пропорции объема ведрами, состав, приготовление
Дата: 21 августа 2017
Просмотров: 3486
Коментариев: 1
Состав и пропорции опилкобетона, объем ведрами
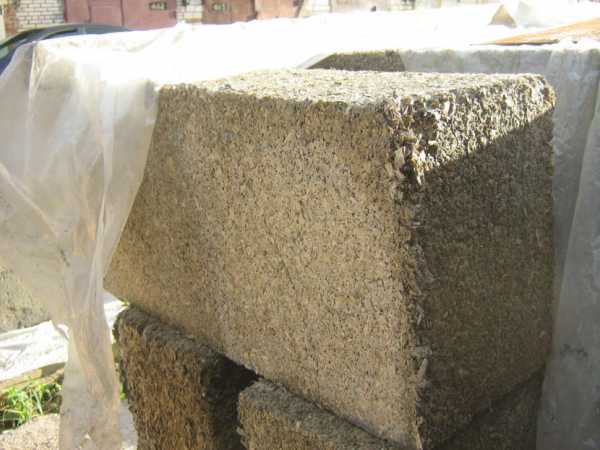
Специалистами строительной отрасли ведется постоянный поиск новых материалов. Одной из разновидностей легкого бетона, в котором используются опилки древесины, является опилкобетон. Он характеризуется повышенными теплозащитными характеристиками, огнестойкостью, соответствует санитарно-гигиеническим нормам. Смешивая бетон с опилками несложно приготовить своими руками готовые блоки для постройки коттеджей, домов, а также строений хозяйственного назначения. Важно соблюдать пропорции и технологию изготовления. Рассмотрим детально технологические нюансы, разберемся с различными вариантами рецептуры.
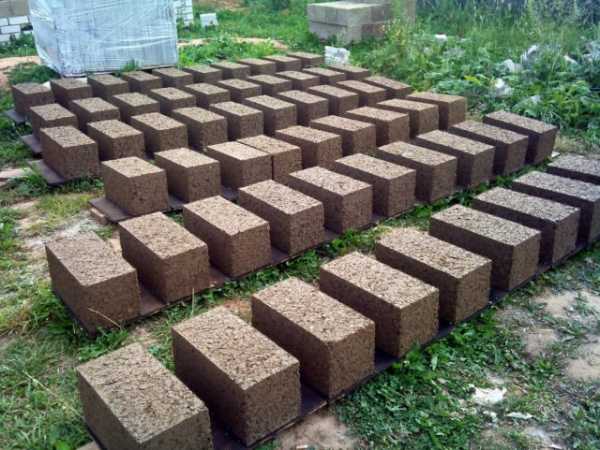
Готовые блоки используют для строительства малоэтажных зданий
Изготовление опилкобетона своими руками
Самостоятельное изготовление легкого бетонного композита осуществляется по следующему алгоритму:
- Выполняется подготовка необходимых материалов. Составляющие нет необходимости приобретать предварительно. Все компоненты можно заготовить непосредственно перед изготовлением, посетив магазины или склады стройматериалов, а также воспользовавшись отходами производства деревообрабатывающих предприятий.
- Смешиваются ингредиенты согласно пропорции. Перемешивание компонентов может осуществляться механическим способом с применением бетоносмесителя или ручным путем с использованием лопат. Автоматизация технологического процесса путем применения бетономешалки повышает производительность, улучшает интенсивность смешивания, положительно влияет на качество продукции.
- Производится формовка. Преимущественно используется групповой процесс формовки, когда предварительно перемешанный состав заливается в несколько десятков форм. Применяются единичные и групповые формы разборной конструкции, изготовленные из древесины толщиной 2 см и обитые металлом или пластиком. Применение полиэтиленовой пленки облегчает извлечение готовых изделий.
- Осуществляется сушка готовой продукции естественным путем. Снятие форм производится через 4–5 суток после заливки путем ослабления затяжки барашковых гаек, извлечения резьбовых шпилек и разборки формовочного ящика. Длится процесс естественной сушки в зависимости от пород древесины до трех месяцев, в течение которых значительно снижается концентрация влаги, и изделие приобретает эксплуатационную прочность.
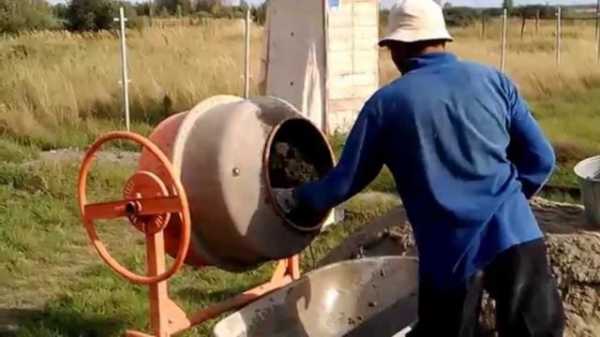
Стандартный состав бетона с опилками: цементно-песочная смесь, деревянная стружка, известь (по необходимости)
Бетон с опилками – состав и соотношение компонентов
Опилкобетон производится на основе ингредиентов, полученных промышленным путем и составляющих природного происхождения:
- портландцемента марки М300;
- просеянного песка размером до 1,8 мм;
- извести;
- древесных опилок;
- воды.
Опилка следующих видов деревьев обеспечивает необходимое качество продукции:
- сосны;
- ели;
- березы;
- тополя;
- ясеня;
- дуба;
- лиственницы.
Период твердения блоков из различных видов древесины значительно отличается. По скорости набора прочности лидирует сосна, у которой процесс твердения завершается через полтора месяца после заливки. На последней позиции находится лиственница, блоки из которой можно использовать через 3,5 месяца после заливки.
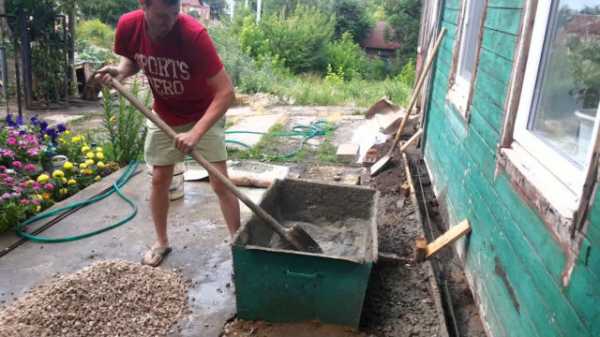
Каждая марка арболита готовится по определенным пропорциям
Концентрация наполнителя и песка влияет на плотность материала. При уменьшении его концентрации удельный вес блоков снижается, что улучшает теплотехнические характеристики, однако уменьшает прочность. Увеличение объема вяжущих ингредиентов и песка повышает водонепроницаемость, а также устойчивость к воздействию отрицательных температур.
Рекомендуемое соотношение компонентов для приготовления состава средней плотности из 100 кг древесной стружки, составляет:
- цемент – 75 кг;
- известь – 50 кг;
- песок – 175 кг.
Пропорции и состав опилкобетона в ведрах
Для приготовления опилкобетона добавлять компоненты ведрами достаточно удобно.
Состав опилкобетона в ведрах регламентируется следующими пропорциями:
- Для марки опилкобетонных блоков М10 соотношение цемента, песка, тырсы и извести составляет 1:2,2:6,5:1,5.
- Опилкобетон, маркируемый М15, включает указанные выше ингредиенты в соотношении 1,2:3:7,8:0,8.
- Блоки с маркировкой М25 содержат портландцемент, просеянный песок, древесную стружку и известь в пропорции 1:2,8:6,4:0,8.
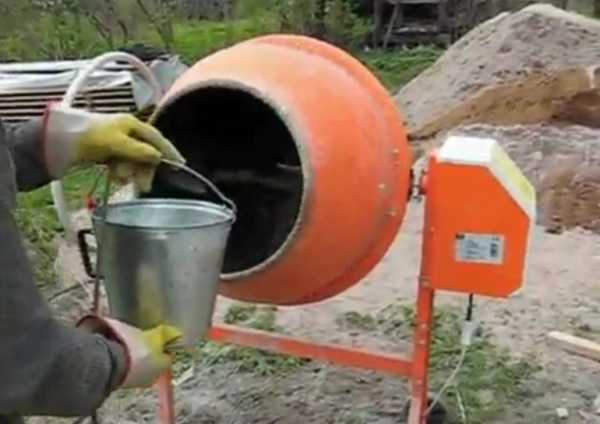
Важно не занижать количества вяжущего материала
На примере материала с маркировкой М10 рассмотрим пропорции ингредиентов при введении ведрами. Смесь включает:
- портландцемент – 1 ведро;
- песок – 2 ведра с горкой;
- опилки – 6 с половиной ведер;
- известь – полтора ведра.
Соблюдая указанные пропорции несложно своими руками подготовить раствор для изготовления блоков различных марок.
Опилкобетон – приготовление смеси
Технологический процесс приготовления смеси можно осуществлять следующим образом:
- подготовить цементный раствор путем разведения портландцемента водой с последующим добавлением просеянного песка, извести, древесной стружки;
- осуществить смешивание извести с тырсой, затем ввести портландцемент с песком, развести перемешанные ингредиенты водой.
Независимо от выбранного метода приготовления, необходимо обеспечить однородность смеси. Важным моментом технологии является предварительная сушка стружки, уменьшающая концентрацию влаги. Правильно приготовленная смесь начинает твердеть через пару часов. Именно поэтому важно готовить раствор в объеме, соответствующем количеству имеющихся форм. При укладке бетонной смеси следует тщательно уплотнить состав с целью недопущения образования воздушных пор.
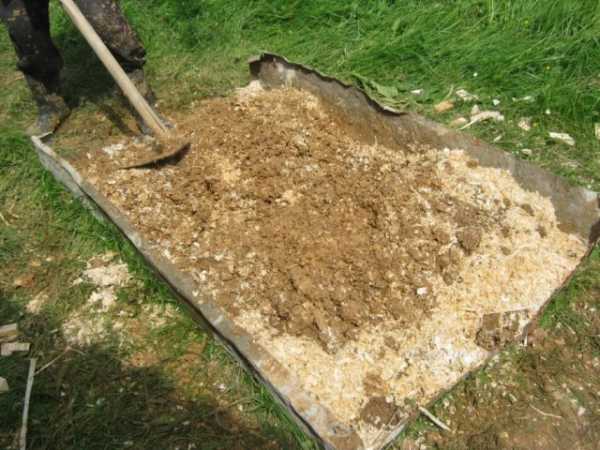
Следует знать, что известь повышает взаимные адгезионные способности компонентов песко-цементного композита
Растворы для различных марок
В зависимости от концентрации ингредиентов опилкобетонные блоки делятся на следующие марки:
- М5. Характеризуется пониженной до 0,6 т/м3 плотностью, уменьшенным коэффициентом теплопроводности, равным 0,18. На один 50-килограммовый мешок цемента необходимо взять по 0,2 тонны опилок и извести, а также 20 кг присеянного песка;
- М10. Коэффициент теплопроводности составляет 0,21, а удельный вес возрастает до 0,8 т/м3. Для приготовления мешок портландцемента необходимо перемешать со 100 кг стружки и 100 кг песка, а также добавить 80 кг извести;
- М15. Плотность и коэффициент теплопроводности увеличиваются и составляют, соответственно, 0,8 т/м3 и 0,24. Для приготовления на 50 кг цемента вводится 70 кг тырсы, 30 кг извести и 115 кг песка;
- М20. Удельная плотность достигает величины 0,95 т/м3, а величина коэффициента теплопроводности увеличивается до 0,3. Опилкобетон готовится путем смешивания по 50 кг цемента и опилок с добавлением 130 килограмм песка и 15 кг извести.
С увеличением марки опилкобетона возрастает коэффициент теплопроводности, увеличивается плотность. Блоки высоких марок позволяют возводить увеличенные помещения, в которых из-за высокого коэффициента теплопроводности сложно поддерживать комфортный температурный режим. Введение специальных добавок, вымачивание древесного сырья в жидком стекле и известковом молоке позволяет использовать сырье с увеличенной влажностью и повышает огнестойкость блоков.
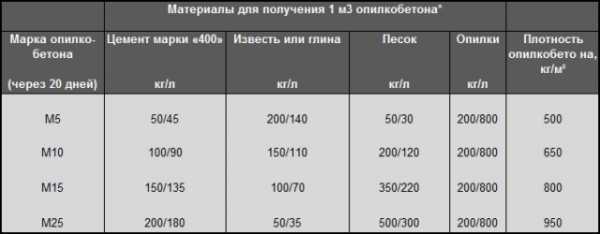
Марка М10 требует такие количества: полведра вяжущего сырья, ведро с горкой очищенного песка и немногим больше трех ведер со стружкой
Готовность перемешанных компонентов определяется путем сжатия подготовленной смеси ладонью. Пластичный и готовый к формовке материал сохраняет следы пальцев, что свидетельствует о готовности раствора к заливке.
Введение в раствор глины вместо извести
В состав материала допускается вводить вместо извести глину, что не сказывается на качестве изделий. Технология использования глины предусматривает следующие этапы:
- смешивание древесного сырья с портландцементом и песчаной массой;
- введение в смесь глиняного теста, тщательное перемешивание;
- добавление воды небольшими дозами;
- перемешивание состава до рабочей консистенции.
Предусмотренные рецептурой пропорции известкового и глиняного теста остаются неизменными.
Раствор на основе гипсового вяжущего вещества
Допускается в качестве вяжущего вещества использовать строительный гипс вместо портландцемента. Может возникнуть вопрос, как замедлить интенсивность твердение гипса при смешивании с водой? Проблема довольно просто решается введением в воду моющего средства, которое способствует замедленному твердению гипса.
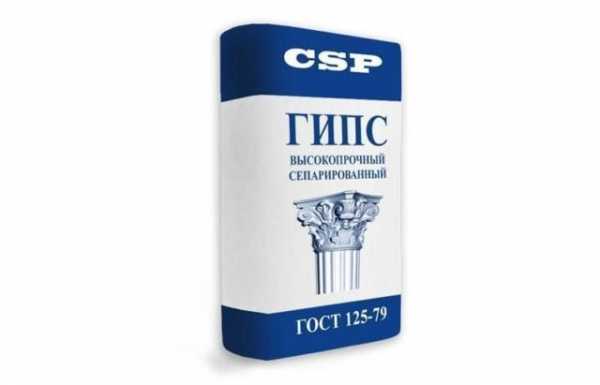
Для обеспечения высокой скорости твердения в М5 добавляют гипс
Особенности применения строительного гипса:
- увеличение по сравнению с цементом скорости твердения блоков в 5 раз;
- незначительное увеличение затрат на изготовление опилкобетонной продукции.
Среди специалистов по строительству ведется полемика о возможности применения опилкобетонных блоков на основе гипса для возведения наружных стен зданий. Надежная защита опилкобетона от отрицательного влияния атмосферных факторов позволяет решить проблему поглощения материалом влаги.
Размер опилок
Несмотря на то что в ряде источников отмечается необходимость просеивания опилок на сите с квадратной ячейкой размером 1 см, размер используемой стружки не имеет принципиального значения.
Важно обратить внимание на следующие моменты:
- следует вводить древесное сырье, являющееся вяжущим веществом, в требуемом количестве;
- проблематично получить однородный состав при использовании опилок, крупность которых отличается в сотни раз;
- древесная стружка с калибровочных станков и оцилиндровочного оборудования не используется при изготовлении опилкобетона;
- целесообразно применять опилки с пилорамы, оснащенной ленточной пилой или дисковым рабочим органом.
Жирные растворы, содержащие вяжущее вещество в избыточном количестве, менее восприимчивы к крупности опилок по сравнению с тощими составами.
Итоги
Руководствуясь пропорциями, приведенными в материале статьи, несложно своими руками подготовить качественную смесь для изготовления опилкобетона необходимой марки. Самостоятельно изготовленные с соблюдением технологии опилкобетонные блоки отличаются прочностью, морозостойкостью, доступной ценой. Освоив технологию изготовления, можно оценить достоинства экологически чистого и простого в изготовлении материала.
pobetony.ru
Цемент с опилками: пропорции
В современном строительстве для теплоизоляции перекрытий и других конструкций нередко используют опилочный цемент. От большинства других защищающих от температурного воздействия материалов он отличается наличием в составе органического заполнителя (в основном, древесных опилок). В такой цемент добавляют большое количество вяжущих веществ, обеспечивающих его высокую прочность и долговечность. Всё это делает стоимость материала довольно высокой, однако увеличивает и его теплоизоляционные свойства, вдвое превышающие аналогичные показатели фибролита и примерно в 15 раз – обычного кирпича.
Рецепты опилочного бетона
Блоки из опилочного цемента изготавливаются заранее, так как до производства работ по их монтажу материал должен приобрести достаточную влажность и прочность. Рецептов же приготовления блоков существует много:
- самые лёгкие блоки получаются с использованием цемента и опилок в массовой пропорции 1:1. Обычно берут 50 кг опилок и стружки, столько же сухого цемента и ровно 100 литров воды. Материал получается прочнее, а расход вяжущего сокращается, если органический наполнитель будет смешанным. Например, если кроме опилок в него добавят перемолотые твёрдые стебли растений;
- более тяжёлый, зато и имеющий повышенную прочность материал получают, используя следующий состав (пропорции уже объёмные): 1 часть цемента М300, 2 части среднеразмерного песка и 6 частей опилок (или смеси). Получившийся опилочный цемент имеет марку 10–15. А сделанные из него блоки приобретают достаточную для строительных работ прочность через 90 дней.
Материал наполнителей
Органическими наполнителями, которые добавляют в различные марки опилочных цементов, могут быть:
- свежие измельчённые отходы от лесозаготовительных работ, а также из лесопильных и других деревообрабатывающих установок. Лучше всего подходят для цемента опилки хвойных деревьев;
- растительная резка, представляющая собой результат дробления стеблей риса, конопли и льна;
- старые опилки, которые перед добавлением в материал следует предварительно обработать. Антисептиком в этом случае выступает кремнефтористый натрий и 25%-ный аммиак, которых на 100 л цементного раствора добавляют соответственно 0,4 кг и 0,65 литра.
Особенности приготовления
Приготовление материала похоже на получение обычного бетона. В первую очередь берётся вяжущий материал (с целью экономии лучше всего приобретать цемент оптом) и перемешивается с песком. Далее в смесь добавляют опилки, а потом воду – причём, малыми порциями, например, из лейки с небольшими отверстиями. Недостаточное количество воды может привести к тому, что опилочный цемент не достигнет требуемой прочности, а избыточное – к медленному затвердеванию. Правильно же приготовленный раствор не разваливается при сжатии в ладони и не смачивает кожу, а лишь увлажняет.
Поверхность цементных блоков после их изготовления затирают цементом, увеличивая их прочность. А уже после установки на место материал штукатурят или даже облицуют в половину или четверть кирпича.
samanka.ru
Стяжка из опилок – пропорция опилкобетона, описание, назначение и использование
Доброго времени суток дорогие читатели!
УНИКАЛЬНАЯ ФОРМУЛА, В ПОИСКОВИКАХ ТАКОГО НЕТ!
Только природные материалы в вашем доме, для вашего здоровья и для здоровья ваших детей. Я использую ее уже около пяти лет. На фото и штукатурка и стяжка выполнены с добавлением опилок. Только положительные отзывы.
Состоит стяжка из двух слоев:
– первый слой нижний – одного ведра цемента (М 400), двух ведер песка, шести ведер опилок.
– второй слой верхний – одного ведра цемента (М 400), двух ведер песка, трех ведер опилок.
Также в стяжку из опилок можно добавить не много гашеной извести (пушонки) 3 кг на одно ведро цемента – для первого нижнего слоя. И для второго верхнего слоя – 1,5 кг гашеной извести (пушонки).
Так как в стяжке у нас используется органический утеплитель (опилки), то лучше добавлять не много извести. Мы не добавляли известь в стяжку и все нормально.
Удивляет, почему до сих пор эту стяжку массово не применяют в строительстве. Наверное хорошая реклама других теплоизоляционных материалов. Задайте вопрос, кто будет рекламировать и продавать обычные опилки. Существует много противоречивых мнений по поводу стяжки с добавлением опилок и куча бесполезных советов. Давайте вместе полностью разберемся в этой уникальной, дешевой и экологически чистой технологии.
Преимущества:
– Очень теплая.
– Легкая.
– Прочная.
– Экологически чистая.
– Не поддерживает горение.
– Повышенная прочность на изгиб.
– Шумоизоляция.
– Дешевая, опилки летом можно даром набрать в цеху лесопилки. Вам спасибо скажут, что убрали мусор.
– Удобна для обработки.
Недостаток:
– Слой 100-150 мм сохнет около месяца (если без химических добавок).
Арболит – легкий бетон, на основе цементного вяжущего, органических заполнителей (до 80-90% объема) и химических добавок. Также известен как древобетон, опилкобетон, оргабетон. Разработан и стандартизирован в 60-е годы в СССР, где было построено более 100 арболитовых заводов.
Как видим, использовался очень давно – дедовские методы – и мы позабыли о нем, хотя сегодня многие современные материалы уступают по многим наиболее важным показателям. Ниже мы подробно разберем практически все показатели, чтобы полностью избавиться от скептического мнения по поводу арболита раз и навсегда.
а) Порядок подачи материалов в мешалку.
– Вода, добавлять понемногу (зависит от влажности материалов).
– Сухие мелкие опилки, лучше всего хвойных пород. Ниже подробнее.
– Цемент (М 400).
– Песок, средней фракции, не принципиально речной или карьерный, желательно без глины и не самый мелкий (Мк 2,0 – 2,5).
– Для минерализации наполнителя используют хлорид кальция на одно ведро цемента 250 грамм (пищевая добавка E509), нитрат кальция, жидкое стекло, сульфат аммония, известь, блокирующие негативное действие органических веществ на затвердевание цемента. Но мы делаем без добавок. Для стяжки добавки не обязательны, проверено временем.
Опилкобетон (арболит) должен получиться по густоте как магазинная сметана, слишком жидкий будет дольше схватываться (около месяца, без химических добавок).
б) Порядок выполнения работ.
Ничего сложного. Делаем как обычную стяжку, только верхний слой делаем с меньшим количеством опилок, три ведра (для прочности).
Выставляем две рейки (направляющие) по уровню. Получается одна полоса шириной около 700 мм (расстояние между рейками). Вначале обливаем рейки, чтобы не болтались в процессе работы . Заливаем первый слой около семи сантиметров (одно ведро цемента (М 400), два ведра песка, шесть ведер сухих опилок).
Второй верхний слой толщиной около трех сантиметров (одно ведро цемента (М 400), два ведра песка, три ведра сухих опилок). Стягиваем уголком по рейкам или полутером. После того как первая полоса залита, достаем дальнюю рейку от вас. И образовавшуюся яму от рейки СРАЗУ, пока свежая стяжка, заделываем опилкобетоном.
Выставляем по уровню только что извлеченную рейку из опилкобетона и повторяем все сначала. Для специалистов более высокого уровня можно пользоваться и одной рейкой.
НЮАНС. На грунт стяжку заливать не советую. По всем нормам необходимо делать ВСЕГДА двойные стяжки, даже бетонные с гидроизоляцией между ними (меньше сырости в доме). Первую сделайте минимальной толщиной около трех сантиметров. Если грунт не нарушен можно без арматуры (состав: одно ведро цемента, три ведра песка, два ведра щебенки).
Если же грунт нарушен, необходимо подсыпать песка сантиметра 3 – 4, утрамбовать или пролить водой. Положить арматуру диаметром 6 мм, размер ячейки 250 на 250 мм и залить стяжкой. Сверху сделать гидроизоляцию по первой стяжке праймером или раскатать обычный рубероид с нахлестом 15 сантиметров.
Вторым слоем будет арболит (древобетон). При желании, для тепла, слой можно сделать по-больше, около 15 сантиметров. И самое приятное – цена этой стяжки будет дешевле приблизительно на 60%, чем цементно-песчаная, плюс куча достоинств.
ВЫВОД: в итоге у нас получилась прекрасная прочная стяжка. Если вы ее примените на первом этаже – будет теплее пол, по сравнению с бетоном. Если на втором этаже – получится прекрасная шумопоглощающая стяжка, которая намного теплее обычной цементной стяжки.
Если сделаете на ЧЕРДАКЕ по плитам (толщиной около 15-20 сантиметров, в первый слой 8 ведер опилок), получится очень дешевое утепление чердака, показатель для Украины, у вас может быть холоднее, тогда ориентируйтесь на климат вашего региона.
г) Штукатурка с добавлением опилок.
В начале статьи вы видите фото штукатурки на стенах с добавлением опилок.
Первый слой (накидочный) состав: штукатурка изготовлена из известкового раствора и для прочности немного цемента М 400. На три ведра готовой смеси необходимо добавить одно ведро опилок. Толщина первого слоя около 3-4 сантиметра, чтобы было тепло.
Второй слой (затирочный) состав: известковый раствор, немного цемента, опилки добавлять НЕ НАДО. Толщина второго слоя минимальная.
в) Качество стяжки из личного опыта.
В 2008 году в доме делали стяжку с добавлением опилок (арболит). По ошибке залили в комнате с теплым полом (водяной) толщиной семь сантиметров от низа трубы. После полного высыхания включили теплый пол и к нашему изумлению температура пола не изменилась.
Подняли температуру на котле до 70 градусов, практически никаких изменений, после этого эксперименты прекратили и, пока заказчик не в курсе, стали разбирать стяжку из опилок по-быстрому. Сюрпризы продолжались, стяжка оказалась достаточно прочной, разбирали с помощью перфоратора. Стяжка забрала намного больше времени на разборку, чем мы думали.
г) Формула арболита большей прочности М-50, D-1100 кг/м3. Для изготовления блоков.
– Цемент (M 400) 20 кг/16,6 л; – (1 ведро).
– Песок (Мк 2,0 2,5) 59 кг/39,3 л; – (2,4 ведра).
– Опилки хвойных пород 20 кг/80 л; – (4,8 ведра).
– Хлористый кальций и другие добавки 500 гр/0,45 л.
– Вода около 10 литров (в зависимости от влажности используемых материалов).
Метод объемного вибропрессования на качественном оборудовании обеспечивает значительное уплотнение материала.
Пример: для строительства жилых домов – одноэтажных, двухэтажных – мы в основном используем крымский ракушечник марки 35. Все здания бескаркасные. Перекрытия – ж/б круглопустотные плиты – ложатся на ж/б пояс, а под ним ракушечник (М-35), который прекрасно держит нагрузку плит и вышележащих конструкций.
Если вы находитесь далеко от Крыма и привезти ракушечник слишком дорого, можно вполне использовать блоки из арболита. Они тоже теплые, как ракушечник и обладают более высокой маркой (М-50).
Возможно недалеко от вас находится производство таких блоков, ведь древесные опилки есть практически везде. Можете смело приобретать. Так как опилки стоят копейки, то цена таких блоков тоже должна быть низкой.
Скоро будет новая статья с объективной критикой шлакоблока, если не хотите пропустить, подпишитесь на бесплатную рассылку в правом верхнем углу ЛУЧШЕЕ-ПОДПИСЧИКАМ, или в конце статьи.
д) Подготовка древесных опилок.
Для изготовления арболита можно использовать опилки практически из всех пород дерева. Опилки из хвойных пород дерева меньше подвержены гниению. Желательно, но не обязательно, выдержать свежие опилки под навесом 2-3 месяца.
Вы можете спросить, зачем сушить опилки, если их снова придется мочить при замешивании в мешалке. Дело в том, что во время сушки свежие опилки интенсивно выделяют органические вещества, замедляющие процесс схватывания (не ухудшают, а замедляют).
Эту тему мы обсуждаем ЗДЕСЬ
.
.
а) Экологичность. На сегодняшний день очень актуальный показатель.
Арболит – состоит из природных, безопасных и экологически чистых материалов: опилки, песок, цемент. Благодаря уникальным санитарно-гигиеническим характеристикам материалов, содержанию большого количества опилок (более 60%) арболит по многим показателям соответствует древесине, обеспечивая прекрасный микроклимат в домах. Имеет отличные показатели звукопоглощения.
Вывод: арболит экологически чистый строительный материал, отвечает всем современным санитарно-гигиеническим нормам. Почти все современные “модные” материалы значительно уступают арболиту по экологичности.
б) Теплотехнические показатели. Из-за постоянного роста цен природных ресурсов, требования постоянно увеличиваются.
Арболит обладает отличными теплотехническими показателями. Теплопроводность арболита (блоки) плотностью 800 кг/м3 равна 0,32 Вт/(м·К). Давайте сравним эти показатели с одним из самых “модных” на сегодняшний день, лидером строительных материалов, газо-пенобетоном. Теплопроводность газо-пенобетона плотностью 600 кг/м3 равна 0,24 Вт/(м·К).
Можно сделать вывод, что арболит практически не уступает газо-пенобетону по теплотехническим показателям. Для большей наглядности ниже приведем сравнения и с другими материалами:
– Керамзитобетон 0,92 Вт/(м·К).
– Глиняный кирпич 0,81 Вт/(м·К).
– Железобетон 2,04 Вт/(м·К).
– Сосна вдоль волокон 0,35 Вт/(м·К).
– арболит 0,07-0,17 Вт/(м·К)
– пенобетон 0,14—0,3 Вт/(м·К).
– древесина 0,15 Вт/(м·К).
Итак: если вы сделаете стену 500 мм из глиняного кирпича теплопроводностью 0,81 Вт/(м·К), то это будет соответствовать стене в 200 мм из арболита (блоки) 0,32 Вт/(м·К).
Вывод: арболит отвечает всем необходимым и установленным теплотехническим требованиям, предъявляемых к современным строительным материалам. Показатели теплосопротивления арболита превосходят большинство традиционных строительных материалов.
в) Прочность арболита.
Проведенные испытания на прочность арболита (растяжение и изгиб) показали, что данный материал превосходит большую часть современных строительных материалов. В этих испытаниях он значительно обошел даже такой часто используемый материал, как пено-газобетон. Прочность арболиту обеспечивают опилки, которые представляют собой армировку.
Уникальность данного материала состоит в том, что изделия из арболита (блоки, стяжки, штукатурка) могут быть разной марки по прочности – на сжатие, на изгиб, по плотности. Предел прочности на сжатие арболита варьируется от М5-М10 для теплоизоляционного, до М25-М50 и даже до М100 – для конструкционного. Арболит обладает повышенной прочностью на изгиб и растяжение.
Вывод: значительно превосходит по прочности современных лидеров в строительстве!
г) Огнестойкость (пожаробезопасность).
Арболит не поддерживает горение. Казалось бы, состоит из 60% опилок, что является горючим материалом, но изготовлен-то данный материал по определённой технологии. А именно: цементно-песочная стенка надежно закрывает все деревянные опилки, иными словами каждая древесная пластинка герметично упакована в цементную скорлупу.
В результате чего при нагревании материала органические волокна самозатухают. Предел огнестойкости, при температуре 1100-1200 С, составляет более двух с половиной часов, а несущая способность сохраняется и спустя более трёх часов воздействия высокой температуры.
Арболит по огнестойкости значительно превосходит популярный строительный материал пенополистиролбетон, который соответствует требованиям огнестойкости. Заполнитель пенополистиролбетона – это пенопластовые шарики. Цементно-песчаные стенки — защищают пенопласт от возгорания, но в случае длительной температуры, как вы думаете, что будет гореть “лучше” – шарики пенопласта или опилки?
Вывод: хотя арболит и содержит большое количество опилок (около 60%) является не горючим материалом, благодаря технологии производства. Использование арболита уместно при строительстве любого объекта. Огнестойкость арболита выше некоторых современных строительных материалов.
д) Водопоглощение арболита (процентное отношение влаги в материале).
Отвечает за морозостойкость. Чем воды меньше, тем лучше. Водопоглощение арболита 8 – 12%, зависит от плотности материала. Если обработать специальным водоотталкивающим составом опилки, входящие в состав опилкобетона, а также применить гидрофобизирующую добавку для бетона, то водопоглощение снизится еще больше. Это теория, нас она не очень интересует.
ПРАКТИКА: арболитовая стяжка – лежит на гидроизоляции, сверху шпаклюется и грунтуется под ламинат или керамогранитную плитку. Защищена со всех сторон. Арболитовая штукатурка – тоже шпаклюется и грунтуется под обои или покраску.
Арболитовые блоки – снаружи защищены лицевым кирпичем либо наружной шукатуркой, изнутри грунт, штукатурка, шпаклевка. Утепление чердака арболитом – лежит на пароизоляции, если крыша построена правильно, то чердак САМОЕ СУХОЕ МЕСТО в доме. Теперь сравним водопоглощение арболита с другими современными материалами:
– Газо— и пенобетон, газо— и пеносиликат — 8-10%
– Керамзитобетон — 8%
– Кирпич глиняный (ГОСТ 530-80) — 2-4%
– Полистиролбетон (ГОСТ Р51263-99) — 8%.
– Сосна и ель вдоль волокон (ГОСТ 9463-72) — 20%
– Арболит 8 – 12%
В строительстве применяется гипсовые изделия (гипсоблоки, позагребнивые) с водопоглощением 6-15%. Я строил гипсовые перегородки в санузлах. Гипсовые плиты были зеленоватого цвета и пропитаны специальной водооталкивающей добавкой. Если использовать такие же добавки для арболита, его водопоглощение можно еще больше снизить.
Вывод: арболит отвечает требованиям по водопоглощению и не уступает современным материалам. А при использовании добавок, может даже значительно лидировать.
е) Вывод по основным характеристикам арболита:
– Экологичность – почти все современные “модные” материалы значительно уступают арболиту.
– Теплотехнические показатели – показатели теплосопротивления арболита превосходят большинство традиционных строительных материалов. Варьируется от 0,07 – 0,9 Вт/(м·К). Можно сделать под любой запрос.
– Прочность – можно строить как одноэтажные, так и многоэтажные здания.
– Огнестойкость – практически негорючий материал. Значительно лучше некоторых лидеров.
– Водопоглощение – не хуже чем у современных материалов, с добавлением специальных добавок будет лидером.
– Универсальный материал, используют как – стяжка, штукатурка, утеплитель, стеновые блоки.
– Очень легок в обработке благодаря высокому содержанию опилок.
Итог: удивляюсь, почему до сих пор никто не запатентовал такой прекрасный, универсальный, дешевый материал.
Думаю скептикам добавить больше нечего.
Я использую арболит уже более пяти лет. Строю на заказ. Только положительные отзывы. Если буду строить дом себе, то использую:
– Стяжки из арболита.
– Штукатурка из арболита. Состав: на три ведра готового раствора для штукатурки добавляем одно ведро опилок.
– Стеновые блоки из арбобита (марка 35) или ракушечник (марка 35).
– Утеплю чердак арболитом.
За копейки из природных чистых материалов получится прекрасный дом. Для здоровья моей семьи!
.
|
Закончил лить стяжку.Впечатления от работы положительные.Понравилось что не разводиться болото как от цементно песчаной. На мой взгляд проще ее делать следующим образом.
В два слоя как вы и описывали метод. Но с помощью стяжечного лазерного уровня и другим каким способом без маяков. Затем пролить мешком растекайки.Получим и гидрозащиту и крепость и прочие опции.
Для себя решил применять ее по возможности всегда.
Статью вашу в скором времени скопирую и выложу от вашего имени. Спасибо за
полный технологический процесс.
Самое интересное и полезное на эту же тему:
stroyimdom.com
пропорции объема ведрами и состав
Опилкобетон – это легкий класс пескоцемента с экологически чистым составом и абсолютно безвредными для человека компонентами. На опилкобетоне получаются блоки с высокими санитарно-гигиеническими параметрами, паропроницаемостью и звукопоглощением. Другие названия материала – арболит, деревобетон.
Готовые блоки используют для строительства малоэтажных зданий. При изготовлении опилкобетона отсутствуют значительные энергетические и тепловые затраты, что снижает себестоимость готовой продукции. Рассмотрим состав опилкобетона.
Стандартное соотношение компонентов
Арболит выполняет те же функции, что и классический вяжущий строительный материал. Стандартный состав бетона с опилками: цементно-песочная смесь, деревянная стружка, известь (по необходимости). Допускается использование древесной стружки, которая увеличивает прочность моноблоков. Перед приготовлением сухую смесь следует просеять на ситах с размером ячеек 20х20, 10х10, 5х5 мм, а стружки – на ситах величиной 10х10 мм.
Каждая марка арболита готовится по определенным пропорциям. Классическими соотношениями считаются:
- стружки к извести — 1:1;
- вяжущего вещества к воде — 1:2.
Песок и известь нужно брать в одинаковых количествах. Достаточное количество воды на 1м3 готовой смеси является 250 — 300 литров. При этом жидкость не должна выталкиваться из раствора, а находиться в нем.
Вернуться к оглавлениюПропорции
Для трех наиболее популярных марок арболита вместо 1м3 предлагаются конкретные объемы основных компонентов ведрами (далее сокращение в.).
- Марка М10 требует такие количества: полведра вяжущего сырья, ведро с горкой очищенного песка и немногим больше трех ведер со стружкой.
- Арболит М15 готовится из чуть больше половины емкости трехкальциевого силиката, полутора в. песка, четырех частей со стружками.
- Состав опилкобетона М25 получается из половины объема силиката, немногим меньше чем полтора в. песка, трех в. с горкой стружки.
Пропорции этими емкостями были подобраны и отработаны давно для каждой марки, чтобы облегчить строителям задачу без использования расчетов через величины в 1м3. В качестве отдельного компонента или возможной добавки допустимо использование гашеной извести. Цель ее примешивания — обессахаривания стройсмеси. Вместо нее можно добавлять пушонку.
Вернуться к оглавлениюПриготовление для стяжки
Для стяжки используется высокая марка вяжущего компонента М400. Приготовить ее можно своими руками. Смесь состоит из верхнего и нижнего слоев. Оптимальное соотношение силиката, песка и стружки:
- для нижнего слоя составляет 1:2:6, также допустима добавка 3 кг гашеной извести;
- для верхнего – 1: 2:3 с добавкой или без 1,5 кг известки.
Первой наливается вода, затем последовательно добавляется стружка, цемент, песок и в конце по необходимости – добавки. Важным условием смешения является достижение густоты раствора как у 20%-ой сметаны. Более жидкие смеси сохнут дольше.
Стяжке толщиной 10 – 15 см такого состава сохнуть месяц. Ускорить сушку можно примешиванием специальных добавок, таких как нитрат или хлорид кальция, жидкое стекло, аммоний сульфат. Эти вещества ускоряют процесс минерализации, поэтому заливка твердеет быстрее.
Вернуться к оглавлениюСостав раствора для различных марок
Помимо М10, М15, М25 существуют другие марки арболита с разным составом. Например, смесь М5 высокой плотности можно приготовить своими руками из таких количеств, измеренных в ведрах: 4,5 частей силиката, смешанного с 3 и 80 частями песка и опилок, соответственно. Для обеспечения высокой скорости твердения в М5 добавляют 14 в. известки или глины. Количество ингредиентов можно пересчитать на 1м3. Такой продукт подходит для создания подвалов с хорошей теплоизоляцией.
Промежуточная марка М20 готовится из 18, 30 и 35 в. наполнителя, песка и известки, соответственно. Пропорции берутся из расчета на 80 частей. В промышленных масштабах, а именно для возведения стен, используются М10 и М15 и готовятся они как представлено в таблице.
Таблица: Приготовление строительных смесей М10 и М15:
- ингредиенты М10; М15;
- опилки 80; 80;
- цемент 9,5; 13,5;
- песок 12; 21;
- известь или глина 10,5; 7.
Важно не занижать количества вяжущего материала. Это может привести к потере будущей конструкцией плотности, водонепроницаемости, устойчивости к температурным колебаниям, коррозионной стойкости арматуры. Однако преувеличение содержания цемента удорожает себестоимость готового продукта.
Вернуться к оглавлениюРаствор с известью и без
Следует знать, что известь повышает взаимные адгезионные способности компонентов песко-цементного композита. К тому же использование или отсутствие в его составе глины существенно влияет на количественное соотношение основных ингредиентов. Решить, применять ее или нет, нужно на начальном этапе строительства в зависимости от назначения готового монолита, марки прочности изделия.
Максимальной плотностью обладают растворы без глины. На 10 литров рабочей смеси потребуется 2 кг стружки, 2 кг (М15) или 3 кг (М25) цемента, 6,3 кг (М15) или 6,7 кг (М25) песка. Эти же марки с известью будут содержать 1,5 и 2 кг цемента, 3,5 и 5 кг песка, 1 и 0,5 кг глины на 2 кг опилок в 10 л раствора, соответственно.
Составу с наименьшей плотностью потребуется несколько другое количество:
- М5 из полкило цемента на 2 кг гашенки, полкило песка и 2 кг стружки;
- М10 на 2 кг древесного материала требует 1 кг цемента, 1,5 глины, 2 кг песка.
О размере опилок
При достаточном количестве вяжущего компонента величина опилок не играет роли. Как правило, древесный материал получают с ленточной и дисковой пилорамы. Размеры отходов с разного оборудования практически не разнятся. Однако древесный материал с оцилиндровочных и калибровочных механизмов не подходит. Сложно получить однородный бетон, если фракции отличаются в более чем 100 раз.
Определить хорошее качество замеса можно вручную. Нужно набрать его в руку и сильно сжать. Если вода не стекает, а комок не рассыпается, значит, жидкий арболит готов.
kladembeton.ru
Опилки как утеплитель: за и против, технология
Утепление дома — ответственная и полезная процедура, позволяющая решить сразу несколько проблем. Она изменяет микроклимат, предохраняет от разрушения конструкции стен и перекрытий, обеспечивает заметную экономию на обогреве жилья. В то же время утепление требует немалых расходов. Если дом большой, площадь внешних поверхностей и перекрытий велика, то количество теплоизоляционного материала будет значительным, что обойдётся в немалую сумму. Поэтому любая возможность снизить стоимость утепления без потерь качества и эффективности рассматривается владельцами жилья как привлекательный бонус.
Опилки как утеплитель используются достаточно широко, их в избытке в любом деревообрабатывающем цеху, и обычно их отдают даром. Если у владельца дома есть возможность получить опилки для утепления дома, то расходы снижаются до минимума.
Характеристика опилок как утеплителя
Древесина обладает низкой теплопроводностью, что делает её хорошим теплоизолятором. При этом слой деревянной обшивки имеет немалый вес, создавая значительную нагрузку на утепляемые поверхности. Кроме того, стоимость такой теплоизоляции чрезвычайно высока. Опилки — это отходы деревообработки, которые практически ничего не стоят. С физической точки зрения, опилки представляют собой большое число деревянных частиц, между ними находятся воздушные полости, которые сами по себе являются хорошим теплоизолятором. Полученное сочетание позволяет обеспечить качественное теплосбережение. Плотность такого материала гораздо ниже плотности массива древесины, поэтому вес его намного меньше и не создаёт заметной нагрузки на несущие конструкции. В дополнение к основной функции опилки способны обеспечивать качественную звукоизоляцию, повышая комфорт для людей, живущих в доме.
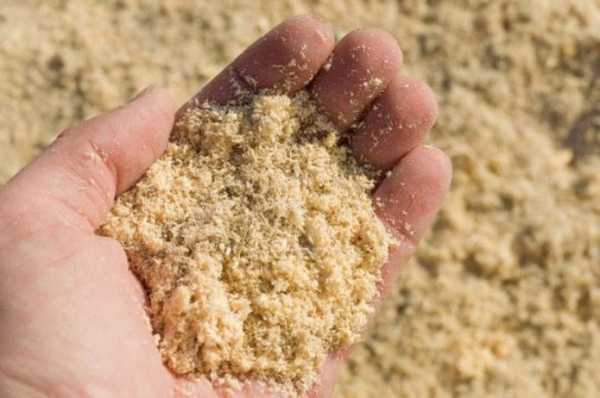
Опилки применяются в качестве утеплителя для крыш, пола, стен и перекрытий
Основная особенность опилок состоит в том, что они — сыпучий материал, что ограничивает использование только горизонтальными поверхностями. Решением проблемы стало связывание опилок с другими компонентами, придающими жёсткость и способность удерживать заданную форму. Благодаря этому появилась возможность использовать материал для любых поверхностей, как горизонтальных, так и вертикальных.
Это важно! Необходимо различать опилки и стружку. В большинстве случаев под термином «опилки» подразумевают как раз стружку, которая имеет большую упругость, способна удерживать форму и сохранять тепло. Она образуется в результате станочной обработки древесины на строгальном оборудовании.
Сами по себе опилки — это мелкая древесная крошка, которая образуется при пилении и обладает большей плотностью и весом. Она имеет меньший объём воздушных прослоек, склонна к слёживанию и может уплотняться до состояния, близкого к массиву дерева.
Слой стружки более рыхлый, имеет меньший вес. Слой опилок плотный, тяжёлый. Выбирая материал, надо отличать эти виды и брать стружку, имеющую более удачный набор свойств.
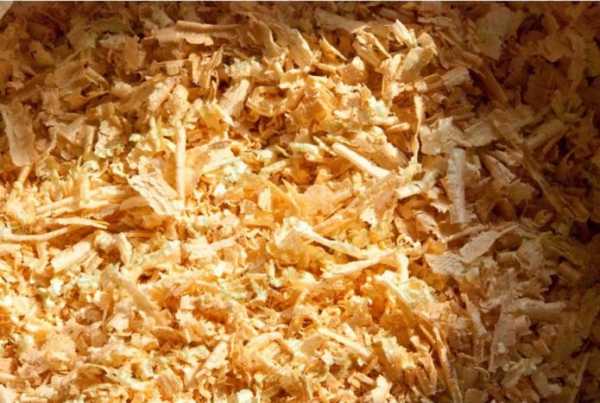
Для утепления в основном используют древесную стружку сосны и ели, поскольку в хвойных породах содержится больше лигнина
Достоинства и недостатки
Любой материал имеет как положительные, так и отрицательные стороны, которые необходимо учитывать при выборе и эксплуатации. Опилки также обладают достаточно сложным набором качеств. К положительным можно отнести:
- Высокую теплосберегающую способность;
- Малый вес;
- Экологическую чистоту;
- Дешевизна опилок далеко опережает все остальные материалы. Даже при необходимости их покупать, расходы будут гораздо ниже, чем при использовании других вариантов.
Существуют и недостатки:
- Опилки являются материалом биологического происхождения и способны гнить, склонны к образованию плесени, появлению грибка.
- Неустойчивость к воздействию воды. Материал гигроскопичен, хорошо впитывает воду, отчего значительно увеличивается вес и начинаются процессы разложения.
- В массе опилок заводятся насекомые или грызуны, селятся птицы.
- Высокая пожароопасность материала требует особой осторожности в эксплуатации и нуждается в принятии соответствующих мер.
Отрицательные качества опилок известны и требуют профилактических действий, позволяющих снизить или вовсе исключить возможность нежелательных последствий от их использования.
Применение вспомогательных компонентов
Слой засыпки из опилок представляет собой определённую опасность. Это относится к возможности возгорания или появлению проблем биологического характера. Кроме того, материал зависим от внешних факторов и склонен изменять свои качества со временем, нуждаясь в проведении специальных мероприятий по стабилизации эксплуатационных качеств.
Необходимо учитывать, что использование материала в чистом виде практически никогда не встречается, разработано немало способов обезопасить утеплитель и уменьшить его отрицательные качества. Это обусловлено одним из свойств материала — со временем опилки слёживаются, уплотняются в более однородную массу. Прослойки воздуха понемногу уходят, изменяя структуру слоя утепления, что способствует возникновению нежелательных последствий — гниению, появлению колоний насекомых или грызунов. Поэтому перед использованием опилок в качестве утеплителя необходимо решить две проблемы:
- Биологическая. Возможность гниения, появления насекомых или грызунов представляет существенную угрозу не только для утеплителя, но и для всех остальных элементов конструкции. Для решения вопроса используется пропитка материала антисептиком, например — медным купоросом или борной кислотой. Методика вполне эффективная и недорогая, проверенная многолетней практикой.
- Механическая. Для исключения слёживания производится соединение опилок и связующего материала, позволяющего сохранять форму и дающего возможность изготовления жёстких плит. Используются различные компоненты — цемент, гипс, известь и глина.
Некоторые владельцы частных домов относятся к утеплению опилками как к временной мере, позволяющей не слишком озадачиваться состоянием материала. Низкая стоимость этого утеплителя позволяет попросту менять его через некоторый промежуток времени. Однако такая возможность имеется далеко не всегда. Например, если утеплена потолочная плита и доступ к материалу со стороны чердачного помещения открыт, то процедура замены теплоизолятора проста и не занимает много времени.
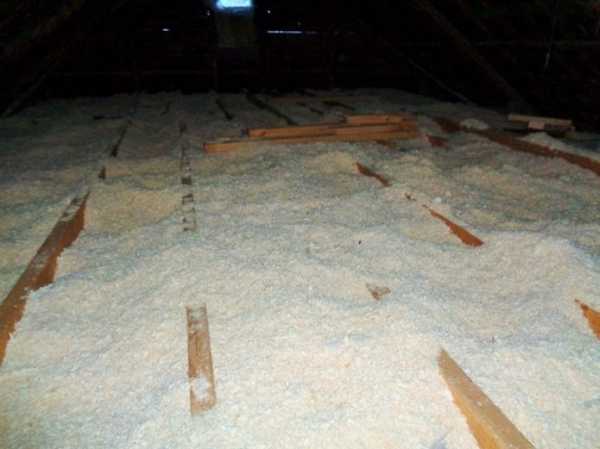
Утепление потолка сверху опилками
Другое дело, если для извлечения отслужившего слоя опилок надо вскрывать стены или производить демонтаж перекрытий — мероприятие превращается в сложные и трудоёмкие ремонтные работы, которых надо избегать. В таких случаях соединение опилок с дополнительными материалами, стабилизирующими форму и выполняющими антисептические функции, становится необходимым и обязательным.
Простейшим способом обработки является пропитка готовым антисептиком, борной кислотой или раствором медного купороса с последующей просушкой. Опилки становятся невосприимчивыми к биологическим воздействиям и в значительной степени теряют способность к горению. Но способность к слёживанию остаётся, что требует принятия более радикальных мер.
Технология утепления
Утепление опилками может выполняться в разных технологических вариантах:
- Засыпка горизонтальных плоскостей — межэтажных или чердачных перекрытий.
- Засыпка в стеновые конструкции при кладке кирпича колодцем.
- Установка плит из опилок, соединённых с дополнительными компонентами на горизонтальные или вертикальные поверхности. В частности, распространена теплоизоляция опилками стен каркасных домов.
Все варианты требуют стабилизации материала и придания ему определённой жёсткости. Рассмотрим наиболее проверенные и распространённые варианты соединения опилок и связующих компонентов для получения эффективного и долговечного утеплителя.
С известью
Прежде всего, опилки необходимо подготовить — пропитать антисептиком и хорошо просушить. После этого материал перемешивают с известью-пушонкой в пропорции 1:10 (на 1 ведро извёстки используется 10 вёдер опилок). Получается смесь, которую можно использовать различными способами:
- Засыпать на горизонтальные поверхности — межэтажные или чердачные перекрытия;
- Плотно утрамбовать между планками обрешётки или каркасом стеновых конструкций.
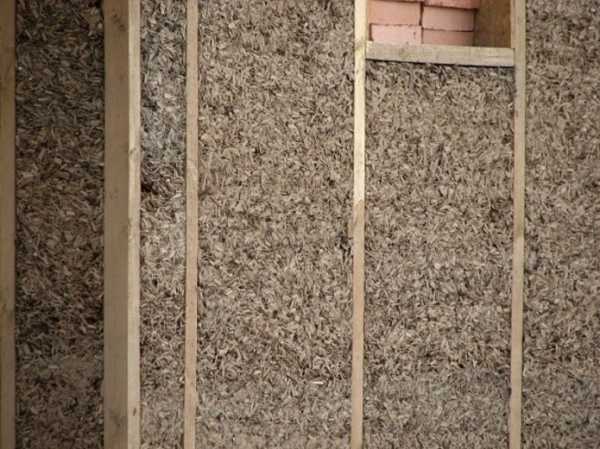
Пропитанные антисептиком опилки подходят для утепления преимущественно горизонтальных поверхностей
Полученный утеплитель лишён обычных для опилок недостатков — огнеопасности и подверженности гниению, вероятности появления насекомых и т. д. Значительно снижена слёживаемость, материал становится более стабильным и достаточно хорошо держит форму, что позволяет утеплять стены на длительный срок.
С глиной
Глина имеется в большинстве регионов страны. Её необязательно покупать, можно просто накопать необходимое количество в местах залегания. Особенностью глины является влагонепроницаемость в сочетании со способностью удерживать воду в порах. Это позволяет изготавливать глиняный раствор нужной степени текучести. Обычно рекомендуется в бочке с водой растворить 5 вёдер глины до появления раствора средней вязкости, не слишком жидкого, но и не густого, способного нормально смешиваться с опилками. Замешивание опилок с глиной лучше всего производить в бетономешалке.
Это важно! Пропорции определяются по ходу дела, на выходе должна получаться смесь средней густоты. При высыхании глина даёт заметную усадку, поэтому слишком большого количества опилок добавлять не рекомендуется.
Перед нанесением раствора поверхность перекрытия следует застелить полиэтиленовой плёнкой, иначе вода протечёт вниз. В идеале плёнку укладывают полосами внахлёст с проклейкой стыков скотчем. Если утеплитель укладывается в промежутки между поперечинами, установленными на ребро, то плёнку можно укладывать в них без соединения с соседними полосами, так как в этом нет необходимости. Материал укладывают слоем в 10 – 15 см толщиной и приглаживают для получения ровной поверхности.
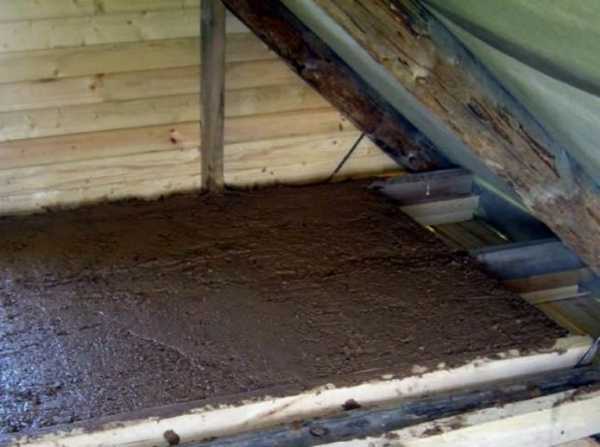
Масса из опилок и глины — недорогой и эффективный утеплитель
Высыхание длится несколько дней, в течение которых на поверхности могут образоваться трещины. Их можно замазать влажной глиной, или не предпринимать никаких действий, так как принципиального значения эти трещины не имеют, а размер их обычно невелик.
Использование такого раствора для вертикальных поверхностей аналогично процессу нанесения штукатурки. На подготовленную поверхность стены, очищенную от грязи, пыли и осыпающихся или отслоившихся участков, наносится слой смеси и тщательно выравнивается. Можно использовать штукатурные маяки (направляющие), обеспечивающие ровный и качественный слой утеплителя. После просушки образовавшиеся трещины повторно затирают глиняным раствором.
С цементом
Для создания утеплителя необходимо взять 1 часть цемента, 1 часть извести и 10 частей опилок. Сначала необходимо сделать водный раствор цемента с известью, после чего туда добавляют опилки. Полученная смесь должна иметь консистенцию, достаточную для нанесения с сохранением формы. Проверяется следующим образом — берётся комок раствора и сжимается в руке. Если из него не течёт вода, значит, состав имеет правильные пропорции. После приготовления состав смачивают из лейки раствором антисептика.
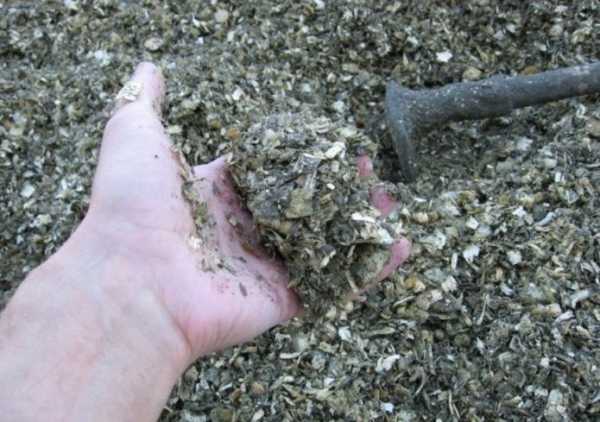
Существует несколько вариантов подготовки материала из цемента и опилок
Существует другой вариант. Используются опилки, вода и цемент в соотношении 20:3:2. Опилки должны быть подготовлены (пропитаны антисептиком и высушены). Смесь перемешивается и укладывается на полиэтиленовую подложку или слой песчаной засыпки, выравнивается и трамбуется. Достаточно 5 – 10 см толщины. После высыхания теплоизолятор способен выдерживать определённые нагрузки, по нему можно ходить.
Это важно! Для увеличения времени жизнеспособности состава рекомендуется вносить замедлитель, позволяющий исключить спешку и нервозность при выполнении работ. Цемент схватывается довольно быстро, вынуждая делать относительно небольшие порции материала, что снижает производительность и замедляет процесс. Замедлитель позволяет увеличить количество замешиваемого за один раз теплоизолятора, что ускоряет работу.
Нанесение материала производится путём заполнения промежутков между планками обрешётки (на вертикальных поверхностях) или между поперечинами перекрытий. Состав необходимо уплотнять, наличие полостей или зазоров нежелательно. Образовавшиеся пустоты заполняют смесью или штукатурят.
Опилки в смеси с цементом можно использовать как сырьё для изготовления плит.
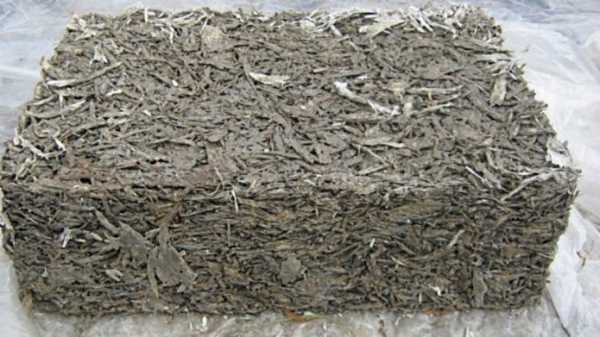
Опилочно-цементные плиты легко использовать в качестве теплосберегающего материала
Изготавливаются формы, которые наполняют смесью и оставляют до схватывания. Затем плиты вытряхивают и досушивают. Готовый материал удобен для установки на любые поверхности, вертикальные или горизонтальные. Оптимальный вариант монтажа на стены — использование клеевого состава для керамической плитки. Внешнюю поверхность можно оштукатурить или защитить слоем обшивки.
С гипсом
Использование гипса позволяет быстро изготовить теплоизолятор, имеющий малый вес и хорошие теплосберегающие свойства. Существенным недостатком этого материала является гигроскопичность и неустойчивость к воздействию воды. При нанесении его необходимо качественно гидроизолировать, накрывать слоем полиэтиленовой плёнки или другим материалом.
Опилки с гипсом смешивают в соотношении 8:1. В зависимости от качества гипса пропорции можно изменять, добиваясь наилучшего качества теплоизолятора. На 1 кг гипса берётся 0,7 л воды. Смешивание производится в специально отведённой ёмкости небольшого размера, чтобы весь объём смеси можно было извлечь и использовать без потерь.
Это важно! Схватывание гипса происходит очень быстро, поэтому при замешивании раствора вместо воды рекомендуется использовать замедлитель. В этом случае срок жизнеспособности смеси увеличится до получаса. Тем не менее, необходимо готовить порции небольшого объёма, чтобы имелась возможность быстро использовать их до начала затвердения.
Нанесение материала производится тем же способом, что и другие составы.
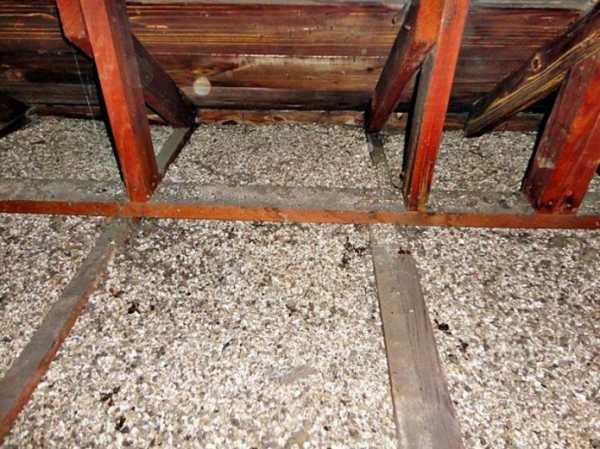
Смесь гипса и древесных опилок — отличный вариант для утепления пола и потолка
Смесью наполняют промежутки между планками обрешётки или поперечинами перекрытий. Следует работать быстро, чтобы материал не пропадал зря. Для этого необходимо продумать ход работ и организовать изготовление смеси так, чтобы успевать наносить её до начала схватывания.
Видео: утепление опилками пола и потолка
Использование опилок в качестве утеплителя позволяет получить дешёвый утеплитель, но требует выполнения множества профилактических и рабочих операций, что в сумме образует немалые трудозатраты. Результат утепления вполне эффективен, материал способен к полноценному выполнению своих функций, долговечность зависит от качества и технологии установки. При наличии некоторого опыта и навыков монтажа, опилки способны успешно заменить любой альтернативный тип утеплителя и решить поставленные задачи.
Оцените статью: Поделитесь с друзьями!kotel.guru
состав, пропорции, производство своими руками, отзывы и видео
Поиск более новых материалов, имеющих большое количество преимуществ вкупе с доступностью, продолжается долгое время. Так, опилкобетон можно считать одним из новейших типов блоков, которые имеют множество особенностей. Именно о них стоит поговорить подробнее.
Описание материала
Опилкобетон — это материал, который можно отнести к категории легких. Для его создания используются непосредственно опилки, цемент и песок. Разработан он был в 60-х годах, но широко применяемым стал лишь с 90-х годов.
Благодаря высоким санитарно-гигиеническим свойствам, его можно использовать для возведения абсолютно любых зданий и учреждений, в том числе и тех, которые предназначаются для детей.
Блоки можно подвергать абсолютно любой механической обработке, так как они практически не дают трещин и сколов. Очень часто их путают с арболитовыми блоками. Отличаются эти два строительных материала применением в них разных заполнителей.
Что касается арболита, то для его изготовления применяют дробленную щепу, которую получают за счет измельчения отходов древесины, а также дробления камыша и стеблей хлопчатника, а для изготовления опилкобетона применяются только опилки.
Технические характеристики
Плотность опилкобетонных блоков можно регулировать самостоятельно, увеличив долю опилок и песка в его составе. Характеристики материала в сфере тепло- и звукоизоляции будут тем выше, чем больше будет его плотность. Возрастет в таком случае и его прочность.
Можно выделить несколько групп опилкобетонных блоков, которые подразделяются от высоких технических характеристик к более низким:
- М5. Самый оптимальный вариант для возведения фундаментов и стен построек, так как обладает большей плотностью.
- М10. Блоки с подобной прочностью хороши для реконструкции стен и подвалов.
- М15 и М20 одинаково хорошо подойдут для возведения внутренних стен и перегородок, а так же для облицовки.
Основные показатели характеристик опилкобетонных блоков отражены в таблице:
Средняя плотность, кг/м3 | 500-850 |
Прочность при сжатии, МПа | 0,5-3,5 |
Теплопроводность, Вт/(м2·?С) | 0,08-0,17 |
Прочность при изгибе, МПа | 0,7-1 |
Модуль упругости, МПа | 250-2300 |
Морозостойкость, цикл | 25-50 |
Водопоглощение, % | 40-85 |
Усадка, % | 0,4-0,5 |
Биостойкость | V группа |
Огнестойкость | 0,75-1,5ч |
Звукопоглощение, 126-2000Гц | 0,17-0,6 |
Производство опилкобетонных блоков
Изготовление данных блоков не является очень сложным процессом, именно поэтому и возможно осуществить это своими руками. Главное, строго следовать технологическому процессу и не нарушать его.
Подготовка смеси
Создание опилкобетонных блоков оправдано, если неподалеку от производства находится лесопилка. В таком случае производство их своими руками станет наиболее выгодным, поскольку много затрат для этого не потребуется.
Для приготовления материала, который необходим для разных целей, понадобится взять компоненты в следующих пропорциях:
- Для получения высокой плотности: по 200 кг цемента и опилок, 50 кг извести, 500 кг песка.
- Для получения средней плотности на 200 кг опилок понадобится уже 150 кг цемента, 100 кг извести и 350 кг песка.
- Низкая плотность предполагает снижение количества дополнительных материалов на 200 кг опилок в несколько раз. Так, нужно всего лишь по 50 кг песка и цемента, а извести — 200 кг.
Кстати, известь возможно заменить глиной. В данном случае на качестве опилкобетона это не способно сильно сказаться.
Если эксплуатация блоков предполагается в местности с большой влажностью или же опилки лежалые, то заполнитель потребует дополнительной обработки минерализаторами. Это поможет увеличить огнестойкость и снизит возможность поглощения воды. Отличный способ обработки — это вымачивание их в жидком стекле. Предварительно нужно вымочить их в известковом молоке.
Смесь должна быть сухая, когда будут перемешиваться опилки, песок и бетон. Вода добавляется уже после, при помощи распрыскивателя.
Так как вручную компоненты очень тяжело перемешивать, особенно в больших количествах, рекомендуется позаимствовать растворосмеситель или же бетономешалку.
Проверить готовность раствора можно, сжав ее в кулаке. Если комок пластичен и на нем хорошо видны отпечатки, значит, материал готов.
Подготовка форм и оборудования
Изначально необходимо изготовить щитки специально для опалубки. Они должны быть четко вымерены, чтобы получить равные по размеру блоки. Доски для щитка должны иметь толщину в 38 мм. После следует приступить к просеиванию опилок. Как только щепа и кора будут отделены, потребуется добавить к ним древесную стружку. Это позволит увеличить прочность материала в несколько раз.
Укладку можно производить в две группы форм:
- Габаритные блоки. Для них потребуется обычно в виде ящиков из досок. Они обычно разборные, так как это позволяет быстро разбирать и собирать вновь.
- Небольшие блоки. Представляют собой небольшие по размеру формы, благодаря которым обычно могут изготавливаться до 9 блоков одновременно.
К укладке следует приступать немедленно, так как уже после двух часов она начнет быстро твердеть. Предварительно доски опалубки внутри увлажняются водой. Укладка должна производиться слоями раствора в 150 мм, при этом каждую его часть нужно хорошо утрамбовывать, дабы избежать образования пустот.
Опалубку целесообразно снимать по прошествии четырех дней, когда раствор полностью застынет. Сами блоки нужно оставить еще на этом месте на 4 дня, так как в подобном случае прочность повышается в несколько раз.
Сушку блоков лучше проводить на сквозняке, поскольку тогда она будет производиться равномерно. При этом важно оставить между ними зазоры. На случай дождя лучше закрыть их полиэтиленовой пленкой, дабы предотвратить намокание блоков.
Окончательная сушка осуществляется при помощи столбов. Блоки необходимо для этого уложить на кирпичи, возводя невысокие столбы из опилкобетонных блоков и обязательно оставляя зазоры между ними. Таким образом 90% прочности можно достигнуть уже после месяца сушки.
На видео — технология производства опилкобетонных блоков своими руками при помощи станка «Блокмастер»:
Применение опилкобетонных блоков
В строительстве самых разных строений находит свое применение опилкобетон. Дачи, дома, хозяйственные постройки, коттеджи — все они получаются прочными и обладают прекрасными качествами. Из этого материала можно строить и временные жилища, ведь обойдутся блоки достаточно дешево.
Применим опилкобетон и для постройки прочного фундамента. При этом в реставрации он не будет нуждаться длительное время.
Плюсы и минусы
Блоки отличаются следующими преимущественными характеристиками:
- Высокая теплоизоляционность;
- Экологичность;
- Паропроницаемость;
- Огнеустойчивость;
- Устойчивость к холодам и морозам.
Особым плюсом будет его вес, так как он составит всего 50 тонн при площади в 250 м2. Благодаря этому качеству материала можно существенно снизить затраты на постройку фундамента. Кроме того, низкая стоимость самих опилкобетонных блоков также позволит сэкономить.
К основному минусу, которым обладает опилкобетонный блок, можно отнести его возможность впитывать влагу. Это очень плохо для материала, но предотвратить впитывание жидкости возможно, если внешне окрасить их некоторыми составами и красками, а внутри провести качественную гидроизоляцию.
Отзывы
Георгий, г. Саратов:
Построил цельный дом из опилкобетона. В целом доволен, хотя, конечно, стоило уделить больше внимания проведению паро- и гидроизоляционных слоев, поскольку совсем недавно обнаружил конденсат. Советую строить дом из подобных блоков только в том случае, если Вы самостоятельно способны провести меры по изоляции.
Владислав, г. Омск:
Дачная постройка вышла в несколько раз дешевле, чем, если бы я закупал другой материал. А здесь сделал его сам, вроде бы ничего сложного, но достаточно трудоемким оказался процесс.
Если соберетесь строить дом из опилкобетона, который будет изготовлен самостоятельно, то потребуется нанять бригаду рабочих. Они будут помогать его изготавливать, иначе процесс будет достаточно длителен. Но при задействовании рабочих в итоге сумма выйдет такая же. Не знаю, но все же я бы строил дом из более традиционных материалов.
Родион, г. Бийск:
Сделал несколько построек на основе опилкобетонных блоков. Доволен очень, на следующий год планирую заняться масштабной стройкой из этого материала.
stroyres.net
Как сделать опилкобетон своими руками? Технология
Опилкобетон – это одна из разновидностей легких бетонов, обладающих пониженной плотностью. Он был разработан в 60-х годах 20 века в Советском Союзе и прошел абсолютно все технические и качественные испытания, после чего был стандартизирован. Массовое применение в частном домостроении и потребительский спрос опилкобетон получил лишь в середине 90-х годов, после чего его уникальные свойства неизменно привлекают потребителей.
Главными преимущественными характеристиками этого стройматериала являются:
- экологическая безопасность;
- огнестойкость;
- прочность;
- массовое отношение влаги;
- паропроницаемость;
- теплотехнические показатели;
- морозостойкость;
- доступная стоимость материала.
Область применения опилкобетона
Этот строительный материал широко применяется при строительстве домов, дач, коттеджей и хозяйственных построек. Он также используется при работах по утеплению подвалов и реконструкции зданий. При такой реконструкции не возникает необходимости в усилении фундамента.
Для строительства здания из опилкобетона подойдет любой проект, созданный для домов из других материалов. Однако затраты на строительство будут существенно ниже. Дом, построенный из опилкобетона, достаточно легкий: при площади в 250 м2 его вес составляет около 50 тонн. Это обстоятельство позволяет не закладывать сложный фундамент. Кроме этого есть еще множество преимуществ, среди которых можно назвать хорошую звукоизоляцию, простоту сборки, экологичность, экономичность, долгий срок эксплуатации.
Состав опилкобетона
Основой этого строительного материала, как понятно из названия, являются древесные опилки. Кроме этого, в состав входят песок, вяжущие материалы (песок, известь) и вода. Благодаря санитарно-гигиеническим показателям опилкобетон является одним из оптимальных материалов для возведения стен зданий.
Плотность стройматериала зависит от соотношения песка и опилок. Соответственно, плотность тем меньше, чем меньшее количество песка пошло на изготовление опилкобетона. В этом случае улучшаются теплотехнические свойства, но уменьшается прочность материала. С увеличением количества песка и вяжущих материалов прочность возрастает. Также улучшаются морозостойкость и водонепроницаемость, что в свою очередь препятствует воздействию коррозии на стальную арматуру. Такая арматура применяется при укладке стен из блоков, сделанных из опилкобетона. Поэтому, прежде чем приступать к изготовлению, необходимо четко знать свойства бетонируемой конструкции. Здесь не бывает мелочей, принимается в расчет толщина стен, количество этажей, наружная, внутренняя стена это будет или несущая конструкция.
В зависимости от состава, опилкобетон подразделяется на марки. Блоки марок М5 и М10 применяются для строительства, реконструкции и утепления подвалов, поскольку им свойственны прекрасные теплоизоляционные характеристики. Марки М15 и М20 наилучшим образом подходят для возведения как внутренних, так и наружных стен домов.
Марки и пропорции опилкобетона:
- М5. На 200 кг опилок берется 50 кг цемента, 50 кг песка, 200 кг извести или глины. Плотность – 500 кг/м3.
- М10. На 200 кг опилок берется 100 кг цемента, 200 кг песка, 150 кг извести или глины. Плотность – 650 кг/м3.
- М15. На 200 кг опилок берется 150 кг цемента, 350 кг песка, 100 кг извести или глины. Плотность – 800 кг/м3.
- М20. На 200 кг опилок берется 200 кг цемента, 500 кг песка, 50 кг извести или глины. Плотность – 950 кг/м3.
Изготовление опилкобетона своими руками
Заготовка необходимых материалов. Компоненты, входящие в состав опилкобетона, хороши тем, что их не нужно заготавливать заранее. Все составляющие можно купить в магазинах, торгующих стройматериалами, на рынках или складах. Благодаря этому к заготовке можно приступить практически за один день до начала изготовления.
Смешивание компонентов. Приготовление вручную опилкобетона является очень трудоемким процессом, поэтому для смешивания компонентов по возможности желательно использовать бетономешалку или растворосмеситель. Прежде всего, высушенные опилки необходимо просеять через сито, ячейки которого должны быть по размеру 10*10 миллиметров. Затем опилки смешиваются с песком и цементом. После этого в приготовленную смесь добавляют глиняное или известняковое тесто и тщательно перемешивают. Получившуюся смесь разводят водой, постепенно добавляя ее в малых порциях через лейку. После каждого долива смесь необходимо перемешать.
Если смесь приготовлена правильно и хорошо перемешана, то при сжатии в кулаке она образует пластичный комок, на котором видны вмятины от пальцев, при отсутствии капель воды. Это является основным признаком готовности смеси. После этого ее можно формировать в блоки. В этом деле медлить нельзя ни в коем случае, так как по истечении 1,5-2 часов смесь начинает твердеть. Укладывая смесь в форму, ее необходимо хорошо утрамбовать, чтобы исключить наличие воздуха.
Размеры блоков. Такие размеры стандартами не установлены. Они напрямую зависят от толщины стен, ширины простенков и проемов, расстояния от проемов до углов строения, а также от способа укладки. Для наибольшего удобства при строительстве длина участков стены или ширина простенков должны быть кратными блочным размерам.
Толщина блока обычно равняется двум толщинам красного кирпича, учитывая и уложенный между ними раствор. В общем, это составляет 140 миллиметров. Учитывая то, что при кладке часто используется и красный обожженный кирпич, такой подход является очень практичным.
Большие опилкобетонные блоки сохнут достаточно долго. Для ускорения процесса высыхания в них делают 2-3 отверстия, что не только позволяет блоку быстрее высохнуть, но и улучшает теплозащитные свойства этого стройматериала.
Формы для отливки. Наиболее оптимальным вариантом является возведение стен не при помощи опалубки, а из заранее подготовленных блоков. Они высушиваются в течение трех месяцев, после чего опилкобетон приобретает свою марочную прочность. Перед тем, как начать приготовление смеси, изготавливаются формы для отливки блоков. Форму с опилкобетонного блока снимают не сразу, а по прошествии от трех до пяти дней. Для ускорения процесса изготовления делают 10-20 форм. Таким образом, процесс не прервется, а также не потратится время на ожидание высыхания блоков. Количество форм напрямую зависит от того количества блоков, которое вы планируете изготовить за один раз.
- Формы для габаритных блоков. Для крупных блоков изготавливаются разборные одинарные или двойные формы. Они выполняются в виде сбитых из досок ящиков. Формы являются разъемными, что позволяет очень быстро их разбирать и собирать. Делаются они из досок, толщина которых составляет 20 миллиметров. Части разъемной конструкции скрепляются при помощи стальных стержней Г-образной формы, обладающих резьбой М8, на которую накручивается барашковая гайка.
- Формы для небольших блоков. Для изготовления мелкогабаритных блоков изготавливаются в собранных из 20 миллиметровых досок сотовых формах. В основном такие формы делают для производства 9 блоков из опилкобетона одновременно. По желанию количество ячеек может варьироваться. Эти формы, состоящие из внутренних и боковых досок, так же легко и быстро собираются и разбираются. Составляющие ячейки внутренние доски крепятся между собой при помощи задвижных пазов. Торцевые же доски прикрепляются к боковым стальными Г-образными стержнями и барашковыми гайками.
Внутренние стенки форм. Чтобы доски, из которых изготавливаются формы для отливки, не впитывали влагу, внутренние стенки обивают кровельной сталью, пластиком или прокладываются полиэтиленовой пленкой. Из формы, подготовленной таким образом, блоки вынимаются очень легко и просто, не приставая к деревянным стенкам.
Учитывая то, что при высыхании происходит усушка блоков, формы делаются немного больших размеров, чем должны получиться готовые блоки. Эта разница должна составлять приблизительно 10%:
- Для цельных блоков с размерами 120*250*140 мм (ширина*длина*высота) размер ящика должен быть 132*235*154 мм.
- Для блоков с размерами 190*390*140 мм размер ящика составляет 209*430*154 мм.
- Для блоков с размерами 130*410*140 мм размер формы должен быть 143*450*154 мм.
Производство блоков из опилкобетона
Деревянные формы, перед тем как заполнить их опилкобетонной смесью, устанавливают на поддоны, изготовленные из стали или пластика, предварительно посыпанные тонким слоем опилок. В форме располагают обернутые толем деревянные пробки, необходимые для получения сквозных отверстий. После этого подготовленную смесь плотно укладывают в форму, трамбуя при этом специально изготовленной ручной трамбовкой. После проведения этих работ формы с опилкобетоном оставляют на 3-4 дня. В течение этого времени стройматериал приобретает прочность, процентная доля которой составляет 30-40 процентов от марочной.
По истечении указанного срока вынимают пробки и толь, сами формы разбирают, а блоки оставляют на том же месте еще на 3-4 дня, чтобы их прочность еще возросла. Теперь она составляет 60-70% от марочной прочности. После этого блоки следует перенести под навес для последующей сушки. Для достижения лучшего результата необходимо соблюдать некоторые условия:
- опилкобетонные блоки при сушке лучше всего расположить на сквозняке. Так их сушка будет более равномерно осуществляться;
- при укладывании блоков для сушки оставляйте между ними зазоры;
- если нет навеса, то блоки необходимо укрыть полиэтиленовой пленкой в случае дождливой погоды.
Для окончательной сушки из блоков сооружают столбы. Это происходит так: на предварительно обожженные кирпичи укладывают два блока, на них располагают поперек еще два, затем поперек еще пару и так далее. Расположенные так, блоки окончательно просохнут и затвердеют. 90% прочность стройматериал приобретает уже через месяц, однако для достижения стопроцентной прочности потребуется три месяца.
Полностью готовые блоки очень прочны, тверды и не имеют трещин. Доказательством прочности стройматериала является то, что блок не разбивается при падении с высоты, достигающей 1 метра.
sekretystroyki.ru