8 станков и приспособлений для резки пенопласта
Из пенопласта можно делать разные декоративные поделки. Материал этот доступный и недорогой.
Однако главная загвоздка в том — что аккуратно и ровно отрезать пенопласт ножом не всегда получается. Не говоря уже о том, когда нужно вырезать из него различные фигурные элементы. В сегодняшней статье рассмотрим простые в изготовлении самодельные станки и приспособления для резки пенопласта и вспененных материалов.
Содержимое
- 1 Резак для пенопласта из ПВХ-труб и нихромовой проволоки
- 1.1 Основные этапы работ
- 1.2 Видео
- 2 Самодельный станок для резки вспененных материалов
- 2.1 Определяем длину нихромовой нити
- 2.2 Изготовление рабочей площадки станка
- 2.3 Рамка для натяжения нихромовой нити
- 2.4 Сборка станка и электромонтажные работы
- 2.5 Видео
- 3 Как сделать портативный термонож для резки пенопласта
- 3.1 Основные этапы работ
- 3.
2 Видео
- 4 Станок для прямолинейной и фигурной резки пенопласта
- 4.1 Основные этапы работ
- 4.2 Сборка всей конструкции
- 4.3 Видео
- 5 Самый удобный и быстрый способ резки пенопласта
- 5.1 Основные этапы работ
- 5.2 Видео
- 6 Резка пенопласта с помощью сварочного аппарата
- 6.1 Основные этапы работ
- 6.2 Видео
- 7 Простое приспособление для горячей фигурной резки пенопласта
- 7.1 Основные этапы работ
- 7.2 Видео
- 8 Устройство для резки пенопласта и экструдированного пенополистирола
- 8.1 Основные этапы работ
- 8.2 Видео
Резак для пенопласта из ПВХ-труб и нихромовой проволоки
Для быстрой резки пенопласта в домашних условиях можно использовать самодельный резак, изготовленный из кусков ПВХ-труб и нихромовой проволоки.
Читайте также: Как сделать циклон для пылесоса: 14 бюджетных идейОбратите внимание, что если требуется высокая точность резки, то для таких работ данная самоделка не подойдет.
Чтобы сделать раму резака, потребуется четыре отрезка полипропиленовой трубы диаметром 22 мм, тройник, уголок и три пластиковых заглушки.
И первым делом необходимо будет нарезать полипропиленовую трубу по размеру. Как соединить заготовки между собой, смотрите на фото ниже.
Основные этапы работ
Читайте также: Как сделать пистолет для силикона с электроприводомНа следующем этапе нужно просверлить еще одно отверстие в тройнике, чтобы установить кнопку. После этого можно уже приступать к сборке конструкции. Куски труб и фитинги автор соединяет с помощью клея.
Концы провода выводятся через вертикальные трубы. Автор крепит их к болтам, которые вкручиваются в заглушки. Затем на болты накручивается нихромовая проволока.
Читайте также: Как сделать пылеуловитель для дрели и перфоратораВидео
Подробнее о том, как своими руками изготовить простенький резак для пенопласта из ПВХ-труб и нихромовой проволоки, смотрите в видеоролике на нашем сайте.
Самодельный станок для резки вспененных материалов
В данном обзоре автор изготавливает своими руками самодельный станочек для резки различных вспененных материалов: поролона, пенопласта, пенополистирола и других.
Режущим элементом будет являться раскаленная нихромовая нить. Ее можно купить на радиорынке или, например, снять со старого (нерабочего) бытового фена.
Далее необходимо будет опытным путем определить подходящую для работы длину нити. Для этого из куска ДСП и двух саморезов автор собрал небольшой стенд. Между саморезами натягиваем нихромовую нить.
Читайте также: Насадка для скручивания полиэтиленовых пакетов в рулоныШнур для питания всей системы можно взять от фена или другого нерабочего электроприбора. Дополнительно автор использует понижающий трансформатор, который преобразовывает 220 вольт из розетки в 12 вольт переменного напряжения.
Определяем длину нихромовой нити
Подключаем сетевой шнур к трансформатору. Длину выходящих проводов в случае необходимости можно нарастить.
Один контакт автор крепит на один край конструкции, другой — будет скользящим, то есть будет свободно перемещаться вдоль нихромовой нити.
Изменяя расстояние между контактами, мы изменяем сопротивление и, соответственно, температуру нагрева нихромовой нити.
Необходимо подобрать такую температуру, чтобы нить хорошо резала поролон.
В данном случае наиболее оптимальное расстояние между контактами — примерно 9-10 см. От этих размеров и будем отталкиваться при изготовлении станка.
Изготовление рабочей площадки станка
Площадка станка будет состоять из столешницы (рабочего стола) и четырех ножек. Изготовим их из фанеры толщиной 12 мм. Размер столешницы по чертежу мастера составляет 30х31 см.
Отпиливаем заготовки необходимого размера, после чего обрабатываем их на шлифовальном станке или с помощью шлифмашинки. Кромки у столешницы надо немного скруглить, чтобы они не цепляли заготовку.
Ножки крепим к столешнице на косой шуруп. Для этого автор сверлит под углом два отверстия диаметром 4 мм, затем сверлом на 10 мм нужно будет расширить отверстия по шляпке шурупа.
Рекомендуем также прочитать статью-обзор: как сделать кондуктор с фиксатором для соединений косой шуруп. Такое приспособление в мастерской точно лишним не будет.
Далее размечаем и сверлим крепежные отверстия для соединения ножек между собой при помощи отрезков фанеры. Размечаем места крепления ножек, отступив некоторое расстояние от края площадки.
Рамка для натяжения нихромовой нити
Сначала размечаем центр столешницы. При помощи электролобзика надо будет сделать направляющую прорезь для крепления П-образной рамки.
Для изготовления самой рамки мастер использует алюминиевый уголок размером 25*25 мм и толщиной 2 мм. Отрезаем заготовки нужной длины, и потом собираем их на заклепки. Примеряем рамку на свое место.
Сверлим крепежные отверстия для крепления нихромовой нити.
Алюминиевая рамка будет использована в качестве проводника — в верхней части нихромовая нить будет крепиться напрямую к ней.
В нижней части места крепления нити нужно будет изолировать. Для этого мастер делает нижнее крепление из двух кусочков фанеры.
Размечаем и сверлим в одной из заготовок необходимые для монтажа отверстия. В середине квадратика нужно просверлить отверстие под болт М5, к которому и будет крепиться нихромовая нить.
Во второй заготовке делаем углубление под шляпку болта.
Потом склеиваем обе заготовки столярным ПВА, стягиваем струбциной. После полного высыхания надо сошлифовать остатки клея.
Сборка станка и электромонтажные работы
На следующем этапе отрезаем два алюминиевых уголка. Прикручиваем их под столешницей. К ним крепим понижающий трансформатор.
Далее в одной из ножек размечаем и сверлим отверстие под выключатель.
Контакты питающего провода будут крепиться к алюминиевой рамке с помощью гайки и шайбы. К ним и нужно припаять концы проводов. Для контакта, который будет крепиться к рамке, сверлим отверстие, а потом прикручиваем его.
Монтируем алюминиевую рамку на свое место, после чего подключаем провод питания к трансформатору.
На последнем этапе останется только просверлить отверстие для нихромовой нити в самой столешнице. Чтобы раскаленная нить не касалась фанеры, автор вставляет в отверстие втулку из медной трубки.
Отрезаем кусок нихромовой нити подходящей длины и наматываем на нижнее крепление рамки между двух шайб, прижимаю барашком. После этого закрепляем второй конец нити на верхнем креплении. Станок собран и готов к работе.
Видео
Подробно о том, как изготовить самодельный станок для резки вспененных материалов, смотрите на видео ниже. Обзор создан на основе видеоролика с YouTube канала TileCraft workshop.
Как сделать портативный термонож для резки пенопласта
Для прямолинейной резки пенопласта и экструдированного пенополистирола можно использовать канцелярский нож. А вот для фигурной резки лучше всего подойдет термонож.
В данном обзоре расскажем, как сделать это приспособление своими руками.
Идея самоделки принадлежит автору YouTube канала DIY Pro — советуем взять на заметку.
Первым делом отпиливаем деревянный брусок длиной 10 см, и сверлим по краям два отверстия.
В просверленные отверстия вставляем два карандаша (приклеиваем на термоклей). Вместо карандашей можно также использовать круглые деревянные палочки.
Возможно, вам интересно будет прочитать статью: как в домашних условиях изготовить круглые деревянные палочки любого диаметра.
Основные этапы работ
На следующем этапе в торцах карандашей сверлим отверстия, и вставляем в них колечки, изготовленные из медной проволоки. Заматываем концы карандашей изолентой.
Далее нам потребуется батарейный отсек. Приклеиваем его при помощи термоклея к деревянному бруску.
Рядом с батарейным отсеком необходимо будет приклеить на термоклей кнопку включения/выключения. Затем подключаем провода, как показано на фото ниже.
Концы электрических проводов подключаем к медным колечкам, а между ними — натягиваем нихромовую проволоку.
Вставляем батарейки в батарейный отсек, включаем кнопку, и можно приступать к резке пенопласта.
Видео
Пошаговый процесс изготовления портативного термоножа вы можете посмотреть на видео ниже.
How to make a Foam Cutter at Home? Awesome DIY project! Wow!Станок для прямолинейной и фигурной резки пенопласта
В данном обзоре автор покажет, как собрать своими руками простенький станок, с помощью которого можно резать пенопласт.
Особенность конструкции заключается в том, что можно делать как прямолинейные, так и фигурные резы (например, можно вырезать из пенопласта круг нужного диаметра).
Для изготовления самодельного станка нам потребуется фанера и немного металла.
Советуем вам также прочитать: как собрать простое приспособление для разметки круглых заготовок.
Основные этапы работ
Первым делом из фанеры автор собирает основание станка. Отпиливаем две боковых стенки, и прикручиваем их к рабочей поверхности.
После этого необходимо будет вырезать заднюю стенку. К задней стенке автор крепит вертикальную стойку (ее можно сделать из квадратного прутка или профильной трубы).
Стойка крепится с помощью болта, и является подвижной — ее можно выставлять под разными углами. К нижней части приваривается болт.
Сборка всей конструкции
На последнем этапе останется только приварить к стойке «плечо» и натянуть нихромовую нить, которая и будет резать пенопласт. Изготавливаем и крепим к основанию упор из уголка.
Затем автор выполняет все необходимые электромонтажные работы и устанавливает регулятор напряжения.
Для фигурной резки пенопласта необходимо будет изготовить отдельную площадку из фанеры или доски.
Видео
Подробно о том, как изготовить станок для прямолинейной и фигурной резки пенопласта, можно посмотреть на видео ниже. Идеей поделился автор YouTube канала
Самый удобный и быстрый способ резки пенопласта
В данном обзоре мы хотим поделиться с вами удобным и быстрым способом резки пенопласта — с помощью терморезака.
Самоделка представляет собой компактный настольный станочек с нагревательным элементом (резаком) и блоком питания на 12 В. Изготовить приспособление можно своими руками.
Рекомендуем также прочитать, как собрать компактный станочек для быстрой заточки сверл в условиях мастерской.
Основные этапы работ
Станину станка и столешницу автор решил сделать из фанеры. Отпиливаем четыре заготовки (две широких и две узких). В одной из широких заготовок надо вырезать отверстие.
Потом склеиваем все четыре заготовки в короб. Дополнительно скрепляем детали гвоздями.
К тыльной части основания автор крепит кусок фанеры с выступом в верхней части. Обшиваем фанеру ламинированным ДСП.
Возле выступа необходимо будет сделать прорезь.
Из металлической полосы автор изготавливает Г-образную стойку, к концу которой будет крепиться нагревательный элемент (в данном случае — это нихромовая нить). В столешнице сверлим отверстие под проволоку.
На задней стенке нужно вырезать полукруглый паз и установить фиксатор. Это надо для того, чтобы можно было менять угол наклона стойки.
Спереди автор прикручивает металлическую пластину, на которой будут располагаться элементы контроля и управления: цифровое табло, кнопка включения и регулятор для блока питания.
Под столешницей крепим блок питания.
Рядом с просверленным отверстием устанавливаем уголок, к которому будет крепиться один конец нихромовой проволоки.
Второй конец проволоки будет крепиться на стойке.
На последнем этапе останется только изготовить и установить параллельный упор из алюминиевого уголка. Самоделка готова.
Видео
Подробный процесс изготовления терморезака для пенопласта можно увидеть на видео ниже. Идеей поделился автор YouTube канала Mistry MakeTool.
Make A Hot Wire Foam Cutter || DIY Foam Cutting MachineРезка пенопласта с помощью сварочного аппарата
Сварочный инверторный аппарат можно использовать не только для сварки металла, но также и для других целей. Например, для быстрой резки пенопласта и поликарбоната.
Для этого нужно всего лишь изготовить нехитрое приспособление из подручных материалов.
Потребуется две шпильки с шайбами и гайками, две мощные пружины, нихромовая проволока толщиной 0,5 мм и кусок доски.
Рекомендуем ознакомиться:
Термомеханический мини станок для быстрой резки пенопласта
Простое приспособление для горячей фигурной резки пенопласта
Первым делом отпиливаем кусок доски или деревянного бруска длиной 120 см. Также необходимо отрезать две шпильки М10.
Основные этапы работ
Отступив по 2-3 см от краев, нужно просверлить в доске два сквозных отверстия сверлом по дереву диаметром 10 мм.
В просверленные отверстия вставляем шпильки и фиксируем их с двух сторон гайками с шайбами.
На следующем этапе в каждой шпильке (с одной из сторон) нужно будет просверлить отверстия диаметром 4 мм — на расстоянии примерно 2 см от края.
Надеваем на шпильки пружины и фиксируем их с помощью штифтов (их можно сделать из обычного гвоздя или электрода).
Далее откусываем нужной длины нихромовую проволоку и крепим ее к пружинам. Натяжка должна быть максимальной.
В конце останется только закрепить брусок на столе, подключить к шпилькам «плюс» и «минус» от сварочного аппарата, и приспособа готова к работе. Сила сварочного тока должна быть около 20 Ампер.
Видео
Подробно о том, как работает это приспособление, смотрите на видео ниже.
ИДЕЯ ДЛЯ СВАРОЧНОГО АППАРАТА!!! ПРИГОДИТСЯ В ВАШЕЙ МАСТЕРСКОЙ!ТАКОГО ЕЩЕ НИКТО НЕ ВИДЕЛ!Простое приспособление для горячей фигурной резки пенопласта
При помощи простого самодельного приспособления можно резать пенопласт и пенополистирол горячим методом.
Используя эту самоделку, можно быстро вырезать различные фигуры, которые не получится вырезать канцелярским ножом «на холодную».
Первым делом необходимо подготовить основание, на котором будут размещаться все основные элементы. И для этого мастер вырезает из листа фанеры кусок подходящих размеров, после чего шлифует его наружную поверхность.
Далее нужно будет сделать разметку и просверлить в фанере четыре отверстия, в которые потом мастер вкручивает 4 резиновые ножки по краям.
Таким образом, основание для самоделки будет более устойчивым (особенно на гладких поверхностях).
Основные этапы работ
На следующем этапе надо будет просверлить еще два отверстия по краям основания (на осевой центральной линии). В эти отверстия вставляются длинные болты, к которым мастер подключает провода.
Также необходимо будет прикрутить к фанере металлический уголок, в котором предварительно нужно просверлить несколько отверстий — для крепежа и болта. Данный элемент конструкции выполняет роль натяжителя проволоки.
На последнем этапе к болтам и натяжителю крепится нихромовая проволока толщиной 0,3 мм, которая и будет резать пенопласт и пенополистирол.
Видео
Подробный процесс изготовления самодельного приспособления для горячей фигурной резки пенопласта смотрите в видеоролике на нашем сайте.
How to Cut Polystyrene FoamУстройство для резки пенопласта и экструдированного пенополистирола
В этой статье мы расскажем, как изготовить своими руками самодельное устройство, которое предназначено для резки листов пенопласта и экструдированного пенополистирола.
Идея данной самоделки принадлежит автору YouTube канала DEZERTTER.
Первым делом необходимо будет изготовить П-образную раму. Отрезаем три заготовки из квадратной профильной трубы, и скрепляем их между собой с помощью мебельных соединительных уголков из металла.
К боковым стойкам рамы прикручиваются мебельные направляющие.
Далее потребуется два куска строительного металлического уголка. Отрезаем заготовки нужного размера, и крепим их к мебельным направляющим.
Собранную конструкцию необходимо прикрутить к основанию, в качестве которого используется лист МДФ. Также можно использовать лист фанеры или мебельный щит.
Рекомендуем также прочитать статью: бюджетная точечная сварка из трансформатора от микроволновки.
Основные этапы работ
На следующем этапе в нижнюю часть стоек устанавливаются пластиковые заглушки, в которые вставлены болты. В шляпках болтов предварительно необходимо просверлить отверстия.
Далее между стойками необходимо будет натянуть сварочную проволоку толщиной 0,8 мм. Для этого используются винтовые соединители для проводов.
На противоположной стороне конец проволоки соединяется с болтом посредством пружины.
Вместе с проволокой также устанавливаем медный провод сечением 6 мм2. Концы этих проводов подключаем к трансформатору. На перекладине рамы устанавливаем кнопку.
С помощью этого устройства можно резать пенопласт как под прямым углом (в продольном и поперечном направлениях), так и под углом 45 градусов.
Видео
Подробно о том, как изготовить самодельное устройство для резки пенопласта и экструдированного пенополистирола, вы можете посмотреть на видео ниже. Спасибо за внимание.
DIY styrofoam cutter | Przecinarka do styropianuАндрей Васильев
Задать вопрос
Станок для резки пенопласта своими руками. Технология изготовления самодельного станка для резки пенопласта. Инструкция по изготовлению станка, советы по резке и выбору материала.
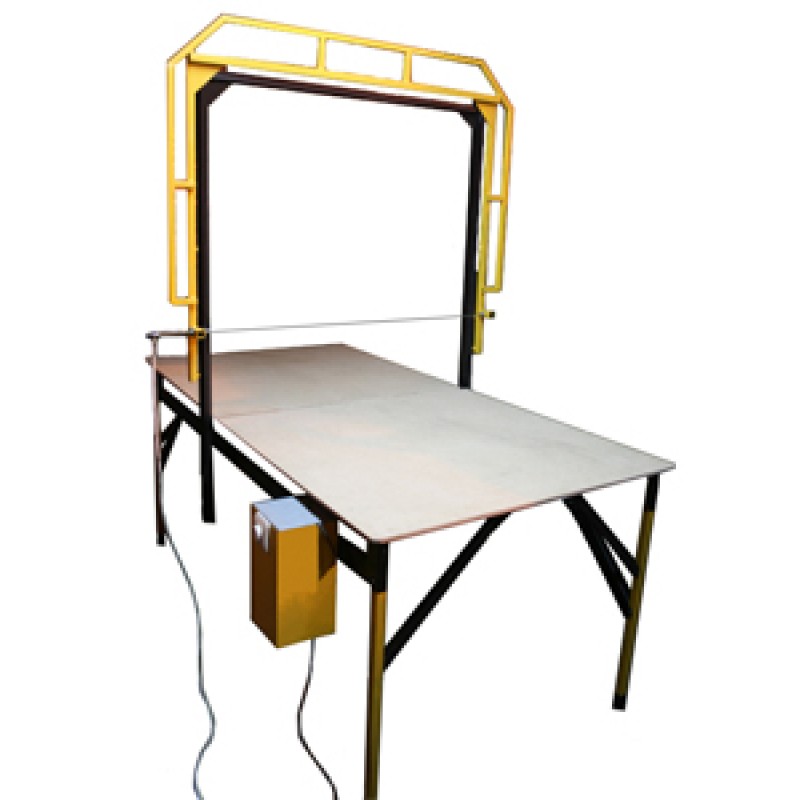
Пенопласт – замечательный материал, используемый во многих областях строительства и декора. С его помощью обустраивают гидро- и теплоизоляцию, создают декоративные потолочные покрытия, багеты и многое другое. При всей своей многофункциональности, он еще и дешевый. Единственная проблема, возникающая во время работы с ним – это резка.
Содержание
- Резка пенопласта: станок своими руками
- Полезные советы
- Выбор пенопласта для обустройства теплоизоляции
Резка пенопласта: станок своими руками
Порезать пенопласт самостоятельно так, чтобы получить чистый и ровный рез крайне сложно. Он крошится и лопается, если применять пилу, даже лезвие или бритва не решают проблему.
Выходом может послужить горячий металл, но как воспользоваться им в домашних условиях? Сконструировать самодельный станок для резки пенопласта!
Способ №1.
Для осуществления данной затеи потребуются:
- стол, лучше если каждая из его сторон будет не короче 2 м;
- металлические пружины с низким сопротивлением тока;
- трансформатор, преобразовывающий ток с 220-ти на 24 Вольта;
- струна с высоким сопротивлением, если есть старый обогреватель, снимите с него.
Также понадобится регулятор высоты струны. В качестве него используйте пару балок. Между ними будет перемещаться режущая струна с держателем.
Трансформатор необходим не в каждом случае. Это зависит от того, из какого материала сделана струна. Если она хромированная – допустимым считается и ток в 220 Вольт. Но, работая с таким разрядом, следует четко соблюдать правила безопасности, иначе дело может закончиться печально.
Если работать с разрядом 24 Вольт, то опасность для жизни и здоровья отсутствует. Он просто не ощутим, и при поражении необходимо просто промыть пострадавшее место водой.
Следует также помнить, что при резании пенопласта раскаленным металлом, выделяются токсичные пары, поэтому нужно в обязательном порядке использовать защитную маску и хорошо проветривать помещение, иначе отравление будет обеспечено. А лучше всего, вообще, работать на улице, но это возможно, если есть собственный двор.
Для того чтобы было легче собрать из вышеперечисленных материалов станок для резки пенопласта, ниже приведен схематичный чертеж:
Способ №2.
За неимением подходящего стола, в качестве основания для устройства вполне подойдет лист ДСП, фанера, доска.
Последовательность сборки самодельного станка:
1. Нихромовую проволоку прикрепите к пружинам, пружины оденьте на винты М4, а их, в свою очередь, вкрутите в специальные стойки.
2. Металлические стойки заблаговременно запрессуйте в крышу стола, плиту ДСП, или любую другую поверхность, выбранную в качестве основания. Высота стойки и толщина основания зависит от нужд владельца станка. Если толщина плиты составляет 1,8 см, а стойка в высоту – 2,8 см, то в полностью вкрученном состоянии винт не пройдет основание насквозь, а при полном выкручивании сможет нарезать пенопласт толщиной 5 см.
3. Если в будущем потребуется более толстая нарезка, то короткие винты нужно будет удалить и вкрутить на их место длинные.
4. Для запрессовки просверлите в основании отверстие. Его диаметр должен быть меньше диаметра стойки на пол миллиметра. Стойки вбейте молотком в отверстия, но перед этим, чтобы облегчить себе данную процедуру, пройдитесь наждачкой по острым кромкам торцов.
5. Перед тем как вкрутить винт в стойку, выпилите под самой его шляпкой канавку. Чтобы это осуществить, зажмите его конец шуруповертом, а под головкой приложите тонкий напильник и включите вращение. Эта канавка нужна для того, чтобы зафиксировать в одном положении проволоку, которая иначе может перемещаться при регулировке.
6. Чтобы проволока не провисла, удлинившись из-за нагревания, прикрепите ее сначала к пружинам, а их уже к винтам.
7. После того как все крепежные детали готовы, зафиксируйте нихромовую проволоку. Чтобы контакт между ней и токопроводящим проводом был надежным, используйте способ крепления «скрутка с обжатием». Медный провод должен иметь сечение не меньше 1,45 кв.мм.
8. Снимите изоляцию с окончаний проводов примерно на 2 см. Медные проводники накрутите на проволоку в тех местах, где она крепится к пружине. Конец проволоки, придерживая плоскогубцами, обмотайте вокруг проводника. Благодаря такой намотке контакт проволоки и токопроводящего провода будет иметь большую площадь, и когда станок заработает, места соединения не будут раскаляться.
9. Чтобы получить возможность регулировать толщину резки материала, сделайте отвод токопроводящих проводников в виде петли. А чтобы провода не путались под руками во время использования станка, проделайте в основании отверстия, пропустите через них мешающий отрезок и прикрепите к обратной стороне поверхности при помощи скоб.
10. Провода лучше всего сложить вместе и перекрутить в виде нетугого жгута. Так они не будут путаться.
11. На концах проводов припаяйте накидные клеммы, чтобы подключить их к источнику питания.
Сконструированного по вышеописанной инструкции устройства будет вполне достаточно для использования в домашних условиях. Кроме этого, его возможно использовать как станок для фигурной резки пенопласта.
Полезные советы
Во время резки скорость движения материала должна быть средней. Если двигать пенопласт очень быстро, тогда он точно так же раскрошится, как и при резке пилой. Если же напротив, перемещать его очень медленно, края вырезаемой фигуры будут оплавляться.
Если пенопласт требуется для утепления дома при строительстве, то лучше приобретайте более толстый. Из-за простого изготовления и небольшой востребованности, такой материал стоит гораздо более дешево, чем тонкий.
Если на чердаке еще с советских времен завалялся стереомагнитофон «Маяк», то трансформатор не покупайте, а возьмите с него. Он как раз является подходящим, т.к. подает напряжение 24 Вольта.
В случае, когда работы проводятся в условиях отсутствия электроэнергии, соедините друг с другом три кроны по 9 Вольт, и используйте их. Таким образом, устройство сможет функционировать 30-40 минут.
Но применять автоаккумуляторы для данной цели категорически запрещается. Несмотря на низкое напряжение, они имеют очень большую силу тока, которая может сжечь струну и она попросту лопнет. Это при хорошем раскладе, а при плохом – брызнет раскаленным металлом.
Выбор пенопласта для обустройства теплоизоляции
Существует специальный пенопласт, предназначенный именно для утепления фасадов. На упаковке обычно имеется соответствующая маркировка в виде буквы «Ф». Он имеет высокую, в сравнении с обычным материалом, плотность и устойчив к механическому воздействию. Он хорошо пружинит, благодаря чему плохо поддается ломке.
При нарезании пенопласта, для теплоизоляции не следует устанавливать струну ниже 50 мм. Дело в том, что более тонкий материал не будет достаточно эффективен, а при намокании вообще утратит большую часть своих замечательных свойств. При высокой влажности такая теплоизоляция будет проницаема для холодного воздуха, как и обычная кирпичная кладка.
В качестве дополнительного материала для теплоизоляции используйте плиту минеральной ваты. Кроме упомянутых свойств она обладает еще одним важным достоинством – в случае возникновения пожара не будет гореть.
Станок для резки пенопласта, видео:
Станки для резки пенопласта своими руками
Пенопласт используется сегодня во многих отраслях строительства и промышленности. С его помощью можно обустроить тепло- и гидроизоляцию, сформировать декоративные покрытия, багеты, а также многое другое. В качестве единственной проблемы, которая возникает при работе с данным материалом, выступает необходимость правильного раскроя. Станки для резки пенопласта можно приобрести в магазине, но гораздо дешевле будет выполнить такое оборудование самостоятельно.
Изготовление конструкции для резки листов пенопласта
Для того чтобы получить чистый и ровный срез, нужно использовать соответствующее оборудование. В качестве выхода может послужить горячая сталь, однако использовать ее в домашних условиях весьма проблематично. Остается только одно решение, которое выражено в самостоятельном изготовлении станка.
Подготовительные работы
Для того чтобы изготовить станок для фигурной резки пенопласта, необходимо подготовить определенные материалы и инструменты. Понадобится стол, к которому предъявляются определенные требования, таким образом, каждая из его сторон не должна оказаться меньше двух метров. Мастер должен подготовить стальные пружины, которые имеют низкое сопротивление тока. В работе никак не обойтись без трансформатора, который способен преобразовывать ток с 220 на 24 вольта. Следует использовать струну с высоким сопротивлением, если в наличии имеется старый обогреватель, то этот элемент может быть позаимствован из данного оборудования. Мастеру будет необходимым и регулятор высоты струны, в роли которого возможно применить две балки. Между ними станет перемещаться режущая струна, которая имеет держатель. Трансформатор может понадобиться не в каждом случае. Это будет зависеть от того, какой материал будет лежать в основе струны.
Безопасность использования
Если станок для 3d резки пенопласта изготавливается с пользованием хромированной струны, то допустимым будет ток в 220 вольт. Но, работая с подобным разрядом, необходимо соблюдать правила безопасности. Если использовать разряд в 24 вольта, то опасность для жизни отсутствует. Он будет несущественным. Необходимо помнить о том, что станок для резки пенопласта, который использует в работе раскаленную сталь, будет функционировать, а в воздух будут выделяться токсичные пары, это указывает на необходимость использования защитной маски. Работать при этом нужно в хорошо проветриваемом помещении. Предпочтительнее производить работы по резке на улице.
Рекомендации специалиста по изготовлению станка
Изготавливая станок для резки пенопласта, вы можете не найти стола, параметры которого соответствуют вышеприведенным. В роли основания в этом случае можно использовать полотно ДСП, доску или фанеру. Технология проведения работ по сборке станка предполагает использование нихромовой проволоки, которая должна быть зафиксирована к пружинам, последние из них необходимо надеть на винты, а последний из них вкрутить в специальные стойки. Стальные стойки предварительно нужно запрессовать в крышку стола. Высота стойки и толщина основания будут зависеть от предпочтений и нужд владельца. Если толщина полотна будет равна 1, 8 см, а высота стойки составит 2, 8 см, то в полностью вкрученном состоянии винт не будет способен пройти полотно насквозь. Тогда как если его полностью выкрутить, то он сможет нарезать полотно, толщина которого равна 5 см.
Изменение параметров станка
Изготавливая станки для резки пенопласта, необходимо учесть тот момент, что в будущем возникнет необходимость производить нарезку более толстых полотен материалов, при этом короткие винты можно будет выкрутить и установить на их место более длинные. Для того чтобы произвести запрессовку, в основании нужно сделать отверстие. Его диаметр должен оказаться меньше данного показателя, свойственного стойке, разница должна составить 0,5 миллиметра. Изготавливая станки для резки пенопласта, стойки нужно вбить молотком в отверстия, но для облегчения процедуры необходимо обработать острые кромки торцов с помощью наждачной бумаги. Перед тем как приступать к вкручиванию винта в стойку, нужно выпилить под его шляпкой канавку. Для того чтобы это осуществить, необходимо зажать его конец шуруповертом, тогда как под головку следует проложить тонкий напильник, а после задействовать вращение. Канавка необходима для того, чтобы укрепить в одном положении проволоку, которая может перемещаться при корректировке. Для того чтобы проволока не провисала, удлинившись после нагревания, ее нужно зафиксировать к пружинам, а уже после к винтам. Выполняя станки для резки пенопласта, нужно подготовить все крепежные элементы, а после укрепить нихромовую проволоку. Для того чтобы обеспечить надежный контакт между ней и токопроводящим проводом, нужно применить технологию, которая называется “раскрутка с обжатием”. Медный провод должен иметь сечение не меньше 1,45 кв.мм.
Заключительные работы
На следующем этапе нужно снять изоляцию с окончания проводов на 2 сантиметра. Медные проводники должны быть накручены на проволоку в тех зонах, где она зафиксирована к пружине. Конец проволоки следует придерживать плоскогубцами, а после обмотать вокруг проводника. Для того чтобы обеспечить возможность корректировки толщины резки полотна, необходимо сделать отвод токопроводящих проводников. Исключить провисание проводов нужно методом проделывания в основании отверстия, через которое пропускается отрезок и фиксируется с обратной стороны поверхности с помощью скоб. Если вами будет производиться резка пенопласта, станок своими руками может быть с легкостью изготовлен. Провода при проведении процесса должны быть сложены вместе в виде жгута, это исключит их спутывание. На концах проводов нужно укрепить клеммы, чтобы появилась возможность подсоединить их к источнику питания.
В заключение
Если вы самостоятельно решили изготовить ЧПУ станок для резки пенопласта, то его вам будет вполне достаточно для использования в домашних условиях, если только вы не собираетесь наладить производственную линию. Скорость движения полотна при резке не должна быть излишне высокой. Если мотор работает очень быстро, тогда это станет способствовать крошению материала. Допустить этого никак нельзя, так как в данном случае не будет целесообразно изготавливать и использовать станок автоматического типа. Ведь для проведения работ все же придется потратить определенное количество сил и времени. Это необходимо учесть при выборе составляющих будущей конструкции.
станок для фигурной резки, прибор, нож
Самодельный станок для резки пенопласта
Инструмент для резки пенопласта можно изготовить своими руками в домашних условиях. Модель выбирают в зависимости от конструктивных особенностей.
Изготовление терморезака
Из лобзика и паяльника можно изготовить термонож для пенопласта:
- Главная деталь в этом устройстве — втулка. Ее изготовляют из пластины, которую предварительно оттачивают, выгибают, а затем проделывают отверстие. Отверстие необходимо для нити.
- Выходящие из отверстия провода отрезают. В местах разрыва отверстия припаивают. Получается выжигатель.
- В готовую пластину монтируется лобзик. Его разрезают на две части и закрепляют болтами сверху пластины. Нижнюю часть пластины устанавливают на основание, закрепляя саморезами.
- Втулку устанавливают в лапку.
- В основании просверливают отверстие с резьбой диаметром 5 мм.
- Чтобы нихромовый провод выпрямился, включают выжигатель и его проводами дотрагиваются до проволоки. Выжигатель начнет гудеть при слабом нагреве проволоки. Значит, она имеет слабое сопротивление, и проволоку заменяют на более тонкий вариант.
После изготовления проводят пробное разрезание.
Резак из нихрома
Отличительная черта этого устройства — способность разрезать материал двумя способами: вдоль и поперек. Он состоит из нити или проволоки. Эта часть инструмента является основной, и ее нельзя ничем заменить. Для изготовления проволоки и нити используют сплав из никеля и хрома. Чтобы разрезать лист определенной высоты, нить устанавливают в горизонтальное положение. Устройство с нихромовой проволокой разрезает толстый лист пенопласта на более тонкие части.
Пошаговая инструкция:
- В деревянный брусок вкручивают два самореза. Они располагаются на меньшем расстоянии друг от друга, чем длина нитки.
- Сверху саморезов натягивают проволоку.
- С двух сторон нитей цепляют крокодильчики блока питания. Блок питания должен быть на 1 ампер. Крокодильчики меняют местами, если устройство не заработало.
- Нагревание нити происходит, если зацеп передвинуть ближе к центральной точке.
- Из алюминиевой арматуры длиною около 50 см изготавливают основание для резака. На концах нагретой арматуры вставляют ПВХ палочки (изоляторы). Крепят их на разрезанной пополам стеклотекстолитовой полоске.
- Провода проводят к установленному основанию от электролобзика или плиткореза. К продетым в текстолите болтикам цепляют провода и стальные колечки из проволоки. С одной стороны нити привязывают пружину, а с другой стороны закрепляют кольцо.
С помощью такого аппарата можно изготавливать фигурные изделия по готовым шаблонам.
Перед тем как резать пенопласт с помощью нихрома, спираль устанавливают на необходимую высоту. Высоту отмеряют линейкой. Прибор подключают к зарядному устройству. Лист пенопласта плавно передвигают по столешнице тогда, когда струна станет горячей. Не стоит забывать, что при работе с устройством необходимо соблюдать технику безопасности.
youtube.com/embed/v2MKpd2sDxk?feature=oembed” frameborder=”0″ allow=”accelerometer; autoplay; clipboard-write; encrypted-media; gyroscope; picture-in-picture” allowfullscreen=””>Лазерное оборудование для резки полистирола
Более современным и технологичным оборудованием рассматриваемого класса является станок для лазерной резки пенопласта. Такие лазерные резаки и граверы используются для изготовления малогабаритных изделий из листовых неметаллических материалов.
Такими станками можно изготавливать различную продукцию художественного типа в виде 3Д-сувениров или элементов мебели, комнатной отделки. Ими на поверхности изделий можно наносить различные надписи и ажурные гравировки. Такое оборудование также широко используется в рекламной индустрии. Лазерные станки с ЧПУ для резки пенопласта в Россию в основном поступают из Китая с 2009 года.
Для заказа станочного оборудования такого класса нужно зайти на сайт продавца, узнать, сколько стоит аппарат, и начать переговоры с менеджером торгующей компании. Специалист даст пространную консультацию по функциональности, назначению тех или иных станков и предоставит прайс-лист на любое оборудование.
Если для начала предпринимательства у человека нет таких сумм, какие указаны напротив станков для лазерной резки с ЧПУ, можно поискать предложения б/у станков резки пенопласта. Таких вариантов на сайтах продавцов оборудования также достаточно. Нужно лишь выбрать подходящий вариант оборудования, согласовать условия начального этапа эксплуатации и гарантийный срок.
Цены на такое оборудование порой на порядок ниже, чем на новое, а его рабочие качества в основном остаются на том же уровне, что и в момент первой продажи.
Фигурная резка
Последнее время достаточно востребованной является фигурная резка пенопласта, для которой применяется терморезак. Режущим элементом в данном случае выступает нихромовая проволока, закрепляемая на оборудованной ручке из изолирующего материала. Терморезак дает возможность выполнять в пенополистироле углубления разной формы.
После подобной обработки на поверхности материала формируется оплавленная корочка, придающая большую прочность материалу, но и перекрывающая поры. Поэтому необходимо использовать понижающий трансформатор, который изготавливается самостоятельно. Только нужно приобрести специализированное трансформаторное железо.
Чтобы правильно выбрать величину тока, необходимо изготовить реостат, для чего можно использовать спираль электроплиты, предварительно растянутую. Чтобы сделать каркас обмотки, можно воспользоваться керамической или асбоцементной трубой (параметры трубы: толщина 1,5-2 см, длина 8 см). Нихромовую проволоку необходимо наматывать на трубу до полного заполнения каркаса.
Пошаговая инструкция по самостоятельному изготовлению станка и резке пенопласта
Шаг 1. Заготовка столешницы. В качестве столешницы аппарата для резки пенопласта своими руками, можно взять любой кусок ДСП нужного размера. Поверхность, по которой будет передвигаться пенопласт, должна быть гладкой. В столешнице просверливаются отверстия для стоек. В качестве стоек удобно использовать металлические штыри с резьбой диаметром 10-12 мм. Высота стоек должна соответствовать толщине листов пенопласта плюс запас по высоте. Штырь фиксируется гайками.
Для придания конструкции устойчивости, снизу к столешнице прикрепляются бруски, которые будут так же служить для безопасного прохождения электрического провода.
Шаг 2. Подключение подающих ток проводов. Снизу под столешницей провода подключаются к металлическим стержням-стойкам: провод наматывается на нижний конец штыря и прижимается болтом.
Второй конец проводов должен быть подключен к источнику питания в зависимости от выбранного способа. Самым лучшим соединением будет соединение через вилку, которая будет соединяться с розеткой ЛАТЕРа. Возможно соединение через самозажимные клеммы, а так же при помощи скрутки и пайки. Это зависит от выбранного источника питания.
Шаг 3. Закрепление нихромовой спирали. Нихромовая спираль закрепляется между двумя стойками. С одного конца спирали прикрепляется пружина (их может быть и две).
Пружина нужна для того, чтобы натягивать нихромовую нить во время работы. Дело в том, что при нагреве нихромовая нить удлиняется и провисает. Нить в таком состоянии не даст качественного реза. Поэтому нить закрепляют в изначально напряженном состоянии, так чтоб пружина была слегка растянута.
Для крепления нихромовой нити на штыре используются шайбы с внутренним диаметром немного большим чем диаметр штыря. В шайбе делается небольшое отверстие для крепления самой спирали. Также делается небольшая заточка со стороны внутреннего диаметра для того, чтоб шайба могла фиксироваться на резьбе штыря.
В одну шайбу вставляют пружину с прикрепленной к ней спиралью и одевают её на первый штырь. Вторую шайбу надевают на второй штырь и в просверленное отверстие продевают нихромовую спираль. Далее её натягивают так, чтоб пружина растянулась, и фиксируют.
Шаг 4. Резка пенопласта. Чтобы распустить лист пенопласта на два листа заданного размера, спираль выставляют на нужную высоту. Необходимое расстояние отмеряют линейкой.
Затем станок подключают к источнику питания. Нить нагревается и теперь можно резать пенопласт, плавно продвигая его вперед по столешницы.
Скорость резки зависит от температуры накаливания нити, что в свою очередь зависит от поданного напряжения и толщины самой нити. Не стоит стараться подать больше напряжение, чтобы достичь большой скорости, т.к. это может привести к быстрому перегоранию нити. Здесь опытным путем должен быть подобран баланс между напряжением, толщиной и длиной нити. Нить не должна перекаляться во время работы. При разогреве она становится красного или алого цвета. Но она не должна становиться белой – это говорит о перегреве нити и о том, что напряжение желательно снизить, иначе в таком режиме нить долго не прослужит. Конечно же, плавная регулировка легко делается, если есть в наличии ЛАТЕР. Но если его нет, то лабораторный блок питания можно сделать и из компьютерного блока питания, на видео ниже есть больше информации. После того как вы своими руками сделали этот станок для резки пенопласта, нужно убедиться, что аппарат безопасный.
Шаг 4. Резка пенопласта под углом. Иногда возникает необходимость разрезать пенопласт таким образом, чтоб одна сторона была выше, а другая ниже.
Для этого спираль выставляется под уклоном с нужными параметрами. Таким образом можно получить листы пенопласта различного сечения.
Полезное видео
youtube.com/embed/2hDira2ZEsA?feature=oembed” frameborder=”0″ allow=”accelerometer; autoplay; clipboard-write; encrypted-media; gyroscope; picture-in-picture” allowfullscreen=””>Рекомендуем вам еще:
Конструкция станка
Основанием приспособления для резки пенопласта послужил лист ДСП (древесно-стружечной плиты). Размер плиты нужно брать исходя из ширины пластин пенопласта, которые планируется разрезать. Я использовал дверку от мебели размером 40×60 см. При таком размере основания можно будет разрезать пластины пенопласта шириной до 50 см. Основание можно сделать из листа фанеры, широкой доски, закрепить струну резки непосредственно на рабочем столе или верстаке.
Натягивать нихромовую струну между двумя гвоздями предел лени домашнего мастера, поэтому я реализовал простейшую конструкцию, обеспечивающую надежную фиксацию и плавную регулировку высоты расположения струны в процессе резки над поверхностью основания станка.
Крепятся концы нихромовой проволоки за пружины, одетые на винты М4. Сами винты закручены в металлические стойки, запрессованные в основание станка. При толщине основания 18 мм, я подобрал металлическую стойку длиной 28 мм, из расчета, чтобы при полном вкручивании винт не выходил за пределы нижней стороны основания, а при максимально выкрученном состоянии обеспечивал толщину нарезки пенопласта 50 мм. Если потребуется нарезать листы пенопласта или поролона большей толщины, то достаточно будет заменить винты более длинными.
Чтобы запрессовать стойку в основание, сначала в нем просверливается отверстие, диаметром на 0,5 мм меньше, чем внешний диаметр стойки. Для того, чтобы стойки легко можно было забить молотком в основание, острые кромки с торцов были сняты на наждачной колонке.
Прежде, чем закручивать в стойку винт, у его головки была проточена канавка, чтобы нихромовая проволока при регулировке не могла произвольно перемещаться, а занимала требуемое положение.
Чтобы проточить в винте канавку, сначала его резьбу нужно защитить от деформации, надев пластиковую трубку или обернуть плотной бумагой. Затем зажать в патроне дрели, включить дрель и приложить узкий надфиль. Через минуту канавка будет готова.
Для исключения провисания нихромовой проволоки из-за удлинения при нагреве, она закреплена к винтам через пружины.
Подходящей оказалась пружина от компьютерного монитора, используемая для натяжения заземляющих проводников на кинескопе. Пружина была длиннее, чем требовалось, пришлось сделать из нее две, для каждой стороны крепления проволоки.
После подготовки всех крепежных деталей можно закреплять нихромовую проволоку. Так как ток при работе потребляется значительный, около 10 А, то для надежного контакта токоподводящего провода с нихромовой проволокой я применил способ крепления скруткой с обжатием. Толщину медного провода при токе 10 А необходимо брать сечением не менее 1,45 мм2. провода для подключения нихромовой проволоки можно из таблицы. В моем распоряжении имелся провод сечением около 1 мм2. Поэтому пришлось каждый из проводов сделать из двух сечением 1 мм2, соединенных параллельно.
После снятия изоляции с концов проводов на длину около 20 мм, медные проводники навиваются на струну нихромовой проволочки в месте ее крепления к пружине. Затем, удерживая нихромовую проволочку за петлю плоскогубцами, сделанная обвивка медного провода овивается свободным концом нихромовой в противоположную сторону.
Такой способ соединения токоподводящего медного провода с нихромовым проводом обеспечит большую площадь их контакта и исключит сильный нагрев в месте соединения при работе станка для резки пенопласта. Это подтвердила практика, после продолжительной резки пенопласта, полихлорвиниловая оболочка токоподводящего провода не оплавилась, медный провод в зоне соединения не изменил своего цвета.
Для возможности регулировки толщины резки пенопласта на приспособлении, отвод токоподводящих проводников сделан с петлей. Чтобы провода не мешали при работе, они пропущены через отверстия в основании и закреплены на обратной его стороне скобками. По углам основания прибиты такие же скобки в качестве ножек.
Токоподводящие провода резака, чтобы не запутывались, свиты между собой. На концах проводов для подключения к источнику питания, запаяны накидные клеммы.
Как правильно резать пенопласт ножом, чтобы он не крошился
Когда в процессе утепления стен, перекрытий, кровли своими руками используются плиты полимерного материала, термические резаки не всегда оправданы. Конструкции, как правило, имеют строго геометрические формы, и разрезать материал вполне можно простым ножом, главное чтобы лезвие было тонким, а его длина превышала толщину листа утеплителя. Хороший инструмент для такой работы — канцелярский нож, если предстоит резать пенополистирол небольшой толщины.
Для резки пенопласта ножом нужно выбирать длинное лезвие
Дело в том, что лезвие подобного инструмента очень тонкое и при разрезании листа большой толщина идеально ровного среза добиться вряд ли получится, на срезе могут образоваться извилины, которые не позволят сделать плотное примыкание отдельных частей утеплителя. А это приведет к образованию мостиков холода.
Кроме ножа потребуется:
- Мерная жесткая линейка или рейка идеальной формы.
- Рулетка.
- Простой карандаш, маркер.
Режут полистирол на твердом основании, чтобы лист не «играл» в руках. На поверхности полистирольной плиты делают отметки нужного размера, после чего укладывают жесткую линейку или рейку, и делают острым ножом разрез. Если длины лезвия ножа недостаточно, можно сделать разрезы с двух противоположных сторон листа, главное не сбиться с размера. Затем по разрезу лист просто разламывают. При должной сноровке работа будет проходить быстро, без лишнего шума и затрат электричества. Мусор, конечно, будет, но не так уж много, как от ножовки. Главное чтобы инструмент был очень острым и нужной длины.
Пенопласт разрезан канцелярским ножом и термическим – сравнении лини среза
Как разрезать пенопласт без использования термических приборов
Принцип резки листов пенопласта при помощи ножовки, независимо, будет это полотно по металлу или по дереву, ничем не отличается от резки ножом, главное, чтобы зубцы были мелкими, а полотно достаточной длины.
В этом случае рез будет более ровным и не образуется много мелкого мусора. Движения пилой нужно совершать плавно, без рывков. Но и при таком методе резания будет много крошек пенополистирола.
Порезать пенопластовые листы можно с использованием электрического лобзика или угловой шлифовальной машинки (болгарки). Однако при таком методе огромное количество мусора гарантировано.
Болгарка для резки пенопласта
Высокая скорость вращения диска болгарки и достаточно крупные зубья спровоцирует сильное разрушение структуры материала в месте реза. При использовании электролобзика также невозможно получить на срезе идеально ровную поверхность, за счет вибрирования пилки, которое к тому же приводит к образованию мелкого полимерного мусора.
Меньше всего образуется крошек пенопласта при его раскрое, если используется самодельный прибор для резки пенопласта. Простейший вид подобного устройства представляет собой обычную тонкую проволоку (струну), к концам которой приделаны ручки, для большего удобства. Диаметр проволоки нужно выбирать самый меньший, не более 0,5 мм. Здесь одному человеку не справиться, нужен будет помощник. Проволоку устанавливают по намеченной отметке на пенопласте и делают равномерные движения с двух сторон. В результате трения металлической проволоки о пенополистирол происходит ее нагревание и материал начинает плавиться в месте реза.
Почему возникают сложности
Пенопласт представляет собой материал, который состоит из гранул, спрессованных в определенных условиях. Хотя гранулы и спекаются между собой, они не сплавляются, что способствует простоте разъединения гранул. Такая структура и создает сложности в процессе резки материала. Если кому-то приходилось иметь дело с резкой пенопласта, то легко заметить, что листы повышенной плотности режутся проще и для этого можно использовать хорошо заточенный инструмент с тонким жалом. Резать можно с применением электроинструментов. При этом чем выше скорость движения полотна и чем меньше зуб, тем быстрее и проще осуществляется рез.
В промышленных условиях резка пенопласта осуществляется другими методами, одним из которых является гидроформирование. Тонкая струя воды подается на блок под большим давлением, что обеспечивает простоту его резки и практически не оставляет отходов. Другим методом является применение нихромовой нити. Она имеет большое сопротивление, поэтому при пропускании через нее электричества температура поднимается до определенного значения, что вызывает плавление пенопласта. На промышленных станках установлено сразу несколько нитей, которые выполняют рез в нескольких плоскостях.
ЧПУ станка СФР-Стандарт
Рассмотрим принцип работы станка СФР по программе Penop. В меню заложено программное управление станком через определенные команды кнопками. Чтобы они были с быстрым управлением, для этого сдублированы и вынесены на панель инструментов. Функционал программы позволяет создавать файлы с нужными профилями будущих фигур, их размерами и масштабом. Также программа автоматически подбирает мощность и скорость резания, температуру накаливания нитей и другие параметры станка при резке полимерного материала.
Она разрешает настроить и сохранить выбранные параметры, поэтому на агрегате производится резка без дополнительной настройки. При нанесении профиля детали, главное соблюсти замкнутость линий: чтобы начало очередного элемента было концом предыдущего. Это необходимо для того, чтобы аппарат резал заданный профиль заготовки без сбоев.
Технология самостоятельного изготовления резака
Существует немало вариантов сооружения из подручных средств эффективных резаков для пенопласта. Особой популярностью пользуются два из них – резак и станок с нихромовой нитью. Каждый инструмент достаточно прост в использовании и способен обеспечить ровный и качественный раскрой ячеистого материала.
Резак для пенопласта своими руками
В процессе изготовления режущего приспособления необходимо использовать такие материалы и инструменты:
- шуруповерт или перфоратор со сверлом;
- паяльный прибор;
- два одинаковых карандаша;
- щипцы с округлым сечением на концах;
- клей ПВА или другой термостойкий клеящий состав;
- нить нихромовая;
- две медные проволоки;
- деревянный брусок длинной в 10 сантиметров;
- изоляционная лента;
- двухместный бокс для батареек;
- провода – один метр;
- выключатель.
Для питания такого портативного резака используются две обычные пальчиковые батарейки.
Процесс изготовления
Собрав все необходимые детали можно приступать к сборке конструкции резака:
- На каждом конце деревянного бруска проделать одно отверстие соответствующее диаметру подобранного карандаша. Глубина его должна достигать половины деревянной планки. От края планки нужно сделать отступ в 1,5 сантиметр.
- В нижней части карандашей формировать отверстие для установки проволоки из меди, концы которой свернуть кольцом.
- Пластиковый бокс для батареек усадить сверху бруска на клей. Карандаши зафиксировать тем же составом в ранее проделанных отверстиях.
- Для регулировки тока на струну на деревянной планке установить выключатель.
- Два провода следует припаять к коннектору, расположенному в контейнере для батареек. Оттуда проводник тока вывести к выключателю, а затем зачистить от оплетки концы и с помощью паяльника зафиксировать к медной проволоке на каждом отдельном карандаше.
Места соединений изолировать.
- Нихромовую струну туго натянуть, продев и хорошо закрепив между медными кольцами.
В готовый резак следует вставить батарейки и можно приступать к работе. Такой инструмент способен раскраивать пенопласт толщиной до 4 сантиметров. При этом с его помощью можно вырезать несложные фигуры.
Самодельный станок
Стационарная установка для резки пенопласта позволяет более точно выполнить раскрой ячеистого изделия по намеченным линиям. В процессе обработки не нужно производить движения инструментом, а просто перемещать сам материал. Сделать станок можно своими руками.
Самодельный станок для резки пенопласта
Для изготовления стационарного резака необходимо подготовить такие приспособления:
- два длинных самореза с широкими шляпками.
- нихромовая струна;
- провода для подключения тока;
- реостат для регулировки силы заряда;
- понижающий трансформатор с напряжением в 12 вольт.
В качестве основы используется стол. Опорную часть можно сделать самостоятельно. Основным условием ее изготовления является наличие ровной гладкой поверхности. Размеры стола подбираются произвольно.
Техника изготовления
Самодельный станок собрать не составляет особой сложности:
- По центру стола обозначается продольная линия. На ее концах с двух сторон опорной плоскости фиксируются саморезы;
- Нихромовая нить натягивается между установленными винтами. С одного конца она просто фиксируется, а с другого проводится через пружину. Струна должна располагаться на высоте 10 – 15 сантиметров от уровня поверхности стола.
- Провода, исходящие от трансформатора, подсоединяются к обоим концам натянутой нихромовой нити. С одной стороны самореза, на котором закреплена проволока, подвешивается груз. Он обеспечивает хорошее натяжение режущему элементу.
В действие устройство приводится при подаче питания к трансформатору. Процесс резки происходит за счет нагревания струны. При этом она должна слишком сильно накаляться иначе получится широкий разрез.
Чтобы раскроить пенопласт следует протянуть через раскаленную нить. Ячеистая структура материала позволяет быстро и точно произвести термическую резку. Края изделия от высокой температуры запаиваются, обеспечивая ровность раскроя.
Такая резка требует осторожности и применения мер безопасности. В качестве индивидуальной защиты используются перчатки, а также маска, защищающая от паров исходящих в процессе термической обработки материал
Резку пенопласта в домашних условиях можно осуществлять любым удобным способом. Главное чтобы подобранный инструмент имел способность обеспечить ровные края и точность раскроя.
Подготовка рабочего места
Для этого стоит придерживаться нескольких основных правил:
- Поверхность должна быть освобождена от лишних предметов и обязательно ровной.
Для удобства можно использовать наклонную поверхность в виде стола для чертежей. Но это подходит для фигурной резки. Часто столы оборудуют крепежами, чтобы лист не скользил.
- Рабочее место должно быть хорошо освещено, то есть находиться возле окна или иметь всестороннее искусственное освещение, которое расположено по левую руку.
- Заранее должны быть подготовлены инструменты. Не стоит забывать об инструментах для выполнения разметки: линейка и карандаш. Защитная одежда также не станет лишней. Это перчатки, защитные очки и фартук.
- Для вырезания фигур нужно изготовить жесткие шаблоны из картона. Так процесс максимально ускорится. А все детали будут одинаковыми по размерам и формам между собой.
- Обрезки следует сразу же убирать с поверхности, чтобы мусор не мешал выполнять резку. Убирать следует даже мелкие частички, сметать их можно с помощью жесткой щетки.
Если все пункты выполнять, то уменьшится риск порчи материала, а это сэкономит финансы, которые будут тратиться на замену.
Изготовление лазерного резака
Для начала необходимо извлечь лазерный резак из привода. Эта работа не представляет никакой сложности, но придется набраться терпения и максимум внимания. Так как там содержится большое количество проводов, структура у них одинаковая
При выборе привода важно учитывать наличие пишущего варианта, так как именно в такой модели лазером можно делать записи. Запись производится при испарении тонко нанесенного слоя металла с самого диска. В случае когда лазер работает на чтение, он используется вполсилы, подсвечивая диск
В случае когда лазер работает на чтение, он используется вполсилы, подсвечивая диск.
Схема лазерной резки.
При демонтаже верхних крепежей, можно обнаружить каретку с расположенным в ней лазером, который способен двигаться в двух направлениях
Ее следует осторожно извлечь путем откручивания, тут присутствует большое количество разъемных устройств и шурупов, которые важно аккуратно снять. Для дальнейшей работы необходим красный диод, при помощи которого осуществляется прожиг
Для его извлечения будет необходим паяльник, а также нужно с аккуратностью убрать крепежи
Важно взять на заметку, что незаменимую деталь для изготовления лазерного резака нельзя встряхивать и ронять, в связи с этим, извлекая лазерный диод, рекомендуется проявлять осторожность
Для его извлечения будет необходим паяльник, а также нужно с аккуратностью убрать крепежи
Важно взять на заметку, что незаменимую деталь для изготовления лазерного резака нельзя встряхивать и ронять, в связи с этим, извлекая лазерный диод, рекомендуется проявлять осторожность
Как будет извлечен главный элемент будущей модели лазера, необходимо все тщательно взвесить и придумать, куда его поместить и как к нему подключить электропитание, так как для диода пишущего лазера необходимо намного больше тока, чем для диода от лазерной указки, и в этом случае можно использовать несколько способов.
Далее заменяется диод в указке. Для создания мощного лазера уз указки должен быть извлечен родной диод, на его место необходимо установить аналогичный из CD/DVD-RW привода. Указка разбирается с соблюдением последовательности. Она должна быть раскручена и разделена на две части, сверху располагается деталь, которую нужно заменить. Старый диод извлекается и на его место устанавливается требуемый диод, который можно закрепить с помощью клея. Бывают случаи, когда при удалении старого диода могут возникнуть трудности, в этой ситуации можно воспользоваться ножом и немного потрясти указку.
Схема лазерной указки.
Следующим действием будет изготовление нового корпуса. Чтобы будущий лазер можно было удобно использовать, подключить к нему питание и для придания ему внушительного вида можно применить корпус фонарика. Устанавливается переделанная верхняя часть лазерной указки в фонарик и подводится к нему питание от аккумуляторных батареек, которое подключается к диоду
Важно не перепутать полярность питания. Перед сборкой фонарика стекло и части указки нужно извлечь, так как оно будет плохо проводить прямой ход луча лазера
Последним этапом является подготовка к применению. Перед подключением необходимо проверить прочность закрепления лазера, правильность подключения полярности проводов и ровно ли установлен лазер.
После совершения этих нехитрых действий лазерный резак готов к использованию. Такой лазер можно использовать для прожига бумаги, полиэтилена, для розжига спичек. Область применения может быть обширна, все будет зависеть от фантазии.
Станки для фигурной резки пенопласта
Станки для фигурной резки пенопласта, с использованием современных, компьютеризированных технологий, позволяют создавать, практически, любые изделия самой сложной формы, быстро, аккуратно и относительно недорого. 3D фигурная резка пенопласта используется для создания: объемных букв, логотипов (3D логотипов), вывесок, графики, надписей для наружной и внутренней рекламы, реквизит магазинов и оформление витрин, выставочных стендов, ярмарочных киосков, элементов декора, декорации, например, для театра или кино, P. O.P. дисплеев для точек продаж, муляжей товарной продукции, тематических реквизитов, архитектурных масштабных моделей, изоляций труб, колонн, форм сборных железобетонных конструкций и т.д.
Сделайте свои идеи реальностью …
ПРИМЕНЕНИЕ СТАНКОВ
ЧПУ станки для фигурной резки пенопласта могут быть использованы для резки самых разнообразных изделий и могут вырезать практически всё что угодно из вспененного (EPS) или экструдированного (XPS) полистирола.
Некоторые из наиболее распространенных применений:Предел станков это ваше воображение!
Формы, изготовленные при помощи термической резки (метод горячей струны), не подвергаются температурному расширению, поэтому они не могут треснуть на морозе или деформироваться от жары.
- НАДПИСИ И 3D ЛОГО — Сколько раз вы сталкивались с проблемой создания сложных 3D-логотипов? И все известные методы, такие как резка пилой, ножом, фрезой казалось бы работают, но требуют последующей обработки материала, оставляют много пыли и мелкой стружки, и как следствие требуют дополнительных затрат.
Наши ЧПУ станки выполнят такие работы легко, быстро и с чистой, готовой для дальнейшей покраски поверхностью.
- АРХИТЕКТУРНЫЕ ЭЛЕМЕНТЫ — Архитектурные элементы из пенополистирола, такие как: молдинги, наконечники, перила, замковые камни, шапки парапетов, балясины, лепнины, все больше и больше набирают популярность в дизайнерских мастерских и архитектурных студиях. В конечном виде элементы могут быть покрыты укрепляющей сеткой, грунтом или раствором и окрашены в необходимый цвет. Небольшой вес конструкций, легкий монтаж, точность изготовления и экологическая чистота делают архитектурные элементы из пенопласта незаменимой частью любого дизайна.
- ВНЕШНЯЯ ИЗОЛЯЦИЯ СТЕН — ЧПУ станок для резки пенопласта на строительной площадке? Почему бы и нет? Станки выполнены из алюминиевых профильных систем, что позволяет очень быстро и без особых усилий разобрать/собрать станок в любой мастерской или на строительной площадке. Это лучший способ изготовления внешней изоляции стен на месте, что приводит к экономии рабочего времени и высокому качеству термоизоляции, а так же повышает Ваш профессиональный уровень перед клиентом или заказчиком.
- ЯРМАРОЧНЫЕ, КИНО И ТЕАТРАЛЬНЫЕ ДЕКОРАЦИИ — Нет полезней способа при создании ярмарочных киосков, кино и театральных декораций чем ЧПУ термическое оборудование (метод резки горячей струной). Скорость, чистота и точность резки станков с ЧПУ управлением позволяет создавать каждую декорацию и сценографию в кротчайшие сроки и не тратя много денег.
ЧТО ТАКОЕ ЧПУ?
ЧПУ станок для фигурной резки пенопласта представляет собой компьютер-управляемое устройство (Числовое Программное Управление) для вырезки любых форм из вспененных или экструдированных пенополистиролов. Нагретая проволока (как правило это сплав Нихрома) перемещается по осям Y и X благодаря микро-шаговым двигателям (приводами), управляемых компьютеризованной системой. Это позволяет обеспечить безупречную точность, высокую скорость процессов обработки и неизменно отличное качество.
Точные механизмы и совершенное электронное управление движением, позволяют оператору вырезать любую форму, пока ее размеры соответствует размерам материала. Существует также возможность проектирования и резки нескольких различных проекций одной и той же формы, что приводит к очень привлекательным 3D фигурам. Поворотный стол позволяет вырезать, например, сферы, токарный станок незаменим в резке колонн, еще больше возможностей приходят с использованием устройства для фасонного инструмента (проволоки).
СОФТ УПРАВЛЕНИЯ
Уникальное программное обеспечение, сделанное специально для наших ЧПУ станков для резки пенопласта, поставляется бесплатно со всеми P60, T-Series! и MW-Series! моделями. Софт имеет очень простой и понятный интерфейс, поэтому даже самый не опытные пользователь сможет легко и быстро научится использовать софт в считанные часы. Базовая версия насчитывает 11 языковых версий.
- Поддержка форматов:
— HPGL.plt (e.g. CorelDraw)
— dxf (e.g. AutoCad)
— RAW 3D (e.g. Rhinoceros 3D)
— EPS/AI (e.g. AdobeIllustrator)
— dxf 3D (e.g. AutoCad) - Авто связь объектов и генерация путей.
- Настраиваемые параметры.
- Полный контроль аксессуаров: Поворотный стол и Токарный станок.
- Ручное управление всеми осями (X, Y и Z).
- Неограниченные материальные и экономичные параметры конфигураций.
- Авто остановка при обрыве; продолжение после замены проволоки.
- Передовой модуль дублирования.
- Моделирование процесса резки.
- Неограниченные бесплатные обновления.
- Наличие ПК
- Windows XP, Vista, 7, 8, 10
- Любые грфические программы с HPGL.plt или .dxf экспортом, например, Corel Draw, AutoCAD, и т.
д.
- Свободный последовательный порт (USB)
ДОСТУПНЫЕ МОДЕЛИ
Мы предлагаем станки для фигурной резки пенопласта в 3 конфигурациях:
- P60-Series! = 1 режущая проволока, длина проволоки постоянна 60 см.
- T-Series! = 1 или 2 режущих проволоки, длина проволоки: 60, 130, 150, 250 или 300 см. Огромный выбор дополнительных аксессуаров.
- MW-Series! = 10 режущих проволок, длина проволоки: 130, 250 или 300 см
В P60-Series! длина проволоки всегда 60 см (Z ось). В двух других сериях («T» и «MW»), цифры после букв T или MW (например, T 1300, T 3000, MW 2500 и т.д.) = длина проволоки в мм (Z ось).
Оси:
- Длина проволоки = ширине машины = Z ось
- Высота машины = Y ось = у наших машин это всегда, примерно, 122-129 см
- Последний размер это X ось = длина машины (не путать с длиной проволоки = Z ось).
Z ось = ширина машины = длина режущей проволоки
X ось = длина машины
Y ось = высота машины
Станки для фигурной резки пенопласта выпускаются в 3-х различных длинах или 3 варианта оси X:
- Small (Малая) модель составляет 122 см длиной (X ось)
- Medium (Средняя) модель составляет 244 см длиной (X ось)
- Large (Большая) модель составляет 305 см длиной (X ось)
Примеры:
- P60 Small — длина проволоки/ширина машины = 60 см, длина машины = 122 см
- T1300 Medium – длина проволоки/ширина машины = 130 см, длина машины = 244 см
- T1500 Medium – длина проволоки/ширина машины = 150 см, длина машины = 244 см
- MW3000 Large –длина проволоки/ширина машины = 305 см, длина машины = 305 см
Если Вы не знаете какая модель будет отвечать вашим потребностям, или не уверены в своём выборе, пришлите нам запрос с информацией (требуемые размеры, количество режущих проволок и необходимость в дополнительном оборудовании), и мы прокомментируем Ваш выбор или порекомендуем Вам конкретную модель именно под Ваши нужды.
Аксессуары
В зависимости от применения, мы можем предложить ряд аксессуаров, которыми вы можете оснастить ваш ЧПУ станок для резки пенопласта. В списке ниже, представлена базовая информация о доступности и использовании дополнительных опций для различных моделей.
Поворотный столДоступность: станки серии «P60, «T-Series!» и «MW-Series!
Использование: последовательная резка (2.5 D) для нестандартных симметричных и не симметричных форм, сфер, колонн, резки под углом и т.д.
Токарный станокДоступность: станки серии «P60, «T-Series!» и «MW-Series!
Использование: круговая резка, все виды колонн, резьбы, канавки и т.д.
Устройство для Фасонной проволокиДоступность: станки серии «P60, «T-Series!» и «MW-Series!
Использование: все виды гравировки, точение, полые и симметричные формы и т. д.
Доступность: станки серии «T-Series!»
Использование: 2 режущие проволоки позволяют вырезать по 2 идентичных изделия одновременно.
Пневматический натяжитель проволокиДоступность: станки серии «T-Series!» для 2.5 и 3.0- метровой ширины
Использование: взамен стандартного пружинного натяжителя для достижения более высоких скоростей и качества резки.
Проволока из титанового сплаваДоступность: станки серии «T-Series!» и «MW-Series! шириной от 1.3 метра и больше.
Использование: взамен стандартной проволоки NiCr для достижения более высоких скоростей и качества резки.
Независимое управление осями резкиДоступность: станки серии «T-Series!»
Использование: для резки любых конусообразных форм.
ГАЛЛЕРЕЯ
РЕЖУЩАЯ НИТЬ
При нагреве, температура режущей нихромовой проволоки, может достигать 300 — 500 градусов Цельсия. В зависимости от ширины станка для фигурной резки пенопласта (т.е. длины режущей проволоки) рекомендовано использовать нихромовую проволоку следующих диаметров: 0.15, 0.25, 0.45 и 0.55 мм. Станоки для фигурной резки пенопласта поставляются с бесплатной 100-ой граммовой катушкой режущей проволоки.
Мульти-проволочные станки для фигурной резки пенопласта MW-Series! и T-Series!, могут быть оснащенные пневматическими натяжителем проволоки или более сильными прижинными натяжителями, что позволит использовать проволоку более высокого качества из титанового сплава. Хотя проволока из титанового сплава немного дороже чем стандартная нихромовая проволока NiCr, периодичность ее замены реже (в среднем, она служит в 5-6 раз дольше, чем проволока NiCr) и она гораздо устойчивей к растяжениям при высоком нагреве, что приводит к более высокой скорости и улучшению качества резки. Проволока из Титанового сплава доступна, за дополнительную плату для всех MW-Series! и T-Series! станков шириной 1.3 метра и шире.
ВЫБОР ПЕНОПЛАСТА
Существуют два типа пенопласта, наилучшим образом подходящих для обработки станками для резки пенопласта с горячей проволокой:
Вспененный полистирол (EPS) пожалуй наиболее распространенный в повседневной жизни — эту белую пену можно увидеть в стаканчиках для горячих напитков, холодильниках, термоизоляции, упаковке и т.д. Пенопласт состоит на 98% из воздуха и на 2% из полистирола. Гранулы полистирола нагревают паром так, что они быстро расширяются (вспениваются) и образуют блок (в специальной форме) низкой плотности. Такой материал является не дорогим и легким,—обычно весом 15-30 кг на метр кубический. Вспененный полистирол не теряет свих свойств со временем и может быть полностью переработан, с последующим использованием вторично.
Экструдированный полистирол (XPS) имеет тот же химический состав что и вспененный, но производится по другой технологии, в результате полученная пена имеет меньшие воздушные карманы и более однородна. Часто бывает розового, голубого, зеленого цвета и т.д. Экструдированный полистирол идеально подходит для изготовления любых демонстрационных панелей.
Есть несколько причин, по которым указанные выше материалы имеют столь широкое применение. Как правило, пенопласт это:
Дешевизна.
Малый вес.
Идеально подходит для наружных и, как в случае с материалом EPS, внутренних работ.
Возможность нанесения различных покрытий (краски на водной основе, цементные покрытия, металические покрытия и т.д.).
Длительное использование — если покрытия нанесены должным образом, эксплуатация может длиться десятилетиями.
ГАРАНТИЯ
Все ЧПУ станки для фигурной резки пенопласта поставляются с «неограниченной» 5-летней гарантией.
- Гарантия распространяется на все электронные и механические детали, а также на программное обеспечение.
- Единственное, на что не распространяется гарантия, это режущая проволока.
- Все запасные части представлены на EXW (ex-works) основе.
- Большинство запасных частей отправляются клиентам в тот же день (или на следующий день), когда подтверждается гарантийный случай.
Для более подробной информации, пожалуйста, свяжитесь с нами!
ОТПРАВИТЬ ЗАПРОС
ОТПРАВИТЬ ЗАПРОС
ДОСТАВКА ОБОРУДОВАНИЯ
ДОСТАВКА ОБОРУДОВАНИЯ
Мы осуществляем продажу и доставку ЧПУ оборудования по всему миру!
Каждый станок для фигурной резки пенопласта расценивается как отдельный проект и в зависимости от комплектации станка его производство, сборка может занять от 3 до 6 недель. Для более подробной информации, свяжитесь с нами!
Мы базируемся в Эстонии, в городе Таллинн и основной наш склад так же находится в Таллинне по улице Петербури тээ 65 (Петербургское шоссе 65). ЧПУ станки для фигурной резки пенопласта мы отправляем по всему миру. Сроки доставки варьируются от страны к стране, они также зависят от того, насколько эффективно работают Ваши местные курьерские и почтовые организации. Тем не менее, приблизительная оценка 2-16 рабочих дней для стран Европы. Начиная от 7 рабочих дней доставка в страны СНГ. Обращаем Ваше внимание на то, что стоимость доставки рассчитывается отдельно для каждого конкретного заказа и зависит от направления и способа доставки.
Пользуемся услугами следующих транспортных компаний: DHL, UPS, DPD, Omniva и Itella Logistics,
“Your specialist for insulation cutting systems!”
Резак для пенопласта своими руками из паяльника.

Пенопласт – хороший теплоизолятор, отличающийся долговечностью и небольшим весом. Он используется для создания разнообразных форм, заготовок и моделей, в качестве превосходного утеплителя. Работать с ним достаточно просто. Но нередко такой материал выпускается в виде блоков с большими геометрическими параметрами. Разрезать их пилой либо ножом очень неудобно. Изделия крошатся, что нарушает их структуру.
Проблему с раскроем теплоизоляционного материала решает резак для пенопласта, нередко называемый резчиком. Его можно приобрести в строительном магазине либо сделать самостоятельно. Во втором случае домашний мастер получает в свое распоряжение инструмент, который подходит ему по всем параметрам.
Элементарный резчик – полчаса и готов!
Самый простой инструмент для раскроя листов пенопласта (вспененного полистирола) изготавливается без малейших затруднений при помощи 4–5 батареек для электрофонарика и обычной гитарной струны. Процесс создания резчика будет следующим:
- элементы питания последовательно соединяются между собой в один блок;
- к торцам получившегося модуля фиксируется струна для гитары.
В результате этих действий получается инструмент с электрической замкнутой дугой. Ток, проходя по ней, станет разогревать струну. На участке ее соприкосновения с раскраиваемым материалом будет наблюдаться процесс плавления и разрезания листа пенополистирола на две части.
Для работы описанного самодельного термоножа необходим нагрев струны до 130–150 °С. С помощью такого простейшего инструмента можно раскроить 1–3 блока пенопласта. Применять его для резки большого количества листов нецелесообразно из-за того, что элементы питания будут очень быстро садиться.
Разновидности электрических термоножей и их особенности
Если мастер использует пенопласт регулярно и выполняет большие объемы работ, ему желательно сделать своими руками инструмент, который функционирует от бытовой электрической сети. Такие самодельные термические ножи, не требующие отдельных зарядных устройств, используются для:
- линейной резки;
- фигурного раскроя.
В качестве рабочего термоэлемента в них применяется нихромовая нить либо пластина из металла. Обязательным блоком подобных приборов является трансформатор, понижающий напряжение (рисунок 1). Его обмотки должны соответствовать далее приведенным требованиям:
- сечение кабелей – от 1,5 мм;
- напряжение – от 100 В (первичная обмотка), 15 В (вторичная).
Специалисты рекомендуют подключать понижающий аппарат к автотрансформатору (ЛАТР), который позволяет плавно настраивать выходное напряжение. Если приобретать такой дорогостоящий прибор нет желания, можно поступить иначе:
- поставить переключатель на отводы вторичной обмотки;
- оснастить понижающий трансформатор реостатом.
Устройство для линейной резки – как сделать?
Самодельный термонож для раскроя плоских листов вспененного пенополистирола представляет собой простую конструкцию. Принцип ее создания поймет любой народный умелец.
Основа сооружения – рама, сделанная из стального профиля либо деревянных брусков. В нижней ее части монтируется рабочая поверхность из древесностружечных плит, фанеры большой толщины. Некоторые мастера используют листы текстолита для ее сооружения.
Функцию рабочей поверхности может выполнять и обычный стол либо верстак. Тогда необходимость в раме отпадает. А сам процесс сооружения конструкции выглядит следующим образом:
- На столе (иной ровной поверхности) монтируются две вертикальные опоры, которые закрепляются изоляторами.
- К последним через электроконтакты подключают трансформатор для понижения напряжения.
- Между изоляторами протягивается нихромовая проволока. К ней подвешивается специальный груз. Он нужен для натяжения нити.
Функционирует такой резак для пенопласта просто. Электроток проходит по нити, разогревает ее, что приводит к растяжению проволоки. Груз не позволяет последней провисать.
Нагретая нихромовая нитка легко разрезает по горизонтали блок пенопласта, который перемещается руками. В результате этого получаются плоские листы утепляющего материала. Их толщина определяется дистанцией, отделяющей натянутую проволоку от рабочей поверхности стола.
При выполнении описанной операции важно обеспечить подачу пенополистирола с максимально равномерной скоростью.
В случаях, когда материал необходимо кроить вертикально, конструкция резчика немного видоизменяется. Раму требуется дополнительно оснастить лапой-держателем. Подвесить к нему нихромовую нить и грузик, пропустив последний через предварительно просверленное в столе отверстие. В него желательно установить полую трубу из металла, которая защитит мастера от ожогов при нагревании проволоки.
Правила изготовления инструмента для фигурного раскроя
Если резке в домашних условиях будут подвергаться большие по толщине либо геометрическим размерам листы пенопласта, не помещающиеся на рабочую поверхность из-за своих параметров, рекомендуется сделать термонож из слесарной ножовки или ручного лобзика. Работы выполняются так:
- Режущее полотно лобзика (ножовки) снимается.
- К ручке инструмента подсоединяется электрокабель.
- Нихромовая проволока изгибается под заданным углом.
- Фигурно согнутая нить устанавливается на место, где раньше размещалось полотно, и фиксируется гайками и винтами.
Все металлические элементы на самостоятельно сделанной конструкции изолируются. При желании можно сразу изогнуть под разными углами несколько нихромовых полотен. Тогда фигурная резка будет проходить более комфортно.
Пенопласт – это долговечный, легкий и очень хороший теплоизоляционный материал. Выполнять с ним работы очень просто. Но есть и некоторые нюансы в работе с данным материалом.
Поскольку его изготавливают в виде плит больших размеров, то очень часто нужно прибегать к их обрезке. Сделать это можно, используя и обычный нож, но им, как ни старайся аккуратно это выполнить, не получится.
А все потому, что при механическом воздействии будет происходить нарушение структуры пенопласта. Именно потому специалисты рекомендуют для таких действий использовать исключительно резчик или, как еще его называют, резак для пенопласта.
Такой многофункциональный инструмент можно, конечно же, и купить, но если вы сделаете его своими руками, то сможете приспособить под свои потребности и, конечно, же, сэкономите деньги.
Если же вы планируете работать с резаком в промышленных целях, то все же лучше купить электрический прибор, который будет предназначен для больших и частых нагрузок.
Как сделать самостоятельно
Необходимость в резаке может возникнуть в любой момент, если вы довольно часто делаете какие-либо дела по дому. Возможно, кто-то сталкивался с тем, что необходимо сделать деталь, прибегая к специальной форме для отливки эпоксидной смолой.
И чтобы выполнить это, нужен будет кусок пенопласта. К примеру, можно использовать пенопласт от упаковки телевизора. На нем необходимо расчертить с помощью линейки, циркуля и шариковой ручки места, где в дальнейшем надо будет сделать отверстия.
Вот тут-то и возникает потребность в электрическом резаке. Ведь выполнить данное действия, не испортив лист пенопласта, будет сложно без такого инструмента. Рассмотрим один из вариантов, как же сделать устройство такого типа в домашних условиях.
Самодельный прибор для порезки может быть различной конструкции. Именно от нее и типа резки будет зависеть, как именно резак справляется с поставленными целями.
Виды
Перед тем как начинать делать резак, вам стоит определиться, с какой целью он вам нужен, ведь в зависимости от целей, они делятся на несколько групп:
- с рабочей пластиной из металла ;
- для линейной резки;
- для фигурной резки.
Этапы создания
Поскольку линейная резка самая распространенная, давайте рассмотрим именно этот вариант подробнее:
- Режущая часть. Для этого понадобится проволока из нихрома, приблизительно спираль с диаметром в 0,6 мм. Ей можно взять от старых электроплиты или иных нагревательных электроприборов.
Длина такой проволоки должна составить 14 см (ее сопротивление будет составлять 2 ом).
- Применение трансформатора. Чтобы все было верно, первым делом надо произвести расчет напряжения и тока для нагрева режущей части. Выполнить это можно, используя формулу – закон Ома I=U/R. Таким образом, можно определиться с мощностью трансформатора питания.
- Изготовление резака. Основу можно выполнить из какого-либо металла, но его длина должна быть не менее 11 см. Дальше в торец надо прикрепить изолятор – пластинку текстолита. А теперь по краям пластины закрепить контактные группы, их можно изъять из электророзетки. Именно в эти контакты можно будет закреплять спирали с разной формой.
- Как работает резак. После того, как резак будет включен в сеть, его спираль будет нагреваться и станет слегка красноватого цвета. Именно это и имеет значение, так как подогретый резак даст возможность легко и быстро порезать пенопласт, который при этом не будет шелушиться.
Важно знать: получив такой прибор, уже за три минуты можно будет вырезать необходимую форму из листа пенопласта.
В обязательном порядке соблюдайте все правила безопасности, чтобы не травмировать себя и окружающих. Ведь мощности резака достаточно, чтобы повредить какую-либо часть тела при работе. А подключение к электричеству еще больше увеличивает риск травмирования.
Поэтапное изготовление терморезака
Изготовить терморезак можно с использованием выжигателя или паяльника и старого лобзика. Рассмотрим изготовление такого устройства пошагово:
- Втулка. Изначально нужно сделать основное и самое сложное – втулку. Итак, для этого пластину надо изогнуть, выточить. Дальше во втулке надо проделать отверстие, туда будет в дальнейшем вставлена нить.
- Выжигатель. Нужно отрезать провод, который ведет к отверстию, и взять подходящие разъемы, потом припаять в место разрыва.
Обратите внимание: такие участки в обязательном порядке необходимо изолировать.
- После того, как все выполнено можно подключить терморезак. Старый лобзик распилить пополам. В верхнюю часть надо прикрепить заблаговременно подготовленную пластину-лапку на винты. А вот низ крепим к основанию, используя саморезы.
- Вставить втулку в лапку. Теперь с особым вниманием надо из отверстия по отвесу, либо угольнику, отметить точку под отверстием втулки. Далее сверлим отверстие в основании. Диаметр отверстия в основании должен составлять около 5 мм.
- Терморезка. Итак, когда все готово, надо расправить нихромовый провод. Для этого вам стоит включить на всю мощность выжигатель и проводами от него коснуться нихромки. Все нужно сделать таким образом, чтобы между проводками осталось расстояние, равное высоте устройства. Если нить не нагревается, но при этом выжигатель начинает гудеть, найдите более тонкую проволоку. Это необходимо, потому что у выбранной вами недостаточное сопротивление.
Возьмите на заметку: нихром должен быть горячий, но не должен нагреваться до красна. Если струна стала красного цвета, необходимо уменьшить посредством регулятора ее нагрев. В том случае, если нихром красный даже на минимуме, то выше пружинки на 5-10-15 см нихромовой проволоки стоит оставить компенсатор. И только после этого можно подцеплять контакт.
- Работа прибора. С предварительно установленной направляющей вам нужно нарезать плашки из пенопласта заданной толщины, также вы можете сделать форму фигурной.
Применение
Если вы делаете ремонт или занимаетесь резкой по дереву, или вам нужно порезать кусок фанеры, то вам очень пригодится электрорезак, который к тому же можно использовать даже для порезки плотной ткани.
Если вы думаете, что для всех вышеперечисленных действий вам достаточно будет применить термонож, либо хватит ножовки, то вы ошибаетесь.
Ведь ножовка не сделает края ровными и не рваными, как выходит в случае с резаком.
При строительных и отделочных работах возникает вопрос, чем осуществить резку пенопласта так, чтобы он не крошился. Для этого используют специальные инструменты и приемы, которые выбираются на основании размеров пенопластовой плиты. Такие резаки можно приобрести в магазине или изготовить самостоятельно. Чтобы сделать инструмент своими руками, не потребуются специальные знания или навыки.
Нихромовый резак своими руками
Осуществляется резка пенопласта струной, раскаленной до +120…+150°С и плавящей материал. Благодаря этому срез ровный, а пенопласт не крошится. На таких приспособлениях устанавливается нихромовая нить, через которую пропускается электричество. Сделать простой резак можно своими руками. Он отличается от станка портативностью и компактностью, поэтому температуру нагрева нихромовой проволоки на нем регулировать нельзя.
Необходимые инструменты и материалы
Чтобы сделать резак с нихромовой проволокой для резки пенопласта, понадобятся такие инструменты и материалы:
- небольшой деревянный брусок;
- шуруповерт и сверло;
- 2 карандаша;
- 2 отрезка медной проволоки;
- круглогубцы;
- термоклей или ПВА;
- изолента;
- коннектор для батареек;
- выключатель;
- 1 м проводов;
- паяльник;
- нихромовая нить.
Последняя продается в магазине радиодеталей. Также ее можно взять со старых нагревательных элементов от фена, кипятильника, бойлера и пр.
Самодельный резак для пенопласта
Самодельный резак предназначен для незначительных работ. Раскроить им весь лист пенополистирола не представляется возможным. Чтобы осуществить резку пенопласта в домашних условиях, необходимо:
- В деревянном бруске длиной 10-11 см сделать 2 отверстия. Они должны совпадать с диаметром карандашей. От края нужно отступить на 1-1,5 см. Углубление должно быть немного глубже половины бруска, чтобы зафиксировать карандаши. Благодаря такому расстоянию можно порезать лист пенопласта практически любой толщины.
- Оба карандаша вклеить в отверстия с помощью термоклея или ПВА.
- В каждом из карандашей сверху сделать небольшое отверстие для медной проволоки.
- Медную проволоку согнуть круглогубцами таким образом, чтобы на ее концах получились маленькие кольца. После этого установить в отверстия в карандашах.
- Коннектор для батареек приклеить перпендикулярно к деревянному бруску. Дополнительно он будет исполнять роль ручки.
- На брусок наклеить выключатель, чтобы можно было обесточивать струну.
- Затем подключить к коннектору 2 провода. После этого соединить с выключателем, а потом каждый вывести на отдельный карандаш. Чтобы провод не провисал и не мешал работе, его фиксируют изолентой. Чтобы обеспечить надежное качество подключения, нужно припаять провода к коннектору. Места соединений нужно изолировать с помощью термоусадочной трубки или изоленты.
- Второй конец каждого провода очистить от оплетки и прикрутить к медной проволоке. Соединение припаять.
- Нихромовую нить продеть в кольца из медной проволоки и закрепить на них. Струна должна быть туго натянута между карандашами. При нагревании она растягивается и немного провисает. Чем сильнее натяжение, тем меньше провисание.
- В коннектор вставить батарейки и приступить к резке пенопластовых листов.
Таким образом можно сделать простой прибор для резки пенопласта своими руками. И еще один вариант изготовления станка смотрите на видео:
Станок для резки пенопласта своими рукам
Станки для резки удобнее тем, что в них режущая нить зафиксирована и нужно двигать только пенопласт. Это позволяет повысить точность движений. При изготовлении понадобятся такие же инструменты и техника, как и в предыдущем случае.
Для начала нужно сделать столик, который представляет собой деревянное основание с небольшими ножками. Стол должен быть ровным и гладким, чтобы не допустить деформации пенопласта. Размеры основания выбираются произвольно. Перпендикулярно к столешнице прикручивается брусок, а к нему под углом 90° крепится деревянная перекладина. Затем необходимо усилить конструкцию перемычкой.
Угловой линейкой отмечается место, в которое будет уходить нить накаливания. Если поверхность достаточно ровная, это можно сделать с помощью отвеса. Для этого в торец вкручивается саморез с широкой шляпкой, а на него накручивается нить с грузом. В выбранном месте сверлится отверстие диаметром 6 мм. Чтобы струна не обжигала дерево, устанавливается пластина из текстолита или металла. Следует поставить материал заподлицо с поверхностью.
В отверстие продевается проволока, нижний конец которой надевается на саморез. Шуруп вкручивается рядом с отверстием. Длина спирали должна быть такой, чтобы при нагревании последняя становилась красной. Поскольку при высоких температурах проволока удлиняется, необходимо использовать компенсирующую пружину, чтобы избежать провисания. На верхний саморез насаживается пружина, а к ней крепится нихромовая нить.
К концам нити подсоединяется источник энергии, которым может служить аккумулятор с напряжением 11,7-12,4 В. Чтобы регулировать этот показатель, используют схему тиристорного регулятора. Регулятор можно взять от электрической болгарки. Также контролировать напряжение можно с помощью спирали на станке для резки пенополистирола.
Эта спираль устанавливается на деревянном бруске, к которому крепится верхний край нити накаливания. Соединяется с проволокой последовательно. Ее функция заключается в удлинении нихромовой нити и, соответственно, уменьшении напряжения. Достичь этого можно, меняя место подключения к нихромовой спирали. Чем меньше расстояние, тем сильнее греется нить и больше плавится пенопласт.
Если к станку подключается трансформатор, он должен иметь гальваническую развязку. При этом должен использоваться трансформатор с отводами.
Для плавных и ровных срезов нужно сделать направляющую рейку. Ее изготавливают из бруска или любого другого ровного материала.
С помощью такого несложного станка осуществляется резка пенопласта своими руками. Дополнительно можно сделать разные приспособления. Можно изготовить во время ремонта стусло своими руками или лоток, которые помогут ровно порезать материал под нужными углами.
Технология 3D-резки пенопласта
Пенополистирольную продукцию стали широко использовать в маркетинговых и декоративных целях. Из пенополистирола делают логотипы компаний, вырезают названия, различные фигурки, элементы декора и пр. Поэтому 3D-резка приобрела широкую популярность. Использование пенопласта позволяет сэкономить средства и в то же время получить качественный и долговечный продукт.
Объемная резка осуществляется на специальных станках. Они раскраивают материал с помощью длинных струн или лазера и позволяют придать пенопласту любую форму.
Фигурная резка пенопласта
Фигурная резка пенополистирола осуществляется на специальных станках. Некоторые из них оборудованы ЧПУ. При работе на станке толщина листов пенопласта не имеет значения. Однако для несложной резки можно использовать простой резак, сделанный своими руками.
Тем, кто задумал утеплить квартиру или новопостроенный дом своими руками, обязательно следует ознакомиться со способами, которыми осуществляется резка пенопласта в домашних условиях, ведь это один из самых популярных и доступных способов изоляции.
Пенопласт – это вспененный материал и по большей части состоит из воздуха, поэтому он очень легкий и с ним просто работать. Однако не стоит думать, что никаких проблем не возникает, ведь кроме всего пенопласт и довольно хрупкий материл. Поэтому если воспользоваться электрической болгаркой, то на ровные края надеяться не стоит, к тому же все помещение и площадка будет усыпана раскрошенным пенопластом.
Каким бы острым ни был нож, материал все равно будет крошиться. Безусловно, это незначительный дефект и листы будут пригодны к использованию, а вот уборка превратится в хлопотное мероприятие . Из такого положения есть выход, вы можете воспользоваться термоножом. При этом края материала оплавляются и он не крошится. Но вот незадача, стоит такое приспособление очень много, но в принципе можно нагреть и обыкновенный нож. Однако в этом случае надо быть весьма аккуратным, чтобы не получить ожога, да и работа существенно затянется.
Для этой цели можно воспользоваться различным режущим инструментом, например, болгаркой, только тогда следует использовать самый тонкий диск. Очень часто строители пользуются и простым острым ножом. Иногда советуют брать и ножовку с очень мелкими зубьями, но последний метод весьма сомнительный. Кроме того, в магазинах продают специальные термоножи, предназначенные для работ с пенопластом.
Термонож нагревается до 600 °С всего за 10 секунд. Однако этот инструмент довольно дорогостоящий, поэтому далеко не всегда есть смысл покупать его.
Выходом же из положения во многих случаях станет приспособление для резки листов пенопласта, сделанное самостоятельно. Вероятно, оно несколько громоздкое, зато при наличии необходимых компонентов абсолютно бесплатное и всегда доступное. А если вам придется заниматься масштабной работой, например, у вас впереди , который вы возвели для своей большой семьи, то вопрос, как удобно разрезать пенопласт, да еще много и быстро, не всплывет на протяжении всего мероприятия, насколько бы оно ни затянулось.
Для того чтобы собрать резак для пенопласта, понадобится столешница, по паре пружин, винтов М4 и стоек длиной в 28 мм, а также нихромовая нить, которая и будет выступать в качестве режущего инструмента. Сначала делаем в основании два отверстия, запрессовываем в них стойки, а у основания шляпки винта пропиливаем небольшую канавку, благодаря которой нить будет надежно фиксироваться в заданном положении.
Когда все собрано, крепим к винтам струну, но так как она может провисать во время нагревания, следует соединять ее через пружины, тогда нить будет всегда находиться в натянутом положении. Источник же питания подсоединяется к такому приспособлению посредством обыкновенных скруток. Так можно сделать самодельный и очень эффективный резак для пенопласта, при этом затратив минимум сил, времени и денег.
Пробуем разрезать пенопласт самостоятельно
Теперь немного поговорим о различных технологиях, методах и, конечно же, приведем подробную инструкцию, что и как делать.
Как самостоятельно разрезать пенопласт – пошаговая схема
Шаг 1: Подготовительные работы
Неважно, каким именно инструментом вы собираетесь пользоваться – ножом, нихромовой нитью либо же иными режущими приспособлениями, все равно начинать необходимо с разметки. Так что берем линейку, угольник, рулетку, карандаш и наносим на поверхности листа отметки, затем соединяем их в линии. В общем, рисуем контуры будущего разреза.
Есть и еще способы, как можно . Например, с использованием нихромовой нити. В этом случае на нее подается небольшой ток, который способен раскалить струну до нужной температуры, и резка аккуратно производится по заданному контуру. Безусловно, качество реза в этом случае получится значительно лучше, однако немного придется потрудиться, чтобы сделать станок. Поэтому данный метод не всегда оправдывается, если вам необходимо обработать всего несколько листов, просто нет смысла тратить время на конструирование приспособления. Как видим, нельзя дать однозначного ответа, чем же лучше резать пенопласт, все зависит от объемов и навыков.
Пенопласт является универсальным материалом. Применяется в строительстве (утеплитель), в производстве (ремонте) бытовых электроприборов, дизайне помещений, рекламе. Одна из основных характеристик материала – плотность. Чем выше этот показатель, тем прочнее материал. Однако это здорово влияет на цену.
При использовании материала в качестве наполнителя для утепления стен, обычно выбирается самая неплотная структура (по причине низкой стоимости). Однако рыхлый пенопласт сложно обрабатывать – при раскрое он сильно крошится, создавая сложности при уборке мусора.
Нож для резки пенопласта должен быть тонким и острым, но это не спасает от разрушения кромки. Даже если вы работаете на улице, разлетающиеся мелкие шарики засоряют окружающую среду.
Поэтому профессиональные строители производят резку пенопласта нихромовой проволокой или горячей пластиной. Материал легкоплавкий, несмотря на пожарную безопасность.
Важно! При выборе утеплителя, обратите внимание на характеристики. Там должно быть указано: «самозатухающий». Такой пенопласт отлично режется с помощью температуры, но при пожаре он не станет источником горения .
Промышленный аппарат для резки пенопласта может обрабатывать листы любого размера, кроить материал как поперек, так и вдоль массива.
Однако резка пенопласта в домашних условиях не предполагает подобных объемов и размеров. При ремонтных работах в своем жилище (или гараже) вполне достаточно компактного термического ножа. Он легко справится как с линейным раскроем, так и с фигурной подгонкой плит, при укладке на участках со сложной формой.
Любой инструмент имеет стоимость, и всегда есть возможность сэкономить на покупке.
Приспособления для резки пенопласта своими руками
Для линейного раскроя отлично подходит гильотина. Только воздействие будет не механическим, иначе образуется много мусора. Используем проверенную технологию – резка пенопласта натяжной разогретой струной.
Требуемые материалы
- Нихромовая (вольфрамовая) нить
- Источник питания, желательно регулируемый
- Любые конструкционные материалы: брус, металлический профиль, труба, для изготовления натяжной рамки
- Мебельные направляющие для ящиков.
На столе, верстаке, или иной ровной поверхности, устанавливаем вертикальные стойки для крепления гильотины. С помощью мебельных направляющих, закрепляем рамку резака таким образом, чтобы она двигалась без перекосов. Обе стороны должны перемещаться синхронно.
Самая ответственная часть резака – проволочный механизм. Первый вопрос: где взять материал. Нихром можно приобрести в магазинах, торгующих радиодеталями. Но поскольку мы стремимся к условно бесплатной конструкции – поищем альтернативу.
- Старый паяльник. Модели производства СССР, рассчитанные на 36-40 вольт, можно найти в любой домашней мастерской. Обмотка нагревателя – отличный донор для нихромовой гильотины. Правда, длина проволоки не более метра.
- Утюг с классическим спиральным нагревателем. Проволока более толстая, подойдет для линейного раскроя. Фигурная резка допустима, при невысоких требованиях к точности.
- Спиральные нагреватели от фена, или тепловентилятора. Принцип тот же, для точного раскроя не подходят.
Обратите внимание
Совет: При распрямлении спирали, не следует тянуть проволоку вдоль пружины. Могут появиться петли, и нить лопнет. Лучше разматывать витки как с катушки ниток. Можно надеть спираль на гвоздь или карандаш, и тянуть проволоку поперек витков.
Принцип работы рамки изображен на схеме
Проволочный резак должен быть электрически изолирован от рамки. Поэтому она может быть сделана из металла. Важно обеспечить постоянное натяжение проволоки. При нагреве нихром расширяется, прибавляя в длине до 3%. Это приводит к провисанию струны.
10 лучших идей и вдохновения для резки пенопласта
Подробнее
Откройте для себя 10 лучших идей и вдохновения Pinterest для ножа для пенопласта. Вдохновляйтесь и пробуйте новое.
Сохранено с cs.trains.com
Скос? – Журнал Model Railroader
Model Railroader — крупнейший в мире журнал о моделях поездов и схемах моделей железных дорог. Мы предлагаем справку для начинающих и продвинутых по всем моделям железных дорог, включая планы компоновки путей, обзоры продуктов для моделей железных дорог, новости о моделях поездов и форумы по моделям железных дорог.
Woodworking Garage
Woodworking Designs
Fine Woodworking
Woodworking Crafts
Woodworking Chisels
Woodworking Quotes
Youtube Woodworking
Intarsia Woodworking
Woodworking Chair
More information…
Rania saved to Tools
Сохранено с makezine.com
5-Minute Foam Factory
Сделайте этот простой резак для пены с помощью горячей проволоки и повторно используйте остатки пенополистирола, чтобы создавать сокровища из мусора.
Металлические рабочие проекты
Сварные проекты
DIY Projects
Halloween Projects
Остатки повторного использования
Foam Cutter
. Идеи для поделок
Сохранено с youtu.be
Чертежи по дереву Бесплатно
Резак для пенопласта со скосом
Чертежи по дереву Бесплатно
деревообрабатывающие джигс
проекты по деревообработке
Мебельные проекты
Деревянная мебель
пенопластовой режущий
Построить стену
Настенные полки
Бин
Подробнее . ..
Sci -Scipspeppled To Diepking To Diy jigking Diging To Diy Diagking To Diy Diagking To Diy Diagking To Diy Diagking To Diy Diagking To DIY DIY TO DIY TO DIY DIGKING KISKIPPONGIN
Сохранено с instructables.com
Как сделать электрический резак для пенопласта
Как сделать электрический резак для пенопласта: В современном мире «пенополистирол» широко используется в проектах и продуктах «сделай сам». Раньше пенополистирол резали стационарным ножом, который создавал много пыли вокруг. Электрические резаки для пены помогают избавиться от этого …
Pot Mason Diy
Mason Jar Crafts
Mason Jars
Foam Cutter
Diy Cutter
Projects To Try
Craft Projects
Craft Ideas
Wie Macht Man
More information…
SaritaS
Sarita сохранено в творчестве с фантазией welden
Сохранено с youtube.com
Дешевый недорогой резак для пенопласта с ЧПУ costycnc arduino самодельный станок с горячей проволокой taglia полистироло
Мой окончательный проект https://www. youtube.com/watch?v=6v2BGdD2p8EMy Онлайн бесплатное изображение для программы gcode js https://www.costycnc.it/cm8My онлайн бесплатное изображение для gc…
Routeur Cnc
Cnc Router Plans
Arduino Cnc
Diy Cnc Router
Woodworking Plans Free
Router Table
Router Woodworking
Dremel Tool Projects
Cnc Router Projects
More information…
Рубер сохранен на ЧПУ / 3D и технологиях
Сохранено с youtube.com
Как сделать электрический резак для пенопласта в домашних условиях
Сделай сам: узнайте, как сделать электрический резак для пенопласта. Посетите веб-сайт, чтобы узнать все основные подробности. : https://navinkhambhala.com/mr-nkОсновной канал – crazyNK: https…
Инструменты для изготовления дерева
Инструменты для поделок
Поделки из пенопласта
Самоделки и поделки
Кусачки для пенопласта
9005
Резьба из пены
DIY Doors Doors
Hobby Tools
Дополнительная информация . ..
Бриттанис Ларп Сэкономлен на семинаре
Сэкономлен на YouTube.com
как сделать резак из пенопласта в домашних условиях. Теперь вы можете резать Thermocol, не создавая беспорядка в доме 🙂 Он также известен как резак для пены горячей проволокой, так как пенопласт…0005
Деревообрабатывающая работа показывает
TEDS Woodworking
Youtube Woodworking
Деревообрабатывающая механизм
DIY Crafts To Do
DIY -проекты, чтобы попробовать
Spray Foam
больше …
Jacob Saved Saved Laked Lakeen
. musetacrafts.com
Резак для пенопласта с электропитанием – Резак для пенопласта своими руками | Museta Crafts
Соберите самодельный резак для пенопласта с горячей проволокой с ограниченным бюджетом. Удивительный инструмент, работающий от источника питания, который поможет вам с вашими проектами по производству пенопласта или полистирола.
пенопластовой резак
DIY Cutter
Crafts
DIY Инструменты. Изделия из пенополистирола
Сохранено с instructables.com
Самодельный резак для пенопласта с горячей проволокой
Самодельный резак для пенопласта с горячей проволокой: Дешевый и простой в сборке резак для пенопласта с горячей проволокой из обычных деталей. Мой вариант выполнен на напряжении 6v. Напряжение питания зависит от используемого провода, его сопротивления и длины. Без проблем можно построить на 12v или другом напряжении. Вы также можете увидеть этот пр…
пенопластовая резак
Проводной режущий
Режущики
Пенисская плата DIY
HOTWIRE
PVC Pipe
DIY Life
DIY Projects
ARKADA
More Information …
ADACHADARISARKADS
ARKADADS
ARKADIS
ARKADIS
ARKADS
. Adach сохранено в Inspiracje
Сохранено из Загружено пользователем
Как резать пенопласт с помощью Cricut Explore 2
Cricut Explore
Товары для офиса
Пена
Проекты
Проекты из бревен
Чертежи
Дополнительная информация. ..
Бумага, сохраненная в Советы и инструменты
машина для резки
от 32.500,00 €
до обзор машины Контакты сша
ПРОГРАММНОЕ ОБЕСПЕЧЕНИЕ
CUT4000S
ДОКУМЕНТЫ
Информация
ЦЕНА от
32.500,00 € плюс НДС
Станок для резки пенопласта с ЧПУ для компьютерной резки 2D контуры из пенопласта, стиродура, неопора и других пенопластов.
Машины серии CUT 4000S имеют качество Сделано в Германии .
Чрезвычайно устойчивый открытый станочный стол из сварной и окрашенной стали.
профилей позволяет быстро и легко загружать машину со всех
стороны. Станок имеет две оси и может перерезать до 10 проводов.
Натяжение режущей проволоки контролируется двумя жесткими пружинами. Эти машины
подходят для обработки блоков из пенополистирола и неопора размером до
размером 5000x1250x1050 мм.
Опционально все станки серии CUT 4000S могут быть оснащены с тележками . Этот повышает производительность и сокращает время простоя при очистке машины по до 40% .
Это идеальная серия станков для всех отраслей промышленности, где требуется резка быстро и легко в больших количествах с до 10 проводов .
Product-Highlights
- Качество “Сделано в Германии”
- Интеллектуальный : Компьютерное управление (ЧПУ) через ПК с ОС Windows
- Сложный : Подпружиненная режущая проволока, всегда натянутая, длинная переменная
- Универсальный : Для 2D-объектов, панелей, изоляционных плит
- Прочный : Сварная и окрашенная стальная конструкция – без алюминия!
- Многослойная резка : Резка нескольких панелей из пенополистирола или пенополистирола.
за один шаг
Основные моменты обслуживания
- Доставка : около 12 недель
- Готов к использованию : Машина поставляется предварительно собранной и полностью протестированной (готов к запуску)
- Быстро : Обслуживание внутри Германии в течение 48 часов
- Модульный : Оператор может легко заменить компоненты
- Обучение: нашими опытными сотрудниками
- Консультация : Мы поможем вам от первого контакта до мы нашли ваше решение
- Ресурсы : Мы предоставим вам ресурсы для EPS и XPS поставщиков полистирола.
Удлинители
- Загрузка тележки
- Независимые оси Y
- Вращающиеся режущие лопасти
- Компьютерный пакет
»CUT 4000S обеспечивает бесперебойную работу нашего производства работа, 6 дней в неделю.
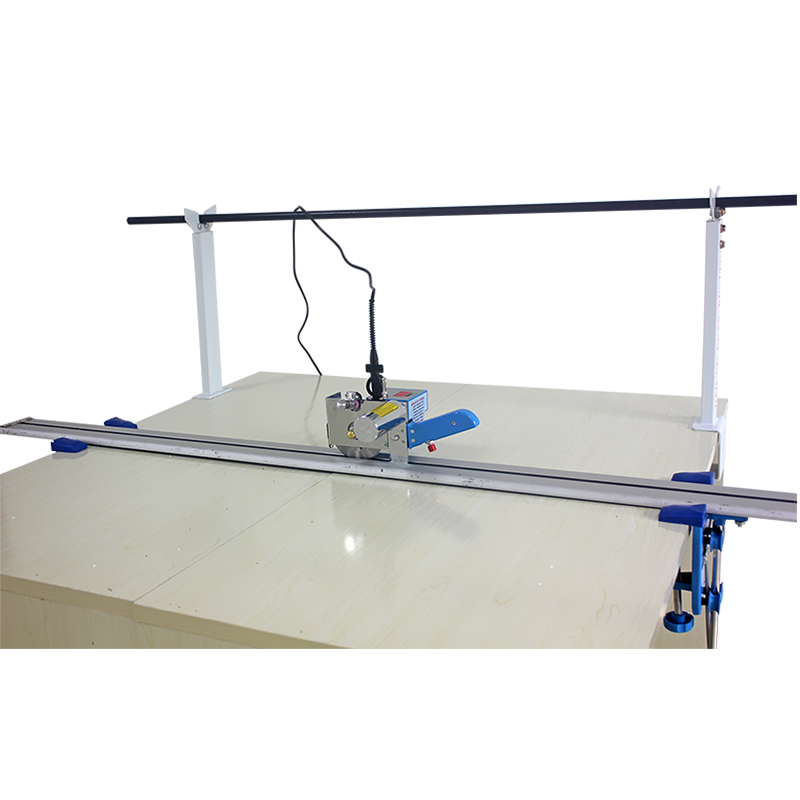
Рольставни GeoPac (CEO)
Коммерческое производство
Стабильная стальная рама, быстрые приводы и несложное управление. серия CUT 4000S впечатляет коммерческих и промышленных пользователей. Он режет 2D-формы, профили, отрезки труб, пластины и многое другое Вот как CUT 4000S обеспечивает производство коробов для роллет так же заняты, как и производители лепнины и профилей .
Станок с ЧПУ CUT 4330S – Резка бетона молдинги из пенополистирола и неопор..
CUT 4000S – Характеристики
Станки CUT 4000S имеют качество “Сделано в Германии” . Каждая машина собран вручную , настроен и тщательно протестирован перед поставкой, чтобы убедиться, что все машины будут работать гладко для
долго.
Базовая машина
Станок CUT 4000S был разработан для обработки стандартных блоков пенополистирола размером размером 1250×1050 мм и длиной до 5 м в кратчайшие сроки. В отличие от станков серии CUT 5000S не блокирует но режущий портал, который перемещается. Это обеспечивает высокую производительность с меньшими требованиями к пространству.
Чрезвычайно устойчивый открытый станочный стол из сварного и окрашенного стальные профили позволяют быстро и легко загружать машину из все стороны. Таким образом, большие пенопластовые блоки можно загружать либо вилкой, либо вилкой. подъемник или с возможностью загрузки тележки
Умный держатель проволоки
В CUT 4000S две спиральные пружины контролируют натяжение режущей кромки.
провод. Пружины гарантируют, что проволока не провиснет при разрезании.
и что у него всегда оптимальное натяжение . Так что вы можете быть уверены
чтобы у вас всегда был точный и чистый результат резки .
Благодаря пружинам проволоку можно быстро снять и снова вставить без инструментов . Прежде всего, это упрощает и ускоряет изменить провода и установить расстояние между проводами.
Расстояние между проволоками устанавливается с помощью шкалы с обеих сторон резьбового стержни. Это самый быстрый способ установить провода и не будет не только экономит ваше время, но и позволяет резать больше.
Блок питания
Режущая проволока серии CUT 4000S всегда имеет правильную температура, обеспечивающая чистый срез при обработке пенополистирола, стиродура или пены Неопор. Причиной этого является сложное течение блок управления, который содержит микропроцессор, управляющий подачей питания особенно во время 3D-монтажа.
Таким образом, мы можем гарантировать, что каждый разрез будет чистым и точным.
ЧПУ до 3-х каналов
Серия CUT4000S поставляется с 4-осевым ЧПУ собственной разработки
контроль.
Регулятор может быть загружен до 8,0 ампер на канал. Кроме того, управление может быть расширено 3-м каналом, что управление дополнительная ось, напр. вторая ось Y.
Программное обеспечение машины, включая контроллер LAN
Наши машины укомплектованы, все включено, даже машина программное обеспечение и еще более безопасный и надежный контроллер LAN для все текущие версии Windows . Экран программного обеспечения был разработан оптимизирован для резки проволоки по 4 и 5 осям и прошел всесторонние испытания на практике. Вы можете быть уверены, что все сразу заработает.
Все, что вам нужно, это компьютер или ноутбук с Windows и одним бесплатным подключением к локальной сети. и около 10 минут, чтобы установить все. Это не может быть проще.
Дополнительные аксессуары
Машины серии CUT 4000S можно модернизировать с помощью следующих
аксессуары. Благодаря этому машины подключаются и работают, и вы можете быть уверены
что ваша машина будет работать надежно с необходимой производительностью .
Загрузка тележки
Пока машина для резки пенопласта еще работает, загрузите тележку со следующим блоком полистирола. Затем вы подкатываете машину к машине и пристыковать его там. Сдвиньте блок на стол станка и зафиксируйте его. с помощью защелкивающейся системы. В зависимости от типа машины, несколько транспортных также можно использовать тележки. После резки задвиньте блок обратно на тележки. Затем отрезанные детали можно удалить вдали от машины. из блока и упакованы. Непроизводительные простои машины сведены к минимуму и ушли в прошлое.
Независимые оси Y
CUT 4000S может быть дополнен двумя независимыми осями Y. Это позволяет
вы, чтобы сократить, например. скатные, ендовные и коньковые доски, а также кровля
башни вырезаются из цельного куска. Программирование может быть выполнено с помощью
с помощью нашего программного обеспечения StyroCAM через ввод параметров. Раздражающее создание
чертежей больше не требуется.
Вращающиеся режущие рычаги
Расширьте станки для резки пенополистирола CUT 4000S опцией вращающиеся режущие рычаги. Режущие рычаги могут свободно вращаться с помощью 90°. Это позволяет горизонтальным и вертикальным контурам и листовым режет до 10 проводов . Таким образом, можно обрабатывать стандартные блоков сверху и спереди одной машиной.
Компьютерный пакет
Немедленно закажите станок с ПК Windows, оптимизированным для ЧПУ.
резка . В комплект входят: ПК с ОС Windows, TFT-экран, клавиатура
и мышь. Установлена последняя операционная система Windows и ЧПУ.
оптимизирован. Пакет готов к работе по принципу «подключи и работай» .
Сканер штрих-кода
Дополните машину сканером штрих-кода. Дополнительный модуль штрих-кода делает операцию детской игрой. Загрузите файл резки, связанный с заказом, напрямую в программное обеспечение машины с помощью сканера. Это позволяет избежать ошибок и производство еще быстрее.
Программное обеспечение CAM
Для создания 2D- и 3D-режимов мы рекомендуем программа стирокам. Это облачное программное обеспечение для резки пенопласта . для расчета цен предложения и создания файлов резки для стандартных 2D и 3D резка. Дополнительную информацию можно найти в разделе «Программное обеспечение».
Технические характеристики
Серия | CUT4100S | CUT4200S | CUT4300S |
---|---|---|---|
Длина провода | 1250 мм | 2000 мм | 3000 мм |
Перемещение вперед/назад (X) | 1250 мм | ||
Перемещение вверх/вниз (Y) | 1300 мм | 1300 мм | 1300 мм |
Высота стола | 400 мм | 400 мм | 400 мм |
Количество проводов | 10 | 10 | 10 |
Количество осей | 2 | 2 | 2 |
Тип привода | Стойка, цепь | Стойка, цепь | Стойка, цепь |
Скорость резания макс.![]() | 3 м/мин | 3 м/мин | 3 м/мин |
Включение/выключение провода | Программное обеспечение | Программное обеспечение | Программное обеспечение |
Подключение к сети | 220–380 В переменного тока, 50–60 Гц | 220–380 В переменного тока, 50–60 Гц | 220–380 В переменного тока, 50–60 Гц |
Потребляемая мощность | 2,250 Вт | 3,950 Вт | 4,950 Вт |
Вес | до 450 кг | до 450 кг | до 450 кг |
ЗАПРОС | ЗАПРОС | ЗАПРОС |
(Цена) плюс НДС
Комплект поставки
Станок CUT 4000S — это ваш вход в класс производства пенополистирола . машины для резки. Просто снимите упаковку, установите, подключите и
начать – вот как это просто. Посылка содержит все необходимое
для начала:
Maschine Plug&Play
Провод питания
Программное обеспечение станка
Проволока для резки
Машина
- Предварительно собранная и испытанная машина
- ЧПУ
- Провод питания
- LAN-контроллер
- Программное обеспечение для обработки
- Руководство по эксплуатации, инструкция по сборке
- 1 год гарантии
Необходимые аксессуары
- Программное обеспечение CAM
- Компьютерный пакет
Дополнительные принадлежности
- Независимые оси Y
- Вращающиеся режущие лопасти
- Загрузка тележки
- Проволока для резки
- Пружины
Что наши клиенты делают
листы
Профили для формования
Профили, TRIM, Stucco
Плавающий корпус
Профили
Установка для водных площадок
.
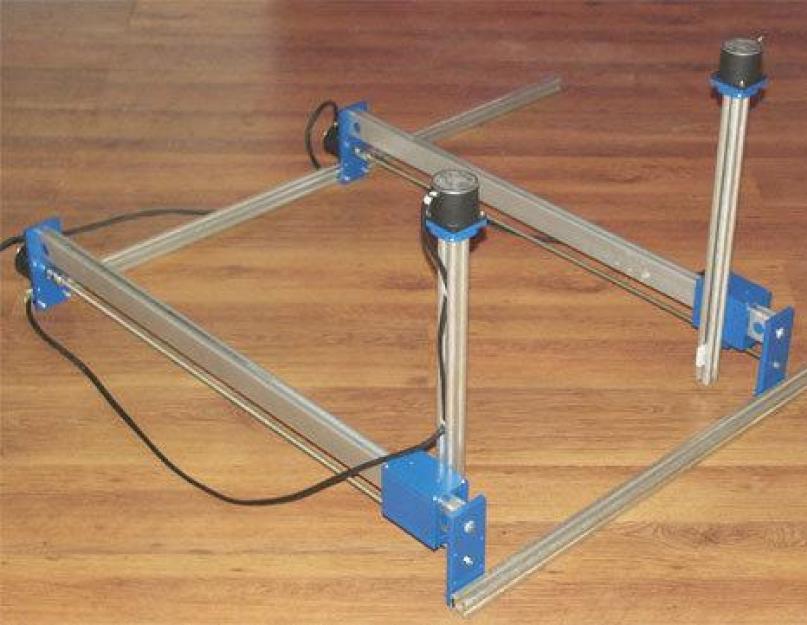
Отличие от программного обеспечения
На первый взгляд, большинство машин для резки горячей проволокой кажутся очень похожими. Разница становится очевидной в обычном повседневном производстве в Условия экономии времени и денег. Особенно важно, что прост в использовании, мощное программное обеспечение . В этом заключается одна из выдающихся сильных сторон чпу-мультитул. Вы вряд ли найдете что-то подобное на рынке.
Даже самое лучшее оборудование практически бесполезно, если программное обеспечение
ограничивающий фактор. Чтобы полностью использовать потенциал CUT 4000S,
мы рекомендуем вам следующее программное обеспечение:
Corel Draw®
С помощью этого программного обеспечения для рисования вы можете легко и быстро создавать буквы,
логотипы, надписи и многое другое в векторном формате. Включает прямой экспорт
для дальнейшей обработки.
Основные моменты
- Проверенная программа векторного рисования
- Быстрый дизайн букв, символов и логотипов
- Импорт данных EPS
- Доступ ко всем стандартным компьютерным шрифтам
- Экспорт в файлы DXF или PLT
CAD Std
Сильной стороной этой программы САПР является простота и быстрота пользователь может создавать рисунки в векторном формате. Последующий DXF экспорт может быть обработан немедленно.
Основные моменты
- Программа для рисования САПР
- Бесплатно
- Неограниченное количество загрузок
- Очень прост в использовании
- Очень быстрые результаты
Программное обеспечение styroCAM
Облачное программное обеспечение для резки пенополистирола для расчета цен предложения
и создание файлов резки для стандартных 2D и 3D разрезов.
Особенности
- Расчет режимов резки для 2D и 3D резов
- Чрезвычайно прост в использовании
- Форматы данных: DWG, DXF, PLT, 3D STP
- Экспорт данных из CorelDraw, Adobe Illustrator, AutoCAD и другие
- Работает как программное обеспечение как услуга в современных интернет-браузерах (SaaS)
Модели в сравнении
Помимо множества преимуществ, конструкция станка CUT4000S имеет также их пределы. Разрез с более длинным проводом к сожалению не в пределах Царство серии 4000S. Для таких случаев мы разработали CUT. Серия 3500SV , которая благодаря своим 4 осям также может выполнять резьбу резка конусами, коническими профилями и многим другим одним проводом. это стоит взглянуть на сестер CUT 4000S…
Серия | РЕЗКА 3500SV | РЕЗКА 4000S | РЕЗКА 5000S |
Перемещение вперед/назад (X) | до 5000 мм | до 5000 мм | до 3000 мм |
Перемещение вверх/вниз (Y) | 1600 мм | 1300 мм | 1400 мм |
Длина провода (Z) | до 5000 мм | до 3000 мм | до 3000 мм |
Количество осей | 4 | 2 | 2 |
Количество проводов | 1 | 10 | 10 |
Цена в евро | 37. | 32 500,00 €* | 34 500,00 €* |
ВЫРЕЗАТЬ 3500СВ | ВЫРЕЗАТЬ 5000С |
* цены начинаются с плюс НДС
Как насчет тест-драйва?
Подходит ли вам эта машина для резки пенопласта? Мы будем рады помочь и проконсультируем вас обо всех плюсах и минусах в телефонном звонке. Как и мы ежедневно перерабатывая полистиролы, мы уверены что мы можем ответить на все ваши вопросы, исходя из нашего собственного опыта – от пользователей для пользователей.
Убедитесь сами, насколько мощными на самом деле являются наши машины для резки горячей проволокой. находятся. Отправьте нам быстрое сообщение и дайте нам знать, как мы можем помочь. Или просто
позвоните нам прямо сейчас.
КОНТАКТЫ
Как собрать резак для пенопласта с ЧПУ с горячей проволокой — версия с параллельным портом
В этом посте подробно описана моя исходная сборка резца пенопласта с ЧПУ, которую я сейчас обновил до новой версии. Вот ссылка, если вы предпочитаете собирать USB-версию https://rckeith.co.uk/how-to-build-a-usb-cnc-hot-wire-foam-cutter/
. Версия USB, потому что настройка Mach4 и LinuxCNC на компьютерах с параллельным портом довольно длительна. Калибровка также более сложная. Так что, если вы новичок в резке пенопласта с ЧПУ, создайте USB-версию, которая намного проще,
Параллельный порт уже давно снят с производства, но в 2022 году он по-прежнему может использоваться. Если вы посмотрите на Amazon или eBay, вы увидите, что продается много контроллеров с ЧПУ, которые все еще используют его. Если у вас есть старый ПК, это идеальный кандидат, или вы можете купить дополнительную карту параллельного порта для более современного ПК.
Зачем создавать станок для резки пены с ЧПУ с горячей проволокой?
Для меня это был способ изготовления крыльев и фюзеляжей для радиоуправляемых самолетов, которые были недоступны. Сделать это самостоятельно (DIY) не так сложно, как вы думаете.
Традиционные методы сборки радиоуправляемых самолетов включают в себя множество операций по резке и склеиванию пробкового дерева. Я могу вырезать сердцевину крыла из пенопласта примерно за 15 минут, и обычно я вырезаю несколько штук за раз. Создание собственных моделей очень полезно, а когда они хорошо летают, это настоящий кайф.
Я построил свою первую машину в 2012 году, и вот несколько проектов, которые я сделал с ее помощью0374
Основные части
- Как это работает?
- Сложно построить?
- Сколько стоит сборка
- Детали, необходимые для сборки станка для резки пенопласта с ЧПУ Hot Wire
- Программное обеспечение для станка для резки пенопласта
- Первый самолет, изготовленный с помощью станка для резки пенопласта с ЧПУ Hot Wire
- Обновления, внесенные мной в Hot Wire Резак для пенопласта с ЧПУ
- Схемы, детали и инструкции
Как это работает?
Если вы не знаете, что такое резак для пенопласта с ЧПУ Hot Wire, позвольте мне объяснить. Большинство типов пенопласта можно резать горячей проволокой, и если вы сможете точно контролировать проволоку, то сможете делать крылья и фюзеляжи для радиоуправляемых самолетов и многое другое, например знаки. Можно обойтись без станка с числовым программным управлением (ЧПУ), просто проводя горячую проволоку по шаблонам. Этот метод менее дорог и является хорошей отправной точкой в путешествии по резке пенопласта с ЧПУ с горячей проволокой. Вы получите хороший опыт работы с горячей проволокой. Мои крылья Super VC10 были сделаны таким образом до того, как у меня появилась машина.
Сложно построить?
Нет. Если вы достаточно практичны, то у вас есть все необходимые навыки. Не пугайтесь электроники. Это может показаться немного пугающим, но если вы будете следить за моими статьями на веб-сайте или подпишитесь на электронную книгу, у вас будет вся необходимая информация. Если вам нужна помощь, свяжитесь со мной через страницу контактов, и я вернусь к вам с некоторыми ответами. Я получаю довольно много вопросов со всего мира с просьбой дать совет и порекомендовать запчасти для покупки. Я предоставил ссылки на все части, которые я использовал, и рекомендации.
После долгих исследований и нескольких действительно хороших советов с форумов ЧПУ я разработал эту версию. Полная информация на этой странице https://rckeith.co.uk/cnc-detailed-build-and-plans/
Сколько стоит построить станок для резки пены с ЧПУ с горячей проволокой
Вероятно, не так дорого, как вы думаете. Мой 4-осевой комплект ЧПУ прибыл из Китая и включал в себя шаговые двигатели, плату контроллера и несколько кабелей. Они различаются по цене, поэтому проверяйте список запчастей, чтобы узнать последние новости. Я регулярно проверяю их, чтобы убедиться, что они по-прежнему являются лучшими, на мой взгляд.
Блок питания я изначально сделал из двух старых компьютерных блоков питания, а остальные купили в местных магазинах DIY. Полный список со ссылками см. на странице сборки. Я потратил больше денег на программное обеспечение, чем на остальную часть сборки, но теперь есть несколько очень хороших бесплатных альтернатив, проверьте страницу сборки
Большая часть стоимости, если вы используете опции бесплатного программного обеспечения, будет контроллером ЧПУ, шаговые двигатели и блок питания. Если у вас есть старый настольный ПК с параллельным портом, это снизит стоимость. Исходя из средних цен в 2022 году, если бы вам пришлось покупать все, кроме ПК, я бы выделил примерно 280 долларов США (США) и 220 фунтов стерлингов (Великобритания), но вы можете сделать это дешевле, если у вас уже есть подходящие материалы. Версия USB немного дешевле, около 200 долларов, потому что она основана на компонентах 3D-принтера. Которые сейчас настолько популярны, что снижают затраты. Но проверьте список запчастей, чтобы узнать последние цены.
Это небольшая инвестиция, но вам не потребуется много времени, чтобы окупить затраты. Я построил несколько крыльев и пару фюзеляжей, и это настоящий кайф, когда сердцевина крыла выглядывает из пеноблока. Модели из пенопласта сейчас могут быть довольно дорогими, ребята из моего аэроклуба часто платят от 200 до 400 фунтов стерлингов за самолет с большим EDF. Я видел пару таких уничтоженных без возможности восстановления.
Детали, необходимые для изготовления станка для резки пенопласта с ЧПУ с горячей проволокой
- Шаговые двигатели — они приводят в движение башни, к которым прикреплена проволока с подогревом
- Плата управления 4 оси – посылает сигналы шаговым двигателям для перемещения на определенную величину и в каком направлении. Получает входные данные от концевых выключателей и подвесок
- Компьютер – управляет панелью управления. Он получает g-код и преобразует его в сигналы для платы управления.
- Ходовой винт — подключен к шаговым двигателям, а затем к башням для перемещения их в нужном направлении,
- Программное обеспечение — я использовал LinuxCNC, но начал с Mach4, который превращает g-код в сигнал о том, что плата управления и шаговые двигатели можешь использовать.
Затем я использую Profili2 Pro и DevFus Foam для создания g-кода из проекта. Вы можете использовать LinuxCNC и бесплатное программное обеспечение для создания g-кода для крыльев и фюзеляжей. Проверьте мою статью Бесплатное программное обеспечение для ЧПУ
- Направляющие для выдвижных ящиков – используются для вертикального и горизонтального перемещения двух опор
- Блок питания 24 В – питает плату управления и шаговые двигатели
- Горячая проволока – обычно нихромовая проволока.
Точность резки пенопласта
Я решил использовать резьбовые стержни для ходовых винтов, потому что точность, необходимая для резки пенопласта горячей проволокой, не так критична, как для фрезерного станка с ЧПУ. Но я по-прежнему получаю очень хорошие результаты, когда сравниваю вырезанные детали с чертежами в масштабе.
Ходовые винты сейчас намного дешевле, чем когда я впервые построил машину, но все же дороже, чем резьбовые стержни. Если вы предпочитаете, я бы использовал ходовые винты T8.
Источник питания -24 Вольта
Я использовал 2 блока питания ATX для ПК, соединенных последовательно, чтобы получить 24 Вольта. Это может быть немного опасно, если вы не позаботитесь об изоляции второго блока питания, поэтому я бы порекомендовал приобрести один, специально разработанный для подачи 24 Вольт. Они теперь довольно дешевы и занимают меньше места. Подробности в списке деталей
Первоначальная сборка резака для пенопласта
Ниже приведены фотографии моей первоначальной сборки. В нем использовались материалы из кабинета на чистке. Это была МДФ высокой плотности, очень стабильная, но тяжелая. У меня был ограниченный бюджет, а эта древесина была бесплатной, поэтому я построил машину из нее.
В 2012 году 3D-печать не была так популярна, как сейчас, поэтому я купил 4-осевой комплект ЧПУ, который включал все 4 шаговых двигателя NEMA23 и TB6560 на одной плате контроллера. Он оказался на 100% надежным.
Закончена- TB6560 от Ebay
- Фотография с заполненной сборкой
- NEMA 23 Stepper
- Y и Z Axis Block
- SPIKED TEE NUT позволяет Easy Alignment
- ОБЩЕСТВЕННА Соединители RJ 45
- Свинцовый груз поднимается по мере того, как башни расходятся дальше друг от друга
- 20-фунтовая леска используется
- Шкив и груз
- Все сделано на этой машине
Сборка завершена, смотрите фото выше и видео ниже. Проверено, и это работает. Я использовал кабели и разъемы RJ45 для подключения двигателей к контроллеру.
Программное обеспечение контроллера станка для резки пены с ЧПУ
Для управления станком с ЧПУ с параллельным портом вам потребуется некоторое программное обеспечение, и после долгих исследований я изначально решил использовать Mach4 от ArtSoft http://www.machsupport.com/, он очень хорошо поддерживается и есть есть несколько видеороликов на YouTube, в которых описывается, как установить и настроить. Нелицензионная версия позволяет использовать 500 строк g-кода, но вы будете удивлены, сколько строк потребуется для создания крыла. Лицензионная версия стоит 175 долларов.
Какой компьютер я могу использовать?
Компьютеру необходим параллельный порт, к которому подключаются принтеры. Сейчас они устарели, но вы все еще можете легко их найти. Mach4 или LinuxCNC прекрасно работают на очень скромном оборудовании.
Я использовал старый компьютер Dell GX620 с XP, и для Mach4 не было установлено никакого другого ненужного программного обеспечения. Для LinuxCNC я использовал ту же машину и просто поменял местами диск. Теперь есть и другие варианты подключения USB и Ethernet (LAN), см. мой пост здесь https://rckeith.co.uk/mach4-parallel-port/
Программное обеспечение для генерации G-кода
G-коды — это инструкции, отправляемые машине, которые сообщают ей, как далеко и в каком направлении следует перемещать шаговые двигатели. Вам не нужно изучать g-код, поскольку программное обеспечение преобразует рисунки в код. Первоначально я использовал Profili 2 Pro, а теперь перешел на DevWing Foam 2, который делает гораздо больше, чем генерирует g-код для профилей крыльев. Вот серия видеоруководств по DevWing Foam, ссылка на мой канал YouTube здесь
DevWing Foam 2 — это программное обеспечение следующего поколения, заменяющее Profili 2 Pro. Если вы только начинаете, я бы пока не рекомендовал это, так как это может показаться немного пугающим. Я бы посоветовал начать с бесплатных опций ниже, а затем, по мере развития ваших навыков и потребностей, приобрести DevWing Foam 2. Это лучшее программное обеспечение для создания g-кода, и оно хорошо поддерживается.
Вот бесплатный генератор g-кода крыла, который сгенерирует код для вас http://swarfer.co.za/rc/wire/index.php Я использовал его на своей машине, и он работает хорошо и довольно легко использовать. Проверьте мой пост здесь https://rckeith.co.uk/foam-wing-free-cnc-software/.
Горячая проволока
Проволока обычно из нихрома, но можно использовать и другие, включая гитарные струны. Я запитал свой провод с помощью iCharger 206, у которого есть программа для резки пенопласта, но я использовал зарядное устройство для автомобильного аккумулятора, подключенное к домашнему диммеру, для ручной резки. Это позволяет контролировать тепло и работает очень хорошо. Зарядное устройство RC, настроенное на NiCad или NiMH, также работает.
Наилучшие результаты я получаю, используя очень тонкую проволоку диаметром около 0,4 мм. Не требует большого тока для нагрева. Значение пропила, количество расплавленной пены очень мало. Это помогает в процессе проектирования. В основном я использую настройки программы по умолчанию и иногда корректирую значение пропила для стреловидных крыльев.
Проволока между двумя каретками может быть натянута пружиной, чтобы они могли двигаться независимо для конических крыльев. Иногда я использовал шкив с грузом. Пружины хороши для крыльев, но я обнаружил, что при изготовлении фюзеляжа проволока может иметь очень крутые углы, что создает слишком большое напряжение на каретках.
Использование шкива с грузом поддерживает постоянное натяжение троса под любым углом. Я использовал 20-фунтовую леску с колесом на оси, чтобы проложить леску со свинцовым грузом весом 1,5 фунта или около 0,7 кг. Картинки ниже должны помочь объяснить это. Провел несколько тестов, вроде все работает. Может быть сложно правильно отрегулировать вес, и вы должны убедиться, что вес не достигает нижнего предела.
Это работает
Это довольно интересно, когда вы включаете все это, перемещаете клавиши курсора и видите, как вращаются шаговые двигатели. На видео показан небольшой тест аэродинамического профиля, который был примерно с 5-й попытки. Горячая проволока отсекает мое сияние, так что она фактически плавит пену перед собой. Мои первые куски были не очень хорошими, так как подача была слишком медленной, но, как вы можете видеть, получилось не так уж плохо, когда я правильно нарезал подачу
Ниже показано летающее крыло, которое было первой моделью самолета, которую я сделал с помощью этой машины. Это был просто быстрый тест в качестве доказательства концепции, и оказалось, что это модель, на которой я чаще всего летаю. Летает очень хорошо и быстро. Profili2 Pro был очень хорош для генерации кода и имеет обширную базу аэродинамических профилей. Теперь его заменил DevWing Foam 2.
Надеюсь, вы нашли это интересным, и если вам нужен совет или помощь, вы можете связаться со мной через этот сайт.
Я включил конфигурацию для Mach4 с платой контроллера TB6560 на этой странице. программное обеспечение/
Первый самолет, сделанный на станке для резки пенопласта с ЧПУ Hot Wire
Это первое летающее крыло, которое я сделал на станке с ЧПУ, и это была маленькая жемчужина. Я летал на нем почти все выходные. Он очень быстрый с двигателем 2200KV и винтом 6×4. Это взрыв. Если вы хотите его построить, проверьте https://rckeith.co.uk/hot-wire-cnc-ymf-38-flying-wing/. Я также включил G-код для каждого крыла.
Разбил ее в 2017 году, ошибка пилота, дох!. Итак, я сделал еще один, вот полный плейлист
Первое летающее крыло, сделанное с помощью резака для пенопластаАвария летающего крыла, восстановление с помощью станка для резки пенопласта с ЧПУ HotWire – часть 1
Авария летающего крыла, поиск, восстановление и восстановление на станке с ЧПУ HotWire – часть 2
Авария летающего крыла, поиск, восстановление и восстановление на станке с ЧПУ HotWire – часть 3
Hot Wire CNC Flying Wing Обновление и бортовое видео
Теперь я сделал Hawker Hurricane на станке с ЧПУ как крыло, так и фюзеляж, вы можете увидеть это здесь https://rckeith.co.uk/cnc-hot- wire-hawker-hurricane/
Я также сделал гораздо большее крыло для FPV (вид от первого лица), подробности здесь https://rckeith. co.uk/fpvfw/
Станок с ЧПУ теперь начинает окупаться, так как я больше не покупаю модели ARTF, ничего против них не имею, просто мне нравится исследовать и делать свои собственные радиоуправляемые самолеты.
Обновления, которые я внес в станок для резки пенопласта с ЧПУ Hot Wire
Теперь я снял этот оригинальный станок и использую новую версию USB. Во время его использования я решил приложить усилия, чтобы LinuxCNC работал в 2018 году, и это было мое предпочтительное программное обеспечение для версии резака для пенопласта с параллельным портом. В моем видео ниже показано, как делать крылья с помощью бесплатного программного обеспечения с LinuxCNC 9.0005
Сделав несколько моделей и протерев много пены, я поменял только муфты на шаговые двигатели. Резиновые шланги иногда отрывались, что разрушало часть пены, поэтому я купил несколько подходящих соединителей, и они оказались очень надежными. Подробности на странице сборки.
Схемы, детали и инструкции
Новый USB-резак для пенопласта также можно использовать с параллельным портом. Полная информация приведена в электронной книге.
8 | Направляющие для ящиков 600 мм x 2 пары – всего 4 Направляющие для ящиков 450 мм x 2 пары – всего 4 | |
4 | Гибкие муфты x 4 M10 x 5 мм для NEMA17 M10 x 6,35 для NEMA23 | |
4 | 10 x 1,5 мм Т-образные гайки x 4 | |
40 | Болты M6 с крестообразными дюбелями 50 мм и цилиндрические гайки x40 | |
4 | 10 x 1,5 мм x 1000 мм (нарезать по размеру) Резьбовой стержень x 4 Если вы предпочитаете использовать ходовые винты T8, также потребуются соединители M5 x 8 мм. 450 мм для вертикального 750 мм для горизонтального Шаг/мм также необходимо пересчитать. Также можно использовать 3/8″-16. См. См. здесь | |
1 | МДФ 12 мм Влагостойкий или красить после сборки.![]() |
Конструкция параллельного порта почти идентична версии USB, за исключением электроники. В планах есть альтернативная часть B для шаговых двигателей NEMA23. Они больше, чем NEMA17, которые вы все еще можете использовать, если хотите.
Плату контроллера и степпер рекомендую покупать в комплекте, включая блок питания. Нагрузки на Amazon, AliExpress и Gearbest. Проверьте список деталей ниже, чтобы увидеть, что я использовал, и рекомендации.
Контроллер TB6560/TB6600 с параллельным портом
Этот контроллер используется с Mach4 или LinuxCNC, который интерпретирует g-коды и через плату контроллера управляет шаговым двигателем. Есть несколько альтернатив, но я просто перечислю те, которые я купил и использовал.
С доской «все в одном» немного проще строить. С отдельными драйверами намного больше проводки. Моя доска «все в одном» была на 100% надежной и никогда не пропускала ни одного шага. Вы можете найти комментарии на форумах ЧПУ о том, что они не годятся, но у меня не было проблем с моим.
Кол-во | Изображение | Описание |
1 | Отдельные драйверы TB6560 | Плата контроллера 4 Axis TB6560 |
1 | Плата контроллера 4 Axis TB6560 Все в одном с блоком питания. Драйверы все на одной плате обычно дешевле | |
4 | Шаговый двигатель Nema 23 | Шаговый двигатель NEMA 23 57BYGH56-401A или аналогичный. |
Настройка DIP-переключателя TB6560 на моей Blue Board
У меня есть несколько комментариев на веб-сайте от людей, пытающихся заставить свою машину работать правильно. Вот как я настроил свой.
Настроен на ток 75%, режим быстрого затухания и микрошаг 1/2. Мои шаговые двигатели рассчитаны на 2,8 ампера, а привод будет подавать 3 ампера при 100%, поэтому я уменьшил это значение до 75%, чтобы получить 2,2 ампера, и двигатели работают нормально и работают так несколько лет.
LinuxCNC и Mach4
LinuxCNC раньше назывался EMC2 и существует уже некоторое время, и я предпочел использовать его вместо Mach4 для обеих своих машин. Сейчас пользуюсь USB-версией. У меня есть полный пост об установке, настройке и LinuxCNC здесь
Mach4 существует уже некоторое время и очень хорошо задокументирован с несколькими хорошими обучающими видео на их веб-сайте. Хотя и не специально для машины с горячей проволокой, они заслуживают внимания. Я просматривал их несколько раз http://www.machsupport.com/help-learning/videos-tutorials/
Mach4 и LinuxCNC предназначены для использования старого параллельного порта принтера, который теперь является устаревшим, чего нет в современных ПК. есть больше. Есть несколько вариантов:
- Приобретите старый ПК с портом для принтера. Mach4/LinuxCNC не нуждается в высокопроизводительном ПК, поэтому большинство старых ПК будут работать нормально. Это то, что я сделал, и у меня также есть несколько запасных.
Много на eBay от 50 до 80 долларов
- Установите дополнительную плату порта принтера.
- Используйте плату контроллера движения USB или Ethernet. Это с программным драйвером настроит Mach4 для использования вашего порта USB или Ethernet. Затем TB6560 подключается к контроллеру движения. Проверьте мою статью для вариантов https://rckeith.co.uk/mach4-parallel-port/
Использование Mach4
Я использовал старый Dell GX 620 ussf под управлением Windows XP с 2 ГБ ОЗУ. Mach4 будет работать только на 32-битной версии Windows. Я также использую LinuxCNC на этой машине. У меня был диск для каждого, и я просто менял его, когда мне нужен был другой.
На моем ПК была установлена только что установленная Windows для Mach4, и больше ничего. Он не был подключен к Интернету, поэтому мне не нужны антивирусы и обновления. Я даже отключил много ненужных сервисов. Я получил g-код с помощью USB-накопителя.
Конфигурация Mach4 с TB6560 и все мои настройки идут на эту страницу https://rckeith. co.uk/4-axis-cnc-hot-wire-configuration-for-tb6560-and-mach4/ включает настройку домой и концевые выключатели.
Использование LinuxCNC
Это хороший вариант, и он хорошо работает. Подробная информация здесь https://rckeith.co.uk/foam-wing-free-cnc-software/
На мой взгляд, дисплей намного лучше для 4-осевых резаков для пенопласта. , Mach4 может выглядеть немного странно на 4 осях.
Теперь он работает и на моем маршрутизаторе OX. На моем канале YouTube есть видео, а на этом сайте LinuxCNC – статья.
Наконец
Версия станка для резки пенопласта с ЧПУ с параллельным портом по-прежнему является жизнеспособным вариантом в 2022 году, и если вы строите очень большую машину, это может быть именно то, что вам нужно. Любителям радиоуправления, строящим крылья и фюзеляжи, я бы порекомендовал USB-версию, так проще настроить электронику и программное обеспечение. Но не отчаивайтесь, если вы действительно хотите собрать версию с параллельным портом. Просто напишите мне, если у вас возникли проблемы, и несколько фотографий для добавления в галерею конструктора
Happy CNC FOAM RUTCH
НАСТОЯЩИЕ:
Нравится нагрузка . ..
VEVOR HOT WIRE FOAM RUTH STROCK MACHIN
Люди, которые купили этот товар, также купили
Описание Спецификация Вопросы и ответы Отзывы
Станок для резки пенопласта
Этот станок для резки пенопласта может резать и гравировать пенопласт, губку, картон KT и другие материалы, а также превращать их в архитектурные модели, столы для песка. , модели самолетов, губчатые подушки для автомобилей и т. д. С бесступенчатой регулировкой температуры для адаптации к различным материалам. Идеальный инструмент как для дома, так и для школы.
Прочное оборудование и инструменты, меньше платите
VEVOR — ведущий бренд, специализирующийся на оборудовании и инструментах. Наряду с тысячами мотивированных сотрудников VEVOR стремится предоставлять нашим клиентам прочное оборудование и инструменты по невероятно низким ценам. Сегодня VEVOR оккупировал рынки более чем 200 стран с более чем 10 миллионами членов по всему миру.
Почему выбирают ВЕВОР?
- Премиальное прочное качество
- Невероятно низкие цены
- Быстрая и безопасная доставка
- Бесплатный возврат в течение 30 дней
- Внимательное обслуживание 24/7
Прочное оборудование и инструменты, платите меньше
VEVOR — ведущий бренд, специализирующийся на оборудовании и инструментах. Наряду с тысячами мотивированных сотрудников VEVOR стремится предоставлять нашим клиентам прочное оборудование и инструменты по невероятно низким ценам. Сегодня VEVOR оккупировал рынки более чем 200 стран с более чем 10 миллионами членов по всему миру.
Почему выбирают ВЕВОР?
- Высокое качество
- Невероятно низкие цены
- Быстрая и безопасная доставка
- 30-дневный бесплатный возврат
- Внимательное обслуживание 24/7
Гибкая регулировка
Угол наклона колонны и нагревательной проволоки, а также положение направляющей линейки можно свободно регулировать в соответствии с требованиями резки.
Регулируемая температура
Адаптер питания оснащен кнопкой бесступенчатой регулировки температуры для регулировки температуры нагревательной проволоки для адаптации к различным материалам. Также с защитой от перегрузки по току для безопасности во время работы.
Круглая форма для резки
Круглая форма для резки в комплекте для резки пенопласта на круглое кольцо, коноид, цилиндр и т. д. .
Конструкция с двойными отверстиями
Выбор другого отверстия приведет к другой максимальной ширине резки, что сделает резку более либеральной.
Катушка премиум-класса и нагревательный провод
Использует нагревательную проволоку 0,2 мм и высококачественную катушку емкостью 20–40 м (0,3–0,4 мм) для длительного использования.
Технические характеристики
Электрический ток: 3A
Напряжение: 10-240V
. Пожарная проволока: 0,28 мм
. Ширина среза: 25,6 дюйма (65 см)
Макс. высота среза: 9,8 дюйма (25 см)
Температура: 50–300 ℃ (бесступенчатая регулировка)
Размер продукта: 30,71 x 12,99 x 2,17 “(78 x 33 x 5,5 см)
Размер пакета: 33,07 x 14,96 x 4,33″ (84 x 38 x 11 Com)
“(84 x 38 x 11000) Tough Equipment & Tools, Pay Less
VEVOR — ведущий бренд, специализирующийся на оборудовании и инструментах. Наряду с тысячами мотивированных сотрудников VEVOR стремится предоставлять нашим клиентам прочное оборудование и инструменты по невероятно низким ценам. Сегодня VEVOR оккупировал рынки более чем 200 стран с более чем 10 миллионами членов по всему миру.
Почему выбирают ВЕВОР?
- Высокое качество Tough
- Невероятно низкие цены
- Быстрая и безопасная доставка
- 30-дневный бесплатный возврат
- Внимательное обслуживание 24 часа в сутки 7 дней в неделю
в оборудовании и инструментах. Наряду с тысячами мотивированных сотрудников VEVOR стремится предоставлять нашим клиентам прочное оборудование и инструменты по невероятно низким ценам. Сегодня VEVOR оккупировал рынки более чем 200 стран с более чем 10 миллионами членов по всему миру.
Почему выбирают ВЕВОР?
- Premium Tough Quality
- Невероятно низкие цены
- Быстрая и надежная доставка
- 30-дневный бесплатный возврат
- Внимательное обслуживание 24 часа в сутки 7 дней в неделю
Машина для резки пенопласта и гравировки губки и гравировки
5 , картон KT и другие материалы, и превратить их в архитектурные модели, столы для песка, модели самолетов, автомобильные подушки из губки и т. Д. С бесступенчатым контролем температуры для адаптации к различным материалам. Идеальный инструмент как для дома, так и для школы.
- Прочное качество
- Быстрый нагрев
- Высокая гибкость
- Точное измерение
Гибкая регулировка
Угол наклона колонны и нагревательной проволоки, а также положение направляющей линейки можно свободно регулировать в соответствии с требованиями резки.
Регулируемая температура
Адаптер питания оснащен кнопкой бесступенчатой регулировки температуры для регулировки температуры нагревательной проволоки для адаптации к различным материалам. Также с защитой от перегрузки по току для безопасности во время работы.
Круглая форма для резки
Круглая форма для резки в комплекте для резки пенопласта на круглое кольцо, коноид, цилиндр и т. д. .
Конструкция с двойными отверстиями
Выбор другого отверстия приведет к другой максимальной ширине резки, что сделает резку более либеральной.
Катушка премиум-класса и нагревательный провод
Использует нагревательную проволоку 0,2 мм и высококачественную катушку емкостью 20–40 м (0,3–0,4 мм) для длительного использования.
Содержание пакета
- 1 x набор пенопластовой резаки (с круговой режущей формой)
- 1 x Power Cable
- 1 x Ритч-проволока
Спецификации
- Электрический ток: 3A 15
- Электрический.
- Толщина нагревательной проволоки: 0,28 мм
- Материал: огнестойкий МДФ + сплав
- Макс. Ширина кошения: 25,6 дюйма (65 см)
- Макс. Высота среза: 9,8″ (25 см)
- Температура: 50-300℃ (бесступенчатая регулировка)
- Размер продукта: 30,71 x 12,99 x 2,17″ (78 x 33 x 5,5 см)
- Размер упаковки: 33,07 x 14,96 x 4,371 ” (84 x 38 x 11 cm)
- Electric Current
- 3A
- Voltage
- 10-240V
- Heating Wire Thickness
- 0.
28 mm
- Material
- Fire MDF + Alloy
- Макс. Ширина резки
- 25,6 “(65 см)
- MAX. Высота резания
- 9,8″ (25 см)
- ТЕМПЕРА
- 50-3007
- 50-3007. Стивно-адаптабельный)
- 50-3007 (Steeping Steeplable)
- . x 12,99 x 2,17″ (78 x 33 x 5,5 см)
- Размер упаковки
- 33,07 x 14,96 x 4,33″ (84 x 38 x 11 см)
Цена 4.8
Качественный 4,5
Функции 4.
6
Легко использовать 4.7
- Корзина
- Список желаний
- Свяжитесь с нами
- Отследить ваш заказ
- О нас
- НАДПИСИ И 3D-ФОРМЫ – Сколько раз вы сталкивались с проблемой создания сложных 3D-логотипов? И все уже известные способы показались неподходящими или слишком дорогими? Станок с ЧПУ для резки пенопласта с горячей проволокой справится практически со всем. Его ограничивает только ваше воображение!
- АРХИТЕКТУРНЫЕ ЭЛЕМЕНТЫ – Архитектурные детали из пенополистирола (формы, навершия, перила, замковые камни, концы парапетов, балясины), покрытые укрепляющими сетками и лепниной, становятся очень популярными благодаря легкому весу, простоте сборки, точности исполнения, цене и тому факту, что они экологически чистые.
- ИЗОЛЯЦИЯ НАРУЖНЫХ СТЕН – Станок для резки пенопласта с ЧПУ на строительной площадке? Ну да, так как это лучший способ подготовки наружного утепления стен на месте, что приводит к экономии трудозатрат и максимально качественной теплоизоляции.
- ДЕКОРАТИВНЫЕ ДЕКОРАЦИИ ДЛЯ ЯРМАРОК, ТЕАТРА И КИНО – Нет станков, столь же полезных, как станки для резки пенопласта с ЧПУ с горячей проволокой при строительстве выставочных киосков и декораций для фильмов или театров. Его скорость и точность резки позволяют создавать любые декорации и сценические решения в короткие сроки и без больших финансовых затрат.
Типичные вопросы и ответы о 9004 продуктах 9004 Долговечен ли продукт? …
Задайте первый вопрос
Отзывы клиентов
23 Отзыв
ТБ
владелец
отлично, все что мне нужно. Резак для пенопласта пришел вовремя, настройка была легкой, с хорошими четкими инструкциями. Я только что закончил свой первый проект, и он идеально подходил для этой работы!
См. Подробнее см. Меньше
0
Томас
Великий реза Показать больше Показать меньше
0
pascal
tres bon vendeur
voila j ais u de souci avec le mat_ielle ,mais le vendeur _ait a mon _oute est le probl_e a _ r_olut tr_ rapidement ,merci au vendeur pour sont s_ieux ,je recommande sont magasin tr_ s_ieux est a l _oute de c_st client
См. больше См. меньше
0
Helen ODea
Горячая проволока Dipone Foam Cutting Machine Steely Cutter S0005
См. Подробнее см. Меньше
0
Pascal
TRES Bon Vendeur
Voila jais u de souci avec le matériel, mais reere émere éte éte éte étere éte éte éte émere émere émere éte émere émere. ,merci au vendeur pour sont sérieux ,je recommande sont magasin très sérieux est a l écoute de c’est client
Показать больше Показать меньше
0
Просмотреть все отзывы клиентов
Люди, которые просматривали этот товар, также просматривали
Вернуться к началу
44-330-175-5511
С понедельника по пятницу, с 08:00 до 16:00, GMT+1
© 2009 – 2022 VEVOR. Все права защищены. возможность точно вырезать любую форму аэродинамического профиля из проекта САПР. Правильно настроенный резак для пенопласта с ЧПУ с горячей проволокой может сэкономить вам много усилий и обеспечить гладкую поверхность. В этой статье вы узнаете, как сделать своими руками простой резак для пенопласта с ЧПУ с горячей проволокой, чтобы вырезать крылья из пенопласта для производства пенопластового самолета.
Это будет резак для пенопласта с ЧПУ с горячей проволокой с функцией 3D-резки и программным обеспечением для управления Arduino.
Машина будет иметь нихромовую проволоку (горячую проволоку), натянутую между двумя опорами. Проволока нагревается за счет пропускания через нее тока, а опоры перемещаются относительно друг друга, определяя форму разреза. Вырезаемый 3D-проект САПР преобразуется в G-код и передается на машину, которая перемещается по четырем независимым осям для создания сложных контуров, таких как конические крылья.
Движение каждой оси, которое управляется независимо, может быть достигнуто любыми средствами, такими как линейные подшипники на гладких стержнях или с помощью выдвижных направляющих различных размеров. Каждая ось приводится в движение шаговым двигателем через ходовой винт, ремень и шкив GT2 также могут использоваться в зависимости от размера станка для резки пенопласта с ЧПУ с горячей проволокой . Силы резания, связанные с режущим станком, минимальны, а алюминиевая конструкция должна быть достаточно жесткой, чтобы выдерживать натяжение проволоки, натянутой между опорами. Двигатель является обязательным для режущего станка, мы обычно используем шаговый двигатель для резака.
Удивительно, но это настоящий четырехосевой станок, способный одновременно резать любые формы с обеих сторон. Прежде чем приступать к следующей работе, возникает проблема – как управлять 4 независимыми осями одновременно. время. Многие технические специалисты сосредотачиваются на 3-осевых машинах, таких как 3D-принтеры, но, похоже, недостаточно документации по созданию четырехосевой машины с использованием легкодоступных деталей и программного обеспечения с открытым исходным кодом. Мы нашли несколько человек, которые выполняли аналогичные проекты с использованием Arduino и Grbl, и решили сделать собственный резак для пенопласта с ЧПУ с горячей проволокой.
Шаг 1: Аппаратное обеспечение
В зависимости от дизайна, который вы любите нарисовать, чтобы вы могли заменить детали, которые вы найдете локально в своем районе, вы также можете связаться с нами для доставки запчастей, вы можете потратить дополнительный налог если покупать за границей. Например, вы можете переключать стальные трубы/гладкие стержни с помощью ползунка ящика, который может действовать как линейная ось.
Фанера (12 мм)
Направляющие (стальные трубы, гладкие стержни)
Ходовой винт (M8 x 600 мм, если требуется ось)
Муфта двигателя M8-M5 (M8 для ходового винта и M5 для вала двигателя)
Arduino Mega 2560
Плата Ramps 1.4
Шаговые двигатели (по одному на каждую ось)
A4988 Шаговый драйвер (по одному на каждый шаговый двигатель)
Блок питания 12 В для Arduino+Ramps проволочный режим)
Нихромовая проволока (калибр 32-28, в зависимости от размера машины)
Основными компонентами и деталями являются Arduino Mega, Ramps 1. 4, шаговые драйверы и двигатели. В остальном машина может быть изготовлена с любым дизайном и оборудованием.
Step 2: Software
Grbl Hotwire Controller
4 Axis G-code Generator
Wing Gcode
Jedicut
FoamXL
The difficult thing in making a 4 axis hot wire CNC foam cutter is finding программное обеспечение для генерации G-кода и управления машиной. Многие люди используют DevFoam и profilli для генерации G-кода и управления своей машиной. мы можем поставить это управляющее программное обеспечение, если вы покупаете машину у нас.
Мы делаем сообщение, это было для для резки пенопласта с ЧПУ с горячей проволокой с использованием Arduino и GRBL, оттуда мы начали строить машину.
Шаг 3: Строительство машины
Конструкция конструкции изготовлена из 12 -миллиметровой фанеры, линейная сборка изготовлена с использованием стальных труб 1/2 дюйма с фанерными раздвижными блоками. Вы также можете попробовать другие варианты, если хотите. Конструкция скользящих блоков очень хороша, ее можно улучшить, чтобы предотвратить прямой контакт, введя линейный подшипник или втулку. Поскольку мы используем ходовые винты, у них достаточно крутящего момента, чтобы преодолеть трение и при этом обеспечить хорошее разрешение. Две стальные трубы создают опорную силу и удерживают направляющий блок на одной оси.
Вертикальная стойка расположена поверх горизонтального направляющего блока. Она имеет четыре трубки для надлежащего ограничения движения. Требуется минимум три, чтобы предотвратить изгиб вертикальной башни. Это необходимо для того, чтобы прочная конструкция делала движение стабильным.
Ходовой винт, направляющий движение, крепится к шаговому двигателю с помощью гибкой муфты. Это помогает при любой незначительной несоосности между валом и винтом. Вертикальная башня имеет шаговый двигатель со встроенным ходовым винтом, который можно приобрести или заменить на обычный шаговый двигатель и муфту.
Две башни являются зеркалами друг друга, и в основании предусмотрено место для зажима машины, мы разработаем новый резак для пены с ЧПУ с горячей проволокой, пространство двух башен будет разделенным и гибким, вы можете настроить горячую Длина провода, потому что это разделенный корпус для резака.
Примечание. При использовании поверхностей скольжения, в зависимости от материала, может произойти явление, называемое «прилипание и скольжение». Это приведет к тому, что движение станет неровным и вызовет вибрации. Это также может привести к блокировке поверхностей, что приведет к чрезмерным нагрузкам и пропущенным шагам при использовании шагового двигателя.
Шаг 4: Подключение электроники
Следующим шагом является подключение электроники, перемещение двигателей и настроить машину. это не сложно. У нас есть 4 шаговых двигателя, которые нужно подключить к нашей плате Ramps. Провода должны удлиняться, чтобы обеспечить достаточный ход осей.
Проводка на станке подключается к нашей плате Ramps, которая представляет собой плату с ЧПУ для Arduino Mega2560. Ramps может поддерживать до 5 драйверов шаговых двигателей, таких как A49.88. Мы используем двигатели Nema 17 с 200 шагами на оборот с шагом 1/16 микрошага, что обеспечивает плавное вращательное движение.
Важно, чтобы драйверы шаговых двигателей A4988 можно было прикрепить поверх пандусов, по одному на каждую ось станка. Убедитесь, что микросхема A4988 правильно ориентирована, прежде чем прикреплять ее к плате пандусов. Каждый шаговый двигатель может потреблять до 2 ампер, драйверы шаговых двигателей имеют радиаторы для отвода тепла. На плате также есть полевой МОП-транзистор на 11 А для контроля температуры провода, подключенного к контакту D8. Все компоненты на плате будут нагреваться, убедитесь, что обеспечено надлежащее охлаждение.
Важно, чтобы при включении системы шаговые двигатели продолжали потреблять ток для удержания позиции удержания. Это означает, что машина находится в хорошем состоянии, когда она удерживает позицию. Такие компоненты, как драйверы шаговых двигателей и полевые МОП-транзисторы, могут сильно нагреваться во время работы. Не используйте плату Ramps без активного охлаждения.
Мы вырезали лазером основу для Arduino и Ramps и прикрепили вентилятор на 12 В постоянного тока, чтобы обеспечить активное охлаждение платы.
Шаг 5: Настройка машины
Каждый горячий проводной пенопластовой резак должен быть должным образом настроен перед работой. Поскольку мы используем шаговые двигатели в системе с разомкнутым контуром (без обратной связи), нам нужно знать, как далеко будет перемещаться каретка при каждом обороте шагового двигателя. Это зависит от количества шагов на оборот двигателя, шага ходового винта и уровня микрошага, который вы используете.
Двигатель важен для движения, и мы используем шаговый двигатель, как известно. Мы используем шаговый двигатель со скоростью 200 шагов/об, приводимый в действие драйвером A4988 с микрошагом 1/16, приводящим в движение ходовой винт с шагом 2 мм.
Ходовой винт, который я использовал, был двухзаходным, следовательно, значение было бы вдвое меньше, чем указано выше, т.е. «800». Если это четырехзаходный винт, то значение составляло бы четверть указанного выше значения.
После прошивки Mega 2560 с помощью файла Grbl8c2MegaRamps откройте последовательный монитор и введите «$$», чтобы получить доступ к панели настроек Grbl. Чтобы изменить любое значение, введите $number=value. Например, $0 = 100, вам нужно проверить это, как только машина настроена, убедитесь, что машина перемещает точную сумму, как показано в контроллере.
Шаг 6: Прикрепление горячей проволоки
Чтобы разрезать пену, вам нужен провод сопротивления (горячий провод, как общеизвестный), изготовленный из подходящего материала (нихрома или титановых материалов), который может противостоять нагреву и будет иметь одинаковую температуру по всей длине.
Нихром является подходящим материалом и наиболее часто используется. Лучше всего использовать как можно более тонкую проволоку, чтобы уменьшить образование пропила при резке и получить четкие линии разреза. Как правило, чем длиннее проволока, тем большее натяжение должно быть приложено и тем толще должна быть проволока. Таким образом, вам необходимо учитывать ширину вашего реза, а затем спроектировать длину горячей проволоки. Это может быть не очень хорошо, если ширина реза слишком велика, потому что это будет неточно в движении.
Поэкспериментируйте с проводами различной толщины от 32AWG до 28AWG.
Следующим шагом для изготовления станка для резки пенопласта с ЧПУ с горячей проволокой является прикрепление нихромовой проволоки к станку, поскольку у нас есть 4 независимые оси, мы не можем просто привязать оба конца проволоки к башням. Проволока должна иметь некоторое удлинение либо с помощью пружины, либо с грузом, прикрепленным к концу с помощью подвесного молотка или шкива.
Примечание. К проволоке можно приложить постоянное натяжение с помощью плоской пружины (пружины постоянной силы) или путем подвешивания собственного груза на конце. Дешевый способ получить пружину с постоянным усилием – использовать натяжные катушки с идентификационными картами. Возьмите качественный, и вы даже можете поставить пружины параллельно, чтобы обеспечить большее тяговое усилие.
Шаг 7: Программное обеспечение управления и генерация G-Code
GRBL Hotwire Controller
Мы используем панель управления GRBL, разработанную Гарретом Виссер, которая была адаптирована для вырезания Hotwire Daniel Rascio. Панель имеет независимое управление толчковым движением для всех осей, включая возврат в исходное положение. Также есть инструмент визуализации графиков Gcode и возможность сохранять собственные макросы. Температурой Hotwire можно управлять с помощью M3/M5 для включения/выключения и команды S”xxx” для установки выходного напряжения либо вручную, либо с помощью полосы прокрутки в программном обеспечении. Горячий провод должен быть подключен к выходу «D8» и питается от питания, подключенного к входу «11A» на Ramps.
Генератор G-кода крыла
Генератор G-кода крыла — это программа для генерации G-кода XYUV для резки горячей проволокой крыльев модели самолета. Он работает на Python 2.7, а также может интегрироваться с интерфейсом LinuxCNC Axis. Есть и онлайн-версия. Это позволяет вам вводить параметры крыла, такие как хорда корня, хорда законцовки, развертка, длина гентри и даже размыв опоры. Он имеет базу данных аэродинамических профилей в формате .dat. Таким же образом можно импортировать новые аэродинамические поверхности.
Это простое в использовании программное обеспечение позволяет накладывать крылья на один и тот же кусок пенопласта для экономии материала. Полученный G-код можно отправить на станок для резки пенопласта с ЧПУ через контроллер Grbl.
Jedicut 2.4
Jedicut — отличная программа, поскольку она может работать как в CAD/CAM, так и в качестве контроллера машины. Думал, что контроллеру машины нужен ПК со старым интерфейсом параллельного порта. Он также имеет плагин для генерации G-кода. Не самый простой в настройке. Некоторые параметры и сообщения об ошибках на французском языке, но если вы посидите с ним какое-то время, вы сможете заставить его работать.
Он имеет множество функций, таких как мастер резки, который поможет вам сделать зачистку крыльев и компенсировать разрез проволоки, добавив толщину обшивки. Он может резать не только профили крыльев, но и надписи и другие формы.
Примечание. G-код Wing генерирует G-коды в абсолютном режиме, который без проблем работает на Grbl, но Jedicut генерирует G-код в добавочном режиме. У нас были трудности, когда мы сначала заставили его работать, когда машина просто двигалась вперед и назад. Если это произойдет, отредактируйте G-код, чтобы удалить ненужные строки в заголовке.
G-код Wing и Jedicut генерируют G-код с некоторыми неподдерживаемыми кодами Grbl в заголовке. Контроллер отобразит на мониторе такие ошибки. Отредактируйте G-код и удалите ненужные строки кода.
Рабочие G-коды с обоими программами прилагаются, используйте их для проверки контроллера.
Шаг 8: Установка скорости подачи и температуры
Горячая проволока работает на разрезании, таяв окружающий пластик, и когда проволока остается в одном положении в течение некоторого времени, окружающие пенопласты продолжают таять. Это увеличивает ширину разреза и может привести к неточности размеров. у нас есть решения для этого. Есть две переменные, которые влияют на разрез разреза.
1. Скорость резки.
2. Температура провода.
Скорость резания — это скорость, при которой проволока прорезает материал. в основном обозначает в мм в минуту. Чем выше скорость, тем меньше пропил, но тем выше требуемая температура, а также натяжение проволоки должно быть достаточным, чтобы выдерживать силы резания. Хорошие скорости резки составляют от 350 мм/мин до 500 мм/мин.
Необходимо знать, что температура проволоки должна быть немного выше, чем температура плавления пенопласта, который вы режете. В идеале вы хотите резать только лучистым теплом, когда проволока на самом деле не касается материала, а режет перед ним. Температура регулируется величиной тока, протекающего через провод, который определяется приложенным напряжением. Дополнительные знания. Если вы хотите разместить больше горячих проводов, трансформатор напряжения на машине важен для количества горячего провода. Чем больше трансформатор, тем больше количество горячих проводов.
Существует программное обеспечение, которое позволяет использовать ШИМ-управление проволокой для ее нагрева в нужные моменты для оптимизации скорости подачи при резке. Температура провода определяется квадратом силы тока, умноженной на сопротивление.
Если вы используете нихромовую проволоку, Калькулятор применения нихромовой проволоки — это классное приложение, которое поможет вам определить температуру проволоки в зависимости от ее длины и приложенного напряжения. Для нашей установки с длиной проволоки 850 мм мы приложили напряжение 26 В и резали со скоростью подачи 350 мм/мин.
Шаг 9: Рабочий процесс резки с горячим проводом
Возьмите систему Coreldraw и Mach В качестве примера, во -первых, вам нужно рисовать графику в Coreldraw и экспортировать его в формат DXF, тогда импортируйте этот формат DXF в DeVfoam, Creat. траектория резки и экспорт в формат ЧПУ. Наконец, загрузите формат ЧПУ в систему MACH и начните работу по резке.
Процесс начинается с проекта, который экспортируется в формате DXF. Затем этот файл импортируется в программное обеспечение CAM и выводится в виде G-кода. Станок включен и откалиброван, материал помещен на верстак, и установлено начало координат. Включите горячую проводку, запустите файл G-кода и наблюдайте, как машина сделает всю работу за вас.
Надеюсь, вам понравилось руководство. Попробуйте сами, машину легко собрать, и она очень неприхотлива. С ним можно сделать много удивительных вещей. Счастливого полета!
Myaid Machinery может поставить этот станок для резки пенопласта с ЧПУ с горячей проволокой курьером DHL.
Станок для резки пенопласта с ЧПУ – AEROBASE
Станок для резки пенопласта с ЧПУ
Используя современные технологии, Станки для резки пенопласта с ЧПУ с горячей проволокой позволяют создавать практически любые изделия самой сложной формы быстро, точно и относительно недорого.
Станки для резки пенопласта с ЧПУ с горячей проволокой используются для создания букв, логотипов (3D-логотипов), графики, вывесок, этикеток для внутренней и наружной рекламы, элементов декора, ярмарочных киосков, реквизита и дисплеев магазинов, P.O.P. экспонаты, декорации для театра или кино, макеты изделий, все виды упаковки, аттракционы, архитектурные формы, масштабные архитектурные макеты, тематический реквизит, изоляция труб, сборные железобетонные формы, колонны и т. д.
D Горячая проволока Фрезы для пенопласта с ЧПУ может использоваться для самых разных операций по резке. Они могут вырезать практически все из пенополистирола – пенополистирол и экструдированный пенополистирол – пенополистирол
Резак для пенопласта с ЧПУ – это станок , управляемый компьютером PC , способный вырезать любые трехмерные объекты из экструдированного и пенополистирола (EPS и XPS) . Резка выполняется с помощью горячей режущей проволоки , перемещающейся по вертикальной и горизонтальной осям с помощью шаговых двигателей , управляемых электронным контроллером , подключенным к ПК и управляемым с помощью нашего уникального программного обеспечения . Это обеспечивает безупречную точность, высокую скорость обработки и неизменно отличное качество.
Точные механизмы и идеальное электронное управление движением двигателей позволяют оператору вырезать любую форму, если ее толщина соответствует толщине материала. Существует также возможность разработать и вырезать несколько разных контуров одного и того же проекта, в результате чего получаются очень привлекательные 3D-формы. TurnTable позволяет резать, например. сфер, токарный станок незаменим при резке колонн, дополнительные возможности дает инструмент ShapeWire Tool
Режущая проволока
Режущая проволока NiChrome во время резки достигает температуры в несколько сотен градусов Цельсия. В зависимости от ширины резака для пены (т.е. длины режущей проволоки) мы используем никель-хромовые проволоки следующих диаметров: 0,15, 0,25, 0,40 и 0,60 мм. Каждый станок для пенопласта с ЧПУ Hot wire поставляется с катушкой проволоки для свободной резки (100 г). Basic Станки для резки пены с ЧПУ с горячей проволокой поставляются со стандартной никель-хромовой проволокой. В зависимости от параметров, заданных оператором, этого провода должно хватить на ок. 8-10 часов работы. Он недорогой и идеально подходит для повседневного использования.
Многопроволочные резаки для пенопласта и резаки самой широкой серии с пневматическим натяжением проволоки поставляются с изготовленной на заказ проволокой из титанового сплава высочайшего качества NiCr. Хотя проволока из титанового сплава немного дороже, чем обычная никель-хромовая проволока, она реже ломается, чем (в среднем, она служит в 5-6 раз дольше, чем , никель-хромовая проволока ), и обладает гораздо большей устойчивостью к растяжению при высоких температурах. В результате его можно использовать с более сильной натяжной пружиной или пневматическим натяжением, что дает значительно более высокая скорость резки и улучшенное качество резки . Он доступен за дополнительную плату для всех наших блоков шириной 1,3 метра или шире.