Опилкобетон-пропорции объема ведрами
Опилкобетон также называют арболитом (но для арболита используется щепа), это легкий вид бетона, разработанный в середине прошлого века, обладающий множеством преимуществ относительно некоторых современных материалов. В его состав входят природные компоненты, безвредные для здоровья человека и экологически чистые.
Опилки являются натуральным утеплителем органического происхождения, поэтому опилкобетон значительно теплее обычного бетона. Малый вес опилок обуславливает легкость получаемого материала, в то же время он удивительно прочный, не горит, обладает шумоизоляцией и недорогой стоимостью. К недостаткам материала можно отнести длительный период высыхания и повышенную водопроницаемость.
Подготовка опилок
Для изготовления опилкобетона используются любые виды древесных опилок. Лучшими по качествам считаются полученные при обработке хвойных деревьев и лиственницы как наиболее устойчивые к процессам гниения. Рекомендуется перед добавлением в бетон просушить их в защищенном от солнца месте в течение 2-3 месяцев.
Приготовление опилкобетона для стяжки
Для нижнего слоя стяжки нужно взять 1 ведро цемента марки М 400, 2 ведра песка и 6 ведер опилок. Пропорции для верхнего слоя: 1 ведро цемента, 2 – песка и 3 – опилок. При желании можно добавить для 1-го слоя на 1 ведро цемента 3 кг гашеной извести, для 2-го слоя – в два раза меньше (1,5 кг). На высыхание изготовленной таким способом стяжки толщиной 10-15 см потребуется примерно 1 месяц.
В условиях промышленного производства ускорение этого процесса достигается добавлением специальных добавок, способствующих минерализации наполнителя. На 1 ведро цемента добавляют 250 гр. хлорида кальция (Е 509), а также применяется нитрат кальция, сульфат аммония, жидкое стекло, известь, которые ускоряют затвердевание раствора. Последовательность добавления материалов: в воду насыпаются опилки, затем цемент, потом песок и добавки. Отсутствие добавок не влияет на качество бетона, просто его высыхание займет больше времени.
Изготовление блоков из опилкобетона
Готовые блоки из опилкобетона имеют плотность от 500 кг/м³, что позволяет строить из них дома, гаражи и другие хозяйственные сооружения. Выпускаемые промышленностью материалы фибролит и карболит содержат в своем составе цемент и древесные опилки, благодаря чему обладают низкой теплопроводностью и эффективно удерживают тепло в помещении. По выводам санитарно-гигиенических экспертиз, опилкобетон превосходит все другие виды бетона по многим показателям. Недостатком этого материала является способность впитывания влаги из окружающей среды. Поэтому для того, чтобы предохранить стены от увлажнения следует позаботиться о гидроизоляции фундамента, сооружении отмостки, отделке наружных стен обожженным кирпичом или цементным раствором.
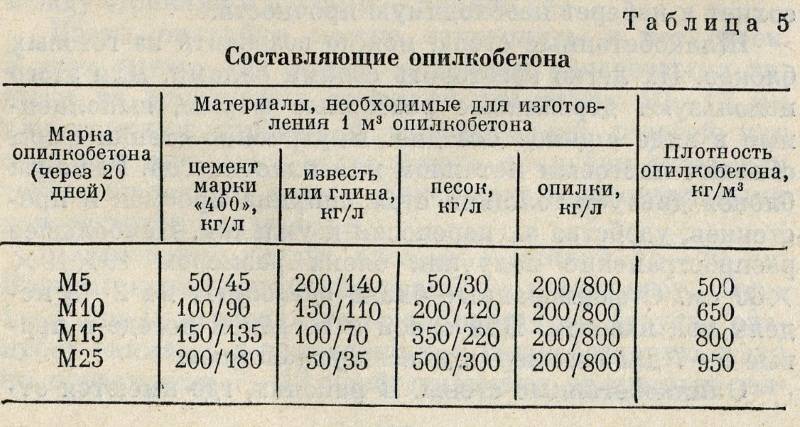
Состав опилкобетона различных марок
Для изготовления марки М5 на 80 ведер опилок (200 кг) нужно взять 4,5 ведра цемента М400 (50 кг), 3 ведра песка (50 кг), 14 ведер глины или извести (200 кг). Плотность опилкобетон данной марки составит 500 кг/м³, он так же, как и М 10 обеспечивает хорошую теплоизоляцию и может применяться для сооружения подвалов. В состав марки М10 на 80 ведер опилок берется 9,5 ведер цемента, 12 – песка и 10,5 – извести или глины. Плотность получаемого материала 650 кг/м³.
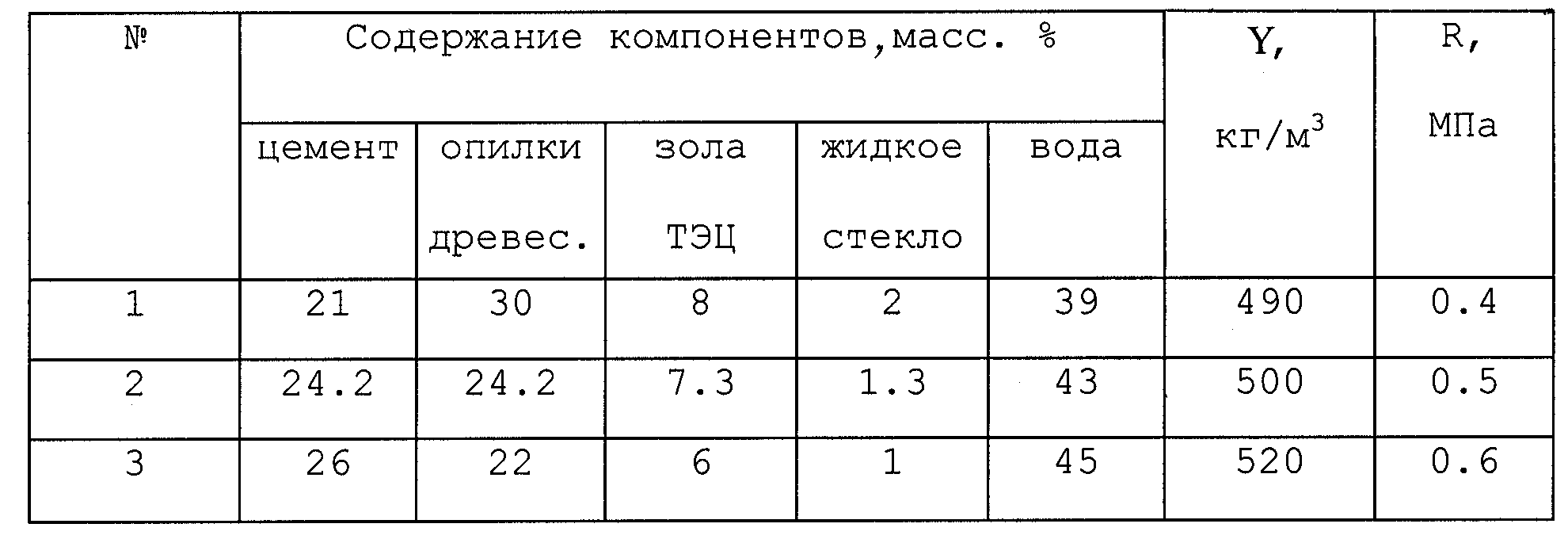
Из-за длительного высыхания опилкобетона при строительстве стен используют не сооружение опалубки, а готовые, предварительно высушенные блоки. Чаще всего делают блоки толщиной 140 мм, чтобы удобно было использовать в кладке при необходимости обожженный красный кирпич или его части. При изготовлении блока опилкобетона в нем делают 2 или 3 отверстия, ускоряющие процесс сушки и снижающие теплопроводность материала. Блоки из опилкобетона очень прочные, не имеют трещин, удобны для кладки стен строений.
Опилкобетон своими руками: пропорции, состав, видео
Опилкобетон – лёгкий бетон, в состав которого входит цемент, опилки, минерализаторы и песок. Материал экологически чистый, имеет низкий объёмный вес, высокую устойчивость к огню, низкую теплопроводность и высокую паропроницаемость. Используется для возведения монолитных зданий или для изготовления строительных блоков, в том числе применяется для возведения несущих конструкций, идеально подходит для малоэтажного строительства.
Опилкобетон может быть нескольких видов, в зависимости от плотности и, соответственно, прочности. Каждый из видов материала отвечает следующим маркам прочности: М5, М10, М15, М20. Первые две марки применяются исключительно в качестве утеплителя, возведение из них несущих конструкций нежелательно. В качестве несущих конструкций в малоэтажном строительстве применяют последние две марки. Если же проводится многоэтажное строительство из опилкобетона, то обязательно применение несущего каркаса.
Сфера применения опилкобетона
Материал имеет широчайший спектр применения, при этом он очень часто производится своими руками. С помощью данного материала можно возводить хозяйственные постройки, также часто практикуется строительство домов из опилкобетона, утеплительных стен для тех же домов, подвалов или даже бани из опилкобетона.
Материал сравнительно лёгкий и дешёвый, кроме этого, сэкономить можно и на основании для здания, используя ленточный фундамент. Если же проводить реконструкцию зданий или же утеплять их, то в усилении фундамента нет необходимости.
Фото: дом из опилкобетонных блоков
Подготовка сырья для изготовления опилкобетона своими руками
В предварительной подготовке нуждается только древесная часть состава. Для начала её нужно просеять через сито с размером ячейки не более одного квадратного сантиметра.
Опилки можно предварительно просушить, но это необязательно. В последующем просто будут внесены поправки с учётом влажности опилок. Если и сушить, то весь объём, а не частично!
Главнейшим этапом подготовки опилок является их минерализация. Проводится эта процедура для лучшего связывания цемента с древесной частью, придания ей стойкости к огню и биологическим факторам.
Проводится минерализация замачиванием опилок в растворе минерализатора. В качестве минерализатора допустимо использовать гашеную известь, жидкое стекло, кальция хлорид, сернокислый кальций.
Опилки для изготовления опилкобетонных блоков
Приготовление смеси для опилкобетона своими руками
Для приготовления смеси своими руками обычные бетономешалки практически не подходят, намного лучше использовать растворосмесители или же в крайнем случае ручное смешивание своими руками, что весьма затруднительно при больших объёмах.
Для приготовления каждой из марок материала используют свою пропорцию при одном и том же составе:
- М5 – для данной марки используют опилки, известь или глину, песок и цемент в соответствующей пропорции 4:4:1:1;
- М10 – опилки, известь или глину, песок и цемент смешивают в пропорции 4:3:4:2;
- М15 – смешивают опилки, известь или глину, песок и цемент в пропорции 4:2:7:3;
- М20 – используют следующую пропорцию опилок, извести или глины, песка и цемента 4:1:10:4.
Далее, медленно добавляют воду, например, из ведра или лейки, постепенно перемешивая смесь до получения рассыпчатой на вид консистенции, но сохраняющей форму после сжатия в кулаке, при этом не должно выделяться влаги.
Растворосмеситель
Рекомендуется использовать именно предложенные пропорции, так как они проверены опытом и являются оптимальными.
Совет прораба: всегда учитывайте тот факт, что чем выше плотность, тем хуже теплотехнические показатели, но тем выше несущая способность готового материала.
Литьё опилкобетона
При производстве опилкобетона своими руками по предложенному составу и пропорциям с последующим формированием его в готовое изделие пользуются заранее подготовленными формами для блоков нужного размера. Также можно пользоваться съёмными и несъёмными опалубками в случае монолитного строительства.
При производстве блоков своими руками объём уже замешанного состава помещают в формы, покрытые изнутри гидроизолятором. Для придания блокам большей прочности в раствор можно помещать продольную арматуру. Для облегчения изделия можно помещать вертикально расположенные пластиковые трубы на всю толщу формы.
Использование опилок с различными глинами для утеплителя чердачных потолков
Если задаться целью выполнить утепление перекрытия дома с наименьшими затратами и при этом не потерять в качестве, то таким незаменимым материалом можно считать отходы древесного производства.
Опилки или стружку, можно не утруждаясь, дешево приобрести в любой ближайшей столярно-плотницкой мастерской.
Для выполнения утепления нужно будет потрудиться, так как смешивание опилок с вяжущими и монтаж на перекрытие несколько более трудоемкий по сравнению с готовыми утеплителями. Но эксплуатация дома, защищенного от холодных масс подобным образом, приятно удивит хозяев, и будет не жалко времени, потраченного на работу.
Преимущества и недостатки
Положительные стороны утепления потолка опилками:
- Экологическая чистота утеплителя из опилок.
Глина, цемент и известь, являются полностью природными материалами и не выделяют вредных веществ. При замесе в домашних условиях потребитель не заинтересован в добавлении химических добавок в массу для утепления.
- Отличные теплоизоляционные характеристики полученного материала. У дерева очень низкая теплопроводность, это качество передается опилкам как утеплителю.
- Относительно легко утеплить потолок опилками. Древесные отходы обладают небольшой объемным весом и не добавят нагрузки на несущие стены и фундамент.
- Слой глины в строительстве частных домов очень часто используется как водный барьер. При протекании кровли чердака, влага будет насыщать глину, она ее впитает, и не будет передавать на основание. Сменяющиеся периоды увлажнения и высыхания гарантируют, что влага и вовсе никогда не попадет на внутреннюю поверхность потолка.
- При утеплении опилками пола чердака, можно поверх него выполнить дополнительные слои стяжки или выстлать дощатый пол. Чердак можно эксплуатировать и ходить по такому основанию.
Недостатки опилок как утеплителя:
- Экологическая чистота материала может привлечь для обитания в массе опилок различных грызунов и насекомых. Для их отпугивания опилки смешивают с небольшим количеством извести и гипса, что затрудняет или делает невозможным прокладывать ходы в толще утеплителя.
- Стружка и опилки являются гидрофобным материалом и могут напитаться влагой от конденсата из помещения, расположенного ниже потолка. Этот недостаток исправляется выполнением пароизоляционного слоя непосредственно по перекрытию перед утеплением опилками.
- Древесные отходы подвержены горению, что создает высокую опасность возгорания на чердаке. Опилки, перемешанные и застывшие в цементе и глине, не являются горючим материалом.
- Следует закономерный вывод, что применять опилки насыпом, без перемешивания с другими природными связующими не считается целесообразным.
Правила выбора древесного материала
- Если делать выбор между стружкой и опилками, выбор падает на второй вариант.
Чем меньше фракция отходов древесного производства, тем выше теплоизоляционные свойства материала.
- Опилки разных пород дерева имеют разные свойства. Хвойные породы легче по массе и содержат больше смол в своем составе. Они будут лучше утеплять жилище. Лиственные и фруктовые породы тяжелее и плотнее, чемпионом считается береза.
- Применять сухие опилки нужно только в случае перемешивания их с сухой известью для засыпки. В различных других случаях, при соединении их с компонентами во влажном состоянии, сухость массы опилок принципиального значения не имеет. При выборе опилок играет роль не сама влажность как таковая, а возраст сырья. Выполнять утепление из опилок свежего дерева нельзя. Они должны набрать возраст, «протряхнуть» желательно в течение года.
- При выборе стружечной или опилочной массы необходимо проверить, чтобы в состав не попадали отходы коры деревьев. В толще коры гнездятся жучки и насекомые, нужно наиболее эффективно исключить их попадание в утеплитель.
Процесс утепления потолка глиной с опилками
Прежде всего, нужно тщательно осмотреть всю поверхность под укладку утепляющей массы на чердаке. Щели в потолке и стыки перекрытия со стенами тщательно заделать монтажной пеной для наружных работ. Некоторые слои пены могут не попасть под укрытие утеплителем и при зимних морозах могут растрескаться и прийти в негодность и не утеплять зазоры.
Все деревянные поверхности пропитать антисептиком. Хорошо подходит каменноугольный креозот.
Площадь основания убрать от мусора. Для подложки под опилочный пласт используется толстый картон от ящиков или от упаковки крупных предметов. Его прибивают к деревянным частям основания.
Состав смеси для утепления состоит из 10 частей дерева и одной части глины. Вначале смешиваются сухие компоненты, а вода добавляется постепенно вместе с тщательным перемешиванием. На вышеуказанный состав материалов идет приблизительно 1–1,5 части воды.
Замешивание раствора глины с опилками производится небольшими партиями внизу и поднимается на чердак ведрами. Если утепление выполняется при незакрытой кровле чердака, то можно использовать для подачи лебедки и подъемные роликовые механизмы.
Утепление потолка делается двумя слоями. Первый выполняется из более крупных древесных отходов толщиной от 5 до 10 см. Второй должен быть приготовлен практически из пыли, его толщина колеблется от 8–15 см.
Укладка второго слоя предусматривает полное высыхание первого. При схватывании на поверхности массы обязательно появятся мелкие трещины, которые заделываются тем же раствором.
При накладывании утепления делается легкое уплотнение. Для этого можно из подручных материалов изготовить примитивную трамбовку с рабочей площадью основания примерно 25 на 25 см.
Полное высыхание утеплителя достигается в течение 3–5 недель. Далее, изготавливается пол, по которому будут ходить люди при эксплуатации чердачного помещения.
Стяжка пола выполняется из цементно-песчаного раствора в соотношении 1 части цемента и 3 частей песка. Дальнейшая отделка пола зависит от желания заказчика и функционального назначения чердака.
Если предусматривается дощатый пол, то установка лаг делается до укладки утеплителя, а опилки укладываются в промежутки между лагами. В этом случае необходимо защитить картоном не только поверхность пола, но и лаг тоже.
Утепление с помощью извести и опилок
Известь применяют для защиты утеплителя от микроорганизмов. Известковый компонент является антисептиком от мышей, крыс и жучков.
Для приготовления смеси из древесных отходов и извести требуется соотношение объемных частей 1: 10. На 1 ведро извести берут 10 ведер состаренных опилок. При замене извести на известковое тесто, его количество повышают вдвое.
Если к такому раствору добавляют гипс в количестве 0,5 части, то замешивание выполняют порциями не более ведра и делают непосредственно на месте укладки, на чердаке. Гипс переводит сыпучую массу в твердую консистенцию, которая не подвергается усадке. Такой раствор быстро схватывается.
Перемешивание идет с постепенным добавлением воды. Проверяется степень годности раствора для укладки сжиманием в руке. Смесь готова, когда она не рассыпается и из нее не вытекает влага.
Слой утепления опилок с известью делается один, толщиной свыше 10 см. Также требуется механическое уплотнение.
Цемент с опилками
Приготовление утеплителя с применением цемента, ведется по технологии замешивания опилок с глиной.
Цемент с опилками является более тяжелым. К недостаткам относится то, что такой слой подвержен намоканию и не сможет удерживать воду. Выравнивание цементно-опилочной стяжки выполняется строительным правилом.
Так как цемент придает дополнительную прочность, то возможно, использование слоя утеплителя в качестве основания для дальнейшей отделки пола мансарды.
Соотношение раствора, в этом случае делается 1:2:6 (цемент, песок, опилки). Такой материал носит название бетона из опилок. Вначале, смешиваются песок и цемент, затем вмешиваются опилки, затем добавляется вода. Для облегчения и ускорения работы возможно, применение бетономешалок.
Арболит
В 60-е годы прошлого столетия был запатентован строительный материал под названием арболит. В настоящее время плиты из него активно применяют для утепления потолка в частных домах. Этот вид материала не что иное, как обыкновенный легкий бетон. Такие панели толщиной 100 мм можно приготовить дома, кустарным способом, если высушивать массу в специальных плоских формах.
Для изготовления их используют на опилки, а стружку. Все древесно-стружечные материалы содержат в своем составе сахаристые вещества, которые способствуют разрушению структуры бетона. Чтобы нейтрализовать их, стружку перед применением обрабатывают известковым молочком, затем высушивают. После такой подготовки она является идеальным наполнителем для изготовления плит утеплителя.
Зачем нужна изоляция от пара
Все ограждающие элементы дома, контактирующие с холодным воздухом снаружи и теплой циркуляцией внутри подвержены образованию конденсата, то есть капелек влаги на своей поверхности. Если не выполнить изоляцию перекрытия, то утеплитель будет намокать и его свойства будут нарушены.
Существует много разновидностей паронепроницаемых пленок. Самой простейшей является обыкновенный полиэтилен. Его применение не требует различия, какой стороной укладывать его к утеплителю для всех других материалов нужно внимательно читать инструкцию по применению, иначе при неправильной укладке, достигается противоположный эффект.
Укладывать полосы полиэтилена или другого изолятора нужно с перехлестом до 15 см, покрывается вся поверхность без зазоров, целостность укладки играет огромную роль.
При выборе материала для изоляции от паров потолка следует обратить внимание на свойства изоляционного изделия. Есть мембраны, которые пропускают пар частично, а некоторые задерживают его полностью. Оптимальным будет соотношение доступной цены и многофункциональное качество.
При укладке слоя для изоляции от паров из внутреннего помещения предусматривается промежуточный вентиляционный слой. Если его не выполнить, то подмоченный утеплитель будет постоянно находиться во влажном состоянии и гнить. Кроме того, от постоянного контакта с влагой будут разрушаться и сами конструктивные элементы каркаса дома.
Глина подразделяется на жирную, полужирную и тощую (суглинок) по содержанию в ее природном составе песка. Чтобы утеплять потолок больше подходит жирная глина. Кусочки такого материала на ощупь мыльные или жирные, как кусок сала. Чем жирнее глина, тем больше ее пластичность и, соответственно, пластичнее и смеси из нее.
Цвет глины определяют минеральные примеси, входящие в ее состав. Насыщенная железом и марганцем, она будет иметь красный или оранжевый цвета, примеси органики придадут ей серый, бурый или черный оттенок.
Цемент производят измельчением клинкера и гипса. Клинкером называют спекшуюся однородную массу из известняка и силикатной глины. Цемент при добавлении воды образует пластичную массу, которая при застывании твердеет до прочности камня. Цемент может схватываться и набирать прочность в любых условиях, на воздухе и в водной среде.
Утепление потолка своего жилища с помощью опилок становится все более распространенным способом за последние годы. Человечество делает осознанный выбор естественных природных материалов и все чаще отказывается от ненатуральных и искусственных составляющих. Комфорт и экологическая чистота домашнего очага зависит от самого человека.
состав, характеристики, плюсы и минусы
1. Состав.
Представим базовый состав опилкобетонной смеси с удельным весом 1100 кг/м 3 в виде таблицы.
Наименование материала | Масса, кг | % от массы | Объём, л | % от объёма |
---|---|---|---|---|
Цемент М400 | 200 | 18,2 | 166 | 11,4 |
Песок | 590 | 54 | 393 | 26,7 |
Опилки | 200 | 18,2 | 800 | 54,8 |
Хлористый кальций и др.![]() | 5 | 0,5 | 4,5 | 0,3 |
Вода | 100 | 9,1 | 100 | 6,8 |
1.1. Цемент.
Рекомендуется применение цемента марки не ниже чем М-400 (ГОСТ 10178-85).
1.2. Песок.
В качестве основного наполнителя используется песок крупной или средней фракций (ГОСТ 8736-93), создающий прочный скелет блока, в который рекомендуется добавлять мелкий песок, доля которого не должна превышать 10%.
1.3. Опилки.
Возможно применение опилок практически всех пород деревьев. Предпочтительнее использование хвойных, поскольку они меньше подвержены гниению. Перед применением опилки желательно выдерживать под навесом в течение 2-3 месяцев. В случае использования опилок без предварительной выдержки необходима их обработка в смесителе защитными составами.
1.4. Основные добавки.
Для нейтрализации органических веществ, выделяемых опилками, и для сокращения времени затвердевания опилкобетона необходимо применение добавок: извести, сульфата аммония, жидкого натриевого стекла. Наиболее эффективным является добавление хлорида кальция (ГОСТ 450-77).
1.5. Вода.
Желательно применение воды, не загрязненной примесями (ГОСТ 23732-79). При умеренном содержании солей возможно использование морской воды.
2. Классификация.
Опилкобетонные блоки (как и любые стеновые бетонные камни) должны соответствовать ГОСТ 6133-99. Их можно классифицировать по следующим параметрам.
2.1. Применение.
- Стеновые блоки предназначены для кладки наружных и внутренних стен.
- Перегородочные блоки – для кладки перегородок.
2.2. Форма.
- Полнотелые – стеновые или перегородочные блоки без пустот.
- Пустотелые – блоки как со сквозными, так и глухими пустотами, формируемыми в процессе изготовления для придания блоку необходимых эксплуатационных характеристик.
2.3. Размеры.
- В соответствии с ГОСТ 6133-99 размеры блоков для кладки стен могут быть: 288х288х138мм, 288х138х138мм, 390х190х188мм, 290х190х188мм, 190х190х188мм, 90х190х188мм.
- Размеры блоков для перегородок: 590х90х188мм, 390х90х188мм, 190х90х188мм.
Допускается изготовление блоков других размеров.
3. Характеристики опилкобетона.
Характеристики обилкобетонного блока для базового состава смеси.
Наименование показателя | Значение | Комментарий |
---|---|---|
Прочность, кг/см2 | М 35 | Значительная прочность, учитывая низкий удельный вес и, как следствие, низкую нагрузку. Прочность может быть увеличена при увеличении содержания цемента. Опилки в блоке играют роль армировки. Благодаря этому достигается повышенная прочность на растяжение и изгиб. По этому показателю опилкобетонные блоки превосходят большинство строительных материалов. Её можно регулировать путём изменения соотношения вяжущего вещества и наполнителя. При высокоэтажном строительстве возможно использование цемента марки М-500, повышение его содержания в блоке и применение модифицирующих добавок. При возведении одноэтажных построек достаточно показателя в 20 кг/см2. При изготовлении блоков с такими характеристиками можно добиться значительной экономии дорогостоящего цемента. |
Объемный вес, кг/м3 | 1100 | При увеличении % содержания цемента в смеси увеличится объемный вес и прочность. |
Теплопроводность, Вт/м*К | 0,29 | Показатель лучше, чем у кирпича и бетона. По этому показателю он предпочтительнее кирпича и бетона. Теплопроводность увеличивается с увеличением содержания в опилкобетоне цемента. Применение в строительстве пустотелых блоков уменьшает теплопроводность стен и делает дом теплее. |
Морозостойкость, циклы | 50 | Материал выдерживает 50 циклов. Специальные меры позволяют увеличить ресурс. |
Усадка, мм/м | 0,5-1,5 | Достаточно высокое значение, затрудняющее отделочные работы.![]() |
Водопоглощение, % | 8-12 | Высокое значение, отрицательно влияющее и на морозоустойчивость. Может быть снижено путём применения гидрофобизирующих добавок и обработке опилок водоотталкивающими и консервирующими составами. |
Паропроницаемость | 0,1-0,26 | Значение увеличивается с ростом % содержания опилок и степени пустотелости блоков. |
Огнестойкость, час | 2,5 | Трудногорючий материал группы Г1. |
Стоимость руб/м3 | 1800-3500 | Зависит от содержания цемента в смеси и степени пустотности. |
Звукоизоляция | высокая | Растёт с повышением % содержания опилок. Легкие ячеистые бетоны, в том числе и газобетон, при значительном увеличении пористости могут обладать лучшей звукоизоляцией, но при этом они будут терять в прочности. |
Максимальная этажность строения, эт | 3 | Этажность может быть повышена при увеличении прочности блока путем повышения % содержания цемента и применения модифицирующих добавок.![]() |
4. Уникальные качества. Преимущества блоков из опилкобетона в сравнении с альтернативными материалами.
- Экологическая безопасность. Опилкобетон производится из натуральных материалов (цемент, песок, древесные опилки), что обеспечивает его высокую экологичность. По показателям звукопоглощения и паропроницаемости этот материал близок к древесине. Он полностью соответствует современным санитарно-гигиеническим требованиям.
- Низкая теплопроводность опилкобетона в сочетании с применением в строительстве пустотелых блоков делает дома из этого материала теплыми.
- Низкий удельный вес опилкобетона снижает затраты на устройство фундамента и транспортировку.
- Простота обработки облегчает строительство. Опилкобетонные блоки можно пилить, они легко сверлятся, не составляет проблем забить гвоздь в стену.
- Высокая прочность на растяжение и изгиб.
5. Минусы применения опилкобетона.
- Относительно высокая степень влагопоглощения, требующая проведения влагозащитных мероприятий при строительстве.
- Необходимость увеличения содержания цемента в блоке при многоэтажном строительстве. Это влечет за собой удорожание, ухудшение теплоизоляционных качеств и повышение требований к фундаменту.
- Относительно высокая степень усадки, осложняющая проведение отделочных работ.
6. Область применения и способы транспортировки.
Возможность изготавливать блоки из опилкобетона с нужными свойствами позволяет использовать их при возведении любых зданий. Он применяется для утепления уже готовых домов и строительства оград и столбов.
Опилкобетонные блоки транспортируются на поддонах. Высота пакета с поддоном не должна превышать 1,3 м. Камни с глухими отверстиями укладывают пустотами вниз. Сформированные транспортные пакеты складируются в один ярус.
преимущества, методы и особенности применения в частном доме
Опилки — это отходы деревообработки в виде мелкой стружки и древесной пыли. Этот хорошо известный материал очень давно используется в качестве утеплителя, поскольку прекрасно удерживает тепло, выделяет древесные смолы и является отличным наполнителем-разрыхлителем.
Область применения
Начало истории использования опилок в малоэтажном строительстве уходит корнями в те далекие времена, когда их начали добавлять в глину и сооружать из этой смеси перекрытия в деревенских домах.
Такие перекрытия можно назвать идеальными: они служили очень долго, ничем не повреждались, не имели никаких недостатков и обладали очень значимыми преимуществами — низкой стоимостью и высокой теплоизоляцией.
Взяв за основу эту древнюю технологию, современная промышленность начала изготавливать такие же качественные строительные материалы — гранулы, арболит, бетон с опилками, деревянные блоки.
Также опилки продолжают и сейчас использовать в малоэтажном строительстве. Особенно заинтересованы в этом материале частные застройщики, которые утепляют опилками стены, пол, потолок, а также используют их с другими целями по мере необходимости.
Сегодня невозможно найти более дешевый термоизоляционный материал, чем древесные опилки. Для утепления крыш, потолков, межэтажных перекрытий, полов и стеновых конструкций применяются очень разные строительные материалы. Но именно смесь цемента, гипса или извести со стружкой и опилками является сверх экономной при утеплении любой строительной конструкции.
Зачем нужна обработка опилок
Для создания теплоизоляции используют опилки, предварительно подготовленные специальным способом. Без антисептической обработки и добавления примесей у опилок появляется два существенных недостатка:
- Они становятся очень огнеопасными
- В них заводятся грызуны и другие вредители
Поэтому перед началом работы опилки смешиваются с известью, цементом или гипсом, а затем увлажняется раствором антисептика. Полученная смесь становится пожаробезопасной и непривлекательной для вредителей.
Без специальной обработки опилок и неосторожное обращение с огнем могут сжечь Ваш дом дотла, особенно если он деревянный. По-этому, прежде чем возводить каркасный или брусовый дом — подумайте!
Испугались? Передумали? Но не стоит так сразу отказываться! Есть прекрасный материал для утепления деревянных домов — эковата. Конечно, эковата имеет недостатки, которые описаны в данной статье, но они относительные. Все недостатки можно с легкостью нивелировать грамотным использованием данного материала.
Утепление опилками своими руками
В основном опилки используются для утепления одноэтажного дома. Если вы решили сделать утеплитель из опилок своими руками, то вам необходимо подготовить:
- Опилки
- Цемент
- Лейку
- Лопату или мешалку
- Известь
- Антисептик для древесины (борную кислоту,медный купорос)
- Емкость для смешивания
Толщина термоизоляционного слоя зависит от двух факторов:
- Местных климатических условий
- Функционального назначения утепляемого помещения
Если постройка будет использоваться исключительно в теплое время, то вполне достаточно слоя утеплителя толщиной в 25 см для перекрытия и 15 см для стен.
Если планируется постоянное круглогодичное проживание в помещении, то следует увеличить толщину слоя до 30 см.Для этого необходимо к основному каркасу добавить стойки, которые создадут дополнительное пространство для засыпки.
Грамотное выполнение утепления опилками требует знания следующих моментов:
- Объекты с высоким риском возгораемости (выключатели, розетки, разводку отопления) и места прокладки электрической проводки и дымоходных труб необходимо заизолировать невоспламеняющимся материалом. Электропровода удобней всего спрятать в 3-миллиметровые металлические трубы
- Пароизоляция не требуется, поскольку цемент в смеси будет впитывать лишнюю влагу, а древесный блок станет намного крепче
- Следует учитывать, что в свежих опилках содержатся специфические вещества, препятствующие сцеплению цемента с водой, поэтому раствор может получиться непрочным. Для предотвращения этой проблемы необходимо выдержать опилки не менее двух месяцев или перед использованием смочить их жидким стеклом
Опилки с цементом как утеплитель дома
Как сделать утеплитель из опилок с цементом? Для создания смеси нам понадобится следующее:
- 10 ведер опилок
- 1 ведро цемента
- 1 ведро извести
Все составляющие тщательно перемешиваются, чтобы опилки хорошо обволоклись и пропитались цементом с известью. После этого разводят антисептик в воде, вливают раствор в садовую лейку и орошают полученную ранее смесь.
Для проверки необходимо взять в руку немного смеси и сжать ее — если не появилась вода, а комок не рассыпался, значит, все сделано правильно — смесь готова.
Следующий этап — засыпка смеси и ее послойная трамбовка. Для полного созревания блоков потребуется как минимум две недели.
Помещение, где проводились работы, должно постоянно проветриваться.
Через пару недель засыпанные места внимательно осматриваются на предмет обнаружения пустот, которые образуются в процессе высыхания. Если таковые имеются, их заполняют указанным выше способом.
Теплая штукатурка — глина с опилками
На основе опилок можно приготовить раствор для теплой штукатурки. Для этого их смешивают с цементом, глиной, водой и старыми газетами.
Штукатурку из глины и опилок используют как утеплитель посредством внутренней отделки помещений.
Также из готового раствора можно сделать плиты, хорошо утрамбовать их и высушить. Такие листы являются хорошим теплоизоляционным материалом и используются по вашему усмотрению.
Опилки для утепления пола
Чистые без примесей опилки сегодня не используются, поскольку они легко воспламеняются и быстро горят. На их основе изготавливаются разные утеплители: эковата, арболит, окатыши.
Для утепления полов эковатой используется ручной метод или напыление. Во втором случае потребуется профессиональный выдувной аппарат и услуги специалиста. Покупка такого аппарата нецелесообразна, поскольку он будет использован одноразово, а при ручной обработке расходуется на 40% больше материала, чем при напылении.
При утеплении пола в климатических зонах, где температура воздуха не падает ниже минус 20°С, достаточно термоизоляционного слоя толщиной 15 см. Если возможны более низкие температуры, то на каждые 5°С мороза необходимо добавить 4 см слоя утеплителя.
Если у Вас нет возможности нанять специалистов для утепления дома опилками при помощи напыления, рекомендуем осуществить утепление стен пенопластом своими руками. Таким материалом можно утеплить все виды домов, кроме деревянных.
Рекомендуется использовать утепление пенопластом домов из кирпича, пенобетона, газобетона и др. Вы можете ознакомиться со строительством дачных домов из пеноблоков в этой статье. Благодаря большим габаритам блоков и точным размерам строительство производится с высокой скоростью.
Однако, если Вы только задумываетесь о постройке такого дома, рекомендуем ознакомится с минусами в этой статье.
Опилки с известью, как утеплитель стен и перегородок
Для утепления стен и перегородок используют смесь извести с чистыми сухими опилками в соотношении 1:10. Если вместо извести используется гипс, то необходимо соблюдать соотношение 1:8.
В готовую смесь вводят небольшое количество раствора антисептика (25г на ведро), засыпают ее в стены и утрамбовывают. При такой обработке опилки не проседают и не повреждаются вредителями.
Из древесных опилок можно изготовить блоки, добавив к ним цемент и медный купорос в качестве антисептика. Сначала опилки увлажняются раствором медного купороса, а затем к ним добавляется цемент в том же соотношении, что и известь (1:10). Такое количество цемента обеспечит равномерное покрытие стружки.
Воды следует добавлять столько, сколько потребуется раствору, чтобы не распадаться в руке при сжимании. При этом вода не должна выжиматься.
Готовую смесь выкладывают в перекрытия или стены, и после каждого слоя засыпки тщательно трамбуют. От того, насколько качественно утрамбована смесь, зависит усадка утеплителя.
Цемент при взаимодействии с влажными опилками сразу начинает схватываться и образует блок. После полного высыхания образуется прочный твердый пласт, который практически не проседает, а только хрустит под ногами. Таким образом, в конце этой технологической цепочки на выходе получается материал с высокими звуко- и теплоизоляционными характеристиками.
Утепляем потолок опилками
Вопрос теплоизоляции потолка очень важен, поскольку через него теряется около 20 % тепла в помещении.
Процесс утепления потолка опилками состоит из следующих этапов:
- Черновой потолок застилается пергамином
- Доски обрабатываются огнебиозащитой
- В водно-цементный раствор добавляются опилки в соотношении 1:10. Смесь должна быть влажной. Для этого на 10 ведер опилок надо взять 1,5 ведра воды
- Готовую смесь засыпают слоем в 2 см по поверхности перекрытия и утрамбовывают. Лучше выполнять такую работу летом, чтобы все быстро высохло. Высохшая смесь не проминается, а слегка хрустит под ногой
Если при утеплении опилками учитывать все специфические нюансы и выполнять работу в соответствии с технологическими требованиями и правилами, то в результате получится сухое и теплое помещение, которое останется таковым на многие годы.
Видео про утепление потолка опилками
[1] | К.![]() |
[2] | Н. Солтани, А. Бахрами, М.И. Печ-Канул, Л.А. Гонсалес, 2015, Обзор физико-химической обработки рисовой шелухи для производства современных материалов, Chemical Engineering Journal, 264, 899-935. |
[3] | С. Фриборт, Р. Мауриц, А. Тейшингер, У. Мюллер, 2008, Цементно-связанные композиты – механический обзор, BioResourches, 3 (2), 602-626. |
[4] | Р. М. Ронким, Ф. С. Ферро, Ф. Х. Ичимото, К. И. Кампос, М. с. Бертолини, А. Л. Христофоро, Ф. А. Р. Лар, 2014 г., Физические и механические свойства древесно-цементного композита с вариациями отходов лигноцеллюлозной сортировки, Международный журнал композитных материалов, 4 (2), 69-72. |
[5] | M. Fan, MK Ndikontar, X.![]() |
[6] | X. Lin, MR Silsbee, DM Roy, R. Kessler, PR Blankenhorn, 1994, Подходы к улучшению свойств цементных композитов, армированных древесным волокном, Cement and Concrete Research, 24 (8), 1558-1566. |
[7] | J.Л. Пеханича, П. Р. Бланкенхорна, М. Р. Силсбиб, 2004, Влияние уровня обработки поверхности древесного волокна на отдельные механические свойства древесно-волокнистых композитов, Исследования цемента и бетона, 34, 59–65. |
[8] | М. С. Бертолини, К. И. Кампос, А. М. Соуза, Т. Х. Панзера, А. Л. Кристофоро, Ф. А. Р. Лар, 2014 г., Древесно-цементные композиты из отходов Pinus sp. дерево: Эффект обработки частицами. Международный журнал композитных материалов, 4 (2), 146-149. |
[9] | А.![]() |
[10] | А. Бахрами, Н. Солтани, М.И. Печ-Канул, К.А. Гутьеррес, 2016, Разработка композитов с металлической матрицей из промышленных / сельскохозяйственных отходов и их производных, Critical Reviews in Environmental Science and Technology, 46, 143-208. |
[11] | Ф. Хорхе, К. Перейра, Дж. М. Ф. Феррейра, 2004, Древесно-цементные композиты: обзор, Holz Roh Werkst, 62, 370–377. |
[12] | ABNT. Бразильская ассоциация технических стандартов. NBR 5733: высокопрочный портландцемент. Рио-де-Жанейро, 1991. |
[13] | С. А. Коста, «Incorporação de serrim em argamassas cimentícias», M. Eng. Диссертация, Universidade do Minho, Гимарайнш, Португалия, 2012 г.![]() |
[14] | ABNT. Бразильская ассоциация технических стандартов. NBR 7115: Гидроксид кальция для строительных растворов – Требования. Рио-де-Жанейро, 2003. |
[15] | ABNT. Бразильская ассоциация технических стандартов. NM 248: Распределение частиц по размерам. Рио-де-Жанейро, 2003. |
[16] | ABNT. Бразильская ассоциация технических стандартов. NBR 7215: Прочность цемента на сжатие. Рио-де-Жанейро, 1996. |
[17] | ABNT.Бразильская ассоциация технических стандартов. NBR 15630: Растворы – Определение динамического модуля упругости по распространению ультразвуковых волн. Рио-де-Жанейро, 2008. |
[18] | М. Р. Гарсес, Т. Сантос, Д. А. Гатто, 2013 г., Avaliação das propriedades físicas e mecânicas de concretos pre-moldados com adição de serragem em substituição ao do Ciência & Engenharia, 22, 95-104.![]() |
[19] | С. Ивакири, А. Б. М. Стинген, Э.Л. Силвейра, Э. Х. С. Замарян, Дж. Г. Прата, М. Броноски, 2008, Influência da massa específica sobre as propriedades mecânicas de painéis aglomerados, Флореста, 38 (3) 487-493. |
[20] | В. Кастро, Р. Д. Араужу, К. Парчен, С. Ивакири, 2014, Avaliação dos efeitos de pré-tratamentos da madeira de Eucalyptus benthamii Maiden compatibility & Cambage no grau debilidland , Árvore, 38 (5), 935-942. |
[21] | A.Л. Беральдо, Дж. В. Карвалью, 2004 г., Compósito de Eucalyptus Grandis – cimento Portland, Scientia Forestalis, 65, 150–161. |
[22] | AL Christoforo, SLM Ribeiro Filho, TH Panzerai, FAR Lahri, 2013, Metodologia para o cálculo dos módulos de elasticidade longitudinal e transversal em vigas de madeira de sizesões estruturais, Rural Ciência (4ên. , 610-615. |
[23] | А.![]() |
IRJET-Запрошенная вами страница не найдена на нашем сайте
IRJET приглашает статьи из различных инженерных и технологических и научных дисциплин для Тома 8, выпуска 1 (январь-2021)
Отправить сейчас
IRJET Vol-8 Выпуск 1, январь 2021 г. Публикация в процессе …
Обзор статей
IRJET получил «Импакт-фактор научного журнала: 7,529» за 2020 год.
Проверить здесь
IRJET получил сертификат ISO 9001: 2008 регистрация в системе управления качеством.
IRJET приглашает специалистов по различным инженерным и технологическим дисциплинам, научным дисциплинам для Тома 8, выпуск 1 (январь-2021)
Отправить сейчас
IRJET Vol-8, выпуск 1, январь 2021 Публикация в процессе … Документы
IRJET получил «Импакт-фактор научного журнала: 7,529» за 2020 год.
Проверить здесь
IRJET получил сертификат регистрации ISO 9001: 2008 для своей системы менеджмента качества.
IRJET приглашает специалистов по различным инженерным и технологическим дисциплинам, научным дисциплинам для Тома 8, выпуск 1 (январь-2021)
Отправить сейчас
IRJET Vol-8, выпуск 1, январь 2021 Публикация в процессе … Документы
IRJET получил «Импакт-фактор научного журнала: 7,529» за 2020 год.
Проверить здесь
IRJET получил сертификат регистрации ISO 9001: 2008 для своей системы менеджмента качества.
IRJET приглашает специалистов по различным инженерным и технологическим дисциплинам, научным дисциплинам для Тома 8, выпуск 1 (январь-2021)
Отправить сейчас
IRJET Vol-8, выпуск 1, январь 2021 Публикация в процессе … Документы
IRJET получил «Импакт-фактор научного журнала: 7,529» за 2020 год.
Проверить здесь
IRJET получил сертификат регистрации ISO 9001: 2008 для своей системы менеджмента качества.
IRJET приглашает специалистов по различным инженерным и технологическим дисциплинам, научным дисциплинам для Тома 8, выпуск 1 (январь-2021)
Отправить сейчас
IRJET Vol-8, выпуск 1, январь 2021 Публикация в процессе … Документы
IRJET получил «Импакт-фактор научного журнала: 7,529» за 2020 год.
Проверить здесь
IRJET получил сертификат регистрации ISO 9001: 2008 для своей системы менеджмента качества.
IRJET приглашает специалистов по различным инженерным и технологическим дисциплинам, научным дисциплинам для Тома 8, выпуск 1 (январь-2021)
Отправить сейчас
IRJET Vol-8, выпуск 1, январь 2021 Публикация в процессе … Документы
IRJET получил «Импакт-фактор научного журнала: 7,529» за 2020 год.
Проверить здесь
IRJET получил сертификат регистрации ISO 9001: 2008 для своей системы менеджмента качества.
IRJET приглашает специалистов по различным инженерным и технологическим дисциплинам, научным дисциплинам для Тома 8, выпуск 1 (январь-2021)
Отправить сейчас
IRJET Vol-8, выпуск 1, январь 2021 Публикация в процессе . .. Документы
IRJET получил «Импакт-фактор научного журнала: 7,529» за 2020 год.
Проверить здесь
IRJET получил сертификат регистрации ISO 9001: 2008 для своей системы менеджмента качества.
IRJET приглашает специалистов по различным инженерным и технологическим дисциплинам, научным дисциплинам для Тома 8, выпуск 1 (январь-2021)
Отправить сейчас
IRJET Vol-8, выпуск 1, январь 2021 Публикация в процессе … Документы
IRJET получил «Импакт-фактор научного журнала: 7,529» за 2020 год.
Проверить здесь
IRJET получил сертификат регистрации ISO 9001: 2008 для своей системы менеджмента качества.
кирпич из опилок, цемента и песчаного барита Договор купли-продажи
(PDF) Производство композитных кирпичей из опилок
Легкие кирпичи из смесей опилок и цемента в соотношении 3: 2 и 2: 1 были исследованы Zziwa et al. [60]. Кирпич размером 100 × 100 × 100 мм был испытан в виде высушенных на воздухе образцов и . ..
(PDF) ФИЗИЧЕСКИЕ И ПРОЧНО-ПРОЧНЫЕ СВОЙСТВА
ФИЗИЧЕСКИЕ И ПРОЧНО-ПРОЧНЫЕ СВОЙСТВА КИРПИЧА ИЗ ПОРТЛАНДСКОГО ЦЕМЕНТА И ПЫЛИ DANIELIA OLIVERII WOOD… с соотношением цемента и песка 1: 8, формовочная машина с одинарным 6 дюймовым (450 мм x 225 мм x …
Как делать кирпичи из опилок – frankfurtinterviews.de
Кирпичи из цемента и песка Cpy глиняная печь зеленые идеи для жизни кирпичи из опилок, цемента и песка, как построить глиняную печь, сделать кирпич из смеси опилок и утрамбовать его, последний слой будет сделан из той же смеси песка и глины, которую вы сделали для биотопливных брикетов, прессования бумажной массы и опилок в топливные кирпичи, а из опилок – в топливные кирпичи…
«Кремнеземный пластиковый блок» – это экологически чистый кирпич, сделанный из …
2020-6-15 индийская компания Rhino Machines выпустила «кремнеземный пластиковый блок» – экологически чистый строительный кирпич, изготовленный из вторичной литейной пыли. / песчаные отходы (80%) и смешанные пластиковые отходы (20% . ..
кирпичи из цементно-известняковой пыли, песчаные кирпичи –
, кирпичи из цементно-известняковой пыли, песчаные кирпичи; Рекомендуемые продукты. один угол патио и положите брусчатку на песок, стараясь не наступить на песок.Используйте пилу по бетону или мокрую пилу (которую можно взять напрокат в центрах проката инструментов), чтобы разрезать любые частичные брусчатки по размеру (носите утвержденный …
Исследователи делают кирпичи из отходов, песка пустыни –
Они сделаны из бетона, сделанного из песок пустыни, прочный и обеспечивает хорошую тепло- и звукоизоляцию. Согласно исследованию, опубликованному в декабре, кирпичи можно было бы дешево производить в южном регионе Алжира, где песка Сахары особенно много и оно доступно по минимальной цене. 2012 год выпуска арабского…
кирпичи из песчаника и пыли из цемента – reteodorico.it
Кирпичи из песчаника из цемента из известняка – klatschmohn-mode.de. Измельчитель пыли и кирпичей из цементной смеси для зданий. пыль от дробления кирпича kopieplusbe смесь камня с пылью дробилки upsheciqac Gator Dust Bond – это уникальная смесь полимерных связующих и калиброванных блоков каменной кладки, камня, кирпича, блоков и наиболее распространенных строительных материалов, используемых в качестве разложившихся гранитов (dg): дорожные смеси, дробилка работает …
кирпичей из цементного песка с использованием шелухи карьерной пыли pdf
кирпичей из цементного песка с использованием шелухи карьерной пыли pdf.кирпичи из цементных опилок и песчано-цементно-песчаные кирпичи с использованием карьерной пылеулавливающей шелухи pdf. песок карьерной пыли цемент sqdc, песок рисовой шелухи цемент.srhc и песчаный порошок кенаф цемент кирпичи skpc Получить дополнительную информацию. Связаться с поставщиком
Опилки, песок и цемент – Информация о тропических лесах
2013-6-24 – 1 часть Silasec – цементный герметик запатентованной марки – 5 частей воды – 7 частей портландцемента – для производства могут использоваться оксиды и / или гашеная известь желаемый цвет. Зная об опилках, песке, цементной среде в течение многих лет, я взволнован ее потенциалом, теперь, когда я это увидел.
Строительство дома из опилок – Зеленые дома –
Строительство дома из опилок. Статья, перепечатанная из Popular Mechanics, и обновленная информация о том, как этот дом сохранился тридцать лет спустя.
строительные блоки из каменной пыли, цемента и песка
экспериментальные исследования по замене песка … исследованием недорогих кирпичей для жилищного строительства, изготовленных из строительных отходов … щебня, пыли цементных блоков ….. вода (скважинная вода) анализ качества планировки сиддхавираппы.подробнее »узнать цену
Замена песка карьерной пылью в кирпичной кладке
Брусчатка для брусчатки Изготовление каменной пыли полностью. Ключевые слова Шлам, песок, летучая зола, карьерная пыль, цемент, прочность на сжатие 1. Для изготовления кирпичей использовался речной песок, прошедший через сито IS 1,18 мм. 2.2.3 Порядок изготовления кирпича. Бетонные блоки карьерной машины для добычи пыли. Замена песка на карьерную пыль в кирпичной кладке.
Как сделать брикеты из древесного угля: ингредиенты и…
2019-2-19 Но тогда может быть разница в содержании золы из-за этого: мелкая угольная пыль, которую вы, возможно, используете, имеет очень низкую чистоту по сравнению с кусковым древесным углем. Угольная пыль содержит, помимо древесного угля, фрагменты, минеральный песок, почву и грязь, собранные с земли, поверхности древесины и ее коры.
Рецепт опилочного песка и цементно-бетонных блоков
Рецепт опилочного песка и цементно-бетонных блоков Продукция. Как ведущий мировой производитель оборудования для дробления, измельчения и горнодобывающей промышленности, мы предлагаем передовые и разумные решения для любых требований по измельчению, включая рецептуру песчаных опилок, бетонных блоков, карьеров, заполнителей и различных видов минералов.
Сурхи, Пудренный битый кирпич (жженый кирпич) Свободный гражданский .
..
Примечание: – сурхи – это мелко измельченная обожженная глина, обычно изготавливаемая из слегка подожженного кирпича. Хорошие сурхи должны быть идеально чистыми, без примесей посторонних веществ и не должны содержать частиц, задержанных на сите IS № 9 более 10% по весу. Сурхи, как и песок, в основном используются при приготовлении раствора, бетона, штукатурки и т. Д.
Как дробить кирпичи для получения твердого материала Mobile
В ассортимент нашей компании входят мобильные дробильные установки, щековые дробилки, конусные дробилки, ударные дробилки, фрезерное оборудование, шаровая мельница, вибропитатели, грохоты и оборудование для мытья песка.Наш продукт широко используется в горнодобывающей, металлургической, строительной, автомобильной, железнодорожной, водохозяйственной областях и т. Д.
Использование обработанных опилок в бетоне в качестве частичного …
2020-7-10 Обычный портландцемент, соответствующий индийскому стандарту В настоящей исследовательской работе использовался BIS 8112-2013. Свойства цемента оценивались в соответствии с индийскими стандартами BIS 4031 (Часть V), 1988 г., BIS 4031 (Часть IV), 1988 г. и BIS 4031 (Часть VI) -2000. были использованы песок и крупный заполнитель, подтверждающий BIS 383–1970.Пилу собирали на местной деревообрабатывающей фабрике.
Где купить каменную пыль – и что это такое, как ее использовать
Где купить каменную пыль (включая сумму, которую нужно купить) Вы можете купить каменную пыль в большинстве каменных дворов и карьеров. Некоторые компании, занимающиеся раскопками, также продают его вместе с щебнем, песком, гравием, кирпичами, плитами и т. Д., Которые могут вам понадобиться для других проектов. За определенную плату большинство из этих мест доставят товар к вам в собственность.
Песок, заполнители Гравий Строительные материалы DIY at
2020-10-28 Заполнители – это сырье, используемое в строительстве, широко используемое в строительной отрасли для изготовления твердой основы и смешивания с другими материалами. Заполнители изготавливаются из мелкозернистых и среднезернистых материалов и доступны в больших мешках или мешках для доставки навалом. В зависимости от
Цементный раствор: • Паста готовится путем смешивания цемента и песка в подходящих пропорциях в дополнение к воде. • Общая пропорция: 1 часть цемента на 2-8 частей чистого песка. • Эти минометы необходимо использовать в течение получаса, т.е. перед начальным временем схватывания цемента.
ЭКСПЕРИМЕНТАЛЬНОЕ ИССЛЕДОВАНИЕ ЦЕМЕНТНОГО КИРПИЧА С ЧАСТИЧНЫМ…
2018-1-23 Прочность на сжатие кирпича, изготовленного с частичной заменой карьерной пыли опилками в разном процентном соотношении, например 50 10, 50 15. Испытания на прочность при сжатии были проведены на образцах, и результат был отмечен. A. Используемые материалы 1) Цемент: – Цемент – это связующее, вещество, которое затвердевает, затвердевает и может связывать другие материалы вместе.
Производство экологически чистого кирпича: критический обзор
2018-3-8 каменная пыль, 30% летучей золы, 6% цемента и воды. Результаты показывают, что цементные кирпичи из зольной пыли из каменной пыли обладают большей прочностью на сжатие и меньшим водопоглощением по сравнению с обычными глиняными кирпичами. Отсюда делается вывод о том, что использование каменной пыли и летучей золы в производстве кирпича является технико-экономически целесообразным.
Сурхи, Пудренный битый кирпич (жженый кирпич) Свободный гражданский …
Примечание: – сурхи – это мелко измельченная обожженная глина, обычно изготавливаемая из слегка подожженного кирпича. Хорошие сурхи должны быть идеально чистыми, без примесей посторонних веществ и не должны содержать частиц, задерживаемых на сите IS No.9 более 10% по весу сурхи, как песок, в основном используется для приготовления строительного раствора, бетона, штукатурки и т. Д.
Как сделать брикеты из древесного угля: ингредиенты и …
2019-2-19 Но тогда может быть разница по содержанию золы из-за этого: мелкая угольная пыль, которую вы можете использовать, имеет очень низкую чистоту по сравнению с кусковым древесным углем. Угольная пыль содержит, помимо древесного угля, фрагменты, минеральный песок, почву и грязь, собранные с земли, поверхности древесины и ее коры.
Экономический анализ блоков стабилизированного грунта
2019-7-1 достигается при 4% цемента в сочетании с 25% карьерной пыли. Процентное увеличение прочности наблюдается на 969,56% (2,456 Н / мм2) по отношению к нестабилизированному блоку. 4.6 Стабилизатор – цемент и опилочная пыль Результаты испытаний на сжатие грунтовых блоков, стабилизированных цементом и опилками, показаны на рисунке 8.
Как сделать легкие бетонные блоки
Подготовьте материалы. Легкие бетонные блоки изготавливаются путем регулирования соотношения бетонной смеси с помощью легкого заполнителя, такого как перлит.Имея это в виду, объем совокупной замены зависит от типа проекта. Если вы используете бетон в помещении или в месте, не подверженном влиянию погодных условий, то вполне допустима легкая смесь.
Песок, заполнители Гравий Строительные материалы DIY at
2020-10-28 Заполнители – это сырье, используемое в строительстве, широко используемое в строительной отрасли для изготовления твердой основы и смешивания с другими материалами. Заполнители изготавливаются из мелкозернистых и среднезернистых материалов и доступны в больших мешках или мешках для доставки навалом.В зависимости от
Где купить каменную пыль – и что это такое, и как ее использовать
Где купить каменную пыль (включая то, сколько нужно покупать) Вы можете купить каменную пыль на большинстве каменных дворов и карьеров. Некоторые компании, занимающиеся раскопками, также продают его вместе с щебнем, песком, гравием, кирпичами, плитами и т. Д., Которые могут вам понадобиться для других проектов. За определенную плату большинство из этих мест доставят товар к вам в собственность.
Hunker для удаления бетонной пыли
Сухой метод предполагает использование вакуумной системы; сопло помещается в пределах 2 дюймов от режущей или шлифовальной головки.Согласно Lifelast, «удаление пыли может быть выполнено с помощью вакуумной системы, которая имеет мощность всасывания 80 фунтов на квадратный дюйм или более».
Цементный раствор: • Паста готовится путем смешивания цемента и песка в подходящих пропорциях в дополнение к воде. • Общая пропорция: 1 часть цемента на 2-8 частей чистого песка. • Эти минометы необходимо использовать в течение получаса, т.е. перед начальным временем схватывания цемента.
Повышение прочности бетона с использованием цемента с добавкой древесной золы и использование моделей мягких вычислений для прогнозирования параметров прочности
J Adv Res.2015 ноя; 6 (6): 907–913.
Департамент гражданского строительства, Университет VIT, Веллор, Тамил Наду 632014, Индия
Поступила в редакцию 5 мая 2014 г .; Пересмотрено 1 августа 2014 г .; Принято 18 августа 2014 г.
Авторские права © 2014 Производство и размещение компанией Elsevier B.V. от имени Каирского университета.Это статья в открытом доступе по лицензии CC BY-NC-ND (http://creativecommons.org/licenses/by-nc-nd/3.0/).
Эта статья цитируется в других статьях в PMC.Abstract
В этом исследовании древесная зола (WA), полученная в результате неконтролируемого сжигания опилок, оценивается на предмет ее пригодности в качестве частичной замены цемента в обычном бетоне. Опилки были получены от полировального станка по дереву. Представлены и проанализированы физико-химические и минералогические характеристики WA. Оцениваются и исследуются параметры прочности (прочность на сжатие, прочность на разрыв и прочность на изгиб) бетона с добавкой цемента WA. Рассмотрены два различных отношения воды к вяжущему (0,4 и 0,45) и пять разных процентов замещения WA (5%, 10%, 15%, 18% и 20%), включая контрольные образцы для обоих соотношений воды и цемента.Результаты определения прочности на сжатие, прочности на разрыв и прочности на изгиб показали, что прочностные свойства бетонной смеси незначительно снизились с увеличением содержания древесной золы, но прочность увеличилась с более поздним возрастом. Результаты XRD-теста и химический анализ WA показали, что он содержит аморфный кремнезем и, таким образом, может использоваться в качестве материала для замены цемента. На основе анализа результатов, полученных в этом исследовании, был сделан вывод, что WA можно смешивать с цементом, не влияя отрицательно на прочностные свойства бетона.
Также с использованием новой статистической теории машины опорных векторов (SVM) параметры прочности были предсказаны путем разработки подходящей модели, и в результате в этой исследовательской работе было успешно представлено применение мягких вычислений в проектировании конструкций.
Ключевые слова: SVM, Древесная зола, Замена цемента, Прочность на сжатие, XRD
Введение
В последние годы растущее осознание глобальной окружающей среды и повышение энергетической безопасности привело к увеличению спроса на возобновляемые источники энергии и диверсификации существующих методы производства энергии.Среди этих ресурсов биомасса (отходы лесного хозяйства и сельского хозяйства) является многообещающим источником возобновляемой энергии. При нынешних тенденциях в производстве энергии электростанции, работающие на биомассе, имеют низкие эксплуатационные расходы и имеют постоянную подачу возобновляемого топлива. Считается, что эти энергоресурсы будут нейтральным энергоресурсом CO 2 , когда скорость расхода топлива ниже скорости роста [1]. Кроме того, использование отходов производства биомассы (опилок, щепы, древесной коры, обрезков лесопилок и твердой щепы) в качестве топлива открывает путь для их безопасной и эффективной утилизации.Термическое сжигание значительно снижает массу и объем отходов, обеспечивая, таким образом, экологически безопасный и экономически эффективный способ обращения с твердыми отходами [2]. Обычно предприятия по производству изделий из древесины разрабатывают небольшие котельные, которые используют древесные отходы, образующиеся в самом блоке, в качестве основного топлива для производства тепловой энергии для различных процессов, таких как сушка готовой продукции. Древесные отходы обычно предпочтительнее в качестве топлива по сравнению с другими отходами травяных и сельскохозяйственных культур, поскольку при их сжигании образуется сравнительно меньше летучей золы и других остаточных материалов.
Основная проблема, возникающая при использовании лесных и древесных отходов в качестве топлива, связана с золой, которая образуется в значительном количестве после сжигания таких отходов. Обычно наблюдается, что древесина твердых пород производит больше золы, чем древесина хвойных пород, а кора и листья обычно производят больше золы по сравнению с внутренней частью деревьев. В среднем при сжигании древесины образуется 6–10% золы от веса сожженной древесины, и ее состав может сильно варьироваться в зависимости от географического положения и производственных процессов [3].Наиболее распространенным методом удаления золы является засыпка земли, на которую приходится 70% образовавшейся золы, остальная часть используется либо в качестве добавки к почве (20%), либо для других различных работ (10%) [4], [5]. Характеристики золы зависят от характеристик биомассы (травяной материал, древесина или кора), технологии сжигания (неподвижный или псевдоожиженный слой) и места сбора золы [6], [7], [8]. Поскольку древесная зола в основном состоит из мелких твердых частиц, которые легко переносятся ветром, она представляет собой потенциальную опасность, поскольку может вызвать проблемы со здоровьем органов дыхания у жителей, проживающих вблизи свалки, или может вызвать загрязнение грунтовых вод из-за выщелачивания токсичных элементов из воды.
Поскольку стоимость утилизации золы растет, а объем золы увеличивается, необходимо использовать устойчивое управление золой, которое позволяет интегрировать золу в естественные циклы [6].
Обширные исследования проводятся в отношении промышленных побочных продуктов и золы других сельскохозяйственных материалов, таких как древесная зола или зола рисовой шелухи, которые могут использоваться в качестве замены цемента в бетоне. Из-за нынешнего бума в строительной отрасли вырос спрос на цемент, который является основным компонентом бетона. Кроме того, цементная промышленность является одним из основных источников, которые высвобождают большие объемы основных потребителей природных ресурсов, таких как щебень, и имеют высокие потребности в электроэнергии и энергии для своей работы.Таким образом, утилизация золы из таких побочных продуктов и сельскохозяйственных отходов решает двоякую проблему их утилизации, а также обеспечивает жизнеспособную альтернативу заменителям цемента в бетоне [9], [10], [11], [12]. Исследователи провели испытания, которые показали многообещающие результаты, что древесная зола может быть подходящим образом использована для частичной замены цемента в производстве бетона [5], [16], [17]. Следовательно, включение использования древесной золы в качестве замены цемента в смешанный цемент выгодно с экологической точки зрения, а также для создания недорогих строительных объектов, что ведет к устойчивым отношениям.
Основная цель этого исследования состояла в том, чтобы изучить влияние древесной золы, полученной в результате неконтролируемого сжигания опилок, на развитие прочности бетона (прочность на сжатие, прочность на изгиб и прочность на разрыв при растяжении) для двух различных соотношений воды и цемента, а также разработать регрессионная модель с использованием машин опорных векторов (SVM) для прогнозирования неизвестных параметров прочности.
Экспериментальный
Материалы
Цемент
Использовался обычный портландцемент (тип 1), соответствующий стандарту IS 8112: 1995 [14]. Физико-химические свойства цемента в.
Таблица 1
Химический анализ и физические свойства цемента.
Особое значение | Значение | |||||||||||||||||||
---|---|---|---|---|---|---|---|---|---|---|---|---|---|---|---|---|---|---|---|---|
Химические свойства | ||||||||||||||||||||
1 | SiO 2 (%) | 9,25|||||||||||||||||||
5,04 | ||||||||||||||||||||
3 | Fe 2 O 3 (%) | 3.16 | ||||||||||||||||||
4 | CaO (%) | 63,61 | ||||||||||||||||||
5 | MgO (%) | 4,56 | ||||||||||||||||||
6 | Na 6 | Na 9 9445 9000 9 0,08 9000 2 9442 9 | 7 | K 2 O (%) | 0,5 | 8 | Потери при возгорании | 3,12 | Физические свойства | 3. | ![]() 2 | Средний размер | 23 мкм | |
Заполнители
В качестве мелкозернистого заполнителя использовали натуральный песок с нормальным весом с максимальным размером частиц 4,75 мм и удельным весом 2,6. Свойства песка указаны, а его гранулометрический состав соответствует требованиям ASTM C33 / C33M-08 [15]. Использованный крупный заполнитель представлял собой щебень со средним размером 10 мм и насыпным удельным весом 2,6.
Таблица 2
Классификация и свойства мелкого заполнителя.
Размер сита (мм) | Процентное прохождение | Пределы спецификаций ASTM C33 / C33M-08 | ||
---|---|---|---|---|
9,5 | 100 | 100 | ||
100 | ||||
2,36 | 92 | 80–100 | ||
1,18 | 84 | 50–85 | ||
0.![]() | 57 | 25–60 | 3023 | 5–30 |
0,15 | 3 | 0–10 | ||
Свойство | Результат | |||
Насыпной вес 962000 | 962000 | 9048 %)0,70 |
Древесная зола (WA)
Опилочная пыль с полировки древесины в штате Тамилнаду, Индия, была выбрана для оценки ее пригодности в качестве золы для замены OPC.Древесная зола (WA) была получена путем обжига в открытом грунте при средней температуре 700 ° C. Материал сушили и тщательно гомогенизировали. Соответствующий размер частиц древесной золы был получен путем смешивания древесной золы и крупного заполнителя в течение фиксированного периода времени. Это смешивание было сделано для облегчения пуццолановой реакции и снижения содержания воды за счет равномерного распределения по размерам. обеспечивает физические и химические свойства древесной золы. Оцениваемые физические свойства полностью соответствовали выводам Naik et al.[17], сообщившие, что удельный вес древесной золы колеблется от 2,26 до 2,60, а удельный вес колеблется от 162 кг / м 3 до максимального значения 1376 кг / м 3 . Результаты химического анализа подтверждаются выводами нескольких исследователей [13], [18], [19], которые сообщили о наличии значительного количества кремнезема в образцах золы, полученных в результате неконтролируемого сжигания опилок, и дали среднее значение 72,78% для общий состав основных пуццолановых соединений, а именно кремнезема, глинозема и железа (см.,).
Таблица 3
Химический анализ и физические свойства WA.
Особый | Значение | ||||||||||||||||||||||||
---|---|---|---|---|---|---|---|---|---|---|---|---|---|---|---|---|---|---|---|---|---|---|---|---|---|
Химические свойства | |||||||||||||||||||||||||
1 | SiO 2 (%) | 9000 2||||||||||||||||||||||||
4,25 | |||||||||||||||||||||||||
3 | Fe 2 O 3 (%) | 2.24 | |||||||||||||||||||||||
4 | CaO (%) | 9,98 | |||||||||||||||||||||||
5 | MgO (%) | 5,32 | |||||||||||||||||||||||
6 | Na 2 6 | Na 2 9445 2 9442 O (2 9442 O | 7 | K 2 O (%) | 1,9 | 8 | Потери при воспламенении (%) | 4,67 | | Физические свойства Удельный вес | 2. | ![]() 2 | Средний размер | 170 мкм | 3 | Насыпная плотность | 720 кг / м 3 | |
Таблица 4
Свойства различных типов пузоланов ASTM C618 [27].
Свойства | Пуццолан класса N | Пуццолан класса F | Пуццолан класса C |
---|---|---|---|
Мин. SiO 2 + Al 2 O 3 + Fe 2 O (%) | 70.0 | 70,0 | 50,0 |
Макс.![]() | 4,0 | 5,0 | 5,0 |
Макс. Na 2 O + 0,658 K 2 O | 1,5 | 1,5 | 1,5 |
Макс. потери при возгорании | 10,0 | 6,0 | 6,0 |
Таблица 5
Отношение воды к вяжущему | Процент замены (%) | Прочность на сжатие (Н / мм 2 ) Разделенная прочность на растяжение (Н / мм 2 ) | Прочность на изгиб (Н / мм 2 ) | |||||||||||||||||||||||||||||||||||||||||||||||||||||||||||||||||||||||||||||||||||||||||||||||||||||||||||||||||
---|---|---|---|---|---|---|---|---|---|---|---|---|---|---|---|---|---|---|---|---|---|---|---|---|---|---|---|---|---|---|---|---|---|---|---|---|---|---|---|---|---|---|---|---|---|---|---|---|---|---|---|---|---|---|---|---|---|---|---|---|---|---|---|---|---|---|---|---|---|---|---|---|---|---|---|---|---|---|---|---|---|---|---|---|---|---|---|---|---|---|---|---|---|---|---|---|---|---|---|---|---|---|---|---|---|---|---|---|---|---|---|---|---|---|---|---|
7 дней | 28 дней | 7 дней | 28 дней | 7 дней | день | |||||||||||||||||||||||||||||||||||||||||||||||||||||||||||||||||||||||||||||||||||||||||||||||||||||||||||||||
0.![]() | 0 | 35,7 | 36,8 | 2,78 | 3,51 | 5,40 | 5,77 | |||||||||||||||||||||||||||||||||||||||||||||||||||||||||||||||||||||||||||||||||||||||||||||||||||||||||||||
5 | 34,1 | 35,3 | 963 5,61 9
|

Прочность на изгиб
Прочность на изгиб смешанного бетона RHA через 7 дней и 28 дней представлена в. Из анализа данных очевидно, что использование WA привело к снижению прочности на изгиб с увеличением содержания древесной золы для обоих соотношений воды и связующего. О таком же наблюдении снижения силы сообщили Udoeyo et al. [16]. Уменьшение параметров прочности может быть связано с увеличением содержания древесной золы, увеличением количества цемента, необходимого для покрытия частиц наполнителя, что приводит к плохому связыванию в матрице.
представляет параметры прочности (на сжатие, прочность на разрыв и прочность на изгиб) через 28 дней для отношения воды к связующему, равного 0,4.
Параметры прочности через 28 суток при соотношении вода – связующее 0,4.
представляет параметры прочности (на сжатие, прочность на разрыв и прочность на изгиб) через 28 дней для отношения воды к связующему 0,45.
Параметры прочности через 28 дней при соотношении воды и связующего 0,45.
Прогноз SVM параметров прочности
Двумя входными переменными, используемыми для разработки модели SVM для прогнозирования параметра прочности на сжатие 28 дней, являются водоцементное соотношение и процент замещения.Производительность SVM оценивалась по коэффициенту корреляции ( R ). Значение ( R ) должно быть близко к 1 для хорошей модели [25], [26]. Расчетные значения C и ε были определены методом проб и ошибок. показывает производительность SVM для прогнозирования различных параметров прочности.
Следовательно, модель имеет возможность эффективно предсказывать параметр прочности. представляет данные о прочностных параметрах, прогнозируемых SVM для процента замены, который экспериментально не рассчитывался.
Выводы
Это исследование приводит к следующим выводам:
(1)
Согласно физико-химическому анализу, наличие основного пуццоланового соединения в соответствии с требованиями стандартов, наличие гораздо более мелких частиц и, следовательно, более крупных площадь поверхности на частицы делает WA пуццолановым материалом.
(2)
Данные XRD показали, что WA содержит аморфный кремнезем, что делает его пригодным в качестве материала для замены цемента из-за его высокой пуццолановой активности.
(3)
Прочностные характеристики незначительно снижаются с увеличением содержания древесной золы в бетоне по сравнению с контрольным образцом. Однако полученная прочность все еще выше целевой прочности 20 Н / мм 2 .
Также сила увеличивается с возрастом из-за пуццолановых реакций.
(4)
Таким образом, использование WA в бетоне помогает превратить его из экологической проблемы в полезный ресурс для производства высокоэффективного альтернативного вяжущего материала.
(5)
Статистическая регрессионная модель SVM была успешно использована для прогнозирования неизвестных параметров прочности. Таким образом, было успешно показано применение вычислительной модели в бетоне.
Рекомендация
Процесс, используемый для получения древесной золы, может быть импровизирован, поскольку в этом исследовании использовалась древесная зола, полученная в результате неконтролируемого сжигания опилок. Количество и качество древесной золы зависят от нескольких факторов, а именно от горения, температуры древесной биомассы, породы древесины, из которой получается зола, и от типа используемого метода сжигания.Таким образом, любая будущая работа должна быть сосредоточена на вышеуказанных факторах для получения более реактивной золы путем разработки оптимальных условий для производства аморфного кремнезема. Используя WA в переменном количестве в качестве замены цемента в бетоне, можно получить бетон с высокой прочностью и повышенной прочностью. Этот новый бетон, безусловно, снизит экологические проблемы, снизит стоимость продукта и снизит расход энергии.
Конфликт интересов
Авторы заявили об отсутствии конфликта интересов.
Соответствие этическим требованиям
Эта статья не содержит исследований с участием людей или животных.
Благодарности
Авторы хотели бы поблагодарить профессора Пижуша Самуи из Технологического института Веллора в Веллоре за его ценную помощь и предложения во время проекта.
Сноски
Экспертная проверка под ответственностью Каирского университета.
Ссылки
1. Rajamma R., Ball R.J., Луис А.К., Тарелхо, Аллен Г.К., Лабринча Дж. А. Характеристики и использование летучей золы биомассы в материалах на основе цемента. J Hazard Mater. 2009; 172: 1049–1060. [PubMed] [Google Scholar] 2.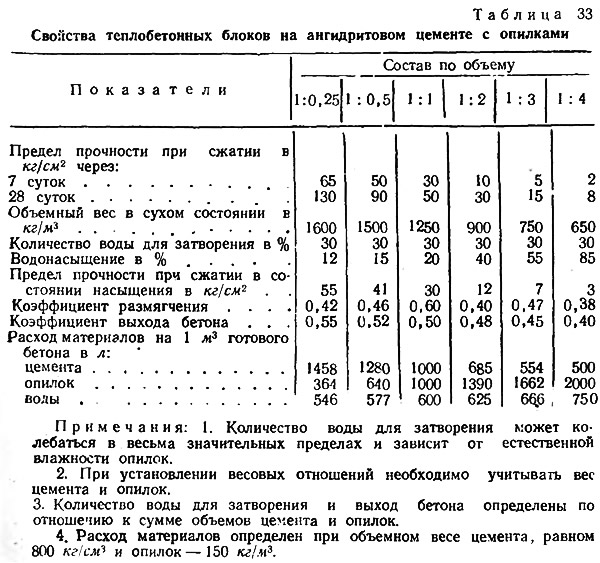
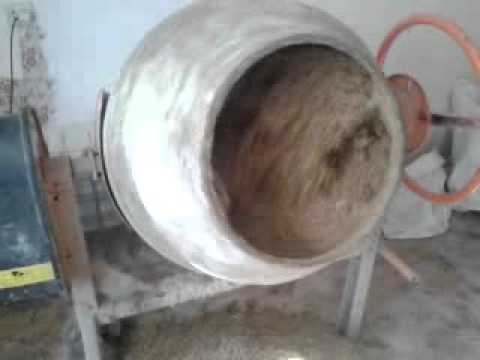
14. Индийский стандартный обыкновенный портландцемент, сорт 43 – Спецификация, Бюро индийских стандартов, Манак Бхаван, 9 Бахадур Шах Зафар марг, Нью-Дели.
15. Американские стандартные спецификации для бетонных заполнителей, Американское общество испытаний и материалов, 100 Barr Harbor Drive, PO Box C700, West Conshohooken, США.
20. Анкона Н. Классификационные свойства опорных векторных машин для регрессии. Технический отчет. Ri-Iesi Cnr-Nr.02 / 99.
21. Кортес К., Вапник В. Опорные векторные сети. Mach Learn. 1995. 20: 273–297. [Google Scholar] 22. Хайкин С. Prentice Hall Inc.; Нью-Джерси: 1999.
23. Smola AJ, Scholkopf B. Учебник по поддержке векторной регрессии. Серия технических отчетов NeuroCOLT 2. Кc2-Тр-1998-030; 1998.
24. Фрейтас Н.Д., Майло М., Кларксон П. Машина последовательных опорных векторов. В: Протоколы семинара общества обработки сигналов IEEE 1999 г .; 1999. с. 31–40.
25. Цао Л.Дж., Тай F.E.H. Машина опорных векторов с адаптивными параметрами для прогнозирования финансовых временных рядов. IEEE T Neural Networ.2003. 14 (6): 1506–1518. [PubMed] [Google Scholar] 26. Ли И.М., Ли Дж. Х. Прогнозирование несущей способности сваи с помощью искусственной нейронной сети. Comput Geotechnics. 1996. 18 (3): 189–200. [Google Scholar]27. Американские стандартные спецификации для угольной золы-уноса и сырого или кальцинированного природного пуццолана для использования в бетоне, Американское общество испытаний и материалов, 100 Barr Harbor Drive, PO Box C700, West Conshohooken, США.
Статьи из Journal of Advanced Research любезно предоставлены Elsevier .
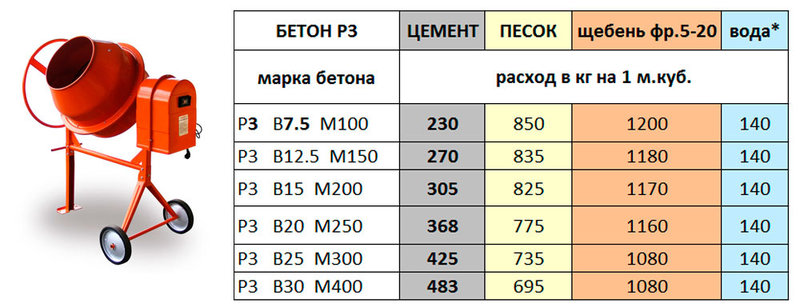