видео-инструкция по монтажу своими руками, особенности оборудования, заводов, технология, цена, фото
С каждым годом производители теплоизоляции в России наращивают объемы поставок своей продукции. Такая тенденция объясняется ростом популярности термоизоляционных материалов, используемых как в промышленных целях, так и в частном хозяйстве.
Что такое тепловая изоляция, с какой целью она производится и чем объясняется ее востребованность?
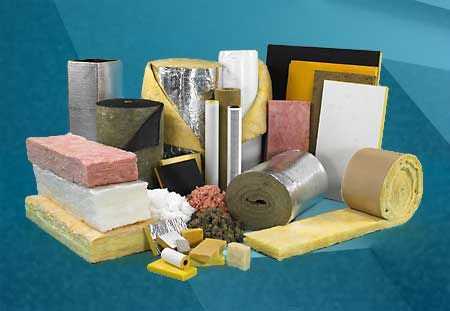
Широкий спектр утеплителей
Наиболее востребованные утеплители и их характеристики
Теплоизоляция – это широкий перечень материалов с низкой степенью теплопроводности, основной задачей которых является минимизация теплопередачи тех или иных сооружений и конструкций.
Классификация
Тепловая изоляция классифицируется в соответствии со сферой применения:

Использование утеплителя в строительстве
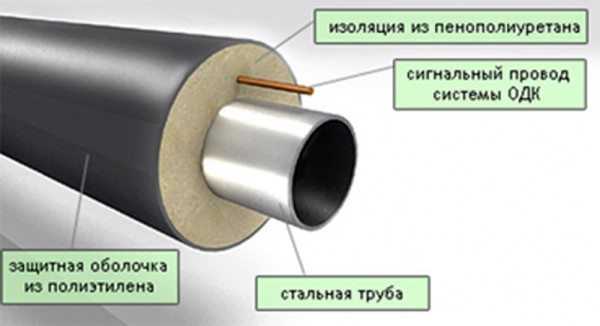
Изоляция трубопровода
- специальная изоляция представляет собой вакуумное и отражающее утепление.
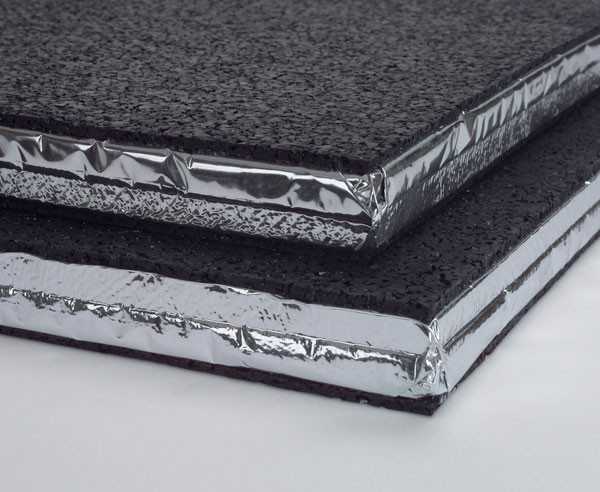
Вакуумные термоизоляторы
В соответствии с ГОСТ 16381-77, теплоизоляционные материалы классифицируются по следующим признакам:
- по типу использованного при производстве сырья – органические и неорганические;
- по типу структуры – волокнистые, зернистые и ячеистые;
- по типу консистенции – плоские (маты, плиты, войлок), рыхлые (перлит и вата), фасонные (сегменты, цилиндры и полуцилиндры), полосы.
Также утеплители классифицируются по степени горючести на:
- сгораемые;
- трудносгораемые;
- несгораемые.
Продукция современных предприятий
Современные производители теплоизоляционных материалов изготавливают следующие типы термоизоляции:
- Органические утеплители, представленные широким спектром разнообразных полимеров (вспененный полиэтилен, пенополистирол и т.д.). Такие материалы изготавливаются с объёмной массой 10-100 кг на 1 куб.м.
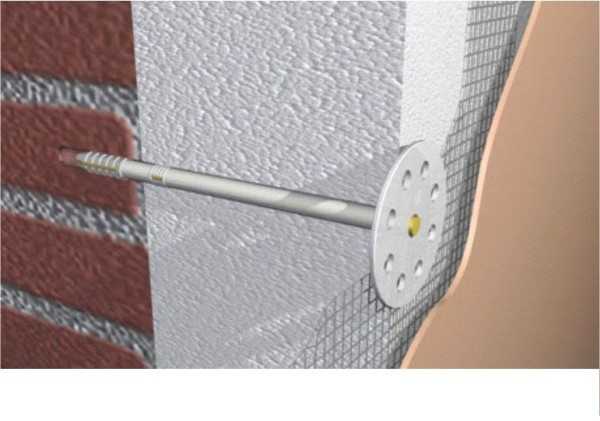
На фото пенополистирол на стенах
Первоочередным недостатком утеплителей данного типа является малая огнестойкость. В итоге, применение данной теплоизоляции не допускается при температуре выше +90 °C.
Материалы характеризует невысокая биостойкость, ограниченная гидрофобность и относительно доступная цена.
- Неорганические утеплители — это широкий перечень материалов, включая минеральную вату и производные, ячеистый и монолитный пенобетон, стеклянное волокно, пеностекло, перлит, вермикулит, сотопласты и т.д.
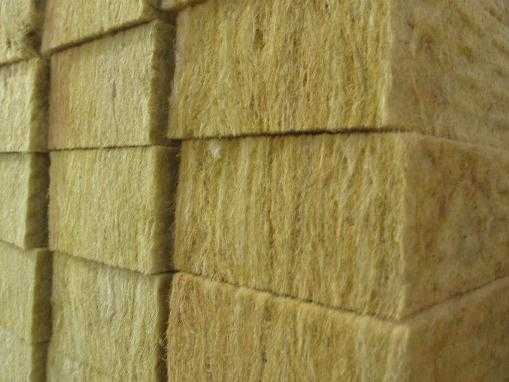
Минеральная вата в плитах
Производство теплоизоляционных плит из минеральной ваты осуществляется путем термической и механической переработки ряда металлургических шлаков и горных пород. Теплоизоляция характеризуется низкой прочностью в сочетании с повышенным водопоглощением. Поэтому инструкция применения этих материалов предусматривает использование пароизоляции в строгом соответствии с технологическими требованиями.
Современный производственный процесс, в ходе которого применяется оборудование для производства теплоизоляции, позволяет изготавливать минераловатные изделия с высокой степенью гидрофобизации волокон. В результате, водопоглощение материала при транспортировке и в ходе монтажа снижается.
- Смешанные утеплители применяются как монтажные материалы и производятся с применением асбеста, например, асбестовый войлок, картон и бумага.
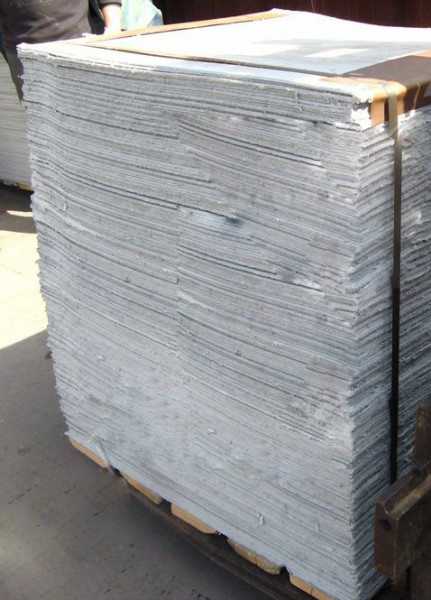
Асбестокартон для пожароустойчивой термоизоляции
На данный момент любой крупный завод по производству теплоизоляционных материалов изготавливает следующие типы продукции:
- пенобетон монолитный и ячеистый с плотностью не более 300 кг на м³;
- изделия из минеральной ваты (маты, плиты, скорлупы, цилиндры и т. д.;
- эковата;
- вспененный и экструдированный пенополистирол;
- вспененный полиэтилен ППЭ, НПЭ;
- пенополиуретан;
- вспененный каучук;
- вакуумные утеплители.
Жидкие утеплители и их преимущества
Не так давно рядом отечественных предприятий было освоена технология для производства жидкой теплоизоляции. Такой утеплитель внешне схож со стандартным ЛКП, но существенно отличается по своему составу.
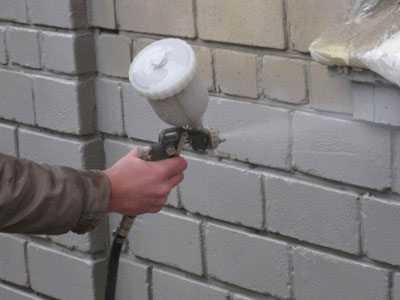
Нанесение жидкого утеплителя
Утеплители данного типа представляют жидкий раствор малоразмерных керамических или силиконовых шариков с вакуумом внутри. В качестве жидкой среды применяется синтетический каучук, акриловые полимеры, дополненные неорганическими пигментами.
Внешне жидкая изоляция напоминает суспензию, которая, по мере высыхания, образует сверхтонкое эластичное покрытие.
Данные материалы характеризуются:
- малым весом;
- эластичностью;
- относительной прочностью на истирание;
- отличной адгезией;
- простотой нанесения.
Основным преимуществом таких составов является возможность нанесения своими руками на поверхность любой конфигурации.
Важно: современные жидкие утеплители пригодны для обработки пластика, металла, бетона, а также штукатурных кирпичных и стеклянных поверхностей.
Лучшие образцы таких покрытий сохраняют свои технические и эксплуатационные качества в широком температурном диапазоне от -40 до +250 °C.
Производственные технологии
На данный момент более 60 % повсеместно используемой теплоизоляции составляют материалы с волокнистой структурой — это стеклянная, минеральная и базальтовая вата, изготовленная на основе тонких и супертонких волокон.
Производство теплоизоляционных материалов в России – это процесс, реализация которого осуществляется в промышленных условиях путем смешения и переработки песка, соды, известняков и целого ряда других химических добавок.
Полученная шихта погружается в оборудование для производства теплоизоляционных материалов и плавится до состояния вязкой стекловидной массы, из которой впоследствии производятся микроволокна. Для того чтобы скомпоновать готовый материал в единое целое микроволокна смешиваются со связующим веществом.
Производство шлаковаты осуществляется посредством плавления металлургических шлаков в сочетании с рядом добавок и с добавлением связующих веществ.
Производство минеральной ваты, в качестве основного сырья, использует широкий спектр минеральных ископаемых (глина, доломиты и т.п.). Для улучшения ряда эксплуатационных качеств, в состав утеплителя интегрируются такие добавки, как базальт, габбро, диабазам и прочие горные породы.
Производство базальтовой ваты осуществляется с применением расплавленного базальта и целого ряда сходных по параметрам горных пород. Такая технология производства теплоизоляционных материалов не предусматривает необходимости в использовании каких-либо синтетических и минеральных добавок.
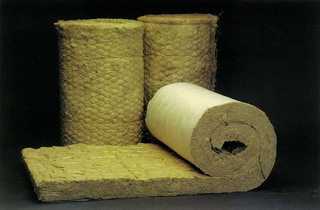
Базальтовая вата в матах
Для того чтобы придать расплаву базальтовых волокон большую текучесть в него интегрируется известняк или шихта в количестве 10-35 % от общего объема. Такая мера делает волокнистый материал менее устойчивым к воздействию высоких температур и агрессивных сред.
Важно: несмотря на то, что в качестве основного сырья, при производстве данного материала, был использован базальт, полученный утеплитель не является базальтовым волокном и его называют минеральной ватой.
Особенности тонких и супертонких базальтовых волокон
Тонкие волокна, в отличие от супертонких, получаются более короткими и толстыми. Например, базальтовые супертонкие волокна имеют толщину от 1 до 3 микрон при длине — более 50 мм. В то же время, базальтовые тонкие волокон имеют толщина волокна от 5 до 15 микрон при средней длине 50 мм.
Линия по производству базальтовой ваты
К категории тонких волокон относятся такие утеплители как стекловолокно, минеральное волокно и шлаковолокно, так как диаметр сечения таких волокон превышает 4 мкм. Особенности структуры тонких волокон негативно сказываются на степени прочности готового изделия.
А поэтому, для упрочнения структуры утеплителя, в массу волокон внедряются фенолформальдегидные смолы и аналогичные вещества в пропорции не более 10 % от общего объема материала.
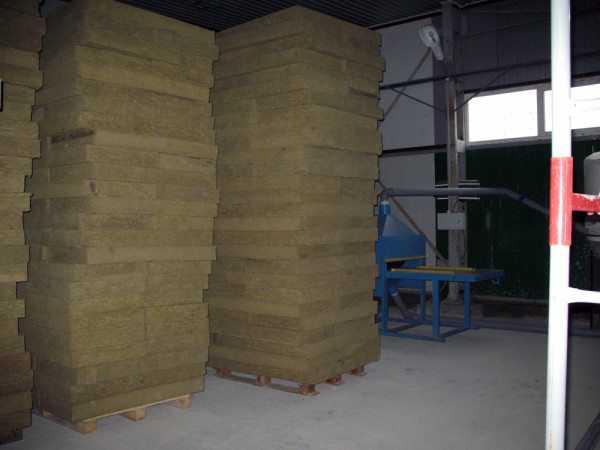
Утеплитель готовый к отправке
Теплоизоляционные материалы, произведённые на основе базальтовых волокон, характеризуются высокой температурой применения. Изделия, произведённые на основе тонкого базальтового волокна, могут закладываться на объектах, где максимальная краткосрочная температура достигает 400 – 600°С.
В то же время, теплоизоляция, произведённая из супертонкого базальтового волокна, имеет температуру долговременного применения до 700°С и краткосрочного использования до 1000 °С.
Вывод
Достаточно ввести в поисковую систему запрос «производство теплоизоляция» и можно будет увидеть то, что проблема повышения энергоэффективности объектов и сооружений актуальна. Повсеместная нехватка энергоресурсов и как следствие их перманентное удорожание вынуждает иначе относиться к методам повышения энергоэффективности зданий, трубопроводов и т.д.
Принимая во внимание востребованность эффективных и недорогих теплоизоляционных материалов, отечественные и зарубежные производители разрабатывают принципиально новые технологии снижения степени теплопроводности тех или иных материалов.
Воспользоваться этими разработками можно уже сегодня, так как утеплители для широкой сферы применения представлены на строительных рынках и в специализированных магазинах. Если возникли какие-либо вопросы по применению утеплителей, посмотрите видео в этой статье.pro-uteplenie.ru
Глава 3. Технология производства теплоизоляционных материалов
3.1. Описание технологической схемы производства теплоизоляционных материалов
Производство полужестких плит из базальтового волокна, получаемых из расплава горных пород методом центрифугирования.
Описание процесса.
Складирование сырья.
Сырье: базальт в виде щебня или бута поступает на завод авто или железнодорожным транспортом, хранится в не отапливаемом складе раздельно в отсеках, исключающих загрязнения посторонними примесями (глина, песок, металл) с минимальным запасом сырья до одного месяца работы предприятия.
Дробление сырья.
При поступлении крупными кусками сырье дробится на щековой и конусной дробилках с выделением на грохоте необходимых фракций. Мелкие фракции (отсев) реализуется, дробление сырья производится последовательно, дробленное сырье направляется ленточными конвеерами в соответствующие отсеки на промежуточное хранение.
Транспортировка исходного сырья.
Из отсеков исходное сырье загружается грейферным краном в автосамосвал, которым оно транспортируется в приемный бункер шихто-приготовительного отделения.
Приготовление шихты.
При использовании однокомпонентной шихты, дозирование и смешивание из процесса исключают.
Получение расплава.
Загрузка шихты в плавильную печь производится равномерным слоем через
загрузочные окна с помощью загрузчиков. Работа загрузчиков осуществляется от уровнеметра. Плавление сырья производится в ванной плавильной печи непрерывного действия с фидером.
Производительность печи до 28 тонн расплава в сутки. Удельный съем расплава с плавильной части печи до 900 кг/мг в сутки. Печь и фидер отапливаются мазутом и керосином форсунками. Уровень расплава контролируется уровнеметром. В стенах и в своде печи предусмотрены отверстия для установки термопар и уровнеметра. Для уменьшения расхода топлива и утилизации тепла отходящих газов, воздух идущий на горение, подогревается в регенераторе. Подача воздуха до 5000С. Газовая среда в печи окислительная, давление слабоположительное.
Получение расплава осуществляется по стадиям: плавление и стеклообразование, дегазация и гомогенизация в плавильной части печи. Для получения однородного расплава в выработочной части печи предусмотрен порог. Студка расплава до температурного интервала выработки происходит в выработочной части печи и фидере. Ванна бассейна печи и канал фидера выполняются из бакорового огнеупора, свод и стены рабочего пространства выкладываются динасовыми огнеупорами.
Выработка расплава.
Из плавильной части бассейна печи расплава поступает в выработочную часть печи и далее в фидер. Фидер имеет индивидуальное отопление керосином, с помощью которого поддерживается в нем необходимая температура. Фидер представляет собой канал шириной 0.5 м с приподнятым по отношению к ванне дном. Фидер оканчивается отверстием, через которое струя расплава направляется в сливное устройство, заканчивающееся водоохлаждающим и регулируемым лотком, направляющим струю расплава на первый валок центрифуги.
Волокнообразование и формирование ковра.
Струя расплава направляется на первый валок центрифуги с координатами по ширине точно в цент валка, по окружности- под углом 450 к вертикальной плоскости, проходящей через ось валка. Расплав, сбрасываемый с первого валка, должен полностью попадать на поверхность второго валка и далее последовательно на валки 3 и 4. В процессе волокнообразования участвуют все четыре валка. Благодаря высокому числу оборотов валков расплав приобретает ускорение и при этом вытягивается в волокно. Образовавшие волокна отдуваются от валков с помощью воздушных систем воздушного шкафа в камеру волокноосаждения.
При смещение струи с указанного места, вследствие образования на лотке настыли, оператор должен крючком сбросить настыль в отходы. Если смещение струи расплава произошло в результате значительного изменения выхода расплава, оператором регулируется положение струи перемещением лотка.
В камере волокноосаждения волокна охлаждаются и осаждаются на сетке приемно-формирующего конвейера. Под верхней ветвью сетки приемного конвейера установлена вакуум камера для удаления отработанного энергоносителя (воздуха).
Толщина волокнистого ковра регулируется скоростью движения приемного конвейера.
Скорость движения сетки конвейера регулируется от 1 до 5 м/мин. Перед сушильной камерой ковер уплотняется прижимным барабаном. Ковер должен иметь равномерную плотность.
Сушильная камера предназначена для установления свойств полужесткой плиты: степени затвердевания, толщины, плотности. Материал проходит через всю камеру между двумя конвеерами, которые определяют его толщину. Горячий воздух температурой 150…3000С просачивается через материал, в результате чего происходит сушка ковра последнего (отвердевание).
Резка затвердевшего ковра на отдельные плиты, осуществляется механизмами отрезки (ножи поперечной и продольной резки) через определенные промежутки времени по сигналу концевых выключателей. Предельные отклонения от номинальных размеров плит не должны превышать приведенных в таблице.
Таблица 7
Размеры | мм | Допускаемые отклонения, мм |
Длина | от 1000 до 2000 | + 30 ; – 20 |
Ширина | от 1000 до 2000 | |
Толщина | 50,60,70,80,100 | ± 20 ; +5 ; – 4 |
Маты должны иметь прямоугольную форму, ровные края и равномерную плотность.
Для подачи плиты далее по линии имеем промежуточный конвейер. Привод осуществляется от примыкающего агрегата.
Стол штабелёр поз. 20 служит сборником плит определенной высоты пачки.
Толкатель выполняет роль податчика собранного пакета плит на упаковочную машину или ЛУМП-2.
Упаковочная машина поз. 22 и ПУМП2 полностью автоматизированная линия для упаковки продукции в термоусадочную пленку, в данном случае пакет полужестких плит.
Транспортировка упакованного ковра на склад готовой продукции осуществляется тележкой.
Хранение.
Полужесткие плиты хранятся в штабелях высотой не более двух метров на очищенных бетонных площадках сухих, неотапливаемых помещений, при хранении в контейнерах возможна высота складывания до 4,5 метра.
studfiles.net
Теплоизоляционные материалы 2
Теплоизоляционные материалы (ТИМ) – материалы и изделия, обладающие низкой теплопроводностью и предназначенные для тепловой изоляции зданий, сооружений, тепловых промышленных установок, технологического оборудования, холодильных камер, трубопроводов, транспортных средств и других объектов.
Применение теплоизоляционных материалов является одним из важнейших методов энергосбережения, а также имеет важное технологическое значение, позволяя уменьшать толщину конструкционных элементов. Теплоизоляционными называют материалы, характеризующиеся низкой теплопроводностью и применяемые для тепловой изоляции строительных конструкций, промышленного оборудования и трубопроводов. Ассортимент применяемых в настоящее время утеплителей достаточно широк – от пенопластов до минераловатных композиций на полимерных и неорганических связующих.
Все теплоизоляционные материалы и изделия из них классифицируются по разным признакам на несколько групп. По виду основного исходного сырья различают: органические (пенополистирол, пенополиуретан, пенополивинилхлорид, вспененный полиэтилен, древесно-волокнистые изоляционные плиты, арболитовые изделия и др.) и неорганические (базальтовое волокно, минеральная, керамическая и стеклянная вата и изделия из них, диатомит, вспученный перлит и вермикулит, керамзит, пеностекло, ячеистые бетоны и др.). По структуре: волокнистые, зернистые (сыпучие), ячеистые. По форме: плоские (плиты, маты, войлок), рыхлые (вата, перлит), шнуровые (шнуры, жгуты), фасонные (сегменты, цилиндры, полуцилиндры и др.). По содержанию связующего вещества: содержащие и не содержащие. По термостойкости: несгораемые, трудносгораемые и сгораемые.
В настоящее время наиболее широкое распространение получили следующие виды теплоизоляционных материалов: минеральная вата, базальтовое волокно, стекловата и изделия из них, перлитовые теплоизоляционные материалы, пенодиатомитовые теплоизоляционные материалы, пеностекло, ячеистые бетоны (пенобетон и газобетон) и керамзит. А с развитием современных технологий фасадной отделки зданий и сооружений особенно бурно растет российский рынок утеплителей из волокнистых теплоизоляционных материалов на композиционных полимерных и неорганических связующих, одним из компонентов которых являются ПОЛИВИНИЛАЦЕТАТНЫЕ ДИСПЕРСИИ.
Твердой фазой и основной составляющей всех волокнистых теплоизоляционных материалов является волокнистая вата, получаемая из расплавов различных горных пород и других силикатных материалов, а также из доменных и мартеновских шлаков и из прочих отходов металлургических производств. Волокнистая вата состоит из стекловидных волокон и неволокнистых включений, образованных в результате затвердевания силикатного расплава. Волокна в среднем имеют диаметр 1 – 10 мкм и длину от 2 – 3 до 20 – 30 см. Минеральную вату получают из расплава легкоплавких горных пород, силикатных промышленных отходов, доменных шлаков и их смесей. Минеральная вата предназначена для изготовления теплоизоляционных, звукоизоляционных и звукопоглощающих изделий, а также в качестве теплоизоляционного материала в строительстве и промышленности с предельной температурой эксплуатации до 600 – 700 °C. При более высоких температурах наблюдается спекание волокон минеральной ваты. Базальтовое волокно и каменную вату получают из расплава базальтовых пород (базальтов, габбро, диабазов и близких к ним метаморфических горных пород и мергелей) при температуре около 1500 °C. В отличие от минеральной ваты, выпускаемой, преимущественно из смеси легкоплавких пород с промышленными минеральными отходами, теплоизоляционные материалы из базальтового волокна обладают более длительным сроком службы, повышенной виброустойчивостью, термо- и водостойкостью. Базальтовая теплоизоляция не изменяет своих начальных свойств в течение всего времени эксплуатации, не выделяет вредных веществ в окружающую среду, и не образует токсичных соединений с другими материалами. Основными компонентами для производства стекловолокна и стекловаты являются стеклобой, песок, сода, доломит, известняк, этибор и другие компоненты. Процесс волокнообразования происходит из расплавленной при температуре около 1400 °C стеклянной массы, которая распускается на волокна, как правило, под действием центробежной силы на центрифугах.
В настоящее время при производстве волокнистых теплоизоляционных материалов используют три основные технологии волокнообразования: центробежно-дутьевая, многовалковая и фильерно-вертикально-дутьевая. Наиболее распространенным является центробежно-дутьевой способ. При этом следует отметить, что вырабатываемая данным способом вата отличается низким качеством, с большим (до 25%) количеством неволокнистых включений и отходов волокнообразования. Фильерно-вертикально-дутьевой способ обеспечивает безотходную переработку расплава, но ввиду малой мощности и дороговизне применяемых в технологическом процессе питателей из платинородиевого сплава он используется, в основном, на линиях низкой производительности. Центробежно-валковый способ (центробежно-многовалковый) наиболее широко распространен в зарубежной практике и основан на подаче расплава на быстро вращающиеся валки. В России данная технология также внедрена на ряде крупных российских предприятий.
Качество изделий из волокнистых теплоизоляционных материалов определяется многими параметрами. Среди наиболее значимых – химический состав твердой фазы, содержание неволокнистых включений, геометрия и ориентация волокон в пространстве, качественное, экологически безопасное связующее.
От химического состава твердой фазы в первую очередь зависят такие характеристики теплоизоляционных материалов как прочность, термостойкость, химическая стойкость. Прочность теплоизоляционных материалов определяется также параметрами поровой структуры изделия и ориентацией волокон в направлении действия напряжений. Однородное распределение пор по объему и уменьшение их среднего диаметра повышает прочность теплоизоляционных материалов. Прочность на сжатие возрастает с ростом количества вертикально ориентированных волокон. Положительно влияет на прочность также подбор связующего с улучшенными адгезионными свойствами по отношению к заполнителям.
Волокнистая структура также обеспечивает другое важное свойство волокнистых теплоизоляционных материалов – низкую теплопроводность, а также пренебрежимо малую усадку и сохранение геометрических размеров изделий в течение всего периода эксплуатации. Теплопроводность разных типов минеральных ват при нормальной температуре составляет 0,034 – 0,045 Вт/(мм/°С) и во многом зависит от геометрии и ориентации волокон в пространстве. Наиболее эффективными теплоизоляторами являются изделия с беспорядочно ориентированными волокнами.
Большинство изделий из волокнистых теплоизоляционных материалов обладают высокой термостойкостью, эффективно препятствуют распространению пламени и применяются в качестве противопожарной изоляции и огнезащиты. Более кислые составы имеют большую стойкость, чем основные. Волокнистые изделия из горных пород базальтовой группы могут применяться в условиях очень высоких температур. Базальтоволокнистые материалы способны выдерживать температуру до 1000 °C и выше, и даже после разрушения связующего компонента, их волокна остаются неповрежденными и связанными между собой, сохраняя свою прочность и создавая защиту от огня.
Важной составляющей волокнистых теплоизоляционных материалов, оказывающей большое влияние на эксплуатационные и теплофизические характеристики волокнистых утеплителей, являются современные многокомпонентные связующие. Для волокнистых теплоизоляционных материалов характерно высокое водопоглощение, достигающее при погружении в воду до 600%. А, как известно, увеличение влажности теплоизоляционного материала значительно ухудшает его теплоизоляционные свойства. Применение гидрофобизирующих пропиток в составе связующего позволяет снизить водопоглощение до 1,5 – 2%. Исследования по выбору связующего для производства теплоизоляционных плит показали эффективность использования для этих целей композиций из компонентов органического и неорганического происхождения. Применяемые в настоящее время комбинированные связующие, содержащее в своем составе ПОЛИВИНИЛАЦЕТАТНУЮ ДИСПЕРСИЮ, синтетические смолы, натриевое жидкое стекло, поверхностно-активные вещества, гидрофобизатор, обеспыливающие и другие добавки, обеспечивают высокие эксплутационные свойства получаемых изделий, с повышенными показателями термо- и водостойкости, эффективными водоотталкивающими свойствами, неизменностью структуры, стабильностью геометрических размеров на весь
mirznanii.com