сырье и технология производства, фракции и цены
ОГреческое слово «Керамос» (глина) прослеживается во многих названиях современных стройматериалов – керамзитовый гравий, щебень или песок. Керамзит – это продукт, получаемый при обжиге глины легкоплавких сортов. Рабочий процесс превращает исходное сырье в легкие, пористые зерна кубической или овальной формы. Характеризуется огнестойкостью, не пропускает воду, имеет низкую теплопроводность. Основные свойства – высокая прочность, малый вес, устойчивость к химическим воздействиям, антисептические качества. Важной особенностью является экологическая безвредность при неограниченном сроке использования.
Оглавление:
- Из чего делают керамзит?
- Технология изготовления
- Цена за мешок и куб
Характеристики обработки глины регулируют получение разного веса и насыпной плотности в отдельно взятом объеме. В зависимости от способа изготовления и режима воздействия можно получить керамзитовый щебень, крупный гравий или песок. Этим обуславливается использование материала в легких бетонах, как засыпка для звуко и теплоизоляции в конструктивах зданий, сооружений, составляющая строительных растворов. Также керамзит широко используется, имея положительные характеристики, в грунтовом растениеводстве. Со стоимостью мешка керамзита вы можете ознакомиться, пройдя по ссылке.
Производственное сырье
Из чего же делают керамзит? Промышленное сырье — это легкоплавкие осадочные глинистые породы, содержание кварца в которых менее 30 %. Реже используется камнеподобный материал. Во время производства для образования воздушных пустот (вспучивания) применяют определенные добавки, имеющие оксиды железа, солярка, мазут.
Основным критерием выбора материала для керамзита является способность к вспучиванию при 1000 – 1250 градусах. Во время процесса продукт приобретает ячеистую структуру с равномерным распределением закрытых пор. Используемое в производстве сырье должно быть тонкодисперсным, низкой запесоченности, с интервалом размягчения в пределах 50 градусов. Наилучшими считаются монтмориллонитовые и гидрослюдистые. Улучшение качества слабо вспучиваемых глин делают введением в состав шихты добавок, таких как:
- молотый каменный уголь;
- мазут;
- соляровое масло;
- сульфитно-спиртовая барда;
- пиритные огарки;
- пылевидные железные руды.
Основной состав шихты включает в себя:
- оксид алюминия 12%;
- оксид и окись железа 10%;
- кремнезем 70%;
- кварц 30%;
- органика 1-2%.
Степень качества, пригодности глиняного сырья определяется и контролируется лабораторными исследованиями на производстве.
Методика изготовления
Технология изготовления керамзита состоит из доставки материала и его предварительной подготовки, термической обработки, охлаждения конечной продукции, сортировки, перевозки на склад хранения. Существует четыре вида методик: сухая, мокрая, пластическая, порошково-пластическая. Качество и характеристики сырья диктуют выбор определенного способа производства.
1. Для использования камнебитной глины более приемлем сухой тип. Масса измельчается на мелкие фракции, а затем подвергается обжигу.
2. Шликерный (мокрый) метод требует разведения глины водой в специальных емкостях до 50% влажности. Из накопительных бассейнов масса отправляется на обжиг. В печи устроена завеса из цепей, на которых шликер просушивается и разрушается на мелкие фрагменты.
3. Чаще всего используется пластический способ. Он основан на увлажнении сырьевой массы и переработке ее в цилиндрические гранулы. Затем полуфабрикат просушивается в сушильной емкости и подается в печь.
4. Последняя технология предусматривает измельчение сухого материала в порошок. После добавления воды из получившейся массы формуют гранулы. Заключительная стадия процесса такая же, как при пластическом способе обработки.
Основное оборудование для производства керамзита включает в себя формовочные аппараты, конвейеры, агрегаты сушки сырья, печи для обжига, холодильные установки. Глиняный материал поступает сверху в наклонный барабан с расположенной внизу форсункой. Гранулы подвергаются тепловому удару. В потоке встречного горячего газа они постепенно опускаются вниз. Под действием жара глина закипает, вспучивается, оплавляется наружный слой. Длительность цикла – примерно 45′.
Следующая операция – охлаждение. Во избежание растрескивания готовых гранул делается медленное понижение температуры. Благодаря поступающему воздуху, действие начинается в печке, продолжается в аэрожелобах и заканчивается барабанными холодильниками. Остывший керамзит отправляют на склад. Процесс изготовления этим завершается.
Стоимость готового продукта
Цена зависит от многих факторов: стоимость сырья, материалов, цена используемых энергоносителей. Кроме того, стоит не забывать про транспортные расходы, критерии оптовых и розничных продаж.
Купить керамзит можно по следующим ценам:
Фракция | Россыпью, цена за м3/руб | В мешках (0,03 м3), цена за мешок/рубли |
0-5 | 2200 | от 70 |
5-10 | 1900 | 60 |
10-20 | 1300 | 42 (при объеме 1000 мешков) |
20-40 | 1300 | 42 (при объеме 1000 мешков) |
Керамзит среднего размера (фракции 10-20 мм) наиболее востребован в производстве строительных работ.
stroitel-list.ru
какое сырье используется, цена за м3 и мешок
Керамзит представляет собой пористый сыпучий материал в виде гранул овальной или округлой формы. В зависимости от режима обработки сырья получаются разные фракции – от песка до гравия. Используют как заполнитель в производстве легких бетонов, а также в виде теплоизолирующей засыпки при строительстве зданий.
Оглавление:
- Из чего производится керамзит?
- Технология изготовления и оборудование
- Виды и характеристики
- Расценки за куб и мешок
Из чего же делают керамзит?
В качестве промышленного сырья используют глинистые легкоплавкие породы (кремнезем) с содержанием кварца не менее 30 %. Их добывают в карьерах открытым способом. Во время разработки не выделяют отдельные пласты, а снимают глину по всей высоте залежи. Для добычи мягкого сырья используют экскаваторы. В случае камнеподобных пород (аргиллиты, глинистые сланцы) проводятся буровзрывные работы. Чтобы непрерывно обеспечивать производство сырьем, делают вместительные морозостойкие хранилища.
Главное требование к глинистым породам – способность к вспучиванию при сверхвысоких температурах. Во время обжига керамзит приобретает пористую структуру с равномерно распределенными воздушными ячейками. Поэтому шихта должна быть тонкодисперсной с низким содержанием песка. Для улучшения качества и усиления вспучиваемости в нее вводят некоторые добавки: угольный порошок, солярку, мазут, железные и алюминиевые руды.
Технология изготовления керамзита
Подготовленное глиняное сырье обжигают в специальных печах при постоянном вращении. В процессе производства температуру резко повышают до 1300 градусов и удерживают в течение получаса. В результате термического удара глина сильно вспучивается и превращается в пористую стекловидную массу. Быстрое оплавление наружной поверхности образует прочную герметичную оболочку.
Методики изготовления:
1. Сухой – простая переработка, применяемая для камнебитной глины с однородной структурой. Перед отправкой в печь делается дробление. Достоинства сухого метода: минимальные затраты и низкая энергоемкость.
2. Шликерный (мокрый) – перед обжигом делают шликер – разводят сырье водой, добиваясь 50% влажности. Во вращающейся печи масса разбивается на гранулы и подсушивается. Мокрый способ помогает хорошо очистить глинистую породу от твердых включений. Шликер имеет однородную консистенцию, в него легко вводить присадки. Недостатком является большой расход топлива.
3. Пластический – методика основана на увлажнении рыхлого сырья с последующим формированием цилиндрических гранул. Им делают округлые формы, просушивают и отправляют в печь на обжиг. Пластический способ считается сложным в исполнении, энергозатратным и дорогостоящим, зато благодаря структурным изменениям массы получается керамзит с высокими качественными характеристиками.
4. Порошково-пластический – сначала из сухого сырья делают порошок, который разводят водой и получают пластичную массу. Затем из нее формируют одинаковые по размеру гранулы. Недостатки: измельчение глины и сушка влекут за собой дополнительные расходы по производству.
Способ изготовления определяют на основе качества и характеристик исходного сырья.
Оборудование для производства керамзита
Технологическая линия включает в себя агрегаты для рыхления, перемешивания, формования и сушки, печи, конвейерные ленты, бункеры, гравийные сортировщики, холодильные установки. Предварительная обработка заключается в измельчении. Это делается при помощи специальной дробилки.
Печь для обжига представляет собой стальной барабан, установленный под небольшим наклоном. Диаметр вращающейся емкости – 2-5 м, длина достигает 70 м. Раздробленное сырье засыпают в печь сверху. Снизу находится топка с форсункой. Полный цикл порообразования занимает 30-45 минут с момента разогрева.
Для изготовления керамзита из низкокачественного сырья используют печи с двумя барабанами. Они разделены между собой и вращаются с разной скоростью.
Характеристики керамзита
Готовые гранулы керамзита имеют пористую структуру и прочную спекшуюся оболочку. Они обладают малым весом, огнестойкостью, газо- и водонепроницаемостью.
Ячеистый материал классифицируют по типоразмеру, форме зерен, прочности и насыпной плотности.
- Гравий – окатыши овальных форм фракцией от 5 до 40 мм и выше. Цвет снаружи – буро-коричневый, на изломе – черный. Керамзитовый гравий широко применяется в строительной отрасли. Наиболее востребована фракция – 10-20.
- Щебень – результат дробления крупных конгломератов керамзита. Форма неправильная с острыми угловатыми краями, фракция – 5-40. Применяется при производстве бетона в качестве добавочного компонента.
- Песок (отсев) – Мелкие частицы фракции 0-5. Представляют собой побочный продукт обжига или дробления керамзита. Используются в качестве наполнителя при изготовлении строительных блоков.
Стоимость керамзита
Фракция, мм | Цена, руб/куб | Цена, руб/мешок* |
0-5 | 1800-2200 | 70-140 |
5-10 | 1700-1900 | 60-120 |
10-20 | 1000-1300 | 40-95 |
20-40 | 1000-1300 | 40-85 |
Тем, кто планирует купить фасованный керамзит, следует помнить, что в одном мешке содержится 0,03-0,005 м3.
stroitel-lab.ruСостав керамзита и его свойства. Какой керамзит лучше использовать
Керамзит – недорогой, экологичный материал с отличными показателями звуко- и теплоизоляции и малым весом.
Он используется не только в качестве утеплителя стени перекрытий зданий и наполнителя для легких бетонов, но и при строительстве дорог, мелиоративных работах на водонасыщенных грунтах, а также в ландшафтном дизайне в для оформления дорожек, зон отдыха, декорирования клумб.
Состав керамзита
Керамзит, в состав которого входит глина или глиняные сланцы, изготавливается путем обжига исходного сырья в специальных печах-барабанах, где при нагреве до 1000-1300 градусов происходит вспучивание глины и переход в пиропластическое состояние.
В зависимости от качества глины, температуры и продолжительности обжига и других технологических особенностей производства получают различные технические характеристики керамзита. Наиболее значимые из них – размер зерен, насыпная плотность и объемный вес.
Размер зерен может существенно отличаться: керамзитовый песок имеет гранулы размером до 5 мм, гравий и щебень – от 5 до 40 мм с подразделением на фракции 5-10 мм, 10-20 мм, 20-40 мм.
Марки керамзита
Разделение керамзита на марки производится на основании его насыпной плотности, на 10 марок, от 250 до 800 (марка 250 свидетельствует о том, что насыпная плотность материала составляет до 250 кг/м3, марка 500 – до 500 кг/м3, марка – 800 – до 800 кг/м3).
Какой керамзит лучше?
Это зависит от области его применения, насыпная плотность практически не имеет значения, если он используется в качестве утеплителя или в ландшафтном дизайне, но важна при производстве керамзитобетона, сооружении фундамента. Следует учитывать, что с увеличением размера фракций насыпная плотность снижается.
Также важна и однородность фракций: коэффициента соотношения наибольшей и наименьшей гранул должен быть менее 1,5, при его увеличении до 2 прочность материала снижается на 27%. При выборе материала следует обратить внимание и на форму гранул, предпочтительней, чтобы они были шарообразными, а не угловатыми, но керамзитный щебень чаще всего имеет большое количество граней.
Объемный вес керамзита зависит, прежде всего, от величины зерна. Вес кубометра гранул, величина которых 20-40 мм, составляет около 350 кг, а кубометр керамзитного песка с диаметром фракции 0-5 миллиметров весит около 600 кг. Но на данную характеристику влияет и исходное сырье, используемое при производстве – глины бывают легкими и тяжелыми.
Этот показатель имеет существенное значение, если предстоит перевозка материала на значительные расстояния, а также при использовании его для утепления крыш.
Также могут иметь значение и такие свойства керамзита как водопоглощение и морозоустойчивость. Показатель водопоглощения не должен превышать 20%, но производится керамзит, у которого его значение значительно ниже – 8%.
Морозоустойчивость измеряется в циклах, ее минимальное значение 25, то есть керамзит должен, не меняя своих технических характеристик, выдерживать не менее 25 циклов заморозки – быстрого оттаивания.
Видео:
Loading …Понравилась статья? Нажимай |
rmnt.net
Керамзит – состав и технология производства, свойства, виды, область применения
Керамзит – легкий гранулированный материал с пористой структурой, продукт ускоренного обжига при сверхвысоких температурах глины и глинистых сланцев. Представляет собой керамические шарики с плотной спекшейся оболочкой темно-бурого цвета, почти черного на изломе.
Технология получения керамзита
Сырьем для его производства являются определенные сорта глины – легкоплавкие, имеющие в составе до 30 % кварца, вспучивающиеся – с повышенным содержанием окислов железа (не менее 6 %) и органических веществ. При необходимости для усиления вспучивания проводят обогащение сырца мазутом или соляровым маслом.
Наиболее распространены два варианта производства керамзитовой продукции.
Пластичный (мокрый) способ
Подготовленная природная глина с влажностью не более 30 % проходит два этапа помола специальными зубчатыми вальцами – грубый и тонкий. В результате получают первичные гранулы диаметром в 5–10 мм, которые подают в сушильный барабан. Здесь полуфабрикат подсушивается и проходит окончательную обкатку, приобретая овальную форму. Только после этого начинается обжиг в печи с помощью высоких температур (800–1350⁰ С) и при постоянном вращении. Спекшиеся керамические шарики, увеличившиеся после вспучивания в диаметре, направляют во вращающийся холодильный агрегат. Последний этап – рассев керамзита по фракциям.
Сухой способ
В случае получения керамзита из плотного материала – каменистых глинистых пород, сланца – используют сухую технологию. Исходное сырье размельчают на специальном дробильном оборудовании до зерен размером в 1–20 мм. Сырец обжигают в барабанных печах, охлаждают и разделяют по фракциям. При таком способе производства отсутствует этап формовки зерна, поэтому продукт имеет кубические угловатые очертания.

Изготовление керамзита в промышленных объемах
Технические и эксплуатационные свойства
Благодаря техническим параметрам и рабочим показателям, керамзит выгодно выделяется в категории инертных материалов.
- Обладает оптимальным сочетанием прочности и веса. Продукцию М500, М700, М800 используют для изготовления стенового материала, перекрытий, в мостостроении, т. е. там, где особенно важны прочностные характеристики наряду с уменьшением массы конструкций.
- Благодаря пористой структуре, обладает хорошей гигроскопичностью, обеспечивает естественную циркуляцию воздуха.
- Является универсальным утеплителем, который по теплоизоляционным свойствам сравним с натуральной древесиной, а в отдельных случаях и превосходит ее на 10–15 %. Теплопроводность в пределах 0,07– 0,16 Вт/м позволяет избегать до 70 % потерь тепла.
- Пройдя обработку при сверхвысоких температурах, материал полностью огнеустойчив и пожаробезопасен.
- Имеет низкий уровень водопоглощения (не более 25 %), выдерживает до 50 циклов сезонного замораживания.
- Характеризуется минимальным уровнем усадки – коэффициент не более 0,14 мм/м.
- Состоит только из экологически чистых компонентов натурального происхождения.
Классификация
По параметрам и конфигурации зерен различают следующие виды керамзита.
- Керамзитовый щебень. Отличительная черта – зерно произвольной, чаще кубической угловатой формы размером от 5 до 40 мм. Получают сухим способом дробления вспученных глинистых масс.
- Керамзитовый гравий. Имеет сферическую окатанную форму, делится на три фракции (5–10 мм, 10–20 мм, 20–40 мм).
- Керамзитовый песок. Получают путем отсева мелкой фракции – до 5 мм, с самым большим насыпным весом (до 1300 кг/м3).
В зависимости от насыпной плотности керамзит подразделяют на очень легкий (250–300 кг/м3), легкий (до 500 кг/м3), средний (до 700 кг/м3), тяжелый (свыше 700 кг/м3).
Прочность, а, значит, и сферы использования керамзита зависят от насыпного веса. Легкая продукция годится для применения насыпом, тяжелая – в качестве заполнителя в бетоны, стеновые блоки, панели, плиты.
Сферы использования
Этот инертный материал искусственного происхождения востребован в строительной индустрии, сельском хозяйстве, ландшафтной планировке территорий.
Более 60 % производимого продукта уходит на изготовление керамзитобетона, бетонной стяжки, несущих строительных конструкций – стеновых панелей, блоков, межэтажных перекрытий. Для этих целей больше подходит пористый наполнитель мелких фракций (5–20 мм) и песок.
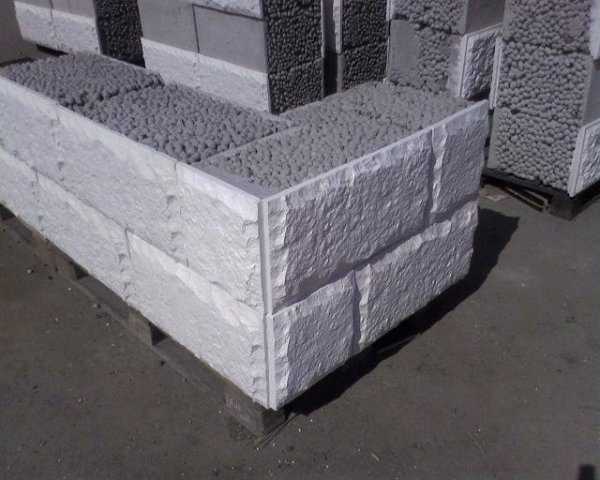
Керамзитобетонные блоки – достойная альтернатива тяжелым бетонам
На теплоизоляционные засыпки расходуется примерно четверть продукции, как правило, более крупного размера. Идеально подходит для утепления насыпом полов, чердаков, отмостки, теплотрасс. В качестве теплоизоляционного заполнителя популярен в каркасном домостроении.
Благодаря высоким дренажным возможностям находит широкое применение в садоводстве – при разбивке газонов как составляющая часть грунта для посадки комнатных растений и субстрат для гидропоники, а также в декоративных целях в ландшафтном проектировании.
taxi-pesok.ru
Из чего делают керамзит
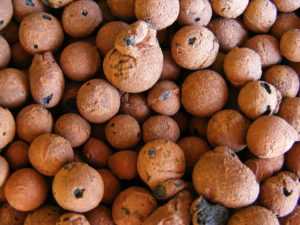
Внешний вид керамзита
В своей жизни многие сталкивались с керамзитом, кто-то использовал его в качестве утеплителя, кто-то в качестве основы грунта в своих террариумах, а кто-то просто видел его в строительных блоках. Из чего же делают керамзит, что его применение так обширно?Керамзит — это лёгкий пористый строительный материал, получаемый путём обжига глины или глинистого сланца. Керамзитовый гравий имеет овальную форму. Керамзитовый щебень отличается лишь тем, что его зёрна имеют в основном кубическую форму с острыми гранями и углами. Производится также в виде песка — керамзитовый песок.
В зависимости от режима обработки глины или сланца можно получить керамзит различным объёмным весом — от 350 до 600 кг/м³ и выше.
Способ изготовления керамзита
Обжиг глины производится в металлических барабанах-печах, диаметром от 2 до 5 метров и длиной до 70 метров. Барабаны — это вращающиеся печи, которые устанавливаются под небольшим углом.
Гранулы керамзитового полуфабриката засыпаются в верхнюю часть печи и под воздействием силы тяжести скатываются к нижней части, где установлена форсунка для сжигания топлива.
Время пребывания гранул в печи около 45 минут.
Иногда используют двухбарабанные печи, где барабаны отделены друг от друга порогом и вращаются с разными скоростями. Подобные печи позволяют использовать менее качественное сырье, хотя на выходе качество керамзитового щебня или гравия не отличается или выше полученного в однобарабанных печах.
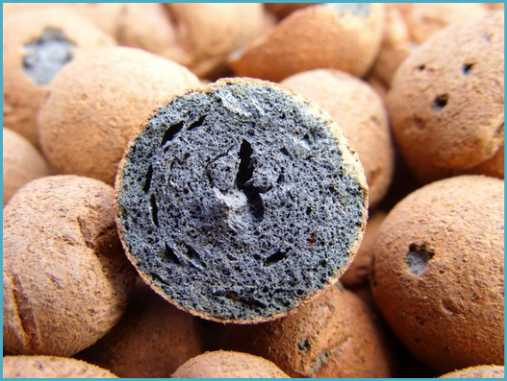
Керамзит в разрезе
Применение керамзита
Керамзит имеет широкое применение, вот основные из них:
- утеплитель в виде засыпки (часто можно встретить на чердаках старых домов),
- при изготовлении керамзитобетона,
- в сельском хозяйстве и гидропонике,
- в домашнем цветоводстве,
- в качестве составной части грунта в террариумах,
- декоративный материал, позволяющий обеспечить теплоизоляцию грунта и газонов,
- дренажный и теплоизоляционный материал для земляных насыпей дорог, прокладка которых производится в водонасыщенных грунтах.
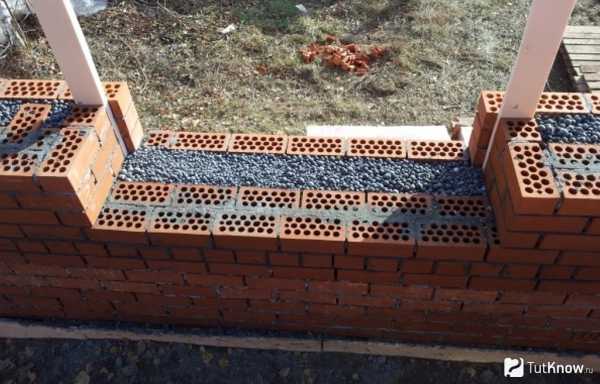
Керамзит в качестве утеплителя между стен
Широкое применение керамзит получил благодаря своим положительным особенностям. Керамзит имеет отличные теплоизоляционные свойства, керамзит — это один из самых экологически чистых материалов, т. к. изготавливается из глины и сланца.
Керамзит отлично подходит для современного, экологически чистого домостроения. Часто используется в декоративных целях. В домашних условиях керамзит используют при выращивании домашних растений, он не даёт испаряться влаге, тем самым контролируя водный баланс растения.
Свойства керамзита:
- высокая прочность;
- хорошая теплоизоляция;
- морозоустойчивость, огнеупорность;
- химическая инертность и кислоустойчивость;
- долговечность;
- натуральный, экологически чистый материал;
- оптимальное соотношение цены и качества.
Рекомендую к просмотру видео о том из чего делают керамзит:
izchegodelaut.ru
основные свойства и особенности, производство и области применения материала
Наверняка у всех, кто задумывался о постройке собственного дома, появлялась такой вопрос: какой материал лучше использовать? Выбор действительно велик и каждый строительный материал имеет свои как положительные, так и отрицательные качества. Широко известны кирпич и бетон. А слышали ли вы о керамзите?
Что такое керамзит?
Керамзит – это легкий материал, напоминающий стекло и имеющий пористую структуру. Как правило, гранулы керамзита овальной формы, а их поверхность имеет спекшуюся оболочку. Различают три фракции материала:
-
Гравий — это пористые частички, имеющие практически круглую форму, поверхность которых оплавлена и покрыта коркой. Именно в качестве гравия создается керамзит. Он, как правило, темно-бурого цвета. Размер гравия составляет от пяти до сорока миллиметров. Гравий устойчив к низким температурам, огнестоек, а также не имеет в своем составе примесей, способных нанести вред цементу.
- Щебень — применяется для заполнения легких бетонов, имеющих произвольную форму, чаще всего угловатую. Размер керамзитового щебня примерно такой же, как и у гравия. Его можно получить дробя крупные куски керамзита, чтобы обеспечить лучшую сцепляемость в бетоне.
- Песок— применяется для заполнения легких бетонов и растворов, размер частиц которого может варьироваться от 0,14 до 5 мм. Его получают в результате обжига глины в специальных печах, дроблением больших кусков керамзита или же при отсеивании отходов во время производства керамзита.
Способ изготовления
Керамзит получают в результате обжига глины в специальных вращающихся печах, имеющих форму барабанов, диаметр которых составляет от 2 до 5 метров, а длина – около 70 метров, установленных под некоторым углом. В верхнюю часть печки засыпают керамзитовый полуфабрикат в гранулах, который скатывается в нижнюю часть. Там расположена форсунка, основное предназначение которой – сжигать топливо.
Процесс изготовления керамзита занимает примерно 45 минут. В зависимости от того, какой режим работы печи применялся в процессе производства, можно получить продукт с разной плотностью – от 250 кг/м³ до 800 кг/м³. Но несмотря на это, в результате все равно получится легкий пористый материал – керамзит, который полностью экологичен и безопасен.
В некоторых случаях применяют двухбарабанные печи. У них барабаны отделены порогом, что позволяет им совершать вращательные движения с различными скоростями. Даже если было использовано некачественное сырье, получившийся керамзитовый щебень или гравий по качеству не уступают, а частенько даже превышают изготовленные в однобарабанных печах те же фракции керамзита.
Также стоит отметить, что сырье, применяемое в производстве, обязано содержать в себе кварц, количество которого должно составлять примерно треть от всей массы исходного материала.
Свойства керамзита
-
Высокая теплоизоляция. Керамзит задерживает в помещении тепло и не позволяет попадать туда холоду с улицы. А все благодаря его пористости, которую он приобретает в результате обработки, проведенной в определенном режиме. Однако, кроме так необходимых для обеспечения теплоизоляции пор, в керамзите образуется стекло, большой процент содержания которого приводит к снижению теплоизоляционных свойств данного материала. Чтобы составить наглядное представление о степени теплопроводности керамзита, нужно отметить, что десятисантиметровый слой этого материала соответствует доске, толщиной в 25 сантиметров, или кладки из кирпича 80-120 сантиметров.
- На керамзит не действуют какие-либо химические вещества, устойчив к пагубному воздействию кислот. Также ему не смогут навредить различные опасные микроорганизмы, такие как грибок, плесень и другие.
- Керамзит, в отличие от других материалов, очень долговечен. Это связано с тем, что при его изготовлении в качестве основного компонента используют глину.
- Обладает звукоизоляционными свойствами, которые полностью зависят от того, насколько порист этот материал. Иными словами, чем ниже его марка, тем хуже в помещение будет проникать шум. Такое свойство керамзита ценят владельцы квартир. В том случае, если высота потолка разрешает, под бетонную стяжку насыпают слой керамзита, формируя, таким образом, звукоизоляцию между этажами.
- Благодаря высокой прочности, данный материал можно применять для наполнения бетона и изготовке керамзитовых блоков. Керамзитобетон стал популярным материалом, используемым для постройки не только жилых домов, а и промышленных объектов, потому что является универсальным, так как объединяет в себе свойства хорошего строительного материала и утеплителя. К тому же керамзитобетон практически не впитывает воду, следовательно, весьма долговечен и не разрушается под воздействием низких температур.
- Обладает таким свойством, как морозоустойчивость.
- Поскольку основой керамзита является глина, то данный материал считается абсолютно экологически чистым.
- Влагостоек и к тому же практически не поглощает воду, что позволяет применять его как дренаж.
- Обладает высокой огнестойкостью и не подвержен самовозгоранию.
Область применения
- При постройке зданий для обеспечения теплоизоляции. Кроме того, он может применяться в качестве утеплителя. Способен защищать фундамент от промерзания, обеспечить высокую теплоизоляцию крыш.
- Применяется для заполнения легких бетонов.
- Применяется для изготовления легких керамзитовых блоков.
- Керамзит применяют при создании дренажа, а также для обеспечения теплоизоляции дорог, особенно в тех случаях, когда работы проводят на грунте, насыщенном подземными водами.
- Применяется для утепления теплопровода. К тому же в случае аварии или проведения плановых ремонтных работ, керамзит не создаст проблем для доступа к трубе.
- Применяется для разведения различных растений без почвы.
- Используется в ландшафтном дизайне для газонов. Вместе с тем керамзит теплоизолирует грунт и создает хорошие условия для развития корней.
- Может применяться в качестве удерживающей подсыпки в горшках с цветами.
Процесс изготовления блоков
Как правило, для производства керамзитоблоков применяют следующее оборудование:
- Бетономешалка. С ее помощью изготавливают исходный раствор, состоящий из песка, цемента и керамзита. Их соотношение полностью зависит от производителя, поскольку есть много вариантов и каждый из них влияет на определенные свойства блока, причем не всегда в лучшую сторону. Например, если керамзит составляет четверть от всей массы блока, то он получится легким, однако его механическая прочность будет невелика. Кроме того, чтобы улучшить эксплуатационные свойства, в раствор добавляют различные пластификаторы.
- Пресс. Это основное устройство для производства блоков. В специальные формы, количество которых может составлять от 1 до 12 – этот параметр существенно влияет на стоимость данного оборудования, заливают раствор. Пресс бывает трех видов: с ручным приводом, вибрационным и с компрессорной установкой.
Полученные в результате блоки имеют такие характеристики:
- Плотность – 900 кг/м³;
- Теплопроводность – 0,48 Вт/м*К;
- Прочность при сжатии – 75 кг/см²;
- Количество циклов морозостойкости – 50.
Такие показатели являются одними из лучших среди подобных строительных материалов. Лишь газобетон может похвастаться теми же параметрами, однако, из-за высокой стоимости, он не пользуется большой популярностью.
Керамзитоблоки в строительстве
Все чаще и чаще можно встретить дома, построенные из керамзитобетона. Стоит отметить, что данный материал не накладывает ограничения на размеры конструкций, то есть они могут быть как хозяйственными постройками, так и большими особняками. Это связано характерными свойствами керамзитовых блоков.
Данный материал обеспечивает конструкции высокую прочность, долговечность и легкость. К тому же он хорошо взаимодействует с раствором, поскольку является пористым материалом.
С помощью керамзита возможно провести выравнивание поверхности, имеющей большой перепад, и сделать им это намного легче, чем каким-либо другим материалом.
Оцените статью: Поделитесь с друзьями!kotel.guru
Что такое керамзит: свойства, применения
Керамзит – это строительный материал, получаемый путем вспучивания и обжига глины в специальных барабанных печах. Его подразделяют на несколько видов, в зависимости от размера гранул (фракции).
- Керамзитовый песок – наполнитель фракции от 0,1 до 5 мм.
- Керамзитовый гравий – овальные или округлые частицы размером от 5 до 40 мм.
- Керамзитовый щебень. Производится по сухой технологии, в результате получается материал угловатых форм фракции от 5 до 40 мм.
Также в зависимости от технологии обработки сырья получают керамзит различного объемного веса, который колеблется в пределах 350 – 600 кг/м³. Более пористый материал обладает меньшим объемным весом, при этом он обладает меньшей теплопроводимостью, то есть, более высокими теплоизоляционными свойствами.
Технология производства
При производстве керамзита используют легкоплавкие сорта глины или же глинистого сланца. После предварительной обвальцовки и просушки, сырье засыпается во вращающиеся барабанные печи, которые установлены под небольшим уклоном. Под действием силы тяжести глинистые гранулы скатываются к нижнему краю печи, где установлены тепловые форсунки. Обжиг производится при температуре от 1000 до 1300 C°. За счет высокой температуры происходит быстрое вспучивание глины, чем объясняется высокая пористость керамзита. При этом происходит оплавление верхнего слоя, что дает ему хорошую прочность и достаточно высокую герметичность оболочки.
От скорости вращения барабана, в котором происходит обжиг, зависит скорость прохождения сырья что, в свою очередь, влияет на прочность и легкость конечного продукта. Чем меньше скорость прохождения гранул в печи, тем легче и менее прочный получается продукт. Именно поэтому строгое соблюдение всех норм технологического процесса лежит в основе получения высококачественного керамзита.
Свойства
Благодаря такой технологии производства готовый материал имеет следующие свойства:
- высокая пористость, и как следствие легкость материала;
- отличные теплоизоляционные и высокие звукоизоляционные свойства;
- высокая прочность и долговечность;
- огнеупорность, устойчивость к химическому и кислотному воздействию.
Применение
Исходя из вышеперечисленных свойств, керамзит нашел свое применение в качестве утеплителя в виде сухой засыпки, используется при изготовлении легкого бетона и строительных блоков на его основе. В сельском хозяйстве керамзит применяется для улучшения дренажа почвы, а также гидропонике. В декоративных целях применяется и в домашнем цветоводстве, и как составляющая часть грунта для террариумов.
Особое внимание хочется обратить на тот факт, что керамзит – один из немногих действительно экологически чистых строительных материалов, изготовленных искусственным путем из естественного сырья. И это не удивительно, ведь для его изготовления применяется глина и более ничего. Ведь, как известно, глина – один из первых природных материалов, который человек начал применять для своих нужд.
bouw.ru