Производство утеплителя из камня.
Существует несколько видов и способов производства утеплителя из камня. Рассмотрим их.
1.Шлаковата.Самый древний самый массовый и самый дешёвый это разогрев смеси минералов (известняка с минералами базальтовой группы) в вагранке с использованием коксующего угля в качестве теплоносителя. В состав шихты добавляется доменный шлак металлургических производств.
Эта масса расплава раскалённой толстой струёй льется на центрифугу. Валки центрифуги вращаются со скоростью 5000 об/мин разбивают струю на мелкие капли и придают им реактивные скорости. Разлетаясь капли удлиняются, мгновенно остывают превращаются в очень тонкие и короткие волокна.
В поток мелких волокон вдувается фенолформальдегидная смола для того чтобы склеить волокна и образовать теплоизоляционные плиты. Раньше полученное таким способом волокно называли, совершенно справедливо, шлаковата.
Сейчас на сайтах продавцов такого утеплителя можно прочитать что это минеральная вата на базальтовой основе. Некоторые копирайтеры не понимая о чём пишут называют шлаковату базальтовой ватой. Больше всего у нас производиться и продаётся теплоизоляционных плит полученных именно таким способом.
2.Минеральная вата.Другой способ производства каменных волокон: использование в качестве теплоносителя природного газа, при плавке смеси минералов базальта с известняком в плавильной печи. В этом случае в составе расплава не будет доменного шлака. Полученное волокно называется минеральной ватой, можно добавить: “на базальтовой основе”.
Такое производство волокон дороже чем производство шлаковаты, но утеплитель получается более качественный, т.к. сами волокна будут длиннее.
В качестве клея связывающего волокна для получения теплозвукоизоляционных плит опять же будет использована фенолформальдегидная смола.
Лучшие минеральные плиты выпускают ведущие европейские производители Parock и Rockwool, которые успешно продаются у нас.
В России работают несколько заводов этих брендов.
3.Базальтовая вата.Первые базальтовые волокна были получены в середине прошлого века в Советском Союзе. Главное отличие от минеральной ваты – в плавильную печь загружается только минерал базальтовой группы. Там не будет ни известняка, ни доломита, ослабляющих волокна.
Базальтовый расплав густой и его нельзя превратить в волокна с помощью центрифуги. Для получения тонких и длинных базальтовых волокон применяется вертикальный раздув сжатым воздухом под давлением 9 атм. Струи расплава истекают из отверстий раскалённого стального питателя и попадают в сопла раздувочного устройства.
3.1.Технология производства плит теплоизоляционных.
Базальтоволокнистые теплоизоляционные плиты производит компания «Базальт-Мост».Технология получения теплоизоляционных плит так же совершенно другая, чем при производстве минеральных плит. Базальтоволокнистый ковер проливается водным раствором дисперсии ПВА. Излишняя влага удаляется методом вакуумирования. Сушка плит происходит методом прососа горячего воздуха сквозь толщу ещё влажной теплоизоляционной плиты.
4.Экологичность.4.1 Мелкие невидимые невооруженным глазом минеральные волокна могут попасть в легкие человека.
Базальтовые волокна длиннее и толще, чем минеральные и в легкие человека попасть не могут.
4.2 В базальтовых теплоизоляционных плитах в качестве связующего используется безопасный клей ПВА.
Page not found – Сайт b-utepliteli!
Главным преимуществом базальтового волокна можно отметить следующие позиции:
1. Низкая теплопроводность, это позволяет достичь поставленных задач по теплопроводности в условиях низких температур северных регионов.
2. Базальтовая вата отличается длительным сроком службы. Производители отмечают ее срок эксплуатации в 40-50 лет, это – намного больше, если сравнивать Базальтовую вату с другими теплоизоляционными материалами.
3. Базальтовая вата или на профессиональном языке Базальтовый утеплитель или Базальтовое волокно не подвержена образованию плесени, грибка, гниению, и отличается высокой устойчивостью к воздействию ультрафиолета.
4. Базальтовый утеплитель (базальтовое волокно) не разрушается доже в условиях повышенной вибрации, что нельзя сказать про другие теплоизолирующие материалы.
5. Базальтовый утеплитель (волокно) обладает повышенным звукоизолирующими характеристиками.
6. Базальтовое волокно известно очень низкой плотностью, это свидетельствует о высоких теплозвукоизоляционных ее свойствах.
7. Базальт отличается химической устойчивостью.
8. Базальтовый утеплитель отличается высоким показателем устойчивости к открытому огню, а значит Базальтовый утеплитель отвечает пожаробезопасностью при его использовании. Взрывобезопасность ровна нулю.
9. Базальтовый утеплитель не теряет своих технических свойств и под воздействием температурных перепадов. Базальт легко переносит нагрев, и охлаждение.
10. Базальт отличает высокая температура своего применения. Если прочие минерал ватные материалы можно применять только до температуры до 400 градусов по Цельсию, то изделия на основе базальтового волокна можно применять до 700 градусов, а краткосрочно – и до 1100 градусов.
11. Базальт в Мире известен как самый экологически чистотой продукт. Он не содержит в себе ни органических веществ, ни горючих, ни канцерогенных. Химическая формула
Базальта совпадает с формулой натурального камня – базальта.
ООО «СМП-МЕХАНИКА» – ЗАВОД БАЗАЛЬТОВОЙ ТЕПЛОИЗОЛЯЦИИ
ООО «СМП-Механика» с 2002 года выпускает экологически чистую, теплоизоляционную, огнезащитную продукцию без синтетических связующих, из тонкого базальтового волокна, под торговой маркой WATTAT. Более 17 лет компания производит базальтовые прошивные маты. В 2015 году запущено производство непрерывного базальтового волокна и выпуск на его основе вибростойкой изоляции, композитов, а также армирующей основы для композитных материалов.
Выпускаемая продукция:
– Маты базальтовые прошивные WATTAT МП, плотность: 50, 75, 100, 125 кг/м3. ГОСТ 21880-2011.
-Маты базальтовые прошивные энергетические WATTAT МБПЭ, плотность: 35, 50, 60, 75, 80, 100, 125 кг/м3. ТУ 5769-002-57231417-2008.
-Плиты негорючие термостойкие базальтовые ПНТБ-200 на бентонитовом глинистом связующем. ТУ 5769-001-57231417-04.
-Базальтовые иглопробивные маты ИПМ-Б WATTAT. СТО 5769-003-57231417-2015.
-Базальтовая фибра. СТО 23.99.19-005-57231417-2016.
-Базальтовые шнуры, ленты. СТО 23.99.19-006-57231417-2017.
-Базальтовая арматура. ГОСТ 31938-2012.
-Продукция из стекловолокна ПСХ-Т, ИПМ-С, навивные цилиндры.
Базальтовые прошивные маты, выпускаемые ООО «СМП-Механика» под торговой маркой WATTAT, являются уникальными и в отличие от абсолютного большинства (99% всего рынка изоляции) минераловатных утеплителей, не содержат синтетические связующие (фенолформальдегидные, карбамидные, какие-либо другие смолы и добавки). В производстве продукции не используется «подшихтовка» сырья легкоплавкими породами, модуль кислотности готовой продукции Мк ≥ 4, что говорит о длительном сроке эксплуатации изоляции, превышающем срок службы изолируемых конструкций. Температура применения 700°С, краткосрочно 900°С. В отсутствии серьёзных вибраций они могут прослужить долгие годы, создавая высоконадёжный теплоизолирующий слой.
Данное обстоятельство имеет важное значение для предприятий, относящихся к химической и нефтехимической промышленности нашей страны, имеющих в эксплуатации трубопроводы, транспортирующие сильные окислители: кислород, хлор, фтор, озон, азотная кислота, серная кислота, перманганат калия и др. В соответствии с п. 5.10 СП 61.13330.2012 «Тепловая изоляция оборудования и трубопроводов», изоляция таких трубопроводов минераловатными изделиями со связующими запрещена. Могут применяться маты базальтовые прошивные WATTAT или маты БСТВ.
Завод WATTAT производит всю возможную линейку матов базальтовых прошивных теплоизоляционных, всех плотностей, толщин и с любыми обкладками. Маты выпускаются в соответствии с ГОСТ 21880-2011, часть матов для энергетической отрасли, выпускается на основании ТУ 5769-002-57231417-2008 в соответствии с ГОСТ.
Разработчик Межгосударственного стандарта (ГОСТ 21880-94, 21880-2011) «Маты прошивные из минеральной ваты теплоизоляционные» АО «ТЕПЛОПРОЕКТ» рекомендует применение матов WATTAT для промышленных объектов и оборудования, термонагруженных агрегатов и аппаратуры.
Альбом технических решенийПродукция сертифицирована, имеет: сертификаты соответствия, сертификаты пожарной безопасности, экспертные заключения:
СетификатыЗавод WATTAT имеет благодарственные письма за организацию своевременных поставок материалов и высокое качество продукции.
Подтверждением высокого качества выпускаемой продукции служит признание матов прошивных базальтовых теплоизоляционных WATTAT, плит ПНТБ-200 и иглопробивных базальтовых матов ИПМ-Б Лауреатом конкурсов «Лучший товар Республики Татарстан» и Дипломантом конкурсов «100 лучших товаров России», а также другие многочисленные награды, полученные на международных специализированных выставках. В 2013 году ООО «СМП-Механика» заслужила звание Лауреата Всероссийской Премии «За вклад в экономическое развитие России» в номинации «Российский производитель».
Резидент ТОР «Хабаровск» завод «ТехноНИКОЛЬ – Дальний Восток» начал поставки каменной ваты в Канаду
Первая партия базальтовой изоляции производства хабаровского завода «ТехноНИКОЛЬ – ДВ», якорного резидента ТОР, доставлена в Канаду по заказу международного производителя сэндвич-панелей.По словам Министра Российской Федерации по развитию Дальнего Востока Александра Галушки, «значение экспорта готовой продукции с Дальнего Востока будет только нарастать, поэтому так важно, что инвесторы, пришедшие в ТОРы уже начинают экспортировать свою продукцию. Мы будем оказывать всё необходимое содействие в поддержке экспорта с Дальнего Востока” – отметил Министр.
Хабаровский завод «ТехноНИКОЛЬ – ДВ», входящий в структуру компании ТехноНИКОЛЬ, приступил к активной реализации своей экспортной программы. Практически с первого дня работы предприятия стартовало сотрудничество с Китаем. А в октябре завод «ТехноНИКОЛЬ – ДВ» поставил первую партию хабаровского базальтового утеплителя уже в Канаду. Продукция была доставлена в Ванкувер морем и сейчас поступила к заказчику – производителю сэндвич-панелей. В перспективе компания ТехноНИКОЛЬ планирует расширить круг потребителей хабаровского базальтового утеплителя в Канаде и организовать регулярные поставки материалов в эту страну.
«Высокотехнологичное оборудование, которым укомплектован завод, позволяет нам выпускать утеплитель на основе каменной ваты так называемого нового поколения. Он соответствует не только российским требованиям к теплоизоляционным материалам, но и европейским, которые, как известно, гораздо выше, чем в нашей стране, – комментирует Пётр Орешко, генеральный директор завода «ТехноНИКОЛЬ – Дальний Восток». – Теперь перед нами стоит задача закрепить существующие партнёрские отношения в Северной Америке и продолжить освоение рынка в этом регионе».
Напомним, завод «ТехноНИКОЛЬ – Дальний Восток» по производству каменной ваты был введён в эксплуатацию в конце августа 2016 года. Ежегодный объём выпускаемой продукции составляет 750 тыс. куб. м. К 2019 году объём экспортируемых материалов, произведённых заводом компании в составе ТОР «Хабаровск», увеличится до 20%.
Бизнес на производстве минеральной ваты (декабрь 2021) — vipidei.com
Производство минеральной ваты можно разбить на несколько стадий: подготовка сырья, получение волокна из расплава, полимеризация и нарезка готового материала. Минеральная вата на данный момент является отличным материалом, который имеет широкий спектр применения в различных отраслях.
Высокую эффективность применения данного материала специалисты отмечают и в строительной индустрии. Среди многообразия минеральной ваты, которая представлена на рынке строительных материалов, потребители выделяют уникальные свойства такого материала, изготовленного из базальтовых пород.
Что нужно знать о базальтовой минеральной вате перед началом производства
Данный материал имеет волокнистую структуру. Если перевести с английского языка «базальтовый утеплитель», то дословно можно получить «горная шерсть».
Именно из-за того, что структура материала имеет волокнистый компонент, в ней идет накопление воздуха в больших объемах. При этом такие объемы воздуха практически не перемещаются по толщине этого материала. Это объясняется наличием ряда препятствий в виде большого количества волокон. Такое свойство в комбинации с малым диаметром волокна дает возможность базальтовой вате иметь высокие теплоизоляционные свойства.
На данный момент специалисты выделяют два типа базальтовых волокон, которые встречаются в утеплителях:
- Штапельное волокно. Для данного типа характерным является его диаметр.
- Непрерывное волокно.
При этом сами базальтовые волокна, которые применяются в изготовлении минеральной ваты, могут иметь различные диаметры, от 0,6 мкм до 500 мкм.
Поэтому принято разделять волокна на следующие виды:
- Микротонкие с толщиной 0,6 мкм.
- Ультратонкие с диаметром порядка 1,0 мкм.
- Супертонкие. Их диаметр составляет 3 мкм.
- Тонкие с толщиной около 15 мкм.
- Утолщенные, в диаметре равные 25 мкм.
- Грубые. Такие волокна могут достигать в диаметре 500 мкм.
Во время процесса изготовления материал формируется в рулоны. Также часто применяется формирование его в плиты или маты. При этом материал подразделяется специалистами на нефольгированный и фольгированный виды.
Технология производства минеральной ваты
Способ, с помощью которого производится минеральная вата, был открыт на Гавайских островах. Это стало возможным, когда были найдены камни в результате извержения вулкана. Тогда нашли тонкие нити вулканической породы. Это были первые представители современных волокон, которые используются при изготовлении минеральной ваты. После этого в 1897 г. в Северной Америке получили и первую минеральную вату.
Для производства материала используется следующая технология:
- Применяется специальная печь, в которой температура достигает 1500°С.
- В печь помещается горная порода. Из нее выходит специальный огненный расплав в жидком виде.
- Далее происходит вытягивание такого расплава в волокна. Для этого применяется несколько способов, среди них центробежное дутье, простое дутье и модифицированные методы.
- Когда волокна уже сформированы, в них вводится специальное связующее вещество. Для этого может применяться технология распыления на волокна. Часто используют и полив на ковер из ваты базальтового типа. Есть еще вариант, связанный с приготовлением гидромассы.
- Чтобы минеральной вате придать дополнительные свойства при ее последующей эксплуатации, добавляется специальная смесь. Она позволяет улучшать показатели плотности, проницаемости, гидрофобности и ряд других характеристик.
- Полученный ковер, на который нанесено связующее вещество, обрабатывают термическим путем при температуре, достигающей 230°С. Это позволяет тепловому носителю провоцировать реакцию поликонденсации связующего элемента.
- Когда проведена термическая обработка базальта и туда добавлены необходимые примеси, то на выходе получаем продукт.
Он имеет структуру, которая характеризуется ячеистой сеткой открытой формы. Такой продукт может работать на эффективном уровне при температуре, достигающей 1000°С. Это так называемый верхний предел рабочего диапазона температур минеральной ваты.
- В таком готовом продукте содержание веществ, имеющих органическое происхождение, не превышает обычно показателя в 3%.
- Теперь технология изготовления этого материала выходит на свою завершающую стадию. Производится нарезка в виде плит, которые необходимы для утепления. После этого выполняется упаковка материала и доставка потребителям.
Какое оборудование выбрать?
Оборудование для производства минеральной ваты состоит из шахтной печи, сушильных линий, подпрессовочного оборудования, камеры термообработки.
Достоинства и недостатки бизнеса по производству минеральной ваты
Бизнес на производстве и продаже минеральной ваты — это очень выгодно и не требует крупных вложений.
Данный продукт имеет отличные показатели в плане эксплуатации. Также данный утеплитель может эффективно применяться и при высоких температурах, которые характерны для мест с повышенным коэффициентом пожарной опасности.
Среди недостатков такого продукта специалисты отмечают свойство материала впитывать влагу. Это может значительно ухудшить его свойства тепловой изоляции, а в некоторых случаях привести и к их полной потере. Поэтому, чтобы исключить такие факторы, производители используют покрытия кашированного или алюминиевого типа.
Данный тип минеральной ваты активно используется в строительстве как эффективное средство, при помощи которого осуществляется тепловая изоляция помещений.
Перед тем как применять ее, необходимо обратиться за консультацией к специалистам, которые помогут эффективно организовать утепление дома.
оборудование для производства утеплителя из базальта
оборудование для базальта
оборудование для производства утеплителя из базальта Оборудование для производства утеплителя В этой статье мы рассмотрим оборудование для производства утеплителя из базальта, пеноизола, целлюлозы, льна
Get PriceПроизводство утеплителя из базальта: как
Поэтому приходится «залезать в долги и занимать крупные суммы Для организации производства линии утеплителей из базальта достаточно 300
Get PriceОборудование для производства базальтовых
· 5 Оборудование для производства базальтовых волокон и изделий 51 УСТАНОВКА ДЛЯ ПРОИЗВОДСТВА БАЗАЛЬТОВОГО СУПЕРТОНКОГО ВОЛОКНА (БСТВ) Установка состоит из малогабаритных плавильных печей с
Get PriceЗавод по производству утеплителя из базальта
Завод по производству утеплителя из базальта В наступившем году вновь произошло увеличение цен на энергоносители, например цены на газ ежегодно повышаются на 26%
Get Priceизготовление линии для переработки базальта
переработка базальта оборудование по переработки базальта Карьерное оборудование при,оборудование по переработке базальта,для переработки оборудование по переработки базальта,0 Тендер “оборудование по
Get PriceБазальтовая теплоизоляция, базальтовый
И как водится, не всегда положительными Как показывает практика, полимерные материалы для теплоизоляции, достаточно быстро выходят из строя (изнашиваются), приводя к разрушению утеплителя
Get PriceКомпания “БАЗАЛЬТ” композитная
Оборудование для производства Кремнеземные материалы Емкостное оборудование с этим графиком будем аккуратно поставлять все необходимые для производства материалы Условия
Get Priceоборудование для расплава базальта в китае
впродажепескомойкадляпроизводствабазальта оборудование для расплава базальта в китае Pursuit of innovation and excellence We will provide you with the best products and the best service
Get PriceБизнес на производстве минваты, как его начать
· В этой статье мы рассмотрим оборудование для производства утеплителя из базальта, пеноизола, целлюлозы, льна
Get Priceпроизводство утеплителя из лигнита
Одним из таких направлений является производство утеплителя из базальта, так как базальтовое волокно пользуется огромным спросом среди всех существующих утеплителей
Get PriceНаплавка валков центрифуг производства
Оборудование для производства минеральной ваты и базальтового утеплителя включает стандартный набор, в состав которого входит центрифуга (рис 1)
Get PriceБазальтовый утеплитель: виды, характеристики
· Ценные преимущества готового утеплителя из базальта Современный российский рынок предлагает большое разнообразие изолирующих материалов для обустройства дома, качественных и не слишком
Get PriceОборудование и технологии производства
· Оборудование для производства арболита Технология производства строительных шлакоблоков Бизнес по производству арболитовых блоков: оборудование, технологии
Get PriceТехнологии переработки горных пород
Технологии переработки горных пород, типа базальта, в волокнистые материалы Благодаря своим уникальным свойствам, базальтовое волокно и продукция на его основе находит все более широкое применение во всех отр а
Get PriceКупить базальтопластиковые гибкие связи, цена
Гибкие связи это стержни из базальта, длина которых составляет 2060 см Такие связи служат в качестве анкера для фиксирования в швах кладки трехслойных стен
Get PriceПроизводство теплоизоляции, минеральной ваты
Основное оборудование, инструменты и механизмы для производства: ленточный конвейер 30 000 р; специальная печь для плавки материала 65 000 р; центрифуга для
Get PriceОборудование для производства минеральной ваты
· Оборудование для производства минеральной ваты Типы оборудования Рынок строительных материалов является одним из самых
Get Priceоборудование для расплава базальта в китае
впродажепескомойкадляпроизводствабазальта оборудование для расплава базальта в китае Pursuit of innovation and excellence We will provide you with the best products and the best service
Get PriceБизнес на производстве минваты, как его начать
· В этой статье мы рассмотрим оборудование для производства утеплителя из базальта, пеноизола, целлюлозы, льна
Get Priceпроизводство утеплителя из лигнита
Одним из таких направлений является производство утеплителя из базальта, так как базальтовое волокно пользуется огромным спросом среди всех существующих утеплителей
Get PriceНаплавка валков центрифуг производства
Оборудование для производства минеральной ваты и базальтового утеплителя включает стандартный набор, в состав которого входит центрифуга (рис 1)
Get PriceОборудование и технологии производства
· Рассмотрим процесс производства теплоблоков как бизнес: необходимое оборудование и этапы изготовления материалов, можно ли сделать блоки самостоятельно Вовторых, при производстве стоит использовать достаточно
Get PriceКупить базальтопластиковые гибкие связи, цена
Гибкие связи это стержни из базальта, длина которых составляет 2060 смТакие связи служат в качестве анкера для фиксирования в швах кладки трехслойных стен
Get PriceУтеплитель ЭКОВЕР из базальтовой минеральной
· техника, оборудование, инструменты утеплители и технологии пенопласт минеральная вата Утеплитель ЭКОВЕР из базальтовой минеральной ваты Отзывы13
Get PriceОборудование для эковаты — делаем установку
По стандарту для утепления полов плотность эковаты должна быть в пределах 4045 кг/кубм Именно поэтому, если планируется укладка своими руками без использования выдувной машины, лучше выбирать утеплитель с
Get PriceОборудование для производства теплоблоков с
Чтобы купить оборудование для производства теплоблоков мощностью до 5 м3, подготовить к работе помещение, закупить сырье и оформить все документы, потребуется не
Get PriceОборудование для производства минеральной ваты
· Оборудование для производства минеральной ваты Типы оборудования Рынок строительных материалов является одним из самых
Get PriceAKFA Group запустит завод по производству базальтовой ваты в Ташкенте – Газета.
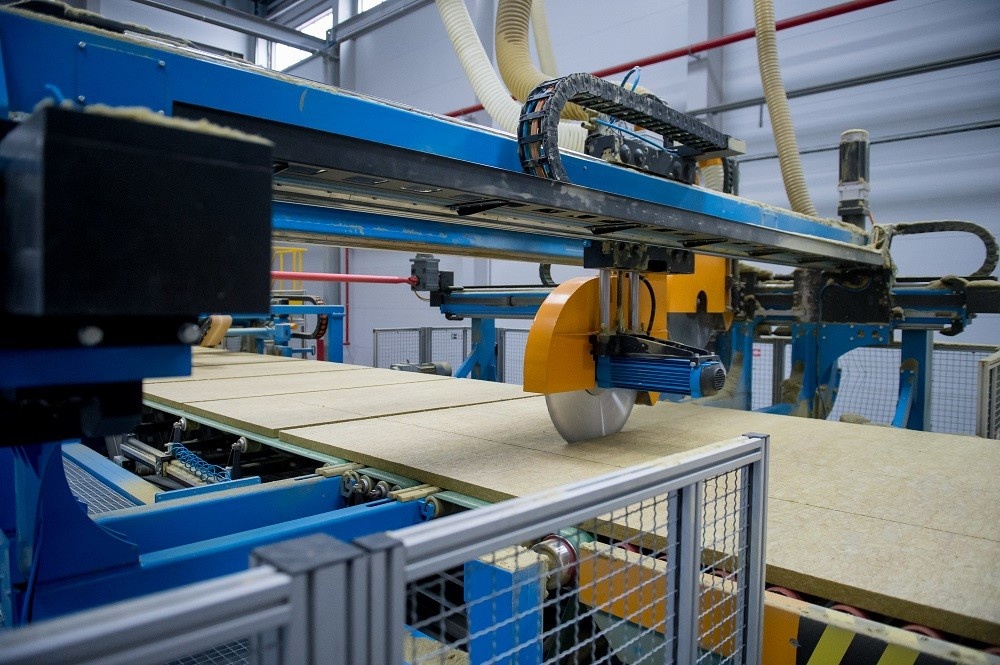
5 декабря в ходе переговоров AKFA Group и итальянской компании STM Technologies S.r.l. был заключен договор на поставку производственно-технологического оборудования по выпуску базальтовой ваты.
STM Technologies S.r.l. является одной из ведущих компаний в мире по поставке, вводу в эксплуатацию и наладке производственных линий. Обладая 25-летним опытом и более 100 проектами в области установки оборудования на пяти континентах, технологические системы STM гарантируют готовую продукцию в соответствии с мировыми отраслевыми стандартами (EN, ASTM), все больше и больше используемой в современном строительном бизнесе.
Благодаря этому группа компаний AKFA планирует запустить в Узбекистане полный цикл автоматизированной линии производства мощностью до 6 млн кв.м. базальтовой ваты в год, что будет соответствовать строгим требованиям экологической безопасности.
Производственная площадь будет расположена на более чем 24 тысячах кв. м территории бывшего завода ТАПОиЧ. В производственный процесс будут вовлечены опытные специалисты из зарубежных стран, а также появится более 150 новых рабочих мест.
Базальтовая вата — современное и наиболее оптимальное решение для теплоизоляции стен, крыш, пола, фундамента, трубопроводов жилых и производственных помещений. Ею также утепляют фасады, промышленное оборудование и любые другие виды строительных конструкций.
Базальтовая вата, которая будет выпускаться в рамках проекта, обладает высокой коррозийной и химической стойкостью. Кроме того, базальт отличается низкой теплопроводностью, высокой прочностью при низких температурах и долговечностью. Эти характеристики делают его практически единственным пригодным для дорожного и жилищного строительства материалом. Срок эксплуатации базальтовой ваты достигает 70 лет.
Запуск нового завода, многолетний опыт работы в строительстве, высокоэффективная технологическая линия, специальная сырьевая база и удачное географическое расположение позволят AKFA Insulation стать надежным поставщиком и партнером для строительной индустрии не только в Узбекистане, но и Центральной Азии.
В ходе ознакомления с процессом строительства делового центра Olmazor Business City в Алмазарском районе Ташкента президент Шавкат Мирзиёев прокомментировал ситуацию на рынке строительных материалов в Узбекистане:
«Необходимо увеличить число домов, сделать жилье доступнее за счет экономии ресурсов. Для этого следует расширить производство строительных материалов, базальтового волокна, сделать так, чтобы они дошли до каждого региона».
На правах рекламы.
|
|
Оборудование и технологии для производства непрерывного базальтового волокна
Публичное акционерное общество «Научно – исследовательский институт стеклопластиков и волокон» предлагает Лучшее в мире , новейшие разработки в области оборудования и технологии производства волокна из непрерывного базальтового волокна (далее – НБВ)
Предлагаем все формы сотрудничества – от разработки ТЭО инвестиций до сдачи завода «под ключ» и обучения персонала заказчика.
CBF основано на использовании последних достижений научно-технического прогресса. Все оборудование выполнено в соответствии с требованиями современного рынка, безопасности и экологичности.
Новизна и неоспоримые преимущества новой технологии в полной мере используют специфику и возможности физики расплавленных базальтовых пород для удешевления производства. Наши решения позволяют при сохранении качества значительно снизить стоимость готовой продукции, повысить производительность оборудования, что дает производителям неоспоримое преимущество на рынке неорганических волокон.
Ровинг Базальтовое волокно NBR 15 – 200х30 на упаковках (с нанесением смазки). ТУ У 023.001-2001
Нить текстильная базальтовая.
Фибра базальтовая рубленая НБС 15-200 ТУ У 023,001-2001
Фибра базальтовая рубленая.
Сырье поступает со склада в виде базальтовой крошки крупностью 5-15 мм. Входной контроль сырья осуществляется в соответствии с техническими условиями, по двум показателям: крупность фракции и засоренность. Сырье поставляется готовым к переработке (промытый и прошедший магнитную сепарацию).
Сырье загружается в мобильный бункер емкостью 0,5 м3, приводимый в движение электротельфером. Из бункера сырье подается в устройство загрузки печи, разработанное институтом.
Плавка осуществляется в базальтовых плавильных печах. Все они оснащены сертифицированными газовыми горелками NB 10.11. В конструкцию топки входил теплообменник для охлаждения отходящих газов и нагрева воздуха, подаваемого на горение. Подача воздуха для горения с помощью вентиляторов высокого давления (1 рабочий, 1 резервный на 5 печей). Над теплообменником расположен зонт, через который осуществляется отсос дымовых газов. С целью снижения температуры дымовых газов на отводящих трубах установлены дополнительные теплообменники для нагрева воздуха для сушки волокна и нагрева воды в доме.
Производство нитей с использованием платино-родиевых втулок при температуре плавления, обеспечивающей вязкость, при которой расплав вытекает из втулок и образует непрерывную прядь.
Нити собираются в пучок на роликовом смазочном материале и служат для блокировки вала намоточной машины.
После намотки пряжи на определенную массу катушка автоматически меняется.
Сушка мультифиламентной пряжи осуществляется до остаточной влажности не более 3%. Сушильная камера, разработанная нашими специалистами, использует воздух после теплообменника на пути отходящих газов из печей. Движение воздуха осуществляется вентилятором, включенным сушильным агрегатом.
Выгруженная из сушилки нить на стеллажах, транспортируемых к месту перемотки.Мультифиламентная пряжа Hank, установленная на шпулярно-дублирующей машине и намотанная в ровинг с заданными характеристиками. Готовые упаковки устанавливаются на поддоны и используются по дальнейшему назначению.
Основой производства CBF являются печи, разработанные нашими специалистами.
Характеристики печи:
Производительность: 8 кг сухого волокна в час
Установленная электрическая мощность – 14 кВт · ч
Расход природного газа – 8 м3 / ч
оборотная вода – 2 м3 / ч
Другое технологическое оборудование:
- Намоточное оборудование для намотки первичного волокна.
- Перемоточное оборудование.
- Прядильное оборудование.
- Оборудование для приготовления связующих.
- Химические насосы для вяжущих.
- Сушильные установки для сушки волокна и обрезков.
- Теплообменники.
- Вентиляторы высокого давления.
- Вытяжные вентиляторы.
- Система циркуляции воды.
- Упаковка.
- Вилочный погрузчик.
Кроме этого оборудования для производства CBF необходима втулка из сплава платина (90%) – родий (10%), 2000 грамм на одну рабочую единицу.
Экономические показатели производства ровницы CBF.Все экономические показатели основаны на фактических данных о текущей производственной мощности 1 000 тонн в год.
Себестоимость продукции складывается из следующих составляющих:
Сырье – 10%
Газ и другая энергия – 16%
Работы и услуги производственного характера – 3%
Основные и дополнительные. С пансионом – 24%
Социальные отчисления – 9%
Производственные затраты – 36%
Затраты будущих периодов – 2%
Дж.Compos. Sci. | Бесплатный полнотекстовый | Разработка и механические свойства армированного базальтовым волокном акрилонитрил-бутадиен-стирола для применения в космическом производстве
1. Введение
Целью данной статьи является разработка нового исходного материала для производственных целей в космосе, который будет использоваться для длительных исследовательских миссий. , что в идеале дает возможность напечатать на 3D-принтере среду обитания вне Земли. В частности, эта статья будет сосредоточена на разработке материала для строительства среды обитания на поверхности Марса, поскольку НАСА объявило о миссии на Марс в ближайшем будущем [1].Идеальный материал должен быть прочным, жестким, ударопрочным и обеспечивать защиту от радиации для космонавтов и оборудования внутри среды обитания. Материал также должен содержать как можно больше местных (на Марсе) материалов, чтобы свести к минимуму количество строительных материалов, которые необходимо отправить на Марс.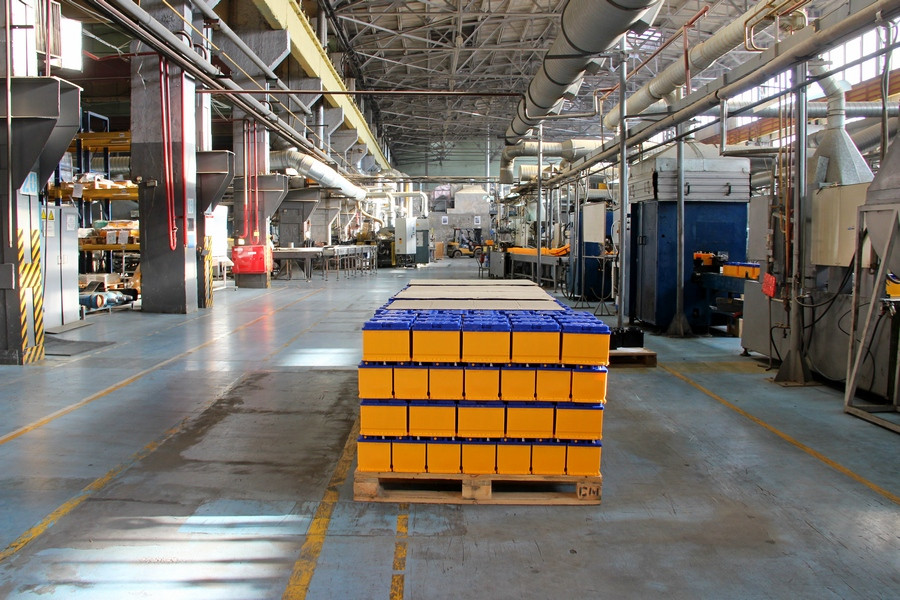

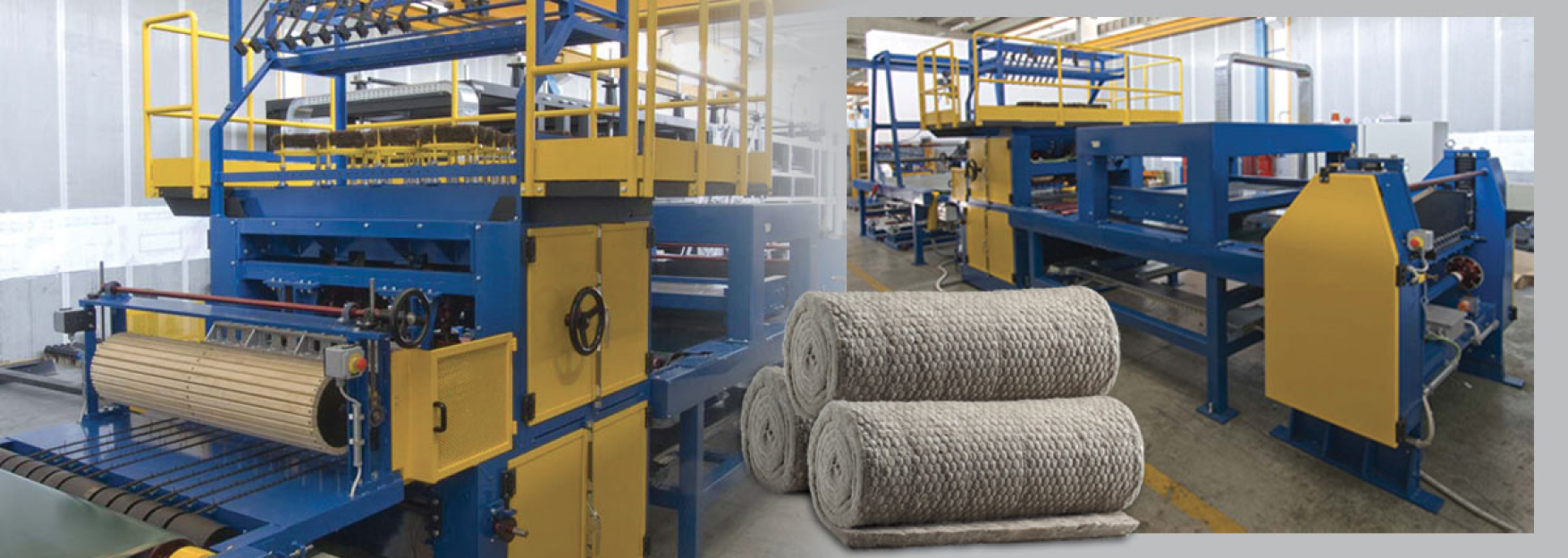



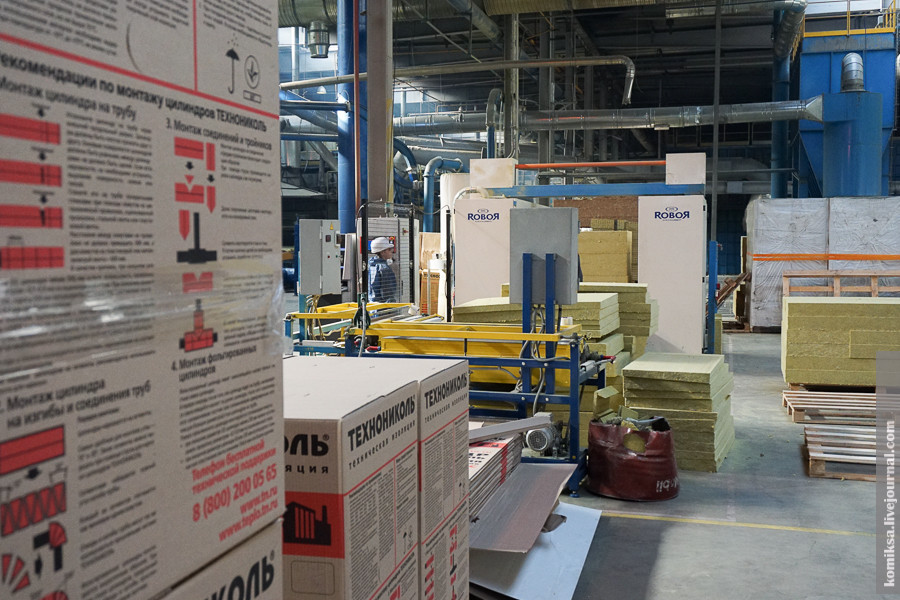

Целью этой статьи является разработка нового материала, который будет прочным и жестким и может быть использован для создания полноразмерной среды обитания для космонавтов, чтобы жить и работать внутри. Кроме того, радиация является серьезной проблемой для космонавтов, и необходимо использовать системы радиационной защиты. Строительные материалы, используемые для создания среды обитания, также должны обеспечивать некоторую радиационную защиту, чтобы минимизировать воздействие космонавтов, когда они находятся внутри среды обитания.И последнее и самое важное: в этом материале должно использоваться как можно больше материала с поверхности Марса, потому что доставка материалов на Марс будет дорогостоящей. В оставшейся части статьи будет подробно описан процесс разработки материала и причины, которые привели к исследованию армированного базальтом композитного материала АБС, а также представлены данные экспериментальных испытаний критических свойств материала для этого применения.
2.
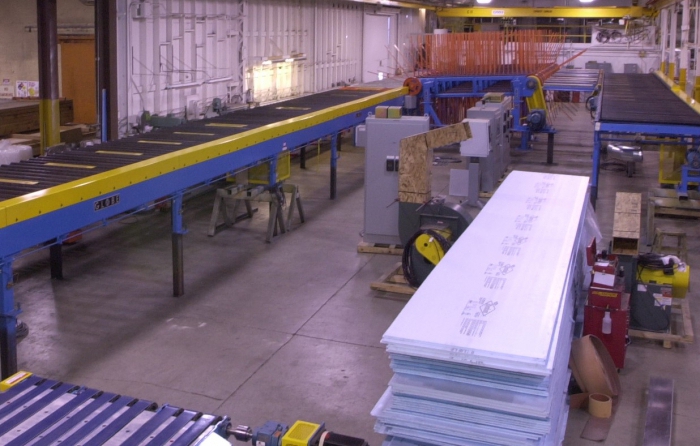
В этом исследовании новый композитный материал АБС-базальт на волокне разработан и испытан с использованием метода изготовления готовых деталей из плавленых волокон (FFF).В результате процесса подготовки материала (подробно описанного в последующих разделах) получается нить диаметром 1,75 мм, которая затем используется в 3D-принтере FFF для изготовления тестовых образцов. Было изготовлено и испытано несколько соотношений базальтового волокна к матрице из АБС этого материала для определения свойств материала при каждом соотношении материалов. Всего было изготовлено 5 соотношений материалов (0%, 10%, 25%, 40%, 60% волокна по весу), причем 4 из этих соотношений в конечном итоге можно было напечатать на 3D-принтере. Тестирование свойств материала включало механическое разрушающее испытание (на растяжение, изгиб, сжатие и удар), получение изображений под микроскопом для определения смешивания волокон и их адгезии к полимеру, а также тестирование защиты от рентгеновских лучей.
2.1. Варианты материалов
Для достижения цели разработки материала для 3D-печати, который можно использовать для жилья в космосе на Марсе, по крайней мере, некоторая часть материала должна быть получена с Марса, потому что будет невозможно отправить все строительные материалы. на Марс через грузовые миссии. Кроме того, только сырьем будет сложно обосновать грузовые миссии. Следовательно, материальное решение, в котором используются материалы, полученные с Марса, при повторном использовании материалов для транспортировки / упаковочных материалов из других грузов было бы идеальным.Кроме того, поскольку этот материал будет использоваться для жилья (строительные материалы, которые будут использоваться для строительства зданий для проживания и работы космонавтов), этот материал также должен обеспечивать некоторую радиационную защиту. Поскольку базальт можно легко добывать и производить из него волокна на Марсе, имеет смысл использовать базальтовые волокна для усиления термопластичного материала в этом приложении.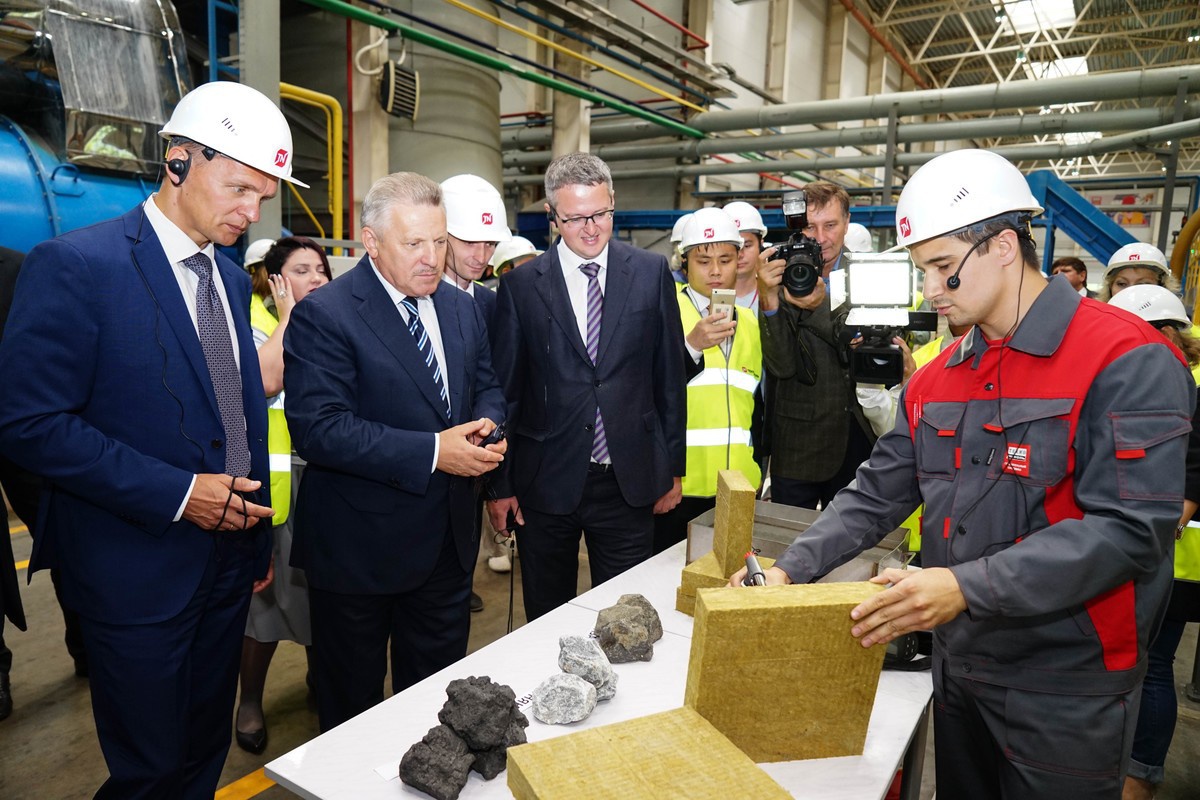
2.2. ABS
ABS является распространенным материалом для 3D-печати и предлагает несколько преимуществ, перечисленных в таблице 1. Хотя другие материалы изначально имеют более высокий предел прочности на растяжение (когда армирование не используется), было ясно, что ABS все еще может быть лучшим решением из-за других факторов. такие как возможность экструдирования при более низких температурах, свидетельство того, что материал может быть напечатан на 3D-принтере в условиях микрогравитации, и было показано, что его можно использовать в упаковочных материалах, а затем переработать в строительный материал.АБС-пластик, использованный в этом исследовании, был окрашен в естественный цвет Sabic MG94 (Filastruder, Snellville, GA, USA). Гранулы сушили в вакуумной печи в течение 24 часов при 70 ° C для удаления влаги перед экструзией материала.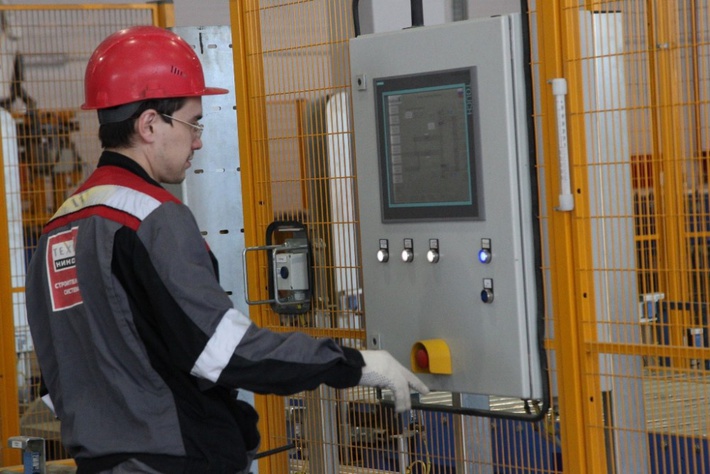
2.3. Базальтовые волокна
Базальтовые волокна, которые обычно используются в качестве арматуры в бетоне, являются уникальными для мира аддитивного производства. Базальт представлял интерес для аддитивного производства в дальнем космосе из-за его большого количества на Марсе [61]. Базальт можно найти на поверхности Марса, что делает процесс очистки и получения более простым и менее дорогостоящим, чем другие более прочные альтернативы, такие как углеродное волокно, оксид графена или углеродные нанотрубки.Базальтовое волокно имеет плотность 2,65 г / см 3 , предел прочности при растяжении 3300 МПа и максимальное удлинение 3,2% [62]. Другими привлекательными свойствами базальтового волокна являются его устойчивость к ультрафиолету (УФ), низкий коэффициент теплового расширения, электрическая изоляция, более высокое сохранение прочности при повышенных температурах, чем у других материалов (например, E-стекла), устойчивость к агрессивным жидкостям, кислотам и щелочам, возможность вторичной переработки и, что потенциально наиболее важно для этого приложения, защита от излучения [63].
2.4. Приготовление смеси
АБС и базальтовые волокна измеряли отдельно при заданном весовом соотношении, а затем объединяли вместе в большом контейнере и смесь перемешивали вручную (см. Рисунок 1). Стандартная испытательная катушка с нитью с 25% -ным соотношением волокон содержала 200 г материала (т.е. катушка 200 г с 25% -ным соотношением волокон содержала 150 г АБС и 50 г базальтовых волокон). Смесь ABS и BF готовили в одношнековом смесительном экструдере Randcastle RCP-0500 (Randcastle, Cedar Grove, NJ, USA).Диаметр материала, полученного в экструдере Randcastle, был слишком большим для 3D-печати (примерно 5 мм в диаметре). Затем 5-миллиметровую нить разрезали на кусочки размером с гранулы, используя гранулятор Hellweg MRS-H (Hellweg Maschinenbau GmbH & Co., Рётген, Германия). Полученные «гранулы» собирали в чистый мешок. В промежутках между каждым испытанным соотношением материалов экструдер для компаундирования Randcastle опорожняли, а гранулятор Hellweg очищали.2,5. Экструзия нити для 3D-принтера
Для производства нити для тестирования на 3D-принтере использовалась изготовленная на заказ система экструзии нити (показанная на рис. 2).Цилиндр экструдера нагревается тремя ленточными нагревателями, каждый со своими регулируемыми зонами. Одиночный винт имеет длину 400 мм и диаметр 20 мм, в результате чего отношение L / D составляет 20. Диаметр отверстия матрицы составляет 2,5 мм. Температура фильеры была установлена на 200 ° C, температура зоны измерения была установлена на 180 ° C, а зона плавления была установлена на 160 ° C. Когда нить покидала матрицу, она охлаждалась и закаливалась с помощью множества вентиляторов, обдувающих нить воздухом комнатной температуры. Затвердевшая нить измеряется лазерным сканером диаметра Micro Epsilon OptoControl 2500 (Micro Epsilon, Роли, Северная Каролина, США) на выходе из ряда охлаждающих вентиляторов.Затем нить перемещается в систему тяговых колес, приводимых в движение шаговым двигателем. После того, как нить протянута через колеса, она подается в систему намотки нитей Filawinder (Filastruder, Snellville, GA, USA), где она наматывается для будущих испытаний. Чтобы обеспечить контроль качества диаметра нити, информация от лазерного сканера диаметра передается на микроконтроллер, который затем регулирует скорость шагового двигателя в системе съемника. Постепенные регулировки скорости вытягивания производятся до тех пор, пока диаметр не станет равным 1.75 мм.Соотношения материалов 0%, 10% и 25% были созданы относительно легко. Каждый этап процесса работал хорошо, от начального компаундирования до наматывания материала и, наконец, 3D-печати. Однако соотношение 40% и 60% оказалось более трудным. По мере увеличения содержания волокна материал становился более жестким. При соотношении волокон 40% материал стал настолько жестким, что стало трудно наматывать материал на стандартную катушку с материалами для 3D-принтера (внутренний диаметр типичных катушек составляет 80–100 мм).Катушка с большим внутренним диаметром (120 мм) использовалась для намотки волокна с соотношением 40%.
2.6. 3D-печать
Для изготовления всех тестовых образцов использовался 3D-принтер FlashForge Creator Pro (Flashforge USA, Лос-Анджелес, Калифорния, США). FlashForge Creator Pro и программное обеспечение слайсера позволяют тестировать ряд переменных печати, таких как температура сопла, температура рабочей пластины, размер сопла, траектория печати и скорость экструзии. Критические параметры сборки показаны в таблице 2. Температура соплабыла увеличена до 250 ° C с 230 ° C, когда соотношение базальтовых волокон было выше 25%.При более высоком содержании базальтового волокна вязкость композитного материала снижалась, что приводило к засорению сопла и проблемам с измельчением нити ведущей шестерни. Изменение температуры экструзии на 250 ° C уменьшило эти проблемы заедания. Как и в случае с большинством 3D-печати из ABS, деформация может быть проблемой для неотапливаемых камер сборки. Чтобы бороться с этим, рабочая пластина была нагрета до 110 ° C, однако этого было недостаточно. На нагретую стеклянную рабочую пластину также наносили «суспензию из АБС-пластика», что является обычным решением проблемы деформации из АБС-пластика.Суспензия ABS представляет собой смесь приблизительно 100 мл ацетона с 10–20 г ABS, растворенными в растворе. Суспензия из АБС-пластика плотно прилипает к рабочей пластине, позволяя первому напечатанному на 3D-принтере слою также прочно прилипать и уменьшать степень деформации.
2.7. Испытания материалов
Испытания механических свойств проводились в соответствии с применимыми стандартами ASTM: ASTM D638 (растяжение), ASTM D695 (сжатие), ASTM D790 (изгиб) и ASTM D256 (ударная вязкость по Изоду).Для каждого испытанного соотношения были напечатаны и испытаны не менее шести образцов каждого разрушающего испытания. Для испытаний на растяжение и изгиб использовалась система электромеханических испытаний MTS Insight (MTS, Eden Prairie, Миннесота, США) с тензодатчиком 5 кН и экстензометром 20 мм. Для испытаний на сжатие использовалась универсальная испытательная машина MTS Landmark (MTS, Иден-Прери, Миннесота, США) с датчиком нагрузки 100 кН и встроенным линейным переменным дифференциальным трансформатором (LVDT) для измерения удлинения. Испытания на ударную вязкость проводились на откалиброванном испытательном стенде Izod, изготовленном по индивидуальному заказу.
Оптический (Keyence VHX 600 (Keyence Corporation of America, Итаска, Иллинойс, США)) и лазерный сканирующий топографические микроскопы (Keyence VK-9710 (Keyence Corporation of America)) использовали для изображения образцов материала. Система рентгеновского изображения NSI M5000 (North Star Imaging, Роджерс, Миннесота, США) использовалась для проникновения рентгеновских лучей в образцы материалов с целью определения характеристик экранирования рентгеновских лучей и равномерного перемешивания волокон.
4. Обсуждение
Конечное использование этого материала приводит к другому набору целей и ограничений, чем большинство традиционных композитных материалов.Поскольку добавление базальтовых волокон обеспечивает защиту от излучения и повышение прочности, стоимость пренебрежимо мала по сравнению со стоимостью доставки матричных материалов для соединения с волокнами, выгодно использовать столько базальтового волокна, сколько практически можно поместить в материал, в то время как по-прежнему позволяя процессам экструзии филамента и нанесения 3D-печати функционировать, как обычно.
Гранулы АБС-базальт могли быть изготовлены для каждого протестированного соотношения волокон (0%, 10%, 25%, 40% и 60%).Нить соответствующего диаметра (1,75 мм) для 3D-печати также могла быть изготовлена для каждого соотношения волокон. Соотношение волокон 60% оказалось слишком жестким для намотки и не является жизнеспособным решением для мелкомасштабной 3D-печати. Однако большие 3D-принтеры, рассчитанные на полномасштабную среду обитания, не будут использовать катушки с нитью. Они будут подаваться гранулами в экструдер для гранул. Несмотря на то, что невозможно протестировать материал с 60% -ным соотношением волокон на небольшом 3D-принтере, это все же может быть вариантом для больших 3D-принтеров с экструдерами гранул.
При испытаниях на растяжение, изгиб и сжатие механические свойства материала увеличиваются (становятся прочнее и жестче) с увеличением доли волокон до достижения 40% доли волокон. Есть две возможные причины, по которым при соотношении волокон 40% не наблюдается увеличения прочности или жесткости. Как отмечалось в разделе 2.6, температура экструзии (сопла) 3D-принтера была увеличена до 250 ° C, чтобы позволить материалу иметь достаточно низкую вязкость для выдавливания из сопла с постоянной скоростью. Нагрев АБС до высоких температур в конечном итоге вызовет термическое разложение [66].Более высокая температура экструзионного сопла (250 ° C) всего на 20 ° C выше, чем стандартная температура 3D-печати для ABS. Хотя некоторое разложение могло начаться, это не считается основным источником потери прочности. Как показано на рисунке 4, волокна плотно упакованы в поперечном сечении материала и в некоторых местах контактируют с другими волокнами. Это, вероятно, не способствует хорошему сцеплению между волокном и материалом матрицы, оставляя небольшие концентраторы напряжений внутри материала, вызывая преждевременный выход из строя.Таблица 3, Таблица 4, Таблица 5 и Таблица 6 показывают увеличение прочности и жесткости. При добавлении 25% (по массе) базальтового волокна к АБС прочность на разрыв улучшилась почти на 40%, увеличившись с 36,55 МПа до 50,58 МПа, в то время как модуль упругости увеличился примерно на 120% с 2,15 ГПа до 4,79 ГПа. Прочность на изгиб увеличилась примерно на 20% с 56,94 МПа до 68,51 МПа, а модуль упругости при изгибе увеличился примерно на 70% с 1,81 ГПа до 3,05 ГПа. Хотя результаты сжатия не показали значительного улучшения прочности, добавление волокон также не привело к снижению прочности на сжатие.Это важно, учитывая, что базальтовые волокна обеспечивают защиту от излучения. На рисунке 10 показаны цифровые рентгенограммы образцов, напечатанных на 3D-принтере и пронизанных рентгеновскими лучами. Поскольку цвета каждого образца относительно постоянны по всему образцу, изображения показывают, что волокна равномерно распределены по всему образцу. Предыдущие попытки использовать другие методы для смешивания базальтовых волокон и матричного материала АБС не привели к получению равномерно смешанного композитного материала. Рисунок 10 и Таблица 7 также ясно показывают, что материал обеспечивает защиту от рентгеновского излучения.Однако поверхность Марса подвергается воздействию излучения с более высокой энергией (выше, чем рентгеновские лучи), и базальтовые волокна могут не обеспечивать такой же уровень защиты от других типов космического излучения, как от рентгеновского излучения. Чтобы определить правомерность использования этого материала для приложений 3D-печати, было создано несколько реальных объектов. На рисунке 11 показаны три из этих объектов: гаечный ключ с открытым зевом на 12 мм, косозубая шестерня и зажим для поручня. Подобные объекты были напечатаны как тестовые объекты в оригинальной 3D-печати в экспериментах в условиях микрогравитации на МКС [47].Хотя ни один из этих объектов не был испытан до отказа, они были намного жестче, чем их контрольные аналоги из АБС.5. Выводы
Армированная базальтовым волокном нить из АБС-пластика была произведена с пятью различными соотношениями волокон и использована для 3D-печати образцов для испытаний. Механические испытания показали, что прочность и жесткость улучшились до 40% доли волокон, после чего жесткость все еще немного увеличилась, но прочность снизилась. Наиболее вероятная причина снижения прочности была связана с более плотной упаковкой волокон в матрице, что снизило общее качество связи между волокном и матрицей ABS.Цифровая рентгенография показала, что композитный материал был равномерно перемешан во время процессов экструзии и осаждения. Рентгеновские изображения также показали, что чем выше соотношение содержания волокон, тем больше рентгеновских лучей экранируется материалом. Кроме того, было продемонстрировано, что из этого материала можно распечатать на 3D-принтере небольшие полезные предметы, такие как гаечные ключи, шестерни и зажимы.
Необходимо провести дополнительные испытания этого материала, чтобы узнать о его усталостной прочности (кривая SN). Повторение аналогичных испытаний для этой статьи, но добавление дополнительных соотношений содержания волокон между 25% и 40% также будет полезно для будущих дизайнеров.Соотношение волокон выше 40% также следует тестировать на крупномасштабных 3D-принтерах, оснащенных экструдером для гранул. Наконец, необходимо провести исследования, связанные с возможностью вторичной переработки упаковочных материалов из АБС-пластика, которые затем используются в качестве строительного материала из АБС-базальта для 3D-печати.
Базальтовое каменное волокно
Базальтовое волокно, изготовленное из волокон базальтовой породы, очень похоже на углерод и стекловолокно, имеет лучшие физико-механические свойства и дешевле. Один килограмм базальтовой арматуры равен 9.6 кг стали. Они имеют множество применений в полевых условиях и могут заменить многие дорогостоящие и редкие материалы. Его производственный процесс очень прост, а сырье можно найти практически в каждой стране. Базальтовые волокна могут решить самую большую проблему в цементной и бетонной промышленности.
Базальтовое волокно – это материал, который изготовлен из очень тонких волокон базальта, который состоит из пироксена, минералов плагиоклаза и оливина. Это очень похоже на углеродное волокно и стекловолокно, которое имеет лучшие физико-механические свойства, чем стекловолокно, но значительно дешевле, чем углеродное волокно.Он также используется в качестве волокнистого текстиля в автомобильной промышленности и авиакосмической промышленности, а также может использоваться в качестве композитного материала для производства таких изделий, как штативы.
Базальт широко известен как камень, который можно найти практически во всех странах мира. Волокна Basalt Rock не токсичны с воздухом и водой, негорючие и взрывобезопасные. При контакте с другими химическими веществами они не вызывают химических реакций, которые могут нанести вред здоровью или окружающей среде.Композиты на основе базальта могут заменить сталь и известные армированные пластмассы. Один кг базальтовой арматуры равен 9,6 кг стали. Кажется, есть что-то довольно поэтичное в использовании волокна, сделанного из натурального камня, для усиления материала, который вполне обоснованно можно назвать искусственным камнем. Сырьем для производства базальтового волокна является порода вулканического происхождения.
ИЗДЕЛИЯ ИЗ БАЗАЛЬТОВОГО ГОРНОГО ВОЛОКНА; ПЕРВИЧНЫЕ ПРОДУКТЫ ИЗ БАЗАЛЬТА; Непрерывные базальтовые волокна; Рубленые волокна; CBF ровинг; Пряжа CBF; ВТОРИЧНЫЕ ПРОДУКТЫ ИЗ БАЗАЛЬТА; Базальтовая арматура; Базальтовый геотекстиль; Базальтовая сетка; Трубы из базальтового волокна; Базальтовые ламинаты; Преимущества и недостатки базальтового волокна
Объем рынка базальтового волокна, доля
Анализ рынка базальтового волокна на 2020-2027 годы:Базальтовое волокно – это материал, изготовленный из чрезвычайно тонких волокон базальта, который состоит из минерального плагиоклаза, фироксена и оливина.Базальтовое волокно требует плавления измельченной и промытой базальтовой породы при температуре около 1500 ° C (2730 ° F). Базальтовое волокно широко используется в военной и гражданской областях. Базальтовое волокно можно использовать для изготовления защитной одежды как при высоких, так и при низких температурах. Базальтовое волокно используется в различных отраслях промышленности и сферах применения, поскольку оно предназначено для использования в строительстве и инфраструктуре, благодаря своим экологически чистым свойствам, высокой совместимости с бетоном и легкому смешиванию при высокой концентрации.Кроме того, он обладает высокой прочностью и пригодностью для вторичного использования, что способствует его спросу в различных отраслях промышленности. Не требует специального технологического оборудования.
Анализ объема и структуры рынка
Метрика отчета | Подробная информация |
Объем рынка, доступный по годам | 2019–2027 | 2019 |
Период прогноза | 2020–2027 |
Единицы прогноза | Стоимость (долл. США) и объем (тонны) |
Охватываемые сегменты | Тип, применение, отрасль конечного использования и регион |
Охватываемые регионы | Северная Америка (США.Южная и Канада), Европе (Германия, Великобритания, Франция и остальная часть Европы), Азиатско-Тихоокеанском регионе (Китай, Япония, Индия и остальная часть Азиатско-Тихоокеанского региона) и LAMEA (Бразилия, Мексика, ОАЭ, юг. Африка и остальная часть LAMEA) |
Компании охвачены | KamennyVek (Россия), Zhejiang GBF Basalt Fiber Co. (Китай), Mafic SA (Ирландия), Technobasalt-Invest LLC (Украина), Russian Basalt (Россия), ISOMATEX SA (Бельгия), INCOTELOGY GmbH (Германия), Sudaglass Basalt Fiber Technology (U.S.), Shanxi Basalt Fiber Technology Co., Ltd (Китай) и Mudanjiang Basalt Fiber Co. (Китай) |
Вспышка коронавируса привела к потере более 200 миллиардов долларов в странах Азиатско-Тихоокеанского региона. COVID-19 сильно повлиял на рост рынка базальтового волокна.
Азиатско-Тихоокеанский регион является наиболее активным и крупнейшим рынком базальтового волокна с присутствием большого количества производителей с высокой производственной мощностью.Однако из-за спада производства рост строительной отрасли замедлился, что, в свою очередь, ограничило спрос на базальтовое волокно.
Основные факторы воздействия: анализ рыночных сценариев, тенденции, движущие силы и анализ воздействияОсновными движущими силами мирового рынка базальтового волокна являются рост спроса на строительную деятельность во всем мире; увеличение спроса на высокоэффективные уплотнители, шины и шинный клей; быстрое развитие автомобильного сектора в развивающихся странах.Кроме того, ожидается, что расширение применения базальтового волокна для борьбы с загрязнением воды, например, для очистки сточных вод и очистки естественных водоемов, будет способствовать росту рынка.
Однако наличие продуктов-заменителей, таких как углеродное волокно и стекловолокно, которые хорошо зарекомендовали себя на рынке, значительно препятствует росту мирового рынка.
Запуск нового продукта для ускорения роста рынка Компания «КаменныйВек» – ведущий мировой производитель непрерывного базальтового волокна, которое производится и продается на рынке под зарегистрированной торговой маркой «Базальтовое волокно».Непрерывное базальтовое волокно обладает такими свойствами, как кислотно-щелочная стойкость, улучшенные электрические свойства, более высокая прочность на растяжение и улучшенные механические свойства. Кроме того, это волокно является экологически чистым, что делает его пригодным для различных применений, таких как опорные сетки, трубы, контейнеры, электроизоляционные материалы и изделия из базальтового пластика. Кроме того, это неорганическое волокно, которое можно использовать в качестве материала баллистической брони для защиты.
Базальтовое волокно демонстрирует высокую механическую прочность, которая требуется для строительства в экстремальных условиях, и при более низкой цене по сравнению со всеми другими волокнами, такими как стекловолокно и арамидные волокна.
Ожидается, что рынок базальтового волокна будет расти экспоненциально в течение прогнозируемого периода. Это связано с ростом продаж автомобилей, ростом населения и быстрой урбанизацией. Кроме того, базальтовое волокно используется в звукопоглощающей и теплоизоляционной промышленности, что способствует росту его спроса во всем мире. Кроме того, базальтовые волокна используются в тормозных, электрических и электромагнитных устройствах, что способствует росту рынка.
Ключевые сегменты покрыты
Сегмент | Подсегмент |
Тип | 9057 |
2 Применение Армирование Бетон | |
Промышленность конечного использования |
|
Ключевые преимущества отчета16 902
Вопросы, ответы на которые приведены в отчете об исследовании мирового рынка базальтового волокна:
- Какие ведущие игроки рынка активны на мировом рынке базальтового волокна?
- Каковы грядущие тенденции на рынке базальтового волокна?
- Каковы движущие факторы, ограничения и возможности рынка?
PISCES ищет предложения по технико-экономическому обоснованию производства базальтового волокна на Гавайях
Тихоокеанский международный космический центр исследовательских систем (PISCES) – государственный аэрокосмический центр, расположенный в Хило – ищет квалифицированную фирму для проведения всеобъемлющего рыночное технико-экономическое обоснование.Цель исследования – определить, принесет ли предприятие по производству базальтового волокна в графстве Гавайи пользу местной экономике.
PISCES выпустил запрос предложений (RFP) от 12 декабря 2017 года, чтобы принимать предложения от организаций, заинтересованных в проведении технико-экономического обоснования.
Запрос предложений вместе с инструкциями по подаче и сроками доступен для просмотра в Интернете.
Мировая промышленность по производству базальтового волокна в настоящее время оценивается в 100 миллионов долларов и, как ожидается, будет расти.Успешная деятельность на Гавайях создаст новые производственные рабочие места, экономический рост и возможности для бизнеса, а также появится новый экологически чистый строительный материал с широким спектром применения.
КомпанияPISCES изучает вулканический базальт острова Гавайи в качестве сырья для использования ресурсов на месте для исследования космоса и подтвердила, что мелкие частицы базальта, обнаруженные в местных карьерах, соответствуют требованиям, необходимым для производства базальтового волокна.
СТАТЬЯ ПРОДОЛЖАЕТСЯ НИЖЕ ADБазальтовое волокно, хотя и менее известно, имеет схожие применения с изделиями из стекловолокна и углеродного волокна, но считается лучшим в нескольких аспектах: стойкость к коррозии и истиранию, термическая стабильность, теплоизоляция, вибрация и химическая стойкость.Базальтовое волокно может заменить практически все области применения асбеста. Его также можно использовать для изготовления структурной сетки, прочной ткани, изоляционного материала, гидропонной среды для выращивания, базальтовой арматуры и в качестве заполнителя для армирования бетона.
СТАТЬЯ ПРОДОЛЖАЕТСЯ НИЖЕ ADКрайний срок для завершенных предложений, полученных по электронной почте, как указано в RFP, – не позднее полудня (HST) 22 января 2018 г.
С вопросами о RFP обращайтесь к специалисту по административным вопросам PISCES Полли Рот по телефону [электронная почта защищена] или по телефону (808) 935-8270.
RFP выпускается Исследовательской корпорацией Гавайского университета (RCUH).
СТАТЬЯ ПРОДОЛЖАЕТСЯ НИЖЕ ОБЪЯВЛЕНИЯО РЫБАХ
PISCES – это гавайский аэрокосмический центр, финансируемый государством, при Департаменте бизнеса, экономического развития и туризма (DBEDT). Агентство из Хило работает над тем, чтобы позиционировать штат как лидера в освоении космоса, одновременно разрабатывая экологически чистые продукты и технологии, которые приносят пользу островам.Посредством прикладных исследований, развития рабочей силы и долгосрочного бизнеса и экономического развития PISCES предоставляет практический опыт будущим ученым и инженерам Гавайев, подготавливая их к удовлетворению требований высококонкурентной отрасли, улучшая местную экономику за счет диверсификации рабочих мест и инноваций. продукты и новые отрасли.
О ДБЭДТ (Департамент бизнеса, экономического развития и туризма)
DBEDT – это гавайский ресурсный центр по экономическим и статистическим данным, возможностям развития бизнеса, информации об энергии и сбережении, а также преимуществам во внешней торговле.Миссия DBEDT – создать экономику Гавайев, которая объединяет инновации и является глобальной конкурентоспособной, динамичной и продуктивной, предоставляя возможности для всех жителей Гавайев. Через свои прикрепленные агентства департамент способствует запланированному развитию сообществ, создает доступное жилье для рабочей силы в высококачественной среде обитания и способствует росту рабочих мест в инновационном секторе.
Mafic – Волокно из базальта
Волокно базальтовое
ЖурналBusiness View Magazine берет интервью у Джеффа Томпсона, руководителя отдела продаж и маркетинга Mafic, в рамках нашей серии статей об индустрии композитов.
Базальт – это магматическая порода, образовавшаяся в результате быстрого охлаждения базальтовой лавы, выходящей на поверхность земли. Более 90 процентов всех вулканических пород на Земле составляют базальты. Mafic – это прилагательное, описывающее любую породу, такую как базальт, богатую магнием и железом; это слово обозначает портманто из магния и железа. Mafic – это также название компании, созданной в 2012 году для производства базальтового волокна – высококачественного композитного материала – на рынке, где преобладали стекловолокно и углеродное волокно.
Джефф Томпсон
Руководитель отдела продаж и маркетинга
«Стекловолокно – это рабочая лошадка отрасли; Углеродное волокно – это высококачественный материал в композитной промышленности, – объясняет Джефф Томпсон, глава отдела продаж и маркетинга Mafic, – и мы почувствовали, что между этими двумя материалами существует огромная пропасть, которую не удалось решить. Высококачественные материалы из базальтового волокна действительно заполнили эту рыночную нишу ». Базальтовое волокно чаще всего используется в качестве арматуры из пластикового композитного материала для повышения жесткости или прочности, но базальт также может использоваться для высокотемпературной изоляции или армирования бетона.«Мы плавим породу при температуре около 1500 градусов по Цельсию и протягиваем ее через платино-родиевые втулки, чтобы сформировать конечный продукт, который представляет собой непрерывную базальтовую нить, которую затем можно наматывать, нарезать или обрабатывать».
Mafic начал свою деятельность в Келлсе, Ирландия, примерно в 125 милях к югу от самого известного в мире месторождения базальта, Дороги гигантов, области примерно 40 000 базальтовых колонн на северном побережье Северной Ирландии. «Этот первоначальный производственный объект в Келлсе мы рассматриваем в долгосрочной перспективе как объект исследований и разработок, который мы будем поддерживать», – говорит Томпсон.«А затем здесь, в США, мы запускаем наше более крупное производственное предприятие в Шелби, Северная Каролина, которое должно быть введено в эксплуатацию в конце этого года. Этот производственный объект представляет около 6000 тонн годового производства и является первым предприятием по производству непрерывного базальтового волокна здесь, в Северной Америке ».
По словам Томпсона, новое предприятие Shelby, в котором сейчас работает всего около десяти человек, будет расширяться в ближайшие месяцы и вырастет до 100 сотрудников. «Мы очень рады расширению нашей команды здесь», – заявляет он.«Мы создаем много производственных рабочих мест здесь, в Шелби, и мы обнаружили, что эта область богата талантами в области композитов, и много умных, трудолюбивых людей в этой области, которые могут сделать нас очень успешными. . »
Новое предприятиеMafic поможет удовлетворить потребности своих нынешних и будущих клиентов в различных отраслях промышленности, которые используют композиты в своих производственных процессах. «Это может быть в автомобильной сфере; в таких вещах, как высокотемпературные ткани для утепления; аэрокосмическая промышленность; и растущая отрасль «композиты в строительстве».У наших волокон есть много разных применений. Например, недавно появился ряд разработок с базальтовым волокном для трехмерной печати. Но, вообще говоря, продукты из базальтового волокна можно увидеть везде, где вы могли бы, в противном случае, использовать материалы из стекловолокна или углеродного волокна. Пустота на рынке, которую мы заполняем, – это области, на которые не обращает внимания очень дорогая альтернатива, углеродное волокно, или та, которая требует материалов с более высокими характеристиками, чем в настоящее время предлагает продукция из стекловолокна.”
Одна из миссий Mafic – ознакомить потенциальных клиентов с преимуществами базальтового волокна. «Мы видим, что есть много людей, которые имеют поверхностные знания или базовые представления о композитных материалах и, в частности, о том, что может предложить базальтовое волокно, и хотят делать с ними больше и лучше понимать», – говорит Томпсон. Он добавляет, что компании также необходимо преодолеть некоторые негативные представления о материалах из базальтового волокна. «Раньше они не всегда соответствовали строгим стандартам качества, которые требовались, а сами продукты не были доступны на производственных предприятиях в Северной Америке.Осуществляя производство здесь, в Северной Каролине, мы можем сделать эти отечественные материалы доступными для клиентов здесь, в штатах, благодаря более тесной цепочке поставок, большей надежности и фантастическому американскому производству, которое, как мы знаем, ценится многими клиентами ».
Mafic также предлагает своим клиентам беспрецедентный сервис. «Одна из вещей, на которой мы сосредоточены, – это требования клиентов», – утверждает Томпсон. «У многих клиентов есть разные индивидуальные и специфические требования, которые нам необходимо решить. Наиболее очевидным является разработка конкретных размеров – химическое покрытие, которое наносится на внешнюю поверхность базальтового волокна, которое позволяет ему соединяться с различными системами смол, – и наша способность адаптировать наши системы калибровки к различным потребностям клиентов в разных термореактивных материалах. и термопластические материалы, что затем позволяет каждому клиенту иметь индивидуальный «рецепт» того, что он ищет, и помогает убедиться, что наше волокно максимизирует свои свойства в их процессе.”
«Раньше на рынке базальтового волокна применялся универсальный подход», – продолжает он. «И хотя есть предложения, которые адекватно решаются с помощью материала из одного источника, мы определенно знаем, что наличие разнообразного набора продуктов и проклеивающих материалов занимает важное место в списках многих клиентов в отношении склеивания и необходимых им характеристик. чтобы увидеть. Это внимание к деталям проявляется и в других вещах, на которые мы обращаем внимание, например, в обеспечении того, чтобы наши объекты соответствовали высоким стандартам качества, и в других областях, в которых клиенты знают, что они могут положиться на нас.”
ВладельцыMafic, которые уже вложили «значительную сумму денег здесь, в Северной Каролине», по словам Томпсона, планируют продолжить расширение операций компании в США. «Мы стремимся к расширению, опираясь на ту твердую основу, которая у нас есть сегодня, и на то, чего мы добьемся через год с годовой производительностью на нашем предприятии в США», – говорит Томпсон. «Мы стремимся к расширению за счет дополнительных мощностей помимо нынешнего, чтобы удовлетворить дополнительные потребности клиентов на рынке композитных материалов в Северной Каролине и за ее пределами.
«Сегодня у нас много клиентов, которые работают с нашей продукцией здесь, в США и других регионах Северной Америки, которые в настоящее время используют наши продукты с нашего производственного предприятия в Ирландии, и мы надеемся и дальше расширять возможности использования этих продуктов. и, кроме того, поддерживать растущую клиентскую базу в Европе, куда мы в настоящее время поставляем продукцию с нашего ирландского производственного предприятия и нуждаемся в дополнительных производственных мощностях для удовлетворения их потребностей ».
Томпсон рассматривает композитную промышленность – и ее рынок – как необычную область сотрудничества, как в химическом, так и в братском плане: «Мы – инструмент в наборе инструментов для композитов, но мы знаем, что для использования продуктов из базальтового волокна, часто – почти каждый раз, – на самом деле – вы используете вместе с этим и другие составные продукты.Часто это полимерная система, но часто для изготовления детали используются как углеродное, так и базальтовое волокно. Или, чтобы вся система работала, у вас есть стекловолокно, углеродное волокно и базальтовое волокно для различных областей применения. В композитах нет единого полного решения; есть много разных инструментов, которые работают вместе, чтобы вся система работала ».
Что касается сотрудничества между компаниями, Томпсон сообщает, что «конечный пользователь композитного продукта почти никогда не покупает готовый продукт какого-либо отдельного лица.Чаще всего они говорят: «Мне нужно решить проблему А.» И чтобы решить эту проблему, нужно объединить пять разных компаний. Мы рассматриваем рынок базальта как рост пирога из композитных материалов. И задача для такой компании, как Mafic, и одна из наших задач – найти продуктивных партнеров для решения этих проблем, эффективного удовлетворения требований рынка и стремления сделать это выгодным для всех компаний, с которыми мы работаем. внутри отрасли, чтобы добиться успеха.”
Работая над тем, чтобы сделать весь сектор успешным, Томпсон убежден, что у Mafic есть все необходимое для успеха здесь, в США, благодаря своим превосходным техническим знаниям и отличным производственным возможностям. «Мы технически подкованная компания», – говорит он. «Внутреннее обучение, которое мы проводим, продолжает давать отличных сотрудников, и мы ожидаем, что это будет продолжаться.