Лазерная резка. Принцип работы. Вопросы и ответы
Современная техника и оборудование, которое используется при работе с металлом – это высокоэффективные и мощные устройства, позволяющие обрабатывать материал быстро и с высокой точностью. Одним из наиболее эффективных способов считается лазерная обработка металла, при которой необходимы оборудование и специальные навыки.
Известно много особенностей работы с лазерным оборудованием. А чтобы понять суть этого метода обработки, стоит разобраться в принципах работы лазерной установки для резки заготовок из металла.
Резка металла лазером: особенности метода
На производствах и в мастерских применяют различные способы раскроя из листового металла заготовок с определенными параметрами. Наиболее точный и предпочтительный способ – это применение лазерной установки.
Сам по себе метод резки – это, по сути, раскрой из листового металла заготовки необходимой формы и в определенном количестве.
Если есть потребность обработать листовой металл, а при этом важна точность, то может помочь только лазерная установка. Лазерная резка – это способ раскроя металлического листа определенной толщины при использовании лазера высокой мощности.
Процесс разделения происходит за счет сфокусированного лазерного пучка на конкретную область металла. В месте контакта температура материала повышается до температуры плавления. Области вокруг не меняют свой температурный показатель, что позволяет не деформироваться краю заготовки. Линия разреза получается точной и достаточно тонкой, что позволяет сэкономить на расходном материале.
Основной принцип работы лазера для резки – это прожиг металлического листа высокотемпературным и точно сконцентрированным лучом.
В чем основные преимущества метода?
Лазерная обработка материалов имеет ряд преимуществ, которые выражены в следующем:
- нет прямого механического контакта с обрабатываемым материалом, а значит это дает возможность работать с хрупкими материалами;
- под действием направленного луча происходит плавление даже очень твердых металлов;
- высокая скорость обработки металла;
- возможность организации скоростной и непрерывной резки, что увеличивает производительность;
- процесс полностью автоматизированный, что практически полностью исключает вероятность воздействия человеческого фактора.
Существенные минусы в работе
- Достаточно большое потребление электроэнергии.
- Высокая стоимость самой лазерной установки.
- При ошибке в настройках есть вероятность порчи обрабатываемого материала.
- Высокотемпературный лазер опасен для человека.
Использование лазерного оборудования – это высокая производительность. Но по карману такое устройство только крупным производствам. Поэтому сегодня очень популярна услуга осуществления изготовления конкретных заготовок под заказ в специализированных мастерских.
Ваши вопросы – наши ответы
У простого обывателя или того, кто впервые сталкивается с таким видом обработки металла, может возникнуть масса вопросов. Мы сформулировали наиболее актуальные вопросы об особенностях применения и возможностях лазерной резки и ответили на них:
1. Что такое лазер, которым режут металл?
Лазер – это сфокусированный пучок огромной оптической энергии. За счет концентрирования высокой тепловой энергии материал, на который направляется лазер, просто испаряется или стекает по направлению, противоположному к самому лучу.
2. Какие бывают виды лазерных установок?
Есть некоторая градация типов лазерных установок, которые применяются на производствах:
- газовые;
- твердотельные;
- волоконные;
- полупроводниковые.
Но такие установки для резки – это основные аппараты. Существуют и другие устройства, которые используют иные принципы воздействия на обрабатываемый металл лазером. В основном такое оборудование изготавливается на специальных производствах. Но некоторые установки можно изготовить дома (например, газовую лазерную установку). Также все аппараты отличаются по стоимости использования и сложности управления.
3. Что можно резать лазером?
При помощи резки лазером в принципе можно разрезать любой материал. Однако все зависит от типа установки, параметров настройки и свойств самого обрабатываемого материала. Граничный показатель (за основу берется листовая сталь) – листовой материал толщиной до 35 мм. Поэтому разумно предположить, что единственным существенным ограничением для лазера является толщина обрабатываемого материала.
Здесь в основном рассматривается резка лазером металла. Но стоит сказать, что металлическими листами все не ограничивается, лазеру под силу резать дерево, пластик, акрил и многое другое. При этом резка получается точной и быстрой, без необходимости дополнительной обработки.
4. Что не под силу разрезать лазеру?
Сфокусированный высокотемпературный лазер – это мощный инструмент. Однако и для такого оборудования есть свои «крепкие орешки» – это любые материалы с оптическим эффектом. Ярким примером является медь (к сплавам на основе этого металла это свойство не относится).Медные, даже очень тонкие листы, лазер не в состоянии разрезать, потому что луч отражается от поверхности. При отражении тепловая энергия направляется на линзу аппарата, что становится причиной ее поломки.
Есть некоторые трудности и с резкой стекла – луч лазера проходит сквозь прозрачную поверхность. Это не относится к резке оргстекла, которое лазером режется очень просто.
5. Какой ширины разрез образовывается от лазера?
Ширина разреза лазером – это минимальное значение разреза, который можно сделать в материале. Этот показатель составляет 250 микрометров. Это и считается основной причиной экономного размещения отдельных элементов на одном листе.
6. Что из себя представляет лазерная установка?
Оборудование для лазерной резки металла по факту является столом, который служит рабочей площадкой, с движимой определенным образом лазерной головкой. На столе размещается лист обрабатываемого материала. Сама лазерная головка движется по двум осям – абсцисс и ординат. Характер движения загружается в специальный программный продукт, а также устанавливаются определенные настройки самого лазера.
7. Как справляется лазер с необходимостью резки нестандартных форм и заготовок?
Лазеру, при правильном обращении с программой, под силу изготовить заготовку любой сложности. От геометрически ровного разреза до сложных узоров – все это можно сделать при помощи лазера.
Этот факт стал главной причиной популярности такого оборудования. Лазерные установки широко используются в разных сферах, так как позволяют проделать необходимую работу эффективнее, точнее и быстрее, чем альтернативные способы обработки.
8. Остаются ли следы на заготовке, если ее резали лазером?
Резка лазером – это высокотехнологичный процесс, при котором воздействие на конкретную область среза – минимальное. За счет того, что обработка лазером происходит очень быстро, материал по обе стороны среза не успевает накалиться. Это позволяет не оставлять видимых следов по кромке изделия.
Однако лазер используется и при гравировке металла (и прочих материалов). В этом случае видимые следы, которые выполняют декоративную или функциональную задачу, являются частью технологии.
Это наиболее распространенные вопросы, которые возникают относительно лазерной обработки металлов и прочих материалов. Они позволят человеку, который не сталкивался с подобным оборудованием, понять принцип его работы и узнать некоторые его особенности. Относительно самого процесса работы, особенностей управления и так далее – это компетенция исключительно профессионалов. Но вы всегда можете обратиться в специализированный сервис, где обязательно получите подробную консультацию относительно данного вопроса, а также заказать изготовление вашего индивидуального заказа.
Принцип работы станков лазерной резки | RuAut
Недостатками механических методов резки являются: потеря материала, низкая производительность процесса, износ и поломка инструмента. Все это результат контакта инструмента с материалом. Основные недостатки термических методов резки: низкое качество реза и невозможность обработки не металлических материалов. Здесь бессильны и газопламенная и плазменные технологии. Лазерной резки поддаются практически все материалы независимо от твердости. Благодаря отсутствию механических усилий, могут разрезаться не жесткие материалы.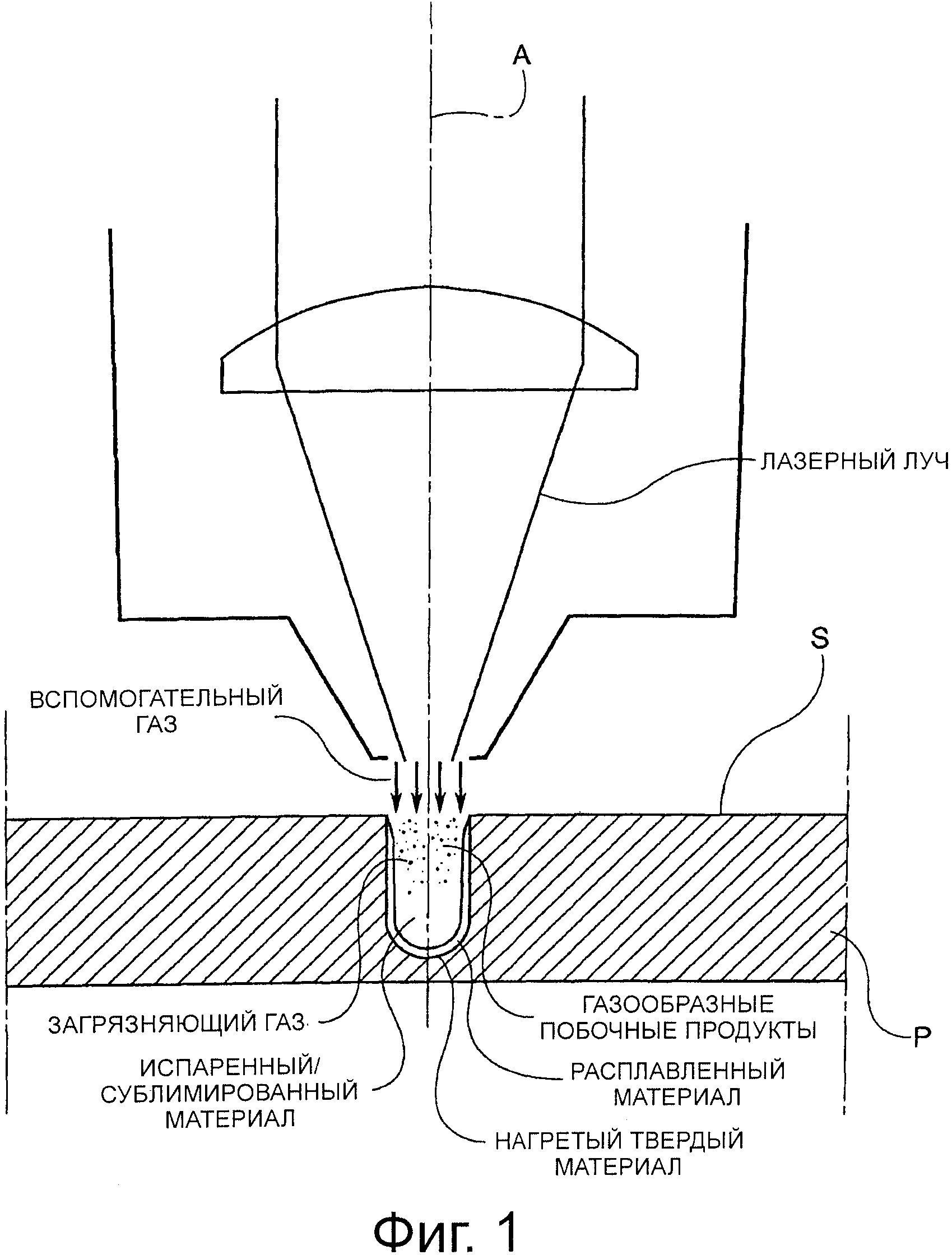
Сущность лазерной резки состоит в расплавлении, разложении или испарении материала и удалении продуктов разрушения из канала реза. При работе станка лазерной резки в режиме испарения поверхность материала разогревается до температуры кипения и вещество из канала реза удаляется в парообразном состоянии. Механизм испарения характерен для материалов у которых удельная энергия испарения мало отличается от удельной энергии плавления.
Для подачи газа в зону лазерной резки применяют специальные сопла.
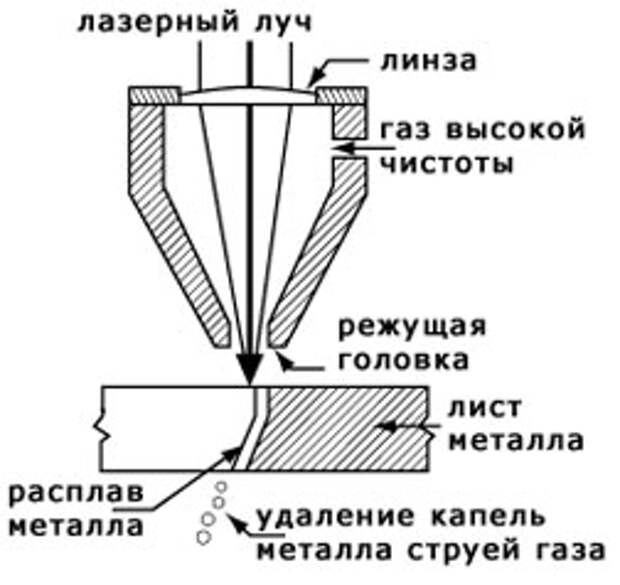
Существенное влияние на производительность процесса и качество работы станка лазерной резки оказывает распределение плотности мощности лазерного пучка. Оптимальным распределением плотности мощности считается нормальное или гауссовое. Важное значение имеет ориентация плоскости поляризации лазерного луча, определяемое положением вектора напряженности электромагнитного поля относительно направления резки. Максимальная скорость лазерной резки, минимальная ширина зоны термического влияния и параллельность кромок достигаются при совпадении плоскости поляризации и направления резки, когда энергия выделяется в основном только на лобовой поверхности резки. Поэтому при резки металлов по сложному контуру, поляризация должна быть или круговой или линейной, плоскость которой синхронно поворачивается с изменением траектории движения.

С увеличением мощности лазерного излучения глубина прорезания увеличивается, достигая 10-12 мм для металлов. И 50-60 мм для неметаллических материалов. Поэтому наиболее эффективна лазерная резка при изготовлении деталей сложного контура из листовых материалов, соответствующих диапазону толщин. В станках лазерной резки применяются твердотельные лазеры периодического действия, газовые лазеры непрерывного действия, твердотельные лазеры непрерывного действия.
От декоративных элементов садовых домиков до разнообразных деталей современных машин, таков диапазон применения станков лазерной резки.
принципы работы, виды и особенности
Лазерную резку используют для раскроя листовых материалов, чаще всего – металлов. Одно из ее главных отличий – возможность изготовления деталей со сложным контуром.
Принципы работы лазерной резки
Использование этого метода основано на тепловом воздействии лазерного излучения на материалы. При этом разрезаемый металл нагревается сначала до температуры плавления, а потом до температуры кипения, при которой он начинает испаряться. Лазерная резка испарением требует высоких энергозатрат, поэтому ее используют для работы с тонкими металлами.
Относительно толстые листы разрезают при температуре плавления. Чтобы облегчить этот процесс, в зону резки подается газ: азот, гелий, аргон, кислород или воздух. Его задача – удалять из зоны резки расплавленный металл и продукты его сгорания, поддерживать горение металла и охлаждать прилегающие зоны. Наиболее эффективен для этого кислород. Он заметно увеличивает скорость и глубину резки.
Подробнее о процессе лазерной резки можно узнать из видео ниже:
Параметры резки разных металлов
Скорость резки зависит не только от мощности лазера и толщины металла, но и от его теплопроводности. Чем она выше, тем интенсивнее отводится тепло из зоны резки и тем более энергозатратным будет весь процесс. Так, если лазером мощностью 600 Вт можно легко разреза́ть черные металлы или титан, то алюминий или медь, обладающие высокой теплопроводностью, обрабатывать значительно сложнее. Средние параметры для работы с разными металлами выглядят следующим образом:
Малоуглеродистая сталь | Инструментальная сталь | Нержавеющая сталь | Титан | |||||||
Толщина, мм | 1,0 | 1,2 | 2,2 | 3,0 | 1,0 | 1,3 | 2,5 | 3,2 | 0,6 | 1,0 |
Мощность лазера, Вт | 100 | 400 | 850 | 400 | 100 | 400 | 400 | 400 | 250 | 600 |
Скорость резания, м/мин | 1,6 | 4,6 | 1,8 | 1,7 | 0,94 | 4,6 | 1,27 | 1,15 | 0,2 | 1,5 |
Виды лазерной резки
Лазерные установки состоят из трех основных частей:
- Рабочей (активной) среды.
Она является источником лазерного излучения.
- Источника энергии (системы накачки). Он создает условия, при которых начинается электромагнитное излучение.
- Оптического резонатора. Система зеркал, усиливающих лазерное излучение.
По типу рабочей среды лазеры для резки делят на три вида:
- Твердотельные. Их основным узлом является осветительная камера. В ней находятся источник энергии и твердое рабочее тело. Источником энергии служит мощная газоразрядная лампа-вспышка. В качестве рабочего тела используют стержень из неодимового стекла, рубина или алюмо-иттриевого граната, легированного неодимом или иттербием. По торцам стержня устанавливают два зеркала: отражающее и полупрозрачное. Лазерный луч, излучаемый рабочим телом, многократно отражается внутри него, усиливается в ходе отражений и выходит через полупрозрачное зеркало.
К твердотельному виду относятся и волоконные лазеры. В них излучение усиливается в стекловолокне, а источником энергии служит полупроводниковый лазер.
Так устроен твердотельный лазер
Для понимания механизма работы лазера можно рассмотреть установку с рабочим телом в виде стержня из граната, легированным неодимом. Ионы последнего и служат активными центрами. Поглощая излучение газоразрядной лампы, ионы переходят в возбужденное состояние, то есть у них появляется излишек энергии.
Ионы возвращаются в исходное состояние и отдают энергию в виде фотона – электромагнитного излучения или по-другому света. Фотон вызывает переход в обычное состояние других возбужденных ионов. В итоге процесс нарастает лавинообразно. Зеркала способствуют движению луча в определенном направлении. Многократно возвращая фотоны в рабочее тело при отражении, они способствуют образованию новых фотонов и усилению излучения. Его основные характеристики – малая расходимость луча и высокая концентрация энергии.
- Газовые. В них рабочим телом является углекислый газ или его смесь с азотом и гелием.
Газ прокачивается насосом через газоразрядную трубку. Он возбуждается с помощью электрических разрядов. Для усиления излучения устанавливают отражающее и полупрозрачное зеркало. В зависимости от особенностей конструкции такие лазеры бывают с продольной и поперечной прокачкой, а также щелевые.
Так устроен газовый лазер с продольной прокачкой
- Газодинамические. Эти лазеры самые мощные. В них рабочим телом является углекислый газ, нагретый до 1 000–3 000 °К (726–2726 °С). Он возбуждается с помощью вспомогательного маломощного лазера. Газ со сверхзвуковой скоростью прокачивается через суженный посередине канал (сопло Лаваля), резко расширяется и охлаждается. В результате его атомы переходят из возбужденного в обычное состояние и газ становится источником излучения.
Схема работы газодинамического лазера
Преимущества и недостатки лазерной резки
Можно выделить следующие преимущества лазерной резки металлов:
- Нет механического контакта с поверхностью разрезаемого металла.
Это делает возможным работу с легкодеформируемыми или хрупкими материалами.
- Можно разрезать металлы разной толщины. Сталь в пределах 0,2–30 мм, алюминиевые сплавы – 0,2–20 мм, медь и латунь – 0,2–15 мм.
- Высокая скорость резки.
- Возможность изготовления изделий с любой конфигурацией.
- Чистые кромки разрезаемого металла и низкое количество отходов.
- Высокая точность работы – до 0,1 мм.
- Экономный расход листового металла за счет более плотной раскладки деталей на листе.
Недостатками лазерной резки считаются высокое энергопотребление, дорогое оборудование.
Назначение и критерии выбора лазерной резки
Лазерную резку используют для обработки не только металлов, но и резины, линолеума, фанеры, полипропилена, искусственного камня и даже стекла. Она востребована при изготовлении деталей для различных приборов, электротехнических устройств, сельскохозяйственных машин, судов и автомобилей. Такой способ раскроя материала используют для получения жетонов, трафаретов, указателей, табличек, декоративных элементов интерьера и многого другого.
Основной критерий выбора вида лазерной резки – тип обрабатываемого материала. Так, углекислотные лазеры подходят для резки, гравировки, сварки разных материалов – металла, резины, пластика, стекла.
Твердотельные волоконные установки оптимальны при раскрое латунных, медных, серебряных или алюминиевых листов, но не подходят для неметаллов.
Полезная информация / Принцип обработки металла лазером
Лазерная обработка металла как вид обработки появилась, по историческим меркам, совсем недавно. Но уже успела прочно занять свое место в промышленности. Сейчас практически ни одно промышленное предприятие не обходится без аппарата лазерной резки металла. А такая область как микроэлектроника, возможно, и не существовала бы, во всяком случае, такого уровня достигнуть ей не удалось бы.Перечень операций выполняемых лазером в промышленности огромен, но все они в итоге сводятся к резке и сварке металлов. Это, собственно, вытекает из свойств лазерного луча – концентрация огромной энергии на маленькой площади.

Для того чтобы прожечь стальную пластинку толщиной 1 мм достаточно энергии лазера всего лишь в половину джоуля и одной миллисекунды. И мы получим красивое изящное отверстие диаметром в одну-две десятые доли миллиметра. Лучом такой мощности можно сваривать тонкую фольгу или проволоку. Для того чтобы резать сталь толщиной в пять миллиметров уже потребуется увеличить энергию лазера до 20 и даже до 100 джоулей.

Существует огромное множество видов лазеров по виду активного, рабочего вещества. Самые первые лазеры строились на кристалле искусственного рубина. Они обладают сравнительно невысокой мощностью. Сейчас широко используются полупроводниковые лазеры в бытовой электронике и технике связи, а также газовые лазеры, широко распространенные в промышленности, применяемые для резки и сварки металлов и других материалов.
Принцип лазерной резки металла | ТК Ноябрь
Разделительные операции с различными металлами – основа всех процессов их последующей обработки. Каждая из технологий резки имеет свои области рационального применения. Например, резка пластическим сдвигом используется в крупносерийном и массовом производстве, газопламенная резка – при единичном и т.д. Во многих случаях единственным способом получения исходных заготовок считается лазерная резка.
Разделение металлов при помощи лазерного луча
В основу лазерной резки положен принцип концентрированного локального выделения значительной тепловой энергии, и её последующего воздействия на разделяемые поверхности металла. При этом не имеет значения, токопроводящим ли является материал заготовки или нет (эта особенность лазерного разрезания широко используется при лазерной обработке гранита, кварца, керамики и прочих материалов – изоляторов).
Необходимыми составляющими процесса лазерной резки являются:
- Оптический квантовый генератор как источник излучения (газоразрядная лампа).
- Собирающая линза, при помощи которой происходит фокусирование светового потока.
- Режущая головка.
- Источник вспомогательного газового потока, назначение которого обеспечить огнебезопасность зоны раздела и эвакуировать частицы металла, которые оказались под линией реза.
- Узел охлаждения лазерной головки.
- Механизмы для программированного перемещения инструментальной головки (или заготовки) в соответствии с направлением линии раздела металла.
Процесс особенно эффективен в случае разделения тонких материалов – плёнки, фольги – толщина которых не превышает 2…5 мм. Для заготовок большей толщины удельная энергоёмкость процесса становится весьма значительной, а, следовательно, и неконкурентоспособной с альтернативными технологиями резки металлов.
Установки лазерной резки различаются:
- По своей производительности (удельной тепловой мощности, которую способны ввести в зону разделения).
- По частоте возбуждения лазерного луча в единицу времени (скважности импульсов).
- По внешним условиям протекания лазерного разряда (в воздухе или в жидкости).
- По направлению подачи вспомогательного газа (чаще всего – аргона), ответственного за эвакуацию продуктов эрозии из зоны обработки.
- По способу управления процессом – полуавтоматический, автоматический, программный (ручные установки для лазерной резки используются в основном, для лабораторных целей).
Параметры лазерного разрезания металлов и сплавов
Выбор подходящей установки производится по следующим факторам:
- По энергии излучения генератора лазерного излучения.
- По величине фокусного расстояния системы управления лучом и по пределам его требуемого смещения.
- По длительности импульса.
- По количеству импульсов в единицу времени.
- По виду металла обрабатываемой заготовке (значение имеют его теплофизические параметры – теплопроводность и теплоёмкость, а механические – твёрдость и прочность – несущественны).
Гамма современных станков, предназначенных для лазерной резки довольно обширна. Например, в часовой промышленности используется оборудование малой энергоёмкости (не более 1 Дж), зато с повышенной точностью обработки и толщиной линии раздела, исчисляемой микронами. Наоборот, для резки заготовок металла с большими размерами энергия излучения достигает нескольких сотен джоулей.
Практически градация оборудования производится не по энергии излучения, а по величине напряжения накачки газоразрядной лампы. В свою очередь, это напряжение определяется ёмкостью конденсаторной батареи накопителя питающего блока, которые запасает энергию, а затем отдаёт её рабочему разрядному контуру.
Стабильность работы квантового генератора зависит от тепловых процессов, которые развиваются в процессе лазерной резки. Поэтому рабочий контур режущей головки нуждается в постоянном охлаждении: в противном случае оптические элементы головки быстро стареют, и КПД установки снижается. Прогрессивным вариантом является ведение процесса лазерного разделения металла под небольшим (до 10…15 мм) слоем жидкости, в качестве которой используют четырёххлористый углерод, а то и обычную воду.
Совокупность всех энергетических параметров лазерного луча – скважность, толщина, расстояние до обрабатываемого металла – определяет эффективность лазерной резки.
Последовательность процесса лазерной резки
Вначале заготовку, подлежащую разделению, позиционируют на столе, и при помощи программы ЧПУ устанавливают траекторию перемещения инструментальной головки.
Далее включают блок накачки контура квантового генератора, и производят накопление энергии. Фокусируют лазерный луч (диаметр пятна обычно не превышает 0,5…0,8 мм, в зависимости от разрезаемого металла, при точности фокусировки ±0,005…0,1 мм).
Непосредственно перед началом процесса резки в зону разделения подают струю инертного газа. Осуществляют подачу инструментальной головки к поверхности заготовки на требующийся зазор.
При обычной продолжительности импульса от 0,1·10-3 до (8…10)·10-3с начинается процесс размерного испарения металла, с последующим выдуванием микрочастиц при помощи аргонной струи. Длительность фазы импульса подбирается такой, чтобы исключить возможное проплавление металла, которое сопровождается резким ухудшением качества поверхности раздела.
Ведение процесса лазерной резки под слоем рабочей жидкости обеспечивает лучшее охлаждение торцов разрезаемого металла, которые весьма сильно нагреваются, особенно, если частота следования импульсов высока.
Выбор оптимального режима резки (прежде всего, производительности и качества) зависит от металла. Например, по мере снижения производительности металлы и сплавы можно расположить в следующий ряд: медь и её сплавы→алюминий и его сплавы→нержавеющие стали→углеродистые стали→тугоплавкие металлы. В отношении роста шероховатости торцов на линии реза зависимость несколько иная: тугоплавкие металлы→медь и её сплавы→алюминий и его сплавы→нержавеющая сталь→углеродистая сталь. Из этого следует, что применение принципа лазерной резки к тугоплавким металлам и сплавам нецелесообразно.
Преимущества и недостатки лазерной резки
Лазерная резка пригодна для разделения любых плотных материалов, как кристаллических, так и аморфных (например, пластмассы). При этом со стороны лазерного луча не прикладываются никакие механические усилия, которые могли бы вызвать хрупкое раскалывание материала под воздействием значительного перепада температур.
Поскольку лазерный луч проходит сквозь любую прозрачную среду, то обработку металлических изделий можно вести изолированно, например, в ёмкостях. Лучу доступны любые поверхности, к которым невозможно подвести иной разделительный инструмент. Тепловая энергия лазера может быть легко сконцентрирована в очень малых объёмах, при этом не требуется каких-либо направляющих приспособлений и узлов.
Лазерный принцип резки обеспечивает очень высокую производительность, поскольку одновременно с разделением металла можно проводить и контроль качества поверхности раздела. Работают такие установки тихо, и обеспечивают высокую стерильность производства.
К недостаткам процесса относятся невозможность разрезания заготовок большой толщины, а также повышенную энергоёмкость установок.
метод резки, технические характеристики, физические возможности
Автор perminoviv На чтение 4 мин Просмотров 15 Опубликовано
Лазерная резка – наиболее оптимальный и технологичный способ обработки различных видов металла. Этот способ обработки металла активно применяется в промышленном производстве и составляет более 35 % всего использования лазера. Лазерная резка имеет ряд конкурентов: механическое резание с использованием полотен, абразивов и фрез, газокислородная и плазменная резка. Однако, по сравнению с традиционными методами резки, использование лазера при обработке тонколистового металла, имеет ряд неоспоримых преимуществ, таких как: простота, скорость резки и качество поверхности реза.
Хотя современное оборудование лазерной резки имеет ряд преимуществ, но оно также имеет ряд ограничений для дальнейшего увеличения скорости обработки. Учет деформации тонколистового проката, что возникает при нахождении его в рулоне без дальнейшей правки, а также температурные изменения в материале во время интенсивного нагрев места реза являются одними из таких ограничений.
Чрезвычайно важным является соблюдение стабильной фокусного расстояния относительно листа, раскраивать, особенно на высоких скоростях и ускорениях перемещения режущей головки лазера.
С целью увеличения точности обработки, наращиванием темпов производства применяют лазерную резку.
Применение лазерной резки металла можно назвать самым высокотехнологичным и современным способом обработки металла. Сфокусированное лазерное излучение, которое обеспечивает высокую концентрацию энергии в одной точке, дает возможность разрезать почти все металлы и сплавы, независимо от их тепловых и физических свойств.
Раскрой металла происходит за счет сквозного прожига листа металла точно сфокусированным лазером. При этом степень термического воздействия на окружающую поверхность минимальна, никаких существенных изменений в структуре металла не происходит. Лазерная резка металла происходит на специальных станках которые предназначены для лазерной резки. Управление лазером осуществляется с помощью вычислительной техники. Передовые станки позволяют производить резку с точностью до сотых долов миллиметра. Современные лазерные установки способны излучать лазерный луч для резки металла толщиной 45 мм (резка сжатым кислородом) и 50 мм (резка азотом). Лазерная режущая головка с помощью ЧПУ и новейших поводов способна развивать осевое ускорение до 30 м/с2 и развивать скорость позиционирования до 10 м/с, что обеспечивает максимальную производительность за счет уменьшения времени холостого хода.
Лазерная резка основано на действии когерентного луча монохроматического света, излучаемого лазером. Лазеры позволяют получать фокальное пятно, диаметр которого составляет 0,1 мм, и, как следствие, мощность излучения в фокусе до 5 МВт/см2, благодаря этому процесс происходит при большой скорости и толщина шва и зона термического влияния невелики. Толщина металла, режется не должна превышать 20…25 мм. Преимуществами способа является экономичность, возможность получения деталей разнообразных форм с точностью 0,05 мм без неровных поверхностей резания, автоматизация и роботизация процесса.
При создании изделий методом лазерной резки луч фокусируется на заданной стенке и прожигает требуемое отверстие. Отличная управляемость процесса прожига также увеличивает точность отверстий.
Лазерная резка металла применение
Резка по металлу лазером одним из наиболее эффективных методов резки металлов и сплавов. Особенностью этого процесса является то, что характерное время перестройки кристаллической структуры в металлах и сплавах в условиях лазерной обработки становится равным времени нагрева и охлаждения. Основными преимуществами этого процесса являются:
- отсутствие остаточных деформаций;
- возможность формирование в чугунах стали структур, имеющих высокую износостойкость и твердость;
- возможность управления геометрическими размерами упрочненных слоев.
С физической точки зрения процесс резка приповерхностного слоя металлов и сплавов сводится к получению структур, затрудняющих протекание процессов пластической деформации, то есть к созданию препятствий движению дислокаций.
На сегодняшний день выполнено большое количество теоретических и экспериментальных исследований, посвященных изучению физико-химических процессов, протекающих в материалах при воздействии лазерного излучения. Доказано и научно обоснованно, одними из основных факторов, которые существенно влияют на тепловое состояние материала во время обработки лазерным лучом, распределение мощности пучка на обрабатываемой поверхности, размеры и форма его сечения. Удачный выбор этих характеристик позволяет более эффективно использовать энергию излучения и значительно расширить технологические возможности лазерной обработки.
Лазерная резка позволяет изготавливать минимальные партии деталей или даже единичные образцы без траты значительных средств. Большая плотность мощности лазерного излучения создает высокую производительность процесса в сочетании с отличным качеством разрезаемых деталей. Несложное и сравнительно легкое управление лазерным лучом дает возможность делать резку по усложненному контуру плоских и объемных изделий и заготовок с большой степенью автоматизации процесса. Как осуществляется лазерная резка металла можно посмотреть по фото.
В отличие от электронно-лучевого метода, лазерная обработка выполняется вне вакуумной камерой. Устройство состоит из блока питания и лазерной головки. Число импульсов за минуту регулируется в пределах 0,25-12. В наше время лазерная обработка широко применяется при сверлении твердых материалов (алмазов, вольфрама, коррозионно стойких сталей).
Технология лазерной резки металла
- Информация о материале
Создано: 17 декабря 2012
Просмотров: 5258
Сегодня можно увидеть, что лазерная резка металла применяется почти во всех отраслях, которые связаны с металлопрокатом и с каждым днем спрос на этот вид услуг только возрастает.
Принцип функционирования лазерной резки металла
Лазерная резка листового металла осуществляется с применением кислорода, выполняющего роль вспомогательного газа. Рассматривая детальнее причины сколь высоко качество лазерного кроя, нужно отметить следующее.
Известно, что узконаправленный световой поток может нагревать предметы до неимоверно высоких температур. В этом случае лазер – это поток, который отличается небольшим диаметром и значительной интенсивностью. При попадании на какую-либо поверхность он нагревает ее. Температура места, куда воздействует лазер, настолько высока, что металл в точке контакта начинает быстро плавиться.
Но, не смотря на это, прилегающие к потоку лазера участки металла остаются неповрежденными и нагретыми. Точное и направленное передвижение луча лазера обеспечивает тонкий срез с гладкими краями. Лазер может разрезать абсолютно любые металлы. На сегодняшний день есть только одно ограничение по толщине металла. Лазер может разрезать металлы шириной не более 25 мм. Если же пробовать резать более толстые листы, то возникает вероятность некачественного среза. В настоящее время лазерная резка металла совмещает в себе 2 типа работ, а именно резка и раскрой.
Лазерная резка в работе
Обычно качественное оборудование, предназначенное для лазерной резки металла достаточно дорогостоящее, но эффективное. Стоимость раскроя выполненного с использование этого устройства выше, чем эта же услуга, но выполненная вручную. Но разница все, же очевидна. Измеряется точность лазерной резки металла в микронах, а не в миллиметрах и контролируется программным обеспечением. Благодаря компьютеру возможен раскрой не единиц, а сотен и даже тысяч сложных и маленьких деталей, к тому же за короткое время.
Сложно не согласиться с тем, что за такую работу не возьмется не один токарь какой бы квалификации он не был. Скорость резки металла лазером превышает скорость электроэрозионной обработки. Также существует возможность бесконтактного обрабатывания заготовок, что содействует улучшению не только производительности труда, но и рентабельности предприятия, т. к. временные издержки в производстве значительно сокращаются. Стоит подчеркнуть, что этот тип резки позволяет существенно сократить расходы материала для выполнения разнообразных заданий.
Тонкий луч лазера разрезает металл с небольшим расстоянием между деталями. Помимо этого, режущие инструменты не давят на лист, а значит, он не прогибается и вероятность возникновения брака сводиться к минимуму.
Выгодна лазерная резка металла не только во время работы со сложными деталями, к которым обычно предъявляются высокие требования, со сложными и большими проектами. Кроме этого такой метод резки наиболее эффективен по сравнению с его аналогами.
В результате лазерной резки металла края получаются без заусениц. Они не требуют дополнительной обработки и полностью пригодны для работы. Лазерная технология резки металлического материала является первым шагом в совершенствовании производства металлоконструкций.
Лазерная резка – Процессы резки
Произведено из слов L ight A Усиление S Timulated E Миссия R Лазеры с пробегом были олицетворением эффективности и качества обработки материалов с момента их появления в шестидесятых годах.
Они предложили совершенно новую форму энергии, которая, в свою очередь, нашла применение в производстве, медицине и связи. Лазеры, способные нагревать, плавить и даже испарять материал, считаются идеальной средой для передачи интенсивной, но контролируемой энергии.
Нажмите здесь, чтобы увидеть наши последние подкасты по технической инженерии на YouTube .Самым популярным применением лазеров является резка.
Лазерная резка
Лазерная резка – это в основном термический процесс, при котором сфокусированный лазерный луч используется для плавления материала в определенной области. Коаксиальная газовая струя используется для выброса расплавленного материала и создания пропила. Непрерывный рез производится путем перемещения лазерного луча или заготовки под управлением ЧПУ.Существует три основных разновидности лазерной резки: резка плавлением, газовая резка и дистанционная резка.
При резке плавлением инертный газ (обычно азот) используется для вытеснения расплавленного материала из пропила. Газообразный азот не вступает в экзотермическую реакцию с расплавленным материалом и, таким образом, не участвует в подаче энергии.
При газовой резке кислород используется в качестве вспомогательного газа. Помимо приложения механической силы к расплавленному материалу, это вызывает экзотермическую реакцию, которая увеличивает подвод энергии к процессу.
При дистанционной резке материал частично испаряется (удаляется) высокоинтенсивным лазерным лучом, что позволяет резать тонкие листы без вспомогательного газа.
Процесс лазерной резки поддается автоматизации с помощью автономных систем CAD / CAM, управляющих либо трехкоординатными планшетными системами, либо шестиосевыми роботами для трехмерной лазерной резки.
Повышение точности, прямоугольности кромок и управления подводом тепла означает, что лазерный процесс все больше заменяет другие методы профилирующей резки, такие как плазменная и кислородно-топливная.На рынке имеется множество современных лазерных станков для резки, которые можно использовать для резки металлов, древесины и искусственной древесины.
Характеристики резания | Преимущества |
---|---|
|
|
Как линза влияет на толщину реза?
Процесс лазерной резки включает фокусировку лазерного луча, обычно с помощью линзы (иногда с вогнутым зеркалом), в небольшое пятно, которое имеет достаточную плотность мощности для выполнения лазерной резки.
Объектив определяется его фокусным расстоянием, которое представляет собой расстояние от объектива до сфокусированного пятна. Критическими факторами, определяющими эффективность процесса, являются диаметр сфокусированного пятна (d) и глубина резкости (L).
Глубина резкости – это эффективное расстояние, на котором может быть достигнута удовлетворительная резка. Его можно определить как расстояние, на котором площадь сфокусированного пятна не превышает 50%.
Диаметр фокусного пятна лазера и глубина резкости зависят от диаметра исходного лазерного луча на линзе и фокусного расстояния линзы.Для постоянного диаметра необработанного лазерного луча уменьшение фокусного расстояния линзы фокусирующей линзы приводит к уменьшению диаметра фокусного пятна и глубины резкости. Для линз с постоянной фокусной длиной увеличение диаметра необработанного луча также уменьшает как диаметр пятна, так и глубину резкости.
Поэтому для сравнения лазеров с разными диаметрами пучка мы используем коэффициент, называемый фокусным числом f, который представляет собой фокусное расстояние F, деленное на диаметр входящего необработанного пучка D.
Требования к резке следующие:
a) высокая плотность мощности и, следовательно, малый размер сфокусированного пятна
b) большая глубина резкости для обработки более толстых материалов с разумным допуском к изменению положения фокуса.
Поскольку эти два требования противоречат друг другу, необходимо найти компромисс. Единственное другое соображение заключается в том, что чем короче фокусное расстояние, тем ближе линза к заготовке, и, следовательно, более вероятно, что она будет повреждена брызгами в процессе резки.
Фактически, можно было бы оптимизировать фокусное расстояние для каждой толщины материала, но это потребовало бы дополнительного времени на настройку при переходе от одного задания к другому, которое необходимо было бы уравновесить с увеличением скорости.На самом деле замену линзы избегают, и используется компромиссная скорость резки, если только конкретная работа не требует особых требований.
Какие типы лазерной резки используются для листового металла?
В настоящее время большая часть промышленной лазерной резки листового металла выполняется с использованием двух типов лазеров: CO 2 и волоконного.
CO
2 ЛазерЛазер CO 2 (лазер на диоксиде углерода) генерируется в газовой смеси, которая в основном состоит из диоксида углерода (CO 2 ), гелия и азота.Накачка такого лазера осуществляется с помощью электрического разряда.
CO 2 лазеры обычно излучают на длине волны 10,6 мкм. Те, которые используются для обработки материалов, могут генерировать лучи мощностью в несколько киловатт. Эффективность настенной розетки лазеров CO 2 составляет около 10%, что выше, чем у большинства твердотельных лазеров с ламповой накачкой (например, ND: YAG-лазеры), но ниже, чем у многих лазеров с диодной накачкой.
Лазер CO 2 может резать материалы большей толщины (> 5 мм) быстрее, чем волоконный лазер той же мощности.Он также обеспечивает более гладкую поверхность при резке более толстых материалов.
Лазерная резка листового металла исторически началась с лазеров CO 2 . Большинство станков для лазерной резки CO 2 представляют собой трехосные системы (X-Y, двумерное управление позиционированием с контролем высоты по оси Z).
Однако есть несколько способов достижения движения X-Y: перемещение лазерной головки, перемещение заготовки или их комбинация.
Самый популярный подход известен как система «летающей оптики», при которой заготовка остается неподвижной, а зеркала перемещаются по осям X и Y.Преимущества этого подхода в том, что двигатели всегда перемещают известную фиксированную массу. Часто это может быть намного тяжелее, чем заготовка, но его легче прогнозировать и контролировать.
Поскольку заготовка не перемещается, это также означает, что нет реального ограничения веса листа. Недостатком летающей оптики является изменение размера луча, поскольку лазерный луч никогда не бывает идеально параллельным, а на самом деле немного расходится на выходе из лазера.
Это означает, что без контроля расходимости могут быть некоторые различия в производительности резки между различными частями стола из-за изменения размера необработанного луча.Этот эффект можно уменьшить, добавив повторно коллимирующую оптику, или в некоторых системах даже используется адаптивное управление зеркалом.
Альтернативой является система «фиксированной оптики», в которой лазерная головка остается неподвижной, а заготовка перемещается по осям X и Y. Это идеальная ситуация с точки зрения оптики, но хуже с точки зрения механики, особенно для более тяжелых листов.
При относительно небольшом весе листа фиксированная оптическая система может быть жизнеспособным вариантом, но по мере увеличения веса листа точное позиционирование материала на высокой скорости может стать проблемой.
Третий вариант известен как «гибридная» система, в которой лазерная головка перемещается по одной оси, а материал перемещается по другой оси. Это часто является улучшением по сравнению с фиксированной оптикой, но все же возникает проблема с более тяжелым весом листа.
Волоконные лазеры
Волоконные лазеры относятся к семейству твердотельных лазеров. В твердотельных лазерах луч генерируется твердой средой. Волоконные лазеры, дисковые лазеры и лазеры Nd: YAG относятся к той же категории.
Луч волоконного лазера генерируется серией лазерных диодов.Затем лазерный луч передается по оптическому волокну, где он усиливается (аналогично обычному лазерному резонатору в лазерах CO 2 ). Усиленный луч на выходе из оптического волокна коллимируется и затем фокусируется линзой или вогнутой поверхностью на разрезаемом материале. Источники волоконного лазера имеют следующие преимущества:
- В отличие от обычного резонатора CO 2 , источник волоконного лазера не имеет движущихся частей (например, вентиляторов для циркуляции газа) или зеркал в источнике генерации света.Это большое преимущество с точки зрения снижения требований к техническому обслуживанию и эксплуатационных расходов.
- Волоконные лазеры обычно в два-три раза более энергоэффективны, чем СО 2 лазеры той же мощности.
- Волоконный лазер может резать тонкие листы быстрее, чем лазер CO 2 той же мощности. Это связано с лучшим поглощением длины волны волоконного лазера на фронте резки.
- Волоконные лазеры способны резать светоотражающие материалы, не опасаясь, что обратные отражения повредят машину.Это позволяет без проблем резать медь, латунь и алюминий.
Прямые диодные лазеры
Прямая диодная лазерная технология является последним достижением в области твердотельных лазеров. В этой технологии несколько лазерных лучей, излучаемых лазерными диодами с разной длиной волны, накладываются друг на друга с использованием так называемых методов объединения лучей. В отличие от волоконных лазеров, прямые диодные лазеры не включают каскад для увеличения яркости, что дает им более низкие оптические потери и более высокую эффективность подключения к розетке.Однако по той же причине прямые диодные лазеры в настоящее время имеют более низкое качество луча по сравнению с волоконными лазерами. Прямые диодные лазеры с мощностью в несколько киловатт коммерчески доступны и успешно используются для резки листового металла.
Какие трудности вызывает отражение?
Все металлические материалы отражают лазерные лучи CO 2 до тех пор, пока не будет достигнуто определенное пороговое значение плотности мощности.
Алюминий обладает большей отражающей способностью, чем углеродистая марганцовистая сталь или нержавеющая сталь, и может вызвать повреждение самого лазера.
В большинстве станков для лазерной резки используется лазерный луч, направленный перпендикулярно плоскому листу материала. Это означает, что если лазерный луч будет отражен плоским листом, он может быть передан обратно через оптику доставки луча в сам лазер, что может привести к значительным повреждениям.
Это отражение исходит не полностью от поверхности листа, а вызвано образованием ванны расплава, которая может иметь высокую отражательную способность. По этой причине простое напыление на поверхность листа неотражающего покрытия не устранит проблему полностью.
Как правило, добавление легирующих элементов снижает коэффициент отражения алюминия для лазера, поэтому чистый алюминий труднее обрабатывать, чем более традиционный сплав серии 5000.
При хороших стабильных параметрах резки вероятность отражения может быть снижена почти до нуля, в зависимости от используемых материалов. Тем не менее, по-прежнему необходимо иметь возможность предотвратить повреждение лазера при разработке условий или в случае, если что-то пойдет не так с оборудованием.
«Система резки алюминия», которую использует самое современное оборудование, на самом деле представляет собой способ защиты лазера, а не инновационный метод резки. Эта система обычно представляет собой систему обратного отражения, которая может определять, слишком ли много лазерного излучения отражается обратно через оптику.
Это часто приводит к автоматической остановке лазера до того, как будет нанесен какой-либо серьезный ущерб. Без этой системы обработка алюминия сопряжена с риском, поскольку невозможно определить наличие потенциально опасных отражений.
Как работает лазерный резак? Сравнение CO2 и волокна
Лазерная резка – это повседневный метод производства металлических и неметаллических деталей. Промышленность стоимостью 4 миллиарда долларов отвечает за производство автомобилей, кораблей, машин, мебели и т. Д.
Постоянное развитие привело к появлению широкого спектра лазерных резаков, подходящих для самых разных материалов. Сегодня мы можем выбирать между CO2 и волоконными лазерами, но эта технология уходит корнями в начало прошлого века.
История лазерной резки
Laser – это аббревиатура – Light Amplification by Stimulated Emission of Radiation.Сокращенная форма необходима из-за ее основного присутствия. Резка металла – один из широко распространенных вариантов использования. Хотя многие считают это новой технологией, история лазерной резки насчитывает более ста лет.
Конечно, это гений Альберт Эйнштейн, который стоит за идеей ускорения производства. В 1917 году он изложил теоретические основы создания лазера в своей статье «Квантовая теория излучения».
Другие ученые усовершенствовали идеи Эйнштейна.Различные достижения первой половины века сделали возможными современные технологии. В середине века развитие ускорилось.
Первый прототип импульсного лазера датируется 1960 годом. Вскоре после этого появился первый газовый лазер, способный работать в непрерывном режиме. В 60-х годах лазерная резка рассматривалась как решение. Проблема, соответствующая решению, по-прежнему отсутствовала. Людям не потребовалось много времени, чтобы осознать потенциальные возможности их применения в различных отраслях.
Это привело к созданию первых серийных станков для лазерной резки в 1965 году.Western Electric, компания, производящая эти машины, использовала их для вырезания отверстий в алмазных фильерах.
Через 50 лет после статьи Эйнштейна, в 1967 году, станки для газовой лазерной резки стали использоваться для резки металлических листов толщиной 1 мм. Продемонстрированные возможности многих всколыхнули. Лазерная резка до сих пор была технологией с меньшим пропилом.
Среди поднятых голов была аэрокосмическая промышленность. Они начали использовать промышленные лазеры для резки материалов, включая титан и керамику, в 70-х годах.Это был большой шаг к современному варианту использования, поскольку раньше лазеры в основном могли резать неметаллы.
Как лазерный резак режет?
Преимущества лазерной резки сделали ее доминирующей технологией резки металла. Некоторые из основных аспектов успеха – это скорость, эффективность, точность и несколько вариантов использования, а именно резка, лазерная гравировка, маркировка и т. Д.
Есть 2 основных типа лазерных станков – углекислотные и волоконные. Принципы работы этих двух устройств отличаются друг от друга, что приводит к заметным различиям.Например, CO2-лазеры дешевле, в то время как волоконные лазеры превосходят их по эффективности, что является более поздней инновацией.
Однако предпочтение сводится к материалам, которые необходимо разрезать.
Принцип работы CO2-лазера
В начале процесса лазерной резки лазерное устройство создает луч света и направляет его через зеркала к выходному отверстию. Зеркала образуют резонатор, накапливающий световую энергию в луче.
По пути он проходит через фокусирующую линзу, концентрирующую луч.Режущая головка имеет сопло, которое направляет луч на обрабатываемую деталь. Сфокусированный лазерный луч плавит металл.
Принцип работы CO2-лазераВ процессе резки выделяется газ. При резке низкоуглеродистой стали выделяется чистый кислород, который запускает процесс горения. При лазерной резке нержавеющей стали или алюминия лазерный луч просто плавит металл. Режущим газом в этом случае является азот, чтобы выдувать расплавленный металл и поддерживать чистоту порезов.
Чтобы лазеры работали, материал должен поглощать излучаемое тепло.В случае металлов большая часть света отражается обратно. Следовательно, необходим мощный лазер, чтобы генерировать необходимое количество тепла для резки, несмотря на отражение.
Отраженный свет может повредить машину. Некоторые типы металлов, такие как медные сплавы и некоторые марки алюминия, обладают слишком высокой отражающей способностью для СО2-лазеров. Это ограничение мешает различным вариантам использования.
Принцип работы волоконного лазера
Принцип работы волоконного лазерного резака
Первые волоконные лазеры были представлены на выставке EuroBlech в 2008 году.Различные методы транспортировки лазерного луча позволили резать металлы с высокой отражающей способностью. Теперь для лазерной резки доступны такие металлы, как алюминий, латунь, медь и оцинкованная сталь.
Волоконные лазеры проще и долговечнее. Лазерный свет сначала создается блоками диодов. Затем он проходит через оптические кабели, где усиливается.
Кабели легированы редкоземельными элементами, такими как эрбий, тулий и т.п. Эти элементы используются для усиления света.Наконец, линза фокусирует свет, чтобы сформировать лазерный луч, готовый к резке. Новая система не требует ни газов, ни переналадки зеркал, ни прогрева.
Большим преимуществом волоконных лазеров является высокая скорость преобразования энергии. Около 75% принимаемой мощности преобразуется в лазерный луч. КПД лазера СО2 составляет около 20%.
Существенная разница в основном связана с низкими потерями при выработке тепла. Это делает волоконные лазеры мощностью 2 кВт сопоставимыми с более мощными аналогами на CO2.
Основные улучшения побуждают инженеров продолжать разработку этой революционной технологии. Это указание на будущее.
Тенденции будущего
Хотя большая часть рынка все еще находится под контролем СО2-лазеров, волоконные лазеры догоняют их. Теперь все более значительная доля новых продаж приходится на последние.
Стоимость обслуживания волоконных лазеров – важный аргумент. Меньше движущихся частей и меньше настроек.Это приводит к сокращению времени простоя из-за технического обслуживания.
Сегодня волоконный лазер значительно быстрее режет тонкие металлы. CO2 по-прежнему превосходит волокно при резке более толстых материалов (10 мм и более) благодаря лучшему качеству кромки.
В целом будущее волоконных лазеров кажется светлым. Производство – это традиционная отрасль, в которой изменения требуют длительного времени. Но волокно нацелено на свержение CO2 в качестве лидера в этом секторе. То же самое можно сказать об оборудовании как для «традиционной», так и для лазерной резки труб.
Важность человека
Ищете лазерную резку в Великобритании? Информации о машинном парке недостаточно для принятия решения о выборе поставщика. Доступность питания является показателем потенциальных возможностей. Однако это не гарантия качества.
Хотя резка выполняется автоматически, настройка – нет. Операторы станков играют большую роль в обеспечении окончательного качества ваших деталей. Знания и опыт позволяют им выбирать правильные параметры для каждой производственной потребности.
Таким образом, поиск подходящих производителей по-прежнему является утомительной задачей. Компания Fractory готова помочь вам в изготовлении листового металла.
Руководство по лазерной резке и станку для лазерной резки с ЧПУ
Станок для лазерной резки с ЧПУ вырезает конструкции в металлический лист.Изображение предоставлено: Андрей Армягов / Shutterstock.com
Лазерная резка – это производственный процесс, в котором используется сфокусированный мощный лазерный луч для резки материала по индивидуальной форме и дизайну.Этот процесс подходит для широкого спектра материалов, включая металл, пластик, дерево, драгоценные камни, стекло и бумагу, и позволяет производить точные, замысловатые и сложные детали без необходимости использования специального инструмента.
Доступно несколько различных типов лазерной резки, включая резку плавлением, резку окислением и разметку. Каждый процесс лазерной резки позволяет производить детали с точностью, аккуратностью и высококачественной обработкой кромок и, как правило, с меньшим загрязнением материала, физическим повреждением и отходами, чем при других традиционных процессах резки, таких как механическая резка и гидроабразивная резка.Однако, хотя лазерная резка демонстрирует определенные преимущества по сравнению с более традиционными процессами резки, некоторые производственные приложения могут быть проблематичными, например, резка световозвращающего материала или материала, требующего вторичной механической обработки и отделочных работ. Требования и спецификации, предъявляемые к конкретному процессу резки – например, материалы и их свойства, пределы потребления энергии и мощности, вторичная обработка и т. Д. – помогают определить тип процесса резки, наиболее подходящий для использования.
Несмотря на то, что каждый процесс резки имеет свои преимущества и недостатки, в этой статье основное внимание уделяется лазерной резке, излагаются основы процесса лазерной резки, а также необходимые компоненты и механика станка для лазерной резки. Кроме того, в статье исследуются различные методы и области применения лазерной резки, преимущества и ограничения этого процесса, а также проводится сравнение между лазерной резкой и другими типами процессов резки.
Станок для лазерной резки и процесс
Лазерная резка – это бесконтактный термический процесс изготовления металлических и неметаллических материалов.Чтобы процесс лазерной резки шел гладко и с оптимальной производительностью, необходимо учитывать несколько факторов, таких как конфигурация и настройки станка для лазерной резки, разрезаемый материал и его свойства, а также тип используемого лазера и вспомогательного газа.
Обзор компонентов и механики лазерных станков
В отличие от механической резки, при которой используются режущие инструменты и оборудование с механическим приводом, и гидроабразивной резки, при которой используется вода под давлением и абразивный материал, при лазерной резке используется станок для лазерной резки для выполнения надрезов, гравировки и маркировки.В то время как станки для лазерной резки различаются от модели к модели и от области применения к области применения, типичная установка включает узел лазерного резонатора, зеркала и головку для лазерной резки, которая содержит линзу для фокусировки лазера, узел сжатого газа и сопло. Базовый процесс лазерной резки включает следующие этапы:
- генерация луча
- фокусировка луча
- Нагрев и плавка локализованные
- выброс материала
- движение луча
Каждый этап является неотъемлемой частью процесса лазерной резки и при правильном выполнении обеспечивает точный разрез.
Генерация луча
Термин «лазер» происходит от аббревиатуры «ЛАЗЕР» или «Усиление света за счет вынужденной эмиссии излучения». По сути, этот акроним суммирует основные принципы лазерной генерации – стимуляции и усиления. Наряду с этими принципами в лазерном резонаторе используются процессы спонтанного излучения и стимулированного излучения для создания пучка света высокой интенсивности, который является как пространственно, так и спектрально когерентным (то есть лазерным лучом).
- Спонтанное излучение: Резонатор лазера содержит активную лазерную среду (например,g., CO 2 , Nd: YAG и т. д.), электроны которых стимулируются внешним источником энергии, например, импульсной лампой или электрической дугой. Когда среда получает и поглощает энергию, в ее атомах происходит процесс, известный как спонтанное излучение. Во время этого процесса энергия, поглощенная атомом, заставляет электроны атома на короткое время перескакивать на более высокий энергетический уровень, а затем возвращаться в свое основное состояние. По возвращении электронов в свое основное состояние атом излучает фотон света.
- Вынужденное излучение: Фотоны, производимые спонтанным излучением, перемещаются в среде, которая находится в полости лазерного резонатора между двумя зеркалами.Одно зеркало является отражающим, чтобы фотоны перемещались в среде, поэтому они продолжают распространять стимулированные излучения, а другое зеркало является частично пропускающим, что позволяет некоторым фотонам улетучиваться. Вынужденное излучение – это процесс, в котором фотон (то есть падающий фотон) стимулирует атом, который уже находится на более высоком уровне энергии. Это взаимодействие заставляет стимулированный атом перейти в основное состояние, испуская второй фотон той же фиксированной длины волны или когерентный с падающим фотоном.
Процесс распространения одного фотона излучением другого фотона усиливает силу и интенсивность светового луча. Таким образом, вынужденное излучение фотонов света (т. Е. Разновидность электромагнитного излучения) вызывает усиление света; другими словами, усиление света за счет вынужденного излучения излучения. Неправильно выровненные фотоны внутри резонатора проходят через частично пропускающее зеркало, не отражаясь в среду, создавая начальный лазерный луч.После генерации луч попадает в лазерную режущую головку и направляется зеркалами в фокусирующую линзу.
Фокусировка луча
Фокусирующая линза фокусирует лазерный луч через центр сопла на конце лазерной режущей головки, падающий на поверхность заготовки. Фокусируя луч, линза концентрирует энергию луча в меньшее пятно, что увеличивает интенсивность луча ( I ). Следующее уравнение иллюстрирует основной принцип, лежащий в основе этого происшествия:
Где P представляет мощность начального лазерного луча, а πr 2 представляет площадь поперечного сечения луча.По мере того как линза фокусирует лазерный луч, радиус ( r ) луча уменьшается; это уменьшение радиуса уменьшает площадь поперечного сечения луча, что, в свою очередь, увеличивает его интенсивность, поскольку его мощность теперь распределяется по меньшей площади.
Локальный нагрев, плавление и выброс материала
Когда луч падает на поверхность материала, материал поглощает излучение, увеличивая внутреннюю энергию и выделяя тепло. Высокая интенсивность лазерного луча позволяет ему нагревать, плавить и частично или полностью испарять локализованный участок поверхности детали.Ослабление и удаление пораженного участка материала формируют нужные порезы. Перекачиваемый в лазерную режущую головку и проходящий коаксиально к сфокусированному лучу, вспомогательный газ, также называемый режущим газом, используется для защиты и охлаждения фокусирующей линзы и может использоваться для вытеснения расплавленного материала из пропила – ширина удаляемого материала и производимого реза – и поддерживает процесс резки. При лазерной резке используются несколько различных типов механизмов резки и удаления материала, включая резку плавлением, резку с химическим разрушением, резку испарением, разметку и резку окислением.
- Резка плавлением: Также называемая резкой расплавом в инертном газе или резкой в инертном газе, резка плавлением используется станками для лазерной резки CO 2 и Nd: YAG. Лазерный луч, создаваемый режущим станком, расплавляет заготовку, и расплавленный материал выталкивается через дно пропила струей используемого вспомогательного газа. Используемый вспомогательный газ и давление вспомогательного газа зависят от типа разрезаемого материала, но инертный газ всегда выбирается на основании отсутствия у него химической активности по отношению к материалу.Этот механизм подходит для лазерной резки большинства металлов и термопластов.
- Химическое разложение: Химическое разложение используется в станках для лазерной резки CO 2 и подходит для лазерной резки термореактивных полимеров и органических материалов, таких как дерево. Поскольку термореактивные и органические материалы не плавятся при воздействии тепла, лазерный луч вместо этого сжигает материал, превращая его в углерод и дым.
- Резка испарением: Резка испарением используется станками для лазерной резки CO 2 и подходит для таких материалов, как лазерная резка акрила и полиацеталя из-за близости их точек плавления и кипения.Поскольку лазер испаряет материал, испаряется вдоль разреза, получаемая кромка обычно глянцевая и полированная.
- Разметка: Разметка используется станками для лазерной резки CO 2 и Nd: YAG для создания частичных или полностью проникающих канавок или перфораций, обычно на керамических или кремниевых стружках. Эти канавки и перфорации допускают механическое разрушение по ослабленным структурным линиям.
- Окислительная резка: Окислительная резка, также называемая газовой кислородной резкой, используется станками для лазерной резки CO 2 и Nd: YAG и подходит для лазерной резки низкоуглеродистой и углеродистой стали.Окислительная резка является одним из примеров режущего механизма резки расплава реактивного газа, в котором специально используются химически активные вспомогательные газы. Как и в случае инертности, реакционная способность вспомогательного газа зависит от разрезаемого материала. Окислительная резка, как следует из названия, использует кислород в качестве вспомогательного газа, который экзотермически реагирует с материалом. Вырабатываемое тепло ускоряет процесс резки и приводит к образованию окисленной оплавленной кромки, которую можно легко удалить струей газа, чтобы получить более чистую кромку, обрезанную лазером.
Движение луча
После начала локального нагрева, плавления или испарения машина перемещает зону удаления материала по заготовке, чтобы произвести полный рез. Станок выполняет движение за счет регулировки отражающих зеркал, управления лазерной режущей головкой или манипулирования заготовкой. Станки для лазерной резки бывают трех различных конфигураций, в зависимости от того, как лазерный луч перемещается или перемещается по материалу: движущийся материал, летающая оптика и гибридные системы лазерной резки.
- Движущийся материал: Станки для лазерной резки движущегося материала оснащены стационарным лазерным лучом и подвижной режущей поверхностью, к которой прикреплен материал. Заготовка механически перемещается вокруг неподвижной балки для выполнения необходимых резов. Эта конфигурация обеспечивает равномерное и постоянное расстояние зазора и требует меньшего количества оптических компонентов.
- Flying Optics: Станки для лазерной резки Flying optics оснащены подвижной головкой для лазерной резки и неподвижной заготовкой.Режущая головка перемещает балку по неподвижной заготовке по осям X и Y для выполнения необходимых резов. Гибкость машин с летающей оптикой позволяет резать материалы различной толщины и размеров, а также сокращает время обработки. Однако, поскольку балка постоянно движется, необходимо учитывать изменение длины балки на протяжении всего процесса. Изменяющейся длиной луча можно управлять путем коллимации (юстировки оптики), с использованием оси постоянной длины луча или с помощью адаптивной оптики или емкостной системы управления высотой, способной вносить необходимые корректировки в режиме реального времени.
- Гибрид: Гибридные станки для лазерной резки сочетают в себе свойства движущихся материалов и станков с летающей оптикой. Эти станки оснащены столом для обработки материалов, который перемещается по одной оси (обычно по оси X), и лазерной головкой, которая перемещается по другой (обычно по оси Y). Гибридные системы обеспечивают более стабильную доставку луча, уменьшают потери мощности и большую мощность на ватт по сравнению с системами летающей оптики.
Лазеры выпускаются в виде импульсных или непрерывных волновых лучей.Пригодность каждого из них зависит от свойств разрезаемого материала и требований к лазерной резке. Импульсные лучи производятся как короткие всплески выходной мощности, в то время как непрерывные волновые лучи производятся как непрерывные, с высокой выходной мощностью. Первый, как правило, используется для скрайбирования или резки с испарением и подходит для резки тонких конструкций или прокалывания толстых материалов, в то время как последний подходит для высокоэффективной и высокоскоростной резки.
Типы вспомогательных газов
При лазерной резке используются различные вспомогательные газы для облегчения процесса резки. Используемый процесс резки и разрезаемый материал определяют тип вспомогательного газа – инертный или активный – который наиболее подходит для использования.
Для резки в среде инертного газа (например, для резки плавлением или резки расплава в среде инертного газа), как указано в названии, используются химически инертные вспомогательные газы. Конкретный используемый вспомогательный газ зависит от реактивных свойств материала. Например, поскольку расплавленные термопласты не вступают в реакцию с азотом и кислородом, сжатый воздух можно использовать в качестве вспомогательного газа при лазерной резке таких материалов.С другой стороны, поскольку расплавленный титан реагирует с азотом и кислородом, аргон или другой химически инертный газ должен использоваться в качестве вспомогательного газа при лазерной резке этого материала. При лазерной резке нержавеющей стали в процессе резки в среде инертного газа в качестве вспомогательного газа обычно используется азот; это связано с тем, что расплавленная нержавеющая сталь химически реагирует с кислородом.
При лазерной резке материала посредством процесса реактивного сдвига расплава активный (т.е. химически реактивный) вспомогательный газ – обычно кислород – используется для ускорения процесса резки.В то время как при резке инертным газом материал нагревается, плавится и испаряется исключительно за счет мощности лазера, при резке с использованием реактивного газа реакция между вспомогательным газом и материалом создает дополнительное тепло, которое способствует процессу резки. Из-за этой экзотермической реакции резка с использованием реактивного газа обычно требует более низких уровней мощности лазера для резки материала по сравнению с уровнем мощности, необходимым при резке того же материала с помощью процесса резки инертным газом.
Давление резания используемого вспомогательного газа также определяется применяемым процессом резания, свойствами и толщиной разрезаемого материала.Например, для полимеров обычно требуется давление струи газа 2–6 бар во время процесса резки инертным газом, в то время как для нержавеющей стали требуется давление струи газа 8–14 бар. Соответственно, более тонкие материалы также обычно требуют более низкого давления, а более толстые материалы обычно требуют большего давления. При окислительной резке все наоборот: чем толще материал, тем ниже необходимое давление и чем тоньше материал, тем выше требуемое давление.
Типы станков для лазерной резки
Доступно несколько типов станков для лазерной резки, которые подразделяются на газовые, жидкостные и твердотельные.Типы различаются в зависимости от состояния активной лазерной среды, т. Е. От того, является ли среда газом, жидкостью или твердым материалом, и из чего состоит активная лазерная среда (например, CO 2 , Nd: YAG и т. Д. .). Основными двумя типами используемых лазеров являются CO 2 и твердотельные лазеры.
Один из наиболее часто используемых лазеров в газовом состоянии, CO 2 лазер, использует смесь углекислого газа в качестве активной лазерной среды. CO 2 лазеры обычно используются для резки неметаллических материалов, поскольку ранние модели не были достаточно мощными, чтобы разрезать металлы.С тех пор лазерная технология эволюционировала, чтобы позволить лазерам CO 2 прорезать металлы, но лазеры CO 2 по-прежнему лучше подходят для резки неметаллов и органических материалов (таких как резина, кожа или дерево) и простой гравировки металлов. или другие твердые материалы. Лазеры на чистом азоте – еще один широко используемый лазер в газовом состоянии. Эти лазеры используются в тех случаях, когда требуется, чтобы материал не окислялся при резке.
Доступно несколько разновидностей твердотельных лазеров, в том числе кристаллические и волоконные лазеры.В кристаллических лазерах используются различные кристаллические среды, например, иттрий-алюминиевый гранат, легированный неодимом (Nd: YAG) или ортованадат иттрия, легированный неодимом (Nd: YVO 4 ), что позволяет производить лазерную резку металлов и неметаллов с высокой мощностью . Хотя лазеры на кристаллах универсальны в отношении режущих возможностей материалов, они обычно более дороги и имеют более короткий срок службы, чем другие типы лазеров. Волоконные лазеры предлагают более дешевую и долговечную альтернативу кристаллическим лазерам. Этот тип лазера сначала генерирует луч через серию лазерных диодов, который затем передается по оптическим волокнам, усиливается и фокусируется на заготовке для выполнения необходимых разрезов.
Рекомендации по установке лазерной резки
Как описано в предыдущем разделе, тип лазера, подходящий для лазерной резки, в значительной степени определяется разрезаемым материалом. Однако при выборе и настройке станка для лазерной резки для конкретного применения могут быть приняты во внимание другие соображения, такие как конфигурация станка, мощность лазера, длина волны, временной режим, пространственный режим и размер фокусного пятна.
Конфигурация машины : см. Движение луча , выше
Мощность лазера : Мощность лазера или мощность может увеличивать или уменьшать общее время обработки для резки.Это происходит из-за увеличения интенсивности луча по мере увеличения мощности лазера (плотность мощности (интенсивность) = P / πr 2 ). Цена станка для лазерной резки обычно зависит от мощности лазера; чем мощнее лазер, тем дороже оборудование. Поэтому производители и мастерские должны найти баланс между затратами на обработку и затратами на оборудование при выборе лазерной машины на основе мощности лазера.
Длина волны : Длина волны лазерного луча – это пространственная длина одного полного цикла вибрации для фотона в луче.Конкретная длина волны лазерного луча частично определяет скорость поглощения излучения материалом, которая позволяет материалу нагреваться, плавиться и испаряться для получения необходимых разрезов.
Режим луча : Режим определяет, как интенсивность лазерного луча распределяется по площади поперечного сечения луча. Этот режим влияет на размер фокального пятна луча и его интенсивность, что, в свою очередь, влияет на качество резки. Обычно оптимальный режим имеет гауссово распределение интенсивности (ТЕМ 00 ).
Фокальное пятно : Луч направляется через линзу или специальное зеркало и фокусируется в небольшом пятне высокой интенсивности. Точка, в которой диаметр луча наименьший, называется фокусным пятном или фокусом. Оптимальное положение фокуса для лазерной резки зависит от нескольких факторов, включая свойства и толщину материала, форму и режим луча, тип вспомогательного газа и состояние фокальной линзы.
Материальные аспекты
Лазерная резка металлаИзображение предоставлено: Metal Works of High Point, Inc.
Лазерная резка подходит для различных металлических и неметаллических материалов, включая пластик, дерево, драгоценные камни, стекло и бумагу. Как упоминалось в предыдущих разделах, тип разрезаемого материала и его свойства в значительной степени определяют оптимальный режущий механизм, режущий газ и давление режущего газа, а также лазерный станок, используемый для лазерной резки.
В таблице 1 ниже показана пригодность каждого механизма лазерной резки, описанного ранее, для резки материала.
Таблица 1 – Пригодность механизмов лазерной резки для резки различных материаловМатериал | Резка плавлением | Химическая деструкция | Испарительная резка | Разметка | Окислительная резка |
Черный сплав | х | х | |||
Сплав цветных металлов | х | х | |||
Термопласт | х | х | |||
Термореактивный | х | х | |||
Керамика | х | х | |||
Стекло | х | х | |||
Эластомер | х | ||||
Композитный | х | х | х | ||
Дерево | х |
В таблице 2 ниже показана пригодность каждого обычно используемого вспомогательного газа для резки материала.
Таблица 2 – Пригодность вспомогательных газов для резки различных материаловМатериал (расплав) | Азот | Кислород | Аргон / инертные газы |
Термопласты | X (инертный) | X (инертный) | |
Титан | X (инертный) | ||
Нержавеющая сталь | X (инертный) | X (реактивная) | |
Углеродистая сталь | X (инертный) | X (реактивная) | |
Легированная сталь | X (инертный) | X (реактивная) | |
Алюминий | X (инертный) | X (реактивная) | |
Никель | X (инертный) | X (реактивная) | |
Медь | X (инертный) | X (реактивная) |
В таблице 3 ниже показана пригодность каждого типа лазера, описанного ранее, для резки материала.
Таблица 3 – Пригодность типов лазерных станков для резки различных материаловМатериал (расплав) | CO 2 | Азот | Nd: YAG / Кристалл | Волокно |
Металлы | X (сталь и алюминий) | х | х | |
Пластик | X (низкая контрастность) | X (высокая контрастность) | ||
Стекло | х | |||
Бумага | х | |||
Дерево | х | |||
Камень | х |
Помимо реактивных или нереактивных свойств разрезаемого материала, еще одним соображением, которое производители и рабочие мастерские могут принять во внимание при принятии решения о пригодности лазерной резки для их применения, является отражательная способность.Чем выше коэффициент отражения материала, тем больше процент излучения отражается, а не поглощается им. Эта более низкая скорость поглощения замедляет процесс резки и увеличивает время обработки, а также увеличивает требования к мощности лазера для резки материала. Материалы с высокой отражающей способностью, такие как медь и алюминий, также могут вызвать повреждение лазерного устройства, так как луч может отражаться в направлении компонентов лазерного резака.
Преимущества лазерной резки
По сравнению с другими видами резки, лазерная резка имеет несколько преимуществ.К ним относятся:
- Повышенная точность и аккуратность резки
- Более качественная кромка
- Более узкая ширина пропила
- Меньшая зона термического влияния и меньшее искажение материала
- Меньше загрязнения материалов и отходов
- Снижение затрат на техническое обслуживание и ремонт
- Повышенная безопасность оператора
Станки для лазерной резки способны вырезать широкий спектр конструкций с большей точностью и аккуратностью, чем более традиционные станки для резки.Поскольку станки для лазерной резки могут полностью управляться ЧПУ, они могут многократно и последовательно производить сложные и замысловатые детали с высокими допусками. Лазерная резка также обеспечивает высококачественные разрезы и кромки, которые обычно не требуют дополнительной очистки, обработки или отделки, что снижает потребность в дополнительных процессах отделки.
Сфокусированный луч позволяет уменьшить ширину пропила, а локализованный нагрев обеспечивает минимальное тепловое воздействие на большую часть разрезаемого материала. Меньший пропил сводит к минимуму количество удаляемого материала, а низкий подвод тепла сводит к минимуму зоны термического влияния (ЗТВ), что, в свою очередь, снижает степень термической деформации.Бесконтактный характер процесса лазерной резки также снижает риск механической деформации, особенно для гибких или тонких материалов, а также снижает риск загрязнения материала. Благодаря более жестким допускам, меньшей ширине пропила, меньшим зонам термического влияния и меньшей степени деформации материала детали, вырезанные лазером, можно расположить ближе друг к другу на материале. Такая близость конструкции снижает количество отходов материала, что со временем приводит к снижению затрат на материалы.
Хотя первоначальные вложения в оборудование для лазерной резки обычно выше, чем в другие процессы резки, эксплуатационные расходы и затраты на техническое обслуживание сравнительно низкие. Станки для лазерной резки способны выполнять множество операций и приложений без необходимости покупать или менять отдельные инструменты, разработанные по индивидуальному заказу; Эта характеристика лазерной резки снижает как общие затраты на оборудование, так и время между различными процессами и приложениями. Кроме того, поскольку лазерная резка является бесконтактным процессом, компоненты лазера испытывают меньшую усталость и, следовательно, служат дольше, чем компоненты в процессах контактной резки, таких как механическая резка или ротационная высечка.Вместе с относительной дешевизной заменяемых лазерных компонентов долговечность лазерных компонентов со временем еще больше снижает общие затраты на оборудование.
Другие преимущества лазерной резки включают снижение риска травм оператора и более тихую работу. В процессе лазерной резки практически не используются механические компоненты и он происходит внутри корпуса, поэтому риск травмирования оператора снижается. Поскольку в процессе лазерной резки создается меньше шума, улучшается и общее рабочее место.
Ограничения лазерной резки
Хотя лазерная резка демонстрирует преимущества по сравнению с другими формами резки, процесс также имеет ограничения, в том числе:
- Ассортимент подходящих материалов
- Несоответствие производительности
- Закалка металла
- Повышенное потребление энергии и мощности
- Более высокие затраты на оборудование
Как указывалось в предыдущих разделах, лазерная резка подходит для широкого спектра металлов и неметаллов.Однако разрезаемый материал и его свойства часто ограничивают пригодность некоторых режущих механизмов, вспомогательных газов и типов лазеров. Кроме того, толщина материала играет важную роль в определении оптимальной мощности лазера, давления вспомогательного газа и положения фокуса для лазерной резки. Различные материалы или толщина в пределах одного материала также требуют корректировки скорости и глубины резания на протяжении всего процесса резки. Эти корректировки создают несоответствия во времени производства, а также увеличивают время выполнения работ, особенно при больших производственных партиях.
Одним из преимуществ лазерной резки является получение высококачественных резов, которые обычно не требуют обширной вторичной очистки, обработки или отделки. Хотя в некотором отношении это является преимуществом, возникающее в результате наклепывание кромок, обрезанных лазером, может быть проблематичным для некоторых применений. Например, детали, требующие дальнейшей обработки, такой как порошковое покрытие или окраска, сначала потребуют обработки поверхности после процесса лазерной резки перед нанесением необходимого покрытия или краски.Добавление этого шага увеличивает как время выполнения, так и общие затраты на обработку.
Хотя лазерная резка может со временем снизить затраты на техническое обслуживание и материалы, для некоторых производственных приложений может быть более рентабельным использование других процессов резки. Например, хотя лазерной резкой можно подвергать как металлические, так и неметаллические материалы, лазерная резка пластика вызывает выброс потенциально вредных и токсичных газов. Эти выбросы требуют оборудования для контроля загрязнения воздуха, что увеличивает стоимость необходимого оборудования.Для производителей и начинающих мастерских, хотя запасные части и детали для обслуживания относительно недороги, первоначальные вложения в оборудование для лазерной резки также имеют тенденцию быть намного выше по сравнению с более традиционными процессами резки. Кроме того, оборудование для лазерной резки обычно потребляет больше мощности и энергии, чем другие процессы резки, что приводит к дальнейшему увеличению эксплуатационных расходов. В целом, высокие начальные затраты на оборудование и эксплуатационные расходы могут сделать лазерную резку непригодной для низкобюджетных операций.
Альтернативные способы резания
Хотя лазерная резка позволяет производить сложные и прецизионные детали с высокими допусками, она может не подходить для каждого производственного применения, а другие процессы резки могут быть более подходящими и экономичными. Ниже проиллюстрированы некоторые сравнения лазерной резки с другими процессами резки.
Таблица 4 – Сравнение процессов лазерной и механической резкиПреимущества | Лазерная резка | Механическая резка |
Точность / допуски | х | |
Возможности сложной конструкции | х | |
Без механических искажений | х | |
Затраты на материалы (за вычетом отходов) | х | |
Стоимость оборудования | х | |
Операционные расходы | х | |
Расходы на обслуживание | х |
Механическая резка – это производственный процесс, в котором используется оборудование с механическим приводом, т.е.g., токарные станки, фрезерные станки и прессы – для резки, формовки и резки материала в нестандартные формы и конструкции. Как показано в Таблице 4 выше, лазерная резка имеет несколько преимуществ по сравнению с механической резкой; он обеспечивает большую точность и более высокие допуски, а также предлагает более низкие затраты на материалы (например, меньше отходов) и затраты на техническое обслуживание. Однако лазерная резка также обычно требует гораздо более высоких начальных капиталовложений и эксплуатационных затрат, чем механическая резка, из-за дорогостоящего оборудования для лазерной резки и высокого энергопотребления оборудования.
Таблица 5 – Сравнение процессов лазерной резки и высечкиПреимущества | Лазерная резка | Высечки |
Точность / допуски | х | |
Возможности сложной конструкции | х | |
Быстрое прототипирование / корректировка дизайна | х | |
Множественные операции (в линии) | х | |
Ускорение производственного цикла | х | |
Постоянная скорость / давление резания | х | |
Крупногабаритная / серийная продукция | х |
Производство штампованных деталей – это одно производственное применение, для которого лазерная резка может служить альтернативой процессам механической резки, таким как плоская высечка или ротационная высечка.Как показано в Таблице 5 выше, лазерная резка позволяет повысить точность и ускорить создание прототипов. В то время как высечка позволяет в определенной степени производить прецизионные детали, лазерная резка предлагает еще более жесткие допуски для более сложных конструкций и узоров. Кроме того, лазерная резка более рентабельна для создания прототипов и корректировок конструкции, поскольку процесс не требует создания отдельных компонентов штампа для тестирования новых конструкций. Однако высечка, особенно ротационная высечка, дает определенные преимущества по сравнению с лазерной резкой.Например, ротационная высечка позволяет выполнять несколько операций в линию, а также обеспечивать постоянное и непрерывное давление резания. В совокупности эти соображения позволяют ротационной высечке обеспечить более быстрый производственный цикл, чем лазерная резка, особенно при больших или длительных производственных циклах.
Таблица 6 – Сравнение процессов лазерной и гидроабразивной резкиПреимущества | Лазерная резка | Гидроабразивная резка |
Точность / допуски | х | |
Возможности сложной конструкции | х | |
Композитный / многослойный материал | х | |
Толстые материалы | х | |
Без механических искажений | х | |
Нет теплового искажения | х | |
Операционные расходы | х | |
Тихая работа | х |
Гидроабразивная резка – это производственный процесс, в котором используется вода под давлением, а также абразивные материалы, такие как гранат или оксид алюминия, для резки и формовки материала в нестандартные формы и конструкции.Как показано в Таблице 6 выше, лазерная резка может производить детали с большей точностью и сложностью, чем гидроабразивная резка, в то время как гидроабразивная резка может производить детали из более толстых и многослойных материалов, что может быть проблематичным для процесса лазерной резки. Хотя при лазерной резке меньше риск механических искажений, гидроабразивная резка снижает риск тепловых искажений. По сравнению с лазерной резкой, гидроабразивная резка также производит больше шума и больше отходов, т. Е. Использованной воды и абразивных смесей, которые требуют очистки и утилизации, что увеличивает эксплуатационные расходы.
Таблица 7 – Сравнение процессов лазерной и плазменной резки G.E. Компания МатисПреимущества | Лазерная резка | Плазменная резка |
Точность / допуски | х | |
Возможности сложной конструкции | х | |
Толстые материалы | х | |
Диапазон подходящих материалов | х | |
Оборот | х | |
Стоимость оборудования | х | |
Операционные расходы | х |
Плазменная резка, также называемая плазменной дугой, представляет собой производственный процесс, в котором используется конус перегретого ионизированного газа для резки и придания электропроводному материалу нестандартных форм и конструкций.Как показано в Таблице 7 выше, по сравнению с лазерной резкой, которая позволяет резать металлические и неметаллические материалы, плазменная резка имеет более ограниченный диапазон подходящих материалов, поскольку с помощью процесса плазменной резки можно резать только электропроводящие материалы. Кроме того, детали плазменной резки производятся со значительно меньшей точностью и меньшими допусками из-за более широкого пропила, производимого во время процесса. Несмотря на эти ограничения, плазменная резка предлагает более низкие затраты на оборудование и эксплуатационные расходы (из-за, как правило, более низкой мощности и энергопотребления) и более быстрый производственный цикл по сравнению с лазерной резкой, а также возможности для резки более толстых и многослойных материалов.
Сводка
Выше описаны основы станка для лазерной резки, процесс лазерной резки, принцип работы лазерной резки, различные возможности и области применения лазерной резки, а также некоторые соображения, которые могут быть приняты во внимание производителями и механическими цехами при принятии решения о том, следует ли выполнять лазерную резку. наиболее оптимальное решение для их конкретного применения.
Для получения дополнительной информации о местных коммерческих и промышленных поставщиках перейдите на платформу Thomas Supplier Discovery Platform, где вы найдете более 500 000 коммерческих и промышленных поставщиков, в том числе более 2500 поставщиков услуг по лазерной резке.
Источники
- http://www.engineerstudent.co.uk/
- https://www.messer-cs.com/us/processes/laser-cutting/
- https://www.me.iitb.ac.in/~ramesh/courses/ME677/lasercutting.pdf
- https://www.boconline.co.uk
- https://www.behance.net/gallery/32298803/Laser-Cutting-Advantages-And-Disadvantages
- http://laserexp.co.uk/wp-content/uploads/2012/10/LASER-CUTTING-FROM-FIRST-PRINCIPLES-TO-THE-STATE-OF-THE-ART.pdf
- https: // www.exploainthatstuff.com/lasers.html
- https://www.us-metalcrafters.com/laser-cutting/
- https://www.gemathis.com/services/precision-laser-processing/laser-cutting-metal-services/
Прочие изделия для резки
Больше от Custom Manufacturing & Fabricating
Принцип работы оптоволоконного станка для лазерной резки
Выпущено 6 августа 2020 г.
В сегодняшней области промышленного производства станки для волоконной лазерной резки с ЧПУ имеют широкий спектр применения во всех сферах жизни благодаря их эффективным и гибким технологическим преимуществам.Станок для резки металла с волоконным лазером стал незаменимым инструментом для всех производителей оборудования, особенно в области обработки металлов, и повседневная жизнь людей тесно связана, но большинство людей не знают, как это работает. Сегодня Mister Laser познакомит вас с принципом работы станка для лазерной резки волокна, чтобы каждый мог понять его глубже.
Станок для лазерной резки стали предназначен для фокусировки лазерного света, излучаемого лазером, в лазерный луч с высокой плотностью мощности через систему оптического пути.Лазерный луч облучает поверхность заготовки, чтобы она достигла точки плавления или кипения, а газ под высоким давлением, коаксиальный с лучом, сдувает расплавленный или испарившийся металл. По мере того, как взаимное положение балки и заготовки перемещается, материал в конечном итоге образует щель, чтобы достичь цели резания.
В процессе лазерной резки используется невидимый луч вместо традиционного механического ножа.Принцип его работы также определяет преимущества, которых нет у других методов обработки:
(1) Высокая точность, высокая скорость, узкий режущий шов, минимальная зона термического влияния, гладкая режущая поверхность без заусенцев.
(2) Лазерная режущая головка не касается поверхности материала и не царапает поверхность заготовки.
(3) Прорезь узкая, местная деформация заготовки крайне мала, механическая деформация отсутствует.
(4) Он может резать сталь, сталь, углеродистую сталь, нержавеющую сталь, лист из алюминиевого сплава и другие твердые материалы без деформации.
(5) Программирование с числовым программным управлением позволяет обрабатывать любой план, резать всю доску большого формата, нет необходимости открывать форму, экономично и экономит время.
Преимущества волоконной лазерной резки также делают станок для лазерной резки металла в рекламной индустрии, рукоделии, обуви, игрушках, компьютерной вышивке для резки, моделей одежды, строительной промышленности, резки металла, производства электрических переключателей, производства лифтов, производство бытовой техники, производство кухонной посуды, инструменты для обработки и другие отрасли производства и обработки машинного оборудования имеют широкий спектр применения.
Являясь лидером в области интеллектуального лазерного оборудования, MYST Laser специализируется на предоставлении отличной технической поддержки, и у нас есть один профессиональный станок для лазерной резки и центр связи для станков для лазерной маркировки. мы будем строить нашу Индустрию 4.0 и будущие заводы, помогая компаниям строить интеллектуальное производство и обеспечивая интеллектуальное производство. Ценности нашей компании – клиентоориентированность, стремление к постоянным инновациям, реализация ценности компании и мечты сотрудников.
Процесс лазерной резки – обзор
4.4 Анализ теплопередачи жидким металлам в присутствии вспомогательного газа
В процессе лазерной резки вспомогательный газ используется либо для защиты поверхности от высокотемпературных экзотермических реакций окисления, таких как аргон, либо для возникновения экзотермической реакции, например кислород. Струя газа, вызывающая экзотермическую реакцию, приводит к увеличению скорости резания; однако точность и тонкость резки частично зависят от добавления газового потока для определенных скоростей газового потока.В попытке исследовать силы, действующие на тонкий расплавленный слой струей инертного газа, ранее были решены уравнения движения газового потока [9,10]. При анализе поток газа предполагался ламинарным, а вклад химической реакции не учитывался. Поэтому возникла необходимость в расширении предыдущих моделей. Дорранс [7], используя простую модель реагирующей газовой смеси, протекающей по нагретой плоской пластине, смог продемонстрировать, что уравнения пограничного слоя применяются до точки, где зона реакции присоединяется к плоской пластине.В предложенной модели предполагалось, что зона реакции прикреплена к поверхности жидкости; считалось, что реакции протекают на границе газ – жидкость, а остальная часть газовой фазы замораживается (массовая скорость изменения частиц и на единицу объема постоянна). Было продемонстрировано, что передача тепла от пограничного слоя, состоящего из реагирующего газа, не зависит от местоположения зоны реакции внутри пограничного слоя в первом порядке приближения [9,10]. Это приближение включает предположение, что транспортные свойства не зависят от пограничного слоя газовой смеси или, по крайней мере, их изменение с составом имеет второстепенное значение по сравнению с их изменением с температурой.Поскольку предполагается, что химические реакции происходят на границе раздела жидкость-газ, а остальная часть газовой фазы заморожена, состав газовой смеси во всем пограничном слое будет определяться конвекцией и диффузией продуктов и реагентов через пограничный слой, частицы газа, присутствующие во внешнем потоке, и частицы газа на границе раздела. Анализ, связанный с передачей тепла в жидкий металл, представлен ниже в свете предыдущего исследования [9].
Чтобы вывести уравнения теплопередачи в жидкий металл, который подвергается химическим реакциям на поверхности (т. Е. На границе раздела газ-жидкость), можно написать уравнение для теплового баланса на границе раздела. Рассматривая Рис. 4.6, тепловой баланс на границе раздела газ-жидкость дает
Рис. 4.6. Схематическое изображение границы раздела жидкость – газ.
(4.90) q˙LJ− (ρV) g [hχ (L)] g = q˙g− (ρV) ghg
, где χ обозначает химический символ, обозначающий содержание материала, подвергающегося химической реакции, ( ρV ) г – объемный поток паровой фазы, выходящей с поверхности, q˙g – теплоотдача к поверхности жидкого металла за счет проводимости и диффузии (−q˙g = (k∂T∂y + ρD12∑ ihi∂Ci∂y) g), а q˙LJ – теплопередача от границы газа к жидкому металлу при наличии массопереноса, происходящего на поверхности жидкости.Для содержания материала χ
(4,91) [hχ (L)] g + Lv = [he (g)] g
, где h – энтальпия, а L v = теплота испарения материала. содержание χ .
Объединение уравнений (4.90) и (4.91) дает
(4.92) q˙LJ = q˙g− (ρV) ghg + (ρV) g [hχ (g)] g− (ρV) gLv
Представляя уравнение ( 4.91) в уравнение (4.92) дает
(4.93) q˙LJ = CHρeUe (Ie − Ig) −∑ihio [(Ci) e− (Ci) g] + G (∞, Pr) G (∞, S ) ∑i (hi) g [(Ci) e− (Ci) g] −MT1Hg + MT1 [hχ (g)] g − MT1Lv
, где I – полная энтальпия (h + U22), ρ e – плотность газа в набегающем потоке, U e – скорость газа в набегающем потоке, C H – коэффициент теплопередачи, C i – массовая доля частиц, MT 1 – параметр массопереноса, а L v – теплота испарения.Теплопередача к поверхности жидкого металла (q˙g) равна [9]
(4.94) −q˙g = CHρeUe (Ie − Ig) {1 + G (∞, Pr) G (∞, S) −1 × ∑i (Ci) ehio1− (Zi) gIe − Ig + G (∞, Pr) G (∞, S) × ∑i (Ci) e (hi) g1− (Zi) gIe − Ig}
Z i – приведенная массовая доля (Zi = Ci (Ci) e) и
(4.95) Ie − Ig = (If) e [1− (gf) g] + ∑ihio (Ci) e [1− (Zi) g]
и
G (η, Z) = ∫0ηZCexp [-∫0η′ZCfⅆη ′] ⅆη ′.
и MT 1 – параметр массопереноса, определяемый как
(4.96) MT1 = (ρV) gρeUeCH
Вставка полной энтальпии (I = If + ∑iCihi0) в уравнение (4.93) дает
(4.97) q˙LJ = CHρeUe {(If) e− (If) g + G (∞, Pr) G (∞, S) × [∑i (hi) g [(Ci) e− (Ci) g] —MT2hg + MT2hχ (g) g] −MT1Lv}
, где MT 2 в уравнении (4.97) определяется как MT2 = G (∞, S) G (∞, Pr) MT1.
Определите другую форму, называемую потенциалом химической энтальпии h c как
(4.98) hc = ∑i (hi) g [(Ci) e- (Ci) g] −MT2∑i (Ci) g ( hi) g + MT2 [hχ (g)] g
Поскольку энтальпия газовой смеси h = ∑iCihi, то
(4.99) hc = ∑i = E (hi) g [(Ci) e− ( 1 + MT2) (Ci) g] + hχ (g) [MT2- (1 + MT2) (Cχ) g]
, где (Cχ) g = 0, поскольку все частицы χ , покидающие поверхность жидкости, ограничены пограничный слой, согласно ранее сделанному предположению.
Объединение уравнений (4.97) и (4.99) дает
(4.100) q˙LJ = CHρeUe [(If) e− (If) g + G (∞, Pr) G (∞, S) hc − MT1Lv]
В уравнении (4.100) q˙LJ представляет собой теплоотдачу жидкому металлу при наличии массопереноса, происходящего на поверхности жидкости. Термин h c обозначает тепло, выделяемое или поглощаемое из-за химической реакции между частицами газа у поверхности.
Для определения скорости теплопередачи необходимо найти массовые доли различных частиц на поверхности и краю пограничного слоя (которые используются для определения h c из уравнения (4.99)). Также необходимо разработать метод расчета ( ρV ) г в зависимости от химического состава поверхности.
Для расчета ( ρV ) g можно рассмотреть следующее уравнение [9]:
(4.101) (ρV) g = −ρeUeμe [2 (2s¯) 1 / 2f′∂η∂s + f (2s¯) 1/2]
На поверхности (жидкость)
(4.102) f ′ (0) = 0
Следовательно,
(4.103) (ρV) g = −ρeUeμef (0) ( 2s¯) 1/2
, где
(4.104) f (0) = – (CiS) g
, поскольку
(4.105) Ci = ρiρ
, где ρ – плотность всей смеси. Как только давление на краю пограничного слоя и температура границы раздела известны, можно рассчитать массовые доли частиц C i . Следовательно, можно определить f (0) и, следовательно, ( ρV ) g .
Лазерная резка | Полуприцепы
Вы ищете дополнительную информацию по этому и другим вопросам? Не ищите ничего, кроме онлайн-обучения Semitracks.Онлайн-обучение Semitracks содержит короткие курсы и другие материалы, полезные для любого инженера, пытающегося изучить новые предметы или освежить в памяти старые.
Что такое лазерная резка?
Лазеры уже много лет используются для изменения или изоляции проводников в интегральных схемах. Системы, разработанные для этой цели, работают по принципу, что лазерный свет (обычно от импульсного лазера) при фокусировке через оптику микроскопа может выборочно удалять материал с ИС, не повреждая его иным образом.Если все сделано правильно, лазеры можно использовать для резки или удаления металлических линий, открытия отверстий в некоторых типах пассивирования или разрезания поликремниевых проводников на ИС. Если все сделано неправильно, материал разрезаемого проводника может попасть в изолирующие слои, что приведет к короткому замыканию.
Для лазерной резки можно использовать три преобладающих типа лазера. В инфракрасном диапазоне длин волн наиболее распространены лазеры на Nd: YAG (неодим-иттрий-алюминиевый гранат), работающие на частоте 1064 нм. В видимом диапазоне длин волн (зеленый) чаще всего используются два основных типа лазеров: лазер Nd: YAG с удвоенной частотой на длине волны 532 нм и газовый ксеноновый лазер, работающий на длине волны 500 нм, с выходной импульсной мощностью около 150 мкДж.
Инфракрасный
Первыми лазерами на основе YAG, разработанными для кремниевой хирургии, были инфракрасные (ИК) лазеры, работающие на длине волны 1064 нм или в ИК-диапазоне. Это основная частота лазеров Nd: YAG, которые используются во многих приложениях вместе с микроскопами, предназначенными для инфракрасного излучения. У ИК-лазеров есть несколько ограничений. Большинство материалов, используемых при изготовлении интегральных схем (ИС), поглощают энергию более эффективно на более коротких длинах волн, чем материалы, производимые ИК-лазерами.Это означает, что для выполнения той же работы требуется гораздо больше энергии по сравнению с использованием лазера с более короткой длиной волны. Эта избыточная энергия часто приводит к ненужному повреждению областей, прилегающих к интересующей области. Как упоминалось выше, ИК-YAG-лазер работает только с микроскопами, разработанными специально для ИК-длин волн. Напротив, большинство микроскопов, используемых для анализа отказов, можно использовать только в видимом спектре. Использование YAG-лазера с микроскопом, отличным от YAG, скорее всего, приведет к сгоранию какой-то части оптики микроскопа.Кроме того, использование микроскопа, отличного от YAG, приводит к значительному снижению энергии по сравнению с тем, что доступно с микроскопом, совместимым с YAG. Другой недостаток ИК-лазеров в кремниевой микрохирургии заключается в том, что размеры разреза ограничены минимум 2 мкм x 2 мкм из-за большей длины волны.
видимый
Сегодня большинство поставщиков и специалистов по анализу неисправностей используют лазеры с “зеленой” длиной волны, такие как Nd: YAG-лазер с удвоенной частотой или газовый ксеноновый лазер. Большинство металлов, используемых в ИС (алюминий, золото, титан-вольфрам и др.)) поглощают больше зеленого света, чем инфракрасного излучения, поэтому для выполнения конкретной работы требуется меньше энергии. Как упоминалось выше, предпочтительна более низкая энергия, потому что в соседних областях возникает меньше повреждений. Зеленые лазеры также хорошо подходят для стандартной оптики микроскопов видимого света, наиболее часто используемой при анализе отказов. Минимальный размер пятна для зеленого лазера составляет приблизительно 1 мкм x 1 мкм.
Ультрафиолет
Некоторые лазеры вырабатывают энергию в ультрафиолетовом (УФ) диапазоне, в том числе лазеры на Nd: YAG с утроенной или учетверенной частотой и эксимерные лазеры (XeCl, XeFl и т. Д.)). Ультрафиолетовый диапазон начинается чуть ниже видимого спектра или менее 400 нм. Ультрафиолетовые лазеры имеют преимущество перед инфракрасными и зелеными лазерами, потому что большинство пассивирующих материалов поглощают больше ультрафиолетовой энергии, чем инфракрасная или видимая энергия. Следовательно, для непосредственного удаления пассивации необходимо еще меньшее количество УФ-энергии. С помощью лазеров инфракрасного или видимого диапазона пассивирование удаляется косвенно путем нагрева материала под ним и «сдува» пассивирования за счет тепла, выделяемого лежащим под ним металлом.УФ-лазеры могут непосредственно удалять пассивацию, потому что большинство пассивирующих материалов напрямую поглощают УФ-энергию.
Однако УФ-лазеры имеют связанную с микроскопом проблему, аналогичную той, которая встречается при использовании ИК-лазеров. Разница в том, что УФ-лазеры работают на противоположном конце видимого спектра по сравнению с ИК-лазерами. Поскольку энергия УФ-лазера ниже 400 нм, оптика в большинстве микроскопов, используемых для анализа отказов (предназначенных для видимого света, 400–700 нм), не пропускает более коротковолновую УФ-энергию.Если кто-то может решить проблемы микроскопа, связанные с оптикой, не пропускающей УФ-излучение, можно будет найти некоторую помощь с линзами объектива. Некоторые типы объективов микроскопов, называемые отражающими, работают в УФ-спектре. К сожалению, качество изображения отражающего объектива намного хуже, чем у стандартных объективов микроскопа для анализа отказов. Кроме того, доступны светоотражающие объективы с ограниченным количеством увеличений; наиболее распространенными для использования лазера являются 36x и 52x. Это делает их пригодными только для удаления относительно больших участков пассивации и вырезания довольно больших линий.Тем не менее, по мере того, как микроскопические технологии улучшают длину волны УФ-излучения, УФ-излучение станет отличной альтернативой для анализа отказов из-за эффективного поглощения энергии большинством пассивирующих материалов, улучшенного контроля глубины резания и потенциально субмикронных размеров реза.
В качестве примера на рисунках 2 и 3 показана металлическая линия до и после резки ксеноновой лазерной системой. В этом случае отверстия на лазере были настроены так, чтобы разрезать одну линию и оставить линии вокруг нее нетронутыми.Хотя выбор подходящего уровня мощности для использования должен производиться методом проб и ошибок, следует проявлять осторожность, чтобы не использовать слишком большую мощность, поскольку это может привести к попаданию металла в изолирующие слои и вызвать короткое замыкание.
Зачем выполнять лазерную резку?
Лазерная резка может выполняться по разным причинам и из самых разных материалов. Лазеры используются для двух целей: выборочного удаления слоя и изоляции межсоединений. Многие типы отказов ИС могут быть идентифицированы, если проблемный участок может быть электрически отделен от остальной ИС и изучен отдельно.Часто, когда цепь не повреждена, доступную электрическую информацию трудно интерпретировать. Например, если на ИС произошел разрыв оксида затвора, схема не будет функционировать должным образом. Когда плохой транзистор активирован, IC потребляет избыточный ток. Серия лазерных разрезов может изолировать неисправный транзистор от остальной части ИС. После изоляции микрозонды можно использовать для измерения ВАХ транзистора. Этот тип анализа может доказать, что рассматриваемый транзистор неисправен.
В приведенном выше примере предполагается, что пассивация ИС была удалена до микрозондирования. В некоторых случаях лазер может быть успешно использован для удаления пассивации на проводниках, что позволяет проводить зондирование. Пассивирование нитридом кремния можно легко удалить с алюминия с помощью ксенонового лазера. Диоксид кремния и оксинитрид кремния можно удалить, но с некоторыми трудностями. Использование лазеров с разными длинами волн может облегчить выборочное удаление оксидов.
Как выполняется лазерная резка?
Использовать лазерный резак очень просто.После того, как процедура, которую необходимо выполнить, выбрана, будь то выборочное удаление материала или изоляция проводников, лучше всего поэкспериментировать с уровнем мощности лазера либо на несущественной области ИС, либо на второй ИС той же технологии. Лучше всего начинать с малой мощности лазера и постепенно увеличивать мощность, пока не будет получен желаемый результат. При открытии отверстий при пассивации увеличивайте мощность до тех пор, пока отверстие не откроется, но металл под ним не будет нарушен. При изоляции металлических линий используйте самую низкую мощность, которая полностью перерезает линию за один лазерный импульс.Каждый раз при изменении уровня мощности перемещайте образец на новое место перед включением лазера. Это гарантирует, что материалы не будут изменены предыдущим лазерным импульсом.
Если линия все еще частично цела, увеличьте уровень мощности и попробуйте перерезать линию снова. Повторяйте эту процедуру, пока линия не будет полностью изолирована. Всегда лучше попытаться получить правильный уровень мощности на тестовом образце, если это возможно. Если тестовый образец недоступен, попробуйте найти репрезентативную область на ИС, которая не используется, т.е.е. проверьте транзисторы на кристалле или в областях пропила, оставленных на краях кристалла.
Если другая схема была повреждена, возникла одна из трех проблем. Во-первых, возможно, было использовано слишком много энергии. Попробуйте уменьшить мощность и определить, полностью ли отрезана линия. Во-вторых, возможно, лазер не сфокусировался в нужном месте. Некоторые лазерные резаки имеют маркер, видимый через окуляры, который показывает расположение и форму области, подлежащей лазерной обработке. Другие системы полагаются на маркер, наложенный на телевизионное изображение поля зрения.При использовании этих систем в тестовой зоне делается разрез, а маркеры перемещаются в то место, где лазерный луч попадает на образец. Наконец, некоторые системы позволяют пользователю регулировать длину и ширину лазерного разреза, регулируя несколько отверстий. Используйте эти отверстия для дальнейшего ограничения луча, чтобы луч не попал в соседние контуры.
В большинстве случаев лазер не сможет разрезать линию до тех пор, пока не будет достигнут пороговый уровень мощности. Большинство систем не показывают постепенного увеличения резания с увеличением уровня мощности.
Сколько энергии мне нужно?
Чтобы ответить на этот вопрос, необходима некоторая информация о вашем микроскопе и устройстве для отбора проб.
Наиболее эффективными объективами для резки и удаления пассивации являются объективы 50x, 80x и 100x. С помощью объективов с меньшей мощностью можно выполнить очень небольшую резку, поскольку в образец фокусируется недостаточная плотность энергии. Хотя общая энергия через каждую цель для данной настройки энергии почти одинакова, плотность энергии резко меняется.В частности, плотность изменяется пропорционально квадрату изменения увеличения. Это связано с тем, что энергия лазера эффективно «фокусируется» объективами с более высокой мощностью. В таблице 1 показана эта взаимосвязь с использованием объектива 50x в качестве ориентира.
Линза объектива (= a) | Коэффициент увеличения (против объектива 50x = a / 50) | Коэффициент плотности энергии (против объектива 50x = a2 / 502) |
---|---|---|
10 х | 10/50 = 0.2 | 100/2500 = 0,04 |
20x | 20/50 = 0,4 | 400/2500 = 0,16 |
50x (ссылка) | 50/50 = 1,0 | 2500/2500 = 1,0 |
80 х | 80/50 = 1.3 | 6400/2500 = 2,56 |
100x | 100/50 = 2,0 | 10000/2500 = 4,0 |
Если для получения адекватной плотности энергии для большинства задач лазерной резки требуется объектив с 50-кратным увеличением, из таблицы очевидно, что с объективами с 10-кратным и 20-кратным увеличением можно сделать очень мало.Также очевидно, насколько резко возрастает мощность резания при переходе к объективу 80x или 100x. Для решения той же задачи с объективом 80x или 100x требуется меньше энергии, чем с объективом 50x.
Пассивация?
Большинство пассивирующих материалов поглощают меньше видимой лазерной энергии, чем металлические линии. Таким образом, эффективное удаление пассивации требует большей энергии, чем требуется для удаления металлической полосы такого же размера. Если деталь не пассивирована, а вы предполагаете, что она есть, первый лазерный импульс может разрезать линию и повредить подложку ниже.На рис. 1 показаны коэффициенты поглощения алюминия и золота.
Зависимость поглощения энергии от длины волны для алюминия и золота (после Норта).Для разных типов пассивации требуются разные уровни энергии. Для удаления оксида и нитрида требуется меньше энергии, чем для удаления полиимида. Например, с объективом 50x может потребоваться 50% максимальной мощности для удаления оксида или нитрида и 75% для удаления полиимида. Поскольку тепло, выделяемое металлом, расположенным ниже, используется для «сдувания» пассивации, успех в некоторой степени будет зависеть от количества нагреваемого металла.Будет намного проще удалить полиимид с большой металлической поверхности, чем с небольшой металлической поверхности, поскольку большая металлическая поверхность сможет поглощать больше энергии без повреждений. В общем, легче удалить пассивацию с линии, сделав точечный лазерный маркер в виде длинного прямоугольника по длине линии. Кроме того, результаты будут лучше при удалении пассивации с объективом 80x или 100x, чем с объективом 50x.
Насколько велик – насколько мал?
Для удаления большой площади материала требуется более высокий уровень энергии, чем для удаления небольшой области того же материала.Поскольку плотность энергии остается постоянной при открытии лазерной апертуры, можно было бы ожидать, что плотность энергии, необходимая для удаления маленькой линии, также применима к большей линии. Однако металл является отличным проводником тепла, и некоторая энергия, помещенная в целевую область, рассеивается в окружающие области. В итоге для удаления большой площади материала требуется более высокая плотность энергии, чем для удаления небольшой площади.
Практическое применение этого явления можно увидеть, столкнувшись с необходимостью перерезать большую линию или автобус.Если шина слишком длинная для того, чтобы ее можно было разрезать за один раз, можно попробовать либо: а) сделать длинный узкий (2–3 мкм) надрез, или б) использовать технику откусывания, т. Е. Сделать несколько меньших надрезов 5–10 мкм. в длину.
С чего начать?
В какой-то момент вы можете столкнуться с первым использованием лазера или чипа неизвестного происхождения. С чего начать удаление пассивации или сокращение? Техника брекетинга, которая начинается с очень низкой энергии и приближается к цели, является первым рекомендуемым шагом в этом процессе.В следующем примере используется система лазерной резки New Wave Research LCS-1. С объективом 50x начните с переключателя энергии в верхнем положении и аттенюатора на 300 и попробуйте выстрелить в тестовой зоне. Если установка 300 не дает достаточно энергии, установите аттенюатор на 400, выберите новое место и попробуйте еще один выстрел. Для достижения наилучших результатов каждый новый тестовый снимок будет производиться в новом месте. Если 400 слишком мало для достижения желаемых результатов, увеличьте энергию до 500, затем до 600 и т. Д., Пока не будет достигнут слишком высокий уровень энергии.Затем вернитесь на 50 пунктов, то есть с 600 до 550, и попробуйте сделать еще один снимок. Если это все еще слишком велико, понизьте еще 25 пунктов до 525. Большинство материалов имеют большой порог урона. Следуя этой процедуре, вы можете заметить некоторое удаление материала на 400, немного больше на 500 и, наконец, желаемые результаты на 600.
Некоторые материалы имеют небольшой или узкий порог повреждения. В эту категорию попадают тонкопленочные резисторы и очень маленькие линии. Вы можете обнаружить, что 200 недостаточно, а 300 – слишком много.В этом случае вы можете добиться лучших результатов, переместив переключатель энергии в положение «низкий». Это приводит к снижению уровня энергии на 50% для данной настройки аттенюатора. Это означает, что теперь вам, возможно, придется переместить аттенюатор на 400 или 450, чтобы получить те же результаты, что и на 200.
Переключатель высокой / низкой энергии дает вам больший динамический диапазон, что особенно полезно для приложений с очень низким энергопотреблением, таких как подстройка тонкопленочного резистора. Аттенюатор даст вам ослабление> 50: 1; с переключателем High / Low это становится> 100: 1.Этот переключатель также является очень удобной функцией для быстрого снижения уровня энергии. Например, после удаления пассивации, когда переключатель энергии находится в положении «Высокое», используйте положение «Низкое», чтобы удалить металлическую линию под ним или очистить разрез.
Как отмечалось выше, для получения желаемого результата может потребоваться несколько снимков. Иногда могут потребоваться два выстрела с одинаковой настройкой энергии. В других приложениях может потребоваться один импульс высокого давления для удаления пассивации, как описано в приведенном выше примере, и второй выстрел с меньшей энергией, чтобы разрезать линию.Если один выстрел не решает вашу задачу, попробуйте несколько вариантов.
Это лишь некоторые характеристики лазеров и методов их применения в кремниевой микрохирургии. Лазерные и микроскопические технологии быстро расширяются и совершенствуются. Наиболее важными улучшениями являются объективы с более высокой мощностью и адекватным рабочим расстоянием, что позволит проводить операции на меньших геометрических размерах, и УФ-оптика, которая позволит использовать УФ-излучение для удаления пассивации с большим контролем глубины.
Рекомендуемые длины волн для лазерной резки полупроводников
В следующей таблице приведены оптимальные длины волны, рекомендуемые для обычных полупроводниковых материалов. В таблице 3 перечислены рекомендуемые настройки для удаления пассивации поверх верхнего металлического слоя. После удаления пассивации используйте 1 или 2 дополнительных выстрела с зеленым (532 нм) при настройке, используемой для удаления оксидной пассивации.
1064 нм (инфракрасный) | 532 нм (зеленый) | 355 нм (ультрафиолет) | |
---|---|---|---|
Диэлектрики | Диоксид кремния | Нитрид | |
Нитрид | Полиимид | ||
Полиимид (большой разрез) | тефлон | ||
СОГ (вращение по стеклу) | Силокс | ||
Межсоединение | Алюминий | Поликремний | Золото (импульсная резка) |
Золото | Алюминий | ||
Алюминий | |||
Вольфрам | |||
Медь | |||
Толстые и тонкопленочные резисторы |
Образец | Размер резки | Линза объектива микроскопа | Длина волны | Настройка энергии | Энергетический диапазон | Выстрелов |
---|---|---|---|---|---|---|
Полиимид | 40 x 40 мкм | 50x NUV | 355 нм | 200 | Lo | 75 |
Si3N4 | 40 x 40 мкм | 50x NUV | 355 нм | 300 | Lo | 40 |
Si3N4 | 4 x 4 мкм | 50x NUV | 532 нм | 500 | Привет | 2 |
SiO2 | 2 x 4 мкм | 50x NUV | 532 нм | 500 | Привет | 1 |
SiO2 | 2 x 4 мкм | 100x | 532 нм | 200 | Привет | 1 |
SiO2 | 1.8 x 3 мкм | 50x NUV | 532 нм | 400 | Привет | 1 |
SiO2 | 1,8 x 3 мкм | 100x | 532 нм | 200 | Привет | 1 |
SiO2 | 2 x 4 мкм | 50x NUV | 532 нм | 350 | Привет | 2 |
SiO2 | 2 x 4 мкм | 100x | 532 нм | 200 | Привет | 1 |
Si3N4 и SiO2 | 2 x 4 мкм | 50x NUV | 355 нм | 600 | Lo | 5 |
Si3N4 и SiO2 | 2 x 4 мкм | 50x NUV | 355 нм | 400 | Привет | 3 |
Si3N4 и SiO2 | 1 x 2 мкм | 100x NUV | 355 нм | 350 | Привет | 3 |
Si3N4 и SiO2 | 20 x 4 мкм | 50x NUV | 355 нм | 300 | Lo | 20 |
Si3N4 и SiO2 | 20 x 4 мкм | 50x NUV | 355 нм | 300 | Привет | 2 |
Si3N4 и SiO2 | 2 x 4 мкм | 100x NUV | 355 нм | 150 | Lo | 15 |
Si3N4 и SiO2 | 2 x 4 мкм | 100x NUV | 355 нм | 350 | Привет | 2 |
Резка верхнего слоя металла
Если верхний пассивирующий слой состоит из нитрида или полиимида, удалите его, используя настройки, указанные в таблице 3 выше. Затем перейдите на объектив 100x и используйте один снимок зеленого (энергия 532 нм) и настройку 500, Hi, чтобы удалить следующий слой оксида (если он присутствует), а затем второй снимок с той же настройкой энергии. удалить верхний слой металла. Следующий слой металла (если он существует) также может быть удален одним выстрелом для удаления межслойного диэлектрика и вторым выстрелом для удаления следующего металлического слоя.Лучше всего снизить температуру при удалении второго металлического слоя, чтобы свести к минимуму возможность короткого замыкания между слоями.
Когда выполняется лазерная резка?
Лазерная резка используется для двух различных целей: открытие отверстий в пассивировании и изоляция проводников на ИС. После того, как для характеристики неисправности были использованы другие методы неразрушающей диагностики, деструктивные методы могут помочь полностью понять электрическую сигнатуру неисправности на ИС.В некоторых случаях дефект обработки или маски может привести к попаданию проводника в непредусмотренное место. В этих случаях можно использовать лазерный резак, чтобы доказать, что ИС будет полностью функциональна после внесения коррекции. Всегда дешевле вырезать лазером материал из нескольких нефункциональных ИС, чтобы доказать, что смена маски решит проблему, чем изготовить новую маску и изготовить партию пластин без решения проблемы. Лазерные резаки или эквивалентные системы с фокусированным ионным пучком неоценимы для этих приложений.
Ссылки на лазерную резку
- W.E. Риз, “Использование импульсного лазера в анализе отказов”, Proc. Int. Надежный. Phys. Symp., Апрель 1973 г., стр. 124–127.
- Р.Л. Уотерс и Ф.Р. Потховен, “Лазерный резак для анализа отказов”, Proc. Int. Symp. Тестирование и провал. Anal., Ноябрь 1983 г., стр. 69–72.
- S.J. Кирх и Д. Томази, “Передовые методы микрообработки для анализа отказов”, Proc.Int. Symp. Тестирование и провал. Anal., Ноябрь 1991 г., стр. 35-40.
- Э. Норт, «Основы кремниевой микрохирургии», внутренняя публикация в New Wave Research, 1996.
Рисунок 1
Схема ксеноновой лазерной системы. (С любезного разрешения Florod Corp.).
Рисунок 2
Фотография показывает металлическую линию до того, как она будет разрезана ксеноновой лазерной системой. (Фото любезно предоставлено Sandia Labs).
Рисунок 3
Фотография показывает металлическую линию после резки ксеноновой лазерной системой. (Фото любезно предоставлено Sandia Labs).
Рисунок 4
На фотографии показан разрез размером 50 x 50 мм, сделанный из полиимида с использованием около 50 снимков очень низкой мощности (<15% от максимальной) с помощью линзы объектива с 50-кратным увеличением в ближнем УФ-диапазоне. (С любезного разрешения New Wave Research).
Рисунок 5
На фотографии показан разрез 100 x 200 мм, сделанный из полиимида с использованием температуры 50 x 50 мм, сканированный по матрице, когда лазер находился в режиме импульсной резки (355 нм, <15% макс.оптическая сила, 20 Гц, объектив с 50-кратным увеличением ближнего УФ). (С любезного разрешения New Wave Research).
Рисунок 6
Фотография показывает удаленный участок полиимида размером 50 x 50 мм, удаленный SiO2 с 3 алюминиевых линий и срез верхней алюминиевой линии. Это было выполнено с использованием примерно 50 выстрелов с низкой УФ-энергией с 50-кратным увеличением ближнего УФ-объектива, за которыми последовали четыре одиночных выстрела лазером 532 нм с мощностью примерно 40% с использованием 100-кратного объектива, а затем один выстрел лазером 532 нм для резки алюминиевая линия.(С любезного разрешения New Wave Research).
Рисунок 7
На фотографии показан удаленный участок полиимида размером 50 x 50 мм и удаленный участок металла 3 (алюминий) размером 20 x 20 мм, чтобы обнажить металл 2 и металл 1 внизу. Это было выполнено с использованием около 50 выстрелов из лазера 355 нм при низкой энергии, за которыми последовали два выстрела из лазера 532 нм при мощности 50%, чтобы открыть металл 3. (любезно предоставлено New Wave Research).
Рисунок 8
На фотографии показана базовая система импульсной лазерной резки Nd: YAG (удвоенная и утроенная частота).(С любезного разрешения New Wave Research).
Принцип и классификация лазерной резки металла – Знания
Лазерная резка металла – одно из важных применений современной лазерной технологии. С развитием волоконной лазерной технологии лазерная резка металла постепенно стала основным рынком для лазерных приложений, а оборудование для лазерной резки постепенно стало основной силой, заменяющей традиционное оборудование для резки металла.
Фактически, процесс резки на станке для лазерной резки металла существенно отличается от процесса традиционной обработки. Лазерная резка металла – это облучение лазерным лучом поверхности металлической заготовки и достижение цели резки или гравировки путем плавления и испарения металлической заготовки. Лазерная резка имеет такие преимущества, как точность и скорость, неограниченные режимы, экономия материалов, гладкие торцы и низкие общие затраты на обработку.
Из первоначального подразделения лазерную резку металла можно разделить на следующие категории:
1) Газовая резка
Используйте лазерный луч с высокой плотностью энергии для нагрева заготовки.Он испаряется за короткий промежуток времени с образованием пара. Сделайте надрезы в материале. Теплота испарения материалов обычно велика, поэтому для лазерного испарения и резки требуются высокая мощность и плотность мощности.
2) Резка расплава
При лазерной плавке и резке металлический материал расплавляется за счет лазерного нагрева, в сопло распыляется неокисляющий газ (Ar, He, N и т. Д.), А жидкий металл выпускается под сильным давлением газа в образуют надрез.Требуемая энергия составляет лишь 1/10 энергии, необходимой для резки паром. Лазерная резка плавлением в основном используется для резки некоторых неокисленных материалов или активных металлов, таких как нержавеющая сталь, титан, алюминий и их сплавы.
3) Кислородная резка
Он использует лазер в качестве источника тепла для предварительного нагрева, а кислород и другие активные газы в качестве режущего газа. С одной стороны, продуваемый газ вступает в реакцию с режущим металлом, вызывая реакцию окисления и выделяя большое количество теплоты окисления; с другой стороны, расплавленный оксид и расплав выдуваются из зоны реакции, и скорость резки намного выше, чем резка с лазерным испарением и резка с плавлением.