МГХ-К (Мастика Битумно-каучуковая). Цены, технические характеристики, сертификаты
Мастика Битумно-каучуковая МГХ-К – данная мастика холодного применения, т.е. продукт полностью готов к применению. МГХ-К это однородная смесь из таких составляющих как, нефтяной битум, резиновая крошка, каучук, растворители и природные смоляные кислоты. Такой состав позволяет мастике МГХ-К иметь эластичность в широком температурном интервале (-30С до +130С) в отличии от обычных битумных мастик. Есть и еще один плюс, мастика МГХ-К имеет высокий показатель относительного удлинения при разрыве. Это значит что мастичный слой из МГХ-К, прежде чем придет в негодность (например порвется) при усадке или подвижке знания или сооружения, будет растягиваться не нарушая своих гидроизоляционных свойств.
Мастику Битумно-каучуковую МГХ-К можно применять в качестве гидроизоляции различных конструкций, устройства мастичной кровли, приклеивания рулонной битумной гидроизоляции, также используют для ремонта кровельного покрытия и многого другого.
Мастику наносить на сухую, очищенную поверхность. Для лучшей адгезии, поверхность необходимо заранее обработать битумным праймером.
Технические характеристики:
Показатель | Значение |
Условная прочность, МПа (кгс/см2) | не менее 0,5 (5,0 кгс/см2) |
Жизнеспособность, час | не менее 0,5 часа |
Относительное удлинение при разрыве, % | не менее 300 |
Водопоглощение в течение 24 ч., % по массе | не более 0,5 |
Условная вязкость, секунд | не менее 15 |
Массовая доля нелетучих веществ, % | не менее 50 |
Прочность сцепления с бетоном, МПа (кгс/см2) | не менее 0,4 (4,0 кгс/см2) |
Температура размягчения, K (°С) | не ниже 403 (130°С) |
Гибкость на брусе с закруглением радиусом, мм, 5.![]() |
на поверхности образца не должно быть трещин |
Мастика битумно-резиновая (холодного применения) | Завод теплоизоляции АМАКС
Представляет собой однородную массу, состоящую из нефтяного битума, наполнителей и пластификаторов. Превосходит по качествам и удобству применения горячую кровельную мастику.
Изготавливается по ТУ 5775-001-86863093-2009
Свойства и характеристики:
- Защитные покрытия из мастики битумно-резиновой МБР “Альфа-Маст” обладают значительной адгезией по все обрабатываемой поверхности, механической прочностью и эластичностью.
- Гибкость и эластичность больше, чем у битумно-полимерной мастики.
- Сохраняет свои свойства при динамически меняющейся температуре окружающей среды от – 45 до + 65 С°.
- Фактический расход составляет 0,8-1,4 кг/мл при двухслойном нанесении, с толщиной слоя 1,5-2 мм.
- Применяется на предварительно обработанную поверхность.
Области применения:
- Защита строительных конструкций: кровли, фундаменты, подвалы, сваи и другие объекты углубленные в землю или постоянно контактирующие с влажной средой.
- Ремонт любых типов кровель с армированием, защита металических и других поверхностей, в том числе трубопроводов, металоконструкций, фундаментов, ванн бассейнов, санузлов, душевых комнат, кузовов автомобилей.
- Мастика битумно-резиновая МБР Альфа-Маст идеально совместима с любыми кровельными материалами, поэтому хорошо подходит для устройства мастичных и ремонта всех видов кровель, с рулонными материалами и без них.
- Может применятся как антикоррозийное и противошумное средство.
Нанесение мастики битумно-резиновой МБР Альфа-Маст:
- При необходимости, допускается разбавление мастики растворителями (толуолом, уайт-спиритом, бензином) до нужной консистенции, но не более 20% от массы мастики. При разбавлении свыше 20% ухудшаются технические характеристики гидроизоляционной пленки;
- Нанесение мастики производится при температуре окружающего воздуха не ниже -15С°, при больших отрицательных температурах продукт рекомендуется подогревать до +20 +25С°.
- При нанесении мастики основание очистить от грязи, оставшегося старого покрытия, рыхлой и пластовой ржавчины, пыли, наледи, инея, свободной воды. При необходимости обработать коррозийные участки преобразователем ржавчины.
- Наносить кистью, швабрилом, валиком или шпателем до 2-4 слоев, с межслойной сушкой 1час, последующий слой сушить 24-48 часов.
- Расход мастики 0,8-1,4 мл/м2 при двухмлойном нанесении с толщиной слоя 1,5-2 мм
Здесь Вы найдете Альбом технических решений на мастику АЛЬФА-МАСТ
Мастика выпускается в полиэтиленовых ведрах по 10 и 30 л, бочки 200 л. Температура хранения от -20 до +40 С°. Перевозится обычным автотранспортом, не требующим специального разрешения.
Заказывайте мастику битумно-резиновую АЛЬФА-МАСТ холодного применениня у менеджеров Группы компании АМАКС сегодня, и мы доставим её уже завтра на объект.
Битумная мастика для кровли как пользоваться?
Использование мастик для устройства кровель частных домов без рулонных материалов — сравнительно новая технология для нашей страны. Но она стремительно завоёвывает популярность благодаря новым материалам, позволяющим с минимальными затратами выполнять эту работу самостоятельно.
Мастика или битум: в чем отличие этих составов?
Для строительных работ сегодня применяются различные материалы, включая мастики и битум. Производители предлагают всевозможные варианты мастик, которые могут наноситься в холодном или горячем виде.
Битумная мастика используется в строительстве в основном для гидроизоляции. Ее наносят на поверхность только в горячем виде.
Своими руками для кровельных и прочих работ можно подготовить специальную битумную мастику, но наносится она только в горячем виде. Применение таких материалов во многом зависит от внешних и прочих условий, поэтому к выбору состава надо подходить серьезно.
Pgsnik › Блог › Рецепты антикора
Есть 2 основных типа антикора — мастичный и масляный.
Мастичный хорошо держится, защищает долговременно — на несколько лет, но для того, чтобы оно так и было, поверхтность нужно хорошо подготовить — зачистить до металла от старого покрытия, убрать остатки ржавчины преобразователем, просушить от влаги, особенно в углах, стыках, сварных швах. На старых машинах, где коррозия пробралась глубоко под предыдущее, обеспечить все эти условия весьма проблематично и придется немало потрудиться. Если же этого не сделать, слой новой мастики просто закроет сверху очаги коррозии вместе с влагой, и процесс будет продолжаться, только в скрытой форме.
Масляный антикор (он действительно на масляной основе) обладает гораздо большей проникающей способностью, сам в достаточной степени вытесняет влагу, содержит ингибиторы коррозии, не требует тщательной подготовки поверхтности — достаточно отодрать отслоившиеся ошметки старого покрытия. Но слой антикора не особо стойкий, рекомендуется обновлять покрытие по крайней мере раз в год. Следует обратить внимание, что есть состав для внутренних полостей и для днища. Так вот, при обработке днища сначала рекомендуется пролить составом для внутр. полостей — он проникает в мельчайшие щели, а уже затем через несколько часов — составом для днища, который, частично полимеризуясь, обеспечит более стойкую защиту от смывания.
Дальше просто разные рецепты которые были найдены на просторах нэта (без корректировок просто скопированные).
2 литра мовиля и 1литр солярки и дуй куда хочеш
можно битума с маслом наколотить
Кровельная мастика: герметик, виды, горячая, холодная, огнезащитный, гост, битумная, резиновая Мастика для кровли Мастика для крыш – виды, плюсы и минусы, инструкция правильного нанесения мастики пошагово, советы по выбору, видео — Стройматериалы Пирамида в Демихово Что такое кровельная мастика, правила нанесения кровельной мастики Мастика для кровли Кровля из мастики: технология нанесенияСрытые полости обрабатывал так — в мовиль добавлял нигрол приблизительно 5 к 1 и разбавлял уайт спиритом, днище — битумная мастика + отработка (3кг+0,5л) развел бензином (до жидкой сметаны) задул 3 слоя. 3 года мастика пластичная коррозии на металле нет
Вот такой бодягой скритие полости. Мовиль (2-3 банки) пушечное сало 1кг, отработка по вкусу. Задуваю кипятком.
по обработке скрытых полостей из моего личного опыта, состав: мовиль 2 части, нигрол 1 часть, пушечное сало 1 часть, все в емкость вариш до кипения, заливать в горячем виде, первый раз таким составом обработал машину лет пятнадцать назад, до сих пор ни где ржавчины нет, но обработку нужно производить в теплое время года неменее 20 градусов, конечно потрахкатся надо но игра стоит свеч. пушечное сало вчистом виде лить нельзя так как на морозе оно стает как кусок хозяйственного мыла.
я обычно покрываю днище и арки бодиевским гравитексом, на среднюю машину хватает 5-6 литровых банок, но тут одно но, нужно тщательно готовить обрабатываюмую поверхность, есть бюджетный вариант, тоже неплохо работает, береш две трехкилограмовые банки битумно-каучуковой мастики, сначало отмываеш поверхность водой проходиш щеткой по металлу, набираеш немного мастики разводиш в бензине чтобы она была жидкая как вода вобщем делаеш праймер, кисточкой наносиш на поверхность, после чего мастику бензином разводиш до консистенции гравитекса и пуликом для гравитекса наносиш, каждый слой нужно сушить, обычно я ложу в три слоя а там посвоему усмотрению, первый раз я этой гадостью воспользовался лет шесть назад прошлой осень смотрел днище этой машины, ничего все держится
Мой рецепт такой5л. солярки3кг. Пуш. сала2л. мовили присадки без разницыВ сервесах обходяца одной литровой бутылкой мовили проливая самые видные места и легко доступные крылья. короба, двери создавая впечатление полностью обработочной машины.
всем привет хочу поделиться хорошим рецептом антикорозийки, итак для основы нам нужно купить мастику резино-битумную, берем железную ненужную кастрюлу, ложим туда мастику и нагреваем ее горелкой или на костре, дальше добавляем автопластилин примерно на 3 кг мастики грамм 150-200 пластилина, потом берем пушечное сало примерно 200-300 грамм и все это дело кипитим до полного растворения всех компонентов, далее наносим в горячем виде на обробатываемую поверхность, можно разбавить мовилем или растворителем! Поверхность получается тостаточно толстой чтобы протевостоять гравию, зимой не трескается и находится в пластичном состоянии! вообщем отличная штука.
Битумная мастика холодного применения: для гидроизоляции и приклеивания- плюсы и минусы +
Эта статья поможет понять, что такое мастика битумная холодного применения. В чем заключается разница между холодной и горячей мастикой. Где ее используют. Как правильно выбрать материал по свойства и качествам, для требующихся работ.
Битум – это твердая смола, на его основе изготавливается мастика. Для того, чтобы материал стал пластичным его температуру повышают, что значительно увеличивает время работ и имеет явный недостаток – риск пожара.
По этой причине гораздо удобнее использовать мастику холодного применения. Благодаря растворителям присутствующим в составе, гидроизоляционный материал находится в жидком состоянии и для использования не требуется нагрев.
Горячую и холодную мастики используют для достижения полной гидроизоляции. Растворитель испаряется, материал застывает. Получается высокопрочный гидроизоляционный слой.
Первый вид
Изготавливается на основе растворителей. Это полностью готовые для работ смеси. Мастика, изготовленная на основе растворителя пригодна для использования при минусовой температуре.
Схватывается данный вид гидроизоляции в течение 24 часов. Полное затведевание мастики и приобретение свойств гидроизоляции, требует данный вид материала применяют в кровельных работах.
Второй вид битумного гидроизоляционного покрытия
Изготавливают на водной основе – что характеризует материал, как не несущий вреда не имеет резкого запаха, высыхает за пару часов.
Гидроизоляцию изготовленную на водной основе нельзя применять при пониженной температуре. Хранить материал также стоит в теплом помещении.
Битумная мастики имеет разные модификации
Рассмотрим их.
Немодифицированная гидроизоляция. Состав не содержит полимеров и иных компонентов, повышающих свойства материала. Для крыш это вид не подойдет, для фундамента идеальный вариант. Гидроизоляция примененная для фундамента не испытывает атмосферных перегрузок.
Мастику без полимеров применять для кровельных работ не рекомендуется.
Битумно-полимерная мастика. Из названия материала понятно, что этому виду гидроизоляции присущи высокие показатели.
Прекрасно адаптирован к большому диапазону температуры.
Очень хорошая молекулярная связка (адгезия), что позволяет применять мастику для приклеивания рубероида и аналогичных материалов.
Битумно–полимерная мастика благодаря своим качествам, обширно применяется для покрытия плоских крыш.
Битумно–резиновая мастика. В составе присутствует крошка из резины. Обладает достойными антикоррозийным свойством. Применяют для покрытия конструкций из металла.
Для кровельных работ битумно – резиновая мастика НЕ подходит.
Битумно–каучуковая гидроизоляция, она же жидкая резина — очень эластичная с высокими физико – механическими показателями. Данные качества увеличивают износостойкость покрытия. Прекрасно подходит для покрытия крыши.
Каучуковая мастика способна стать самостоятельным кровельным покрытием. Практически не подвержена, атмосферному влиянию.
Тип мастики напрямую связан с содержащимися в ней компонентами.
Однокомпонентная – готовое к работе покрытие.
Двухкомпонентная мастика перед началом работ требует смешивания с отвердителем. Используется в профессиональных целях. Обладает хорошими показателями.
При использовании двухкомпонентной мастики ВАЖНО точно следовать инструкции по смешиванию. Не правильные пропорции приведут к увеличению срока застывания.
Основные достоинства битумной мастики холодного применения
- Сокращает время работ по гидроизоляции
- Мастику можно развести растворителем, что сделает ее нужной консистенции
- Срок эксплуатации более 25 лет
- Покрытие можно применять на поверхностях из разного материала
- Легкое нанесение.
- Самостоятельное использование
Минусы данного материала
- Высокая стоимость.
- Битумно – полимерная мастика дает большую усадку, что сказывается на расходе материала.
Применение
- Кровельные работы. Применяют для ремонта кровельного покрытия, для монтажа черепицы(мягкой), для связки с рулонными материалами.
- Для гидроизоляционной обработки фундамента. Покрытие делается, как на ленточном фундаменте, так и на свайном.
- Битумный материал используют, как гидроизоляцию под стяжку.
Прекрасно подходит для полов в ванной, подвале, гараже.
- При сооружении бассейнов и террас. В этих случаях для работ применяют резиновую мастику.
Битумная мастика холодного применения расход материала:
- Для склеивания 0,8 – 1 кг на квадратный метр
- Для гидроизоляционного слоя 2 – 3,8 кг на квадратный метр
На рынке лидируют два производителя:
- Мастика битумная ТЕХНОНИКОЛЬ
- Битумная мастика ЭКСПЕРТ
Оба производителя отвечают всем требованиям. Возможна разница в стоимости. И некоторых нюансах, таких как расход материала и время высыхания.
Важно помнить. Перед применением мастики необходимо очистить поверхность от мусора, грязи. Обрабатываемая площадь обязательно должна быть сухой. Если поверхность пористая ее необходимо предварительно обработать праймером.
Основные достоинства
Мастика имеет широкий спрос как строительный материал, вследствие своих свойств:
- Большие характеристики гидроизоляции.
- Надежно скрывает трещины, сглаживает плоскости.
- Противостоит образованию, распространению грибковых, плесневых образований.
- Высокая сцепливаемость с любой плоскостью.
- Структура не разрушается при воздействии прямого солнечного излучения.
- Выдерживает морозы, при этом структура сохраняет свои свойства (благодаря повышенной эластичности).
- Легкость в использовании.
- Характерная вязкость дает возможность равномерно нанести слой.
- Долгий период эксплуатации (до 25 лет).
- Доступность, низкая цена.
Недостатками можно назвать неиспользование материала в дождливую погоду, на неровности уходит больше сырья.
Особенности разбавления
Степень густоты разведения мастики определяется методом её нанесения:
- Вручную.
- Распылителем.
В первом случае применяется кисть или валик, во втором – специальный краскопульт или пульверизатор. Естественно, что для приготовления раствора, наносимого вручную, нет необходимости добиваться точности достижения жидкости требуемой степени текучести. Другое дело – применение распыляющего оборудования. Здесь подвижность разбавленной смеси должна иметь точно требуемое значение. В противном случае оно просто не будет функционировать.
Распыление мастики пульверизатором
Размазывание битумной мастики ручным методом подходит для обработки незначительной по площади поверхности, краскопультом – для большой территории и трудно доступных мест. При решении вопроса, как и чем развести битумную мастику для кровли, всегда должна учитываться технология нанесения. Для машинного способа необходимо подбирать компоненты, создающие мелкодисперсный раствор. Лучше всего применять растворитель, рекомендуемый самим производителем мастики.
Подготовка основания и нанесение праймера
Наносить готовую, разбавленную до нужной консистенции мастику можно только на предварительно подготовленную поверхность. Этапы технологии выглядят следующим образом:
- На поверхности устраняются дефекты – неровности, отслоения, трещины, пробоины.
- При необходимости изъяны залатываются, шпаклюются, бетонируются.
- Поверхность очищается и высушивается.
- Затем покрывается равномерным слоем грунта.
Битумный праймер
Грунтовка выполняется праймером. В его состав входят твёрдые фракции битумов. Поэтому перед нанесением раствор расплавляют. Пример технологии приготовления популярного варианта праймера состоит из следующих этапов:
- Твёрдый битум разрубается на небольшие куски.
- Далее они помещаются в ёмкость с заранее разогретым растворителем.
- При постоянном перемешивании смесь разогревается до температуры, не превышающей 200 °C.
- После полного растворения средство равномерно распределяют по поверхности.
- 10 литров готового праймера, как правило, достаточно для обработки 5-10 м²поверхности.
Выбор мастики для кровли разного уклона
При плоской кровле (уклоне не более 2,5%) монтаж осуществляется с минимальными трудозатратами. Армирование в этом случае не используют, потому как горячая мастика равномерно распределяется по поверхности.
Уклон от 2,5 до 10% будет усложнять процесс монтажа горячей мастики. Лучше использовать армирующие материалы, чтобы избежать стекания мастики до полного затвердевания.
При уклоне в 10-15% используют двойное армирование с посыпкой минеральными веществами. Причём и мастику наносят в 2 слоя.
Для уклона 15-25% мастику укладывают в 3 слоя, обеспечивая двойное армирование. Сверху — защитное покрытие в виде покраски.
При уклоне более 25% использование рулонных или мастичных материалов не рекомендовано.
Инверсионная кровля
Более длительный период эксплуатации заставляет многих застройщиков использовать этот метод. Стоит отметить, что предыдущий вид является далеко не совершенным и такие кровли начинают течь уже через несколько лет, хотя этого внешне и не видно. Если рассматривать инверсионную крышу с этой же стороны, то она не протечет даже через десятилетие.
Заглянув в разрез данной кровли можно сразу увидеть отличия. Дело в том, что здесь поменялись местами некоторые слои. Именно благодаря этому трюку инверсионная кровля выигрывает во всем. Помимо высоких показателей ее можно монтировать на уже эксплуатируемое здание. Для этого достаточно убрать несколько слоев старой крыши и уложить изоляцию в нужное место, а затем закрыть пирог в нужной последовательности.
За счет расположения слоев инверсионная кровля может быть эксплуатируемой. Как уже говорилось ранее, на ней можно оборудовать что-то типа мастерской или разместить лужайку с садом. В наши дни озеленение играет важную роль в жизни человека.
Данная кровля обладает своими подвидами. Деление происходит в зависимости от величины нагрузки.
- Если на крышу действует минимальное давление, то ее структура будет включать ли стандартный кровельный пирог: пароизоляционный слой, теплоизоляционные плиты и гидроизоляция. В качестве примера можно привести летнюю площадку
- В случае размещении на кровельной плоскости более серьезных весов стоит прибегнуть к укладке толстых и более прочных теплоизоляционных продуктов.
Завершающие покрытие таких крыш украшают тротуарными плитками или другие продукты с идентичными защитными качествами
- Когда вы планируете организовывать банкеты прямо у себя на крыше или хотите разместить на ней бассейн, то эти нагрузки называются высокими. Структура данного подвида будет содержать в себе укрепляющие материалы, расположенные промеж основных. Крыша будет готова, после укладки завершающего элемента – железобетонной плиты
Поняв в чем положительные стороны инверсионной кровли, наверняка, вам захотелось здание именно с такой крышей.
Создание инверсионной кровли
До начала строительства в зависимости от ваших потребностей сперва стоит определиться с будущими нагрузками, ведь от них будет зависеть вся структура будущей крыши.
- Сначала, как и везде, приступают к подготовительным работам. Начало работ требует прогрунтовать основание специальными растворами. Это делается для лучшей адгезии наплавляемого материала с поверхностью
- После подготовки укладывается слой гидроизоляционного материала.
Стоит отметить, что сперва укладывается водонепроницаемый материал, как правило, это ПВХ мембрана. На данном этапе уже можно отметить существенно отличающуюся от традиционных методов укладку
- Укладка теплоизоляции. Для инверсионных кровель идеальным вариантом материала является геотекстиль. Он укладывается промеж внутренней изоляцией и завершающим покрытием
- В качестве наружного слоя может применяться множество продуктов. Подбор необходимого материала производится исходя от функционального назначения крыши. Если вы не планируете размещать на ней массивное оборудование, то им может быть любые рулонные покрытия. При средней нагрузке необходимо укладывать тротуарную плитку и более качественные материалы. Что касается самых больших показателей прочности, то они достигаются путем укрепления каждого слоя геотекстилем, а сверху весь пирог накрывают железобетонной плитой
Обустраивать слишком сложную кровлю, выдерживающую колоссальные нагрузки и затем не пользоваться ей по назначению – нецелесообразно. Перед строительством обсудите этот вопрос со своими членами семьи или знакомыми.
Сроки выполнения работ
Услуга | Крыша площадью до 50 кв. м. | Кровля площадью более 50 кв. м. |
Установка опор для стропил | 1-2 дня | 2-3 дня |
Строительство стропильной системы | 4-6 дней | 4-8 дней |
Возведение шаговой обрешетки | 4-6 дней | 6-8 дней |
Строительство контробрешетки | 4-6 дней | 6-8 дней |
Монтаж финишного покрытия | 3-4 дней | 4-5 дней |
Любое здание немыслимо без крыши. Она является той преградой, которая защищает внутренние помещения от атмосферных осадков и препятствует утечке тепла. То, насколько комфортным будет проживание в доме, во многом зависит от монолитности кровли. Раньше, в целях создания герметичности крыши, использовали глину и листовое железо. Эти способы были не слишком долговечны, и крыше требовался регулярный ремонт. С развитием строительной отрасли и изобретением новых материалов ситуация изменилась. Появилась новая технология .
Для создания надежной гидроизоляции крыши, обычно используют наплавляемые рулонные материалы.
СПЕЦИФИКАЦИЯ ДЛЯ КУРСОВ ИЗНОСА БИТУМНОЙ МАСТИКИ
СПЕЦИФИКАЦИЯ ДЛЯ КУРСОВ ИЗНОСА БИТУМНОЙ МАСТИКИПРЕАМБУЛА (НЕ ЧАСТЬ СТАНДАРТА)
Эта библиотека книг, аудио, видео и других материалов из Индии и об Индии курируется и поддерживается Public Resource. Цель этой библиотеки – помочь студентам и ученикам Индии, которые учатся на протяжении всей жизни, в их стремлении к образованию, чтобы они могли улучшить свой статус и свои возможности, а также обеспечить для себя и других справедливость, социальную, экономическую и политическую.
Этот элемент был размещен в некоммерческих целях и способствует добросовестному использованию академических и исследовательских материалов для личного использования, включая исследования, для критики и обзора работы или других работ, а также воспроизведения преподавателями и студентами в процессе обучения. . Многие из этих материалов либо недоступны, либо недоступны в библиотеках Индии, особенно в некоторых из более бедных штатов, и эта коллекция призвана заполнить серьезный пробел, существующий в доступе к знаниям.
Чтобы узнать о других коллекциях, которые мы курируем, и получить дополнительную информацию, посетите страницу Бхарат Эк Ходж. Джай Гьян!
КОНЕЦ ПРЕАМБУЛЫ (НЕ ЧАСТЬ СТАНДАРТА)
IRC: 107-2013
(первая редакция)
Опубликовано:
ИНДИЙСКИЙ ДОРОЖНЫЙ КОНГРЕСС
Кама Коти Марг,
Сектор-6, Р.К. Пурам,
Нью-Дели-110 022
Ноябрь 2013 г.
Цена: 200 ₹ / –
(плюс упаковка и почтовые расходы)
ПЕРСОНАЛ КОМИТЕТА ПО СПЕЦИФИКАЦИЯМ И СТАНДАРТАМ МАГИСТРАЛЬНЫХ ДОРОГ
(По состоянию на 19 -го июля 2013 г.)
1. | Kandasamy, C. (руководитель) | Генеральный директор (RD) & Spl.![]() |
2. | Патанкар, В.Л. (содокладчик) | Доп. Генеральный директор, Министерство автомобильного транспорта и автомобильных дорог, Транспорт Бхаван, Нью-Дели |
3. | Кумар, Манодж (член-секретарь) | Главный инженер (R) S, R&T, Министерство автомобильного транспорта и шоссейных дорог, Транспорт Бхаван, Нью-Дели |
Участники | ||
4. | Басу, С. | Главный инженер (в отставке) МОРТ, Нью-Дели |
5 . | Bongirwar, P.L. | Советник, L&T, Мумбаи |
6. | Бозе, д-р Сунил | Головка ФПК Дивн. CRRI (в отставке), Фаридабад |
7. | Духсака, Ванлал | Главный инженер, PWD (шоссе), Айзвал (Мизорам) |
8.![]() | Гангопадхьяй, д-р С. | Директор, Центральный научно-исследовательский институт дорог, Нью-Дели |
9. | Гупта, Д.П. | DG (RD) & AS (Retd.), MORTH, Нью-Дели |
10. | Джайн, Р.К. | Главный инженер (в отставке) Харьяна PWD, Sonipat |
11. | Джайн, Н.С. | Главный инженер (в отставке), МОРТ, Нью-Дели |
12. | Джайн, доктор С.С. | Профессор и координатор, Центр транспорта Engg., IIT Roorkee, Roorkee |
13. | Кадияли, д-р Л. | Главный исполнительный директор L.R. Kadiyali & Associates, Нью-Дели |
14. | Кумар, Ашок | Главный инженер, (в отставке), МОРТ, Нью-Дели |
15. | Куриан, Хосе | Главный инженер, DTTDC Ltd., Нью-Дели |
16. | Кумар, Махеш | Главный инженер, Haryana PWD, Чандигарх |
17, | Кумар, Сатандер | Бывший ученый, CRRI, Нью-Дели |
18.![]() | Лай, Чаман | Главный инженер, Совет по сельскохозяйственному маркетингу штата Харьяна, Чандигарх |
19. | Манчанда, Р.К. | Консультант, Intercontinental Consultants and Technocrats Pvt.Ltd., Нью-Дели. |
20. | Marwah, S.K. | Доп. Генеральный директор (в отставке), МОРТ, Нью-Дели, |
21. | Pandey, R.K. | Главный инженер (планирование), МОРТ, Нью-Дели |
22. | Патерия, д-р И.К. | Директор (технический), Департамент национальных сельских дорог. Агентство, (Мин. Сельского департамента), Нью-Дели, |
23. | Прадхан, до н.э. | Главный инженер, Национальные шоссе, Бхубанешвар |
24. | Prasad, D.N. | Главный инженер, (NH), RCD, Патна |
25. | Рао, П.Дж. | Инженер-консультант, H.![]() |
26. | Редди, К. Сива | Главный инженер (R&B) адм., Дорожно-строительный департамент.Хайдарабад |
27. | Представитель BRO | (Шри Б.Б. Лал), кафедра. DG, HQ DGBR, Нью-Дели |
28. | Саркар, д-р П.К. | Профессор, кафедра. транспортного планирования, Школа планирования и архитектуры, Нью-Дели |
29. | Шарма, Арун Кумар | Генеральный директор (шоссе), GMR Highways Limited, Бангалор |
30. | Шарма, М. | Член (технический), Национальное управление автомобильных дорог Индии, Нью-Дели |
31. | Шарма, Южная Каролина | DG (RD) & AS (Retd.), MORTH, Нью-Дели |
32. | Синха, А.В. | DG (RD) & SS (Retd.) MORTH Нью-Дели |
33. | Сингх, Б.Н. | Член (проекты), Национальное управление автомобильных дорог Индии, Нью-Дели |
34.![]() | Сингх, Нирмал Джит | DG (RD) & SS (Retd.), MORTH, Нью-Дели |
35. | Васава, С. | Главный инженер и доп. Секретарь (Панчаят) Департамент дорог и строительства, Гандинагар |
36. | Ядав, д-р В.К. | Доп. Генеральный директор, DGBR, Нью-Дели |
Члены-корреспонденты | ||
1. | Бхаттачарья, C.C. | DG (RD) & AS (Retd.) MORTH, Нью-Дели |
2. | Дас, доктор Анимеш | Доцент, ИИТ, Канпур |
3. | Хусто, доктор C.E.G. | 334, 14 th Main, 25 th Cross, Banashankari 2 nd Stage, Bangalore-560 070. |
4. | Момин, С.С. | (бывший президент, IRC) 604 A, Israni Tower, Mumbai |
5. | Панди, проф. Б. Б. | Советник, ИИТ Харагпур, Харагпур |
Бывшие члены | ||
1.![]() | Кандасами, C. | Генеральный директор (дорожное строительство) и специальный секретарь, MORTH и президент IRC, Нью-Дели |
2. | Прасад, Вишну Шанкар | Генеральный секретарь Индийского автомобильного конгресса, Нью-Дели |
ТЕХНИЧЕСКИЕ ХАРАКТЕРИСТИКИ КУРСОВ ИЗНОСА БИТУМНОЙ МАСТИКИ
1 ВВЕДЕНИЕ
Индийский автодорожный конгресс опубликовал Предварительные технические условия для курсов по износостойкости битумной мастики в 1992 году.Этот документ служил профессии более двух десятилетий. Тем не менее, тем временем произошли технологические разработки в области проектирования, строительства и управления процессом износа битумной мастики. Комитет по гибкому дорожному покрытию (H-2) счел необходимым пересмотреть документ. Соответственно, была образована подгруппа под председательством доктора Сунила Боса, в которую вошли Шри Б.Р. Тьяги, Шри Р.С. Шукла, Шри Р.К. Панди и Шри С. К. Нирмал как его члены для пересмотра IRC: 107-1992.Проект документа, подготовленный подгруппой, обсуждался Комитетом на нескольких заседаниях. Комитет H-2, наконец, утвердил проект документа на своем заседании, состоявшемся 17 -го июня 2013 года. Комитет HSS одобрил проект документа на своем заседании, состоявшемся 19 -го июля 2013 года. Собрание , состоявшееся в Нью-Дели 11 -го и 12 -го августа 2013 года, одобрило проект пересмотренной версии IRC: 107 «Спецификация курсов ношения битумной мастики» после принятия во внимание комментариев, предложенных членами.
Состав комитета H-2 приведен ниже:
А.В. Синха | ——– | Конвертер | |
Д-р Сунил Бозе | ——– | Сопредседатель | |
S.K. Нирмал | ——– | Член Секретарь | |
Участники | |||
Арун Кумар Шарма | К.![]() | ||
Б.Р. Тяги | Н.С. Джайн | ||
B.S. Сингла | P.L. Бонгирвар | ||
Чаман Лал | Прабхат Кришна | ||
Чандан Басу | R.K. Джайн | ||
Col. R..S. Бханвала | R.K. Панди | ||
D.K. Пачаури | Раджеш Кумар Джайн | ||
Др.Animesh Das | Представитель ГД (Бразилия) (бригадир Р.С. Шарма) | ||
Д-р Б. Б. Пандей | Представитель IOC Ltd (д-р А.А.Гупта) | ||
Доктор К. Судхакар Редди | Представитель NRRDA (д-р И.К. Патерия) | ||
Доктор П.К. Джайн | С.Б. Basu | ||
Доктор Раджив Маллик | S.![]() | ||
Доктор С.С. Джайн | Ванлал Духсака | ||
Члены-корреспонденты | |||
С.Ч. Бхаттачарья | Проф. А. Веерарагаван | ||
Доктор C.E.G Justo | Проф. Притхви Сингх Кандхал | ||
Доктор С.С. Сехра | Шри Бидур Кант Джа | ||
Шри Сатандер Кумар1 | |||
Бывшие члены | |||
Шри К. Кандасами | Генеральный директор (развитие дорог) и специальный секретарь, MORTH и президент, IRC | ||
Шри Вишну Шанкар Прасад | Генеральный секретарь, IRC |
2 ОБЛАСТЬ ПРИМЕНЕНИЯ
Этот стандарт охватывает основные принципы проектирования, изготовления и контроля, необходимые для нанесения слоя битумной мастики. Этот документ не относится к тонкому слою мастики на настилах мостов под слоем битумного бетона.
Битумная мастика состоит из минерального наполнителя подходящего сорта и крупных заполнителей, мелких заполнителей и твердого битума для образования когерентной, непроницаемой, непроницаемой массы, твердой или полутвердой при нормальных температурных условиях, но достаточно текучей при нагревании. подходящая температура для распределения с помощью поплавка при ручном строительстве и асфальтоукладчика при механизированном строительстве.
Использование этого материала в его нынешней формулировке не рекомендуется в местах, где ожидается обильное капание мазута на поверхность тротуара, например, автобусные депо, автозаправочные станции и станции технического обслуживания и т. Д.
3 МАТЕРИАЛЫ
3,1 Битум
3.1.1
Битум для мастичного асфальта должен быть битумом промышленного класса 85/25, отвечающим требованиям, приведенным в таблице 1 .
С.№ | Характеристика | Требование | Метод испытания |
---|---|---|---|
1) | Пенетрация при 25 ° C в 1/100 см | от 20 до 40 | IS: 1203-1978 |
2) | Температура размягчения (метод кольца и шара) | 80-90 ° С | IS: 1205-1978 |
3) | Пластичность при 27 ° C, не менее, см | 3 | IS: 1208-1978 |
4) | Потеря тепла, процент, (максимальная) | 1 | IS: 1212-1978 |
5) | Растворимость в трихлорэтилене, процент (минимум) | 99 | IS: 1216-1978 |
3.1,2
Для мастичного асфальта на больших высотах (2000 м) следует использовать связующее класса VG 40, соответствующее IS: 73.
3,2 Крупный заполнитель
Крупнозернистый заполнитель должен состоять из чистой, твердой, прочной, дробленой породы, не содержащей дезинтегрированных кусков, органических и других вредных веществ и прилипающих покрытий, оставшихся на сите 2,36 мм. Они должны быть гидрофобными, иметь низкую пористость и удовлетворять физическим требованиям, изложенным в таблице 2 . 2
С.№ | Тест | Допустимое (максимум в процентах) | Метод испытаний |
---|---|---|---|
1) | Значение абразивного износа по Лос-Анджелесу или | 30 | IS: 2386 (Часть IV) |
Суммарная величина воздействия | 24 | -do- | |
2) | Комбинированный индекс относительного удлинения при шелушении | 35 | IS: 2386 (Часть 1) |
3) | Значение зачистки | 5 | IS: 6241 |
4) | Прочность i) Потери из-за сульфата натрия 5 циклов | 12 | IS: 2386 (Часть V) |
ii) Потери из-за сульфата магния 5 циклов | 18 | -do- | |
5) | Водопоглощение | 2 | IS: 2386 (Часть III) |
Классификация грубых заполнителей битумной мастики в зависимости от толщины готового слоя должна соответствовать , таблица 3. Минимальная и максимальная толщина битумной мастики для покрытия износа должна составлять 25 мм и 50 мм соответственно, за исключением пешеходных дорожек мостов, где она должна составлять 20 мм и 25 мм соответственно.
S. No. | Вид работ | Сортировка грубых заполнителей | Толщина готового профиля мм | Процент грубых заполнителей | |
---|---|---|---|---|---|
IS Сито | Процент проходящего сита IS | ||||
1) | Покрытие для покрытия дорожного покрытия и настилов мостов | 19 мм | 100 | а) 25-40 | а) 30-40 |
13.2 мм | 88-96 | или | или | ||
2,36 мм | 0-5 | б) 41-50 | б) 40-50 | ||
2) | Пешеходные дорожки | 6,3 мм | 100 | 20-25 | 15-30 |
2,36 мм | 70-85 |
3.

Мелкие заполнители должны состоять из измельченной твердой породы или природного песка или смеси обоих, прошедших сито 2,36 мм и удерживаемых на сите 0,075 мм. Классификация мелких заполнителей, включая присадочный материал толщиной 0,075 мм, должна быть такой, как указано в таблице 4 .
3.4 Наполнитель
Наполнитель должен быть порошком известняка толщиной 0,075 мм и иметь содержание карбоната кальция не менее 80 процентов по массе при определении в соответствии с IS: 1514.3
Проходящее сито IS | Остается на сите IS | Весовые проценты |
---|---|---|
2,36 мм | 600 мкм | 0-25 |
600 мкм | 212 мкм | 5-25 |
212 мкм | 75 мкм | 10-20 |
75 мкм | – | 30-50 |
ДИЗАЙН 4 МИКСОВ
4.

Число твердости битумной мастики должно определяться при 25 ° C в соответствии с методом, указанным в Приложении-D IS: 1195-1978. Он должен соответствовать следующим требованиям:
- Без крупных заполнителей при 25 ° C 30-60
- С крупными заполнителями при 25 ° C 10-20
4,2 Содержание связующего
Содержание связующего должно быть таким фиксированным, чтобы соответствовать требованиям к смеси, указанным в пункте 4.1 . Содержание связующего и градация должны соответствовать Таблице 5.
IS Сито | Массовые проценты | ||
---|---|---|---|
Переходный | Оставлено | Минимум | Максимум |
2.36 мм | 600 мкм | 0 | 22 |
600 мкм | 212 мкм | 4 | 30 |
212 мкм | 75 мкм | 8 | 18 |
75 мкм | – | 25 | 45 |
Содержание битума | 14 | 17 |
5 ОБОРУДОВАНИЕ ДЛЯ БИТУМНОЙ МАСТИКИ
Битумную мастику можно приготовить двумя способами. Обычный метод – использовать мастику. Другой метод – использование полностью механизированных агрегатов для крупномасштабных работ. Подробная информация об оборудовании, требуемом для этих двух методов, доступна в Приложении -I и II.
6 ЭКСПЛУАТАЦИЯ СТРОИТЕЛЬСТВА
6.1 Производство битумной мастики
6.1.1
Производство битумной мастики включает несколько этапов. Первоначально только наполнитель нагревается до температуры от 170 ° C до 200 ° C в мастике с механическим перемешиванием4
и добавлено половину необходимого количества битума, нагретого до 170–180 ° C.Их нужно перемешать и варить в течение часа. Затем мелкие заполнители и балансный битум (от 170 ° C до 180 ° C) должны быть добавлены к этой смеси в варочном котле и нагреты до 170 ° C до 200 ° C, а затем перемешаны в течение еще одного часа. На заключительном этапе необходимо добавить грубые заполнители и нагреть смесь еще в течение часа. Таким образом, на приготовление мастики потребуется не менее трех часов. Во время смешивания и варки необходимо следить за тем, чтобы содержимое ни в коем случае не нагревалось до температуры, превышающей 200 ° C.
6.1.2
В случае, если материал не требуется для немедленного использования, битумная мастика с наполнителем, мелкими заполнителями и битумом должна быть отлита в блоки весом около 25 кг каждый. Блоки битумной мастики (без крупных заполнителей) должны показать при анализе состав с пределами, указанными в Таблице 5. Эти блоки, если они предназначены для последующего использования, должны транспортироваться на площадку, разбитые на куски размером не более 60 мм куб. и переплавляют в варочном котле при температуре от 170 ° C до 200 ° C, тщательно добавляя необходимое количество крупных агрегатов, как указано в , таблица 3 , и непрерывно перемешивают в течение одного часа.Перемешивание должно продолжаться до тех пор, пока не будут завершены операции по укладке, чтобы крупные заполнители оставались во взвешенном состоянии. На любой стадии температура в процессе смешивания не должна превышать 200 ° C.
6.2 Укладка битумной мастики
6.2.1
Подготовка основания Основание, на которое следует укладывать битумную мастику, должно быть подготовлено, сформировано и кондиционировано до заданных уровней, сорта и выпуклости в соответствии с указаниями. Если существующая поверхность слишком неровная и волнистая, она должна быть заделана трещинами, заделана выбоина, а затем улучшена путем внесения корректирующих действий путем использования битумно-бетонной смеси или плотного битумного щебня в соответствии с IRC: 111.Поверхность должна высохнуть до того, как на нее будет нанесен слой мастики. Если поверхность мокрая, ее следует просушить паяльной лампой, прежде чем продолжить строительство. Поверхность должна быть тщательно вымыта и очищена от пыли и других вредных веществ. Пятна с высоким содержанием вяжущего подлежат утилизации и ремонту. Битумную мастику ни в коем случае нельзя наносить на основу, содержащую связующее, которое размягчается при высокой температуре нанесения. Если такое место или область существует, то перед укладкой битумной мастики их необходимо вырезать и отремонтировать.Для приема и удержания мастики уголки размером 25 или 50 мм размещаются на необходимом расстоянии до конца работы.
На бетонную поверхность (как старую, так и новую) прихватку наносить прямогонным битумом марки ВГ 10. Количество связующего слоя должно соответствовать IRC: 16. На бетонной поверхности следует также принять некоторые дополнительные меры против образования пузырей, например, нагреть поверхность паяльной лампой. Если асфальтовая мастика накладывается на свежий битумный слой (в качестве корректирующего слоя), нет необходимости в нанесении связующего слоя.
6.2.2
Транспортировка смесиКогда битумная мастика, должным образом приготовленная с добавлением грубых заполнителей на месте производства, должна транспортироваться на большие расстояния и доставлена на кладку5
, меры по его транспортировке должны быть выполнены в транспортном средстве с буксируемой мешалкой с надлежащими условиями для нагрева и перемешивания, чтобы заполнители и наполнитель оставались взвешенными в смеси до момента укладки. Однако для небольших работ и там, где место укладки находится рядом с местом производства, смесь можно транспортировать в тачках / плоских баках для раствора, чтобы предотвратить прилипание расплавленного материала к тачкам / лоткам, внутренняя часть транспортера может быть разбрызгана. с минимальным количеством мелкодисперсных неорганических материалов, таких как известь, каменная пыль. Однако цементную золу или масло использовать нельзя.
6.2.3
Укладка смеси6.2.3.1
Битумная мастика должна сливаться в емкости, посыпанные известью, каменной пылью или промытые известью.Битумную мастику наносят непосредственно на подготовленное основание непосредственно перед разбрасывателем, где ее равномерно распределяют деревянными терками до необходимой толщины. Смесь должна быть уложена шириной 1 м между стандартным уголком размером от 25 до 50 мм для размещения и содержания мастики необходимой толщины. Температура смеси при укладке 170 ° C. Если при укладке битумной мастики происходит выдувание, пузыри следует проткнуть, пока мастика горячая, а поверхность выпрямляется. Поскольку битумная мастика является дорогостоящим материалом, при установке уголка следует проявлять особую осторожность и проверять их уровень с помощью инструмента через подходящие промежутки времени.
6.2.4
Укладка битумно-мастичного покрытия поверх существующего настила мостаПеред укладкой битумной мастики поверх существующего настила моста поперечный уклон / выпуклость, компенсаторы и водосточные желоба должны быть тщательно проверены на предмет их надлежащего функционирования в конструкции настила моста, и любые обнаруженные недостатки должны быть сначала устранены.Незакрепленные элементы в компенсаторе должны быть надежно закреплены. Трещины в бетонной поверхности, если таковые имеются, должны быть отремонтированы и заделаны должным образом или заменены новым бетоном указанной марки перед укладкой битумной мастики на настил моста.
6.2.5
Укладка битумной мастики поверх нового настила моста Новому бетонному настилу моста, не имеющему достаточного изгиба / перекрестия, сначала необходимо обеспечить требуемый изгиб и перекресток с помощью подходящей бетонной или битумной обработки. При укладке битумной мастики на бетонную поверхность необходимо принять следующие меры:
- Для надлежащего сцепления с новым бетонным настилом поверхность должна быть придана шероховатости с помощью жесткой щетки / металлической щетки или фрезерного станка и очищена от выступов и впадин с помощью сжатого воздуха. №
- Перед заливкой битумной мастики на бетонный настил необходимо нанести битумную связку с битумом марки ВГ 10. Количество битума для связующего слоя должно соответствовать IRC: 16.
- После нанесения связующего слоя арматуру куриной сетки из стальной проволоки 22 калибра (0,76 мм) с шестигранными или прямоугольными отверстиями от 20 до 25 мм следует разместить продольно и удерживать на бетонной поверхности перед укладкой битумной мастики.6
6.3 Соединения
Все стыки конструкции должны быть правильно сварены без неровностей. Эти швы должны быть выполнены путем нагревания существующей битумной мастики путем нанесения избыточного количества горячей битумной мастики, которая затем должна быть обрезана, чтобы она была заподлицо с поверхностью на другой стороне.
Стыки должны быть окрашены слоем битума марки VG 30, затем обработаны блоками основной мастики (без крупных заполнителей, которые содержат больше битума), а затем размягчены паяльными лампами и протерты салфеткой до поверхности. Следует следить за тем, чтобы мастичные материалы на расплавленной основе проникали до низа лицевой стороны швов. Это будет облегчено, если вертикальной поверхности стыка будет придана Y-образная форма.
Следует позаботиться о том, чтобы швы были выполнены как можно более экологически чистыми, в противном случае уложенная поверхность из мастичного асфальта начнет стареть / окисляться, и это еще больше усугубит дорожное движение, что приведет к проблеме надлежащего склеивания в течение нескольких дней между старая мастиковая поверхность и свежеуложенная мастиковая поверхность.
6.4 Прививка чипсов
Для ручной укладки битумно-мастичное покрытие имеет очень мелкую текстуру, которая при укладке обеспечивает очень небольшое сопротивление скольжению. Следовательно, битумная мастика, пока она еще горячая и в пластичном состоянии, должна быть покрыта предварительно покрытой битумом мелкозернистой твердой каменной крошкой / агрегатами утвержденного качества размером от 9,5 мм до 13,2 мм, в зависимости от толщины мастики, с использованием битума от 2 до 3%. марки ВГ 30 и агрегата 0,05 куб. за 10 кв.м (5.4 – 8,1 кг на кв.м) и вдавливается в поверхность при температуре битумной мастики от 80 ° C до 100 ° C. Такие заполнители с предварительным покрытием при укладке должны выступать на 3–4 мм над мастичной поверхностью. Индекс шелушения каменных агрегатов, используемых для противоскольжения, должен быть менее 25 процентов.
Движение разрешено после завершения работ, когда битумная мастика остыла до температуры окружающей среды.
7 ОРГАНОВ УПРАВЛЕНИЯ
7.1 Органы управления
7.1,1
Ситовой анализ каждого типа используемого заполнителя должен проводиться не реже одного раза в день, чтобы убедиться, что градация агрегатов соответствует первоначальной градации, как было утверждено. Дополнительные испытания должны проводиться в случае изменения классификации или поступления новой поставки материала. Количество образцов, подлежащих испытанию в день, будет зависеть от объема поставок заполнителей, производимых за день на производственной площадке. Физические свойства, такие как ударная вязкость, индекс шелушения, водопоглощение и т. Д., должно быть определено при 1 испытании на каждые 50 кумов агрегатов или в соответствии с указаниями инженера на месте.
7.1.2
Для каждой партии битума необходимо провести два набора испытаний для проверки пенетрации и точки размягчения в соответствии с IS: 1203-1978 и IS: 1205-1978.7
7.1.3
Для наполнителя содержание карбоната кальция и его тонкость должны проверяться из расчета одного набора испытаний для каждой партии груза, при условии, как минимум, одного набора испытаний на 5 тонн или их часть.
7.1.4
Необходимо обеспечить, чтобы агрегаты не были влажными перед нагревом, в противном случае это может отрицательно повлиять на производительность. Во время нагрева необходимо периодически регистрировать температуру агрегата, чтобы следить за тем, чтобы она не превышала предписанные пределы.
7.1.5
Материал в виде блоков должен быть отобран, отбирая приблизительно равное количество по частям не менее чем из шести блоков, выбранных наугад. Общий вес испытуемого образца должен быть не менее 5 кг.В случае, если приготовление смеси осуществляется на месте, необходимо собрать как минимум один образец на каждые 10 тонн битумной мастики, выгружаемой из битумной мастики, или как минимум один образец на каждую плиту в день и провести следующие испытания:
- Два образца диаметром 10 см каждый. или квадрат 10 см и толщиной 2,5 см должны быть подготовлены и испытаны на число твердости.
- Битум должен быть извлечен из примерно 1000 г образца мастики, а содержание битума определяется, как указано в Приложении C IS: 1195-1978.
- После извлечения битума необходимо провести ситовый анализ агрегатов и определить градацию в соответствии с процедурой, изложенной в IS: 2386 (Часть 1).
7.1.6
Температура битумной мастики во время укладки не должна превышать 200 ° C и быть не менее 170 ° C.
7.1.7
Продольный профиль готовой поверхности должен быть испытан с помощью прямой кромки длиной 3 м и поперечного профиля с шаблоном изгиба, пока уложенная мастика еще не остыла.Неровности более 4 мм в продольном и поперечном профиле должны быть исправлены путем подбора мастики на всю глубину пораженной панели и перекладывания.
7.1.8
Битумную мастику нельзя укладывать на влажную или мокрую поверхность, а также при температуре воздуха в тени 15 ° C или ниже.
7.1.9
При механизированной укладке мастики следует поддерживать среднюю скорость от 1,2 до 1,5 м / мин. Проблема образования пузырей на асфальте вскоре после стяжки может возникать по следующим причинам:
- Поверхность дорожного покрытия, на которую укладывается мастика, должна быть сухой, чтобы предотвратить развитие полостей или пустот, вызванных захваченной влагой и расширяющимся паром.
Этот пар или захваченный воздух в большинстве случаев выходит через мастичный мат, но часто остается в ловушке при охлаждении слоя. Ситуацию следует исправить, проткнув пузыри острым инструментом. Вибрационная стяжка может помочь в отводе влаги или захваченного воздуха, пока смесь битумной мастики еще горячая. Такие виброрейки с регулируемой частотой должны подходить для смесей. Укладка должна быть выполнена таким образом, чтобы колеса были задвинуты друг над другом, чтобы проткнуть пузыри мастичного асфальта.8
- Механическое перемешивание и нагрев смеси в транспортере необходимо для предотвращения расслоения смеси и поддержания однородной температуры в массе.
- Если мастиковая смесь кажется вялой, следует рассмотреть возможность использования природного песка округлой формы вместо искусственного мелкого заполнителя.
- Битумная мастика должна быть нанесена на участок перед отслаивающейся стяжкой таким образом, чтобы в смесь не попал воздух.Этого можно добиться с помощью лотков или других устройств, которые предотвратят падение битумной мастики.
- Вертикальные стыковые швы в механизированной мастике могут быть образованы путем распиловки затвердевшего материала либо в конце производства каждый день, либо всякий раз, когда укладка дорожного покрытия прерывается и смесь существенно охлаждается. Необходимо избегать наложения затвердевших и свежих смесей.
- Движение может быть ограничено как минимум на 24 часа, а готовое покрытие перед вскрытием должно быть подвергнуто механической очистке для удаления излишков стружки.
7.2 Обработка поверхности
Поверхность битумной мастики, испытанной с помощью линейки длиной 3 м, расположенной параллельно центральной линии проезжей части дороги, не должна иметь углублений более 4 мм. То же самое относится и к поперечному профилю при испытании с использованием шаблона изгиба.
ССЫЛКИ
- Опыт Пенсильвании в проектировании, строительстве и исполнении Gussasphalt, – П.С. Кандал и Дейл. Б. Меллотт, опубликовано в журнале Ассоциации технологов асфальтобетонных покрытий, Технология асфальтового покрытия, том 46, 1977.
- «Руководство по асфальтовым покрытиям и обработкам, используемым для покрытия дорожных покрытий», Клифф Николлс, Транспортная исследовательская лаборатория Великобритании (1998).
- Норма европейского стандарта EN 13108-6 Май 2006 ICS 93.080.20 Английская версия Битумные смеси – Характеристики материалов – Часть 6: Мастичный асфальт.
- БРИТАНСКИЙ СТАНДАРТ BS 1446: 1973, Технические условия на мастичный асфальт (мелкозернистый натуральный асфальтобетон) для дорог и тротуаров.
- Асфальтоукладчик с мастичным покрытием – G.К. Деспанде и В.Г. Дешпанде – Индийские шоссе, май 2009 г.
- IS Технические характеристики – Смазочная мастика для настила мостов и дорог – (Вторая редакция) -IS: 5317: 2002.
- IS Спецификация промышленного битума IS: 702-1988.
- IS Технические условия на битум для дорожных покрытий IS: 73-2006.9
Приложение-I
(см. Раздел 5)
ОБОРУДОВАНИЕ ДЛЯ РУЧНОЙ УКЛАДКИ БИТУМНОЙ МАСТИКИ
1 МАСТИКА ОБЫЧНЫМ МЕТОДОМ
1.
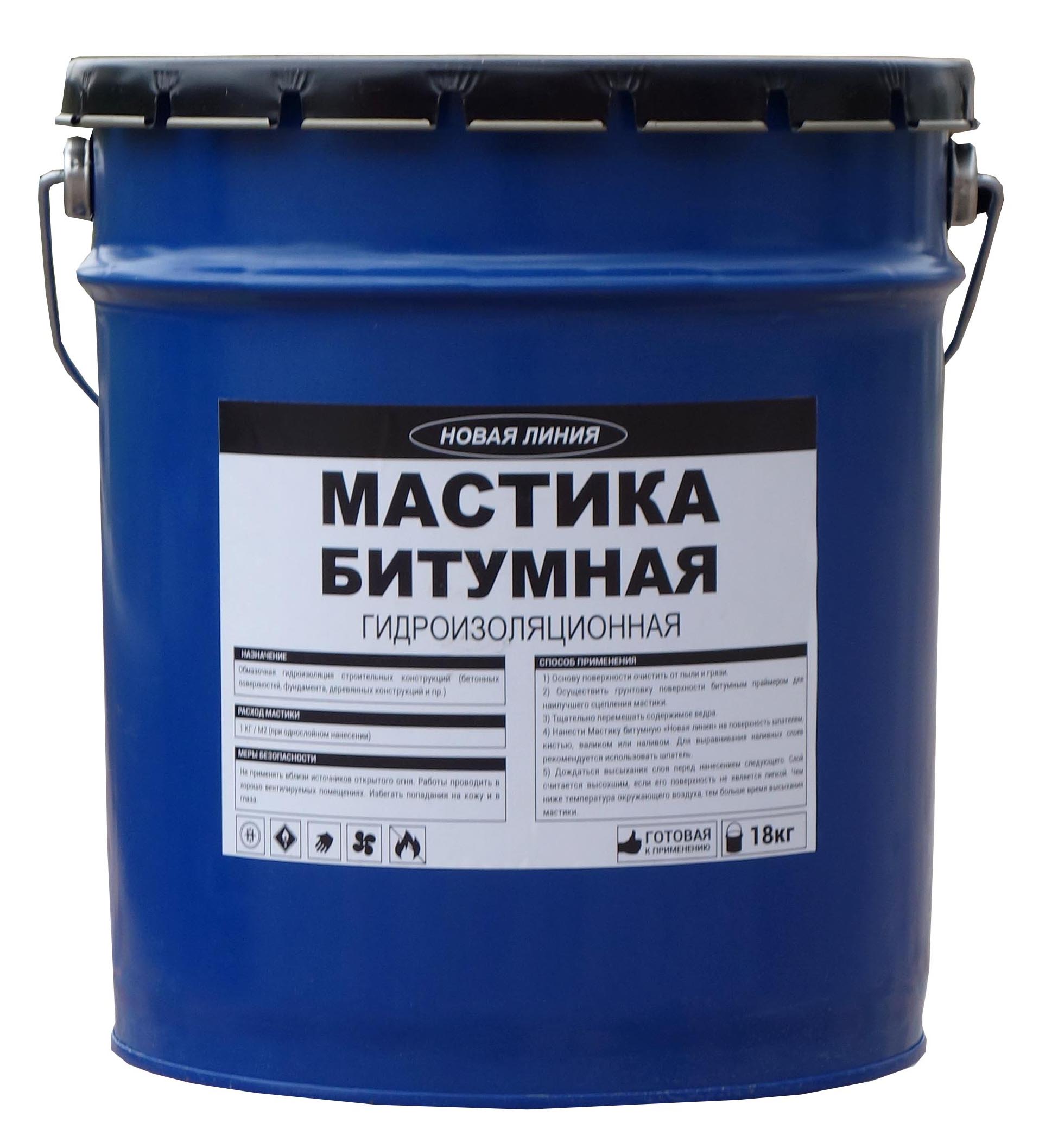
Мастиковые плиты очень похожи на котлы с дегтем. Это изотермические цистерны, смонтированные на колесном шасси. Нагрев битума и материала обычно осуществляется с помощью горелок, работающих на жидком топливе. Мастичные плиты имеют отсеки. Центральное и основное отделение используется для подогрева битума и приготовления смеси. Боковые карманы или отделения предназначены для предварительного нагрева крупных и мелких заполнителей. Поскольку нагрев осуществляется с помощью горелок, работающих на жидком топливе, температуру можно легко контролировать, контролируя пламя или подачу топлива.В зависимости от объема работ используются мастиковарки различной мощности от 1 /2 тонны до 3 тонн.
Кроме мастиковарки, для транспортировки и укладки необходимы следующие приспособления:
- Колесная тачка и плоские отстойники (для перевозки на короткие расстояния) и небольшие самосвалы (для перевозки на большие расстояния).
- Деревянные шпатели, тяжелые деревянные терки, подходящий ручной инструмент, линейка и ручной уровень.
- Уголки, необходимые для удержания мастики желаемой ширины и толщины 10
Приложение-II
(см. Раздел 5)
1 МАСТИКА, ПРИГОТОВЛЕННАЯ НА ЗАВОДЕ
Завод должен обеспечивать правильное соотношение различных компонентов, их тщательный нагрев и перемешивание, чтобы обеспечить подачу с требуемой скоростью для укладки на место. Он должен функционировать без нарушения экологических норм по шумо-пылевому загрязнению.
Различные компоненты смесительных установок должны быть:
- Бункеры холодного хранения: Эти бункеры должны состоять из нескольких компонентов для таких заполнителей, как песок, каменная крошка и т. Д.Эти материалы должны стекать по конвейерной ленте с контролируемой скоростью из отверстий, находящихся на их дне.
- Осушитель: Это должен быть изолированный вращающийся наклонный стальной цилиндр, работающий от горелок.
Материалы с конвейерной ленты должны подаваться в нее так, чтобы они достигли указанной температуры. Все органические примеси должны сгореть, а влага, если таковая имеется, должна быть удалена. В сушилке должна достигаться температура до 250 ° C.
- Горячий бункер: Горячий заполнитель из сушилки поднимается и выливается в горячий бункер с помощью ковшового элеватора для горячего.Этот бункер должен располагаться достаточно высоко над барабаном смесителя, где хранятся горячий заполнитель из сушилки и известняковый порошок из устройства подачи извести, пока он не будет засыпан в барабан смесителя. Порошок известняка должен подаваться из бункера горячей извести с помощью винтового элеватора.
- Температура материала в горячем бункере должна поддерживаться рубашкой с горячим маслом или изоляцией высокой плотности.
- Бункер должен вмещать десять партий, скажем, около 20 тонн, а вес должен контролироваться датчиками, установленными в диспетчерской.
- Резервуар для хранения битума: Температура битума должна поддерживаться на уровне 170 ° C с помощью горелок, предусмотренных для резервуара.
- Горячий бункер для порошка извести и устройства подачи извести: Бункер должен представлять собой калиброванный контейнер для порошка извести, который имеет приспособления для нагрева с помощью системы циркуляции горячего масла. Порошок должен непрерывно перемешиваться вращающимися рычагами в бункере, установленном на оси. Горячий известковый порошок из бункера перекачивается в приподнятый бункер с помощью винтового подъемника.Подаваемое количество должно контролироваться по содержимому бункера для извести с помощью автоматической системы взвешивания для каждой партии. Винтовой элеватор должен быть снабжен масляной рубашкой для обеспечения потери тепла11
- Весовая секция: Установка должна быть оборудована системой взвешивания, позволяющей взвешивать до 5 различных заполнителей, два типа наполнителя, битум и два типа добавок.
При необходимости он должен взвесить различные заполнители, наполнитель, битум и добавки.Это должно быть подходящим для емкости одной партии в две тонны. Эта секция будет выгружать материал после взвешивания в двухвальный смеситель для гомогенного перемешивания.
- Смеситель двухвального типа с горячей рубашкой: Он должен быть на приподнятом стальном каркасе на подходящей высоте для облегчения заливки смеси в транспортеры. Смеситель должен иметь вращающиеся стальные рычаги или нагреватели, установленные на центральных осях и предназначенные для эффективного перемешивания битума, известкового порошка и заполнителя.Битум должен закачиваться в смеситель из системы взвешивания битума (соответствует потребности одной партии). Во время перемешивания в смесителе будет подготовлена вторая партия после выгрузки из горячего бункера в секции взвешивания для немедленной выгрузки в смеситель. Время перемешивания выбирается в зависимости от достижения проектных свойств смеси, как указано в спецификациях.
Затем мастиковая смесь должна быть залита в транспортер, открыв выходную заслонку через отверстие в верхней части транспортера.Около 60 секунд перемешивания в барабане миксера или столько, сколько будет сочтено достаточным, так как все компоненты находятся при очень высокой температуре и перемешивание происходит достаточно эффективно.
- Диспетчерская и цифровые панели управления: Диспетчерская с кондиционированием воздуха должна контролировать все операции установки с помощью электрических датчиков в различных местах. Дозирование различных компонентов, их температура, масса известкового порошка, битума и заполнителей из горячего бункера для каждой партии, время смешивания и т. Д.должны наблюдаться и контролироваться с помощью компьютеризированной системы. Это должно позволить смеси быть в соответствии с формулами смешивания должностей.
- Система циркуляции горячего масла: Поскольку различные компоненты смеси должны храниться при указанных высоких температурах, потери тепла при хранении или транспортировке из бункера в смеситель и т.
Д. Должны предотвращаться циркуляцией горячего масла в полости. в рубашках вокруг труб, бункеров, бочек и т. д. Для этой цели масло должно нагреваться в резервуаре для хранения, из которого оно перекачивается насосом по изолированным трубам.Используемое масло должно быть термическим маслом, которое можно нагревать до 250 ° C. (Фото 1)
Фото 1 Общий вид завода12
- Автотранспортные средства: Действие смешивания компонентов должно продолжаться в транспортном средстве после того, как в него будет залита смесь с завода. Он должен иметь изолированный наклоняющийся стальной барабан, снабженный вращающимся смесительным рычагом, и нагревательное оборудование с жидкотопливными горелками для циркулирующего термического масла в его рубашке.Пока смесь не выльется на покрываемую поверхность, открыв выпускное отверстие и наклонив барабан; операция перемешивания должна продолжаться и обеспечивать однородную горячую смесь.
- Асфальтоукладчик: Это поможет равномерно распределить и разложить пластиковую смесь по поверхности до желаемой ширины и толщины с правильным уклоном и изгибом за счет нагретого стального поплавка без деформации и поворотных распределителей с мечом.
(фото 2)
Фото 2 Вид на асфальтоукладчик
Он должен приводиться в действие дизельным двигателем и с помощью гидравлической системы. (Фото 3)
Фото 3 Асфальтоукладчик в работе 13
Обогрев поплавка должен производиться с помощью сжиженного нефтяного газа с прикрепленными к нему инфракрасными обогревателями. Специальное профилирование с точными и сглаживающими зонами на поплавке или рабочей планке гарантирует оптимальные условия и результаты наслоения. Отдельные удлинители следует менять в соответствии с желаемой шириной захвата. (Фото 4)
Фото 4 Вид готовой работы
- Основные характеристики завода: Должна быть возможна подача около 2500 кв.м.работы в день с одним заводом и асфальтоукладчиком. Он должен производить от 15 до 20 тонн смеси в час.
- Покрывающая стружка: Покровная стружка размером 4,75 мм и удерживаемая на сите 2,36 мм должна быть покрыта 2-процентным битумом марки VG 10 каждый день перед началом производства.
Щепа с битумным покрытием должна храниться в бетонных бункерах, прилегающих к территории завода, и периодически переворачиваться с помощью фронтального погрузчика для предотвращения накопления тепла.
- Механизированный разбрасыватель стружки: Для предотвращения заноса транспортных средств в условиях влажной погоды необходимо обязательно принять метод нанесения битумной стружки одинакового размера на уложенную поверхность с помощью разбрасывателя стружки с приводом от двигателя.Это устройство должно быть размещено примерно в 3 м позади стяжки и должно наносить стружку для предотвращения скольжения. Щепа подается в загрузочном бункере и механически доставляется подающим роликом к дорожному покрытию из расчета 5,4 – 8,1 кг на кв.м. Стружку также можно разложить вручную с задней платформы разбрасывателя стружки в те области, которые не имеют достаточного покрытия14
(PDF) Реологические характеристики битумной мастики в зависимости от состава и дисперсности наполнителя
1
Материалы данной работы могут использоваться на условиях Creative Commons Attribution 3. 0 лицензия. Любое дальнейшее распространение
этой работы должно содержать указание на автора (авторов) и название работы, цитирование журнала и DOI.
Опубликовано по лицензии IOP Publishing Ltd
1234567890 ‘’ “»
3-я международная конференция по реологии и моделированию материалов (ic-rmm3) IOP Publishing
IOP Conf. Серия: Физический журнал: конф. Серия 1045 (2018) 012026 doi: 10.1088 / 1742-6596 / 1045/1/012026
Реологические характеристики битумной мастики в зависимости от состава
и дисперсности наполнителя
М.С. Лебедева1 и Н.И. Кожухова2
1 Белгородский государственный технологический центр Университет имени В.Г.
г. Шухов, ул. Костюкова, 46, г. Белгород, Россия
2 Кафедра материаловедения и материаловедения Белгородского государственного технологического университета
кал. Шухов, ул. Костюкова, 46, Белгород, Россия
E-mail: [email protected]
Аннотация. Поскольку наполнители в асфальтобетоне используются для повышения вязкости битума, модификации структуры необходимо оценить эффект структурирования наполнителя в битумном вяжущем. Для этой цели исследовано влияние фазовых и размерных параметров мелкодисперсных порошкообразных наполнителей на реологические характеристики битумных мастик (битумно-наполнительный состав). Максимальный эффект
на свойства битума наблюдается у таких наполнителей, как каолин и мел. Эти два наполнителя
имеют самую высокую удельную поверхность (SSA) и самое высокое содержание пустот. Таким образом, они способны поглощать
более высокого содержания битума по сравнению снаполнители с более низкими значениями SSA и пустотного содержимого. Вариации значений Delta Ring и Ball для мастик на основе каолина и мела при 83 ° С и
24 ° С соответственно значительны по сравнению с другими составами (до 8–10 ° С).
можно связать со структурирующим эффектом при высоких температурах. Существенное изменение физических и механических свойств битума может произойти, когда применение каолина связано с тонкими чешуйками
его частиц.Исследование реологических характеристик битумных мастик методом динамического сдвига
remoter при высоких температурах демонстрирует более низкие значения комплексного модуля для битумных мастик
, содержащих известняковые и песчаные наполнители со средней и высокой дисперсностью, по сравнению с мелом-
и на основе каолина. аналоги.
1. Введение
Наполнители, добавляемые в асфальтобетон, представляют собой мелкодисперсные порошки, полученные путем измельчения горных пород или
порошкообразных промышленных побочных продуктов.Они используются в качестве модификатора битума для увеличения вязкости вяжущего
(т.е. структурирующего эффекта), а также для расширения диапазона рабочих температур. Образовавшаяся структурированная дисперсная система
действует как связующий компонент в битумном бетоне. Это приводит к снижению
деформации ползучести (пластической текучести) и увеличению примеси битума. Принято считать, что структурирующая способность наполнителя
связана с высокоразвитой поверхностью.
Однако следует отметить, что не все дисперсные материалы одинаково влияют на битум из-за
следующих причин: минеральный и химический состав, дисперсность, форма частиц и поверхностная реакционная способность
из них. Эти параметры взаимосвязаны, поэтому трудно определить конкретное влияние каждого параметра
на общий структурирующий эффект материалов на основе асфальта.
Степень структурирования органического связующего, содержащего наполнитель, связана с распределением частиц в массе
i.е. плотность упаковки. Также этот параметр может определяться гранулометрическим составом, т.е. дисперсностью наполнителя
, а также формой частиц [1, 2]. В случае мультимодального распределения частиц – это количество межчастичных контактов
, плотность их упаковки и прочность системы [3].
Лабораторное исследование свойств модифицированной асфальтовой мастики на основе диатомита и базальтового волокна
Чтобы улучшить характеристики асфальтовой мастики, некоторые исследователи добавили диатомит или базальтовое волокно в качестве модификатора к асфальтовой мастике, и результаты показывают улучшены некоторые свойства асфальтовой мастики.Не сообщалось об одновременном добавлении диатомита и базальтового волокна, двух видов модификатора, смешанной асфальтовой мастики; В этой статье были подготовлены тринадцать групп модифицированных составом диатомита и базальтового волокна (DBFCMAM) асфальтовой мастики с различным содержанием для изучения характеристик. Испытания точки размягчения, проникновения конуса, вязкости и DSR были проведены для оценки высокотемпературных характеристик DBFCMAM, тогда как испытания на пластичность по усилию и BBR были использованы в исследовании низкотемпературных характеристик DBFCMAM.Результаты показали, что высокотемпературные характеристики DBFCMAM были увеличены; кроме того, низкотемпературные характеристики DBFCMAM улучшены диатомитом и базальтовым волокном в соответствии с результатами испытания на силовую пластичность; однако вывод данных испытаний BBR несовместим с испытанием на пластичность по усилию. Таким образом, высокотемпературные и низкотемпературные свойства DBFCMAM были улучшены.
1. Введение
По сравнению с цементобетонным покрытием, асфальтовое покрытие имеет преимущества низкой стоимости, низкого уровня шума, безопасности и комфортного вождения, а также вторичного использования.Поэтому асфальтовая смесь широко применяется в дорожном строительстве. Примерно 90% дорог в Китае построено из асфальтобетонных смесей [1, 2]. Асфальтовая мастика – важная составляющая асфальтобетонной смеси. Соответствующая производительность напрямую влияет на характеристики асфальтовой смеси [3, 4]. Асфальт – это типичный вязкоупругий материал, который характеризуется текучестью при высокой температуре и хрупким твердым состоянием при низкой температуре. Это вызывает образование колей и трещин на асфальтовом покрытии [5].Модифицированный асфальт используется для улучшения свойств при высоких и низких температурах и сопротивления усталости. Это важное средство для продления срока службы асфальтового покрытия. В настоящее время обычный модификатор асфальта можно разделить на полимер-модифицированный материал и неорганический модифицированный материал [6–14]. За счет использования неорганических модифицированных материалов, таких как диатомит и базальтовое волокно, в качестве модификатора, можно было бы не только улучшить характеристики асфальта, но также можно было бы избежать загрязнения окружающей среды полимерным модификатором.
Поэтому исследователи постепенно обращают внимание на использование неорганических модифицированных материалов [15–26].
Диатомит – это материал с легким весом, высокой пористостью, низкой плотностью, высокой степенью поглощения поверхности, высокими запасами и низкой стоимостью. Благодаря этим характеристикам он был использован в модифицированных асфальтовых мастиках и модифицированных асфальтовых смесях [15]. Cong et al. [16] изучали модифицированную диатомитом асфальтовую мастику. Результаты показали, что никакой химической реакции между диатомитом и асфальтом не происходило.Вязкость и комплексный модуль битумной мастики, модифицированной диатомитом, увеличивались по мере увеличения содержания диатомита при высокой температуре. Но диатомит не смог улучшить характеристики асфальта при низкой температуре. Бао [17] изучил основные свойства асфальтовой мастики, модифицированной диатомитом, и пришел к выводу, что по мере увеличения содержания диатомита проницаемость и пластичность модифицированной асфальтовой мастики уменьшаются, тогда как точка размягчения увеличивается. Ван [18] изучил микромеханизм против старения и механические свойства диатомитовой асфальтовой мастики.Результаты показали, что диатомит значительно улучшает старение асфальтовой мастики по сравнению с минеральными порошками. Асфальтовая мастика имела оптимальные механические свойства при высокой температуре, когда коэффициент замещения диатомита составлял 75%. Cheng et al. [8] сообщили, что улучшение содержания диатомита в асфальтовой мастике было более значительным, чем извести, гашеной извести и летучей золы при умеренной температуре и высокой температуре. Ли и др. [19] исследовали свойства модифицированной диатомитом асфальтовой мастики и соответствующих асфальтовых смесей.Результаты показали, что прочность на изгиб и деформация изгиба асфальтовой смеси, модифицированной диатомитом, были ниже, чем у эталонного материала при низкой температуре. Zhu et al. [20] оценили высокотемпературную стабильность и сопротивление низкотемпературному растрескиванию битумной смеси, модифицированной диатомитом, в лабораторных условиях.
Результаты показали, что диатомит значительно улучшил сопротивление колейности асфальтовой смеси, тогда как при увеличении модуля упругости при изгибе низкотемпературные характеристики снизились.Вышеупомянутые результаты продемонстрировали, что добавление диатомита способствовало высокотемпературной стабильности и улучшению характеристик защиты от старения асфальтовой мастики и смеси, в то время как она не способствовала пластичности асфальтовой мастики при низкой температуре. В этих условиях модуль жесткости при низких температурах увеличился, а гибкость снизилась.
Базальтовое волокно – это разновидность волокна с высокими эксплуатационными характеристиками, которое изготавливается из базальтовой породы. Благодаря соответствующей высокой прочности и высокой устойчивости к воде, кислотам и щелочам, а также применимости в широком диапазоне температур и хорошей долговечности, базальтовое волокно вызвало широкое беспокойство в исследовательском сообществе [21].В последние десятилетия базальтовое волокно широко используется в качестве армирующего модификатора для характеристик асфальтовой мастики и асфальтобетонных смесей [22–26]. Rong et al. [22] добавили рубленое базальтовое волокно в асфальтобетонную смесь, обнаружив, что усталостная прочность смеси значительно увеличилась. Морова [23] обнаружил, что добавление 0,5% базальтового волокна может значительно повысить высокотемпературную стабильность асфальтовой смеси. Zheng et al. [24] изучали усталостные свойства асфальтовых смесей в сложных условиях (характеристики низкотемпературного изгиба, проникновение хлоридов, цикл замораживания-оттаивания и соответствующий эффект сцепления).Результаты показали, что характеристики низкотемпературного изгиба и усталостные свойства асфальтовых смесей в сложных условиях могут быть значительно улучшены за счет добавления базальтового волокна. Wang et al. [12] провели испытание на прямое растяжение и недавно разработанное испытание на усталость для битума, модифицированного базальтовым волокном. Результаты испытаний на прямое растяжение показали, что при соответствующем содержании прочность на разрыв асфальтовой мастики улучшается вместе с использованием базальтового волокна.
Результаты испытаний на усталость показали, что усталостная долговечность асфальтовой мастики была значительно улучшена за счет базальтовых волокон. Xiong et al. [25] обнаружили, что высокотемпературные характеристики асфальтовой мастики могут быть улучшены добавлением базальтового волокна. Лю и др. [26] исследовали различные эффекты трех типов волокон на низкотемпературные характеристики как асфальтовой мастики, так и асфальтобетонной смеси с помощью испытания BBR и испытаний на низкотемпературный изгиб балки. Результаты показали, что при -10 ° C, по сравнению с чистой асфальтовой мастикой, асфальтовая мастика, модифицированная базальтовым волокном, имела более низкую жесткость ползучести () и более высокую скорость ползучести (), низкотемпературные характеристики асфальтовой мастики, модифицированной базальтовым волокном, были улучшены, и также была улучшена стойкость к низкотемпературному растрескиванию асфальтобетонной смеси с базальтовым волокном.Gu et al. [13] изучили реологическое поведение асфальтовой мастики, армированной базальтовым волокном, с помощью динамических реологических испытаний на сдвиг и повторных испытаний на ползучесть, обнаружив, что базальтовое волокно обладает высокой степенью поглощения, высокой прочностью на разрыв, высоким модулем упругости и высокой температурной стабильностью.
Можно было заметить, что базальтовое волокно способствовало повышению трещиностойкости асфальтовой мастики при низкой температуре и сопротивления деформации при высокой температуре соответственно. Таким образом, можно заметить, что характеристики асфальтовой мастики можно улучшить добавлением диатомита или базальтового волокна.Однако некоторые недостатки все же существуют. Низкотемпературные характеристики асфальтовой мастики были снижены добавлением диатомита, которое можно было повысить одновременным добавлением диатомита и базальтового волокна.
В данной статье были изучены тринадцать различных групп асфальтовой мастики, модифицированной диатомитом и базальтовым волокном (DBFCMAM). Испытание точки размягчения, испытание на проникновение конуса, испытание на вязкость и испытание DSR применяли для оценки высокотемпературных характеристик DBFCMAM; испытание на пластичность и испытание BBR были использованы в исследовании низкотемпературных характеристик DBFCMAM.Согласно результатам, было проанализировано влияние на свойства асфальтовой мастики добавления диатомита и базальтового волокна, что послужило эталоном для диатомитового и базальтового волокна при применении в асфальтовых покрытиях.
2. Экспериментальная
2.1. Материалы
Использованный асфальт AH-90 в этой бумаге был поставлен компанией Panjin Petrochemical Industry, расположенной в провинции Ляонин, Китай. Физические показатели чистого асфальта представлены в таблице 1.
|
Диатомит образовался из Горный район Чанбайшань провинции Цзилинь.Физические свойства и гранулометрический состав представлены в таблице 2. Базальтовое волокно было поставлено компанией Jiuxin Basalt Industry Co., Ltd в провинции Цзилинь, а технические характеристики представлены в таблице 3.
|
|
2.2. Приготовление DBFCMAM
Согласно стандартному методу приготовления диатомитовых или модифицированных волокнами асфальтовых мастик [9, 13, 16, 25–28], оптимальное содержание диатомита составляет около 15% или базальтового волокна составляет около 3%. Таким образом, чтобы комплексно проанализировать эффективность составной модифицированной асфальтовой мастики при изменении содержания диатомита и базальтового волокна, содержания диатомита 5%, 10% и 15% и содержания базальтового волокна 1%, 2% , 3% и 4% были приняты, и выполнено комплексное проектирование следов диатомита и базальтового волокна.Наконец, в этой статье мы получили 13 групп различных составных модифицированных асфальтобетонных мастик. Содержание диатомита и базальтового волокна указано в таблице 4.
|
Подготовка DBFCMAM в этой статье описывалась следующим образом.Во-первых, чистый диатомит асфальта и базальтовое волокно отдельно помещали в печь при 150 ° C на 4 часа, что обеспечивало достаточную текучесть асфальта и чтобы диатомит и базальтовое волокно достигли температуры смешивания. Затем диатомит и базальтовое волокно добавляли в асфальтобетонные мастики в определенной пропорции и перемешивали с помощью высокоскоростного гомогенизатора со сдвигом (KRH-I, Shanghai Konmix Mechanical & Electrical Equipment Technology Co. Ltd., Китай) с баком для сохранения тепла. Температура перемешивания составляла 150 ° C, скорость сдвига составляла 5000 об / мин, а продолжительность перемешивания составляла 50 минут, так что диатомитовое и базальтовое волокно могло быть равномерно распределено в асфальтовой мастике.Содержание диатомитового или базальтового волокна рассчитывали по весу чистого асфальта. Из-за различных значений плотности трех материалов асфальтовая мастика, модифицированная компаундом, была нанесена по прошествии определенного периода времени, диатомит и базальтовое волокно будут проседать, и DBFCMAM следует снова перемешать перед дальнейшим использованием.
2.3. Физические и механические свойства по результатам испытаний DBFCMAM
2.3.1. Тест на проникновение конуса
Из-за добавления диатомита и базальтового волокна однородная система асфальта превратилась в гибридные дисперсии.Содержание и размер частиц повлияли на соответствующие характеристики асфальтовой мастики; следовательно, данные теста на проникновение были очень дискретными. Благодаря исследованию Chen et al. [14, 25], в этой статье для измерения текучести и сопротивления сдвигу DBFCMAM был использован тест на проникновение конуса.
В этой статье, в соответствии с методом испытаний на проникновение битумных материалов (ASTM D5 / D5M-2013), для измерений был разработан тест на проникновение конуса. Изготовленный на заказ конус заменил стандартную иглу инструмента для пенетрации, а размер структуры конуса представлен на Рисунке 1.По глубине конуса напряжение сдвига было рассчитано как тестовый индекс. Напряжение сдвига (кПа) DBFCMAM можно рассчитать по следующему уравнению: где – напряжение сдвига (кПа), – качество конуса (90,3 г), – глубина погружения (0,1 мм) и – угол конуса (30 °).
2.3.2. Тест точки размягчения
Точка размягчения широко используется при оценке чувствительности к высоким температурам асфальтовой мастики [29]. Поэтому испытание точки размягчения DBFCMAM с различным содержанием было выполнено методом, указанным в ASTM D36 (ASTM D36 / D36M-2014).
2.3.3. Тест на пластичность по усилию
В 1976 году Андерсон и Уайли представили тест на пластичность по усилию, за которым последовало большое количество исследователей, которые использовали этот метод для оценки свойств асфальта при растяжении [29–31]. Результаты [7, 8, 31, 32] показали, что испытание силы растяжения было надежным и эффективным методом. В этой статье с помощью этого метода были оценены низкотемпературные свойства DBFCMAM при растяжении. Согласно стандартам EN13589 [33] и EN13703 [34], максимальная сила (), удлинение при растяжении () и энергия деформации () использовались в качестве оценочных показателей.Максимальные значения силы () и удлинения при растяжении () были получены путем записи эксперимента, и были построены кривые сила-удлинение с данными регистрации, полученными из записи эксперимента. Энергию деформации () можно было рассчитать по площади под кривой от 20 мм до 40 мм [34]. Испытание было выполнено с использованием той же испытательной формы для испытания на упругое восстановление (ASTM D6084-13). Температура испытания составляла 5 ° C, а скорость растяжения составляла 1 см / мин ± 0,5 см / мин.
2.3.4. Тест на вязкость
Вязкость представляет собой сдвигающую способность асфальта при высоких температурах. В соответствии с экспериментальным методом стандарта ASTM D4402 (ASTM 2015b) в этой статье испытание на вязкость проводилось при температуре 135 ° C. В качестве испытательного оборудования использовался асфальтобетонный ротационный вискозиметр Brookfield SD-0625 (Шанхайский институт геолого-геофизических исследований и технологий), где был выбран ротор 21 #.
2.3.5. Испытание реометра динамического сдвига (DSR) (AASHTO T315-09)
Испытание реометра динамического сдвига может измерять вязкость и упругие свойства асфальтовой мастики при средних и высоких температурах.В этом исследовании Malvern Bohlin Gemini 200 (British Malvern Instruments Ltd) использовался для измерения комплексного модуля () и фазового угла (), как подробно описано в стандарте ASTM D7175 (ASTM 2015a). Согласно стандарту ASTM D7175 (ASTM 2015a) испытания проводились на параллельной пластине с зазором 1,0 мм и диаметром 25 мм. Образец асфальта помещали между двумя параллельными плитами; нижняя пластина была закреплена. Верхняя пластина колебалась с частотой нагружения 10 рад / с (1.59 Гц). Комплексный модуль сдвига () и фазовый угол () были измерены при 52 ° C, 58 ° C, 64 ° C и 70 ° C. В спецификации Superpave в качестве показателя оценки связующего материала при высоких температурах использовался коэффициент колейности ().
2.3.6. Испытания реометра изгибающей балки (AASHTO T313-09)
Испытания реометра изгибающей балки (BBR), предложенные SHRP, широко используются для измерения свойств ползучести при низких температурах асфальтовой мастики. BBR испытание было разработано для измерения модуля жесткости асфальтовой мастики и оценки соответствующей трещиностойкости [32].В испытании BBR были измерены жесткость на ползучесть () и -значение (). В соответствии со стандартом ASTM D6648 (ASTM 2008), в данном исследовании свойство ползучести DBFCMAM при низких температурах измеряли с помощью реометра изгиба (TE-BBR, Cannon Instrument Company, США). Температура испытания составляла -12 ° C, и образец был сформирован с алюминиевой пленкой размером 125 мм × 12,5 мм × 6,25 мм.
DBFCMAM нагревали до 150 ° C в течение 3 часов для обеспечения достаточной ликвидности. После этого он был перемешан перед заливкой в форму.Формы, заполненные образцами, помещали на испытательный стенд. Затем образцы охлаждали при комнатной температуре в течение 60 мин; вскоре после этого формы были изолированы от окружающей среды при -5 ° C в течение 1 мин и извлечены из формы. Образцы помещали в тестовый раствор при -12 ° C на 60 мин. Затем образцы были помещены на две стальные опоры (пролет 102 мм) и приложена длительная нагрузка 0,98 кН в течение 240 с. Через нагрузку и измеренный центральный венец были рассчитаны жесткость на ползучесть () и скорость ползучести ().Значение – представляет способность DBFCMAM к релаксации напряжений.
Жесткость на ползучесть () и скорость ползучести () были рассчитаны по (2), когда продолжительность приложенного нагружения составляла 8,0 с, 15,0 с, 30,0 с, 60,0 с, 120,0 с и 120 с.
В соответствии со стандартом ASTMD6648 оба и были определены при продолжительности нагрузки 60 с. Жесткость к ползучести () была выше, а асфальтовая мастика была тверже и весьма склонна к растрескиванию при низких температурах. Чем выше была скорость ползучести (), тем лучше была способность релаксации напряжений.
3. Результаты и обсуждение
3.1. Измерения при испытаниях традиционной асфальтовой мастики
Глубина конуса, напряжение сдвига, точка размягчения и результаты испытаний на вязкость асфальтовой мастики представлены в таблице 5.
|
Согласно данным таблицы 5, глубина конуса DBFCMAM, по-видимому, уменьшилась, тогда как прочность на сдвиг значительно увеличилась.Температура размягчения асфальтовой мастики после добавления диатомита и базальтового волокна была увеличена. Величина вязкости DBFCMAM также была улучшена за счет добавления диатомита и базальтового волокна, что указывает на то, что текучесть DBFCMAM снижается при высокой температуре, но более высокая вязкость приведет к увеличению температуры смешивания и температуры уплотнения [33]. Диатомит может эффективно адсорбировать низкомолекулярные группы и низкополярные ароматические молекулы для соответствующей мезопористой структуры [35]; поэтому точка размягчения и вязкость DBFCMAM были выше по сравнению с чистым асфальтом.Xiong et al. [25] указали, что базальтовое волокно может вызвать эффект трехмерной пространственной сети. Кроме того, волокна могут поглощать легкие компоненты асфальта и увеличивать жесткость и вязкость асфальта [14]. Соответственно, базальтовое волокно в большей степени влияет на уменьшение глубины погружения конуса, улучшая напряжение сдвига и увеличивая размягчение и вязкость DBFCMAM.
Уменьшение глубины погружения конуса и увеличение касательного напряжения показали увеличение жесткости DBFCMAM.Повышенная жесткость указывает на более высокую стойкость к колееобразованию у мастеров из модифицированного асфальта. Температура размягчения и вязкость увеличивались при добавлении диатомита и базальтового волокна. Это означало, что модификация диатомитом и базальтовым волокном сделала асфальтовую мастику менее восприимчивой к деформации, вызванной движением транспорта при высоких температурах, по сравнению с чистой асфальтовой мастикой. Эти изменения глубины конуса, точек размягчения и вязкости были полезными; была улучшена высокотемпературная стабильность асфальтовой мастики с добавлением диатомита и базальтового волокна, и они были дополнительно проверены с помощью тестов DSR.
3.2. Испытание на силовую пластичность
Испытание на силовую пластичность при 5 ° C использовали для оценки свойств низкотемпературного растяжения асфальтовой мастики. Для количественного сравнения низкотемпературных характеристик асфальтовой мастики путем добавления диатомита и базальтового волокна,,, и были использованы для оценочного индекса. Кривые усилие-удлинение показаны на рисунке 2, а значения, и перечислены в таблице 6.
|
Из данных испытаний можно сделать следующие выводы: DBFCMAM превышает соответствующее значение для чистого асфальта. представляет прочность на разрыв при когезионном разрушении асфальтовой мастики. Это указывает на то, что прочность на когезионное разрушение при растяжении DBFCMAM увеличилась; поэтому прочность DBFCMAM на растяжение при низких температурах улучшилась.Когда содержание диатомита и базальтового волокна составляло (5%, 3%), свойства DBFCMAM на растяжение при низких температурах были наилучшими. представляет деформационные характеристики асфальтовой мастики. DBFCMAM уменьшилось по сравнению с чистым асфальтом; Было продемонстрировано, что низкотемпературная гибкость DBFCMAM при растяжении была снижена.
С учетом противоречивых выводов, полученных из и рассмотрения, энергия деформации (), которая была всеобъемлющим показателем, была выбрана для оценки низкотемпературных характеристик DBFCMAM; раскрыл результаты и.был выше; сопротивление растяжению асфальтовой мастики было лучше [8]. Как показано в Таблице 6, свойства DBFCMAM на растяжение были улучшены. Когда содержание диатомита и базальтового волокна составляло (7,5%, 3%), DBFCMAM имел наилучшие свойства при низкотемпературном растяжении.
Результаты таблицы 6 продемонстрировали, что низкотемпературные характеристики DBFCMAM были улучшены по сравнению с чистым асфальтом. Когда содержание диатомита остается постоянным, по мере увеличения содержания базальтового волокна, низкотемпературные характеристики сначала увеличиваются, а, следовательно, уменьшаются.Когда содержание диатомита и базальтового волокна составляло (7,5%, 3%), низкотемпературные характеристики DBFCMAM были лучшими. В общем, когда содержание диатомита и базальтового волокна различается, свойства асфальтовой мастики при низких температурах различаются, но свойства DBFMCAM на растяжение при низких температурах улучшаются.
3.3. Испытание на динамический реологический сдвиг (DSR)
Испытание на динамический реологический сдвиг (DSR) использовалось для измерения вязкоупругости асфальтовой мастики при средней и высокой температуре.Основными вязкоупругими параметрами асфальтовой мастики являются комплексный модуль сдвига () и фазовый угол ( δ ). использовали для оценки противозадирных свойств асфальтовой мастики. Фазовый угол ( δ ) представляет собой временной интервал между приложенным напряжением сдвига и результирующей деформацией сдвига [32]. Когда фазовый угол ( δ ) был равен нулю, асфальтовая мастика была чистым эластичным материалом, тогда как когда δ составляла 90 °, асфальтовая мастика была чисто вязким материалом. При высокой температуре уменьшение фазового угла асфальтовой мастики может повысить эластичность.Чем выше было значение, тем больше была жесткость и, следовательно, более устойчива к образованию колейностей асфальтовая мастика. Чем меньше фазовый угол ( δ ), тем эластичнее связующее [36, 37].
В этой статье был проведен тест DSR для сравнения разницы реологических свойств между разными асфальтовыми мастиками. Были получены комплексный модуль () и фазовый угол ( δ ) при определенной температуре (52 ° C, 58 ° C, 64 ° C и 70 ° C) и определенной частоте (10 рад / с), которые можно рассматривать что сдвиговые реологические свойства различных асфальтобетонных мастик могут быть сравнены и проанализированы согласно справочным материалам [8, 10, 28].
Экспериментальные данные перечислены в таблице 7. Асфальт был типичным вязкоупругим материалом, который имеет небольшой комплексный модуль упругости при высокой температуре и большой модуль при низкой температуре. Чтобы сравнить тенденцию изменения, δ, , и с различным содержанием при разных температурах, результаты (, δ , и) были нормализованы обработки и затем показаны на рисунках 3–5. Уравнение (3) использовалось для нормализации. – нормализованный параметр, – параметр DBFCMAM, – параметр чистого асфальта,%, 7.5%, 10% (содержание диатомита) и%, 2%, 3% и 4% (содержание базальтового волокна).
Из графика тенденции комплексного модуля сдвига (рис. 3) можно было наблюдать, что все комплексные модули сдвига DBFCMAM были выше, чем у чистого асфальта.Комплексный модуль сдвига () был уменьшен за счет повышения температуры испытания. При той же температуре, когда содержание диатомита было постоянным, прирост постепенно увеличивался по мере увеличения содержания базальтового волокна. В соответствии с рисунком 4 можно было наблюдать, что фазовый угол ( δ ) DBFCMAM изменил тенденцию, а фазовый угол ( δ ) DBFCMAM уменьшился по сравнению с чистым асфальтом, тогда как снижение было уменьшено в ходе испытания. поднялась температура; это указывало на то, что вязкость асфальтовой мастики незначительно изменялась при повышении температуры.При той же температуре, когда содержание диатомита было постоянным, уменьшение δ постепенно увеличивалось по мере увеличения содержания базальтового волокна. Увеличение и уменьшение фазового угла δ указывает на то, что добавление диатомитовых и базальтовых волокон к асфальтовой мастике снижает термическую восприимчивость DBFCMAM. Таким образом, DBFCMAM будет более способен восстанавливать свою первоначальную форму после воздействия нагрузок. Увеличение и уменьшение δ продемонстрировало, что жесткость асфальтовой мастики была увеличена за счет использования диатомитовых и базальтовых волокон, что означало повышенную стойкость к колейности при более высоких температурах. Коэффициент колейности () – это мера жесткости устойчивости к высоким температурам или колейности асфальтовой мастики и регулярно используется для описания колейности при высоких температурах [38]. Для метода Superpave требуется кПа для образца асфальтовой мастики [39, 40]. Чем выше он был, тем лучше было сопротивление колейности асфальтового покрытия [41]. На Рисунке 5 значения DBFCMAM были выше, чем у чистого асфальта. При той же температуре, когда содержание диатомита было постоянным, прирост постепенно увеличивался по мере увеличения содержания базальтового волокна, что можно объяснить хорошим распределением волокон в разных направлениях в асфальтовой мастике, которая сопротивлялась сдвиговым смещениям и улучшала сопротивление сдвигу. асфальта от внешних сил [42].По мере повышения температуры приращение постепенно уменьшалось. Устойчивость асфальтобетонной мастики к колейности снижалась при высокой температуре, но сопротивление колейности улучшалось за счет добавления диатомита и базальтового волокна. Все факторы колейности превышали 1,0 кПа при 70 ° C, поэтому способность DBFCMAM к колейности удовлетворяла требованиям Superpave. Эти параметры показали, что диатомит и базальтовое волокно могут обеспечивать лучшую стойкость к колейности при высокой температуре эксплуатации. 3.4. Испытание на реометре изгибающейся балки (BBR)Жесткость на ползучесть и скорость (наклон) ползучести DBFCMAM определяли при различных температурах с помощью реометра изгибающей балки (BBR) в SHRP в США.Для SHRP обычно требуется МПа [26]. Чем меньше было, тем лучше криогенная гибкость и недеформируемость модифицированной асфальтобетонной мастики; была выше, жесткость асфальта при ползучести была ниже, способность асфальтовой мастики к релаксации криогенных напряжений была лучше, а характеристики при низких температурах были лучше. С помощью данных, полученных в ходе испытания BBR, можно оценить низкотемпературные характеристики различного содержимого DBFCMAM. Получив среднее значение трех параллельных тестов, результаты при низкой температуре (-12 ° C) были представлены на рисунках 6 и 7. Согласно рисунку 6, когда содержание базальтового волокна было постоянным, по мере того как содержание диатомита увеличивалось и увеличивалось. Если содержание диатомита было постоянным, содержание базальтовых волокон увеличивалось, что приводит к увеличению. Там по мере увеличения содержания диатомита и базальтового волокна увеличивались. Значения DBFCMAM были выше по сравнению с чистым асфальтом. Когда содержание было (5%, 1%), было похоже на чистый асфальт. Согласно рисунку 7, значения были ниже, чем у чистого асфальта.Значение сначала уменьшалось, а затем увеличивалось по мере увеличения содержания диатомита и базальтовых волокон. Низкотемпературная жесткость DBFCMAM на ползучесть была больше, чем у чистого асфальта, что указывает на то, что там, где были добавлены диатомит и базальтовое волокно, вязкость и жесткость асфальтовой мастики увеличивались, тогда как ударная вязкость снижалась, а способность к релаксации напряжений ослаблялась. Таким образом, низкотемпературная производительность DBFCMAM снизилась. При -12 ° C было ниже 300 МПа, -значение превышало 0,3 в рамках требований SHRP; Таким образом, DBFCMAM соответствует требованиям к рабочим характеристикам при низких температурах при –12 ° C. Данные испытания BBR показали, что добавление диатомита и базальтового волокна не улучшило низкотемпературные характеристики асфальтовой мастики. Вывод не соответствовал силе пластичности. Противоречивые выводы испытаний BBR и испытания на пластичность по усилию были вызваны различными условиями испытаний и механизмом испытаний двух испытаний. В испытании BBR были получены значения напряжения изгиба и деформации изгиба, которые использовались для расчета жесткости на ползучесть () и скорости ползучести (наклон).В конце испытания BBR деформации образцов были очень низкими. Он не мог отражать сшивающий эффект базальтового волокна. И жесткость ползучести была улучшена для абсорбирующего действия диатомита. Однако в испытании на пластичность под действием силы образцы достигли предельного разрушения; базальтовые волокна играли армирующую роль. Таким образом, тест BBR, вероятно, не подходил для оценки низкотемпературных характеристик DBFCMAM. Лю и др. [26] пришли к выводу, что жесткость асфальта с базальтовым волокном была меньше, чем у чистого асфальта, в то время как значение жесткости было выше, чем у чистого асфальта при -10 ° C.Криогенные свойства асфальта были улучшены базальтовым волокном при этой температуре. Однако базальтовое волокно ослабило криогенные свойства асфальта при -20 ° C согласно результатам теста BBR, тогда как волокно могло улучшить криогенные свойства асфальтовой смеси против трещин. В этой статье заключение теста BBR при -12 ° C не согласуется с предыдущим исследованием, проведенным Liu et al. при -10 ° С. Могут быть две причины, по которым результат BBR не согласуется с Liu et al.Первый был другой температурой испытаний. Другой – это различные модификаторы (например, базальтовое волокно в исследовании Лю, диатомит и базальтовое волокно в этой статье). В [16, 43] было высказано предположение, что криогенная жесткость к ползучести модифицированной диатомитом асфальтовой мастики выше, что приводит к снижению криогенных характеристик асфальта. Таким образом, вывод этой статьи не полностью согласуется с выводом Liu et al. Однако в этой статье заключение испытания силовой пластичности согласуется с выводом Liu et al.что криогенные свойства асфальтовой смеси против растрескивания были улучшены. Поэтому мы рекомендуем, чтобы испытание на пластичность было более надежным для оценки свойств DBFCMAM на растяжение при низких температурах. 4. ВыводыВ данной работе исследованы свойства асфальтовой мастики, модифицированной диатомитом и базальтовым волокном; с помощью лабораторных экспериментов можно было сделать следующие выводы. () В соответствии с тестом на проникновение конуса, тестом на точку размягчения и тестом на вязкость глубина конуса была уменьшена, тогда как напряжение сдвига, точка размягчения и вязкость увеличились, когда к асфальтовой мастике были добавлены диатомит и базальтовое волокно.Следовательно, асфальт на основе диатомитовых и базальтовых волокон (DBFCMAM) имел лучшую стойкость к колейности при высокой температуре по сравнению с чистым асфальтом; высокая термостойкость асфальтовой мастики была улучшена диатомитом и базальтовым волокном. () Тест DSR продемонстрировал, что после добавления диатомита и базальтового волокна комплексный модуль сдвига и коэффициент колейности () увеличились, а фазовый угол ( δ ) уменьшился. Добавление диатомита и базальтового волокна значительно улучшило жесткость и эластичность асфальтовой мастики; поэтому характеристики DBFCMAM при высоких температурах резко увеличились по сравнению с чистым асфальтом. () Низкотемпературные характеристики асфальтовой мастики были улучшены за счет добавления диатомита и базальтового волокна в соответствии с результатами испытания на пластичность. Испытание BBR было сочтено неподходящим для оценки низкотемпературных характеристик DBFCMAM, поскольку испытание BBR не могло отразить эффект сшивки базальтового волокна. Конфликт интересовАвторы заявляют об отсутствии конфликта интересов в отношении публикации этой статьи. БлагодарностиАвторы выражают признательность за финансовую поддержку Национальному фонду естественных наук Китая в рамках грантов №№. 51678271, 51508150 и 51408258, Программа развития научных технологий провинции Цзилинь (20160204008SF) и Проект транспортной науки и технологий провинции Цзилинь (2015-1-13). Паспорт безопасности битумной мастикиПАСПОРТ БЕЗОПАСНОСТИ БИТУМНАЯ МАСТИКАРАЗДЕЛ 1: ИДЕНТИФИКАЦИЯ ВЕЩЕСТВА / СМЕСИ И КОМПАНИИ / ПРЕДПРИЯТИЯ 1.1. Идентификатор продукта Название продукта БИТУМНАЯ МАСТИКА 1.2. Соответствующие установленные области применения вещества или смеси и нерекомендуемые области применения 1.3. Реквизиты поставщика паспорта безопасности Поставщик ATDM CO.LTD00982188552948 1,4. Телефон экстренной связи 00982188729845 (круглосуточно) РАЗДЕЛ 2: ИДЕНТИФИКАЦИЯ ОПАСНОСТИ БИТУМНОЙ МАСТИКИ2.1. Классификация вещества или смеси Классификация (1999/45 / EEC) Carc. Кот. 3; R40. N; R51 / 53. R10. 2.2. Элементы этикеток содержит ТОПЛИВО, ДИЗЕЛЬ № 2; ГАЗОЙЛ – НЕ УКАЗАННАЯ маркировка Фразы риска Фразы безопасности 2.3. Прочие опасности Вредно Опасно для окружающей среды R10 Легковоспламеняющийся. R40 Ограниченные доказательства канцерогенного действия. R51 / 53 Токсично для водных организмов, может вызывать долговременные неблагоприятные изменения в водной среде. S2 Хранить в недоступном для детей месте. S13 Хранить вдали от продуктов питания, напитков и кормов для животных. S29 / 56 Не сливать в канализацию, утилизировать этот материал и его контейнер в пунктах сбора опасных или специальных отходов. S36 / 37/39 Пользоваться подходящей защитной одеждой, перчатками и средствами защиты глаз / лица. S46 При проглатывании немедленно обратиться к врачу и показать этот контейнер или этикетку. S51 Использовать только в хорошо вентилируемых помещениях. S61 Избегать попадания в окружающую среду. См. Специальные инструкции / паспорта безопасности. РАЗДЕЛ 3: СОСТАВ / ИНФОРМАЦИЯ ОБ ИНГРЕДИЕНТАХ 3.2. Смеси
Полный текст всех фраз риска и указаний на опасность отображается в Разделе 16. Комментарии к композиции Продукт содержит диоксид кремния, который в том виде, в котором он поставляется, не опасен, однако следует избегать вдыхания пыли, образующейся от высушенного материала. РАЗДЕЛ 4: МЕРЫ ПЕРВОЙ ПОМОЩИ 4.1. Описание мер первой помощи Вдыхание Немедленно удалите пострадавшего от источника воздействия. Немедленно выведите пострадавшего на свежий воздух.Обратитесь за медицинской помощью. Проглатывание НЕ вызывать рвоту. Немедленно обратитесь за медицинской помощью. Контакт с кожей Немедленно промойте загрязненную кожу водой с мылом или мягким моющим средством. Немедленно снимите одежду в случае проникновения и промойте кожу водой. Немедленно обратитесь за медицинской помощью, если после мытья появятся симптомы. Попадание в глаза Немедленно промыть глаза водой. Продолжайте полоскание в течение как минимум 15 минут и обратитесь за медицинской помощью. 4.2. Наиболее важные симптомы и воздействия, как острые, так и замедленные 4.3. Указание на необходимость немедленной медицинской помощи и специального лечения РАЗДЕЛ 5: МЕРЫ ПОЖАРОТУШЕНИЯ 5.1. Средства пожаротушения Средства пожаротушения Используйте средства пожаротушения, подходящие для окружающих материалов. 5.2. Особые опасности, исходящие от вещества или смеси 5.3. Совет пожарных Средства защиты пожарных Надеть автономный дыхательный аппарат РАЗДЕЛ 6: МЕРЫ ПРИ СЛУЧАЙНОМ ВЫБРОСЕ 6.1. Меры по обеспечению личной безопасности, защитное снаряжение и порядок действий в чрезвычайной ситуации Избегайте контакта с кожей и глазами. Обеспечьте соответствующую вентиляцию. Используйте средства индивидуальной защиты. Надеть автономный дыхательный аппарат. 6.2. Меры по защите окружающей среды Не допускать попадания в канализацию и водоемы. 6.3. Методы и материалы для локализации и очистки Собирать пылесосом или абсорбирующим веществом, хранить в закрытом контейнере для утилизации. 6.4. Ссылка на другие разделы РАЗДЕЛ 7: ОБРАЩЕНИЕ И ХРАНЕНИЕ 7.1. Меры предосторожности для безопасного обращения Избегайте проливания, контакта с кожей и глазами. Хорошо проветривайте, избегайте вдыхания паров. Используйте одобренный респиратор, если загрязнение воздуха превышает допустимый уровень. 7.2. Условия безопасного хранения с учетом несовместимости Хранить при умеренных температурах в сухом, хорошо вентилируемом помещении. Класс хранения Токсичное хранилище. 7.3. Специфическое конечное использование РАЗДЕЛ 8: КОНТРОЛЬ ВОЗДЕЙСТВИЯ / ЛИЧНАЯ ЗАЩИТА 8.1. Параметры контроля
WEL = предел воздействия на рабочем месте. Комментарии к ингредиентам WEL = Пределы воздействия на рабочем месте 8.2. Средства контроля воздействия Средства защиты Технические мероприятия Обеспечьте соответствующую общую и местную вытяжную вентиляцию. Респираторное оборудование Если вентиляция недостаточна, необходимо обеспечить соответствующую респираторную защиту. Надевайте маску, входящую в комплект поставки: Газовый баллончик для органических веществ. Защита рук Необходимо использовать защитные перчатки, если существует риск прямого контакта или брызг.Используйте защитные перчатки из: Нитрила. Используйте тонкие хлопчатобумажные перчатки под резиновыми перчатками, если есть риск аллергии. Защита глаз Носите брызгозащищенные очки для защиты глаз. Гигиенические меры В случае загрязнения кожи немедленно промыть. Мойте руки в конце каждой рабочей смены, а также перед едой, курением и посещением туалета. РАЗДЕЛ 9: ФИЗИКО-ХИМИЧЕСКИЕ СВОЙСТВА 9.1. Информация об основных физико-химических свойствах Фиброзная паста для внешнего вида Цвет Черный. Запах растворителя. Растворимость Нерастворимо в воде Относительная плотность 1,45 Температура вспышки (° C) 50 CC (в закрытом тигле). 9.2. Другая информация РАЗДЕЛ 10: СТАБИЛЬНОСТЬ И РЕАКЦИОННАЯ СПОСОБНОСТЬ 10.1. Реакционная способность 10.2. Химическая стабильность Стабилен при нормальных температурных условиях. 10.3. Возможность опасных реакций 10.4. Условия, которых следует избегать 10,5. Несовместимые материалы 10.6. Опасные продукты разложения РАЗДЕЛ 11: ТОКСИКОЛОГИЧЕСКАЯ ИНФОРМАЦИЯ 11.1. Информация о токсикологическом воздействии Общая информация Известный или предполагаемый канцероген для человека. РАЗДЕЛ 12: ЭКОЛОГИЧЕСКАЯ ИНФОРМАЦИЯ Экотоксичность Опасно для окружающей среды: Может оказывать долгосрочное вредное воздействие на водную среду. 12.1. Токсичность 12.2. Стойкость и разлагаемость 12.3. Потенциал биоаккумуляции 12.4. Подвижность в почве 12,5. Результаты оценки PBT и vPvB 12.6. Другие побочные эффекты РАЗДЕЛ 13: УТИЛИЗАЦИЯ Общая информация Этот материал классифицируется как особые отходы согласно определению Специальных правил обращения с отходами 1996 г. и должен утилизироваться уполномоченным подрядчиком. 13.1. Методы обращения с отходами Утилизируйте отходы и остатки в соответствии с требованиями местных властей. РАЗДЕЛ 14: ТРАНСПОРТНАЯ ИНФОРМАЦИЯ 14.1. Номер ООН № ООН (ADR / RID / ADN) 1133 № ООН (IMDG) 1133 № ООН (ИКАО) 1133 14.2. Собственное транспортное наименование ООН Надлежащее отгрузочное наименование КЛЕИ (НАФТА (НЕФТЬ), ГИДРОСЕРЬФУРИЗОВАННЫЙ ТЯЖЕЛЫЙ; НИЗКОЕ КИПЕНИЕ) 14.3. Класс (ы) опасности при транспортировке ADR / RID / ADN, класс 3 ADR / RID / ADN, класс 3: легковоспламеняющиеся жидкости.Наклейка ADR № 3 Класс 3 IMDG Класс / раздел 3 ИКАО Транспортные этикетки ВОСПЛАМЕНЯЮЩАЯСЯ ЖИДКОСТЬ 3 14.4. Группа упаковки ADR / RID / ADN Группа упаковки III IMDG Группа упаковки III ИКАО Группа упаковки III 14,5. Опасности для окружающей среды Вещество, опасное для окружающей среды / загрязнитель моря 14.6. Особые меры предосторожности для пользователя EMS F-E, S-D Кодекс действий в чрезвычайной ситуации • 3YE № опасности (ADR) 30 Код ограничения проезда через туннели (D / E) 14.7. Транспортировка наливом в соответствии с Приложением II MARPOL73 / 78 и Кодексом IBC .РАЗДЕЛ 15: НОРМАТИВНАЯ ИНФОРМАЦИЯ 15.1. Нормы / законодательные акты по безопасности, охране здоровья и окружающей среды, относящиеся к веществу или смеси Нормативные акты Правила о химических веществах (информация об опасностях и упаковка для поставки) 2009 г. (S.I 2009 № 716). Контроль веществ, опасных для Здоровье. Утвержденный свод правил Классификация и маркировка веществ и препаратов, опасных для поставок. Указания Пределы воздействия на рабочем месте Eh50. Введение в местную вытяжную вентиляцию HS (G) 37. . ➤ |