Что такое экструзионный пенополистирол?
Экструзионный пенополистирол — это теплоизоляционный материал нового поколения. Производство экструзионного пенополистирола возникло в начале прошлого века в США. Уникальность технологии заключалась в том, что экструзия полистирола позволила получать материал с закрытыми ячейками.
Основными характеристиками нового материала стали низкая теплопроводность, минимальное водопоглощение, высокая удельная прочность.
Впервые данный вид полистирола был применен в 1942 году при изготовлении шестиместных плотов для береговой охраны США. Сейчас постепенная замена обычного пенополистирола на экструзионный стала мировой тенденцией.
Здоровое и комфортное жилище возможно лишь при условии того, что в нем будут поддерживаться соответствующие температура и влажность. Конденсацию влаги, пятна сырости, рост плесени и грибков в местах мостиков холода и образование термических трещин можно эффективным образом предотвратить, если использовать изолирующие материалы, такие как ТЕХНОПЛЕКС.
Надежная теплоизоляция строительных конструкций имеет решающее значение для снижения затрат на отопление и значит экономит долгие годы Ваши затраты.
Важнейшей причиной применения эффективной теплоизоляции является и то, что качественный теплоизоляционный материал уменьшает выбросы газов, сажи и пыли и, таким образом, приводит к прямому улучшению состояния окружающей среды.
Основные свойства теплоизоляционных плит ТЕХНОПЛЕКС:
– низкая теплопроводность
– отсутствие водопоглощения
– низкая паропроницаемость
– высокая прочность на сжатие
– стойкость к горению
– биологическая устойчивость
– простота и удобство применения
– долговечность
– это экологически чистый материал
Как получают пенополистирол?
Современный метод позволяет получить материал с равномерной структурой, состоящий из мелких, полностью закрытых ячеек с размерами 0,1-0,2 мм. Материал получают путем смешивания гранул полистирола при повышенной температуре и давлении с введением вспенивающего агента и последующим выдавливанием из экструдера. В качестве вспенивающего агента используются смеси легких фреонов или двуокись углерода (СО2).
Фреоны, применяемые для производства плит ТЕХНОПЛЕКС, относятся к группе озонобезопасных, нетоксичных и негорючих.
После изготовления плит в ячейках происходит относительно быстрое замещение остатков вспенивателя воздухом. Благодаря своей структуре плиты ТЕХНОПЛЕКС обладают стабильными теплотехническими показателями и необычайно высокой прочностью на сжатие.
Сравнительные характеристики:
Характеристика |
Техноплекс |
Пенопласт |
Стекловата |
||
30250 35250 |
45500 |
||||
Прочность на сжатие при 10% деформации, не менее (КПа) |
ГОСТ 17177-94 |
250 |
500 |
40-160 |
|
Плотность, кг/м3 |
ГОСТ 17177-94 |
25-38 |
38,1-45 |
15-50 |
11-30 |
Теплопроводность при (25±5) oC, Вт/(м.К) |
ГОСТ 7076-94 |
0,029 |
0,03 |
0,038 – 0,041 |
0,036 – 0,043 |
Расчетный коэффициент теплопроводности при условиях эксплуатации “А” |
ГОСТ 7076-94 |
0,031 |
0,032 |
0,040 – 0,043 |
0,042 – 0,050 |
Расчетный коэффициент теплопроводности при условиях эксплуатации “Б” |
ГОСТ 7076-94 |
0,031 |
0,032 |
0,042 – 0,047 |
0,046 – 0,055 |
Водопоглощение, % по объему, не более |
ГОСТ 17177-94 |
0,2 |
0,2 |
1,8 – 4,0 |
10-15 |
Группа горючести |
СНиП 21-01-97 |
Г1 и Г4 |
Г2 – Г4 |
НГ – Г1 |
источник: www.technoplex.ru
www.stroitel.cn.ua
Что такое экструдер и экструзия, принципы работы
Экструзия исключает из производственного цикла трудоемкую механическую обработку. Это быстрый и недорогой способ получения пленок, труб, профиля и других изделий, выпускаемых погонажом из полимерного сырья. В статье расскажем, что такое экструдер, как происходит процесс экструзии полиэтилена, разберем тонкости экструзионной технологии.
Что такое экструзия полимеров?
Процесс экструзии происходит при нагреве полимеров максимум до 250 0С. Производство идет на скорости до 120 метров/минуту. Около 30 % всего объема полимеров перерабатывается по экструзионной технологии с помощью экструдеров. Попробуем разобраться в тонкостях этого процесса.
Экструзия полимеров — это технология получения формовочных изделий из термопластов и их композиций на шнековых прессах. Осуществляется путем продавливания (под давлением) однородного расплава через щель формовочной головки экструдера.
Щель имеет определенную форму, которая определяет геометрию изделия — сайдинг, пленка, оконный ПВХ профиль. В качестве сырья используются гранулы полиэтилена ПВД и ПНД, полипропилена, ПВХ, полистирола и других полимеров.
Экструзия включает в себя следующие этапы:
- получение однородного расплава в экструдере;
- формование;
- охлаждение продукции;
- натяжение и намотка (пленки), нарезка (профиль, труба).
Устройство и принцип работы экструдера, что это такое
Уже по тому, что слова «экструдер» и «экструзия» являются однокоренными, становится понятным, что экструдер — это основной рабочий орган экструзионной линии.
По длине экструдер для полимеров условно делится на три зоны: загрузки, сжатия расплава и дозирования.
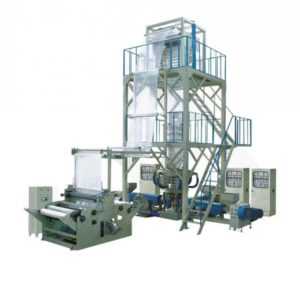
Экструдер для пленки
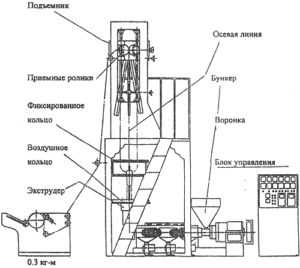
Схема экструдера для полиэтилена
- Зона загрузки. Гранулы (порошок, вторичное сырье) подаются в бункер самотеком или под напором сжатого компрессором воздуха. Шнек, который приводится в движение работой привода, вращается, и уплотняя полимер до состояния пробки, продвигает его к горячим секциям экструдера.
- Зона плавления. Здесь шаг между витками начинает уменьшаться. Как следствие один и тот же объем полимера пытается поместиться в уменьшившемся пространстве. Пробка прижимается к обогреваемым стенкам трубы экструдера, плавится, расплав перемешивается. Хотим уточнить, что плавление происходит, в основном, не за счет нагревателей (они лишь интенсифицируют процесс), а из-за огромных сдвиговых деформаций в уплотняющемся полимере.
- Зона дозирования. На выходе из экструдера полимер продавливается через систему фильтрующих сеток и проходит через формующее отверстие, профиль которого зависит от формы выпускаемой продукции.
Важно! Экструдер может различаться по типу и количеству шнеков. Выпускаются: одношнековые, двухшнековые и многошнековые, дисковые и многодисковые экструдеры.
О конструкции одношнекового экструдера.
Внутри толстостенного корпуса (трубы) вращается шнек — металлический стержень с винтовой навивкой. Шнек перемещает гранулы по направлению к экструзионной головке. Корпус опоясывают секции хомутовых нагревателей, которые греют металл и плавят полимер, прижимаемый винтом к внутренней поверхности трубы. «Горячую» часть оборудования помещают в водоохлаждаемый кожух, и сверху утепляют термочехлом.
Одношнековый экструдер, схема
Экструзия пленки
Наиболее популярными формовочными изделиями, которые получают с применением экструзии, являются пленки. Их изготавливают из полистирола, полипропилена, полиамида, лавсана, поликарбоната, ПВХ, но самыми востребованными из них являются, конечно же, пленки из экструдированного полиэтилена высокого и низкого давления. Именно на их примере мы рассмотрим, какие этапы этот материал проходит на выходе из экструдера.
Существует два метода экструдирования пленок:
- Метод раздува рукава.
- Метод плоскощелевой экструзии.
Читайте также какие дефекты могут возникнуть при экструзии пленки и как их устранить.
Метод раздува рукава.
Полимер выдувается из экструдера для пленки через кольцевую щель в формующей головке. Визуально это выглядит, как из фильеры поднимается сплошной пленочный цилиндр, раздуваемый изнутри воздухом. Воздух подается под давлением через дорн — отверстие в центре головки.
Охлаждение при экструзии полиэтилена, в зависимости от ориентации рукава, может производиться по двум схемам:
- Если рукав направлен вертикально вверх или горизонтально, то пленка обдувается воздухом, поступающим через охлаждающие кольца по периметру рукава;
Раздувной экструдер
- При отводе рукава вниз используется водяное охлаждение — такая схема сокращает время кристаллизации.
После остывания пленка складывается с помощью специальных «щек» в полотно и протягивается через отжимающие воздух валки. Готовый материал отправляется на намотку.
Чем быстрее охладить расплав полиэтилена на выходе из экструдера, тем выше будет прозрачность и блеск пленки. Почему так происходит? Дело в том, что при остывании в пленке образуется два вида молекулярных структур — кристаллическая и амфорная. Когда материал охлаждают медленно, то макромолекулы полимера успеют сформироваться в кристаллы, и экструдированная пленка будет мутной и неэластичной, но прочной. При быстром охлаждении кристаллы не успевают соединиться и пространство между ними заполняют амфорные связи, придающие пленке прозрачность, хорошую эластичность и гибкость.
Метод плоскощелевой экструзии.
Отверстие в фильере плоскощелевого экструдера протачивают в виде тончайшей щели. Пленка из формовочной головки выходит в виде непрерывного полотна определенной толщины и ширины.
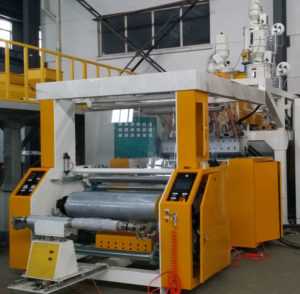
Плоскощелевой экструдер для производства стрейч-пленки
Существует два варианта охлаждения пленки полученной плоскощелевым методом:
- Первый, это когда экструзионный полиэтилен сразу же после формования подается на охлаждающий барабан, температура поверхности которого поддерживается на уровне 30…50 0С.
- Второй вариант — пленку пропускают через ванну с проточной водой. Такое шоковое охлаждение позволяет получать блестящий и прозрачный материал, но есть свои нюансы. Когда пленка заходит в воду, она вызывает рябь на ее поверхности, из-за которой на полиэтилене появляются пятна.
После охлаждения и сушки полиэтилен протягивается через натягивающие валы и идет на намотку.
Соэкструзия и коэкструзия.
Соэкструзия — это технология, использующаяся для получения многослойных пленок.
В качестве сырья может использоваться: полиэтилен низкой и высокой плотности, полипропилен, полиамидная пленка и др. полимеры. Гранулят этих пластических масс плавится в разных экструдерах, после чего соединяется и проходит через одну формовочную фильеру (головку). Для прочного склеивания нужно, чтобы молекулярная сетка полимеров была похожа по структуре. Но если нужно связать барьерный слой, например, EVOH и линейный полиэтилен, то потребуется специальные вяжущие сополимеры.
Соэкструзионные многослойные пленки используются для вакуумирования продуктов, как транспортная упаковка, с/х пленка (для мульчирования, пленка с эффектом антифог), упаковка фармацевтических препаратов.
По похожей технологии, которая получила название коэкструзия, изготавливают панели сайдинга и профиль ПВХ. Поливинилхлорид — основа профиля, занимает около 80% толщины панели, оставшиеся 20% — акрил. Как и в случае соэкструзии, используется работа двух коэкструдеров, где отдельно плавят ПВХ и акрил. Соединяются эти расплавы в щелевой филере, откуда выходят уже готовым спаянным изделием.
Коронарная обработка пленки после экструзии
Химическая инертность и малая поверхностная энергия пленки делают ее невосприимчивой к типографской или любой другой краске. Нанесение покрытия на поверхность полиэтилена станет возможным, если его поверхностная энергия будет хотя бы на 10 дин/см выше энергии наносимой краски. В ином случае краска будет просто собираться в капли. «Подзарядить» пленку можно коронированием. Каждая экструзивная линия оборудована активатором обработки коронным разрядом, который состоит из: генератора, трансформатора и электродов. При пропадании пленки в область электромагнитного поля растет ее поверхностная энергия и повреждается верхний слой макромолекул (микротравление).
Применение технологии экструзии
- Химическая промышленность. Почти все термопласты и их композиции могут перерабатываться экструзией в готовые изделия (пленки, трубы, оболочки изоляции, сайдинг, листы).
- Производство комбикорма. Измельченное сырье для производства комбикорма поступает в экструдер, где подвергается уплотнению, сжатию и температурной обработке при температуре до 200 0С. Этот способ переработки повышает питательность и усвояемость корма, сохраняет в нем витамины и препятствует размножению микроорганизмов.
- Брикетирование твердого биотоплива. Переработка биомассы (торфа, угольной пыли, шелухи подсолнечника, отходов сахарного производства, соломы сои, щепы) и прессование ее в гранулы или брикеты производится на экструдерах;
- Пищевая промышленность. Макароны, кукурузные палочки и хлопья, жевательная резинка и чипсы, соевые продукты— все эти продукты изготавливают с помощью пищевой экструзии.
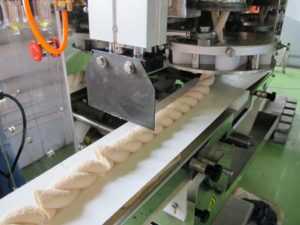
Экструзия теста, экструдер для теста
Развитие экструзионного производства сейчас идет сейчас по трем направлениям. Это: усовершенствование существующего оборудования, применение новых композиций полимеров, совершенствование автоматизированных систем управления. Последнее направление представляется наиболее актуальным — уже сейчас в России появились установки оборудованные АСУ на основе микропроцессора. Они позволяют автоматически контролировать не только работу экструдера, но и системы подготовки сырья, калибровки и обрезки готовых изделий.
oplenke.ru
Экструзия (технологический процесс) – это… Что такое Экструзия (технологический процесс)?
У этого термина существуют и другие значения, см. Экструзия. Пищевой экструдер Shtak-72 Экструдер в линии по производству пластикового плинтуса Алюминиевые детали, полученные методом экструзииЭкстру́зия (от позднелат. extrusio — выталкивание) — технология получения изделий путем продавливания расплава материала через формующее отверстие. Обычно используется в производстве полимерных (резиновых смесей, пластмасс, крахмалсодержащих и белоксодержащих смесей), ферритовых изделий (сердечники), а также в пищевой промышленности (макароны, лапша и тп.), путем продавливания расплава материала через формующее отверстие экструдера.
Экструзия представляет собой непрерывный технологический процесс, заключающийся в продавливании материала, обладающего высокой вязкостью в жидком состоянии, через формующий инструмент (экструзионную головку, фильеру), с целью получения изделия с поперечным сечением нужной формы. В промышленности переработки полимеров методом экструзии изготавливают различные погонажные изделия, такие, как трубы, листы, плёнки, оболочки кабелей, элементы оптических систем светильников- рассеиватели и т. д. Основным технологическим оборудованием для переработки полимеров в изделия методом экструзии являются одночервячные, многочервячные, поршневые и дисковые экструдеры.
Экструдер — машина для формования пластичных материалов, путем придания им формы, при помощи продавливания (экструзии) через профилирующий инструмент (экструзионную головку).
Экструдер состоит из: корпуса с нагревательными элементами; рабочего органа (шнека (винт Архимеда), диска, поршня), размещённого в корпусе; узла загрузки перерабатываемого материала; силового привода; системы задания и поддержания температурного режима, других контрольно-измерительных и регулирующих устройств. По типу основного рабочего органа (органов) экструдеры подразделяют на одно-, двух- или многошнековые (червячные), дисковые, поршневые (плунжерные) и др. Двухшнековые экструдеры в зависимости от конфигурации шнеков могут быть параллельными или коническими. В зависимости от направления вращения — с сонаправленным или противонаправленным вращением шнеков.
Виды экструзии
- Холодная синяя экструзия — возможны только механические изменения в материале вследствие медленного его перемещения под давлением и формованием этого продукта с образованием заданных форм.
- Теплая экструзия — сухие компоненты сырья смешиваются с определенным количеством воды и подают в экструдер, где наряду с механическим его подвергают еще и тепловому воздействию. Продукт нагревается извне. Получаемый экструдат отличается небольшой плотностью, незначительным увеличением в объёме, пластичностью, а также ячеистым строением. Иногда экструдату необходимо подсушивание.
- Горячая экструзия — процесс протекает при высоких скоростях и давлениях, значительном переходе механической энергии в тепловую, что приводит к различным по глубине изменениям в качественных показателях материала. Кроме того, может иметь место регулируемый подвод тепла как непосредственно к продукту, так и через наружные стенки экструдера. Массовая доля влаги в сырье при горячей экструзии составляет 10…20 %, а температура превышает 120 °C.
Применение экструзионной технологии
Химическая промышленность
В химической промышленности метод экструзии применяется для нагрева, пластификации, гомогенизации и придания необходимой формы исходному сырью. Химический состав конечного продукта при этом идентичен химическому составу исходного сырья, что позволяет добиваться стабильного качества продукта прибегая при этом к минимальному количеству настроек экструдера, этим объясняется относительная простота машин, работающих в химической промышленности. Методом экструзии в химической промышленности изготавливают различные погонажные изделия, такие как трубы, листы, плёнки, оболочки кабелей, элементы оптических систем светильников — рассеиватели и т. д.
Пищевая промышленность
В пищевой промышленности метод экструзии применяется намного шире. В ходе процесса под действием значительных скоростей сдвига, высоких скоростей и давления, происходит переход механической энергии в тепловую, что приводит к различным по глубине изменениям в качественных показателях перерабатываемого сырья, например денатурация белка, клейстеризация и желатинизация крахмала, а также другие биохимические изменения.
Экструзионные продукты, получаемые на пищевых экструдерах
- пельмени
- кукурузная палочка
- подушечки и трубочки с начинкой
- хрустящие хлебцы и соломка
- фигурные сухие завтраки
- хлопья кукурузные и из других злаков
- быстрозавариваемые каши
- детское питание
- фигурные чипсы
- экструзионные сухарики
- мелкий шарик из риса, кукурузы, гречи, пшеницы, для наполнения и обсыпки шоколадных изделий, мороженого и других кондитерских изделий
- пищевые отруби
- набухающая мука, панировка
- продукты вторичной переработки хлеба
- соевые продукты: соевый текстурат, концентрат (применяются в производстве колбасы, сосисок, котлет и т. д.), кусковые соевые продукты (фарш, гуляш, бифштекс, тушенка и т. д.)
- продукты переработки отходов животноводства
- модифицированный крахмал
- реагент на основе крахмала применяемый в нефте- и газодобыче
- строительные крахмалсодержащие смеси
- основы для клеев
Комбикормовая промышленность
- полножирная соя
- зерновые экструдаты
- корма для кошек, собак, домашних грызунов, крупного рогатого скота
- корма для промысловых и аквариумных рыб
Производство твердого биотоплива
Одним из наиболее популярных методов получения топливных брикетов является использование специальных экструдеров. Процесс предствляет собой прессование шнеком отходов (шелухи подсолнечника, гречихи и т. п.) и мелко измельченных отходов древесины (опилок) под высоким давлением при нагревании от 250 до 350 С°. Получаемые топливные брикеты не включают в себя никаких связующих веществ, кроме одного натурального — лигнина, содержащегося в клетках растительных отходов. Температура, присутствующая при прессовании, способствует оплавлению поверхности брикетов, которая благодаря этому становится более прочной, что немаловажно для транспортировки брикета.
См. также
Ссылки
В этой статье не хватает ссылок на источники информации. Информация должна быть проверяема, иначе она может быть поставлена под сомнение и удалена. Вы можете отредактировать эту статью, добавив ссылки на авторитетные источники. Эта отметка установлена 28 июля 2012. |
dic.academic.ru
метод переработки полиэтилена и пластмасс
Экструзия – это процесс плавления полимера (допустим, полиэтилена), в результате которой он превращается в изделие определенного размера. Общая технология экструзии всегда одна и та же, но некоторые факторы изменяются в зависимости от толщины, которую необходимо получить. После плавки полиэтилен сушится воздухом, и этот процесс тоже считается частью экструзии. Машина, которая выполняет данную работу, называется экструдером. В наше время это самый распространенный метод создания полиэтиленовой пленки.
Описание процесса экструзии
Такая сложная и комплексная процедура не может выполняться без соответствующего оборудования. Для получения качественной пленки необходим надежный и исправно работающий экструдер. Для начала в бункер машины загружаются полиэтиленовые гранулы, а затем включается функция нагрева. Вскоре гранулы плавятся и превращаются в вязкую прозрачную массу. Это и есть основа будущей пленки.
Вязкая масса проходит сквозь узкие отверстия, которые формируют кольцо. Результатом этой операции является «труба» из пленки. Как правило, в экструдерах предусмотрена функция изменения диаметра этой «трубы».
Затем пленка подвергается воздействию сжатого воздуха, после чего меняет форму. Она становится похожей на сильно вытянутый по вертикали баллон. Посреди валков элеватора находится небольшой зазор, в области которого соединяются края «баллона». Как результат, пленка оседает на дно экструдера и представляет собой сплюснутый рукав.
Нередко для изготовления полиэтиленовых пакетов применяются фальцеватели. В результате получается рукав с фальцовкой. Если изготовитель хочет сразу же нарезать пленку, то в конце сушки он применяет специальные ножи.
Особенности экструзии
Метод экструзии почти одинаков для большинства полимеров. Но температура плавки у каждого своя. Производители полиэтиленовой пленки пользуются расчетными номограммами, чтобы точно определять температуру, при которой плавятся те или иные термопласты. Чаще всего для плавки используются:
- полиэтилен;
- полипропилен;
- поливинилхлорид;
- полиформальдегид;
- полистирол.
В отличие от большинства плавящихся веществ, температура плавления полимеров может колебаться в довольно широком диапазоне. Так, полиэтилен плавится при температуре от 100 до 125°С, а различные виды полипропилена могут требовать температуру от 80 до 170°С. Это обуславливается составом полимеров, а также условиями проведения экструзии.
Экструзия полимеров требует от изготовителя пленки высоких профессиональных знаний. К примеру, поликарбонат и полиметилметакрилат – это полимеры с высокой вязкостью, которые при неосторожном превышении температуры могут потерять свои ключевые свойства.
Как известно, изначально полиэтилен существует в виде порошка. Но для того, чтобы загрузить его в экструдер, нужно сначала добиться гранулированной формы. Для этого проводятся следующие операции:
- Литье или прессование (иногда применяются другие методы) для получения цельной массы полимера.
- Плавка с последующим пропусканием через круглые отверстия (диаметр – от 1,5 до 2,5 мм).
- Нарезка полученной толстой нити на небольшие гранулы.
Только после этого полиэтилен можно загружать в экструдер. Аналогичные операции нужно проделывать и с полипропиленом, а также с некоторыми другими полимерами. Практически любая линия экструзии может работать со всеми полимерами, но машины не в силах сами подстраиваться под изменение материала.
Плавление и охлаждение полиэтилена
Экструзия полиэтилена мало отличается от экструзии других полиолефинов, но нужно помнить одну важную вещь. При плавке полиэтилена выделяется намного больше тепла, чем, скажем, при плавке «родственного» полипропилена. Поэтому, если в прошлый раз экструдер работал с полипропиленом, а теперь необходимо экструдировать полиэтилен, то перед началом работы нужно снизить мощность нагревателей. Если пренебречь этим правилом, то пленка будет кристаллизоваться, станет хрупкой и непрозрачной.
Такой же результат – помутнение и хрупкость – ожидает и при неправильном охлаждении. Полиэтилен нужно охлаждать быстро и интенсивно. Если полимер будет слишком долго сохранять свое тепло, то начнется кристаллизация, которая в первую очередь скажется на прозрачности, а потом и на ударопрочности пленки.
Процесс экструзии с помощью кольцевого зазора (именно он был описан в начале статьи) имеет один существенный недостаток. Полученная пленка имеет неравномерную толщину и часто образовывает складки. Чтобы снизить риск этих побочных явлений, была сконструирована специальная головка экструдера. Ее внутренние и наружные стенки одновременно вращаются, минимизируя разброс толщины. Шанс появления складок тоже заметно падает.
Несмотря на этот недостаток, кольцевой зазор – лучший способ экструзии из ныне существующих. Именно он лежит в основе большинства полиэтиленовых изделий, которые используются на производствах, при строительстве и в быту.
Коронаторная обработка пленки после экструзии
Существуют специальные приспособления – коронаторы, которые применяются для обработки наружной поверхности пленочных рукавов. Они обдают пленку коронными разрядами тока. Данная процедура является необходимой, если изготовленная пленка будет подвергаться флексопечати.
Структура любого полимера – не волокнистая, поэтому краска будет легко держаться на на пленке и без дополнительной обработки (клейка, стимуляция и т.д.). Но использование коронаторов обязательно, ведь без них краска будет слезать с пленки в течение нескольких секунд. Краска, какой бы она ни была, превратится в каплю и будет спокойно передвигаться по полимерной пленке. Коронные разряды тока обеспечивают для пленки и краски валентную связь, и изначальная форма сохраняется на долгое время.
Дефекты пленки и их устранение
Такой сложный процесс, как экструзия пластмасс и полимеров, нечасто может обойтись без погрешностей. В большинстве случаев возникают недочеты, которые необходимо устранить. Поэтому мы рассмотрим основные погрешности при экструзии полиэтилена, а также опишем способы их устранения:
- Плохая прозрачность пленки. Эта проблема чаще всего решается повышением температуры плавки, а также повышением (или, наоборот, понижением) интенсивности охлаждения. Если ни один из способов не помогает, то остается только сменить марку полиэтилена.
- Посторонние вкрапления. Для решения этой проблемы нужно проверить, правильно ли хранится сырье (гранулированный полиэтилен), а также протестировать его качество.
- Полосы на пленке. Чаще всего они бывают продольными, реже – поперечными или хаотичными. Почти всегда это связано с плохим состоянием головки экструдера. Ее необходимо отполировать и очистить от нагара.
- Потускнение поверхности пленки. Чтобы избавиться от этого неприятного эффекта, нужно снизить температуру плавки, поднять давление во время экструзии, снизить скорость вращения шнека, отполировать головку экструдера.
- Шероховатость поверхности. Для избавления от этой проблемы можно отполировать головку и повысить температуру плавки, а также подсушить полиэтиленовые гранулы. Но это не всегда помогает, и тогда приходится заменять партию полимера.
Отдельного внимания заслуживает проблема разнотолщинности, которая уже была описана выше. Неравномерная толщина может иметь разный характер, и в зависимости от этого варьируется способ устранения проблемы:
- если раздутый рукав полностью асимметричен, то нужно изменить размер зазора по периметру, а также проверить, равномерно ли прогревается головка экструдера;
- если разнотолщинность проявляется только поперек рукава, то нужно также изменить размер зазора и отрегулировать температуру плавки;
- если разнотолщинность проявляется только вдоль рукава, то нужно изменить скорость его отвода, отрегулировать скорость вращения шнека, параметры температуры и охлаждения.
Заключение
Итак, экструзия – это процесс, при котором полиэтилен из гранулированного материала превращается в прозрачную пленку. Данная процедура является комплексной и требует не только специального оборудования, но и профессиональных навыков человека, который будет работать с экструдером. Тем не менее, при создании изделий из полимеров без экструзии обойтись невозможно.
propolyethylene.ru
Что такое экструзия? – ЭКО-процессинг
Экструзия – это процесс плавления полимера (допустим, полиэтилена), в результате которой он превращается в изделие определенного размера. Общая технология экструзии всегда одна и та же, но некоторые факторы изменяются в зависимости от толщины, которую необходимо получить. После плавки полиэтилен сушится воздухом, и этот процесс тоже считается частью экструзии. Машина, которая выполняет данную работу, называется экструдером. В наше время это самый распространенный метод создания полиэтиленовой пленки.
Такая сложная и комплексная процедура не может выполняться без соответствующего оборудования. Для получения качественной пленки необходим надежный и исправно работающий экструдер. Для начала в бункер машины загружаются полиэтиленовые гранулы, а затем включается функция нагрева. Вскоре гранулы плавятся и превращаются в вязкую прозрачную массу. Это и есть основа будущей пленки.
Вязкая масса проходит сквозь узкие отверстия, которые формируют кольцо. Результатом этой операции является «труба» из пленки. Как правило, в экструдерах предусмотрена функция изменения диаметра этой «трубы».
Затем пленка подвергается воздействию сжатого воздуха, после чего меняет форму. Она становится похожей на сильно вытянутый по вертикали баллон. Посреди валков элеватора находится небольшой зазор, в области которого соединяются края «баллона». Как результат, пленка оседает на дно экструдера и представляет собой сплюснутый рукав.
Нередко для изготовления полиэтиленовых пакетов применяются фальцеватели. В результате получается рукав с фальцовкой. Если изготовитель хочет сразу же нарезать пленку, то в конце сушки он применяет специальные ножи.
Метод экструзии почти одинаков для большинства полимеров. Но температура плавки у каждого своя. Производители полиэтиленовой пленки пользуются расчетными номограммами, чтобы точно определять температуру, при которой плавятся те или иные термопласты. Чаще всего для плавки используются:
- полиэтилен;
- полипропилен;
- поливинилхлорид;
- полиформальдегид;
- полистирол.
В отличие от большинства плавящихся веществ, температура плавления полимеров может колебаться в довольно широком диапазоне. Так, полиэтилен плавится при температуре от 100 до 125°С, а различные виды полипропилена могут требовать температуру от 80 до 170°С. Это обуславливается составом полимеров, а также условиями проведения экструзии.
Экструзия полимеров требует от изготовителя пленки высоких профессиональных знаний. К примеру, поликарбонат и полиметилметакрилат – это полимеры с высокой вязкостью, которые при неосторожном превышении температуры могут потерять свои ключевые свойства.
Как известно, изначально полиэтилен существует в виде порошка. Но для того, чтобы загрузить его в экструдер, нужно сначала добиться гранулированной формы. Для этого проводятся следующие операции:
- Литье или прессование (иногда применяются другие методы) для получения цельной массы полимера.
- Плавка с последующим пропусканием через круглые отверстия (диаметр – от 1,5 до 2,5 мм).
- Нарезка полученной толстой нити на небольшие гранулы.
Только после этого полиэтилен можно загружать в экструдер. Аналогичные операции нужно проделывать и с полипропиленом, а также с некоторыми другими полимерами. Практически любая линия экструзии может работать со всеми полимерами, но машины не в силах сами подстраиваться под изменение материала.
Экструзия полиэтилена мало отличается от экструзии других полиолефинов, но нужно помнить одну важную вещь. При плавке полиэтилена выделяется намного больше тепла, чем, скажем, при плавке «родственного» полипропилена. Поэтому, если в прошлый раз экструдер работал с полипропиленом, а теперь необходимо экструдировать полиэтилен, то перед началом работы нужно снизить мощность нагревателей. Если пренебречь этим правилом, то пленка будет кристаллизоваться, станет хрупкой и непрозрачной.
Такой же результат – помутнение и хрупкость – ожидает и при неправильном охлаждении. Полиэтилен нужно охлаждать быстро и интенсивно. Если полимер будет слишком долго сохранять свое тепло, то начнется кристаллизация, которая в первую очередь скажется на прозрачности, а потом и на ударопрочности пленки.
Процесс экструзии с помощью кольцевого зазора (именно он был описан в начале статьи) имеет один существенный недостаток. Полученная пленка имеет неравномерную толщину и часто образовывает складки. Чтобы снизить риск этих побочных явлений, была сконструирована специальная головка экструдера. Ее внутренние и наружные стенки одновременно вращаются, минимизируя разброс толщины. Шанс появления складок тоже заметно падает.
Несмотря на этот недостаток, кольцевой зазор – лучший способ экструзии из ныне существующих. Именно он лежит в основе большинства полиэтиленовых изделий, которые используются на производствах, при строительстве и в быту.
Экструзия – это процесс, при котором полиэтилен из гранулированного материала превращается в прозрачную пленку. Данная процедура является комплексной и требует не только специального оборудования, но и профессиональных навыков человека, который будет работать с экструдером. Тем не менее, при создании изделий из полимеров без экструзии обойтись невозможно.
www.ekoprozess.ru
Экструдированный – это… Что такое Экструдированный?
- Экструдированный
То же что экструзионный (см. Экструзионный). Определение «экструдированный» обычно применяется к пенополистеролу. Технология производства экструдированного пенополистерола состоит из следующих этапов: приготовление сухой вспенивающейся композиции, состоящей из полистирола и технологических добавок; ее дозирование в зону загрузки экструдера; непрерывная переработка в экструдере; выдавливание и вспенивание материала на выходе из экструзионной головки; калибрование и термостатирование плиты; охлаждение и стабилизация размеров плиты; отрезка плиты по длине на резательном устройстве. Плиты из экструдированного пенополистирола обладают одним из самых низких коэффициентов теплопроводности среди широко применяемых в строительстве утеплителей. Кроме того, преимуществами плит из экструдированного пенополистирола являются высокая механическая прочность и практически нулевое водопоглощение, что позволяет эффективно использовать их для утепления фундаментов, подвалов, стен, плоских кровель, устройства теплых полов (в том числе промышленных), теплоизоляции авто- и железнодорожного полотна и т. д.
Словарь строителя. 2008.
- Экстерьер
- Экструзионный
Смотреть что такое “Экструдированный” в других словарях:
экструдированный — прил., кол во синонимов: 1 • экструзионный (1) Словарь синонимов ASIS. В.Н. Тришин. 2013 … Словарь синонимов
Экструдированный — – обычно применяется к пенополистиролу. Технология производства экструдированного пенополистирола состоит из следующих этапов: – приготовление сухой вспенивающейся композиции, состоящей из полистирола и технологических добавок;… … Энциклопедия терминов, определений и пояснений строительных материалов
экструдированный компаунд — — [Я.Н.Лугинский, М.С.Фези Жилинская, Ю.С.Кабиров. Англо русский словарь по электротехнике и электроэнергетике, Москва, 1999 г.] Тематики электротехника, основные понятия EN extruded compound … Справочник технического переводчика
экструдированный мясной [мясосодержащий] продукт — Мясной [мясосодержащий] продукт, изготовленный методом экструзии из мясных или мясных и немясных [мясных и немясных] ингредиентов. [ГОСТ Р 52427 2005] Тематики производство мясных продуктов … Справочник технического переводчика
Экструдированный утеплитель — получают путем смешивания гранул полистирола при повышенных температурах с последующим введением вспенивающего агента и выдавливанием из экструдера. Процесс экструдирования позволяет получить утеплитель с равномерной структурой, состоящей из… … Энциклопедия терминов, определений и пояснений строительных материалов
Экструдированный пенополистирол — Экструзионный пенополистирол (XPS, ЭПС, экструдированный пенополистирол) синтетический теплоизоляционный материал, впервые созданный в США в начале XX века. Экструзионный пенополистирол имеет широкую сферу применения: теплоизоляция фундаментов и… … Википедия
экструдированный пенополистирол — 3.3.2 экструдированный пенополистирол: Жесткий теплоизоляционный материал с закрытой ячеистой структурой, полученный методом экструзии вспенивающегося полистирола или одного из его сополимеров с образованием или без образования пленки на его… … Словарь-справочник терминов нормативно-технической документации
Мясной (мясосодержащий) продукт экструдированный — Экструдированный мясной [мясосодержащий] продукт: мясной [мясосодержащий] продукт, изготовленный методом экструзии из мясных или мясных и немясных [мясных и немясных] ингредиентов… Источник: ПРОМЫШЛЕННОСТЬ МЯСНАЯ. ПРОДУКТЫ ПИЩЕВЫЕ. ТЕРМИНЫ И… … Официальная терминология
геомат пластмассовый экструдированный — 2.1.39 геомат пластмассовый экструдированный: Геомат из полимерных мононитей и других синтетических элементов, скрепленных термическим или химическим способом. Источник … Словарь-справочник терминов нормативно-технической документации
Геомат пластмассовый экструдированный — Геомат пластмассовый экструдированный; ГМА ГПЛ Э (geomat extruded; GMA E): проницаемая пространственная конструкция из полимерных мононитей и других синтетических элементов, скрепленных термическим, химическим способами… Источник: Распоряжение… … Официальная терминология
builder.academic.ru
Экструзия. Общее представление об экструзии — «Эксимпак-Оборудование»
19.09.2013
Рейтинг: 4.5/5 из 30Из истории экструзии
Экструзионные установки для переработки полимеров появились в 30-е годы XX века. Первый термопласт появился в Германии около 1935 года (инженер – Пуаль Трестер). До этого момента экструдеры служили для переработки каучука (шнековые или поршневые экструдеры с паровым подогревом и с малым соотношением длина/диаметр). После 1935 года появились экструдеры большей длины, оснащенные электронагревателями. Примерно в это же время были сформулированы основные принципы экструзии термопластов итальянцем Р. Коломбо, который совместно с К. Паскуэтти разрабатывал машину для смешения ацетата целлюлозы. С 1950-х годов внимание к устройству экструдеров и совершенствованию процесса экструзии усилилось: внедрялись новые технологии, проводились исследования. В последнее время было разработано новое поколение машин с более эффективным смешением и диспергированием полимеров.
Описание технологического процесса экструзии пленки
Экструзия – метод формования в экструдере для пленки изделий или полуфабрикатов неограниченной длины продавливанием расплава полимера через формующую головку с каналами необходимого профиля.
Представим схему оборудования для производства рукавной пленки:
Основными элементами экструдера являются следующие агрегаты:
- бункер для загрузки сырья,
- шнек и цилиндр для расплава сырья,
- фильтр с сеткой для очистки материала,
- формующая головка с воздушным кольцом для формирования материала,
- устройство вытяжки материала,
- устройство намотки готового материала,
- блок управления экструзионной установкой.
Процесс внутри шнековой пары
Термопластичный полимер в процессе экструзии последовательно переходит сначала из твердого состояния (в виде гранул) в расплав, а затем вновь в твердое состояние (в виде пленки) после выхода из формующей оснастки.
Структуру твердого полимера составляют длинные молекулы (макромолекулы), свернутые в клубок или переплетенные между собой, формирующие высокоупорядоченные кристаллические или неупорядоченные аморфные образования. Отдельные фрагменты полимерных цепей находятся в непрерывном движении под действием тепловой энергии.
При нагреве, с возрастанием температуры, увеличивается подвижность молекул, разрушаются кристаллические образования, молекулы принимают клубкообразную или спиральную форму и начинают смещаться относительно друг друга. Полимер из твердого состояния переходит в расплав. У полимеров кристаллической структуры этот переход отвечает узкому интервалу температур, а у аморфных – широкому. В интервале между температурами плавления и разложения полимер находится в вязкотекучем состоянии. Именно в состоянии расплава материал экструдируется. Реальный интервал температур переработки несколько уже, чем интервал между температурой плавления и разложения, так как, с одной стороны, необходимо иметь достаточно подвижный расплав, а с другой стороны, необходимо избежать разложения полимера при экструзии.
Технологический процесс экструзии полимерного сырья состоит из последовательного проталкивания материала вращающимся шнеком по зонам:
- питания (I),
- пластикации и плавления (II),
- дозирования расплава (III),
- продвижения расплава в каналах формующей головки.
Схема одношнекового экструдера
Основные типы шнеков
Зоны технологического процесса экструзии
Деление шнека на зоны I-III осуществляется по технологическому признаку и указывает на то, какую операцию в основном выполняет данный участок шнека. Разделение шнека на зоны условно, поскольку в зависимости от природы перерабатываемого полимера, температурно-скоростного режима процесса и других факторов, начало и окончание определенных операций могут смещаться вдоль шнека, захватывая различные зоны или переходя из одного участка в другой.
Цилиндр также имеет определенные длины зон обогрева. Длина этих зон определяется расположением нагревателей на его поверхности и их температурой. Границы зон шнека I-III и зон обогрева цилиндра могут не совпадать. Для обеспечения успешного перемещения материала большое значение имеют условия продвижения твердого материала из загрузочного бункера и заполнение межвиткового пространства, находящегося под воронкой бункера.
Питание шнека зависит от формы частиц сырья и их плотности. Гранулы, полученные резкой заготовки на горячей решетке гранулятора, не имеют острых углов и ребер, что способствует их лучшей сыпучести. Гранулы, полученные холодной рубкой прутка-заготовки, имеют острые углы, плоское сечение среза, что способствует их сцеплению и, как следствие, худшей сыпучести. При длительной работе экструдера возможен перегрев цилиндра под воронкой бункера и самого бункера. В этом случае гранулы начнут слипаться и прекратится их подача на шнек. Для предотвращения перегрева этой части цилиндра в нем могут быть сделаны полости для циркуляции охлаждающей воды (Источник: инструкция пользователя. Лебедев П.Г., Лебедева Т.М., Митина Л.Н.)
Компания «Эксимпак-Оборудование» уже более 20 лет занимается поставкой экструзионной техники на отечественный рынок и рынки стран СНГ – от простых ПВД/ПНД однослойных моделей производства рукавной пленки шириной до 700 мм (например, модель YF-MHB-45) до многослойных A-B-C экструдеров производственной мощностью до 300 кг продукции в час. Покупатели могут не сомневаться в “тотальной” компетентности наших технологов относительно всего, что происходит внутри и снаружи шнека; равно как и надежность наших машин также не подлежит сомнению.
www.eximpack.com