Лазерная резка металла – преимущества и недостатки технологии
Из школьного курса элементарной физики вы знаете о сильном тепловом воздействии сфокусированного света. Познавательный трюк с увеличительным стеклом ясно показывает возможности преломленного потока солнечного луча.
Принципом действия работы лазера может служить его перевод с английского: усиление света вынужденным излучением. По-простому — это световое излучение, вызванное атакой фотонов на рабочую среду с усилением за счет ответной реакции. Световой поток через систему оптических призм и зеркал фокусируется в узконаправленный луч импульсной или непрерывной модуляции. Мощность и интенсивность лазера зависит от используемого активатора и сложности резонирующих систем.
В качестве первичного активного вещества используют все возможные агрегатные состояния: твердое, газообразное, жидкое и плазменное. Важнейшим критерием является способность к возбуждению и отдаче свободных квантов-фотонов. Накачка первичных световых атомов производится разными способами. Это может быть сфокусированное солнечное излучение, специальные лампы, другие лазеры, электрическое воздействие или химические процессы. Для увеличения силы потока делают многоуровневые атакующие каскады. В основе резонаторов применяют плоскопараллельные и сферические зеркала или их комбинации. Главный параметр хорошего прибора — устойчивое сохранение светового луча и его точная фокусировка.
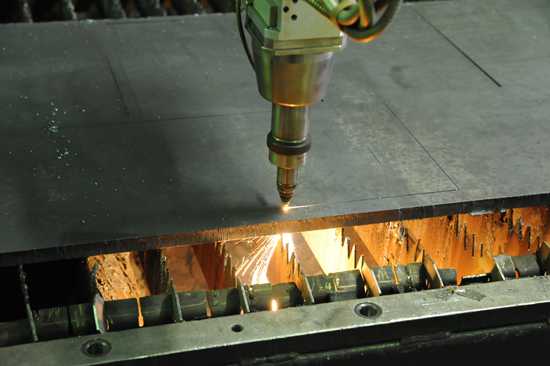
Принцип лазерной резки
Первый лазер был сделан на рубине в 1960 году, он работал в инфракрасном диапазоне и являлся началом эры световых помощников человека. История развития прикладной квантовой науки шла по пути усиления первоначальных систем накачки и совершенствования оптических резонаторов для достижения мощного и управляемого луча. Выискивались новые рабочие среды, были испробованы и получили путевку в жизнь лазерные установки на красителях, на свободных электронах, химические модели и полупроводниковые исполнения.
Производственное использование лазера
Лазер называют самым красочным и одним из важнейших изобретений XX века. Многие годы никто не понимал его практического применения, прибор называли устройством, которое само ищет задачи для решения. Теперь лазерные аппараты лечат людей, исследуют звезды и применятся для развлекательных мероприятий.
Машиностроительные производства давно начали использовать резку металла лазером. Пионерами выступили судостроительные верфи, авиационные заводы и автомобильные гиганты, искавшие передовые методы работы для увеличения производительности труда. Возрастающая конкуренция стимулировала появление инновационных обрабатывающих центров с принципиально новыми системами влияния на рабочий процесс.
К настоящему времени на промышленных предприятиях лазерная резка металла представлена следующими видами установок:
- твердотельные — основанные на кристаллических драгоценных камнях или соединениях редкоземельных элементов, для накачки фотонов используется импульсные лампы или лазерные диоды;
- газовые — в качестве активаторов применяются смеси инертных газов с источником возбуждения в виде электрических разрядов или направленной химической реакции;
- волоконные — активная среда и резонатор сделаны целиком из оптического волокна или скомбинированы с другими конструктивными элементами.
Следующее видео представляет волоконный лазерный станок.
Для работы с цветными металлами и антикоррозионными сталями, имеющими высокую отражающую способность, прикладными исследовательскими институтами разработаны специальные модели традиционных лазеров с резонатором из оптико-волоконной трубки. Световой луч в таких установках более сфокусированный и концентрированный и не рассеивается о зеркальную поверхность алюминиевых, титановых или нержавеющих заготовок.
Широко распространенные газовые СО₂-лазеры работают на рабочей смеси углекислого газа, азота и гелия, зеркала резонатора покрыты серебряным или золотым напылением для увеличения отражающей способности.
Технология лазерной резки металлов постоянно совершенствуется: пробуются новые типы установок, усложняются системы управления процессом, применяются компьютерные комплексы для контроля режимов обработки. Основной упор делается на увеличение точности, чистоты реза и производительности.
Особенности технологического процесса
В результате воздействия светового луча материал заготовки проходит несколько промежуточных изменений для превращения в обработанную деталь:
- первая стадия — воздействие лазера на металл в точке начала реза вызывает нагревание вещества до температуры плавления и появлению усадочной раковины;
- вторая стадия — энергия излучения приводит к кипению и испарению металла;
- третья стадия — при проплавлении заготовки на полную глубину начинается поступательное движение рабочего органа в соответствии с заданной траекторией.
В действительности, процесс испарения металла наблюдается только у тонких заготовок, при средней и большой толщине реза удаление остатков вещества из рабочей зоны производится с помощью струи вспомогательного газа (азот, кислород, воздушная смесь или инертные газы).
Такие установки, работа которой представлена на видео, называют газолазерными резаками.
Активный кислород, подаваемый в зону резания не только выводит продукты плавления металла и охлаждает поверхность среза, но и способствует поддержанию температуры и ускоряет режимы обработки. При лазерной резке не происходит деформации заготовки, следовательно, отсутствуют затраты материала на припуск линейных размеров и необходимость в дополнительных чистовых операциях.
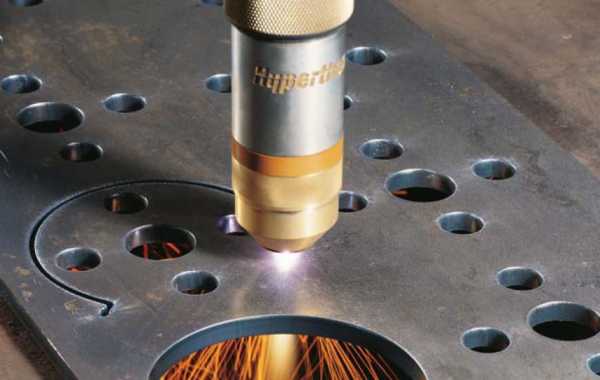
Сравнительные характеристики лазерной и плазменной резки приведены
Современные лазерные комплексы
Мировая станочная индустрия идет в ногу со временем и предлагает своим потребителям самое разнообразное оборудование для лазерной резки металла. Многокоординатные аппараты призваны заменить шумные и низко производительные механические резаки. Мощность лазера зависит от специфики производства и экономического обоснования выбранного агрегата.
Новое поколение прецизионных обрабатывающих станков с ЧПУ позволяют проводить обработку материалов с точностью до 0,005 мм. Площадь обработки некоторых моделей лазерных установок достигает нескольких квадратных метров. Большим достоинством является минимизация человеческого фактора, заключающаяся в высокой автоматизации производственного процесса.
Геометрия детали задается в программный блок, осуществляющий управление лазером и рабочим столом с заготовкой. Системы настройки фокуса автоматически выбирают оптимальное расстояние для эффективного резания. Специальные теплообменники регулируют температуру лазерной установки, выдавая оператору контрольные данные текущего состояния инструмента.
Лазерный станок оснащается клапанными механизмами для подключения газобаллонного оборудования, чтобы обеспечить подачу вспомогательных газов в рабочую зону. Система дымоулавливания призвана оптимизировать расходы на вытяжную вентиляцию, включая её непосредственно в момент обработки. Область обработки полностью экранируется защитным кожухом для безопасности обслуживающего персонала.
Лазерная резка листового металла на современном оборудовании превращается в легкий процесс задания числовых параметров и получения на выходе готовой детали. Производительность оборудования напрямую зависит от параметров станочного комплекса и квалификации оператора, создающего программный код. Технология лазерной резки металлов гармонично вписывается в концепцию роботизированного производства, призванного полностью освободить человека от тяжелого труда.
Производители предлагают различные типы лазерных станков: универсальные и специализированные. Стоимость первых на порядок больше, но они позволяют производить несколько операций и выпускать детали более сложной формы. Большое количество рыночных предложений дает возможность выбора для заинтересованных потребителей.
Преимущества и недостатки
Специалисты машиностроительных предприятий понимают перспективы использования данной технологии для получения точных деталей с хорошей шероховатостью. Область применения обширна: от простого раскроя листового металлопроката до получения сложных кузовных деталей автомобилей. Явные плюсы лазерной резки металлов сводятся к нескольким резюмирующим аспектам:
- высокое качество обработанной поверхности;
- экономия материала;
- способность работы с хрупкими материалами и тонкими заготовками;
- возможность получения деталей сложной конфигурации.
Среди минусов: высокая стоимость оборудования и расходных материалов.
Лазерная резка стали и цветных металлов пользуется большим рыночным спросом. Способность быстро выдавать чистовые детали нестандартной формы привлекает в профильные предприятия заказчиков малых партий разнообразных изделий. Лазерные технологии активно используются в декоративном творчестве при изготовлении дизайнерских украшений и оригинальных сувениров.
Решение о применении лазерной обработки должно приниматься с учетом расчета окупаемости оборудования и величине эксплуатационных расходов. В настоящее время такие установки могут себе позволить, в основном, крупные предприятия с большим производственным циклом. С развитием технологии будут снижаться стоимость станков и количество потребляемой энергии, поэтому в будущем лазерные аппараты вытеснят своих конкурентов из сферы резки любых материалов.
wikimetall.ru
Принцип работы станков по лазерной резке металлов
Суббота, 5 Сентябрь, 2015
При обработке металла часто требуется его резка. Для обработки металла было придумано большое количество различных методов его резки. Наиболее современным и технологичным методом резки металла является лазерная резка.
Принцип действия лазера
В состав лазера, генерирующего световое излучение, входит рабочее тело, генератор накачки, резонатор и другие вспомогательные элементы. Лазеры бывают следующих видов:
- твердотельный лазер;
- газовый;
- волоконный.
В твердотельном лазере в качестве генерирующего тела используется твердотельный элемент, например, рубин. Лампа накачки вырабатывает световое излучение, которое поглощается рубином, атомы которого возбуждаются и выделяют большое количество световой энергии.
В газовом лазере рабочим телом является газ. Этот газ проходит через газоразрядную лампу, в которой происходит электрический разряд, возбуждающий атомы газа. Наиболее эффективными являются газовые лазеры на углекислом газе.
Волоконный лазер состоит из генератора накачки на светодиоде, световода, в котором происходит генерация, и резонатора.
Преимущества лазерной резки
На станках лазерной резки можно обрабатывать металлы с различными физико-механическими свойствами. К ним относятся:
- сталь;
- нержавеющая сталь;
- алюминиевые сплавы;
- латунь;
- медь;
- сплавы из титана.
При этом для различных типов металла необходимо использовать лазеры различной мощности и разный режим резания. Лучше всего обрабатываются материалы с малой теплопрводностью. Такие материалы как латунь и медь имеют большую теплопроводность, поэтому для их резки требуется повышенная мощность лазера. Наиболее трудной является резка листов из сплавов таких материалов как титан. Этот металл имеет хорошую теплопроводность и отражательную способнось, а кроме того, он очень прочный и быстро окисляется. Для его резки требуется мощный лазер и продувка места резки инертными газами для защиты от окисления.
Использование станков для лазерной резки металлов имеет следующие преимущества:
- возможность обработки металлов с различными свойствами;
- высокая скорость резания металла;
- возможность обработки сложных контуров;
- минимальное механическое воздействие на металл;
- использоание компьютеризированного управления.
Конструкция станка
В состав современного станка для лазерной резки металла входят:
- лазерный источник;
- станина;
- приводы и передачи;
- система охлаждения;
- система подачи газа и дымоудаления;
- система автоматического управления;
- программное обеспечение.
Чаще всего в станках для резки металлов используются волоконные и газовые лазеры. В волоконном лазере формирование луча происхоит в волоконном резонаторе, а затем энергия луча по волоконному тракту передается к режущей головке. В газовом лазере луч формируется в резонаторе с газами, а затем с помощью системы зеркал энергия луча передается в головку. Режущая головка включает набор линз. Луч этой головки автоматически фокусируется.
В зависимости от типа станка мощность таких лазерных источников может достигать 4-6 кВт. При этом кпд лазеров не превышает 10-15 %.
Станина представляет собой цельносварную конструкцию, которая должна быть жесткой, надежной и долговечной.
Приводы станка должны обеспечивать быстрое и точное передвижение координатой системы станка. Эти приводы мощные и не имеют люфта. Для примера, в станках компании Mitsubishi точность положения режущей головки по каждой из осей должна быть порядка ±0,01 мм. Максимальная скорость резания в таких станках достигает 50 м/мин.
В процессе резки металла требуется охлаждение лазерного источника. Это охлаждение бывает воздушным или водяным.
Для удаления продуктов резания рабочая область резания снабжается продувкой технологичекими газами. В качестве такого газа может быть использован сжатый воздух. А для удаления возникающего при резании металла дыма имеется специальная система.
Для управления такими мощными и скоростными станками необходима современная система управления. Система управления станком для резки металла лазером представляет собой компьютиризованную систему типа ЧПУ. В ее состав входит процессор, память, монитор, программное обеспечение. Управление режущей головкой осуществляется по 3 осям, при этом для управления по оси Z (регулировка высоты) используется обратная связь. Для определения положения лазерного луча используются специальные датчики.
Программное обеспечение станка обычно реализуется на основе стандартной операционной системы, например, Windows. В комплект программного обеспечения, как правило, входит большое число программ. Дополнительные программы могут вводиться с локальной сети предприятия или с помощью разъема USB.
Выводы:
- Наиболее эффективным способом резки металлов является лазерная резка.
- Лазерная резка обладает рядом преимуществ, основными из которых является точность, высокая скорость резания и возможность автоматизации процесса.
- Современные станки для лазерной резки представляют собой сложные комплексы, позволяющие быстро и точно производить сложную резку различных металлов.
mk-madis.ru
принципы работы, виды и особенности
Лазерную резку используют для раскроя листовых материалов, чаще всего – металлов. Одно из ее главных отличий – возможность изготовления деталей со сложным контуром.
Принципы работы лазерной резки
Использование этого метода основано на тепловом воздействии лазерного излучения на материалы. При этом разрезаемый металл нагревается сначала до температуры плавления, а потом до температуры кипения, при которой он начинает испаряться. Лазерная резка испарением требует высоких энергозатрат, поэтому ее используют для работы с тонкими металлами.
Относительно толстые листы разрезают при температуре плавления. Чтобы облегчить этот процесс, в зону резки подается газ: азот, гелий, аргон, кислород или воздух. Его задача – удалять из зоны резки расплавленный металл и продукты его сгорания, поддерживать горение металла и охлаждать прилегающие зоны. Наиболее эффективен для этого кислород. Он заметно увеличивает скорость и глубину резки.
Подробнее о процессе лазерной резки можно узнать из видео ниже:
Параметры резки разных металлов
Скорость резки зависит не только от мощности лазера и толщины металла, но и от его теплопроводности. Чем она выше, тем интенсивнее отводится тепло из зоны резки и тем более энергозатратным будет весь процесс. Так, если лазером мощностью 600 Вт можно легко разреза́ть черные металлы или титан, то алюминий или медь, обладающие высокой теплопроводностью, обрабатывать значительно сложнее. Средние параметры для работы с разными металлами выглядят следующим образом:
Малоуглеродистая сталь | Инструментальная сталь | Нержавеющая сталь | Титан | |||||||
Толщина, мм | 1,0 | 1,2 | 2,2 | 3,0 | 1,0 | 1,3 | 2,5 | 3,2 | 0,6 | 1,0 |
Мощность лазера, Вт | 100 | 400 | 850 | 400 | 100 | 400 | 400 | 400 | 250 | 600 |
Скорость резания, м/мин | 1,6 | 4,6 | 1,8 | 1,7 | 0,94 | 4,6 | 1,27 | 1,15 | 0,2 | 1,5 |
Виды лазерной резки
Лазерные установки состоят из трех основных частей:
- Рабочей (активной) среды. Она является источником лазерного излучения.
- Источника энергии (системы накачки). Он создает условия, при которых начинается электромагнитное излучение.
- Оптического резонатора. Система зеркал, усиливающих лазерное излучение.
По типу рабочей среды лазеры для резки делят на три вида:
- Твердотельные. Их основным узлом является осветительная камера. В ней находятся источник энергии и твердое рабочее тело. Источником энергии служит мощная газоразрядная лампа-вспышка. В качестве рабочего тела используют стержень из неодимового стекла, рубина или алюмо-иттриевого граната, легированного неодимом или иттербием. По торцам стержня устанавливают два зеркала: отражающее и полупрозрачное. Лазерный луч, излучаемый рабочим телом, многократно отражается внутри него, усиливается в ходе отражений и выходит через полупрозрачное зеркало.
К твердотельному виду относятся и волоконные лазеры. В них излучение усиливается в стекловолокне, а источником энергии служит полупроводниковый лазер.
Так устроен твердотельный лазер
Для понимания механизма работы лазера можно рассмотреть установку с рабочим телом в виде стержня из граната, легированным неодимом. Ионы последнего и служат активными центрами. Поглощая излучение газоразрядной лампы, ионы переходят в возбужденное состояние, то есть у них появляется излишек энергии.
Ионы возвращаются в исходное состояние и отдают энергию в виде фотона – электромагнитного излучения или по-другому света. Фотон вызывает переход в обычное состояние других возбужденных ионов. В итоге процесс нарастает лавинообразно. Зеркала способствуют движению луча в определенном направлении. Многократно возвращая фотоны в рабочее тело при отражении, они способствуют образованию новых фотонов и усилению излучения. Его основные характеристики – малая расходимость луча и высокая концентрация энергии.
- Газовые. В них рабочим телом является углекислый газ или его смесь с азотом и гелием. Газ прокачивается насосом через газоразрядную трубку. Он возбуждается с помощью электрических разрядов. Для усиления излучения устанавливают отражающее и полупрозрачное зеркало. В зависимости от особенностей конструкции такие лазеры бывают с продольной и поперечной прокачкой, а также щелевые.
Так устроен газовый лазер с продольной прокачкой
- Газодинамические. Эти лазеры самые мощные. В них рабочим телом является углекислый газ, нагретый до 1 000–3 000 °К (726–2726 °С). Он возбуждается с помощью вспомогательного маломощного лазера. Газ со сверхзвуковой скоростью прокачивается через суженный посередине канал (сопло Лаваля), резко расширяется и охлаждается. В результате его атомы переходят из возбужденного в обычное состояние и газ становится источником излучения.
Схема работы газодинамического лазера
Преимущества и недостатки лазерной резки
Можно выделить следующие преимущества лазерной резки металлов:
- Нет механического контакта с поверхностью разрезаемого металла. Это делает возможным работу с легкодеформируемыми или хрупкими материалами.
- Можно разрезать металлы разной толщины. Сталь в пределах 0,2–30 мм, алюминиевые сплавы – 0,2–20 мм, медь и латунь – 0,2–15 мм.
- Высокая скорость резки.
- Возможность изготовления изделий с любой конфигурацией.
- Чистые кромки разрезаемого металла и низкое количество отходов.
- Высокая точность работы – до 0,1 мм.
- Экономный расход листового металла за счет более плотной раскладки деталей на листе.
Недостатками лазерной резки считаются высокое энергопотребление, дорогое оборудование.
Назначение и критерии выбора лазерной резки
Лазерную резку используют для обработки не только металлов, но и резины, линолеума, фанеры, полипропилена, искусственного камня и даже стекла. Она востребована при изготовлении деталей для различных приборов, электротехнических устройств, сельскохозяйственных машин, судов и автомобилей. Такой способ раскроя материала используют для получения жетонов, трафаретов, указателей, табличек, декоративных элементов интерьера и многого другого.
Основной критерий выбора вида лазерной резки – тип обрабатываемого материала. Так, углекислотные лазеры подходят для резки, гравировки, сварки разных материалов – металла, резины, пластика, стекла.
Твердотельные волоконные установки оптимальны при раскрое латунных, медных, серебряных или алюминиевых листов, но не подходят для неметаллов.
zmkmsk.ru
Принцип работы станков лазерной резки | RuAut
Недостатками механических методов резки являются: потеря материала, низкая производительность процесса, износ и поломка инструмента. Все это результат контакта инструмента с материалом. Основные недостатки термических методов резки: низкое качество реза и невозможность обработки не металлических материалов. Здесь бессильны и газопламенная и плазменные технологии. Лазерной резки поддаются практически все материалы независимо от твердости. Благодаря отсутствию механических усилий, могут разрезаться не жесткие материалы. А жесткие должны быть лишь зафиксированы без специального закрепления.Процесс лазерной резки легко автоматизировать. В состав автоматизированного станка для лазерной резки входят: лазер с источником питания, тракт передачи излучения в зону обработки, система управления. По механизму воздействия на материал лазерный луч аналогичен газовому пламени и плазменной дуге. Это тепловой источник. Однако концентрация его мощности на несколько порядков выше и составляет 100 000 … 10 000 000 Вт/кв.см. Благодаря этому, обеспечивается высокая скорость резки, получение узкого разреза, минимальная протяженность зоны термического влияния, отсутствие деформации и крапления.
Сущность лазерной резки состоит в расплавлении, разложении или испарении материала и удалении продуктов разрушения из канала реза. При работе станка лазерной резки в режиме испарения поверхность материала разогревается до температуры кипения и вещество из канала реза удаляется в парообразном состоянии. Механизм испарения характерен для материалов у которых удельная энергия испарения мало отличается от удельной энергии плавления. И как правило реализуется реализуется при облучении короткими импульсами с высокой плотностью мощности. Лазерная резка в режиме плавления характерна для металлов при действии на них непрерывного излучения. Для удаления расплава в зону обработки станка лазерной резки подается струя газа. Этот режим при низких скоростях резки характеризуется периодическим протеканием процесса образования и удаления расплава. Качество реза при этом невысокое. Увеличение скорости резки переводит процесс в стационарный режим. Качество реза в стационарном режиме повышается. Подача кислорода в зону обработки при резки например низкоуглеродистых сталей или титана за счет энерго вклада эзотермической реакции горения позволяет увеличить скорость резки в 1.5 … 2 раза. При резке ряда полимерных материалов возможно образование слоя угля на кромках резки. Его толщина может быть значительно снижена при использовании нейтрального газа.
Для подачи газа в зону лазерной резки применяют специальные сопла. При сверхзвуковых скоростях потока у кромки детали может появиться скачок уплотнения, ограничивающий скорость газа в канале реза. Оптимальное давление обеспечивающее максимальную кинетическую энергию потока составляет около 0.2 МПа.
Существенное влияние на производительность процесса и качество работы станка лазерной резки оказывает распределение плотности мощности лазерного пучка. Оптимальным распределением плотности мощности считается нормальное или гауссовое. Важное значение имеет ориентация плоскости поляризации лазерного луча, определяемое положением вектора напряженности электромагнитного поля относительно направления резки. Максимальная скорость лазерной резки, минимальная ширина зоны термического влияния и параллельность кромок достигаются при совпадении плоскости поляризации и направления резки, когда энергия выделяется в основном только на лобовой поверхности резки. Поэтому при резки металлов по сложному контуру, поляризация должна быть или круговой или линейной, плоскость которой синхронно поворачивается с изменением траектории движения.
С увеличением мощности лазерного излучения глубина прорезания увеличивается, достигая 10-12 мм для металлов. И 50-60 мм для неметаллических материалов. Поэтому наиболее эффективна лазерная резка при изготовлении деталей сложного контура из листовых материалов, соответствующих диапазону толщин. В станках лазерной резки применяются твердотельные лазеры периодического действия, газовые лазеры непрерывного действия, твердотельные лазеры непрерывного действия.
От декоративных элементов садовых домиков до разнообразных деталей современных машин, таков диапазон применения станков лазерной резки.
ruaut.ru
Лазерная резка. Основы и принцип работы лазеров.
Этот материал открывает цикл статей, посвященных лазерной резке. Признаюсь честно, я долго не решался приступить к этой обширной, сложной и головокружительно интересной теме. Лазерная резка – это наиболее современный тип обработки тонколистового металла, наиболее наукоемкий, а также наиболее развивающийся и перспективный. Куда ни посмотри – сплошные преимущества, но не все так просто… Давайте постепенно разбираться.
Не знаю как у вас, но у меня прежде всего лазеры ассоциируются с фильмом из детства. Помните “Гостью из будущего”? Как залихватски стреляли лазерными лучами космические разбойники. Помню, тогда на меня это произвело неизгладимое впечатление.
Но что же такое лазер? Само понятие произошло от английской аббревиатуры LASER (Light Amplification by Stimulated Emission of Radiation) что означает “усиление света с помощью вынужденного излучения”. То есть лазер – это устройство, контролирующее силу света, усиливающее и подчиняющее ее. Звучит неправдоподобно и даже как-то пафосно, но, тем не менее – это абсолютная правда. Главная миссия любого лазера – создать как можно более согласованный поток света с максимально возможным КПД (коэффициентом полезного действия).
Вне зависимости от типа и сферы применения любой лазер имеет три основные составляющие: активную среду, резонатор и систему накачки.
Активная среда – это вещество, в котором искусственным образом накапливается и высвобождается энергия атомов. Накопление и высвобождение энергии происходит за счет ее перехода на разные уровни. Чем выше уровень, тем энергия больше и наоборот. Что характерно, атомы всегда стремятся вернутся к базовому низкому значению энергии, при этом отдают ее в пустоту без всякого зазрения совести. Так вот, в активной среде создаются все условия для взращивания энергии. В такой ситуации атомов с высокой энергией больше, чем атомов с низкой. Затем среда возбуждается электромагнитной волной и энергия высвобождается.
Для того чтобы освобожденную энергию многократно увеличить используется резонатор. Грубо говоря, это два параллельных зеркала. Одно зеркало глухое (не пропускающее свет), другое – полупрозрачное. Между зеркалами располагается уже знакомая нам активная среда. Энергия возвращается, отражаясь от глухого зеркала и поступает куда следует через полупрозрачное зеркало. Причем, понятно, что полупрозрачное зеркало пропускает только энергию определенных значений – достаточно больших.
Ну а система накачки – это то, что возбуждает энергию атомов. Тут все зависит от типа лазера. В твердотельных и жидкостных лазерах используют импульсные лампы или лазеры, газовые среды возбуждают электрическим разрядом, полупроводники – электрическим током и так далее.
Несмотря на то, что все кажется простым на первый взгляд – все очень сложно. Ведь в этих процессах великое множество нюансов и тайн. И ничего тут не поделаешь – квантовая физика! Этим все сказано.
Ниже представлена принципиальная схема лазера:
1 – активная среда; 2 – энергия накачки лазера; 3 – непрозрачное зеркало; 4 – полупрозрачное зеркало; 5 – лазерный луч.
Таким образом, мы разобрались, что такое лазер и рассмотрели основы его функционирования. Дальше поговорим об основных типах лазеров. Будет еще интереснее.
При подготовке информации я использовал: 1. П.Г. Мазеин, М.Р. Ахметов, С.Р. Сайфутдинов «Применение станков лазерной резки», 2011; 2. О.Б. Ковалев, В.М. ФОМИН «Физические основы лазерной резки толстых листовых материалов», 2013г. 3. А.Г. Григорьянц, А.А. Соколов «Лазерная резка металлов», 1988г.
mehanolog.ru
Технология и виды лазерной резки металла
Резка металла лазером — один из наиболее экономичных и эффективных способов металлообработки. Кроме этого, лазерная резка обеспечивает высокую скорость и точность раскроя металлического листа. Технология применяется на промышленных предприятиях, специализирующихся на металлообработке.
Как выполняется резка металла лазером
Лазерная резка основана на эффекте отражения и поглощения высокоимпульсного луча. Под действием излучения высокой интенсивности твёрдый материал быстро набирает температуру собственного плавления и испарения.
Подробнее процесс выглядит следующим образом:
- Луч лазера воздействует на металлическую заготовку, формируя на её поверхности точку небольшого диаметра.
- В месте воздействия лазера происходит быстрый нагрев и плавление материала.
- В точке воздействия возникает углубление.
- Под действием мощной энергии луча металл начинает испаряться, обеспечивая раскрой заготовки.
Стоит учитывать, что кипения металла происходит только при резке тонких листов. Раскрой толстолистового металла осуществляется с привлечением газа, выдувающего расплавленные частицы с места реза. Широко распространено применение кислорода, азота, инертного газа и воздушной смеси.
Типы лазерной металлообработки
Станок для раскроя метала лазером включает в себя основные узлы:
- Источник лазерной энергии, называемый системой накачки.
- Рабочее тело, излучающее под воздействием энергии.
- Оптический резонатор, представляющий собой систему зеркал.
Типы резки классифицируются по виду применяемого для проведения работ лазера, а также его мощности. Они разделяются на следующие группы:
- Твердотельные лазеры. Их мощность не может превышать 6 кВт.
- Газовые лазеры, мощность которых достигает 20 кВт.
- Газодинамические лазеры, мощность которых до 100 кВт и более.
На производстве традиционно применяются лазеры твердотельного типа. Лазерный луч подаётся ими непрерывно или в виде импульсов. Рабочее тело выполняется из рубина, неодимового стекла или же флюорита кальция (CaF2). Основное достоинство устройств этого типа — возможность выдачи импульса высокой мощности в течение долей секунд.
Лазерные установки газового типа используются для технической и научной металлообработки. Рабочее тело представляет собой газовую смесь с использованием азота, углекислоты и гелия. Под воздействием электроразряда атомы газов возбуждаются и формируют направленный монохроматичный луч.
Газодинамические типы лазеров относятся к наиболее мощным. Рабочим телом в них является углекислый газ, нагреваемый до максимальной температуры. Затем разогретый газ проходит через узкий канал, в котором осуществляется его расширение и резкое охлаждение. При этом выделяется большое количество энергии, которая направляется затем на проведение лазерной резки.
За счёт принципа действия и мощности, газодинамические лазеры могут быть использованы для металлообработки изделий любого типа. Малый расход энергии луча позволяет проводить резку металла на расстояние от головки лазера без снижения эффективности.
Где применяется лазерная резка
Производительность, максимальная точность и крайняя эффективность металлообработки с применением лазера обеспечили широкое распространение технологии во всех сферах. Она используется для получения изделий следующего типа:
- Деталей для машин и механизмов.
- Торгового и бытового оборудования и конструкций.
- Элементов систем отопления и водоснабжения.
- Элементов ограждений и ворот.
- Выпуска металлических изделий оригинальной формы.
- Производства высокоточных деталей.
Обработка металла лазером отличается массой преимуществ, по сравнению с традиционными видами металлообработки. Чем и обеспечивается её высокая популярность на предприятиях.
Статья подготовлена специалистами Antex-Lazer.ru
make-self.net
принцип работы и преимущества –
Лазерная резка – современная технология раскроя металла. Этот способ является очень быстрым, удобным и экономичным. Он позволяет изготавливать необходимые детали из металлических листов для приборов, корпусов, агрегатов и машин, торгового оборудования, строительных конструкций, элементов дизайна и рекламы.
Так, лазерная резка отличается от других способов тем, что с ее помощью все необходимые работы производятся максимально оперативно. Причем такая скорость позволяет создавать детали безупречного качества. А готовые изделия при этом отличаются достаточно приемлемой ценой, что очень важно для многих.
Стоит отметить, что резка металла лазером – это один из самых передовых способов обработки листовых материалов. Он используется чаще всего. Таким образом можно резать практически любой металл – от нержавеющей и черной стали до алюминия, а их толщина может быть даже более 15 миллиметров.
К достоинствам следует отнести и то, что раскрой необходимых деталей производится практически без помощи человека. Таким образом минимизируется влияние человеческого фактора на конечный результат. Все осуществляется благодаря специальному программному оснащению, которое имеет лазерное оборудование.
Принцип такой обработки достаточно специфичен. Так, в качестве инструмента используется лазерный луч, он нагревает и расплавляет металл по заранее заданной схеме. Лишний расплав удаляется оптикаструей газа или кислорода, который подается под высоким давлением.
Лазерный луч передается к поверхности обрабатываемого металла от неподвижного источника излучения с помощью особой системы, состоящей из зеркал и линз, которые движутся под управлением приводов с ЧПУ. Такой принцип профессионалы называют «летающей оптикой».
Кромка, создаваемая для новых деталей, получается очень четкой и без каких-либо неровностей и других дефектов, поэтому их дополнительная обработка не требуется. В результате общий цикл создания значительно сокращается. Сама точность обработки деталей составляет в пределах 0,1 миллиметра.
Как видно из всего вышенаписанного, достоинств и преимуществ у лазерной резки более, чем предостаточно. Принцип ее, несмотря на свою некоторую специфичность, является совсем несложным. Все в купе делает такой способ обработки металла самым популярным и демократичным по цене на сегодняшний день.
Просмотров: 4444
Дата: Четверг, 28 Февраля 2013
etalon-ufa.ru