МГХ-К (Мастика Битумно-каучуковая) 18 кг.
Мастика Битумно-каучуковая МГХ-К – данная мастика холодного применения, т.е. продукт полностью готов к применению. МГХ-К это однородная смесь из таких составляющих как, нефтяной битум, резиновая крошка, каучук, растворители и природные смоляные кислоты. Такой состав позволяет мастике МГХ-К иметь эластичность в широком температурном интервале (-30С до +130С) в отличии от обычных битумных мастик. Есть и еще один плюс, мастика МГХ-К имеет высокий показатель относительного удлинения при разрыве. Это значит что мастичный слой из МГХ-К, прежде чем придет в негодность (например порвется) при усадке или подвижке знания или сооружения, будет растягиваться не нарушая своих гидроизоляционных свойств.
Мастику Битумно-каучуковую МГХ-К можно применять в качестве гидроизоляции различных конструкций, устройства мастичной кровли, приклеивания рулонной битумной гидроизоляции, также используют для ремонта кровельного покрытия и многого другого. Применение до -10С. При использовании МГХ-К в отрицательную температуру, необходимо выдержать в плюсовой температуре не менее суток или разогреть мастику до +50С (например, в паровой бане, прежде снять приоткрыть крышку) Важно! Не применять открытое пламя!
Мастику наносить на сухую, очищенную поверхность. Для лучшей адгезии, поверхность необходимо заранее обработать битумным праймером.
Технические характеристики:
Показатель | Значение |
Условная прочность, МПа (кгс/см2) | не менее 0,5 (5,0 кгс/см2) |
Жизнеспособность, час | не менее 0,5 часа |
Относительное удлинение при разрыве, % | не менее 300 |
Водопоглощение в течение 24 ч., % по массе | не более 0,5 |
Условная вязкость, секунд | не менее 15 |
Массовая доля нелетучих веществ, % | не менее 50 |
Прочность сцепления с бетоном, МПа (кгс/см2) | не менее 0,4 (4,0 кгс/см2) |
Температура размягчения, K (°С) | не ниже 403 (130°С) |
Гибкость на брусе с закруглением радиусом, мм, 5.0±0.2 при температуре, K (°С), не выше 268 (минус 5) | на поверхности образца не должно быть трещин |
gidroizol.ru
Мастика битумно-резиновая Аquamast: защита строительных конструкций
Защитить от воздействия жидкостей строительные конструкции внутри и снаружи или отремонтировать кровлю – для этого подойдет мастика битумно-резиновая AquaMast или Технониколь № 20, или же вид холодной смеси для гидроизоляции – битумная мастика Грида МГХ Г.
Содержание статьи
Мастика: характеристика
МГХ-Г производства Грида – черное однородное вещество, которое готовится на основе соединения разных видов продуктов нефтепереработки, органических растворов и минеральных примесей.
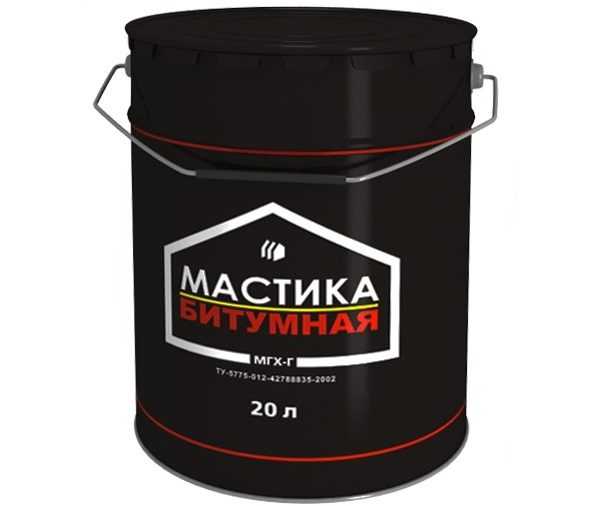
МГХ-Г – это холодное соединение и его следует перед использованием разогреть до температуры 30-50 градусов Цельсия, учитывая температуру внешней среды, а также, если возникнет потребность снизить вязкость мастики. Работать с веществом можно при минусе десяти, но не ниже.
Разогревается битумная масса на водяной/ паровой бане либо другим способом, но ни в коем случае не при помощи открытого огня и иных средств, создающих искры. Чтобы нагреть битумную МГХ-Г Грида, откупоривают емкость, а по окончанию процесса разогрева смесь перемешивают.
Для нанесения гидроизоляции лучше использовать шпатель. Чтобы воспользоваться кистью либо валиком в битумную смесь добавляют 20-50% химического раствора, зависимо от веса мастики. Наносится вещество на сухую поверхность, которую заранее очищают от любых видов загрязнений.
Хранить битумную МГХ-Г Грида следует 12 месяцев от дня изготовления.
Производитель выпускает материал в жестяных ведрах весом 3, 10, 18, 20 и 45 кг.
Масса Технониколь
Среди гидроизоляционных мастик, изготовленных Технониколь, выделяется битумно-резиновая смесь №20. В ее состав входят битумы нефтяные, видоизмененная резиновая крошка, технологические и минеральные добавки, а также органические растворы. Эта резинобитумная масса применяется при ремонте или установке любых кровель, зданий и прочих стройконструкций.
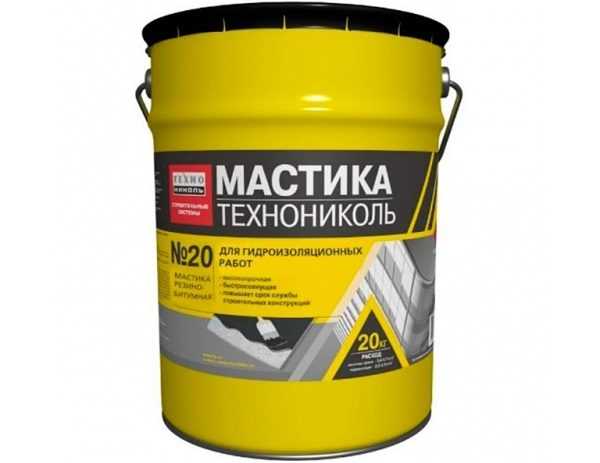
Укладывая гидроизоляцию, затрачивают 2.5 – 3.5 кг смеси на 1 кв. м, а мастичную кровлю – 3.8-5.7 кг смеси на 1 кв. м.
Температурный диапазон использования мастики находится в пределах -20 …+40°С. Если показатели опускаются ниже +5 градусов, перед применением выдержать смесь в теплом помещении на протяжении суток.
Срок годности – не больше 18 месяцев с момента изготовления (в месте сухом и темном). Приобрести Технониколь можно только в ведре весом 20 кг.
Мастика Аквамаст
В число холодных смесей входит и резинобитумная мастика AquaMast, которая предназначена для работы с кровлей и для защиты от жидкостей. Для работ необходима температура от –10 до +40 градусов.
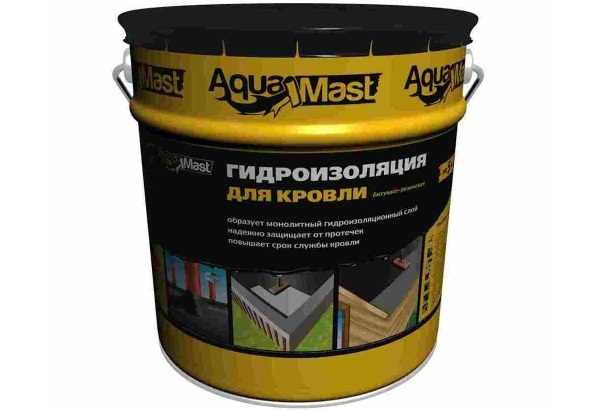
При устройстве мастичной кровли, Аквамаст советуют класть в три слоя (каждый толщиной не больше 1.5 мм), при этом затраты на 1 квадратный метр составляют 3.3-4.3 кг.
Особенности работы при этом:
- Перед тем, как накладывается смесь, очищают поверхность от пыли и грязи;
- Затем наносится праймер Аквамаст, которому нужно 10 часов, чтобы высохнуть;
- Эксперты рекомендуют между всеми слоями вещества класть малярную паутинку, что повысит уровень прочности окончательной работы;
- Каждому слою дают около 12 часов на высыхание;
- Поверх последнего слоя насыпают защиту от ультрафиолета (гравий или Технониколь 57).
Хранят мастику в темном и сухом помещении на протяжении 18 месяцев. Вещество фасуют в металлическую тару массой 3, 10 и 18 кг.
Очень похожа по способу использования на AquaMast БМ 3 – битумная смесь, в составе которой есть бутилкаучук. Применяется она только при наружных работах, будь то кладка кровли или изоляция от влаги фундамента, водопровода или железобетонных строений. Но в отличие от первой БМ имеет лишь 12 месяцев срока годности, а помещения для хранения должно быть хорошо проветриваемым.
Отличительные параметры БМ:
- Размер слоя мастики – 1.5 – 2 миллиметра;
- Слой со стекловолокном сохнет около полутора суток.
В итоге на три слоя идет приблизительно 5-7 кг БМ на 1 кв. м.
Вконтакте
Одноклассники
gipsohouse.ru
характеристики и сфера применения материала
Ассортимент рынка гидроизоляционных материалов обширен. Существует множество водоотталкивающих покрытий, каждое из которых надежно защищает конструкции от контакта с влагой. Битумные составы пользуются особой популярностью. Они универсальны, сцепляются со всеми видами оснований, применяются для обустройства гидро-, пароизоляции, крепления рулонных материалов. Битумно-резиновая мастика – один из наиболее практичных гидроизоляторов.
Битумно-резиновые составы всех марок отличаются хорошими адгезионными свойствами. Они долговечны, эластичны, не лопаются при усадке зданий, отлично растягиваются, сопротивляются механическим нагрузкам. При выборе конкретной марки учитывают особенности основания и виды запланированных работ. Какими свойствами обладает готовое покрытие? Какие виды материала пользуются особой популярностью у отечественных строителей?
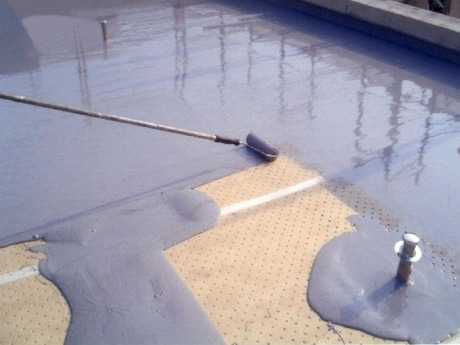
Битумно-резиновая мастика
- Однородность. Состав должен иметь однородную структуру без посторонних включений. Необходимо, чтобы каждая частица наполнителя была пропитана вяжущим веществом.
- Практичность и удобство нанесения. Гидроизоляционные работы приходится проводить в самых разных условиях. Материал должен хорошо ложиться на поверхность, не расслаиваться, намертво прилипать.
- Экологичность. Сырье, из которого изготовлены мастики, должно быть экологически безопасным. Недопустимо испарение вредных веществ в атмосферу.
- Теплостойкость. Материал должен хорошо переносить нагрев до температуры не менее 70°С, сохраняя свои свойства и эксплуатационные характеристики.
- Биостойкость. Готовое покрытие должно быть гигиеничным, чтобы на нем не размножались грибки, бактерии, плесень.
- Водонепроницаемость. Это главное требование к любому гидроизолятору. Он должен надежно защищать основание от попадания влаги.
- Долговечность. Срок службы материалов во многом зависит от условий эксплуатации. Необходимо правильно подбирать мастики с учетом всех особенностей объектов. Также стоит покупать только высококачественные составы, которые хорошо зарекомендовали себя на рынке.
Нанесение мастичного покрытия на основание
Битумно-резиновые мастики (МБР) выпускаются в виде составов, готовых к применению. Материал представляет собой черную однородную массу густой консистенции, которую можно сразу же использовать по назначению. Некоторые мастики выпускают в виде смесей, которые нужно разводить растворителями.
Мастика состоит из нескольких сортов нефтяного битума, резиновой крошки, наполнителей, растворителей и различных добавок. Количество и тип компонентов определяются назначением каждого конкретного вида материала.
Готовое мастичное покрытие эластично, благодаря чему отличается такими свойствами:
- хорошо переносит высокие и низкие температуры;
- не лопается, не дает трещин в случае резких температурных перепадов;
- сохраняет свои свойства при температуре окружающей среды от -30˚C до +130˚C.
Материал применяют для гидроизоляции кровельных конструкций, бетонных сооружений. Его используют в качестве клеевого состава и дополнительного герметика при укладке рулонных гидроизоляторов.
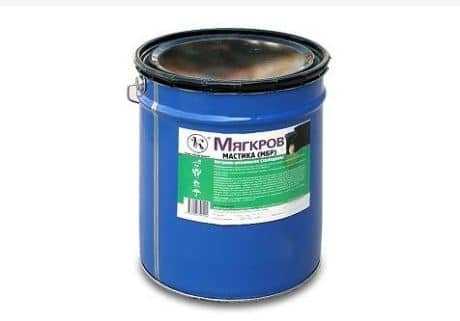
Мастика холодного нанесения
Плюсы гидроизоляционного материала ↑
- Высокий уровень адгезии. Составы хорошо сцепляются со всеми видами оснований, подходят для вертикальной и горизонтальной гидроизоляции.
- Стойкость к негативным факторам окружающей среды. Битумно-резиновые смеси не боятся осадков, ветра, бактерий, грибков. Они не гниют, не разлагаются под воздействием химических веществ.
- Защита от коррозии. Битумно-резиновые покрытия подходят для обработки металлических поверхностей. Прилипая к материалам, они надежно защищают их от сырости.
- Биозащита. В состав мастик добавляют специальные компоненты с антибактериальными свойствами. Покрытия защищают не только от влаги, но и от грибков, плесени.
- Выравнивание поверхностей. При нанесении на поверхности мастики равномерно растекаются по основаниям, выравнивая их и маскируя небольшие дефекты.
- Экономный расход. Точный расход материала на 1 м.кв. площади зависит от его консистенции. Каждая марка имеет свои особенности, поэтому при расчете следует ориентироваться на рекомендации производителя.
Состав горячего нанесения
Несколько минусов битумно-резиновых мастик ↑
- Требования к погодным условиям. Из-за особенностей состава мастик их не рекомендуют применять, если температура окружающей среды ниже -5°С, идет дождь или снег.
- Пожароопасность. Мастики горячего нанесения потенциально опасны, поэтому при их применении следует строго придерживаться правил техники безопасности, иначе не исключено возгорание.
- Ограничения в применении. Теоретически битумно-резиновые составы можно использовать внутри помещений, однако на практике их применяют преимущественно для наружных работ.
- Некоторые трудности при нанесении. Материал можно наносить вручную – валиком, щеткой – или с помощью механических приспособлений. Второй способ предпочтительней, т.к. равномерно нанести состав, используя валик, довольно сложно. Могут образоваться «наплывы» и неровности.
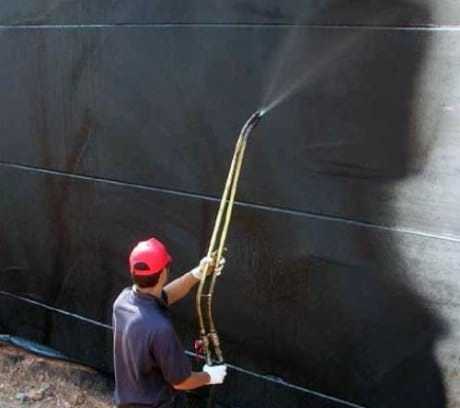
Гидроизоляционные работы
Для обозначения битумно-резиновой мастики применяют аббревиатуру МБР. Рядом с буквами обычно указана цифра. Она указывает температуру, при которой состав размягчается и готов к применению. В зависимости от этого различают марки мастик – МБР 65, 75 и т.д. Каждый состав имеет собственные особенности и сферу применения. Буква Х после цифры обозначает способ нанесения состава – холодный.
Составы разных марок
Мастики МБР 65 и 90: характеристики и сфера применения ↑
Битумно-резиновая мастика МБР 65 подходит для изоляции инженерных систем, трубопроводов, гидрозащиты бетонных и железобетонных конструкций, бассейнов, резервуаров. Ее наносят горячим способом, нагревая до температуры не ниже 65°С и не выше 220°С.
Готовое покрытие выдерживает низкие температуры (до -25°С) без изменения своих свойств. Способно растягиваться до 5 см. Проникает вглубь до 40 мм. Для получения прочного и долговечного покрытия требуется тщательно подготовить поверхность – очистить, обеспылить, осушить.
Мастику МБР 90 можно наносить холодным и горячим способом. Материал уступает в эластичности МБР 65: растягивается на 3 см, проникает на 20 мм. Готовое покрытие может дать трещины при температуре ниже -15°С. Состав применяют для укладки рулонных изоляторов, защиты коммуникаций, трубопроводов, подземных сооружений, резервуаров.
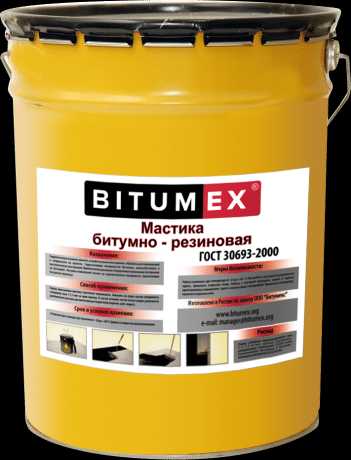
Мастика производства компании BITUMEKS
Битумно-резиновые мастики содержат токсичные и огнеопасные растворители. При работе с ними следует придерживаться правил техники безопасности (СНиП 12-04-2002). Мастера должны иметь соответствующие навыки, пройти инструктаж. Применение средств индивидуальной защиты обязательно.
Гидроизоляционные работы проводят вдали от источников огня, а рядом должны находиться средства, необходимые для тушения пожаров. Если горячий материал попадет на кожу, его следует удалить специальным средством, а рану обработать препаратом от ожогов.
Внимание! Курение в местах приготовления и применения битумных мастик строго запрещено.
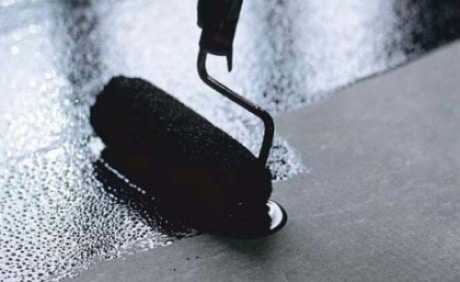
Нанесение мастики вручную
Наибольшей популярностью у наших соотечественников пользуются битумно-резиновые мастики торговых марок «Технониколь», Bitumast, AquaMast. Это высококачественные материалы, проверенные временем. Они универсальны, подходят для обработки оснований разных типов, образуют высокопрочные покрытия на поверхностях. Перед применением следует ознакомиться с рекомендациями изготовителя, а во время работ придерживаться правил техники безопасности.
gidroguide.ru
Мастика битумно-каучуковая «Питон» — Анлес
Описание
Химическая основа:
Битумная-каучуковая мастика на основе битума, раствора каучука, ингибитора коррозии, полезных добавок, растворителя.
Технические данные в соответствии с ТУ 5775-018-44297874-02:
Внешний вид | Однородная вязкая масса черного цвета без видимых посторонних включений |
Массовая доля сухого остатка, %, не менее | 55 |
Продолжительность высыхания при 200С, час, не более Температура размягчения Прочность сцепления между слоями, МПа (кгс/см²), не менее Водопоглощение за 24 часа, %, не более | 12 100 ± 10 0,1 (1,0) 2 |
Свойства:
Обладает высокой эластичностью и теплостойкостью (до +1000С), повышенной устойчивостью к механическим и химическим воздействиями.
Указания к применению:
Перед употреблением мастику тщательно перемешать, при необходимости разбавить растворителем (бензин БР-1, толуол, уайт-спирит). Мастику наносить на сухие и очищенные от грязи поверхности. Основание рекомендуется прогрунтовать мастикой, разбавленной рекомендованным растворителем в соотношении 1:2. Мастику наносить при температуре не ниже +10°С кистью, шпателем, методом пневматического или безвоздушного распыления в один или два слоя (промежуточная сушка около 6 часов, толщина слоя — не более 1 мм). Перед эксплуатацией обработанную поверхность рекомендуется подсушить в течение 24 часов. Приклеивание рулонных материалов может производиться по стыкам или по всей поверхности.
Расход:
1-3 кг на 1 кв.м
Условия хранения и транспортировки:
Мастика должна храниться в упаковке предприятия-изготовителя в крытых складских помещениях при температуре от минус 20 до плюс 30°С, вдали от отопительных приборов, с предохранением от попадания влаги, солнечных лучей.
Транспортирование мастики осуществляют любым видом транспорта, . Допускается транспортирование мастик при минусовых температурах.
Срок хранения в герметично закрытой таре – 12 месяцев со дня изготовления.
Меры предосторожности:
Мастика – легковоспламеняющийся продукт. При работе с мастикой следует соблюдать следующие меры предосторожности: работы проводить вдали от открытых источников огня, в хорошо проветриваемом помещении. При воспламенении для тушения применять песок, асбестовое одеяло.
Мастика разрешена к применению Центром Государственного санитарно-эпидемиологического надзора Санкт-Петербурга, санитарно-эпидемиологическое заключение № 78 01 05 577 П 004957 08 02
anles.ru
Способ получения битумно-каучуковой мастики
Изобретение относится к технологии производства строительных материалов и может быть использовано в качестве гидроизоляционных и кровельных мастик. Сущность перед смешиванием с модифицирующей добавкой битум нагревают до температуры 150-190°С, вводят отходы производства поликапроамида, перемешивают до однородного состояния и в полученную смесь вводят пластификатор и органический растворитель, перемешивают. В полученную смесь вводят модифицирующую добавку, представляющую собой комплекс из низкомолекулярного гидроксилсодержащего каучука, с соотношением мономеров бутадиена и изопрена 80:20, молекулярной массой 3000-3500, содержанием гидроксильных групп 0,7-1,1 мас.%, полиизоцианата, наполнителя, влагопоглотителя, катализатора уретанообразования, пластификатора, низкомолекулярного спирта. Затем перемешивают при температуре 20-50°С до гомогенного состояния. Компоненты модифицирующей добавки берут в следующем соотношении, мас.ч.: низкомолекулярный гидроксилсодержащий каучук 100, полиизоцианат 20-36, наполнитель 100-250, влагопоглотитель 5-20, катализатор уретанообразования 0,001-3,0, пластификатор 40-100, низкомолекулярный спирт 0,5-8, при следующем соотношении компонентов мастики, мас.ч.: битум 25-200, пластификатор 17-200, отходы производства поликапроамида 0.5-100, модифицирующая добавка 100. Технический результат: повышение адгезии к основанию и теплостойкости, возможность формирования гидроизолирующих и кровельных покрытий заданной толщины холодным способом путем налива или обмазки. 2 табл.
Изобретение относиться к технологии производства строительных материалов и может быть использовано в качестве гидроизоляционных и кровельных мастик.
Известен способ получения битумно-каучуковой мастики, включающий подачу в турбосмеситель низкомарочного битума, введение в него при постоянном перемешивании полимерной добавки, дивинилстирольного термоэластопласта ДСТ-30, тонкодисперсного наполнителя и перемешивание их. Часть наполнителя вводят в битум в соотношении 1:0,028, затем в полученную смесь порциями в течение 5-10 минут вводят полимерную добавку до получения смеси с соотношением компонентов битум:добавка:наполнитель 1:0,058:0,028, смесь перемешивают в течение 40-60 минут, после чего добавляют оставшееся количество наполнителя и осуществляют окончательное перемешивание до получения композиции содержащей, мас.%: битум 72-85, ДСТ-30 5-8, наполнитель 10-20 (патент РФ 2016019, С 08 L 95/00, 1994).
Недостатком данного способа является низкая адгезия мастики к основанию.
Известен способ получения битумно-каучуковой мастики путем смешения в смесителе битума, бутилкаучука, пластификатора и наполнителя, в состав композиции дополнительно вводят фенолформальдегидную или нефтеполимерную смолу с температурой размягчения не ниже 85°С, диоксид кремния и антисептик, при этом первоначально осуществляют при 100-120°С смешение бутилкаучука, смолы и диоксида кремния до получения однородной массы, затем в полученную массу вводят разогретый до 170-190°С битум, при этом введение наполнителя осуществляют или до введения битума, или двумя равными порциями, одну из которых вводят на стадии смешения бутилкаучука с добавками, другую вместе с битумом при следующем составе композиции, мас.%: битум 50-64%, пластификатор 5-8%, бутилкаучук 8-15%, синтетическая смола 2-4%, минеральный наполнитель 15-22%, диоксид кремния 2-3%, антисептик 0,5-1% (патент РФ 2016018, С 08 L 95/00).
Недостатком указанного способа является сложность и длительность процесса, низкая теплостойкость покрытия.
Наиболее близким решением к предлагаемому изобретению по технической сущности является способ изготовления битумно-каучуковой мастики (патент 2139904, С 09 D 195/00, 1999) путем смешивания каучука, битума, антиоксиданта, модифицирующей добавки и наполнителя, причем перед смешиванием с битумом каучук диспергируют в органическом растворителе с антиоксидантом и перемешивают в высокоскоростном смесителе в течение 15-30 минут, затем в полученную смесь вводят остальные указанные реагенты и дополнительно перемешивают 30-60 минут, весь процесс ведут при температуре 20-50°С, в качестве модифицирующей добавки используют салициловую кислоту, в качестве каучука хлоропреновый, этиленпропиленовый, хлоркаучук и 1,2-полибутадиен, и дополнительно вводят вулканизующий агент и нефтеполимерную или инденкумароновую синтетическую смолу при следующем соотношении, мас.%: битум 3,0-10,0, хлоропреновый каучук 2,0-10,0, этиленпропиленовый каучук 0,2-2,0, 1,2-полибутадиен 0,01-0,5, хлоркаучук 0,5-3,0, синтетическая смола 3,0-10,0, антиоксидант 0,1-0,5, вулканизующий агент 0,1-1,0, салициловая кислота 0,01-0,5, наполнитель 0,5-5,0, органический растворитель все остальное.
Недостатком данной композиции является низкая адгезия к основанию, недостаточно высокая теплостойкость. Мастика используется в виде праймера, обязательна сушка нанесенного покрытия. При этом в процессе сушки возможно образование усадочных трещин и пузырей, что снижает эксплутационные качества покрытия. Из-за высокого содержания легколетучего растворителя формирование гидроизолирующего покрытия слоем необходимой толщины наливным способом невозможно без дополнительной приклейки рулонного материала.
Задачей предлагаемого технического решения является разработка технологичного способа получения битумно-каучуковой мастики, обладающей повышенной адгезией к основанию, повышенной теплостойкостью и возможностью формирования гидроизолирующих и кровельных покрытий заданной толщины холодным способом путем налива или обмазки без применения дополнительных рулонных изолирующих материалов.
Техническим результатом является повышение адгезии к основанию и теплостойкости битумно-каучуковой мастики, возможность формирования гидроизолирующих и кровельных покрытий заданной толщины холодным способом путем налива или обмазки без использования дополнительных рулонных изолирующих материалов.
Технический результат достигается тем, что в способе получения битумно-каучуковой мастики путем смешивания битума, модифицирующей добавки перед смешиванием с модифицирующей добавкой битум нагревают до температуры 150-190°С, вводят отходы производства поликапроамида, перемешивают до однородного состояния и в полученную смесь вводят пластификатор и органический растворитель, перемешивают, затем в полученную смесь вводят модифицирующую добавку представляющую собой комплекс из низкомолекулярного гидроксилсодержащего каучука, с соотношением мономеров бутадиена и изопрена 80:20, молекулярной массой 3000-3500, содержанием гидроксильных групп 0,7-1,1 мас.%, полиизоцианата, наполнителя, влагопоглотителя, катализатора уретанообразования, пластификатора, низкомолекулярного спирта и дополнительно перемешивают при температуре 20-50°С до гомогенного состояния, вышеуказанные компоненты модифицирующей добавки берут в следующем соотношении, мас.ч..:
Низкомолекулярный | |
гидроксилсодержащий каучук | 100 |
Полиизоцианат | 20-36 |
Наполнитель | 100-250 |
Влагопоглотитель | 5-20 |
Катализатор уретанообразования | 0,001-3,0 |
Пластификатор | 40-100 |
Низкомолекулярный спирт | 0,5-8 |
при следующем соотношении компонентов мастики, мас.ч.:
Битум | 25-200 |
Пластификатор | 17-200 |
Отходы производства | |
Поликапроамида | 0.5-100 |
Модифицирующая добавка | 100 |
Сущность изобретения заключается в том, что битум нагревают до температуры 150-190°С для того, чтобы битум расплавился до гомогенного состояния и в нем полностью растворились отходы производства поликапроамида, имеющие температуру плавления 135-145°С. Совмещение с модифицирующей добавкой проводят при температуре 20-50°С, так как она содержит полиизоцианат, который при повышенной температуре может вступить в реакцию уретонообразования. Использование битума, органического растворителя, отходов производства поликапроамида, пластификатора и добавки, представляющей собой комплекс модифицирующих агентов из низкомолекулярного гидроксилсодержащего каучука марки ПДИ-1К, полиизоцианата, наполнителя, влагопоглотителя, катализатора уретанообразования, пластификатора, низкомолекулярного спирта, позволяет достигнуть поставленную задачу. Каучук, битум, пластификатор и отходы производства поликапроамида благодаря совместимости образуют гомогенную однородную композицию взаиморастворимых компонентов. Низкомолекулярный гидроксилсодержащий каучук с полиизоцианатом формирует эластичную трехмерно сшитую структуру за счет химического и физического взаимодействия каучука с битумом, каучука и битума с полиизоцианатом, отходов производства поликапроамида с полиизоцианатом. Каучук с полиизоцианатом, совмещаясь и химически связываясь с битумом, образует единую пространственную сетку, эластифицирует композицию, обеспечивая высокую теплостойкость. Отходы производства поликапроамида представляют собой низкомолекулярные примеси, отделяемые экстракцией горячей водой из полимера с последующим выпариванием полученного раствора. Это смесь олигокапроамидов (89-94%), циклических олигомеров (1-3%) и ε-капролактама (5-8%). Ввиду наличия в отходах полярных групп (аминных, амидных, карбоксильных) повышается адгезия к основанию.
Готовая битумно-каучуковая мастика до отверждения представляет собой жидкую массу, позволяющую формировать покрытие слоем заданной толщины способом свободного литья. После отверждения за счет химического взаимодействия компонентов композиции образуется гидроизоляционное покрытие с необходимыми свойствами. При этом мастика, адгезионно связываясь с бетонным, цементным, металлическим или другим основанием, в процессе отверждения не требует дополнительного приклеивания рулонных материалов и непосредственно выполняет функцию гидроизоляционного покрытия.
Наполнители, влагопоглотители, низкомолекулярные спирты, входящие в состав функциональной добавки на основе низкомолекулярного каучука, способствуют усилению технического результата, участвуя в формировании эластомерной сетчатой структуры путем химического взаимодействия с каучуком, битумом, полиизоцианатом.
Введение наполнителя более 250 мас.ч. приводит к значительному повышению вязкости мастики, что затрудняет переработку методом свободного литья. Уменьшение содержания наполнителя менее 100 мас.ч. ведет к снижению твердости покрытия.
Введение влагопоглотителя более 20 мас.ч. нецелесообразно, так как увеличение его содержания не изменит эффекта. Уменьшение содержания влагопоглотителя менее 5 мас.ч. приводит к образованию подпененного покрытия, что отрицательно сказывается на значениях адгезии.
Увеличение содержания пластификатора в функциональной добавке более 100 мас.ч. приводит к выпотеванию последнего на поверхность отвержденного покрытия. Уменьшение содержания пластификатора менее 40 мас.ч. не позволяет достичь необходимой вязкости.
Увеличение содержания низкомолекулярного спирта более 8 мас.ч. приводит к появлению хрупкости покрытия. Уменьшение содержания низкомолекулярного спирта менее 0,5 мас.ч. ведет к несколькому снижению твердости покрытия.
Введение катализатора уретанообразования менее 0,001 мас.ч. нецелесообразно ввиду продолжительного времени отверждения композиции для покрытий. Увеличение более 3,0 мас.ч. снижает время жизнеспособности композиции.
Уменьшение количества полиизоцианата менее 10 мас.ч. приводит к образованию слабосшитой структуры и образованию гелеобразного покрытия. Увеличение свыше 36 мас.ч. нецелесообразно из-за склонности к вспениванию при отверждении.
Введение отходов производства поликапроамида более 100 мас.ч. ведет к значительному повышению вязкости мастики и снижению адгезии покрытия к основанию. Снижение их содержания менее 0,5 мас.ч. не позволяет достигнуть данного уровня адгезии.
Увеличение содержания битума более 200 мас.ч. ведет к образованию слабосшитого покрытия, с низкими эксплутационными характеристиками. Уменьшение доли битума менее 25 мас.ч. снижает гидроизоляционные свойства мастики.
Снижение доли пластификатора менее 17 мас.ч. в мастике не позволяет достичь необходимого значения вязкости, а увеличение более 200 мас.ч. – ведет к образованию гелеобразного покрытия.
Снижение доли органического растворителя менее 8 мас.ч. не позволяет достичь необходимой вязкости, увеличение его доли более 100 мас.ч. приводит к чрезмерно низкой вязкости.
Способ получения битумно-каучуковой мастики следующий. В нагретый до 150-190°С битум вводятся при перемешивании отходы производства поликапроамида. После полного растворения отходов в смесь вводится пластификатор и растворитель. Смесь перемешивают до однородного состояния. В полученную битумную массу вводят модифицирующую добавку, которая представляет собой комплекс из низкомолекулярного гидроксилсодержащего каучука, с соотношением мономеров бутадиена и изопрена 80:20, молекулярной массой 3000-3500, содержанием гидроксильных групп 0,7-1,1 мас.%, полиизоцианата, наполнителя, влагопоглотителя, катализатора уретанообразования, пластификатора, низкомолекулярного спирта и дополнительно перемешивают при температуре 20-50°С до гомогенного состояния, вышеуказанные компоненты модифицирующей добавки берут в следующем соотношении, мас.ч.: низкомолекулярный гидроксилсодержащий каучук 100; полиизоцианат 20-36; наполнитель 100-250; влагопоглотитель 5-20; катализатор уретанообразования 0,001-3,0; пластификатор 40-100; низкомолекулярный спирт 0,5-8. При следующем соотношении компонентов мастики, мас.ч.: битум 25-200; пластификатор 17-200; отходы производства поликапроамида 0.5-100; модифицирующая добавка 100.
Изобретение иллюстрируется на следующих примерах.
Пример 1. Соответствует составу №3 в таблице 1. В аппарат загружают битум, включают нагрев и доводят температуру до 150°С, затем загружают отходы производства поликапроамида и перемешивают до полного растворения последнего. После этого вводят пластификатор – хлорпарафин ХП-470, органический растворитель – уайт-спирит и перемешивают. Полученную массу охлаждают до температуры 20°С и совмещают с модифицирующей добавкой и дополнительно перемешивают до гомогенного состояния.
Пример 2. Соответствует составу №4 в таблице 1.В аппарат загружают битум, включают нагрев и доводят температуру до 170°С, затем загружают отходы производства поликапроамида и перемешивают до полного растворения последнего. После этого вводят пластификатор – соляровое масло, органический растворитель – уайт-спирит и перемешивают. Полученную массу охлаждают до температуры 35°С и совмещают с модифицирующей добавкой и дополнительно перемешивают до гомогенного состояния.
Пример 3. Соответствует составу №9 в таблице 1. В аппарат загружают битум, включают нагрев и доводят температуру до 190°С, затем загружают отходы производства поликапроамида и перемешивают до полного растворения последнего. После этого вводят пластификатор – отработанное индустриальное масло, органический растворитель – сольвент и перемешивают. Полученную массу охлаждают до температуры 50°С и совмещают с модифицирующей добавкой и дополнительно перемешивают до гомогенного состояния.
Низкомолекулярный гидроксилсодержащий каучук марки ПДИ-1К представляет собой сополимер изопрена с бутадиеном с содержанием бутадиена 80% (ТУ 38. 103342-88). Имеет следующие характеристики: молекулярная масса 3000-3500, содержание гидроксильных групп 0,7-1,1 мас.%, плотность 900 кг/м3.
В качестве полиизоцианата в композиции используются полиметилен-полифенилизоцианаты на основе 4,4-дифенилметандиизоцианата (ТУ 6-03-375-75, 113-03-38-106-90, 113-03-603-86, 2224-152-04691277-96) или их импортные аналоги: десмодур, супрасек 5005, воратекс СД-100 фирмы Нунстман Полиуретан, Бельгия с содержанием изоцианатных групп 29-32%.
В качестве катализатора уретанообразования применяют третичные амины или металлорганические соединения, например триэтиламин (ГОСТ 9966-85), диметилбензиламин (ТУ 6-09-2974-78), дибутилдилаурат олова (ТУ 6-02-818-73).
В качестве битума может использоваться битум нефтяной окисленный, битум марок 90/10, 80/20, 70/30.
В состав битумно-каучуковой мастики могут быть введены компоненты, не влияющие на предусматриваемый технический результат, но придающие материалу покрытия другие преимущества, например облегчающие диспергирование и сокращающие время смещения, в частности стеариновая, олеиновая кислоты, органический разбавитель (уайт-спирит).
Для изготовления мастики используется смесительное оборудование, обеспечивающее гомогенизацию компонентов в низкомолекулярном каучуке и битуме, диспергирование порошкообразных компонентов, растворение каучука в пластификаторе и битуме, либо пластификатора и битума в каучуке. Степень перетира твердых частиц не должна превышать 100 мкм. При промышленном использовании холодной мастики полиизоцианат поставляют в комплекте с композицией и перемешивают с ней непосредственно перед нанесением на основание. Катализатор уретанообразования также может перемешиваться с композицией перед ее использованием.
Для повышения прочности покрытия возможно применение армирующих материалов, например стеклоткани.
Таблица 1 | ||||||||||||||||
Наименование компонентов | Состав, мас.ч.. | Прототип пат. РФ 2139904 | ||||||||||||||
1 | 2 | 3 | 4 | 5 | 6 | 7 | 8 | 9 | 10 | 11 | 12 | 13 | 14 | 15 | ||
1. Битум | 100 | 100 | 150 | 150 | 100 | 100 | 100 | 100 | 100 | 100 | 50 | 25 | 200 | 100 | 100 | 100 |
2. Модифицирующая добавка, в том числе: | 100 | 100 | 100 | 100 | 100 | 100 | 100 | 100 | 100 | 100 | 100 | 100 | 100 | 100 | 100 | |
салициловая кислота | 5 | |||||||||||||||
низкомолекулярный каучук ПДИ-1 К | 100 | 100 | 100 | 100 | 100 | 100 | 100 | 100 | 100 | 100 | 100 | 100 | 100 | 100 | 100 | |
полиизоцианат | 20 | 22 | 20 | 20 | 24 | 26 | 30 | 36 | 20 | 22 | 20 | 20 | 22 | 36 | 16 | |
наполнитель: | ||||||||||||||||
– мел | 150 | 200 | 180 | 150 | 150 | 200 | 150 | 150 | 200 | 150 | 150 | |||||
– каолин | 100 | 100 | ||||||||||||||
– барит | 250 | |||||||||||||||
влагопоглотитель: | ||||||||||||||||
– оксид кальция | 10 | 10 | 10 | 20 | 10 | 10 | 10 | |||||||||
– цемент | 10 | 5 | 15 | 5 | 15 | |||||||||||
– гипс | 15 | 20 | 5 | |||||||||||||
катализатор уретанообразования | 0,5 | 2,0 | 1,5 | 0,02 | 0,1 | 0,5 | 3,0 | 1,5 | 0,5 | 1,0 | 2,5 | 0,001 | 3,0 | 0,05 | 0,005 | |
пластификатор: | ||||||||||||||||
– хлорпарафин ХП-470 | 80 | 90 | 80 | 80 | 90 | 80 | 90 | 80 | 80 | |||||||
– диоктилфталат | 40 | |||||||||||||||
– масло Нетоксол | 40 | 100 | ||||||||||||||
– масло МП | 60 | |||||||||||||||
Низкомолекулярный спирт: | ||||||||||||||||
– глицерин | 3 | 3 | 3 | 5 | 4 | 0,5 | 3 | 8 | 10 | |||||||
– триметилолпропан | 2 | 4 | ||||||||||||||
– триэтаноламин | 3 | |||||||||||||||
3. Пластификатор: |
1 | 2 | 3 | 4 | 5 | 6 | 7 | 8 | 9 | 10 | 11 | 12 | 13 | 14 | 15 | Прототип | |
– хлорпарафин ХП-470 | 70 | 90 | 135 | 100 | 115 | 150 | 180 | 35 | 17 | 145 | 200 | 250 | ||||
– соляровое масло | 105 | 100 | ||||||||||||||
– отработанное индустриальное масло | 70 | |||||||||||||||
4. Отходы производства поликапроамида | 0,5 | 10 | 15 | 4 | 25 | 40 | 65 | 100 | 2 | 10 | 0,5 | 1 | 5 | 100 | 110 | |
5. Органический растворитель: | ||||||||||||||||
– уайт-спирит | 30 | 40 | 60 | 45 | 50 | 60 | 65 | 90 | 40 | 15 | 8 | 80 | 100 | |||
– сольвент | 35 | 95 | ||||||||||||||
– трет.бутанол | ||||||||||||||||
– толуол | 638 | |||||||||||||||
6. Хлоропреновый каучк | 100 | |||||||||||||||
7. Этиленпропиленовый каучук | 5 | |||||||||||||||
8. 1,2-полибутадиен | 2 | |||||||||||||||
9. Хлоркаучук | 5 | |||||||||||||||
10. Синтетическая смола | 100 | |||||||||||||||
11. Антиоксидант | 5 | |||||||||||||||
12. Вулканизующий агент | 10 | |||||||||||||||
13. Наполнитель | 30 | |||||||||||||||
Примечания: 1. В составах 1, 4-6, 9, 12, 14, 15 использован в качестве катализатора уретанообразования дибутиллаурат олова, в составах 2, 3, 8 – диметилбензиламин, в составах 7, 10, 11, 13 – триэтиламин. 2. В составах 1-4 использовался полиизоцианат на основе 4, 4-дифенилметандиизоцианата, в составах 5-7 использовался десмодур, в составах 8-10 – супрасек 5005, в составах 11-15 – Воратекс СД-100; |
Таблица 2 | ||||||||||||||||
Наименование показателей | Свойства | |||||||||||||||
1 | 2 | 3 | 4 | 5 | 6 | 7 | 8 | 9 | 10 | 11 | 12 | 13 | 14 | 15 | Прототип | |
Адгезил к стали, кгс/см2 | 11,2 | 10,1 | 8,7 | 10,3 | 8,5 | 6,3 | 5,8 | 5,3 | 11,1 | 10,8 | 11,1 | 11,2 | 9,03 | 6,1 | 3,1 | 5,1 |
Теплостойкость по Вика, °С | 130 | 130 | 120 | 120 | 130 | 135 | 130 | 125 | 125 | 130 | 135 | 135 | 130 | 130 | 110 | 110 |
Предел прочности армированного покрытия при растяжении, кгс/см2 | 35 | 35 | 35 | 35 | 36 | 36 | 35 | 35 | 36 | 35 | 35 | 35 | 36 | 36 | 35 | 35 |
Состав мастики представлен в таблице 1.
Свойства композиции приведены в таблице 2. Испытания материала покрытия проводились по ГОСТ 209-75 «Метод определения прочности связи с металлом при отрыве», ГОСТ 270-75 «Метод определения упругопрочностных свойств при растяжении». Адгезия определялась путем разрыва стальных грибков с площадью 2 см2, склееных между собой испытуемым составом. Испытания проводились на разрывной машине РМ-05. Образцы выдерживались при температуре не менее 25°С в течение 7 суток.
Из данных таблицы 2 видно, что применение в качестве модифицирующей добавки комплекса агентов из низкомолекулярного гидроксилсодержащего каучука, полиизоцианата, наполнителя, влагопоглотителя, катализатора уретанообразования, пластификатора, низкомолекулярного спирта обеспечивает получение гидроизоляционного покрытия с повышенным уровнем адгезионных свойств, теплостойкости, чем у прототипа. При этом композиция отличается лучшей технологичностью и более широким интервалом использования. Она может наноситься слоем любой заданной толщины без нагрева. Отверждение покрытия происходит сомопроизвольно. Нанесенный слой композиции выполняет функцию кровельного и гидроизолирующего покрытия без наклейки дополнительных рулонных материалов.
Покрытия из состава 15 имеет худшие показатели свойств, что связано с отклонением содержания компонентов композиции от оптимальных.
Таким образом, заявленная битумно-каучуковая мастика обладает повышенной адгезией к основанию, теплостойкостью, может успешно применятся в жидком виде для формирования покрытий заданной толщины.
Способ получения битумно-каучуковой мастики путем смешивания битума, модифицирующей добавки, отличающийся тем, что перед смешиванием с модифицирующей добавкой битум нагревают до температуры 150-190°С, вводят отходы производства поликапроамида, перемешивают до однородного состояния и в полученную смесь вводят пластификатор и органический растворитель, перемешивают, затем в полученную смесь вводят модифицирующую добавку, представляющую собой комплекс из низкомолекулярного гидроксилсодержащего каучука, с соотношением мономеров бутадиена и изопрена 80:20, молекулярной массой 3000-3500, содержанием гидроксильных групп 0,7-1,1 мас.%, полиизоцианата, наполнителя, влагопоглотителя, катализатора уретанообразования, пластификатора, низкомолекулярного спирта и дополнительно перемешивают при температуре 20-50°С до гомогенного состояния, вышеуказанные компоненты модифицирующей добавки берут в следующем соотношении, мас.ч.:
Низкомолекулярный | |
гидроксилсодержащий каучук | 100 |
Полиизоцианат | 20-36 |
Наполнитель | 100-250 |
Влагопоглотитель | 5-20 |
Катализатор уретанообразования | 0,001-3,0 |
Пластификатор | 40-100 |
Низкомолекулярный спирт | 0,5-8 |
при следующем соотношении компонентов мастики, мас.ч.:
Битум | 25-200 |
Пластификатор | 17-200 |
Отходы производства | |
поликапроамида | 0,5-100 |
Модифицирующая добавка | 100 |
www.findpatent.ru
Мастика битумно-каучуковая: применение, характеристики, цены
Мастика битумно-каучуковая ─ универсальный материал, имеющий обширную область применения в строительстве. Превосходные характеристики состава позволяют использовать его в качестве клеящей основы для напольных покрытий из дерева, линолеума, мягких кровельных материалов. Купить мастику битумно-каучуковую рекомендуется для устройства надежной и долговечной антикоррозийной защиты деревянных, бетонных, металлических конструкций, трубопроводов подземных коммуникаций.
Исключительно эластичная каучуковая мастика создана в результате смешения нефтяного битума с наполнителями и пластификатором ─ синтетическим каучуком. Она имеет полужидкую консистенцию, перед нанесением не нуждается в предварительном разогреве. Масса, разбавленная органическим растворителем, обладает низкой степенью вязкости, благодаря чему ровным слоем легко наносится на сухие чистые поверхности с помощью шпателя, кисти, валика и других простых приспособлений.
Битумно-каучуковая мастика, применение которой для гидроизоляции позволяет продлить до 25 лет срок ее эффективного функционирования, образует при нанесении однородную пленку с максимальной устойчивостью к разрушающему воздействию:
- избытка влаги,
- химически агрессивных веществ,
- ультрафиолета,
- контрастных температур в диапазоне от – 600 до +1000 С,
- вибрационных деформаций,
- микроорганизмов.
Такие уникальные эксплуатационно-технологические качества и высокая степень адгезии к наклонным поверхностям незаменимы при ремонте кровли, герметизации швов, гидроизоляции балконов, резервуаров, подвалов, санузлов.
Несмотря на то что мастика кровельная горячая по цене дешевле битумно-каучуковой смеси холодного нанесения, проведение огневых работ для ее подогрева требует особых условий безопасности, высокой квалификации строительных рабочих. Меньшая, чем у состава с каучуком теплостойкость значительно сокращает сферу ее применения.
Битумно-каучуковой мастики цена выше, но она реально отражает ее универсальность, удобство работы с ней, надежность и долговечность эксплуатации гидроизоляционного покрытия на ее основе. Нанесение смеси такого состава может производиться при внешних температурных показателях от +400 до -100 С. Размягчение каучукового защитного слоя на обработанных конструкциях происходит лишь при нагреве их свыше 800 С.
oil-export.com
Битумно-каучуковая мастика
Изобретение относится к строительным материалам и может быть использовано в качестве кровельных материалов, для защиты металлических, бетонных и других оснований, а также для герметизации швов в дорожном строительстве. Сущность: мастика содержит мас.%: битум нефтяной 59,0-80,5; бромбутил каучук или бутадиеновый каучук, или бутилкаучук, или низкомолекулярный полиэтилен 6,0-15,0; рапсовое масло или фракция α-олефинов С20-С26, или отход производства тримеров и тетрамеров пропилена 8,0-15,0; сера 0,5-1,0; доломитовый порошок или порошок окатышей горно-обогатительных комбинатов 5,0-10,0. Технический результат: повышение качественных характеристик мастики. 2 табл.
Изобретение относится к строительным материалам и может быть использовано в качестве кровельных материалов, для защиты металлических, бетонных и других оснований, а также для герметизации швов в дорожном строительстве.
Известна композиция (авт. св. СССР №834049, кл. С 08 L 95/00, опубл. 1981), включающая битум, бутилкаучук, пластификатор и наполнитель. Недостатком композиции является то, что совокупность невысокой прочности и слишком большого удлинения приводит к отрыву композиции из швов покрытий автомобильных дорог. Кроме того, композиция отличается недостаточной морозостойкостью.
Наиболее близкой к предлагаемому изобретению является битумно-каучуковая мастика (авт. свид. СССР №1715757, кл. С 04 В 26/26, С 08 L 95/00, опубл. 1992, прототип), включающая битум, бутадиенметилстирольный каучук, канифоль, наполнитель – известь-пушонку, растворитель – толуол и поливинил-н-бутиловый эфир, серу и тиурам при следующем соотношении компонентов, мас.%:
Битум | 17,5-22,5 |
Бутадиенметилстирольный каучук | 7,5-9,5 |
Канифоль | 0,5-2,5 |
Известь-пушонка | 15-20 |
Поливинил-н-бутиловый эфир | 0,5-2,5 |
Сера | 0,25-0,5 |
Тиурам | 0,25-0,5 |
Толуол | Остальное |
Известная композиция мастики обладает сравнительно низкими значениями водостойкости, теплостойкости и адгезии к бетонной поверхности.
Задачей изобретения является создание битумно-каучуковой мастики, обладающей более высокими значениями теплостойкости, водостойкости и адгезии к бетонной поверхности.
Поставленная задача решается созданием битумно-каучуковой мастики, включающей битум нефтяной, каучук, наполнитель, растворитель и серу, отличающейся тем, что содержит в качестве наполнителя доломитовый порошок или порошок окатышей горно-обогатительных комбинатов, в качестве растворителя и дополнительно пластификатора – рапсовое масло или фракцию α-олефинов C20-С26, или отход производства тримеров и тетрамеров пропилена, представляющий собой смесь изомеров олигомеров пропилена С15, в качестве каучука – бромбутил каучук или бутадиеновый каучук, или бутилкаучук, или низкомолекулярный полиэтилен при следующем соотношении компонентов, мас.%:
Битум нефтяной | 59,0-80,5 |
Бромбутил каучук или бутадиеновый | |
каучук, или бутилкаучук, или | |
низкомолекулярный полиэтилен | 6,0-15,0 |
Рапсовое масло или фракция α-олефинов | |
C20-С26, или отход производства тримеров | |
и тетрамеров пропилена | 8,0-15,0 |
Сера | 0,5-1,0 |
Доломитовый порошок или порошок | |
окатышей горно-обогатительных комбинатов | 5,0-10,0 |
В качестве битума нефтяного применяют битумы изоляционные по ГОСТ 9812-74, или строительные по ГОСТ 6617-76, или кровельные по ГОСТ 9548-74.
Фракция α-олефинов С20-С26 побочный продукт при производстве альфа-олефинов C8-C10, С10-С12, C12-C18 термокаталитической олигомеризацией этилена, соответствует ТУ 2411-068-05766801-97: температура вспышки – 171°С, самовоспламенения – 250°С.
Масло рапсовое по ГОСТ 8988-77 вырабатывается путем прессования и экстракции семян рапса.
Отход производства тримеров и тетрамеров пропилена – продукт ОАО «Нижнекамскнефтехим» представляет собой смесь изомеров олигомеров пропилена С15.
Бромбутил каучук по ТУ 2294-096-05766801-2000 – продукт ОАО «Нижнекамскнефтехим».
В качестве бутилкаучука применяют бутилкаучук марки БК-2045Т или марки БК-1530 по ГОСТ 2199-78.
Бутадиеновый каучук марки СКБ получают анионной полимеризацией бутадиена, инициированной металлическим натрием. Указанный каучук (продукт Казанского завода синтетического каучука) имеет нерегулярное строение. Содержание 1,4-звеньев в среднем составляет 34%, 1,2-звеньев – 66%. Молекулярный вес достигает 200 тыс. а. е. Температура стеклования составляет – (50°С).
Низкомолекулярный полиэтилен (побочный продукт, отделяемый при сепарации возвратного этилена при высоком давлении 20-60 МПа) – воскообразное, полупрозрачное, гидрофобное вещество белого цвета, обладающее высокой адгезией к различным материалам. Продукт состоит из смеси насыщенных углеводородов, преимущественно нормального строения (температура плавления – 90°С, температура каплепадения 80°С, температура вспышки в открытом тигле – 263°С, молекулярная масса – 1500, температура начала кипения – 330°С.
В качестве серы применяют элементную товарную серу по ГОСТ 126-76.
Применяемый порошок окатышей – побочный продукт в технологическом процессе производства восстановленного горячебрикетированного железа (продукт Лебединского горно-обогатительного комбината. Белгородская область, г. Губкин). Гранулометрический состав окатышей следующий: остаток на сите 0,14 мм – не более 2 мас.%. Состав окатышей, мас.%: FeO – 1,53; Fe3O4 (FeO F2O3) – 4,90; F2О3 – 90,53; SiO2 – 3,30; CaO – 0,11; S – 0,007; Р – 0,006. Остальные 1,117% составляют (по мере убывания): Al2О3, MgO, K2O, Na2O, TiO2.
Доломитовый порошок и порошок окатышей горно-обогатительных комбинатов имеют следующий зерновой состав, мас.%:
0,315 мм | не менее 100 |
0,07 мм | не менее 90 |
Последовательность приготовления мастик следующая: один из вышеперечисленных каучуков в расчетном количестве вводили в один из перечисленных растворителей, оставляли на сутки для набухания, затем перемешивали при 90-100°С до полной однородности. Полученный раствор в расчетном количестве вводили в битум, нагретый до 80°С, перемешивая до однородности, затем туда при той же температуре добавляли серу при перемешивании и на заключительной стадии добавляли расчетное количество порошка доломита или окатышей и перемешивали при 90°С до полной однородности. Составы и свойства приготовленных образцов мастик приведены в табл.1 и 2, соответственно.
Таблица 1 Составы приготовленных мастик | |||||||||||
№№ образца | Состав, % мас. | ||||||||||
Битум | Бром-бутил каучук | Низкомолекулярный полиэтилен | Бутилкаучук | Бутадиеновый каучук | Фракция α-олефинов | Рапсовое масло | Отход пр-ва тримеров и тетрамеров пропилена | Доломитовый порошок | Порошок окатышей | Сера | |
1 | 59,0 | 15,0 | – | 15,0 | 10,0 | 1,0 | |||||
2 | 65,2 | – | 12,0 | – | – | – | 13,0 | 9,0 | 0,8 | ||
3 | 70,0 | – | – | 10,0 | – | – | – | 11 | 8,0 | 1,0 | |
4 | 74,0 | 8,0 | 10,0 | – | – | – | 7,4 | 0,6 | |||
5 | 80,5 | 6,0 | – | – | 7,0 | 5,5 | 0,5 | ||||
6 | 75,5 | 6,0 | 8,0 | 10,0 | 0,5 | ||||||
7 | 66,0 | 15,0 | 12,0 | 6,0 | 1,0 | ||||||
8 | 67,0 | 11,0 | 15,0 | 5,0 | 1,0 |
Таблица 2 Свойства мастик | |||||||||
Свойства мастик | №№ образцов | ||||||||
1 | 2 | 3 | 4 | 5 | 6 | 7 | 8 | прототип | |
Теплостойкость, °С, ГОСТ 2678-81 | 100 | 120 | 110 | 105 | 100 | 110 | 120 | 120 | 80-90 |
Гибкость слоя мастики при температуре, °С, ГОСТ 10296-79: | |||||||||
на стержне диаметром 10 мм | -25 | -20 | -15 | -20 | -25 | -15 | -25 | -20 | -(10-25) |
на стержне диаметром 20 мм | -35 | -35 | -30 | -35 | -35 | -30 | -30 | -30 | -(10-35) |
водопоглощение в воде за 24 часа при 20°С, г/м2, ГОСТ 2678-81 | 3 | 4 | 5 | 3 | 6 | 4 | 3 | 6 | 10-14 |
Адгезия к бетонной поверхности, кг с/см2 ГОСТ 2678-81 | 2,7 | 3,0 | 3,0 | 2,5 | 2,6 | 3,0 | 2,5 | 3,0 | 1,2-2,0 |
Водонепроницаемость под гидростатическим давлением, кг с/см2 | 2,8 | 3,0 | 3,0 | 2,9 | 3,0 | 2,9 | 3,0 | 2,8 | 1,5-2,5 |
Битумно-каучуковая мастика для гидроизоляции и герметизации, включающая битум нефтяной, каучук, наполнитель, растворитель и серу, отличающаяся тем, что содержит в качестве наполнителя доломитовый порошок или порошок окатышей горно-обогатительных комбинатов, в качестве растворителя и дополнительно пластификатора рапсовое масло или фракцию α-олефинов С20-С26, или отход производства тримеров и тетрамеров пропилена, представляющий собой смесь изомеров олигомеров пропилена С15, в качестве каучука бромбутил каучук, или бутадиеновый каучук, или бутилкаучук, или низкомолекулярный полиэтилен при следующем соотношении компонентов, мас.%:
Битум нефтяной | 59,0-80,5 |
Бромбутил каучук, или бутадиеновый | |
каучук, или бутилкаучук, или | |
низкомолекулярный полиэтилен | 6,0-15,0 |
Рапсовое масло, или фракция α-олефинов | |
С20-С26, или отход производства тримеров | |
и тетрамеров пропилена | 8,0-15,0 |
Сера | 0,5-1,0 |
Доломитовый порошок или порошок | |
окатышей горно-обогатительных комбинатов | 5,0-10,0 |
www.findpatent.ru