горная порода, характеристика, температура плавления, структура
БАЗАЛЬТ (лат. basaltes, basanites, от греч. basanos – пробный камень; по другой версии, от эфиоп. basal – железосодержащий камень * англ. basalt, basaltic rocks; нем. Basalt; франц. basalte; испанс. basalto) – излившаяся кайнотипная основная порода, эффузивный аналог Габбро. Окраска базальта тёмная до чёрной. Состоит главным образом из основного плагиоклаза, моноклинного пироксена, оливина, вулканического стекла и акцессорных минералов – магнетита, ильменита, апатита и др. Структуры базальта – интерсертальная, афировая, реже гиалопилитовая, текстуры – массивная либо пористая, миндалекаменная. B зависимости от крупности зерна различают: наиболее крупнозернистый – Долерит, мелкозернистый – анамезит, тонкозернистый – собственно базальт. Палеотипные аналоги базальта – Диабазы.
Химический состав базальта
Средний химический состав базальта по P. Дэли (%): SiO2 – 49,06; TiO2 – 1,36; Аl2O3 – 15,70; Fe2O3 – 5,38; FeO – 6,37; MgO – 6,17; CaO – 8,95; Na
Физические свойства базальта
Физико-механические свойства базальта весьма различны, что объясняется разной пористостью. Базальтовые магмы, обладая низкой вязкостью, легко подвижны и характеризуются разнообразием форм залегания (покровы, потоки, дайки, пластовые залежи). Для базальта характерна столбчатая, реже шаровидная отдельность. Оливиновые базальты известны на дне океанов, океанических островах (Гавайи) и широко развиты в складчатых поясах. Толеитовые базальты занимают обширные площади на платформах (трапповые формации Сибири, Южной Америки, Индии). C породами трапповой формации связаны месторождения руд железа, никеля, платины, исландского шпата (Сибирь). B миндалекаменных базальтовых порфиритах района Верхнего озера в США известно месторождение самородной меди.
Плотность базальта
Плотность базальта 2520-2970 кг/м³. Коэффициент пористости 0,6-19%, водопоглощение 0,15-10,2%, сопротивление сжатию 60-400 Мпа, истираемость 1-20 кг/м², температура плавления 1100-1250°C, иногда до 1450°C, удельная теплоёмкость 0,84 Дж/кг•К при 0°C, модуль Юнга (6,2-11,3)•104 Мпa, модуль сдвига (2,75-3,46)•104 Мпa, коэффициент Пуассона 0,20-0,25. Высокая прочность базальта и относительно низкая температура плавления обусловили применение его в качестве строительного камня и сырья для Каменного литья и минеральной ваты.
Применение базальта
Применение базальта – базальт широко используется для получения щебня, дорожного (бортового и брусчатки) и облицовочного камней, кислотоупорного и щелочестойкого материала. Требования промышленности к качеству базальта как сырью для щебня такие же, как и к другим изверженным породам. Для производства минеральной ваты базальт используется обычно в шихтовке. Установлено, что температура плавления сырья не должна превышать 1500°C, a химический состав расплава регламентируется следующими пределами (%): SiO
B CCCP на щебень разведано 50 месторождений c промышленными запасами 40 млн. м³. Два месторождения базальта c промышленными запасами 6,5 млн. м³ разведаны на облицовочный камень (Армянская CCP, Грузинская CCP). Годовая добыча базальта свыше 3 млн. м³. B CCCP месторождения базальта сосредоточены в основном в Армении, Восточной Сибири и на Дальнем Востоке. Базальтовые покровы в восточных районах США образуют крупные месторождения в штатах Нью-Йорк, Нью-Джерси, Пенсильвания, Коннектикут (самые крупные карьеры и камнедробильные заводы).
www.mining-enc.ru
Базальт – это что такое? Описание, преимущества, сфера применения базальта (фото)
Базальт – это натуральный камень. Чаще всего встречается вблизи вулканов. Самые большие месторождения обнаружены в России, Украине, Америке, на Гавайских и Курильских островах. В природе базальт встречается в виде пластин, бесформенных и округлых камней, а также потока лавы.
Что такое базальт?
Это горная порода, имеющая определенные характеристики. Перечислим их:
- Полевой шпат и авгит являются основными составляющими базальта.
- Цветовая гамма: темно-серая, черная, асфальтовая, а также встречаются экземпляры с зеленоватым оттенком.
- При нулевой температуре удельная теплоемкость составляет 0,85 Дж/(кг·К).
- Сопротивление варьируется от 50-400 МПа.
- Упругость материала находится в пределах 0,2-0,25.
- Температура плавления разная, у некоторых экземпляров – на уровне 1000-1200°C, у других – 1500°C.
- Базальт – камень плотностью от 2500 до 2900 кг/м2.
- Поглощение влаги колеблется на уровне 0,25-10%.
Состав базальта: особенности
Каждый человек еще со времен школы знает, что все минералы имеют определенное строение. Как правило, при их рассмотрении учитывается как химический состав, так и минеральный. Это позволяет непросто отличать на внешний вид базальт, гранит, мрамор и т. д., а иметь наиболее полные сведения об их технических характеристиках. Именно эти знания помогают эргономично применять тот или иной материал.
В состав любого базальта входит климопироксен, титаномагнетит, вулканическое стекло, плагиоклазит, магнетит. Его структура отличается порфировой поверхностью, иногда афированой. При этом иногда встречаются виды гладкие, как стекло. На данные критерии влияет особенность расположения месторождений базальта. Те, которые находятся на поверхности, чаще всего пузыристые, так как во время остывания вулканической лавы через эти отверстия выходят пары и газы. Впоследствии в пустотелых местах могут откладываться такие минералы, как медь, пренит, кальций, цеолит. Ученые выделили такие образования в определенный вид, называемый миндалекаменный.
Минеральный состав базальта, взятого из разных месторождений, может значительно отличаться. В основном это обусловлено вхождением в него определенных примесей. Например, структура некоторых отличается наличием призм пироксенов, благодаря ним базальт приобретает черный цвет. А вот кристаллы оливина окрашивают камень в желто-зеленый оттенок. Необходимо заметить, что размер примесей может достигать ¼ всей массы. Реже встречаются базальты, в состав которых входят такие минералы, как роговая обманка, апатит, ортопироксен.
Популярные виды
Базальт – это обобщающее название. Оно объединяет множество различных видов. Наиболее распространенные из них:
- Азиатский – недорогой камень, широко применяемый во время дизайнерского оформления помещений, а также в архитектуре. Его окрас преимущественно цвета «мокрого асфальта».
- Сумеречный – большие месторождения находятся в Китае. Он темно-серого, даже черного цвета. Считается самым качественным видом среды всех остальных, поскольку обладает высоким уровнем устойчивости к перепадам температур, механическому повреждению, колебанию влажности и др.
- Мавританский – миндалекаменный вид. На своей поверхности имеет множество разнообразных вкраплений. Цветовая гамма в основном зеленых оттенков. Внешний вид такого базальта достаточно оригинальный, что позволяет применять его для украшений помещений и зданий. Однако стоит отметить, что его технические показатели несколько уступают: морозоустойчивость и твердость имеет невысокий уровень.
- Базальтин – самый распространенный вид. Большие месторождения находятся недалеко от Рима. Относится к наиболее дорогостоящим материалам. Имеет оригинальную поверхность, что позволяет широко использовать его в архитектурной сфере. По прочности такой базальт можно сравнить с гранитом, после укладки он длительное время сохраняет все свойственные ему качества.
Сфера применения
Базальт – это достаточно распространенный материал, который широко используется в разных сферах. Основная из них – архитектурная. Но также из него изготавливают качественные строительные материалы, добавляют в бетонные растворы для крепости или используют во время заливки плит. Базальт часто применяют как отделочный материал для полов или дорожек. А для утепления зданий с внешней стороны он просто незаменим. Большинство дизайнеров отдают базальту должное внимание во время декорирования помещений. Широко используют его при отделке каминов, стен. С помощью такого решения легко расставить акценты и внести в интерьер контрастность.
Преимущества базальта
Достоинств у такого вида множество. Самые весомые:
- шумопоглощение;
- паропроницаемость;
- высокий уровень термоустойчивости;
- экологически безопасен;
- качественная теплоизоляция;
- прочность;
- не электризуется;
- пожаробезопасность;
- долговечность.
Продукция на основе базальта
Добывают серый базальт на рудниках и в карьерах. Чаще всего занимается этим горнодобывающая отрасль. После изъятия его отправляют на специальные предприятия, где непосредственно из базальта изготавливают разную продукцию. Это могут быть сэндвич-панели, плитки, каркасы для лестниц, волокна для утепления крыш и других поверхностей. Также используется базальт для сооружения колонн, арок, статуй. Его порошок добавляется во время производства армированных изделий, чтобы обеспечить им надежность и крепость.
И напоследок о стоимости
Базальт, цена которого в отличие от других натуральных материалов считается достаточно доступной, может широкое применяться без повышения себестоимости объекта. Например:
- базальтовая щебенка – от 250 до 400 р. за упаковку;
- облицовочные плиты – от 2000 р. за 1 кв. м;
- брусчатка базальтовая – 3200-3500 р. за 1 кв. м.
fb.ru
БАЗАЛЬТ, плавленный базальт – Легкое дело
БАЗАЛЬТ
— излившаяся горная порода, в состав к-рой входят основной плагиоклаз, железисто-магнезиальные (гл. обр. пироксен) и рудные минералы (магнетит, титано-магнетит). Довольно часто, но не всегда, присутствует оливин, сравнительно редко нефелин и лейцит.
Хорошо раскристаллизованную (мелко-, средне- и крупнозернистую) разновидность базальта наз. долеритом, тонкозернистую — анамезитом. Базальт, несколько измененный вторичными гидротермальными процессами, наз. диабазом, диабазовым порфиритом. В технике диабазом иногда наз. любые полнокристаллические породы базальтового типа.
Базальт используется в естественном виде, а также после переплавления (плавленный базальт) естественных базальтовых пород. обладающих повышенной щелочностью. Плавленный базальт, в отличие от природного, имеет чрезвычайно тонкозернистое строение. Это обусловливает его высокую механич. прочность, термич. и химич. стойкость и хорошие электроизоляционные свойства.
Средний уд. вес кристаллической разновидности базальта 2,7—3,2; базальтового стекла 2,7—2,85. Показатель преломления базальтового стекла 1,55—1,61. Пористость 0,5—1,5%, водопоглощение 0,2—0,4% по весу ц 0,5—1,1% по объему. Прочность на сжатие (кг!см2) сухого базальта — 2640—3200, мокрого — 2500; диабаза—1800—2700; плавленного базальта —3000—9158. Временное сопротивление разрыву плавленного Б.— 460—600 кг!см2, временное сопротивление изгибу—450— 520 кг/см2. Коэфф. теплопроводности при изменении темп-ры от 0 до 400° составляет 5,04—5,06 кал!сек»см»град. Температура плавления в зависимости от состава—от 1150 до 1350°С (ср. t° пл. = 1250°С).
Базальт обладает химич. стойкостью по отношению к концентрированным HNOs, h3S04 и КОН.
Базальт используется как заполнитель в бетонах высоких марок и специальных кислотоупорных и дорожных бетонах. Из природного базальта получают штучный камень, применяемый в качестве стенового, облицовочного и архитектурного материала. Б.— весьма распространенный материал для получения щебня и бутового камня, широко используемого в качестве балласта в сооружениях пром. гражданского и дорожного типа.
Базальт и диабаз служат для производства минеральной ваты. Бетоны, в к-рых минеральная вата является заполнителем, обладают высокими теплоизолирующими и огнестойкими свойствами. Базальтовые плиты грубой обтески применяют для мощения улиц, тротуаров и пр.
Плавленный базальт служит для произ-ва всевозможных фасонных плиток, лестничных ступеней и пр. Порошок из переплавленного базальта может быть использован для изготовления прессованных армированных изделий. Из расплавленного базальта отливают детали различных габаритов и форм для футеровки химич. аппаратуры и для спец. оборудования. Методом отливки также получают изоляторные подставки для аккумуляторов. Из плавленного базальта изготавливают линейные и опорные изоляторы для сетей высокого и низкого напряжения. В горной пром-сти плавленый базальт используют для получения футеровки в пневмотранспортных трубках, шаровых мельницах и т. д.
Диабаз и базальт — породы серо-черного цвета, схожие по свойствам с двумя предыдущими и имеющие те же области применения. Плотность базальта наивысшая из всех горных пород — до 3300 кг/м3.
Базальт (как и диабаз, аналог габбро) представляет собой плотную тяжелую породу, имеющую скрытокристаллическое или стекловатое, а иногда порфировое строение.
Плавление диабаза и базальта чаще всего производят в ванных печах или вагранках при температуре 1400. 1500 °С, а при изготовлении светлого каменного литья — в электрических печах.
http://bibliotekar.ru
legkoe-delo.ru
Способ производства непрерывных волокон из базальтовых пород и устройство для его осуществления
Изобретение относится к области производства волокон из базальтовых, вулканических пород, к конструкции камнеплавильных печей. Техническим результатом изобретения является снижение расхода энергоносителей, увеличение производительности, повышение характеристик базальтовых волокон по прочности, эластичности и термической стойкости. Базальтовое сырье предварительно перед загрузкой подогревают до температур 250-400°С, загрузку базальта осуществляют непосредственно в зону максимальных температур 1450-2000°С пламени горелки-загрузчика, плавление базальтового сырья, дегазацию и гомогенизацию расплава производят при низких уровнях расплава 5-70 мм на плавильной площадке с последующим увеличением уровня до 80-300 мм в ванне печи. Устройство для производства непрерывных волокон из базальтовых пород содержит загрузчик базальта, систему отопления печи, включающую две и более горелок, которые последовательно соединены со смесителем газовоздушной смеси и рекуператором. Рекуператор через коллектор дымоудаления соединен с фидером печи. Устройство содержит дополнительный рекуператор с отводом для нагрева базальта в загрузчике, горелку-загрузчик, под которой на дне ванны размещена плавильная площадка, которые совместно создают локальную зону повышенных температур – зону плавления базальта, дегазации и гомогенизации расплава. Изобретение позволяет увеличить производительность устройства на 28-35%, снизить расход природного газа на 30% и электроэнергии на 55% на производство 1 тонны базальтового непрерывного волокна при обеспечении высокого качества волокон. 2 н. и 4 з.п. ф-лы, 1 ил., 2 табл.
Изобретение относится к области производства волокон из базальтовых пород и конструкции печей для плавления базальтов.
Базальтовые породы, а именно базальты, андезитобазальты, амфиболиты, базаниты, диабазы, габбродиабазы, габбро, долериты, амфиболиты, порфириты, андезитовые порфириты и другие породы, относятся к породам магматического происхождения, имеют высокую природную химическую и термическую стойкость.
Волокна из базальтовых пород обладают высокой прочностью, химической и термической стойкостью, электроизоляционными свойствами. Базальтовые непрерывные волокна и материалы на их основе применяются в различных отраслях промышленности, строительстве, при производстве армирующих и композиционных материалов. Производство базальтовых волокон имеет доступную и практически неограниченную и сырьевую базу.
Однако широкое производство и применение базальтовых волокон сдерживается относительной сложностью технологий, низкой производительностью и высокой себестоимостью их производства. Поэтому особую актуальность представляют разработка и совершенствование технологий и технологического оборудования для производства базальтовых волокон.
Известны способ и устройство для производства базальтовых волокон РСТ. WO 98/22401 [1]. Способ состоит в измельчении базальтового сырья определенного химического состава, его подогреве и загрузке в плавильную печь, плавлении, стабилизации и выдерживании расплава в стабилизационной секции, подаче расплава в фидер и вытяжке непрерывных волокон через фильерные питатели. После плавления базальта температуру его расплава поднимают на 50-250°С до температуры изготовления волокон. Способ предусматривает проведение анализа соотношения химического состава основных компонентов базальтовой породы на стадии стабилизации расплава в фидере. Однако проведение анализа лучше выполнять предварительно на стадии выбора базальтовой породы, что соответствовало бы требованиям технологии производства непрерывных волокон и качеству волокон.
Устройство для осуществления способа включает последовательно соединенные достаточно сложные, массивные и габаритные основные элементы: плавильную печь, стабилизирующую секцию, фидер со сливными устройствами и фильерными питателями. Путь расплава от места загрузки и плавления базальта до места изготовления расплава длинный и проходит через плавильную печь, стабилизационную секцию и длинный фидер, что требует значительных расходов энергии для поддержания высоких температур расплава по всему пути его следования.
Как результат, такие технологическое и конструктивное решения способа и устройства не удовлетворяют требованиям экономичности производства базальтового волокна, обусловливают сложную, габаритную и массивную конструкцию устройства, которая требует значительных расходов энергоносителей, так как печь должна иметь несколько зон для плавления базальта, стабилизации и подготовки расплава, а фидер печи для выработки волокон значительно удален от печи плавления базальта.
Известны способ и устройство для производства базальтовых волокон RU 2193538 [2]. При этом способе и устройстве базальт загружают непосредственно в ванну печи. Однако базальт сразу тонет в расплаве. Поскольку температура в расплаве ниже, чем на его поверхности, плавление базальта происходит при низких температурах достаточно плохо. Поэтому для получения расплава базальта энергии газа недостаточно. Это требует применения электродов для дополнительного нагрева расплава базальтов. Поэтому данный способ и устройство сложны, требуют применения двух видов энергии и нагревателей для плавления базальтов, не отвечают требованиям экономичности плавления базальтов и выработки волокон.
Наиболее близким по совокупности признаков и достигаемому результату является способ и устройство для производства волокон из базальтовых пород UA 77861 [3].
Способ производства непрерывных волокон из базальтовых пород, который состоит в выборе базальтовой породы определенного химического состава и соотношения основных волокнообразующих окислов и сопутствующих оксидов, загрузке измельченного базальта непосредственно в расплав ванны плавильной печи, плавлении базальта в диапазоне температур на 150-260°С, превышающем температуру верхнего предела кристаллизации (Твпк), гомогенизации и стабилизации расплава в ванне печи при уровне расплава 80-250 мм до достижения степени аморфности 90-96%, стабилизации уровня расплава 20-80 мм над фильерным питателем в диапазоне температур 15-60°С выше температуры Твпк, вытяжке волокон через фильерный питатель, нанесении на волокна замасливателя и намотки волокон на бобины.
Данный способ требует дополнительно расхода газа для нагрева базальта в зоне загрузки, поддержания высоких температур в рабочем пространстве печи для плавления базальта и обеспечения требуемой степени аморфности расплава, не позволяет использовать андезито-базальты, андезиты, порфириты и другие базальтовые породы с высокими температурами плавления, а также базальтовые породы с высокотемпературными включениями, например, андезитов, кварца, слюды, а также не обеспечивает требуемой стабильности и безобрывности выработки непрерывных волокон.
Эти недостатки связаны с тем, что загрузка базальта в печь осуществляется при температурах окружающей среды, при этом базальт сразу тонет в расплаве и оседает на дне ванны на глубине 80-300 мм. Температура в расплаве базальта ниже, чем на его поверхности. Для плавления базальта на дне ванной печи и обеспечения требуемого качества расплава необходимо поддержание высокой температуры во всем рабочем пространстве печи, что требует большого расхода газа. Однако даже при этом в расплаве содержатся непроплавленные кристаллы базальтов и высокотемпературных минералов.
При попадании непроплавленных частиц, сгустков кристаллов в отверстия фильерного питателя вытяжка волокон сильно затрудняется, отверстия перекрываются сгустками кристаллов и непроплавов. Для прохождения сгустков непроплавленных кристаллов через отверстия фильерного питателя необходимо держать высокой температуру фильерного питателя на 15-60°С выше температуры верхнего предела кристаллизации (Твпк) расплава базальта. Это требует повышенного расхода электроэнергии на нагрев фильерного питателя. Кроме того, наличие кристаллов в аморфных волокнах существенно снижает их прочность и эластичность.
При плавлении базальтов в расплаве, в результате термохимических реакций и выделения межкристаллической влаги, содержатся пузырьки газов. Из вязкого расплава пузырькам газов сложно выйти на поверхность. Попадание пузырьков газов в отверстия фильерного питателя приводит к обрыву волокон и снижению производительности.
В целом указанный способ характеризуется повышенным расходом энергоносителей для поддержания высоких температур в рабочем пространстве печи и на фильерном питателе, не обеспечивает стабильность и безобрывность выработки непрерывных волокон, а также не позволяет использовать базальты с тугоплавкими включениями и базальтовые породы с повышенным содержанием SiO2, Al2O3 и других оксидов, обеспечивающих прочностные и термические характеристики волокон.
Технический результат состоит в снижении расхода энергоносителя, увеличении производительности, повышении характеристик базальтовых непрерывных волокон по прочности, эластичности и термической стойкости и достигается путем предварительного нагрева базальта и интенсификации его плавления в локальной зоне плавления – зоне высоких температур пламени горелки-загрузчика при низком уровне расплава, что позволит интенсифицировать переход базальтов из кристаллического состояния в расплавленное аморфное, высокую степень аморфности расплава, его дегазацию, плавление тугоплавких включений кварца, слюды, других минералов и базальтов, с повышенным содержанием SiO2, Al2O3 и других оксидов, обеспечивающих прочностные и термические характеристики непрерывных волокон, при снижении температуры в фидерной зоне и на фильерном питателе.
Технический результат достигается тем, что в способе производства непрерывных волокон из базальтовых пород, который состоит: в выборе базальтовых пород химического состава в диапазоне (%): SiO2 45-56, Al2O3 10-19, TiO2 0,9-2,0, Fe2O3 и FeO 7-18, CaO 6-15, MgO и MnO 3,0-7, Na2O и K2O 2,5-6 и соотношения основных волокнообразующих окислов и сопутствующих оксидов в пределах 3,2>(SiO2 + Al2O3)/(TiO2 + Fe2O3 + FeO + CaO + MgO + MnO + K2O + Na2O)>1,6; загрузке измельченного базальта непосредственно в расплав ванны плавильной печи; плавлении базальта в диапазоне температур Тп на 150-200°С выше температуры верхнего предела кристаллизации (Твпк) до достижения степени аморфности 90-96%; гомогенизации и стабилизации расплава в диапазоне температур Тс на 80-160°С выше Твпк; стабилизации уровня расплава в фидере печи на уровне 20-80 мм; при этом плавление, гомогенизация и выработка расплава производятся одностадийно в ванне и фидере печи, вытяжке волокон через фильерный питатель, нанесении замасливателя на волокна и намотке волокон на бобины, согласно изобретению
в качестве базальтового сырья используют основные базальты, которые могут иметь включения андезитов, кварца и другие высокотемпературные включения, а также андезито-базальты, андезиты, амфиболиты, диабазы, габбро, кислые базальтовые породы и минеральное сырье, имеющие повышенное суммарное содержание SiO2, Al2O3 и других оксидов, обеспечивающих прочностные и термические характеристики волокон;
базальтовое сырье предварительно перед загрузкой подогревают до температур 250-400°С и удаляют свободную влагу;
загрузку базальта осуществляют в локальную зону максимальных температур 1450-2000°С пламени горелки;
плавление базальтового сырья, дегазацию и гомогенизацию расплава производят на плавильной площадке при низких уровнях расплава 5-70 мм;
затем температура расплава в ванне и фидере печи снижается на 50-300°С, а уровень расплава в ванне печи увеличивается до 80-300 мм;
вытяжку волокон осуществляют при температуре фильерного питателя на 30-200°С ниже температуры верхнего предела кристаллизации расплава базальта (Твпк).
Для производства непрерывных волокон возможно использовать более широкий состав базальтовых пород: основные базальты, андезито-базальты, андезиты, андезитовые базаниты, диабазы, габбро, долериты, амфиболиты, имеющие повышенное содержание SiO2 и Al2O3 до 86%, а также базальты, имеющие тугоплавкие включения андезитов, кварца и другие тугоплавкие включения.
Данный способ предполагает использование базальтовых пород более широкого диапазона химических составов, включающих основные и кислые базальтовые породы, из которых возможно производить волокна с высокими прочностными и термическими характеристиками. Диапазон химических составов базальтовых пород и минерального сырья для производства волокон может быть существенно расширен до представленного в таблице.
Химический состав | SiO2 | Al2O3 | Fe2O3 FeO | TiO2 | CaO | MgO MnO | K2O | Na2O |
Содержание, % | 45-67 | 4-24 | 5.0-16 | 2-5 | 5-21 | 5-15 | 1.5-4.5 | 3.5-12 |
Предварительный подогрев теплоемкой базальтовой породы позволяет снизить потребление энергоносителя в самой печи, исключить попадание в печь базальтов, содержащих свободную влагу. Предварительный подогрев базальтовой породы и поступающей в горелки газовоздушной смеси позволяет обеспечить плавление базальтов в зоне плавления при температурах до 2000°С.
Плавление базальтовой породы осуществляется в зоне действия наиболее высоких температур пламени горелки 1450-2000°С, при низких уровнях расплава 5-70 мм на плавильной площадке. При попадании базальта на плавильную площадку он не тонет в расплаве, а находится в зоне действия факела горелки. Факел горелки создает в зоне загрузки базальтовой породы на плавильной площадке зону наивысших температур – зону плавления. Пламя горелки обеспечивает интенсивное плавление базальта, догорает на поверхности расплава, отдавая всю энергию непосредственно расплаву. Более высокая скорость потока пламени по поверхности расплава создает разрежение, которое способствует выходу из расплава пузырьков газов – дегазации расплава.
Создание высоких температур в зоне плавления при низком уровне расплава позволяет в процессе плавления обеспечить: интенсивный переход базальтов из кристаллического состояния в расплавленное аморфное; требуемую степень гомогенизации и аморфности расплава более 96%; дегазацию расплава; плавление тугоплавких включений кварца, слюды и других минералов, требующих более высоких температур плавления, андезито-базальтов, андезитов, габбро, амфиболитов и кислых базальтовых пород, которые позволяют производить волокна с высокими характеристиками по прочности, эластичности и термостойкости.
Газы, образующиеся в результате термохимических реакций и закипания межкристаллической воды, легко выходят из более прогретого и менее вязкого расплава базальта.
Плавление подогретых до температуры 250-400°С базальтов в зоне действия пламени горелки при температурах 1450-2000°С, гомогенизация и дегазация расплава при уровне расплава 5-70 мм не требуют необходимости держать повышенные температуры во всем рабочем пространстве печи и фидере.
При подаче перегретого расплава в фильерный питатель нет необходимости нагревать его до высоких температур. При этом температуру фильерного питателя можно снизить на 30-200°С ниже температуры верхнего предела кристаллизации Твпк. Нагрев фильерного питателя обеспечивается в основном за счет тепловой энергии расплава базальта. Фильерный питатель обеспечивает только прохождение подготовленного расплава через фильеры в процессе выработки волокон.
Плавление при высоких температурах основных базальтов с тугоплавкими включениями, андезито-базальтов, андезитов, габбро, амфиболитов и кислых базальтовых пород позволяет производить волокна с высокими характеристиками по прочности, эластичности и термостойкости.
Высокие температуры плавления на плавильной площадке обеспечивают степень гомогенизации и аморфности расплава выше 96% и близкую к 100%, что необходимо при производстве качественных волокон диаметром 6-10 мкм, пригодных для текстильной переработки и производства тканей.
Исследования характеристик базальтовых непрерывных волокон показывают, что плавление базальтов при повышенных температурах до 2000°С обеспечивает образование прочных атомарных кремнекислородных, алюмокислородных и атомарных связей других оксидов, степень аморфности расплава свыше 96%, отсутствие кристаллических включений в элементарных волокнах, что позволяет повысить прочность и эластичность непрерывных волокон на 25-45%. Базальтовые непрерывные волокна становятся более прочными, эластичными и термостойкими, хорошо поддаются текстильной переработке, что позволяет производить крученые нити и ткани высокого качества.
Предлагаемый способ позволяет расширить сырьевую базу базальтовых пород для производства непрерывных волокон, при низком потреблении энергоносителей обеспечивает интенсивное плавление базальтов, гомогенизацию, аморфность расплава и удаление газов из расплава, обеспечить стабильный и безобрывный процесс вытяжки волокон, повысить производительность и качество непрерывных волокон.
Наиболее близким к заявляемому устройству по совокупности признаков и достигаемому результату является устройство для производства непрерывных волокон из базальтовых пород, которое содержит загрузчик базальта, состоящий из бункера и дозатора и загрузочной воронки, систему отопления печи, которая состоит из двух или более горелок, расположенных в своде печи; горелки последовательно соединены со смесителем газовоздушной смеси и рекуператором, рекуператор через двухходовой коллектор дымоудаления соединен с фидером печи, плавильную печь, состоящую из печи и фидера, который является продолжением ванны, в фидере печи за порогом ванны установлен фильерный питатель, под фильерным питателем размещены механизм нанесения замасливателя и наматывающая машина UA 77861 [3].
Недостаток устройства заключается в том, что базальтовое сырье загружается в печь при температуре окружающей среды – холодным – и на его нагрев требуется дополнительная тепловая энергия, что снижает температуры в зоне загрузки и плавления базальта, загрузочная воронка удалена от места установки плавильной горелки, поэтому базальт попадает в расплав ванны печи вне зоны действия высоких температур пламени горелки. Расплав в зоне плавления имеет ту же глубину, что и в ванне печи, что обусловливает низкие температуры на дне ванны в зоне плавления. При этом холодный базальт в зоне загрузки сразу тонет в расплаве и оседает на дне ванны печи, что затрудняет плавление базальта, дегазацию и гомогенизацию расплава. Затем расплав, содержащий непроплавленные сгустки и пузырьки газов из ванны печи, попадает в фидер печи и на фильерный питатель, что приводит к обрывности волокон, снижению производительности выработки непрерывных волокон. Плавление базальта на дне ванны не обеспечивает полное плавление базальта и особенно высокотемпературных включений в базальт: андезитов, кварца, слюды и др. Это приводит к тому, что расплав содержит сгустки непроплавленных кристаллических структур базальта и других минералов. Однако даже при этом непроплавленные кристаллические структуры базальтов попадают в аморфные волокна, что приводит к снижению их прочности и эластичности. Величина кристаллов соизмерима с диаметрами волокон 6-21 мкм и в местах наличия кристаллов волокна легко ломаются.
Для исключения указанных отрицательных факторов при производстве непрерывных волокон нужно увеличивать температуру во всем рабочем пространстве печи в зоне плавления, ванной печи и фидере печи, нагревать фильерный питатель до высоких температур.
Сложности плавления базальта на дне ванны расплава ограничивают диапазон использования устройства определенными видами базальтовых пород с низкой температурой плавления и без высокотемпературных включений. Это также ограничивает интенсивность подачи базальтового сырья в зону плавления, что снижает производительность устройства в целом.
Поддержание высоких температур в рабочем пространстве печи и на фильерном питателе требует повышенного расхода энергоносителей, что не удовлетворяет требованиям экономичности и производительности процесса производства базальтовых непрерывных волокон.
Техническим результатом изобретения является производство непрерывных волокон с высокими характеристиками по прочности, эластичности и термостойкости, повышение производительности и снижение затрат энергоносителей, что достигается усовершенствованием устройства для производства непрерывных волокон из базальтовых пород, нагревом базальта в бункере загрузчика от дополнительного рекуператора, установкой на своде печи в зоне загрузки горелки-загрузчика, а под ней на дне ванны печи плавильной площадки, что обеспечивает высокие температуры плавления базальта, гомогенизацию, аморфность и дегазацию расплава в зоне плавления и тем самым создает оптимальные условия для подготовки расплава перед его выработкой на фильерном питателе.
Технический результат достигается тем, что устройство для производства непрерывных волокон из базальтовых пород, содержащее загрузчик базальта, состоящий из бункера и дозатора, плавильную печь с вытянутым в горизонтальном направлении рабочим пространством, включающим ванну и фидер печи, который является продолжением ванны, ванна и фидер печи перекрыты сводом, в своде размещены две или более горелки, горелки последовательно соединены со смесителем газовоздушной смеси и рекуператором, рекуператор через двухходовой коллектор дымоудаления соединен с фидером печи, в фидере печи за порогом ванны установлен фильерный питатель, под которым размещены механизм нанесения замасливателя и наматывающая машина, отличается тем, что совместно с рекуператором установлен дополнительный рекуператор, который патрубком соединен с загрузчиком базальта, горелка-загрузчик на своде печи, под которой на дне ванны размещена плавильная площадка, которая совместно с горелкой-загрузчиком создают локальную зону плавления базальта, дегазации и гомогенизации расплава.
Наличие плавильной площадки позволяет снизить уровень расплава в зоне плавления до 5-70 мм при уровне расплава в ванной печи 80-300 мм. Незначительная глубина расплава под горелкой-загрузчиком в зоне плавления обеспечивает высокие температуры расплава, а следовательно, малую вязкость расплава, что обеспечивает выход из расплава пузырьков газов – дегазацию расплава. А также полное плавление базальтов, включая плавление высокотемпературных включений и кислых базальтов с повышенным содержанием SiO2 и Al2O3. Высоту плавильной площадки выбирают в зависимости от фракции базальта его химического состава, наличия примесей и характеристик плавления базальтовой породы. При этом плавильная площадка может быть выполнена горизонтально плоской, или вогнутой, или наклонной.
Целесообразно объединить загрузочную воронку и газовую горелку в горелку-загрузчик, которая состоит из загрузочной воронки, расположенной по центру и охватывающей ее кольцом горелки. Загрузка базальта осуществляется через горелку-загрузчик на плавильную площадку в зону действия пламени горелки. Горелка-загрузчик устанавливается на своде печи, при этом горелок-загрузчиков может быть установлено как одна, так и несколько.
На площадке плавления под горелкой-загрузчиком происходит активное плавление базальта, его переход из кристаллической формы в расплавленную аморфную со степенью аморфности более 96%. Отсутствие непроплавленных кристаллических структур и пузырьков газов в расплаве базальтов обеспечивает стабильность и безобрывность выработки непрерывных волокон, повышение производительности устройства.
Целесообразно также оснащать устройство дополнительным рекуператором, совмещенным основным рекуператором, при этом выход дополнительного рекуператора через патрубок подсоединен с бункером загрузчика базальта.
Подогрев измельченной базальтовой породы в загрузочном бункере до температур 250-400°С позволяет исключить попадание базальта в печь со свободной влагой, обеспечить высокие температуры плавления базальта на плавильной площадке, повысить производительность устройства и снизить расход газа.
На чертеже изображено устройство для реализации предлагаемого способа плавления базальтовых пород.
Загрузчик-дозатор (1) базальта. Горелка-загрузчик (2). Горелка (3). Плавильная печь (4). Свод (5) печи. Ванна (6) печи. Плавильная площадка (7). Порог (8) печи. Фидер (9). Коллектор (10) дымоудаления. Рекуператор (11). Дополнительный рекуператор (12) с патрубком. Смеситель (13) газ-воздух. Фильерный питатель (14). Механизм (15) нанесения замасливателя. Наматывающая машина (16).
Устройство для реализации предлагаемого способа, производства волокон из базальтовых пород представлено на чертеже. Устройство содержит: загрузчик-дозатор (1) базальта, горелку-загрузчик (2), горелку (3), плавильную печь (4), свод (5) печи, ванну (6) печи, плавильную площадку (7), порог (8) печи, фидер (9), коллектор (10) дымоудаления, рекуператор (11), дополнительный рекуператор (12) с патрубком, смеситель (13) газ-воздух, фильерный питатель (14), механизм (15) нанесения замасливателя, наматывающую машину (16).
Устройство работает следующим образом. Измельченная базальтовая порода загружается в бункер загрузчика-дозатора (1), где происходит ее нагрев горячим воздухом от патрубка дополнительного рекуператора (12) до температуры 250-400°С. Базальт из загрузчика-дозатора (1) небольшими порциями по 50-300 грамм загружается в плавильную печь, с тем чтобы поддерживать постоянным 20-80 мм уровень расплава базальта над фильерным питателем. Базальт через горелку-загрузчик (2), расположенную на своде (5) печи, загружается на плавильную площадку (7) в зону плавления плавильной печи (4). При попадании базальтового сырья на плавильную площадку (7) он не тонет в расплаве, а находится на поверхности в зоне действия максимальных температур пламени горелки-загрузчика (2). На плавильной площадке (7) в зоне наивысших температур при низком уровне расплава 5-70 мм происходит активное плавление базальтов и тугоплавких включений, дегазация расплава. С площадки (7) расплав перетекает в ванну (6) печи, где уровень расплава составляет 80-250 мм, при этом происходит перемешивание и гомогенизация расплава. В ванне (6) печи происходит подготовка расплава в выработке в фидере (9).
Плавильная печь (4) имеет зону плавления с плавильной площадкой (7), ванну (6) и фидер (9) печи с фильерным питателем (14). Ванна (6) через порог (8) соединена с фидером (9) печи, за порогом (8) печи установлен фильерный питатель (14).
Поскольку плавление базальтов происходит при высоких температурах до 2000°С в зоне плавления, нет необходимости поддерживать высокие температуры в ванне (6) и фидере (9) печи. На пороге ванны (6) уровень расплава снова уменьшается и поддерживается на уровне 20-80 мм от уровня фильерного питателя. Поступление гомогенизированного с высокой степенью аморфности, дегазированного расплава в фильерный питатель позволяет снизить его температуру до температуры верхнего предела кристаллизации расплава базальта (Твпк) и даже на 30-200°С ниже Твпк, обеспечить стабильность и производительность производства непрерывных базальтовых волокон.
Дополнительный рекуператор (12) с патрубком устанавливается совместно с основным рекуператором (11). На рекуператор (11) и дополнительный рекуператор (12) из рабочего пространства плавильной печи (4) через коллектор (10) дымоудаления подаются высокотемпературные газы. Рекуператор (11) обеспечивает подогрев воздуха до температуры 400°С, который подается на смеситель (13) газ-воздух и на газовые горелки (2) и (3). Дополнительный рекуператор (12) служит для нагрева базальта в бункере загрузчика до температур 250-400°С.
Плавление базальта осуществляется горелкой-загрузчиком (2) и горелкой (3). Горелка-загрузчик (2) расположена на своде (5) печи, непосредственно над плавильной площадкой (7).
Горелка-загрузчик (2) состоит из загрузочной воронки, расположенной по центру и охватывающей ее кольцом горелки предварительного смешения. Горелок-загрузчиков (2) может быть установлено на своде печи (5) как одна, так и несколько.
Горелка-загрузчик (2) и плавильная площадка (6) совместно создают высокотемпературную локальную зону плавления базальта, дегазации и гомогенизации расплава. Горелка (3) обеспечивает дополнительный подогрев расплава базальта.
Загрузка подогретого базальтового сырья осуществляется через горелку-загрузчик (2) в зону действия пламени горелки на плавильную площадку. Пламя горелки позволяет создавать температуры от 1450°С до 2000°С в зоне плавления. Это обеспечивает наиболее благоприятный режим интенсивного плавления базальта на плавильной площадке – в локальной зоне плавления.
Плавление базальта при таких температурах позволяет производить прочные, эластичные и высокотемпературные волокна из андезито-базальтов, андезитов, амфиболитов, порфиритов, диабазов, габбро, базальтовых пород и минерального сырья, имеющих повышенное содержание SiO2, Al2O3 и других оксидов, обеспечивающих прочностные и термические характеристики волокон.
Для обеспечения интенсивного плавления базальтовой породы, гомогенизации и дегазации расплава в зоне плавления на дне ванны (6) плавильной печи (4) установлена плавильная площадка (7). Уровень расплава над плавильной площадкой (7) составляет 5-70 мм. Уровень расплава над плавильной площадкой зависит от величины фракции базальта, его химического состава, наличия примесей и характеристик плавления базальтовой породы. Уровень расплава в ванне печи находится в пределах 80-300 мм.
На площадке (7) плавления в зоне наивысших температур при низком уровне расплава происходит активное плавление базальта – переход его из кристаллического в расплавленное аморфное состояние, проплавление инородных включений и дегазация расплава. При этом расплав из зоны плавления перетекает в зону действия второй горелки (3) и ванну (6) печи. При стекании расплава базальта с площадки плавления в ванну (6) печи происходит перемешивание расплава, процессы гомогенизации и дегазации проходят более активно. В ванне (6) печи происходит гомогенизация расплава и подготовка расплава к выработке в фидере (9) печи.
За ванной (6) печи через порог (8) расположен фидер (9), в котором установлен фильерный питатель (14).
Из расплава через фильерный питатель (14) происходит вытяжка первичных волокон. Вытяжка волокон осуществляется наматывающей машиной (16), перед намоткой на волокно механизмом (15) наносится замасливатель.
Для простоты изложения на чертеже показана конструкция плавильной печи с одной горелкой-загрузчиком (2) и оводовой горелкой (3), однако количество горелок может установлено больше.
Данный способ и устройство позволяют использовать для производства волокон базальты более широкого диапазона химического состава и обеспечивают получение аморфных, гомогенизированных и дегазированных расплавов для производства непрерывных волокон диаметром 6-21 мкм.
Способ производства непрерывных волокон из базальтовых пород и устройство для его осуществления позволяют технологически и конструктивно реализовать технологические процессы активного плавления базальтовых пород и перехода их в аморфное состояние, гомогенизации и дегазации расплава, снизить энергопотребление, повысить производительность и обеспечить производство непрерывных волокон с высокими характеристиками по прочности, эластичности и термической стойкости.
Пример реализации изобретения.
В НПО «Вулкан» г.Оса Пермского края работают установки BCF 1C и BCF 2C в составе технологической линии ТЕ BCF-2000 для производства базальтового непрерывного волокна. При изготовлении установок BCF 1C и BCF 2C использованы технические решения данного изобретения.
Установки BCF 1C и BCF 2C имеют следующие основные технические характеристики.
Основные технические характеристики | BCF 1C | BCF 2C |
Производительность установок при производстве БНВ | ||
диаметром (при фильерном питателе на 200 фильер): | ||
9 мкм | 10 кг/час | 20 кг/час |
13 мкм | 12 кг/час | 25 кг/час |
Потребление природного газа (при калорийности 7900 кКал/м3) | 6-7 м3/час | 12-14 м3/час |
Потребление электроэнергии на нагрев фильерного питателя | 3.5-4 кВт час | 7-8 кВт час |
Вес бобины первичного непрерывного волокна | 3.5-5 кг | |
Длина первичных непрерывных волокон на первичной бобине | 40-60 км |
По сравнению с установками BCF 1 и BCF 2, изготовленными на основе технических решений патента прототипа №77861 UK, у установок BCF 1C и BCF 2C удельный расход природного газа на производство 1 кг БНВ снижен на 30% до 0.6 м3 на кг базальтового непрерывного волокна (БНВ) электроэнергии – на 55% до 0.4 кВт на кг БНВ.
Производительность производства БНВ увеличена на 28-35%.
Характеристики производимого ровинга БНВ соответствуют техническим условиям (ТУ) на ровинг БНВ.
Для производства БНВ используются долериты с повышенным содержанием оксидов кремния и алюминия.
Источники информации
1. РСТ. WO 98/22401. 1998. Доманов Г.П., Асланова Л.Г. и др. Способ получения базальтового волокна и устройство для его осуществления.
2. RU 2193538. Способ и устройство для производства базальтовых волокон.
3. UA 77861. МПК G03B 37/00. Оснос С.П. Способ и устройство для производства волокон из базальтовых пород.
1. Способ производства волокон из базальтовых пород, который состоит в использовании основных базальтов диапазона (%): SiO2 45-56, Al2O3 10-19, TiO2 0,9-2,0, Fe2O3 и FeO 7-18, CaO 6-15, MgO и MnO 3-7, Na2O и K2O 2,5-6 и соотношения основных волокнообразующих оксидов и сопутствующих оксидов в пределах 3,2>(SiO2 + Al2O3)/(TiO2 + Fe2O3 + FeO + CaO + MgO + MnO + K2O + Na2O)>1,6, загрузке измельченного базальта в расплав ванны плавильной печи, плавлении базальта в диапазоне температур Тп на 150-200°С выше температуры верхнего предела кристаллизации Твпк до достижения степени аморфности 90-96%, гомогенизации и стабилизации расплава в диапазоне температур Тс на 80-160°С выше Твпк, стабилизации уровня расплава в фидере печи на уровне 20-80 мм над фильерным питателем, при этом плавление, гомогенизация и выработка расплава производится одностадийно в ванне и фидере печи, вытяжка волокон через фильерный питатель производится в диапазоне температур Тв на 15-60°С выше Твпк, нанесении замасливателя на волокна и намотке волокон на бобины, отличающийся тем, что базальт предварительно перед загрузкой подогревают до температур 250-400°С, а загрузку базальта осуществляют в зону максимальных температур 1450-2000°С пламени горелки-загрузчика, плавление, дегазацию и гомогенизацию расплава производят на плавильной площадке при низких уровнях расплава 5-70 мм с последующим увеличением уровня расплава до 80-300 мм в ванне печи.
2. Способ по п.1, отличающийся тем, что вытяжку волокон осуществляют при температуре фильерного питателя на 30-200°С ниже температуры верхнего предела кристаллизации расплава базальта Твпк.
3. Устройство для производства непрерывных волокон из базальтовых пород, содержащее загрузчик базальта, состоящий из бункера и дозатора, плавильную печь с вытянутым в горизонтальном направлении рабочим пространством, включающим ванну и фидер печи, который является продолжением ванны, ванна и фидер печи перекрыты сводом, в своде размещены две и более горелки, горелки последовательно соединены со смесителем газо-воздушной смеси и рекуператором, рекуператор через двухходовой коллектор дымоудаления соединен с фидером печи, в фидере печи за порогом ванны установлен фильерный питатель, под которым размещены механизм нанесения замасливателя и наматывающая машина, отличающееся тем, что на своде в зоне загрузки базальта установлена горелка-загрузчик, под которой на дне ванны размещена плавильная площадка, обеспечивающая уровень расплава от 5 до 70 мм, с последующим увеличением уровня расплава в ванне печи до 80-300 мм.
4. Устройство по п.3, отличающееся тем, что загрузочная воронка и горелка конструктивно объединены в одну горелку-загрузчик, состоящую из загрузочной воронки, расположенной по центру, и охватывающей ее кольцом горелки, горелка-загрузчик расположена в своде печи над плавильной площадкой, при этом горелка-загрузчик может быть установлена одна и более.
5. Устройство по п.4, отличающееся тем, что верхняя поверхность плавильной площадки может быть выполнена наклонной в сторону ванны.
6. Устройство по любому из пп.4-5, отличающееся тем, что оно снабжено дополнительным рекуператором, совмещенным с основным рекуператором, при этом выход дополнительного рекуператора через патрубок подсоединен к бункеру загрузчика базальта.
www.findpatent.ru
Химический состав базальтов — Мегаобучалка
Средний химический состав базальта по P. Дэли (%): SiO2 – 49,06; TiO2 – 1,36; Аl2O3 – 15,70; Fe2O3 – 5,38; FeO – 6,37; MgO – 6,17; CaO – 8,95; Na2O – 3,11; K2O – 1,52; MnO – 0,31; P2O5 – 0,45; H2O – 1,62. Cодержание SiO2 в базальте колеблется от 44 до 53,5%. По химическому и минеральному составу выделяют оливиновые ненасыщенные кремнезёмом (SiO2 около 45%) базальты и безоливиновые или c незначительным содержанием оливина слабо пресыщенные кремнезёмом (SiO2 около 50%) толеитовые базальты.
Физико-механические свойства базальта весьма различны, что объясняется разной пористостью. Базальтовые магмы, обладая низкой вязкостью, легко подвижны и характеризуются разнообразием форм залегания (покровы, потоки, дайки, пластовые залежи). Для базальта характерна столбчатая, реже шаровидная отдельность. Оливиновые базальты известны на дне океанов, океанических островах (Гавайи) и широко развиты в складчатых поясах. Толеитовые базальты занимают обширные площади на платформах (трапповые формации Сибири, Южной Америки, Индии). C породами трапповой формации связаны месторождения руд железа, никеля, платины, исландского шпата (Сибирь). B миндалекаменных базальтовых порфиритах района Верхнего озера в США известно месторождение самородной меди.
Плотность базальта 2520-2970 кг/м³. Коэффициент пористости 0,6-19%, водопоглощение 0,15-10,2%, сопротивление сжатию 60-400 Мпа, истираемость 1-20 кг/м², температура плавления 1100-1250°C, иногда до 1450°C, удельная теплоёмкость 0,84 Дж/кг•К при 0°C, модуль Юнга (6,2-11,3)•104 Мпa, модуль сдвига (2,75-3,46)•104 Мпa, коэффициент Пуассона 0,20-0,25. Высокая прочность базальта и относительно низкая температура плавления обусловили применение его в качестве строительного камня и сырья для Каменного литья и минеральной ваты. Базальт широко используется для получения щебня, дорожного (бортового и брусчатки) и облицовочного камней, кислотоупорного и щелочестойкого материала. Требования промышленности к качеству базальта как сырью для щебня такие же, как и к другим изверженным породам. Для производства минеральной ваты базальт используется обычно в шихтовке. Установлено, что температура плавления сырья не должна превышать 1500°C, a химический состав расплава регламентируется следующими пределами (%): SiO2 – 34-45, Al2O3 – 12-18, FeO до 10, CaO – 22-30, MgO – 8-14, MnO – 1-3. Камнелитейные материалы из базальта обладают большой химической стойкостью, твёрдостью и сопротивлением к истиранию, высокой диэлектричностью и используются в виде плит для полов и облицовки, футеровки трубопроводов, циклонов, a также в качестве различных изоляторов.
Физико-механические свойства базальтов и андезито-базальтов весьма разнородны. Это объясняется разнообразием минерального состава, структуры и текстуры пород. Так, базальты микрокристаллической структуры имеют удельный вес до 3,3 Т/м3, объемный вес до 3,0 Т/м3, временное сопротивление сжатию до 5000 кГ/см2, тогда как в пористых базальтах величина прочности на сжатие может быть менее 200 кГ/см2. Древние палеотипные эффузивные породы также характеризуются большой изменчивостью прочностных и деформационных свойств, но в общем имеют более высокие значения этих показателей. Объясняется это раскристаллизацией вулканического стекла, заполнением пор вторичными минералами и другими постмагматическими преобразованиями излившихся пород. Интересные данные о связи прочности андезито-базальтов с их составом, структурой и пористостью приводит Н. В. Овсянников, по которым видно, что прочность андезито-базальтов существенно зависит от минералогического состава.
Наибольшей прочностью обладают оливиновые разности, а наименьшей — авгитовые. Не менее важна и структура породы. Андезито-базальты одинакового состава с витрофировой структурой основной массы имеют значительно меньшую прочность, чем породы с интерсертальной структурой. Исследования В. М. Ладыгина и Л. В. Шаумян позволили установить, что базальты различного петрохимического состава и разной структуры имеют разные физико-механические свойства. Наиболее прочными являются массивные неизмененные порфировые базальты с микродиабазовой и микродолеритовой структурой. Прочность их в среднем составляет 2000 кГ/см2, достигая в отдельных случаях 2800 кГ/см2 при объемном весе 2,80 Г/см3. Динамический модуль упругости пород в массиве в среднем равен 690•103 кГ/см2. В миндалекаменных базальтах влияние структурных и минералогических особенностей породы нивелируется наличием миндалин, содержание которых достигает 15—30%. Для них характерны относительно низкие значения прочности (1200 кГ/см2), модуля упругости (480•103 кГ/см2) и объемного веса (2,66 Г/см3). Установлено, что увеличение содержания денитрифицированного стекла до 10—15% снижает прочность базальтов на 10—20%, такое же влияние оказывает и присутствие миндалин в количестве 10—20%. У выветренных разностей пород прочность резко снижается. Степень выветрелости базальтовых пород и мощность коры выветривания в общем случае зависят от их возраста и климатических условий.
Базальт – аналог габбро – самая распространенная излившаяся порода; в зависимости от условий образования имеет стекловатую или скрытнокристаллическую структуру. Цвет базальта – темно-серый до черного. По физико-механическим показателям базальт аналогичен габбро, а по прочности даже превосходит его (Лсж достигает 500 МПа). Базальты очень твердые, но хрупкие породы, что затрудняет их обработку.
Применение базальта
Практическое применение базальта строительные материалы, изготовленные из этого камня, широко используются в строительстве, поскольку им присущи: устойчивость к истиранию, к влиянию щелочей и кислот, отличные показатели теплоизоляции и шумопоглощения, прочность, термоустойчивость и огнеупорность, высокая диэлектричность, долговечность, паропроницаемость и, что не менее важно, экологичность.
Данный минерал используют в качестве строительного камня, для производства минеральной ваты, наполнителя для бетона и каменного литья. Из него также делают дорожные и облицовочные камни, получают щебень и кислотоупорный порошок. Облицовочные плиты на данный момент одновременно с декоративной целью выполняют функцию изоляторов. Благодаря устойчивости к атмосферным воздействиям, базальт хорошо подходит для отделки внешней части строений, а также для отливания уличных скульптур.
Производство базальта и продукции на его основе чаще всего производство базальта – это горнодобывающая отрасль. В специальных карьерах и рудниках добывается камень, на основе которого в последствии производится разная продукция. В виде базальтового волокна этот минерал применяется для утепления зданий и крыш, в трехслойных панелях-сэндвичах, изоляции низкотемпературных агрегатов оборудования при извлечении азота и создании кислородных колонн, для тепло- и звукоизоляции трубопроводов, плит, каминов и других жаровен, энергетических агрегатов и в целом зданий и сооружений любого назначения. Базальт в расплавленном виде применяется для создания ступеней лестниц, фасонных плиток и других строительных материалов. Из него отливают аппараты произвольных форм, среди которых подставки для аккумуляторов, а также изоляторы для сетей с напряжением различной величины. Порошок из такого материала используется для производства прессованных армированных изделий.
Распространенные виды базальта отличаются друг от друга различными показателями, в первую очередь, такими как цвет и структура. Самой известной торговой маркой является разновидность под наименованием «Базальтина». Это материал итальянского происхождения, который добывают недалеко от столицы этой страны и используют в основном в архитектурных целях ещё со времён Древнего Рима. Его прочность сравнима с прочностью гранита, а декоративные качества с декоративными качествами известняка. Камень после укладки долго сохраняет насыщенность цветовой палитры. Поэтому его стоимость нередко превышает цену иных торговых марок более в чем в два раза.
Другая разновидность – азиатская. Её отличает тёмно-серая окраска и умеренная цена. Его широко используют в дизайнерских и архитектурных целях.
Мавританский зелёный базальт имеет насыщенный тёмно-зелёный оттенок, с присутствующими в нем различными вкраплениями, которые придают камню оригинальный внешний вид при сохранении всех физико-механических характеристик. Только критерии твёрдости и морозостойкости несколько ниже.
Сумеречный базальт привозят из Китая. Он имеет дымчато-серый или чёрный цвет. Его признают самым крепким и износо- и морозостойким среди всех разновидностей данного минерала. Он хорошо защищён от негативного атмосферного воздействия.
Самые известные изделия из базальта: утеплители на базальтовой основе, базальтовая плитка отделочная, базальтовые дымоходы для каминов и печей.
Графики
Рис.8 Лунный базальт: диаграмма
“Температура Дебая химического элемента (Q) – Коэффициент концентрации (Kk)”
Рис.9 Лунный базальт: диаграмма
“Температура Дебая химического элемента (Q) – Содержание химического элемента (С)”
Рис.10 Базальт: диаграмма
“Масса атома химического элемента (М) – Содержание химического элемента (С)”
Рис.11 Лунный базальт: диаграмма
“Масса атома химического элемента (М) – Коэффициент концентрации (Kk)”
Рис.12 Лунный базальт: диаграмма
“Расстояние до инертного газа химического элемента (е) – Коэффициент концентрации (Kk)”
Рис.13 Лунный базальт: диаграмма
“Расстояние до инертного газа химического элемента (е) – Содержание химического элемента (С)”
Приложение А
Приложение Б
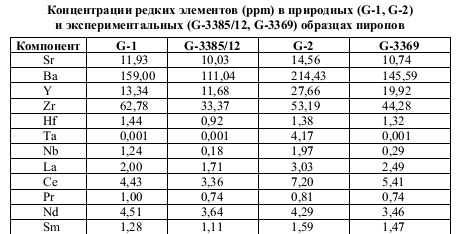
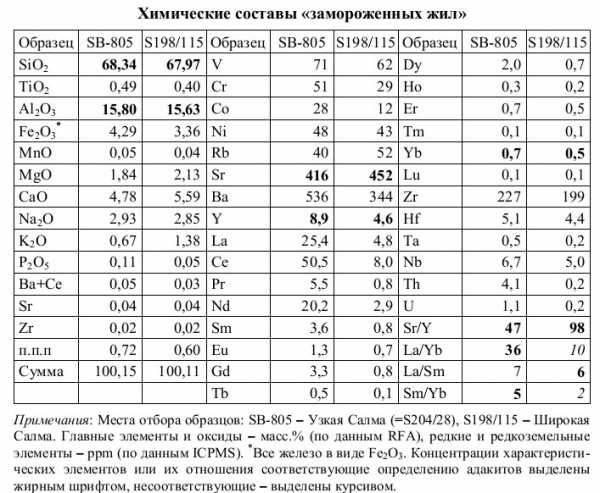
ЛИТЕРАТУРА
1. Бондаренко C.В. Геохимические особенности кварцитов нижнего протерозоя в центральной части Южно-Печенгская зоны./ C.В. Бондаренко, В.А. Шатров, В.И. Сиротин // Геология и геоэкология: исследования молодых. Материалы XVI конференции молодых ученых, посвященной памяти чл.-кор. К.О. Кратца. Под ред. акад. РАН Митрофанова Ф.П – Апатиты, 2005. – 426 с.
2. Гумиров Ш.Ш. Моделирование процесса твердофазной диффузии. /Сбор.тез. участ. 15 Росс. конф. «Юность, наука, культура».- Обнинск: ДНТО Интеллект будущего, 2000.- с.112-113.
3. Гумиров Ш.В. Участие импульса атома в биохимии, углефикации, минерагенезе. / Ш.В. Гумиров – Наукоемкие технологии разработки и использования минеральных ресурсов : сб. науч. статей / Сиб. гос. индустр. ун-т; под общей ред. В.Н.Фрянова. – Новокузнецк, 2014.– с. 345-355.
4. Гумиров Ш.В. Моделирование твердофазной диффузии элементов для объяснения их дифференциации в литосфере и рудогенеза. – Естественные и технические науки, №1, 2008. – с. 183-188.
5. Гумиров Ш.В. Основы теории адаптации неживых объектов и адаптивный анализ в геологии. /Ш.В. Гумиров – Новокузнецк, СМИ, 1993. – 409 с.
6. Гумиров Ш.В. Моделирование процесса твердофазной диффузии химических элементов для объяснения их дифференциации в литосфере. / Ш.В.Гумиров, Ш.Ш. Гумиров // Вестник РАЕН (Западно-Сибирское отделение) Выпуск 5. Кемерово, 2002 г.- С. 273-282.
7. Конилов А.Н. Петрология «Замороженных жил» в эклогитах Беломорской провинции на Кольском полуострове. / А.Н. Конилов, А.А. Щипанский. // Физико-химические факторы петро- и рудогенеза: новые рубежи. Мат. конф. посв. 110-лет. Д.С. Коржинского. – М., 2009.- с. 198-203.
8. Лазько Е.М. Термобарогеохимия и прогнозирование постмагматического оруденения. / Е.М. Лазько и др. // Термобарохимические исследования процессов минералообразования. – Новосибирск: Наука, 1988. – С. 136 – 149.
9. Медведев В.Я. Влияние шоковой декомпрессии на распределение LIL – и HFS-элементов в пиропах из кимберлитов. / В.Я. Медведев, К.Н. Егоров, Л.А. Иванова // Физико-химические факторы петро- и рудогенеза: новые рубежи. Мат. конф. посв. 110-лет. Д.С. Коржинского. – М., 2009.- с. 269-271.
10. Овчинников Л.Н. Образование рудных месторождений. / Л.Н. Овчинников – М.: Недра, 1988. – 255 с.
11. Рундквист Д.В. Общие принципы построения геолого – генетических моделей рудных формаций. Т.1. / Д.В. Рундквист – Новосибирск: Наука, 1983. – С. 14 – 26.
12. Anand М. Petrology and geochemistry of LaPaz Icefield 02205:A new unique low-Ti mare-basalt meteorite. / M. Anand, Lawrence A. Taylor, Christine Floss, Clive R. Neal, Kentaro Terada, Shiho Tanikawa.
megaobuchalka.ru
Базальт Википедия
Характерная столбчатая отдельность базальтаБаза́льт — магматическая вулканическая горная порода основного состава нормального ряда щёлочности из семейства базальтов. Название, возможно, происходит от греч. βασικός — «основной», или, по другой версии, от эфиопского basal (bselt, bsalt) — «кипящий», «железосодержащий камень», так как в рукописях Плиния Старшего упоминается, что первые базальты появились из Эфиопии. Плутоническим аналогом базальтов является габбро, а гипабиссальным аналогом — долериты. К разновидностям базальтов относят траппы. Преобладают среди других кайнотипных (слабо изменённых) вулканических пород[1].
В сейсмологии «базальтовым» называется нижний слой земной коры, выделяемый по повышенной скорости продольных сейсмических волн (VP = 6,5—7,2 км/с), характерной для базальтов. Толщина базальтового слоя на континентах достигает 20—35 км, в океанах не превышает 5—6 км[2]. Для определения природы «базальтового» слоя бурилась Кольская сверхглубокая скважина.
Структура и текстура
Обычно базальты это тёмно-серые, чёрные или зеленовато-чёрные породы, обладающие стекло-волокнистой, скрытокристаллической афировой или порфировой структурой. В порфировых разностях на фоне общей скрытокристаллической массы хорошо заметны мелкие вкрапленники зеленовато-жёлтых изометричных кристаллов оливина, светлого плагиоклаза или чёрных призм пироксенов. Размер вкрапленников может достигать несколько сантиметров в длину и составлять до 20—25 % от массы породы.
Текстура базальтов может быть плотной массивной, пористой, миндалекаменной. Миндалины обычно заполняются плагиоклазом, базальтической роговой обманкой, полевым шпатом, кальцитом, хлоритом и прочими вторичными минералами — такие базальты называются мандельштейнами.
Плотность (2,60—3,10 г/см3)[3].
Состав
- Минеральный состав
Основная масса сложена микролитами плагиоклазов, клинопироксена, магнетита или титаномагнетита, а также вулканическим стеклом. Вкрапленники, как уже было сказано, обычно представлены оливином, клинопироксеном, плагиоклазом, редко ортопироксеном или роговой обманкой. Наиболее распространённым акцессорным минералом является апатит.
- Химический состав
Содержание кремнезёма (SiO2) колеблется от 42 до 52—53 %, суммы щелочей Na2+K2 до 5 %, в щелочных базальтах до 7 %.
Оксид Содержание, %[4] SiO2 47—52 TiO2 1—2,5 Al2O3 14—18 Fe2O3 2—5 FeO 6—10 MnO 0,1—0,2 MgO 5—7 CaO 6—12 Na2O 1,5—3 K2O 0,1—1,5 P2O5 0,2—0,5
Большее значение имеет классификация базальтов на основании химического состава, который находится в определённом соответствии с их минеральным составом: например, содержание SiO2 увеличивается от мелилититов к базальту обыкновенному. По содержанию SiO2 все базальты делятся на три группы: основные, нейтральные и кислые. В группу основных базальтов входят: мелилитит оливиновый, мелилитит, нефелинит оливиновый, нефелинит, а также лимбургит и авгитит, которые характеризуются наличием стекловидной фазы. По химическому составу к этой группе относятся базальтовые породы, содержащие до 42 % SiO2. Следует отметить, что к группе основных базальтов должны быть отнесены образцы базальтов, доставленные с Луны. В их состав входит 40—42 % SiO2. Иногда из группы основных базальтов выделяют ультраосновные (мелилититы и нефелиниты оливиновые) с содержанием SiO2 менее 40 %. В группу нейтральных входят базальты с 43—46 % SiO2: базаниты, лейцититы и оливиновые лейцититы. В этих базальтах имеется полевой шпат. К группе кислых базальтов относятся базальт обыкновенный, базальт оливиновый и тефриты (свыше 46 % SiO2).
Вторичные изменения
Вследствие вторичных изменений исходно тёмно-серые или чёрные базальты обретают характерную зеленоватую окраску (т. н. зеленокаменное перерождение), а в больших массах проявляется характернейшая столбчатая отдельность в виде 3—7-гранных столбов. Происходят и минералогические изменения: стекло может замещаться палагонитом — аморфным гелеподобным веществом зеленоватого или желтоватого цвета, состоящим преимущественно из монтмориллонита; по клинопироксену развивается актинолит; по плагиоклазу — альбит и соссюрит. В целом же самыми распространёнными из вторичных минералов по базальту являются кальцит, пренит, цеолиты.
Распространённость
Трапповое плато ПуторанаБазальты — самые распространённые магматические породы на поверхности Земли и на других планетах Солнечной системы. Основная масса базальтов образуется в срединно-океанических хребтах и формирует океаническую кору. Кроме того базальты типичны для обстановок активных континентальных окраин, рифтогенеза и внутриплитного магматизма.
При кристаллизации по мере подъёма на поверхность Земли базальтовой магмы на глубине иногда образуются сильно дифференцированные по составу, расслоённые интрузии, в частности габбро-норитов (такие как Норильские, Садбери в Канаде и некоторые другие). В таких массивах встречаются месторождения медноникелевых руд и платиноидов.
Основные магматические горные породы в СНГ очень распространены. Они занимают, с учётом Сибирских траппов, 44,5 % площади территории СНГ и представляют большой интерес как сырьё. Известно более 200 месторождений базальтовых пород, из них более 50 месторождений эксплуатируются. В настоящее время базальты применяются не только в строительстве (щебень, штучный камень, облицовка зданий и др.) но и для производства каменного литья, петроситаллов, базальтовых волокон, сырья для получения портландцементного клинкера.
Месторождения базальтов встречаются в Узбекистане, на Камчатке, на Украине, в Армении, Алтае, в Забайкалье и в других районах. Из месторождений Армении известны Джермукское, Кэгбекское и Мозское. Большие залежи базальта открыты в Ровенской области, а также вблизи Донецка.
Происхождение
Базальты образуются при застывании излившегося на поверхность Земли, подразумевая под этим и дно океана, силикатного магматического расплава основного (базальтового) состава. Происхождение базальтовой магмы по одной из гипотез состоит в частичном плавлении типичных мантийных горных пород, гарцбургитов, верлитов и др. Состав выплавки определяется химическим и минеральным составом протолита (исходной породы), физико-химическими условиями плавления, степенью плавления и механизмом ухода расплава.
По геодинамической природе выделяются следующие типы базальтов:
- базальты срединно-океанических хребтов (сокращенно БСОХ, англ. MORB от mid-ocean ridge basalt),
- базальты активных континентальных окраин,
- внутриплитные базальты, которые можно подразделить на континентальные и океанические базальты.
Извержение базальтов срединно-океанических хребтов — важнейший в массовом отношении процесс в верхней части Земли.
Изменения
Базальты очень легко изменяются гидротермальными процессами. При этом плагиоклаз замещается серицитом, оливин — серпентином, основная масса хлоритизируется и в результате порода приобретает зеленоватый или синеватый цвет. Особенно интенсивно изменяются базальты, изливающиеся на дне морей. Они активно взаимодействуют с водой, при этом из них выносятся и оседают многие компоненты. Этот процесс имеет большое значение для геохимического баланса некоторых элементов. Так большая часть марганца поступает в океан именно таким способом. Взаимодействие с водой кардинальным образом меняет состав морских базальтов. Это влияние можно оценить и использовать для реконструкций условий древних океанов по базальтам.
При метаморфизме базальты, в зависимости от условий, превращаются: при относительно низких температурах (330—550 °C) и средних давлениях в зелёные сланцы, амфиболиты; при тех же температурах и значительных давлениях — в глаукофановые сланцы с разновидностью голубые сланцы, получившими своё название по голубому цвету входящих в их состав щелочных амфиболов; а при более высоких температурах и давлениях — в эклогиты, состоящие из пиропового граната и натриевого клинопироксена — омфацита.
Применение
Базальт используют как сырье для щебня, производства базальтового волокна (для производства теплозвукоизоляционных материалов, композитной базальтовой арматуры, и т. д.), каменного литья и кислотоупорного порошка, плиты мощения, брусчатки, облицовочных плит, а также в качестве наполнителя для бетона. Базальт весьма устойчив к атмосферному воздействию и потому часто используется для наружной отделки зданий и для изготовления скульптур, устанавливаемых на открытом воздухе и в качестве строительного и облицовочного материала. Также, начинается развиваться рынок производства арматуры из непрерывного базальтового волокна.
См. также
Примечания
Литература
- Краткий геологический словарь // под ред. проф. Г. И. Немкова. — М., «Недра», 1989.
- Практическое руководство по общей геологии // под ред. проф. Н. В. Короновского. — М., «Академия», 2007.
- Аблесимов Н. Е., Земцов А. Н. Релаксационные эффекты в неравновесных конденсированных системах. Базальты: от извержения до волокна. Москва, ИТиГ ДВО РАН, 2010. 400 с.
Ссылки
wikiredia.ru
описание, свойства, состав, применение базальта
Базальт (с греч. βασικός — основной) – эффузивная магматическая порода основного состава. Базальтовый слой пород выделяют в земной коре, и распространяется как на материковой так и на океанической коре. Базальт является эффузивным аналогом габбро.
Физические свойства базальта
Окраска темная: черная, темно-серая. Структура: плотное строение, тонкозернистое. Текстура пористая, миндалекаменная или массивная. Излом неровный. Шероховатый на ощупь. Удельный вес 2,6-3,11 г/см3. Твердость по шкале Мооса от 5 до 7. Температура плавления 1100 — 1450ºС. Прочность на сжатие горной породы достигает величины 400 МПа. Форма залегания породы чаще всего: потоки, покровы, купола, дайки. Формы отдельности столбчатая либо плитняковая.
Отличительные признаки. Для базальта характерно плотное, тонкозернистое строение, неровный излом, темная (большей частью черная) окраска, большая плотность.
Состав базальта
Минералогический состав базальта. Без микроскопа трудно определить состав. Под микроскопом наблюдается состав, аналогичный составу габбро. Базальт слагают оливин, авгит и полевой шпат (плагиоклаз).
Химический состав. SiO2 45-52%, Al2O3 15-18%, Fe3O4 8-15%, CaO 6-12%, MgO 5-7% и др.
Разновидности и фото базальта
- Трапп – базальт с пластовой отдельностью.
- Долерит – крупнозернистый базальт.
- Столбчатая отдельность базальтов
- Столбчатые базальты
- Столбчатые базальты
- Траппы
Происхождение базальтов
Образование базальтов происходит при излиянии и застывании лавы основного состава (содержание SiO2 45-52%), как на поверхности континентов, так и в глубинах океанов. Базальты являются самой распространенной магматической горной породой на планете, основная масса которых образуется именно в океанах, в срединно-океанических хребтах, формируя основание океанических тектонических плит (океаническую земную кору).
Базальты практически не подвергаются каким либо вторичным процессам после образования, являясь типичной кайнотипной вулканической породой. При гидротермальных процессах оливин замещается серпентином, а плагиоклаз серицитом, порода хлоритизируется и приобретает зеленоватый оттенок. Такие изменения характерны в основном для базальтов, образовавшихся в срединно-океанических хребтах.
В результате метаморфизма, в зависимости от условий базальты переходят в амфиболиты, зеленые и голубые сланцы.
Применение базальта
Базальт используется в качестве строительного, облицовочного, кислотоупорного материала, а также в качестве сырья для каменного литья. Добавление базальтовой фибры (стружки) повышает ударно-прочностные характеристики бетонных изделий в 5 раз.
Применяют породу для изготовления широко применяемого теплоизоляционного материала — каменной ваты или, как ее еще называют, базальтового волокна. Для изготовления базальтовой ваты базальтовую щебенку возвращают до состояния жидкой лавы — плавят, и при помощи несложного механизма преобразовывают жидкий базальт в тонкие нити, которые и слагают каменную вату.
Месторождения базальтов
Базальты по распространению преобладают среди всех вулканических пород. В России базальт встречается на Камчатке, на Алтае (Синюхинское), в Забайкалье (Ангаро-Илимское, Зандинское), Хабаровском крае (Холдаминское, Марусинское).
Есть крупные месторождения в Армении (Джермукское, Мозское и Когбекское), на Украине (Иванчинское, Ивано-Долинское, Берестовецкое), Эфиопии, Индии (Джаканское плоскогорье).
www.geolib.net