Экологическая переработка теплоизоляции из минеральной ваты
Наш портал 7dach.ru регулярно рассматривает проблемы утепления дачных домов современными теплоизоляционными материалами и в первую очередь – изготовленными из минеральной ваты. Срок службы таких утеплителей – несколько десятилетий, но после длительной эксплуатации и они могут снизить свои потребительские качества.
Переработка каменной ваты, фото с сайта fasad-rus.ru
Например, производя ремонт дома или меняя кровельное покрытие, приходится удалять немало старого теплоизоляционного материала. К сожалению, такой материал нельзя просто взять и выбросить, как другие бытовые отходы. Ведь на свалке минеральная вата практически не будет разлагаться, как разлагаются другие отходы в естественных условиях депонирования.
Такой утеплитель необходимо утилизировать специальным способом, чтобы не вредить окружающей среде. А это ведет к дополнительным расходам и трудностям как для заказчика ремонта, так и для подрядчика.
Корпорация «Технониколь» внедрила на своем производстве программу «ТН-Рециклинг», помогающую эффективно утилизировать все виды теплоизоляции из минеральной ваты. Сюда идут и обрезки каменной ваты, и утеплитель, снятый со зданий при ремонте, и обломки плит. Предприятие бесплатно предоставляет транспорт, чтобы вывезти снятую строителями с конструкций каменную вату, и доставляет этот материал на один из своих заводов, коих имеется три: в Рязани, Заинске (в Татарстане) и Красном Сулине (в Ростовской области).
В обязанности строителей входит упаковка отслужившей свое теплоизоляции из минеральной ваты, укладка ее на поддоны и погрузка на бортовые автомобили. А уже доставленный на заводы материал отправляется на вторичную экологичную переработку.
Такая программа выгодна всем. Прежде всего, природе – мы ее не загрязняем неразлагающимися материалами. Строители избавляются от мусора на стройке, а заводы приобретают качественное сырье для повторной переработки и выпуска новой продукции.
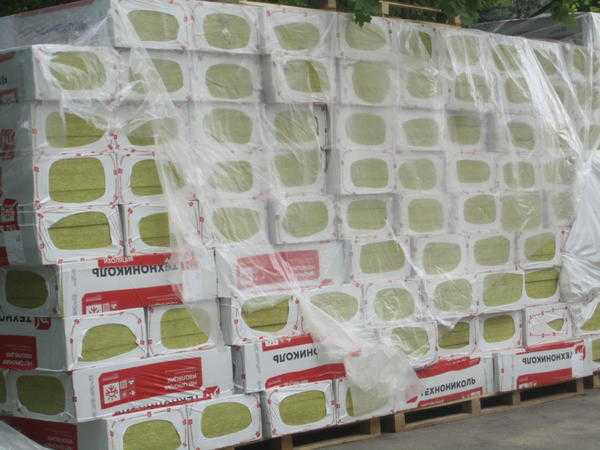
Упаковки теплоизоляции перед установкой на фасад здания, фото автора
Географическое расположение заводов корпорации «Технониколь» дает возможность принять участие в указанной программе владельцам домов и дачных объектов из многих российских регионов.
7dach.ru
Exim – Новости: Переработка и утилизация тепличных отходов
Строительные материалы, упаковка, отработанная минеральная вата, контейнеры для выращивания — все производители сталкивались с необходимостью утилизировать отходы своего тепличного производства. Переработка является наилучшим способом сделать это правильно без урона для экологии.
В России, точно так же как в Европе, часто поднимаются вопросы, связанные с правильной утилизацией производственного мусора. После ремонта теплицы и её переоборудования остается большое количество материалов, которые будучи вывезенными на обычную свалку, будут загрязнять грунт и подземные воды в течение многих лет. Поэтому все большую популярность набирает профессиональная утилизация строительных и расходных материалов, при которой современные технологии позволяют защитить природу от негативного воздействия.
Стоит отметить, что большинство пластмасс, используемых для растение- и овощеводства могут быть успешно переработаны, включая пластиковые контейнеры, лотки, поддоны, горшки, ящики. Многие компании, занимающиеся производством «садовых» пластиков, принимают к переработке отработавшее свое оборудование, поэтому не лишним будет узнать, не занимается ли крупный производитель в вашем регионе переработкой вторсырья. Также любой крупный завод по переработке твердых отходов часто занимается и переработкой пластиков.
Какие пластики подходят для переработки:
Полиэтилен высокой плотности (HPDE) — используется для выращивания рассады
Полиэтилен низкой плотности (LPDE) — пластиковые мульчи, перегородки
Полипропилен (ПП) — горшки, небольшие контейнеры
Полистирол высокой прочности (HIPS) — поддоны, подносы, лотки, ящики для сортировки
Также 1 января 2017 года в соответствии со статьей 12 Федерального закона «Об отходах производства и потребления» председателем правительства Дмитрием Медведевым был утвержден и вступил в силу перечень видов отходов, захоронение (вывоз на полигон) которых запрещено.
№ п/п |
Наименование группы видов отходов, включающих виды отходов, захоронение которых запрещается |
Сроки и условия применения запрета на захоронение |
1. |
|
с 01.01.2017 |
2. |
Лом и отходы, содержащие цветные металлы |
с 01.01.2017 |
3. |
Отходы оборудования и прочей продукции, содержащих ртуть |
с 01.01.2017 |
4. |
Отходы бумаги и картона |
с 01.01.2018 |
5. |
Отходы шин, покрышек, камер автомобильных |
с 01.01.2018 |
6. |
Отходы продукции из термопластов (в части упаковки) |
с 01.01.2018 |
7. |
Отходы стекла и изделий из стекла (в части упаковки) |
с 01.01.2018 |
8. |
Оборудование компьютерное, электронное, оптическое, утратившее потребительские свойства |
с 01.01.2020 |
9. |
Оборудование электрическое, утратившее потребительские свойства |
с 01.01.2020 |
10. |
Отходы несортированные, включающие виды, указанные в пунктах 1 – 9 настоящего перечня |
с 01.01.2024 |
Все перечисленные в таблице отходы производитель обязан сдавать на переработку, утилизацию и обезвреживание.
В частности, в тепличном производстве к таким видам отходов можно отнести:
-пластмассовая тара, не пригодная для дальнейшего использования
-отходы полиэтилена (пленки, упаковки)
-электрические и ртутные лампы
-ртутьсодержащие люминесцентные трубки
-бытовой мусор производства
-металлические элементы конструкции теплицы или оборудования
-элементы остекления
-неисправные датчики
-минеральная вата
-пестициды, упаковка от химических средств обработки
-все виды фильтров
-резинотехнические изделия и др
При этом сортировка отходов должна производиться самим предприятием. Что касается утилизации минеральной ваты, то её переработка достаточно сложна. Тем не менее, в России существует несколько международных компаний, принимающих использованные маты для производства нового сырья.
Правильная утилизация отходов эффективна не только с экономико-социальной точки зрения, но и важна для сохранения экологического баланса в регионе и оздоровления окружающей среды вблизи крупных производств и городов.
Полезная информация:
Кадастр отходов для Московской области
Пункты приема отработанных люминесцентных ламп во всех регионах России
Список предприятий по переработке лома
Уважаемые производители! Пожалуйста, расскажите, как налажен процесс утилизации в вашем тепличном хозяйстве? С какими трудностями вы столкнулись? Мы будем рады опубликовать ваше письмо и поделиться полезной информацией с другими тепличниками! Напишите нам на почту.
agro-exim.com
Установка для переработки отходов производства минеральной ваты
Сущность изобретения: установка для переработки отходов производства минеральной ваты включает приемную воронку, дробильное устройство и механизм возврата отходов в плавильную печь. Дробильное устройство выполнено в виде расположенного под валковой центрифугой дисмембратора. Механизм возврата отходов в плавильную печь состоит из двухрукавной течки, расположенной под выходным отверстием дисмембратора, перекидного шибера и расположенных у каждой течки последовательно двухвинтового конвейера, цепного элеватора, бункера и шнекового загрузчика. 2 ил.
Изобретение относится к промышленности строительных и теплоизоляционных материалов и может быть использовано при производстве минеральной ваты из расплавов шлаков, природных и синтетических материалов.
Известно, что производство минеральной ваты сопровождается большим количеством отходов в виде кусков минеральной ваты, ее пыли, обломков шлаковых корок из желобов, фильерных устройств, смеси “корольков” с минеральной ватой, огненно-жидких капель. Отходы производства минеральной ваты удаляют с помощью скребковых конвейеров или других транспортных устройств за пределы цеха, откуда затем они выводятся на свалку. Известна установка для переработки шлаков, включающая гранулятор и транспортер для уборки гранулята. Гранулятор выполнен в виде вращающегося барабана, по обе стороны от которого расположены две водоохлаждаемые пластины, причем одна из пластин снабжена ножом для очистки барабана. Барабан выполнен полым и охлаждаемым, что обеспечивает безводную грануляцию с равномерным измельчением шлака [1] Недостатком данной установки является невозможность измельчения шлаковых корок и кусков минеральной ваты. Известна также установка для переработки ковшовых остатков, содержащая приемный желоб, устройство для охлаждения, дробления, классификации, выполненная в виде перфорированного барабана с продольными ребрами, устройства для подвода охлаждающей воды, отвода пара и выгрузки [2] Недостатками данной установки являются низкая производительность, неэффективное дробление отходов производства только за счет их соударений, охлаждение отходов металлургического производства путем смешивания их с водой, что требует дополнительной сушки при их повторном использовании, невозможность измельчения всех видов отходов производства минеральной ваты (кусков минваты, минераловатной пыли, шлаковых корок, огненно-жидких капель). Кроме того, не предусмотрен механизм возврата отходов производства минеральной ваты в технологический процесс. Наиболее близкой к изобретению по технической сущности и достигаемому результату является установка для переработки отходов производства минеральной ваты, включающая приемную воронку, дробильное устройство и механизм возврата отходов в плавильную печь [3] Недостатком данной установки является невысокая производительность. Цель изобретения повышение производительности переработки отходов минеральной ваты, переработка и измельчение всех видов отходов производства минеральной ваты, внедрение безотходной технологии производства минеральной ваты путем возврата отходов в технологический процесс. Цель достигается тем, что в установке для переработки отходов производства минеральной ваты, включающей приемную воронку, дробильное устройство и механизм возврата отходов в плавильную печь, дробильное устройство выполнено в виде расположенного под валковой центрифугой дисмембратора, а механизм возврата отходов в плавильную печь состоит из двухрукавной течки, расположенной под выходным отверстием дисмембратора, перекидного шибера и расположенных у каждой течки последовательно двухвинтового конвейера, цепного элеватора, бункера и шнекового загрузчика. На фиг. 1 показана установка для переработки отходов производства минеральной ваты; на фиг.2 измельчающее устройство. Установка для переработки отходов производства минеральной ваты включает измельчающее устройство 1, установленное под центрифугой 2 на эстакаде 3, а также механизм возврата отходов, состоящий из двухрукавной течки 4 с управляемым перекидным шибером, расположенной под выходным отверстием измельчающего устройства 1, а также из четырех винтовых конвейеров 5 и 6, двух цепных элеваторов 7, двух бункеров 8 и двух шнековых загрузчиков 9, размещенных по обе стороны ванной печи 10. Измельчающее устройство 1 состоит из двух соосно расположенных механизмов питателя 1 и дисмембратора 12, имеющих каждый самостоятельные приводы (на фиг.2 не показаны).Формула изобретения
УСТАНОВКА ДЛЯ ПЕРЕРАБОТКИ ОТХОДОВ ПРОИЗВОДСТВА МИНЕРАЛЬНОЙ ВАТЫ, включающая приемную воронку, дробильное устройство и механизм возврата отходов в плавильную печь, отличающаяся тем, что дробильное устройство выполнено в виде расположенного под валковой центрифугой дисмембратора, а механизм возврата отходов в плавильную печь состоит из двухрукавной течки, расположенной под выходным отверстием дисмембратора, перекидного шибера и расположенных у каждой течки последовательно двухвинтового конвейера, цепного элеватора, бункера и шнекового загрузчика.РИСУНКИ
Рисунок 1, Рисунок 2www.findpatent.ru
Способ получения минеральной ваты из отходов промышленности
Изобретение относится к области использования техногенного сырья. В частности, золошлаковых отходов от сжигания углей для получения минеральной ваты с попутным извлечением железа. Техническая задача изобретения – получение минеральной ваты с температурой использования до 1000°С. Способ получения минеральной ваты из техногенного сырья с температурой использования 1000°С включает операции плавления в восстановительной среде с полным разделением расплава на силикатную и металлическую на основе железа части, последующего раздува силикатной части с остаточным содержанием железа не более 0,05% вододутьевым способом. Металлическая часть расплава на основе железа выливается в изложницы для использования в металлургии. 1 н. и 1 з.п. ф-лы.
Изобретение относится к области использования отходов промышленности для получения температуростойкой минеральной ваты с попутным извлечением железа.
В известном способе [Charles Н., Schwarb el al. Apparatus and method for making mineral wool from coal-ash, US Patent 4969940, Nov.13, 1990] получения минеральной ваты из золошлаковых отходов в дуговой трехэлектродной печи, заключающемся в том, что первоначально в дуговой печи плавят металл, затем ведут загрузку золы и добавок, которые плавятся за счет тепла расплавленного металла, подачи расплава золы в специальное отверстие и последующего слива расплава золы на вращающиеся барабаны и сдува образующихся волокон струей воздуха в камеру осаждения. Поскольку процесс плавления идет в условиях, не приводящих к восстановлению железа, полученная минеральная вата имеет ограниченную область температур использования до 600°С.
Известен способ [US Patent 5576252: November 19, 1996. Rapp, et al.] получения стекловолокна неправильной формы, состоящего из двух несмешивающихся стекол с разными коэффициентами теплового расширения (КТР) из чистых окисных материалов: одно (стекло А) – содержит окислы железа, второе (стекло В) – имеет в своем составе значительное количество щелочных окислов (до 20%) и, в приведенном примере наилучшего способа внедрения изобретения, в стекле В отсутствуют окислы железа. В результате после раздува получаются двухкомпонентные волокна, т.е. стекловолокна состоят из двух стекол разных составов (стекло А и стекло В), которые собираются и формируются в стандартный изоляционный продукт. Неправильная форма волокна позволяет достичь однородного заполнения объема, что приводит к более низкому значению теплопроводности, а также обеспечивает лучшую целостность волоконного пакета. На оптических микрофотографиях волокон видны две компоненты, поскольку их коэффициенты преломления различны. Две компоненты можно видеть из-за разницы в цвете, если содержание железа в двух стеклах значительно различается. Железо содержится либо в каждом из двух стеклах этого изоляционного продукта, при этом содержание его может значительно различаться, либо в одном из них. Значительное количество в конечном продукте окислов как щелочных металлов, так и железа не приводит к увеличению температуростойкости полученного изоляционного продукта, особенно при температурах использования 800-1200°С, вследствие фазовых превращений, сопровождающихся изменением объема (усадкой), приводящей к изменению физико-механических свойств.
Известен способ [RU 2149841, 2000, Асланова Л.Г.] получения минераловатных изделий из природных минералов базальтовой группы, отличающихся неоднородностью химического состава и содержащих Fe2О3 (1-7%) и FeO (3-16%). При плавлении в обычных стационарных печах (газовых или электрических) происходит значительное окисление закиси железа и увеличение доли окиси железа в расплаве, т.е. значительно увеличивается соотношение Fe2О3/FeO по сравнению с соотношением их в первоначальной породе. Для минимизации скорости окисления железа закисного в железо окисное, получения наибольшего значения соотношения FeO/Fe2О3, придания необходимых выработочных свойств расплаву (в частности, вязкости) и получения высококачественного температуроустойчивого (850-915°С) волокна состав базальтовой породы ограничивается соотношением основных оксидов: (Al2О3+SiO2)/(СаО+MgO)=3,0-7,0:FeO/FeO3>0,5; а сумма FeO+Fe2O3=7,0-14,5%. Плавление проводится в условиях, не нарушающих эти соотношения. Поскольку используются угольные электроды, в печи создается слабо восстановительная среда, приводящая к улучшению технологических свойств расплава базальтовой породы: специально поддерживаемое необходимое соотношение и сумма железа закисного (FeO) и железа окисного(Fe2O3) (таблица 1, [RU 2149841, 2000, Асланова Л.Г.). Это также приводит к частичному восстановлению оксидов до металлического состояния (сливается через шпуровое отверстие). Неоднородность раздуваемого расплава, обусловленная наличием в нем значительного количества железа в разных валентных состояниях, неизбежно приводит к разбросу механических свойств волокон, что ограничивает температурную область ее использования.
Данный способ выбран в качестве прототипа по максимальному совпадению существенных признаков.
В основу заявляемого изобретения положена задача разработки способа получения минеральной ваты, практически не содержащей железа, с температурой использования до 1000°С из техногенного сырья с попутным извлечением железа.
Поставленная задача решается тем, что в способе получения минеральной ваты из техногенного сырья, заключающемся в том, что в сырье следующего состава, мас.%: SiO2-54,73; Al2О3-10,15; Fe2O3-8,67; СаО-20,72; MgO-4,55; SO3-0,13; TiO2-0,38; Na2O-0,31; К2O-0,36 доводят содержание углерода до 5 мас.% сверх 100 мас.% и плавят в восстановительной среде до полною восстановления железа и разделения расплава, затем силикатную часть расплава раздувают вододутьевым способом с последующим осаждением в камере, а восстановленное железо, содержащее переходные металлы, сливается в изложницы.
Сущность заявляемого способа заключается в том, что в процессе восстановительного плавления окислы железа и переходные металлы, содержащиеся в шихте, восстанавливаются до металлического состояния, опускаются на дно ванны печи, поскольку плотность расплава железа больше плотности силикатной части расплава, и через нижнее шнуровое отверстие расплав на основе железа сливается в изложницы. Раздуву подвергается силикатная часть расплава, при этом содержание остаточного железа в ней составляет не более 0,05 мас. %. Обезжелезненная таким образом силикатная часть расплава, практически не содержащая железа в разных валентных состояниях, обладает необходимыми выработочными свойствами для получения минеральной ваты. Процесс обезжелезнения минеральной ваты приводит к расширению температурного интервала ее использования до 1000°C.
Предлагаемый способ получения минеральной ваты из техногенного сырья, в частности, из золошлаковых отходов поясняется конкретным примером его осуществления.
Пример 1. К 50 кг золошлаковых отходов, содержащих SiO2;Al2О3; Fe2О3; CaO; MgO; SO3; TiO2; Na2O; К2O добавляется углерод в количестве 2,5 кг, шихта плавится в восстановительной среде при температуре 1580-1600°C в течение 4 часов до полного разделения расплава. Силикатная часть расплава, практически не содержащая железа, раздувается вододутьевым способом и осаждается в осадительной камере. Температура использования полученной минеральной ваты – 1000°С. Металлическая часть расплава на основе железа, содержащая переходные металлы, сливается в изложницы через нижнее шнуровое отверстие.
1. Способ получения минеральной ваты из техногенного сырья путем плавления шихты, включающей SiO2, СаО, Al2О3, MgO, Fe2O3, Na2O, К2O, TiO2, SO3, раздува водо-дутьевым способом, осаждения в камере, отличающийся тем, что для повышения температуры использования до 1000°С плавление проводится в восстановительной среде с разделением расплава на силикатную и железную части, а последующий раздув очищенной от железа силикатной части расплава с остаточным содержанием железа общего не более 0,05% при следующем содержании компонентов в исходном техногенном сырье, мас.%: SiO2-54,73, Al2О3-10,15, Fe2О3-8,67, СаО-20,72, MgO-4,55, SO3-0,13, TiO2-0,38, Na2O-0,31, К2О-0,36.
2. Способ по п.1, отличающийся тем, что металлическая часть расплава на основе железа выливалась в изложницы.
www.findpatent.ru
Диссертация на тему «Легкие бетоны неавтоклавного твердения на основе зол и отходов производства минеральной ваты» автореферат по специальности ВАК 05.23.05 – Строительные материалы и изделия
1. Бунни Р. Добавки и смешанные цементы с точюн зрения промышленности 1. Восьмой международный конгресс по химии цемента, Рно-де-Жане%о, 21-27 сентября 1986. – М.: Стройиздат. – 1990. – с. 3 – 20.
2. Дворкин Л.И., Пашков И.А. Строительные материалы из отходов про-мьшшенности. Киев: Вьнца школа. -1989. – 208 с.
3. Кузнецова Т.В., Осокин А.П. Применение промышленньк отходов в технологии строительных материалов // Строительные материалы 1989. – Ш 7. – с. 7 – 10.
4. Дмитриев A.M., Каушанский В.Е. Проблемы использования техногенных материалов при производстве цемента // Цемент. 1980. -Ш9- с. 2 -3.
5. Голубничий A.B., Гавриленко О.И. Снижение энергоемкости производства цемента с помош;ью техногенных гфодуктов /7 Цемент. 1978. – Ш 9 – с. 9 -10.
6. Карелин B.C. Стимулирование использования зол и шлаков ТЭС в производстве цемента // Цемент. -1988. Jfs 9 – с. 10 – 11.
7. Климанова А.Ф. Применение гфомьнплешшк отходов в производстве вяжущих // Цемент. -1988. № 9 – с. 12 -13.
8. Ошйо Акира, Сон Токуажн, Матсу Атсутаи. Свойства бетона с минеральными тонкодисперсными добавками // Онада Кэшао Хококу. 1988 – 40, Ш 118. -с. 41 – 65.
9. Гашка В.Ю., Власов В.И., Мишина Т.Б. Технологические щшемы снижения расхода цемента в мелкозернистых бетонах // Ресурсосберегающая технология производства бетона и железобетона. М. 1988. – с. 33 – 42.
10. Berg W. Internationale Vorschriften &r Beton mit Flugasclie // VGB Kraftwerk stechn. 1989. – 69, ш 8. – s. 829 -833.
11. Манц O.E. Мировое производство зольной шыш и ее использовагше в бетоне // Бетоны на основе золы и шлака ТЭС и комплекс, их нспольз. в стр-ве: Всес. науч.-техн. конф. Сб. докл. Т. 1 / Сиб. металлург, шг-т. Новокузнецк. – 1990. – с. 20 -38,
12. Лугинйна И.Г., Жовтая В.Н. Шлаки и золы в гроизводстве цемента. // Цемент, 1990. – Ш 7, – с. 19 – 20,
13. Сватовская М.Б., Фолитар Л.И. РГспользованне продукта термообработки горючего сланца в цементиой снрьевой шихте // Цемент. 1988. – № 12 – с. 19-21.
14. Кравченко И.А., Ковалева И.Е., Долбилова И.Б., Ильичев СВ. Повышение эффективности цементного производства при использовании техногешшх мате-риалов//Тр. Гос. ВНИИ цемент, пром-сти (НИИЦемент). 1990. – № 99. – с. 33-36.
15. Иванов И.А. Пути утилизации зол и шлашв ТЭС в строитежстве. / Бетоны на основе золы и шлака ТЭС и комплексное их использование в строительстве: Всес. науч.-техн. конф.: Сб. докл. Т. 1 // Сиб. металлург, ин-т. Новокузнецк. – 1990. -с, 126-144,
16. Юрнк Ю.Ю., Якймович В.Д. Возможности использовання зол элеюро-станцин при производстве железобетонных издеиай. // Техн., технол., орг. и экон. С1р-ва. Минск. – 1987. – № 13. – с. 80-83.
17. Павленко СИ., Середааш О.Л., Рехтнн И.В,, Орешкин А.Б. Опыт использования зол и шлаков ТЭС в бетонах // Использ. золошлаж. отходов ТЭС в нар. х-ве: Докл. Всес. совеш;. по утилиз, золошлак. отходов, Дагомыс, – 5-10 нояб. 1990. – М. -199L-c,25-2X
18. Высощаиж СЛ. Золосодержадие цементы и бетоны на их основе // Цемент. 1989. – № 5, – с. 13-14.
19. Sybertz F. Wirksamkeit von Steinkohlenflugaschen. Teil 2. // Betonwerk + FertiAeil- Techn. 1988. – 54, №2. – s. 80-82,84-86, S8.
20. Свойства золы-уноса. /7 Сэменто конкурито. Ks 491. – с. 34-35.
21. Hoehnke Reinhard. ип1ег&исЬш1§еп тшп Einsatz von im Bezirk Ъ/ЫфФащ anfallenden Aschen. // Betontechnik. 1988. – 9, Ш 1. – s.15-1A.
22. Mills R.H., Bnenfeld N. Restricted hydration of nass-c«red concrete containing fly ash. // Fly Ash and Coal Convers. by Prod.: Charact., Util. and Disposal 111; Symp., Boston, Mass., Dec. 1-3, 1986. -Pittsburgji. 1987. -s. 221-228.
23. Mills R.H., Büenfeld N. Resöicted hydration of mass-cmAed concrete containing fly ash. // Microstruct. Dev. Ош-.п§ Hydr. Ceai.:Symp., Boston, Mass., Dec. 24,1986. PittsbmtA. – 1987. – s. 235-243.
24. Krell Jwgen, wisehers Ger4. Einflup der Feinststoffe im Beton auf Konsistenz, FestiAeit und DauerhaftiAeit. // Beton. 1988. – № 10. – s.401-404.
25. Tong Sanduo, Fang Derui, He Qiongyu, Yang Jidian. An effective measure for improving the early strength of fly ash portland cement. // Proc. Beijing Int. Symp. Cem. and Concr., Beijing, May 14-17, 1985. Vol. 1. Beijing. – 1986. – s. 481-492.
26. Павленко СИ., Танаков M.M., Якушенко В.Ф. Прочность и деформатив-ность тяжелого бетона с повышенной дозировкой золы ТЭС за период до 10 лет. // Изв. вузов. Стр-во и архнт. 1990. – № I. – с. 57-60.
27. Qin Tong-ym, Zhuang Wen-hua. The relationdiip between fly ash content and properties of dirinkage and creep of concrete. // Proc. Beijing Int. Symp. Cem. and Concr., Beijing, May 14-17, 19S5. Vol. 2. S. 1. – s. 23-34.
28. Архипенко В.П., Родрн A.H., Кудинов Ю.А. Опыт применения отвальных золошлаковых смесей в качестве легкого запояштедя. /7 Комплекс. нспозн>з. минерал, сырья, 1989. – JCg 5. – с. 71-74.
29. Баженов Ю.М., Высощсая О.Б., Данилович И.Ю. Влияние недожега в золах на морозостойкость бетона. // Долговеч. конструкций из автоклав, бетонов. Тез. докл. 6 Респ. конф. Ч. 1. Таллин. – 1987. – с. 238-241.
30. Бабаев Ш.Т., Башльпсов Н.Ф., Кривобородов Ю.Р. Эффективное использование зол ТЭС в технологии высокогрочного бетона с добавкой сунернластнфшса-тора на основе легкого газойж. // Хим. добавгш для бетонов. М. – 1987. – с. 119-126.
31. Грушко ЖМ., Козаков В.Н. Применение активгфовашшх зол гидроудаления в комплексных минеральных вяжущих. // Использ. золошлак. отходов ТЭС в нар. х-ве: Докл. Всес. совещ. по утилиз, золошлак. отходов, Дагомыс, – 5-10 нояб. 1990. – М, – 1991. – с 21-24
32. Шатохнна Л.П., Здоров А.Й., Федулова T.Ä., Ковшикова И.С., Лаври-ненко А.Г., Грибко В.Ф., Кривиков П. А., Худотенный A.C. Повьшюнйе качества цементов с добавкой актавированной золы-уноса. // Цемент. 1990.- Mq 7. – е. 20-21.
33. Рахманов В.А., Бабаев Ш.Т., Башлыков Н.Ф. Вяжупще низкой водопо-1ребности и бетоны на их основе. // Нов. технол. разраб. в гф-ве сАор. железобетона. -1988,-Жо 1,-с, 3-13,
34. Попова O.e., Хван Ю.Д. Использование отходов ТЭЦ в качестве составляющего смешанного вяжущего. // Строит, матер, из тюпут. продуктов пром-тн. Л. -1987, – с, 38-42.
35. Симеонов С, Бабачев Г., Байлов Л. Активизированньш зольный цемент. 111. полупромьппленные опыты в ГДР. // Строительство. 1987. – 34, № 2. – с. 23-25, 48.
36. Судаси Т., Норихиро И., Наомихи X. Реакционная способность зол в смеси с известью и гипсом Аи гидротермальной обработке. 11. Влияние минеральных микрокомпонентоБ на активность зол. // Сэкко то сэккай. -1988. № 212. – с. IIIS.
37. Юхикава X. Влияние добавок на гидрататрио и формировашге структуры смешанного цемента. // Сементо конкурито. -1987. -№. 483. с. 15-23.
38. Кокубу Кацуро. Добавки для бетона. Молотьш доменный шлак. // Конкурито когаку. 1988. – 26, Ш 4. – с, 25-31,
39. Вишневский В,Б., Рркинский А.М,, Годованная И.Н, Гнедавлические свойства доменных шлаков. // Цемент. 1991. – № 1-2. – с. 55-58.
40. Нагатаки С Пригодность молотого доменного гранулнровашюго шлака в качестве добавки к бетону. // Сементо конкзрито. 19Л7. – № 489. – с. 9-18.
41. Нагатаки С. Использование молотого доменного шлака в качестве добавки к бетону. // Сементо конкурито. 1990. – №519. – с. 46-48.
42. Громозова И.К., Сватовская М.Б. Контроль содержания добавки доменного шлака в цементе с использованием сульфидселективного электрода. // Цемент. -1990.-Ло9.-с, 18-20,
43. Здоров А.И., Шокотова Б,Г., Феднер Л.А,, Васильев Ю.Э. Малоэнергоемкий цемент для тепловлажностной офаботки. /7 Цемент. 1989. – №3. – с. 1920.
44. Юникура Ашу. Применение тонкоддсперсного кремнезема в бетоне. // Технологии Японии.- 1989,-26, № 7,- с, 512-519.
45. Жакибеков Ш.К., Сулейманов А.Т. Влшнне кварцсодержаш,их отходов на процесс твердения и свойства цемента.// Комплекс, использ. минерал, сырья. -1988,-КйЗ,-с. 59-61,
46. Юхикава X. Влияние добавок на гидратащио смешанных цементов и формирование их структуры. // Сементо конкурито. 1987. – № 486. – с. 35-47.
47. Крамар Л.Я., Трофимович Б.Л., Талисман Л.С., Иванов Ф.М., Колбасов В.М. Влияние добавт микро1фемнезема на гидратацшо алита и судьфатостонжость цементного камня. /7 Цемент. -1989. № 6. – с. 14-17.
48. Доброщ)авова Л.А., Манохина О.Н., Советьнжова Н.К. Роль полуфункциональных добавок в формировании структуры высокопрочгшх цементов. // Тр. Моск. хим.-технол. ин-т. 1987. – № 146. – с. 92-97.
49. Кузнецова Т.В., Добронравова Л.А., Советникова Н.К. Влияние модифицированной 1фемнеземсодержащей добавки на процесс твердения цементных систем. // Ж. прикл. химия. 1987. – 60, Ш 10. – с. 2351-2354.
50. Назърскй Д., Крумов В. Влияние микрокремнезема на гиАофизические свойства бетона. /7 Год. Внеш. инст. архнт. и строит. София. Св. 7. 1988. – № 33. – с. 119-124.
51. Какузаки М. Исследование высокопрочного бетона с добавками микро-1фемнеземистого пылеуноса квасцов и золы-уноса. /7 Сементо конкурито. 1987. – № 483,-0.36-47.
52. Краснов A.M., Журавлев В.Г., Аганнна СВ., Новожилова Е.П. Бетонная смесь. // Map. политехи, ин-т. A.c. 1310362, СССР. Заявл. 30.10.84, № 3807224/29 -33, опубл. в Б. И., 1987. – № 18. – MICH С 04 В 28/00.
53. Кита Цутому, Сакаи Эцуро. Цементная композиция. // Дэнкн караку коге кк. Заявка 61-219749. Заявл. 23.03.85. -№ 60-58715, опубл. 30.09.86. МКИ С 04 В 28/02, С 04 В 14/04.
54. Омельченко В.В., Семиндейкин В.Н., Длогов Е,Я., Бахарев М.В,, Юдо-вич Б.Э., Птицьш В.В., Венидиктов В.Н. Добавка термообработашюй опоки повышает активность цемента. // Цемент. 1988. – № 4.- с. 20.
55. Пащенко A.A., Мясникова Е.А., Шкарунина Т.Н. Безгипсовые цементы с добавками отходов химического гАизводства. // Цемент. -1988. № 8. – с. 17-18.
56. Шпьшова Л.Т., Петрушко И.М., Сашщкий Ш.А. Эффективное вяжущее для зимнего бетонирования. // Цемент. 1988. – № 2. – с. 20-22.
57. Чинмай 3., Рамачандрш B.C. Влияние наполнителя из карбоната кальция на гидратацию трехкальциевого еилюсата. // Силикат. 1988. – 16, Жя. 2. – с. 110117,
58. Ramachandran V.S. Themial analyses of cement components hydrated in the presence of calcinm carbonate. // Thermochim. acta. 1988. – 127. – s. 385-394.
59. Оши К., Кату Ж., Кавашума К., Сон Т. Основные свойства бетона с из-вестшковым заполкителем. /7 Сэменто конкурито. 1987. – с. 108-120.
60. Пальгунов П.П., Сумароков М,В, Утилизация промышленных отходов, М,: Стройнздат. 1990. – с, 351.
61. Утилизшщя твА)дых отходов //Под редакцией Внлсона Д.В., М.: Стройнздат. Т.1. – 138 с,
62. Завадский В.Ф., Белан В.И,, Кучерова Э.А. Технология стеновых материалов// Новосибирск. 1993.-89 с.
63. Винокуров О.П, Опыт гфоизводства и применения неавтоклавных ячеистых бетонов// Строительные материалы.- 1986. №. 7.-е 6-8.
64. Сиротин Б,Я., Петров И,В. и др. Применение неавтоклавного газоло-бетона в сельском строительстве.// Бетон и железобетон. -1989. №7.- с. 23-25.
65. Болдырев А.с, Волженский А.В. и др. Строительные материалы на основе отходов производства.// Строительные материаж- 1991. № 1. – с. 2-4.
66. Волженский А.В., Иванов И.И. и др. Применение зол и шлаков в производстве строительных материалов, М,: Стройнздат, -1984 . – 247 с.
67. Галибина Е.А. Автоклавные строительные материалы из отходов ТЭЦ. /7 -Л. -1986.- С.127.
68. Состав и свойства золы и шлака ГЭС. Справочное пособие под редакцией В.А. Мелентьева.// Л.: Энергоатомиздат. 1985.
69. Экономическая эффективность использования вторичных ресурсов в производстве строительных материалов. Под редакгщей Ю.А. Алехина. //М.: Стройнздат. 1988.
70. Бабичев К.В., Герти Н. Золы и шлаки в производстве строительных материалов. // 1Си€в. -1987.
71. Элизон М.П. Топлнвосодержащие отходы промышленности в производстве строительных материалов.// М.: Стройнздат. 198А0.-с. 234.
72. Виноградов В.Н. Влияние заполнителей на свойства бетона. // М.: Стройнздат. 1986. – С.224.
73. Комар А.Г., Баженов Ю.М., Сулименко Л.М. Технология производства строительных материалов. // М.: Высшая школа. -1990. с. 446.
74. Горчаков Г.И., Баженов Ю.М. Строительные материалы. // М.: Стройнздат. 1986. – 668 с.
75. Костин В.В. Легкие бетоны неавтоклавного твердения. // Заявка № 93011869/33 от 04.03.1993 г. (011282) МКИ С04В28/15.
76. Элизон М.П. Топливосодержащие отходит промышленности в производстве строительных материалов.//М.: Стройнздат. -1980.-234 с.
77. Кокубу И.М., Ямара Д. Зола и зольные цементы. Цементы с добавкой водАт V и VI МеждЗ(Пародный конгресс по химии цемента. М.: Стройнздат. – 1979. – 224 с.
78. SS. Иванов И.А. Легкие бетоны с нршенением зол электростанций. IM.: Стройнздат. -1986. -138 с.
79. ГОСТ 30108-94 “Материалы и изделия строительные. Определение удежной эффективной актишости естественных радаонуклвдов”.
80. Вожкенский A.B. Бетоны и изделия из шлаковых и зольных материалов.// М. 1969.- с. 54-58.
81. Конусова Г.И., ИвашАенко E.H. Основы плашфования инженерного эксперимента в строительстве.// Новосибирск. -1991.- с. 40-76.
82. Пальгунов П.П., Сумароков М.В. Утилизация промышленных отходов.// М.: Сзройиздат. 1990. – 352 с.
83. Горчаков Г.И., Баженов Ю.М. Строительные материалы. // М.; Сгрониздат. 1986. – с,662-671.
84. Иванов И.А. Технология легких бетонов на искусственных пористых заполннтелях//М.: Стройнздат.-1974.-287 с.
85. Рудаи Д. Легкий бетон М.: Стройнздат, 1964.-240 с.
86. Завадский B.C. Автоклавные газобетотш М.: Госетройиздат, 1957.-156 с.
87. Белан В.И,, Ерлина Н.Ф. Использование отходов деятельности человека в гроизводстве строительных материалов. НовосибАск, НГАС, 1997. 72 с.
88. ЮУДАРСТВЕННАЯ САНИТАРНО-ЭПИДЕМИОЛОГИЧЕСКАЯ СЛУЖБА1. РОССИЙСКОЙ ФЕДЕРАЦИИ
89. ГЛАВНЫЙ ГОСУДАРСТВЕННЫЙ САНИТАРНЫЙ ВРАЧпо Новосибирской области•г. нимнвне тецицщ вещж)еАНИТАРНО-ЭПИДЕМИОЛОГИЧЕСКОЕ ЗАКЛЮЧЕНИЕ
90. ПЯЮТСЯ (перечислить рассмотренные протоколы исследований, наименование учреждения, ?в”одившего исследования, другие рассмотренные документы):
91. Щ-4УСЭН в Новосибирбкой-облаети закл.отчет Новосиб.НИИ гигиены, 1995г., этокол №96/3 от 21.03.01 ИЛЦ ННИИГ (аттестат аккредитации ГСЭН.Ки.ЦОА.235 от 11.02.99 в Госреестре №РОСС Ки.ООО 1.511656 от 11.02.99).10056059
92. НИСТЕРСТВ0 ЗДРАВООХРАНЕНИЯ РОССИЙСКОЙ ФЕДЕРАЦИИ
93. УДАРСТВЕННАЯ САНИТАРНО-ЭПИДЕМИОЛОГИЧЕСКАЯ СЛУЖБА1. РОССИЙСКОЙ ФЕДЕРАЦИИ
www.dissercat.com