Бизнес на производстве минеральной ваты
Производство минеральной ваты можно разбить на несколько стадий: подготовка сырья, получение волокна из расплава, полимеризация и нарезка готового материала. Минеральная вата на данный момент является отличным материалом, который имеет широкий спектр применения в различных отраслях.
- Что нужно знать о базальтовой минеральной вате перед началом производства
- Технология производства минеральной ваты
- Какое оборудование выбрать?
- Достоинства и недостатки бизнеса по производству минеральной ваты
Высокую эффективность применения данного материала специалисты отмечают и в строительной индустрии. Среди многообразия минеральной ваты, которая представлена на рынке строительных материалов, потребители выделяют уникальные свойства такого материала, изготовленного из базальтовых пород.
Что нужно знать о базальтовой минеральной вате перед началом производства
Данный материал имеет волокнистую структуру. Если перевести с английского языка «базальтовый утеплитель», то дословно можно получить «горная шерсть».
Именно из-за того, что структура материала имеет волокнистый компонент, в ней идет накопление воздуха в больших объемах. При этом такие объемы воздуха практически не перемещаются по толщине этого материала. Это объясняется наличием ряда препятствий в виде большого количества волокон. Такое свойство в комбинации с малым диаметром волокна дает возможность базальтовой вате иметь высокие теплоизоляционные свойства.
На данный момент специалисты выделяют два типа базальтовых волокон, которые встречаются в утеплителях:
- Штапельное волокно. Для данного типа характерным является его диаметр.
- Непрерывное волокно.
При этом сами базальтовые волокна, которые применяются в изготовлении минеральной ваты, могут иметь различные диаметры, от 0,6 мкм до 500 мкм.
Поэтому принято разделять волокна на следующие виды:
- Микротонкие с толщиной 0,6 мкм.
- Ультратонкие с диаметром порядка 1,0 мкм.
- Супертонкие. Их диаметр составляет 3 мкм.
- Тонкие с толщиной около 15 мкм.
- Утолщенные, в диаметре равные 25 мкм.
- Грубые. Такие волокна могут достигать в диаметре 500 мкм.
Во время процесса изготовления материал формируется в рулоны. Также часто применяется формирование его в плиты или маты. При этом материал подразделяется специалистами на нефольгированный и фольгированный виды.
Технология производства минеральной ваты
Способ, с помощью которого производится минеральная вата, был открыт на Гавайских островах. Это стало возможным, когда были найдены камни в результате извержения вулкана. Тогда нашли тонкие нити вулканической породы. Это были первые представители современных волокон, которые используются при изготовлении минеральной ваты. После этого в 1897 г. в Северной Америке получили и первую минеральную вату.
Для производства материала используется следующая технология:
- Применяется специальная печь, в которой температура достигает 1500°С.
- В печь помещается горная порода. Из нее выходит специальный огненный расплав в жидком виде.
- Далее происходит вытягивание такого расплава в волокна. Для этого применяется несколько способов, среди них центробежное дутье, простое дутье и модифицированные методы.
- Когда волокна уже сформированы, в них вводится специальное связующее вещество. Для этого может применяться технология распыления на волокна. Часто используют и полив на ковер из ваты базальтового типа. Есть еще вариант, связанный с приготовлением гидромассы.
- Чтобы минеральной вате придать дополнительные свойства при ее последующей эксплуатации, добавляется специальная смесь. Она позволяет улучшать показатели плотности, проницаемости, гидрофобности и ряд других характеристик.
- Полученный ковер, на который нанесено связующее вещество, обрабатывают термическим путем при температуре, достигающей 230°С. Это позволяет тепловому носителю провоцировать реакцию поликонденсации связующего элемента.
- Когда проведена термическая обработка базальта и туда добавлены необходимые примеси, то на выходе получаем продукт. Он имеет структуру, которая характеризуется ячеистой сеткой открытой формы. Такой продукт может работать на эффективном уровне при температуре, достигающей 1000°С. Это так называемый верхний предел рабочего диапазона температур минеральной ваты.
- В таком готовом продукте содержание веществ, имеющих органическое происхождение, не превышает обычно показателя в 3%.
- Теперь технология изготовления этого материала выходит на свою завершающую стадию. Производится нарезка в виде плит, которые необходимы для утепления. После этого выполняется упаковка материала и доставка потребителям.
Какое оборудование выбрать?
Оборудование для производства минеральной ваты состоит из шахтной печи, сушильных линий, подпрессовочного оборудования, камеры термообработки.
Достоинства и недостатки бизнеса по производству минеральной ваты
Бизнес на производстве и продаже минеральной ваты — это очень выгодно и не требует крупных вложений.
Данный продукт имеет отличные показатели в плане эксплуатации. Также данный утеплитель может эффективно применяться и при высоких температурах, которые характерны для мест с повышенным коэффициентом пожарной опасности.
Среди недостатков такого продукта специалисты отмечают свойство материала впитывать влагу. Это может значительно ухудшить его свойства тепловой изоляции, а в некоторых случаях привести и к их полной потере. Поэтому, чтобы исключить такие факторы, производители используют покрытия кашированного или алюминиевого типа.
Данный тип минеральной ваты активно используется в строительстве как эффективное средство, при помощи которого осуществляется тепловая изоляция помещений.
Перед тем как применять ее, необходимо обратиться за консультацией к специалистам, которые помогут эффективно организовать утепление дома.
vipidei.com
Тонкости производства минеральной ваты, этапы изготовления и лучшие производители утеплителя
Утепление — один из обязательных этапов жилого и промышленного строительства. И наиболее востребованным материалом на сегодняшний день является долговечная, негорючая, устойчивая к внешним нагрузкам и высокой влажности минеральная (каменная, базальтовая) вата. В чем секрет уникальных свойств современной теплоизоляции и через какие этапы должна пройти горная порода, чтобы превратиться в прекрасно сохраняющую оптимальную температуру в помещении базальтовая плита?
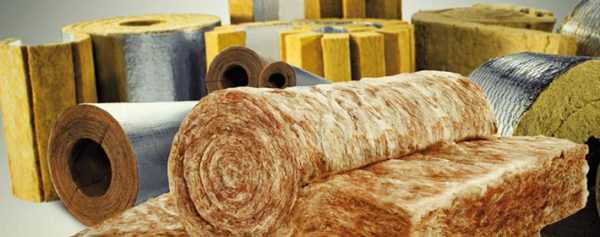
Содержание статьи
Технология производства
Производство минеральной ваты начинается с выбора основного материала. Лучшие производители для этого используют не только базальт, но и другие породы — доломит, известняк, диабаз, а также отходы до металлургии (шлак). Состав того или иного утеплителя всегда хранится в секрете, что делает каждую продукцию по-своему уникальной. От особенностей рецептуры зависит гигрофобность, прочность, устойчивость к химическим, биологическим и температурным воздействиям, вес и толщина утеплителя.
Этапы изготовления минваты
Изготовление плит или рулонной теплоизоляции проходит в несколько этапов, каждый из которых делает тепло- и звукоизоляционные характеристики материала максимальными.
- Порода плавится в вагранках или других специальных печах при температуре 1500 градусов.
- Полученный расплав раздувается струей сжатого воздуха или водяного пара. Такой способ называют дутьевым. Второй метод более дорогостоящий — центробежный. При этом волокна, которые в последующем становятся основой теплоизоляции, вытягиваются со скоростью от 3 до 8 тысяч оборотов в минуту при помощи центробежной силы в центрифугах.
- Ковер из каменных нитей поливается связующим веществом (акрилом, фенолом, битумом и т. д.).
- Формуется структура изделий, от которой будет зависеть сфера применения материала.
- Далее вату подвергают термообработке при 180-230 градусах для поликонденсации связующих компонентов.
- Плиты нарезаются, упаковываются и отправляются на склад или на прилавки строительных магазинов.
Как обеспечиваются теплоизоляционные свойства?
Отличной теплоизоляционной способностью каменный утеплитель обязан хаотичному расположению волокон. Между ними остаются небольшие заполненные воздухом ячейки, которые предупреждают теплоизлучение. В доме, утепленном минплитами, не только тепло зимой, но и прохладно летом.
Важно! Если волокна размещены преимущественно в вертикальном положении, устойчивость к механическим нагрузкам повышается. Такие плиты используются при наружных работах.
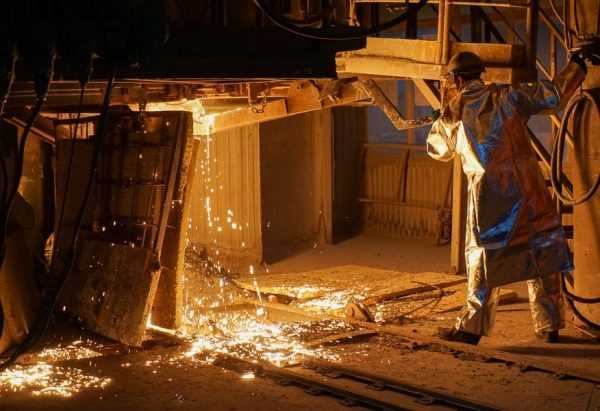
Популярные производители
На строительный рынок регулярно выходят новые компании, производящие теплоизоляционную продукцию. Однако список наиболее популярных брендов практически не меняется. В него входят:
- Rockwool;
- Isover;
- Knauf;
- Белтеп;
- Технониколь;
- Parok;
- Ursa.
Продукция от данных производителей имеет необходимые сертификаты качества, отличается долговечностью, простотой монтажа, износостойкостью при воздействии динамических, температурных и других нагрузок.
Заключение
При выборе теплоизоляции стоит отдавать предпочтение известным торговым маркам, использующим на своих предприятиях самые современные технологии. Как именно происходит создание утеплителя в промышленных масштабах можно узнать из следующего видео:
Вконтакте
Одноклассники
gipsohouse.ru
виды, работа с утеплителем, достоинства и недостатки
Вопрос утепления дома и защищенности его от постороннего шума всегда стоит на первом месте. Люди веками изобретали совершенные способы защиты своего жилища от зимней стужи и летнего зноя. Зачастую выбор падал преимущественно на источники тепла, например, огонь или обогреватель. Однако этот способ не позволял решить вопрос со звукоизоляцией. Но прекрасно достичь двух этих целей – сохранения тепла и обеспечения защиты от посторонних шумов – могут изоляционные материалы, основой которых является минеральная вата. Однако их выбирать следует внимательно и тщательно.
Содержание статьи:
- История возникновения
- Производство материала
- Разновидности
- Стекловата, шлаковая и каменная вата
- Достоинства
- Недостатки
- О чем следует знать при работе с материалом
- Принципы работы
- Марки плотности и область их применения
- Выбор минеральной ваты
История возникновения материала
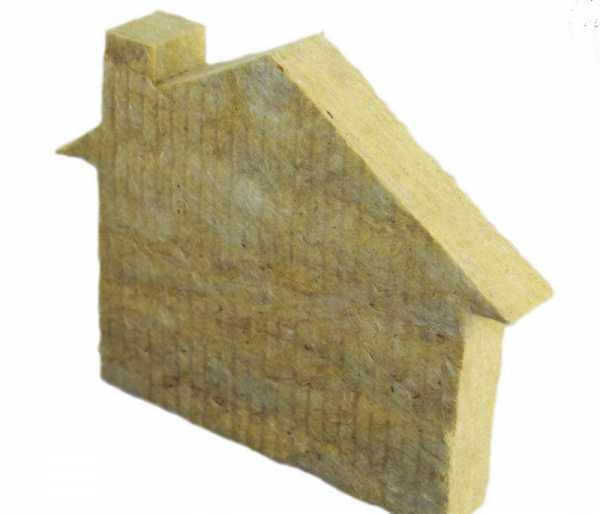
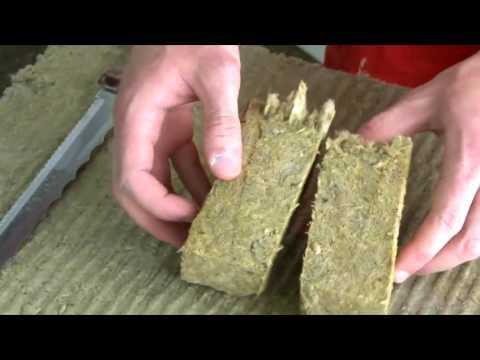
Материал обязан своим происхождением исключительно самой природе. В середине девятнадцатого века английский промышленник по имени Эдвард Перри заметил интересное явление в процессе извержения вулканов. Он обратил внимание, что помимо палящих туч и лавы, образуются особые тонкие нити из расплавленных брызг шлаков.
Промышленник решил, что такой материал станет прекрасным утеплителем. Тогда он воспроизвел процесс формирования нитей из шлака, однако допустил грубую ошибку. Производился материал в открытую, и часть волокон разлеталась по цеху, в результате чего некоторые рабочие пострадали. Тогда Перри отказался от своей идеи.
Но через тридцать лет в одном городе Германии было вновь запущено производство минваты, но с учетом предыдущих ошибок Перри.
Производство материала
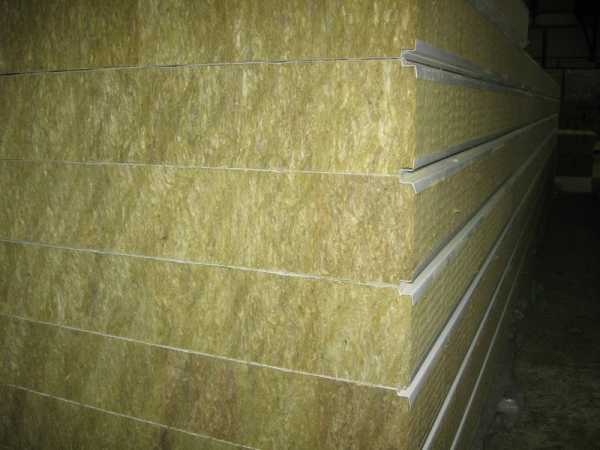
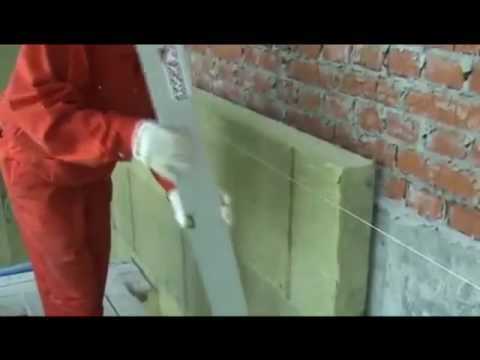
Для производства качественных изделий может быть использован как стекло, так и камень. А для шлаковой ваты принято использовать шлаковые отходы доменной металлургии. Каждый из этих материалов имеет свои преимущества и недостатки. Изделия, выполненные на основе стекла, представляют собой небезызвестную стекловату, которую активно использовали в советские времена. Этот материал образуется при плавлении кварцевого песка или собственно стеклянного боя, после чего он раздувается на тонкие волокна. Стекловата, как правило, является материалом светло-желтого цвета.
Материал, основой которого является камень, носит другое название – каменная вата. Суть производства этого материала во многом сходна со стекловатой, но основным сырьем в этом случае выступает горная порода. Вследствие этого материал часто называют базальтовой ватой, оттенки которой могут быть абсолютно любыми – от желтовато-коричневого до зеленоватого.
И стекловата, и каменная вата обладают практически идентичными свойствами, считаясь одними из лучших утеплителей. Однако некоторое различие между материалами все-таки имеется. Так, стекловата является более упругой и легкой, а каменная имеет более высокие огнестойкие свойства.
Несмотря на то, что каменная вата производства разных компаний внешне похожа, она может значительно различаться по характеристикам. Это объясняется точным составом сырьевых компонентов, который каждый производитель рассчитывает самостоятельно. Составленная рецептура должна быть такая, чтобы производимое волокно было качественным, обладало многочисленными свойствами, а также было нейтральным к металлу и материалам, которые используют в процессе строительства.
Начинается процесс производства минеральной ваты с расплава сырья. Температура плавления составляет 1400-1500 градусов. Здесь крайне важна точность, так как степень вязкости материалов влияет на длину и толщину производимых волокон, соответственно, и на характеристики минеральной ваты.
Следующим этапом является получение волокон из расплавленного сырья. Волокна покрываются связующими компонентами. После этого волокна поступают в отдельную камеру, где они образуют некое подобие ковра.
Далее волоконному ковру придается нужная форма и необходимый объем, после чего он перемещается в особую термокамеру. Именно здесь минеральная вата приобретает свой окончательный вид. Финальная термообработка имеет ключевое значение во всем процессе. Как раз на этом этапе формируются исключительные свойства материала. И, наконец, изделие разрезается на блоки определенного размера и упаковывается.
Разновидности
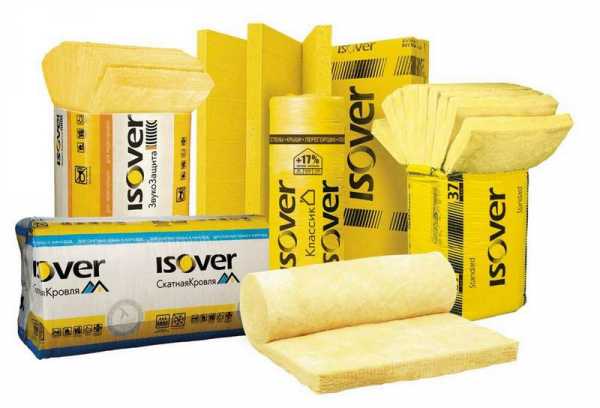
Материалы, в основе которых находится минеральная вата, представлены на современном рынке в большом разнообразии. Здесь можно найти плиты и рулоны разной плотности, а также войлок, гранулы, «сегменты» и «скорлупы». Все эти изделия отличаются прекрасными качественными характеристиками, такими как высокая огнестойкость, теплоизоляционные и акустические свойства. Материалы активно используются при утеплении чердаков, стен, плоских крыш, перекрытий, а также являются отличным материалом для звукоизоляции перегородок между комнатами и потолков.
Минеральная вата делится на:
- Каменная вата, ее еще называют базальтовая
- Стеклянная вата или стекловата
- Шлаковая вата
Стекловата, шлаковая и каменная вата
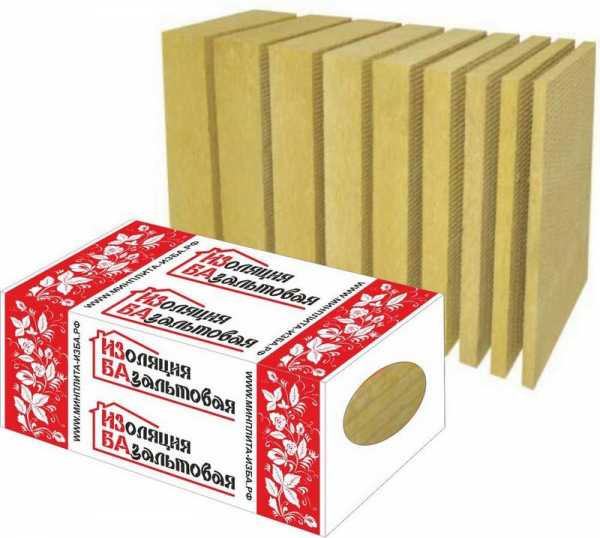
К теплоизоляционным материалам относятся все эти разновидности. Они различаются между собой не только по основному элементу, используемому в производстве, но и толщине и длине волокон, термостойкости, теплопроводимости и устойчивости. Что касается удобства в работе, то больший комфорт в работе приносит минеральная и шлаковая вата, а вот стекловата известна каждому своей колкостью.
Стекловата, как правило, имеет толщину волокон 5-15 мкм, а длина их варьируется от 15 до 50 миллиметров. Это придает материалу упругость и высокую прочность. Работа со стекловатой несет в себе некоторые сложности. В частности, это хрупкость материала и его повышенная колкость. Волокна способны пронзать кожу, попадать в глаза и легкие, поэтому при работе обязательно использовать спецодежду.
Волокна шлаковой ваты имеют длину 16 мм, а толщина их составляет 4-12 мкм. Этот вид минеральной ваты выдерживает наименьшую температуру – всего 300 градусов по Цельсию. Если температура будет выше, волокна начнут спекаться, а теплоизолирующие свойства полностью пропадают. Еще один недостаток шлаковой ваты заключается в ее высокой токсичности. Более того, основа материала – доменные шлаки – имеют остаточную кислотность. Следует отметить и то, что волокна шлаковой ваты хрупкие и колкие, чем несколько похожи на волокна стекловаты.
Каменная вата имеет такие же размеры волокон, как и шлаковая, но все ее характеристики на порядок лучше. С этим материалом проще работать, чем с предыдущими двумя, а его волокна не являются колкими. Наиболее высокие характеристики принадлежат базальтовой вате.
Достоинства материала
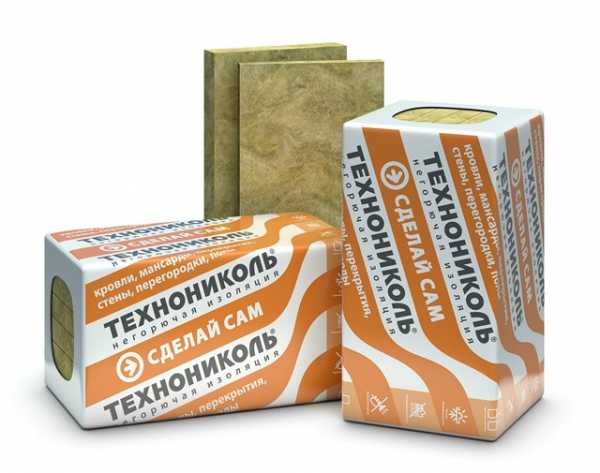
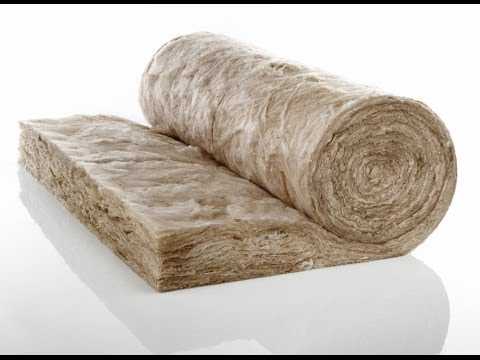
Прежде всего, это превосходная теплоизоляция. Минеральная вата способна ограничить поток тепла, вследствие чего зимой дом не теряет тепло, а летом не нагревается. Этот параметр основывается на двух элементах. Это малый диаметр волокон, который не позволяет накапливать тепло, и беспорядочная внутренняя структура, которая создает множество пазух, препятствующих передаче лучевого теплоизлучения.
Следует отметить и такое качество, как звукоизоляция. Минеральная вата прекрасно удерживает шумы и посторонние звуки. При этом рыхлые плиты материала лучше изолируют воздушные шумы, а полужесткие и жесткие плиты прекрасно справляются с ударными шумами. Этот параметр достигается за счет особой внутренней структуре материала. Звуковые волны быстро затухают, так как не имеют возможности продолжить свое распространение.
Минеральная вата обладает высокой огнестойкостью, и не выделяет вредных веществ при нагревании. Поэтому материал прекрасно подходит в качестве защиты от огня и при противопожарной изоляции.
И, наконец, паропроницаемость. Пар проходит между волокнами минеральной ваты и не впитывается в них. Но при этом важно предусмотреть возможность выведения пара, так как если он будет накапливаться внутри материала, то вызовет его намокание.
Недостатки
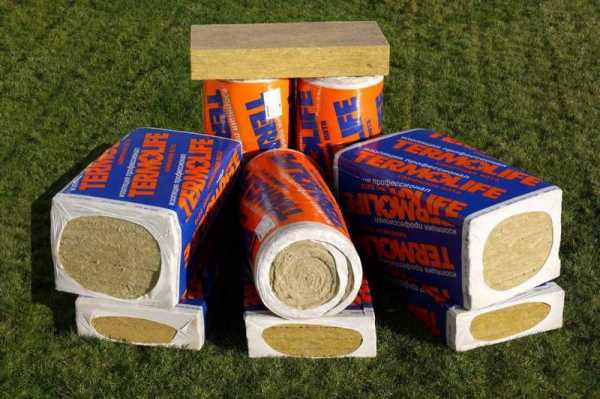
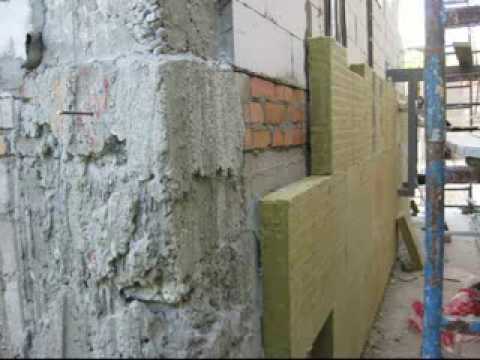
Говоря о преимуществах материала, нельзя не отметить и его недостатков. Например, при работе с минеральной ватой не всегда безопасно, даже учитывая, что колкость у каменной ваты отсутствует. Например, если сырье производится с применением фенолформальдегидных смол, то иногда выделяется фенол, что не способствует здоровью людей, находящихся в здании. Более того, совсем маленькие частицы минеральной ваты в любом случае окажутся в воздухе, а их присутствие в легких явно нежелательно.
Однако всего этого можно избежать. Для этого следует использовать респиратор, а всю поверхность, уложенную материалом, следует покрыть ПВХ-пленкой. Что касается фенола, то при комнатной температуре продукция надежных компаний его не выпускает.
О чем следует знать при работе с материалом
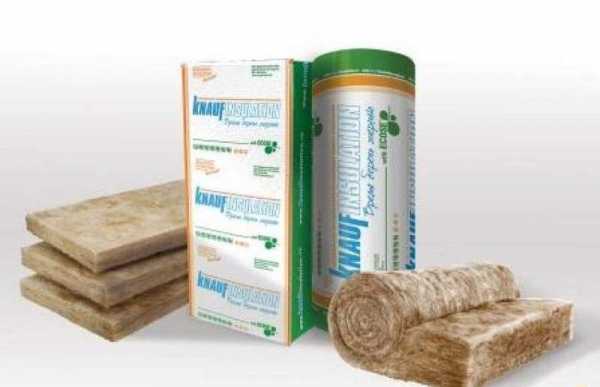
- Когда происходят работы по теплоизоляции плоской крыши, следует укладывать плиты минеральной ваты в два слоя.
- Когда необходимо достичь хорошей звукоизоляции деревянного перекрытия, следует выбирать минеральную вату, изготовленную в виде гранул.
- А для звукоизоляции каркасных стен следует использовать упругую и мягкую минеральную вату. Этот же материал превосходно справляется и со внутренним утеплением стен.
- Плиты с вентиляционными канавками являются наиболее практичными.
- Чтобы придать крыше уклон, предназначенный для стока воды, следует выбирать плиты с переменным сечением.
- На чердаках, которые активно используются хозяевами помещения, следует применять утепление в два слоя.
- Если используется система утепления «мокрого» типа, то следует применить ламельную минеральную плиту.
- В одноэтажных зданиях при трехслойной стене вентиляционная щель не требуется.
- Если на материал нанести прерывистые линии, то можно значительно упростить процесс измерения и резки минеральной ваты.
- Чтобы в процессе укладки материала не появлялись щели, необходимо точно подрезать плиты.
Принципы работы с материалом
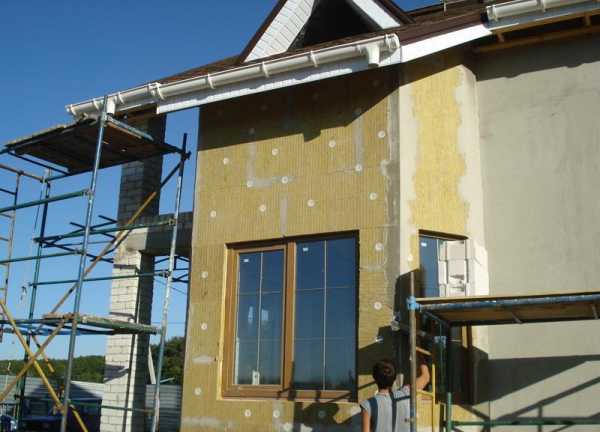
Обычно минеральный утеплитель режется острым и довольно длинным ножом или ножовкой. Но следует помнить и о припусках. В плитах он должен составлять 0,5 см, а в матах от 1 до 2 см. В этом случае после установки материал заполняет пространство довольно плотно. Материал в рулонах следует резать до того, как его разворачивать, плиты обрабатываются по отдельности, не все одновременно.
О хранение материала следует упомянуть отдельно. Перевозить минеральную вату следует в закрытом транспорте, чтобы надежно защитить его от атмосферных осадков. Важно сохранить материал следует так, чтобы защитить его от влаги и возможных атмосферных осадков. Войлок и маты нужно хранить в упаковках в сжатом состоянии, благодаря чему значительно уменьшается объем, занимаемый материалом. Плиты укладываются одна на другую, при этом стопки не должны превышать двух метров, а маты и рулоны устанавливаются в ряд в вертикальном положении. Ходить по жестким плитам и мягкой минеральной вате нельзя, так как материал может быть легко поврежден.
Марки плотности и область их применения
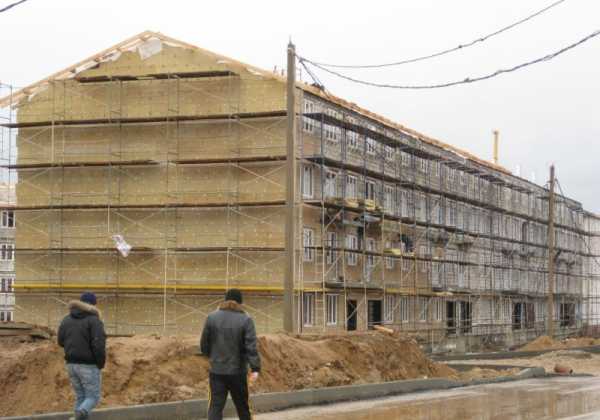
Минеральные плиты различаются по плотности. В зависимости от этого их используют в разных случаях.
- Марка под названием П-75 подходит для чердаков и иногда для теплоизоляции крыши. Часто применяется для газовых и нефтевых проводов.
- Марка П-125 часто используется для теплоизоляции межкомнатных перегородок, а также потолков и полов. Часто применяются в газобетонных, керамзитобетонных и кирпичных стенах.
- Марка ПЖК-175 используется при железобетонных постройках и для перекрытий из металлического листа.
- Марка ППЖ-200 используется там же, где и предыдущая марка, но используется и для повышения огнестойкости зданий.
Часто выпускается и материал, плотность которого менее П-75. Она может прекрасно справиться со своими функциями, если не наблюдаются динамические нагрузки.
Выбор минеральной ваты
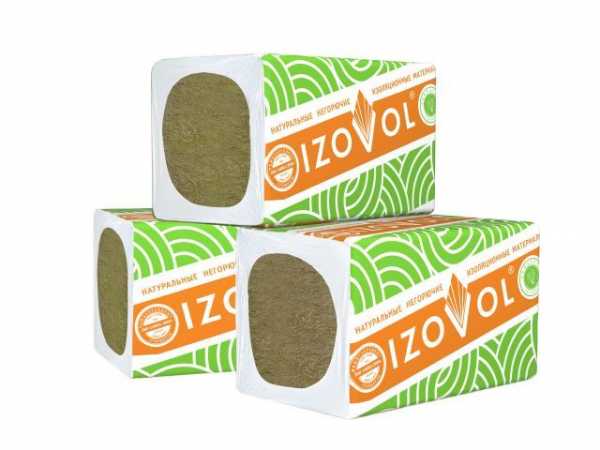
Выбор материала должен быть осуществлен тщательно и внимательно. В первую очередь смотреть необходимо на производителя. Лучше всего брать продукцию известных компаний.
Определите плотность материала. Чем больше плотность, тем дороже материал. Эта зависимость связана с большим количеством волокон и увеличенным расходом материала при производстве. Не стоит обращать внимание на низкую стоимость материала – в этом случае свойства материала будут более низкими, а выполнить установку материала будет нелегко из-за его колкости.
Определите, что важнее – тепло- и звукоизоляционные свойства или стойкость к нагрузкам. В первом случае следует выбирать материал с хаотично расположенными волокнами, а во втором – с их вертикальным расположением.
Минеральная вата должна соответствовать ГОСТу. Следуя этим правилам, можно выбрать именно тот материал, который превосходно справится со всеми своими функциями.
tstinfo.ru
Минеральная вата и стекловата — Теплоизоляционные и огнеупорные материалы
Минеральная вата и стекловата представляют собой волокнистый материал, получаемый в результате специальной переработки силикатных расплавов.
Сырьем для производства минеральной ваты являются различные горные породы осадочного и магматического происхождения: глинистые, карбонатные, базальтовые, гранитные и другие, а также отходы промышленности — доменные и мартеновские шлаки, бой глиняного и силикатного кирпича и др.
В производстве стекловаты применяют те же сырьевые материалы, что и в производстве обычного оконного стекла: песок, известняк, соду и др. Стекловата имеет много общего с минеральной. Различие заключается в свойствах готовой продукции. Основной причиной различий является исходное сырье.
Минеральную вату и стекловату применяют для изготовления теплоизоляционных и акустических изделий в виде плит, скорлуп, матов и т. п. Кроме того, их используют при производстве кровельных и стеклопластиковых материалов..
Практически вся выпускаемая в минеральная вата и базальтовая вата используется в промышленности теплоизоляционных и акустических материалов, стеклянная же вата используется для этих целей лишь в небольшом объеме. Большая часть стеклянного волокна идет на изготовление стеклотканей, применяемых в таких отраслях промышленности, как строительство, радиоэлектроника, самолетостроение и др.
Минеральная вата и изделия на ее основе в нашей стране являются основными теплоизоляционными материалами.
Около 60% общего объема выпускаемой минеральной ваты идет на приготовление различных формованных изделий.
Основными технологическими переделами при производстве изделий на основе как минеральной, так и стекловаты являются получение расплава, превращение его в волокна и формование изделий.
Расплав для производства минеральной ваты может быть получен в результате плавки горных пород или шлаков в специальных печах — ватержакетных вагранках. Кроме того, могут быть использованы огненно-жидкие шлаки из металлургических печей.
В производстве стекловаты стекломассу варят в ванных стекловаренных печах.
Основными способами волокнообразования в производстве минеральной ваты являются пародутьевой, центробежно-дутьевой и центробежный дисковый (многовалковый) (рис. 29). Около 90% общего объема минеральной ваты получают центробежно-дутьевым, 8—9%—центробежным и лишь 1—2%—дутьевым и фильерно-дутьевым способом.
Для получения стеклянного волокна из расплава в основном используют центробежный, фильерный и центробежно-фильерно-дутьевой способы.
Центробежно-дутьевой способ заключается в предварительном разделении струи расплава с помощью центрифуги на отдельные тонкие струйки. Под действием пара, выходящего из сопл с большой скоростью, эти струйки, постепенно охлаждаясь, вытягиваются в волокна.
При центробежном (многовалковом) способе струю, расплава подают на первый (верхний) валок центрифуги, вращающейся с линейной скоростью около 20 м/с. Первый. валок, перерабатывая в волокно ,незначительную часть расплава, почти всю его массу в виде пучка струек и брызг сбрасывает на боковую поверхность второго валка, имеющего линейную скорость около 40 м/с. Второй валок, перерабатывая в волокно значительную часть поступившего на него расплава, излишек его сбрасывает на третий и четвертый валки, вращающиеся со скоростью около 60 м/с. Второй, третий и четвертый валки являются основными волок — нообразующими. Линейная скорость валков влияет на толщину образующихся волокон. Так, волокна, образованные третьим валком, имеющим большую линейную скорость, тоньше волокон, образованных вторым валком, имеющим меньшую линейную скорость.
При дутьевом способе струя пара, воздуха или газовоздушной смеси, перемещаясь с большой скоростью, воздействует на струю расплава, вытягивая его в волокна.
Рисунок 29. Схемы волокно — образования различными способами в производстве минеральной ваты а —дутьевой; б — фильерно — ДУтьевой; в — центробежно — дутьевой горизонтальный; г —центробежный горизонтальный; д — многовалковый; е — центробежнодутьевой вертикальный; ж — фильерно-центробежный
Фильерный способ образования волокон имеет две разновидности:
1) расплав пропускают через фильеры с отверстиями диаметром 2—3 мм. Вытекая из этих отверстий, он наматывается на вращающийся барабан, частота вращения которого превышает скорость вытекания струи расплава из отверстия, что обеспечивает вытягивание струи в волокна диаметром 10—20 мкм;
2) расплав вытекает из фильер платинородиевой лодочки с отверстиями диаметром 1—2 мм. Пучок волокон, собранных в прядь, наматывается на бобину, вытягивающую волокна со скоростью 3000 м/мин и выше.
Первый способ применяют для получения теплоизоляционного стеклянного волокна, второй—для получения волокна, используемого при изготовлении текстильных изделий.
При центробежно-фильерно-дутьевом способе расплав попадает в полый вертикальный вал с частотой вращения до 3000 об/мин. В нижней части вала имеется горизонтальная чаша с 5000—6000 фильерных отверстий диаметром 1—2 мм. Расплав, вытекая из фильер, под действием газовой струи с температурой 1100—1200°С вытягивается в волокна.
Свойства минеральной и стеклянной ваты, полученных различными способами, приведены в табл. 38.
Свойства волокон, полученных различными способами
Способ | Волокно | Объемная масса | Характеристика волокна | |
волокнообразоэатия | ваты, кг/м* | диаметр, мкм | длина, мм | |
Центробежно-дутьевой | Минеральное | 70—160 | 6,5-9 | 18-23 |
Центробежный: валковый | » | 60—100 | 4,7-12 | 3—15 |
дисковый | Стеклянное | 100 | 12—30 | 200—500 |
Минеральное | 160—200 | 8 | 200—500 | |
Дутьевой горизонтальный | » | 200—250 | 5-7 | 6-10 |
Фильерный | Стеклянное | — | 10-30 | Непрерывное |
Фильсрно-дутьевой | э | 40 | 6,6 | 9-27 |
Полученное всеми способами, за исключением фильерного, минеральное или стеклянное волокно —минеральная вата — собирается в камерах волокноосаждения на непрерывно движущейся сетке или перфорированных пластинках.
При производстве изделий из минеральной ваты в камеру волокноосаждения вводят минеральные или органические связующие вещества. В зависимости от объемной
массы (по ГОСТ 4640—66) минеральная и стеклянная пата делится на марки 75, 100, 125 и имеет физико-технические свойства, представленные в табл. 39.
Влажность минеральной ваты не должна превышать 2%, модуль кислотности должен быть не менее 1,2.
Минеральную вату, полученную фильерным способом, выпускают двух марок: 75 и 125. Теплопроводность ее несколько ниже, чем у минеральной ваты, полученной другими способами.
Объемную массу минеральной и стеклянной ваты определяют на специальном приборе (рис. 30). Для этого берут пять навесок ваты массой 0,5 кг каждая. Отобранную навеску укладывают горизонтальными слоями в металлический цилиндр прибора. Сверху на вату при помощи подъемного устройства 3 опускают металлический диск 2 массой 7 кг, что соответствует давлению 0,02 кгс/см2 (0,0002 к Н/см2·) и выдерживают под нагрузкой 5 мин. Высоту сжатого слоя ваты определяют по шкале прибора.
Объемную массу ваты ?к, кг/м3, под нагрузкой вычисляют как среднее арифметическое из пяти значений по формуле
где G—масса навески, равная 0,5 кг; V— объем ваты под нагрузкой, м3; W — влажность ваты, %.
Рис. 30. Прибор для определения объемной массы минеральной ваты 1 —шкала; 2— пригруз; 3— подъемное устройство
Свойства минеральной вaты
Марка ваты | Объемная масса под действием иагрузки 0,02 кгс/см· (0,0002 к Н/см·) | Содержание корольков размером свыше 0.25 мм. %. не более | Теплопроводность, Вт/(м-,К) при средней температуре, °С | Средний диаметр волокон. мкм, не более | ||
25 | 100 | 300 | ||||
75 | 75 | 12 | 0,042 | 0,058 | 0,107 | 6 |
100 | 100 | 20 | 0,044 | 0,058 | 0,102 | 8 |
125 | 125 | 25 | 0,046 | 0,06 | 0,104 | 8 |
Применять рыхлую вату в теплой изоляции нецелесообразно по следующим причинам.
1.Укладка рыхлой ваты в теплоизоляционную конструкцию требует больших затрат ручного 1руда. Условия работы изолировщиков в этом случае краппе неблагоприятны — вага ранит кожу, вызывая зуд и воспаление, а механизировать процесс укладки практически невозможно.
2.Качество рыхлой ваты значительно снижается при транспортировке и хранении на складах: вата уплотняется, комкуется и ломается, превращаясь в пыль. Кроме того, она засоряет транспортные средства и складские помещения.
3.Конструкции изоляции из рыхлой ваты сложны; в процессе эксплуатации за счет вибрации, самоуплотнения и увлажнения теплофи зические свойства конструкции ухудшаются.
Применение изделий из минеральной и стеклянной ваты снижает затраты на устройство и ремонт изоляции, повышает качество конструкции, позволяет дольше сохранять основные свойства конструкции в период эксплуатации. Так, по данным промышленности, применение минераловатных скорлуп вместо набивной минераловатной изоляции трубопроводов уменьшает трудозатраты на каждый 1 м3 уложенной изоляции с 16,8 до 4,1 чел.-дня и снижает стоимость 1 м3 такой конструкции с 44 до 31,6 руб-
По характеру строения минераловатные и стекловат — ные изделия делятся на рыхлые (только минераловатные), гибкие — мягкие и полужесткие — и жесткие.
К рыхлым изделиям относятся гранулированная минеральная вата и различные смеси для мастичной изоляции на ее основе. Объемная масса гранулированной ваты 30— 125 кг/м3 при теплопроводности 0,045 Вт/(??· К) и выше. Смеси для мастичной изоляции имеют объемную массу 300 — 400 кг/м3 при теплопроводности, равной 0,094 Вт/(м K).
Номенклатура мягких, полужестких и жестких минераловатных и стекловатных изделий и их основные свойства приведены в табл. 40.
При изготовлении из ваты изделий для связывания волокон применяют неорганические вещества: цемент растворимое стекло, бентонитовые глины — и органические связующие: синтетические смолы и нефтяные битумы.
Все виды связующих веществ независимо от происхождения должны обладать высокой адгезионной способностью к волокнам, достаточной прочностью и эластичностью, температуростойкостью, водостойкостью, биостойкостью; они должны быть тонкодисперсными для равномерного покрытия волокон, а также недефицитными и недорогими.
arxipedia.ru
Российское производство минеральной ваты: географический срез :: Все для стройки
Динамика производстваПроизводство минеральной ваты как в предкризисный период, так и после него демонстрирует тенденцию к увеличению. В абсолютном выражении прирост составляет 2800 тыс. м3 ежегодно в последние три года. Непосредственно перед кризисом, в 2007 году, этот прирост составил почти 3200 тыс. м3, а в 2008 году мог бы увеличиться и до 3500 тыс. Возможно, именно такими «широкими шагами» отечественное производство и предпочло бы развиваться дальше, в том числе и после упадка, но посткризисное замедление сказывается даже на таком перспективном сегменте.
В 2006 г. российскими предприятиями было произведено 10 млн. м3. теплоизоляционных материалов на основе минеральной ваты, что на 25,1% больше показателя 2005 г. В 2007 г. выпуск составил 13,2 млн. м3, прирост – 31,7%. Несмотря на это, в 2006-2007 гг. на рынке минераловатной теплоизоляции отмечался дефицит продукции. В 2008 г. прирост составил лишь 6,8% – всего было произведено 14,1 млн. м3 минеральной ваты. В 2009 г. впервые за весь период имел место спад: выпуск сократился на 11,7% до 12,5 млн. м3.
Рис. 1. Динамика производства теплоизоляционных материалов из минеральной ваты в РФ в 2005-2011 гг. и прогноз на 2012 г., тыс. м3, и темпы роста, % |
![]() |
Источник. ABARUS Market Research по данным ФСГС РФ |
В 2010 году был зафиксирован заметный прирост – сразу на 22,6%, в 2011 году ситуация была более сдержанной – прирост снизился до 18,2% (но в абсолютном выражении все те же дополнительные 2800 тыс. м3, что и в 2010 году). Логично предположить, что в 2012 году, несмотря на все пессимистичные ожидания, отечественное производство выдаст не меньше чем 20,5 млн. м3.
Помимо сокращения темпов роста в 2008 г. и 2009 г, особенностью этого периода стала иная, чем в 2007 г., динамика выпуска по месяцам. Так, если в 2007 г. наиболее продуктивными были весенние и летние месяцы года, то в 2008-2009 гг. производство активизировалось только к осени. 2010 и 2011 годы повторяют эту динамику, но более высокой линией. Также стоит обратить внимание на сильное снижение объемов производства в первом квартале 2009 г.: лишь в апреле объем выпуска минераловатной теплоизоляции сравнялся с показателями 2008 г., но затем снова упал.
Во втором полугодии 2010 года производство развивается более активно: в апреле-мае выпуск сравнялся с уровнем 2007 и 2008 гг. А с июня объемы производства заметно превышают выпуск всех предыдущих лет.
Рис. 2. Динамика производства теплоизоляционных материалов из минеральной ваты в РФ по месяцам в 2007-2012 гг. (2012 г. – январь-март), тыс. м3 |
![]() |
Источник. ABARUS Market Research по данным ФСГС РФ. |
Весь 2011 год смотрится хорошо – в январе наконец-то произведено столько же, сколько в самом удачном январе всего рассматриваемого периода, а именно – 2007 года. А затем линия уверенно идет вверх, и даже в декабре не делает традиционный «кивок носом», а растет вверх, в расчете на удачный строительный сезон наступающего года. Действительно, начало 2012 года также выглядит оптимистичным – в январе–марте было произведено на 28,7% больше, чем за аналогичный период 2011 года. Но прирост всего 2012 года вряд ли будет таким же высоким, поскольку все еще срабатывает эффект низкой базы – к примеру, в первом квартале прошлого года тоже был прирост 30% по отношению к аналогичному периоду, только в результате (по итогам всего года) получилось 18,3%.
В целом видно, что российский рынок минеральной ваты держится в основном на собственном производстве. До кризиса ежегодные приросты производства были значительно выше, чем приросты рынка, а кризисное падение – меньше. В дальнейшем это соотношение восстановится, и приросты производства снова будут опережать приросты рынка. Обратное соотношение, зафиксированное в 2010-2011 гг., свидетельствует о том, что объем рынка, включая импорт, отталкивался от более низкой базы (импорт сократился сильнее производства, но и восстанавливается в первые годы после кризиса активнее).
Рис. 3. Сравнительная динамика ежегодных приростов производства минеральной ваты и объема рынка в 2006-2011 гг., % |
![]() |
Источник. Расчеты ABARUS Market Research. |
Производство в географическом разрезе
Если рассматривать географический аспект, то обнаруживается, что безусловным лидером на рынке каменной ваты является Центральный округ – его доля в последние три года стабильно держится на уровне 42-43% от общероссийского выпуска.
Рис. 4. Динамика соотношения долей Федеральных округов в общем производстве минераловатной продукции в 2005-2011 гг. (%). |
![]() |
Источник. ABARUS Market Research по данным ФСГС РФ. |
Значительную долю занимают Уральский и Приволжский федеральные округа. Более того, можно сказать, доля ПФО увеличивается за счет УФО, и если в 2005 г. в Уральском округе производилось в 2,5 раза больше, чем в Приволжском, то теперь они почти сравнялись. Создается впечатление, что в Уральском округе сокращается производство минеральной ваты, на самом же деле оно растет, просто в этом производстве участвуют всего два представителя от УФО – Свердловская и Челябинская области – и им трудно соревноваться с многочисленными регионами из других округов.
Доля Северо-Западного округа с 2006 года остается практически неизменной (с еле заметной тенденцией к увеличению). Доля Сибирского округа колеблется от 6% до 10%. Доли Южного федерального округа, как и Дальневосточного, и без того небольшие, продолжают медленно уменьшаться.
Распределение производства по регионам выглядит следующим образом. Основными «соперниками» являются Московская и Челябинская область. В настоящее время выпуск в этих регионах практически одинаков, тогда как в 2005 году в Московской производилось значительно больше. Оба региона испытывают давление со стороны других активно развивающихся областей. Особенно следует выделить Белгородскую, Ленинградскую, Рязанскую и Тамбовскую области, а также Республику Татарстан. В целом можно отметить тенденцию к более равномерному распределению производства по регионам.
Таким образом, можно сказать, что производство минераловатной теплоизоляции тяготеет к рынкам сбыта – региональная структура распределения выпуска все больше становится похожей на структуру распределения строительства. Исключением является только Южный федеральный округ – в плане строительства он находится в лидерах, а в плане производства минеральной ваты – в аутсайдерах. Объяснить это расхождение можно тем, что в южных регионах необходимость теплоизоляции конструкций не так актуальна, как для других регионов страны – северных и восточных.
Также на распределение долей ФО на рынке каменной ваты влияет возможность дешевого импорта, близость к сырьевой базе, развитость инфраструктуры, а также советское наследие. Дефицит теплоизоляционных изделий из каменной ваты в Дальневосточном ФО легко объясняется дешевым импортом из Китая. Незначительное производство материала в Южном федеральном округе определяется особенностями экономической деятельности региона, основной профиль деятельности которого – аграрная промышленность. Напротив, Урал, для которого характерно обилие полезных ископаемых, специализируется на производстве строительных материалов, в том числе теплоизоляционных. Стимулом к производству большого объема каменной ваты в Центральном ФО стала высокая активность строительного сектора в Москве и Московской области. Не стоит также забывать, что предпринимателю проще переоснастить существующий с советских времен завод, чем строить новый. Большинство подобных заводов расположено именно в ЦФО и УФО. Определенное воздействие оказывает и политический фактор – создание особых экономических зон, деятельность на территории которых связана с меньшими административными издержками. В связи с этим в ближайшем будущем стоит ожидать развитие рынка теплоизоляционных материалов в Татарстане.
Низкая плотность материала не способствует снижению издержек на его перевозку, поэтому любой локальный рынок, который предъявляет высокий спрос на минеральную вату, но снабжается при этом завозными материалами, является потенциально привлекательным для инвестиций в местное производство.
Производители
После пяти лет ежегодного мониторинга рынка теплоизоляционных материалов специалисты ABARUS Market Research отмечают все возрастающую разницу между официальной статистикой производства теплоизолирующей продукции, в том числе минеральной ваты, и ее реальным объемом выпуска. Если в 2005 году эта разница составляла 600 тыс. м3 (8000 против 7400), то в 2011 г. это уже 5 100 тыс. м3 (18 100 против 13 000), несмотря на все попытки Росстата усовершенствовать учет. Такой разрыв говорит о том, что на российском рынке теплоизоляции по-прежнему работает множество небольших компаний, не отчитывающихся должным образом перед местными статистическими организациями.
Однако некоторые из этих организаций растут, предпринимают более активные маркетинговые усилия на рынке, что впоследствии делает возможным их обнаружение «в ручном режиме». Так, в мае этого года список производителей минеральной ваты вновь пополнился несколькими компаниями, которые на самом деле работали и до кризиса, просто не попадали в фокус зрения исследователей. Также в данном списке появились и новички – предприятия, открывшиеся или начавшие фактический выпуск минеральной ваты в 2010 или 2011 г. Всего в России, по последним подсчетам, работает порядка 45-50 заводов самого различного масштаба.
Производство минераловатных изделий в РФ по округам и перечень работающих производителей |
![]() |
Источник. Расчеты ABARUS Market Research по данным компаний и официальной статистики. |
Уже в разгар кризиса стало понятно, что не всем участника рынка удастся его пережить, основной объем банкротств пришелся на 2009-2010 гг., но закрытия наблюдались и в 2011 г.
В числе самых крупных потерь можно назвать холдинг «Термостепс», владельцы которого выбрали не самое подходящее время для раскрутки бизнеса под масштабные кредиты, в результате чего встали екатеринбургский, ярославский, салаватский и омский заводы. Хотя еще совсем недавно этот производитель был одним из самых заметных и перспективных игроков российского строительного рынка, оснащающий свое производство современным оборудованием. В результате выстояло всего одно предприятие – Волгоградский завод «Термостепс». На рубеже 2010-2011 гг. существовал риск, что активы этой компании могут подвергнуться принудительной реализации в счет уплаты долгов всей группы, которых накопилось немало, однако по состоянию на середину мая 2012 года волгоградское предприятие «Термостепс» продолжает функционировать и даже понемногу наращивает выпуск. Еще одна компания, бывшая в составе Группы, – «Термостепс-МТЛ» из Самары – сменила собственника и начала «сольную карьеру» сразу же, как только наступили тяжелые времена (в октябре 2008 г.). Теперь кредиторам довольно сложно доказать ее причастность к долгам бывшего холдинга, а «МТЛ» активно развивается, правда, к рынку минеральной ваты имеет не совсем прямое отношение, так как производит материал только для собственных нужд (предприятие изготавливает «сэндвич-панели»).
В 2009 г. процедуру банкротства пережило ОАО «Теплоизоляция», оставив в белгородской области только одного, но зато очень крупного производителя – Завод нестандартного оборудования (Izovol). По всей видимости, совсем потеряла своих производителей Нижегородская область – в 2009 году остановилось производство Группы «Тивул» (заводы «Тивул-Кстово» и «Тивул-Арзамас»), а в 2010 г. прекратило производство ОАО «Теплоизол». Первый завод ГК «Тивул» был запущен в 60-е годы, второй – в 1985 г. Как ГК «Тивул» предприятия существуют с 2006 г. До этого заводы действовали в рамках ГК «Минвата».
В 2010 г. прекратил производство теплоизоляции Воронежский завод строительных материалов, сосредоточив свои усилия на выпуске силикатных изделий. Нет сведений о функционировании новосибирского ЗАО «Термиз». И довольно новое производство в Ставропольском крае («Ойлтехнострой», торговая марка «Базиз»), которое было запущено в январе 2009 года, тоже не продемонстрировало долговечности. В 2011 году остановилось производство на заводе «Изоплит» (Тверская область, также входило в Группу «Термостепс»), а также на Новомальтинском заводе строительных материалов (Иркутская область).
Кроме этого, стоит отметить наблюдавшийся в 2008-2011 гг. процесс смены собственников с отечественных на иностранных у некоторых предприятий, что тоже является прямым следствием кризиса. Как уже было сказано выше, в 2008 г. ОАО «Термостепс-МТЛ» перешло к ИФ Baring Vostok Capital Partners (Tabellion Limited). В июне 2010 г. ЗАО «Троицкий завод минераловатных плит» от компании Linerock перешел в собственность ГК «Rockwool Russia». А сам Linerock в июле 2011 г. стал собственностью международного концерна Saint-Gobain.
Новые игроки рынка
В целом стоит отметить, что крупные российские производители вполне успешно справились с кризисной ситуацией. На большинстве предприятий спад носил ограниченный характер, а на некоторых даже в 2009 г. наблюдался положительный прирост. Главное наблюдение сводится к тому, что кризисный период подтолкнул структуру производства к усилению концентрации. Если в 2007 году на первую тройку компаний приходилось 47% от общего объема производства, то в 2010 г. уже почти 60%. При этом доля малых предприятий стремительно сокращалась.
Но вот кризис отпустил, и на рынке снова стали появляться новые предприятия. Экономический кризис, начавшийся в России в 2008 г., помог в более сжатые сроки очистить рынок от наименее эффективных производителей, а успех отдельных молодых предприятий (главным образом, «Изовол») в сочетании с продолжающимся активным рыночным ростом все еще привлекает в отрасль новых игроков.
Что касается новичков, то самым ярким событием последнего времени стало открытие нового завода Rockwool в Алабуге в феврале 2012 года. Завод, по обещаниям собственников, может стать одним из самых крупных не только в России, но и во всей Евразии. Но пока его мощности – 140 тыс. тонн в год – хоть и являются внушительными для отечественного рынка в целом, но с точки зрения ведущих игроков, скорее, выглядят как средние. Обещана вторая производственная линия в самое ближайшее время.
Среди других новичков можно отметить предприятие «Эковер», заработавшее в Свердловской области в середине 2010 года; башкирское ООО «Агидель», начавшее выпускать минеральную вату под маркой Baswool в 2011 году; ООО «Базальт» из Смоленской области с продукцией Hitrock, а также Завод базальтовых материалов из Якутии. Как показывает практика, наиболее хорошие перспективы открываются компаниям, тщательно прорабатывающим свою маркетинговую стратегию (даже если они одни в своем регионе), включая оригинальную торговую марку. Возможно, именно поэтому наиболее сомневающимся в своем успехе выглядит якутская компания, которая пока не только не обзавелась фирменным названием, но и опирается в своем продвижении не столько на рыночные усилия, сколько на помощь региональных властей.
1
vsedlyastroiki.ru
Технология производства минеральной ваты – стр. 6
Технология производства минеральной ваты
Производство минеральной ваты независимо от типа плавильного агрегата и способа переработки силикатного расплава включает в себя следующие технологические операции: подготовку сырьевых материалов путем измельчения и его сортировку; плавление сырья и получение силикатного расплава; переработку расплава в волокно; осаждение минеральной ваты и формирование минераловатного ковра в камере волокно-осаждения.
Сырьевые материалы
Для производства минеральной ваты используют: шлаки, являющиеся отходами черной и цветной металлургии; природные силикатные и карбонатные горные породы; отходы промышленности (бой глиняного кирпича, горелые породы, пыль-унос цементного и керамзитового производства).
Доменные шлаки – наиболее распространенное сырье для производства минеральной ваты – используют как в твердом состоянии в виде щебня, так и в огненно-жидком состоянии. Шлаки представляют собой сплавы силикатов и алюмосиликатов следующего химического состава (%): SiO2 – 35-40; AL2O3 – 10-15; CaO – 35-45; MgO – 5-10; Fe2O3+FeO – 0,5.
Щебень из доменного шлака применяют для плавления в вагранках, огненно-жидкие шлаки – в шлакоприемных ванных печах.
Фосфорные, никелевые, медеплавильные шлаки, являющиеся отходами цветной металлургии, используют для плавления в вагранках.
Недостаток – высокое содержание СаО, что снижает устойчивость к действию воды, прочность, увеличивает пыление и слеживаемость минеральной ваты. Для уменьшения недостатков в силикатную шихту добавляют подкислители, содержащие повышенное количество SiO2 и AL2O3. Использование огненно-жидких шлаков снижает расход тепла на получение расплава, в связи с чем снижается стоимость минеральной ваты. Однако сложно корректировать состав шлаков.
Горные породы. К числу лучших видов горных пород для производства минеральной ваты относятся изверженные горные (базальты, диабазы, габбро), подобные им по химическому составу метаморфические и осадочные (мергели, доломиты, известняки) породы. Содержание оксидов в состпве горных пород колеблется в следующих пределах (%):SiO2 – 45-65; AL2O3 – 10-20; Fe2O3+FeO – 10-15; CaO – 5-15; MgO – 5-15; Na2O+K2O – 1-3.
Для получения силикатного расплава наиболее пригодны изверженные породы, отличающиеся высокой прочностью и равномерностью химического состава. Для плавления в ванных печах по своему химическому составу подходят осадочные породы.
Основным показателем, определяющим пригодность сырья для производства минеральной ваты служит модуль кислотности Мк, который представляет собой отношение суммы процентного содержания в сырье кислых окислов – кремнезема SiO2 и глинозема AI2O3 к сумме основных окислов – кальция СаО и магния MgO. Модуль кислотности минеральной ваты должен быть не менее 1,2, т.е
Мк=( SiO2+ AI2O3)/(СаО+ MgO)≥1,2
Так как в природе редко встречаются сырьевые материалы с необходимым химическим составом и модулем кислотности, то требуемый состав сырьевых материалов подбирают путем составления сырьевой смеси – шихты, состоящий их двух, иногда и нескольких компонентов.
Отходы керамического и силикатного производства широко используются в композиции с менее кислыми или основными компонентами (шлак, доломит, известняк и др.)
С повышением модуля кислотности увеличивается долговечность минеральной ваты и водостойкость. Водостойкость минеральной ваты характеризуется показателем рН; минеральная вата относится к высшей категории водостойкости при рН<5, первой категории при рН<7. Показатель рН гидролитической стойкости минеральной ваты повышается при увеличении содержания в ней кислых окислов SiO2 и AL2O3. Однако рост количества кислых компонентов приводит к увеличению вязкости, что снижает производительность труда и ухудшает условия волокнообразования.
Подготовка сырьевых материалов
В процесс подготовки сырьевых материалов входят следующие операции: получение определенного фракционного состава сырьевых компонентов и топлива путем дробления сырья и последующего рассева его на определенные фракции; составление рабочей шихты из сырья посредством автоматического весового дозирования каждого компонента сырья и топлива; загрузка порций шихты и топлива – рабочей колоши – в вагранку или только шихты в ванные печи (электродуговой). В стадии освоения находятся циклонные и конвейерные печи.
Для подогрева шлаков применяют специальные печи – шлакоприемники.
Рис. 4. Схема подготовки сырья при получении расплава в вагранке
Для плавления в вагранках применяют только кусковое сырье с размерами частиц 20-100 мм. При плавлении в ванных печах используют сырье с размером частиц до 5 мм.
Общие требования к сырью для вагранок – недопустимость фракций менее 20 мм, которые резко увеличивают аэродинамическое сопротивление столба шихты. Оптимальный размер кусков сырья зависит от вида сырья. Кроме гранулометрического состава важной характеристикой сырья является механическая прочность кусков, которая должна быть не менее 1,5 МПа.
Использование печи того или иного типа зависит в основном от вида сырья и наличия топливных и энергетических ресурсов. Сравнение плавильных агрегатов по тепловой эффективности показывает, что электродуговая печь – наиболее эффективный плавильный агрегат. Однако при ее применении резко увеличивается расход электроэнергии.
Рис. 5. Схема подготовки сырья при получении расплава в ванных печах
Наиболее широкое распространение в минераловатной промышленности получили вагранки.
Плавление сырья
Шахтная печь – вагранка
Широкое распространение вагранок объясняется высоким коэффициентом использования тепла от сжимаемого топлива, большой производительностью при небольших габаритах, простотой конструкции, незначительными капитальными затратами и простотой обслуживания.
Вагранки представляют собой шахтные плавильные печи непрерывного действия, теплообмен в которых происходит по принципу противотока. Сырье, загружаемое в верхнюю часть вагранки, опускается вниз, превращаясь при этом в расплав, а образовавшиеся в нижней части вагранки продукты горения поднимаются вверх, отдавая тепло расплавляемому материалу. Это вертикальная печь диаметром 1000, 1250 или 1400 мм, состоящая из двух основных частей – горновой и шахтной.
В горновой, нижней части вагранки происходит горение топлива и плавление сырья. Здесь развиваются наиболее высокие температуры, поэтому горновая часть защищена водяной рубашкой – ватержакетом (4). Выше ватержакета шихта защищена от воздействия высоких температур футеровкой из шамотного кирпича. Ватержакет представляет собой металлический цилиндр с двумя стенками, между которыми находится охлаждающая вагранку проточная вода, предохраняющая корпус вагранки от перегрева. Температура воды при выходе из ватержакета не должна превышать 70ºC. Низ ватержакета закрывается двухсекционным днищем (2), подвешенным на шарнирах.
Чтобы уменьшить расход воды, целесообразно применять оборотную систему: нагретая в рубашке вода подается в охладительные устройства или охладительные бассейны, и вновь используется в ватержакете. Перепад температуры поступающей и отходящий из водяной рубашки воды при оборотном охлаждении должен составлять не более 15-20ºC, а при прямоточном – 30-40ºC.
Вагранки бывают с испарительной системой охлаждения, позволяющий резко снизить расход воды. В этом случае следует использовать только химически очищенную воду. Испарительные системы охлаждения могут быть открытыми и закрытыми. В испарительных системах допускается нагревание воды до температуры кипения (100ºC).
Воздух, необходимый для горения топлива, подается в вагранку через специальные устройства – фурмы (3), которые симметрично расположены по окружности вагранки в один – три ряда на определенной высоте, равной 0,5-0,8 диаметра вагранки от ее днища. Количество фурм диаметром 60-150 мм в каждом ряду составляет 8-16. Фурмы каждого ряда соединены между собой общим кольцевым коллектором (13) (фурменным поясом), через который воздух поступает по всему периметру вагранки.
Сортированные сырьевые материалы и кокс из расходных бункеров через весовые дозаторы подаются в загрузочное окно (6), расположенное в боковой стене вагранки. Высота рабочей зоны вагранки равна 4-5-ти ее диаметрам. Расход топлива (кокса) в вагранках составляет 18-20% массы сырья.
Нижнюю часть ватержакета, от оси нижнего ряда фурм до днища, называют горном. В горне накапливается жидкий расплав и происходит его гомогенизация по составу температур. Высота горна колеблется в пределах 600-750 мм.
Загруженные сверху сырье и топливо чередующимися слоями опускаются вниз, а образовавшиеся в нижней части вагранки продукты горения топлива – горячие газы – поднимаются вверх, передавая свое тепло верхним слоям материала.
Таким образом, сырье, опускаясь вниз вагранки, разогревается и превращается в расплав. Образовавшийся расплав вытекает из горна через летку (1) и по лотку направляется к узлу волокнообразования. Леткой называется отверстие диаметром 35-80 мм в водоохлаждаемом корпусе, вставляемом в специальный проем ватержакета.
На скорость плавления, производительность вагранки и температуру расплава влияет интенсивность дутья, которая определяется количеством воздуха на единицу площади за единицу времени и равна 40-110 м³/м²мин. Давление дутья зависит от высоты загрузки вагранки и фракционного состава сырья и кокса.
Рис 6. Вагранка для получения минерального расплава: 1 – летка, 2 – днище, 3 – фурмы, 4 – ватержакет. 5 – труба для отвода воды, 6 – загрузочное окно, 7 – искрогаситель, 8 – патрубок для сброса золы, 9 – шахта, 10 – люк для осмотра, 11 – компенсаторы, 12 – труба для подвода воды, 13 – воздушный коллектор; I – зона подогрева и сушки, II – зона плавления, III – зона перегрева
В верхней части вагранки находится искрогаситель (7) для улавливания уносимых газовым потоком искр и частиц пыли. Остывшие частицы скатываются к отверстию патрубка (8) и удаляются.
В зависимости от применяемого способа переработки минерального расплава вагранки устанавливают над уровнем пола на различной высоте (от 2000 до 3500 мм).
Плавление шихты в вагранке
Вагранку по высоте можно условно разделить на три зоны: зону подогрева и сушки сырья – I, зону плавления – II и зону перегрева (гомогенизации) расплава – III.
Зона подогрева и сушки I расположена между зоной плавления и верхним уровнем шихты. Здесь загружаемая холодная шихта подогревается за счет тепла отходящих продуктов горения топлива. В самой верхней части этой зоны при температуре 105-110ºC удаляется механически связанная влага. По мере опускания сырьевых компонентов при температуре 600-1000ºC и выше происходит термическое разложение сырья, если по химическому составу оно содержит карбонатные соединения, способные разрушаться. Если же сырье представляет собой материал, ранее прошедший термическую обработку (например, шлаки), то в этой зоне уже начинается частичное плавление шихты.
II зона – зона плавления, здесь при 1500-1800ºC сырье из твердого состояния переходит в жидкое. Образовавшийся расплав стекает по кускам раскаленного кокса в горн.
Отдельные компоненты сырьевой смеси плавятся неодновременно: легкоплавкие плавятся раньше, тугоплавкие – позднее, растворяясь в легкоплавких. Для ускорения процесса растворения тугоплавкого компонента размеры его кусков должны быть меньше, чем легкоплавкого.
III зона перегрева (гомогенизации) расплава расположена в нижней части вагранки до ее пода. В верхней части зоны III в присутствии кислорода осуществляется интенсивное горение кокса. Основной вид топлива, применяемый в вагранках, – литейный каменноугольный кокс, который обладает большой теплотой сгорания (28560-30240 кДж), высокой механической прочностью, малым содержанием летучих веществ и термической прочностью кусков. По назначению кокс подразделяют на литейный и доменный. В вагранках предпочтительнее литейный кокс, из-за его малой реакционной способности.
Обязательное условие нормальной работы вагранок – однородность кусков сырья и кокса и равномерная загрузка. Наиболее эффективно повышается производительность вагранки при интенсификации дутья, так как ускоряется горение кокса. Однако выше определенного предела потока воздуха снижается температура расплава, увеличивается его вязкость и производительность резко уменьшается.
Повышение расхода кокса способствует росту температуры расплава, но производительность после определенного предела снижается, оптимальный расход – 17-20% массы шихты. Температура расплава и производительность вагранки могут быть повышены при использовании подогретого до 400-500ºC дутья.
К недостаткам вагранок относятся: низкий коэффициент полезного использования тепла, высокие удельные затраты на топливо, плохое качество расплава и недостаточная стабильность струи расплава, неудовлетворительные санитарно- гигиенические условия эксплуатации, обусловленные применением кокса.
В то же время вагранки имеют большую производительность при небольших габаритах, просты по конструкции, требуют невысоких капитальных затрат, просты в обслуживании и ремонте, они могут быть остановлены в любое время и пущены в течение нескольких часов.
Совершенствование ваграночной плавки осуществляется в следующих основных направлениях: модернизация существующих вагранок; применение горячего дутья; создание вагранок, в которых в качестве топлива используется природный газ.
В настоящее время существуют коксогазовые и газовые вагранки, где кокс заменен на 20-30% или полностью природным газом. Это уменьшает расход дефицитного кокса, снижает затраты на тепловую энергию в 2-3 раза, обеспечивает санитарно-технические требования в производстве.
Ванные печи
Небольшие ванные печи используют для получения расплавов при производстве минеральной ваты. По своему устройству они похожи на ванные стеклоплавильные печи. Могут применяться все типы ванных печей: с подковообразным, продольным и поперечным направлением пламени. По способу использования тепла отходящих газов такие печи могут быть регенеративными и рекуперативными. Наибольшее распространение получили регенеративные печи с подковообразным направлением пламени. Для отапливания печей служит газообразное или жидкое топливо.
Ванная регенеративная печь для плавления сырья при производстве минеральной ваты состоит из плавильного бассейна (ванны), горелок (3), вертикальных воздушных регенераторов (2) и выработочной части – фидера (8). С целью подачи на переработку наиболее горячих слоев расплава дно фидера располагают выше дня бассейна.
Газоходы (1) устанавливаются для сброса отходящих газов и загрузчиков сырья. Форма бассейна варочной части (7) печи прямоугольная или суживающаяся к фидеру, глубина бассейна 500 мм.
В бассейн варочной части (7) загрузчиками или гидравлическими толкателями подается через специальные загрузочные окна (6), расположенные в боковых стенках, тщательно подготовленная шихта. В зависимости от производительности печи количество разгрузчиков с каждой стороны может быть от 1 до 4 шт. В плавильной камере установлены от 2 до 4 горелочных устройств, имеющих подковообразное направление пламени.
Рис. 7. Схема подготовки сырья при получении расплава в ванных печах
Рис. 8. Регенеративная ванная печь: 1 – газоход, 2 – регенератор, 3 – места установки горелочных устройств, 4 – свод печи, 5 – под печи,
6 – загрузочные окна, 7 – варочная часть, 5 – фидер, 9 – водоохлаждаемая летка
Полученный в варочной части силикатный расплав поступает в фидер (8). Форма фидера, как и в выработочной части – прямоугольная. Между камерой плавления и фидером выложен порог, служащий для предотвращения поступления в фидер нерасплавленных кусков сырья. Расплав из фидера выдается через водоохлаждаемую летку (9) при центробежно-валковом способе его переработки или через фильерные питатели при фильерном способе.
Перед леткой в своде фидера установлено горелочное устройство (3) для перегрева расплава и достижения его однородности. Дно бассейна (под 5) выложено из многошамотных брусьев, которые уложены на металлические полосы, расположенные на донных балках. Стены бассейнов печи и фидера, загрузочные отверстия, влеты горелок выполнены из бакора (огнеупорного материала с большим содержанием окиси циркония и глинозема) свод и верхнее строение печи и фидера – фасонного динаса.
Регенераторы (левый и правый) размещены в одном блоке перед торцевой стеной варочной части печи и соединены с ней горелками и шлаковиками для осаждения частиц уноса сырья. Насадка регенераторов, выполненная из шамота и высокоглиноземистого кирпича, работает периодически, сначала воспринимая (аккумулируя) тепло отходящих газов из печи, а затем отдавая это тепло потоку воздуха, подаваемому на горение топлива. Насадка регенераторов позволяет нагреть воздух до 1000 ºC.
Направление движения пламени в варочной части печи изменяется автоматически, через определенные промежутки времени и, таким образом, поочередно работает то правый, то левый регенераторы.
Рекуперативные ванные печи более экономичны, чем регенеративные, но требуют изменения высокожароупорных элементов.
Рекуператор – устройство для подогрева воздуха или газа, в котором тепло передается от горячих отходящих газов к нагреваемому воздуху через поверхность разделяющей стенки. Температура плавления достигает 1600ºC.
Ванные печи в теплотехническом и технологическом отношении более совершенны, чем вагранки. В этих печах тепло передается в основном лучеиспусканием (около 95%), что обеспечивает удовлетворительную управляемость процессом плавления и получения гомогенного расплава с необходимыми свойствами. Достоинством ванных печей является так же возможность применять дешевые виды топлива (природный газ, мазут) и отсутствие требований к прочности сырья, так как сырье загружают в печь в измельченном состоянии (с размером кусков 1-2 мм).
К недостаткам ванных печей следует отнести то, что они занимают в 4-5 раз больше производственной площади, чем вагранки, при одинаковой производительности; требуют энергоемких шихтоприготовительных отделений для помола и перемешивания сырья; удельные расходы тепла в них в 2 раза превышают удельный расход тепла в вагранках.
Для получения минеральной ваты применяются также шлакоприемные ванные печи, электродуговые печи для получения силикатного расплава, циклонные печи для мелкокусковых отходов минераловатного производства и др.
Рис. 9. Шлакоприемная ванная печь:
1 – сливной желоб, 2 – печь – шлакоприемник, 3 -печь-питатель, 4 – вытяжной зонт, 5 – камера волокноосаждения, 6 – летка
Свойства расплава
Следующий этап технологии в производстве волокнистых материалов – это получение расплавов. В минеральных расплавах всегда присутствует SiO2, поэтому они называются силикатными расплавами.
При получении расплавов протекают сложные физико-химические процессы, характер которых определяется составом шихты и температурой. Во всех случая происходят процессы силикато- (400-600ºC) и стеклообразования, наиболее интенсивных при появлении жидкой фазы.
Возможность химических взаимодействий определяется законами химической термодинамики и действием кинетических факторов, таких как поверхность контакта. То есть чем мельче шихта, тем больше площадь контакта зерен компонентов, тем быстрее протекают реакции.
Для перевода твердой фазы в жидкое состояние нужно затратить энергию на преодоление сил, действующих между элементами решетки.
В настоящее время наиболее распространен взгляд на силикатные расплавы как на ионные жидкости. Стеклообразователем или сеткообразователем является кремневая кислоты. Установлено, что из всех связей О2- связь с Si4+ – самая прочная, что обуславливает наличие кремнийкислородных комплексов.
Наличие жесткой направленной ковалентной связи Si-O определяет присутствие в расплавленных силикатах устойчивых комплексных ионов (SiхОу)z, образующих анионный скелет расплава. Внутри этого каркаса преобладают ковалентные, а вне – ионные связи.
Структура силикатных расплавов определяет их свойства. Так вязкость расплавов зависит от подвижности анионного каркаса, а электропроводность от подвижности ионов, поляризующих связи Si-O.
Основными свойствами силикатных расплавов, влияющих на свойства минеральных волокон являются вязкость, поверхностное натяжение и кристаллизационная способность.
Вязкость – свойство жидкостей оказывать сопротивление перемещению одной части жидкости относительно другой, обусловленное внутримолекулярным трением. Силикатные расплавы ведут себя в основном как ньютоновские жидкости, при низких температурах наблюдается признаки структурирования, что приводит к ухудшению качества волокна.
Характер изменения вязкости от температуры определяется составом расплавов. По характеру изменения вязкости от температуры различают «длинные» – с большим интервалом вязкости и «короткие» – малый интервал температур от жидкотекучего до хрупкого состояния. Наиболее целесообразны в производстве минеральной ваты жидкие расплавы.
Поверхностное натяжение σ характеризует интенсивность поверхностных межмолекулярных (межатомных, межионных) сил в расплаве. Образование новой поверхности связано с преодолением сил поверхностного натяжения. Чем оно больше, тем большую работу нужно затратить, чтобы образовать единицу новой поверхности.
На поверхностное натяжение влияет состав и температура расплава. Окислы, входящие в состав расплава делятся на 3 группы: поверхностно-неактивные (SiO2, AI2O3, СаО и др.), промежуточные (К2О, В2О3) и поверхностно-активные (Сr2O3, SO3, WO3 и др.). Наименьшим поверхностным натяжением характеризуются SiO2 и Na2O. Снижение поверхностного натяжения благоприятно сказывается на ходе технологических процессов.
Структура и свойства силикатного расплава зависят от его химического состава. Если катион окисла является комплексообразующим, то количество его содержания в расплаве увеличивает вязкость за счет увеличения размера комплексов, это SiO2, AI2O3, Сr2O3.
При добавлении некомплексообразующих СаО, MgO, NaO, K2O и TiO2 вязкость расплавов уменьшается, так как, превращаясь в катионы, они отдают свой кислород комплексам, прекращая их рост.
Переработка силикатных расплавов в волокно происходит в основном в интервале температур 1300-1400ºС, вязкость при этом должна находится в пределах 0,5 – 5 Па∙с.
Каждый компонент влияет на свойства расплава и минеральной ваты по-разному:
SiO2 – повышает вязкость силикатных расплавов и химическую стойкость волокон в любых средах, удлиняет интервал вязкости;
В2О3 – оказывает сильное флюсующее действие, уменьшает поверхностное натяжение расплава и температуру верхнего предела кристаллизации, значительно улучшает выработанные свойства, увеличивает длину волокна, повышает устойчивость к кислотам и щелочам;
AI2O3 – повышает вязкость и поверхностное натяжение расплавов, прочность и модуль упругости волокон, устойчивость к воде, кислотостойкость, температуростойкость;
Fe2O3 – снижает вязкость расплава, повышает поверхностное натяжение и химическую устойчивость;
СаО, MgO – при высоких температурах понижают вязкость расплава, повышают склонность к кристаллизации. При содержании СаО, равном 45%, вязкость возрастает, так как образуется С2S. Влияние MgO на снижение вязкости особенно заметно при повышении содержания до 9% и более. Повышение содержания MgO за счет СаО приводит к значительному повышению химической стойкости волокон;
TiO2 – улучшает химическую устойчивость ко всем средам, является хорошим плавнем и значительно снижает вязкость расплава, но повышает склонность к кристаллизации;
ZrO2 – очень сильно повышает устойчивость ко всем средам и является единственным окислом, который делает многокомпонентные стекла устойчивыми к щелочам; увеличивает тугоплавкость расплава и повышает склонность к кристаллизации. Введение ZrO2 осуществляется, как правило, за счет SiO2;
FeO – снижает вязкость, но повышает поверхностное натяжение расплава, снижает начальную температуру разрушения волокон, одновременно повышая температуру спекания;
MnO – в небольших количествах увеличивает химическую устойчивость, снижает вязкость и склонность к кристаллизации;
Na2O, K2O, LiO – являются плавнями и снижают склонность к кристаллизации, но уменьшают устойчивость волокон в воде. Повышенное содержание K2O уменьшает поверхностное натяжение расплава.
Расплав для получения рядовой минеральной ваты содержит в основном SiO2, AI2O3, СаО и MgO. Содержание их находится в пределах (% по массе): SiO2 – 35-60, AI2O3 – 5-15,СаО – 20-35, MgO – 5-15. В небольшом количестве могут присутствовать Fe2O3, FeO, Na2O, K2O и MgO.
refdb.ru