Расход мастики на м2 – Толщина, условия нанесения слоев
База знаний Битумные мастики Расход, толщина и условия нанесения слоев мастик ТЕХНОНИКОЛЬ
Кровельные и гидроизоляционные мастики
Мастика кровельная и гидроизоляционная ТЕХНОНИКОЛЬ № 21 (Техномаст)
Расход:
- для устройства мастичной кровли – 3,8…5,7 кг/м2;
- для устройства гидроизоляции – 2,5…3,5 кг/м2;
- для противокапиллярной и антикоррозионной обработки для создания готового слоя толщиной 0,6 мм – не менее 1,2 кг/м2.
Допустимая влажность основания: не более 5% по массе
Массовая доля нелетучих веществ: 50 %
Время высыхания одного слоя при +20° С и 50% влажности: 24 ч
Температура применения: от -20 до +40 °С (перед работой при отрицательных температурах выдержать в теплом помещении не менее 24 ч)
Мастика гидроизоляционная ТЕХНОНИКОЛЬ № 24 (МГТН)
Расход:
- Расход для устройства противокапиллярной отсечки и защиты бетона от коррозии – 1,0 кг/м2;
- Расход для устройства гидроизоляции конструкций – 2,5…3,5 кг/м2.
Допустимая влажность основания: не более 5% по массе
Массовая доля нелетучих веществ: 65 %
Время высыхания одного слоя при +20° С и 50% влажности: 24 ч
Температура применения: от -20 до +40 °С (перед работой при отрицательных температурах выдержать в теплом помещении не менее 24 ч)
Мастика битумно-полимерная эмульсионная ТЕХНОНИКОЛЬ №31
Расход:
- для устройства мастичной кровли – 3,8…5,7 кг/м2;
- для устройства гидроизоляции – 2,5…3,5 кг/м2.
Допустимая влажность основания: не более 10% по массе
Содержание вяжущего с эмульгатором: 50-70 % по массе
Время высыхания одного слоя при +20° С и 50% влажности: 8 ч
Температура применения: от 0 до +40 °С, температура основания должна быть не ниже +5°С
Мастика ТЕХНОНИКОЛЬ № 33
Расход:
- для устройства мастичной кровли – 4,5…5,5 кг/м2;
- при устройстве гидроизоляции – 3,5…4,5 кг/м2.
Допустимая влажность основания: не более 10% по массе
Содержание вяжущего с эмульгатором: 53-65 % по массе
Время высыхания одного слоя при +20° С и 50% влажности: 5 ч
Температура применения: от +5 до +35 °С
Мастика кровельная горячая ТЕХНОНИКОЛЬ № 41 (Эврика)
Толщина одного слоя: 2,0 мм
Расход на один слой: 2,0-2,5 кг/м2
Допустимая влажность основания: не более 4% по массе
Массовая доля нелетучих веществ: условно 100% (т.е. при отверждении толщина слоя не уменьшается)
Температура применения: от -20 до +40 °С (перед работой при отрицательных температурах выдержать в теплом помещении не менее 24 ч)
Приклеивающие мастики
Мастика приклеивающая ТЕХНОНИКОЛЬ №22 (Вишера)
Расход: 0,8-1,8 кг/м2 в зависимости от типа основания
Массовая доля нелетучих веществ: 70%
Температура применения: от -20 до +40 °С (перед работой при отрицательных температурах выдержать в теплом помещении не менее 24 ч)
Мастика приклеивающая ТЕХНОНИКОЛЬ №27
Расход: 0,5-1,0 кг/м2 при нанесении на плиту XPS точками
Массовая доля нелетучих веществ: 80-90 %
Температура применения: от -10 до +40 °С (перед работой при отрицательных температурах выдержать в теплом помещении не менее 24 ч)
Защитные мастики
Мастика защитная алюминиевая ТЕХНОНИКОЛЬ № 57
Расход:
- на мастичной кровле – 0,4 кг/м2
- на старой рулонной кровле – 0,6 кг/м2
- на металлической кровле – 0,4 кг/м2
Массовая доля нелетучих веществ: 50%
Температура применения: от -20 до +40 °С (перед работой при отрицательных температурах выдержать в теплом помещении не менее 24 ч)
Мастики для гибкой черепицы
Мастика для гибкой черепицы ТЕХНОНИКОЛЬ №23 (Фиксер)
Расход: зависит от типа выполняемых работ
Массовая доля нелетучих веществ: 75%
Температура применения: от -10 до +40 °С (перед работой при отрицательных температурах выдержать в теплом помещении не менее 24 ч)
Герметизирующие мастики
Мастика герметизирующая битумно-полимерная ТЕХНОНИКОЛЬ №71
Расход на один слой: 0,2 л/погонный метр
Массовая доля нелетучих веществ: 80-90%
Температура применения: от -10 до +40 °С (перед работой при отрицательных температурах выдержать в теплом помещении не менее 24 ч)
Для некоторых типов мастик в частности приклеивающих берутся дополнительные параметры, которые можно уточнить в техническом листе на материал).
Мастика битумно-полимерная эмульсионная ТЕХНОНИКОЛЬ №31 морозостойкая
Подробнее
Мастика герметизирующая битумно-полимерная ТЕХНОНИКОЛЬ №71
Подробнее
Мастика гидроизоляционная ТЕХНОНИКОЛЬ № 24 (МГТН)
Подробнее
Мастика для гибкой черепицы ТЕХНОНИКОЛЬ №23 (Фиксер)
Подробнее
Мастика защитная алюминиевая ТЕХНОНИКОЛЬ № 57
Подробнее
Мастика кровельная горячая ТЕХНОНИКОЛЬ № 41 (Эврика)
Подробнее
Мастика кровельная ТЕХНОНИКОЛЬ № 21 (Техномаст)
Подробнее
Мастика приклеивающая ТЕХНОНИКОЛЬ №22 (Вишера)
Подробнее
Мастика приклеивающая ТЕХНОНИКОЛЬ №27
Подробнее
Мастика ТЕХНОНИКОЛЬ № 33
Подробнее
Показать еще
Оцените эту статью
4.5 (105)
Расход мастики битумной на 1м2 гидроизоляции
Содержание
- Расход битумной мастики на 1 м2 при гидроизоляции фундамента
- Расход битумной мастики на 1м2
- Виды битумной мастики
- Расход битумной мастики на 1 м2 при гидроизоляции фундамента
- Расход битумно-полимерной мастики на 1 м2
- Расход битумной мастики Технониколь на 1 м2
- Расход битумно резиновой мастики AquaMast
- Расход битумной мастики на 1 м2 гидроизоляции фундамента, кровли, пола, труб, колодца
- Назначение битумной мастики
- Типы материала
- Расход битумной мастики в зависимости от консистенции
- Расход в зависимости от количества слоев
- Сухой остаток и толщина слоя
- Расход в зависимости от способа нанесения
- Средние показатели расхода
- Какие еще факторы могут оказывать влияние
- Как снизить расход мастики
- Какой расход мастики на гидроизоляцию фундамента?
- Гидроизоляция фундамента мастикой — расход.
- Битумная гидроизоляция: расход мастики на 1м2
- Расход мастики битумной на 1м2 гидроизоляции
- Основные функции мастики битумной
- Применение мастики битумной
- Как выполнить гидроизоляцию фундамента с помощью битумной мастики?
- Как выполнить гидроизоляцию кровли с помощью битумной мастики?
- Установленный расход битума на 1 м2 гидроизоляции фундамента
- Виды и особенности материала
- Материалы и инструменты, необходимые для работы
- Расход смеси
- Как определить расход битумной мастики на 1 м2 гидроизоляции
- Преимущества средств на основе битума
- Разновидности мастики
- Нормативный расход средства разного способа нанесения
- Расход мастики Технониколь
- Технология правильного нанесения
- Расход битумной мастики на 1 м2 при гидроизоляции фундамента
- Расход битумной мастики на 1м2
- Виды битумной мастики
- Расход битумной мастики на 1 м2 при гидроизоляции фундамента
- Расход битумно-полимерной мастики на 1 м2
- Расход битумной мастики Технониколь на 1 м2
- Расход битумно резиновой мастики AquaMast
- Расход битумной мастики на 1 м2 гидроизоляции фундамента, кровли, пола, труб, колодца
- Назначение битумной мастики
- Типы материала
- Расход битумной мастики в зависимости от консистенции
- Расход в зависимости от количества слоев
- Сухой остаток и толщина слоя
- Расход в зависимости от способа нанесения
- Средние показатели расхода
- Какие еще факторы могут оказывать влияние
- Как снизить расход мастики
- Какой расход мастики на гидроизоляцию фундамента?
- Гидроизоляция фундамента мастикой — расход.
Расход битумной мастики на 1 м2 при гидроизоляции фундамента
Расход битумной мастики на 1м2
Битумная мастика – один из достаточно распространенных современных материалов, используемых для гидроизоляции. Ее можно использовать для гидроизоляции фундамента и крыши здания, а также при подготовке отдельных элементов конструкций, например, для столбов, являющихся основой заграждений или малых архитектурных форм.
Виды битумной мастики
Торговых наименований битумной мастики насчитывается несколько десятков, а вот, собственно, видом мастике всего несколько, точнее – три. Они отличаются по способу нанесения, а также по составу. Первый вариант мастики – применяется вместе с агрессивными химическими растворителями. Их основой чаще всего являются синтетические материалы, которые при смешивании дают раствор, какой можно наносить на обрабатываемую поверхность без предварительного его нагревания. Отличительной чертой подобных мастик является их высокая опасность, поэтому работать с ними требуется только при использовании средств, защищающих органы дыхания.
Второй вариант, в отличие от первого, хоть и состоит из синтетических материалов, однако, в качестве растворителя для него выступает обычная вода. Это в разы повышает безопасность его использования. Единственная сложность их использования – необходимость соблюдения температурных показателей окружающей среды. Они не должны выходить за пределы диапазона от +5 до +30 градусов.
Третьим вариантом мастики пользуются достаточно давно. Он традиционный, но при этом такая мастика создает массу сложностей. Для ее нанесения ее требуется разогревать и для этого применяются специальные инструменты. Мастики горячего нанесения опасны для мастеров во время работы с ними, поскольку температура их плавления достаточно высока, отчего повышается опасность термического ожога.
Расход битумной мастики на 1 м2 при гидроизоляции фундамента
При гидроизоляции фундамента могут быть использованы все перечисленные основные виды битумных мастик. Однако нормы их расхода несколько отличаются. Мастики холодного способа нанесения расходуются в объеме 1-1,5 кг на 1 м2 при условии, что толщина одного слоя составляет порядка 0,5-1 мм. Расход пропорционально повышается при увеличении количества слоев.
Горячие мастики ввиду технологических сложностей наносятся более толстым слоем – 2 мм. Поэтому и расход сырья, соответственно, увеличивается и составляет 2 кг на 1 м2. Стоит учесть, что количество слоев при гидроизоляции фундамента не может быть меньше двух, тоесть расход требуется увеличивать как минимум вдвое.
Расход битумно-полимерной мастики на 1 м2
Битумно-полимерные мастики нередко используются не просто для гидроизоляции, а для склеивания слоя гидроизоляции с основанием, поэтому их расход несколько отличается от основных параметров. В зависимости от бренда производителя, химического состава и назначения такой мастики ее расход может варьироваться от 0,8 до 3 кг на 1м2.
Расход битумной мастики Технониколь на 1 м2
Битумные мастики Технониколь также отличаются по своему составу, соответственно и расход у них отличается. К примеру, битумно-качуковый вид мастики под названием Техномаст, который используется для обработки кровли может расходоваться в объеме от 1 до 3,5 кг на 1 м2. Битумно-полимерные мастики, выпускаемые фирмой Технониколь, а именно Вишера и Фиксер расходуется в объеме не менее 0,8 кг на 1 м2.
Расход битумно резиновой мастики AquaMast
Еще один вид мастики производства Технониколь — битумно-резиновая смесь AquaMast. Она используется не для наружной, а для внутренней гидроизоляции помещений, например, для обработки ванных комнат. Ее расход варьируется в пределах от 0,5 до 1,5 кг на 1 м2
Расход битумной мастики на 1 м2 гидроизоляции фундамента, кровли, пола, труб, колодца
В процессе эксплуатации конструкции зданий, сооружений, а также разного рода коммуникации постоянно подвергаются воздействию неблагоприятных погодных факторов. Для того чтобы защитить их от контакта с влагой и преждевременного разрушения, используются гидроизоляторы. Разновидностей таких материалов существует множество. При этом одним из самых популярных является битумная мастика. Это средство отличается простотой в нанесении и стоит недорого. Перед началом обработки важно сделать соответствующие расчеты и узнать точный расход битумной мастики на 1 м2 гидроизоляции. Это позволит произвести работы максимально эффективно и не допустить лишних трат.
Назначение битумной мастики
Использоваться этот популярный гидроизоляционный материал может для обработки самых разных элементов конструкции зданий и сооружений. Чаще всего битумную мастику применяют для обмазки подземных частей фундамента или цоколей. Также это средство используют для гидроизоляции плоских кровель. Применяют мастику и для защиты цокольных этажей и погребов от проникновения грунтовых вод. В этом случае обработка может производиться как снаружи, так и изнутри. Очень эффективную защиту с использованием этого материала можно сделать и для подземных частей разного рода малых архитектурных форм (беседок, качелей, детских горок и т. д. ). Нижние концы столбов заборов также часто обрабатываются именно этим материалом.
Иногда используют мастику и для наклеивания полос рулонных гидроизоляционных материалов на разные поверхности. Так поступают, к примеру, при отделке кровель или фундаментов рубероидом. Часто мастика применяется также для обработки труб и коммуникационных колодцев.
Типы материала
Расход битумной мастики на 1 м2 гидроизоляции зависит в первую очередь от ее разновидности. Представляет собой этот материал смесь органических веществ, обладающую вяжущими свойствами. Классифицироваться битумная мастика может по нескольким признакам. Различают, к примеру, холодную и горячую ее разновидности. Во втором случае мастика перед применением растапливается в бочке. Холодный вариант средства изначально имеет жидкую консистенцию.
Помимо этого мастика бывает одно- или двухкомпонентной. Первый вариант можно использовать сразу же после покупки. Двухкомпонентные мастики состоят из 2 отдельных средств, которые нужно смешивать перед употреблением. По виду основы такие средства классифицируются на каучуковые (эластичные), масляные и обычные полимерные.
Расход битумной мастики в зависимости от консистенции
Конечно же, чем гуще материал, тем выше будет его расход. Узнать, сколько конкретно мастики требуется для обработки 1 м2 поверхности, можно, если прочитать инструкцию по применению. Этот показатель производители указывают в обязательном порядке. Расход горячей мастики обычно меньше, чем холодной. Дело в том, что растопленный разогретый материал ложится на поверхность максимально ровно, не образует бугров и ям. К тому же горячая мастика практически не дает усадки. В результате этого и снижается расход. У холодной мастики консистенция обычно более вязкая, чем у растопленной. Поэтому для обработки поверхностей ее приходится затрачивать довольно-таки много.
Расход в зависимости от количества слоев
Одноразовое обмазывание фундамента или плоской крыши мастикой нужного результата обычно не дает. Поэтому обрабатывают поверхности с использованием этого материала чаще всего в 2-3 слоя. Это позволяет полностью исключить контакт промазанной поверхности с влагой. Расход битумной мастики на 1 м2 гидроизоляции производителем указывается обычно только для одного слоя. Следовательно, имеющуюся в инструкции цифру при расчете нужно умножать на 2 или на 3.
Сухой остаток и толщина слоя
Холодная мастика, в отличие от горячей, обычно дает очень сильную усадку. Количество материала, присутствующего на обработанной поверхности после испарения жидких веществ, называется сухим остатком. Показатель этот у разных видов мастик не одинаковый и может составлять 20-70%. Соответственно, материала с сухим остатком в 20% будет затрачиваться примерно в три раза больше, чем средства с показателем в 70%. Таким образом, чем выше этот показатель, тем быстрее и проще выполнять работы.
Расход в зависимости от способа нанесения
Работать с битумной мастикой полагается при температуре от -10 до +50 °С. Перед применением материал нужно тщательно перемешивать. Наносится мастика на поверхность в зависимости от разновидности с помощью кисти, распылителя, шпателя или валика. В последнем случае слой обычно получается более ровным. А следовательно, и расход битумной мастики на 1 м2 гидроизоляции снижается. Также количество затрачиваемого средства можно снизить, если использовать распылитель. В этом случае легко с большой точностью дозировать материал.
Средние показатели расхода
Для нанесения слоя в два миллиметра требуется примерно три с половиной килограмма мастики на квадратный метр в сухом остатке, в 1 мм — 1-2 кг. При обработке крыш чаще всего наносится 3-4 слоя материала. Поэтому расход битумной мастики на 1 м2 гидроизоляции кровли увеличивается до 3-5 кг/м 2 . При наклеивании рубероида на поверхности в один слой обычно уходит не более 250-800 грамм средства на 1 м2. Дело в том, что сплошняком материал в данном случае обычно не наносится.
Расход битумной мастики на 1 м2 гидроизоляции труб обычно не превышает полутора килограмм. В этом случае чаще всего используется масляная разновидность материала. Наносится мастика на трубы в 1-2 слоя. В последнем случае расход, конечно же, возрастет примерно в 2 раза и составит 2-3 кг.
Какие еще факторы могут оказывать влияние
Количество нужной для обработки поверхности мастики зависит в том числе и от разновидности последней. При гидроизоляции бетона, как материала очень пористого, средства уходит больше, чем при обмазывании дерева. Дело в том, что в данном случае поверхность часть мастики просто-напросто впитывает в себя. Дерево также имеет поры, но маленькие и не в слишком большом количестве. Расход битумной мастики на 1 м2 гидроизоляции колодца из бетонных колец, к примеру, будет больше, чем для монолитной ленты основания дома (до 3 кг). То же самое касается и фундаментов, собранных из плит. Дело в том, что в данном случае часть материала вбирают в себя стыки.
Помимо этого, количество затрачиваемого средства зависит от того, какая поверхность обрабатывается — вертикальная или горизонтальная. Так, расход битумной мастики на 1 м2 гидроизоляции пола будет составлять примерно 700-800 г. На стены же уйдет не меньше 1-2 кг средства при нанесении в один слой.
Как снизить расход мастики
Для экономии средства обрабатываемый материал можно сначала загрунтовать. Чаще всего для этой цели используется праймер. Обмазывают им поверхность обычно с использованием кисти или валика. Выполняется грунтование этим средством обычно в один слой. Высыхает праймер в течение нескольких часов.
Помимо всего прочего, чтобы снизить расход битумной мастики на 1 м2 гидроизоляции фундамента или кровли, следует тщательно подготовить поверхность. Чем меньше на ней будет трещин и сколов, тем дешевле обойдется гидроизоляция.
Холодную мастику перед применением нужно тщательно перемешать. Обмазывание вертикальных поверхностей производится сверху вниз. Если сделать наоборот, расход мастики увеличится. Да и саму операцию в данном случае будет выполнять сложнее из-за образующихся потеков. Перед нанесением каждого последующего слоя следует дожидаться полного высыхания предыдущего. Проверить готовность поверхности к новому обмазыванию просто. Для этого нужно потрогать ее пальцем. Если он не прилипает, значит, можно наносить следующий слой.
Какой расход мастики на гидроизоляцию фундамента?
С целью гидроизоляции конструкций из бетона и защиты от прочих пагубных внешних факторов рекомендуют обрабатывать поверхности специальными средствами. Важнейшее свойство таких гидроизоляционных составов – стойкость к воздействию влаги. Наиболее эффективное среди них – битумная гидроизоляционная мастика, чаще всего используемая для защиты фундаментов и кровельных перекрытий.
Перед тем как узнать ее расход на гидроизоляцию фундаментного основания, предлагаем сначала ознакомиться с их разновидностями, свойствами и узнать нормативный расход для разных типов битумной смазки. Ниже изложена эта информация, а также указаны нормы на 1 м² обрабатываемой основы.
Гидроизоляция фундамента мастикой — расход.При данной работе могут быть использованы все основные виды битумных мастик. Однако нормы их расхода несколько отличаются. Мастики холодного способа нанесения расходуются в объеме 1-1,5 кг на 1 м2 при условии, что толщина одного слоя составляет порядка 0,5-1 мм. Расход пропорционально повышается при увеличении количества слоев.
Горячие мастики ввиду технологических сложностей наносятся более толстым слоем – 2 мм. Поэтому и расход сырья, соответственно, увеличивается и составляет 2 кг на 1 м2. Стоит учесть, что количество слоев при гидроизоляции фундамента не может быть меньше двух, то-есть расход требуется увеличивать как минимум вдвое.
Мастика битумная Aquamast гидроизоляция фундамента — расход.Еще один вид это — Технониколь — битумно-резиновая смесь AquaMast. Она используется не для наружной, а для внутренней гидроизоляции помещений, например, для обработки ванных комнат. Ее расход варьируется в пределах от 0,5 до 1,5 кг на 1 м2.
Нормативный расход средства разного способа нанесения.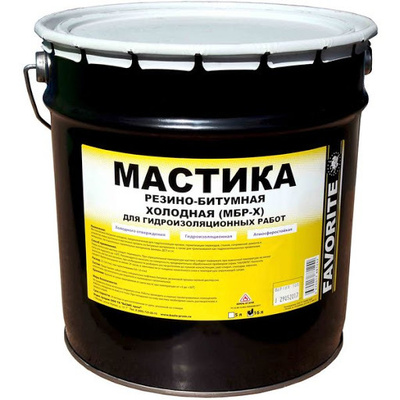
В зависимости от типа битумной смеси, меняется и нормативная затрата. Горячие составы не дают усадки, то есть в процессе нанесения не изменяют толщины. Средние показатели расхода мастичных средств при склеивании двух поверхностей составляют 0,8-1 кг на м² площади. С целью гидроизоляции используют примерно 2-3 кг для обеспечения слоя толщиной в 1 мм.
Если наносится вещество слоем до 2 мм, то получаем так называемый сухой остаток – вещество, что остается после высыхания на поверхности. В таком случае расход будет составлять от 3,5 до 3,8 кг на квадратный метр.
Технические характеристики меняются в зависимости от типа средства, соответственно, различаются и параметры расхода.
С целью гидроизоляции кровельных перекрытий слой битумной смеси наносят толщиной в 2 мм для горячего типа и в 1 мм – для холодного. Для фундамента все увеличивается в двое, так как наносят уже по 2 слоя.
При оценке условий проведения фундаментной гидроизоляции, строители ориентируются на следующие данные (усредненные, могут отличаться у разных производителей):
Битумная гидроизоляция: расход мастики на 1м2
Битумная мастика предотвращает проникновение влажности к арматуре и бетону, то есть служит гидроизоляцией. Такой материал используют для внешних работ, для гидроизоляции фундамента, ремонта крыш и других.
Расход мастики битумной на 1м2 гидроизоляции
Расход мастики битумной зависит от её разновидности, она бывает горячего и холодного использования. При изготовлении мастики холодного использования применяют воду или растворитель. Мастика горячего использования не дает усадку, поэтому её расход будет меньше.
Во время проведения гидроизоляционных работ, расход мастики составляет до 3 килограмм на 1м2, если она наносится одним слоем толщиной 2 миллиметра. На упаковке с материалом должен быть указан расход мастики для различных работ. Для того чтобы произвести гидроизоляцию фундамента понадобиться 2-4 килограмма на 1м2, при установке крыши – 3,5-6.
После нанесения растворители в летучем виде способны испаряться, за счет этого происходит усадка материала. При нанесении мастики в горячем виде, расход будет равняться максимальным показателям.
Основные функции мастики битумной
Бетон является пористым материалом, а также в нем могут появляться мелкие трещинки, через которые проникает влага. Арматура, находящаяся внутри бетона, из-за влажности начинает ржаветь, и становиться хрупкой, соответственно она деформируется, и перестает выполнять свои функции. В результате бетонная поверхность теряет свои свойства, становится неустойчивой, блок фундамента может треснуть или уйти в грунт. Если деформируется фундамент, то стены также искажаются, и дают трещины, это приводит к полному разрушению постройки.
Предотвратить все эти проблемы поможет нанесение гидроизоляции, для этого применяют мастику битумную. Она помогает предотвратить попадание влажности в поры бетона, таким образом, арматура останется в прежнем состоянии, а фундамент будет полностью выполнять свои функции. Также с помощью битумной мастики производят гидроизоляцию крыши во время ремонта или монтажа.
Применение мастики битумной
Чтобы нанести битум в твердом виде, его вначале расплавляют в металлической емкости, при этом происходит его обезвоживание. Вначале поверхность бетона должна хорошо просохнуть, а затем можно приступать к обмазыванию его мастикой. Если поверхность будет влажной, то жидкость закипит от горячей мастики, и под нанесенным слоем появятся пузыри, которые приведут к отслоению.
Для того чтобы нанести расплавленную мастику, необходимо взять широкую щетку или кисточку. Движения кистью осуществляют сверху вниз, мастику наливают в емкость из металла, так как она не плавиться. Материал хорошо втирают в бетон, чтобы заполнить поры, следующую полосу делают внахлест до 15 сантиметров.
Также нужно учитывать, что битум способен очень быстро остывать, поэтому работу необходимо выполнять вдвоем, тогда она будет проходить быстрее.
Мастику в холодном виде наносить намного легче, но перед началом работы, её хорошо перемешивают.
Выполнять гидроизоляционные работы с помощью мастики битумной, необходимо при температурном диапазоне от -10 градусов до +50. Перед тем как начать нанесение, мастику нужно хорошо размешать, допускается добавление растворителей, но их не должно быть больше 20% основной массы. Поверхность должна быть сухой и чистой, тогда гидроизоляция будет хорошо прилегать, не образовывая пузырей, это позволит сэкономить на расходе материала.
Мастика битумная имеет множество положительных качеств:
- Материал способен образовывать специальную пленку, которая не пропускает влажность.
- Мастика закрывает поры и мелкие дефекты, то есть трещины и сколы.
- Гидроизоляция такого вида предотвращает развитие различных микроорганизмов, плесени и грибка.
- Она может сцепляться с любым материалом, и является устойчивой к изменению температуры и влажности.
- Гидроизоляция не ломается, на ней нет трещин, так как материал обладает высокой эластичностью.
Как выполнить гидроизоляцию фундамента с помощью битумной мастики?
Для того чтобы выполнить гидроизоляцию фундамента, мастику битумную можно разбавить бензином, керосином или уайт-спиритом. Но растворители добавляют так, чтобы состав не был слишком жидким. Наносят мастику с помощью кисточки, если слоев несколько, то выполняются они с периодичностью в сутки.
Вначале поверхность фундамента тщательно очищают от загрязнений и пыли, это делается для того, чтобы материал ложился идеально ровно. Затем приступают к нанесению битумного праймера, если состав сильно впитывается, то необходимо сделать повторный слой. Грунтовочный состав наносится с помощью валика или кисточки, если имеются труднодоступные места.
После высыхания праймера наносят основной материал. Если работа проводится при минусовой температуре, то мастику необходимо разогревать до 40 градусов, делают это в металлической емкости.
На участках, где были замазаны трещины, необходимо выполнить армирование с помощью стекловолокна, его погружают в первый слой материала, дожидаются высыхания, а затем наносят второй слой. Если гидроизоляция армированная, то она меньше подвергается растяжению при расхождении трещин, и является более прочной. Стеклоткань наносится внахлест, он должен составлять не меньше 1 сантиметра.
Мастика является однородным составом, в неё добавляются различные компоненты и антисептики, которые выполняют антибактериальные функции. При качественной гидроизоляции, материал не будет отслаиваться, влага, несущая разрушающие действия, не проникает к бетону.
Мастика горячего вида применяется в том случае, если необходимо обеспечить качественную защиту при слишком высоких морозах в зимнее время, для этого используют специальные инструменты.
Как выполнить гидроизоляцию кровли с помощью битумной мастики?
Если необходимо, то в мастику добавляют растворитель, а затем хорошо перемешивают состав. Оставить материал на сутки в теплом помещении, чтобы он подогрелся.
Поверхность очищают от загрязнений и пыли, устраняют различного рода деформацию, убирают наледь и снег. После этого наносится праймер битумный, и высушивается. Если работа будет производиться на влажное основание, то потребуется специальная мастика, это должно быть указано на упаковке.
Затем мастику битумную наливают на поверхность, разравнивают при помощи швабры, и размазывают кисточкой. На тех участках, где образуются холодные швы, гидроизоляцию армируют с помощью стеклоткани, для этого её погружают в первом слое. По поверхности материала проходят валиком, дожидаются высыхания, и наносят следующий слой.
Перед тем как выполнять гидроизоляцию, необходимо проверить влажность поверхности, для этого на неё укладывают полиэтилен, оставляют на сутки, если под ним нет капелек, то можно приступать к работе.
Гидроизоляция армированного вида будет более качественной и долговечной, защитит поверхность от влажности. Отслоение материала не образуется в том случае, если поверхность подготовлена качественно, и не содержит влажности.
Установленный расход битума на 1 м2 гидроизоляции фундамента
Никто не станет оспаривать, что гидроизоляция фундамента имеет важное значение. Необходимость ее объясняется просто – создать защищенность основания объекта от негативного воздействия воды, вызывающей преждевременное разрушение. Разбираясь в данном вопросе более основательно, многие застройщики интересуются, какой расход битума на 1 м2 гидроизоляции фундамента является оптимальным.
Виды и особенности материала
Битумная мастика, применяемая для гидроизоляции фундамента, является материалом, обладающим определенными качествами:
- формирует влагонепроницаемое покрытие;
- заполняет пористые участки и мелкие дефекты;
- является препятствием для размножения вредных паразитов;
- отличается устойчивостью к температурным изменениям;
- обладает высокой эластичностью, сохраняет целостность слоя.
Расход битумной мастики на 1 м2 определяется с учетом вида материала и вариантов его применения.
Рынок стройматериалов предлагает большой выбор мастик, отличающихся составами, использованием и вариантами нанесения.
По составным компонентам битум для обработки фундамента делится на несколько видов:
- на наполнительных компонентах типа золы, цементного материала, мела и других минеральных добавок;
- мастика для фундамента на водной основе;
- масса, изготовленная на каучуковой крошке, минералах и полимерах.
По применению битумные мастики бывают горячими и холодными. Горячая битумная мастика для гидроизоляции фундамента непосредственно до использования разогревается до необходимого температурного показателя и образует в момент остывания монолитный слой. Применяют ее при обработке фундаментных конструкций, кровельных поверхностей, заполнения сколов и устранения небольших дефектных участков.
Основными техническими характеристиками битумной мастики, используемой для гидроизоляции фундамента, считаются:
- полное отсутствие усадок;
- быстрота затвердевания;
- низкая себестоимость из расчета одного квадратного метра площади;
- длительный период хранения и эксплуатации.
Строители предпочитают работать с холодными мастиками. Объясняется данный выбор тем, что в работе такие материалы, защищающие от проникновения влаги, не вызывают сложностей, наносятся обычными инструментами. Подобные смеси бывают одно- и двухкомпонентными. Первая группа перед применением просто перемешивается, а во втором случае придется соединять компоненты в определенных пропорциях.
Материалы и инструменты, необходимые для работы
Определившись, какая мастика для фундамента лучше, следует продумать, чем вы будете наносить гидроизоляционный слой:
- валики и широкие кисти;
- жесткую щетку;
- металлический ковшик;
- острый нож;
- штангенциркуль;
- растворитель – если вами выбрана технология холодного способа нанесения;
- источник под разогрев мастики до температуры, соответствующей готовности к нанесению.
Основательно подготовившись, разрешается переходить к практическим действиям.
Работы с мастичной массой выполняются в сухую погоду по просохшей поверхности.
Расход смеси
Важнейшим параметром битумного состава считают расход материала на 1 м2. Как правило, данный показатель отображен на заводской упаковке. В случае, если подобных сведений на этикетке нет, но указаны рекомендации по толщине наносимого слоя, то ориентировочный расход битумной мастики, необходимой для гидроизоляции всего фундамента, можно легко подсчитать самостоятельно.
К примеру, на покрытие двухмиллиметровым слоем основания вам требуется от 3 до 3.9 кг на каждый квадрат площади состава в сухом остатке. Под таким термином подразумевается объем материала, остающегося после того, как битум высохнет. Это значение выражено соотношением веса от расходованной смеси в процентах.
Согласно ГОСТу, почти все битумные мастики, используемые для гидроизоляции фундамента, данный показатель имеют на одинаковом уровне. При формировании однородного покрытия из битумной мастики, объем гидроизоляционного материала при показателе сухого остатка в двадцать процентов будет расходоваться в разы больше, чем при остатке в семьдесят процентов. Отсюда следует вывод, что при большем сухом остатке выгодней выполнять работы по гидроизоляции не только по трудоемкости, но и по стоимости.
Расход битумной мастики при нанесении ее на фундамент приведен в ниже. Здесь же учтены разновидности состава и толщина наносимого слоя:
Как определить расход битумной мастики на 1 м2 гидроизоляции
С целью гидроизоляции конструкций из бетона и защиты от прочих пагубных внешних факторов рекомендуют обрабатывать поверхности специальными средствами. Важнейшее свойство таких гидроизоляционных составов – стойкость к воздействию влаги. Наиболее эффективное среди них – битумная гидроизоляционная мастика от производителя Технониколь, чаще всего используемая для защиты фундаментов и кровельных перекрытий.
Битумная мастика
Для определения нужного количества мастики, предлагаем сначала ознакомиться с их разновидностями, свойствами и узнать нормативный расход для разных типов битумной смазки. Ниже изложена эта информация, а также указаны нормы на 1 м² обрабатываемой основы.
Преимущества средств на основе битума
Универсальность средств подтверждается многочисленными положительными свойствами мастики:
- Создание гидроизоляционной пленки поверх обрабатываемой основы, что не дает просочиться влаге.
- Закупорка битумной смазкой возможных маленьких дефектов на основе и поверхностных пор.
- Создание препятствия для развития грибка и плесени на основании.
- Высокие адгезивные свойства по отношению к любым стройматериалам.
- Морозоустойчивость битумных средств Технониколь.
- Эластичность и отсутствие растрескивания.
Разновидности мастики
Расход материала на м² будет зависеть от вида средства, типа основания и способа нанесения.
Классификация материалов
В зависимости от составных элементов битумной смеси, ее делят на следующие виды:
- Минеральная, в состав которой входит мел, цемент, зола и прочие добавки.
- Эмульсионная смесь. Для ее создания применяют эмульсию водную с применением битумной мелкодисперсной пыли.
- Полимерная мастика. В процессе изготовления данного типа средства применяют каучуковую крошку, полиуретан или полистирол, минеральные добавки.
- Пломбировочная. В ее состав входят битумы нефтяные, минеральные компоненты и пластифицирующие смолы. Пломбировочная мастика предназначена для приборов, агрегатов и их отдельных узлов, гнезд радиоаппаратуры и прочего.
Кроме того мастика может иметь жидкий (разжиженный) или твердый вид.
Твердый битум
В зависимости от способа нанесения средства делят на горячие и холодные. Горячие заблаговременно разогревают до соответствующей температуры (160-170 °С) перед непосредственным использованием. Заметьте, застывает состав за 1-2 минуты. Когда же нанесенный слой застынет, сверху получается прочное покрытие, которое защищает от влаги.
Этот тип применим для гидроизоляции фундамента, перекрытий, ликвидации трещин, с целью выравнивания поверхностей с неровностями до 6 мм. Горячая мастика быстро застывает, недорогая и не приводит к усадке. К этому типу относят и пломбировочную мастику.
И все же более популярны холодные смеси из-за удобства использования и нанесения. Среди холодной гидроизоляции выделяют смеси на основе одного или двух компонентов. Второй вариант хоть и требует специализированной подготовки, но зато более долговечен при хранении и в нанесенном виде.
Нормативный расход средства разного способа нанесения
В зависимости от типа битумной смеси, меняется и нормативный расход мастики. Горячие составы не дают усадки, то есть в процессе нанесения не изменяют толщины. Средние показатели расхода мастичных средств при склеивании двух поверхностей составляют 0,8-1 кг на м² площади. С целью гидроизоляции используют примерно 2-3 кг для обеспечения слоя толщиной в 1 мм.
Уже разжиженное средство
Если наносится вещество слоем до 2 мм, то получаем так называемый сухой остаток – вещество, что остается после высыхания на поверхности. В таком случае расход будет составлять от 3,5 до 3,8 кг на квадратный метр.
Технические характеристики меняются в зависимости от типа средства, соответственно, различаются и параметры расхода.
С целью гидроизоляции кровельных перекрытий слой битумной смеси наносят толщиной в 2 мм для горячего типа и в 1 мм – для холодного. Для фундамента все увеличивается в двое, так как наносят уже по 2 слоя.
Расход для холодного и горячего битума
Расход мастики Технониколь
Фирма Технониколь выпускает материал, сразу готовый к использованию. В процессе изготовления смесь модифицируют каучуком искусственного происхождения и добавляют в состав минеральные наполнители, технодобавки и растворитель органического происхождения. Последний компонент средства Технониколь обеспечивает высокую степень адгезии, эластичность смазки, высокие показатели стойкости к влаге и температурным режимам.
Что касается расхода фирменного средства, то для гидроизоляции 1 м² основы продукцией Технониколь необходимо от 2,5 до 3,5 кг вещества. Если же нужно лишь склеить два слоя основы, то хватит и 1 кг на м². Средства Технониколь выпускаются разных марок, в зависимости от чего меняются и технические характеристики.
Нормы для разных марок битумных мастик от Технониколь
Технология правильного нанесения
Чтобы нормативные параметры выполнялись, правильно наносите материалы на выбранную поверхность. Методика нанесения предусматривает несколько этапов:
- Грунтование. Этот этап включает смазывание битумной разжиженной пастой эмульсионного типа основания.
- Гидроизоляция битумной смазкой.
- Покрытие высохшей гидроизоляции еще одним слоем защиты. Это может быть покраска, облицовка основы, насыпь гравия или песка крупной фракции.
Нанесение битума валиком
Важно правильно работать со средством. После открытия емкости сразу приступают к работе, следуя производственной инструкции. Наносят вещество на поверхность посредством валика или кисти, забирая его из металлического ковша.
Нахлест нанесенных полос битума не должен в итоге оказаться менее 10-15 см. Если нужно нанести второй слой, то между каждым из них делают перерыв, за который предыдущий слой полностью высохнет.
Зная все данные, легко можно рассчитать, сколько понадобиться такого гидроизоляционного материала, как битумная мастика, расход на 1м2 которой составляет от 2,5 до 3,5 кг.
Расход битумной мастики на 1 м2 при гидроизоляции фундамента
Расход битумной мастики на 1м2
Битумная мастика – один из достаточно распространенных современных материалов, используемых для гидроизоляции. Ее можно использовать для гидроизоляции фундамента и крыши здания, а также при подготовке отдельных элементов конструкций, например, для столбов, являющихся основой заграждений или малых архитектурных форм.
Виды битумной мастики
Торговых наименований битумной мастики насчитывается несколько десятков, а вот, собственно, видом мастике всего несколько, точнее – три. Они отличаются по способу нанесения, а также по составу. Первый вариант мастики – применяется вместе с агрессивными химическими растворителями. Их основой чаще всего являются синтетические материалы, которые при смешивании дают раствор, какой можно наносить на обрабатываемую поверхность без предварительного его нагревания. Отличительной чертой подобных мастик является их высокая опасность, поэтому работать с ними требуется только при использовании средств, защищающих органы дыхания.
Второй вариант, в отличие от первого, хоть и состоит из синтетических материалов, однако, в качестве растворителя для него выступает обычная вода. Это в разы повышает безопасность его использования. Единственная сложность их использования – необходимость соблюдения температурных показателей окружающей среды. Они не должны выходить за пределы диапазона от +5 до +30 градусов.
Третьим вариантом мастики пользуются достаточно давно. Он традиционный, но при этом такая мастика создает массу сложностей. Для ее нанесения ее требуется разогревать и для этого применяются специальные инструменты. Мастики горячего нанесения опасны для мастеров во время работы с ними, поскольку температура их плавления достаточно высока, отчего повышается опасность термического ожога.
Расход битумной мастики на 1 м2 при гидроизоляции фундамента
При гидроизоляции фундамента могут быть использованы все перечисленные основные виды битумных мастик. Однако нормы их расхода несколько отличаются. Мастики холодного способа нанесения расходуются в объеме 1-1,5 кг на 1 м2 при условии, что толщина одного слоя составляет порядка 0,5-1 мм. Расход пропорционально повышается при увеличении количества слоев.
Горячие мастики ввиду технологических сложностей наносятся более толстым слоем – 2 мм. Поэтому и расход сырья, соответственно, увеличивается и составляет 2 кг на 1 м2. Стоит учесть, что количество слоев при гидроизоляции фундамента не может быть меньше двух, тоесть расход требуется увеличивать как минимум вдвое.
Расход битумно-полимерной мастики на 1 м2
Битумно-полимерные мастики нередко используются не просто для гидроизоляции, а для склеивания слоя гидроизоляции с основанием, поэтому их расход несколько отличается от основных параметров. В зависимости от бренда производителя, химического состава и назначения такой мастики ее расход может варьироваться от 0,8 до 3 кг на 1м2.
Расход битумной мастики Технониколь на 1 м2
Битумные мастики Технониколь также отличаются по своему составу, соответственно и расход у них отличается. К примеру, битумно-качуковый вид мастики под названием Техномаст, который используется для обработки кровли может расходоваться в объеме от 1 до 3,5 кг на 1 м2. Битумно-полимерные мастики, выпускаемые фирмой Технониколь, а именно Вишера и Фиксер расходуется в объеме не менее 0,8 кг на 1 м2.
Расход битумно резиновой мастики AquaMast
Еще один вид мастики производства Технониколь — битумно-резиновая смесь AquaMast. Она используется не для наружной, а для внутренней гидроизоляции помещений, например, для обработки ванных комнат. Ее расход варьируется в пределах от 0,5 до 1,5 кг на 1 м2
Расход битумной мастики на 1 м2 гидроизоляции фундамента, кровли, пола, труб, колодца
В процессе эксплуатации конструкции зданий, сооружений, а также разного рода коммуникации постоянно подвергаются воздействию неблагоприятных погодных факторов. Для того чтобы защитить их от контакта с влагой и преждевременного разрушения, используются гидроизоляторы. Разновидностей таких материалов существует множество. При этом одним из самых популярных является битумная мастика. Это средство отличается простотой в нанесении и стоит недорого. Перед началом обработки важно сделать соответствующие расчеты и узнать точный расход битумной мастики на 1 м2 гидроизоляции. Это позволит произвести работы максимально эффективно и не допустить лишних трат.
Назначение битумной мастики
Использоваться этот популярный гидроизоляционный материал может для обработки самых разных элементов конструкции зданий и сооружений. Чаще всего битумную мастику применяют для обмазки подземных частей фундамента или цоколей. Также это средство используют для гидроизоляции плоских кровель. Применяют мастику и для защиты цокольных этажей и погребов от проникновения грунтовых вод. В этом случае обработка может производиться как снаружи, так и изнутри. Очень эффективную защиту с использованием этого материала можно сделать и для подземных частей разного рода малых архитектурных форм (беседок, качелей, детских горок и т. д.). Нижние концы столбов заборов также часто обрабатываются именно этим материалом.
Иногда используют мастику и для наклеивания полос рулонных гидроизоляционных материалов на разные поверхности. Так поступают, к примеру, при отделке кровель или фундаментов рубероидом. Часто мастика применяется также для обработки труб и коммуникационных колодцев.
Типы материала
Расход битумной мастики на 1 м2 гидроизоляции зависит в первую очередь от ее разновидности. Представляет собой этот материал смесь органических веществ, обладающую вяжущими свойствами. Классифицироваться битумная мастика может по нескольким признакам. Различают, к примеру, холодную и горячую ее разновидности. Во втором случае мастика перед применением растапливается в бочке. Холодный вариант средства изначально имеет жидкую консистенцию.
Помимо этого мастика бывает одно- или двухкомпонентной. Первый вариант можно использовать сразу же после покупки. Двухкомпонентные мастики состоят из 2 отдельных средств, которые нужно смешивать перед употреблением. По виду основы такие средства классифицируются на каучуковые (эластичные), масляные и обычные полимерные.
Расход битумной мастики в зависимости от консистенции
Конечно же, чем гуще материал, тем выше будет его расход. Узнать, сколько конкретно мастики требуется для обработки 1 м2 поверхности, можно, если прочитать инструкцию по применению. Этот показатель производители указывают в обязательном порядке. Расход горячей мастики обычно меньше, чем холодной. Дело в том, что растопленный разогретый материал ложится на поверхность максимально ровно, не образует бугров и ям. К тому же горячая мастика практически не дает усадки. В результате этого и снижается расход. У холодной мастики консистенция обычно более вязкая, чем у растопленной. Поэтому для обработки поверхностей ее приходится затрачивать довольно-таки много.
Расход в зависимости от количества слоев
Одноразовое обмазывание фундамента или плоской крыши мастикой нужного результата обычно не дает. Поэтому обрабатывают поверхности с использованием этого материала чаще всего в 2-3 слоя. Это позволяет полностью исключить контакт промазанной поверхности с влагой. Расход битумной мастики на 1 м2 гидроизоляции производителем указывается обычно только для одного слоя. Следовательно, имеющуюся в инструкции цифру при расчете нужно умножать на 2 или на 3.
Сухой остаток и толщина слоя
Холодная мастика, в отличие от горячей, обычно дает очень сильную усадку. Количество материала, присутствующего на обработанной поверхности после испарения жидких веществ, называется сухим остатком. Показатель этот у разных видов мастик не одинаковый и может составлять 20-70%. Соответственно, материала с сухим остатком в 20% будет затрачиваться примерно в три раза больше, чем средства с показателем в 70%. Таким образом, чем выше этот показатель, тем быстрее и проще выполнять работы.
Расход в зависимости от способа нанесения
Работать с битумной мастикой полагается при температуре от -10 до +50 °С. Перед применением материал нужно тщательно перемешивать. Наносится мастика на поверхность в зависимости от разновидности с помощью кисти, распылителя, шпателя или валика. В последнем случае слой обычно получается более ровным. А следовательно, и расход битумной мастики на 1 м2 гидроизоляции снижается. Также количество затрачиваемого средства можно снизить, если использовать распылитель. В этом случае легко с большой точностью дозировать материал.
Средние показатели расхода
Для нанесения слоя в два миллиметра требуется примерно три с половиной килограмма мастики на квадратный метр в сухом остатке, в 1 мм — 1-2 кг. При обработке крыш чаще всего наносится 3-4 слоя материала. Поэтому расход битумной мастики на 1 м2 гидроизоляции кровли увеличивается до 3-5 кг/м 2 . При наклеивании рубероида на поверхности в один слой обычно уходит не более 250-800 грамм средства на 1 м2. Дело в том, что сплошняком материал в данном случае обычно не наносится.
Расход битумной мастики на 1 м2 гидроизоляции труб обычно не превышает полутора килограмм. В этом случае чаще всего используется масляная разновидность материала. Наносится мастика на трубы в 1-2 слоя. В последнем случае расход, конечно же, возрастет примерно в 2 раза и составит 2-3 кг.
Какие еще факторы могут оказывать влияние
Количество нужной для обработки поверхности мастики зависит в том числе и от разновидности последней. При гидроизоляции бетона, как материала очень пористого, средства уходит больше, чем при обмазывании дерева. Дело в том, что в данном случае поверхность часть мастики просто-напросто впитывает в себя. Дерево также имеет поры, но маленькие и не в слишком большом количестве. Расход битумной мастики на 1 м2 гидроизоляции колодца из бетонных колец, к примеру, будет больше, чем для монолитной ленты основания дома (до 3 кг). То же самое касается и фундаментов, собранных из плит. Дело в том, что в данном случае часть материала вбирают в себя стыки.
Помимо этого, количество затрачиваемого средства зависит от того, какая поверхность обрабатывается — вертикальная или горизонтальная. Так, расход битумной мастики на 1 м2 гидроизоляции пола будет составлять примерно 700-800 г. На стены же уйдет не меньше 1-2 кг средства при нанесении в один слой.
Как снизить расход мастики
Для экономии средства обрабатываемый материал можно сначала загрунтовать. Чаще всего для этой цели используется праймер. Обмазывают им поверхность обычно с использованием кисти или валика. Выполняется грунтование этим средством обычно в один слой. Высыхает праймер в течение нескольких часов.
Помимо всего прочего, чтобы снизить расход битумной мастики на 1 м2 гидроизоляции фундамента или кровли, следует тщательно подготовить поверхность. Чем меньше на ней будет трещин и сколов, тем дешевле обойдется гидроизоляция.
Холодную мастику перед применением нужно тщательно перемешать. Обмазывание вертикальных поверхностей производится сверху вниз. Если сделать наоборот, расход мастики увеличится. Да и саму операцию в данном случае будет выполнять сложнее из-за образующихся потеков. Перед нанесением каждого последующего слоя следует дожидаться полного высыхания предыдущего. Проверить готовность поверхности к новому обмазыванию просто. Для этого нужно потрогать ее пальцем. Если он не прилипает, значит, можно наносить следующий слой.
Какой расход мастики на гидроизоляцию фундамента?
С целью гидроизоляции конструкций из бетона и защиты от прочих пагубных внешних факторов рекомендуют обрабатывать поверхности специальными средствами. Важнейшее свойство таких гидроизоляционных составов – стойкость к воздействию влаги. Наиболее эффективное среди них – битумная гидроизоляционная мастика, чаще всего используемая для защиты фундаментов и кровельных перекрытий.
Перед тем как узнать ее расход на гидроизоляцию фундаментного основания, предлагаем сначала ознакомиться с их разновидностями, свойствами и узнать нормативный расход для разных типов битумной смазки. Ниже изложена эта информация, а также указаны нормы на 1 м² обрабатываемой основы.
Гидроизоляция фундамента мастикой — расход.При данной работе могут быть использованы все основные виды битумных мастик. Однако нормы их расхода несколько отличаются. Мастики холодного способа нанесения расходуются в объеме 1-1,5 кг на 1 м2 при условии, что толщина одного слоя составляет порядка 0,5-1 мм. Расход пропорционально повышается при увеличении количества слоев.
Горячие мастики ввиду технологических сложностей наносятся более толстым слоем – 2 мм. Поэтому и расход сырья, соответственно, увеличивается и составляет 2 кг на 1 м2. Стоит учесть, что количество слоев при гидроизоляции фундамента не может быть меньше двух, то-есть расход требуется увеличивать как минимум вдвое.
Мастика битумная Aquamast гидроизоляция фундамента — расход.Еще один вид это — Технониколь — битумно-резиновая смесь AquaMast. Она используется не для наружной, а для внутренней гидроизоляции помещений, например, для обработки ванных комнат. Ее расход варьируется в пределах от 0,5 до 1,5 кг на 1 м2.
Нормативный расход средства разного способа нанесения.
В зависимости от типа битумной смеси, меняется и нормативная затрата. Горячие составы не дают усадки, то есть в процессе нанесения не изменяют толщины. Средние показатели расхода мастичных средств при склеивании двух поверхностей составляют 0,8-1 кг на м² площади. С целью гидроизоляции используют примерно 2-3 кг для обеспечения слоя толщиной в 1 мм.
Если наносится вещество слоем до 2 мм, то получаем так называемый сухой остаток – вещество, что остается после высыхания на поверхности. В таком случае расход будет составлять от 3,5 до 3,8 кг на квадратный метр.
Технические характеристики меняются в зависимости от типа средства, соответственно, различаются и параметры расхода.
С целью гидроизоляции кровельных перекрытий слой битумной смеси наносят толщиной в 2 мм для горячего типа и в 1 мм – для холодного. Для фундамента все увеличивается в двое, так как наносят уже по 2 слоя.
При оценке условий проведения фундаментной гидроизоляции, строители ориентируются на следующие данные (усредненные, могут отличаться у разных производителей):
Сколько битумной мастики расходуется на м2?
Битумная мастика входит в перечень наиболее известных и востребованных гидроизоляционных материалов. Вязкая и достаточно жидкая смола используется в качестве эффективного гидробарьера в кровельных системах, защитного покрытия фундаментных оснований и других конструкций подземного базирования.
В достоинствах битумной мастики:
- доступная стоимость и универсальность применения;
- сохранение рабочих характеристик в широком диапазоне плюсовых и минусовых температур;
- превосходная адгезия и совместимость с минеральными и органическими основаниями.
Экологически чистый состав обмазочной битумной мастики обладает высокой стойкостью к температурным, биологическим и химическим неблагоприятным воздействиям, поэтому не имеет ограничений в технологиях гражданского промышленного и специального строительства. Расход мастики битумной на 1м2 гидроизоляции величина непостоянная, правильный выбор поможет сделать обзор наиболее оптимальных по стоимости и параметрам материалов.
Разновидности битумной мастики
Всё разнообразие битумного обмазочно-клеевого ассортимента состоит из трёх видов.
- Так называемые «холодные» мастики на основе химических растворителей и полимерных присадок не требуют предварительного подогрева, но небезопасны в монтаже, поэтому обязательным условием является применение защитных респираторов. Средний расход битумной мастики Аquamast составляет немногим более одного литра на каждый квадрат изолируемой площади.
- Водорастворимые разновидности битумной мастики менее опасны при нанесении. Существенный недостаток таких покрытий – сохранение рабочего свойства в плюсовом температурном диапазоне от 5 до 30 градусов Цельсия.
- «Горячие» мастики нуждаются перед нанесением в подогреве до определённой консистенции. Недостаток данных материалов в дополнительных затратах энергорессурсов и вероятность получения рабочим персоналом термических травм при неаккуратном обращении. Важное преимущество данной категории, это минимальное время готовности и отсутствие вынужденных технологических перерывов.
Экономические предпосылки
При реализации масштабных проектов, особое внимание уделяется расходу битумной мастики на м2 рабочей площади. Практика подтверждает, что этот показатель зависит от нескольких факторов, в частности, плотности самой мастики, фактуры и рыхлости поверхности основания. В среднем разброс варьируется от 1 до 3 кг/м2.
Таблица расхода в зависимости от температуры применения
Холодная битумная мастика (основа растворитель) | Холодная мастика (водная основа). Фундамент | Горячая битумная мастика. Кровля | Фундамент | Кровля | Фундамент |
Один слой, мм | 1,0 | 0,5-1,0 | 1,0 | 0,5-1,0 | 2,0 |
Расход один слой, кг на 1 м2 | 1,0-2,0 | 1,0-1,4 | 1,4-2,0 | 1,0-1,4 | 2,0 |
Время высыхания при +22°С и влажность 50% | 25 | 6 | 6 | ||
Температура покрытия,°С | -8 – +42 | +5 – +30 | от -8 | ||
Влажность основания,% | 5 | 9 | 5 |
Нормы расхода
Характеристики | Показатели | ||||
Холодное использование (основа синтетика) | Холодное применения (на воде) | Горячее применение | |||
На кровлю | На фундамент | На кровлю | На фундамент | На кровлю | На фундамент |
Слой 1 мм | До 1 | 0,6 – 1,0 | До 1 | 0,5 – 1,0 | 2,0 |
Расход в кг/м2 | 1,0 – 2 | 1,0 – 1,5 | 1,6 – 2 | 1,0 – 1,6 | 2,0 |
Сушка +22ºС, влажность до 50%, 24 часа |
Таблица расхода битумной мастики на 1 метр погонный в зависимости от проектных размеров толщины герметизации.
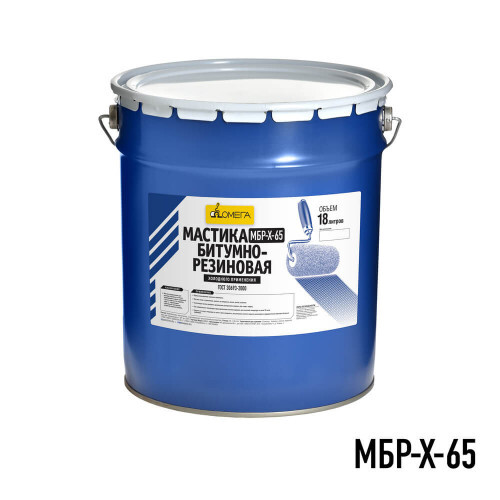
Обзор битумно-мастичной продукции ведущих брендов
В строительстве стабильно высоким спросом пользуется битумная мастика Технониколь. Расход на 1 м2 зависит от укрывистости конкретного состава.
- Эксплуатационный расход битумно-резиновой мастики Аquamast для внутренних помещений составляет от одного до полутора кг/м2.
- Расход фирменных битум-полимерных мастик «Вишера» и «Фиксер» более экономичный, на уровне 0,8 кг/м2.
- Битум-каучуковая разновидность кровельной мастики «Техномаст» демонстрирует стандартный расход на м2 в количестве от 1 до 3,5 кг.
Снижение расхода гидроизоляционной битумной мастики на 1 м2 за счёт разбавления растворителями и другими химическими компонентами может иметь нежелательные последствия, такие как ухудшение изоляционных свойств, сокращение рабочего ресурса и ухудшение экологичности материала.
Особенности гидроизоляции подземных конструкций
Расход битумной мастики для гидроизоляции фундамента зависит от рекомендаций выбранной технологии, состояния рабочей поверхности и других факторов. Чрезмерно шершавая или рыхлая поверхность бетона может увеличить расход мастичной обмазки в полтора-два раза.
Остались вопросы? Набирайте номер +7(499)653 72 82! Менеджеры ГидроСервиса дают исчерпывающие ответы на вопросы, помогут с выбором и рассчитают количество стройматериалов. Не теряйте время на сомнения, звоните!
Мастика битумная расход на 1м2 в Красноярске: 158-товаров: бесплатная доставка [перейти]
Партнерская программаПомощь
Красноярск
Каталог
Каталог Товаров
Одежда и обувь
Одежда и обувь
Стройматериалы
Стройматериалы
Здоровье и красота
Здоровье и красота
Текстиль и кожа
Текстиль и кожа
Детские товары
Детские товары
Продукты и напитки
Продукты и напитки
Электротехника
Электротехника
Дом и сад
Дом и сад
Торговля и склад
Торговля и склад
Промышленность
Промышленность
Вода, газ и тепло
Вода, газ и тепло
Все категории
ВходИзбранное
Мастика битумная расход на 1м2
Базовая смесь Основит Стартолайн FC44 M Производитель: Основит, Фасовка: 25 кг, Минимальная толщина
ПОДРОБНЕЕЕще цены и похожие товары
Ровилайн FC49 суперфинишный наливной пол Основит Производитель: Основит, Фасовка: 20 кг
ПОДРОБНЕЕЕще цены и похожие товары
Наливной пол быстротвердеющий основит PRO 20 кг Производитель: Основит, Фасовка: 20 кг
ПОДРОБНЕЕЕще цены и похожие товары
Шпатлевка Verputz Vershpatel LR+ Производитель: Verputz, Вид шпатлевки: финишная, Основа: полимерная
ПОДРОБНЕЕЕще цены и похожие товары
Юнис Плюс плиточный клей для керамогранита и любой плитки Производитель: Unis, Особенности:
ПОДРОБНЕЕЕще цены и похожие товары
Клей для пробки Decoll Vern 1л. (расход 0,5-1м2)
ПОДРОБНЕЕЕще цены и похожие товары
Клей для плитки Литокол Литоплюс K55 25 кг Производитель: Litokol, Особенности: морозостойкий,
ПОДРОБНЕЕЕще цены и похожие товары
Клей для плитки UNIS Мастер Юнис 2000 (25 кг) Производитель: Unis
ПОДРОБНЕЕЕще цены и похожие товары
Финишная смесь Основит Ниплайн FC42 H Производитель: Основит, Фасовка: 25 кг, Минимальная толщина
ПОДРОБНЕЕЕще цены и похожие товары
Клей плиточный быстрый 25 кг Производитель: Старатели
ПОДРОБНЕЕЕще цены и похожие товары
Универсальная смесь Основит Скорлайн FK48 R Производитель: Основит, Фасовка: 20 кг, Минимальная
ПОДРОБНЕЕЕще цены и похожие товары
Наливной пол быстротвердеющий Основит PRO 20кг Производитель: Основит, Фасовка: 20 кг
ПОДРОБНЕЕЕще цены и похожие товары
Weber. Vetonit / Наливные полы, Weber.Vetonit Производитель: Weber, Фасовка: 25 кг
ПОДРОБНЕЕЕще цены и похожие товары
Наливной пол быстротвердеющий Основит PRO 20кг Производитель: Основит, Фасовка: 20 кг
ПОДРОБНЕЕЕще цены и похожие товары
Наливной пол быстротвердеющий Основит PRO 20кг Производитель: Основит, Фасовка: 20 кг, Вид: финишная
ПОДРОБНЕЕЕще цены и похожие товары
Наливной пол быстротвердеющий Основит PRO 20кг Производитель: Основит, Фасовка: 20 кг, Вид: финишная
ПОДРОБНЕЕЕще цены и похожие товары
Базовая смесь Основит Стартолайн FC41 H Производитель: Основит, Фасовка: 25 кг, Минимальная толщина
ПОДРОБНЕЕЕще цены и похожие товары
Базовая смесь Основит Стартолайн FC43 L Производитель: Основит, Фасовка: 25 кг, Минимальная толщина
ПОДРОБНЕЕЕще цены и похожие товары
Универсальная смесь Старатели Толстый Производитель: Старатели, Фасовка: 25 кг, Минимальная толщина
ПОДРОБНЕЕЕще цены и похожие товары
Основит Наливной пол быстротвердеющий Основит PRO 20кг Производитель: Основит, Фасовка: 20 кг
ПОДРОБНЕЕЕще цены и похожие товары
Наливной пол Основит Pro 20 кг Производитель: Основит, Фасовка: 20 кг
ПОДРОБНЕЕЕще цены и похожие товары
Пескобетон М300 КСС, 40кг. Марка: М300, Время твердения: 1дн, Жизнеспособность раствора : 120мин.
ПОДРОБНЕЕЕще цены и похожие товары
Weber Vetonit L шпаклевка финишная (20кг) Производитель: Weber, Вес: 20кг, Вид шпатлевки: финишная
ПОДРОБНЕЕЕще цены и похожие товары
Наливной пол Старатели Производитель: Старатели
ПОДРОБНЕЕЕще цены и похожие товары
Пескобетон М-300 МКУ 40кг Производитель: МКУ, Марка: М300
ПОДРОБНЕЕЕще цены и похожие товары
Вебер.ветонит ВХ белая Производитель: Weber, Вид: финишная
ПОДРОБНЕЕЕще цены и похожие товары
Пескобетон М300 Марка: М300
ПОДРОБНЕЕЕще цены и похожие товары
Мультидез Тефлекс концентрат, 500 мл Производитель: Тефлекс, Концентрат: Да, Объем: 500мл
ПОДРОБНЕЕЕще цены и похожие товары
2 страница из 6
МАСТИКА БИТУМНО-КАУЧУКОВАЯ МГХ-К ХОЛОДНАЯ ГРИДА
Мастика битумно-каучуковая МГХ-К – поликомпонентная мастика холодного применения на основе нефтяного битума и органических растворителей с добавлением резиновой крошки мелкой фракции, синтетического термопластичного блок-полимера и смоляных кислот.
Сложный состав обеспечивает отличные потребительские характеристики и обладает одним из наилучших среди выпускаемых компанией Грида мастик, показателем относительного удлинения при разрыве.
Отличные показатели эластичности (в диапазоне от -30 до +130°С) и теплостойкости, прочность сцепления с бетоном, обеспечивают формирование надежной и долговечной мастичной кровли.
Сформированный гидроизоляционный слой сохраняет целостность при некоторой деформации конструкций вследствие температурных изменений или вибраций.
Невысокая степень вязкости мастики битумной гидроизоляционной позволяет хорошо смачивать бетон, заполнить пустоты, трещины и щели при ремонте кровельного ковра или гидроизоляции подвала, фундамента, гаража, создавая цельное водонепроницаемое гидроизоляционное покрытие.
Высокие показатели адгезии и условной прочности, в сочетании с большой температурой размягчения, позволяют использовать битумно-каучуковую мастику для гидроизоляции широкого круга строительных сооружений и конструкций.
Битумная мастика МГХ-К используется так же для ремонта дорожного покрытия. Мастика хорошо смачивает поверхность асфальтобетона и дорожных материалов и повышает адгезию, за счет чего достигается надежное сцепление старого и нового дорожного полотна при «ямочном» ремонте.
Защита швов от проникновения влаги при «ямочном» ремонте повышает надежность и продлевает срок службы отремонтированных участков дороги.
Назначение. Мастика битумно-каучуковая МГХ-К «Грида» предназначена для следующих видов гидроизоляционных работ:
Основные характеристики мастики битумно-каучуковой МГХ-К “Грида”
Показатель | Мастика битумно-каучуковая МГХ-К, значение |
Условная прочность, МПа (кгс/см2) | не менее 0,5 (5,0 кгс/см2) |
Жизнеспособность, час | не менее 0,5 часа |
Относительное удлинение при разрыве, % | не менее 300 |
Водопоглощение в течение 24 ч.![]() | не более 0,5 |
Условная вязкость, секунд | не менее 15 |
Массовая доля нелетучих веществ, % | не менее 50 |
Прочность сцепления с бетоном, МПа (кгс/см2) | не менее 0,4 (4,0 кгс/см2) |
Температура размягчения, K (°С) | не ниже 403 (130°С) |
Гибкость на брусе с закруглением радиусом, мм, 5.0±0.2 при температуре, K (°С), не выше 268 (минус 5) | на поверхности образца не должно быть трещин |
Производитель: Грида.
Применение. Перед нанесением мастики в качестве обмазочной гидроизоляции, необходимо подготовить гидроизолируемое основание. Его следует очистить от пыли, песка, остатков старой кровли, слоя старой гидроизоляции и огрунтовать праймером битумным.
Подробнее о подготовке основание перед укладкой наплавляемых гидроизоляционных материалов, читайте в Кратком руководстве.
Перед применением мастику необходимо перемешать по всему объему до образования однородной массы.
Гидроизоляционные работы с использованием мастики допускается проводить при температуре не ниже -10°С.
На поверхность основания мастика наносится шпателем или после разбавления растворителем до требуемой консистенции – с помощью кисти или валика.
Разбавлять мастику допускается в объеме, не превышающем 20-50% от массы с помощью растворителя.
В качестве, которого используются следующие: толулол, ксилол, смесевые растворители – 646, 648, 649, Р-4, РС-2, а так же сольвент нефтяной для лакокрасочной промышленности. Использование обычного автомобильного бензина в качестве растворителя не допускается.
Для устройства гидроизоляции рекомендуется наносить 2-3 слоя мастики, с укладкой между слоями армирующей стеклоткани, существенно повышающей надежность и долговечность гидроизоляционного слоя. Средний интервал нанесения каждого последующего слоя составляет около 6 часов (при условии температуры окружающей среды не менее 20°С).
Для приклеивания строительных материалов, в том числе гидроизоляционных на хорошо подготовленное, ровное основание рекомендуется нанесение одного слоя толщиной 0,7-1,0 мм.
Время полного высыхания мастичного слоя – не менее 24 часов. При понижении температуры окружающей среды, время полного высыхания увеличивается.
При работе с мастикой в условиях отрицательных температур ее рекомендуется подогреть до +30-50°С. Разогревать мастику следует на “водяной бане” или другими способами исключающими использование открытого огня и возможности искрообразования. Перед нагревом необходимо нарушить герметичность тары.
Расход мастики. Средний расход мастики при проведении гидроизоляционных работ составляет 0,8-1л/м2.
Фасовка. Металлическая тара объемом 2, 20 и 50 литров.
Цена. Узнать актуальные цены и купить мастику битумно-каучуковую МГХ-К «Грида» по доступным ценам, вы можете, позвонив нам по контактному телефону.
Сертификаты. На мастику представлены необходимые сертификаты, ознакомиться с которыми можно здесь.
Условия хранения. Хранить в сухом, защищенном от прямых солнечных лучей месте. Вдали от источников огня и тепла.
Меры безопасности. Огнеопасно. Проведение гидроизоляционных работ вблизи источников открытого огня – запрещено. При работе с мастикой необходимо соблюдать противопожарную безопасность и безопасность труда. Работы с мастикой необходимо проводить в резиновых перчатках.
Гидроизоляция Грида – качество по доступным ценам.
Сопутствующие товары: стеклоизол, гидроизол, праймер битумный холодный, мастика битумно-полимерная, линокром, унифлекс, битум строительный, метлы полипропиленовые, лопаты совковые и штыковые, черенки деревянные, мешки полипропиленовые, щетки для пола.
свойства, расход, применение. Использование битумной мастики. Кровельная битумная мастика и ее использование. Свойства материала и основные характеристики.
Апрель 10 • Стройматериалы • Просмотров 2296 • Комментариев к записи Кровельная битумная мастика: свойства, расход, применение нет
Проблема изоляции или ремонта кровли, подвергающейся воздействию влаги, как внутри, так и снаружи, часто возникает в процессе строительства и эксплуатации здания. Вместе с тем, многие задаются вопросом: а есть ли какой-нибудь иной материал, например, для экстренного ремонта крыши, кроме битума? И как провести ремонтные работы, уложившись в небольшую для обычного человека сумму? Выход есть: мастика битумная кровельная.
Содержание
- Общие сведения о материале
- Мастика битумно-полимерная
- Мастика битумнобутилкаучуковая
- Мастика битумная кровельная горячая
- Мастика битумно-латексная кровельная
- Мастика битумно-резиновая кровельная
- Обзор производителей
- Кровельная битумная мастика. Видео
Общие сведения о материале
Мастики применяются для покрытия любого вида кровли: мастичной, металлической, рулонной, бетонной или асбоцементной. При этом перед работой удалять старое покрытие не требуется (кроме крыш, где было положено много слоев рубероида). Главным отличием всех видов мастик от рулонных материалов является то, что на поверхности крыши формируется монолитное покрытие, подобно пленке или мембране, защищающее кровлю от проникновения осадков.
Смесь бывает однокомпонентной и двухкомпонентной. Первая сразу же готова к применению и ее стабилизация происходит благодаря испарениям растворителя. Такой материал поставляется в герметичной емкости с ограниченным сроком хранения, его удобно использовать, однако нельзя хранить в открытом виде.
Двухкомпонентная мастика поставляется в виде двух химически малоактивных составов, которые по отдельности могут храниться больше 12 месяцев, что является несомненным преимуществом, ведь это дает возможность сделать покупку материала заблаговременно.
Количество нанесенных слоев может варьироваться в зависимости от неровностей исходного покрытия или угла кровли. Если он превышает 25°, то использование кровельной мастики не рекомендуется. Материал, в составе которого есть масло, является морозостойким.
По типу разбавителя кровельные мастики различают на водосодержащие, с органическими растворителями и содержащие органические жидкие вещества. Все виды достаточно быстро стабилизируются, приобретая водостойкость, прочность и отличную клеящую способность.
Часто отдельные узлы кровли, покрытой мастикой, армируют для придания прочности. Есть два основных материала, которые для этого используют:
- стеклосетка. Это сеть высокой прочности с различным размером ячеек, сотканная из стеклонити, которая тоже бывает разной толщины;
- стеклохолст – аналогичное полотно, но с произвольным расположением волокон.
Поскольку оба материала очень прочные, снижается и эластичность гидроизоляции. В этом случае следует подбирать подходящую именно для этих работ мастику.
Совет: мастика в сочетании с цементом и песком дает очень прочную эластичную смесь.
Единственный недостаток материала на битумной основе – это то, что за один подход сложно получить равномерную требуемую толщину изоляции, особенно, если дело касается уклончатых или неровных поверхностей. В таком случае, наносят два, а то и три слоя, что увеличивает и расход материала.
Мастика битумно-полимерная
Представляет собой полужидкую черную массу холодного применения на основе модифицированного битума.
Область применения мастики крайне широка: используется для гидроизоляции стен, цоколя, подвала, балкона, межпанельных стыков, кровли и ремонта старых конструкций. Ее используют для гидроизоляции полов в помещениях с повышенной влажностью. Благодаря высокой степени эластичности, даже при возникновении глубоких трещин в здании, мастика препятствует проникновению в них влаги. Таким образом, ее эксплуатационные и технологические свойства в полной мере отвечают техническим условиям.
В состав битумно-полимерной мастики входят модифицированный битум, акрилатная водоэмульсия, различные пластификаторы и адиативы.
По внешнему виду и свойствам, мастика, нанесенная на поверхность кровли, скорее похожа на герметик, нежели на привычный для большинства битум. Разработанные приемы ее применения в строительстве позволяют получить надежное, бесшовное и долговечное изоляционное покрытие. Эта битумная мастика, судя по отзывам, наиболее популярна.
Преимущества мастики:
- материал приятен и удобен в использовании;
- у нее отличная адгезия к большинству строительных материалов: бетону, рубероиду и даже металлу;
- ложится как на сухую, так и на мокрую поверхность;
- легко наносится в самых труднодоступных местах;
- не требует подогрева, в отличие от других кровельных покрытий;
- не содержит растворителей, а потому – нетоксична, возможно нанесение в закрытых помещениях;
- Не боится высоких температур: устойчиво держится на вертикальных поверхностях даже при 120 °С.
Перед использованием мастику следует тщательно перемешать, при необходимости ее можно разбавить растворителем до нужной консистенции (например, сольвентом, уайт-спиритом, нефрасом). Поверхность перед началом обработки нужно высушить, очистить от грязи, пыли, пятен, наледи и прочих загрязнений. Если смесь наносится на пористое основание, его сначала грунтуют праймером на битумной основе.
Наносят мастику послойно, при помощи шпателя, кисти или наливом, разравнивая ее гребками. Можно также наносить распылением, тем самым контролируя ее толщину. Для эффективного воздействия достаточно слоя в 2 мм. Расход мастики битумной на акрилатной основе составляет не более 1-2 кг на 1 м2. Время окончательного застывания и набора свойств – 7 дней.
Совет, как протестировать мастику на качество. Два небольших куска пергамина склеиваются между собой, а затем резко разрываются. Мастика должна остаться целой, а разрыв прийтись на пергамин.
Среди наиболее достойных представителей можно выделить мастику Mabital от компании Supraten производства Молдовы. Она выполнена по технологиям и с использованием ингредиентов, аналогичным ведущим немецким производителям, поэтому ее отличает высокое качество и приемлемая цена.
Мастика кровельная от Технониколь (Беларусь) – это кровельный, готовый к применению материал, в состав которого входит нефтяной битум, модифицированный искусственным каучуком, а также технологические добавки, минеральные наполнители и органический растворитель. Используется как в сочетании со стеклотканью, так и без нее. Расход для устройства гидроизоляции кровли – 2,5 – 3,5 кг на м2. Время высыхания – до 24 часов.
Мастика битумнобутилкаучуковая
Предназначается для проведения работ по гидроизоляции как строительных конструкций, так и устройства крыш в промышленном и гражданском строительстве.
Битумнобутилкаучуковая гидроизоляционная мастика (МГББ) является готовым к применению многокомпонентным материалом, в состав которого входит битумнобутилкаучуковая композиция, наполнители, пластификаторы, модификаторы и органический растворитель. За счет инновационной технологии производства, МГББ является передовым материалом, обеспечивающим высокую степень гидроизоляции конструкций. К ее важным достоинствам относятся высокий уровень эластичности, сцепления с основой, устойчивость к перепадам влаги и температур.
Достоинства МГББ:
- не нуждается в предварительном подогреве
- вулканизация происходит при обычной температуре воздуха
- имеет антикоррозийные свойства и хорошее сцепление со многими поверхностями
- температурный диапазон для работы с мастикой — от -40 до +80 °С.
Применение и расход:
Перед использованием материала, покрытие должно быть тщательно очищено, не иметь видимых пор и трещин. Поверхность следует прогрунтовать битумным праймером или мастикой, разведенной уайт-спиритом в пропорции 1:2.
Подходит для всех видов ремонта кровли и гидроизоляции наружных конструкций. Возможно использование МГББ как в сочетании с рулонными материалами и стеклосеткой, так и без них. Расход – 2-5 кг на м2. Используется в качестве клея для рулонных битумных материалов. Расход: 1,5-2 кг на м2. Гидроизоляция, одновременно с приклеиванием фанеры, ДСП и ДВП на любые бетонные, цементные и гипсобетонные поверхности. Расход: 1,5-2 кг на м2. Гидроизолирующая антикоррозийная обработка металлических поверхностей. Расход: 1-2 кг на м2.
Бесшовное покрытие, нанесенное в несколько слоев, и армированное дополнительным материалом, после того, как завершился процесс испарения растворителя, превращается в водонепроницаемый эластичный слой, устойчивый к механическим повреждениям.
Мастика битумная кровельная горячая
Обозначается как МБК-Г и предназначена для устройства мастичных армированных кровель, а также работ с рулонными материалами. Используется, в том числе для гидроизоляции металлических, бетонных, железобетонных, деревянных и прочих конструкций, включая трубопровод.
Мастика представляет собой однородную густую массу, которую используют в горячем состоянии. Наносится кистью или шпателем слоем толщиной в 2 мм.
В изготовлении мастики задействуют нефтяной кровельный битум и его вяжущие сплавы, соответствующие требованиям ГОСТа 9548. Расплавленный состав должен быть довольно жидким и литься тонким слоем, растекаясь по поверхности кровли.
Преимущества битумной горячей мастики:
- невысокая стоимость
- простота в эксплуатации
- возможность нанесения в труднодоступные места, такие, как вентиляционные колодцы, несущие конструкции, отбойники и прочие
- за счет более жидкой консистенции, ее расход меньше по сравнению с остальными мастиками.
Применение: перед использованием данный вид гидроизоляционного материала нагревают до температуры около 150 °С (эта цифра может быть разной в зависимости от производителя). Самый простой способ нагреть мастику – поставить металлическую емкость со смесью на пенобетонные блоки или кирпичи, оставив между ними зазор, в который затем ставится горелка. Важно: не забудьте снять крышку при нагревании. Закрытую битумную мастику нагревать нельзя. Чтобы убедиться, что мастика достаточно нагрелась, опустите в нее рабочую кисть и протестируйте на небольшом участке: подогретая смесь должна легко наноситься, заполняя поры. Нанесенная тонким слоем, после остывания мастика обретает достаточную прочность.
МБК-Г фирмы Гидроизол. Продается в жестяных ведрах по 18 кг. Температура размягчения должна составлять не менее 100 °С. При нанесении слоем 2 мм, расход мастики составляет 1,5-2 кг на м2. Продукция производителя сертифицирована и соответствует требованиям ГОСТ.
Кровельная горячая мастика Технониколь №41. Предназначается для устройства и ремонта кровли, при заделке трещин и выбоин в стяжках, установке водосточных углублений, в местах стыковки кровли с трубами и прочими сооружениями. Температура разогрева мастики – 160-180 °С. Материал наносится на предварительно загрунтованное битумным праймером покрытие при помощи инструмента, или наливным методом. Поставляется в бумажных герметичных мешках по 30 кг.
Мастика битумно-латексная кровельная
Главное отличие этого материала от остальных в том, что в ее составе содержится полимер – латекс. Благодаря ему мастика становится гораздо более гибкой и ее можно окрашивать в любой цвет. Такой материал идеально подходит для склеивания рулонных кровельных материалов, отсюда ее еще называют «клеящая».
Битумно-латексную мастику на водной основе применяют для всех видов гидроизоляции, в том числе и устройства и ремонта кровель.
Тест на гибкость: на кусочек пергамина наносят битумно-латексную мастику и изгибают его на стержне диаметром 15 мм. Трещин на поверхности быть не должно.
Обзор производителей
Мастика битумная эмульсионная Технониколь №33. Главная ее особенность – возможность механизированного напыления, а значит, можно многократно уменьшить сроки выполнения работ. Двухкомпонентная, негорючая, эта «жидкая резина» в своем составе не содержит растворителей, но при этом обладает повышенными качествами, а в сочетании с коагулирующим раствором (водой и хлоридом кальция), существенно сокращаются сроки высыхания.
Мастика битумно-латексная Ореол-1 ГидроЭластик (Киев). Выпускается в таре 10 кг, благодаря своей высокой адгезии препятствует образованию вздутий и разрывов. Основа – растворитель. Наносится в 2-3 слоя, время высыхания каждого из слоев – 12-24 часа.
Двухкомпонентная мастика Watergum Roof. На водной основе, обладает высокой стойкостью к УФ-лучам. Кроме ремонтной функции, обладает антикоррозийной защитой строительной конструкции. Наносится механически, срок полимеризации – 24 часа.
Мастика битумно-резиновая кровельная
Так же, как и латексная, широко используется для склеивания между собой рулонных материалов. Благодаря введению жидкой резины в составе, а также смол и прочих химических элементов, способных улучшить адгезию, эта мастика не такая текучая, как другие. Из-за повышенной плотности, ее наносят шпателем.
Особые компоненты в составе делают возможным нанесение даже на влажную поверхность. Благодаря наличию каучука, образуется постоянно эластичный слой, сопряженный с основанием, который принимает на себя вибрации и движения, тем самым минимизируя возможность появления трещин.
Битумно-резиновая мастика устойчива к воде, щелочам и слабым кислотам. При нанесении на старый рубероид, проникает в микропоры и возвращает эластичность, создавая на нем защитную пленку.
Применение: Gоверхность очищается от антиадгезийных слоев, загрязнений, снега и наледи. С металлических поверхностей удаляются следы ржавчины. Любые трещины, сколы устраняются при помощи строительного раствора, острые стыки и углы смягчаются фацетами или закруглениями. Покрытие наносят в 2-3 слоя толщиной по 0,5-0,8 мм каждый. Время высыхания в среднем – 12 часов. Если поверхность слоя не является липкой, он считается высохшим. Спустя 7 суток происходит окончательный набор качеств, однако, чем ниже температура окружающей среды, тем дольше будет сохнуть мастика.
Обзор производителей
Мастика битумно-резиновая AquaMast от Технониколь. Идеально подходит для заделки швов и трещин, образуя после высыхания высокопрочное покрытие с широким температурным диапазоном эксплуатации. Средний расход – 3,3-4,3 кг на м2.
TYTAN битумно-каучуковая мастика на водной основе (Польша). В составе смеси присутствует модифицированный каучук и применяется для ремонта кровельных покрытий из рубероида. Темно-коричневая масса наносится слоем в 1 мм, сохнет в течение 6 часов. В зависимости от применения, необходимо 2-4 слоя. Расход: 0,8-1,2 кг на м2.
Мастика битумная Технониколь №21. Отличается особой прочностью и высокими эксплуатационными характеристиками. Применяется для устройства плоской кровли, а также антикоррозийной защиты конструкций трубопровода и прочих сооружений.
После окончания работ инструменты очищают растворителем. Если материал успел засохнуть, убрать его можно только механическим способом.
Работая с любым видом битумной мастики, следует соблюдать определенные меры безопасности. Всегда надевайте спецодежду и резиновые перчатки. Если в составе присутствуют растворители, мастика считается пожароопасной. Вблизи нее нельзя курить и использовать открытый огонь. При попадании на кожу ее смывают сначала растворителем, а после – водой с мылом.
Кровельная битумная мастика. Видео
« Многолетние лианы для сада: виды, посадка и уход Настурция: выращивание из семян »
Мастика битумная: область применения, расход, характеристики, разновидности
Мастика — материал для заполнения трещин и гидроизоляции поверхностей, получаемый путем смешения различных компонентов. Целью обработки является создание водонепроницаемого слоя или стыка элементов. После нанесения покрытие затвердевает за счет испарения разбавителя или в результате взаимодействия его компонентов. Расход битумной мастики на 1 м² гидроизоляции необходимо знать для каждого применения, чтобы правильно рассчитать объем на закупку.
Содержание
- Что представляет собой битуминочная мастика
- свойства
- Применение
- Разнообразие битуминовой мастики
- Как определить расходы
- Скорость потребления для различных методов нанесения
- Рассчет для водонепроницаемой.
- Технология нанесения
Что такое битумная мастика
Состав используется для получения бесшовного гидроизоляционного слоя при ремонте или устройстве новой кровли … Материал нашел применение при строительстве дорог.
Смесь для производства включает Компоненты:
- вяжущее на основе битумной смолы;
- частицы гранул каучука;
- полимерные добавки;
- синтетические масла;
- антисептики, гербициды;
- наполнители из мела, песка, гипса, извести и других материалов.
Мастика выпускается в форме однородная пластичная масса с синтетическими или органическими наполнителями. Смесь модифицирована добавками, поэтому современный вариант изоляционной мастики отличается хорошими эксплуатационными характеристиками и улучшенными техническими характеристиками.
Мастика битумная для гидроизоляции наносится на ржавый металл на влажную плоскость кровли.
Качественная смесь быстро схватывается, сохнет, а в ее составе присутствуют армирующие нити для компенсации колебаний кровельного или дорожного основания.
Свойства
Основным свойством битумной мастики является водостойкость.Битумная гидроизоляция – часто применяемая технология, эффективно справляющаяся с задачей защиты от влаги, при этом не требующая больших затрат на обустройство.
Характеристики смеси Наборы битумов:
- отличная адгезия к бетону, дереву, металлу , прочное соединение с керамикой, пеноблоками, прочность сцепления 0,2 – 1,5 МПа;
- полная водонепроницаемость за счет плотной (непористой) структуры;
- при динамических нагрузках материал проявляет гибкость, не разрушается при сжатии и расширении зазора между кровельными листами;
- Срок службы без ремонта зависит от условий эксплуатации и составляет от 5 до 25 лет.
Действующее Сохранение гибкости слоя на морозе … Такие усилия расцениваются как предел прочности при низких температурах. Параметр теста указывает на степень эластичности при граничном охлаждении, утверждает нижний показатель рабочего диапазона.
Применение
Жидкая масса наносится на плоскость, где затвердевает, образует изолирующую прочную пленку без стыков. Это качество незаменимо при устройстве кровли , защищает конструкции от снега, дождя, солнца.
Другие варианты использования материал:
- при устройстве дорожных покрытий в качестве гидроизоляции;
- для паро- и влагоизоляции ленточных фундаментов, свай, столбов, ростверков, фундаментных балок;
- в качестве гидроизоляционного слоя на межэтажных перекрытиях, особенно в зоне расположения санузлов и кухонь;
- при утеплении стен ванной, других влажных помещений;
- при строительстве бассейнов, водоемов, различных тоннелей, наружных трубопроводов;
- внутри подвала для гидроизоляции стен от грунтовой влаги, под стяжку пола.
Материал можно отнести к универсальному типу. Используется в местах, где затруднительно нанесение клейкой пленки из-за сложной формы конструкций. Горячая битумная кровельная мастика – это материал, который можно наносить на криволинейные и сложные поверхности.
Абсолютная водонепроницаемость
Хорошая адгезия к строительным материалам, прочность сцепления
Низкая стоимость
Экономный расход при соблюдении технологии
Гладкая поверхность под верхний слой кровли
Универсальность применения
Краско-безусадочный слой
Растрескивание со временем, усыхание, ломкость
Плохо устойчив к солнечным лучам (при использовании в качестве финишного покрытия)
Для проходимых кровель требуются марки с высокой прочностью на сжатие и истирание
Разновидности битумных мастик
По составу сырья гидроизоляционные битумные мастики делятся на виды: эмульсионные, каучуковые, полимерные и составные без добавок . .. По замораживанию различают отверждаемые и неотверждаемые мастики. Также материал делится в зависимости от цели использования: для кровли, дорожного полотна, утепления.
Послойным методом наложения виды долей:
- холодная мастика на основе растворителя;
- битум холодный, разбавленный водой;
- битумно-полимерный;
- битумно-каучуковый;
- битумная гидроизоляция.
Холодная мастика на растворителе включает модификаторы, органический растворитель (до 80%) и наполнители. Смесь не нагревается перед работой; для прокатки используются валики, кисти, шпатели. Процесс подачи заявки проходит быстрее.
Холодные мастики на воде состоят из водной эмульсии смолы, наполнителей, эмульгаторов, полимеров и технологических добавок. В составе около 20 – 70% нефтепродуктов. В результате получается нетоксичное, пожаробезопасное покрытие. Эту мастику можно использовать в жилых домах, помещениях.
Мастика гидроизоляционная отличается тем, что со временем из массы удаляются летучие компоненты, поэтому появляется хрупкость, особенно зимой.
Резина битумная материалы содержат в структуре крошку смолы, что придает массе улучшенные качества в виде повышенной гибкости, растяжимости, устойчивости к внешним воздействиям.
Введение полимеров также повышает эластичность, устойчивость к температурным перепадам, химическую и термическую стойкость. Иметь полимерно-битумный компаундов повышена устойчивость к деформациям, материал имеет наибольший срок службы.
Как определить расход
На расход влияет толщина слоя и количество сухого остатка. Мастика характеризуется показателем сухого остатка . Означает объем вещества на плоскости после высыхания и затвердевания мастики. Показатель выражается в процентах от общего расхода используемого материала. Показатель означает, что небольшой сухой остаток приводит к перерасходу исходной массы для получения слоя необходимой по технологии толщины.
Большинство материалов характеризуется индексом сухого вещества 20 – 70%. Расход материала с высоким процентным содержанием будет в 3 раза меньше для формирования нужной толщины, чем при показателе 20%. Помимо стоимости увеличивается трудоемкость работ.
Чтобы найти расход материала на всю поверхность, необходимо знать:
- нормативную толщину слоя;
- количество сухого остатка после отверждения.
Например, при остатке материала 50% в 1 кг мастики содержится 0,5 кг рабочего вещества и 0,5 кг растворителя. После высыхания на плоскости останется 0,5 кг гидроизоляции при нанесении 1 кг мастики.
После нахождения удельного расхода с учетом остатка после отверждения и толщины покрытия определяют количество слоев на поверхности.
Для гидроизоляции кровли стекловолокном требуется 2-3 слоя основного материала. В этом случае потребуется 3 – 4 слоя битумной мастики толщиной 1,5 – 2 мм.
Расход зависит от плотности массы и температуры раствора.
Нормы расхода при различных способах нанесения
Холодные мастики более удобны в применении, применяются для клеевых прослоек между слоями кровли и в качестве гидроизоляции отдельно стоящих конструкций. Горячие, более стойкие к внешним воздействиям материалы должны быть полностью однородными и распределяться по поверхности слоем не менее 1 мм.
Нормы толщины в зависимости от холодного и горячего способа:
- толщина слоя мастики для материала горячего способа облицовки не менее 2 мм ;
- холодный можно использовать толстый не менее 1 мм .
На один квадрат в один слой расходуется холодный материал в растворителе 1 – 2 кг, битумная холодная мастика на воде – 1,5 – 2 кг, горячая масса пойдет 2 кг. Площадь покрытия умножается на расход мастики, затем умножается на количество слоев.
Расчет на гидроизоляцию фундамента
Для расчета расхода нужно рассчитать площадь фундамента и умножить на толщину слояФундаменты бывают разных типов. Проще всего рассчитать расход для ленты типа . В этом случае находится квадратура всей поверхности, которую требуется покрыть составом.
Порядок определения площади:
- ширину ленты умножить на длину, получить площадь по горизонтали;
- боковая высота умножается на длину ленты, затем на 2 – получается квадратура боковых плоскостей;
- иногда нужно рассчитать площадь торцов;
- для каждой отдельной области, считается площадь, затем добавляются показатели.
Для покрытия фундамента в один слой на квадратный метр используют 1 – 1,5 кг холодной мастики на растворителях, 1 – 1,5 кг холодной мастики на воде, 2 кг горячей мастики.
Полученный квадрат обрабатываемой поверхности умножается на квадрат расхода, затем умножается на количество слоев.
Гидроизоляция фундамента предполагает не менее двух слоев обмазочного состава.
Расчет гидроизоляции кровли
В кровельных работах выполняется не только приклеивание различных слоев стеклоткани, стеклохолста. Гидроизоляционная мастика используется и для полноценного финишного покрытия. При этом последний слой должен быть толщиной не менее 2 мм.
Расход мастичной пасты:
- при укладке холодным способом двумя слоями стеклохолста и тремя слоями мастики общий расход на квадрат составит 3,5 – 6 кг;
- при применении с подогревом общий расход на квадрат кровли при таком же составе будет на уровне 6 кг;
- при заполнении швов между железобетонными плитами перекрытий, то норма расхода принимается из расчета 145 – 157 кг на каждые 100 м шва (при толщине плиты 200 мм).
Площадь кровли рассчитывается, умножается на нормативный расход. Так как максимальный показатель дается сразу для нескольких слоев, дополнительно умножать на количество слоев не нужно.
Технология нанесения
Надежная кровля с битумным гидроизоляционным покрытием содержит в конструкции армирующие слои. По инструкции нужно уложить армирующую сетку. Перед началом работы поверхность очистить, пропитать грунтовкой.
Дальнейший процесс укладки :
- нанести мастику ровным равномерным слоем;
- сверху укладывается слой армирующей мембраны, швы проклеиваются специальной лентой, проклеивается битумом;
- второй слой мембраны монтируется так, чтобы стеклоткань перекрывала соединительную ленту на 20 – 30 см, под вкладыши вкладыша заливается битум.
Мастика битумная холодная или горячая незаменима при точечном или капитальном ремонте кровли . Такой состав наносится на влажную поверхность бетона, плит, дерева – другие материалы не справляются с влагой.
Обычно проблемный участок мягкой кровли срезают крестом в проблемном месте, края загибают. Внутрь наносится мастика в необходимом объеме, затем края снова сводятся к центру, прижимаются. Примените сетку, чтобы сделать заплатку.
Подготовка поверхности важна для равномерного нанесения мастики. Перед работой плоскость желательно выровнять растворами – так удастся избежать перерасхода средств. На этой странице Одним из способов удешевить такую конструкцию и сделать ее более удобной является применение недорогого полимера, например полимера-отхода. Основная цель данного исследования заключалась в изучении влияния добавления отработанной резины шин (модификатора резиновой крошки (CRM)) на жесткость и усталостные свойства смесей щебеночно-мастичных асфальтобетонов (SMA). В смеси СМА добавляли разное процентное содержание отработанного СО размером 0,60 мм. Испытание модуля жесткости на непрямое растяжение проводили при температурах 5, 25 и 40°С. Непрямое испытание на усталость при растяжении проводилось при трех различных уровнях нагрузки (2000, 2500 и 3000 Н). Результаты показывают, что модуль жесткости армированных образцов SMA, содержащих различное содержание CRM, значительно выше по сравнению с неармированными образцами, а модуль жесткости армированных образцов фактически меньше подвержен влиянию повышенной температуры по сравнению с неармированными образцами.
Кроме того, результаты показывают, что смеси SMA, армированные CRM, демонстрируют значительно более высокую усталостную долговечность по сравнению с неармированными смесями, что способствует внедрению и продвижению устойчивых технологий путем переработки отходов более экономичным и экологически безопасным способом.
1. Введение
1.1. Дизайн дорожной смеси
Автодороги считаются одним из важнейших элементов инфраструктуры. Они играют важную роль в нашей повседневной жизни в настоящем и будущем. Таким образом, инженеры по строительству дорог должны учитывать требования основного пользователя в отношении безопасности, а также экономичности. Для достижения этой цели проектировщики дорожного строительства должны учитывать три основных требования, которые включают факторы окружающей среды, транспортный поток и материалы асфальтобетонных смесей.
В асфальтобетоне (AC) битум в качестве вяжущего вещества выполняет две основные функции в дорожном покрытии: во-первых, надежно удерживать заполнители и, во-вторых, действовать как герметик против воды.
Однако из-за некоторых проблем, таких как усталостное разрушение, характеристики и долговечность битума сильно зависят от изменений его характеристик со временем, что может привести к растрескиванию дорожного покрытия [1].
Составление битумной смеси включает в себя подбор и дозировку материалов для получения требуемых свойств в готовом изделии. Асфальтобетон (AC) предназначен для сопротивления колееобразованию, усталости, низким температурам, растрескиванию и другим повреждениям. Серьезными повреждениями, связанными с нежесткими покрытиями, являются растрескивание, возникающее при средних и низких температурах, и остаточная деформация, возникающая при высоких температурах. Эти бедствия сокращают срок службы дорожного покрытия и повышают затраты на техническое обслуживание [2].
Однако динамические свойства и долговечность обычного асфальта недостаточны для сопротивления повреждениям дорожного покрытия. Следовательно, задача современных исследователей асфальта и инженеров состоит в том, чтобы искать различные виды модифицированного полимером битума с реологическими свойствами, которые могли бы непосредственно влиять на характеристики асфальтового покрытия [3].
Из-за увеличения обслуживания, плотности движения, нагрузки на ось и низких затрат на техническое обслуживание дорожные конструкции пришли в негодность и, следовательно, быстрее выходят из строя. Чтобы свести к минимуму повреждения дорожного покрытия, такие как устойчивость к колееобразованию и усталостному растрескиванию, асфальт необходимо модифицировать выбранным полимером [3]. Использование первичных полимеров, таких как стирол-бутадиен-стирол (СБС) и стирол-бутадиеновый каучук (СБК), в конструкции дорожного покрытия увеличит стоимость строительства, поскольку они являются очень дорогими материалами. Однако при использовании альтернативных отходов, таких как модификатор резиновой крошки (CRM), это, безусловно, будет полезно для окружающей среды, и оно не только может улучшить свойства и долговечность битумного вяжущего, но также может быть экономически эффективным [20]. , 23–26].
1.2. Новизна использования отходов полимера
Первичный полимер позволяет производить смеси, устойчивые как к колееобразованию, так и к растрескиванию; однако использование первичного полимера является дорогостоящим.
Таким образом, использование переработанного полимера, такого как резиновая крошка, является хорошей и недорогой альтернативой. Кроме того, считается устойчивой технологией, то есть « озеленение асфальта », которая превращает нежелательные остатки в новую битумную смесь, обладающую высокой устойчивостью к разрушению. Таким образом, использование резиновой крошки, полученной из отходов автомобильных шин, не только выгодно с точки зрения снижения затрат, но и оказывает меньшее воздействие на окружающую среду в плане сохранения чистоты окружающей среды и достижения лучшего баланса природных ресурсов.
Резиновая крошка или отработанная шинная резина представляет собой смесь синтетического каучука, натурального каучука, сажи, антиоксидантов, наполнителей и масел-наполнителей, растворимых в марке для горячего дорожного покрытия. Прорезиненный асфальт получают путем включения резиновой крошки из измельченных шин в битумное вяжущее при определенных условиях времени и температуры с использованием либо сухого процесса (метод, при котором добавляют гранулированный модификатор или модификатор резиновой крошки (CRM) из утильных шин вместо процентного содержания заполнитель в асфальтобетонной смеси, а не в составе асфальтобетонного вяжущего) или мокрые процессы (метод модификации асфальтового вяжущего СО из утильных шин перед добавлением вяжущего для образования асфальтобетонной смеси).
Существует два достаточно разных метода использования шинной резины в битумных вяжущих: первый — растворение резиновой крошки в битуме в качестве модификатора вяжущего, второй — замена части мелких заполнителей молотым каучуком, который не полностью реагирует с битумом [4]. ].
Основной характеристикой резины является ее свойство высокой эластичности, позволяющей ей подвергаться большим деформациям, от которых достигается практически полное мгновенное восстановление при снятии нагрузки [5]. Это свойство высокой эластичности обусловлено молекулярной структурой каучука. Каучук относится к классу материалов, известных как полимеры, и его также называют эластомером.
Эластомерный каучук обладает следующими свойствами. (i) Молекулы очень длинные и могут свободно вращаться вокруг связей, соединяющих соседние молекулярные единицы. (ii) Молекулы соединены химически или механически в определенном количестве сайтов для формирования трехмерной сети. Эти соединения называются сшитыми.
(iii) Помимо того, что они сшиты, молекулы могут свободно перемещаться друг относительно друга; то есть силы Ван-дер-Вааля малы.
Подобно битуму, каучук представляет собой термопластичный вязкоупругий материал, деформация которого под нагрузкой связана как с температурой, так и со скоростью деформации. Тем не менее, деформация резины является относительным стимулом к изменению температуры, когда как при низких скоростях деформации, так и при температуре, значительно превышающей температуру окружающей среды, материал остается эластичным. Более широкий диапазон упругих свойств каучука по сравнению с битумом в значительной степени является результатом сшивания длинных молекул каучука. Резина также гораздо более пластична, чем битум, при низких температурах и высоких скоростях нагрузки.
В 1950 году сообщалось об использовании утильных шин в асфальтовом покрытии [6]. В начале 1960-х годов Чарльз Макдональд, работавший главным инженером по материалам в городе Феникс, штат Аризона, обнаружил, что после завершения смешивания резиновой крошки с обычным битумом и выдержки в течение 45–60 минут смешивания были получены новые свойства материала.
При более высоких температурах наблюдалось набухание частиц резины, что позволяло использовать более высокие концентрации жидкого битума в смесях для дорожного покрытия [7]. С тех пор использование резиновой крошки вызвало интерес к модификации дорожного покрытия, поскольку очевидно, что резиновая крошка из резиновой крошки может улучшить эксплуатационные свойства битума [8–11].
1.3. Асфальт с каменной матрицей (SMA)
Асфальт с каменной матрицей (SMA) представляет собой горячую смесь с щелевой градацией, которая завоевала популярность во всем мире. SMA был впервые разработан в Германии в середине 1960-х годов [12] для обеспечения максимальной устойчивости к колееобразованию, вызванному шипованными шинами на дороге. Ранее, в 1990-х годах, технология SMA широко использовалась в США; тем не менее, в отчетах большинства исследователей подчеркивается, что смеси имеют большую вероятность сопротивления колееобразованию, но игнорируется любая потенциальная усталостная устойчивость SMA [13].
В знак признания его превосходных характеристик в 1919 году в Германии был установлен национальный стандарт.84. С тех пор СМА распространилась по всей Европе, Северной Америке и Азиатско-Тихоокеанскому региону. Несколько отдельных стран Европы в настоящее время имеют национальный стандарт на щебеночно-мастичный асфальт, а CEN, европейский орган по стандартизации, находится в процессе разработки европейского стандарта на продукцию. Сегодня SMA широко используется во многих странах мира в качестве верхнего слоя или поверхностного слоя для сопротивления индуцированной нагрузке, и его популярность растет среди дорожных властей и асфальтовой промышленности [14]. Из-за природы смесей SMA (с зазорами) и относительно большой доли битума требуется стабилизация для предотвращения стекания асфальта. Эти требования могут быть достигнуты путем добавления волокна или полимерного модификатора, и, поскольку коммерческий полимер неэкономичен с точки зрения использования, поэтому использование переработанного полимера, такого как CRM, в смесь оказалось более экономичным и безопасным для окружающей среды.
1.4. Асфальт и жесткость
Динамическая жесткость или «модуль упругости» является мерой способности битумных слоев распределять нагрузку; он контролирует уровни деформаций растяжения, вызванных дорожным движением, на нижней стороне самого нижнего битумного связующего слоя, которые ответственны за усталостное растрескивание, а также напряжения и деформации, возникающие в земляном полотне, которые могут привести к пластическим деформациям [15].
Асфальтобетон (AC) должен иметь высокую жесткость, чтобы противостоять остаточной деформации. С другой стороны, смеси должны иметь достаточное растягивающее напряжение в нижней части слоя асфальта, чтобы противостоять усталостному растрескиванию после многих приложений нагрузки. На рис. 1 представлена ориентация главных напряжений относительно положения нагрузки колеса качения.
Для оценки свойств асфальтобетонных смесей использовались различные тесты и подходы. Несколько свойств материала можно получить в результате фундаментальных механических испытаний, которые можно использовать в качестве входных параметров для моделей характеристик асфальтобетона.
Хэдли и др. [17] оценили свойства асфальтобетонных смесей с помощью непрямого испытания на растяжение. Основными аспектами, которые можно охарактеризовать с помощью косвенного испытания на растяжение, являются упруго-упругие свойства, усталостное растрескивание и свойства, связанные с остаточной деформацией. Упругую жесткость асфальтобетонных смесей можно измерить с помощью непрямого испытания на растяжение [2].
1.5. Усталостное растрескивание асфальта
Усталость является одним из наиболее серьезных повреждений конструкции асфальтового покрытия из-за повторяющихся нагрузок интенсивного движения, возникающих при средних и низких температурах. Во всем мире используются различные методы испытаний для измерения сопротивления усталости асфальтобетонных смесей.
В исследовании Афлаки и Мемарзаде [18] изучалось влияние реологических свойств резиновой крошки на усталостное растрескивание при низких и промежуточных температурах с использованием различных методов сдвига.
Результаты показали, что смесь с высоким усилием сдвига оказывает большее влияние на улучшение при низких температурах, чем смесь с низким сдвигом.
Растрескивание обычно считается низкотемпературным явлением, в то время как остаточная деформация считается преобладающим видом разрушения при повышенных температурах. Растрескивание в основном подразделяют на термическое растрескивание и усталостное растрескивание, связанное с нагрузкой. Сильные перепады температуры, происходящие в дорожном покрытии, обычно приводят к термическому растрескиванию. Этот тип разрушения возникает, когда термическое растягивающее напряжение вместе с напряжениями, вызванными движением транспорта, превышает предел прочности материалов на растяжение. Часто характеризуется поперечным растрескиванием вдоль магистрали через определенные промежутки времени. Усталостное растрескивание, связанное с нагрузкой, представляет собой явление разрушения в результате повторяющихся или флуктуирующих напряжений, вызванных транспортной нагрузкой.
Транспортные нагрузки могут вызвать изгиб конструкции дорожного покрытия, при этом максимальная деформация при растяжении возникает в основании битумного слоя. Если эта структура неадекватна заданным условиям нагружения, прочность материалов на растяжение будет превышена, и, вероятно, возникнут трещины, которые проявятся в виде трещин на поверхности дорожного покрытия [14].
Raad и Saboundjian [19] исследовали усталостную долговечность асфальтобетонных смесей, используя испытание на усталость при непрямом растяжении. Во время усталости при непрямом растяжении горизонтальная деформация регистрировалась как функция цикла нагрузки. Образец для испытаний подвергался различным уровням стресса для проведения регрессионного анализа диапазона значений. Это позволило разработать зависимость усталости между количеством циклов при разрушении () и начальной деформацией растяжения () на логарифмической зависимости. Усталостная долговечность () образца – это число циклов до разрушения асфальтобетонных смесей.
Эти модели созданы на основе существующей взаимосвязи между напряжением или деформацией и усталостной долговечностью, представленной в следующих уравнениях: где – количество циклов нагружения до разрушения, – приложенное напряжение, – начальная деформация, , , , – коэффициенты регрессии (параметры усталости), которые связаны со свойствами смеси.
2. Материалы и методы
2.1. Материалы
Для целей исследования использовалось битумное вяжущее марки 80/100 пенетрации. В таблице 1 приведены характеристики битума, использованного в данном исследовании. В целях обеспечения постоянства CRM на протяжении всего исследования использовалась только одна партия резиновой крошки, полученная из одного источника. В данном исследовании для уменьшения сегрегации была выбрана мелкая резиновая крошка (0,6 мм) с удельным весом, эквивалентным 1,161 [3, 20]. Гранитный щебень с заполнителями SMA 20 был доставлен из карьера Kajang (недалеко от Куала-Лумпура, столицы Малайзии) и использовался на протяжении всего исследования.
Градации заполнителя и некоторые физические свойства принятого заполнителя показаны в таблицах 2 и 3 соответственно.
2.2. Изготовление образцов
Образцы были приготовлены при оптимальном содержании асфальта (OAC) с использованием метода Маршалла. Было получено пять различных количеств ОАС для пяти различных содержаний СО: 6,70%, 6,5%, 6,40%, 6,20% и 6,31% ОАС, каждое для 0%, 6%, 12%, 16% и 20% (все по массе частиц заполнителя) содержания СО соответственно.
Для включения каучука в битумную смесь был проведен мокрый процесс. При мокром способе образцы прорезиненного битума готовили путем смешивания CRM с битумом класса пенетрации 80/100 (при скорости вращения 200 об/мин при 180°C и 30 мин) перед смешиванием полученного прорезиненного битума с заполнителем [3]. .
В дальнейшем для приготовления смесей СМА 1100 г заполнителя помещали в печь и нагревали до 160°С в течение 2 часов. Прорезиненный битум, необходимый для образца, одновременно нагревали до температуры 160°С в течение одного часа.
Как только заполнитель и битум достигли необходимой температуры, в заполнители добавляли необходимое количество нагретого прорезиненного битума. Позже битумное вяжущее, модифицированное каучуковой крошкой, и заполнители смешивали вместе (перемешивали вручную) при температуре смешивания 160°C до тех пор, пока заполнитель не был полностью покрыт битумом. Смесь переносили в форму Маршалла. В центр формы помещали термометр из нержавеющей стали, после чего смесь была готова к уплотнению при температуре 160 ± 5°С. Все образцы подвергались уплотнению молотком Маршалла по 50 раз с каждой стороны образца. После завершения уплотнения каждый образец оставляли охлаждаться при комнатной температуре перед экструдированием из формы. Образцы извлекали из пресс-формы Маршалла с помощью гидравлического домкрата и хранили при комнатной температуре для последующего использования для дальнейших испытаний.
2.3. Метод испытаний
2.3.1. Тест на модуль упругости
Динамическая жесткость или «модуль упругости» является мерой способности битумных слоев распределять нагрузку; он контролирует уровни деформаций растяжения, вызванных дорожным движением, на нижней стороне самого нижнего битумного связующего слоя, которые ответственны за усталостное растрескивание, а также напряжения и деформации, возникающие в земляном полотне, которые могут привести к пластическим деформациям [12].
Динамическая жесткость вычисляется с помощью непрямого теста модуля растяжения, который является быстрым и неразрушающим методом.
Это испытание охватывает процедуру испытания восстановленных стержней битумных смесей в лаборатории или на складе для определения значения модуля упругости (MR) с помощью испытания на косвенное растяжение под нагрузкой при определенных условиях температуры, нагрузки и частоты нагрузки. Испытание проводилось путем приложения сжимающих нагрузок заданной синусоидальной формы. Нагрузку прикладывали вертикально в вертикальной плоскости цилиндрического образца битумного образца. Результирующая горизонтальная деформация образца была измерена с предполагаемым коэффициентом Пуассона для расчета значений модуля упругости.
В текущем исследовании параметры испытаний были следующими: (i) температура = 5, 25 и 40°C, (ii) коэффициент Пуассона = 0,34, (iii) усилие = 20 × глубина образца, (iv) подъем время = 70 мс, (v) период импульса = 1 с.
Горизонтальное растягивающее напряжение и модуль жесткости смесей AC могут быть получены следующим образом: где – максимальное горизонтальное растягивающее напряжение в середине образца, – модуль жесткости, – приложенная вертикальная пиковая нагрузка, – амплитуда горизонтальной деформации, – средняя толщина образца, – средний диаметр образца, – коэффициент Пуассона.
. Непрямое испытание на растяжение для определения модуля упругости битума проводили в соответствии со стандартом ASTM D1234 (1987), используя универсальный испытательный прибор для материалов (UMATTA).
2.3.2. Косвенное испытание на усталость при растяжении
Процедура испытания на усталость используется для ранжирования устойчивости битумной смеси к усталости, а также является ориентиром для оценки относительных характеристик смеси асфальтового заполнителя и получения данных и входных данных для оценки поведения конструкции на дороге.
Во время испытания на усталость значение модуля уменьшилось, как показано на рис. 2. Были выделены три фазы. (i) Фаза I: первоначально происходит быстрое уменьшение значения модуля. (ii) Фаза II: изменение модуля приблизительно линейно. (iii) Фаза III: быстрое уменьшение значения модуля.
Повреждение определяется как любая потеря прочности, происходящая в образце во время испытания.
Усталостная долговечность определяется как количество циклов приложения нагрузки (циклов), приводящих либо к разрушению, либо к остаточной вертикальной деформации.
Снижение жесткости на 50% использовалось для представления разрушения образца из-за усталостной деформации.
Горизонтальная деформация растяжения также может быть получена как функция напряжения и жесткости смеси с использованием (3): — максимальное растягивающее напряжение в центре образца, — максимальное растягивающее напряжение в центре образца, — модуль жесткости образца, — коэффициент Пуассона.
Универсальная установка для испытаний материалов (UMATTA) использовалась для определения испытания на непрямое растяжение с повторной нагрузкой в качестве метода оценки сопротивления усталости битумных материалов. В этом исследовании использовались три силы циклической нагрузки (2000, 2500 и 3000 Н) соответственно. Ширина цикла нагружения составляла 100 мс, время повторения цикла нагружения составляло 500 мс, а температура составляла 25°C с осевым смещением около 5-6 мм.
3. Результаты и обсуждение
3.1. Результаты косвенных испытаний на растяжение (модуль жесткости)
Модуль упругости является основной переменной в механистических подходах к проектированию усовершенствованных конструкций дорожных одежд в отношении динамических напряжений и соответствующих деформаций при реакции дорожной одежды [2].
На рис. 3 показано изменение модуля жесткости в зависимости от температуры для образцов армированного SMA асфальта, содержащих разное процентное содержание резиновой крошки, и образцов неармированного SMA. Каждый образец был приготовлен с оптимальным содержанием связующего. Результаты показывают, что при повышении температуры модуль жесткости образцов асфальта снижается. Это происходит из-за изменения вязкости битума в результате повышения температуры, что вызывает проскальзывание частиц в асфальтобетонных смесях. Это впоследствии снижает модуль жесткости как армированных, так и неармированных образцов. Однако по сравнению с неармированными образцами модуль жесткости армированных образцов оказывается повышенным по мере повышения температуры при наличии в образцах SMA асфальта резиновой крошки, которая может противостоять проскальзыванию частиц. Это, в свою очередь, снижает скорость снижения модуля жесткости. Следовательно, показатель модуля жесткости ниже в армированных образцах.
Однако этот положительный эффект ослабляется чрезмерным увеличением CRM, а зазор, образующийся между зернами осыпного материала, вызывает уменьшение модуля жесткости [22].
Результаты IDT (модуль жесткости) свидетельствуют о том, что увеличение содержания CRM приводит к улучшению упругих свойств исследуемых смесей. Модифицированный битум улучшает модуль упругости асфальтобетонных смесей по сравнению с контрольными смесями из-за более высокой вязкости и толстой битумной пленки, что приводит к лучшим свойствам упругости. Таким образом, модифицированный битум позволяет получать асфальтобетонные смеси с повышенной жесткостью и, соответственно, более высокой несущей способностью. Кроме того, связующие, модифицированные резиновой крошкой, показали более низкую чувствительность к температуре. Смеси с модифицированными связующими показали повышенную гибкость при пониженных температурах. Это связано с более низким модулем упругости и более высокой жесткостью, а также пределом прочности при более высоких температурах [2].
3.2. Непрямое испытание на усталость при растяжении (ITFT)
Усталостные характеристики, связанные с накопленной деформацией и числом циклов до разрушения для смесей SMA с армированием CRM и без него, проиллюстрированы в таблице 4 и представлены на рисунках 3, 4 и 5 для различных нагрузок. (2000 с.ш., 2500 с.ш. и 3000 с.ш.). Из рис. 4–6 видно, что добавление связующего CRM в смесь SMA повышает усталостную долговечность и снижает накопленную деформацию. Смесь SMA, армированная 12% CRM, привела к высокой усталостной долговечности и, следовательно, к более низкому значению деформации, как показано в таблице 4. Кроме того, оказалось, что чем выше напряжение, тем ниже усталостная долговечность. При напряжении 2000 и 2500 Н усталостная долговечность увеличилась примерно на 15 %, 29%, 35 % и 49 % с добавкой 6–20 % CRM соответственно, тогда как при напряжении 3000 Н усталостная долговечность увеличивается примерно на 24, 44, 59 и 50 %. Кажется, что смеси SMA имеют более низкую усталостную долговечность при более высоких уровнях напряжения.
Это, вероятно, связано с измельченной резиновой крошкой, которая хорошо распределена в битумной матрице, обладает высоким сопротивлением сдвигу и надежно предотвращает любое перемещение частиц заполнителя, что увеличивает усталостную долговечность за счет эффективного замедления распространения трещины после ее возникновения [1, 2]. .
Чтобы получить представление об усталостной долговечности, уравнение регрессии для каждой смеси вместе с параметрами регрессии для различных значений CRM и напряжения проиллюстрировано в таблицах 5 и 6. Базовая модель усталостной долговечности подтверждает вышеупомянутые эффекты содержания резиновой крошки. и уровни стресса в отношении усталостной долговечности. Посмотрев на коэффициенты модели усталости, можно получить некоторые рекомендации. Как убедительное доказательство, высокие значения разумно указывают на хорошую точность моделей. Это означает, что у смесей, армированных резиновой крошкой, усталостная долговечность выше, чем у исходной смеси (без резиновой крошки).
Полученное соотношение является рациональным в том смысле, что усталостная долговечность снижается по мере увеличения уровня напряжения. Также в таблице 4 показано изменение циклической нагрузки на образцы, содержащие различные проценты модификатора резиновой крошки. Установлено, что по мере увеличения циклов нагружения скорость возникновения деформации растяжения как для армированных, так и для неармированных образцов различна. Модификатор резиновой крошки (CRM) приводит к более высоким напряжениям растяжения в образцах асфальта. Высокая эластичность и прочность на растяжение резиновой крошки позволяют образцам асфальта сдерживать трещины, вызванные ползучестью, а также уменьшать образование и скорость распространения микротрещин. Высокая прочность на растяжение, проявляющаяся в CRM, может сдерживать образование трещин и распространение микротрещин в образцах асфальта [22]. Однако количество циклов до разрушения различно для образцов асфальта, содержащих разное процентное содержание резиновой крошки.
Армированные образцы, как правило, имеют более длительный срок службы по сравнению с неармированными образцами. В таблицах 5 и 6 также представлена модель поведения образцов асфальта, содержащих различное процентное содержание отходов резиновой крошки, и соответствующие коэффициенты корреляции. Отмечено, что отклонение от оптимального содержания СО снижает усталостную долговечность образцов армированного асфальта. Асфальт CRM препятствует легкому образованию растягивающих и вертикальных трещин под действием горизонтальных растягивающих напряжений и останавливает их распространение [2–26].
4. Заключение и рекомендации для будущих исследований
В течение долгого времени потенциал трещин в покрытиях при различных условиях нагрузки и колебаниях температуры был проблемой для целей применения асфальтовых покрытий. Цены на техническое обслуживание и реабилитацию резко возрастают при появлении трещин в асфальтобетонном покрытии [14, 22]. Исследователи предложили два основных решения: во-первых, нанесение более толстого асфальтового покрытия и, во-вторых, производство асфальтовой смеси с измененными характеристиками.
На сегодняшний день было проведено множество экспериментов для исследования влияния армирования CRM на решение проблемы растрескивания асфальтового покрытия. Для целей настоящего исследования было введено и тщательно изучено использование модификатора резиновой крошки (CRM) для армирования асфальтового покрытия.
На основании проведенного исследования можно сделать следующие выводы. (1) Модуль жесткости армированных образцов SMA, содержащих различное содержание CRM, значительно выше по сравнению с неармированными образцами. Однако этот повышенный модуль жесткости не связан с повышенной хрупкостью образцов армированного асфальта. Модуль жесткости армированных образцов на самом деле меньше подвержен влиянию повышенной температуры по сравнению с неармированными образцами. (2) При наличии резиновой крошки усталостная долговечность образцов, армированных CRM, значительно увеличивается. Устойчивость резины отработанных шин к создаваемым горизонтальным растягивающим напряжениям снижает образование вертикальных трещин и предотвращает распространение этих трещин по диаметру образцов асфальта.
Это, в свою очередь, улучшает усталостную долговечность армированных образцов. (3) Полученные зависимости рациональны; чем выше уровень напряжения, тем ниже усталостная долговечность и выше накопленная деформация. (4) Благодаря добавлению CRM наблюдается заметное улучшение усталостной долговечности, которое является более значительным при более высоком уровне напряжения, чем при более низкий уровень стресса. В частности, при интенсивной транспортной нагрузке более заметно усиление битумной смеси, армированной резиновой крошкой, в качестве барьера усталости. образцы. Было очевидно, что высокие значения в разумных пределах свидетельствуют о точности модели. (6) Помимо уменьшения скопления отходов, использование этих отходов улучшило характеристики инженерных конструкций и материалов в производстве асфальта и аналогичных отраслях промышленности. Следовательно, это также сократило затраты на реконструкцию и техническое обслуживание. (7) Поскольку из этого исследовательского проекта были сделаны разные выводы, список рекомендаций для дальнейших исследований в будущем сводится к следующему: (i) использование заполнителя другого типа, градации заполнителя, разных методов смешивания и разных методов уплотнения.
, (ii) выбор различных источников битума с различной степенью проникновения, а также использование другого вида переработанного полимера, такого как использованная пластиковая бутылка, (iii) сравнительная оценка затрат, понесенных на конструкции дорожного покрытия с использованием различного модифицированного асфальта, с теми, которые построены с использованием обычное связующее, (iv) использовать изображения, полученные с помощью сканирующего электронного микроскопа, для оценки адгезии связующего к заполнителю, (v) провести дополнительные исследования усталостных повреждений, включая дополнительные переменные смеси и различные размеры каучука, чтобы оценить влияние размера частиц и текстуры каучука.
Конфликт интересов
Этот документ не имеет конфликта интересов.
Ссылки
A. Mahrez, Свойства прорезиненного битумного вяжущего и его влияние на битумную смесь [M.S. диссертация] , Инженерный факультет, Малайский университет, Куала-Лумпур, Малайзия, 1999.
Ф.К.М. Хамед, Оценка сопротивления усталости модифицированной асфальтобетонной смеси на основе концепции рассеивания энергии [Ph.D. диссертация] , Technische University, Darmstadt, Germany, 2010.
Н. С. Машаан, Влияние модификатора резиновой крошки на свойства и реологическое поведение асфальтового вяжущего [М.С. диссертация] , Инженерный факультет Малайского университета, Куала-Лумпур, Малайзия, 2012 г.
Ю. Хуанг, Р. Н. Берд и О. Хайдрих, «Обзор использования переработанных твердых отходов в асфальтовых покрытиях, Ресурсы, сохранение и переработка , том. 52, нет. 1, стр. 58–73, 2007.
Посмотреть по адресу:
Сайт издателя | Google Scholar
А. Н. С. Бити, «Битум, модифицированный латексом, для повышения сопротивления хрупкому разрушению», Highways and Transportation , vol. 39, нет. 9, pp. 32–41, 1992.
Просмотр по адресу:
Google Scholar
Д.
И. Хэнсон, К. Ю. Фу, Э. Р. Браун и Р. Денсон, «Оценка и характеристика асфальтобетонного покрытия с модифицированной резиной горячей смесью». », Протокол исследования транспорта , нет. 1436, стр. 98–107, 1994.
Посмотреть по адресу:
Google Scholar
Дж. Э. Хаффман, «Концепция асфальто-каучуковых вяжущих Sahuaro», в Proceedings of the 1st Asphalt 90 Rubber User Producer Workshop 90 Rubber User Producer Workshop 90. , Ariz, USA, 1980.
Просмотр по адресу:
Google Scholar
Д. Р. Браун, Д. Джаред, К. Джонс и Д. Уотсон, «Опыт Джорджии с использованием резиновой крошки в горячем асфальте», Отчет об исследованиях транспорта , нет. 1583, стр. 45–51, 1997.
Просмотр по адресу:
Google Scholar
GW Maupin Jr.
, «Применение горячей асфальтобетонной резины в Вирджинии», Transportation Research Record , no. 1530, стр. 18–24, 1996.
Посмотреть по адресу:
Google Scholar
Э. Чарания, Дж. О. Кано и Р. Х. Шнормайер, «Двадцатилетнее исследование асфальтобетонного покрытия в Фениксе, Аризона», Протокол транспортных исследований , том. 1307, стр. 29–38, 1991.
Просмотр по адресу:
Google Scholar
М. Строуп-Гардинер, Б. Чадборн и Д. Э. Ньюкомб, «Бэббит, Миннесота: тематическое исследование предварительно обработанного асфальтобетона, модифицированного резиновой крошкой», Транспорт Протокол исследования , вып. 1530, стр. 34–42, 1996.
Просмотр по адресу:
Google Scholar
Э. Р. Браун и М. Хемант, «Оценка лабораторных свойств смеси SMA», Tech.
Представитель 93-5, Национальный центр технологии асфальта, Обернский университет, 1993.
. Просмотр по адресу:
. 3, нет. 9, pp. 2005–2010, 2006.
Посмотреть по адресу:
Google Scholar
А. Махрез, Свойства и эксплуатационные характеристики щебёночно-мастичных асфальтобетонов, армированных стекловолокном [Ph.D. диссертация] , инженерный факультет Малайского университета, Куала-Лумпур, Малайзия, 2008 г.
C.A. O’Flaherty, Учебник по дорожному строительству , Эдвард Арнольд, Лондон, Великобритания, 3-е издание, 1988 г. диссертация] , Департамент гражданского строительства, Ноттингемский университет, Ноттингем, Великобритания, 1980.
В. Хэдли, В. Хадсон и Т. В. Кеннеди, «Метод оценки свойств материалов при растяжении при непрямом растяжении», Тех. Представитель 41, Центр исследований автомобильных дорог, Остин, Техас, США, 19 лет.
70.
Посмотреть по адресу:
Google Scholar
С. Афлаки и М. Мемарзаде, «Использование двухфакторного дисперсионного анализа и проверки гипотезы при оценке влияния перемешивания модификации резиновой крошки (CRM) на реологические свойства битума», Строительство и строительные материалы , вып. 25, нет. 4, стр. 2094–2106, 2011.
Посмотреть по адресу:
Сайт издателя | Google Scholar
Л. Раад и С. Сабунджян, «Усталостное поведение модифицированных резиной покрытий», Протокол транспортных исследований , №. 1639, стр. 73–82, 1998.
Просмотр по адресу:
Google Scholar
Н. С. Машаан и М. Р. Карим, «Исследование реологических свойств битума, модифицированного резиновой крошкой, и его корреляции с температурной чувствительностью», Materials Research.
, том. 16, нет. 1, стр. 116–127, 2013 г.
Посмотреть по адресу:
Сайт издателя | Google Scholar
М. Кастро и Х. А. Санчес, «Оценка кривых усталости асфальтобетона — подход теории повреждений», Строительство и строительные материалы , том. 22, нет. 6, стр. 1232–1238, 2008.
Посмотреть по адресу:
Сайт издателя | Google Scholar
М. Арабани, С. М. Мирабдолазими и А. Р. Сасани, «Влияние сетки из нитей из отходов шин на динамическое поведение асфальтовых смесей», Construction and Building Materials , vol. 24, нет. 6, стр. 1060–1068, 2010.
Посмотреть по адресу:
Сайт издателя | Google Scholar
Н. С. Машаан, А. Х. Али, М. Р. Карим, М. Абдельазиз, «Влияние концентрации резиновой крошки на физические и реологические свойства прорезиненных битумных вяжущих», Международный журнал физических наук , том.
6, нет. 4, pp. 684–690, 2011.
Просмотр по адресу:
Google Scholar
Н. С. Машаан, А. Х. Али, М. Р. Карим и М. Абдельазиз, «Влияние времени смешивания и содержания резиновой крошки на свойства крошки». битумное вяжущее, модифицированное каучуком», International Journal of Physical Sciences , vol. 6, нет. 9, pp. 2189–2193, 2011.
Просмотр по адресу:
Google Scholar
Н. С. Машаан, А. Х. Али, М. Р. Карим и М. Абдельазиз, «Обзор асфальта, модифицированного резиновой крошкой», Международный журнал физических наук , том. 7, нет. 2, стр. 166–170, 2012 г.
Посмотреть по адресу:
Сайт издателя | Google Scholar
А. Х. Али, Н. С. Машаан и М. Р. Карим, «Исследования физических и реологических свойств состаренного прорезиненного битума», Достижения в области материаловедения и инженерии , том.
2013 г., идентификатор статьи 239036, 7 страниц, 2013 г.
Посмотреть по адресу:
Сайт издателя | Академия Google
Copyright
Copyright © 2013 Nuha Salim Mashaan et al. Это статья с открытым доступом, распространяемая в соответствии с лицензией Creative Commons Attribution License, которая разрешает неограниченное использование, распространение и воспроизведение на любом носителе при условии надлежащего цитирования оригинальной работы.
МБР-75 для гидроизоляции и инструкция по применению Aquamast
При проведении отдельных видов строительно-ремонтных работ конструкция должна быть защищена от влаги. Существует множество материалов, выполняющих эту функцию, в состав которых входит известный многим компонент – битум. Наиболее функциональным и технически обоснованным является использование такого сложного состава, как резино-битумная мастика.
Свойства
Основное назначение мастики – изоляция поверхности, за счет образования на ней эластичной водонепроницаемой пленки, предохраняющей покрываемый ею материал от процессов гниения и коррозии. Компоненты, содержащиеся в резинобитумной мастике, определяют ее свойства и назначение. Основой этого материала чаще всего является нефтяной битум.
Раньше битум очень часто применялся в качестве гидроизоляционного материала для защиты строительных конструкций. Его широкое распространение было оправдано низкой ценой на нефть, ведь битум является продуктом ее переработки. Но со временем защита поверхностей материалом, в состав которого входил только битум, оказалась не очень выгодной, а образовавшийся на поверхности слой не отличался устойчивостью к температурным перепадам. Поэтому производители разработали несколько составов на основе битума.
В связи с различиями в пластичности, температурном режиме работы и надежности образующихся покрытий их разделили на разные виды, в том числе резино-битумные или полимерные мастики.
Современная резино-битумная мастика изготавливается по ГОСТу, где кроме битума присутствуют мелкодисперсный каучук, растворитель и наполнитель.
- Резина и битум являются основными компонентами в составе , определяющими технические характеристики мастики. Благодаря резине покрытие на поверхности не плавится под воздействием высокой температуры, а при низкой в ней не образуются трещины.
- Наполнители придают композиции дополнительную прочность. к воздействию химических веществ и устойчивости к УФ-лучам. В качестве наполнителей могут использоваться такие материалы, как базальтовая вата, известь, асбест, зола, молотый кварц и даже кирпичная пыль.
- Растворитель в составе мастики играет важную роль Именно благодаря ему состав приобретает необходимую консистенцию, а после нанесения слой близок к исходной вязкости.
Скорость испарения зависит от удельного веса растворителя: чем он легче, тем меньше его требуется и тем быстрее он испаряется из состава. Наличие растворителя в составе значительно облегчает способ применения. Холодная мастика не требует предварительного нагрева перед нанесением слоя на поверхность, как при горячем способе, ее нужно только перемешать и добавить немного растворителя с излишней вязкостью.
Назначение
Легко наносимая резино-битумная мастика холодного отверждения может применяться в качестве гидроизоляционного слоя в автомобильной и строительной промышленности. Чаще всего такой состав используется в строительстве; именно в этой сфере он наиболее востребован.
Мастика резинобитумная успешно применяется для гидроизоляции конструкций различного назначения и состоящих из самых разных материалов. Он одинаково хорошо защищает как бетонные элементы фундамента, стен, так и деревянные балки, которые используются в качестве каркасной основы для конструкций.
Кроме того, успешно применяется в качестве антикоррозионной защиты металлических поверхностей, таких как трубопроводы, стальные резервуары различного назначения и другие металлоконструкции.
Отличные гидроизоляционные свойства мастики позволяют использовать состав для ремонта плоской кровли. Кровельная смесь специально разработана для кровли, ее устойчивость к влаге не позволяет образовываться плесени на поверхности, тем самым предотвращая ее преждевременное разрушение.
Герметизирующая функция, присущая резинобитумной смеси, позволяет использовать состав также в качестве заполнителя швов, трещин, сколов и других углублений в строительных материалах без демонтажа старых слоев. Кроме того, его можно использовать для приклеивания различных гидроизоляционных материалов.
Незастывающая мастика применяется для герметизации стыков между оконным или дверным блоком и стеной.
В автомобильной промышленности резинобитумная мастика успешно применяется во многих видах кузовных работ.
Обработка днища и арок автомобиля позволяет повысить их ударопрочность. Но основной функцией мастики по-прежнему является антикоррозийная защита этих наиболее уязвимых для воды мест.
Добавление алюмосиликатов в резинобитумную композицию позволяет повысить звукоизоляционные характеристики автомобиля.
Достоинства и недостатки
Мастика битумно-каучуковая изоляционная, как и любой материал, имеет ряд преимуществ, но имеет и свои недостатки. Рассмотрим достоинства материала.
- Высокая адгезия и вязкость состава. Он одинаково хорошо держится не только на горизонтальных, гладких, но и на вертикальных поверхностях со структурными бороздками. Благодаря сочетанию компонентов, используемых в составе, мастика создает на поверхности литой и достаточно прочный слой, не подверженный воздействию атмосферных осадков, перепадам температуры и развитию колоний плесени.
- Литое покрытие, созданное за счет эластичности состава, позволяет скрыть мелкие изъяны на обрабатываемой поверхности. На нем не видно ни трещин, ни сколов, ни других неровностей, так как пластичный состав хорошо заполняет все бороздки.
- Применение резинобитумной композиции для защиты металлоконструкций от коррозии с экономической точки зрения является очень выгодным вложением средств. Полная замена конструкции обойдется дороже, чем простая обработка мастикой.
- Композиция имеет меньший расход и вес по сравнению с рулонными материалами. Для гидроизоляционных работ достаточно 2-4 кг на 1 м2, для приклеивания материалов потребуется от 1 до 2 кг на 1 м2, а для обустройства кровли нужно от 3,5 до 6 кг на 1 м2.
- Компоненты мастики не относятся к веществам, отрицательно влияющим на здоровье человека, наоборот, состав обладает некоторыми специфическими антибактериальными свойствами, что позволяет использовать его без каких-либо ограничений по месту применения.
Недостатков у состава немного, но они все же присутствуют:
- Битумно-резиновый состав предназначен только для наружных работ.
- Для работы с составом необходимы определенные погодные условия: температура окружающей среды не должна опускаться ниже -5? С, без осадков и ветра.
- При нанесении мастики вручную неравномерное распределение состава.
Производители
Сегодня производством и выпуском резино-битумной мастики занимаются многие предприятия. Наиболее известными фирмами-лидерами, более 20 лет выпускающими наиболее качественный состав резинобитумной мастики, являются четыре: ТехноНИКОЛЬ, Декарт, ХимТоргПроект и Профилюкс.
Отзывы о товарах этих торговых марок исключительно положительные.
- Компания Декарт.
Выпускает резинобитумную композицию холодного отверждения под маркой «Эксперт». Назначение этой мастики – ремонт и устройство кровли, гидроизоляция строительных конструкций, антикоррозионная защита металлических изделий (трубы, днища автомобилей), склеивание рулонных материалов крутки. Композиция расфасована либо в банки по 1,8 кг, либо в ведра по 18 кг.
- Компания “ТехноНИКОЛЬ” . Разработано два вида составов: Аквамаст и ТехноНИКОЛЬ 20. Составы обеих марок можно использовать без предварительной подготовки, при необходимости разбавляя до нужной консистенции растворителем органического происхождения. Применяется для создания гидроизоляционного покрытия конструкций из различных материалов, подходящих для кровли. Мастика Аквамаст – наиболее подходящий состав для кровельных работ. Фасовка осуществляется в ведрах по 3, 10 и 18 кг. Назначение «ТехноНИКОЛЬ 20» – это мастичная гидроизоляция строительных конструкций, зданий и других строительных конструкций.
Фасовка 20 кг (ведра).
- ООО “ХимТоргПроект” . Производит резинобитумную мастику холодного отверждения «Битумаст». Помимо основных компонентов, смесь содержит антисептик и ингибитор коррозии. Не содержит толуола и других токсичных растворителей. Используется в качестве обмазочной гидроизоляции поверхностей из бетона и дерева.
Подходит для защиты от коррозии трубопроводов и металлических емкостей.
Особенности применения
Любая поверхность перед нанесением резино-битумного покрытия должна быть в сухом состоянии, тщательно очищена от крупного и мелкого мусора, плохо прилипших кусков старой отделки. На металлических конструкциях необходимо очистить участки с ржавчиной, удалить песок и пыль с бетонных поверхностей, а минеральные пористые поверхности предварительно обработать грунтом.
Как правило, компания, занимающаяся производством мастики, выпускает грунтовки, прекрасно сочетающиеся с резино-битумными составами.
В подготовительных мероприятиях нуждается не только поверхность конструкции, но и сама резино-битумная композиция. Мастика холодного отверждения, расфасованная в банки, является готовым продуктом и перед применением просто тщательно перемешивается.
Но если загустевает или смесь готовится в два этапа, то необходимо разбавить состав растворителем.
Существуют смеси, которые наносятся на поверхность только горячим способом, для чего мастику нагревают до определенной температуры. В зависимости от температуры, при которой размягчается состав, мастики делятся на марки. Для МБР-65 размягчение состава происходит при нагревании до +65 С, для МБР-75 – до +75 С, а для размягчения мастики МБР-90, его надо будет разогревать до +90 С. работает состав греется до 160-180? С.
Есть инструкция, согласно которой наносить состав нужно слоями.
Если площадь поверхности небольшая, то можно использовать кисть, валик, кисть. Для труднодоступных мест, где необходимо нанести очень тонкий слой состава, лучшим вариантом будет аэрозоль.
Для покрытия больших площадей эффективнее использовать компрессор с распылителем.
Количество слоев зависит от вида работы. Для склеивания материалов достаточно одного слоя, а если состав используется в качестве изоляционного покрытия, то его придется наносить два, а в некоторых случаях и три раза. После нанесения каждого слоя требуется время для высыхания, при температуре +20°С полное отверждение покрытия происходит не ранее, чем через 24 часа.
Работая с мастикой, необходимо соблюдать все меры предосторожности. Это поможет не только избежать травм, но и получить максимально качественный результат.
Подробнее о том, как работать с резино-битумной мастикой, смотрите в следующем видео.
youtube.com/embed/BT5YTdBEWGg” frameborder=”0″ allowfullscreen=””>Оценка характеристик асфальтобетонного покрытия, модифицированного резиновой крошкой и каменной мастикой, в Малайзии Научный исследовательский документ по «Гражданскому строительству»
Hindawi Publishing Corporation Advances in Materials Science and Engineering Volume 2013, ID статьи 304676, 8 страниц http://dx .doi.org/10.1155/2013/304676
Исследовательская статья
Оценка эффективности асфальтобетонного покрытия с модифицированной резиновой крошкой каменно-мастичной мастикой в Малайзии
Нуха Салим Машаан, Асим Х. Али, Сухана Котинг и Мохамед Рехан Карим
Центр транспортных исследований, инженерный факультет, Малайский университет, 50603 Куала-Лумпур, Малайзия Корреспонденцию следует направлять Нуха Салим Машаан; [email protected] Поступила в редакцию 26 мая 2013 г.; Принято 11 июля 2013 г. Научный редактор: Wen-Hua Sun
Copyright © 2013 Nuha Salim Mashaan et al.
Это статья с открытым доступом, распространяемая в соответствии с лицензией Creative Commons Attribution License, которая разрешает неограниченное использование, распространение и воспроизведение на любом носителе при условии надлежащего цитирования оригинальной работы.
Для предотвращения повреждений дорожного покрытия существуют различные решения, такие как применение новых составов смесей или использование добавок к асфальту. Основная цель этого исследования заключалась в изучении влияния добавления резиновой крошки из шин в качестве добавки на эксплуатационные свойства смеси SMA. В этом исследовании изучались основные аспекты модифицированных асфальтовых смесей, чтобы лучше понять влияние модификаторов CRM на объемные, механические и жесткостные свойства смеси SMA. В этом исследовании использовали первичный битум с пенетрацией 80/100, модифицированный резиновой крошкой (CRM) при пяти различных уровнях модификации, а именно, 6%, 12%, 16% и 20%, соответственно, по массе битума.
Было найдено, что подходящее количество добавленного CRM составляет 12% от массы битума. Этот процент обеспечивает максимальный уровень стабильности. Модуль упругости (Mr) модифицированных образцов SMA, включающих различные проценты CRM, был явно выше по сравнению с немодифицированными образцами.
1. Введение
Битум считается термопластичным вязкоупругим клеем и используется для покрытия дорог и автомагистралей, прежде всего, из-за его хорошей вяжущей способности и водонепроницаемости [1]. Сложность химического состава битумных продуктов связана, прежде всего, со сложным составом сырой нефти, из которой получают битумные продукты. Из-за присущих обычному битуму недостатков, которые привели к высокой стоимости обслуживания дорожных систем, возникла необходимость модификации битума. Модификация/армирование битумного вяжущего возможно на разных стадиях его использования, как в промежутке между производством вяжущего и приготовлением смеси, так и перед приготовлением дорожной смеси [2].
Щебеночно-мастичный асфальт (SMA) представляет собой горячую смесь для укладки асфальта, разработанную в Германии в середине 1960-х годов [3] для обеспечения максимальной устойчивости к колееобразованию, вызываемому шипованными шинами на европейских дорогах. В знак признания его превосходных характеристик в 1984 году в Германии был установлен национальный стандарт. Поскольку SMA распространился по всей Европе, Северной Америке и Азиатско-Тихоокеанскому региону, несколько отдельных стран Европы теперь имеют национальный стандарт для щебеночно-мастичных асфальтобетонов,
и CEN. , орган по европейским стандартам, находится в процессе разработки европейского стандарта на продукцию. Сегодня SMA широко используется во многих странах мира в качестве верхнего слоя или слоя покрытия, чтобы выдерживать возникающие нагрузки, и его популярность растет среди дорожных властей и асфальтовой промышленности.
Возросший спрос на шоссейные дороги может снизить их прочностные характеристики и сделать дороги более восприимчивыми к необратимым повреждениям и поломкам.
Как правило, эксплуатационные свойства дорожного покрытия зависят от свойств битумного вяжущего; известно, что обычный битум имеет ограниченный диапазон реологических свойств и прочности, которых недостаточно, чтобы выдерживать повреждения дорожного покрытия. Поэтому исследователи битума и инженеры ищут различные типы модификаторов битума с превосходными реологическими свойствами, которые непосредственно влияют на характеристики асфальтового покрытия. Во всем мире существует множество добавок, используемых в качестве армирующих материалов в битумных смесях, таких как стирол-бутадиен-стирол (SBS), синтетический каучук-стирол-бутадиен (SBR), натуральный каучук, волокно и модификатор резиновой крошки (CRM). Использование коммерческих полимеров, таких как SBS и SBR, в строительстве дорог и тротуаров увеличит стоимость строительства, поскольку они являются очень дорогими материалами. Однако при использовании альтернативных материалов, таких как крошка
модификатор каучука (CRM), он определенно будет экологически выгодным, и он не только может улучшить свойства и долговечность битумного вяжущего, но также может быть экономически выгодным [4].
Резиновая крошка или отработанная шинная резина представляет собой смесь синтетического каучука, натурального каучука, сажи, антиоксидантов, наполнителей и масел-наполнителей, растворимых в марке для горячего дорожного покрытия. Прорезиненный асфальт получают путем включения резиновой крошки из измельченных шин в битумное вяжущее при определенных условиях времени и температуры с использованием либо сухого метода, при котором добавляют гранулированный модификатор или модификатор резиновой крошки (CRM) из утильных шин в качестве заменителя процента заполнителя. в асфальтобетонной смеси, не в составе асфальтобетонного вяжущего, либо мокрыми способами (метод модифицирования асфальтобетонного вяжущего СО из утильных покрышек перед добавлением вяжущего для формирования асфальтобетонной смеси). Существует два довольно разных метода использования шинной резины в битумных вяжущих: во-первых, путем растворения резиновой крошки в битуме в качестве модификатора вяжущего, во-вторых, путем замены части мелких заполнителей молотым каучуком, который не полностью реагирует с битумом [5].
В 1840-х годах самые ранние эксперименты включали в себя добавление натурального каучука в асфальтовое вяжущее для улучшения его технических характеристик. Процесс модификации асфальта с использованием натурального и синтетического каучука был внедрен еще в 1843 г. [6]. В 1923, модификации натурального и синтетического каучука в битуме получили дальнейшее усовершенствование [7, 8]. По словам Йилдрима [8], разработка резино-битумных материалов для использования в качестве герметиков, заплат и мембран началась в конце 1930-х годов. Первая попытка модифицировать битумные вяжущие добавлением каучука была предпринята в 1898 г. Гаудмбергом, который запатентовал процесс производства каучукового битума. Затем Франция получила кредит на установку первой дороги с прорезиненным битумным покрытием [9]. Применение модифицированного резиной асфальтового покрытия началось на Аляске в 19 г.79. Сообщалось о укладке семи прорезиненных покрытий общей протяженностью 4 км с использованием сухого процесса Plus Ride в период с 1979 по 1981 год.
Были описаны характеристики этих секций в отношении смешивания, уплотнения, долговечности, усталости, устойчивости и текучести, а также сцепления шин и сопротивления скольжению. Прорезиненный битум мокрым способом впервые был применен на Аляске в 1988 г. [10]. Ланди и др. (1993) [11] представили три тематических исследования с использованием резиновой крошки как мокрым, так и сухим способом в Mt St. Helens Project, Oregon Dot и Portland Oregon. Результаты показали, что даже после десятилетней службы изделия из резиновой крошки обладают отличной стойкостью к термическому растрескиванию. Хотя резино-битумные смеси можно успешно производить, для обеспечения хороших характеристик необходимо поддерживать контроль качества.
Ассоциация резиновых дорожных покрытий обнаружила, что использование резины для шин в связующей смеси открытого типа может снизить шум от шин примерно на 50%. Кроме того, при распылении частицы резины разных размеров лучше поглощают звук [12]. Кроме того, еще одним преимуществом использования битумной резины является увеличение срока службы дорожного покрытия.
Однако были даны рекомендации по оценке экономической эффективности битумной резины [5].
В Малайзии использование резиновой крошки в качестве добавки для дорожного покрытия предположительно началось в 1940s,
, но никаких официальных записей о такой практике не было. О первом зарегистрированном испытании с использованием технологии прорезиненного битума было сообщено в 1988 году, и процесс мокрой смеси использовался со смесью каучуковых добавок в форме латекса с битумным вяжущим [13]. В 1993 году в Негери-Сембилан было проведено еще одно дорожное испытание прорезиненной ткани с использованием использованных перчаток и натурального каучукового латекса [14]. Кроме того, в Малайзии производится около 10 млн. штук шин в год, и, к сожалению, они утилизируются неэкологичным образом. Чтобы свести к минимуму повреждения дорожного покрытия, такие как устойчивость к колееобразованию и усталостному растрескиванию, асфальт необходимо модифицировать выбранным полимером, таким как модификатор резиновой крошки (CRM), и это, безусловно, будет полезно для окружающей среды, а также улучшит свойства битума, долговечность и снижает стоимость реабилитации [15-19].
Постановка задачи и цель исследования: первичный битум класса пенетрации 80/100 обычно используется в Малайзии, и, кроме того, он подвергается высокой транспортной нагрузке и жарким погодным условиям. Погодные условия в Малайзии приводят к колебаниям температуры примерно от 55°C на поверхности до 25°C на грунтовом основании в жаркие дни. Из-за увеличения плотности служебного движения, нагрузки на ось и низких затрат на техническое обслуживание дорожные конструкции пришли в негодность и, следовательно, быстрее выходят из строя. Основная цель этого исследования заключалась в изучении влияния добавления резиновой крошки из шин в качестве добавки на эксплуатационные свойства смеси SMA. В этом исследовании изучались основные аспекты модифицированных асфальтовых смесей, чтобы лучше понять влияние модификаторов CRM на объемные, механические, а также на жесткостные свойства сопротивления смеси SMA.
2. Материалы и методы
Экспериментальная программа данного исследования направлена на изучение влияния CRM на реологические характеристики прорезиненного битума и механические свойства прорезиненных смесей SMA.
2.1. Материалы. Использовался битум со степенью пенетрации 80/100 и средней температурой размягчения 47°С. Таблицы 1 и 2 иллюстрируют некоторые физические свойства и химический состав битума соответственно. В данном исследовании градации резиновой крошки нет. 40 (0,45 мм). Плотность резиновой крошки составляет около 1,15 (г/см3). Модификатор резиновой крошки (CRM), полученный путем механического измельчения при температуре окружающей среды, был получен от Rubberplas Sdn. Bhd. (малайзийский поставщик). Химические компоненты СО представлены в табл. 3.
Гранитный щебень с заполнителями SMA 14, доставленный из карьера Каджанг (недалеко от Куала-Лумпура, столицы Малайзии), использовался на протяжении всего исследования. Градация принятого заполнителя соответствует стандарту JKR Malaysia [20], как показано в Таблице 4.
2.2. Подготовка образцов и метод испытаний. Метод расчета Маршалла применялся для модифицированных и немодифицированных асфальтобетонных смесей. Для включения каучука в битумную смесь,
Достижения в области материаловедения и инженерии Таблица 1: Физические свойства битума.
Испытание на битум Стандартные методы испытаний на качество битума
80/100
Вязкость при 135°C (мПас) 306,7 ASTM D4402
Пластичность при 25°C >100 ASTM D113
7 73Температура размягчения
Пенетрация при 25°C 88 ASTM D5
Удельный вес при 25°C 1,02 ASTM D70
Температура вспышки при °C 305 ASTM D92
Таблица 2: Химический состав битума (%).
Битум 80/100
Насыщенный 5,4
Ароматические 72,5
Смола 15,5
Асфальтены 6,6
Таблица 3: Химические компоненты CRM №. 40 [9].
Химические компоненты Результат испытаний
Экстракт ацетона (%) 23,1
Углеводород каучука (%) 46,6
Содержание сажи (%) 25,08
Содержание натурального каучука (%) 43,85
Зольность (%) 0,2 Размер частиц 425
Таблица 4: Градация заполнителя SMA 14 [20].
„ в. % прохождения через сито B.S. % остаточной массы (г)
Мин. Максимум.
12,5 100 100 100 0 0
9,5 72 83 77,5 22,5 247,5
4,75 25 33 31,5 46 506
2,36 16 24 20 11,5 126,5
0,6 12 16 66 66
0,3 15 13,5 0,5 5,5 5,5
9000 3 9000 3 9000 3 9000 3 9000 3 9000 3 9000 3 9000 3 9000 3 9000 3 9000 3 9000 3 9000 3 9000 3 9000 3 9000 3 9000 3 9000 3 9000 3 9000 3 9000 3 9000 2 9000 3 9000 3 9000 3 9000 3 9000 3 9000 3 9000 3 9000 2 9000.0,075 8 10 9 4,5 49,5
Чаша 0 0 0 9 99
100 1100
был проведен сухой процесс. В сухом процессе добавка (CRM) смешивается с заполнителем перед добавлением связующего в смесь. Содержание связующего, использованное в этом исследовании, составляет 5%, 5,5%, 6%, 6,5% и 7% по весу от общей массы смеси. Модификатор резиновой крошки добавляют в смесь в различных концентрациях 6%, 12%, 16% и 20% от массы вяжущего. В текущем исследовании использовался 5% наполнитель. Для приготовления смесей СМА 1100 г смешанного заполнителя помещали в печь при 160°С на 2 часа. Битум также нагревали до 120°C перед смешиванием с частицами заполнителя. При сухом способе модификатор резиновой крошки добавляли непосредственно в смесь. Температуру смешения поддерживали постоянной при температуре от 160 до 165°С. Смесь перелили в Marshall 9.0003
Таблица 5: Результаты стабильности (кН) для различного содержания CRM.
Содержание связующего
5% 5,5% 6% 6,5% 7%
CR 0% 11,99 13,10 12,5 11,40 10,8
CR 6% 11,50 12,90 11,9 10,89 10,7
CR 12% 10,55 11,80 11,4 10,90 9,8
CR 12% 10,55 11,80 11,4 10,90 9,8
CR 12% 10,55 11,80 11,4 10,90 9,8
CR % 10.
40 10,40 11,99 9,4 9,4
CR 20% 8,9 9,30 10,89 9,7 8,3
5 5,50 6 6,50 7
Содержание связующего (%)
■ CR 0% ■ CR 16%
■ CR 6% ■ CR 20%
■ ПО 12%
Рисунок 1: Результаты стабильности в зависимости от содержания связующего.
форма. В центр формы помещали термометр из нержавеющей стали, после чего смесь была готова к уплотнению при температуре 160 ± 5°С. Все образцы были подвергнуты 50 ударам пресса молотком Маршалла с каждой стороны образца при температуре 145°С. Лабораторные испытания, использованные для исследования и оценки эксплуатационных свойств битумной смеси SMA, модифицированной образцами CRM, представляли собой Стандартный метод испытаний на сопротивление пластическому течению битумных материалов с использованием аппарата Маршалла [21] и Стандартный метод испытаний на косвенное испытание битумных смесей на прочность при растяжении [21]. 22].
3. Результаты и обсуждение
3.1. Результаты теста Маршалла
3.
1.1. Стабильность Маршалла. Результаты, полученные для различных содержаний CRM для каждого содержания связующего, показаны в таблице 5 и проиллюстрированы на рисунках 1 и 2.
Стабильность по Маршаллу относится к максимальному сопротивлению нагрузке, увеличенному во время процедуры испытания при 60°C при степени нагружения 50,8. мм/мин до разрушения уплотненного образца. Стабильность по Маршаллу определяется «как мера склонности битумной смеси к деформациям, обеспечиваемая частыми и интенсивными транспортными нагрузками».
На рисунках 1 и 2 показаны значения стабильности по Маршаллу в зависимости от содержания CRM для различного содержания связующего. На диаграммах показаны значения стабильности для различного содержания связующего
14 13 12
CRM (%)
6,50% 7%
Рисунок 2: Результаты стабильности в зависимости от содержания CRM.
Таблица 6: Результаты потока (мм) для различного содержания CRM.
Содержание связующего
5 % 5,5 % 6 % 6,5 % 7 %
CR 0 % 3,0 3,2 3,5 4 4,4
CR 6 % 3,4 3,4 3,7 4,7 5,6
CR 12% 3,5 4,1 4,1 4,4 5,2
CR 16% 2,4 3,2 3 3,6 4,4
CR 20% 2,2 2,3 2,5 2,8 3,3
с различным содержанием СО После добавления CRM значение стабильности повышалось до максимального уровня, который составлял примерно 12% от используемого CRM, но затем оно начало снижаться.
По сравнению с контрольной смесью (смесь с 0% CRM) значения стабильности по Маршаллу в целом были выше. Тем не менее, дальнейшее введение битума в смесь приводило к снижению значения стабильности, поскольку внесение избыточного количества битума снижает точку контакта крупного заполнителя в смеси. Единственной смесью с более низким значением стабильности была смесь с 20% CRM. Стабильность улучшается за счет добавления вяжущих материалов CRM в асфальтобетонную смесь, так как улучшается сцепление между материалами в смеси [9]., 23].
3.1.2. Маршалл Флоу. Под текучестью можно понимать измерение остаточной деформации, которая имеет место в испытании Маршалла при разрушении. Это показало, что параметр текучести, полученный в результате теста Маршалла, является довольно неудачным, поскольку более высокое значение текучести не обязательно подразумевает более высокую склонность к течению или деформации под нагрузкой [23]. Результаты, полученные для различных содержаний CRM для каждого содержания связующего, показаны в таблице 6 и проиллюстрированы на рисунках 3 и 4.
На рисунке 3 показано значение потока Маршалла в зависимости от содержания связующего для каждого содержания CRM. Результаты показали, что величина текучести увеличивается с увеличением содержания битума в смеси; то есть значение потока SMA имеет тенденцию к увеличению 9Рис.
6 5,5 5
? Рис.
с более высоким содержанием связующего. Это связано с процентным содержанием дополнительного битума, который позволяет заполнителям плавать в смеси, что приводит к увеличению потока.
В случае зависимости расхода Маршалла от содержания СО (рис. 4) значение расхода ОЗД с СО выше по сравнению с ОЗД без СО. Как показано на рис. 4, присутствие в смеси CRM увеличивает ее текучесть. Кроме того, это показывает, что увеличение содержания СО в смеси СМА не обязательно приводит к увеличению значений текучести. Добавление большего количества СО увеличило поток до оптимального уровня и при дальнейшем добавлении СО в смесь; было замечено явное снижение. Более высокие значения текучести могут быть связаны с увеличением воздушных пустот (требуется большее уплотнение) за счет использования большего количества CRM в смеси, что приводит к более гибкой смеси [9].
, 23].
3.1.3. Плотность уплотняемой смеси (CDM). Полученные результаты показали, что содержание вяжущего влияет на характеристики уплотнения смесей SMA, оказывая, таким образом, значительное влияние на плотность смеси. Таблица 7 и рисунки 5 и 6 показали, что для любого конкретного содержания вяжущего плотность
5 5,50 6 6,50 7
Содержание вяжущего (%)
■ CR 0% ■ CR 16%
■ CR 6% ■ CR 20%
■ CR 12%
Рис. 5: Результаты CDM в зависимости от содержания связующего.
-»- 5% -X- 6,50%
-■- 5,50% –*- 7%
–*- 6%
Рисунок 6: Результаты CDM в сравнении с содержанием CRM.
Таблица 7: Результаты CDM (г/мл) для различного содержания CRM.
Содержание связующего
5% 5,5% 6% 6,5% 7%
CR 0% 2,32 2,33 2,35 2,34 2,35
CR 6% 2,30 2,33 2,33 2,35
CR 12% 2,28 2,30 2,32 2,33
CR 16%. % 2,29 2,29 2,30 2,31 2,32
CR 20% 2,27 2,27 2,29 2,30 2,31
уплотненная смесь постепенно увеличивается по мере увеличения содержания битума в смеси.
Это связано с заполнением битумом пустотного пространства частиц заполнителя.
Результаты показали более низкую плотность смесей с включением резиновой крошки. Оценка результатов по влиянию содержания битума в МЧР (рис. 5) показала, что значение МЧР увеличивается с увеличением содержания битума в смеси СМА. Основной причиной этого является заполнение битумом пустотного пространства частиц заполнителя. Однако после заполнения пустого пространства избыточный процент битума мог привести к значительному увеличению плотности смеси.
Таблица 8: Результаты VIM (%) для различного содержания CRM.
Содержание связующего
5% 5,5% 6% 6,5% 7%
CR 0% 6,24 5,38 4,19 3,36 2,25
CR 6% 7,34 6,37 4,78 4,19 3,45
CR 12% 7,56 6,65 5,28 4,45 3,56
CR 12% 7,56 6,65 5,28 4,45 3,56
CR. % 7,57 6,98 5,43 4,89 3,68
CR 20% 7,83 7,40 5,81 5,10 3,96
Рисунок 6 показал, что при любом содержании связующего плотность уменьшалась по мере увеличения резиновой крошки в смесях SMA.
Увеличение содержания CRM подразумевает увеличение количества битума, поглощаемого CRM, что приводит к увеличению пустот с частицами заполнителя, что приводит к снижению плотности смеси. Разная плотность смесей объясняется влиянием вязкости на совместимость смесей. Повышение вязкости может быть результатом количества асфальтенов в битуме, что улучшает вязкотекучесть образца модифицированного битума в процессе взаимодействия. Более высокая вязкость полученного вяжущего обеспечивала лучшую стойкость при уплотнении смеси, что приводило к меньшей плотности модифицированной смеси. Это согласуется с предыдущим выводом Mahrez [23], который показал, что для идеальной дорожной смеси требуется хорошая корреляция между вязкостью вяжущего и усилием уплотнения.
3.1.4. Пустоты в смеси (VIM). Долговечность битумного покрытия зависит от пустот смеси (VIM) или пористости. Как правило, чем ниже пористость, тем менее проницаема смесь, и наоборот. Слишком большое количество пустот в смеси (высокая пористость) создаст проходы через смесь для проникновения вредного воздуха и воды.
Слишком низкая пористость может привести к вымыванию, когда излишки битума выдавливаются из смеси на поверхность. Влияние содержания CRM при различном содержании вяжущего на пористость исходной смеси и смеси SMA показано в таблице 8 и на рисунках 7 и 8.
На рисунках 7 и 8 видно, что при любом содержании вяжущего увеличение содержания СО в смеси сопровождается увеличением ВИМ, что обусловлено точкой контакта между заполнителями, которая ниже при содержании СО вырос. Большое количество частиц резиновой крошки поглощает связующее, необходимое для инкапсулирования заполнителя и последующего заполнения пустот между заполнителями. Высокая пористость битумной смеси означает наличие большого количества пустот, обеспечивающих проход через смесь воздуха и воды, вызывающих повреждение. С другой стороны, при низкой пористости происходит промывка водой, при которой битум выдавливается из смеси на поверхность [23]. Однако результаты рисунка 7, касающиеся влияния битума, показывают, что любое увеличение содержания битума в смеси приводит к снижению значения VIM, что происходит из-за избыточного заполнения битумом воздушного кармана между заполнителями [24].
. Поэтому очень важно производить смесь с достаточно низким содержанием пустот, чтобы быть непроницаемой и, следовательно, прочной, но с достаточным количеством пустот, чтобы предотвратить деформацию битума.
CR 0% CR 6% CR 12%
5,50 6 6,50
Содержание связующего (%)
■ CR 16% I CR 20%
Рисунок 7: Результаты VIM в зависимости от содержания связующего.
12 CRM
6,50% 7%
5000 4500 -4000 -3500 -3000 -2500 2000 1500 1000 500
CRM 0% CRM 6% CRM 12%
5,50 6,00 6,50
Содержание связующей
■ CRM 16%
■ CRM 20%
Рисунок 9: Модуль упругости в зависимости от содержания битума.
5500 5000 § 4500 4000
S 3500 ten
5 3000 2500 2000
Рисунок 8: Результаты VIM в сравнении с содержанием CRM.
6% 12% 16% CRM (%) по массе вяжущего
AC 5% AC 6,5%
-■- AC 5,5% AC 7%
—A— AC 6%
Рисунок 10: Модуль упругости в зависимости от CRM-контент.
3.2. Результаты косвенных испытаний на растяжение (модуль жесткости). Для определения модуля жесткости проводили измерение модуля упругости образцов в соответствии с [22] при 25°С. . Эти трещины были перпендикулярны направлению максимального растягивающего напряжения; объединение этих микротрещин за счет увеличения деформации приводит к образованию макротрещин. В тандеме с исследованиями эти трещины привели к зоне разрушения в образце. Длина этой зоны разрушения может рассматриваться как параметр материала и может быть истолкована как результат энергии разрушения материала. Температура и процентное содержание битума являются двумя основными параметрами, которые существенно влияют на характеристики асфальта.
Таблица 9 и рисунки 9 и 10 показывают изменение модуля жесткости (Mr) в зависимости от содержания битума для асфальтовых смесей
Таблица 9: Результаты модуля жесткости (МПа) для различного содержания CRM.
Содержание связующего
5% 5,5% 6% 6,5% 7%
CR 0% 3850 3160 4400 3200 3270
CR 6% 3900 3550 4530 3320 3
Cr 12% 4384 4200 4740 4130 43709
CR % 4470 4310 4870 4510 4489
ПО 20% 4570 4410 4990 4810 4600
армированный с разным содержанием СКМ и неармированная асфальтобетонная смесь (содержащая 0% СКМ).
Как показано на рисунках 9 и 10, существует заметная разница между армированными и неармированными образцами по модулю жесткости (Mr). Повышенное содержание битума оказывает значительное влияние на модуль жесткости образцов с различным содержанием CRM из-за того, что оптимальное процентное содержание битума ниже в неармированных образцах. В образцах армированного асфальта с CRM резиновая крошка поглощает часть битума, что приводит к увеличению оптимального процента вяжущего. По мере увеличения содержания резиновой крошки поглощается больше битума, что, в свою очередь, увеличивает оптимальное содержание вяжущего в смеси. Видно, что модуль жесткости армированных образцов асфальтобетона выше по сравнению с неармированными образцами.
Смеси с более высокой жесткостью предполагают, что они не только более жесткие, но и более устойчивы к деформации. Однако следует соблюдать осторожность со смесями с очень высокой жесткостью из-за их более низкой способности к деформации при растяжении до разрушения; то есть такие смеси с большей вероятностью разрушатся из-за растрескивания, особенно при укладке на фундаменты, которые не могут обеспечить достаточную поддержку [23].
4. Заключение и рекомендации для будущих исследований
На основании проведенного исследования можно сделать следующие выводы.
(1) Стабильность улучшается за счет добавления вяжущего CRM в асфальтобетонную смесь, поскольку улучшается адгезия. По сравнению с контрольной смесью (смесь с 0% CRM) значения стабильности по Маршаллу в целом были выше.
(2) Независимо от количества введенного СО, добавление СО в смесь увеличивает ВИМ смеси при снижении ее плотности.
(3) Модуль жесткости образцов СПФ с различным содержанием СО значительно выше по сравнению с неармированными образцами.
(4) Установлено, что соответствующее количество добавляемого CRM составляет 12% по массе битума. Этот процент приводит к максимальному уровню стабильности и VIM.
(5) Объемные характеристики и свойства Маршалла смеси CRM-SMA демонстрируют приемлемые тенденции и могут удовлетворять требованиям стандарта.
(6) Для дальнейших исследований рекомендуется использование различных типов заполнителей, градаций заполнителей, различных методов смешивания и различных методов уплотнения.
Ссылки
[1] SJ Rozeveld, E. Shin, A. Bhurke, L. France, and L. Drzal, «Сетевая морфология прямых и модифицированных полимерами асфальтовых цементов», Исследования и техника микроскопии, том. 38, нет. 5, стр. 529-543, 1997.
[2] R. Richard и T. Bent, Road Engineering for Development, Spon Press, London, UK, 2nd edition, 2004. , “Отчет NCATR № 93-5, Национальный центр технологии асфальта, Обернский университет, 1993.
[4] Машаан Н.С. Влияние модификатора резиновой крошки на свойства и реологическое поведение битумного вяжущего [М.С. диссертация], Малайский университет, Куала-Лумпур, Малайзия, 2012.
[5] Ю. Хуанг, Р. Н. Берд и О. Хайдрих, «Обзор использования переработанных твердых отходов в асфальтовых покрытиях», Ресурсы, сохранение и переработка, том. 52, нет. 1, pp. 58-73, 2007.
[6] D.C. Thompson and A.J. Hoiberg, Eds., Bituminous Materials: Asphalt Tars and Pitches, Krieger Publishing, New York, NY, USA, 19.79.
[7] U. Isacsson и X.
Lu, “Характеристика битумов, модифицированных полимерами SEBS, EVA и EBA”, Journal of Materials Science, vol. 34, нет. 15, стр. 3737-3745, 1999.
[8] Ю. Йылдырым, “Полимерно-модифицированные битумные вяжущие”, Строительство и строительные материалы, т. 1, с. 21, нет. 1, pp. 66-72, 2007.
[9] Марез А. Свойства прорезиненного битумного вяжущего и его влияние на битумную смесь [М.С. диссертация], инженерный факультет, Малайский университет, Куала-Лумпур, Малайзия, 1999.
[10] Л. Раад и С. Сабунджян, «Усталостное поведение резиновых покрытий», Протокол транспортных исследований, №. 1639, стр. 73-82, 1998.
[11] Дж. Р. Ланди, Р. Г. Хикс и Х. Чжоу, «Грунтовые резиновые шины в асфальтобетонных смесях – три истории болезни», Специальная техническая публикация ASTM, STP1193, стр. 262-275, 1993.
[12] Х. Чжу и Д. Д. Карлсон, «Технология распыления резиновой крошки для снижения шума на шоссе», Журнал технологии и управления твердыми отходами, том. 27, нет. 1, стр.
2733, 2001.
[13] З. Суфьян и М. С. Мустафа, «Перспективы прорезиненного битумного покрытия дорог и автомагистралей Малайзии», в материалах конференции по использованию прорезиненного битума в дорожном строительстве, 1997.
[14] А. Самсури , С. Хасшим, М. Х. Харун и А. Л. М. Дева, «Прорезиненный битум для дорожного строительства», в материалах Международной конференции по использованию каучука в инженерных технологиях, Куала-Лумпур, Малайзия, 1995.
[15] Н. С. Машаан , Али А.Х., Карим М.Р. и Абдельазиз М., «Влияние концентрации резиновой крошки на физические и реологические свойства прорезиненных битумных вяжущих», Международный журнал физических наук, том. 6, нет. 4, стр. 684-69.0, 2011.
[16] Н. С. Машаан, А. Х. Али, М. Р. Карим и М. Абдельазиз, «Влияние времени смешивания и содержания резиновой крошки на свойства битумного вяжущего, модифицированного резиновой крошкой», Международный журнал физических наук, том. 6, нет. 9, стр. 2189-2193, 2011.
.
7, нет. 2, pp. 166-170, 2012.
[18] Н. С. Машаан и М. Р. Карим, «Исследование реологических свойств битума, модифицированного резиновой крошкой, и его корреляции с температурной чувствительностью», Материалы. 16, нет. 1, стр. 116-127, 2013.
[19] А. Х. Али, Н. С. Машаан и М. Р. Карим, «Исследования физических и реологических свойств состаренного прорезиненного битума», Достижения в области материаловедения и инженерии, том. 2013 г., ID статьи 239036, 7 страниц, 2013 г.
[20] Jabatan Kerja Raya Malaysia (JKR), Стандартные технические условия для дорожных работ, Jabatan Kerja Raya Malaysia, Куала-Лумпур, Малайзия, 2007 г.
[21] ASTM D1559- 89, «Стандартный метод испытаний на сопротивление пластическому течению битумных смесей с использованием аппарата Маршалла», 1992.
[22] ASTM D, 4123-82, «Стандартный метод испытаний на непрямое растяжение модуля упругости битумных смесей», 1995.
[23] А. Махрез, Свойства и характеристики щебеночно-мастичных асфальтобетонов, армированных стекловолокно [Ph.
D. диссертация], Инженерный факультет, Университет Малайи, Куала-Лумпур, Малайзия, 2008.
[24] Аси И.М., «Лабораторное сравнительное исследование использования битума с каменной матрицей в жарком климате», Строительство и строительные материалы, том. 20, нет. 10, стр. 982-989, 2006.
Авторские права Advances in Materials Science & Engineering являются собственностью Hindawi Publishing Corporation, и их содержание не может быть скопировано или отправлено по электронной почте на несколько сайтов или опубликовано в рассылке без письменного разрешения владельца авторских прав. Однако пользователи могут распечатывать, загружать или отправлять статьи по электронной почте для личного использования.
Заполнитель для трещин|Шовный герметик|Заполнитель для асфальта|Заполнитель для трещин
Что такое битумно-каучуковый герметик для швов?
Битумно-каучуковый мастичный герметик представляет собой однокомпонентный битумно-каучуковый мастичный герметик холодного нанесения на основе растворителя.
Герметик при отверждении образует прочное и гибкое уплотнение. обладает отличной адгезией к бетону, кирпичной кладке, асфальту и большинству оснований из строительных материалов. Мастичный герметик модифицирован не содержащими асбеста волокнами для придания герметику тиксотропности и отсутствия усадки при нанесении на вертикальные поверхности.
Заполнитель трещин , Ремонт трещин , Заполнитель трещин в асфальте , Герметик для трещин
Герметик для трещин – это общий термин для материалов, которые используются для заполнения и тем самым герметизации трещин и швов в асфальтовых и цементных поверхностях дорожного покрытия. Материалы для ремонта трещин иногда также называют в данной области техники такими терминами, как, например, горячая заливка; заделка трещин; герметик для трещин; герметик для трещин; заполнение трещин; заполнитель трещин; стыковое уплотнение; герметик для швов; герметик для швов ; совместная заливка; заполнитель швов; клеи для холодного шва; маркерные клеи; и другие композиции асфальта/смолы/полимера.
В настоящем описании и в прилагаемой формуле изобретения будет использоваться исключительно термин «герметик для трещин», но следует понимать, что этот термин охватывает все материалы, имеющие одинаковый общий состав, применение и/или свойства. Асфальтовая затирка трещин широко используется для заполнения и тем самым герметизации трещин и стыков на автомагистралях, улицах, парковках и подъездных путях от проникновения воды. Использование герметика трещин
продлевает срок службы таких покрытий.Применение битумно-каучуковой мастики для швов:
Эластичный герметик для швов
Стабильность при высоких температурах окружающей среды
Отличная адгезия, прочное прочное соединение
Однокомпонентный
Где можно использовать битумно-каучуковый герметик для швов?
Битумно-каучуковый мастичный герметик для швов идеально подходит для герметизации и заполнения щелей и швов на крышах, заделки горизонтальных желобов для гидроизоляционных мембран и войлока.
Герметизация вокруг крыш/водопроводных труб. Указание между кирпичной кладкой и отливами крыши. Заделка трещин в асфальтобетонных и бетонных покрытиях. Заполнение горизонтальных швов в бетоне и асфальте, где движения не ожидаются.
Как использовать битумно-каучуковый герметик для швов?
Подготовка поверхности
Поверхность должна быть очищена от грязи, пыли и незакрепленных материалов. Любое масляное и жировое загрязнение должно быть полностью удалено. Перед нанесением герметика поверхность необходимо просушить.
Маскировка
Перед нанесением грунтовки и герметика наклейте малярную ленту на прилегающие стороны стыков, чтобы получить аккуратную отделку и избежать разбрызгивания герметика по краям.
Грунтовка
В нормальных условиях грунтовка не требуется. Однако для очень сухих и пористых поверхностей рекомендуется нанести один слой битумной грунтовки на основе растворителя. Аналогичным образом, для швов, подвергающихся постоянному погружению, рекомендуется грунтовка.
Нанесение
Битумно-каучуковый герметик для швов можно наносить с помощью шпателя или кельмы. Поскольку продукт является растворителем, рекомендуется перемешать содержимое ведра лопастным миксером в течение нескольких минут перед нанесением, чтобы смесь стала однородной. Нанесение герметика должно начинаться с нижней части стыка/канавки и продолжаться вверх. Немедленно обработайте шов шпателем или шпателем, чтобы сгладить и сжать герметик, чтобы обеспечить полный контакт с поверхностями шва. Шпатель необходимо смочить очищающим растворителем, чтобы предотвратить прилипание герметика к ножу и обеспечить гладкую и аккуратную поверхность. Если для поддержания чистоты строительных поверхностей использовалась малярная лента, рекомендуется удалить ее в момент завершения заполнения герметиком.
Горячий битумный герметик для заполнения трещин
Горячий заполнитель трещин – это однокомпонентный, наносимый горячим способом, прорезиненный битумный герметик для трещин и швов.
Заполнитель для горячих трещин специально разработан как для плавильных печей с прямым пламенем, так и для плавильных печей с масляной рубашкой. Он термостабилизирован, чтобы выдерживать температуры до 450ºF без разрушения полимера. При расплавлении и правильном нанесении образует эластичный герметик для трещин как на асфальтовых, так и на цементных покрытиях.
Время отверждения битумно-каучуковой мастики для швов
Герметик отверждается при высвобождении растворителя. Первоначальное снятие пленки с поверхности произойдет в течение 24-48 часов, однако полное отверждение зависит от относительной влажности. Глубина уплотнения 10 мм обычно затвердевает в течение 14-21 дней при 23°C и относительной влажности 50%.
Спецификация битумно-каучуковой мастики-герметика
Свойства
Значения
Цвет
Черный
Форма
паста
Содержание твердых частиц, [%]
>80
Спад
нет
Плотность, [г/см3]
1,1 ± 0,05
мАФ, [%]
±10
начальная установка при стандартных условиях [часы]
24-48
Полное отверждение при стандартных условиях [дней]
14-21 день (10 мм)
Химическая стойкость
Морская вода, хлориды и сульфат-ионы.
Рабочая температура, [°C]
от 0 до 80
Температура применения, [°C]
от 5 до 45
Очистка
Инструменты и оборудование следует очищать сразу после использования чистящим растворителем. Затвердевшие материалы можно очищать только механически.
Хранение и срок годности
Ведра и бочки должны храниться в крытом, сухом и затененном месте, вдали от прямых солнечных лучей, ультрафиолетового излучения и других источников тепла и защищены от экстремальных температур. Срок годности герметика швов битумно-каучукового мастичного до 12 месяцев при соблюдении рекомендаций по хранению. Чрезмерное воздействие солнечных лучей и ультрафиолета приведет к ухудшению качества продукта и сокращению срока его хранения.
Паспорт безопасности битумно-каучуковой мастики для швов
Битумно-каучуковый мастичный герметик содержит нефтяной дистиллят, легко воспламеняется.
Хранить вдали от огня, искр или других источников воспламенения. Носите защитную одежду, резиновые перчатки, маску и защитные очки.
1. Пожар – воспламеняется во влажном состоянии.
2. Кожа – Избегайте повторного или длительного контакта. Удалите битумные пятна с помощью подходящего чистящего средства, способного удалить масло или жир, а затем промойте водой с мылом.
3. Глаза – Контакт может вызвать раздражение. Промыть большим количеством чистой воды.
4. Вдыхание – может вызвать головокружение. если затруднение дыхания сохраняется, введите кислород.
Оценка
Теоретический расход: погонный метр на кг герметика
Глубина шва (мм)
6
10
12
15
20
25
30
40
6
27,7
16,6
14
11
8,3
6,6
8
12,5
10,4
8,3
6,2
5
4.
1
10
10
8,3
6,6
5
4
3,3
2,5
12
6,9
5,5
4.1
3,3
2,7
2
15
4,4
3,3
2,6
2,2
1,6
20
2,5
2
1,6
1,3
Как производить герметик для швов из битумно-каучуковой мастики?
Процесс производства битумно-каучуковых мастик, герметика и герметиков следующий:
1.
От 4% до 11% обработанной бентонитовой глины добавляли в чистую воду в смесителе. Когда глина диспергируется или сильно измельчается в коллоидной мельнице, после смешивания она превращается в глинистую суспензию. Вязкость глиняной суспензии составляет от 20 000 до 180 000 сантипуаз (сП) при 77 градусах. Ф.
2. Разбавленный асфальтобетон состоит из 60-80% асфальта и 20-40% уайт-спирита, растворителя Стоддарда.
3. Глинистый раствор и битумно-битумная разбавленная смесь смешиваются вместе, образуя растворимую систему.
4. Добавляется добавка для повышения стабильности растворимой системы.
5. Безасбестовое волокно добавлено для усиления растворимой системной мастики и прочности пленки герметика. Он также обеспечивает дополнительную вязкость и текстуру.
Включены целлюлозная бумага, стекловолокно, минеральное волокно, полимерное волокно, включая полипропилен и полиэтилен.
6. Нереакционноспособные наполнители, обычно называемые наполнителями пигмента, представляют собой, например, натуральная или кальцинированная глина, порошок слюды и кремнезема, сланцевый порошок, угольная зола, летучая зола и т.
д. добавляются в систему для повышения прочности пленки и консистенции продукта.
7. Эластомеры придают композициям буферность, а также прочность на растяжение и удлинение и включают SBR, SBS, SIBS, акрил, стирол, неопрен, поливинил и т. д.0003
% по массе
Суспензия обработанной бентонитовой глины
3-60
Асфальт Битум Cutback
20-90
Волокна
2-10
Наполнители
3-15
Добавки
0,2-1,0
100,0
Этот состав используется для ямочного ремонта, ремонта и установки гидроизоляционного покрытия.
ПРИМЕР 2 Приготовление битумно-каучуковой мастики для швов
% по массе
Суспензия обработанной бентонитовой глины
3-60
Асфальт Битум Cutback
20-90
Волокна
2-6
Наполнители
3-10
Добавки
0,2-1,0
100,0
Этот состав используется для повторного нанесения кистью на фундаментные стены, крышу, металл, дерево, бетон и другие строительные материалы.
ПРИМЕР 3 Приготовление битумных неволокнистых герметиков
% по массе
Суспензия обработанной бентонитовой глины
3-60
Асфальт Битум Cutback
20-90
Наполнители
3-10
Добавки
.2-1.0
100,0
Этот состав имеет такое же применение, как и в примере 2, за исключением распыления.
ПРИМЕР 4 Приготовление эластомерных битумных неволокнистых мастик
% по массе
Суспензия обработанной бентонитовой глины
3-60
Асфальт Битум Cutback
20-90
Волокна
2-10
Наполнители
3-15
Добавки
0,2-1,0
Эластомеры (эластомерные полимеры)
0,5-5
100,0
Подходит как для кровли, так и для фундамента.
ПРИМЕР 5 Приготовление эластомерных битумных герметиков
% по массе
Суспензия обработанной бентонитовой глины
3-60
Асфальт Битум Cutback
20-90
Волокна
2-6
Наполнители
3-10
Добавки
0,2-1,0
Эластомеры
0,5-3
100,0
ПРИМЕР 6 Приготовление эластомерного неволокнистого герметика
% по массе
Суспензия обработанной бентонитовой глины
3-60
Асфальт Битум Cutback
20-90
Наполнители
3-10
Добавки
0,2-1,0
Эластомеры (эластомерные полимеры)
0,5-6
100,0
С учетом вышеизложенного диапазоны и описания компонентов составляют примерно:
% по массе
Бентонит бурового раствора
.
5-11
Вода
3-55
Битум асфальтный
20-90
Cutback, содержащий от 60 до 80 мас. % асфальта и
20-40 вес. % уайт-спирита Stoddard Solvent
Добавки
.2-1
Волокно без асбеста
0-10
Наполнители
3-15
Эластомер
0-8
Конечно, отдельные суммы выбираются таким образом, чтобы обеспечить 100% общую сумму.
ПРОРЕЗИНИРОВАННЫЙ БИТУМ- ПРОРЕЗИНИРОВАННЫЙ АСФАЛЬТ-БИТУМ РЕЗИНА
ПРОРЕЗИНИРОВАННЫЙ БИТУМ
ВНЕДРЕНИЕ ПРОРЕЗИНИРОВАННОГО БИТУМА
Введение каучука в битумные вяжущие не является новой концепцией.
Он широко использовался в США, Австралии и Европе в течение многих лет с эффективными результатами, которые нельзя игнорировать. В Южной Африке использование латекса в эмульсии также эффективно применялось различными способами в течение последних 10-15 лет, но введение лома резины в горячий битум было осуществлено лишь недавно, и это могло бы послужить определенной цели для обзора ситуации в чтобы получить взвешенную и практическую оценку эффективности этого относительно нового продукта в нашей стране.
БИТУМНО-РЕЗИНОВОЕ УПЛОТНЕНИЕ
В различных публикациях были сделаны экстраординарные заявления о том, что прорезиненные битумные уплотнения могут не только препятствовать, но и устранять отражающее растрескивание, термическое растрескивание, усталостное растрескивание, трещины накачки и различные другие типы трещин. Перед тем, как приступить к реализации программы прорезиненно-битумного уплотнения на каком-либо проекте, целесообразно определить и обозначить проблемы, например.
грамм. если нет разрушения основания или подстилающего слоя, но поверхностный слой высох или в покрытии слишком мало связующего, на поверхности может образоваться крокодиловый узор из трещин. Эти трещины могут быть классифицированы как IIdocill или пассивное растрескивание поверхности.
И наоборот, если имеет место перемещение из-за изменений температуры, изменения содержания влаги в нижележащих слоях, дифференциальное движение из-за колесных нагрузок, эти трещины можно классифицировать как «активные» трещины.
Наш опыт в этой области показывает, что герметизирующие покрытия, нанесенные на поверхности, содержащие «активные» или потенциально «активные» трещины, при герметизации прямыми битумными герметиками сохраняются только от 18 до 24 месяцев, прежде чем те же условия снова проявляются на поверхность.
С другой стороны, если пассивные трещины предварительно обработаны и заделаны прямым битумом, срок службы нового герметика может составлять до 12 лет или дольше, в зависимости от трафика.
Следовательно, в этих условиях резинобитумные уплотнители обычно не применяются. Где следует рассматривать резинобитумные уплотнители для поддержания дорожного покрытия?
(i) На поверхностях с интенсивным движением, где
ожидаются трудности с нанесением достаточного количества вяжущего для удержания заполнителя без возникновения проблемы стекания.(ii) Там, где может произойти перемещение слоев основания, подстилающего слоя или земляного полотна из-за движения влаги. Если бы было возможно герметизировать поверхность и воспрепятствовать проникновению воды в слои дорожного покрытия, это можно было бы более эффективно сделать с помощью прорезиненного битумного герметика, поскольку вяжущего можно было бы использовать примерно на 50 % больше, чем обычного битумного вяжущего.
(iii) На насосных поверхностях. Хотя было заявлено, что битумно-резиновые уплотнения решат эту проблему, лучшее, что можно сказать, это то, что они будут препятствовать перекачиванию, но не решат проблему во всех случаях.
Слои дорожного покрытия создают большие гидравлические давления – разрушаются. большие нагрузки на колеса, достаточные для насыщения, чтобы вызвать разрушение дорожного покрытия.
(iv) Первичные трещины в покрытиях, стабилизированных цементом, особенно продольные трещины, образуют идеальные водосборные стоки для проникновения воды в слои покрытия. Обычно основание представляет собой слой, стабилизированный известью или цементом, что является идеальным уплотнением для короба в воде, готового к гидравлическому давлению, создаваемому тяжелыми колесными нагрузками. В этих случаях происходит значительное движение из-за изменений температуры, а также из-за колесных нагрузок на дорожное покрытие.
Перед герметизацией дороги эти трещины необходимо обработать – желательно битумно-резиновыми составами.
Многие из асфальтовых покрытий, укладываемых на эти стабилизированные покрытия, пористые, и во время дождливых периодов большие объемы воды практически прокачиваются через поверхность тяжелыми колесными нагрузками.
Комбинация герметизации трещин и герметизации поверхности
с помощью двунаправленных резиновых уплотнений, несомненно, продлит срок службы дорожного покрытия. Герметизация поверхности битумно-резиновым герметиком, однако, не всегда необходима, если первичная герметизация трещин выполнена своевременно и правильно, а количество транспортных средств не является чрезмерным, т.е. 15 000 v.p.d./ширина дорожки.(v) Там, где имеются кровоточащие, но стабильные поверхности, т. е. там, где поверхностный битум не настолько толстый, чтобы поверхность была неустойчивой и должна быть удалена, можно эффективно использовать битумно-резиновые уплотнители.
ПРОРЕЗИНЕННЫЙ АСФАЛЬТ
С момента широкого использования асфальтовых покрытий в Южной Африке существует постоянная проблема получения экономической жизни от таких покрытий в различных областях.
В Южной Африке используются три основных типа асфальтобетонных покрытий:
(a) Асфальт с непрерывным гранулометрическим составом.![]()
(b) Асфальт с заполнителем с щелевым или полущелевым заполнителем.
(c) Курс ношения «попкорн».(a) Одной из основных причин повреждений асфальтового покрытия (a) и (b) является то, что прогибы дорожного покрытия, возникающие в полевых условиях, превышают прогибы, которые выдерживает слой асфальта. Цитируя работу Хвеема в Калифорнийском дорожном департаменте, мы имеем следующую информацию:
Вышеупомянутые предельные отклонения представляют проблему в правильном свете.
(b) Большинство асфальтовых покрытий имеют большую или меньшую толщину. степень пористая. Как только вода может заполнить пустоты на поверхности, во время продолжительной влажной погоды, при интенсивном движении колес, вступают в действие гидравлические силы, и может иметь место разрушение поверхности. Колесные нагрузки фактически начинают закачивать воду на поверхность или через нее. Ситуация может усугубиться, если заполнитель имеет низкое сродство к битуму – например, наши кварциты в Трансваале.
Очень мало работы было проделано в морозных условиях в Южной Африке, но мы указываем минимальное содержание пустот в наших асфальтах, чтобы предотвратить просачивание на наших асфальтовых покрытиях. В то же время мы замерили минимальные температуры в Свободном штате -7°C, к счастью, в сухих условиях.
С поверхностями для попкорна возникают две проблемы.
(i) Либо поверхность имеет тенденцию слипаться из-за слишком большого количества связующего, либо(ii) поверхность начинает растрескиваться из-за слишком малого количества связующего.
В последнем случае растрескивание происходит за счет отделения вяжущего от заполнителя. В первом случае битум имеет тенденцию течь, и происходит переориентация заполнителя из-за смазывающего действия вяжущего. Введение каучука в битум позволило в значительной степени решить вышеуказанные проблемы.
В результате проведенных на сегодняшний день испытаний были получены следующие результаты и сделаны следующие выводы.
При сравнении теста Instron Beam Fatigue Test на асфальте BSS 594 с щелевой градацией с таким же испытанием, проведенном на битуме с открытой градацией (не для попкорна), получены следующие результаты: протестировано при 20 C (отказов нет)
Полу-градированный битум 60/70 сбой при 70 000
, протестированных при 20 C повторенияСтабильность прорезиненного открытого асфальта составляла 7,7 кН с потоком 2,8 мм с 7% битумом и 2, 2, 2 4% каучука.
Индексы иммерсии значительно выше, чем те, которые обычно встречаются с кварцитовыми агрегатами, и были получены цифры от 92 до 98. На дорогах Р29 проложено несколько участков/2, P157/2 и P2/1.
Высказывались сомнения по поводу возможной колейности материала при движении. Аналогичная спецификация использовалась Ребекчи из Управления дорожного строительства штата Виктория, Австралия, для наложения покрытия в городской черте на бетонную дорогу, имеющую от 30 000 до 40 000 v.p.d.
Это было уложено толщиной 30 мм и после четырех лет использования –
(а) не было колейности и
(б) менее 10% стыков имели очень мелкие незначительные волосяные трещины.Прогиб в стыках этого бетонного покрытия до укладки колебался от 0,2 до 0,8 мм. Признаков термического растрескивания в плечах не было, за исключением нескольких незначительных волосяных трещин на суставах.
Полученные высокие индексы иммерсии являются наиболее важными, поскольку этот индекс является мерой возможного отслоения, которое может иметь место.
Во-вторых, в результате обширных испытаний Reidel & Weber мы получили отличные результаты с прорезиненным битумом в отношении вскрытия.
Проблема стекания избыточного вяжущего вещества с заполнителя при высоких температурах была специально исследована при использовании битумного каучука для смеси для попкорна. Образец прорезиненного битума типа «попкорн» помещали в печь на два часа при температуре 200°С, при этом не наблюдалось явного стекания вяжущего на дно поддона. Это важная проверка, поскольку асфальт должен храниться при высокой температуре, чтобы резина могла перевариться перед укладкой. Тест Маршалла не применим к битумам типа «попкорн», но этот тест был проведен только для сравнительных целей, и при более высоком процентном содержании вяжущего было получено почти вдвое больше стабильности при использовании прорезиненного битума, чем при использовании обычного битума в чистом виде.
Так где же рентабельно использовать прорезиненный асфальт?
(a) Во-первых, дополнительные затраты на прорезиненный асфальт примерно на 10-15% больше, чем на «обычный асфальт».
(b) После ослабления требований S.A.T.S в отношении разрешений на автомобильные перевозки наблюдается неуклонный рост не только количества ESO, использующих нашу дорожную систему, но также увеличилось количество случаев использования этой системы перегруженных транспортных средств. Многие из наших дорог были покрыты тонкими коврами, т.е. двойные уплотнения, уплотнения Cape, асфальтовые покрытия 25 мм и 50 мм.
Стандартной практикой в США было использование не менее 100 мм асфальтобетона на дорогах с интенсивным движением.
с увеличением нагрузки на колеса и интенсивности нагрузки будет увеличиваться величина прогибов покрытия, а также увеличиваться повторение этих больших прогибов.
Страна просто не может позволить себе перестроить свою сеть, чтобы нести возросшую транспортную нагрузку.
Изучая прогибы, возникающие на определенных дорогах, можно будет покрыть эти дороги тонким прорезиненным асфальтовым покрытием, которое может выдерживать повторяющиеся более высокие прогибы, чем обычные асфальты, используемые в настоящее время.
Проблема, с которой в настоящее время сталкиваются поверхности «попкорн», вероятно, может быть эффективно решена.
ЗАКЛЮЧЕНИЕ
(a) Асфальт
При производстве прорезиненного асфальта необходимо соблюдать несколько мер предосторожности:
(i) Необходимо контролировать качество и сортность резиновой добавки.
(ii) Необходимо контролировать количество резины.
(iii) Необходимо контролировать время и температуру разложения.
(iv) Использование добавок, т.е. следует избегать использования парафина или масел-наполнителей.(b) Прорезиненные уплотнения
Прорезиненные битумные уплотнения следует использовать только там, где они наиболее эффективны и решают проблемы, с которыми не могут эффективно справиться обычные уплотнения. Стоимость прорезиненного уплотнителя на данном этапе примерно на 50% больше, чем у обычного уплотнителя. Следовательно, если срок службы одного уплотнения составляет восемь лет, то прорезиненное уплотнение должно прослужить примерно 12 лет, чтобы быть рентабельным на дороге без каких-либо особых проблем.
Преимущества
Более высокая устойчивость к деформации и повышенной температуре дороги повышает комфорт вождения.
Улучшенная адгезия и сцепление с заполнителями, более высокая температура размягчения, высокое сопротивление текучести и более высокая ударопрочность, чтобы выдерживать движение большегрузного транспорта.
Более высокое сопротивление скольжению, лучшее сцепление с дорогой и более плавное торможение транспортного средства существенно снижают вероятность аварии.
Более высокое удлинение и прочность на растяжение повышают эластичность, пониженная термочувствительность снижает вероятность появления всех типов трещин под нагрузкой.
Уменьшает степень колейности, повышает комфорт при вождении даже при более высокой нагрузке на ось.
Более высокие противозадирные свойства и высокая устойчивость к влаге/водопоглощению снижают вероятность повреждения дорог во время сильного дождя даже при неправильном дренаже.
Более высокая стойкость к старению благодаря пассивности к окислению (сопротивление разложению при высоких температурах применения, а также летом обеспечивает более длительный срок службы дорожного покрытия при меньшем техническом обслуживании).