальнейшей механической обработке.
Ещё одно достоинство лазерной резки металла – благодаря программной раскройке листового металла есть возможность уменьшения расходов на выпуск малой партии продукции, потому что отсутствует потребность изготовления литейных форм. Простое управление рабочим инструментам позволяет вырезать контуры в объемных и плоских деталях. Если сравнивать лазерную резку металла своими руками с плазменной, то на сегодня отдается предпочтение первому варианту, потому что лазерная резка металла обходится намного дешевле.
Использование лазерной резки
Процедура лазерной резки металла может применяться не только непосредственно для резки, но и для проведения гравировки разнообразных изделий. Лазерная резка также предназначена для мелкосерийного производства. Для этого принято использовать оборудование, которое характеризуется невысокой мощностью лазера и небольшими размерами.
Если стоит задача выпустить серию деталей, стоит работать с более мощной установкой – лазерной системой, которая в себя включают лазер, координатный стол и компьютер со специальным программным обеспечением для поддержания векторной графики.
На подобном оборудовании можно осуществить с минимальными погрешностями (0,001 миллиметра) достаточно сложные технологические процессы, к примеру, лазерную резку объемных деталей и резку по сложному контуру.
С использованием подобной технологии раскраивают материалы в листах – конструкционную и нержавеющую сталь, алюминий, дерево и даже пластик. Работы проводятся за короткий промежуток времени с приемлемой ценой лазерной резки металла и безупречным качеством. Лазерная резка позволяет изготовить детали, которые имеют сложные контуры, производить такие изделия, как разнообразные логотипы, вывески, сувениры и элементы декора.
Станок для лазерной резки
Оборудование для лазерной резки – достаточно стандартно. Станок состоит из рабочего стола и режущей головки лазера, что перемещается в его плоскости. Процесс перемещения лазерной головки обеспечивается высокоточными приводами по перпендикулярным направляющим для получения четкого контура детали.
Принцип работы станка
Аппарат лазерной резки металла оснащен режущей оптикой для проведения безоксидной резки металла. Оптическая система фокусировки способствует поддержанию заданного положения фокуса, что помогает в результате получить контур обработки более точным и четким. Управляют движением режущей головки посредством специальной компьютерной программы раскроя.
С помощью программы задают последовательность совершения текущих и последующих операций. Эта программа регулирует силу излучения зависимо от глубины резки и поэтому позволяет изготавливать самые сложные декоративные элементы и детали для разной техники. Чтобы автоматически раскроить листовой металл, необходимо наличие файла рисунка, который перенесён в компьютер режущей установки.
Для работы лазерного оборудования требуются незначительные затраты электрической энергии, а высокая скорость резания и отсутствие расходных компонентов создают условия для эффективного рабочего процесса. Производительность станка можно повысить за счет увеличения мощности излучения, которая регулируется в процессе работы. Стоимость лазерной резки металла с помощью специального станка зависит от толщины листа и длины линии реза.
Используются технологические принципы, которые базируются на устройстве газовых и волоконных лазеров, что способны работать в постоянном и импульсном режиме. Работа на станке осуществляется при помощи прожигания насквозь листового материала лучом лазера.
Из-за отсутствия прямого контакта изделия и режущей головки оборудование безопасно обрабатывает хрупкие изделия, твёрдосплавный материал, легко раскраивает тонколистовую сталь на высокой скорости, выгодно при выпуске продукции выпускается небольшими партиями. При лазерной резке металла цветного или черного отсутствуют физические деформации и микротрещины на поверхности готовых изделий.
Цены на станок лазерной резки нового поколения сильно отличаются и зависят от марки производителя и установленного дополнительного оборудования. Для монтажа данного комплекса нет потребности специально устраивать подготовку под фундамент, разместить станок можно в любом удобном месте, что обеспечит технологический доступ к нему.
Предназначение лазерного оборудования
Станки для лазерной резки классифицируются по рабочим параметрам – интенсивности излучения, типу материала заготовки, давлению и составу струи режущего газа. Оборудование для лазерной резки металла подразделяется на такие виды резки: кислородное, кислородное с поддержкой лазером, испарительное, в инертном газе, термоскалывающее. Выпускаются специализированные станки для лазерной резки труб, которые выступают пригодными для любых профилей, причем обработку можно производить непосредственно по всей длине заготовки.
Лазерные станки прекрасно зарекомендовали себя при резке стальных листов толщиной 0,2-25 миллиметров, нержавейки, толщина которой составляет 0,2-30 миллиметров, алюминиевых сплавов толщиной 0,2-20 миллиметров, латуни, толщина которой 0,2-12 миллиметров, меди толщиной 0,2-15 миллиметров. Для обработки разных материалов используются различные типы технологий и лазеров, фото лазерной резки металла можно посмотреть в сети.
Станок нашел широчайшее применение для изготовления деталей из металла, декоративных элементов интерьера, при работе с пластичными и мягкими металлами. Стоимость станка лазерной резки при правильной эксплуатации оправдывает себя и быстро окупается. Продукция, которая изготовлена при помощи оснащенных лазером станков, отличается экономической целесообразностью и высокой рентабельностью.
Таким образом, лазерная резка является передовой технологией в мире работы с металлом, которая с каждым днем набирает обороты. Данная методика позволяет существенно облегчить рабочий процесс. К тому же обработанный металл имеет качественный срез, на нем отсутствуют микротрещины и деформации.
strport.ru
Резка металла своими руками | Строительный портал
Каждому промышленному предприятию или частному лицу, которое занимается металлообработкой, требуется станок для резки металла, что отвечает заданным требованиям к стоимости, производительности и безопасности. Сегодня выделяют большое количество разных методов обработки металла – обработка металла плазмой, лазером и давлением, а также ручная резка металла ножницами. Если вы ещё не определились с оптимальным методом и подходящим оборудованием для резки металла, наша статья поможет вам сделать это.
Содержание:
- Виды резки металла
- Газовая резка металла
- Плазменная резка металла
- Лазерная резка металла
- Гильотинная резка металла
Виды резки металла
Процесс резки металла представляет из себя отделение заготовок от металла литого, сортового или листового. Наиболее распространенными и эффективными с экономической позиции на сегодняшний день выступают такие методы, как плазменная, лазерная и газовая резка. Очень часто металл режут пресс-ножницами, которые способны пробивать пазы и отверстия разных форм в стали разнообразной прочности.
При выборе одного метода обработки металла из выше перечисленных рекомендуется ориентироваться на качество самого процесса работы, количество конечных отходов и точность исполнения. Важным моментом выступает и возможность создания небольшой партии деталей в максимально сжатые строки при оптимальной цене резки на профильных производствах.
Более, того выбор одного из них оправдан при учете определенных критериев, таких как эффективность работы, конечный результат, стоимость изделия. При этом существует определенный список металлов и сплавов, с которыми целесообразно работать тем или другим оборудованием.
Газовая резка металла
Газовая резка представляет собой процесс резки металлических изделий, который основан на свойстве металлов, что нагреты до определенной температуры (1200-1300 градусов), гореть в чистом кислороде. Благодаря газовой резке листового металла в наше время можно осуществлять самые разнообразные типы обработки – подготовка кромок для процесса сварки, прямая резка металла, процедура резки под углом.
Сущность технологии
Резку принято начинать с кромки листа. Поверхность, что предназначена для резки, необходимо очистить от ржавчины, окалины и грязи. Кислород и газ в горелки подается из баллонов, где они содержатся в сжатом состоянии. Масса одного баллона равняется 70 кг. Рабочее давление кислорода на один метр квадратный составляет 300 кН, а газа – достигает 50 кН.
Давление при этом можно отрегулировать в редукторе устройства, который навинчен на штуцер кислородного баллона. Редуктор оснащен манометром высокого давления, который показывает давление кислорода в баллоне, а также оборудован манометром низкого давления, что предоставляет информацию о рабочем давлении.
Лист металла прожигается и разрезается струей кислорода, которая подается под большим давлением. Образующиеся окислы железа вытекают в расплавленном состоянии и выдуваются из полости реза. Технология газовой резки металла предполагает использование резака, который представляет собой некую сварочную горелку со специальным устройством для подвода кислорода.
Виды газовой резки
В данном виде сварки традиционно используются водород (коксовый, нефтяной и природный) и ацетилен, пары керосина и бензина, которые могут достигать в процессе горения температуры в 3200 градусов. Зависимо от применяемого горючего газа, выделяют водородно-кислородную, ацетиленокислородную и бензинокислородную резку, а также машинную и ручную резки.
Отдельным видом газовой резки выступает флюсокислородная резка, что позволяет разделять трудно поддающиеся резке металлы – хромоникелевые и высокохромистые стали, алюминиевые сплавы и чугуны. В этом случае процедуру облегчают порошкообразные флюсы, которые вдуваются вместе с кислородом.
Помимо разделительной кислородной резки, когда режущая струя практически перпендикулярна поверхности металла, используют кислородную обработку, в процессе которой режущую струю направляют к поверхности металла под острым углом.
Данным способом режут листы из углеродистых средне- и низколегированных сталей, которые имеют толщину от 1 до 200—300 миллиметров. На видео о газовой резке металла вы увидите, что возможной считается газовая резка стали толще 2 метров. Кислородная резка широко используется в цветной и чёрной металлургии, а также в частном строительстве.
Предъявляемые требования
Чтобы совершить данный процесс, необходимо выполнить ряд требований. Помните, что металл должен обладать большей температурой плавления, чем показатель температуры горения в кислороде. Напротив, оксиды металла должны отличаться температурой плавления меньшей, чем температура плавления выбранного металла.
Следите, чтобы уровень термального воздействия был достаточен для обеспечения непрерывности процесса резки. Обрабатываемый металл не должен обладать слишком высокой теплопроводностью, так как в противном случае тепловая энергия будет быстро отводиться. Соответственно данным критериям, которые предъявляются к газовой резке, для этой процедуры идеально подходят низкоуглеродистые и низколегированные стали и железо.
Достоинства газовой резки
Главным преимуществом газовой резки металла является возможность раскроя листов металла, которые имеют большую толщину – до 200 миллиметров. При этом ширина среза составляет 2-2,5 миллиметров. При помощи оборудования для газовой резки металла можно провести вертикальную кромку среза, что в ходе процесса не будет закаливаться.
Нельзя не вспомнить и об экономической эффективности данной технологии – газовая резка не требует вложения больших финансовых средств. Минимальны требования, что связаны с техническим обслуживанием процесса. Несомненным достоинством газовой сварки металла является и тот факт, что для её проведения не нужна никакая механическая обработка.
Плазменная резка металла
Резка металлов с использованием струи плазмы вместо резца называется плазменной. Поток плазмы формируется в результате обдува сжатой электрической дуги газ, который нагревается и в процессе ионизируется – распадается на положительно и отрицательно заряженные частицы. Плазменный поток обычно имеет температуру близко 15 тысяч градусов Цельсия.
Способы плазменной резки
Выделяют поверхностную и разделительную плазменную резки. Однако на практике широкое использование получила именно разделительная технология резки металла. Сам процесс резки осуществляют двумя методами – плазменной дугой и струей.
При резке металла плазменной дугой он включается в электрическую цепь. Выше упомянутая дуга возникает между изделием и электродом резака из вольфрама. Если вы выбрали вторую методику, то помните, что в резаке дуга формируется между двумя электродами. Разрезаемый лист не включается в электрическую цепь.
По производительности плазменная резка превосходит кислородную. Но если вам нужно порезать титан или металл большой толщины, то рекомендуется отдать предпочтение кислородной резке. При резании цветного металла плазменная резка считается незаменимой. Особенно это касается алюминия.
Аппараты для плазменной резки
Для образования плазмы принято использовать активные и неактивные газы. К первой группе относят воздух и кислород, которые используются при резке черных металлов (меди, стали и алюминия), и неактивные – водород, аргон и азот для резки сплавов и цветных металлов (высоколегированной стали, которая имеет толщину до 50 миллиметров, латуни, меди, алюминия и титана).
Для механизации процедуры были разработаны аппараты для резки металла – полуавтоматы и переносные машины разных модификаций. Полуавтоматы работают с неактивными и активными газами, в то время как переносные машины используют исключительно сжатый воздух.
Резка металла плазмой в домашних условиях осуществляется при помощи ручных аппаратов, в комплект которых входят режущий плазмотрон, коллектор, кабель-шланговый пакет и зажигалка, предназначенная для возбуждения режущей дуги. Такие комплекты позволяют выполнять ограниченный объем работы с загрузкой оборудования не больше чем на 50%. Поэтому их рекомендуется доукомплектовать на время работы сварочными преобразователями и выпрямителями.
Сущность технологии
Началом процедуры резания металлов является момент, когда возбудилась плазменная дуга. Начав резку, следует поддерживать между поверхностью металла и соплом плазмотрона постоянное расстояние, которое составляет 3 – 15 миллиметров.
Стремитесь к тому, чтобы ток был минимальным в процессе работы, потому что при возрастании силы тока и увеличении расхода воздуха падает ресурс работы электрода и сопла плазмотрона. Но уровень тока при этом должен обеспечивать высокую производительность резки. Самой сложной операцией выступает пробивка отверстий, так как возможно образование двойной дуги и выход плазмотрона из строя.
Помните, что инструмент для резки металла при пробивке должен над поверхностью детали подниматься на 20 – 25 миллиметров. В рабочее положение плазмотрон опускается после того, как лист будет насквозь пробит. Если вы пробиваете отверстия в листах, которые имеют большую толщину, рекомендуется использовать защитные экраны, имеющие отверстия диаметром 10-20 миллиметров. Экраны необходимо помещать между плазмотроном и изделием.
При резке алюминия с использованием аргоноводородной смеси для увеличения стабильности горения дуги содержание водорода не должно быть больше 20%. Резку меди принято выполнять с применением водородосодержащих смесей. Латунь нуждается в азотоводородной смеси или азоте. После резки медь в обязательном порядке нужно зачистить на глубину 1-1,5 миллиметра. Но не это требование совсем не обязательно для латуни.
Лазерная резка металла
Резка лазером является принципиально новым видом обработки металла, который отличается крайне высокой точностью и производительностью. Подобные режущие станки в мире металлообработки совершили революцию, сделав процедуру создания сложных металлических конструкций проще, быстрее и доступнее по цене. Лазерная резка в наше время уверенно вытесняет другие разновидности обработки металлических заготовок и становится все более популярной.
Сущность технологии
Технология лазерной резки металла своими руками на сегодняшний день – одна из самых прогрессивных технологий в создании разных деталей из листовых материалов. Процедура хороша своей универсальностью, потому что она позволяет работать с любыми материалами – металлического и неметаллического происхождения.
Лазерный луч является узконаправленным световым потоком маленького диаметра, что обладает высокой интенсивностью. Если лазерный луч навести на металлическую поверхность или другой твердый объект, изделие нагреется до высокой температуры. Её достаточно, чтобы металл начал плавиться в точке контакта. Но вместе с этим участки поверхности, которые прилегают к лучу, остаются горячими, но не повреждаются.
Двигая по поверхности луч, можно создавать очень тонкую качественную линию резки металла с идеально тонкими краями, несмотря на толщину обрабатываемого металла. Площадь лазерного потока, который попал на плоскость, исчисляют буквально квадратными микронами. Но вместе с этим при лазерной резке плотность энергии, которая направляется на металл, чрезмерно высока, что и служит причиной возникновения области разогрева.
В результате локально совершается расплав металла, который сопровождается уносом молекул вещества. Аппараты для лазерной резки представляют собой обычные координатные столы, что сопрягаются с головкой, которая управляется микропроцессором станка и которая перемещается по заданной программе над поверхностью обрабатываемого листа.
Могут выпускаться станки лазерной резки специального назначения, к примеру, пользуются популярностью в последнее время лазерные станки для труб, что являются пригодными для любых профилей. При этом вы можете провести обработку сразу по всей длине детали. Это достаточно эффективный метод, который обеспечивает жесткий контроль геометрии резки при использовании лазерного станка.
Достоинства лазерной технологии
К несомненным преимуществам лазерной технологии относят:
- полное отсутствие физических деформаций и брака при работе станка;
- возможность функционирования станка с пластичными металлами;
- отсутствие на поверхности готового изделия микротрещин;
- прецизионная точность обработки лазерного станка;
- высокая скорость работы;
- малая толщина реза;
- безотходность станка;
- высокий уровень автоматизации процесса лазерной резки;
- приемлемая стоимость резки металла.
Использование лазерной резки
Работа на лазерном станке происходит при помощи прожигания листового материала насквозь лучом лазера. Благодаря отсутствию прямого контакта детали и режущей головки оборудование позволяет обрабатывать безопасно хрупкие изделия, с успехом справляется с твёрдосплавным материалом, легко обеспечивать скоростной раскрой тонколистовой стали.
Технология считается выгодной и в тех ситуациях, когда продукцию выпускают небольшими партиями, потому что исключаются затраты на изготовление дорогостоящих форм для литья. Оборудование способно справиться со сталью любого состояния и качества, хорошо работает с алюминием, сплавами алюминия, медью, латунью.
Очень существенным нюансом подобного технологического процесса выступает простота в отношении работы с плоскими и объемными деталями, а также сложными контурами.
Лазерная резка является одной из технологий, в рамках которых себестоимость продукта при создании сложных изделий почти не зависит от величины партии, что обрабатывается станком. Именно поэтому технологии лазерной резки широко применяются в частном строительстве и домашнем хозяйстве, при этом время до получения конечного результата минимально.
Гильотинная резка металла
Для качественного и быстрого раскроя металла используются специальные листовые ножницы – гильотины. Название подобных металлорежущих станков происходит от сходства работы ножниц со средневековым орудием казни. Но сегодня гильотинные ножницы применяются в безобидных целях.
Выбор листовых ножниц
Главными критериями выбора гильотины выступает вид производства: штучное или серийное, толщина листа металла, длина линии продольной резки металла и механическая прочность. Потребители зависимо от своих целей могут выбрать простые ручные или электромеханические гильотины. Многие модели листовых ножниц бывают дополнительно оборудованы промышленной электроникой и опциями, которые повышают производительность резки металла.
Несмотря на изобилие типов привода, у всех моделей гильотин одинаков принцип работы. Для начала размещается на рабочем столе разрезаемый лист по выставленным упорам между нижней и верхней ножами. Предварительно стоит поджать к столу гильотины лист металла прижимной балкой. Дальше перемещается верхний нож и осуществляется резка металла. Затем можно транспортировать готовые детали из зоны резанья металла.
Точность резания листов металла посредством гильотинных ножниц обеспечена прижимным механизмом листа. Резка, как правило, осуществляется по разметке или упору: на гильотинах принято устанавливать точные задние линейки, позволяющие добиваться высокой точности процедуры реза. Некоторые модели оснащены возвратным поддоном для сбора отрезанного металла.
Выбирая определенную модель ножниц, нужно точно продумать список востребованных функций, потому что не всегда преимущества работы состоят в большом их количестве, тогда как цена такого станка зависит от данного показателя напрямую. Для работы в домашних условиях вполне подойдет гильотина с набором только необходимых функций, многофункциональные ножницы требуются же на крупных производствах.
Виды гильотин
По принципу устройства листовые ножницы могут быть ручными, пневматическими, гидравлическими, механическими, автоматическими, а также сочетать одновременно несколько комбинаций. Ручные и пневматические гильотины относят к самым простым и используются для прямолинейной резки листов металла.
Гидравлические ножницы с электромеханическим приводом отличаются простотой в управлении и высоким уровнем труда, что можно отметить на видео о резке металла. Точность реза обеспечена регулировкой положения ножей. Огромной популярностью пользуются гильотинные гидравлические ножницы с автоматической или ручной регулировкой зазора, который образуется между ножами.
Использование гильотинных ножниц
Гильотины предназначены для резки в поперечном и продольном направлениях металлических листов, которые имеют разную толщину. Некоторые виды листовых ножниц способны резать круглый, квадратный или угловой металлопрокат. Основными характеристиками гильотин, которые используются для резки металла, считаются длина и максимальная толщина реза.
Использование гильотин позволяет получить точный срез материала без зазубрин и вмятин, при этом оборудование не повреждает полимерное покрытие и окраску металла. Зависимо от технических возможностей применяются гильотинные ножницы на массовых и индивидуальных производствах.
Прочитав нашу статью, вы ознакомились с основными видами резки листового металла. Напомнив ещё раз – гильотинная, лазерная, плазменная и газовая резка. Каждый из них имеет свои достоинства и недостатки. Помните, что каждый вид резки металла связан с использованием специального оборудования и инструмента, что требует от потребителя наличия определенных навыков и строжайшего соблюдения техники безопасности.
strport.ru
Лазерная резка металла – технология обработки лазером
Лазерная резка – инновационная технология обработки металлических заготовок, которая применяется в производственных масштабах компаний, а также умещается в небольших частных мастерских. Благодаря уникальной установке, продуцирующей лазер, на определенном участке материала создает фигурные формы деталей.
Способ лазерной обработки подходит для каждого металлического материала, но индивидуальные особенности конкретного сырья все-таки имеются.
В чем заключается изюминка технологии?
Исходя из названия метода обработки, основное действие выполняется специальным лазером. Дорогостоящее оборудование фокусирует луч на маленькой площади, в результате чего образуется неимоверное количество энергии.
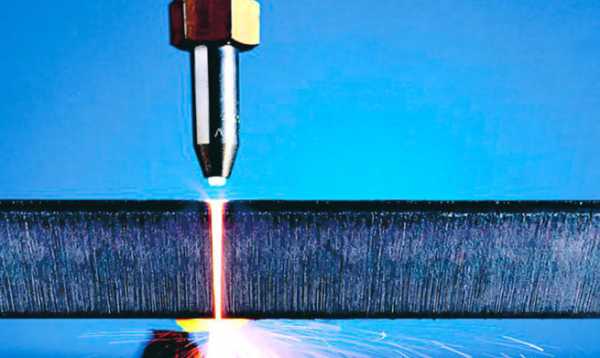
Лазерная резка металла
Под воздействием высокоплотного излучения происходит разрушение любого металла – он плавится, сгорает, иногда моментально испаряться.
Рассматривая характеристики лазерного воздействия, выделяют следующие аспекты процесса:
- отличительной чертой луча в сравнении с обычными световыми волнами является постоянная длина и частота продуцируемой волны. Это свойство обеспечивает отличную фокусировку с помощью системы линз на любой имеющейся поверхности;
- направленность луча всегда поддерживается в высокой концентрации, усиливает эффективность маленький угол рассеивания энергии;
- когерентность – способность сосредоточить в одной области множество однотипных процессов, ведущих к преобразованию материала. Суммарная мощность установки увеличивается за счет полного резонанса, всех происходящих внутри лазера процессов.
Подобные особенности обуславливают энергетическое постоянство, благодаря чему лазерная резка металла считается уникальным высокоэффективным методом получения необходимых деталей.
Тонкости технологического процесса
Современная лазерная установка – идеал оборудования, одновременно воплощающий скорость, невероятную точность обработки и простоту управления сложной машиной.
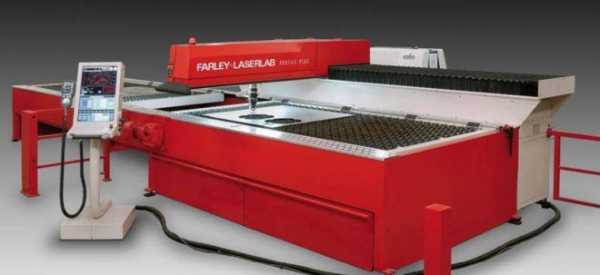
Многоцелевое устройство для лазерной резки
Благодаря внедрению компьютерного оснащения стало возможным устранить фактор человеческой ошибки, избегать излишков, обеспечить качество каждой выпущенной детали.
Работающая автоматизированная машина поддерживает постоянство сфокусированных лучей, совмещая линзами всю энергию в одном мощном потоке – лазере. При соприкосновении с поверхностью происходит нагревание исключительно намеченной линии разреза, при этом остальная часть заготовки остается незадействованной в процессе. Отсутствует лишняя деформация, чрезмерного нагревания всей детали с дальнейшим повреждением особо уязвимых областей не происходит.
Технология лазерной резки металла позволяет работать с мягкими сплавами и тонкими листами заготовок. Способы выполнения обработки подразделяются на два типа:
- лазерную резку плавлением детали;
- выполнение обработки путем испарения.
Плавление наиболее распространенный и дешевый способ достижения результата. Воздействие фокусированных лазерных волн на металл приводит к его нагреванию. Высокая температура на определенном участке становится причиной расплавления детали, а при равномерном смещении луча получают желаемую форму.
Если воздействие луча чрезмерное и энергия достигает второго физического рубежа – молекулы материала начинают закипать. При кипении наблюдается мгновенное испарение частичек детали.
На заметку: процесс испарения считается наиболее эффективным и точным методом обработки. Но для поддержания запредельного уровня энергии требуется множество ресурсов и производственных мощностей. Резку металла лазером по методу испарения считают дорогостоящим этапом производства, он существенно увеличивает себестоимость конечного результата.
Новый лазер – преимущества внедрения технологии
Создание некоторых важных элементов производственных машин и любого профессионального оборудования требует максимальной точности обработки металлических заготовок.
Достигнуть требуемого высокого результата позволяет лазерная резка металла, обладающая весомыми преимуществами в сравнении с известными альтернативными методами обработки:
- автоматизированный программный контроль качества и заложенный алгоритм работы позволяют увеличить точность резки, это является предпосылкой создания сложных элементов;
- скорость процесса существенно превосходит остальные способы;
- лазерное воздействие ограничивает чрезмерный перегрев заготовки, мягко разрезает материал;
- производительность любой лазерной установки обеспечивает заблаговременное выполнение крупных срочных заказов;
- температурному нагреву подвержена исключительно область разреза;
- допускается выполнение контурной резки любой сложности;
- объемы излишков регламентирует компьютер. Программа рассчитывает наиболее рациональное расположение всех необходимых форм;
- отверстия характеризуются минимальным диаметром, равным 0,5 мм.
Лазерную обработку металлов приравнивают к передовым производственным технологиям, что заставляет многих заказчиков уходить от старых производителей деталей к современным методикам.
Если компания внедряет этот метод обработки, то существенно возрастает качество выпускаемой продукции, появляется возможность выполнения индивидуальных заказов.
Резка алюминия – основные нюансы и характеристики процесса
Обработка алюминиевых заготовок происходит по определенному автоматизированному шаблону. В программу загружаются чертежи будущей детали, этот процесс позволяет избежать дорогостоящего привлечения узких специалистов. Дополнительная экономия заключается в рациональном расположении формы детали на имеющейся заготовке, снижается процентное количество излишков.
Распространенным производственным действием считается лазерная резка стали, а также работа с деревянными материалами.
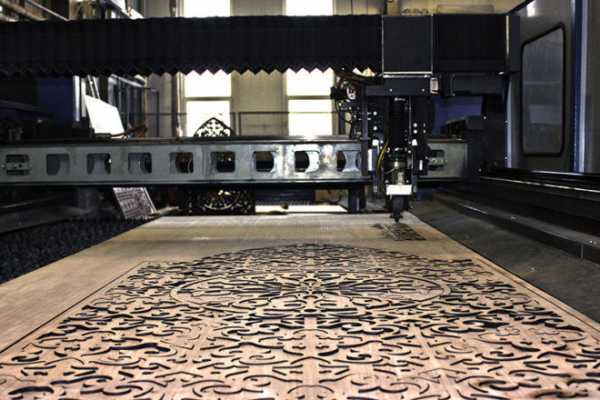
Лазерная резка по дереву
В процессе обработки алюминиевых листов совместно с основным лазерным лучом в сфокусированную зону подается поток воздуха, он увеличивает общую энергию луча, а также служит своеобразным мусоропроводом для образующихся шлаков и продуктов плавления.
Мягкий алюминий характеризуется высокой теплопроводностью, это позволяет ему отлично поглощать энергию лазера. Эта особенность является камнем преткновения многих рядовых производственных цехов, поскольку лишь профессиональный высокомощный лазер способен справиться с этим материалом.
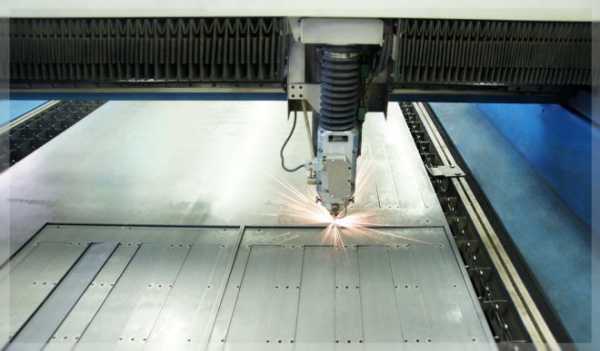
Станок с мощным лазером для резки алюминия
Основными нюансами в работе с алюминиевыми заготовками являются:
- небольшие производственные скорости – высокоскоростные установки не контролируют образование на поверхности заготовки деформаций;
- в процессе работы отсутствует прямой контакт с материалом, лазер просто прожигает поверхность алюминия;
- продувная зона обеспечивает полную очистку контура, эта функция весьма актуальна при дальнейшем сваривании;
- автоматизированная установка при правильно заложенном чертеже справляется с неимоверно сложным проектом детали.
- алюминий не приемлет исправлений – человеческий фактор полностью исключается за счет системы ЧПУ.
При обработке мягких металлов часто появлялся фактор статического влияния крепежных элементов, особенно устаревших производственных машин, но лазерная резка нержавеющей стали не требует закрепления заготовок. Достаточно просто положить заготовку в рабочую зону, а машина выполнит все необходимые операции в точности с заявленным электронным чертежом.
Лазерный станок с ЧПУ
Выполнение резки других материалов
Сложное выполнение художественной резки, раскройка рядовых материалов при работе с автоматизированной лазерной машиной ЧПУ становятся довольно обычной заводской работой. Кроме алюминиевых листов, подобные установки легко справляются с несколькими видами металла:
- нержавеющими материалами;
- листами из других материалов;
- стальными заготовками;
- латунью.
Работа с нержавейкой приравнивается к сложным энергозависимым проектам, поскольку материал отличается высокой сопротивляемостью к любому типу энергетического и физического воздействия. Мощный лазер и компьютеризированная начинка установки позволяют получить сложные фигуры и уникальные детали, прочность которых будет на высоком уровне.
Обработка нержавеющей стали
Лазерная резка нержавейки получила особую популярность. Особенностями процесса обработки нержавейки выступают:
- вся раскройки материала производится бесконтактным способом, что исключает даже минимальную деформацию деталей в местах воздействия машины;
- даже при работе с этим сложных материалов отсутствует фактор погрешности;
- лазерная резка материала исключает шансы образования отслоения краев, заусениц, а кромка края не деформируется;
- общие временные затраты существенно ниже, что обуславливает небольшое снижение стоимости подобных услуг;
- показатель мощности лазера не имеет ограничений по толщине заготовок из нержавейки. Любой лист материала будет равномерно разрезан с учетом заложенного чертежа.
Достоинством процесса лазерной обработки нержавеющих материалов считается отсутствие какого-либо влияния на качественные свойства детали, это не снижает длительность эксплуатационного периода.
Этот материал обладает уникальной защитой от коррозии, а прошлые технологические процессы всегда способствовали снижению способности противостоять окислению. Лазер не способен снижать физические свойства.
Медь и латунь – обработка материала лазером
Для обеспечения раскройки медных листов требуется правильно выставить параметры установки ЧПУ, что во многом предопределяет качество конечных форм. Выполнять резку необходимо на низких скоростях и при максимальной мощности луча. Только такое соотношение условий позволит создать идеальный требуемый продукт. Пренебрежение технологичными нюансами приводит к деформированию кромок и нарушению структурной целостности.
Латунь, как материал, не требует определенной скрупулезной настройки программы резки, допускается проведение раскройки при стандартных параметрах оборудования. Но именно лазерная методика обработки гарантирует отсутствие любых структурных повреждений. Нарушения физических свойств, перегрева детали в процессе работы не происходит. Лазерная резка металла – современный способ ювелирной обработки материалов.
Видео: Лазерная резка стали
promzn.ru
Лазерная резка металла своими руками: применение
Такая процедура, как лазерная резка металла своими руками, появившаяся достаточно недавно, сразу же стала самой прогрессивной и эффективной в области создания высококачественных элементов из металла. Данная процедура проводится при помощи лазера высокой мощности, который путем фокусирования луча на одной точке может резать любой материал, начиная от дерева и заканчивая металлом. Во время действия лазера на поверхности металла образуется окислитель, который повышает поглощение энергии и доводит его до температуры плавления. В том месте, где лазер контактирует с металлом, начинается плавление, при этом остальная часть материала не терпит никаких изменений, а лишь нагревается.
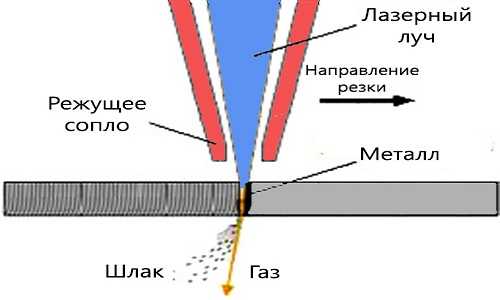
Технология лазерной резки металла.
Для того чтобы резка производилась гораздо быстрее, на поверхность металла подается активный газ, чаще всего кислород, который значительно ускоряется процесс плавления и может сдуть все остатки после него. При выдувании газа металл начинает расслаиваться, давая путь лазеру к следующему слою. Процесс завершается, когда вся толщина металла прорезана. При этом поток кислорода способен быстро охладить расплавленный метал, создавая своеобразный шов вокруг линии разреза. Малая зона воздействия лазера может делать прорез в металле с толщиной в 0,2 мм, что значительно меньше других существующих методов резки.
Большим плюсом этого процесса является возможность полной его автоматизации. Можно запрограммировать процесс и доверить сделать его компьютерной программе, вследствие чего изделие получается максимально точным. В большинстве случаев используются твердотельные лазеры или газовые. Стоит отметить, что лазерная резка может сделать идеально ровный и гладкий срез, который практически невозможно получить при механической резке. Она значительно быстрее и качественнее может выполнить работу, не оставляя после себя продуктов переработки.
Основные преимущества лазерной резки металла своими руками
Схема процесса лазерной резки.
Наличие весомых достоинств сделало лазерную режущую силу самой популярной и востребованной среди всего множества остальных методов. Лазерная резка металла своим появлением дала возможность многим предприятиям создавать более качественные предметы и объекты из металла, увеличивая их производительность. Рекомендуемыми металлами для такого типа резки являются цветные, сталь и сплавы из алюминия.
При помощи режущей силы данного оборудования можно выполнить до этого невозможные процедуры, например, обработку утолщенных листов, резку толстых сплавов, и создавать детали сложной формы. К тому же лазерная резка дает возможность разрезать и обрабатывать сверхтвердые металлы. Если посмотреть на данный процесс с другой стороны, то бесконтактный способ может значительно увеличить продуктивность процесса резки хрупких изделий, которые зачастую требуют высокой точности.
Чтобы выполнить резку при помощи компьютера, нужно лишь загрузить рабочий проект и запустить его. После его выполнения вам не понадобится делать дополнительную обработку, возможности лазерной резки металла предусматривают и этот фактор. Очень важным достоинством для предприятий, занимающимся производством металлических изделий, является то, что для мелкой партии больше не требуется создания литейной формы, которая стоила достаточно дорого и ее изготовление занимало существенный промежуток времени. К тому же изготовление деталей не ограничивается резкой в плоскости, можно производить резку металла в объеме. Если сравнить время выполнения одного изделия и возможности оборудования, предпочтение на сегодняшний день отдается именно лазерной резке.
Вернуться к оглавлению
Лазерная резка металла и ее применение
Схема конструкции твердотельного лазера.
Лазер может использоваться не только для того, чтобы просто разрезать пласты металлических конструкций, но и для выполнения высокоточной гравировки. Очень часто ее применяют для изготовления малых партий деталей или изделий.
Обычно для того, чтобы сделать небольшой заказ, применяется лазер малой мощности, который имеет достаточно компактные размеры. Если же необходимо выполнить выпуск большой партии продукции, используются более современные и мощные лазеры. Они в себя включают лазер высокой мощности, координатный стол и компьютерное оборудование, на которое устанавливается специальное программное обеспечение, способное поддерживать файлы с векторной графикой.
Погрешность такого оборудования крайне мала, оно может осуществлять работу с разносом в 0,001 мм. Как правило, его использование обусловлено необходимостью создания сложных металлических изделий и выполнения резки по сложному контуру. Лазерная резка металла значительно облегчает работу мастеров и делает каждое изделие более доступным за счет коротких сроков выполнения. К тому же режущий лазер может работать не только с металлом, но и с деревом, нержавейкой, алюминием и даже пластиковыми изделиями.
Вернуться к оглавлению
Станок для лазерной резки
Газовый лазер с поперечной прокачкой газа.
Оборудование для такого типа работ представляет собой стандартную конструкцию, которая включает в себя:
- Рабочий стол для объекта нарезки.
- Подвижную головку лазера, которая может перемещаться в пространстве.
Для того чтобы обеспечить высокую точность изготовления, головка оборудована специальными приводами, которые могут двигать ее в перпендикулярных плоскостях. Чтобы обеспечить высокую точность обрезки металла, аппарат оснащают фокусирующей оптикой, которая способна направить луч в одну точку. Данная фокусировка может регулироваться и позволяет создавать разрезы толщиной в десятые доли миллиметра. К тому же при изготовлении крайне тяжелых и мелких деталей обычно применяется компьютер, который с высокой точностью может выполнить данную работу.
Эта программа сама может повернуть лазерную головку в нужном направлении и регулировать мощность излучения лазера в зависимости от требований. Чтобы программа знала точные данные, необходим специальный рисунок, который содержит в себе все очертания и контуры изделия. Очень важным элементом является продув газом. Его применяют не только для того, чтобы расслоить металл, но и для дополнительной обработки. Он может тут же охладить металл и создать ровный и гладкий шов. Кроме того, больше не придется самостоятельно удалять остаточные продукты, все это автоматически делает продув газа.
Чтобы эксплуатировать данное оборудование, не потребуется больших затрат на электроэнергию, быстрая резьба и выполнение изделий сможет значительно увеличить производительность. Одним из важных факторов при работе на станке лазерной резки является то, что для работы ему не требуются расходные материалы. Для того чтобы повысить скорость нарезки, следует регулировать его мощность, которая может изменяться от достаточно маленьких величин до сильного излучения. Как правило, стоимость такой работы зависит от того, какую толщину и тип металла вы будете обрабатывать. Соответственно, чем толще и тверже металл, тем дороже будет стоить такая работа.
Вернуться к оглавлению
Предназначение лазерного оборудования
Существует несколько параметров, которые могут охарактеризовать оборудование для лазерной резки, среди них:
- Интенсивность излучения.
- Тип материала, над которым проводится лазерная резка.
- Давление и состав газа.
Станок уже зарекомендовал себя для изготовления изделий из металла, декоративных элементов, которые могут применяться в интерьере домов или квартир, а также для работы с пластиковыми объектами и мягкими металлами.
Если правильно эксплуатировать станок, он может в кратчайшие сроки окупить себя и принести своему обладателю огромное количество прибыли.
Продукция, выпускаемая при помощи данного станка, отличается высоким качеством, рентабельностью и точностью выполнения.
Каждый желающий может при помощи лазерной резки своими руками создать интересный и достаточно сложный предмет, который будет гармонично дополнять интерьер жилища. Лазерная резка металла становится инновационным и прогрессивным методом для нарезки и обработки материалов и с каждым днем набирает популярность. Произведенные таким образом предметы не будут иметь микротрещин и деформаций.
moiinstrumenty.ru