ДВП мягкая — лучший вариант утепления и отделки дома из натуральных материалов
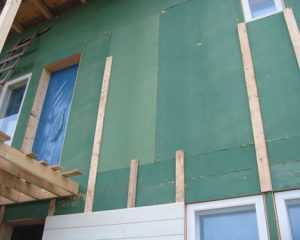
Мягкая древесноволокнистая плита – натуральный экологически чистый строительный материал, который нашел широкое применение в малоэтажном строительстве для обустройства звукоизоляции, утепления и финишной отделки элементов здания.
Основные характеристики мягкой ДВП
Отличительной особенностью МДВП является отсутствие в ее составе клея и других химических связующих. В процессе изготовления волокнистая масса, которую получают путем измельчения древесной щепы, смешивается с водой, затем прессуется и высушивается.
Так же в плитах не содержится формальдегид и других признанных канцерогенными и вредными для человека и природы синтетических добавок. Благодаря этому плита ДВП мягкая абсолютно безопасна при эксплуатации даже для людей, склонных к аллергии. Это – настолько же биологически чистый материал, как и природная древесина.
Разновидности мягкой ДВП
Связующим веществом в мягкой ДВП является сок хвойной древесины – лигнин. При горячем прессовании мягкие древесноволокнистые плиты становятся достаточно прочными и вполне подходят для изготовления листового строительного материала. Поэтому название «мягкая» не стоит воспринимать буквально.
Мягкие древесноволокнистые плиты разделяются по размеру, конфигурации, составу и плотности. Бывают не только стеновые панели МДВП, но есть панели и для утепления пола в деревянном доме и потолка. В зависимости от этих параметров они выпускаются следующими наименованиями:
- Теплозвукоизоляционные плиты
- Ветрозащитные плиты
- Декоративные панели
- Подложка под ламинат
Высокая пористость обеспечивает плитам низкую теплопроводность и делает их теплоизоляторами высшей категории. Благодаря своей структуре мягкие плиты также обладают эффективным поглощением шума и надежной звукоизоляцией, поэтому помимо утепления конструкций используются для улучшения акустики в помещении (предупреждают появление «эффекта эха») и шумозащиты.
Помимо МДВП существует много других утеплителей для дома. Например, эковата. Отзывы об эковате говорят, что этот материал имеет отличные звуко- и теплоизоляционные показатели. У этого утеплителя есть много и других достоинств.
Однако существуют и минусы эковаты, о которых написано здесь. Например, для её монтажа придётся нанимать специалистов.
Теплозвукоизоляционные плиты выпускаются с более плотной и гладкой наружной стороной, за счет которой может использоваться в качестве стенового материала. Такая МДВП является достойной альтернативой гипсокартону, втрое превосходя его по легкости, эластичности и удобству монтажа.
Ветрозащитные мягкие ДВП содержат в своем составе парафин, который обеспечивает более высокую сопротивляемость влаге. Благодаря данному свойству дом может стоять без наружной отделки на протяжении 1 года.
Следует учитывать, что качественная ветрозащитная МДВП получается лишь в тех случаях, когда парафином пропитываются ворсинки дерева во время производственного процесса, а не поверхность готового листа. Такая технология наделяет ворсинки водоотталкивающими свойствами, но сама плита при этом может пропускать пар и выводить влагу из стены наружу.
Декоративные панели из мягкой ДВП бывают потолочными и стеновыми. Они характеризуются легким весом и наличием в своей конструкции соединения шип-паз (такое соединение есть у многих других материалов, например, у имитатора бруса), что вместе взятое позволяет быстро и просто устанавливать их на клей или с помощью степлера прикреплять к обрешетке. Установка декоративных МДВП не требует особой подготовки – их можно монтировать без выравнивания стен даже поверх старых обоев.
Подложка под ламинат из МДВП обладает существенными преимуществами перед любыми другими видами подложек:
- Значительно снижают ударный шум, убирают «эффект каблучков»
- Сглаживает неровности основания, «заполняет» трещины в полу (не более 0,2 см)
- Сохраняет тепло пола
- Имеет высокую степень прочности на сжатие, что наиболее актуально для ламината с замками
- Характеризуется длительным сроком эксплуатации, что обусловлено прочностью структуры древесного волокна
- Продлевает срок службы чистового напольного покрытия
- Обеспечивает «дыхание» дома благодаря высоким показателям паропроницаемости
- Обладает невосприимчивостью к химическим растворителям
- Обеспечивает удобство транспортировки и монтажа
- Может применяться с водными системами теплого пола
- Не выделяет вредных веществ, в своем составе не имеет синтетики и формальдегида
Преимущества МДВП
Мягкие древесноволокнистые плиты обладают немалыми преимуществами и по сравнению с натуральной древесиной:
- Обладает более высокой теплоизоляцией (за счет пористой структуры) – 12 мм плиты соответствуют 44 мм древесины
- Обеспечивает надежную звукоизоляцию благодаря высокому показателю звукопоглощения (23 дБ)
Дополнительными преимуществами МДВП перед деревом являются меньшая стоимость, небольшой вес и эластичность.
Кроме того панели из мягкой ДВП:
- Не боятся резкого изменения температуры и перепадов влажности
- Не растрескиваются при изменении геометрии дома благодаря высокой упругости и гибкости
- Поддерживают микроклимат внутри помещения, что наиболее важно в периодически отапливаемых загородных домах
Внутренняя отделка панелей из МДВП обоями предполагает использование только клея на водной основе, что положительно сказывается на экологичности всего дома.
Один из самых популярных материалов для утепления являются опилки. Этот материал используются уже давно, поскольку отлично удерживает тепло. Опилки как утеплитель обеспечат сухое и теплое помещение на многие годы.
Для утепления фасада довольно часто используют пенопласт. Этот материал недорогой, прост в монтаже и имеет низкую теплопроводность. Об утеплении стен пенопластом читайте здесь.
Ещё один материал для утепления дома – Роквул Венти Баттс, о котором читайте в этой статье. В холодных регионах страны использование Венти Баттс является необходимостью, которую заменить другими материалами невозможно.
Что дает использование МДВП
Современные технологии производства мягкой ДВП определяют технические свойства этого материала, благодаря которым он обеспечивает высокие эксплуатационные качества конструкции в целом:
- Позволяет экономить на отоплении за счет объемной плотности («рыхлой среды») материала: мягкие ДВП характеризуются одновременно высокой удельной теплоемкостью (2,30 кДж/кг К) и низкой теплопроводностью (0,038-0,042 Вт/м ‘С). В такой среде содержится до 70% воздуха, благодаря чему она плохо проводит тепло и способствует созданию комфортного микроклимата
- Создает «эффект деревянного дома», в котором зимой держится тепло, а летом – прохлада. Данное свойство обеспечивается незначительной воздухопроницаемостью, основанной на оптимальном соотношении плотности и мелко-дисперсности. Наличие такого эффекта защищает дом от холода, жары, ветра
- Регулирует влажность за счет высокой паропроницаемости. Древесные волокна способны связывать и отдавать влагу, сохраняя собственные теплоизоляционные свойства. Эта особенность предохраняет строение от грибка и плесени
- Гарантирует высокую степень звукоизоляции;
- Обеспечивает полную экологическую чистоту и безопасность.
Таким образом, мягкая ДВП – это уникальное сочетание низкой теплопроводности, отличной паропроницаемости и высокой экологичности, которое позволяет создавать тепло-звукоизоляцию абсолютно нового качества.
Видео о ДВП мягкой
Проверка на пожаробезопасность
megabeaver.ru
Мягкие древесноволокнистые плиты – практичный и экологичный утеплитель для дома
Чтобы в доме было комфортно в любое время года, независимо от погоды за окном, необходимо своевременно позаботиться о качественной теплоизоляции. Она позволит сохранить тепло в доме зимой и не изнывать от удушающей жары в помещении летом.
Но, столкнувшись с необходимостью выбора и покупки утеплителя, многие люди теряются. Ведь на рынке представлен действительно огромный выбор различных видов утеплителей. Тем не менее, есть наиболее популярные виды, которым чаще всего отдается предпочтение.
Кто-то спросит совета у строителей и будет полагаться на их мнение при выборе материалов, а кто-то любит сам делать выбор, ориентируясь на критерии, которые важны именно для него (цена, качество, безопасность и т.д.). Рассмотрим основные плюсы и минусы популярных видов утеплителей, это поможет малоопытному в данном вопросе покупателю сложить общую картину и сделать выводы для себя, определиться в многообразии представленных вариантов и купить подходящий по всем параметрам утеплитель для своего дома.
К числу наиболее популярных относятся такие виды утеплителей, как:
- минеральная вата;
- стекловата;
- пенополистирол;
- пенополиэтилен;
- натуральные хвойные плиты (правильное их название – древесноволокнистые плиты) и т.д.
Особенности рассматриваемых утеплителей
Минеральная вата и стекловата «заработали» свою популярность благодаря низкой стоимости теплоизоляционного материала, простоте монтажа, а также практичности (эти материалы можно использовать при утеплении стен, крыш и даже полов). Они имеют неплохие параметры тепло- и звукоизоляции, не горючи.
Но не стоит забывать, что они весьма прихотливы в плане условий эксплуатации (плохо переносят воздействие влаги, прямых солнечных лучей), требуют обязательного проведения паро- и гидроизоляции, внешней отделки. Это дополнительные расходы, которые сводят такой фактор, как низкая стоимость утеплителей, практически «на нет».
Но самое главное – при изготовлении этих материалов используются компоненты, которые опасны для здоровья. Это связующие и клеящие составы, которые склеивают волокна в единую плиту, мат и т.д. Их воздействие на организм человека не всегда благоприятно, особенно если речь идет о постоянном проживании в доме, утепленном такими материалами.
Тоже самое касается и таких утеплителей, как пенополистирол (как видно из названия – в его составе имеется стирол – токсичный компонент), экструзионный пенополистрирол и полиэтилен. Они изготовлены из синтетических материалов, небезопасны для здоровья. Как правило, такие материалы горючи, в процессе горения могут выделять ядовитые вещества.
В связи с этим вполне логично возникает вопрос – рациональна ли та мнимая денежная экономия, которую выигрывает покупатель отдавая предпочтение недорогим утеплителям? Ведь речь идет о самом дорогом – здоровье своих близких, собственном здоровье.
В отличие от рассмотренных выше видов утеплителей, плиты МДВП наряду с оптимальной ценой предлагают своим покупателям отличный набор технико-эксплуатационных свойств и характеристик.
Уникальная технология производства древесноволокнистых плит позволяет сохранять 100% экологичность и безопасность материала. Для производства используется древесина хвойных пород, богатая природной смолой, именно она выступает в качестве связующего компонента. Так что, необходимость в использовании искусственных примесей и клеев отпадает сама собой.
Плиты МДВП отлично подходят для утепления стен, полов, кровли. Они просты в монтаже, не прихотливы к условиям эксплуатации, гипоаллергенны, безопасны, надежны и долговечны. Хвойная древесина имеет свойство регулировать микроклимат в помещении, обеспечивая оптимальный уровень влажности. В доме, утепленном МДВП плитам, будет всегда уютно и комфортно – тепло зимой и прохладно летом.
Подводя итоги
Резюмируя кратко рассмотренную информацию об основных видах утеплителей, используемых сегодня нашими соотечественниками для своих домов, можно сказать: если для вас важен только фактор денежной экономии, то можно найти массу бюджетных вариантов.
Но если вы хотите выбрать для своего дома надежный и долговечный, а самое главное – безвредный для здоровья утеплитель и сделать дом уютным и безопасным местом, то выбор в пользу натуральных материалов (например, древесноволокнистых плит МДВП) очевиден.
www.domzamkad.ru
МЯГКАЯ ДВП ИЗОПЛАТ
МДВП – мягкая древесноволокнистая плита или Softboard (международное название). Производится из размолотой древесины до состояния волокна без добавления клея или других химических связующих. Древесные волокна (или фибра) предварительно размачиваются в воде, укладываются на ленту в виде ковра определенной толщины и затем уплотняется горячим прессом. Затем разрезанные листы отправляются в сушильную камеру на несколько часов.
Пористая волокнистая структура плиты МДВП, если посмотреть при увеличении, напоминает войлок. Воздух как-бы запечатывается между древесными волокнами, за счет чего достигаются высокие показатели по теплоизоляции и звукоизоляции. В плите воздух занимает до 80% объема. Поэтому МДВП является теплоизоляционным материалом высшей категории. В этой же группе представлены все известные минеральные и органические теплоизоляционные маты и плиты.
Высокие звукопоглащающие свойства МДВП обеспечиваются пористой структурой (много воздуха) и хаотичным расположением древесных волокон. Звуковая волна разбивается и вязнет в структуре плиты. А высокие звкоизоляционные свойства МДВП обеспечиваются более плотной и волнистой поверхностью листа. Звуковая волна отражается под разными углами. Такая неравномерная плотность плиты (свойство композитного материала) делает плиту универсальным звукоизоляционным материалом, способным заменить несколько слоёв обычной каркасной звукоизоляционной конструкции, например, ваты и гипсокартона.
Для производства плит Изоплат (ISOPLAAT) используются только хвойные породы древесины северных широт, особенно богатые лигнином (это природный сок, который присутствует во всех растениях, но в хвойных его содержание на 30% больше, чем в лиственных). Именно лигнин обеспечивает связи волокон друг с другом. Высокое качество сырья и мелкий равномерный помол выгодно отличает скандинавскую продукцию от других европейских и американских производителей. За счёт отсутствия клея плиты Изоплат даже во влажном состоянии при сильных морозах на разрушаются и сохраняют свои изоляционные свойства.
ekoplat.ru
Древесноволокнистые плиты (ДВП) – прошлое и настоящее – статьи о фанере и пиломатериалах
Актуальную цену на материал уточняйте у менеджеров по телефонам: 8(495)646-72-41,8(495)646-72-43
Древесноволокнистые плиты – это листовой продукт, изготовленный из древесных волокон или других лигноцеллюлозных материалов, первичное соединение которых происходит в силу расположения волокон и присущих им свойств связывания.
Физико-механические свойства твёрдых древесноволокнистых плит близко подходят к соответствующим показателям натуральной древесины, а в некоторой части превосходят их. Поэтому во многих случаях использование вместо натуральной древесины древесноволокнистых плит позволяет получать изделия высокого качества с экономией материалов при снижении общей себестоимости изделия.
Установлено что 1 тыс. квадратных метров твёрдых древесноволокнистых плит может заменить 14-16 кубических метров пиломатериалов.
Являясь в ряде областей равноценным заменителем других строительных материалов, древесноволокнистые плиты нашли широкое применение во времена плановой экономики.
Так, изоляционные плиты древесноволокнистые плиты с малым объёмным весом (до 250 кг/м3) широко применялись для звуко – и теплоизоляции междуэтажных перекрытий, стен, полов и потолков жидых зданий, культурно-бытовых и коммунальных помещений, для утепления кровель и перекрытий промышленных корпусов, для звукоизоляции машинописных бюро и радиостудий, а также для акустики в клубах и театрах.
В настоящее время изоляционные мягкие плиты ДВП незаслуженно забыты. В 1980-х годах в РСФСР выпускалось около 600 тыс. м3 мягких ДВП толщиной 12мм, работало 15 линий по технологии мокрого способа производства. Теперь в РФ осталась одна линия мощностью 80 тыс.м3. В 2008г. было изготовлено всего 36 тыс. м3 мягких ДВП.
В России годовой объём производства теплоизоляционных материалов всех видов составляет 17-18 млн.м3. Однако в связи с ужесточением требований Госстроя РФ по нормативам теплопотерь общая годовая потребность в утеплителях возросла в три раза – до 50-55 млн.м3. Но в современной практике отечественного строительства применяют преимущественно минераловатные утеплители (65%) и пенопласты(20%).
С реализацией программ малоэтажного строительства, спрос на мягкие ДВП к 2015 году, может составлять 800-900 тыс.м3 в год. Сдерживают высокие цены на изоляционные ДВП мокрого способа производства составляющие около 7тыс. руб/м3, в то время как цены на минераловатные утеплители и пенопласты в 2-3 раза ниже.
Снижение стоимости изоляционных ДВП можно обеспечить при использовании принципиально нового сухого способа производства, предлагаемого фирмами Siempelkamp и Dieffenbacher. По сравнению с обычным способом производства обеспечивается снижение себестоимости примерно в два раза до 2000 руб/м3, что позволяет снизить оптовые цены и расширить возможности реализации, в том числе на экспорт.
В Германии на границе с Францией, с 2006 года работает первое в мире сухое производство ДВП (мягкие изоляционные ДВП) на заводе «Гутекс» с оборудованием Siempelkamp, его мощность – 430 тыс.м3 в год. Изоляционные ДВП реализуются в страны Западной Европы и спрос на них возрастает.
В России рынок изоляционных мягких плит недооценён. С учётом прогнозируемого спроса для потребностей малоэтажного домостроения необходимо построить 2-3 завода мощностью 250-400 тыс.м3 в год по выпуску мягких ДВП по новой технологии.
Древесноволокнистые изоляционно-отделочные плиты с объёмным весом свыше 250 кг/м3 применялись в качестве сухой штукатурки для внутренних перегородок в помещениях гражданского и промышленного назначения, для утепления кровель жилых и общественных зданий.
Лёгкость и большие размеры изоляционных плит делали их первоклассным материалом для утепления массово возводимых в тот период времени щитовых домов.
Большое применение плиты находили в качестве материала для полов. Для этой цели использовались сверхтвёрдые плиты, пропитанные синтетическими водоустойчивыми смолами или быстровысыхающими маслами с последующей термической обработкой.
Часто практиковалось применение сверхтвёрдых плит совместно с изоляционными. В этом случае получался «тёплый пол», по характеристике теплопроводности близкий к паркетному.
В мебельной промышленности твёрдые плиты находили применение для изготовления стенок шкафов, днищ ящиков, крышек столов, сидений и спинок стульев и т.д.
Отделанные или фанерованные декоративными породами плиты применялись также для обшивки железнодорожных вагонов и автобусов, для отделки кабин самолётов и кают пароходов, для внутренней отделки зданий, санузлов, кухонь и т.д.
Термин «стеновая плита» впервые появился в 1960г. и относится к древесноволокнистым плитам, которые предназначались для облицовки.
Французский журнал «Bois et scieries» в номере от 20 февраля 1958 г. указывает, что история развития производства древесноволокнистых плит (ДВП) началась в России в 1912 г., когда инженер Кузнецов сделал первые плиты, более прочные и гибкие чем древесина. Они имели размер 1420 х 2220 мм. Однако предложение и эксперименты инженера Кузнецова не возбудили к себе интереса и были вскоре забыты. Лишь через 20 лет, уже в Советской России, инженер Кокурин усовершенствовал способ изготовления древесноволокнистых плит (ДВП), предложенный инженером Кузнецовым, и разработал первый специальный дефибратор для подготовки древесного сырья.
Один из первых заводов для производства древесноволокнистых плит был построен в Англии в 1898 году; на нём вырабатывались плиты из отходов бумаги и газетной макулатуры.
В 1915г. были изготовлены первые жёсткие волокнистые плиты из древесной массы (инсулит).
В 1922г. было организовано аналогичной продукции из жмыха сахарного тростника, т.е. из отходов промышленного тростникового сахара (целотекс).
Производство древесноволокнистых плит в крупных масштабах началось впервые в США в период между двумя мировыми войнами. Первый крупный завод здесь был пущен в 1926г.
Несколько позже получило развитие производство этих плит в Европе. Начало производства волокнистых плит в Швеции относится к 1929г. Тогда в стране имелось два завода, выпускавших всего 11 тыс.т плит в год. В 1939г. в Швеции, Норвегии и Финляндии насчитывалось уже 14 заводов мощностью 161 тыс.т в год (46 млн.м2).
Развитие производства древесноволокнистых плит шло очень быстро. Мировое производство составляло в 1932г. около 10 млн.м2, а к 1938г.увеличилось до 200 млн.м2, т.е. выросло за 6 лет в 20 раз. В 1960г. он составил уже около 1.1млрд.м2.
Промышленный выпуск древесноволокнистых плит впервые в СССР был организован в 1936г. на Новобелицком (Белоруссия) лесохимическом заводе, где был пущен цех мощностью 1.6 млн.м2; второй завод, мощностью в 3.2 млн.м2 твёрдых и изоляционных плит был пущен в Москве в 1937г. Однако наиболее интенсивное развитие их производство получило в послевоенные годы. В 1948г. было выпущено 2.8 млн.м2 древесноволокнистых плит. За период 1946-1965гг. было построено 47 заводов по выпуску ДВП, и в 1965г. их выпуск составил 138 млн.м2. В 1975г. было произведено 408.6 млн.м2 древесноволокнистых плит. В 1980г. объём их выпуска составил 549 млн.м2.
Начиная с 1971г. по объёму промышленного производства древесноволокнистых плит СССР занимает второе место в мире (после США) и первое в Европе.
На предприятиях Минлесбумпрома СССР производилось 90% общесоюзного выпуска древесноволокнистых плит, а остальные министерства и ведомства давали 10%.
В 1990г. насчитывалось 45 предприятий выпускающих древесноволокнистые плиты, которые произвели 484.6 млн.м2. В 1998г. в России насчитывалось только 36 действующих заводов по выпуску ДВП которые произвели только 191.3 млн.м2 (уровень 1967г.), а к 2000г. их количество сократилось до тридцати. Далее объём выпуска ДВП стал постепенно нарастать и в 2000г он составил 271 млн.м2(уровень 1971г.), в 2004г. произведено 342 млн.м2 (уровень 1973г.).и в 2006г. было произведено 373 млн.м3 (уровень 1974г.). Но динамичное развитие производства ДВП наблюдалось только до 2008г., так как в связи с кризисом, в 2009г., падение выпуска ДВП составило 28,7%. Максимальное падение производства ДВП в течение 2009г. достигало 38%. В натуральном выражении в 2009 г их производство составило 372.9 млн.м2.
Однако следует отметить, что кризис несколько ускорил процесс обновления основных фондов с вытеснением неконкурентных производств и сейчас идёт процесс наращивания мощностей по производству ДВП. По данным Федеральной службы государственной статистики в январе – августе 2011г. произведено 278 млн.м2 древесноволокнистых плит.
Все статьи
www.allfanera.ru
11.4. Органические теплоизоляционные материалы и изделия
Органические теплоизоляционные материалы и изделия производят из различного растительного сырья: отходов древесины (стружек, опилок, горбыля и др.), камыша, торфа, очесов льна, конопли, из шерсти животных, а также на основе полимеров.
Многие органические теплоизоляционные материалы подвержены быстрому загниванию, порче различными насекомыми и способны к возгоранию, поэтому их предварительно подвергают обработке. Поскольку использование органических материалов в качестве засыпок малоэффективно в силу неизбежной осадки и способности к загниванию, последние используют в качестве сырья для изготовления плит. В плитах основной материал почти полностью защищен от увлажнения, а, следовательно, и от загнивания, кроме того, в процессе производства плит его подвергают обработке антисептиками и антипиренами, повышающими его долговечность.
Теплоизоляционные материалы и изделия из органического сырья. Среди большого разнообразия теплоизоляционных изделий из органического сырья наибольший интерес представляют плиты древесноволокнистые, камышитовые, фибролитовые, торфяные, пробковая теплоизоляция натуральная, а также теплоизоляционные пенопласты.
Древесноволокнистые плиты применяют для тепло- и звукоизоляции ограждающих конструкций. Изготовляют их из распущенной древесины или иных растительных волокон — неделовой древесины, отходов лесоперерабатывающей промышленности, костры, соломы, камыша, хлопчатника. Наибольшее распространение получили древесноволокнистые плиты, получаемые из отходов древесины, которые изготовляют путем горячего прессования волокнистой массы, состоящей из древесных волокон, воды, наполнителей, полимера и добавок (антисептиков, антипиренов, гидрофобизирующих веществ). Для изготовления изоляционных плит применяют отливочную машину, снабженную бесконечной металлической сеткой и вакуумной установкой, где масса обезвоживается, уплотняется и разрезается на плиты необходимых размеров.
Фото. 11.6. Древесноволокнистые плиты
Древесноволокнистые плиты выпускают пяти видов: сверхтвердые, твердые, полутвердые, изоляционно-отделочные и изоляционные. Изоляционные древесноволокнистые плиты имеют длину 1200…3600 мм, ширину 1000…2800 мм и толщину 8…25 мм, плотность 250 кг/м3, предел прочности при изгибе 1,2 МПа и теплопроводность не более 0,07 Вт/(м•°С).
Наряду с изоляционными применяют плиты изоляционно-отделочные с лицевой поверхностью, окрашенной или подготовленной к окраске.
Камышитовые плиты, или просто камышит, применяют для теплоизоляции ограждающих конструкций малоэтажных жилых домов, небольших производственных помещений, в сельскохозяйственном строительстве.
Фото. 11.7. Камышитовая плита
Это теплоизоляционный материал в виде плит, спрессованных из стеблей камыша, которые затем скрепляются стальной оцинкованной проволокой. Для изготовления камышитовых плит используют зрелые однолетние стебли диаметром 7…15 мм. Заготовку стеблей следует делать в осенне-зимний период. Прессование плит осуществляют на специальных прессах. В зависимости от расположения стеблей камыша различают плиты с поперечным (вдоль короткой стороны плиты) и продольным расположением стеблей. Плиты выпускают длиной 2400х 2800 мм, шириной 550… 1500 мм и толщиной 30…100 мм, марками по плотности Д175, 200 и 250, с пределом прочности при изгибе не менее 0,18…0,5 МПа, теплопроводностью 0,06…0,09 Вт/ (м•°С), влажностью не более 18% по массе.
Торфяные теплоизоляционные изделия изготовляют в виде плит, скорлуп и сегментов и используют для теплоизоляции ограждающих конструкций зданий III класса и поверхностей промышленного оборудования и трубопроводов при температуре от – 60 до – 100°С.
Фото. 11.8. Торфяная плита
Сырьем для их производства служит малоразложившийся верховой торф, имеющий волокнистую структуру, что благоприятствует получению из него качественных изделий путем прессования. Плиты изготовляют размером 1000х500х30 мм путем прессования в металлических формах с последующей сушкой при температуре 120…150°С. В зависимости от начальной влажности торфяной массы различают два способа изготовления плит: мокрый (влажность 90…95%) и сухой (влажность около 35%). При мокром способе излишняя влага в период прессования отжимается из торфяной массы через мелкие металлические сетки. При сухом способе такие сетки в формы не закладываются. Торфяные изоляционные плиты по плотности делят на марки Д 170 и 220 с пределом прочности при изгибе 0,3 МПа, теплопроводностью в сухом состоянии 0,6 Вт/(м•°С), влажностью не более 15%.
Цементно-фибролитовые плиты представляют собой теплоизоляционный материал, полученный из затвердевшей смеси портландцемента, воды и древесной шерсти.
Древесная шерсть выполняет в фибролите роль армирующего каркаса. По внешнему виду тонкие древесные стружки длиной до 500 мм, шириной 4…7 мм, толщиной 0,25…0,5 мм приготовляют из неделовой древесины хвойных пород на специальных древесношерстяных станках.
Фото. 11. 9. Цемнтно-фибролитовая плита
Шерсть предварительно высушивают, пропитывают минерализаторами (хлористым кальцием, жидким стеклом) и смешивают с цементным тестом по мокрому способу или с цементом по сухому (древесная шерсть посыпается или опыляется цементом) в смесительных машинах различного типа. При этом следят, чтобы древесная шерсть была равномерно покрыта цементом. Формуют плиты двумя способами: прессованием и на конвейерах, где фибролит формуют в виде непрерывно движущейся ленты, которую затем разрезают на отдельные плиты (подобно вибропрокату железобетонных изделий). При прессовании плит удельное давление для теплоизоляционного фибролита принимают до 0,1 МПа, а для конструктивного — до 0,4 МПа. После формования плиты пропаривают в течение 24 ч при температуре 30…35°С. Цементно-фибролитовые плиты выпускают длиной 2400…3000 мм, шириной 600… 1200 мм, толщиной 30, 50, 75, 100 и 150 мм. Цементный фибролит выпускают трех марок по плотности: Ф300, 400 и 500, теплопроводностью 0,09…0,15 Вт/(м•°С), водопоглощением не более 20%. Фибролитовые плиты марки Ф300 применяют в качестве теплоизоляционного материала, марки Ф400 и 500 — конструкционно-теплоизоляционного материала для стен, перегородок, перекрытий и покрытий зданий.
Арболитовые плиты получают также формованием и тепловой обработкой (или без нее) органического коротковолнистого сырья (дробленой станочной стружки или цепы, сечки соломы или камыша, опилок, костры и др.), обработанного раствором минерализатора.
Фото.
11 .10. Арболитовые плиты
Химическими добавками служат хлорид кальция, растворимое стекло, сернокислый глинозем. Вторым компонентом при изготовлении арболитовых плит является портландцемент. Плиты формуют длиной и шириной 500, 600 и 700 мм, толщиной 50, 60 и 70 мм. Плотность в сухом состоянии составляет 500 кг/м3, прочность на сжатие 0,3…3,5 МПа, предел прочности при изгибе не менее 0,4 МПа, теплопроводность в сухом состоянии не более 0,12 Вт/(м• °С), влажность не более 20% по массе.
Цементно-стружечные плиты отечественная промышленность производит двух марок: ЦСП-1 и ЦСП-2. Плиты изготовляют путем прессования древесных частиц с цементным вяжущим и химическими добавками.
ЦСП относятся к группе трудносгораемых материалов повышенной биостойкости. Их производят длиной 3200…3600 мм, шириной 1200, 1250 и тощиной 8…10, 12…16, 18…28 и 30…40 мм со шлифованной и нешлифованной поверхностью. ЦСП выпускают плотностью 1100…1400 кг/м3, влажностью до 9%, водопоглощением за 24 ч не более 16% и разбуханием по толщине не более 2%.
Фото. 11.11. Цементно-стружечные плиты
Плиты имеют достаточно высокую прочность на изгиб, для плит толщиной 8… 16 мм она составляет 9… 12 МПа, а для плит толщиной 26…40 мм — 7…9 МПа, теплопроводность— 0,26 Вт/(м•°С). ЦСП применяют в стеновых панелях, ‘плитах покрытий, в элементах подвесных потолков, вентиляционных коробах, при устройстве полов, в качестве подоконных досок, обшивок, облицовочных и других строительных изделий.
Пробковые теплоизоляционные материалы и изделия (плиты, скорлупы и сегменты) применяют для теплоизоляции ограждающих конструкций зданий, холодильников и поверхностей холодильного оборудования, трубопроводов при температуре изолируемых поверхностей от —150 до +70°С, для изоляции корпуса кораблей. Изготовляют их путем прессования измельченной пробковой крошки, которую получают как отход при производстве закупорочных пробок из коры пробкового дуба или так называемого бархатного дерева.
Пробка вследствие высокой пористости и наличия смолистых веществ является одним из наилучших теплоизоляционных материалов и служит для производства плит, скорлуп и сегментов.
Фото. 11.12. Пробковые плиты
Теплоизоляционные пенопласты в виде газонаполненных пластмасс, а также минераловатных и стекловатных изделий изготовляют с использованием полимерном связующем.
По физической структуре газонаполненные пластмассы могут быть разделены на три группы: ячеистые или пенистые (пенопласты), пористые (поропласты) и сотовые (сотопласты). Пенопласты и сотопласты на основе полимеров являются не только теплоизоляционным, но и конструктивным материалом. Теплоизоляционные материалы из пластмасс по виду применяемых для их изготовления полимеров делят: на полистирольные — пористые пластмассы на основе суспензионного (бисерного) или эмульсионного полистирола; поливинилхлоридные — пористые пластмассы на основе поливинилхлорида; фенольные — пористые пластмассы на основе формальдегида.
Поризация полимеров основана на применении специальных веществ, интенсивно выделяющих газы и вспучивающих размельченный при нагревании полимер. Такие вспучивающиеся вещества могут быть твердыми, жидкими и газообразными.
Фото. 11.13. Пенопластовые плиты
К твердым вспенивающим веществам, имеющим наибольшее практическое значение, относятся карбонаты, бикарбонаты натрия и аммония, выделяющие при разложении СО2. К жидким вспенивающим веществам относятся бензол, легкие фракции бензола, спирт и т. п. К газообразным вспенивающим веществам относятся воздух, азот, углекислый газ, аммиак. Для придания эластичности пористым пластмассам в полимеры вводят пластификаторы — фосфаты, фталаты и др.
Пористые и ячеистые пластмассы можно получать двумя способами: прессовым и беспрессовым. При изготовлении пористых пластмасс прессовым способом тонкоизмельченный порошок полимера с газообразователем и другими добавками спрессовывается под давлением 15…16 МПа, после чего взятую навеску (обычно 2…2,5 кг) вспенивают, в результате чего получают материал ячеистого строения.
При изготовлении пористых пластмасс беспрессовым способом полимер с добавками газообразователя, отвердителя и; других компонентов нагревают в формах до соответствующей температуры. От нагревания полимер расплавляется, газообразователь разлагается, и выделяющийся газ вспенивает полимер. Образуется материал ячеистого строения с равномерно распределенными в нем мелкими порами.
Плиты, скорлупы и сегменты из пористых пластмасс применяют для теплоизоляции ограждающих конструкций зданий и поверхностей промышленного оборудования и трубопроводов при температуре до 70°С.
Изделия из пористых пластмасс на суспензионном полистироле по плотности в сухом состоянии делят на марки Д 25 и 35 с пределом прочности при изгибе не менее 0,1…0,2 МПа, теплопроводностью 0,04 Вт/(м•°С), влажностью не более 2% по массе.
Такие же изделия на эмульсионном полистироле по плотности имеют марки Д 50…200, предел прочности при изгибе не менее 1,0…7,5 МПа, теплопроводность не более 0,04…0,05 Вт/(м• °С), влажность не более 1% по массе. Плиты из пористых пластмасс; изготовляют длиной 500…1000 мм, шириной 400…700 мм, толщиной 25…80 мм.
Фото. 11.14. Ячеистая пластмасса
Наиболее распространенными теплоизоляционными материалами из пластмасс являются полистирольный поропласт, мипора и др.
Полистирольный поропласт — отличный утеплитель в слоистых панелях, хорошо сочетающийся с алюминием, асбестоцементом и стеклопластиком. Широко применяется как изоляционный материал в холодильной промышленности, судостроении и вагоностроении для изоляции стен, потолков и крыш в строительстве. Полистирольный поропласт, изготовленный из бисерного (суспензионного) полистирола, представляет собой материал, состоящий из тонкоячеистых сферических частиц, спекшихся между собой. Между частицами имеются пустоты различных размеров. Наиболее ценными свойствами полистирольного поропласта являются его низкая плотность и малая теплопроводность. Полистирольный поропласт выпускают в виде плит или различных фасонных изделий, его производят плотностью до 60 кг/м3, прочностью при 10%-ном сжатии до 0,25 МПа и теплопроводностью 0,03… 0, 04 Вт/(м•°С). Наиболее распространенный размер плит 1200х1000х100(50) мм.
Поропласт полиуретановый применяют для теплоизоляции ограждающих конструкций зданий и поверхностей промышленного оборудования и трубопроводов при температуре до 100°С.
Получают
его из полиэфирных полимеров введением
порообразующих и других добавок. Полиэфирные
полимеры — это большая группа искусственных
полимеров, получаемых с помощью
конденсации многоатомных спиртов
(гликоля, глицерина, пентаэритрита и
др.) и главным образом двухосновных
кислот — фталевой, малеиновой и др.
По плотности в сухом состоянии маты из пористого полиуретана делят на марки Д 35 и 50, теплопроводность их в сухом состоянии 0,04 Вт/(м• °С), влажность не более 1 % по массе. На основе пористого полиуретана выпускают также твердые и мягкие плиты плотностью 30…150 кг/м3 и теплопроводностью 0,022…0,03 Вт/(м• °С). Маты из пористого полиуретана изготовляют в виде плит длиной 2000 мм, шириной 1000 мм, толщиной 30…60 мм.
Фото.11.15. Поропласт полиуретановый
Мипора представляет собой пористый материал, получаемый на основе мочевиноформальдегидного полимера. Сырьем для производства мипоры является мочевиноформальдегидный полимер и 10%-ный раствор сульфанафтеновых кислот (контакт Петрова), а также огнезащитные добавки (раствор фосфорнокислого аммония 20%-ной концентрации).
Фото.11.16. Мипора
Мипору применяют для теплоизоляции строительных конструкций, промышленного оборудования и трубопроводов при температуре до 70°С.
Для получения мипоры в аппарат с мешалкой загружают водный раствор мочевиноформальдегидного полимера и вспениватель, которые энергично перемешивают. Полученную пену спускают в металлические формы, которые направляют в камеры, где масса при температуре 18…22°С отвердевает за 3…4 ч.
Полученные блоки направляют на 60…80 ч в сушила с температурой 30…50°С. Мипору выпускают в виде блоков объемом не менее 0,005 м3, пределом прочности при сжатии 0,5…0,7 МПа, удельной ударной вязкостью 400 МПа, водопоглощением 0,11% за 24 ч, теплопроводностью 0,03 Вт/(м•°С).
Совелитовые теплоизоляционные материалы.
Плиты изготавливаются из доломитовой извести и хризолитового асбеста. Они хорошо выдерживают старение и сохраняют теплоизоляционные свойства на протяжении многих лет. Относятся к группе несгораемых веществ, не воспламеняются и не поддаются гниению. Изделия не содержат коррозийных агентов.
Продукция экологически безопасна.
Фото.11.17. Совелитовые плиты
Плиты совелитовые теплоизоляционные предназначаются для тепловой изоляции промышленного оборудования и трубопроводов, обмуровки паровых котлов, ТЭЦ, ГРЭС, АЭС, предприятиях металлургической и коксогазовой промышленности, а также труб больших диаметров при температуре изолируемых поверхностей до +600оС. Эта плита является универсальным материалом. Так же их можно применять и в бытовых целях (защита нагревательных элементов, грилей, тен) и т. д
Вермикулит (от лат. vermiculus – червячок) – минерал из группы гидрослюд, имеющих слоистую структуру. Он представляет собой легкий, сыпучий, высокопористый материал без запаха. Крупные пластинчатые кристаллы (вермикулитовые плиты) имеют золотисто-желтый или бурый цвет. При нагревании до температуры 900–1 000°C вермикулит вспучивается, проявляя одно из своих самых замечательных качеств: он увеличивается в объеме в 4,5–12 раз, превращаясь во вспученный вермикулит. Это явление объясняется тем, что при прокаливании молекулярная вода в чешуйках и пачках вермикулита превращается в пар, под напором которого листочки слюды раздвигаются всегда в одном направлении, перпендикулярном спайности слюды.
Вспученный
таким образом вермикулит при охлаждении
сохраняет приобретенный им объем с
тончайшими прокладками воздуха взамен
водяного пара между листочками слюды,
что и придает минералу многие его ценные
свойства, например:
долговечность. Бесспорным преимуществом вермикулита является то, что срок его годности и действия не ограничен!
Фото.11.18. Вермикулитовый гравий
– легкость (0,065–0,130 г/см3), пористость и сыпучесть. При засыпке в ходе работ по утеплению здания он заполняет все пустоты небольшого диаметра и любой неправильной формы;
– термостойкость. Температура плавления вермикулита: 1350°C, диапазон рабочих температур: от –260°C до +1200°C. Материал устойчив к высоким температурам и открытому огню. При воздействии высоких температур не выделяет газов, что является несомненным преимуществом по сравнению с другими утеплителями;
– биологическая и химическая стойкость. Материал не имеет запаха. Он не подвержен разложению и гниению под действием микроорганизмов, препятствует образованию плесени, к тому же исключено появление насекомых и грызунов. Вермикулит не вступает во взаимодействие с активными химическими веществами среды.
– радиационная защита. Вермикулит имеет способность отражать гамма-излучения, а также поглощать радиоактивные вещества – стронций‑90, цезий‑137, кобальт‑58;
– экологичность. Вспученный вермикулит – абсолютно не токсичный, экологически чистый и радиационно-безопасный современный материал, свободный от канцерогенных примесей;
– малая гигроскопичность и большое водопоглощение. Вермикулит имеет высокий коэффициент поглощения влаги (объем материала массой 100 гр. поглощает 400 мл воды) и при намокании незначительно теряет свою механическую прочность. После высыхания вспученный вермикулит восстанавливает прежние теплозвукоизоляционные и противопожарные свойства.
– высокие тепло- и звукоизоляционные свойства. Благодаря своей пористой структуре вспученный вермикулит является прекрасным тепло – и звукоизолятором (коэффициент звукопоглощения при частоте 1000 Гц в пределах 0,7–0,8), что позволяет с успехом использовать его в качестве насыпного утеплителя при обработке пола и кровли.
– экономичность. Утепление с использованием вермикулита обеспечивает существенную экономию средств, так как по своим энергосберегающим свойствам вспученный вермикулит в 7–10 раз превосходит такие традиционные строительные материалы, как бетон или кирпич.
Все перечисленные свойства определяют необыкновенно широкие возможности его использования в качестве сырья многоцелевого назначения.
Вспученный вермикулит успешно применяется более чем в 200 областях производственной деятельности по всему миру. Благодаря вышеперечисленным качествам, вспученный вермикулит находит широкое применение в строительстве, атомной, пищевой и химической промышленностях, сельском хозяйстве, металлургии, судостроении.
Эффект от применения вермикулита в качестве несгораемого насыпного материала с отличными тепло- и звукоизоляционными качествами уже оценили в строительстве.
Применение вермикулита в строительстве имеет явные преимущества в сравнении с использованием традиционных материалов. Благодаря этому материалу можно не только уменьшить вес отдельных конструкций и улучшить их качества, но и снизить расход ценных материалов, уменьшить затраты на фундаменты и увеличить полезную площадь зданий за счет тонких стен и перегородок.
Вспученный вермикулит обладает одним из самых низких показателей по теплопроводности среди теплоизоляционных материалов –0,04–0,062 Вт/м•оС. Слой засыпного вермикулита, имеющий толщину всего 12 см, в кирпичной кладке обеспечивают теплоизоляцию, удовлетворяющую современным требованиям.
Засыпная изоляция чердачных помещений и пола.
Слой вермикулита толщиной 5 см, покрывающий чердачные перекрытия, позволяет снизить теплопотери на 75%, а слой толщиной 7,5 см – на 85%. Слой вермикулита толщиной 10 см увеличит теплозащиту на 92%! Часто в чердачных помещениях вермикулит укладывают в мешках, что позволяет легко демонтировать изоляцию в случае необходимости.
Материалы на основе вспученного вермикулита эффективны при решении задач противопожарной и огневой защиты. Высокая температура плавления (1350°С), значительная отражающая способность и высокая термостойкость вермикулита стали решающими факторами при создании огнезащитных вермикулитовых плит и блоков. Это экологически чистый материал, который кроме высокой огнестойкости имеет отличные показатели по звукопоглощению, теплоизоляции.
Применение вермикулита на разных этапах строительства и в различных качествах позволяет решить сразу несколько проблем. Защита сооружений от огня, сохранение тепла, звукоизоляция как снаружи здания, так и внутри между помещениями и их благоустройство – одним словом, сегодня диапазон применения вермикулита в строительстве довольно широк, и в будущем, с развитием строительных технологий, значительно увеличится.
Вспученный перлит.
Перлит (гидроксид обсидиана) является породой вулканического происхождения (по сути, стекло вулканического происхождения). Химический состав: SiО2-75,5; А12О3 -13,6; Fe2О3 – 1,0; CaO -1,0; MgO – 0,3; Na2О – 3,8; K2О – 4,8. Отличительной чертой перлита от других вулканических стекол является то, что при нагревании до определенной температуры в диапазоне его размягчения, он увеличивается в объеме от четырех до двадцати раз против его первоначального объема.
Такой процесс вспучивания происходит вследствие присутствия в природном перлите от двух до шести процентов связанной воды. При быстром нагревании этой породы выше 870°C, она лопается наподобие <поп корна>, так как связанная вода испаряясь создает бесчисленные мельчайшие пузырьки в размягченных остекленевших частицах. Поскольку перлит является формой природного стекла, он относится к химически инертным и имеет pH, приблизительно равным 7.
Перлитовые
плиты-ПЦ изделия применяются для тепловой
изоляции строительных конструкций
жилых, общественных и промышленных
зданий и сооружений.
Перлитоцементные плиты предназначены для тепловой изоляции конструкций общественных и промышленных зданий и сооружений, а также для тепловой изоляции промышленного оборудования при температуре изолируемой поверхности до 600°C (в т. ч. котлов ДКВР и ДЕ).
Фото.11.19. Перлитовая плита
Перлитоцементные плиты упаковываются по 8 плит в упаковке. В 1 кубическом метре 80 плит =10 упаковок.
Физико-механические показатели плит: 1. Плотность, кг/м3 320±25;
2. Прочность при изгибе, кгс/см2 2,5; 3. Теплопроводность, Вт/м•оС 0,070-0,120; 4. Температура, °C до 600; 5. Размер, мм 500x500x50.
Керамзитовый гравий. Керамзит — лёгкий пористый строительный материал, получаемый путём обжига глины или глинистого сланца. Керамзитовый гравий имеет овальную форму. Керамзитовый щебень отличается лишь тем, что его зерна имеют в основном кубическую форму с острыми гранями и углами. Производится также в виде песка — керамзитовый песок (см. Гл. 3).
Шунгизитовый гравий. Шунгизит получают вспучиванием измельченных сланцевых шунгитсодержащих пород, содержащих 1, 2 – 5 % шунгитового вещества. Это особая форма углерода, состоящая из частиц размером 0, 2 мкм, равномерно распределенных в силикатной массе.
studfiles.net
Теплоизоляционная древесноволокнистая плита | Банк патентов
Предлагаемое техническое решение, а именно, теплоизоляционная древесноволокнистая плита, относится к классу теплоизоляционных материалов низкой плотности, получаемых с использованием растительного сырья. Плита предназначена для применения в качестве теплоизоляции жилых зданий и других объектов промышленного и гражданского строительства.
Известен теплоизоляционный материал по патенту RU 2075206 [1], получаемый на основе льняной костры, включающий измельченную методом дефибрирования, очищенную и калиброванную через сито с диаметром отверстий 1-2 мм костру льна, подвергнутую гидролизу в водном растворе гидроксида натрия в течение 1-12 ч с концентрацией меньше 5% и температурой 288-300 К при следующем соотношении массовых долей компонентов: сухая льняная костра 15-17; водный раствор гидроксида натрия 83-85.
Теплоизоляционный материал по указанному выше патенту RU 2075206 [1] является экологически чистым по той причине, что при его изготовлении используется способность льняной костры к разволокнению до фибр с целью увеличения активности межмолекулярного и структурного взаимодействия волокон. Такое взаимодействие, по аналогии с войлоком, обеспечивает сохранение формы теплоизоляционной плиты из льняной костры без использования связующих в виде фенолформальдегидной или других смол. Однако технология получения теплоизоляционного материала на основе льняной костры по патенту КИ 2075206 [1] сложна, т.к. требует длительного гидролиза в водном растворе гидроксида натрия в течение 1-12 ч при температуре 288-300 К. Кроме того, для получения данного материала необходима льняная костра, не относящаяся к классу достаточно распространенного сырья, что ограничивает область применения данного технического решения.
Отмеченные выше недостатки в определенной степени устраняет техническое решение по патенту на изобретение RU 2291051 [2]. Изобретение относится к композициям, применяемым для изготовления древесно-стружечных плит. Описан состав для плит, включающий в качестве наполнителя рисовую шелуху или смесь рисовой шелухи и древесных опилок, жидкое натриевое стекло с модулем 2,4-3,6, диоксид кремния, в качестве которого используют искусственные диоксиды кремния или кремнеземные пылевидные отходы различных производств с содержанием диоксида кремния не менее 80%, при заявленном соотношении компонентов.
Однако техническое решение по указанному выше патенту RU 2291051 [2] не обеспечивает получение теплоизоляционной плиты, поскольку предполагает значительное содержание диоксида кремния, что, кроме того, повышает износ инструмента и затрудняет обработку (резку) плит по данному патенту.
Известна экологически чистая древесно-волокнистая плита высокой плотности мокрого способа получения по патенту на изобретение КЛ 2440235 [3], содержащая в качестве упрочняющих агентов от 0,05 до 2,0 вес. % акриловой смолы и от 0,1 до 2,0 вес. % эпоксидной смолы. Данная плита представляет собой древесно-волокнистую плиту, получаемую в основном из древесной стружки путем пропаривания волокон и превращения их в волокнистую массу с последующим диспергированием в большом объеме воды с получением суспензии волокнистого материала, добавления упрочняющего агента и вещества для повышения влагостойкости, удаления влаги и формования до постоянной толщины с последующим горячим прессованием до плотности 0,80 г/см3 или более. Однако данное техническое решение требует применения акриловой и эпоксидной смол, что усложняет технологию производства плит.
Известна древесно-стружечная плита по патенту на полезную модель RU 114331 [4], содержащая два наружных слоя и внутренний слой, наружные слои расположены со сторон плиты, имеющих большие площади, чем остальные ее поверхности, при этом внутренний слой расположен между наружными слоями и соединен с ними, наружные слои выполнены из мелких частиц древесины и связующего материала, причем внутренний слой содержит полистирол, отличающаяся тем, что мелкие частицы древесины выполнены в виде опилок, а во внутренний слой дополнительно введены стружка и связующий материал, при этом полистирол выполнен в виде гранул размером 0,3-1,5 мм. Таким образом, полезная модель по патенту RU 114331 [4] требует использования дополнительного связующего и гранулированного полистирола, что, как в рассмотренном выше случае, усложняет технологию изготовления и тем самым снижает конкурентоспособность плиты.
Данное техническое решение по патенту на полезную модель 1Ш 114331 [4], как и названные выше технические решения [1-3], не предусматривают возможностей использования других видов сырья, а именно – отходов (побочного продукта) переработки хвойной зелени в виде хвойной лапки. Хвойная зелень, например, в виде измельченной сосновой лапки используется для получения водных растворов биологически активных веществ методом экстрагирования. Свежую хвою, полученную путем отделения от хвойной лапки (ГОСТ 21769-84), измельчают с помощью шнекового режущего аппарата в хвойную муку, экстрагируют из нее водорастворимые биологически активные вещества (низкомолекулярные кислоты, углеводы, некоторые полярные гликозиды фенольных соединений) на водной бане при следующих параметрах проведения процесса: гидромодуль 40 (абс. сух. в.) продолжительность 0,5 часа при перемешивании, фильтрование, отжим на прессе. При этом образуется большое количество отходов в виде существенно дефибрированных фрагментов хвои, содержащих большое количество органических и минеральных веществ, не экстрагируемых водой (различные фенольные соединения, некоторые гликозиды фенольных соединений и терпеноидов, терпеноиды с несколькими кислородсодержащими функциональными группами и т.п.). Однако этот продукт переработки, обычно называемый отходами производства водорастворимых биологически активных веществ, имея ряд полезных свойств, не используется в известных технических решениях для изготовления теплоизоляционных древесноволокнистых плит.
Технический результат от применения предлагаемого технического решения в виде теплоизоляционных древесноволокнистых плит выражается, обеспечивается и обосновывается следующими факторами:
1) теплоизоляционная плита выполнена из экологически чистых отходов производства водорастворимых биологически активных веществ с использованием в качестве сырья хвойной лапки;
2) для повышения прочности плиты ее наружные слои имеют волокнистую структуру более высокой плотности, чем внутренний слой, а все слои выполнены из дефибрированных фрагментов хвойной зелени в виде измельченной хвойной лапки, причем в качестве связующего для внутреннего и наружных слоев использованы не экстрагируемые водой органические соединения, коллоидный лигнин извлеченные из хвойной лапки. Кроме того, для повышения прочности плиты ее наружные имеют волнообразный профиль.
3) упрощается технология изготовления плиты, поскольку не требуются связующие в виде, например, акриловой или эпоксидной смолы, поскольку в качестве связующего используются не экстрагируемые водой органические соединения, коллоидный лигнин как сопутствующие продукты переработки измельченной хвойной лапки;
4) поскольку основным компонентом предлагаемой плиты является побочный продукт (отходы) переработки измельченной хвойной зелени, дефибрирование которой как не одревесневшего материала весьма эффективно происходит без использования дополнительных химических или механических воздействий, то содержащиеся в продукте переработки волокна за счет механохимического взаимодействия обеспечивают достаточную прочность и стабильность размеров плиты.
Техническая реализация теплоизоляционной древесноволокнистой плиты. Для изготовления плиты используется побочный продукт (отходы) переработки измельченной хвойной зелени в виде хвойной лапки сосны обыкновенной. Такой продукт образуется в виде отходов производства водорастворимых биологически активных веществ методом экстрагирования водой при температуре 283 К на водяной бане. В данном случае дефибрирование весьма эффективно происходит без использования дополнительных химических веществ, поскольку переработке подвергаются не одревесневшие части растений и по этой причине для их полного или частичного разделения на отдельные волокна не требуется больших затрат энергии. Тепловая обработка измельченной хвойной лапки в процессе экстрагирования водорстовримых биологически активных веществ приводит к деструкции растительных клеток, частичному разрушению клеточной стенки. При обработке растительного сырья горячей водой или паром под давлением лигнин переходит в раствор, образуя коллоидный лигнин, который при высокой температуре размягчается, превращаясь в смолообразное пластичное вещество, которое в данном производстве являются побочным продуктом.
Однако в заявленном техническом решении не экстрагируемые водой органические соединения, коллоидный лигнин являются естественными связующими для измельченных и дефибрированных остатков хвойной лапки, а также для соединения внутреннего слоя с наружными слоями.
Побочный продукт переработки в виде измельченных и дефибрированных остатков хвойной лапки имеет начальную температуру не более 343-363 К. В горячем состоянии (343-363 К) данный продукт подается в пресс-форму и подвергается прессованию. При прессовании уменьшается содержание влаги, интенсифицируются механохимические взаимодействия волокон остатков хвойной лапки, формируется и фиксируется структура плиты. После набора достаточной прочности плита освобождается от пресс-формы. Плита в горизонтальном положении размещается на стеллажах для окончательного набора прочности, после чего реализуется потребителям.
Техническая реализация одного из вариантов плиты представлена на фиг. 1. Плита содержит состоящие из измельченных и дефибрированных остатков хвойной лапки сосны обыкновенной наружные слои 1 и 2. Между слоями 1 и 2 расположен соединенный с ними внутренний слой 3, также состоящий из измельченных и дефибрированных фрагментов хвойной лапки сосны обыкновенной. Отличие структуры наружных слоев от структуры внутреннего слоя объясняется тем, что при прессовании имеет место перенос влаги, а вместе с ней и наиболее мелких частиц, из среднего слоя к наружным слоям плиты. Кроме того, имеет место неодинаковое механическое и тепловое воздействие на слои в процессе прессования. Наружные поверхности плиты, повторяя профиль плит пресса, имеют волнообразный профиль (фиг. 1).
Плотность материала внутреннего слоя плиты не превышает 1 г/см 3. Толщина плиты определяется теплотехническим расчетом.
Функционирование плиты. В процессе монтажа и функционирования плита подвергается воздействию собственного веса, тепла и влаги. Эти воздействия изменяются с течением времени. Волнообразный профиль наружных слоев 1 и 2 (фиг. 1) и более высокая плотность материала по сравнению с внутренним слоем увеличивают сопротивление плиты эксплуатационным воздействиям по сравнению с плоским профилем. Внутренний слой, имея меньшую плотность, обеспечивает теплоизолирующую функцию плиты.
bankpatentov.ru
Утепление ДВП – Теплоизоляция | утепление | гидроизоляция
ДВП — древесно-волокнистые плиты, представляет из себя мягкий, легко ломкий картон различной толщины и крепости. Одна сторона плиты (лицевая) гладкая, другая — слегка рифленая. Производится ДВП из древесной стружки и других отходов деревоперерабатывающих прнедприятий. К стружке и опилкам добавляют вяжущие и огнезащитные вещества, а также средства против древесных жучков.
ДВП — отличный теплоизолятор, плита толщиной 12 мм эквивалентна одному кирпичу или доске толщиной 45 мм. Плотность п ДВП 30 — 270 кг/м³, теплопроводность 0,04 — 0,09 Вт/(м·°С), класс огнестойкости В1 или В2. ДВП хорошие звукоизоляторы, не разрушаются вредителями, так как антисептированы.
Утепление ДВП стен, потолков, пола не требует много времени, не нужны вспомогательные материалы. Кроме того, ДВП стоит дешево. Плиты легко режутся. для этого подходят обычные столярные инструменты. ДВП с открытыми порами регулируют уровень влажности в помещении и способны компенсировать деформации прилегающих к ним деревянных конструкций. На лицевую сторону плиты хорошо приклеиваются обои, их можно использовать под оштукатуривание и другую облицовку. В качестве теплоизоляционного материала под ДВП очень хорошо подойдет минеральная вата, которая выпускается в плитах или рулонах. Теплоизоляция из высококачественных минераловатных плит на синтетическом связующим существенно снижает затраты на отопление дома.
Утепление при помощи ДВП деревянных стен не представляет труда, и ее может делать один человек. Плиту размером 2500х 1220 мм прибивают 14-16 гвоздями длиной более 35 мм; под шляпки подкла-дывают пластинки из тонкого алюминия (дюраля) размером 15×15 мм. Гвозди располагают в шахматном порядке. Головки гвоздей с пластинками слегка притапливают. При утеплении оштукатуренных стен ДВП приклеивают к ним клеем ПВА, «Бустилатом» или клеющими мастиками.
Обивка потолка Несколько труднее обивать потолок. В этом случае нужен помощник. Плиту осторожно поднимают, прикладывают к месту, подпирают снизу двумя Т-образными подпорками из досок и прибивают гвоздями с алюминиевыми пластинками. Обивая потолок ДВП, необходимо пользоваться защитными очками.
Утепление пола. Утепление пола довольно сложная работа. Снимают чистый пол. На черный пол укладывают два слоя рубероида. Затем кладут ДВП. Сверху на плиты настилают чистый пол. Есть вариант утепления пола с помощью ДВП, но без поднятия чистого пола. Конечно, все знакомы с материалом, называемым ковровым покрытием. Им застилают коридоры и номера в современных гостиницах. Утепление пола начинают со снятия плинтусов. Затем на пол накладывают и прибивают ДВП. Сверху на плиты наклеивают ковровое покрытие. Покрытие перед оклейкой выдерживают в сухом и теплом помещении в развернутом виде одну-две недели. За это время оно выравнивается и усаживается.
Поделитесь статьей:
teploizolyaciya.com