О компании | ООО Мастика
О компании
Сызранский завод изоляционных материалов более полувека трудится на благо отечественной трубопроводной индустрии.
Рождение завода стало результатом бурного развития в послевоенные годы трубопроводного транспорта. Начав с рулонной изоляции, завод в 1961 году расширяет ассортимент продукции, осваивает производство битумно-резиновых мастик трех марок. К 1967 году производство мастик достигает 30 тыс. тонн в год, а к 1976 году мощность производства была увеличена до 80 тыс. тонн в год, что отвечало запросам Миннефтегазстроя. В 1977 году был освоен выпуск грунтовок типа ГТ под липкие полимерные ленты, производство которых составляло 500 тонн в год.
Второе рождение завода относится к 1991 году, когда в результате принятого Миннефтегазстроем решения о расширении завода была сдана в эксплуатацию новейшая по мировым меркам технологическая линия по производству праймеров (грунтовок) мощностью 10 тыс. тонн с уникальным оборудованием и технологическими возможностями (разработка фирм Denso и Berstorff, Германия).
Третий этап в истории завода начался в 1993 году на фоне резкого снижения спроса на отечественные изоляционные материалы. Для лучшего управления и менеджмента завод был разделен по технологическим критериям на битумно-мастичное (ООО «Мастика») и праймерно-эмалевое (ОАО «Адгезия-ЗИМ») направления. С момента создания оба производства постоянно работали над улучшением качества продукции и расширением ассортимента. Заводы сегодня имеют аттестованные лаборатории, которые помимо контроля за качеством сырья и готовой продукции проводят под руководством ведущих отраслевых институтов ВНИИСТ, ВНИИГАЗ и главных специалистов предприятия разработку новых видов мастик и праймеров в соответствии с предъявляемыми требованиями.
Результатом этих работ явилось освоение серийного производства битумно-полимерных мастик (БПМ), конкурентоспособность которых обусловлена, в первую очередь, качеством основного компонента рецептуры — специального изоляционного битума БНИ-IV (поставка по трубопроводу с Сызранского НПЗ), а также добавками, регулирующими температурные зависимости реологических и механических свойств материалов.
В настоящее время завод предлагает битумно-полимерные мастики с широким диапазоном свойств для различных условий применения и эксплуатации.
Имеются битумно-полимерные мастики с температурой плавления до 110 — 120°С и высокой эластичностью (дуктильность от 5 см), имеются «зимние» мастики с температурой хрупкости до минус 30°С и высокой текучестью при отрицательных температурах. С учетом потребностей рынка в новейших материалах, разработана битумно-полимерная мастика для изоляции газопроводов при их капремонте, отвечающая высоким требования, предъявляемым ОАО «Газпром», обладающая уникальными свойствами в области морозостойкости, ударной прочности в условиях отрицательных температур, способностью, в отличие от существующих аналогов, сохранять свои качественные характеристики при неоднократных нагревах в условиях трассовой переизоляции. Мастики используют как превосходный материал для гидроизоляционных и кровельных работ.
Все выпускаемые мастики имеют по сравнению с зарубежными и отечественными аналогами более низкую цену, полученную вследствие оптимизации производства.
Современное технологическое оборудование, квалификация персонала и сотрудничество с отраслевыми институтами позволяют постоянно совершенствовать качество изоляционных материалов. Так без значительных материальных вложений расширен ассортимент праймеров (грунтовок) для изоляции трубопроводов под полимерные ленты и антикоррозионного покрытия металлических и бетонных поверхностей: дополнительно к праймеру П-001, лучшему в начале 1990-х годов, освоено производство праймеров ПМ-001ВК, ПЛ-Л, ПЛ-М. Имеющийся набор праймеров позволяет охватить практически все условия применения и эксплуатации всех типов конструкций изоляционных покрытий и видов полимерных изоляционных лент как отечественного, так и зарубежного производства (фирмы Poliken, Nittoи др.). Праймеры нашли применение как самостоятельное покрытие для антикоррозионной и изоляционной обработки металлических поверхностей (в том числе подкузовной части и скрытых сечений автомобилей), деревянных конструкций, ж/б поверхностей, фундаментов, а также в качестве подклеивающего слоя для различных поверхностей, могут наноситься на влажную металлическую поверхность.
Перечень новых материалов не ограничивается только выпуском грунтовок. В 1994 году на ОАО «Адгезия-ЗИМ» впервые в РФ на реконструированных производственных мощностях был освоен выпуск первого материала из семейства защитнодекоративных эмалей на основе хлорсульфированного полиэтилена (ХСПЭ). Разработанный совместно с институтом физической химии АН России и НТЦ «Адгезия» (г. Москва) состав эмали оказался свободным от недостатков, присущих более ранним отечественным разработкам. В настоящее время эмали на основе ХСПЭ из семейства, получившего торговую марку «Эмалин», предназначены для гидроизоляции, защиты от коррозии и декоративной отделки в промышленном и гражданском строительстве. Эмали могут быть использованы на сооружениях и конструкциях из стали, бетона, кирпича, дерева, полиуретана, стекла, кроме объектов, контактирующих с питьевой водой и пищевыми продуктами. Они предназначены для использования в атмосфере влажного воздуха, солевого тумана, атмосфере химических производств и агрессивных сред.
Защитный эффект и долговечность эмалей «Эмалин» обусловлены тем, что материал покрытия, будучи на первых этапах эксплуатации каучукоподобным, под действием паров воды и ультрафиолетовой составляющей солнечного света самовулканизируется, т.е. переходит в резиноподобное состояние, что делает материал более стойким к действию окружающей среды и механических нагрузок Покрытие на основе «Эмалина» легко переносит самые резкие температурные и влажностные перепады, в отличие от алкидных и кремнеорганических покрытий, то есть отсутствуют вспучивание, растрескивание, шелушение и т.д. Эмали серии «Эмалин» до сегодняшнего времени остаются лучшим в России покрытием для защиты металлических нефтяных резервуаров (рекомендованы к применению НИИ «Проблем хранения» г. Москва). В 1997 году они впервые были применены для покраски металлических резервуаров, металлоконструкций технологической установки ЭЛОУ-АВТ-6 на Сызранском НПЗ. Наши эмали прекрасно зарекомендовали себя не только как антикоррозионные материалы, но и в качестве фасадных красок — это отделка фасадов зданий Сбербанка, главпочтамта, ТЦ «Пассаж» в г.
Положительный эффект в отличие от традиционных фасадных красок достигается благодаря образованию на бетонной или оштукатуренной поверхности прочной и эластичной пленки, устойчивой к воздействию атмосферы.
Кроме эмалей серии «Эмалин» завод освоил и выпускает эпоксидные эмали. Например, эпоксидная эмаль ЭП-5285 способна защищать от коррозии резервуары со светлыми нефтепродуктами, обладает высокой степенью дезактивации, что делает ее незаменимой на объектах атомной энергетики.
В настоящем завод продолжает динамично развиваться, расширяет ассортимент выпускаемой продукции. На предприятии разработана полимерная мастика герметизирующая высыхающая, предназначенная для герметизации сборных элементов жилых, общественных и производственных зданий, для уплотнения мест примыкания строительных конструкций (оконных, дверных блоков), а также стыков специальных сооружений, эксплуатируемых в условиях агрессивной среды.
Предприятие, обладая современным технологическим оборудованием, которое включает оборудование для синтеза и химической модификации полимерных и олигомерных связующих для всех растворных материалов — праймеров, эмалей — готово и далее совершенствовать свою продукцию.
Сегодня наше предприятие пытается найти лучшие конструкции на основе битумных материалов.
Документы об проведении специальной оценки условий труда.
Файл 1
Файл 2
Установка для производства полимерно-битумного вяжущего и битумных мастик
Полимерно модифицируемый битум – это улучшенный материал полученный от взаимодействия битума и полимера на специальном заводе и при определенных условиях.УСТАНОВКА ДЛЯ ПРИГОТОВЛЕНИЯ МОДИФИЦИРОВАННОГО БИТУМА И БИТУМНЫХ МАСТИК «УПМБиБМ»
4-6 т/ч
6-8 т/ч
8-10 т/ч
10-15 т/ч
Установка предназначена для приготовления модифицированного битума и полимерно-битумного вяжущего с улучшенными технологическими характеристиками по теплостойкости, морозостойкости и пр. , а также для производства битумных мастик
УСТАНОВКА ПОСТАВЛЯЕТСЯ В СЛЕДУЮЩЕМ ИСПОЛНЕНИИ
1. Монтируется на базе 40-ка футового контейнера.
Варианты загрузки материалов: – шнековый транспортер;
Состав изделия и основной комплект поставки УПМБиБМ
Наименование | Кол/во |
УСТАНОВКА ДЛЯ ПРИГОТОВЛЕНИЯ МОДИФИЦИРОВАННОГО БИТУМА И БИТУМНЫХ МАСТИК «УПМБиБМ» | |
Система трубопроводов | 1 |
Емкость-смеситель Е1, Е2 с мешалками и обогревом (рубашка масляная), объем 4м3 | 2 |
Платформа весовая с тензо-датчиками | 2 |
Насос подачи битума Н3 | 1 |
Насос подачи присадки-масла Н5 | 1 |
Насос перекачки материала Н1, Н2 | 2 |
Насос выдачи готовой мастики Н4 | 1 |
Насос выдачи готового материала ПБВ Н7 | 1 |
Насос циркуляции теплоносителя Н6 | 1 |
Диспергатор, Электродвигатель 110 кВт | Согласно производительности |
Маслонагревательная станция, 36 кВт | 1 |
Шнек с бункером для хранения на 500л | Согласно производительности |
Система управления: полуавтоматическая | 1 |
Размеры платформы, рабочие: м | 12 х 5,5 х 4,2 |
Контейнер 40 футовый | 1 |
Масло “Газпром МТ-300» | 1200 л |
УСЛОВИЯ ПОСТАВКИ ОБОРУДОВАНИЯ
Конкретные условия поставки оборудования оговариваются Договором и Техническим заданием. Транспортные расходы по доставке оборудования к месту эксплуатации оплачивает Заказчик. Установка поставляется без разгонных емкостей для битума, пластификатора и без емкостей для хранения готовой продукции, поскольку данное оборудование можно задействовать из имеющегося в наличии. При необходимости данное оборудование будет изготовлено и поставлено по дополнительному согласованию.
Как организовать производство мастик
В строительстве для замазки различных стыков и трещин широко используются мастики, которые могут иметь различные свойства, в принципе, как и технологию производства. В зависимости от способа применения такие вещества делятся на горячие и холодные. Особенность горячих мастик в том, что перед нанесением их нужно разогреть. Второй же тип можно применять без каких-либо температурных обработок. Такая возможность использования объясняется тем, что холодные мастики изготовляются на основе растворителей и воды.
Учитывая то, что мастика битумная и другие подобные вещества широко используется для гидроизоляционных работ, ее производство может стать неплохим средством заработка. Главное правильно рассчитать объемы производства и ассортимент изготовляемой продукции.
Особенности производства
Для производства мастик используют различные материалы. Так, это может быть гипс, песок, сера и многое другое. Это стоит учесть при организации производства данного вещества. В качестве же основания для мастики может служить растворимое стекло, каучук, клей и другие вяжущие вещества. Конечно, чаще всего для производства мастики используют именно битум, который можно легко достать на современном рынке.
Что же касается технологии производства мастики, то здесь все в основном зависит от оборудования и продукта, которые в результате должен получиться. В основном процесс приготовления мастики проводится по схожей технологии. Прежде всего, основное вещество – битум, загружается в емкость, которая в дальнейшем будет нагреваться. После того как битум пройдет термическую обработку, в него начинают добавлять различные вещества. Весь процесс приготовления мастики занимается сравнительно немного времени. Здесь все зависит от того, сколько мастики запланировано получить в результате приготовления.
Затраты на бизнес
Для того чтобы организовать производство битумной мастики, необходимо закупить оборудование и сырье. Затраты на оборудование будут зависеть от того, какой объем вы хотите производить. Так, понадобятся смесители или дозаторы, емкости для хранения компонентов мастики, транспортеры и многое другое, что нужно для создания производственной линии. Также при составлении бизнес плана стоит учесть стоимость сырья, из которого и будет производиться мастика.
Немаловажным пунктом в организации бизнеса является и набор персонала. В среднем для обслуживания производственной линии понадобится около 5 человек. Здесь особого внимания стоит уделить не оплате труда, а квалификации рабочих. Ведь, от их профессионализма будет зависеть качество и объемы производства. А хорошим специалистам можно заплатить и сполна
com/embed/ZdTHZSv8Kyc” frameborder=”0″ allowfullscreen=”allowfullscreen”>
Производство – germetik-universal.com
О насНаше предприятие имеет несколько производств на которых производится продукция по технологиям и рецептурам “ГЕРМЕТИК-УНИВЕРСАЛ”. Разрабатываются новые технологии, материалы для строительной отрасли Украины и стран СНГ. Привлекаются специалисты и технологи различных зарубежных компаний, Научно-исследовательских институтов, химики и т.д.
ООО “ТД ГЕРМЕТИК-УНИВЕРСАЛ”
Производство гидроизоляционных битумно-полимерных материалов торговой марки УЛЬТРАСИЛ, бутил-полимерных материалов УЛЬТРАФЛЕКС, битумных мастик холодного применения БИТЭЛАСТ, ГЕРМАБУТИЛ 2М, БУТИПРОЛ 2М, битумных и полимерных герметиков различного назначения, строительных масс и композиций.
Производство холодного асфальта “ANTI-ЯМА”
Производство битумного порошка ПОВ-1
Украина, 49000, г. Днепропетровск, ул. Воронежская, 17
Телефон: +38 056 785-32-21, +38 098 127-99-70, +38 066 099-22-58,
Факс: +38 056 785-56-21
Skype:germetik-universal, ICQ:560-943-243
Адрес производства: Украина, 49000, г. Днепропетровск, Слобожанский проспект, 2 ( проспект им. газеты Правда)
ООО “СТРОЙИЗОЛЯЦИЯ”
www.stroyizolacia.com.ua
Производство битумно-каучуковых лент для строительства и ремонта асфальтовых покрытий, битумных лент строительного нахначения, битумных гидроизоляционных мастик холодного применения СтройИзол, битумных кровельных герметиков, битумных строительных масс различного назначения.
Украина, 49000, г. Днепропетровск, ул. Воронежская, 17
Телефон: +38 056 785-32-21, +38 056 785-56-21, +38 095 714-10-30
Факс: +38 056 785-56-21
Skype:germetik-universal, ICQ:560-943-243
ООО “БИТУМПРОМ”
www.bitumprom.stroika.dp.ua
Производство битумов БН 70/30, БН 90/10, битумных мастик горячего применения МБКГ, МБР, МБИ, МБПИ, заливочных масс для ремонта и строительства асфальтовых покрытий, гидроизоляционных мастик ИЗОЛ, антесептированных и биостойких мастик.
Украина, 49000, г. Днепропетровск, ул. Миронова, 7А, офис 18
Телефон: +38 056 785-32-21, +38 056 785-56-21
Skype:evgeniy-bitum, ICQ:550-395-048
e-mail:[email protected]
О О О ” БИТУМ +”
Производство битума БН 70/30, БН 90/10 ГОСТ 6617-76, горячих битумных мастик
Украина,10029, г. Житомир, ул. Котовского, 35/8
Телефон: +38 097 758-55-04
Skype: promizol
E-mail: [email protected]
О О О “Завод Интер-Герметик-Универсал”
Производство полимерных материалов торговой марки МАГЭЛАСТ, производство холодных битумно-полимерных мастик, праймера.
Украина, 69032, г. Запорожье, Солнечное шоссе, 23
Телефон: +38 061 226-52-35
www.germetik.biz.ua
Приготовление битумных мастик — Кварта
Технологии приготовления битумных и битумно-резиновых мастик.
Приготовление битумных мастик
Перед приготовлением мастики предварительно подготавливаются битум и асбест.
Битум дробят до кусков фракции 50-100 мм. Затем отмеренное количество битума доводится в дробилке до фракции 2-3 мм.
Асбест сушится в ящиках в сушильном отделении при помощи электротерморегулятора. Влажность асбеста после сушки не должна превышать 5%.
В битумоварочный котел загружают битум и нагревают его до 160-1800С. В процессе плавления битум периодически помешивают мешалкой и снимают металлической сеткой плавающие на его поверхности посторонние включения. Затем в обезвоженный битум постепенно добавляют небольшими порциями зеленое масло или керосин, а затем (также небольшими порциями) – наполнители.
Вместо масла возможно использование полимерного пластификатора, который предварительно измельчается и растворяется в растворителе.
Перед введением масла температура битумного сплава должна быть 1200С. После смешивания компонентов смесь охлаждают до 50-600С и вводят растворитель.
Все это тщательно перемешивают. Визуально мастика должна быть однородной, без видимых комков и включений.
Зеленое масло исполняет роль антисептика и пластификатора одновременно.
Приготовленную мастику сливают в герметически закрываемую посуду.
Приготовление битумно-резиновых мастик
В битумоварочный котел загружают битум и нагревают его до 160-1800С. В процессе плавления битум периодически помешивают мешалкой и снимают металлической сеткой плавающие на его поверхности посторонние включения.
Перед введением резиной крошки ее разогревают до 65-750С, а температуру битумного вяжущего поднимают до 200-2100С.
Затем опускают температуру до 1200С и добавляют небольшими порциями зеленое масло или керосин, а затем (также небольшими порциями) – наполнители.
После смешивания компонентов смесь охлаждают до 50-600С и вводят растворитель.
Все это тщательно перемешивают. Визуально мастика должна быть однородной, без видимых комков и включений.
Приготовленную мастику сливают в герметически закрываемую посуду.
Технология производства полимер-модифицированного битума – Добыча
Использование полимер – модифицированного битума (ПМБ) или полимер- битумного вяжущего (ПБВ) растет во всем мире.
Перспективы
Использование полимер – модифицированного битума (ПМБ) или полимер- битумного вяжущего (ПБВ) растет во всем мире.
Использование ПМБ существенно увеличивает срок службы дорог в регионах с большим перепадом температур и повышенной нагрузкой на дороги.
Для приготовления ПМБ используются установки установки модификации битумов.
Модифицированный битум с повышенными технологическими характеристиками по теплостойкости, морозостойкости и др. изготавливают из дорожного, строительного и других видов битума с использованием полимерных добавок – термоэластопластов.
Технология изготовления модифицированного битума:
Исходные материалы вводятся в установку раздельно.
Битум нагревается в котлах или в постоянном течении через теплообменник до температуры около 180оС и закачивается в один из смесителей установки до расчетного уровня.
Полимер, поступающий в мешках, загружается из мешков в смеситель.
Одновременно в тот же смеситель загружается пластификатор.
Установка позволяет готовить модифицированный битум как с пластификатором, так и без него. В ряде случаем одно или несколько ароматических масел вместе с адгезионными реагентами может быть введено в битум для улучшения свойств конечного ПМБ.
Дозировка всех жидкостей осуществляется расходомерами. Актуальное значение регистрируется системой управления и автоматически регулируется в соответствии с заданным рецептом.
Полимеры вводятся посредством автоматизированной весовой системы дозирования. Она состоит из весов расположенных ра тензодатчиках. Тензодатчики соединены с компьютером, к который управляет дозировкой полимеров. Точность системы очень высокая.
Смешение компонентов происходит в смесителе 1 при одновременной работе мешалки смесителя и рециркуляции массы, организуемой с помощью коллоидной мельницы. В мельнице полимерный гранулят дробится на мелкие частицы и эффективно вмешивается в битум.
Далее компоненты через коллоидную мельницу поступают в смеситель 2.
Смеситель 2 оснащен своей насосной станцией.
После окончания смешения с помощью насосной станции производится перекачка готовой массы в битумные котлы для готовой продукции или в смеситель 3 для производства битумной мастики.
Смесь ПМБ должна выстояться 60 минут, чтобы произошло набухание гранулята.
Из хранилища модифицированный битум подается на собственное производство асфальтобетона или сторонним потребителям.
Мастика может заливаться непосредственно в заливщик или расфасовываться в тару для хранения в виде брикетов.
Смесители работают периодически и параллельно.
Загрузка сыпучих компонентов производится вручную, через загрузочные отверстия в емкостях.
Качество модифицированного битума проверяется визуально, а также анализом взятой пробы в аналитической лаборатории на пенетрацию, КиШ, эластичность, растяжимость и другие показатели в соответствии с ГОСТом.
Проба отбирается с помощью крана установленного на рециркуляционном трубопроводе, либо непосредственно из смесителя, либо из емкости с готовой продукцией.
Установка для производства битумной эмульсии.
Производим обучение персонала Покупателя и производим пусконаладочные работы. Гарантия – 12 месяцев;Стоимость данного комплекта оборудования формируем на день получения запроса.
Отличительной особенностью нашего оборудования является:
– простота обслуживания;
– отсутствие коллоидной мельницы в процессе перемешивания;
– оборудование изготовлено из Российских комплектующих;
– приготовленную битумную эмульсию можно транспортировать на расстояния до 800 км, без потери качества и без применения спец. транспорта.
– качество полученной битумной эмульсии отвечает всем международным стандартам;
– на этом же оборудовании можно изготовить водо-мазутное топливо для сжигания в котельных.Это значительно сокращает срок окупаемости оборудования.
Водно-битумные эмульсии применяют для гидроизоляции, кровельных работ, в дорожном строительстве и для изготовления “Холодного асфальта”, который можно упаковать в бумажные мешки и транспортировать на любые расстояния, хранить продолжительное время без потери качества.Битумные эмульсии на водной основе в дорожном строительстве используют:
-для подгрунтовки основания старого дорожного покрытия перед нанесением на них асфальтобетона;
-для приготовления холодных асфальтобетонных смесей;
-для поверхностной обработки дорожных покрытий;
-для устройства защитных слоев покрытий;
-для ямочного ремонта дорог и пр.
Водно битумные эмульсии имеют следующие преимущества:
-не требуют подогрева перед применением;
-обеспечивают экономию битума до 40%;
-могут наноситься на мокрые поверхности, что позволяет вести дорожные работы с ранней весны до
поздней осени;
-не пожароопасные;
-не приводят к загрязнению окружающей среды.
Основным конкурентом битумных эмульсий является дорожный битум, разогретый до высоких температур.
При использовании такого битума в дорожном строительстве и ремонте невозможно достичь достаточного качества ввиду следующих причин:
-низкая сцепляемость битума с поверхностью основания;
-плохое и неравномерное распределение по поверхности;
-необходимость полного отсутствия влаги на очищенной поверхности;
-невозможность варьирования качественными параметрами битума в зависимости от проводимых работ;
-высокая энергоемкость, обусловленная поддержанием высоких температур;
-повышенная опасность производства работ, т.к. используется битум до 160°С.
В отличие от дорожного битума, использование битумных эмульсий обеспечивает:
-полное сцепление с основанием;
-по текучести эмульсия близка к воде, поэтому она растекается по поверхности, заполняя все поры и неровности;
-допускается разлив битумных эмульсий на увлажненную поверхность;
-технология производства битумных эмульсий позволяет варьирования качественными показателями для каждого вида работ;
-более низкая энергоемкость из-за отсутствия необходимости поддержания высокой температуры;
-экономическая эффективность использования битумных эмульсий достигает 70%.
Битумная мастика – Иранский производитель битумной мастики
Битумная мастика Определение
Битумная мастика – это тип асфальта, состоящий из подходящего градуированного минерала и асфальтового цемента, который также должен принимать в надлежащей пропорции твердую или полутвердую форму с однородной массой. при нагревании он находится в жидкой форме, а затем становится твердым.
Мастичный асфальт (МА) представляет собой плотную смесь, состоящую из крупного заполнителя и / или песка, и / или мелкого заполнителя известняка, и / или наполнителя и битума, которые могут содержать добавки (например, полимеры, воски).Смесь разработана с низким содержанием пустот. Содержание связующего регулируется таким образом, чтобы пустоты были полностью заполнены и мог возникнуть даже небольшой избыток связующего. Асфальтовая мастика является сыпучей и может растекаться в рабочем температурном режиме. Не требует уплотнения на месте.
С другой стороны, асфальтовая мастика – аббревиатура AM – это термин, используемый в Европе для описания смеси песка (то есть без заполнителей> 2 мм) и / или мелкозернистого известняка, и / или наполнителя и битума, которые используются. специально для гидроизоляции в различных областях применения.
Состав смеси выбирается в зависимости от
– область применения
– механическая нагрузка
– тепловая нагрузка
– химическая нагрузка
– климатологические воздействия.
Применение битумной мастики
Битумная мастика применяется для кладки из бетона и обычного красного кирпича с цементной штукатуркой. Основным методом строительства полов, фундаментов, резервуаров и т.д. б / у, Битум Мастика имеет хорошую стойкость к слабым, разбавленным кислотам, солям щелочей и т. д., также используется в качестве открытого мастичного покрытия для полов из прочных материалов.
Применяется в:
– Настилы мостов
– Настилы (здания)
– Полы (промышленные)
– Дорожное строительство
– Паркинги на крышах
– Гидравлические конструкции
– Плоские кровли
– Цистерны
Производственный процесс
В прошлом, это означает, что примерно до 1970 года мастичный асфальт часто производился в мобильных плитах (обычно на рабочем месте), которые заполнялись различными компонентами. Медленно нагревая их, компоненты доводились до нужной температуры, при этом смесительное устройство (тогда в основном горизонтально вращающийся вал смесителя) служило для обеспечения гомогенности смеси для обработки.Конечно, таким способом невозможно достичь высоких темпов производства.
В настоящее время мастичный асфальт производится на (специально спроектированных) стационарных промышленных предприятиях. Они предназначены для пропорционального распределения материалов, сушки минеральных заполнителей и их смешивания в условиях контролируемой температуры. Спецификации приложений контролируют температуры, при которых производится материал. Обычно в прошлом температуры производства мастичного асфальта находились в диапазоне от 230 до 270 ºC. Однако в последние годы были проведены (и все еще продолжаются) значительные исследования и инвестиции для снижения этих температур ниже 230 ° C, а в некоторых странах даже ниже 200 ° C.
Упаковка
Битумная мастика доступна в картонной коробке по 25 кг и новой стальной бочке по 20 кг.
НОВЫХ ДОБАВОК ДЛЯ ПРОИЗВОДСТВА МАСТИКОВОГО АСФАЛЬТА …
англ. Л. Иванов Eng. Х. Атанасов НОВЫЕ ДОБАВИТЕЛИ ДЛЯ РАЗДЕЛЕНИЯ МАСТИКИ АСФАЛЬТА strong > ПРОИЗВОДСТВО В настоящее время разделенный мастичный асфальт (SMA) является наиболее распространенным типом асфальта для износа дорожных покрытий.Среди европейских стран больше всего применяется в Германии, Нидерландах, Дании, Франции, Швеции и других. Его применение в Болгарии началось в 1995 году. Многолетний опыт показывает, что SMA демонстрирует лучшие характеристики, чем обычный асфальтобетон. Обладает повышенной прочностью и исключительной устойчивостью к деформациям. Благодаря своим превосходным характеристикам SMA заняла лидирующие позиции в области производства асфальта. Широко применяется для асфальтового покрытия автомобильных дорог, дорог и улиц.SMA гарантирует: – отличную прочность и стабильность при высоких летних температурах и зимних холодах; – гладкая поверхность и очень хорошее сцепление шины с дорожным покрытием; – поглощение транспортного шума (это так называемое «бесшумное» покрытие). SMA не удерживает воду на своей поверхности; – поры заполнителей заполнены мастикой, состоящей из битумного измельченного песка и каменного наполнителя. В мастику добавляются целлюлозные волокна, которые берут на себя функцию агента, препятствующего отслаиванию. Волокна обычно используются в качестве носителя битума – для улучшения битумной пленки и, таким образом, для снижения скорости окисления.SMA обладает хорошей стойкостью к старению; В начале производства SMA в Болгарии производители использовали добавку ARBOCELL – порошковые целлюлозные волокна. Существенным недостатком ARBOCELL является его гигроскопичность, и неправильное хранение может привести к ухудшению характеристик асфальтового покрытия. Это произошло с покрытием участка «ЧЕРНА МАЦА» трассы «ТРАКИЯ». В результате производители SMA начали использовать гранулированные целлюлозные волокна VIATOP. VIATOP производится и запатентован немецкой компанией RETTENMAIER & SOEHNE GmbH и импортируется болгарской компанией SANYMPEX Ltd.
Его преимущества: – волокна целлюлозы покрыты битумом, в результате чего гранулы не впитывают влагу при транспортировке и хранении;
Механическое поведение асфальтовой мастики, полученной из древесных отходов каменных опилок
Это исследование предназначено для оценки использования заполнителя из древесных опилок с асфальтовыми вяжущими и сравнения механических свойств отработанной мастики наполнителя-асфальта с характеристиками асфальтовой мастики, полученной с использованием типичный известняковый наполнитель.Мастики были приготовлены при четырех отношениях наполнителя к асфальту по объему асфальтового связующего: 0,05, 0,10, 0,20 и 0,30. Для оценки свойств контрольного асфальтового вяжущего и мастик использовался реометр динамического сдвига (DSR) с регулируемой деформацией и частотной разверткой. Испытание проводилось при постоянной деформации 10% и частотах нагружения 10, 5,6, 3,1, 1,78, 1,0, 0,56, 0,31, 0,178 и 0,1 Гц в широком диапазоне температур: 10, 20, 30, 40, 50. , 60 и 70 ° С. В ходе испытания измеряли значение комплексного модуля сдвига () и фазовый угол для связующего и мастики.Результаты этого исследования показали, что наполнитель из каменных опилок продемонстрировал более высокую устойчивость к усталости и образованию колейностей, чем наполнитель из известняка. Однако эластичное поведение двух асфальтовых мастик было почти одинаковым и увеличивалось с увеличением объемного соотношения. Также было обнаружено, что наиболее подходящая модель описывает взаимосвязь между объемным соотношением и каждым из и, а отношение модуля мастики к связующему представляет собой экспоненциальную модель с высоким коэффициентом детерминации (). Различия в значениях между известняковым наполнителем и наполнителем из каменных опилок были относительно незначительными, особенно при низких частотах нагружения и высоких температурах.Наконец, отношение модулей мастики к вяжущему уменьшалось с увеличением частоты нагружения.
1. Предпосылки
Хотя асфальтовая смесь приблизительно состоит только из 5% асфальтового вяжущего, а оставшаяся часть является заполнителем, механические свойства и поведение асфальтового вяжущего значительно влияют на свойства асфальтовой смеси и, следовательно, играют большую роль в рабочих характеристиках асфальтобетонной смеси. асфальтовые покрытия.
Сложность битумного вяжущего объясняется его вязкоупругой природой.Его свойства и поведение зависят от времени и температуры. Кроме того, на это поведение влияет режим загрузки. Высокая жесткость и эластичность являются желательными свойствами асфальтовых вяжущих, используемых при проектировании и производстве горячего асфальта. Высокая жесткость необходима, чтобы противостоять колейности при тяжелых нагрузках на тротуаре. С другой стороны, эластичность также необходима для восстановления и устранения части деформаций в покрытиях под нагрузкой, чтобы минимизировать усталостное растрескивание. Исследователи в области технологии асфальта всегда пытались улучшить и оптимизировать свойства асфальта, используемого при строительстве дорожного покрытия.
Модификация битумных вяжущих осуществляется с использованием нескольких модификаторов, которые доступны в широком спектре в промышленности. Некоторые из этих модификаторов производятся таким образом, чтобы их можно было использовать в технологии асфальта по разумной цене. Однако другие модификаторы представляют собой отходы или переработанные материалы, которые можно использовать в асфальте для достижения двоякой цели: (1) улучшения свойств асфальта и (2) помощи в очистке окружающей среды.
Во многих исследованиях использовались отходы и доступные наполнители для улучшения свойств битумных вяжущих и смесей.Отходы, такие как резина отработанных шин, зола горючего сланца, медицинская зола и отходы тонера [1–4], используются для улучшения свойств битумных вяжущих, используемых в технологии горячего асфальта. Кроме того, некоторые исследователи использовали отходы сельскохозяйственных деревьев и растений, такие как пустые плоды фиников и масличных пальм [5], для производства целлюлозного волокна, которое будет использоваться в качестве добавок в связующем асфальте.
Другие исследования были проведены для изучения влияния минеральных наполнителей на механические свойства асфальтовых вяжущих.Комплексные характеристики усталостного поведения были оценены при исследовании асфальтовых вяжущих и мастик, изготовленных с использованием известняковых и гашеных известковых наполнителей [6]. Изучено влияние соотношения наполнителя и асфальта на низкотемпературные и высокотемпературные свойства асфальтовых мастик с использованием минеральных наполнителей [7]; Было обнаружено, что оптимальный диапазон соотношения наполнитель / асфальт составляет 0,9–1,4, чтобы сбалансировать низко- и высокотемпературные свойства согласно исследованию. Было исследовано влияние базальтовых и гашеных известковых наполнителей на характеристики колейности, трещинообразования и стойкость асфальтобетонных мастик к термическому растрескиванию [8]; добавление гашеной извести улучшило характеристики при низких температурах и колейности, а также сопротивление разрушению.
Наполнитель портландцемента был использован для модификации асфальтового вяжущего [9]. Было показано, что увеличение отношения цемента к асфальту улучшило марку с высокими эксплуатационными характеристиками Superpave и сопротивление колейности асфальтовых вяжущих за счет увеличения жесткости и параметра. В исследовании, в котором использовались отходы в асфальтобетонных смесях [10], было обнаружено, что мраморный порошок и летучая зола могут использоваться в качестве наполнителя вместо каменного порошка в асфальтобетоне, а частицы каучука размером от №4 и нет. 200 показал наилучшие результаты по косвенному испытанию на растяжение.
Колейность и усталость считаются двумя основными повреждениями асфальтового покрытия. Асфальтовое связующее играет большую роль в характеристиках асфальтовой смеси и, следовательно, в контроле двух проблем. Различные модификаторы и наполнители были опробованы в литературе, как показано в предыдущих абзацах, для улучшения механических свойств асфальтовых вяжущих. В данном исследовании отходы (каменные опилки) используются для достижения двух целей: улучшения и улучшения механических свойств асфальтовых вяжущих, связанных с колейностью и сопротивлением усталости, и в то же время для избавления от отходов. и поддерживать чистоту окружающей среды.
Нет доступных статистических данных о количестве отходов каменных опилок в Иордании, поскольку эти отходы не относятся к тем видам отходов, которые управляются муниципальными властями или частным сектором. Однако в [11] сообщается, что суспензия обожженного камня (порошок твердых отходов) составляет около 53000 тонн в год, собираемых из 1000 карьеров и фабрик по производству плитки в Иордании. Стоимость перевозки и захоронения такого большого количества отходов составляет около 1 миллиона долларов.
В данном исследовании опилки отходов камня, собранные на участках производства камня для строительных целей, использовались в качестве наполнителя в асфальтовом связующем для исследования механических свойств произведенных асфальтовых мастик.Отходы каменных опилок задерживаются при производстве камня. Следовательно, эти отходы представляют собой материал, образующийся из тех же каменных карьеров, что и известняковый наполнитель, обычно используемый при производстве горячего асфальта в этом районе. С этой целью в данном исследовании было проведено сравнение двух наполнителей.
2. Цели
Основные цели данного исследования заключаются в следующем: (1) Изучить влияние каменных опилок в качестве наполнителя асфальтовой мастики. (2) Оценить влияние каменных опилок на механические свойства. свойства асфальтовых вяжущих (3) Проверить, могут ли наполнители из опилок камня заменить известняковый наполнитель в асфальтовых мастиках, сравнив поведение этих двух наполнителей при смешивании с асфальтом.
3. Асфальтовые материалы и наполнители, использованные в исследовании
В данном исследовании использовалось асфальтовое вяжущее с проницаемостью 60/70. Это асфальтовое вяжущее является наиболее распространенным асфальтовым вяжущим, широко используемым при производстве асфальтовых смесей для дорожных покрытий из асфальта в Иордании. Свойства битумного вяжущего были определены и приведены в таблице 1.
|
В исследовании использовались два наполнителя: известняк и каменные опилки. Эти материалы считаются отходами со строительных площадок в Иордании. Известняк был добыт в местном карьере, а каменные опилки – в процессе производства строительных камней.Оба материала просеивали методом мокрого просеивания. Порция материала, проходящая через сито № 200 (75 мкм, мкм) и сушили в печи в течение приблизительно 24 часов при промежуточной температуре.
Удельный вес, индекс пластичности и угловатость были измерены для двух материалов наполнителя. Результаты этих свойств показаны в таблице 2.
|
4.
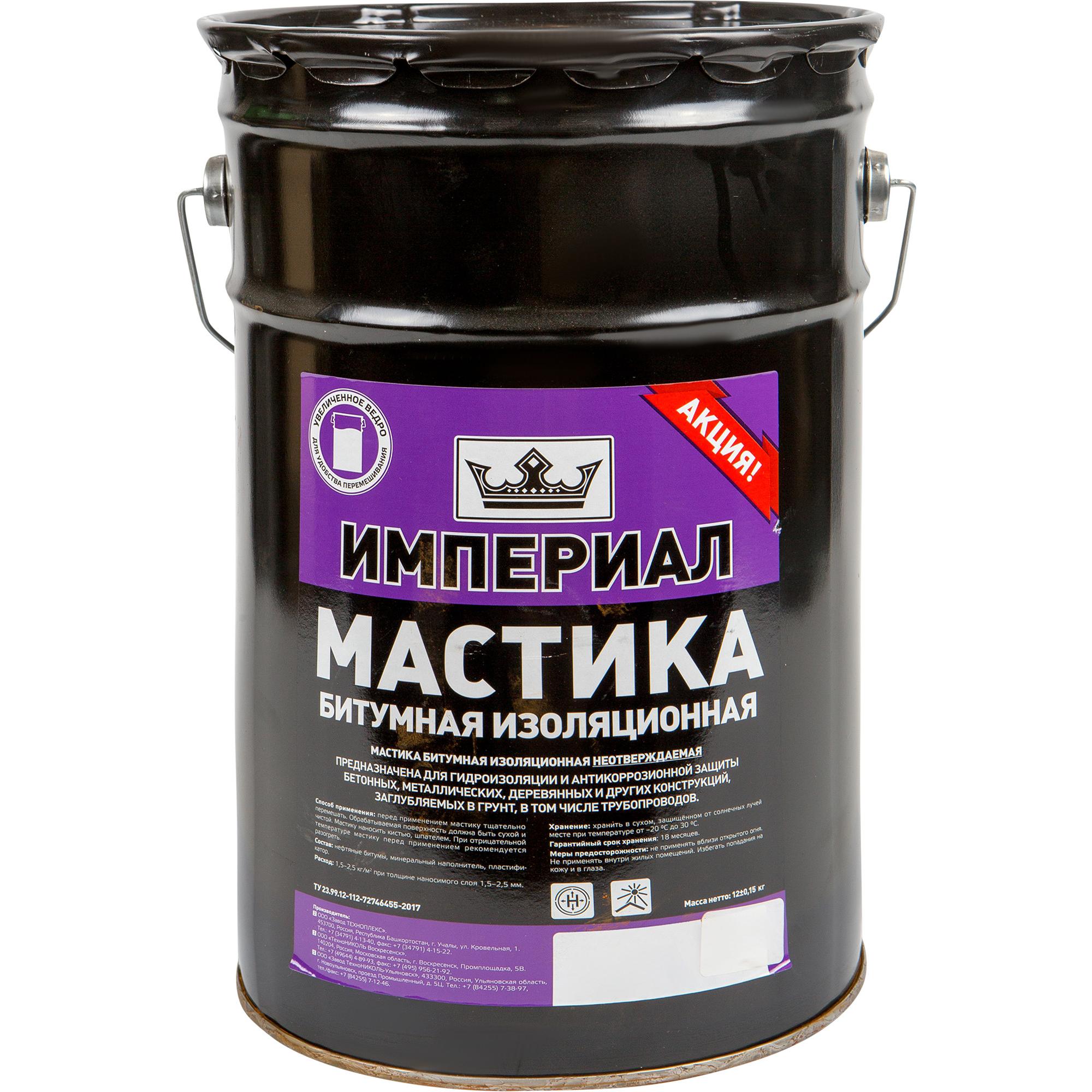
4.1. Приготовление мастики наполнитель-асфальт
Приготовление образцов мастики наполнитель-асфальт (известняково-асфальтовая мастика и каменные опилки-асфальтная мастика) осуществляли в соответствии со следующей процедурой.Наполнитель нагревали в течение одного часа в печи при 150 ° C, чтобы имитировать условия во время процесса смешивания. Асфальтовое вяжущее также нагревали при той же температуре (150 ° C) в течение примерно 20 минут в небольших контейнерах. Смешивание производили вручную в течение примерно 15 минут, постепенно добавляя наполнитель к асфальтовому вяжущему и перемешивая стеклянной палочкой для обеспечения однородности и предотвращения чрезмерного комкования. Наполнитель-асфальтная мастика была произведена при четырех объемных соотношениях (ВР): 0,05, 0,10, 0.20 и 0,30 по объему асфальтового вяжущего.
Для приготовления испытательных образцов реометра динамического сдвига (DSR) асфальтового вяжущего и наполнителя-асфальтовой мастики, асфальтовый материал (вяжущее или мастика) нагревали в печи при температуре около 150 ° C до тех пор, пока он не стал достаточно жидким. быть налитым. Стандартная силиконовая форма диаметром 25 мм использовалась для изготовления образцов асфальта для испытаний DSR (рис. 1). Образцу давали остыть в течение определенного периода времени, пока он не стал достаточно твердым, чтобы его можно было извлечь из формы.
4.2. Частотные испытания асфальтовых вяжущих и мастик
DSR (рис. 2) использовался для измерения механических свойств контрольного асфальтового вяжущего и мастик наполнитель-асфальт при различных температурах. Образец асфальта (вяжущее или мастика) помещали в устройство между двумя плитами, а зазор (толщина образца) устанавливали равным 1 мм (Рисунок 3). Образец испытывали путем приложения синусоидальной динамической деформации с помощью колеблющейся верхней пластины.Использовался тест с разверткой частоты с контролируемой деформацией. Постоянная деформация составляла 10%, а частота нагружения варьировалась от 0,1 до 10 Гц и охватывала значения: 0,1, 0,178, 0,31, 0,56, 1,0, 1,78, 3,1, 5,6 и 10 Гц. Температуры испытаний охватывали широкий диапазон температур (10, 20, 30, 40, 50, 60 и 70 ° C). Матрица тестирования частотной развертки, используемая в этом исследовании, показана в таблице 3.
|
Комплексный модуль сдвига Значение () и фазовый угол () были записаны во время теста развертки частоты. Модуль сдвига представляет собой жесткость асфальтового материала, которая отвечает за сопротивление деформации (колейности) при непрерывном сдвиге связующего при желаемой температуре и частоте нагружения. С другой стороны, фазовый угол представляет собой временную задержку между упругой и вязкой реакцией асфальтового материала, который ведет себя как вязкоупругий материал.
4.3. Параметры усталости, колейности и упругости, используемые в анализе
В системе Superpave [12] параметры усталости и колейности, используемые в критериях эффективности асфальтового вяжущего, равны и соответственно.относится к значению комплексного модуля сдвига асфальтового вяжущего и представляет собой значение фазового угла вяжущего. Значение параметра получено для асфальтового вяжущего при промежуточных температурах для проверки усталостных характеристик вяжущего; максимальное значение, указанное Superpave, составляет 5000 кПа на основе определенных протоколов и процедур, которые должны выполняться на асфальтовом вяжущем. С другой стороны, получают для асфальтового вяжущего при высоких температурах, чтобы исследовать колейность вяжущего; минимальное значение, указанное Superpave, равно 1.00 кПа для исходного асфальтового вяжущего и 2,20 кПа для краткосрочного вяжущего в соответствии с протоколами, описанными в системе Superpave.
Кроме того, в этом исследовании также используется при анализе данных, относящихся к упругой части асфальтового материала. Хорошо известно, что фазовый угол асфальтового вяжущего (вязкоупругого материала) указывает отставание между приложенным напряжением / деформацией и результирующей деформацией / напряжением; по мере того, как битумное вяжущее становится более эластичным, фазовый угол уменьшается, а когда битумное вяжущее становится более вязким, фазовый угол увеличивается.Горизонтальная составляющая комплексного значения модуля сдвига асфальтового вяжущего представляет собой упругую часть вяжущего; он улучшается при уменьшении фазового угла.
5. Анализ данных и результатов
В этой части представлены результаты и анализ данных испытаний с частотной разверткой, полученных для контрольного асфальтового вяжущего, известняково-асфальтовой мастики и каменных опилок-асфальтовой мастики [13]. Анализ включает четыре различных аспекта: сопротивление усталости, сопротивление колейности, эластичность и результаты испытаний на частотную развертку и эталонные кривые контрольного асфальтового вяжущего и наполнителя-асфальтобетонных мастик, а также сравнение известняково-асфальтовых мастик и камня. опилочно-асфальтовые мастики.
5.1. Усталость и колейность асфальтовых мастик
Значение было рекомендовано Superpave в качестве параметра усталости асфальтовых вяжущих. Поскольку усталость возникает при промежуточных температурах, этот параметр определяли для контрольного асфальтового вяжущего и двух мастик при промежуточных температурах. Рисунки 4 и 5 иллюстрируют усталостное поведение связующего и двух мастик при двух низких температурах (20 и 30 ° C) и одной частоте нагружения (1,78 Гц). Эти цифры ясно показывают, что два наполнителя увеличили значение и, следовательно, улучшили сопротивление усталости битумного вяжущего с увеличением объемного отношения.В целом наполнитель из каменных опилок показал более высокую устойчивость к усталости, чем известняк.
Параметром колейности в системе Superpave является значение. Это значение измеряется при высоких температурах (обычно более 45 ° C), чтобы характеризовать асфальтовые связующие в отношении колейности. В этом исследовании использовались семь температур: три (50, 60 и 70 ° C) считаются высокими температурами для колейности, а четыре (10, 20, 30 и 40 ° C) считаются промежуточными температурами для усталостного растрескивания.По мере увеличения значения асфальтовый материал (асфальтовое вяжущее или мастика) становится более жестким и, следовательно, более устойчивым к образованию колейности. С другой стороны, по мере того, как значение становится меньше, асфальтовый материал становится более эластичным и, следовательно, более устойчивым к колейности из-за восстановления части деформации.
На рисунках 6 и 7 показано колейность контрольного асфальтового вяжущего и двух мастик при двух экстремальных температурах (50 и 70 ° C). Эти два рисунка представляют только два примера при одной частоте нагружения (1. 78 Гц). Оба рисунка ясно показывают, что наполнители улучшили параметр колейности с увеличением объемного соотношения. Каменная мастика из опилок-асфальта показала более высокую стойкость к колейности, чем известняково-асфальтовая мастика. Было обнаружено, что соотношение между и объемным соотношением является экспоненциальным. Экспоненциальные модели с коэффициентами детерминации () для двух мастик при всех высоких температурах приведены в таблицах 4 и 5.
|
|
5.2. Эластичное поведение асфальтовой мастики
Значение представляет собой упругую часть комплексного модуля сдвига асфальтового материала. Эта эластичная часть помогает асфальтовому материалу противостоять деформации при сдвиговых нагрузках, особенно при низких и промежуточных температурах. Следовательно, этот параметр играет роль в процессе заживления деформаций колейности и усталостного растрескивания асфальта.
На рисунках 8 и 9 показано эластичное поведение () исходного связующего и двух мастик при двух экстремальных температурах (10 и 70 ° C), различных объемных концентрациях (0,0, 0,05, 0,10, 0,20 и 0,30) и одном одночастотный (1,78 Гц).
Эластичность двух асфальтовых мастик увеличивалась с увеличением объемного соотношения, как показано на этих двух рисунках. Значения для каменных опилок и известняковой мастики были примерно одинаковыми при всех частотах и температурах. Наиболее подходящей моделью, описывающей взаимосвязь между объемным соотношением (VR) и значением, является экспоненциальная модель. Коэффициент детерминации () для модели был высоким во всех случаях, как показано в таблицах 6 и 7.
|
|
С повышением температуры значение для двух мастик уменьшилось, и это типично.Тем не менее, скорость снижения этого значения при более низких температурах была очень резкой и значительной по сравнению с высокими температурами, как показано на рисунках 10 и 11. Наполнитель из каменных опилок сравнивался с наполнителем из известняка с точки зрения мастики. Рисунок 12 демонстрирует это сравнение для наименьшего объемного отношения (0,05) и максимального объемного отношения (0,30) при частоте нагрузки 1,78 Гц. Из рисунка видно, что эластичные свойства обоих наполнительно-асфальтовых мастик схожи. Этот вывод важен и указывает на то, что опилки отработанного камня могут заменить известняковый наполнитель в асфальтовой смеси, в частности, что источником двух материалов является один и тот же камень, который используется для строительства и строительства в этом районе. Другими словами, другие физические свойства двух материалов также совпадают.
6. Результаты испытаний на частотную развертку и основные кривые
Поскольку испытание на частотную развертку проводилось при девяти частотах нагружения и семи температурах, основные кривые для контрольного вяжущего и каждой из восьми наполнитель-асфальтных мастик можно было получить. На рисунках 13–17 показаны кривые потока (значение в зависимости от частоты) для контрольного асфальтового вяжущего, известняковой мастики и мастики из каменных опилок (примеры при 0.05 и 0,30 объемных соотношений).
Приведенные выше кривые текучести показывают, как изменение жесткости битумного вяжущего и мастики происходило из-за увеличения частоты нагружения и температуры испытаний. Кроме того, значение увеличилось из-за трех факторов: (1) снижение температуры, (2) увеличение частоты нагружения и (3) увеличение соотношения объемов.
Мастер-кривые используются для представления огромных данных при различных температурах и частотах нагрузки, как в случае в этом исследовании.Одна эталонная кривая для каждого объемного соотношения при эталонной температуре получается для описания поведения асфальтового материала (асфальтового связующего или мастики) при различных температурах и частотах нагружения.
Были получены эталонные кривые для контрольного битумного вяжущего и восьми мастик наполнитель-асфальт. Используя эталонную температуру 40 ° C для эталонных кривых, для каждой эталонной кривой были рассчитаны коэффициенты сдвига для других температур. Таблица 8 иллюстрирует пример коэффициентов сдвига для 0.05 мастика из опилок камня.
|
На рисунках 18–22 показаны основные кривые для двух мастик при следующих объемных соотношениях: 0.00, 0,05, 0,10, 0,20 и 0,30 соответственно. Эти кривые можно легко использовать для определения поведения асфальтового материала при определенной частоте и температуре.
Основные кривые двух мастик при четырех объемных соотношениях позволяют сделать несколько важных выводов. Различия в значении комплексного модуля сдвига () между известняковым наполнителем и наполнителем из каменных опилок относительно невелики, особенно при низких приведенных частотах (т.е.е., при низких частотах нагружения и высоких температурах). Эти различия становятся больше при высоких частотах нагружения и низких температурах; тем не менее, они все еще незначительны между двумя наполнителями. Эти данные снова предполагают, что каменные опилки могут использоваться в качестве альтернативного наполнителя для известняка в асфальтовых смесях.
Было обнаружено, что отношение модуля эластичности мастики к контрольному модулю битумного вяжущего снижается с увеличением частоты нагружения; это показано на рисунке 23. На рисунке показано сравнение двух мастик при температуре 40 ° C и объемном соотношении 0.30. Аналогичные тенденции были получены и при других температурах и объемных соотношениях.
Комплексное отношение модуля сдвига (мастика к связующему) также было построено в зависимости от объемного отношения для обеих мастик (известняк и каменные опилки). Рисунок 24 иллюстрирует это соотношение для двух мастик при температуре 40 ° C и частоте нагрузки 1 Гц. Соотношение модулей увеличивалось с увеличением объемного отношения, как показано на этом рисунке. Аналогичная тенденция была получена при других температурах и частотах нагружения.Наиболее подходящей моделью, описывающей эту взаимосвязь, оказалась экспоненциальная модель, показанная на рисунке, с высоким коэффициентом детерминации () для обеих мастик. Это относилось ко всем комбинациям семи температур и девяти частот нагружения.
7. Выводы
Анализ и результаты этого исследования позволили сделать следующие основные выводы: (1) Наполнитель из каменных опилок показал более высокую устойчивость к усталости, чем наполнитель из известняка. (2) Мастика из каменных опилок и асфальта также показала более высокую устойчивость к колейности, чем известняково-асфальтовая мастика.Было обнаружено, что соотношение между и объемным соотношением является экспоненциальным. Были обобщены экспоненциальные модели с коэффициентами детерминации () для двух мастик. (3) Эластичность двух асфальтовых мастик увеличивалась с увеличением соотношения объемов. Однако значения для каменных опилок и известняковой мастики были почти одинаковыми при всех частотах и температурах. Наиболее подходящей моделью, описывающей взаимосвязь между объемным соотношением (VR) и значением, является экспоненциальная модель.Коэффициент детерминации () для модели был высоким во всех случаях. (4) Два наполнителя показали типичное уменьшение значения с температурой. Тем не менее, скорость восстановления при более низких температурах была очень высокой и значительной по сравнению с высокими температурами. (5) Различия в значении комплексного модуля сдвига () между известняковым наполнителем и наполнителем из каменных опилок оказались относительно небольшими и незначительными, особенно при низких. частота нагружения и высокие температуры. (6) Было обнаружено, что отношение модулей мастики к связующему уменьшается с увеличением частоты нагружения при всех температурах и объемных соотношениях.Кроме того, отношение модулей нелинейно увеличивается с увеличением объемного отношения; Лучшей моделью, описывающей эту зависимость, является экспоненциальная модель с высоким коэффициентом детерминации ().
Доступность данных
Данные, использованные для подтверждения результатов этого исследования, включены в статью. Любые дополнительные данные, относящиеся к статье, могут быть запрошены у соответствующего автора.
Дополнительные точки
Практическое применение .Вышеупомянутые результаты предполагают, что опилки отработанного камня могут заменить известняковый наполнитель при производстве асфальтобетонной смеси, поскольку оба материала продемонстрировали схожие механические свойства и тенденции в этом исследовании. Более того, важно отметить, что источник этих двух материалов один и тот же. Известняковый наполнитель – это часть известняка, измельченного в местных карьерах из известняковых пород, а каменные опилки – это отходы, собранные на участках производства камня для строительных целей. По этой причине ожидается, что другие физические свойства двух материалов будут одинаковыми.В заключение, это исследование предлагает альтернативу (наполнитель из древесных опилок) известняковому наполнителю, который используется при производстве горячей асфальтовой смеси.
Раскрытие информации
Гази Г. Аль-Хатиб находится в отпуске в Университете Шарджи, P.O. Box 27272, Шарджа, ОАЭ.
Конфликт интересов
Авторы заявляют об отсутствии конфликта интересов в отношении публикации данной статьи.
Научно-практические аспекты создания битумно-эмульсионных мастик | Ф.Кемалов
[1] Кемалов, А.Ф. Практические аспекты разработки универсальных эмульгаторов для водных битумных эмульсий / А.Ф. Кемалов, Р.А. Kemalov World Applied Sciences Journal 23 (6): 858-862, 2013.
[2] Кемалов А.Ф. Интенсификация производства окисленных битумов и модифицированных битумных материалов на их основе – Дисс. доктором технических наук. Казань: КарГТУ, 2005. 354 с.
[3] Кемалов А.Ф., Кемалов Р.А., 2012. Исследование дисперсных полимерных систем для получения высококачественных полимерно-битумных материалов.Химия и технология топлив и масел, 48 (5): 339-343.
[4] Борисов С.В. Комбинированные битумные вяжущие в производстве гидроизоляционных и кровельных материалов: автореферат дис. канд. Казанского гос. техн. Университет, Казань, 2008.
[5] Сингх Б., Л. Кумар, М. Гупта, Г.С. Чаухан, 2013. Полимерно-модифицированный битум из переработанного полиэтилена низкой плотности и малеинированного битума. Журнал прикладной науки о полимерах, 127 (1): 67-78.
[6] Печеный Б.Г. Битумы и битумные композиции / Б.Печеный Г. – М .: Химия, 1990. – 256 с.
[7] Чжан, Х., Х. Цзя, Дж. Ю и Л. Сюэ, 2013. Влияние окисленных битумов и модифицированного битумного вспученного вермикулита на микроструктуру и свойства старения битума, модифицированного стирол-бутадиен-стирольным сополимером. Строительство и строительные материалы, 40: 224-230.
[8] Кашаев Р.С., Кемалов А.Ф., Дияров И.Н., Фахрутдинов Р.З. Корреляция между параметрами ЯМР и характеристиками битума. Роль упорядочивания структуры.Химия и Технология Топлив и Масел. Выпуск 2, февраль 1999 г., страницы 37-39.
[9] A.A. Вашман, И. Пронин. Ядерная магнитная релаксация и ее применение в химической физике. – М .: Наука, 1979. -236с.
[10] Керингтон А., МакЛеклан Э. Магнитный резонанс и его применение в химии. М .: 1970. 447с.
[11] Гользар, К., А. Джалали-Арани и М. Нематоллахи, 2012. Статистическое исследование физико-механических свойств основного и модифицированного полимером битума с использованием искусственной нейронной сети.Строительство и строительные материалы, 37: 822-831.
[12] Сюняев З.И. Масло-дисперсионные системы. / З.И. Сюняев, Р.З. Сюняев, Р.З. Сафиева – М .: Химия, 1990. -226 с.
[13] Байер Дж., Джегер Ф. и Шауманн Г. Э. (2010). Релаксометрия протонного ядерного магнитного резонанса (ЯМР) в почвоведении. Открытый журнал магнитного резонанса, 3, 15-26.
Асфальтобетонных изделий – EAPA
Следующие ниже описания асфальтовых смесей основаны на определениях, данных в Европейских стандартах на асфальт (серия EN 13108).Текст в кавычках – это определения, используемые в Европейских стандартах на асфальт.
1. Асфальтобетон (AC)
«Асфальт, в котором частицы заполнителя непрерывно отсортированы или отсортированы по зазорам для образования взаимосвязанной структуры». Плотный асфальтобетон часто используется в качестве «основного» поверхностного слоя.
2. Асфальтобетон для очень тонких слоев (AC-TL)
«Асфальт для дорожных покрытий толщиной от 20 мм до 30 мм, в котором частицы заполнителя обычно разделены на зазоры для образования контакта камня с камнем и для обеспечения открытой текстуры поверхности ».Эта смесь часто используется во Франции и называется BBTM (Béton Bitumineuse Très Mince).
3. Асфальт мягкий (SA)
«Смесь марок щебня и мягкого битума». Эта гибкая смесь используется в странах Северной Европы для дорог второстепенного значения.
4. Горячекатаный асфальт (HRA)
«Плотная битумная смесь с градуированными зазорами, в которой раствор из мелкозернистого заполнителя, наполнителя и высоковязкого связующего вносит основной вклад в характеристики уложенного материала».Стружка с покрытием (номинально частицы заполнителя одного размера с высокой устойчивостью к полировке, которые слегка покрыты высоковязким связующим) всегда скатывается в слой горячекатаного асфальта и является его частью. Этот прочный поверхностный слой часто использовался в качестве поверхностного слоя в Великобритании.
5. Каменно-мастичный асфальт (SMA)
«Асфальтобетонная смесь с щелевым слоем с битумом в качестве связующего, состоящая из каркаса из крупнозернистого заполнителя, связанного мастичным раствором». Эта смесь часто используется в качестве поверхностного слоя, если требуется высокая стабильность.Структура поверхности также обладает хорошими шумопоглощающими свойствами.
6. Мастичный асфальт (MA)
«Безпустотные асфальтовые смеси с битумом в качестве связующего, в которых объем наполнителя и связующего превышает объем оставшихся пустот в смеси». Эта смесь очень прочная и в некоторых странах часто использовалась в качестве поверхностного слоя.
7. Пористый асфальт (PA)
«Битумный материал с битумом в качестве связующего, подготовленный таким образом, чтобы иметь очень высокое содержание взаимосвязанных пустот, которые пропускают воду и воздух для обеспечения дренажа уплотненной смеси и снижения шума. характеристики”.
8. Двухслойный пористый асфальт (2L-PA)
Верхний слой с зернистостью 4/8 мм имеет толщину около 25 мм, а второй / нижний слой представляет собой пористый асфальт с крупным заполнителем (11/16 мм). . Общая толщина около 70 мм. Из-за более мелкой текстуры наверху (что снижает вибрацию шины) он дает лучшее снижение шума, чем однослойный пористый асфальт.
Двухслойное пористое асфальтовое покрытие
9.Асфальт для ультратонких слоев (AUTL)
“Асфальт для ультратонких слоев (AUTL) – это дорожное покрытие из горячего асфальта, уложенное на связующий слой номинальной толщиной от 10 мм до 20 мм со свойствами, подходящими для предполагаемое использование. Метод склеивания является важной частью процесса, а конечный продукт представляет собой комбинацию системы склеивания и битумной смеси ».
AUTL представляет собой смесь, в которой частицы заполнителя, как правило, разделены по зазору для образования контакта камня с камнем и обеспечения открытой текстуры поверхности.Несколько разновидностей этого слоя часто используются для создания нового хорошего шумоподавляющего поверхностного слоя.
Каменно-мастичный асфальт | Укладка и производство асфальта
Каменно-мастичный асфальт Perth
Stone Mastic Asphalt (SMA) представляет собой грубую смесь из износостойкого материала с высокой долей грубого заполнителя, которая сцепляется, образуя каркасную структуру, сопротивляющуюся постоянной деформации, и связывается мастичным раствором. Поставляется, укладывается и уплотняется в горячем состоянии.
Roads 2000 производит и поставляет свои собственные каменно-мастичные асфальтовые смеси и способна производить и укладывать смеси с максимальным размером камня 10 мм и 7 мм.Наша команда бригад по укладке асфальта сможет помочь вам безопасно уложить нашу смесь SMA в соответствии со спецификациями магистральных дорог и требованиями безопасности для вашего проекта.
Зачем использовать каменно-мастичный асфальт
SMA – это конструкционный асфальт, который в последнее время стал более популярным из-за его свойства маскировать отражающие трещины на открытой текстурированной поверхности. Поэтому он используется на всех дорогах от магистралей до жилых домов. Техническая спецификация IPWEA / AAPA для поставки и укладки горячего асфальтового покрытия дорог (Rev 3) содержит рекомендации по проектированию для SMA.Roads 2000 использует битум класса 320 исключительно для всех каменно-мастичных асфальтов.
При укладке каменно-мастичного асфальта рекомендуется, чтобы толщина слоя была не менее 3x размера камня или более 5x размера камня. Увеличенная толщина ограничивает возможность «волочения» мата. При укладке многослойного асфальта предыдущий слой необходимо дать остыть ниже 40 ° C. Уплотнение должно обеспечиваться только статическими стальными катками, а вибрационные катки или катки с резиновыми шинами не должны использоваться.
Каменно-мастичный асфальт подвергается высокому риску промывки сразу после установки и / или при высоких температурах. Спецификация 502 магистральных дорог для SMA рекомендует запрещать движение по готовому асфальту, если его температура превышает 40 ° C. Это может быть компенсировано измельчением и / или применением воды для (i) уменьшения контакта с поверхностным связующим и (ii) охлаждения асфальта до требуемой температуры. Roads 2000 не рекомендует использовать SMA на автостоянках или перекрестках с круговым движением (ref R2K-05).В США полимер используется в связующем для пересечений, покрытых SMA.
Roads 2000 может предоставить клиентам консультации по дизайну смесей, если это необходимо.
Список литературы
- Техническая спецификация IPWEA / AAPA, тендерная форма и график поставки и укладки дорожного покрытия из горячего асфальта (Ред. 3, апрель 2002 г.)
- Основы битумных покрытий AAPA (2010)
- Спецификация основных дорог 502 для каменно-мастичного асфальта (28.03.2011)
Прорыв в использовании регенерированного асфальта в смесях пористого асфальта
Доля вторичного использования сырья увеличивается втрое и превышает 90 процентов
Утрехт, 22 октября 2015 г. – БАМ удалось произвести ZOAB (пористый асфальтобетон) в промышленных масштабах, 93% которого состоит из регенерированного сырья.По сравнению с текущим процентом переработки ZOAB, который составляет от 0% до 30%, это означает прорыв в устойчивом производстве асфальта. Успешное испытание с использованием примерно 60 тонн ZOAB состоялось в четверг, 22 октября, на территории Brabantse Asfalt Centrale (Брабантский асфальтный завод) в Хелмонде. БАМ разработал этот инновационный метод производства в рамках демонстрационного проекта European Life + LE2AP.
Инновационная смесь ZOABBAM состоит из старого ZOAB, восстановленного камня и мастики.Восстановленная и впоследствии обогащенная мастика вспенивается, так что смесь может быть получена при температуре приблизительно 110 ° C. Помимо высокой стоимости повторного использования, это также обеспечивает снижение выбросов CO2 примерно на 30% и сокращение энергии примерно на 40%.
Камень (PA Stone) недавно был сертифицирован KIWA как новый строительный материал. PA Stone уже успешно используется в ZOAB в нескольких проектах дорог БАМа.
Поведение слоя ZOAB и рекуперированного сырья, используемого в нем, было протестировано с использованием различных методов в масштабе битума, мастики и смеси.Было показано, что восстановленное сырье и произведенный с его помощью асфальт имеют по крайней мере такое же качество, что и традиционно производимый ZOAB, а часто даже более высокого качества.
Рынок замены
С LE2AP БАМ выбирает новый путь переработки асфальта. LE2AP означает асфальтовое покрытие с низким уровнем выбросов, где цифра 2 означает, что это касается как звуковых выбросов, так и материалов, оказывающих воздействие на окружающую среду. Проект LE2AP частично финансируется за счет европейской субсидии LIFE +.
Основная идея LE2AP заключается в том, что принятый метод переработки асфальта ограничен. Эти ограничения были достигнуты промышленностью, и это ограничивает дальнейшее увеличение процента рециркуляции. По мере того как в Нидерландах строится все меньше и меньше дорог, важность горизонтальной переработки отходов возрастает. Рынок асфальта в настоящее время является скорее рынком замены, чем рынком с нуля.
Основная идея LE2AP – прекратить переработку асфальта и начать восстановление сырья из старого асфальта.Затем из восстановленного сырья можно производить новый асфальт. Этот метод работы дает полный контроль над качеством строительных материалов и рецептурой нового асфальта.
Обычно процесс LE2AP состоит из следующих шагов:
- Старый асфальт разделен на камень и мастику. Битум в старом асфальте появляется в основном в восстановленной мастике – смеси песка, наполнителя и битума – это означает, что восстановленный камень содержит только небольшое количество битума (часто <1%).
- Затем камень просеивается на различные фракции. Каменные фракции не нуждаются в дальнейшей обработке и сразу доступны в качестве высококачественного строительного материала (PA Stone) для производства нового асфальта.
- Восстановленная мастика содержит состаренный битум и поэтому требует обработки. Нагревая восстановленную мастику и обогащая ее свежим мягким битумом и омолаживающим средством, получают высококачественную мастику с постоянным процентным содержанием битума и постоянным качеством.Поскольку мастика доступна в виде отдельной фракции материала, ее можно хорошо перемешать во время этого обновления. Это оптимизирует смешивание старого и нового битума, а также создает очень однородную мастику.